百万二次再热锅炉燃烧运行优化分析
锅炉尾部烟道二次燃烧原因、处理及预防措施

锅炉尾部烟道二次燃烧原因、处理及预防措施摘要:锅炉烟道再燃烧经常发生在燃煤锅炉中,严重影响和威胁火力发电机组安全运行,尾部烟道发生再燃烧后不仅会造成机组降负荷或者停炉,有时会造成设备损坏甚至更严重事故。
本文主要根据京能(锡林郭勒)发电有限公司一期工程锅炉尾部烟道设备设施的布置情况展开分析,提出了处理意见及预防措施,为后期锅炉安全稳定运行奠定了基础。
关键词:二次燃烧;尾部烟道;措施一、锅炉简介京能五间房一期工程2×660MW级超超临界燃煤汽轮发电机组,采用单炉膛、前后墙对冲燃烧、一次再热、平衡通风形式。
空气预热器、一次风机、送风机、引风机按照双列布置,两台炉同步安装电除尘、脱硝、脱硝装置,尾部烟道设置有空气预热器旁路凝结水换热器、给水换热器,空气预热器出口安装凝结水换热器及热媒水换热器,锅炉四管、尾部烟道各换热器、脱硝装置及空气预热器同时配置安装一定数量吹灰器。
本期工程燃用煤种为锡林郭勒盟五间房矿区西一矿褐煤,采用微油+少油点火技术,锅炉在燃用设计煤种,最低稳燃负荷不大于30%BMCR。
二、锅炉尾部烟道发生二次燃烧的原因锅炉尾部烟道发生二次燃烧主要是因为沉积在尾部烟道或受热面上的可燃物和未燃尽物达到着火条件后的复燃现象。
其中造成尾部烟道内可燃物的沉积的原因只要如下:1.煤质及运行工况发生变化燃料品质变化偏离设计煤种或锅炉运行工况发生变化时,运行人员燃烧调整不及时或调整不当。
风量过小、煤粉过粗、油枪雾化不良,使未燃尽的炭粒或油滴等未燃尽的可燃物随烟气进入后面烟道并与脱硝催化剂、烟气余热利用换热器、空气预热器蓄热片接触沉积在尾部烟道内或受热面上。
2.点火初期,炉膛温度和烟气流速低,导致尾部烟道可燃物沉积锅炉低负荷运行,点火初期或停炉过程中,由于炉膛热负荷低,分布不均,温度较低区域燃料着火困难,燃烧时间长,使部分燃料在炉膛内无法完全燃尽,极有可能被烟气带至烟道内。
由于当时烟气流速很低,从而发生可燃物的沉积。
锅炉燃烧优化调整方案
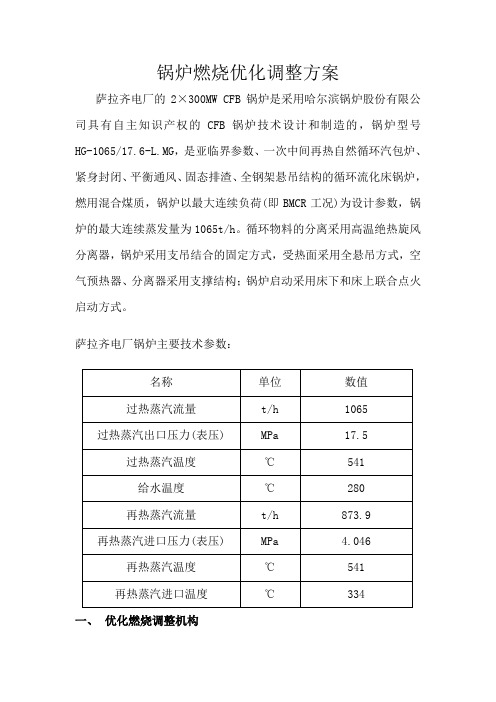
锅炉燃烧优化调整方案萨拉齐电厂的2×300MW CFB锅炉是采用哈尔滨锅炉股份有限公司具有自主知识产权的CFB锅炉技术设计和制造的,锅炉型号HG-1065/17.6-L.MG,是亚临界参数、一次中间再热自然循环汽包炉、紧身封闭、平衡通风、固态排渣、全钢架悬吊结构的循环流化床锅炉,燃用混合煤质,锅炉以最大连续负荷(即BMCR工况)为设计参数,锅炉的最大连续蒸发量为1065t/h。
循环物料的分离采用高温绝热旋风分离器,锅炉采用支吊结合的固定方式,受热面采用全悬吊方式,空气预热器、分离器采用支撑结构;锅炉启动采用床下和床上联合点火启动方式。
萨拉齐电厂锅炉主要技术参数:一、优化燃烧调整机构为了积极响应公司号召,使我厂锅炉燃烧优化调整工作有序进行,做到调整后锅炉更加安全、经济运行,我厂成立了锅炉优化燃烧调整小组:1、组织机构:组长: 杨彦卿副组长:冀树芳、贺建平成员:刘玉俊、蔚志刚、李京荣、范海水、谷威、孔凡林、薛文祥、于斌2、工作职责:1)负责制定锅炉优化燃烧调整的工作计划;2)负责编制锅炉优化燃烧调整方案及锅炉运行中问题的检查汇总;3)负责组织实施锅炉优化燃烧调整工作,保证锅炉长周期连续稳定运行。
