梯度功能复合材料,,
【复合材料概论】复习重点应试宝典

【复合材料概论】复习重点应试宝典第⼀章总论1、名词:复合材料基体增强体结构复合材料功能复合材料复合材料(Composite materials),是由两种或两种以上不同性质的材料,通过物理或化学的⽅法,在宏观上组成具有新性能的材料。
包围增强相并且相对较软和韧的贯连材料,称为基体相。
细丝(连续的或短切的)、薄⽚或颗粒状,具有较⾼的强度、模量、硬度和脆性,在复合材料承受外加载荷时是主要承载相,称为增强相或增强体。
它们在复合材料中呈分散形式,被基体相隔离包围,因此也称作分散相。
结构复合材料:⽤于制造受⼒构件的复合材料。
功能复合材料:具有各种特殊性能(如阻尼,导电,导磁,换能,摩擦,屏蔽等)的复合材料。
2、在材料发展过程中,作为⼀名材料⼯作者的主要任务是什么?(1)发现新的物质,测试其结构和性能;(2)由已知的物质,通过新的制备⼯艺,改变其显微结构,改善材料的性能;(3)由已知的物质进⾏复合,制备出具有优良性能的复合材料。
3、简述现代复合材料发展的四个阶段。
第⼀代:1940-1960 玻璃纤维增强塑料第⼆代:1960-1980 先进复合材料的发展时期第三代:1980-2000 纤维增强⾦属基复合材料第四代:2000年⾄今多功能复合材料(功能梯度复合材料、智能复合材料)4、简述复合材料的命名和分类⽅法。
增强材料+(/)基体+复合材料按增强材料形态分:连续纤维复合材料,短纤维复合材料,粒状填料复合材料,编织复合材料;按增强纤维种类分类:玻璃纤维复合材料,碳纤维复合材料,有机纤维复合材料,⾦属纤维复合材料,陶瓷纤维复合材料,混杂复合材料(复合材料的“复合材料”);按基体材料分类:聚合物基复合材料,⾦属基复合材料,⽆机⾮⾦属基复合材料;按材料作⽤分类:结构复合材料,功能复合材料。
5、简述复合材料的共同性能特点。
(1)、综合发挥各组成材料的优点,⼀种材料具有多种性能;(2)、复合材料性能的可设计性;(3)、制成任意形状产品,避免多次加⼯⼯序。
梯度功能材料的制备与应用及其发展状况(功能材料论文)
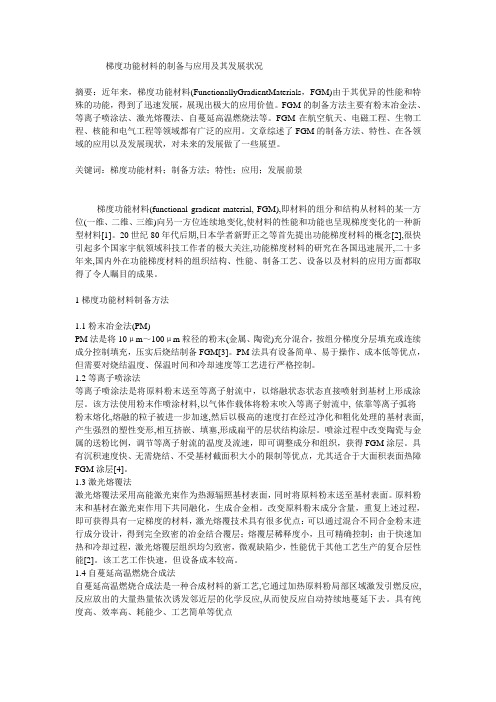
梯度功能材料的制备与应用及其发展状况摘要:近年来,梯度功能材料(FunctionallyGradientMaterials,FGM)由于其优异的性能和特殊的功能,得到了迅速发展,展现出极大的应用价值。
FGM的制备方法主要有粉末冶金法、等离子喷涂法、激光熔覆法、自蔓延高温燃烧法等。
FGM在航空航天、电磁工程、生物工程、核能和电气工程等领域都有广泛的应用。
文章综述了FGM的制备方法、特性、在各领域的应用以及发展现状,对未来的发展做了一些展望。
关键词:梯度功能材料;制备方法;特性;应用;发展前景梯度功能材料(functional gradient material, FGM),即材料的组分和结构从材料的某一方位(一维、二维、三维)向另一方位连续地变化,使材料的性能和功能也呈现梯度变化的一种新型材料[1]。
20世纪80年代后期,日本学者新野正之等首先提出功能梯度材料的概念[2],很快引起多个国家宇航领域科技工作者的极大关注,功能梯度材料的研究在各国迅速展开,二十多年来,国内外在功能梯度材料的组织结构、性能、制备工艺、设备以及材料的应用方面都取得了令人瞩目的成果。
