李传栻 关于硅在铸铁中的固溶强化作用 for 百铸网
硅在铸铁中的固溶强化作用,专家的几点看法!

硅在铸铁中的固溶强化作用,专家的几点看法!近年来,为了适应多方面的要求,各种新工艺、新材料不断涌现,轻合金铸件、铸钢件的应用都发展很快,但是到目前为止,铸铁件的需求量仍然稳居首位。
2012年,世界各国各类铸件的总产量为10083万t,其中:灰铸铁件4599.6万吨,占45.6%;球墨铸铁件2516.7万t,占24.9%;可锻铸铁件127.5万t,占1.3%。
也就是说,目前世界各类铸件的总产量中,灰铸铁件和球墨铸铁件就占70%以上。
近年来,为了遵循可持续发展的理念,除了对铸铁件功能的要求日益增强以外,还增加了轻量化、低成本、节能减排、珍惜资源等多方面的要求。
因此,各国铸造行业都非常重视改进铸铁材质方面的研究、开发工作。
硅是地壳中蕴藏最丰富的元素,无匮乏之虞,而且在各种铸铁中,硅都是主要构成元素之一,对铸铁组织中石墨的形态、数量,乃至基体组织的形成,都有非常重要的作用。
但是,时至今日,硅在铸铁中的作用,我们的认知还很不够,有待进一步探索的空间仍然广阔。
一、硅在铸铁中的作用硅在铸铁中的作用是多方面的,其中,我们最关注的首先是“促进石墨化”和“固溶强化”两项,除此以外,硅还有不少重要的作用,在这里,简单地提一提以下两点:(1)溶于液态铸铁中的硅,使铁液抗氧化能力大为增强,而且硅还可以使氮在铁液中的溶解度降低。
正是由于硅的这种作用,铸铁才可以在强氧化性、富氮的条件下熔炼。
各种铸造合金中,只有铸铁才能够用冲天炉、氧气回转炉这类熔炼设备,在富氧、富氮的气氛中熔炼。
(2)将铸铁中硅含量提高到3.5%以上,铸铁的抗氧化能力、抗热生长性能都大为改善。
早期,各国耐热铸铁的标准中,就都有了硅系耐热铸铁的牌号。
近年来,出于节能的考虑,各种内燃机提高了排气的温度,各国汽车行业中,都很重视耐热硅钼球墨铸铁件的应用。
1.硅在铸铁中促进石墨化的作用铸铁中硅是促进石墨化作用最强的合金元素,硅促进石墨化的能力,是镍的3倍,铜的5倍。
不同炉前硅含量对高硅固溶强化铁素体球墨铸铁性能及组织的影响
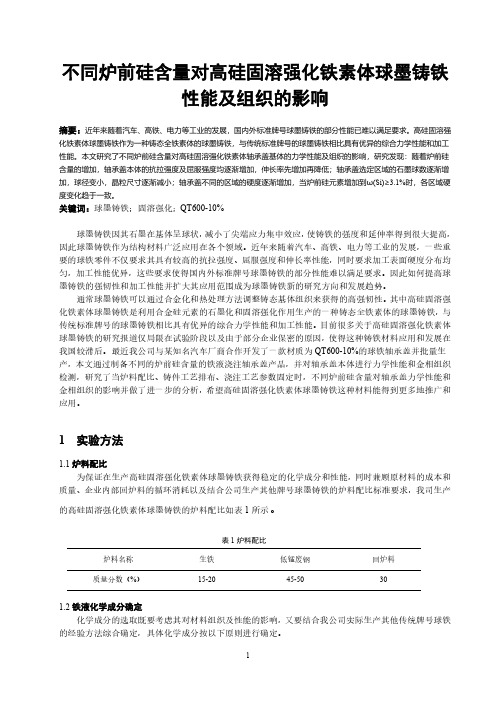
不同炉前硅含量对高硅固溶强化铁素体球墨铸铁性能及组织的影响摘要:近年来随着汽车、高铁、电力等工业的发展,国内外标准牌号球墨铸铁的部分性能已难以满足要求。
高硅固溶强化铁素体球墨铸铁作为一种铸态全铁素体的球墨铸铁,与传统标准牌号的球墨铸铁相比具有优异的综合力学性能和加工性能。