二、优化燃烧调整工作内容:1、入炉煤粒度调整:1)CFB锅炉对入炉煤粒径分布要求很高,合理的粒径分布是影响锅炉燃烧安全稳定和经济的最重要因素之一,入炉煤粒径对锅炉的影响有以下几点:a)入炉煤细粒径比例较少,粗颗粒比例多,阻力相应增加锅炉流化所需一次风量增大,细颗粒逃逸出炉内的几率增高,锅炉飞灰含碳量上升;b)入炉煤细颗粒比例多,粗颗粒比例少,在相同的一次风量下锅炉床层上移,床温升高,锅炉排烟温度也相应提高;c)入炉煤粒径过粗还会影响到锅炉的正常流化和排渣,粒径过粗容易使排渣不畅导致流化不良甚至结焦,为此我厂应严格控制入炉煤粒度;每星期对入炉煤粒度进行分析两次,并根据入炉煤粒度分析及时检查高幅筛筛条或调整碎煤机间隙。
百万等级锅炉调试过程中典型问题分析及措施

Typical Problems in Megawatt Boiler Debugging and Their Countermeasures
SUN Lei,YE Qi-xian
(Shanghai Power Construction Test Institute,Shanghai 200031,China)
(7)加强 炉 膛 管 壁 壁 温 的 检 测 和 监 督。 对 四 面的高温部位选 点 进 行 制 度 性 的 硬 度、现 场 金 相 检查集 中 位 置 进 行 普 查 ,对 存 在 焊 接 表 面 缺 陷 的 ,进 行 打 磨 处 理 ,圆 滑 过 渡 。 1.2 调 试 方 面
百万二次再热机组冷态启动过程优化

百万二次再热机组冷态启动过程优化摘要:根据我厂1000MW机组的特点以及公司关于机组优化启动的指导意见,以“安全第一、预防为主”为基础,以经济效益为中心,把经济运行放到重要位置, 合理利用资源,努力降低消耗,真正树立“成本意识”和“节约意识”。
降低机组启动能耗特此编制了我厂1000MW机组的优化启动方案,以达到启动过程中缩短启动时间尽早带负荷提高经济效益的目的。
关键词:冷态启动运行方式优化一.研究对象主设备汽轮机汽轮机为上海汽轮机有限公司生产的型号为N1000-31/600/620/620的超超临界、二次中间再热、单轴、六缸六排汽、十一级回热抽汽、单背压、反动凝汽式汽轮机。
汽轮机整体由六个汽缸组成,即一个单流超高压缸、一个双流高压缸、一个双流中压缸和3个双流低压缸串联布置。
汽轮机转子在每两个缸之间都由单轴承支撑,整个轴系共有7个轴承。
转子通过刚性联轴器将六个转子连为一体,汽轮机低压转子C通过刚性联轴器与发电机转子相连,汽轮机整个轴系总长度约为44.6m。
汽轮机的通流部分由超高压、高压、中压和低压部分组成,共设105级,均为反动级。
超高压部分为15级,高压部分为2×12级,中压部分为2×15级,低压部分为3×2×6级。
DEH控制系统提供超高/高/中压缸联合启动、高/中压缸联合启动两种启动方式。
锅炉我公司2×1000MW超超临界锅炉为上海锅炉股份有限公司制造的SG-2778/32.45-M7053型超超临界参数直流锅炉,锅炉形式为单炉膛、二次中间再热、四角切圆燃烧方式、平衡通风、固态排渣、全钢构架悬吊结构塔式炉燃煤锅炉。
