粉末冶金原理-烧结(PPT48页)
粉末冶金新技术-烧结

用SPS制取块状纳米晶Fe90Zr7B3软磁的过程是: 先将由非 晶薄带经球磨制成的50~150μm非晶粉末装入WC/Co合金 模具内,并在SPS烧结机上烧结(真空度1×10-2Pa以下、升温 速度0.09~1.7K/s、温度673~873K、压力590MPa), 再把所 得的烧结体在1×10-2Pa真空下、以3 7K/s速度加热到923K、 保温后而制成。材料显示较好的磁性能:最大磁导率29800、 100Hz下的动态磁导率3430, 矫顽力12A/m。
3
双频微波烧结炉 生产用大型微波烧结炉 已烧结成多种材料:如陶瓷和铁氧体等材料。另 外,在日本又开发出相似的毫米波烧结技术,并成功 地在2023K下保温1h烧结成全致密的AlN材料。
4
2.爆炸压制技术 爆炸压制又称冲击波压制是一种有前途的工艺
方法,它在粉末冶金中发挥了很重要的作用, 爆炸压 制时,只是在颗粒的表面产生瞬时的高温,作用时间 短,升温和降温速度极快。适当控制爆炸参数,使得 压制的材料密度可以达到理论密度的90%以上,甚至 达到99%。
3)快速脉冲电流的加入, 无论是粉末内的放电部位还是焦耳 发热部位, 都会快速移动, 使粉末的烧结能够均匀化。
11
与传统的粉末冶金工艺相比,SPS工艺的特点是:
• 粉末原料广泛:各种金属、非金届、合金粉末,特别是 活性大的各种粒度粉末都可以用作SPS 烧结原科。
• 成形压力低:SPS烛结时经充分微放电处理,烧结粉末表 面处于向度活性化状态.为此,其成形压力只需要冷压烧 结的l/10~1/20。
17
SPS制备软磁材料 通常用急冷或喷射方法可得到FeMe(Nb、Zr、Hf)B的非 晶合金,在稍高于晶化温度处理后, 可得到晶粒数10nm,具有 体心立方结构,高Bs 、磁损小的纳米晶材料。但非晶合金目 前只能是带材或粉末, 制作成品还需要将带材重叠和用树脂固 结, 这使得成品的密度和Bs均变低。近年, 日本采用SPS工艺研 究FeMeB块材的成形条件及磁性能。
粉末冶金知识讲义(ppt 48页)
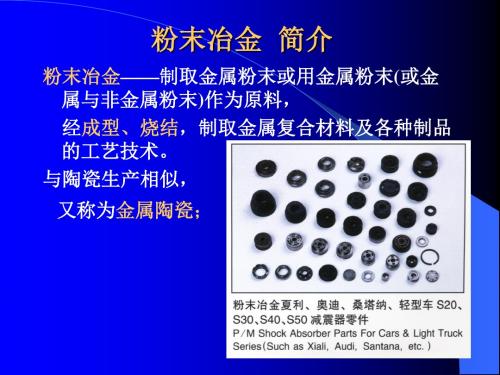
5、粉末性能及测定 成分-
金属粉末、合金粉末、金属化合物粉末;
聚集状态 单颗粒、 二次颗粒; 2-1
外形-球形、多角形、树枝形 2-4;
粒度: 粗粉-150~500微米; 中粉-40~150微米, 细粉-10~40微米; 极细粉-0.5~10微米 超细粉-0.5微米以下; 纳米粉-100纳米及以下;
粉末压坯,在适当的温度和气氛中, 所发生的物理化学变化, 由粉末颗粒的聚集体→晶粒的聚集体; 颗粒之间发生粘结、强度↑,多数情况下密度也↑ 粉末有自动粘结的倾向(比表面积大,能量高), 特别是极细粉末;
烧结是制品达到所要求的性能-关键;
烧结的热力学过程 -5-1 ①烧结初期: 颗粒之间接触点或面 →晶体结合, 经过形核长大→烧结颈;即颗粒界面→晶粒界面, 烧结体不收缩,密度↑极小,强度、导电性明显↑
粉末冶金 简介
粉末冶金——制取金属粉末或用金属粉末(或金 属与非金属粉末)作为原料, 经成型、烧结,制取金属复合材料及各种制品 的工艺技术。
与陶瓷生产相似,
又称为金属陶瓷;
一、发展历史 公元前3000年,古埃及人用C还原氧化铁
制成海绵状的铁, 经高温锻造成致密块状的Fe, 再制出铁器; 本世纪初,电灯W丝问世(爱迪生发明), 使粉末冶金得以迅速发展;