本文研究了不同炉前硅含量对高硅固溶强化铁素体轴承盖基体的力学性能及组织的影响,研究发现:随着炉前硅含量的增加,轴承盖本体的抗拉强度及屈服强度均逐渐增加,伸长率先增加再降低;轴承盖选定区域的石墨球数逐渐增加,球径变小,晶粒尺寸逐渐减小;轴承盖不同的区域的硬度逐渐增加,当炉前硅元素增加到ω(Si)≥3.1%时,各区域硬度变化趋于一致。
关键词:球墨铸铁;固溶强化;QT600-10%球墨铸铁因其石墨在基体呈球状,减小了尖端应力集中效应,使铸铁的强度和延伸率得到很大提高,因此球墨铸铁作为结构材料广泛应用在各个领域。
近年来随着汽车、高铁、电力等工业的发展,一些重要的球铁零件不仅要求其具有较高的抗拉强度、屈服强度和伸长率性能,同时要求加工表面硬度分布均匀,加工性能优异,这些要求使得国内外标准牌号球墨铸铁的部分性能难以满足要求。
因此如何提高球墨铸铁的强韧性和加工性能并扩大其应用范围成为球墨铸铁新的研究方向和发展趋势。
通常球墨铸铁可以通过合金化和热处理方法调整铸态基体组织来获得的高强韧性。
其中高硅固溶强化铁素体球墨铸铁是利用合金硅元素的石墨化和固溶强化作用生产的一种铸态全铁素体的球墨铸铁,与传统标准牌号的球墨铸铁相比具有优异的综合力学性能和加工性能。
目前很多关于高硅固溶强化铁素体球墨铸铁的研究报道仅局限在试验阶段以及由于部分企业保密的原因,使得这种铸铁材料应用和发展在我国较滞后。
最近我公司与某知名汽车厂商合作开发了一款材质为QT600-10%的球铁轴承盖并批量生产,本文通过制备不同的炉前硅含量的铁液浇注轴承盖产品,并对轴承盖本体进行力学性能和金相组织检测,研究了当炉料配比、铸件工艺排布、浇注工艺参数固定时,不同炉前硅含量对轴承盖力学性能和金相组织的影响并做了进一步的分析,希望高硅固溶强化铁素体球墨铸铁这种材料能得到更多地推广和应用。
如何面对铸铁中干扰元素的影响-下

热加工
!"#$%&’
铸! ! 造
! ! ! ! ! ! !
据报道,日本、俄罗斯和巴西都生产类似的高纯生 铁。近年来,我国也已开始生产这种高纯生铁。 看来,采用高纯生铁是解决铸铁行业原材料困扰的 重要途径之一,希望大家都来关注高纯生铁生产和应用 方面的各种问题,使我国高纯生铁的生产能健康地发展 壮大,为提高我国铸铁件的技术含量创造条件。 目前,我国河北承德市保通铸铁型材公司能生产两 种高纯生铁,其成分规格见表 # 和表 $ 。
表 &! 高纯生铁的分级及成分规格 ( 未列范围者为最高值,质量分数) ( % )
牌号 /1(232-&,—4 & 67 8 9 ’( )* + ’ ;7 ;4< ;7 8 ;7 ;< ;7 ;6 ;7 ;4< 9 ;7 ;;# ;7 ;5< ;7 ;5; ;7 ;;# ;7 ;5< ,( &. /0
栏目主持 ! 田文华! !
