汽车零件供应商质量要求页
汽车配件质量保证书

汽车配件质量保证书兹有(供应商名称)向(购买方名称)供应以下汽车配件,为明确双方的质量责任,特订立本质量保证书。
一、产品质量承诺1. 供应商保证所提供的汽车配件符合国家相关质量标准,并满足购买方提出的技术要求和质量指标。
2. 供应商应确保所供配件的制造工艺精良,材料选用优质合格,且无任何缺陷和瑕疵。
二、质量保证期限1. 本质量保证书自供应之日起生效,期限为(具体时间,如一年、两年等)。
2. 在保证期限内,如配件出现质量问题,供应商应负责无偿更换或修理。
三、售后服务1. 供应商应提供完善的售后服务,包括技术咨询、维修保养等。
2. 供应商应定期对已供应的配件进行质量跟踪和回访,确保客户满意。
四、违约责任1. 如供应商未能履行上述质量承诺,购买方有权要求供应商承担违约责任,包括但不限于赔偿损失、退货退款等。
2. 如因质量问题导致购买方车辆损坏或引发交通事故等,供应商应承担相应的法律责任和经济赔偿责任。
五、其他1. 本质量保证书一式两份,供应商和购买方各执一份,具有同等法律效力。
2. 本质量保证书未尽事宜,可由双方另行协商解决。
供应商(盖章):____________________法定代表人授权代表签字:_____________日期:__________________________购买方(盖章):____________________法定代表人授权代表签字:_____________日期:__________________________汽车配件质量保证书(1)兹有(供应商名称)向(购买方名称)供应以下汽车配件,为明确双方的质量责任,特订立本质量保证书。
一、产品质量承诺1. 供应商保证所提供的汽车配件符合国家相关质量标准,并满足购买方提出的技术要求和质量指标。
2. 供应商应确保所供配件的制造工艺精良,材料选用优质合格,保证配件在正常使用情况下能够长期稳定工作。
二、质量保证期限1. 本质量保证书自供应之日起生效,为期(具体时间,如一年)。
汽车配件质量管理规定
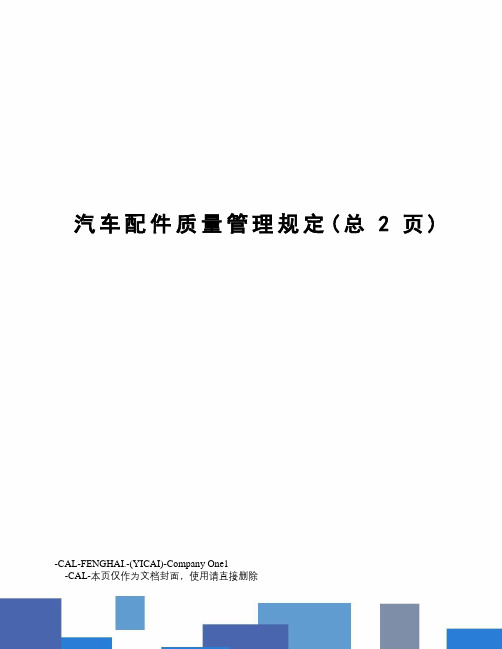
汽车配件质量管理规定(总2页) -CAL-FENGHAI.-(YICAI)-Company One1-CAL-本页仅作为文档封面,使用请直接删除汽车配件质量管理规定为加强汽车配件质量管理,保证车辆维修质量,确保车辆安全运行。
根据公司《质量管理规定》,特制定本规定。
一、汽车配件采购程序1、供货方的选择:对具有合法经营资质的供货商进行公开招标,根据资质、经营实力和配件质量等,同类配件确定2-3家供货方进行长期合作;汽车安全件,如刹车片、方向机等,要同配件生产厂建立直接关系,避免因中间商造成的质量问题。
2、汽车配件的质量认可:供货方必须出具合法的配件检验报告、抽检报告和产品合格证;同时,列入国家强制性认证目录的配件产品,还必须提供强制性产品认证证书,产品必须具有中国强制性产品认证标志。
3、质量保证要求:供货方在满足上述两条的基础上,必须满足如下质量要求。
(1)保证配件质量。
所提供的配件必须100%为合格品,符合国家及有关标准,在国家规定质量保证期内发生质量问题,应无条件更换或退赔,所造成的一切后果由供货方负责。