分类和牌号 YG类(钨钴类)
—Y、G:硬、钴,其后数字代表钴含量。 牌号后面的“C”表示为粗晶粒合金,
“X”表示细晶粒合金。 YT类(钛钨类)-除WC、Co外,
还有硬度比WC更高的TiC粉末。 耐磨性高但强度和韧性低。 YW类-新发展起来的硬质合金, 含有TaC,红硬性提高。 用来切削耐热钢、不锈钢、
2、多孔材料 含油轴承:Fe粉+石墨粉+硬脂酸锌=混合、
粉末冶金原理与工艺-烧结原理

30
表面张力作用在烧结颈上的拉应力引起的驱动力 1、烧结初期: 由拉普拉斯方程,颈部弯曲面上 的应力ς为 ς=γ(1/x-1/ρ) ≌-γ/ρ (x>>ρ) 作用在颈部的张应力指向颈外 导致烧结颈长大,孔隙体积收缩 LOGO 随着烧结过程的进行,∣ρ∣的 数值增大 烧结驱动力逐步减小
31
表面张力作用在引起的驱动力
19
二、烧结颈的形成与长大
前期的特征 形成连续的孔隙网络,孔隙表面光滑化 后期的特征 孔隙进一步缩小,网络坍塌并且晶界发 生迁移
LOGO
20
为什么会导致颗粒间的距离缩短? 原子的扩散,颗粒间的距离缩短 烧结颈间形成了微孔隙 微孔隙长大 聚合导致烧结颈间的孔隙结构坍塌 银粉的烧结提供了相关证据
55
与Kingery-Berge烧结动力学方程联立 L/L
28
合金粉末烧结的驱动力
合金粉末
烧结驱动力则主要来自体系的自由能降低
• △G=△H-T△S • △G≠0 且<0
自由能降低的数值远大于表面能的降低 表面能的降低则属于辅助地位
LOGO
29
颗粒尺寸10µm的粉末的界面能降低为110J/mol 化学反应的自由能降低一般为100-1000J/mol, 比前者大了两个数量级,合金化也是一种特 殊的化学反应
颈部生长速率
*
(a)
V L 5D LOGO 3 3( V L kT
6 2 2/5 ) r 5 t 5 (b)
颗粒中心逼近速率
47
表面扩散 基本观点: 低温时,表面扩散起主导作用
而在高温下,让位于体积扩散
细粉末的表面扩散作用大。
LOGO
48
烧结早期孔隙连通,表面扩散的结 果导致小孔隙的缩小与消失,大孔 隙长大 烧结后期表面扩散导致孔隙球化
粉末冶金烧结原理

粉末冶金烧结原理
粉末冶金烧结是一种常用的制备金属和陶瓷材料的工艺。
其原理基于粉末颗粒在高温下通过表面扩散和颗粒间的相互作用力而实现的固相结合。
首先,通过研磨和混合的方式将所需的金属或陶瓷粉末混合均匀。
混合的目的是使不同粉末颗粒在烧结过程中能够更好地接触和相互结合。
接下来,将混合后的粉末填充到模具中,并施加一定的压力。
压力的作用是使粉末颗粒之间产生一定的接触力,这样可以促进烧结过程中的颗粒扩散。
然后,将填充好的模具放入烧结炉中,进行高温处理。
在高温下,粉末颗粒表面会发生表面扩散,即颗粒表面的原子或离子会向颗粒内部扩散。
同时,由于高温下颗粒间的相互作用力增强,颗粒之间产生局部的结合。
经过一段时间的高温处理,粉末颗粒表面扩散和颗粒间的结合逐渐扩展到整个颗粒,形成了一个密实的整体。
这个过程称为固相烧结,通过这种方式,粉末的体积会明显减小。
最后,将烧结后的样品冷却并取出,进行进一步的加工和处理。
根据需要,可以对烧结样品进行后续的热处理、机加工等工艺步骤。
总之,粉末冶金烧结是一种通过高温和压力作用下,将粉末颗
粒固相结合的制备材料的方法。
通过控制烧结过程中的温度、压力和时间等参数,可以获得具有预期性能的金属和陶瓷材料。
