端盖冲压模具设计资料讲解
轴承端盖冲压工艺分析及冲压模具设计

轴承端盖冲压工艺分析及冲压模具设计Summary:轴承端盖冲压工艺追求零件工艺参数计算的精准与设备选择的正确,它设计模具结构对零件伸拉过程中可能产生的拉裂现象进行分析,并提出相应技术解决措施。
本文中就分析了轴承端盖冲压工艺与冲压模具的设计技术要点,对主要零件的设计与与标准件选用、冲压设备的选择与校核进行了深度剖析。
Keys:轴承端盖;冲压工艺;冲压模具设计;标准件选用、冲压设备校核轴承端盖属于手扶拖拉机就中的重要零部件,它在装配后会直接外露表面,且对零件提出了诸多技术要求,例如表面划伤划痕要在0.15mm以内,且不允许出现任何拉裂、起皱、缺料等等缺陷问题。
一般来说轴承端盖的生产批量较大,每年产量超过10000件,所以针对它的冲压工艺与冲压模具设计必须做到技术娴熟、精细到位。
1.轴承端盖工件的基本工艺设计分析图1轴承端盖工件的基本结构示意CAD图如图1为待加工的轴承端盖工件,它的零件制作材料选择了硬度较高的08F钢,针对生产要求追求小批量,它的材料厚度一般设置为1.5mm左右,采用工件CAD图配合优质碳素结构钢进行制作,这其中所采用到的08F钢中含碳质量大约为0.07%~0.20%(低碳钢)。
轴承端盖的抗剪切强度一般控制在220~320MPa之间,它的屈服点也能达到180MPa左右,整体看来材料的焊接性与塑性表现相当好,适合冲裁施工。
从零件外形看来,其对零件的冲压制造需要围绕3步工序完成,它分别包括了落料、拉深与切边,结合3种方案展开级进模加工。
在具体施工中,要基于每道工序展开1套模具配合3套模具施工,有效提升生产效率,保证工件精度到位,最大限度节约搬运半成品时间与财力投入。
在施工过程中要保证模具制作到位,有效降低制造成本,提高生产效率,全面优化工件精度,最后提出最适合开展的轴承端盖冲压模具设计施工方案如下[1]:落料→拉深→切边→复合生产2.轴承端盖工件的重要工艺设计分析轴承端盖工件的重要工艺设计围绕多方面技术要点展开,下文简单谈3点。
端盖冲压工艺与模具设计综述

端盖冲压工艺与模具设计综述引言端盖是一种常见的机械设备零件,广泛应用于汽车、摩托车、工程机械等领域。
而端盖的成型过程中,冲压工艺和模具设计起着至关重要的作用。
本文将对端盖冲压工艺和模具设计进行综述,以帮助读者更全面地了解并掌握相关知识。
一、端盖冲压工艺概述1.1 端盖冲压工艺的定义冲压工艺是一种利用模具对金属材料进行变形、分离和加工的方法,通过冲击或压力使材料产生塑性变形,从而得到所需形状的工件。
端盖冲压工艺即指在冲压工艺中,针对端盖的加工特点进行的工艺处理。
1.2 端盖冲压工艺的优势端盖冲压工艺具有以下优势:•高效率:冲压工艺可以实现连续生产,提高生产效率;•高精度:冲压工艺可以获得高度精确的工件尺寸和形状;•节约材料:冲压工艺可以最大限度地利用材料,减少废料产生;•适应性强:冲压工艺适用于多种材料和复杂形状的加工。
二、端盖模具设计概述2.1 端盖模具设计的意义模具是冲压工艺中的关键设备,直接影响到冲压工艺的质量和效率。
端盖模具设计是为实现端盖冲压工艺提供必要的技术支持,保证工艺能够正常进行。
2.2 端盖模具设计的基本要求端盖模具设计需要满足以下基本要求:•合理性:模具设计应考虑到冲压工艺的特点,采取合理的设计方案,以确保工艺能够稳定、高效地进行;•易制造性:模具设计应考虑到模具的制造和维修难度,尽量采用标准化部件和加工工艺,以降低制造成本;•高可靠性:模具设计应确保模具在长期使用过程中具有较高的可靠性和寿命,减少故障和损坏的可能性。