锅炉运转层以下紧身封闭、运转层以上露天布置。
锅炉设计煤种为神府东胜烟煤,以晋北烟煤作为校核煤种;实现无油启动,采用等离子系统点火及稳燃。
灰渣采用分除方式,飞灰采用气力干除灰,除渣方式为干式除渣;烟气脱硫采用石灰石—石膏湿法脱硫工艺;烟气脱硝采取选择性催化还原(SCR)法去除烟气中NOx,还原剂采用尿素。
二次再热对热工的影响
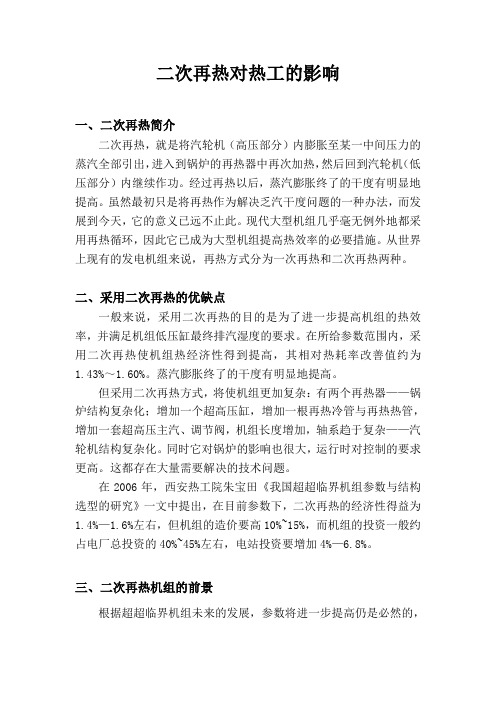
二次再热对热工的影响一、二次再热简介二次再热,就是将汽轮机(高压部分)内膨胀至某一中间压力的蒸汽全部引出,进入到锅炉的再热器中再次加热,然后回到汽轮机(低压部分)内继续作功。
经过再热以后,蒸汽膨胀终了的干度有明显地提高。
虽然最初只是将再热作为解决乏汽干度问题的一种办法,而发展到今天,它的意义已远不止此。
现代大型机组几乎毫无例外地都采用再热循环,因此它已成为大型机组提高热效率的必要措施。
从世界上现有的发电机组来说,再热方式分为一次再热和二次再热两种。
二、采用二次再热的优缺点一般来说,采用二次再热的目的是为了进一步提高机组的热效率,并满足机组低压缸最终排汽湿度的要求。
在所给参数范围内,采用二次再热使机组热经济性得到提高,其相对热耗率改善值约为1.43%~1.60%。
蒸汽膨胀终了的干度有明显地提高。
但采用二次再热方式,将使机组更加复杂:有两个再热器——锅炉结构复杂化;增加一个超高压缸,增加一根再热冷管与再热热管,增加一套超高压主汽、调节阀,机组长度增加,轴系趋于复杂——汽轮机结构复杂化。
同时它对锅炉的影响也很大,运行时对控制的要求更高。
这都存在大量需要解决的技术问题。
在2006年,西安热工院朱宝田《我国超超临界机组参数与结构选型的研究》一文中提出,在目前参数下,二次再热的经济性得益为1.4%—1.6%左右,但机组的造价要高10%~15%,而机组的投资一般约占电厂总投资的40%~45%左右,电站投资要增加4%—6.8%。
三、二次再热机组的前景根据超超临界机组未来的发展,参数将进一步提高仍是必然的,当温度达到 650~720℃、压力超过30MPa、采用二次再热,届时电站的效率将进一步提高,可以获得与IGCC和PFBC 发电技术相媲美的优良经济性。
按照 ABB,SIEMENS,GECALSTOM为主的欧洲汽轮机制造业提出的“高参数燃煤电站(700℃)发展计划,即到2015年左右,超超临界机组的参数达到40mpa/700℃/720℃的水平,即是为此阶段的超超临界机组提出的。
1000MW二次再热机组再热汽温调整与优化-4页文档资料

1000MW二次再热机组再热汽温调整与优化一、运行情况概述该厂2×1000MW二次再热锅炉型式为2710t/h超超临界参数变压运行螺旋管圈直流炉,单炉膛塔式布置、四角切向燃烧、平衡通风。
设计煤种为神华煤。
过热蒸汽/一次/二次再热蒸汽额定温度605/613/613℃ 根据设计在65%~100BMCR负荷段,一次、二次再热蒸汽温度应能达到在额定值。
然而该厂二期两台机组投产初期,均存在再热汽温偏离设计值较多问题,月度均值只有587℃左右,机组效率大幅受限。
