化学热处理工艺及应用
热处理工艺

热处理工艺热处理工艺是通过加热和冷却对金属材料进行控制的工艺过程,目的是改变其原有的物理和化学性质,以提升材料的性能。
热处理工艺包括退火、正火、淬火、回火、疏松加热等不同方法。
本文将介绍热处理工艺的原理、方法和应用。
一、热处理工艺原理1.金属材料的组织结构与性能金属材料由于晶粒和晶界结构,其中晶粒内的原子排列方式称为晶态。
金属材料的物理和力学性质与其晶粒和晶界结构有关。
晶粒的大小、形状、分布和晶界的状态对金属材料的强度、硬度、塑性、韧性、导电性等性质影响显著。
2.热处理过程的原理由于金属材料在加热和冷却过程中的物理和化学反应,其晶粒和晶界组成的结构也会发生变化,从而影响其物理和化学性质。
热处理工艺就是通过控制材料的加热、保温时间和冷却速度等参数来控制金属材料的组织结构,从而提高材料的性能。
二、热处理方法1.退火退火是将金属材料加热至一定温度,保温一定时间后慢冷的热处理方法。
通过退火可以改变金属材料的晶界和晶粒的结构,增强塑性、韧性和延展性能。
退火方法也有多种不同的类型,包括全退火、球化退火、等温退火和局部退火等。
2.正火正火是将金属材料加热至一定温度,保温一定时间后慢冷的热处理方法。
通过正火可以改变金属材料的晶粒组织结构,提高其强度和硬度。
3.淬火淬火是将金属材料加热至一定温度,然后迅速浸入冷却介质中,使其迅速冷却的热处理方法。
淬火可以使晶粒迅速细化,提高材料的硬度和强度,但同时也会减少塑性和韧性。
4.回火回火是在淬火后将材料重新加热至一定温度并保温一定时间后冷却的热处理方法。
回火可以通过改变材料的晶界和晶粒组织结构来调整其硬度和韧性。
5.疏松加热疏松加热是将金属材料加热至一定温度并保温一定时间,旨在在已存在的材料中生成孔洞或气体,使材料产生疏松现象。
此工艺常用于铸造后处理中,其目的是在材料中消除潜在的缺陷和裂纹。
三、应用热处理工艺广泛应用于制造业中,包括钢铁、铸造、航空航天、汽车和电子等领域。
化学热处理工艺及应用

化学热处理工艺及应用除渗碳、渗氮外,渗金属主要有渗Al 、Cr、V、Si、B、S 等金属和非金属。
下面简单介绍。
1. 渗铬适用于各种钢制件的耐磨性、耐蚀性和抗高温氧化能力。
渗后硬度:低碳钢为200~250HV ;高碳钢为1250~1300HV。
渗层深度:一般为0.10~0.30mm。
渗层金相组织:低碳钢50%左右铬在铁素体中的固溶体;高碳钢由铬的碳化物(Cr7C3)、(CrFe)7C3 组成。
渗铬方法:固、液、气体渗,还有真空渗等。
固体法:将以下配方研成粒度小于50目(约0.297mm)粉末,然后装箱进行。
配方1:50%~55%铬铁粉末+40~50%氧化铝+2~3%氯化铵。
配方2:60%~65%铬铁粉末+30~35%耐火土+3~4%氯化铵。
装炉温度为800~850C,保温1〜1.5h后升温到1000〜1050E .。
保温12〜15h (视层深要求而定)。
然后随炉冷却600〜700E出炉空冷即可。
液体法:采用70%氯化钡+30%氯化钠为基盐。
将金属铬或铬铁粉末经盐酸处理后放入基盐中,加热到1000〜1050E保温1.0〜1.5h即开始渗,同时应不间断地用惰性气体或还原气体保盐浴表面不被氧化。
气体法:利用干净铬块+氯化铵+氢气,在950〜1100C通入氯化铜蒸汽进行。
渗铬后的处理:在一定载荷下工作并要求一定的强度的零件,渗铬后正火处理可细化晶粒,提高基体强度和韧性,淬火和回火处理可根据需要调整基体的性能。
2、渗B渗硼是指将工件放在一定比例的含硼介质中加热。
适用范围:提高各种钢、铸铁和粉末冶金等材料制作的工件耐磨性。
渗后硬度:900~1200H V0.1 以上。
金相组织:为致密的单相Fe2B。