1梯度功能材料制备方法1.1粉末冶金法(PM)PM法是将10μm~100μm粒径的粉末(金属、陶瓷)充分混合,按组分梯度分层填充或连续成分控制填充,压实后烧结制备FGM[3]。
PM法具有设备简单、易于操作、成本低等优点,但需要对烧结温度、保温时间和冷却速度等工艺进行严格控制。
1.2等离子喷涂法等离子喷涂法是将原料粉末送至等离子射流中,以熔融状态状态直接喷射到基材上形成涂层。
该方法使用粉末作喷涂材料,以气体作载体将粉末吹入等离子射流中, 依靠等离子弧将粉末熔化,熔融的粒子被进一步加速,然后以极高的速度打在经过净化和粗化处理的基材表面,产生强烈的塑性变形,相互挤嵌、填塞,形成扁平的层状结构涂层。
喷涂过程中改变陶瓷与金属的送粉比例,调节等离子射流的温度及流速,即可调整成分和组织,获得FGM涂层。
11.【复合材料】复合材料新技术(2)

楔形块状聚合物制备法
根据活性聚合物体系中两种单体的混合比,构 造分子内结构,使某分子链内具有从某一聚合 物组分向另一聚合物组分变化的部分,这种聚 合物称之为楔形块状共聚物。这种共聚物可 以采用原子自由基共聚(ATRP) 等方法来制备。
张彬等用原子自由基共聚法,在水分散体系中合成了 苯乙烯(St) 和甲基丙烯酸甲酯(MMA) 的梯度共聚物; 华东理工大学的王涛也通过原子转移自由基聚合以 及连续补加第二单体的方法制备了St 和MMA 的梯 度共聚物。 Gray 等通过硝基氧媒介控制自由基聚合反应 (nitroxide2mediated controlled radical polymerization) 方法制备了高分子量苯乙烯(S)P42 乙酸基苯乙烯(AS) 以及苯乙烯(S)P42羟基苯乙烯 (HS) 梯度共聚物。
FGM的研究内容
材料设计 材料制备 材料特性评价 三个部分,三者相辅相成
FGM的设计
首先根据材料的实际使用要求,进行材料内 部组成和结构的梯度分布设计。在设计时, 以知识库为基础选择可供合成的材料组成和 制备技术,然后选择表示梯度变化的分布函 数,并以材料基本物性数据库为依据进行功 能(温度、热应力等)的解析计算,最后将 最优设计方案提交材料合成部门。
制备方法举例
日本大阪市立工业研究所热塑性树脂第二研究室应用此法,已 成功开发出聚氯乙烯-聚甲基丙烯酸甲酯(PVC-PMMA) 等聚 合物功能梯度材料(膜材) 。 上利研究组发现此法还可能制造不相容性聚合物功能梯度材 料,如聚碳酸酯-聚苯乙烯混合物。 钱浩、林志勇通过聚合物共混,也得到了表面浓度呈梯度变化 的不相容型PP-EVA 梯度功能高分子材料。
图4 就是用该方法 制备的PP-talc 梯度 材料样品的数码照 片,其talc 含量由内 向外逐渐递增。
功能梯度材料的概述
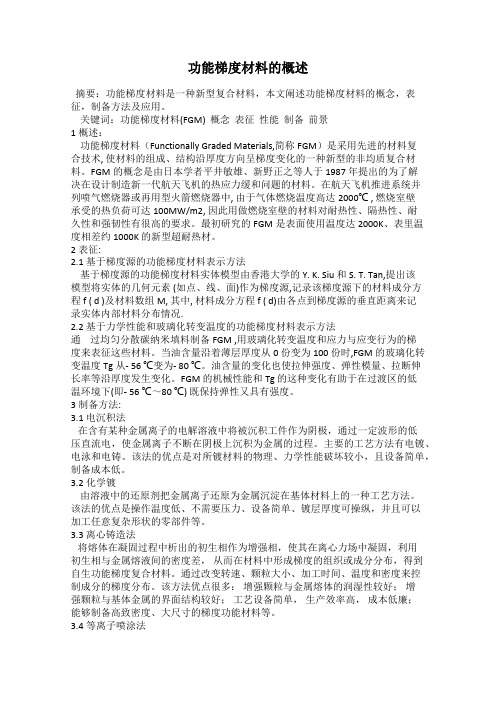
功能梯度材料的概述摘要:功能梯度材料是一种新型复合材料,本文阐述功能梯度材料的概念,表征,制备方法及应用。
关键词:功能梯度材料(FGM) 概念表征性能制备前景1 概述:功能梯度材料(Functionally Graded Materials,简称FGM)是采用先进的材料复合技术, 使材料的组成、结构沿厚度方向呈梯度变化的一种新型的非均质复合材料。