由于1000MW 等级的二次再热机组尚属首例,无成功调整经验借鉴,因此该厂从机组特性上深入研究,在磨组组合、吹灰、二次风门调整及煤种掺烧配烧中探索出一条二次再热1000MW超超临界机组再热汽温控制手段。
二、运行调整与优化1.吹灰方式调整从二次再热锅炉受热面布置可以看出,低温过热器受热面处于燃烧器出口,即处炉膛温度最高区域。
由于低温过热器受热面的辐射特性,较干净的低过受热面势必造成低过吸热过多,从而导致锅炉再热汽温低于设计值。
运行数据显示,低温过热器温升及烟气温降均大于设计值,说明低温过热器受热面吸热占较大。
针对此现象通过减少一次再热高再热段以下区域重点减少低过受热面区域吹灰频率和吹灰器数目,达到增加再热器的吸热,提高再热汽温的目的。
2.磨组运行方式优化通过磨煤机的组合方式来调节再热汽温与改变燃烧器的摆角的原理一样,都是改变燃烧中心来调整再热汽温。
选取下列磨组运行方式。
高负荷ABDEF、ABCDF运行时,一、二次再热器汽温距额定值甚远,主要原因是主燃区分为两段,降低了炉膛火焰的集中度,使锅炉燃烧剧烈程度降低。
如表1所示,在磨煤机组合中,ACDEF组合运行时的一、二再热蒸汽温度最高。
一是由于该种运行方式拉长了主燃烧区域的高度,炭粒子在炉膛的停留时间延长所致。
在600MW~800MW,重点比较BCDE/CDEF两种磨组运行方式。
采用上4台磨组运行时,由于主燃烧区域的上移,即火焰中心的上抬,再热汽温有着明显升高。
锅炉燃烧优化调整技术

2)掺冷风量对排烟温度影响
②运行控制磨煤机出口温度偏低 按照《电站磨煤机及制粉系统选型导则》(DL/T 466-
2004)规定的磨煤机出口温度,见表1。 锅炉设计时热风温度的选择主要取决于燃烧的需要; 所选定的热风温度往往高于所要求的磨煤机入口的干
燥剂温度,因此要求在磨煤机入口前掺入一部分温度 较低的介质; 运行中磨煤机出口温度控制的越低,则冷一次风占的 比例越大,即流过空预器的风量流量降低,这样引起 排烟温度升高。
➢ 排烟热损失主要取决于排烟温度与排烟氧量 (过剩空气系数)
➢ 排烟热损失是锅炉各项热损失中最大的 (5%~7%);
➢ 排烟温度每升高10℃.排烟损失约增加0.5%~ 0.7%);机组发电煤耗升高约1.7 ~2.2 g/kWh。
➢ 过高的排烟温度,对锅炉后电除尘及脱硫设备 的安全运行也构成威胁。
烟气余热利于系统图
~180
贫煤 130 烟煤、褐煤 70
褐煤 90 烟煤 120
烟煤 70~75 褐煤 70 Vdaf≤15%的煤 100
当Vdaf<40%时,tM2=[(82-Vdaf)×5/3±5] 当Vdaf≥40%时,tM2<70
高热值烟煤<82,低热质烟煤<77,次烟煤、褐煤 <66
备注:燃用混煤的,可允许tM2较低的相应煤种取值;无烟煤只受设备允许 温度的限制
W火焰燃烧方式
➢ 无烟煤这种反应特性极低的煤种 (可燃基挥发分低于10%),
➢ 采用“W”火焰的燃烧方式,通过 提高炉膛的热负荷,延长火焰行程 等手段来获得满意的燃烧效果。
左侧墙
右侧墙
燃尽风口
燃烧器
➢ ➢
前后墙对冲燃烧方式 ➢
