Cu含量对耐海水腐蚀不锈钢组织与性能的影响
化学成分对不锈钢的组织和性能的影响
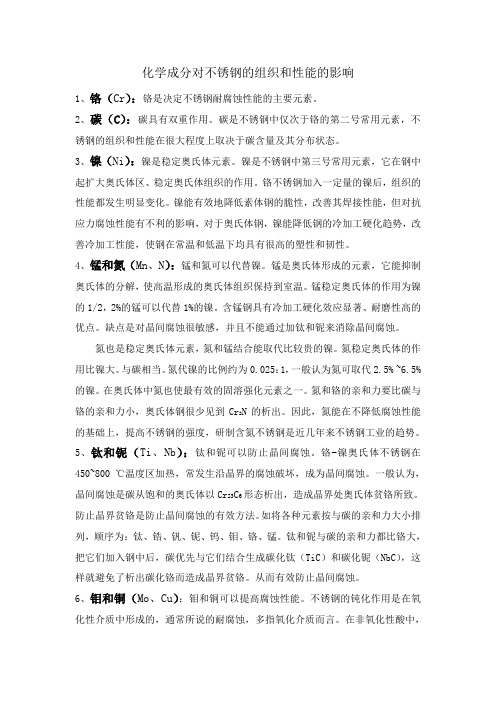
化学成分对不锈钢的组织和性能的影响1、铬(Cr):铬是决定不锈钢耐腐蚀性能的主要元素。
2、碳(C):碳具有双重作用。
碳是不锈钢中仅次于铬的第二号常用元素,不锈钢的组织和性能在很大程度上取决于碳含量及其分布状态。
3、镍(Ni):镍是稳定奥氏体元素。
镍是不锈钢中第三号常用元素,它在钢中起扩大奥氏体区、稳定奥氏体组织的作用。
铬不锈钢加入一定量的镍后,组织的性能都发生明显变化。
镍能有效地降低素体钢的脆性,改善其焊接性能,但对抗应力腐蚀性能有不利的影响,对于奥氏体钢,镍能降低钢的冷加工硬化趋势,改善冷加工性能,使钢在常温和低温下均具有很高的塑性和韧性。
4、锰和氮(Mn、N):锰和氮可以代替镍。
锰是奥氏体形成的元素,它能抑制奥氏体的分解,使高温形成的奥氏体组织保持到室温。
锰稳定奥氏体的作用为镍的1/2,2%的锰可以代替1%的镍。
含锰钢具有冷加工硬化效应显著、耐磨性高的优点。
缺点是对晶间腐蚀很敏感,并且不能通过加钛和铌来消除晶间腐蚀。
氮也是稳定奥氏体元素,氮和锰结合能取代比较贵的镍。
氮稳定奥氏体的作用比镍大。
与碳相当。
氮代镍的比例约为0.025:1,一般认为氮可取代2.5% ~6.5%的镍。
在奥氏体中氮也使最有效的固溶强化元素之一。
氮和铬的亲和力要比碳与铬的亲和力小,奥氏体钢很少见到Cr2N的析出。
因此,氮能在不降低腐蚀性能的基础上,提高不锈钢的强度,研制含氮不锈钢是近几年来不锈钢工业的趋势。
5、钛和铌(Ti、Nb):钛和铌可以防止晶间腐蚀。
铬-镍奥氏体不锈钢在450~800 ℃温度区加热,常发生沿晶界的腐蚀破坏,成为晶间腐蚀。
一般认为,晶间腐蚀是碳从饱和的奥氏体以Cr23C6形态析出,造成晶界处奥氏体贫铬所致。
防止晶界贫铬是防止晶间腐蚀的有效方法。
如将各种元素按与碳的亲和力大小排列,顺序为:钛、锆、钒、铌、钨、钼、铬、锰。
钛和铌与碳的亲和力都比铬大,把它们加入钢中后,碳优先与它们结合生成碳化钛(TiC)和碳化铌(NbC),这样就避免了析出碳化铬而造成晶界贫铬。
Cu_Ni合金海水腐蚀行为研究进展

第9卷第1期 1997年1月 腐蚀科学与防护技术CORROSION SCIENCE AND PROTECTION TECHNOLOGY V ol.9N o.1Jan.1997Cu-Ni合金海水腐蚀行为研究进展朱小龙 林乐耘 雷廷权1(北京有色金属研究总院北京100088)(1哈尔滨工业大学哈尔摈150001)摘 要 综述了Cu-N i合金在海水中材料因素和海水环境及其对腐蚀行为的影响.阐述了该合金海水腐蚀热力学和化学成分、微观组织结构、初始表面状态与耐蚀性的关系;并讨论了海水的物理因素(流速、温度)、化学因素(溶解氧、硫化物)和生物因素及其协同效应对Cu-N i合金腐蚀过程的影响.关键词 Cu-N i合金,海水腐蚀,材料特性,海水环境.学科分类号 T G172.5Cu-Ni合金广泛应用于海洋工程中各类舰船的冷凝器管、滨海发电厂的热交换器以及海水淡化处理设备的管道系统等.虽然这种合金进入实际应用已有几十年历史,但是该合金在服役过程中曾发生过严重腐蚀和泄漏事故.因此,人们对Cu-Ni合金海水腐蚀进行了大量研究,由于涉及因素错综复杂,迄今为止Cu-Ni合金的腐蚀机理及如何有效控制尚不完全清楚.