(2)价格合理。
所提供的配件价格应低于市场价,如发现有以次充好、以副厂配件充正厂配件等质量问题,造成的一切损失,由供货方负责。
(3)配件送货及时。
常用配件和急用配件应在三十分钟内送到,需预订的配件应在允诺的时间内及时送到。
因配件送货不及时造成的一切的损失由供货方负责。
(4)供货的合格率(批合格率)为100%。
所提供的配件无论从型号、规格、数量都应与需方所需采购的配件相符合,配件有包装的应提供正规的包装。
供货方必须按照以上四方面要求向需方供货,如供货方不能满足需方这四方面内容要求中的任何一点,需方将取消其供货资格。
4、鉴定供货协议:满足上述条件的供货方提供营业执照、税务登记证、组织机构代码证和开户行等信息,证实合法后,鉴定供货协议。
二、汽车配件质量验收1、到货的汽车配件与需求计划单型号、规格等信息相符。
汽车零件生产中的供应商质量管理与评估

汽车零件生产中的供应商质量管理与评估在汽车制造业中,供应商质量管理与评估是确保汽车零件生产过程中的质量与可靠性的关键环节。
供应商质量管理涉及到从供应商的选择、培训、审核到日常质量监督与持续改进的全过程。
本文将探讨汽车零件生产中的供应商质量管理与评估的重要性,以及如何建立有效的供应商质量管理体系。
一、供应商质量管理的重要性在汽车制造业中,供应商质量管理的重要性不言而喻。
首先,供应商的产品质量直接影响到汽车的整体质量和可靠性。
若供应商提供的零件存在质量问题,会导致汽车在使用过程中出现故障,给消费者带来不良的用车体验,甚至会危及乘车人员的安全。
其次,建立良好的供应商质量管理体系有助于减少生产中的缺陷率和产品退市率,提高汽车生产效率和竞争力。
最后,供应商质量管理还能够降低生产成本,提高利润率,为企业带来经济效益。
二、供应商质量管理的关键要素1. 供应商选择与审核供应商选择是供应商质量管理的第一步。
汽车制造商需要对潜在供应商进行评估,选择那些有能力提供高质量零部件的供应商。
评估供应商时,可以考虑供应商的生产能力、技术实力、质量控制体系等方面的指标。
审核供应商时,可以通过现场考察、质量管理体系评估以及样品检测等方式,验证供应商的能力以及其零部件的质量。
2. 合同与质量要求建立明确的合同和质量要求对供应商质量管理至关重要。
在合同中,汽车制造商应明确规定供应商需遵循的质量标准、交付时间、数量要求等,以确保供应商提供的零部件符合预期质量水平。
此外,还可以在合同中约定供应商的退货政策、索赔条款等,以应对供应商提供的零部件存在质量问题的情况。
3. 供应商培训与支持为了确保供应商能够按照质量要求进行生产,汽车制造商应提供必要的培训和技术支持。
培训内容可以包括质量管理知识的传授、生产工艺流程的培训以及质量检验方法的教育等。
通过培训,供应商可以提高自身的技术能力和质量意识,提高零部件的质量水平。
4. 质量监督与持续改进汽车制造商需要对供应商的生产过程进行质量监督,确保供应商的质量控制体系得以有效实施。
SGM供应商质量要求

2006 年 5 月 23 日
2006 年 5 月 23 日
Page 1 of 30
仅限 SGM 及供应商内部使用,不能擅自复制、转发!
