粉末冶金原理-烧结
粉末烧结原理

粉末烧结原理
粉末烧结是一种常见的金属材料制备工艺,通过高温加热和压力作用,将金属粉末颗粒相互结合,形成致密的块状材料。
这种制备方法被广泛应用于粉末冶金、陶瓷制备、复合材料制备等领域。
下面将介绍粉末烧结的原理及其在材料制备中的应用。
首先,粉末烧结的原理是基于固态扩散和颗粒间的结合作用。
在烧结过程中,粉末颗粒表面发生固态扩散,使得颗粒间的空隙逐渐减小,最终形成致密的结构。
同时,高温和压力的作用使得颗粒间发生结合,形成坚固的结构。
这种固态扩散和颗粒结合作用是粉末烧结的基本原理。
其次,粉末烧结在材料制备中具有重要的应用价值。
首先,粉末烧结可以制备高性能的工程材料。
通过粉末烧结,可以制备出具有良好力学性能、耐磨性、耐腐蚀性的材料,广泛应用于航空航天、汽车制造、机械加工等领域。
其次,粉末烧结还可以制备具有特殊功能的材料。
例如,通过粉末烧结可以制备出具有磁性、导电性、导热性等特殊功能的材料,用于电子器件、磁性材料等领域。
因此,粉末烧结在材料制备中具有广泛的应用前景。
总之,粉末烧结是一种重要的材料制备工艺,其原理是基于固态扩散和颗粒结合作用。
粉末烧结在材料制备中具有重要的应用价值,可以制备高性能的工程材料和具有特殊功能的材料。
随着材料科学的发展,粉末烧结技术将会得到进一步的发展和应用,为各个领域提供更加优质的材料产品。
粉末烧结原理

粉末烧结原理粉末冶金是一种重要的金属材料制备技术,而粉末烧结则是粉末冶金中的一项关键工艺。
粉末烧结是指将金属或非金属粉末在一定的温度、压力和时间条件下进行加热压制,使粉末颗粒之间发生冶金结合,从而形成致密的块状材料的工艺过程。
下面将详细介绍粉末烧结的原理。
首先,粉末烧结原理的第一步是粉末的预处理。
通常情况下,粉末材料需要经过混合、干燥和成型等工艺步骤,以确保粉末颗粒的均匀性和成型性。
在混合过程中,不同种类的粉末可以被混合在一起,以获得特定性能的材料。
然后,干燥工艺可以去除粉末中的水分,有利于后续的成型工艺。
最后,成型工艺将粉末压制成特定形状的坯料,为后续的烧结工艺做好准备。
其次,粉末烧结的第二步是烧结过程。
在烧结过程中,粉末坯料被置于高温环境中,通常伴随着一定的压力。
在高温下,粉末颗粒之间会发生扩散和结合的过程,从而形成致密的晶粒结构。
在烧结过程中,温度、压力和时间是三个重要的参数,它们将直接影响到烧结后材料的密度、晶粒大小和性能。
最后,粉末烧结的第三步是后处理工艺。
烧结后的材料通常需要进行热处理、表面处理和精加工等工艺步骤,以进一步提高材料的性能和精度。
热处理可以消除烧结过程中产生的残余应力和缺陷,提高材料的强度和韧性。
表面处理可以改善材料的耐腐蚀性能和外观质量。
精加工则可以使材料达到特定的尺寸和形状要求。
总之,粉末烧结是一种重要的材料制备工艺,它通过预处理、烧结和后处理三个步骤,将粉末材料转化为致密的块状材料。
粉末烧结工艺可以制备出具有特定性能和形状的材料,广泛应用于汽车、航空航天、电子、医疗器械等领域。
通过对粉末烧结原理的深入了解,可以更好地掌握这一重要工艺,为材料制备和应用提供技术支持。
粉末冶金烧结炉原理
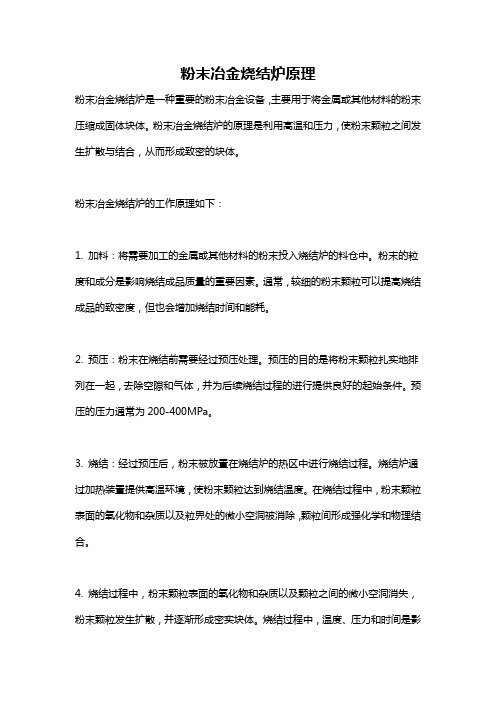