渗层深度:一般为40~100um渗B方法:固体、液体、气体和膏剂渗。
固渗法:目前市场上有商品固体渗B剂可供应,并附有详细使用说明。
也可按下面配方:5%KBF4+0.5~0.3%(NH2)CS (硫脲)+20~30%木炭+62~84BFe (硼的质量分数不小于20%,铝和硅的质量分数分别不大于3.5%~4.0%)。
磷酸化热处理
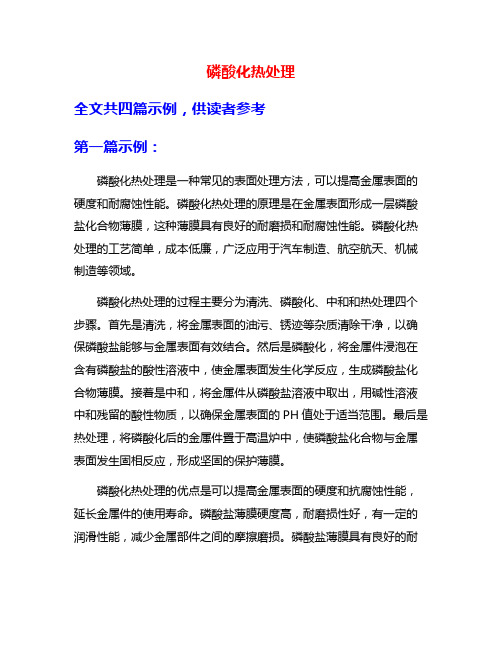
磷酸化热处理全文共四篇示例,供读者参考第一篇示例:磷酸化热处理是一种常见的表面处理方法,可以提高金属表面的硬度和耐腐蚀性能。
磷酸化热处理的原理是在金属表面形成一层磷酸盐化合物薄膜,这种薄膜具有良好的耐磨损和耐腐蚀性能。
磷酸化热处理的工艺简单,成本低廉,广泛应用于汽车制造、航空航天、机械制造等领域。
磷酸化热处理的过程主要分为清洗、磷酸化、中和和热处理四个步骤。
首先是清洗,将金属表面的油污、锈迹等杂质清除干净,以确保磷酸盐能够与金属表面有效结合。
然后是磷酸化,将金属件浸泡在含有磷酸盐的酸性溶液中,使金属表面发生化学反应,生成磷酸盐化合物薄膜。
接着是中和,将金属件从磷酸盐溶液中取出,用碱性溶液中和残留的酸性物质,以确保金属表面的PH值处于适当范围。
最后是热处理,将磷酸化后的金属件置于高温炉中,使磷酸盐化合物与金属表面发生固相反应,形成坚固的保护薄膜。
磷酸化热处理的优点是可以提高金属表面的硬度和抗腐蚀性能,延长金属件的使用寿命。
磷酸盐薄膜硬度高,耐磨损性好,有一定的润滑性能,减少金属部件之间的摩擦磨损。
磷酸盐薄膜具有良好的耐腐蚀性能,可以在恶劣的工作环境下保护金属表面免受腐蚀侵蚀。
磷酸盐薄膜的颜色稳定,不易褪色,能够提升金属表面的美观度。
磷酸化热处理的应用范围广泛,特别在汽车制造、航空航天、机械制造等领域得到了广泛应用。
在汽车制造中,发动机零部件、汽车底盘、车身构件等金属件经过磷酸化热处理后,可以提高抗疲劳性能和抗腐蚀性能,延长汽车的使用寿命。
在航空航天领域,飞机发动机零部件、飞行控制系统等关键金属件经过磷酸化热处理后,可以提高耐高温性能和耐腐蚀性能,保障飞机的安全飞行。
在机械制造领域,工业机床、模具、轴承等金属件经过磷酸化热处理后,可以提高耐磨损性能和耐腐蚀性能,延长设备的使用寿命。
磷酸化热处理是一种简单、经济、有效的表面处理方法,可以提高金属表面的硬度和耐腐蚀性能,广泛应用于各个领域。
随着技术的不断进步,磷酸化热处理的工艺将会更加完善,应用范围将会更加广泛,为金属制品的生产和应用带来更多的便利和效益。
化学热处理
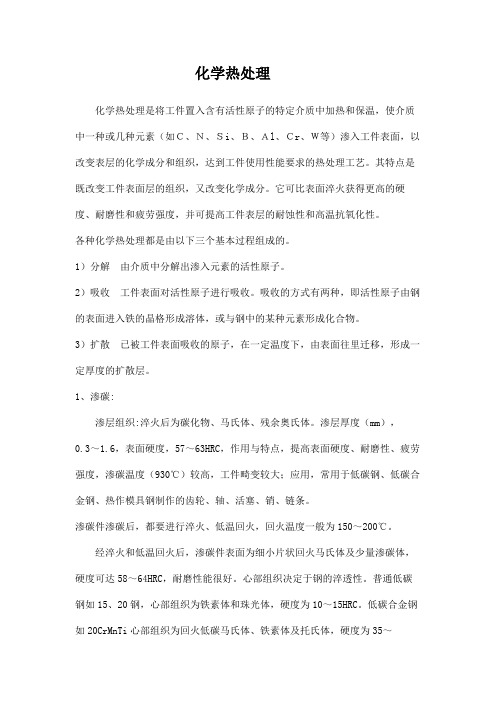
化学热处理化学热处理是将工件置入含有活性原子的特定介质中加热和保温,使介质中一种或几种元素(如C、N、Si、B、Al、Cr、W等)渗入工件表面,以改变表层的化学成分和组织,达到工件使用性能要求的热处理工艺。
其特点是既改变工件表面层的组织,又改变化学成分。
它可比表面淬火获得更高的硬度、耐磨性和疲劳强度,并可提高工件表层的耐蚀性和高温抗氧化性。
各种化学热处理都是由以下三个基本过程组成的。
1)分解由介质中分解出渗入元素的活性原子。
2)吸收工件表面对活性原子进行吸收。
吸收的方式有两种,即活性原子由钢的表面进入铁的晶格形成溶体,或与钢中的某种元素形成化合物。
3)扩散已被工件表面吸收的原子,在一定温度下,由表面往里迁移,形成一定厚度的扩散层。
1、渗碳:渗层组织:淬火后为碳化物、马氏体、残余奥氏体。
渗层厚度(mm),0.3~1.6,表面硬度,57~63HRC,作用与特点,提高表面硬度、耐磨性、疲劳强度,渗碳温度(930℃)较高,工件畸变较大;应用,常用于低碳钢、低碳合金钢、热作模具钢制作的齿轮、轴、活塞、销、链条。