上海通用汽车对供应商质量要求的规定
(2006 年 5 月版)
主要修订记录
2004 年 10 月,第一版制订
2005 年 6 月主要修订内容: 1. SGM 供应商质量声明参考 GM2005 年 3 月版本更新,并增补 SGM 对
3. General Motors Procedures and Reference Documents: 通用汽车的程序和参考文件:
• Suppliers are to adhere to the requirements contained in the following documents:
ITEZ1401H – KCDS Manual for ITDC Application ITEZ1401H– ITDC 应用 KCDS 手册
GP-5 Supplier Quality Processes and Measurements Procedure. GM-1746 GP-5 供应商质量过程和测量程 序 GM-1746
painting or other finishing services directly to Shanghai General Motors must be certified to ISO/TS 16949 or QS-9000 and have a current certificate available demonstrating compliance to GM supplements. All suppliers should migrate to ISO/TS 16949 at the expiration of their current QS9000 certificate but before December 14, 2006.. 所有向通用直接提供a)生产材料,b)生产或服务件,或c)热处理、涂镀、油漆或其他最终服务的供应 商必须通过ISO/TS 16949 或QS-9000 标准的认证, 并且取得相应证书。在现行的QS9000 证书 2006 年 12 月 14 日到期之前,所有供应商应该通过ISO/TS16949 认证。
汽车零件供应商质量要求页
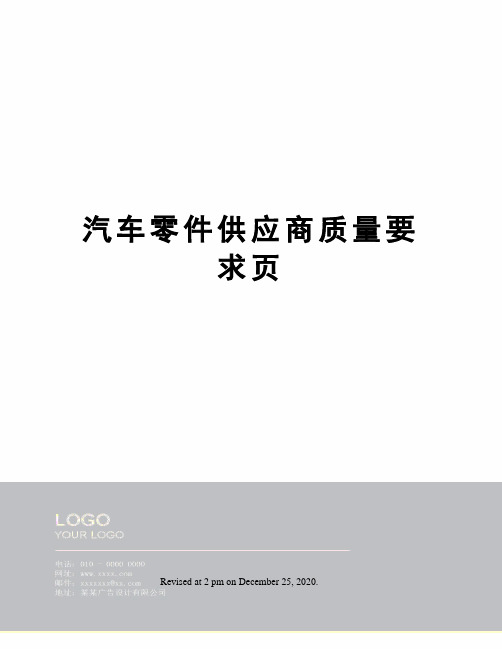
汽车零件供应商质量要求页Revised at 2 pm on December 25, 2020.1.供应商质量基本要求:•卖方同意参加买方的供应商质量和开发项目并满足,随时间变化而修改的、买方提出的所有质量要求和程序,包括在质量体系要求QS-9000中提出的适用于卖方的要求。
另外,买方具有在合理的时间进入卖方的设施,在本合同所涵盖之下,对买方的设施、产品、材料及买方的任何财产进行检查。
买方对产品的检查,不论是在生产制造过程之中,还是在交付之前或交付之后的合理时间之内,均不构成对任何在制品或产成品的接受。
♦所有供应商均应向SGMW提供零缺陷的产品。
零件必须满足所有工程规范和功能要求,并能够满足设计的意图。
•在初始及随后的报价中应包括用于检测错误发生(防错装置等)和防止缺陷流出到顾客的成本。
在以后实施的控制而发生的成本由供应商负责。
2.ISO/TS 16949 或 QS-9000 –质量体系要求•直接向SGMW提供以下产品的供应商: a) 生产材料, b) 生产或服务零件, 或 c) 热处理, 电镀, 喷漆或其它表面处理,必须获得 ISO/TS 16949 或 QS-9000的认证并且具有表明符合通用附加要求的证明. 所有供应商在2006年12月4日之前在其目前QS9000有效期满时应过渡到ISO/TS 16949。