粉末冶金烧结炉原理粉末冶金烧结炉是一种重要的粉末冶金设备,主要用于将金属或其他材料的粉末压缩成固体块体。
粉末冶金烧结炉的原理是利用高温和压力,使粉末颗粒之间发生扩散与结合,从而形成致密的块体。
粉末冶金烧结炉的工作原理如下:1. 加料:将需要加工的金属或其他材料的粉末投入烧结炉的料仓中。
粉末的粒度和成分是影响烧结成品质量的重要因素。
通常,较细的粉末颗粒可以提高烧结成品的致密度,但也会增加烧结时间和能耗。
2. 预压:粉末在烧结前需要经过预压处理。
预压的目的是将粉末颗粒扎实地排列在一起,去除空隙和气体,并为后续烧结过程的进行提供良好的起始条件。
预压的压力通常为200-400MPa。
3. 烧结:经过预压后,粉末被放置在烧结炉的热区中进行烧结过程。
烧结炉通过加热装置提供高温环境,使粉末颗粒达到烧结温度。
在烧结过程中,粉末颗粒表面的氧化物和杂质以及粒界处的微小空洞被消除,颗粒间形成强化学和物理结合。
4. 烧结过程中,粉末颗粒表面的氧化物和杂质以及颗粒之间的微小空洞消失,粉末颗粒发生扩散,并逐渐形成密实块体。
烧结过程中,温度、压力和时间是影响烧结成品的主要因素。
过高的温度会导致颗粒过度烧结,而过低的温度则会影响烧结效果;过高的压力会增加成本和能耗,而过低的压力则会影响烧结致密度;烧结时间过短会导致颗粒结合不良,而过长的时间则会浪费能源。
5. 冷却:烧结完成后,烧结块体经过冷却处理。
在冷却过程中,热区的温度逐渐降低,使得烧结块体逐渐冷却固结,并保持其致密度。
粉末冶金烧结炉的原理是基于粉末颗粒的热扩散和力学固结过程。
在高温环境下,粉末颗粒表面的氧化物和杂质会被清除,颗粒之间发生扩散,表面分子运动速度加快,相互碰撞并结合到一起。
随着时间的推移,这些颗粒之间的结合不断增强,最终形成密实的块体。
粉末冶金烧结炉通过提供高温和压力环境,利用粉末颗粒之间的扩散和力学结合过程,实现了金属或其他材料的粉末烧结成块体的目标。
粉末冶金烧结炉在制造工业、材料科学、航空航天等领域具有重要的应用价值。
粉末冶金新技术-烧结

用SPS制取块状纳米晶Fe90Zr7B3软磁的过程是: 先将由非 晶薄带经球磨制成的50~150μm非晶粉末装入WC/Co合金 模具内,并在SPS烧结机上烧结(真空度1×10-2Pa以下、升温 速度0.09~1.7K/s、温度673~873K、压力590MPa), 再把所 得的烧结体在1×10-2Pa真空下、以3 7K/s速度加热到923K、 保温后而制成。材料显示较好的磁性能:最大磁导率29800、 100Hz下的动态磁导率3430, 矫顽力12A/m。
3
双频微波烧结炉 生产用大型微波烧结炉 已烧结成多种材料:如陶瓷和铁氧体等材料。另 外,在日本又开发出相似的毫米波烧结技术,并成功 地在2023K下保温1h烧结成全致密的AlN材料。
4
2.爆炸压制技术 爆炸压制又称冲击波压制是一种有前途的工艺
方法,它在粉末冶金中发挥了很重要的作用, 爆炸压 制时,只是在颗粒的表面产生瞬时的高温,作用时间 短,升温和降温速度极快。适当控制爆炸参数,使得 压制的材料密度可以达到理论密度的90%以上,甚至 达到99%。
3)快速脉冲电流的加入, 无论是粉末内的放电部位还是焦耳 发热部位, 都会快速移动, 使粉末的烧结能够均匀化。
11