四、烧结.ppt
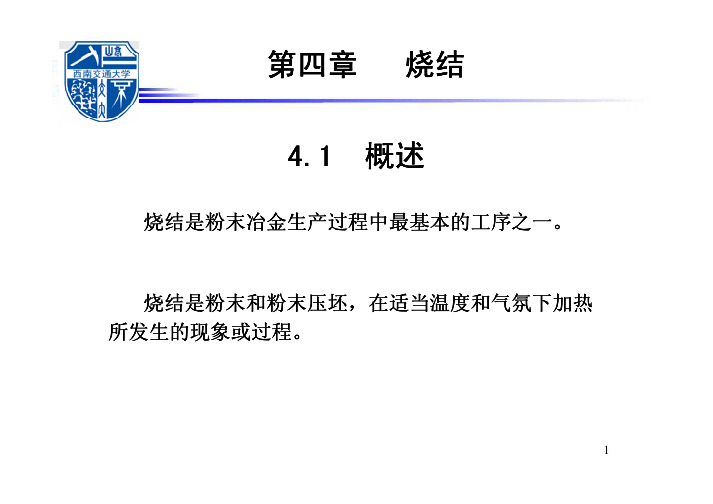
1第四章烧结4.1 4.1 概述概述烧结是粉末冶金生产过程中最基本的工序之一烧结是粉末冶金生产过程中最基本的工序之一。
烧结是粉末和粉末压坯烧结是粉末和粉末压坯,,在适当温度和气氛下加热所发生的现象或过程所发生的现象或过程。
2按烧结过程有无明显的液相出现和烧结系统的组成分为和烧结系统的组成分为::1)单元系烧结2)多元系固相烧结3) 3) 多元系液相烧结多元系液相烧结3粘结阶段颗粒的原始接触点或面转变成晶体结合颗粒的原始接触点或面转变成晶体结合,,即通过成核即通过成核、、结晶长大等原子过程形成烧结颈等原子过程形成烧结颈。
烧结体密度烧结体密度、、烧结体强度烧结体强度、、导电性等的变化烧结颈长大阶段原子向颗粒结合面迁移原子向颗粒结合面迁移,,烧结颈扩大烧结颈扩大,,颗粒间距缩小颗粒间距缩小,,晶粒长大,晶界越过孔隙移动晶界越过孔隙移动。
烧结体密度烧结体密度、、烧结体强度等的变化闭孔隙球化和缩小阶段烧结体致密度达到烧结体致密度达到90%90%90%以上以上以上,,孔隙闭合后孔隙闭合后,,孔隙形状趋于球形并缩小缩小。
4.2 4.2 烧结的基本过程烧结的基本过程41)烧结为什么会发生烧结为什么会发生??2)烧结是怎样进行的烧结是怎样进行的??4.34.3 烧结理论的两个最基本的问题51)烧结为什么会发生烧结为什么会发生??烧结是系统自由能减低的过程。
•由于颗粒结合面的增大和颗粒表面的平直化,粉末体的总表面积和总表面自由能减小•粉末体内孔隙的总体积和总表面积减小•粉末内晶格畸变的消除62)烧结是怎样进行的烧结是怎样进行的??烧结的机构和动力学问题,研究烧结过程中各种物质迁移方式以及速率。
7单元系烧结是指:纯金属或有固定成分的化合物的粉末在固态下的烧结,不会出现新组成物或者新相,也不会出现凝聚状态的改变。
4.4 4.4 单元系烧结单元系烧结8一、烧结温度和时间•单元系的烧结主要机构是扩散和流动构是扩散和流动。
粉末冶金:粉末烧结

烧结机理
烧结过程中物质的迁移方式
➢ 粘性流动:在剪切应力作用下,产生粘性流动, 物质向颈部迁移
➢ 蒸发凝聚:表面层原子向空间蒸发,借蒸汽压差 通过气相向颈部空间扩散,沉积在颈部
➢ 体积扩散:借助于空位运动,原子等向颈部迁移 ➢ 表面扩散:原子沿颗粒表面迁移 ➢ 晶界扩散:晶界为快速扩散通道,原子沿晶界向
颈部迁移 ➢ 位错管道扩散:位错为非完整区域,原子易于沿
此通道向颈部扩散,导致物质迁移
烧结过程中物质的迁移方式
扩散
蒸发凝聚
回复再结晶和聚晶长大
➢ 回复 ➢ 再结晶 ➢ 聚晶长大
◊无限固溶系 ◊有限固溶系 ◊完全不溶系
液相烧结 多元系液相烧结
◊稳定液相烧结 ◊瞬时液相烧结 ◊熔浸
烧结理论的研究范畴
研究粉末压坯在烧结过程中微观结构的 演化和物质变化规律 ➢ 热力学:烧结过程的驱动力(Why) ➢ 动力学:烧结过程中物质迁移方式和迁移 速度(How)
烧结理论的发展
➢ 烧结工艺始于公元前3000年 ➢ 烧结理论始于20世纪中期 ➢ 目前还没有成熟的理论
烧结基本过程
三阶段:
(1) 颗粒之间形成接触 (2) 烧结颈长大
➢ 粘结阶段
(3) 连通孔洞闭合 (4) 孔洞固化
➢ 烧结颈长大阶段
(5) 孔洞收缩和致密化 (6) 孔洞粗化
(7) 晶粒长大
➢ 闭孔隙球化和缩小阶段
水分挥发 化学反应 应力消除 回复和再结晶