沿炉膛宽度方向热负荷分布均匀 过热器、再热器区炉宽方向的烟温 分布更加均匀 燃烧器具有自稳燃能力
锅炉燃烧调整与各项指标的控制措施
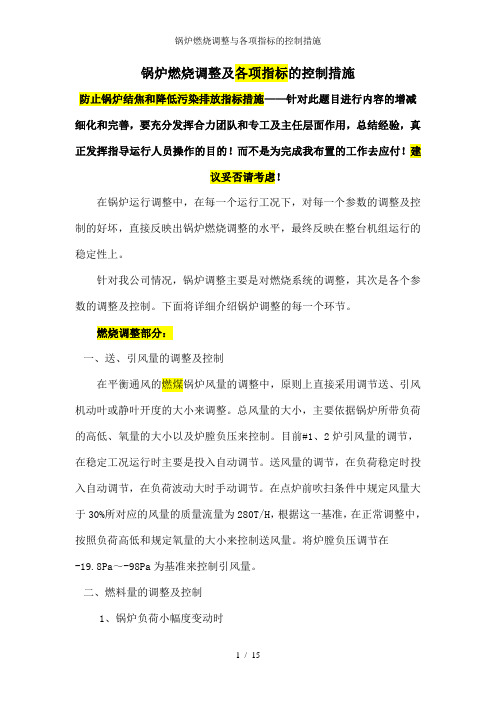
锅炉燃烧调整及各项指标的控制措施防止锅炉结焦和降低污染排放指标措施——针对此题目进行内容的增减细化和完善,要充分发挥合力团队和专工及主任层面作用,总结经验,真正发挥指导运行人员操作的目的!而不是为完成我布置的工作去应付!建议妥否请考虑!在锅炉运行调整中,在每一个运行工况下,对每一个参数的调整及控制的好坏,直接反映出锅炉燃烧调整的水平,最终反映在整台机组运行的稳定性上。
针对我公司情况,锅炉调整主要是对燃烧系统的调整,其次是各个参数的调整及控制。
下面将详细介绍锅炉调整的每一个环节。
燃烧调整部分:一、送、引风量的调整及控制在平衡通风的燃煤锅炉风量的调整中,原则上直接采用调节送、引风机动叶或静叶开度的大小来调整。
总风量的大小,主要依据锅炉所带负荷的高低、氧量的大小以及炉膛负压来控制。
目前#1、2炉引风量的调节,在稳定工况运行时主要是投入自动调节。
送风量的调节,在负荷稳定时投入自动调节,在负荷波动大时手动调节。
在点炉前吹扫条件中规定风量大于30%所对应的风量的质量流量为280T/H,根据这一基准,在正常调整中,按照负荷高低和规定氧量的大小来控制送风量。
将炉膛负压调节在-19.8Pa~-98Pa为基准来控制引风量。
二、燃料量的调整及控制1、锅炉负荷小幅度变动时调节原则:通过调节运行着的制粉系统的出力来进行。
调节过程(以少量加负荷为例)1)在给煤量不变的情况下,首先将A磨煤机的调整做为燃烧稳定的基础,然后通过适当开B、C磨煤机容量风门开度来调整负荷,调整时不要大幅度开容量风门,根据负荷情况,可单侧或双侧调整,调整幅度控制在2%开度左右,调整后,密切注意汽包压力或主汽压力以及氧量的变化趋势,如果压力上升快,可适当对单侧容量风门回调来进行控制。
2)在各台磨煤机容量风门开至40-45%时,此时应根据磨煤机料位及电流情况,来增加给煤量,根据长时间观察,每台磨煤机给煤量最稳定工况出力在54-56T/H之间,在掺烧劣质煤(如金生小窑煤)时,出力在48-50T/H之间。
- 1、下载文档前请自行甄别文档内容的完整性,平台不提供额外的编辑、内容补充、找答案等附加服务。
- 2、"仅部分预览"的文档,不可在线预览部分如存在完整性等问题,可反馈申请退款(可完整预览的文档不适用该条件!)。
- 3、如文档侵犯您的权益,请联系客服反馈,我们会尽快为您处理(人工客服工作时间:9:00-18:30)。
百万二次再热锅炉燃烧运行优化分析摘要:介绍了百万二次再热超超临界锅炉磨煤机和燃烧器的特点。
通过制粉系统优化调整试验,得到动态煤粉分离器转速、磨煤机通风量、风门挡板特性和磨煤机出力特性;通过调整锅炉氧量、SOFA风门开度及水平摆角、磨煤机组合、再循环风量等运行参数,有效调整锅炉汽温偏差,优化了锅炉燃烧系统的运行参数。
关键词:作者简介:雷州电厂1000MW机组锅炉型号为HG-2764/33.5/605/623/623-YM2,该锅炉为二次中间再热、超超临界压力变压运行带内置式再循环泵启动系统的直流锅炉、单炉膛双切圆的π型锅炉。