渗碳件渗碳后,都要进行淬火、低温回火,回火温度一般为150~200℃。
经淬火和低温回火后,渗碳件表面为细小片状回火马氏体及少量渗碳体,硬度可达58~64HRC,耐磨性能很好。
心部组织决定于钢的淬透性。
普通低碳钢如15、20钢,心部组织为铁素体和珠光体,硬度为10~15HRC。
低碳合金钢如20CrMnTi心部组织为回火低碳马氏体、铁素体及托氏体,硬度为35~45HRC,具有较高的强度、韧性及一定的塑性。
2.液体氮化也称软氮化,低温氰化,或者氮碳共渗,在渗氮过程中,碳原子也参与,因而比一般的单一气体渗氮具有更高的渗速,在渗层表面硬度相当的情况下,氮化层的脆性也比气体氮化小,软氮化因此得名。
氮化主要是往炉中加入纯氨,在200℃以上氨分解为活性氮原子,在500~580℃时,活性氮原子往钢件表面渗氮和扩散,得到0.3~0.5mm厚的高硬度、耐腐蚀、抗疲劳的氮化层。
表面化学热处理技术

化学热处理渗碳:为了获得高硬度、高耐磨的表面及强韧的心部,渗碳后必须进行淬火加低温回火处理。
按渗碳介质可分为:气体渗碳、液体渗碳、固体渗碳。
渗氮:①渗氮层具有高硬度、高耐磨性;②渗氮层比热容打,在钢件表面形成压应力层可显著提高耐疲劳性能,渗氮层的耐疲劳性优于渗碳层;③渗氮层表面有化学稳定性高的ε相,能显著提高耐腐蚀性。
渗氮能形成性能优越的渗氮层,但由于工艺时间太长,使得生产率太低,成本高,应尽量少采用。
渗氮一般用在强烈磨损、耐疲劳性要求非常高的零件,有的场合是除要求机械性能外还要求耐腐蚀的零件。
碳氮共渗(俗称“氰化”):按工艺温度分:低温碳氮共渗(520-580℃),工艺温度低,共渗过程是以氮原子为主、碳原子为辅的渗入过程,俗称“软氮化”;中温碳氮共渗(780-880℃);高温碳氮共渗(880-930℃)。
优点:①与渗碳相比处理温度低,渗后可直接淬火,工艺简单,晶粒不易长大,变形裂倾向小,能源消耗少,共渗层的疲劳性和抗回火稳定性好;②与渗氮相比,生产周期大大缩短,对材料适用广。
氮碳共渗:氮碳共渗起源于西德,是在液体渗氮基础上发展起来的。
早期氮碳共渗是在含氰化物的盐浴中进行的。
由于处理温度低,一般在500-600℃,过程以渗氮为主,渗碳为辅,所以又称为“软氮化”。
氮碳共渗工艺的优点如下:①氮碳共渗有优良的性能:渗层硬度高,碳钢氮碳共渗处理后渗层硬度可达HV570-680;渗氮钢、高速钢、模具钢共渗后硬度可达HV850-1200;脆性低,有优良的耐磨性、耐疲劳性、抗咬合性和耐腐蚀性。
②工艺温度低,且不淬火,工件变形小。
③处理时间短,经济性好。
④设备简单,工艺易掌握。
存在问题是:渗层浅,承受重载荷零件不宜采用。
渗硼:渗硼是一种有效地表面硬化工艺。
将工件置于能产生活性硼的介质中,经过加热、保温,使硼原子渗入工件表面形成硼化物层的过程称为渗硼。
金属零件渗硼后,表面形成的硼化物(FeB、Fe2B、TiB2、ZrB2、VB2、CrB2)及碳化硼等化合物的硬度极高,热稳定性。
热处理工艺中的氮化处理及其应用
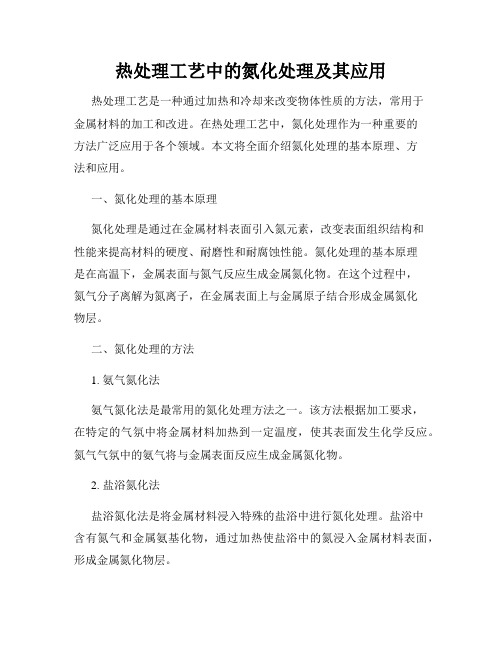
热处理工艺中的氮化处理及其应用热处理工艺是一种通过加热和冷却来改变物体性质的方法,常用于金属材料的加工和改进。
在热处理工艺中,氮化处理作为一种重要的方法广泛应用于各个领域。
本文将全面介绍氮化处理的基本原理、方法和应用。
一、氮化处理的基本原理氮化处理是通过在金属材料表面引入氮元素,改变表面组织结构和性能来提高材料的硬度、耐磨性和耐腐蚀性能。
氮化处理的基本原理是在高温下,金属表面与氮气反应生成金属氮化物。
在这个过程中,氮气分子离解为氮离子,在金属表面上与金属原子结合形成金属氮化物层。