有关Si-Mo球墨铸铁的一些问题

t o t h e h e a t . r e s i s t a n t n o d u l a r i r o n . A S i . Mn n o d u l a r i r o n h a s b e c o me c o mm o n l y u s e d c a s t a l l o y i n t h e
提 高S i 4 球铁的抗蠕变强度和断裂强度。碳和碳 当量 、锰 、磷 、硫等也对s i - M n 球铁 的性能有一定 的影响。为此 ,对于s i - M n  ̄ ,其碳 当量应略 大于常规球铁 ,锰含量一般 不超过 0 . 4 %~0 . 5 %, 磷含量应低于 0 . 0 5 %,硫含Байду номын сангаас控制在 0 . 0 1 O %~0 . 0 1 5 %。此外 ,还论述 了s i - M n 球铁在化学成分 和力学性 能要 求等方面的标准,以及熔炼、炉前处理 、铸件收缩缺 陷的预防、冷 隔及其预防、厚 壁铸件 中的碎块状石墨、铸件的热处理等生产工艺问题 。 关键词 :球 墨铸铁 ;石 墨化 ;铁素体;珠 光体 ; 固溶强化
wh i l e s i l i c o n c o n t e n t i s i n c r e a s e d a s ma l 1 a mo u n t o f mo l y b d e n u m( p r e f e r a b l y 0 . 5 t o 1 . 0 % a l s o i S a d d e d
周继扬 SiC在炼钢上的应用 for 百铸网

SiC在炼钢上的应用一、碳化硅在炼钢上的应用碳化硅是好脱氧剂,但也只是近几年的事。
现广泛使用的材料是硅化粉、碳粉、碳化钙。
近十年来,由于炼钢原材料价格猛涨,增加炼钢成本,从采伐、廉价的脱氧材料这件事才将SiC从冶金企业推出转到铸造领域。
国外,早在60年代,研究与应用。
经电炉炼钢的实际使用结果十分理想,节约了炼钢成本(1500元/t),还提高了钢水质量。
它是一种高性能复合脱氧剂,可代替价格昂贵的传统脱氧剂——硅铁粉,合金粉,适用于普通碳钢、合金钢,特种钢冶炼过程的脱氧。
优点如下;1、脱氧迅速,成渣早;2、自身由两个强还原元素(C、Si)构成,所以还原气氛浓;3、泡沫多,液面覆盖性好;4、综合价格比传统材料低;5、除了脱氧功能外,还有一定的增碳作用。
在需要C、Si两个元素都不足时,SiC增脱氧剂的功效更显突出,使用更为方便。
SiC增Si同时还可增C,SiC从状态图分析当温度升高时,达2100℃~2500℃,SiC也不能只靠温度而熔化,它是一个由单质形式的碳、硅以共价键方式相互结合成SiC化合物的。
二、SiC对钢铁熔液内的精炼、净化、去渣作用在冲天炉、电炉熔炼钢铁材料过程中,渣相成分内都存在一定数量的FeO,多则15%以上,少则百分之几,越少越好。
FeO的存在能使渣的熔点下降,必然促使更多的渣变成液体。
那些刚刚由固态或粘的渣子感应炉的强烈搅拌下,会在熔体中“均匀化”,以极小尺寸的渣粒悬浮在钢铁液体内,数目以万计的FeO和MnO (常称硅酸锰渣)液态渣粒数不好排除,留在铸件内形成夹杂。
SiC从冶金工业转入铸造的历史,最早是从钢液冶炼及耐火材料行业开始的。
因为铸造是冶金中的一部分,冶金又是铸造的基础。
小电炉与大电炉的冶炼原理、使用原辅材料品种与炉子操作不存在原则区别,所以冶金厂电炉的冶炼过程,使用的添加料SiC很早便被“移居”铸造领域。