2.3 端盖模具设计的关键技术端盖模具设计涉及到许多关键技术,包括但不限于以下几个方面:•模具结构设计:确定模具的整体结构,包括顶模、底模、导向机构等;•模具材料选择:选择适合冲压工艺的模具材料,考虑到材料的强度、硬度和耐磨性等;•模具零件设计:设计各个模具零件的形状和尺寸,包括模腔、模板、导向柱等;•模具热处理:对关键部件进行适当的热处理,提高模具的硬度和耐磨性;•模具装配和调试:对完成的模具进行装配和调试,确保模具的正常工作。
端盖冲压工艺及模具设计

端盖冲压工艺及模具设计端盖冲压工艺及模具设计端盖是一种常见的零部件,广泛应用于机械、电子、汽车等领域。
端盖的冲压工艺是一种重要的加工方法,它可以通过模具将金属板材快速成形为具有一定形状和尺寸的端盖。
在端盖冲压过程中,模具是起着重要作用的工具,模具的设计和加工质量是决定产品质量的关键。
一、端盖冲压工艺流程端盖的冲压过程一般分为下料、模具调试、冲压成形、清洁、涂装等几个环节。
1. 下料:下料是冲压工艺的第一步,它是根据产品图纸,按照板材的尺寸进行的。
下料可以采用剪板机、切割机等设备进行,将整张金属板分割成具有所需形状和尺寸的板材。
2. 模具调试:模具调试是为了适应端盖的尺寸和形状要求。
模具调试包括刀模的套装、修正,以及调整模具中央孔的大小等。
调试完成后,需要进行冲压测试,以确保成形品的尺寸、形状、表面质量等达到要求。
3. 冲压成形:冲压成形是将板材置于模具之间,施加一定的压力,使板材在模具的形状下变形,形成所需形状和尺寸的端盖。
在冲压过程中,需要对板材的表面进行保护,以免划伤或磨损。
4. 清洁:清洁是为了去除端盖上的铁锈、污渍等,制备好产品的表面。
清洁过程包括浸泡、刷洗、喷洒清洁剂等。
5. 涂装:涂装是为了提高端盖的容基性,增强其耐用性和耐腐蚀性。
涂装方式可以采用喷涂、浸涂、静电喷涂等。
二、端盖冲压模具设计1. 模具结构设计端盖冲压模具的结构设计要根据端盖的形状和尺寸进行模拟和分析。
具体的设计应该包括切口、冲头、冲模、定位、夹紧等结构。
切口、冲头和冲模是需要特别关注的部分,需要保证其准确度和可靠性。
定位和夹紧结构是为了保证制品的准确度和稳定性。
2. 材料选择模具材料需要具有足够的强度和硬度,以满足生产要求。
现在,常用的模具材料有高速钢、硬质合金、陶瓷、钢、塑料等。
需要注意的是,模具材料的选择要考虑到材料的性能、使用寿命、制造成本等因素。
3. 表面处理模具表面处理是为了提高其耐磨性和耐腐蚀性,延长模具使用寿命的关键。
端盖冲压成形工艺与模具设计
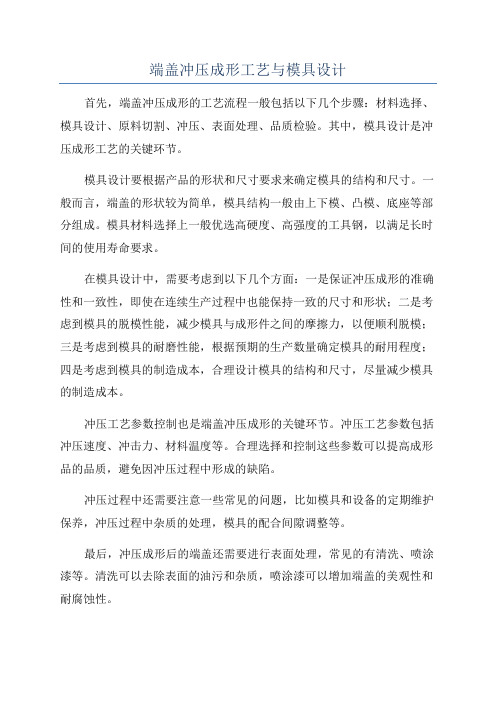
端盖冲压成形工艺与模具设计
首先,端盖冲压成形的工艺流程一般包括以下几个步骤:材料选择、模具设计、原料切割、冲压、表面处理、品质检验。
其中,模具设计是冲压成形工艺的关键环节。
模具设计要根据产品的形状和尺寸要求来确定模具的结构和尺寸。
一般而言,端盖的形状较为简单,模具结构一般由上下模、凸模、底座等部分组成。
模具材料选择上一般优选高硬度、高强度的工具钢,以满足长时间的使用寿命要求。
在模具设计中,需要考虑到以下几个方面:一是保证冲压成形的准确性和一致性,即使在连续生产过程中也能保持一致的尺寸和形状;二是考虑到模具的脱模性能,减少模具与成形件之间的摩擦力,以便顺利脱模;三是考虑到模具的耐磨性能,根据预期的生产数量确定模具的耐用程度;四是考虑到模具的制造成本,合理设计模具的结构和尺寸,尽量减少模具的制造成本。