二、氮化处理的方法1. 氨气氮化法氨气氮化法是最常用的氮化处理方法之一。
该方法根据加工要求,在特定的气氛中将金属材料加热到一定温度,使其表面发生化学反应。
氮气气氛中的氨气将与金属表面反应生成金属氮化物。
2. 盐浴氮化法盐浴氮化法是将金属材料浸入特殊的盐浴中进行氮化处理。
盐浴中含有氮气和金属氨基化物,通过加热使盐浴中的氮浸入金属材料表面,形成金属氮化物层。
3. 等离子氮化法等离子氮化法是利用等离子体的高温和高能量对金属材料进行表面处理。
等离子体中存在大量的活性氮离子,可以使金属表面迅速地与氮元素结合形成金属氮化物层。
三、氮化处理的应用1. 工具材料氮化处理可以提高工具材料的硬度和耐磨性,延长其使用寿命。
在切削工具、钻头、刀具等制造中广泛应用氮化处理技术,使工具具备更好的切削性能和耐久性。
2. 模具材料氮化处理可以显著提高模具材料的硬度、耐磨性和耐蚀性,使其能够承受更高的工作负荷和更复杂的加工环境。
在塑料模具、压铸模具和冲压模具等制造中广泛应用氮化处理技术,提高模具的使用寿命和稳定性。
3. 表面涂层氮化处理可用作一种表面涂层技术,通过在金属表面形成一层坚硬的金属氮化物,提高材料的耐磨、耐蚀和耐高温性能。
在汽车、航空航天和船舶等领域应用广泛,用于加强金属材料的表面保护。
4. 天然石墨的改性氮化处理可以用于改性天然石墨的制备。
氮化处理后的天然石墨具有较高的硬度和耐磨性,可用于电池、润滑材料和导热材料等领域。
钢的化学热处理
渗剂
吸收: 析出的活性原子克服表面能垒进入金属表面, 形成固溶体或化合物。
Fe〃[C]吸附 → Fe〃C溶
溶解
3Fe〃[C]吸附 → Fe3C
化合
吸收必须进行得足够快,否则会因发生其它反应而失去活性 。 吸收能力与钢的表面活性有关,表面缺陷多(位错、晶界露 头)、粗糙、干净无污染则表面活性高,吸附力强,可促进化 学热处理。
常用的气体介质:天然气、煤气、液化石油气。
使用时,直接通入炉罐里。 CH4→2H2+[C]
2CO→CO2+[C]
CO+H2→H2O+[C]
良好的渗碳介质应具备下列条件:
价格低廉,安全卫生,易于获取; 具有较好的活性,既保证能获得较高的渗碳速度,同时不致使
渗碳层碳浓度过高,而造成大量的过剩碳化物;
5)化学催渗:渗剂中加入一定的化学药剂或触媒剂以加速分解或吸收过程
6)物理催渗:eg:高频电场下的扩散。
化学热处理进行的条件:
1. 渗入元素的原子必须是活性原子, 而且具有较大的扩散能力 2. 零件本身具有吸收渗入原子的能力, 即对渗入原子有一定的 溶解度或能与之化合, 形成化合物。
分解、吸收、扩散三者的协调进行是确保化学热处理成功进行的关键。
产生的“碳黑”“焦炭”少。 渗碳剂分解产物中如果含有较多的不饱和碳氢化合物易形成过
多的碳黑附着在零件表面,使渗碳不均匀;附着在炉壁上,使
炉罐导热性差,从而使渗碳速度降低,同时也增加清理时的麻 烦。 含硫量低。
举例:
18CrMnTi钢汽车后桥主动伞齿轮渗碳工艺
固体渗碳:
化学表面处理工艺
化学表面处理工艺
化学表面热处理又称化学热处理。
将钢件或合金工件置于适当的介质中加热保温,使一种或几种元素渗入它的表层,以改变其化学成分和组织,从而获得所需性能的热处理工艺。
工业中广泛采用的化学热处理方法都是在工件表层渗入某种元素,即所谓的渗入法,按所渗入的元素,可以将化学热处理分为渗非金属、渗金属及金属与非金属共渗3大类。
渗非金属包括渗碳、渗氮、渗硼、渗硅、渗硫以及氮碳共渗、碳氮共渗、氧氮共渗、硫氮共渗、硼硅共渗、硫氮碳共渗等;渗金属有渗铬、渗铝、渗锌、渗钒及铬铝共渗等;金属与非金属共渗有铝硅共渗、铬铝硅共渗、铝硼共渗、钛硼共渗、钛氮共渗等。