•没有获得ISO/TS 16949 或 QS-9000认证的供应商, 或那些正在建设或采购用于生产制造报价产品设施的供应商,必须在其报价中包含认证取得计划以备下一步考虑。
3.通用公司文件及参考文件•供应商应遵循下述文件的要求:4.质量策划要求:•APQP:供应商必须使用遵循通用公司APQP项目计划的先期产品质量策划程序(GM1927-1) ,以保证生产准备状态能够使零件100%满足产品的规范要求。
•操作者培训: 培训计划必须包括新操作者及从事新岗位的现有操作者。
培训状态应该在制造现场目视化获得。
汽车配件质量制度范本
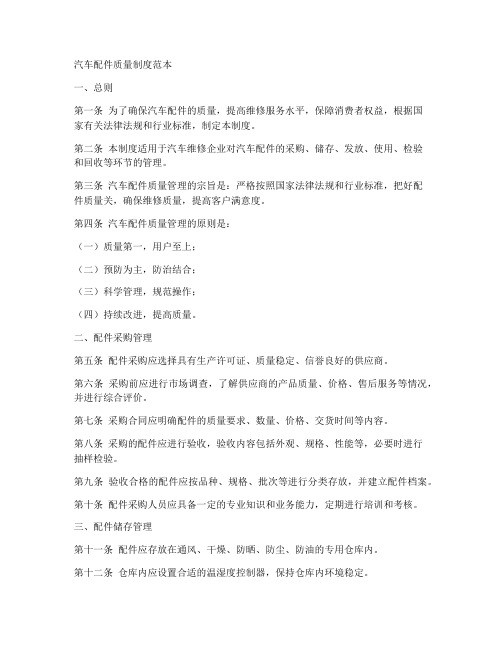
汽车配件质量制度范本一、总则第一条为了确保汽车配件的质量,提高维修服务水平,保障消费者权益,根据国家有关法律法规和行业标准,制定本制度。
第二条本制度适用于汽车维修企业对汽车配件的采购、储存、发放、使用、检验和回收等环节的管理。
第三条汽车配件质量管理的宗旨是:严格按照国家法律法规和行业标准,把好配件质量关,确保维修质量,提高客户满意度。
第四条汽车配件质量管理的原则是:(一)质量第一,用户至上;(二)预防为主,防治结合;(三)科学管理,规范操作;(四)持续改进,提高质量。
二、配件采购管理第五条配件采购应选择具有生产许可证、质量稳定、信誉良好的供应商。
第六条采购前应进行市场调查,了解供应商的产品质量、价格、售后服务等情况,并进行综合评价。
第七条采购合同应明确配件的质量要求、数量、价格、交货时间等内容。
第八条采购的配件应进行验收,验收内容包括外观、规格、性能等,必要时进行抽样检验。
第九条验收合格的配件应按品种、规格、批次等进行分类存放,并建立配件档案。
第十条配件采购人员应具备一定的专业知识和业务能力,定期进行培训和考核。
三、配件储存管理第十一条配件应存放在通风、干燥、防晒、防尘、防油的专用仓库内。
第十二条仓库内应设置合适的温湿度控制器,保持仓库内环境稳定。
第十三条配件应按品种、规格、批次等分类摆放,标识清晰,方便查找。
第十四条定期对仓库进行清理、整理,确保仓库内配件整齐、干净、安全。
第十五条仓库管理员应做好配件的出入库记录,确保账物一致。
四、配件发放管理第十六条配件发放应根据维修作业单据进行,确保配件与车辆维修项目相符。
第十七条发放配件时应进行核对,确认配件的品种、规格、数量等无误。
第十八条发放的配件应附有配件清单,清单上应注明配件的名称、规格、数量、发放日期等信息。
第十九条配件发放人员应具备一定的专业知识和业务能力,定期进行培训和考核。
五、配件使用管理第二十条维修人员应按照维修手册和操作规程使用配件。
汽车零部件质量验收标准最新版本

汽车零部件质量验收标准最新版本1. 引言本文档旨在确定汽车零部件的质量验收标准,以确保所采购和使用的零部件符合相关的质量要求。
本标准适用于所有供应商和制造商。
2. 标准概述本标准涵盖了以下方面的质量验收要求:- 材料和零部件的规范要求- 制造过程的质量控制要求- 零部件的性能指标和测试要求- 零部件的尺寸和外观要求- 包装、标识和交付要求3. 材料和零部件的规范要求供应商必须根据汽车制造商的要求提供材料和零部件的规范。
规范应包括材料的化学成分、物理性质、机械性能等详细信息,以及零部件的几何尺寸和外观要求。
4. 制造过程的质量控制要求供应商必须实施有效的质量控制措施,以确保零部件的制造过程符合要求。