三、碳化硅在铸钢冶炼上的应用效果1、脱氧期在氧化末期,钢中含氧量大致在0.01%~0.06%,氧化渣中大约含20%FeO,有小于5%的氧化渣还留于炉内,平均每吨钢液中氧化渣含量为15kg,渣中氧化铁为15×20%,合成纯氧是0.86千克/t钢水,由此得到钢和渣中总氧量0.91kg/t,反应式SiC+3[O]=(SiO2)+CO如使用75号碳化硅,则1吨钢需要的SiC为:kg/t (按反应式算出的理论值)在实际使用中,还应考虑到SiC在炉内受到的烧损,随炉气透出,还应加上损耗,所以应大于1.04kg/t。
如何面对铸铁中干扰元素的影响

如何面对铸铁中干扰元素的影响作者:中国铸造协会李传轼这里所说的“干扰元素”,是对灰铸铁和球墨铸铁的性能有负面影响而言的,不一定都是通常所谓的有害元素,其中有的在钢材中是重要的合金元素,有的对于某些合金铸铁也是必不可少的。
干扰元素的来源有三个方面:一是钢材、铸钢件和铸铁件中通常都含有的有害元素,如硫、磷(一些耐磨铸铁中有时故意加入少量的磷)、铅(易切削钢中有时加入少量的铅)等;二是为改善钢材的性能而特意加入的合金元素,如锰、铬、钼、钛、钒、铌、硼等;三则是混杂在炉料中的污染物。
一.问题的提出改革开放以来,随着国民经济的发展,我国铸造行业欣欣向荣,铸件的产量增长很快,为了使大家有明确的印象,下面简要地列出一组统计数字:1986年,我国各类铸件的总产量为440万吨;1996年,我国各类铸件的总产量为1090万吨,其中各种铸铁件占875万吨;2006年,我国各类铸件的总产量为2810万吨,其中各种铸铁件占2100万吨。
铸件产量的迅速增长,拉动了对各种金属原材料的需求,铸造生铁、废钢和各种铁合金的供应日趋紧张,不仅价格不断上涨,质量也难以稳定一致。
另一方面,随着我国工业的发展,对各类铸件的质量要求日益提高,尤其是对高性能球墨铸铁件和厚截面、铁素体球墨铸铁件的需求增多,等温淬火球墨铸铁件和蠕墨铸铁件也逐步推广应用。
所有这些,都要求提高铸铁材质的纯净度,炉料带来的干扰元素的影响逐渐成为大家不能不面对的问题。
1.铸造生铁中的干扰元素炼钢用生铁中所含的磷、硫等干扰元素,可以在以后的炼钢过程中脱除,而铸造生铁只是在重熔后直接制成铸件,各种干扰元素相当一部分仍然保留,如果含量超过允许值,就会影响材质的性能。
制造高质量铸铁件时,原料生铁中干扰元素的含量必须严格控制。
为适应这种要求:我国于1982年制定了《GB718-82铸造用生铁》国家标准,以区别于炼钢生铁;1985年又制定了《GB1412-85球墨铸铁用生铁》国家标准;冶金工业部于1990还制定了一项规定微量元素含量的推荐性铸造生铁标准《YB(T)14-90 铸造用生铁》,其中对P、S、As、Pb、Sn、Sb、Zn、Cr、Ni、Cu、V、Ti、Mo等元素的允许含量都作了具体的规定。
无芯感应电炉熔炼灰铸铁的技术应用与发展_下_李传栻

废钢中的氮含量高于铸造生铁。用感应电炉熔 炼铸铁时,由于炉料中所用的铸造生铁锭少、废钢 多,制得的铸铁中氮含量会相应较高。
熔炼的是 低 碳 当 量 铸 铁,目 标 成 分 是: wC = 2. 55% ,wSi = 1. 7% ,wMn = 0. 4% 。
76
F铸 造 oundry
出铁温度为 1510 ~ 1530℃ 。 增碳剂加在浇包内,不同增碳剂的增碳效率可 参见表 5。
表 5 在浇包内加入不同增碳剂的增碳效率
增碳剂 鳞片石墨 电极碎屑 粒状碳制品 无烟煤 焦炭