锅炉设计参数见表1。
表1 锅炉设计参数项目单位数值主蒸汽流量t·h-12683.8主蒸汽出口压力MPa32.60主蒸汽出口温度℃605给水温度℃328给水压力MPa36.51高压再热蒸汽流量t·h-12378.5高压再热蒸汽出口压力MPa10.502高压再热蒸汽出口温度℃623低压再热蒸汽流量t/h2036.2低压再热蒸汽出口压力MPa 3.208低压再热蒸汽出口温度℃6231 锅炉燃烧系统设备概况1.1 燃烧器布置炉膛为长方形结构,前后墙各布置四角燃烧器。
八角燃烧器均为摆动式燃烧器,在炉膛内部形成反向双切圆,在炉膛的左、右半部分中心分别形成顺时针旋向和逆时针旋向的两个直径稍有不同的假想切园,见图1。
其中主燃烧器分为两组,根据各风室的高度布置喷嘴,油风室中间布置有带稳燃叶轮的喷嘴。
图1 燃烧器平面布置1.2 燃烧器结构燃烧器采用MPM低氮燃烧技术。
出口中心浓外围淡的气流能有效防止煤粉气流的离析、贴壁,保护燃烧器区域水冷壁的安全使用。
一次风喷口出口气流设计为中心浓淡,在一次风喷口出口处加装十字花形扩散器,浓淡燃烧除可降低NO x,同时对煤粉稳燃、提前着火有积极作用。
二次风喷嘴可作上下各摆动30°,一次风喷嘴可作上下各摆动20°,以此来改变燃烧中心区的位置,调节炉膛内各辐射受热面的吸热量,从而调节再热汽温,燃烧器煤粉喷嘴结构见图2。
图2 煤粉喷嘴及其摆动机构锅炉最大连续负荷(BMCR)工况时燃烧器的主要设计参数见表1。
作者简介:表2 燃烧器的主要设计参数项目单位数值一次风率%23.2一次风温℃68二次风率%71.8二次风温℃330一次风喷嘴间距mm14334.51.3 受热面布置锅炉过热器系统为三级布置,分别为分隔屏、后屏、末过,均布置在炉膛上部,采用煤水比调节;再热器系统采用烟气再循环、尾部烟气挡板和燃烧器摆动的组合式调温方式,锅炉受热面布置见图3。
图3 锅炉受热面布置示意图2 冷态试验与制粉系统运行优化2.1 冷态一次风调平对6台磨分别开展冷态一次风速调平,各粉管风速见表3。
调平后的各层燃烧器粉管风速均满足偏差小于5%的要求。
表3 一次风调平数据磨煤机编单位A B C D E F号调平前最大风速m/s28.527.128.227.225.330.6最小风速m/s23.824.72524.821.826.5最大偏差%10.18.56.75.29.612.5调平后最大风速m/s27.426.827.427.224.230.1最小风速m/s25.324.926.225.322.428.8最大偏差%4.23.74.53.63.94.12.2 磨煤机入口风道改造及风门挡板特性试验磨煤机入口风道冷、热风混合距离极短,流场分布整体偏移较大,局部产生紊流或涡流现象,导致磨入口风量测量存在较大偏差,部分磨煤机冷热风门无法正常投入自动运行,并且风量显示与风门挡板调节出现“倒挂”现象。
运行人员无法有效监控磨煤机风量及一次风粉管风速,实际运行过程中一次风速可能过大,造成粉管磨损及飞灰含碳量偏大。
对磨煤机入口风道进行如下改造:增加冷风扩口及冷风风箱,将冷风气流分隔为多股,加强冷风的均布性以及与热风的混合;在风道90°转角处布置导流板,增加导向作用;在风量测量元件上游布置均流板,对气流起到均布作用,改造后的风道示意图见图4。