FGM的概念是由日本学者平井敏雄、新野正之等人于1987 年提出的为了解决在设计制造新一代航天飞机的热应力缓和问题的材料。
在航天飞机推进系统并列喷气燃烧器或再用型火箭燃烧器中, 由于气体燃烧温度高达2000℃ , 燃烧室壁承受的热负荷可达100MW/m2, 因此用做燃烧室壁的材料对耐热性、隔热性、耐久性和强韧性有很高的要求。
最初研究的FGM是表面使用温度达2000K、表里温度相差约1000K 的新型超耐热材。
2 表征:2.1 基于梯度源的功能梯度材料表示方法基于梯度源的功能梯度材料实体模型由香港大学的Y. K. Siu 和S. T. Tan,提出该模型将实体的几何元素 (如点、线、面)作为梯度源,记录该梯度源下的材料成分方程f ( d )及材料数组M, 其中, 材料成分方程f ( d)由各点到梯度源的垂直距离来记录实体内部材料分布情况.2.2 基于力学性能和玻璃化转变温度的功能梯度材料表示方法通过均匀分散碳纳米填料制备FGM ,用玻璃化转变温度和应力与应变行为的梯度来表征这些材料。
当油含量沿着薄层厚度从0 份变为100 份时,FGM 的玻璃化转变温度Tg从- 56 ℃变为- 80 ℃。
油含量的变化也使拉伸强度、弹性模量、拉断伸长率等沿厚度发生变化。
FGM 的机械性能和Tg 的这种变化有助于在过渡区的低温环境下(即- 56 ℃~80 ℃) 既保持弹性又具有强度。
3 制备方法:3.1 电沉积法在含有某种金属离子的电解溶液中将被沉积工件作为阴极,通过一定波形的低压直流电,使金属离子不断在阴极上沉积为金属的过程。
功能梯度复合材料的制备及隔热性能模拟研究
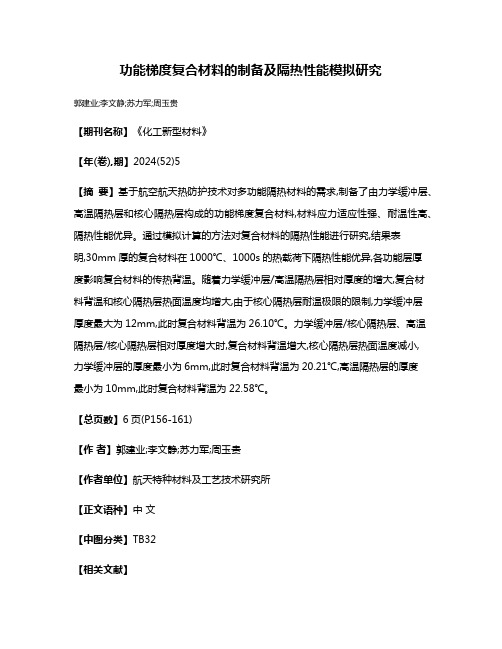
功能梯度复合材料的制备及隔热性能模拟研究
郭建业;李文静;苏力军;周玉贵
【期刊名称】《化工新型材料》
【年(卷),期】2024(52)5
【摘要】基于航空航天热防护技术对多功能隔热材料的需求,制备了由力学缓冲层、高温隔热层和核心隔热层构成的功能梯度复合材料,材料应力适应性强、耐温性高、隔热性能优异。
通过模拟计算的方法对复合材料的隔热性能进行研究,结果表
明,30mm厚的复合材料在1000℃、1000s的热载荷下隔热性能优异,各功能层厚
度影响复合材料的传热背温。
随着力学缓冲层/高温隔热层相对厚度的增大,复合材料背温和核心隔热层热面温度均增大,由于核心隔热层耐温极限的限制,力学缓冲层
厚度最大为12mm,此时复合材料背温为26.10℃。
力学缓冲层/核心隔热层、高温隔热层/核心隔热层相对厚度增大时,复合材料背温增大,核心隔热层热面温度减小,
力学缓冲层的厚度最小为6mm,此时复合材料背温为20.21℃,高温隔热层的厚度
最小为10mm,此时复合材料背温为22.58℃。
【总页数】6页(P156-161)
【作者】郭建业;李文静;苏力军;周玉贵
【作者单位】航天特种材料及工艺技术研究所
【正文语种】中文
【中图分类】TB32
【相关文献】
1.离心法制备环氧树脂/不锈钢短纤维梯度功能复合材料的电性能研究
2.功能梯度铜基复合材料的制备及干摩擦磨损性能
3.功能化改性碳纳米管接枝聚氯乙烯复合材料的制备及性能研究(二)——复合材料的制备、表征及性能研究
4.具备隔音隔热性能的PVC复合材料的制备及其性能研究