近年来,发展了另一大类化学热处理,是将具有某种特殊性能的化合物直接沉积于金属基体表面,形成一层覆盖层,例如气相沉积氮化钛、碳化钛等。
化学热处理主要用于提高工件表面的硬度、耐磨性、疲劳强度或某种化学性能及物理性能等。
四大热处理工艺
四大热处理工艺
热处理工艺是一种通过改变材料的物理结构、化学成分和性质来改善其性能的技术。
在热处理工艺中,有四项主要的工艺,分别是退火、淬火、回火以及表面处理。
这四种热处理工艺都具有不同的特点和应用范围,并被广泛应用于现代工业生产中。
1. 退火工艺
退火工艺是将金属材料加热到一定温度,然后缓慢冷却至室温的工艺。
此工艺可以减少材料中的残余应力和提高硬度,改善材料的延展性和韧性,提高材料的加工性能,适用于铸造、锻造和变形加工等多种材料加工领域。
退火的最佳温度和持续时间会因材料不同而异。
2. 淬火工艺
淬火是将金属材料加热到一定温度后,通过迅速冷却来改变材料的组织结构和性质的工艺。
此工艺可以提高材料的硬度、强度和耐磨性,适用于制造各种机械零部件、工具等。
淬火温度、冷却速度和时间会对最终的材料性能产生显著的影响。
3. 回火工艺
回火工艺是在淬火后,将已经变硬的材料重新加热到一定温度,然后缓慢冷却的工艺。
此工艺可以减轻材料的脆性,并使其具有较好的延展性和韧性,适用于制造各种高强度零部件,如弹簧、轴承、齿轮等。
回火的最佳温度、时间和冷却速度也会因材料不同而异。
4. 表面处理工艺
表面处理工艺是将材料表面进行改性的工艺,包括氮化、硬化、镀膜等多种方法。
通过这些方法可以改善材料表面硬度、抗腐蚀性、耐磨性和抗疲劳性等,适用于制造各种高性能零部件和设备。
综上所述,四种热处理工艺在现代工业中都具有广泛的应用。
不同材料和加工要求会产生不同的需要,因此选择合适的热处理工艺不仅可以改善材料的性能,也可以提高生产效率,实现工业生产的可持续发展。
常用表面处理工艺及热处理工艺
正火:又称常化,是将工件加热至Ac3或Acm以上40~60℃,保温一段时间后,从炉中取出在空气中或喷水、喷雾或吹风冷却的金属热处理工艺。
运用范围:①用于低碳钢,正火后硬度略高于退火,韧性也较好,可作为切削加工的预处理。
②用于中碳钢,可代替调质处理作为最后热处理,也可作为用感应加热方法进行表面淬火前的预备处理。
③用于工具钢、轴承钢、渗碳钢等,可以消降或抑制网状碳化物的形成,从而得到球化退火所需的良好组织。
④用于铸钢件,可以细化铸态组织,改善切削加工性能。
⑤用于大型锻件,可作为最后热处理,从而避免淬火时较大的开裂倾向。
⑥用于球墨铸铁,使硬度、强度、耐磨性得到提高,如用于制造汽车、拖拉机、柴油机的曲轴、连杆等重要零件。
目的:使晶粒细化和碳化物分布均匀化,去除材料的内应力,降低材料的硬度。
退火:将金属构件加热到高于或低于临界点,保持一定时间,随后缓慢冷却,从而获得接近平衡状态的组织与性能的金属热处理工艺。
目的:降低硬度,改善切削加工性;消除残余应力,稳定尺寸,减少变形与裂纹倾向;细化晶粒,调整组织,消除组织缺陷。
退火工艺随目的之不同而有多种,如等温退火、均匀化退火、球化退火、去除应力退火、再结晶退火,以及稳定化退火、磁场退火等等。
注: 正火与退火工艺相比,其主要区别是正火的冷却速度稍快,因而正火组织要比退火组织更细一些,其机械性能也有所提高。
故退火与正火同样能达到零件性能要求时,尽可能选用正火。
大部分中、低碳钢的坯料一般都采用正火热处理。
一般合金钢坯料常采用退火,若用正火,由于冷却速度较快,使其正火后硬度较高,不利于切削加工。
淬火:将钢件加热到临界温度Ac3(亚共析钢)或Ac1(过共析钢)以上某一温度,保温一段时间,使之全部或部分奥氏体1化,然后以大于临界冷却速度的冷速快冷到Ms以下(或Ms附近等温)进行马氏体(或贝氏体)转变的热处理工艺。