( 2) 石油焦 这是目前广泛应用的增碳剂。 石油焦是精炼原油得到的副产品。原油经过常 压蒸馏或减压蒸馏得到的渣油及石油沥青,都可以 作为制造石油焦的原料,再经焦化后就得到生石油 焦。在原油加工过程中,产出的生石油焦一般不到 原油的 5% 。美国生石油焦的年产量约 3000 万 t。生 石油焦中的杂质含量高,不能直接用作增碳剂,必 须先经过煅烧处理。 生石油焦有海绵状、针状、粒状和流态等品种。 海绵状石油焦是用延迟焦化法制得的,由于其 中硫和金属含量较高,通常用作煅烧时的燃料,也 可作为煅烧石油焦的原料。经煅烧的海绵焦,主要 用于制铝业和用作增碳剂。 针状石油焦是用芳香烃含量高、杂质含量低的 原料,由延迟焦化法制得的。这种焦炭具有易于破 裂的针状结构,有时称之为石墨焦,煅烧后主要用 于制造石墨电极。 粒状石油焦呈硬质颗粒状,是用硫和沥青烯含 量高的原料,用延迟焦化法制得的,主要用作燃料。 流态石油焦是在流态床内用连续焦化法制得的, 呈细小 颗 粒 状,结 构 无 方 向 性,硫 含 量 高,挥 发 分低。 石油焦 的 煅 烧 是 为 了 脱 除 硫、 水 分 和 挥 发 分。 将生石油焦在 1200 ~ 1350℃ 煅烧,可以使其成为基 本上纯净的碳。 煅烧石油焦的最大用户是制铝业,70% 用来制 造使铝矾土还原的阳极。美国生产的煅烧石油焦用 于铸铁增碳剂的约占 6% 。 各种石油焦制品的成分列于表 1,供参考。 ( 3) 天然石墨 可分为鳞片石墨和微晶石墨 两类。
2019高考化学一轮选择题练习10新人教版1412

2019高考化学一轮选择题练习(10)李仕才1.(2016·十堰一中月考)实验室加热约150 mL液体时,可以使用的仪器是( )A.①③④⑥B.②③④⑥C.①③④⑤D.②③⑤⑥解析实验室加热约150 mL液体时,需在烧杯中进行,热源用酒精灯,烧杯不能直接加热,需要垫石棉网。
答案 A链接----【2017新课标1卷】支撑海港码头基础的钢管桩,常用外加电流的阴极保护法进行防腐,工作原理如图所示,其中高硅铸铁为惰性辅助阳极。
下列有关表述不正确的是A.通入保护电流使钢管桩表面腐蚀电流接近于零B.通电后外电路电子被强制从高硅铸铁流向钢管桩C.高硅铸铁的作用是作为损耗阳极材料和传递电流D.通入的保护电流应该根据环境条件变化进行调整【答案】C【名师点睛】该题难度较大,明确电化学原理是以及金属的防腐蚀原理是解答的关键,钢管桩表面腐蚀电流的理解是难点,注意题干信息的挖掘,即高硅铸铁为惰性辅助阳极,性质不活泼,不会被损耗。
2.【2017江苏卷】温度为T1时,在三个容积均为1 L的恒容密闭容器中仅发生反应:2NO2(g)2NO(g)+O2(g) (正反应吸热)。
实验测得:v正= v(NO2)消耗=k正c2(NO2),v逆=v(NO)消耗=2v(O2)k逆c2(NO)·c(O2),k正、k逆为速率常数,受温度影响。
下列说法正确的是消耗=A.达平衡时,容器Ⅰ与容器Ⅱ中的总压强之比为4∶5B.达平衡时,容器Ⅱ中比容器Ⅰ中的大C.达平衡时,容器Ⅲ中NO的体积分数小于50%D.当温度改变为T2时,若k正=k逆,则T2> T1【答案】CD可以求出平衡常数K=,平衡时气体的总物质的量为0.8 mol,其中NO占0.4 mol,所以NO的体积分数为50%,。
在平衡状态下,v正=v(NO2)消耗=v逆=v(NO)消耗,所以k正c2(NO2)=k逆c2(NO)•c(O2),进一步求出。
A.显然容器II的起始投料与容器I的平衡量相比,增大了反应物浓度,平衡将向逆反应方向移动,所以容器II在平衡时气体的总物质的量一定小于1 mol,故两容器的压强之比一定大于4:5,A错误;B.若容器II在某时刻,,由反应 2NO2 2NO + O2起始量(mol/L) 0.3 0.5 0.2变化量(mol/L) 2x 2x x平衡量(mol/L) 0.3−2x 0.5+2x 0.2+x因为,,解之得x=,求出此时浓度商Q c=>K,所以容器II达平衡时,一定小于1,B错误;C.若容器III在某时刻,NO的体积分数为50%,由反应 2NO2 2NO + O2起始量(mol/L) 0 0.5 0.35变化量(mol/L) 2x 2x x平衡量(mol/L) 2x 0.5−2x 0.35−x由0.5−2x=2x+0.35−x,解之得,x=0.05,求出此时浓度商Q c=>,说明此时反应未达平衡,反应继续向逆反应方向进行,NO进一步减少,所以C正确;D.温度为T2时,>0.8,因为正反应是吸热反应,升高温度后化学平衡常数变大,所以T2>T1,D正确。