随着海洋的不断开发和Cu-Ni合金应用范围的日益拓宽,人们越来越重视研究该合金在海水中耐蚀性以及发掘其潜力,从而延长使用寿命,防止早期失效,充分服务于海洋工程.本文综述了Cu-Ni合金海水腐蚀研究结果,试图从材料本性探讨该合金的腐蚀规律以及这方面研究的发展趋势;还从海水环境方面综述Cu-Ni合金的耐蚀性与海水环境的关系以及影响该合金腐蚀的海水因素.1Cu-N i合金海水腐蚀的材料本性1.1合金海水腐蚀热力学Efird[1]采用电化学方法建立了90Cu-10Ni和70Cu-Ni合金在海水中电位-pH图,电位-pH图可分为免蚀区、腐蚀区、钝化区和脱合金成分敏感区.随着镍含量从10%增至30%,腐蚀与钝化转变线的位置从pH8.5移至pH7.8,一价铜离子和二价铜离子转变也由+0.030V 移至0.070V(SCE).在腐蚀区,脱合金腐蚀为层型;在钝化区,脱合金腐蚀主要发生在缝隙处呈塞型.还应指出这两种合金均位于析氢平衡线上方,这表明合金不能通过H+还原作为阴极反应进行腐蚀,然而当含有硫化物时,合金腐蚀电位负移,这时阴极过程可通过析氢反应进行[2].金属腐蚀与防护国家重点实验室项目,国家自然科学基金资助项目 收到初稿:1996-01-12,收到修改稿:1996-04-15Fig .1Po lar ization cur ves o f Cu-N i alloy s in N aCl solut ion (pH 8.1,scan r ate :0.5mv ・s -1)[3]1.2影响腐蚀行为的材料因素1.2.1化学成分 Crouiser 和Beccaria研究了Cu -Ni 合金随Ni 含量变化在NaCl溶液中的电化学行为[3].结果表明,Cu-Ni合金与纯Cu 的极化曲线主要差异在于阳极极化部分出现一个电流平台,随着Ni 含量增加,电流平台降低,当N i 含量达到30%时,合金的平台电流值与纯Ni 的钝化电流接近(图1).在Ni 含量为10%时,合金的电流平台较宽,表明合金钝态性能稳定,这可能是Cu-Ni 合金含Ni 量为30%和10%的原因.添加0.5~2%Fe 可以显著改善Cu -Ni 合金耐海水腐蚀性能,特别是抗流动海水冲击腐蚀性能.Efir d [4]对不同Ni 和Fe 含量的Cu-Ni 合金在静态和高速流动海水中进行腐蚀试验发现,未添加Fe 的合金形成的腐蚀产物中氧含量高;添加一定量Fe 的合金所形成的腐蚀产物中富Ni.70Cu-30Ni 合金添加0.5~2.0%Fe 明显改善流动海水中耐蚀性,并且在静态海水中也得到证实[5].通常,无论是70Cu-30Ni 还是90Cu -10Ni 合金均添加一定量Fe .添加少量的Fe 有益于耐蚀性,其作用存在两种观点.固溶态铁的作用在于形成含水氧化铁的腐蚀产物膜,这种化合物充当阴极抑制剂.North 和Pry-or [6]认为另一种机制可能起作用,至少起部分作用,他们证实了Ni 能够掺杂到缺陷的Cu 2O 点阵中,因此增加腐蚀产物膜的阳极(离子)和阴极(电子)阻力,并认为Fe 具有相同的效应.70Cu-30Ni 合金与90Cu-10Ni 合金在海水中腐蚀行为尚存在不同看法.