质量控制措施可以包括:- 制定和实施质量管理体系- 使用合适的工艺和设备- 进行过程控制和监测- 对制造过程进行记录和分析5. 零部件的性能指标和测试要求零部件必须符合特定的性能指标和测试要求。
供应商必须提供相关的测试数据和证明,以确认零部件的性能符合规定标准。
6. 零部件的尺寸和外观要求零部件的尺寸和外观必须符合规定要求。
供应商必须使用合适的测量工具和方法对零部件的尺寸和外观进行检测和测试。
7. 包装、标识和交付要求供应商必须确保零部件在包装、标识和交付过程中符合相关要求。
包装应能够保护零部件免受损坏,并提供正确的标识信息。
交付的零部件应按时到达目的地,并符合交付要求。
8. 结论该文档为汽车零部件质量验收标准的最新版本,供供应商和制造商参考和遵循。
通过严格执行这些标准,能够确保所采购和使用的零部件的质量符合要求,从而提高整体产品质量和顾客满意度。
以上是《汽车零部件质量验收标准最新版本》的内容概述。
如有任何疑问或需要进一步细节,请与相关部门联系。
汽车零部件供应质量保证措施

汽车零部件供应质量保证措施1. 概述本文档旨在提供关于汽车零部件供应质量保证措施的详细信息。
汽车零部件供应链是确保车辆质量和安全的关键环节,因此有必要采取一系列措施来保证供应质量。
2. 零部件供应商资质筛选为确保零部件的质量和可靠性,必须对供应商进行严格的资质筛选。
供应商应具备以下条件:- 有合法经营资质和相关认证;- 有丰富的生产经验和零部件质量控制能力;- 有稳定的供应能力和充足的库存管理措施;- 有良好的商业信誉和客户反馈。
3. 高质量标准与规范为确保提供高质量的零部件,供应商应符合一系列的标准与规范,包括但不限于:- 合乎相关法律法规和行业标准的生产流程;- 严格的质量控制和检测流程,包括原材料的验收、生产过程的监控和最终产品的检验;- 控制零部件缺陷和不合格品数量的有效措施,如六西格玛和质量管理工具的应用;- 保证零部件的尺寸、性能、可靠性和耐久性符合设计要求。
4. 监督与检查为确保供应商的质量保证措施得到有效执行,需要进行监督与检查的工作。
以下是一些常用的监督与检查方式:- 定期的供应商评估和审核,包括对供应商的工厂、质量管理体系和质量记录的检查;- 随机抽查样品进行质量检验,检测零部件的物理、化学和功能性能;- 对供应商的不良记录进行追踪和反馈,并要求供应商采取改进措施。
5. 应急计划与质量纠正措施即使采取了一系列的质量保证措施,仍然可能发生零部件质量问题。
为了应对紧急情况并确保质量问题得到及时控制和纠正,应制定应急计划与质量纠正措施,包括:- 建立质量问题报告和处理流程,确保及时上报和跟进质量问题;- 确保零部件质量问题的调查和分析,找出问题原因并采取纠正措施;- 及时通知相关车辆制造商和客户,展开召回或零部件更换工作;- 监测和评估纠正措施的有效性,以防止类似问题再次发生。
6. 培训与合作供应商和车辆制造商之间的合作与沟通至关重要。
以下是一些应考虑的合作与培训措施:- 提供供应商培训,提升其对质量保障的理解和能力;- 定期的沟通与会议,讨论和解决质量问题以及改进措施;- 与供应商共享车辆制造商对质量要求的更新和变化。
- 1、下载文档前请自行甄别文档内容的完整性,平台不提供额外的编辑、内容补充、找答案等附加服务。
- 2、"仅部分预览"的文档,不可在线预览部分如存在完整性等问题,可反馈申请退款(可完整预览的文档不适用该条件!)。
- 3、如文档侵犯您的权益,请联系客服反馈,我们会尽快为您处理(人工客服工作时间:9:00-18:30)。