与传统的粉末冶金工艺相比,SPS工艺的特点是:
• 粉末原料广泛:各种金属、非金届、合金粉末,特别是 活性大的各种粒度粉末都可以用作SPS 烧结原科。
• 成形压力低:SPS烛结时经充分微放电处理,烧结粉末表 面处于向度活性化状态.为此,其成形压力只需要冷压烧 结的l/10~1/20。
17
SPS制备软磁材料 通常用急冷或喷射方法可得到FeMe(Nb、Zr、Hf)B的非 晶合金,在稍高于晶化温度处理后, 可得到晶粒数10nm,具有 体心立方结构,高Bs 、磁损小的纳米晶材料。但非晶合金目 前只能是带材或粉末, 制作成品还需要将带材重叠和用树脂固 结, 这使得成品的密度和Bs均变低。近年, 日本采用SPS工艺研 究FeMeB块材的成形条件及磁性能。
粉末冶金烧结的原理是什么

粉末冶金烧结的原理是什么
在粉末冶金烧结过程中,需要选择适当的还原气氛。
还原气氛可以通
过控制烧结过程中的气氛组成和气氛温度来实现。
正确选择还原气氛对于
提高烧结过程中的烧结密度和机械性能非常重要。
目前常用的还原气氛有氢气气氛、氮气-氢气混合气氛、氩气气氛等。
选择适当的还原气氛要考虑以下几个方面:
1.烧结物质的物理和化学性质:不同的物质对于还原气氛的需求是不
同的。
例如,一些物质在氢气气氛中容易发生返还反应,从而产生高纯度
的材料。
而一些物质在氢气气氛中容易脱氧,使材料中的氧含量降低。
2.烧结温度:烧结温度也会影响还原气氛的选择。
一般来说,高温下
需要使用高活性的还原气氛,以确保物质能够进行有效的还原反应。
同时,还原气氛的选择也要避免过高温度会导致烧结物质溶解和气体的浪费。
3.烧结压力:一些还原反应需要一定的压力才能进行,因此在烧结过
程中需要考虑烧结的压力。
一般来说,较高的烧结压力可以增加材料的烧
结密度,同时也可以促进还原反应的进行。
4.烧结时间:不同的还原气氛对烧结时间的要求也不同。
一些气氛需
要较长的烧结时间来实现完全的还原反应,而一些气氛则可以在较短的时
间内完成还原。
总的来说,选择适当的还原气氛是粉末冶金烧结过程中非常重要的一步。
需要综合考虑烧结物质的性质、烧结温度、烧结压力和烧结时间等因素,以确保烧结过程中所需的还原反应能够进行,并获得高质量的烧结材料。
粉末烧结技术
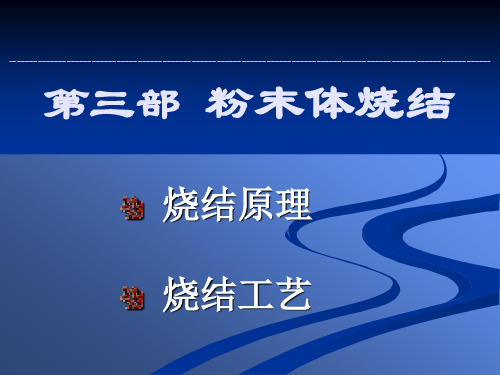
加压烧结—加压和加热同时并用,以达到消除孔
隙的目的,从而大幅度提高粉末制品的性能。常用
的加压烧结工艺有热压、热等静压及烧结-热等静压。
热压—将粉末装在压模内,在加压的同时把粉末加热到熔
点以下,使之加速烧结成比较均匀致密的制品。
热等静压—把粉末压坯或把装入特制容器内的粉末置于热
等静压机高压容器内,使其烧结成致密的材料或零件的过 程。
烧结-热等静压—把压坯放入烧结-热等静压设备的高压容
器内,先进行脱蜡、烧结,再充入高压气体进行热等静压。
反应烧结—先将原材料(如制备Si3N4时使用Si粉)
粉末以适当方式成形后,在一定气氛中(如氮气)
加热发生原位反应合成所需的材料并同时发生烧结。
微波烧结—材料内部整体地吸收微波能并被加热,
使得在微波场中试样内部的热梯度和热流方向与常规 烧结的试样相反。
电火花等离子烧结—也叫等离子活化烧结或电火
花等离子烧结,是利用粉末间火花放电多产生的等