粘结面和晶界的形成
粘结面和晶界的形成
烧结后的孔隙
粉末冶金原理-烧结
粉末冶金原理-烧结烧结是粉末冶金中一种常用的加工方法,它通过高温和压力的作用,将金属粉末粒子相互结合成致密的块状体,从而获取所需的材料性能和形状。
本文将介绍烧结的原理、方法以及应用。
1. 烧结原理粉末冶金烧结的原理基于固相扩散和短程扩散的作用。
在烧结过程中,金属粉末颗粒之间的接触面发生原子间的扩散,使得粒子之间形成更强的结合力,从而实现粉末的聚结。
烧结过程中,首先是金属粉末颗粒之间的接触,原子开始扩散。
随着温度的升高,扩散速率也随之增加。
当粉末颗粒之间的接触点扩散到一定程度后,开始形成颗粒之间的原子键合。
键合的形成使得颗粒间的结合力增强,同时形成新的晶体结构或弥散态结构。
2. 烧结方法2.1 传统烧结传统烧结是指采用外加热源和压力来实现烧结过程。
该方法通常包括以下几个步骤:1.装料:将金属粉末和所需添加剂按照一定比例混合,并形成一定的装料形状,如坯料或颗粒。
2.预压:将装料放入模具中,并施加一定的压力,使装料初步固结成形。
3.高温烧结:将装料放入烧结炉中,在一定的温度下暴露一段时间,使装料中的金属粉末颗粒扩散、晶粒长大并结合。
4.冷却:烧结完成后,将烧结块从炉中取出,经过冷却以稳定材料结构。
5.表面处理:根据需求,对烧结块进行加工、修整和处理,以得到最终所需的形状和表面特性。
2.2 反应烧结反应烧结是指在烧结过程中引入化学反应,利用固相反应进行金属粉末的结合。
相较于传统烧结,反应烧结可以实现更高的烧结温度,加快晶粒生长和结合的速度。
反应烧结的具体步骤包括:1.装料:将金属粉末和反应剂按照一定比例混合,并形成装料。
2.高温烧结:将装料放入烧结炉中,在一定的温度下暴露一段时间。
在高温下,反应剂与金属粉末发生固相反应,生成新的物质并结合金属粉末颗粒。
3.冷却:烧结完成后,将烧结块从炉中取出,经过冷却以稳定材料结构。
4.表面处理:根据需求,对烧结块进行加工、修整和处理,以得到最终所需的形状和表面特性。
3. 烧结应用烧结方法在粉末冶金中具有广泛的应用。
粉末冶金原理烧结ppt课件
二、烧结的热力学问题
粉末有自动粘结或成团的倾向 粉末烧结使系统自由能减少的过程 烧结系统自由能降低是烧结过程的原动力。烧结
后系统自由能降低包括下述几个方面: (1)由于颗粒结合面(烧结颈)的增大和颗粒表
面平直化,粉末体的总比表面积和总表面自由能 减小; (2)烧结体内孔隙的总体积和总表面积减小; (3)粉末颗粒内晶格畸变部分消除。
借助于建立物理、几何或化学模型, 进行烧结过程的计算机模拟(蒙特-卡 洛模拟)
粉末烧结过程模拟
多相粉末烧结
液相烧结
三、烧结技术的发展
● 外力的引入(加压同时烧结): ➢ HP、HIP、超高压烧结(纳米晶材料)等 ➢ 气压烧结
●快速烧结技术
1 电固结工艺 2 快速热等静压(quick-HIP) 3 微波烧结技术 4 激光烧结 5 等离子体烧结 6 电火花烧结
按烧结过程有无液相出现
固相烧结:
单元系固相烧结:单相(纯金属、化合物、固溶体)粉末 的烧结:烧结过程无化学反应、无新相形成、无物质聚集 状态的改变。 多元系固相烧结:
两种或两种以上组元粉末的烧结过程,包括反应烧结等。
无限固溶系:Cu-Ni、Cu-Au、Ag-Au等 有限固溶系:Fe-C、Fe-Ni、Fe-Cu、W-Ni等 互不固溶系:Ag-W、Cu-W、Cu-C等
烧结颈长大