1.供应商质量基本要求:•卖方同意参加买方的供应商质量和开发项目并满足,随时间变化而修改的、买方提出的所有质量要求和程序,包括在质量体系要求QS-9000中提出的适用于卖方的要求。
另外,买方具有在合理的时间进入卖方的设施,在本合同所涵盖之下,对买方的设施、产品、材料及买方的任何财产进行检查。
买方对产品的检查,不论是在生产制造过程之中,还是在交付之前或交付之后的合理时间之内,均不构成对任何在制品或产成品的接受。
♦所有供应商均应向SGMW提供零缺陷的产品。
零件必须满足所有工程规范和功能要求,并能够满足设计的意图。
•在初始及随后的报价中应包括用于检测错误发生(防错装置等)和防止缺陷流出到顾客的成本。
在以后实施的控制而发生的成本由供应商负责。
2.ISO/TS 16949 或QS-9000 –质量体系要求•直接向SGMW提供以下产品的供应商:a) 生产材料, b) 生产或服务零件, 或c) 热处理, 电镀, 喷漆或其它表面处理,必须获得ISO/TS 16949 或QS-9000的认证并且具有表明符合通用附加要求的证明. 所有供应商在2006年12月4日之前在其目前QS9000有效期满时应过渡到ISO/TS 16949。
•没有获得ISO/TS 16949 或QS-9000认证的供应商, 或那些正在建设或采购用于生产制造报价产品设施的供应商,必须在其报价中包含认证取得计划以备下一步考虑。
3.通用公司文件及参考文件•供应商应遵循下述文件的要求:4.质量策划要求:•APQP:供应商必须使用遵循通用公司APQP项目计划的先期产品质量策划程序(GM1927-1) ,以保证生产准备状态能够使零件100%满足产品的规范要求。
•操作者培训: 培训计划必须包括新操作者及从事新岗位的现有操作者。
培训状态应该在制造现场目视化获得。
•防错: 供应商应该实施防错计划用来控制材料、过程及所有供给SGMW的产品。
供应商应该实施防错技术来保证在缺陷产生之前发现并纠正缺陷(例如:在即使有错误发生的情况下防止制造出有缺陷的产品)。
防错的实施通过“已防错%”来衡量。
已防错%是指在制造过程中已经实施防错的总计工位的百分比。
供应商的防错水平必须达到不可能向SGMW发运有缺陷的产品。
•可追溯性: 应按照相关要求制定可追溯性方案。
可追溯性方案应包括生产日期代码和批次控制。
应该在APQP过程中确定可追溯性项目。
•顾客使用特性的验证:顾客使用特性(如装配、形状、功能、配合面等)应该体现在PFMEA、过程控制计划、分层次检查以及防错之中。
其它需要检查的项目应该在APQP过程中确认。
对这些特性必须100%进行验证。
•量检具要求:♦供应商须按照零件在整车上的位置进行量检具设计,除非供应商质量工程师批准其它情形。
♦所有顾客监控APQP的零件,量检具在制造之前,其设计须由供应商质量工程师或顾客方量检具批准代表进行批准(相应地区不同要求,请与有关SQE取得联系)。
量检具的设计应按照批准的GD&T 基准方案,同时,量检具必须能够在尺寸/形状上评价零件。
♦供应商对次基准KPC和那些在装配线或其随后工序需要安装零件的、并对最终整车规范产生影响的(如内饰板、格删、杂物箱盖等)地方需使用手动夹具。
♦供应商应能够对总成产品进行检查。
分供方也应能够对零件进行检查。
任何夹具均应能够证明与其相关零件和附件相匹配。
♦具有适当的功能性测试和最终检验来保证产品在实际整车状态下能够达到设计要求。
♦供应商应保证量检具的采购能够及时进行以满足重要的项目进度(如首件制造、GP11、功能评估和PPAP)。