用于冷凝器的70Cu -30Ni 合金比90Cu -10Ni 合金能耐流速更高的海水腐蚀;然而,70Cu -30Ni 合金对局部高温区点蚀较敏感,90Cu-10Ni 合金在相对较高温度下服役较为有利.M acdonald 等[7]发现,只要氧浓度不超过6.60mg ・L -1,70Cu-30Ni 合金在流速为1.2m ・s -1海水中比90Cu-10Ni 合金耐蚀性好;铸态70Cu -30Ni 合金在相对较高流速12.2m ・s -1海水中耐蚀性低于90Cu -10Ni 合金;70Cu-30Ni 合金在流动海水中局部腐蚀敏感性远高于90Cu-10Ni 合金;70Cu-30Ni 管在硫化物污染的海水中失效率低于90Cu-10N i 管.这两种合金均对硫化物诱发点蚀倾向敏感,然而导致70Cu-30Ni 合金所需的硫化物浓度更高,长期暴露在硫化物浓度较低的海水中90Cu -10Ni 合金腐蚀比70Cu -30Ni 合金严重.M n 能显著提高Cu-Ni 合金抗冲击腐蚀性能,并且当Fe 含量比较低时,M n 能起到替代Fe 的作用;Mn 还能消除Cu-Ni 合金中过剩C 的影响[8].近年来发展了一种含2%Fe 、2%Mn 耐高速流动海水的70Cu -30Ni 合金.1.2.2微观组织结构 从相图上看,Cu-Ni 合金为无限互溶的连续固溶体.但在322℃以下,该合金存在一个产生亚稳分解的成分-温度区域.当添加某些合金元素如Fe 、Mn 等将改变亚稳分解的成分-温度区域的大小和位置[8].Fe 在Cu -Ni 合金中的溶解度很小,通常70Cu -30Ni 合金中Fe 溶解量约为0.5~1.0%,90Cu -10Ni 合金中Fe 溶解量约为1.0~491期朱小龙等:Cu -Ni 合金海水腐蚀行为研究进展50腐蚀科学与防护技术9卷1.5%.当Fe完全固溶时,合金表现出良好的耐蚀性;若合金出现沉淀态的Fe,所形成的腐蚀产物无Ni的富集且颜色变暗[4].此外,还可能导致Cu-Ni合金在氨环境下耐应力腐蚀性能下降.Cu-Ni合金在一定条件下沉淀析出极小的Ni-Fe富集相,该Ni-Fe富集相不仅明显影响合金的强度,而且降低合金的耐蚀性.Richter和Pepperhoff[9]应用M ossbauer谱探测到缓冷处理的70Cu-30Ni和90Cu-10Ni合金的Ni-Fe颗粒,其中Ni含量约为60%~70%.Drolenga 等[10]系统研究了90Cu-10Ni合金化学成分和微观组织结构对耐蚀性影响,发现固溶处理后在600℃或650℃退火时,合金产生连续沉淀,导致硬度和磁透率增加.仅当退火时间超过100h,才可能在电镜下观察到这种沉淀物;合金在450℃退火时在晶界析出不连续沉淀物.在海水中长时间暴露结果表明:90Cu-10Ni合金为均匀固溶体时腐蚀电位在活化方向略有变化,R-1p值低且稳定,随铁量增加而增大;连续沉淀的合金腐蚀电位在活化方向出现一个电位跃迁,在某些情况下,电位跃迁之后观察到强烈的电位波动,R-1p在含Fe为2.0%和2.5%时达到最大;在晶界上存在不连续沉淀物的合金腐蚀电位在活化方向出现一个电位跃迁,并且R-1p值始终较高且与含Fe量无关,还表明不连续沉淀的90Cu-10Ni合金形成的黑色腐蚀产物膜厚且多孔疏松而易脱落,其下为桔黄色晶体,Efird[4]发现自由腐蚀电位基本在-200至-250m V之间,而与微观组织结构和Fe量(< 3.5%)无关.Cu-N i合金沉淀相析出的条件尚不清楚,目前尚未找到有效地抑制Cu-Ni合金沉淀特别是不连续沉淀发生的途径.1.2.3初始表面膜 Cu-Ni合金在海水中耐点蚀能力取决于初始表面状态或服役条件.