通常也将铝合金、铜合金、钛合金、钢化玻璃等材料的固溶处理或带有快速冷却过程的热处理工艺称为淬火。
- 1、下载文档前请自行甄别文档内容的完整性,平台不提供额外的编辑、内容补充、找答案等附加服务。
- 2、"仅部分预览"的文档,不可在线预览部分如存在完整性等问题,可反馈申请退款(可完整预览的文档不适用该条件!)。
- 3、如文档侵犯您的权益,请联系客服反馈,我们会尽快为您处理(人工客服工作时间:9:00-18:30)。
一.化学热处理工艺及应用除渗碳、渗氮外,渗金属主要有渗Al、Cr、V、Si、B、S等金属和非金属。
下面简单介绍。
1.渗铬适用于各种钢制件的耐磨性、耐蚀性和抗高温氧化能力。
渗后硬度:低碳钢为200~250HV;高碳钢为1250~1300HV。
渗层深度:一般为0.10~0.30mm。
渗层金相组织:低碳钢50%左右铬在铁素体中的固溶体;高碳钢由铬的碳化物(Cr7C3)、(CrFe)7C3组成。
渗铬方法:固、液、气体渗,还有真空渗等。
固体法:将以下配方研成粒度小于50目(约0.297mm)粉末,然后装箱进行。
配方1:50%~55%铬铁粉末+40~50%氧化铝+2~3%氯化铵。
配方2:60%~65%铬铁粉末+30~35%耐火土+3~4%氯化铵。
装炉温度为800~850℃,保温1~1.5h后升温到1000~1050℃.。
保温12~15h(视层深要求而定)。
然后随炉冷却600~700℃出炉空冷即可。
液体法:采用70%氯化钡+30%氯化钠为基盐。
将金属铬或铬铁粉末经盐酸处理后放入基盐中,加热到1000~1050℃保温1.0~1.5h即开始渗,同时应不间断地用惰性气体或还原气体保盐浴表面不被氧化。
气体法:利用干净铬块+氯化铵+氢气,在950~1100℃通入氯化铜蒸汽进行。
渗铬后的处理:在一定载荷下工作并要求一定的强度的零件,渗铬后正火处理可细化晶粒,提高基体强度和韧性,淬火和回火处理可根据需要调整基体的性能。
2、渗B渗硼是指将工件放在一定比例的含硼介质中加热。
适用范围:提高各种钢、铸铁和粉末冶金等材料制作的工件耐磨性。
渗后硬度:900~1200H V0.1以上。
金相组织:为致密的单相Fe2B。
渗层深度:一般为40~100um渗B方法:固体、液体、气体和膏剂渗。
固渗法:目前市场上有商品固体渗B剂可供应,并附有详细使用说明。
也可按下面配方:5%KBF4+0.5~0.3%(NH2)CS(硫脲)+20~30%木炭+62~84BFe(硼的质量分数不小于20%,铝和硅的质量分数分别不大于3.5%~4.0%)。
固渗温度和时间,根据渗B层深度确定。
盐浴渗B应用较为广泛:配方:90~70%Na2B4O7+10~30%SiC或者5%B4C+15%NaBF+80%NaCL等。
使用温度为920~950℃,常用钢盐浴渗硼深度与温度及时间的关系见下表。
膏剂渗硼:即将渗硼膏剂涂敷于工件表面需渗硼的部位,干燥后放入盛有惰性填料的箱内,进行加热渗硼。
可采用下列配方:50%B4C+35%CaF+15%Na2SiF6。
在920~940℃,保温4h后出炉。
膏剂涂层厚度应为13mm左右,在120~150℃烘干。
惰性填料以在高温条件下无氧化脱碳为宜,如新铸铁屑、石英粉+炭粉等均可。
几种钢膏剂渗硼温度、时间与层深及硬度的关系如下表渗硼后根据心部硬度要求,直接淬火或缓冷均可。
渗硼在热锻模上的应用,见下表渗硼与未渗硼滚压模的寿命比较见下表3、渗V渗钒是将工件放在产生钒原子的介质中,经一定温度加热和保温,将V 渗入其表面的热处理工艺。
使用范围:提高各种钢制作的工件的耐磨性和耐蚀性(耐酸、盐腐蚀)。
渗后组织:表面组织为钒在铁素体中的固溶体,中高碳钢为碳化钒或碳化钒与铁素体的混合物。