- 1、下载文档前请自行甄别文档内容的完整性,平台不提供额外的编辑、内容补充、找答案等附加服务。
- 2、"仅部分预览"的文档,不可在线预览部分如存在完整性等问题,可反馈申请退款(可完整预览的文档不适用该条件!)。
- 3、如文档侵犯您的权益,请联系客服反馈,我们会尽快为您处理(人工客服工作时间:9:00-18:30)。
关于硅在铸铁中的固溶强化作用中国铸造协会李传栻进入铁器时代,是人类文明开始快速发展的里程碑。
铸铁件的生产、应用,促进了早期的产业革命,推动了科学技术的进步。
到现在,‘铸造’依旧是制造业的基础,但各行各业的发展却又反过来拉动铸造行业,使之进入了现代化的新时代。
近年来,为了适应多方面的要求,各种新工艺、新材料不断涌现,轻合金铸件、铸钢件的应用都发展很快,但是,到目前为止,铸铁件的需求量仍然稳居首位。
2012年,世界各国各类铸件的总产量为10083万吨,其中:灰铸铁件4599.6万吨,占45.6%;球墨铸铁件2516.7万吨,占24.9%;可锻铸铁件127.5万吨,占1.3%。
也就是说,目前世界各类铸件的总产量中,灰铸铁件和球墨铸铁件就占70%以上。
近年来,为了遵循可持续发展的理念,除了对铸铁件功能的要求日益增强以外,还增加了轻量化、低成本、节能减排、珍惜资源等多方面的要求。
因此,各国铸造行业都非常重视改进铸铁材质方面的研究、开发工作。
硅是地壳中蕴藏最丰富的元素,无匮乏之虞,而且,在各种铸铁中,硅都是主要构成元素之一,对铸铁组织中石墨的形态、数量,乃至基体组织的形成,都有非常重要的作用。
从三千多年前进入铁器时代起,我们铸造行业的同仁,就一天也离不了硅,人类对硅的认识,也随着经验的积累和科学技术的进步而不断深化。
但是,时至今日,硅在铸铁中的作用,我们的认知还很不够,有待进一步探索的空间仍然广阔。
一、硅在铸铁中的作用硅在铸铁中的作用是多方面的,其中,我们最关注的首先是‘促进石墨化’和‘固溶强化’两项,除此以外,硅还有不少重要的作用,在这里,简单地提一提以下两点:●溶于液态铸铁中的硅,使铁液抗氧化能力大为增强,而且硅还可以使氮在铁液中的溶解度降低。
正是由于硅的这种作用,铸铁才可以在强氧化性、富氮的条件下熔炼。
各种铸造合金中,只有铸铁才能够用冲天炉、氧气回转炉这类熔炼设备、在富氧、富氮的气氛中熔炼。
●将铸铁中硅含量提高到3.5%以上,铸铁的抗氧化能力、抗热生长性能都大为改善。
早期,各国耐热铸铁的标准中,就都有了硅系耐热铸铁的牌号。
近年来,出于节能的考虑,各种内燃机提高了排气的温度,各国汽车行业中,都很重视耐热硅钼球墨铸铁件的应用。
1、硅在铸铁中促进石墨化的作用铸铁中硅是促进石墨化作用最强的合金元素,硅促进石墨化的能力,是镍的3倍,铜的5倍。
无论在液态或固态的铸铁中,硅与铁结合的作用都比碳强。
液态铸铁中含有硅,就会使碳的溶解度降低。
铁液中硅的含量愈高,碳含量相应地愈低,就会有更多的碳被排挤出来。
铁液为过共晶成分时,硅含量高,凝固过程中,就有更多的碳以初生石墨的形态析出,直到剩余的铁液达到共晶成分后发生共晶转变。
铁液为亚共晶成分时,凝固过程中,硅富集于初生奥氏体中。
共晶转变时,硅富集于早期结晶的共晶奥氏体中,抑制碳与铁化合成渗碳体,增强碳在奥氏体中的扩散速度,促使碳以共晶石墨的形态析出。
共析转变时,固溶于奥氏体中的硅,仍然抑制碳与铁形成渗碳体,增强碳在奥氏体中的扩散速度,促使碳以共析石墨的形态析出。
在灰铸铁、球墨铸铁、蠕墨铸铁和黑心可锻铸铁中,碳和硅是影响石墨形态、数量的主要元素。