离子活化颗粒,同时在外力作用下进行的一种特殊
烧结方法。
真空热压烧结炉图
微波生物陶瓷烧结炉图
微波烧结炉图
热等静压烧结炉图
放电等离子烧结炉图
物理 化学变化
烧结后期还可能出现二次再结还可能发生固相的溶解与析出。
烧结驱动力
烧结的驱动力----一般为体系的表面能和缺陷能。烧
结实际上是体系表面能和缺陷能降低的过程。通常体
系能量的降低靠的是高温热能激活下的物质传递过程。
烧结原动力----烧结颈部与粉末颗粒其它部位之间存 在化学位差。
扩散机制将发生孔隙的孤立、球化及收缩。
氧化铝陶瓷典 型的不同烧结 阶段显微结构
粉末冶金的烧结技术
粉末冶金的烧结技术粉末冶金是一种通过将金属或非金属粉末在一定条件下,加工成具有一定形状和尺寸的零部件的方法。
烧结技术是粉末冶金中的关键步骤之一,它将粉末颗粒通过加热并施加压力使其质点之间结合得更加牢固,形成一体化的零部件。
本文将对粉末冶金的烧结技术进行深入探讨。
一、烧结技术的基本原理和过程烧结技术是将粉末颗粒通过加热至其熔点以下,但高于材料的再结晶温度,同时施加压力,使粉末颗粒发生结合,形成一体化的零部件。
其基本原理是利用了粉末颗粒与粉末颗粒之间的扩散作用和表面张力降低效应。
烧结过程中,颗粒间的间隙先得到迅速消除,然后颗粒之间产生再结晶,通过扩散使粒间结合更为牢固。
整个烧结过程可以分为初期活化期、再结晶期和液相期三个阶段。
初期活化期是指在烧结过程开始的阶段,颗粒发生活化并形成结合,此时烧结坯体变得更为致密。
再结晶期是指烧结坯体中增强再结晶的发生。
液相期是指在达到受结合的颗粒之间的最小距离后,材料产生液相,并通过液相扩散加快了颗粒间的结合。
在这个过程中,烧结坯体结构的致密度和强度会显著提高。
二、烧结技术的主要参数在进行粉末冶金的烧结过程中,有许多参数需要注意和控制,如温度、压力、时间和气氛等。
这些参数会对烧结过程和烧结产品的质量产生重要影响。
1. 温度:温度是烧结过程的关键参数之一。
合适的温度能够使粉末颗粒迅速熔结,并形成均匀的结构。
过高或过低的温度都会影响烧结效果和质量。
2. 压力:在烧结过程中,施加的压力可以使粉末颗粒更加紧密地结合在一起。
增加压力可以提高烧结物品的致密度和强度。
3. 时间:烧结时间是烧结过程中的一个重要参数。
适当的烧结时间可以使粉末颗粒充分结合并形成致密的结构。
时间过长或过短都会影响产品的质量。
4. 气氛:烧结过程中的气氛对烧结质量和产品性能有很大影响。
不同的气氛可以对不同材料产生不同的效果。
常用的烧结气氛有氢气、氮气、氧气和真空等。
三、烧结技术的应用和优点烧结技术在现代工业中有着广泛的应用,尤其是在金属材料和陶瓷材料的制备过程中。
烧结的原理
烧结的原理
烧结是一种粉末冶金工艺,通过在高温和压力下将金属或陶瓷粉末进行热处理,使其形成一种固体材料的过程。
其原理主要包括以下几个步骤:
1. 混合:首先将金属或陶瓷粉末按照一定比例混合在一起,以得到所需的配料。
这些粉末可以是不同种类的金属或陶瓷材料,也可以添加一些其他的添加剂,以改变材料的性能。
2. 压制:将混合好的粉末置于模具中,然后施加一定的压力。
这样可以使粉末颗粒之间发生变形和变稠,在压力作用下相互黏结在一起。