冲压工艺参数控制也是端盖冲压成形的关键环节。
冲压工艺参数包括冲压速度、冲击力、材料温度等。
合理选择和控制这些参数可以提高成形品的品质,避免因冲压过程中形成的缺陷。
冲压过程中还需要注意一些常见的问题,比如模具和设备的定期维护保养,冲压过程中杂质的处理,模具的配合间隙调整等。
最后,冲压成形后的端盖还需要进行表面处理,常见的有清洗、喷涂漆等。
清洗可以去除表面的油污和杂质,喷涂漆可以增加端盖的美观性和耐腐蚀性。
总结来说,端盖冲压成形工艺与模具设计需要综合考虑材料选择、模
具设计、冲压工艺参数控制等多个因素。
通过合理的选择和控制这些因素,可以保证冲压成形的准确性和一致性,提高产品的质量,减少缺陷的发生。
同时,还需要重视模具和设备的定期维护保养,以延长模具的使用寿命,
减少生产中的故障。
端盖冲压工艺及模具设计说明书

端盖冲压工艺及模具设计说明书一、引言端盖是一种常用的金属制品,广泛应用于机械设备、汽车等领域。
端盖的生产过程中,冲压工艺和模具设计起着至关重要的作用。
本文档旨在介绍端盖的冲压工艺流程和模具的设计要点,以帮助读者了解并应用于实际生产。
二、冲压工艺流程端盖的冲压工艺流程主要包括材料准备、模具设计、冲压操作和零件加工。
1.材料准备材料准备是冲压工艺的第一步。
一般情况下,端盖的制作材料为金属板材,常用的材料有冷轧钢板、不锈钢板等。
在材料准备阶段,需要根据设计要求选择合适的材料,并进行切割、平整等处理。
2.模具设计模具设计是冲压工艺的关键。
模具的设计应根据端盖的形状和尺寸要求进行。
一般情况下,模具应包括上模、下模和导向装置。
上模和下模的设计要考虑到端盖的形状,确定冲模的凹线和凸线,以确保冲压过程中的精度和质量。
3.冲压操作冲压操作是将模具设计的零件在冲压机上进行加工的过程。
在冲压操作中,需要将材料放置在冲床上,并通过冲压动作将材料加工成端盖的形状。
操作时要注意材料的位置和冲压的速度、力度,以避免材料变形或断裂。
4.零件加工零件加工是冲压工艺的最后一步。
在冲压操作完成后,需要对端盖进行修整和整理,以达到要求的尺寸和表面质量。
同时,还需要进行表面处理,如喷涂、镀锌等,以提高端盖的耐腐蚀性能。
三、模具设计要点模具设计是冲压工艺的核心,合理的模具设计可以提高生产效率和产品质量。
以下是一些模具设计的要点:1.模具材料选择模具的材料应选择硬度高、耐磨损、耐腐蚀的材料。
常用的模具材料有合金工具钢、硬质合金等。
选择合适的材料可以延长模具的使用寿命,并提高模具的加工精度和稳定性。
2.模具结构设计模具的结构设计要简单、合理。
需要考虑到冲压力度和速度等因素,确定模具的构造强度,并确保模具的刚性和稳定性。
模具的上模和下模应配合良好,确保冲压过程中的精度和质量。
3.凸模和凹模设计凸模和凹模的设计要根据端盖的形状和尺寸要求进行。
在设计凸模和凹模时,需要考虑到材料的弹性变形和回弹等因素,以确保冲压过程中的形状和尺寸精度。
冲压模具课程设计说明书.doc

冲压模具课程设计说明书.doc冲压模具课程设计说明书导言本文档是冲压模具课程设计的详细说明书,旨在帮助学生深入理解冲压模具的设计原理、工艺流程和相关技术要求。
本文档详细介绍了冲压模具的基本概念、设计流程、材料选择、加工工艺等内容,以及课程设计的具体要求和评估标准。