就是基本上不含石墨的白心可锻铸铁,在其脱碳退火的过程中,硅促进碳在奥氏体中扩散,对于这种可锻铸铁的脱碳也有重要的作用。
此外,铸铁中的氧和氮都有稳定碳化物的作用。
铸铁中含有的硅,可以使其中的氧、氮含量降低,这样,又间接地增强了硅对石墨化的作用。
2、硅在铁素体中的固溶强化作用在固态的铸铁中,硅几乎全部固溶于奥氏体和铁素体,不进入碳化物。
硅原子与铁原子可以结合成具有强共价键的含硅铁素体,不仅促进铁素体形成,而且使铁素体强化的作用很强。
为了了解硅强化铁素体的能力,避免石墨形态和其他合金元素的影响,上世纪50年代,国外有人在碳含量为0.1%、不含其他合金元素的钢中,加入不同量的硅,以比较硅对力学性能的影响,结果见表1。
表1中,还列出了组织为全部珠光体、不含其他合金元素的碳钢的性能,供对比。
表1 不同硅含量的铁素体的力学性能由表1可见,硅强化铁素体的作用很明显。
硅含量的提高后,抗拉强度和硬度都随之提高。
但是,硅固溶强化的铁素体,抗拉强度和硬度的值仍明显地低于珠光体。
铸铁中,利用硅的固溶强化作用,可以减少或不用铜、镍、锡、钼、铬等提高强度的合金元素,当然是有益的。
可是,很长时间以来。
铸造行业还没有充分地利用硅的这种潜能就灰铸铁而言,由于片状石墨切割基体的作用很大,铸铁的强度不高,一般对伸长率也不要求。
虽然提高灰铸铁的强度,主要是靠控制石墨的形态、数量,以及减小共晶团的尺寸,但也不能不尽可能地增强基体组织。
除需求量很少的低牌号灰铸铁外,一般都要求基体组织全部为珠光体。
为了得到珠光体基体,铸铁中的硅含量当然不宜太高。
因此,铸造行业的同仁也就很少注意硅的固溶强化作用就球墨铸铁而言,所有的牌号对伸长率都有严格的要求。
由表1可见,珠光体中固溶的硅量增多,伸长率相应地有所降低,硅含量超过3%后尤为明显。
此外,从很多有关球墨铸铁力学性能的试验报告中,都可见到类似的数据。
经相当长的一段时间,逐渐形成了这样一种观念,即:铸铁中的硅含量太高,会导致延性、韧性降低。
因此,硅的固溶强化作用往往就没有受到重视。
实际上,有些试验数据中只考虑硅含量的改变,忽略了其他因素的影响,无意中夸大了硅的‘脆化’作用。
二、硅固溶强化作用的应用硅在球墨铸铁中的固溶强化作用,最近已经受到了广泛的关注。
谈到这里,不能不提及我国三十多年前在灰铸铁方面所做的工作。
1、硅在灰铸铁中的固溶强化作用牌号HT250以上的灰铸铁,基体组织都是珠光体。
为了确保强度达标,生产中,通常都加入铜、锡、锑之类的合金元素。
珠光体中,铁素体约占90%,如果适当地提高铸铁中的硅含量,在铁素体中起固溶强化作用,而铸铁组织中又不至于出现铁素体,当然可以节省合金元素,同时也简化了操作。
1980年前后,北京钢铁学院(现在的北京科技大学)钟雪友等人进行了这方面的研究、试验工作。
在灰铸铁碳当量为4.05%左右的条件下,适当地提高硅含量(Si/C比为0.78左右),不加合金元素,铸铁的抗拉强度就可以保持在300 MPa以上。
80年代,这项工艺曾在多家铸造厂得到确认并在生产中应用。
2、硅在球墨铸铁中的固溶强化作用生产球墨铸铁件,球化率、石墨球数量和石墨球平均尺寸等是基本的质量要求。
在石墨球化正常的条件下,其切割基体的作用较在灰铸铁中大为减轻。
通过控制基体组织,可以在很大的范围内调整球墨铸铁的力学性能,以适应多种不同工况条件的要求。
除等温淬火球墨铸铁和高镍奥氏体球墨铸铁外,常规的球墨铸铁目前已有十多种牌号,抗拉强度可以在350 MPa~900 MPa之间改变,最低伸长率则可相应地在22%~2%之间改变。
QT450-10、QT500-7、QT550-5和QT600-3等牌号的球墨铸铁件,都由控制基体组织中铁素体与珠光体所占的份额,以确保力学性能符合要求。