对于表面状态的影响,在生产过程中最终光亮退火形成残留碳膜或富锰氧化膜被认为是有害的.Marsde分析了Cu-Ni热交换器管早期失效并指出加工过程中的润滑剂在退火时分解为残留的碳膜,该碳膜相对于Cu为阴极,导致点蚀[11].较普遍观点认为碳膜是有害的,但富锰的氧化膜并不是点蚀的原因,因为富锰的氧化膜在氯化程度较高的海水中相对合金基体为强阴极,使沉积物周围或其下产生局部腐蚀,然而这种氧化膜通常在海水中随时间而消失.管表面有M nO或经喷砂处理后的点蚀敏感性均较低[12].特殊的服役条件对铜合金海水腐蚀影响较大,如海水过氯化.Gusmano和Trav ersa[13,14]研究70Cu-30Ni合金在流动海水中的腐蚀行为,他们指出初始富锰膜本身并不导致局部腐蚀,而海水过分氯化才是局部腐蚀的原因.对于中等氯化海水,自由Cl2量不超过0.5mg/L,该合金耐局部腐蚀性能良好,且与初始表面膜无关.当自由Cl2量为0和1.3m g/L时,该合金耐局部腐蚀性能均较差.至今较普遍认为初始表面的富锰膜不是Cu-Ni合金管局部腐蚀的原因.2Cu-N i合金腐蚀行为的海水环境影响因素海洋是一个富有挑战性的、维持着物理、化学和生物的动平衡体系.海水环境极为复杂,它不仅含有地壳中大多数元素,而且还拥有无数有机分子和海洋生物,此外季节、潮汐和阳光等的介入进一步增加海水环境的不确定性.材料在海水中的腐蚀行为实际上是材料与海水环境相互作用的过程.海水的诸多因素直接或间接参与该过程,同时,这些因素相互作用和协同效应使腐蚀过程更加复杂.2.1物理因素2.1.1流速 Cu-Ni合金在海水中使用时存在一个相对极限流速.超过这个相对极限流速,将因冲击腐蚀而失效.Cu -Ni 合金相对极限流速受诸多因素的影响,无法精确测定.试验表明,90Cu -10Ni 合金能够承受的流速范围为2.5~3.5cm ・s -1海水冲击,该合金允许流速达4.5cm ・s -1.冲击腐蚀的机理迄今为止尚不完全清楚,已经提出的机理主要有如下三种:(1)流动海水在合金表面产生剪切应力,随着流速增加,剪切应力增加.剪切应力超过一定值使得合金表面腐蚀产物机械分离.因此,腐蚀产物膜的机械性能决定了临界流动速度,即临界流动速度对应的剪切应力略超过腐蚀产物与基体之间结合力[15].Efird [15]计算出90Cu-10Ni 和70Cu-30Ni 的临界剪切应力分别为43.1N/m 2和47.9N/m 2.临界剪切应力随管径不同而变化,管径越大,铜基合金允许海水流速越高.Sato 和Nag ata [16]发现冷凝器管入口端的剪切应力等于管内一段距离后剪切应力的两倍,这些结果解释了管道入口端经常发现冲击腐蚀.Ferrara 和Gu-das 研究了旋转园盘上平板试样的流速影响[17],这种条件,90Cu-10Ni 合金在周边速度为7.9至8.8m ・s -2之间的腐蚀速度比70Cu-30Ni 合金低得多.虽然70Cu-30Ni 合金冷凝器和热交换器对入口处的冲击腐蚀表现出很高耐蚀性,但是90Cu -10Ni 合金作为船舶的外壳所遇到海水流速更高却显示更好耐蚀性.(2)高速流动海水由于质量传输系数大,使得表面pH 值降低以及表面膜通过可溶性Cu(I)化合物扩散溶解速度增加;在侵蚀腔内,局部腐蚀形成活化-钝化电池,这种电池具有自催化效应.(3)在流动海水介质中,如果其中气泡尺寸大于界面层厚度,则气泡对保护层产生机械破坏作用.所产生的力可能破坏水力学上界面层,再加上直接局部液体冲击和保护层局部破坏等因素,使腐蚀不断发展.2.1.2温度 Francis 研究发现[18],在10℃以下,Cu-Ni 合金腐蚀速度随温度降低而增大,并认为温度下降导致了腐蚀产物膜中无Fe 富集.