3.封闭孔隙球化和缩小阶段 当烧结体密度达到90%以后, 多数孔隙被完全分隔,闭
孔数量大的增加,孔隙形状趋近球形并不断缩小。在这个 阶段,整个烧结体仍可缓慢收缩,但主要是靠小孔的消失 和孔隙数量的减少来实现。这一阶段可以延续很长时间, 但是仍残留少量的隔离小孔隙不能消除。也就是一般不能 达到完全致密。
对烧结定义的理解-1:
● 粉末也可以烧结(不一定要成形) 松装烧结,制造过滤材料(不锈钢,青铜,黄铜,钛等)
粉末冶金培训资料-烧结理论
粉末冶金钢的烧结
• 为什么烧结 ? • • • • • • 烧结工艺 影响烧结的参数 烧结过程中发生了什么? 烧结机理 烧结粉末冶金钢 烧结的类型
为什么烧结?
生坯状态 (冷焊)Leabharlann 烧结状态 (颗粒间的粘接)
金属粉末压坯
多孔金属
生坯和烧结状态
压制后
烧结后
烧结工艺
温度
1 室温
2
3
4
时间 1 脱蜡 (300 - 700℃) 2 C 分解 (800 - 950℃) 3 烧结 (1100 - 1300℃) 4 冷却 (冷却速率)
• 相变: F, P, B, M, γ • 碳化物析出
烧结的不同类型
• 温度 (< 1150 ℃, >1150 ℃) • 烧结炉 (批次炉, 推杆炉, 网带炉, 步进梁炉) • 气氛 (真空, 吸热性气氛, N2/H2) • 状态 (液相, 固相) • 压力 (常压, 增压) • 活化能 (颗粒尺寸, 形状,合金系统)
Fe - Cu 体系烧结膨胀机理
90%Fe 10%Cu 1150 ℃
烧结收缩机理
Fe-Cu 和 Fe-Cu-C 体系的尺寸变化
Cu
Cu + 1%C
影响尺寸变化的因素
• • • • • • • • 颗粒尺寸 合金元素 充填和压制不均匀 零件中合金元素分布不均匀 形成液相 烧结温度和时间 烧结炉的温度分布不均匀 烧结炉内气体流动不好
Ni 在 Fe-基的均质化
影响均质化的因素
Ni 颗粒尺寸: 5 um, 10 um 温度: 1000 - 1300C 时间: 0.5 -500 h
重要因素:
• 温度 • Ni 颗粒尺寸 • 时间
粉末制备与烧结ppt课件
(3) 氢还原三氧化钨的工艺
生产可锻致密金属钨用的钨粉是用氢还 原三氧化钨制得的。 生产硬质合金用的钨粉,一般也用氢还 原法制得,因为氢还原法制得的钨粉纯 度较高,粒度易控制。
四、金属热还原法
金属热还原法主要应用于制取稀有金属 (Ta、Nb、Ti、Zr、Th、U、Cr等)
2)氢气的影响
i) 氢气湿度的影响
氢气湿度过大,使还原速度减慢,还原不充 分,结果钨粉颗粒变粗、钨粉含氧虽也增高
氢气湿度过大,增大炉管内的水蒸气浓度, 这样可使很细的钨粉重新氧化成WO2或 W2(OH)2,当它再被氢还原时便沉积在粗粒的 钨粉上,使细W粉不断减少,粗W粉不断长大, 这就是所谓“氧化—复原〞长大机构。
1)原料 i) 三氧化钨粒度的影响 制造钨粉的原料由于原料杂质含量及
煅烧温度不同,所得WO3粒度不相 同。
锻烧钨酸(H2W04)而得到的WO3,颗 粒呈不规则的聚集体,颗粒较细。
煅烧仲钨酸铵 [5(NH4)2O·12WO3·11H2O] 而
i i) 三氧化钨中水含量的影响
WO3中水含量增加,可使钨粉粒度增 加、粒度分布不均匀。
可以很高钨粉质量的均匀程度。在还原过程中, 出于舟皿中上下层物料与氢接触的条件不一样, 不可避处地会们现物料质量不均,采用两阶段还 原,便可提高其均匀程度.