因版权原因,仅展示原文概要,查看原文内容请购买。
梯度功能材料

报告人:张倩 专 业:动力工程及工程热物理
2015-10-28
目 录
1 2 3 4 概述 梯度折射率材料
热防护梯度功能材料
梯度功能材料的应用
概述
梯度功能材料(functionally gradient materials,缩写 FGM)是两种或多种材料复合成组分和结构呈连续 梯度变化的一种新型复合材料,是应现代航天航空 工业等高技术领域的需要,为满足在极限环境下能 反复地正常工作而发展起来的一种新型功能材料。 随着梯度功能材料的研究和发展,其应用不再局 限于宇航工业,已经扩展到核能源、电子材料、光 学工程、化学工业和生物医学工程等领域。
概述
梯度功能材料的主要特征:
1.材料的组分和结构呈连续梯度变化 2.材料内部没有明显的界面 3.材料的性质也相应呈连续梯度变化
材料组合方式:
1.金属/陶瓷 2.金属/非金属 3.陶瓷/陶瓷 4.陶瓷/非金属 5.非金属/塑料
梯度折射率材料
梯度折射率材料是一种非匀质材料,它的组分和 结构在材料内部按一定规律连续变化,从而使折射 率也相应地持续变化。 无机材料(如:玻璃梯折材料) 梯度折射率材料
热防护梯度功能材料
热防护梯度功能材料的设计
使金属和陶瓷的组分和结构呈连续变化,从而物性 参数也呈连续变化的复合材料。
热防护梯度功能材料
过程:
热力学边界条件
热防护梯度功能材料的设计
选择材料组合体系、制备方法
材料体系物理参数
温度分布模拟和热应力模拟
结果提交材料合成部门
热防护梯度功能材料
热防护梯度功能材料的种类
梯度功能材料的应用
2.作梯度折射光学材料
梯度折射率透镜
大大减小组件总数 和非球面组件总数、 简化结构
梯度功能材料

梯度功能材料梯度功能材料State:1. 此⽂在是从中英⽂⽂献中的“简单总结”,没列出相应的参考⽂献2. 是为允诺⼀位朋友⽽做,也可以算作⾃⼰的读书⼩笔记,仅此⽽已背景梯度功能材料( Functionally Gradient Materials ,简称FGM)是由于航空航天技术的发展⽽提出的新概念。
航天飞机在⼤⽓层中长时间飞⾏,机头尖端和发动机燃烧室内壁的温度⾼达2100 K 以上,因此材料必须承受很⼤的⾼温以及内外的温度差别,服役的环境很恶劣。
1984 年,⽇本学者Masyuhi NINO,Toshio HIRA,和Ryuzo WATANBE等⼈⾸先提出了FGM 的概念,其设计思想⼀是采⽤耐热性及隔热性的陶瓷材料以适应⼏千度⾼温⽓体的环境,⼆是采⽤热传导和机械强度⾼的⾦属材料,通过控制材料的组成、组织和显微⽓孔率,使之沿厚度⽅向连续变化,即可得到陶瓷⾦属的FGM。
所谓梯度功能材料(FGM), 即在材料制备过程中,使组成、结构及孔隙率等要素在材料的某个⽅向上连续变化或阶梯变化, 从⽽使材料的性质和功能也呈连续变化或阶梯变化的⼀种⾮均质复合材料。
功能梯度材料的研究开发最早始于1987 年⽇本科学技术厅的⼀项“关于开发缓和热应⼒的功能梯度材料的基础技术研究”计划。
该项⽬于1992 年完成,随后将⼯作重⼼转向模拟件的试制及其在超⾼温、⾼温度梯度落差及⾼温燃⽓⾼速冲刷等条件下的实际性能测试评价上,并于1993 年开始研究具有梯度结构的能量转换材料。
第⼀届国际FGM 研讨会于1990 年在⽇本仙台召开,之后每两年举办⼀届。