温度对Cu -Ni 合金腐蚀行为影响的研究结果各异,即温度升高,Cu-Ni 合金腐蚀速度减小、增加或保持不变.这些差异是由于实验条件不同造成的,包括水流、pH 值变化、溶解氧等.Wang 等[19]研究了Cu-Ni 合金在20~80℃的静态海水中腐蚀失重与时间的关系,其结果与Kato 等[20]在25℃N aCl 溶液中所得到Cu -Ni 合金腐蚀失重曲线一致,失重与时间呈抛物线关系(y =at 1/2),这表明溶解过程在整个温度范围内遵循质量传输极限机制.溶解过程速度控制步骤是Cu +和Ni 2+离子的扩散.这意味与Fe 的氧化膜覆盖能力相关的离子扩散愈慢,合金腐蚀速度亦愈低.2.2化学因素影响腐蚀过程的海水化学因素主要有盐度、溶解氧和硫化物.海水的总盐量可表示为含氯量和盐度.氯含量定义为每千克海水中氯、溴和碘的总量.假设溴和碘均用氯代替,盐度与氯量的关系为盐度S (‰)=0.03+0.1805×Cl (‰).在自然海水中,盐度在32000和36000mg /L 之间变化,氯量在18000和20000mg /L 之间随地理位置变化.Cl 在与Cu 、Fe 形成金属离子络合物时起重要作用,进而影响腐蚀过程.氯化物一方面可以降低金属氧化还原电位,从而扩大可能产生腐蚀反应的范围;另一方面它加速金属的氧化速度,如铜合金腐蚀,氯离子直接参与氧化机制.Cu ++2Cl -=CuCl 2+e-氯化物还影响腐蚀产物.在90Cu-10Ni 合金腐蚀产物分析中发现,氯离子存在于多层腐蚀产物中,并且在金属表面腐蚀层与中间膜层的界面区氯浓度最高.此外,还注意到氯浓度影响产生点蚀和缝隙腐蚀的临界电位及其发展速度,还可能影响保护电位.通常随氯量降低,临界点蚀电位增加,而点蚀速度减小.511期朱小龙等:Cu -Ni 合金海水腐蚀行为研究进展正常海水pH 值在7.8~8.3范围内,一般pH 值在该范围内变化对腐蚀过程影响不大.2.2.1溶解氧 海水中溶解氧量主要决定于盐度和温度.若知绝对温度T (K )和盐度S (‰),就可以计算出溶解氧的平衡浓度.溶解氧对Cu-Ni 合金腐蚀的影响可以用Evans 图来描述(图2)[21].阴极反应: 1/2[O 2]+[H 2O]+2e =2[OH -] ,线AB 表示吸附的氧;阳极反应: 2Cu=2Cu +sol +2e ,线CD 表示不发生钝化时阳极过程.Fig .2Cor ro sion behaviour of co pper -nickel alloy s in aer at-ed and de -aer ated seawat er [21]Cu -Ni 合金浸在充气海水中很快形成一层保护性腐蚀产物:2Cu +sol +2[OH -]=Cu 2O+[H 2O]这使腐蚀产物上产生的I R 降(斜率即阻力)从CD 线所给定的值上升到T 1线所给定的值.T 1线(钝化的阳极过程)与AB 线(阴极过程)交点相对应的腐蚀电位和腐蚀电流分别为E 1和i 1.随着暴露时间增加,腐蚀产物膜随之增厚,因此IR 降即阳极曲线斜率增加,而阴极过程不变化导致腐蚀电位增加,腐蚀电流下降.最终当IR 降充分大时,以致使腐蚀电位达到E Cu 2O/Cu 2(OH)3Cl ,这时外层腐蚀产物Cu 2(OH)3Cl 形成即2[Cu 2+sol ]+3[OH -]+Cl -=Cu 2(OH )3Cl .Cu-Ni 合金腐蚀速度依赖于海水中溶解氧[22].