第一章冲压模具概述1.1 冲压模具的定义1.2 冲压模具的分类1.2.1 单工位模具1.2.2 多工位模具1.2.3 复合模具1.3 冲压模具的基本组成部分1.3.1 上模1.3.2 下模1.3.3 引导装置1.3.4 顶针1.3.5 顶板1.4 冲压模具的工作原理1.5 冲压模具在工业生产中的应用第二章冲压模具设计流程2.1 产品设计分析2.2 模具设计准备2.2.1 工艺方案选择2.2.2 材料选择2.2.3 设计任务书编写2.3 模具零部件设计2.3.1 上模设计2.3.2 下模设计2.3.3 引导装置设计2.3.4 顶针设计2.3.5 顶板设计2.3.6 其他相关组件设计2.4 模具总体设计2.5 模具制造与加工2.6 模具调试与试产第三章冲压模具材料选择3.1 冲压模具材料性能要求3.2 常用模具材料3.2.1 工具钢3.2.2 合金工具钢3.2.3 超硬合金3.2.4 陶瓷材料3.2.5 复合材料3.3 模具材料的选择原则第四章冲压模具加工工艺4.1 冲压模具加工流程4.2 模具零部件加工4.2.1 零部件加工设备选择4.2.2 加工工艺规程确定4.2.3 加工工艺文件编制4.3 模具装配与试验4.3.1 模具装配前准备工作4.3.2 模具装配过程4.3.3 模具试验与调试4.4 模具维护与保养4.4.1 模具使用生命周期管理4.4.2 模具保养与维护方法4.4.3 模具故障排除与处理第五章课程设计要求与评估标准5.1 课程设计要求5.2 评估标准5.2.1 设计方案合理性评估5.2.2 模具设计准确性评估5.2.3 模具加工工艺评估5.2.4 模具试验与调试评估5.2.5 学生报告书评估附件1.产品设计分析报告范本2.模具零部件设计图纸范本3.模具装配图范本4.模具加工工艺文件范本5.模具试验与调试记录范本法律名词及注释1.冲压模具:指用于冲压加工的模具,用于将板材等材料加工成具有一定形状和尺寸的零件。
密封端盖模具设计说明书
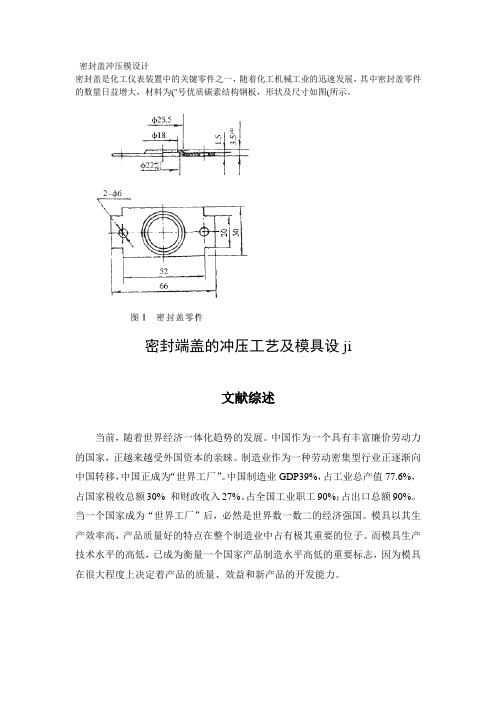
密封盖冲压模设计密封盖是化工仪表装置中的关键零件之一,随着化工机械工业的迅速发展,其中密封盖零件的数量日益增大,材料为("号优质碳素结构钢板,形状及尺寸如图(所示。
密封端盖的冲压工艺及模具设ji文献综述当前,随着世界经济一体化趋势的发展。
中国作为一个具有丰富廉价劳动力的国家,正越来越受外国资本的亲睐。
制造业作为一种劳动密集型行业正逐渐向中国转移,中国正成为“世界工厂”。
中国制造业GDP39%,占工业总产值77.6%,占国家税收总额30% 和财政收入27%。
占全国工业职工90%;占出口总额90%。
当一个国家成为“世界工厂”后,必然是世界数一数二的经济强国。
模具以其生产效率高,产品质量好的特点在整个制造业中占有极其重要的位子。
而模具生产技术水平的高低,已成为衡量一个国家产品制造水平高低的重要标志,因为模具在很大程度上决定着产品的质量、效益和新产品的开发能力。
一、我国模具的使用历史模具这项在世界上广泛运用的加工手段,正式我们祖先智慧的结晶。
是我们中华民族对世界的又一重大贡献。
我国使用模具的历史可以追述到商朝。
在商朝,青铜器的使用就已经非常的普遍。
同时青铜器的制造水平也很高,模具的使用也是非常的普遍。
于是才有了“司母戊大方鼎”和“四羊方樽”这样的青铜器精品。
到了春秋战国时期,铁器开始出现,并逐渐的取代青铜器。
模具的使用技术也更为完善。
在秦汉时期,模具技术已非常的完善了,如地动仪的产生,就缺不了模具的功劳。
以后的各个朝代,对模具的使用都非常的大。
当时中国的模具技术一直走在世界的前列。
在这段时间里,模具技术通过各种途径传到了世界各国。
并在生产中发挥了极其重要的作用。