中国于2002 年在北京主办过第七届FGM国际研讨会。
特点功能梯度材料的关键特点是控制界⾯的成分和组织连续变化,使材料的热应⼒⼤为缓和。
从材料的组成⽅式看,功能梯度材料可分为⾦属/陶瓷、⾦属/⾮⾦属、陶瓷/陶瓷、陶瓷/⾮⾦属和⾮⾦属/聚合物等多种结合⽅式。
从组成变化可划分为:功能梯度整体型(组成从⼀侧到另⼀侧呈梯度渐变的结构材料),功能梯度涂覆型(在基体材料上形成组成渐变的涂层)和功能梯度连接型(粘结两个基体间的接缝呈梯度变化)。
功能梯度材料

功能梯度材料功能梯度材料(FGM)是一种具有梯度性质的复合材料,其性能在材料内部呈现出逐渐变化的特点。
这种材料的设计灵感来源于自然界中许多生物体的结构,比如贝壳、骨骼等,它们都具有类似的梯度性质,能够有效地抵抗外部环境的影响,具有很高的韧性和强度。
功能梯度材料的设计理念是将不同性能的材料通过一定的方式结合起来,使得整体材料的性能在空间上呈现出梯度变化。
这种设计能够充分发挥各种材料的优势,同时弥补它们的缺陷,从而实现材料性能的最优化。
在实际应用中,功能梯度材料已经被广泛应用于航空航天、汽车制造、医疗器械等领域,取得了显著的效果。
功能梯度材料的制备方法多种多样,包括堆砌法、激光熔覆法、沉积法等。
其中,堆砌法是一种比较常见的制备方法,它通过层层堆砌不同性能的材料,然后进行烧结或热压,最终形成具有梯度性质的复合材料。
激光熔覆法则是利用激光熔化金属粉末,将不同成分的金属粉末逐层熔覆在基底上,形成梯度材料。
沉积法则是通过化学气相沉积、物理气相沉积等方法,在基底上沉积不同性能的材料,形成梯度材料。
功能梯度材料的应用前景广阔,它可以为工程领域提供更多的可能性。
比如,在航空航天领域,功能梯度材料可以用于制造航天器的热防护层,提高其对高温和高速气流的抵抗能力;在汽车制造领域,功能梯度材料可以用于制造车身结构件,提高汽车的安全性和舒适性;在医疗器械领域,功能梯度材料可以用于制造人工关节和骨科植入物,提高其与人体组织的相容性和稳定性。
总的来说,功能梯度材料是一种具有巨大潜力的新型材料,它将为人类社会的发展带来新的机遇和挑战。
随着科学技术的不断进步,功能梯度材料必将在更多领域展现出其独特的价值和魅力,为人类社会的可持续发展做出更大的贡献。
- 1、下载文档前请自行甄别文档内容的完整性,平台不提供额外的编辑、内容补充、找答案等附加服务。
- 2、"仅部分预览"的文档,不可在线预览部分如存在完整性等问题,可反馈申请退款(可完整预览的文档不适用该条件!)。
- 3、如文档侵犯您的权益,请联系客服反馈,我们会尽快为您处理(人工客服工作时间:9:00-18:30)。
采用铸造−倾析−铸造技术制备A390/A356铝合金功能梯度复合材料时过热和凝固层厚度对其界面接合的影响Abstract: T he cast−decant−cast is a new method for the preparation of thefunctionally graded components that has been developed in recent years. The functionally graded cylindrical shape component with a