供应商至少应对非正式工装和正式生产工装的首件检查具有CMM 测量夹具。
5.质量控制要求•分层次检查:应具有书面的、最低频次为每班一次的分层次检查计划。
所有不符合均应立即处理并且纠正措施应予以记录。
检查计划应包括管理的多个层次。
现场主管应负责保证与书面计划的符合性。
•遏制措施:所有不符合及问题材料必须受控,并且必须清楚的确定控制方法。
应实施目视化控制。
所有不合格材料必须隔离并标识。
在项目投放阶段应实行GP12控制计划。
在SGMW提出时可能要求采取另外的不同层次的预防性的遏制措施。
一旦问题发生,要求供应商来实施有效的和立即的遏制措施,并满足GP5的全部要求,另外可能要实行发货控制。
•质量表现:每个供应商的高级管理层均应承诺来保持并持续不断的改进质量。
SGMW供应商质量开发部门将对供应商质量数据如PPM, PRRs, 一级和二级发货控制, 总装厂重大质量事故, 以及QS-9000, ISO/TS16949 和ISO14001 认证状态进行监控. 供应商应对其质量表现通过定期的质量信息报告进行监控。
•生产质量:♦要求所有供应商具有有效的生产制造流程和程序来保证零缺陷的零件持续不断的交付给SGMW生产线。
•现有产品改进流程(CPIP):供应商应积极参与SGMW有关现有产品所发现问题的及时解决。
供应商在被要求时,应提供适当的纠正措施记录和项目进度报告。
6.问题解决要求:•要求供应商证明其通过使用高级问题解决技术来解决复杂问题的能力。
7.现场支持要求:•在试生产和投放阶段提供现场支持: 在SGMW SQE提出要求时, 供应商应在试生产和生产投放阶段提供现场支持技术人员。
•所有班次的紧急联系方法: 供应商应指定具体的供应商代表来支持SGMW工厂每个班次的生产。
供应商指定的代表应至少负责以下事宜:♦实施立即控制方法来控制缺陷产品并确认缺陷产品不被发运到SGMW工厂。
♦同意SGMW现场SQA有关返工和挑选的要求。
♦协调并提供从事零件返工和挑选所需的资源。
♦提供与质量问题有关的返修所需的零件。
♦提供有关缺陷产品在提供给SGMW工厂路途中的明确的信息(如何识别缺陷,如何处理的意见)。
♦协调经过验证的合格零件的特殊交付。
•质量数据: 在SGMW要求时,供应商必须提供与质量有关的数据(如:历史性的检验数据、FTQ一次下线合格率、不合格数据等)。
这些数据可能在SGMW被用来制定趋势图以及对质量问题进行根本原因分析。
8.一级供应商责任(包括复杂系统/分总成的供应商)•一级供应商负责对总成的所有部件,包括直接购买零件实施AIAG和GM的相关要求,除非SGMW供应商质量开发部门另有说明。
SGMW可以决定在适当时候指定SQE来和一级供应商的SQE一起工作,以加强相互间的沟通、学习并就相关问题达成一致。
9.动力总成供应商:•动力总成供应商必须遵循供应商质量要求的动力总成附加要求。
10.系统和程序的获得:•供应商应能够从因特网访问通用汽车公司网站,从该网站可以获得供应商质量相关程序和文件。
•供应商可以从相应的SGMW SQE处获得供应商质量相关程序和文件。
供应商质量要求动力总成附加要求1. 要求对关键产品特性(KPCs) 和产品质量特性(PQCs)。
参见GM 1805 和AIAG PPAP 手册,第1.2.2.9条如果在产品/过程开发阶段认为有困难满足上述能力要求,请立即与SQE取得沟通,然后制定计划来保证符合和/或取得与上述要求相背离的书面批准。
2. Process Failure Mode and Effects Analysis (PFMEA)•一般情况下, RPNs 应小于等于40。