压制过程中,常常采用均匀的压力分布,以确保整个烧结体具有均匀的压力和密度。
3. 烧结:经过压制的粉末坯体被置于高温炉中进行烧结。
在高温下,粉末颗粒会发生扩散和结晶,使得颗粒之间相互溶解或结合。
同时,由于高温下的不同原子或分子的运动,形成了新的结晶相和晶界,使得颗粒逐渐合并,并改变了材料的物理和化学性质。
4. 冷却和处理:烧结后的坯体通过冷却,使得材料固化和成型。
通常还需要进行一些后续处理,如热处理、机械加工或表面涂层等,以进一步改善材料的性能和外观。
总的来说,烧结通过压制和高温处理的方式,使粉末颗粒逐渐结合,形成了一个整体材料。
其优点包括制造成本低、能耗低、
材料利用率高以及可以生产复杂形状的工件等。
因此,烧结在金属、陶瓷、粉末冶金等领域有着广泛的应用。
粉末烧结原理
粉末烧结原理粉末冶金是一种利用粉末作为原料,通过成型和烧结工艺制备金属、陶瓷和复合材料的工艺方法。
其中,粉末烧结是粉末冶金中最为重要的一环,它通过高温烧结使粉末颗粒互相结合,形成致密的块体材料。
本文将介绍粉末烧结的原理及其在工业生产中的应用。
首先,粉末烧结的原理是基于固相烧结的物理化学过程。
在烧结过程中,粉末颗粒之间发生扩散、溶解、再结晶等过程,最终形成致密的块体材料。
这一过程主要受温度、压力、时间等因素的影响。
在高温下,粉末颗粒表面发生扩散,原子间的结合能降低,颗粒之间出现结合,形成颗粒间的颈部,最终形成致密的结构。
其次,粉末烧结的原理还与粉末颗粒的形状、大小和分布有关。
通常情况下,形状不规则、尺寸均匀的粉末颗粒更有利于烧结过程中的颗粒间结合。
此外,粉末颗粒的分布均匀性也对烧结效果有着重要影响。
分布不均匀会导致烧结过程中局部温度过高或过低,影响颗粒间的结合质量。
再者,粉末烧结的原理还与烧结助剂的选择和添加有关。
烧结助剂可以改善粉末颗粒间的结合情况,促进烧结过程中的颗粒间扩散和溶解。
常用的烧结助剂有氧化铝、氧化锆等,它们能够形成液相,填充颗粒间的空隙,促进颗粒间的结合。
最后,粉末烧结在工业生产中有着广泛的应用。
在制备金属材料方面,粉末烧结可以制备具有特殊功能的工程材料,如高温合金、硬质合金等。
在制备陶瓷材料方面,粉末烧结可以制备高性能的陶瓷材料,如氧化铝、氮化硅等。
此外,粉末烧结还可以制备具有复合功能的粉末冶金材料,如金属陶瓷复合材料、金属基复合材料等。
总之,粉末烧结作为粉末冶金中的重要工艺环节,其原理是基于固相烧结的物理化学过程,受到温度、压力、时间等因素的影响。
在工业生产中,粉末烧结已经得到了广泛的应用,为制备高性能的材料提供了重要的技术手段。
粉末冶金烧结原理
粉末冶金烧结原理
粉末冶金烧结是一种常用的制备金属和陶瓷材料的工艺。
其原理基于粉末颗粒在高温下通过表面扩散和颗粒间的相互作用力而实现的固相结合。
首先,通过研磨和混合的方式将所需的金属或陶瓷粉末混合均匀。
混合的目的是使不同粉末颗粒在烧结过程中能够更好地接触和相互结合。
接下来,将混合后的粉末填充到模具中,并施加一定的压力。
压力的作用是使粉末颗粒之间产生一定的接触力,这样可以促进烧结过程中的颗粒扩散。
然后,将填充好的模具放入烧结炉中,进行高温处理。
在高温下,粉末颗粒表面会发生表面扩散,即颗粒表面的原子或离子会向颗粒内部扩散。
同时,由于高温下颗粒间的相互作用力增强,颗粒之间产生局部的结合。