风道改造后开展入口风量标定测试,风量及风门卡杜变化见图5。
风量在线测量数据准确,风量与风门开度跟踪性好,无风量“倒挂”现象。
图4 磨煤机入口风道改造示意图图5 改造后磨煤机风门挡板特性曲线2.3 制粉系统运行优化(1)动态分离器调节性能试验控制磨煤机出力在65t/h、85t/h工况下,磨煤机进口一次风量按设计风煤比曲线自动控制,分别调整动态分离器转速为450r/min、480r/min及510r/min进行试验。
煤粉细度R90与分离器转速的关系见图6,煤粉细度R90随分离器转速升高明显降低,在低转速时转速对细度影响较大;在高转速时转速对细度影响降低。
图6 不同分离器转速下煤粉细度变化(2)磨煤机出力特性试验分离器变频器转速控制在470 r/min,磨煤机出力在90.6~110.5t/h进行4个工况的试验。
煤粉细度R90与出力呈直线变化关系,R90随出力增加而升高,但与其他配静态分离器的磨煤机相比较,煤粉细度受出力的影响相对较小;磨煤机电流与出力基本呈直线关系,出力增加约20t/h,电流增加9.9A;进出口差压也随出力增加而升高。
图7 不同出力下磨煤机参数3.燃烧优化调整3.1 运行氧量优化试验在1000MW工况下,针对不同运行氧量开展优化试验,分别在炉膛出口氧量2.5%、2.7%、2.9%、3.1%工况下进行测试,各参数变化情况见图8。
运行氧量从2.5%提高到3.1%,排烟温度变化较小,飞灰含碳量降低。
但由于烟气量的增加,排烟损失q2将明显升高;飞灰含碳量随着氧量的提高有所降低,但是机械不完全燃烧损失q4与排烟热损失相比要小得多;烟气中CO浓度下降,在氧量2.5%工况下部分位置CO浓度最大值达600μL/L;氧量提高时,引风机电流上升明显。
图8 不同运行氧量下锅炉性能参数3.2 燃尽风门开度试验在1000MW负荷下,磨煤机组合为BCDEF,分别对SOFA风开度为30%、50%、70%开展试验,NO x浓度随SOFA风门开度增加而升高。
图9 不同SOFA风门开度下NO浓度x3.3 磨煤机组合试验在1000MW负荷下,进行三种磨煤机组合试验ABCDE、ABCDEF、BCDEF,不同磨煤机组合运行方式下锅炉性能参数见图10。
试验结果表明,当下5层磨煤机运行时,飞灰可燃物含量偏低,NO x排放浓度较高;上5层磨煤机运行时,飞灰可燃物含量偏高,NO x排放浓度降低。
图10 不同磨煤机组合运行方式锅炉性能参数3.4 再循环风量调整试验对再循环风机风量进行优化试验,即通过调整再循环风机运行数量与风机运行转速改变再循环风量,图11是应用理论热力计算的方法研究烟气再循环率对主蒸汽温度、再热蒸汽温度的影响。
计算结果显示,随着烟气再循环率的升高,炉膛理论燃烧温度下降、屏底温度变化较小;辐射受热面吸热量下降,对流受热面吸热量增加;分离器出口及主汽温度降低,高压、低压再热蒸汽温度提高。
图11 烟气再循环率对蒸汽温度的影响在1000MW负荷,磨煤机组合BCDEF工况下,保持高压再热烟气侧挡板开度10%、低压再热烟气侧挡板开度100%不变,对四台运行再循环风机开展转速调整试验,记录调整过程中再热汽温变化情况。