radial gradient, e.g. the first alloy (A390) with high wear resistance on the surface of the piece and toughness and the second alloy (A356) of low machining costs in the core of the piece can be produced via this melt process. The effectof the second alloy superheat at temperatures of 750, 820 and 860 °C as well as the effect of the first alloy solidified layer at 25, 35 and 45 s decanting time on achieving the perfect interface between the twoalloys was investigated. The characterization of the interface was carried out by optical microscopy and scanning electron microscopy,and its width was measured by the microhardness test. The results showed that the best interface was obtained at 860 °Cand 35 s decanting time with a width of 500 µm. Also, the wear resistance test was performed to measure and compare the surface wear resistance to the core. Key words: A390 alloy; A356 alloy; functionally graded material; cast−decant−cast process摘要:铸造−倾析−铸造技术是近年来发展起来的一种制备功能梯度材料的新方法。
采用这种方法制备在径向具有梯度功能的圆柱形试样,其外表层为具有高耐磨性的A390铝合金,芯部为具有较高韧性和加工性能的A356铝合金。
研究芯部熔体在不同过热温度(750,820和860 °C)和表层在不同倾析时间(25,35和45 s)下的A390/A356铝合金界面接合情况。
采用光学显微镜和扫描电镜对界面进行表征,对界面区的显微硬度进行测量。
结果表明,在过热温度为860 °C,倾析时间为35 s的条件下,可以获得一宽度约为500 μm的接合良好的界面层。
比较了试样表面层和芯部的耐磨性能。
关键词:A390铝合金;A356铝合金;功能梯度材料;铸造−倾析−铸造技术1引言工程中的许多组件需要材料的对立特性,如质轻和耐磨,耐磨性和可加工性,横截面的硬度和韧性等。
梯度功能材料(FGM)填补了这种材料科学的缺口,就是组件需要在不同的位置有不同的属性和实现均相横截面的最优属性的材料。
功能梯度材料是成分和显微结构沿厚度变化的材料[ 1 ]。