模具技术也得到了相应的发展。
但是在近代,由于封建统治者的政策失误和连年的战争,导致了我国在模具方面的技术远远的落在了其他发达国家的后面。
所以,我们现在不得不从国外引进先进的技术来发展本国的模具技术。
二、我国模具生产的现状由于历史原因形成的封闭式、“大而全”的企业特征,我国大部分企业均设有模具车间,处于本厂的配套地位,自70年代末才有了模具工业化和生产专业化这个概念。
冲压模具结构及其设计介绍
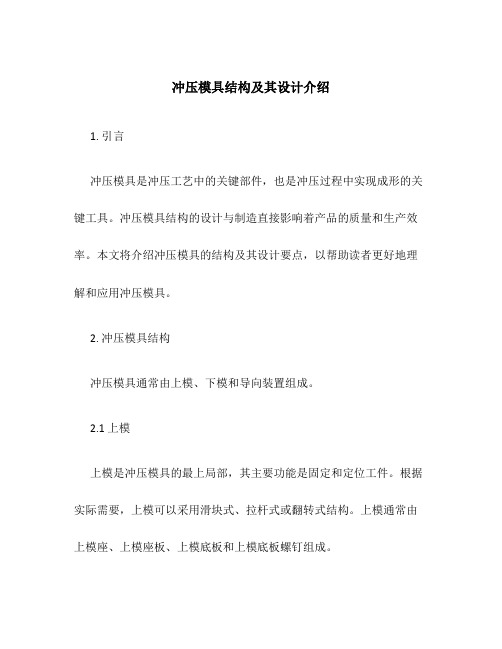
冲压模具结构及其设计介绍1. 引言冲压模具是冲压工艺中的关键部件,也是冲压过程中实现成形的关键工具。
冲压模具结构的设计与制造直接影响着产品的质量和生产效率。
本文将介绍冲压模具的结构及其设计要点,以帮助读者更好地理解和应用冲压模具。
2. 冲压模具结构冲压模具通常由上模、下模和导向装置组成。
2.1 上模上模是冲压模具的最上局部,其主要功能是固定和定位工件。
根据实际需要,上模可以采用滑块式、拉杆式或翻转式结构。
上模通常由上模座、上模座板、上模底板和上模底板螺钉组成。
2.2 下模下模是冲压模具的最下局部,其主要功能是支撑工件和提供成形空间。
下模通常由下模座、下模座板、下模底板和下模底板螺钉组成。
2.3 导向装置导向装置是冲压模具的重要组成局部,其主要功能是确保上模和下模的定位和运动精度。
导向装置可以分为直线导向和滑动导向两种形式,具体结构的选择需根据实际应用需求而定。
3. 冲压模具设计要点冲压模具设计时需要考虑以下几个要点:3.1 工件形状分析在进行冲压模具设计之前,需要对工件的形状进行分析。
通过对工件形状的分析,可以确定冲压模具的结构、材料选择、工艺布局等设计参数。
3.2 材料选择冲压模具的材料选择直接影响着模具的寿命和性能。
一般而言,冲压模具的工作部位应选择高硬度、高强度、高热稳定性的材料,如优质合金工具钢等。
3.3 充气系统设计充气系统是冲压模具设计中必不可少的一局部,其作用是通过充气将工件弹出模具。
充气系统的设计应考虑到冲压过程中的力学特性,并确保充气均匀、稳定。
3.4 固定方式设计冲压模具的固定方式设计直接影响着模具的稳定性和定位精度。
常见的固定方式有机械固定和气动固定两种,具体选择需根据模具的具体结构和工艺要求而定。
3.5 冲压力分析冲压过程中的冲压力分析是冲压模具设计的重要环节。
通过对冲压力的分析,可以确定模具的结构强度和刚度,以及选取适宜的冲压机。
4. 结论冲压模具是冲压工艺中不可或缺的工具,其结构和设计直接影响着产品质量和生产效率。
- 1、下载文档前请自行甄别文档内容的完整性,平台不提供额外的编辑、内容补充、找答案等附加服务。
- 2、"仅部分预览"的文档,不可在线预览部分如存在完整性等问题,可反馈申请退款(可完整预览的文档不适用该条件!)。
- 3、如文档侵犯您的权益,请联系客服反馈,我们会尽快为您处理(人工客服工作时间:9:00-18:30)。
端盖冲压模具设计冲压模具课程设计说明书系部:机械工程系专业:模具设计与制造班级:模具1231班实习人员:组长:谌辉祥成员:廖真、文新、罗怀刚、简鹏、胡瑞、蒋宏伟、陈建军、何银实习性质:课程设计实习时间:2014.3.3∽2014.3.14实习地点:一教509指导教师:李林鑫、梅静目录摘要前言1.工件的工艺性分析2.冲压工艺方案的确定3.模具的技术要求及材料选用4.主要设计尺寸的计算4.1毛坯尺寸的计算4.2 冲压力的计算4.3 拉深间隙的确定4.4 冲裁件的排样5.工作部分尺寸计算5.1 拉深凸凹尺寸的确定5.2 圆角半径的确定6.模具的总体设计6.1 模具的类型及定位方式的选择6.2 推件零件的设计7.主要零部件的结构设计7.1 工作零件的结构设计7.2 其他零部件的设计与选用8.模具的总装图9.模具的装配结束语致谢参考文献摘要我设计的是一个落料拉深复合冲裁模,在本次设计中我参考了大量有关冷冲模模具设计实例等方面的资料。