渗后硬度:中高碳钢渗V 后,硬度不低于2000HV 。
渗V 方法:目前有盐浴法、粉末法和气体法等。
其中盐浴法处理温度较低,使用较为广泛。
盐浴法:所用成分是在熔融的硼砂浴中加入质量分数为80%Na 2B 4O 7及20%钒铁(钒的质量分数在43%以上)的混合物[粒度为100-150目(约为0.097-0.150mm )],其加入量以盐浴呈碱性(PH 值为9)为准。
使用温度为930-970℃。
钢件渗V 后,表面由白亮层和过渡区组成。
几种钢930-970℃渗V 后的硬度和白亮层厚度见下表:为了使心部获得一定的强度和韧性,渗V后应空冷正火细化晶粒,然后按正常的强度进行淬火和回火。
但高合金钢(如淬火温度在970℃以上的Cr12MoV和W18Cr4V等)可以渗钒后,继续升温到其正常淬火温度进行保温及冷却,然后回火。
粉末法:可以采用的渗剂成分(质量分数)为:60%钒铁+37%高岭土+3%的氯化铵。
装箱方法与固体渗碳相同。
渗钒温度为1000~1100℃。
低碳钢渗V后,表层为钒在铁素体中的固溶体,中高碳钢渗V后,表面层为碳化钒或碳化钒与铁素体的混合物。
气体渗V:通常使用氯化钒及氢气作介质,在专用炉中于1000~1100℃的温度下渗V。
二、多元共渗化学热处理工艺及其应用多元共渗除碳氮共渗外,还有氮氧、氮硫、铬铝、硫碳氮、铝铬硅等共渗。
下面简单介绍分别以铬为基、以硼为基的多元共渗及应用;固体和盐浴覆层工艺及其应用。
1、以铬为基的多元共渗及应用铬、铝、硅等是冶炼特殊性能(耐磨、耐蚀和抗高温氧化等)钢和铸铁时,不可缺的重要合金元素。
如果工件的基体对性能没有特殊要求时,则可以在普通钢制作的工件表面,通过化学热处理方法增加这些元素,使其表面具有所要求的特殊性能。
如此,在满足工件表面特殊性能要求的同时,又可节约昂贵的特殊钢。
1-1铬铝共渗铬铝共渗是通过渗入Cr提高工件的耐磨性和耐蚀性能;渗入Al提高抗高温氧化能力的化学热处理工艺。
铬铝共渗方式:可以先渗铬后渗铝,或先渗铝后渗铬,或两者同时共渗。
铬铝共渗方法:固体粉末法、气体法和盐浴法等。
常用的是固体粉末法,共渗剂成分及热处理工艺见下表:铬铝共渗的抗氧化能力比单一渗铬或铝更好,主要取决于渗层中的铬与铝的比例。
实践表明,渗入量以Cr:Al=5:1(质量比)的比例最佳。
共渗层的脆性比单独渗Al 的少,950℃以下的耐热疲劳性能比渗Al的更好。
其力学性能比单独渗Cr好。
1-2 铬硅共渗铬硅共渗是利用渗铬提高工件的耐磨性、耐蚀性、渗硅是提高工件对酸类、海水等的耐蚀性的化学热处理工艺。
铬硅共渗可以先渗Cr后渗硅,或者铬和硅同时渗入。
实例1,先渗铬后渗硅的固体复合渗工艺。
先在成分(质量分数)为50%铬+38%三氧化二铝+2%氧化铵的渗剂中,进行1000℃加热保持4h的渗铬;然后再在通有氯气的硅粉中,进行900℃加热保持2h渗硅。
实例2,铬和硅同时渗的固体共渗工艺。
在成分(质量分数)为49%~55%铬+42%三氧化二铝+1%~7%硅+2%氯化铵的渗剂中,于900℃~1000℃加热保持10h。
适用于工业纯铁。
1-3铝硅共渗炼制高温合金、耐热钢和耐热铸铁时,铝和硅经常是铬和镍的代用元素,使其具有抗氧化能力。
在普通钢鉄材料上进行铝硅共渗,可达到上述目的。
实例:20钢镀锌板的铝硅共渗采用膏剂共渗法。
渗剂配方成分(质量分数):60%~70%铝铁+28%~38%硅+1%~2%氯化铵。
操作过程如下:①清除工件表面油污和杂物。
②将渗剂和粘结剂混合均匀,调成悬浮液状;③将渗剂刷涂于工件表面,厚度约3mm;④在150℃的温度下烘干3~10min;⑤工件表面包裹4mm厚度的耐火泥进行密封;⑥在150℃预热10~15min(如果表面有裂纹,再重新封补)。