在最近的几十年里,一些熔融工艺已被用于批量制作功能梯度材料。
最常见的方法是离心铸造[ 2 ],功率超声铸造[ 3 ],沉降[4],磁分离[5]和熔体渗透[ 6]。
2005年,都柏林大学开发了生产功能梯度轻合金铸造的新技术;该技术被称为铸造−倾析−铸造(CDC)技术。
SCANLAN等人确定了三个与CDC(铸造−倾析−铸造)进程相关联的技术:转向,内部倾析和低压技术。
通过这些方法生产的功能梯度材料,已被用于生产下面的模型。
首先将铝合金引入模具,让部分凝固在模壁或核心,以形成一层。
当该层得到所需厚度,慢慢倒出剩余的第一种合金未凝固的部分和第二种合金,然后引入模具。
每个加工工艺共同的步骤是倾析。
这项工作的主要目的是制造一个在一个表面上径向梯度变化具有高的耐磨性和硬度的Al -Si合金的FGM活塞,在另一个表面上或在一块的核心具有高切削性和韧性。
生产Al -Si合金的FGM活塞的研究已经通过另一个工艺,如离心铸造。
然而,当CDC (铸造−倾析−铸造)过程有能力生产径向梯度的功能梯度材料,这一过程,尤其是转换工艺,已经用于该项研究。
有关其产品和其他功能梯度材料产品主要关注的是实现不同层或合金是由推定的方法或传输方式产生不同层或合金之间的完美界面。
研究人员还没有详细地报告这一过程。
这可以通过第二合金过热度的影响及第一合金凝固层的影响实现理想的界面和宽的过渡带。
因此,在本工作中,关于实现理想的界面与上述参数的影响进行了研究。
同时,热分析是探讨一个可靠的和可重复的方法进行的测量第一合金凝固层的固相体积分数。
2实验2.1材料和设备该项目的重点是使用的Al-Si合金可以结合许多上述对立的的材料特性。
两种合金分别采用:第一,A390铝合金,过共晶Al-Si合金;第二,A356铝合金,一种亚共晶Al-Si合金。
两种合金的化学成分见表1。
A390铝合金是一种坚硬,具有耐磨性硅含量~16%的合金。
A356铝合金是一种硅含量为7%的更为强硬的材料。
这种技术的装置是一个简单的圆柱型的侧手柄st37钢用,如图1所示。
手柄能使模具倒立。
2.2表征微观结构的表征是使用光学显微镜进行(OM)和扫描电子显微镜(SEM)。
能量色散X射线光谱(EDS)被用来分析界面,研究硅梯度。
2.3显微硬度和耐磨性显微硬度试验是从一个距离界面区100μm的间隔的右侧和左侧的进行,以确定所述过渡区的宽度,并测量其中存在的硅含量和微观结构的梯度。
干滑动磨损试验是以测量和比较的表面耐磨性为核心在25m㎡的立方体样品用销-盘磨损试验机进行的。
应该考虑的是0.25m/ s 的滑动速度,50 N的载荷和1000米的磨损距离。
磨损的单位是磨损质量(毫克)。
磨损表面用扫描电子显微镜观察。
2.4热分析使用高速数据采集系统(模拟- 数字(A /D)转换器)连接到笔记本电脑收集该温度- 时间数据。
在这项工作中使用的A / D转换器有一个敏感的16路通道的16位转换器,他的响应时间0.02秒,检测精度高。
K型热电偶用来测量熔体合金凝固过程中的温度。
热电偶位于从模具底部25毫米高度的永久模具中心的位置。
模具预热温度至200°C。
CDC(铸造−倾析−铸造)的过程的熔融情况是,A390铝合金的熔点在750°C。
使用热分析软件和Excel软件绘制冷却曲线和一阶导数曲线。