再结合老师布置的题(设计一个工件为盒形件的复合冲裁模),我充分运用了资料上所有设计模具中通用的表、手册等,如修边余量的确定、拉深件毛坯直径的计算公式、盒形件用压边圈拉深系数、盒形件角部的第一次拉深系数等,然后再集结了自己平时的所学,还有通过对工件的零件、模具工作部分(凸凹模、拉深凸模、落料凹模)、模具装配图的绘制,我的绘图功底也有了一定程度地提高。
本次设计的主要内容:工件的工艺性分析;冲压工艺方案的确定;模具的技术要求及材料选用;主要设计尺寸的计算;工作部分尺寸计算;模具的总体设计;主要零部件的结构设计;模具的总装图;模具的装配等。
我觉得通过本次的毕业设计,达到了这样的目的:1.综合运用本专业所学课程的理论和生产实际知识,进行一次冷冲压模具(落料拉深冲裁模)设计工作的实际训练,从而培养和提高我们独立工作的能力。
2.巩固与扩充所学有关冷冲模具设计课程的内容,掌握冷冲压模具设计的方法和步骤。
3.掌握冷冲压模具设计的基本技能,如计算、绘图、查阅设计资料和手册,熟悉标准和规范等。
关键词:冷冲压落料拉深前言冲压是使板料经分离或成形而得到制件的加工方法。
冲压利用冲压模具对板料进行加工。
常温下进行的板料冲压加工称为冷冲压。
冷冲压模具在工业生产中的地位:是大批生产同形产品的工具,同时也是工业生产的主要工艺装备。
模具工业是国民经济的基础工业。
模具可保证冲压产品的尺寸精度和质量稳定,而且在加工中不破坏产品表面。
用模具生产零件可以采用冶金厂大量生产的廉价的轧制钢板或钢带为坯料,且在生产中不需要加热,具有生产效率高、质量好、重量轻、成本低且节约能源和原材料等一系列优点,是其它加工方法所不能比拟的。
使用模具已成为当代工业生产的重要手段和工艺发展方向。
现代制造工业的发展和技术水平地提高,在很大程度上取决于模具工业的发展。
目前,工业生产中普遍采用模具成形工艺方法,以提高产品的生产效率和质量。
一般采用压力机进行零件加工,一台普通压力机每分钟可生产零件几件到几十件,而高速压力机的生产效率已达到每分钟数百件甚至上千件。
据不完全统计,飞机、汽车、拖拉机、电机、电器、仪器、仪表等产品,有60﹪左右的零件是利用模具加工出来的;而自行车、手表、洗衣机、电冰箱及电风扇等轻工业产品,90﹪左右的零件是利用模具生产出来的;至于日常生活所用的五金、餐具等的大批量生产基本上也是靠模具来进行生产的。
显而易见,模具作为一种专用的工艺装备,在生产中的作用和地位正日趋上升。
1.冲压件工艺性分析1.1材料分析零件材料为Q235,其塑性韧性较好,抗剪强度为310MPa,抗拉强度为390MPa,利于各种工序的加工。
1.2尺寸精度分析从零件图上看,其尺寸公差要求不高,故精度不高,属于回转体零件,其未注公差按IT10级处理,既能满足设计要求,又给模具制造带来了很多方便。
1.3冲压工序分析冲压工序可分为单工序冲压、复合工序冲压和连续冲压。
单工序冲压是在压力机一次行程中完成一道工序;复合工序冲压是在压力机一次行程中,在模具的同一位置同时完成两道或两道以上工序;连续冲压是把完成一个冲件的几个工序,排列成一定的顺序,组成连续模,在冲压过程中,条料在模具中依次在不同的工序位置上,分别完成冲件所要求的工序,除最初几次冲程外,以后每次冲程都可以完成一个(或几个)冲压件。