结果表明,再循环风量对再热汽温调节作用明显,再循环风机转速从450r/min提高至750r/min,高压、低压再热汽温显著升高。
图12 不同再循环风机出力下再热汽变化3.5 汽温偏差调整为减弱炉膛内气流的残余旋转,减少炉膛出口两侧烟温偏差,SOFA燃烧器喷口设计有水平摆动功能,各燃烧器喷口可做±10°水平摆动。
在SOFA燃烧器与煤粉燃烧器水平摆角一致时,从水冷壁顶棚集箱到汽水分离器出口均存在B侧高于A侧约10~15℃的汽温偏差。
在完成各磨煤机粉管一次风调平、消除粉管风速对汽温偏差的影响后,分别调节SOFA燃烧器水平摆角至-5°及-10°反切位置(摆角0°代表与煤粉燃烧器摆角相同),不同角度及汽温情况见下表。
通过调整SOFA燃烧器水平摆角,汽温偏差减小明显,水冷壁顶棚集箱入口汽温偏差从17.4℃减小至2.4℃,分离器出口汽温偏差从10.4℃减小至1.7℃。
表4 不同SOFA燃烧器水平摆角下汽温变化SOFA燃烧器水平摆角测点位置水冷壁顶棚集箱入口汽温(℃)后烟道集箱入口汽温(℃)分离器入口汽温(℃)分离器出口汽温(℃)0°A442.8454.8453.6451.8 B460.2471.1468.2462.2-5°A445.3458.1457.8457.7 B452.6466.2464.5463.8-10°A447.1461.7459.7457.6 B444.7463.4461.6459.34 结论(1)磨煤机动态分离器转速对煤粉细度调节作用明显,当锅炉燃用煤种或出力变化时,应及时调整分离器转速;随着转速升高,分离器转速变化对煤粉细度影响降低。
(2)磨煤机入口风道改造后磨煤机入口在线风量测量准确,风量与风门挡板开度跟踪性好。
(3)运行氧量提高时,排烟温度变化较小,飞灰含碳量降低,引风机电流上升明显。
(4)NO x浓度随SOFA风门开度增加而升高;下5层磨煤机运行与上五层对比,飞灰可燃物热含量降低,NO x排放浓度升高。
(5)随着烟气再循环率的升高,高压、低压再热蒸汽温度提高,再循环风机对再热汽温调节作用明显。
(6)SOFA燃烧器水平摆角调整至反切位置,能够有效减小水冷壁至分离器汽温偏差。
参考文献[1]马新立. 2980t/h超超临界锅炉燃烧系统优化运行分析[J]. 发电设备, 2009(03):181-187.[2]高继录, 邹天舒, 冷杰,等. 1000MW超超临界锅炉燃烧调整的试验研究[J]. 动力工程学报, 2012(10):6-11.[3]邹磊, 梁绍华, 岳峻峰,等. 1000MW超超临界塔式锅炉NOx排放特性试验研究[J]. 动力工程学报, 2014, 034(003):.169-175,195.[4]刘建全, 孙保民, 张广才,等. 1000MW超超临界旋流燃烧锅炉稳燃特性数值模拟与优化[J]. 中国电机工程学报, 2012.[5]胡志宏, 杨兴森, 王军,等. 1000MW超超临界锅炉燃烧优化调整[J]. 锅炉技术, 2008, 39(4):42-46.[6]高小涛, 盛昌栋. 1000MW机组锅炉掺烧贫煤NO x排放的燃烧优化[J]. 电力工程技术, 2018, 037(003):14-20.。