经过一段时间的高温处理,粉末颗粒表面扩散和颗粒间的结合逐渐扩展到整个颗粒,形成了一个密实的整体。
这个过程称为固相烧结,通过这种方式,粉末的体积会明显减小。
最后,将烧结后的样品冷却并取出,进行进一步的加工和处理。
根据需要,可以对烧结样品进行后续的热处理、机加工等工艺步骤。
总之,粉末冶金烧结是一种通过高温和压力作用下,将粉末颗
粒固相结合的制备材料的方法。
通过控制烧结过程中的温度、压力和时间等参数,可以获得具有预期性能的金属和陶瓷材料。
- 1、下载文档前请自行甄别文档内容的完整性,平台不提供额外的编辑、内容补充、找答案等附加服务。
- 2、"仅部分预览"的文档,不可在线预览部分如存在完整性等问题,可反馈申请退款(可完整预览的文档不适用该条件!)。
- 3、如文档侵犯您的权益,请联系客服反馈,我们会尽快为您处理(人工客服工作时间:9:00-18:30)。
有限固溶系:Fe-C、Fe-Ni、Fe-Cu、W-Ni等
互不固溶系:Ag-W、Cu-W、Cu-C等
液相烧结
在烧结过程中出现液相的烧结。
包括:稳定液相(长存液相)烧结
不稳定液相(瞬时液相)烧结
二、烧结理论研究的目的、范畴和方法
研究目的:研究粉末压坯在烧结过程中微观结构的演化
物质蒸发的角度
3.蒸气压差
曲面与平面的饱和蒸气压之差
P P0 / KTr
1 1 1 r x
吉布斯-凯尔文方程
x
1 1 r
P 0 / KT 颈 P
对于球表面,1/r=2/a (a为球半径)
P 0 2 / KTa 球 P
颗粒表面(凸面)与烧结颈表面(凹面)之间存在大的蒸气压 差,导致物质向烧结颈迁移
烧 结 的 重 要 性
4)纳米块体材料的获得依 赖烧结过程的控制
(三) 烧结的分类
粉末体烧结类型 不施加外压力
施加外压力
固相烧结 单相粉末
多相粉末
液相烧结
长存液相 瞬时液相
热压 热锻
热等静压
反应烧结
活化烧结
超固相线烧结 液相热压 反应热压 反应热等静压
强化烧结
按烧结过程有无外加压力
●无压烧结 (Pressureless sintering) 包括:固相烧结、液相烧结等 ●加压烧结(有压烧结)
烧结颈长大
3.封闭孔隙球化和缩小阶段 当烧结体密度达到90%以后,• 多数孔隙被完全分隔,闭 孔数量大的增加,孔隙形状趋近球形并不断缩小。在这个 阶段,整个烧结体仍可缓慢收缩,但主要是靠小孔的消失 和孔隙数量的减少来实现。这一阶段可以延续很长时间, 但是仍残留少量的隔离小孔隙不能消除。也就是一般不能 达到完全致密。
宏观迁移:V—V
● 体积扩散(volume or lattice diffusion):借助于空位运 动,原子等向颈部迁移。 ● 粘性流动(viscous flow):非晶材料,在剪切应力作用下, 产生粘性流动,物质向颈部迁移。 ● 塑性流动(plastic flow):烧结温度接近物质熔点,当颈部 的拉伸应力大于物质的屈服强度时,发生塑性变形,导 致物质向颈部迁移。 ● 晶界扩散(grain boundary diffusion):晶界为快速扩散通 道。原子沿晶界向颈部迁移。
§3-2 烧结过程的热力学基础
一、烧结的基本过程
原始接触
烧结颈长大
孔隙球化
粉末等温烧结过程的三个阶段