组合冲压工序比单工序冲压生产效率高,加工的精度等级高。
零件形状尺寸通过落料、拉深、整形等冲压工序获得。
该零件尺寸采用mm1的10钢板冲压而成,可保证足够的刚度和强度。
拉深件底部及口部圆角半径2R偏小,故应在拉深后另加整形工序,并用制造精度较高,间隙较小的模具来进行加工2.冲压工艺方案的确定该工件包括落料、拉深两个基本工序,可有以下三种工艺方案:方案一:先落料,后拉深。
采用单工序模生产。
方案二:落料-拉深复合冲压。
采用复合模生产。
方案三:拉深级进冲压。
采用级进模生产。
方案一模具结构简单,但需两道工序两副模具,生产效率低,难以满足该工件大批量生产的要求。
方案二只需一副模具,生产效率较高,尽管模具结构较方案一复杂,但由于零件的几何形状简单对称,模具制造并不困难。
方案三也只需一副模具,生产效率高,但模具结构比较复杂,送进操作不方便,加之工件尺寸偏大。
通过对上述三种方案的分析比较,该件若能一次拉深,则其冲压生产采用方案二为佳。
3. 模具的技术要求及材料选用利用模具生产制品零件,其模具质量的好坏,寿命的长短,直接关系到产品制造精度、性能和成本,是提高劳动生产率、降低消耗、创造效益,尽快使产品占领市场的重要性条件。
而模具的质量、使用寿命、制造精度及合格率很大程度上取决于设计时对模具材料的选用、热处理工艺要求、模具零件配合精度及公差等级的选择和表面质量要求。
一、冷冲模材料的性能冷冲模包括冲裁模、弯曲模、拉深模、成形模和冷挤压模等。
冷冲模在工作中承受冲击、拉深、压缩弯曲、疲劳磨擦等机械的作用。
模具常常发生脆断、堆塌、磨损、啃伤和软化等形成的失效。
因此,作为冷冲模主要材料的钢材,应具有以下几个方面的性能:1. 应具有较高的变形抗力:主要抗力指标包括淬火、回火抗压强度、抗弯强度等。
其中硬度是模具重要的抗力指标,高的硬度是保持模具耐磨性的必要条件。
工作零件热处理后的硬度在60HRC,强度和抗弯强度才能保证,模具才会具有较高的变形能力。
2. 应具有较高的断裂抗力:主要抗力指标有材料的抗冲击性能、抗压强度、抗弯强度、断裂抗力等。
冲击载荷下抵抗模具产生裂纹的性质也是作为防止断裂的一个重要依据,模具材料基体中碳含量越高,冲击韧性越高。
故载荷较大的冷冲镦及剪切模易受偏心弯曲载荷的细长凸模或有应力集中的模具,都需要有较高的韧性。
3. 应具有较高的耐磨性和抗疲劳性能:对于在一定条件下工作的模具钢,为了提高耐磨性,可在硬度高的材料表面上均匀涂抹大量细小硬的碳化物。
在相同硬度下提高钢的耐磨性可减小模具在交变应力条件下产生的疲劳破坏,如模具长期使用刮痕凹槽等。
4. 应具有较好的冷、热加工工艺性:钢材的加工工艺性能包括可锻性、可加工性、淬透性、淬硬性较小的脱碳敏感性和较小变形倾向等,以方便模具的加工,易于成形及防止热处理后变形等。
二、冷冲模材料的选择原则1.要选择满足模具零件工作要求的最佳综合性能的材料。
2.要针对模具失效形式选用钢材:钢材的失效是影响模具寿命的主要因素,包括:(1)为防模具开裂,要选用韧性好的材料(2)为防磨损,应选用合金元素高的材料(3)对于大型冲模应选用淬透性好的材料(4)为保持钢材硬度性能,要选用耐回火性高的含铬、钼合金钢(5)为防热处理变形,对于形杂的零件应选用含碳量高、淬透性好的高合金材料3. 要根据制品批量大小,以最低成本的选材原则选用:对于需冲压数量较多模具,一般采用优质合金钢,而数量少的则采用碳素钢,以降低成本。