可以提高生产率,因为三氧化钨还原成二氧化钨 后,舟皿中的物料体积大大减小,装舟再去还原, 便可允分利用舟皿的容积 。
(2〕影响钨粉粒度和纯度的因素
Fe稳定
FeO稳定
Fe3O4稳定
固体碳直接还原铁氧化物的反应
当温度高于570℃时 3Fe2O3十C =2 Fe3O4十CO2 Fe3O4十C =3FeO十CO2 FeO十C =Fe十CO2
- 1、下载文档前请自行甄别文档内容的完整性,平台不提供额外的编辑、内容补充、找答案等附加服务。
- 2、"仅部分预览"的文档,不可在线预览部分如存在完整性等问题,可反馈申请退款(可完整预览的文档不适用该条件!)。
- 3、如文档侵犯您的权益,请联系客服反馈,我们会尽快为您处理(人工客服工作时间:9:00-18:30)。
1 概述
一、烧结在粉末冶金生产过程中的重要性 1、烧结是粉末冶金生产过程中最基本的工序之
一。粉末冶金从根本上说,是由粉末成形和粉 末毛坯热处理(烧结)这两道基本工序组成的, 在特殊情况下(如粉末松装烧结),成形工序 并不需要,但是烧结工序,或相当于烧结的高 温工序(如热压或热锻)却是不可缺少的。
2、 烧结也是粉末冶金生产过程的最后一道主要工 序,对最终产品的性能起着决定性作用,因为由烧 结造成的废品是无法通过以后的工序挽救的,烧结 实际上对产品质量起着“把关”的作用。
3、从另一方面看,烧结是高温操作,而且一般要 经过较长的时间,还需要有适当的保护气氛。因此, 从经济角度考虑,烧结工序的消耗是构成产品成本 的重要部分,改进操作与烧结设备,减少物质与能 量消耗,如降低烧结温度,缩短烧结时间等,在经 济上的意义是很大的。
为了反映烧结的主要的组成进行分类:
(1)单元系烧结 纯金属(如难熔金属和纯铁软磁材
料)或化合物 (
等),在其熔点
以下的温度进行的固相烧结过程。
(2)多元系固相烧结 由两种或两种以上的组分构成 的烧结体系,在其中低熔组分的熔点温度以下所进行的固 相烧结过程。粉末烧结合金有许多属于这一类。根据系统 的组元之间在烧结温度下有无固相溶解存在,又分为:
(2)烧结颈长大阶段 ---原子向颗粒结合面的大量迁 移使烧结颈扩大,颗粒间距离缩小,形成连续的孔隙 网络;同时由于晶粒长大,晶界越过孔隙移动,而被 晶界扫过的地方,孔隙大量消失。烧结体收缩,密度 和强度增加是这个阶段的主要特征;
(3)闭孔隙球化和缩小阶段---当烧结体密度达到 90%以后,多数孔隙被完全分隔,闭孔数量大为增加, 孔隙形状趋近球形并不断缩小。在这个阶段,整个烧 结体仍可缓慢收缩,但主要是靠小孔的消失和孔隙数 量的减少来实现。这一阶段可以延续很长时间,但是 仍残留少量的隔离小孔隙不能消除。
烧结机构就是研究烧结过程中各种可能的物质迁移方式 及速率的
烧结时物质迁移的各种可能的过程如表 示。
两球几何模型
在烧结的任一时刻,颈曲 率半径与颈半径的关系是:
烧结机构示意图
(一)粘性流动
粘性流动:在小的应力作用下,应变速度开始随时间变 化(降低)很快,但随时间延长,最后趋于一个常数。
1)无限固溶系 如
在合金状态图中有无限固溶区的系统,
2)有限固溶系 统,如
在合金状态图中有有限固溶区的系 等;
3)完全不互溶系 组元之间既不互相溶解又不形成化 合物或其他中间相的系统,如 等所谓“假合金”。