RPN超过40的过程必须获得SGMW SQE的书面批准。
•应使用GM 动力总成PFMEA 评定表(参见APQP 手册GM1927-28)。
3. 清洁度要求: 在制定PFMEA时应考虑零件和过程的清洁度。
应该按照RPN的分值来采取适当的措施。
供应商质量要求SGMW附加要求1. 供应商应充分理解本质量要求,签署并在报价书中返回本质量要求的理解确认单(第6页)。
2. 供应商应在其报价书中提供项目开发计划(附表1),并应至少包括SGMW提出的主要时间节点;如若供应商计划新建厂房、设施、购买机器和设备,则需要供应商在报价时提交签署的新设施计划和机器设备采购计划;如若供应商为未获得QS9000或TS16949的认证,则需要供应商在报价时提交签署的QS/TS质量体系认证计划;如若供应商接受过GM 相关SQE的供应商质量体系评审,则需要供应商在报价时提交供应商质量体系评审中发现的问题的整改措施实施状态报告。
以上信息均做为SGMW采购决定时的参考。
3. 供应商在被正式通知成为SGMW供应商以后,需在APQP启动会上向SGMW提供详细的、按照SGMW规定的格式的项目进度计划(附表1)、APQP进度计划(附表2),包括详细工装开发计划(含设施/设备计划),并在APQP启动会结束后的1周内最终确认该计划并连同供应商内部联系人清单(附表3)一起向SGMW SQE提交。
4. 供应商,需在APQP启动会结束后的1个月内,组织内部的有关部门对SGMW的产品技术规范进行充分的分析和理解,并按要求向SGMW SQE提交TSA技术规范分析表(附表4-9)。
其中,供应商应按照通用汽车公司KCDS手册要求对零件的产品特性进行分析并确认KPC。
零件评估计划说明了在正式生产之前为满足工程标准和检验标准,供应商对零件的试验和验证计划,该计划时间应从SGMW工程图纸发放到开始生产的后三个月时间,并且对SGMW不同阶段的制造活动都有侧重点(如样车,非销售车,可销售车的制造等等)。
计划应提出用于针对不同质量特性 (尺寸,外观,材料,性能和功能)的检验而要求的最低零件数量。
5. 供应商应分别为非工装样件、工装样件及PPAP的生产完成零件的评估计划(表8)、测量计划(表9),提交SGMW SQE并在生产的至少2周之前获得批准;由顾客监控的APQP,供应商需在工装样件和PPAP生产的至少2周之前完成生产场地平面布置图(表10)、过程流程图(表11)、FMEA(表12)、过程控制计划(表13)的更新以及测量系统分析计划(表14)、过程能力分析计划(表15)的制定并获得SGMW SQE的批准。
6. SGMW供应商应对为SGMW提供的所有零件及总成的质量负全部责任。
包括那些由供应商生产的零件及所有其二级至N级供应商生产的零件。
所有采购产品必须具有入厂检验和/或质量控制手段,除非得到SGMW供应商质量工程师的同意。
对关键的零件和分总成,一级供应商应对其分供方进行控制计划审核、PPAP和GP9并在被要求时向SGMW SQE 提交上述报告。
对SGMW指定采购的材料/零件,供应商负责入厂质量控制并在需要时与其原供应商进行沟通。
7. 所有供应商应制定并实施零件检验标准来确定那些在零件发往SGMW之前进行成品检验的产品特性(尺寸、外观、材料、性能及功能)。
标准应指定所有被检验产品特性的检验频次、方法和地点。
对那些需要时间长、费用高的功能和性能试验,由供应商负责所有试验,包括费用;供应商应按照SGMW供应商质量开发工程师批准的控制计划定期提供试验报告给SGMW。