在这项工作中,热分析技术被用来量化A390铝合金凝固过程中的固相分数。
从凝固试验样品放出的热量可以用以下一阶导数曲线和零线(基线)之间的面积来计算[ 9 ]。
固相分数的热量成比例。
因此,外部合金凝固层可以通过热分析技术获得相关是固相分数。
值得注意的是,热测试分析仪是在恒定温度下被用于找到外部合金(A390铝合金)的凝固层厚度。
计算的精度在很大程度上取决于零点曲线评估。
本文基于巴洛和斯特凡内斯库采用的牛顿模型给出零点曲线的计算分析。
因此,为了确定固相分数,需要绘制冷却曲线(CC),一阶导数曲线,和零点(ZC)曲线。
最后,通过以下公式计算是固相分数的数值:2.5步骤为了探讨过热度对两种合金的界面之间的影响,A390铝合金作为第一合金,A356铝合金作为第二合金在750°分别在两个单独炉和不同的过热温度750,820和860°C被熔融。
该步骤是通过以下方式进行。
首先,将A390铝合金倒入模具中,然后使其固化,在模具的侧壁形成一层。
层厚度随时间向中心增加。
当该层达到所要求的其被认为是浇注熔融后固化时间是35秒厚度,为了从模具中除去未固化的A390铝合金用手柄将模具倒置。
含有一层A390铝合金的模具固化反对侧壁回到了直立位置。
然后,将剩余的A356铝合金在750,820和860℃的不同过热温度倒入中央空腔。
这导致了填充件的芯与该表面的有不同的合金。
足以影响界面形成的另一个重要的参数是模壁凝固层厚度。
为此,利用热分析的结果作为固体的体积分数,我们认为三次倾析的时间是25,35和45S。
宏观的样品如图2所示。
应该说,根据以往的研究结果当其它条件不变时,A356铝合金的过热温度是860℃。
通过这种方法,提高表面的高硅A390及减少低硅A356为核心,生产梯度硅构件。
值得注意的是倾析和第二合金之间的浇注必须达到足够短的时间,以实现良好的金属粘合,没有任何无效的氧化膜。
3结果与讨论3.1过热温度的影响在不同的过热温度制备的样品的界面的宏观形貌和显微照片如图3所示。
可以看出,在过渡区域中的两种合金相互粘合。
在这个区域中的A390铝合金在左侧和A356铝合金在右侧。
在不同过热温度下采取了样品的宏观形貌,以显示第二铝合金(A356)的颗粒尺寸。
在图3中,显然所观察到的晶粒尺寸随过热温度的升高而增加。
以750°C的过热温度,尚未获得理想的界面和良好的金属粘合。
尽管750℃的过热温度,两种合金在820℃下能完全结合,但如图3(e)所示的显微组织,这两种合金似乎没有互相均匀混合,并且在过渡区域中获得了薄弱界面。
然而,在过热度是860℃时(图3(C,F)),产生了理想的完全混合的界面。
结果发现,为了实现了良好的粘合,高温熔融的第二合金至关重要,因为第二合金的高过热状态导致了内层部分凝固合金的再熔融,并与第一合金的液体混合。
最初的合金重熔过程中过渡区微观结构的特点是通过以下方式确定的。
主要因素是硅含量从表层到中心逐渐降低。
结果,靠近凝固层的第二合金中Si含量的增加,固化时,如图4所示,由于相邻的凝固层有较高的凝固速率,它有了一个新的含有细晶和初晶Si的结构特点。
两种合金从侧面合金的显微组织可以区分的区域称为过渡区域。
强化的过共晶合金Si粒子和树枝状的过共晶合金α(AI)之间的距离确定了过渡区的宽度。