(3)多元系液相烧结 以超过系统中低熔组分熔点的 温度进行的烧结过程。由于低熔组分同难熔固相之间互 相溶解或形成合金的性质不同,液相可能消失或始终存 在于全过程,故又分为:
烧结过程中不管是否使总孔隙度减低,但孔隙的总表 面积总是减小的。隔离孔隙形成后,在孔隙体积不变 的情况下,表面积减小主要靠孔隙的球化,而球形孔 隙继续收缩和消失也能使总表面积进一步减小,因此, 不论在烧结的第二或第三阶段,孔隙表面自由能的降 低,始终是烧结过程的驱动力
三、烧结驱动力的计算
但由于 很小
二、烧结的概念与分类 1、烧结是粉末或粉末压坯,在适当的温度和气 氛条件下加热所发生的现象或过程。 2、烧结的结果是颗粒之间发生粘结,烧结体的 强度增加,而且多数情况下,密度也提高。如果 烧结条件控制得当,烧结体的密度和其它物理、 机械性能可以接近或达到相同成分的致密材料。 3、从工艺上看,烧结常被看作是一种热处理, 即把粉末或粉末毛坯加热到低于其中主要组分熔 点的温度下保温,然后冷却到室温。在这过程中, 发生一系列物理和化学的变化,粉末颗粒的聚集 体变成为晶粒的聚结体,从而获得具有所需物理、 机械性能的制品或材料
(2)烧结体内孔隙的总体和总表面积减小;
(3)粉末颗粒内晶格畸变的消除。
对烧结过程,特别是早期阶段,作用较大的主要是表 面能。
烧结后颗粒的界面转变为晶界面,由于晶界能更低,故 总的能量仍是降低的。随着烧结的进行,烧结颈处的晶 界可以向两边的颗粒内移动,而且颗粒内原来的晶界也 可能通过再结晶或聚晶长大发生移动并减少。因此晶界 能进一步降低就成为烧结颈形成与长大后烧结继续进行 的主要动力
所以垂直作用于
+)
曲面上的合力为
而作用在面积
上的应力为
负号表示作用在曲颈面 上的应力是张力, 方向朝颈外,其效果是使烧结颈扩大。 随着烧结颈 )的扩大,负曲率半径的 绝对值亦增大,说明烧结的动力也减小。
对于形成隔离孔隙的情况,烧结收缩的动力可用下述 方程描述:
孔隙的半径
5.3烧结机构
烧结过程中,颗粒粘结面上发生的量与质的变化以 及烧结体内孔隙的球化与缩小等过程都是以物质的迁移 为前提的。
5.2 烧结过程的热力学基础 一烧结的基本过程
粉末的等温烧结过程,按时间大致可以划分为三个 界限不十分明显的阶段:
(1)粘结阶段---烧结初期,颗粒间的原始接触点或面 转变成晶体结合,即通过成核、结晶长大等原子过程形 成烧结颈。在这一阶段中,颗粒内的晶粒不发生变化, 颗粒外形也基本未变,整个烧结体不发生收缩,密度增 加也极微,但是烧结体的强度和导电性由于颗粒结合面 增大而有明显增加;
1)稳定液相烧结系统如:
2)瞬时液相烧结系统如:
合金等。
对烧结过程的分类,目前并不统一。盖彻尔(是把金 属粉的烧结分为1)单相粉末(纯金属、固溶体或金属 化合物)烧结;2) 金属或金属非金属)固相烧结; 3)多相粉末液相烧结;4) 熔浸。他把固溶体和金属 化合物这类合金粉末的烧结看为单相烧结,认为在烧 结时组分之间无再溶解,故不同于组元间有溶解反应 的一般多元系固相烧结。
(a)
(b) (c、d)
图 5-1 球形颗粒的烧结模型 烧结前颗粒的原始接触; 烧结早期的烧结颈长大; 烧结后期的孔隙球化
二、烧结的热力学问题
烧结系统自由能的降低,是烧结过程的驱动力,包括 下述几个方面 : (1)由于颗粒结合面(烧结颈)的增大和颗粒表面的 平直化,粉末体的总比表面积和总表面自由能减小;