4. 要根据冲模零件的作用选择:凸、凹模模具应选用优质的钢材制作,对于数量不多或厚度不大的可采用有色金属或黑色金属。
而对于支撑板、卸料零件、导向件应选用一般钢材。
5. 要根据冲模精密程度选用:在制造小型精密模具而又复杂时,可选用优质合金钢制作,而对于比较简单,形状、精度要求不高的模具应选用比较便宜的碳钢或低合金钢。
4. 主要设计尺寸的计算4.1 毛坯尺寸的确定根据毛坯尺寸的确定原则可知有两种方法来计算毛坯的计算原则:1.面积相等原则:由于拉深前和拉深后材料的体积不变,对于不变薄拉深,假设材料厚度拉深前后不变,拉深毛坯的尺寸按“拉深前后的表面积相等”来确定。
2.形状相似原则:拉深毛坯的形状一般与拉深件横截面的形状相似,即当零件的形状是圆形或椭圆形时,其拉深前毛坯的展开形状也基本上是圆形或椭圆形。
根据本零件的特点:为简单形状的旋转体,可以采用面积相等的原则来确定。
先确定修边余量△h :根据 35.04014===∆d hh ,取 2.1=∆h 按如图4.1所示。
图4.1 零件图])2[()](2[]8)2(2[])[(4222321212313d r d d d L d r r d r h r h h d D --+++++-+--∆+=π22436783708.61600)8672(4.12694-+⨯+++⨯-⨯⨯=π2640781.2156973.4282.3091+++=154.8648=)(5.90mm =4.2 冲压力的计算4.2.1落料力的计算 落料力 KLt F =落料力τtL K F P =式中,τ为材料抗剪强度,a MP ;L 为冲裁周边总长,mm ; t 为材料厚度,mm ;p K 系数是考虑到冲裁模刃口的磨损;凸模与凹模间隙的波动(数值的变化或分布不均),润滑情况、材料力学性能与厚度公差的变化等因数而设置的安全系数,一般取1.3。
当查不出材料抗剪强度τ时,可用抗拉强度b σ代替τ,此时1=p K 。
tL K F p =3001)(1⨯⨯⨯=D π ()N 11826=4.2.2拉深力的计算采用压边圈的圆筒形件b dt K F σπ=式中,--d 拉深件的直径)(mm ; --t 材料厚度 )(mm ;b σ——材料的强度极限()MPa ;--F 拉深力()N ;--K 修正因数;()N dt K F MPa K bb 415993201696.0320,6.0=⨯⨯⨯====πσπσ4.2.3压边力的计算毛坯的相对厚度:1.15.901==D t用式()m Dt-≥1045.0由表可查得无凸缘圆筒件用压边圈时的拉深因数,得50.0=m 。
确定是否使用压边圈:如果满足()m Dt-≥1045.0时,0225.05.0045.0011.0=⨯≤=Dt上式不等式不成立则在拉深模设计压边装置。
()[]p r d D F Q 212244+-=π()[]42232p r d D +-=π式中,--p 单边压边力()MPa ; --D 平板毛坯直径()mm ;--n d d ~1第1~n 次拉深直径()mm ;r 凹--拉深凸模圆角半径()mm ; 得3.2=p()[]()[]()N pr d D F 174343.216695.904222232=⨯+-=+-=ππ4.2.4冲压工艺总力的计算冲压工艺总力 Z F()N F F F F Z 154168 ==压落++4.3 拉深间隙的确定拉深间隙是指凸凹模横向尺寸的差值,双边间隙用Z 表示。