等温烧结过程按时间大致可分为三个界限不十分明显的阶段: 1.粘结阶段 烧结初期,颗粒间的原始接触点或面转变成晶体结合,• 即 通过成核,结晶长大等原子过程形成烧结颈。在这一阶段 中,颗粒内的晶粒不发生变化,颗粒外形也基本未变,整 个烧结不发生收缩,密度增加也极微,但是烧结体的强度 和导电性由于颗粒结合面增大而有明显增加。
对烧结定义的理解-3:
● 低于主要组分熔点的温度 * 固相烧结 — 烧结温度低于所有组分的熔点 * 液相烧结 — 烧结温度低于主要组分的熔点, 但可能高于次要组分的熔点: WC-Co合金, W-Cu-Ni合金
(二) 烧结的重要性
1)粉末冶金生产中不可缺少的基本工序之一 (磁粉芯和粘结磁性材料例外) 2)对PM制品的性能有决定的影响(烧结废品很难补救, 如铁基部件的脱渗碳和严重的烧结变形) 3)烧结消耗是构成粉末冶金产品成本的重要组成部分 (设备、高温、长时间、保护气氛)。
Sf -振动熵 ;Ef’-空位形成能 对于完整晶粒(无应力) 设受应力为σ时
Cvo exp(S f / K ) exp(E f / KT )
-空位体积
E f E f '
1
Cv Cvo exp( / KT ) exp( / KT ) 1 / KT
§3
烧结
Sintering
第一节 概述
一、基本概念 (一) 烧结的定义
● 简单描述:烧结(Sintering)指粉末或粉末压坯在适当温 度、气氛下受热,借助于原子迁移实现颗粒间联结的过程。 ● 定义:粉末或粉末压坯在一定的气氛中,在低于其主要 成分熔点的温度下加热而获得具有一定组织和性能的材料
或制品的过程。
原始接触
粉末等温烧结过程的三个阶段
等温烧结过程按时间大致可分为三个界限不十分明显的阶段: 2.烧结颈长大阶段 原子向颗粒结合面的大量迁移使烧结颈扩大,颗粒间距离 缩小,形成连续的孔隙网络;同时,由于晶粒长大,晶界 越过孔隙移动,而被晶界扫过的地方,孔隙大量消失。烧 结体体积收缩,密度和强度明显增加。
施加外压力 (Applied pressure or pressure-assisted sintering) ,热等静压 HIP、热压HP等
按烧结过程有无液相出现
固相烧结:
单元系固相烧结:单相(纯金属、化合物、固溶体)粉末 的烧结:烧结过程无化学反应、无新相形成、无物质聚集
状态的改变。 多元系固相烧结: 两种或两种以上组元粉末的烧结过程,包括反应烧结等。
烧结温度,保温温度,低于粉末或粉末压坯的基体组元熔 点的温度,大约是0.7~0.• 8T(T:绝对熔点)。
对烧结定义的理解-1:
● 粉末也可以烧结(不一定要成形)
松装烧结,制造过滤材料(不锈钢,青铜,黄铜,钛等)
和催化材料(铁,镍,铂等)等。
对烧结定义的理解-2:
● 烧结的目的 依靠热激活作用,使原子发生迁移,粉末颗粒形 成冶金结合。Mechanical interlocking or physical bonging → Metallurgical bonding → 改善烧结体组织 → 提高烧结体强度 等性能
2 ( x) 2 x x 2
F
( ) x
1
1
由于烧结颈半径x远大于曲率半径
x>>
烧结动力是表面张力造成的一种机械力,它垂直作用于烧结颈曲面上, 使烧结颈向外长大。 假如颗粒半径2m x=0.2μ ρ=10-8~10-9m 则σ=107 N/m2