共渗处理工艺:在电阻炉中,950℃加热保持2h。
然后,清除表面耐火泥,重新加热至1050℃,保持1h后于水中淬火冷却。
处理结果:渗层深度为115um,清理后表面呈光滑的银灰色。
1-4铬铝硅共渗对镍基合金和钴基合金制作的汽轮机零件,进行铬铝硅共渗可以提高其抗高温腐蚀和抗高温氧化的综合性能。
1-4-1高温铬铝硅共渗高温铬铝硅共渗采用粉末装箱进行。
渗剂配方(质量分数):15%铬[粒度为250目(约为0.057mm)]+5%铝[粒度为200目(约为0.074mm)]+79.4%碳化硅[粒度为240目(约为0.059)]+0.4%溴化铵及0.2%三氧化二铝[粒度为100目(约为0.15mm)]。
操作过程如下:①按上述配方将渗剂混合均匀后装箱;②共渗工艺:在箱式炉中,于850℃加热透烧后,炉温升至1090℃保持7h,然后冷至95℃取出工件。
③对冷却后的工件进行清刷,并用氢氧化铵液清洗。
处理结果:钴基合金共渗深度为25~75um;镍基合金共渗后深度为50~100um;铁基合金共渗层深25~250um1-4-2中温铬铝硅共渗中温铬铝硅共渗也要用粉末装箱法进行,对渗剂技术要求如下:①铝粉纯度为99.9%(质量分数),细度为0.09mm;②三氧化二铝粉纯度为99%(质量分数);③耐火粘土中含有不低于60%(质量分数)的二氧化硅;④氯化铵和氯化钠均为化学纯试剂。
渗剂配方(质量分数)如下:37%Al2O3+20%Al+32%Cr2O3+8%SiO2+2%NH4CL+1%NaF。
共渗剂在混合罐内混合好后静置10min即可装箱。
箱分双层,内箱装工件,外箱与内箱之间放渗剂。
工件放在料架上,不得面与面相互接触。
共渗剂装箱时,一层(5mm)渗剂再放一层钢纤维,逐层直至箱顶部,最后再放一层渗剂。
共渗工艺及操作过程:共渗箱在80~100℃的电阻炉中烘干2h后,将炉温升至750℃并保持1h,再升温至850℃并保持2h后出炉。
待共渗箱冷却至200℃以下拆箱。
1-5铬钒共渗铬钒共渗,旨在使工件获得比单一渗铬或钒更优良的耐磨性、耐蚀性和抗高温氧化性和抗热疲劳能力。
生产实践中的铬钒共渗,经常采用盐浴共渗法。
盐浴铬钒共渗的渗剂成分和工艺见下表:2.以硼为基的多元共渗及其应用2-1硼氮共渗硼氮共渗的目的,是为了比单一渗硼进一步提高耐磨性、耐蚀性和热硬性等。
采用成分(质量分数)为5%B4C+5%KBF4+1%活性炭+0.5%NH4CL+5%(NH2)2CO,余量为SiC的固体硼氮共渗剂。
操作过程:将工件清洗干净,烘干后装入共渗箱内。
将工件加热到580~600℃保持2~3h预热的,升温到560~910℃,保持4~10h,然后随炉冷却到400℃左右出炉空冷,在室温开箱。
通常需要重新加热淬火,以满足工件心部的使用性能要求和避免使用时极薄的共渗层被压裂。
实例:1Cr18Ni9Ti奥氏体不锈钢模具装入共渗箱内,经580℃预热3h后,升温到900℃并保持8h。
处理结果:表面显微硬度为1553~1980HV0.2;共渗层深度为0.05~0.08mm;最外层组织为FeB+Fe2B,次层为Fe2B+ɑ-Fe,第三层为Fe2B+ɑ-Fe+r-Fe 2-2硼铝共渗比单一渗硼进一步提高耐磨性、耐蚀性和抗高温氧化性能等。
在生产中,常采用固体粉末装箱共渗法和膏剂共渗法。
①固体粉末法,其渗剂成分(质量分数)为:21%B4C+4%Na2B4O7+72%FeAl+3%NH4CL或49%Al2O3+29.4%B2O3+19.6%Al+2%Na2F。
处理工艺和操作:将渗剂和工件装在共渗箱内(工件摆放和渗剂添充与固体渗碳相同),用水玻璃调制耐火泥密封箱口。
根据所处理的钢种和心部要求的性能,选择共渗温度,一般为800~1050℃;根据所要求的深度,保持4~6h。