一般说来,生产这类球墨铸铁件时,应力求通过控制铸铁的化学成分和生产过程中的各项工艺条件,使铸件的铸态组织符合要求,以避免费时、耗能的热处理工序。
在工艺控制不足以确保铸铁的强度的情况下,加入少量铜、镍之类的合金元素,也是常用的应对措施,但是,这样做,既提高了生产成本,还要耗用珍贵的资源。
随着对球墨铸铁认识的逐渐深化,十多年前,欧洲就开始注意到硅在球墨铸铁中强化铁素体的作用,瑞典的研究工作发现:用途很广的500-7牌号球墨铸铁中,将硅含量提高到3.5%,基体组织全部是铁素体,不仅可以在保持抗拉强度在500 MPa的条件下提高伸长率,更为重要的是,铸件的硬度均匀、切削性能显著改善。
在此基础上,国际标准ISO 1083《球墨铸铁分类》2004年修订时,补充了一项“高硅球墨铸铁”的牌号JS500-10。
欧洲标准EN 1563《球墨铸铁件》2011年修订时,补充了3项“固溶强化铁素体球墨铸铁”牌号,见表2。
2012年,德国Herbert Löblich发表了有关硅固溶强化的铁素体球墨铸铁力学性能的研究报告。
2013年,日本九州大学和日之出水道机器公司技术开发部也对此进行了试验研究。
三、硅固溶强化球墨铸铁的力学性能近年来,关于硅固溶强化球墨铸铁的力学性能,已经发表了不少研究报告。
目前见到的文献资料中,日本九州大学和日之出水道机器公司提供的数据比较全面,在这里简要地介绍给大家,供参考。
试验中,熔炼两种珠光体-铁素体球墨铸铁(QT1,QT2),两种高硅铁素体球墨铸铁(SiQT1,SiQT2),铸造厚度30㎜、高50㎜、长200㎜的U-型试块,然后制成试样,测定力学性能。
QT、QT2相当于QT500-7和QT600-3。
SiQT1和SiQT2则是在二者是基础上提高硅含量,并相应地调整碳含量和其他成分。
1、球墨铸铁的成分和金相组织高硅球墨铸铁中,相应地降低碳含量,使碳当量大致相当。
常规球墨铸铁QT1和QT 中,加有少量的铜,并稍稍调高锰含量,以使组织中的珠光体含量符合要求。
4种球墨铸铁的化学成分见表3,试样金相组织的要点见表4,金相图片见图1。
表4 4种球墨铸铁试样金相组织的要点图1 试样的金相组织2、抗拉强度、屈服强度和伸长率为了了解各种球墨铸铁抗拉强度与伸长率的关系,进行了大量的拉伸性能测试。
常规球墨铸铁取了90种试样,其抗拉强度在400~700 MPa之间,铜含量和锰含量也稍有差别;高硅球墨铸铁取了19种试样,抗拉强度在500~600 MPa之间,硅含量在3.3~4.65%之间。
抗拉强度与伸长率的关系见图2,屈服强度与伸长率的关系见图3。
图2和图3中,黑点是常规球墨铸铁的数据,空白点是高硅球墨铸铁的数据。
为了与现行标准的要求比较,两图中的小方块是标准规定的抗拉强度、屈服强度和伸长率的最低值,其间还有联有曲线,落在曲线右方的数据都符合标准要求。
图2 几种球墨铸铁抗拉强度与伸长率的关系图3 几种球墨铸铁0.2%屈服强度与伸长率的关系由图2可见,在抗拉强度相同的条件下,高硅球墨铸铁的伸长率比常规球墨铸铁高。
由图3可见,在伸长率相同的条件下,高硅球墨铸铁的屈服强度比常规球墨铸铁高得多。
图4表示几种球墨铸铁抗拉强度和屈服强度的关系。
由图4可见,在抗拉强度相同的条件下,高硅球墨铸铁的0.2%屈服强度比常规球墨铸铁高得多,硅的固溶强化作用使球墨铸铁的屈强比大为提高。
图4 几种球墨铸铁抗拉强度与0.2%屈服强度的关系3、疲劳特性就表3所列的4种球墨铸铁进行了旋转弯曲疲劳试验,应力振幅与断裂循环次数的关系见图5。
硅固溶强化的球墨铸铁,疲劳极限高于常规的球墨铸铁。
图5 4种球墨铸铁的S-N曲线4、冲击韧性为了了解硅固溶强化对球墨铸铁冲击韧性和脆性转变的影响,就SiQT1和QT1两种球墨铸铁,测定了标准试样在不同温度下的冲击吸收能量。