2) 多元系液相烧结:烧结温度超过系统中低熔成分的熔点,在 烧结过程中出现液相。
由于低熔成分的液相同难熔固相之间互相溶解或形成合金的 性质不同,液相可能中途消失或始终存在于全过程,根据液 相在烧结过程存在时间的长短,液相烧结又可分为:
烧结过程始终存在液相的系统,如WC-Co W-Ni-Fe等;
(microstructure evolution)和物质传递规律,包括 ——
孔隙数量或体积的演化—致密化
晶体尺寸的演化—晶粒的形成与长大
(纳米金属粉末和硬质合金)
孔隙形状的演化—孔隙的连通与封闭
孔隙尺寸及其分布的演化—孔隙粗化、收缩和分布
研究范畴: 烧结过程的驱动力 烧结热力学,即解决Why的问题 物质迁移方式 烧结动力学—烧结机构,即解决How的问题, 即物质迁移方式和迁移速度 上述理论在典型烧结体系中的应用
研究方法:
烧结几何学 烧结物理学 烧结化学 烧结模型:两球模型、球-板模型 物质迁移机构:扩散、流动 组元间的反应(溶解、形成化合物) 及与气氛间的反应
计算机模拟
借助于建立物理、几何或化学模型, 进行烧结过程的计算机模拟(蒙特-卡 洛模拟)
粉末烧结过程模拟
多相粉末烧结
液相烧结
三、烧结技术的发展
二、烧结的热力学问题
粉末有自动粘结或成团的倾向 粉末烧结使系统自由能减少的过程 烧结系统自由能降低是烧结过程的原动力。烧结 后系统自由能降低包括下述几个方面: (1)由于颗粒结合面(烧结颈)的增大和颗粒表 面平直化,粉末体的总比表面积和总表面自由能 减小; (2)烧结体内孔隙的总体积和总表面积减小; (3)粉末颗粒内晶格畸变部分消除。
在形成孔隙中气体阻止孔隙收缩和烧结颈长大,有效力: 开孔: Pv=1atm =105 N/m2 闭孔: Ps Pv
Ps Pv
2 r
r-孔隙半径 孔隙收缩使Pv增大,达到一个平衡值 ∴仅延长烧结时间不能消除孔隙
物质扩散的角度
2. 空位浓度梯度 应力使空位浓度发生变化
Cv exp(S f / K ) exp(E f ' / KT )
烧结后期液相消失的系统,如Fe-Ni-Al, Cu-Sn等;
液相烧结特例:熔浸,多孔骨架的固相烧结和低熔金属浸透 骨架后的液相烧结同时存在,如W-Ag W-Cu Fe-Cu。
4.烧结理论所研究的问题 (1)烧结为什么会发生? 烧结的原动力或热力学问题 (2)烧结是怎样进行的? 烧结的机构和动力学问题
Cv Cvo (1 / KT ) Cv Cv Cvo Cvo / KT Cvo / KT
o 2 空位浓度梯度: Cv / Cv / KT
过剩空位浓度梯度引起烧结颈表面下微小区域内的空位向球体扩 散,原子朝相反方向迁移,烧结颈长大
粉末烧结的驱动力来自系统的过剩自由能的降低, 其中表面能的降低在烧结过程中处于主导地位。
三、烧结的原动力
表面张力的角度 1.表面张力 库钦斯基两球模型 取ABCD使ρx形成的张角为θ
Fx x θ Fx x A
B
Fρ ρ θ ρ
C
D Fρ
Fx AD BC
F AB CD
-表面张力
AD sin
很小 sin
Fx
AB x sin
垂直作用于ABCD上的合力
F x
F 2( Fx sin F sin ) 2 ( x) 2 2
ABCD的面积为 xθ×ρθ,作用在上面的应力为