在除气的海水中,腐蚀速度基本为零.这是由于阴极过程缺氧而只可能通过析氢反应进行:2[H +]+2e =H 2,该过程用线EF 表示.EF 与CD 交点对应的腐蚀电位E 2和腐蚀电流i 2较充气海水中腐蚀电位E 1和腐蚀电流i 1低得多.i 1在未污染近乎中性水中很低,相应的腐蚀速度基本为零.在实际体系中,除气海水的腐蚀电位和电流受痕量氧和其他的还原性物质控制.Cu-Ni 合金在流动海水中腐蚀行为在某种程度上也可以用上述模型解释.M acdonald 等[7]发现当氧含量保持在空气溶解度或低于6.60m g/L 时,70Cu-30Ni 合金显示出比90Cu-10Ni 合金更优的耐蚀性,在氧含量较高的条件下,镍含量高的合金耐蚀性出现迅速下降,在氧溶解度[O 2]=26.3mg /L 时,合金的耐蚀性与镍量无关.2.2.2硫化物 硫化物进入海水中途径较多如腐烂的动植物、工业废弃物、自然产生硫酸盐细菌还原等.在完全无氧的情况下,海水中的硫化物使Cu-Ni 合金腐蚀电位向活化方向迁移.在活化电位时,阴极反应依赖于氢离子还原,因此,即使在无氧时,腐蚀反应仍能进行.Cu-N i 合金在硫化物污染海水中的腐蚀行为可以用Evans 图来描述(图3)[21].在除气、硫化物污染海水(DS -Seaw ater )和在充气、硫化物污染海水(AS -Seaw ater )中腐蚀机理讨论如下:在DS 海水中,线IJ 描述的阴极反应与在无污染除气海水中的速度较低的阴极反应相同,即氢离子的还原.阳极反应亦与无污染除气海水中相似,即Cu +形成.然而,在DS 海水中阳52腐蚀科学与防护技术9卷极反应(线AB ′)移至更低电位(线CD),这种迁移是因为Cu +sol 离子与S 2-sol 离子反应沉积使离子活度降低.2[Cu +sol ]+[S 2-sol ]=Cu 2S该硫化亚铜膜为多孔、非保护性腐蚀产物、并且沉积于金属表面.当存在1g ・m -3[S 2-]时,Cu 浓度从向9×10-10降至5×10-12mo l/L.根据Nernest 方程计算,相应腐蚀电位下降值超过600m V.这使得腐蚀电流(i 3)比除气、无污染、海水中腐蚀电流(i 2)大得多.但是污染海水中腐蚀电位(E 3)却比除气、未污染海水中相应腐蚀电位(E 2)低得多.Cu -Ni 合金在海水中不能形成保护性产物,所以腐蚀电流和腐蚀电位应保持相对稳定.然而腐蚀电流和腐蚀电位依赖于海水中S 及O 的介入,S 和O 的含量均难以控制从而导致腐蚀电流和腐蚀电位出现小波动.Fig .3Co rr o sion beha vio ur o f co pper -nickel a lloy s in aerat ed and de-aeraed sulphide -po lluted seaw ater [21]在AS 海水中,Cu -Ni 合金腐蚀速度最高.硫化物与氧共同加速Cu-Ni 合金腐蚀,如前所述,在充气海水中,合金形成保护性腐蚀产物,阳极反应遵循线A'B,如果不存在保护性腐蚀产物,阳极反应遵循AB'线,阳极反应与阴极反应(线EF'交点处腐蚀电流(i 4)很大.Cu -Ni 合金在硫化物存在时不能形成保护性腐蚀产物膜[22],硫化物还与Cu +离子反应降低腐蚀产物与金属的界面上Cu +离子的浓度,从而使阳极曲线从线AB'降至线CD .此外,硫化物还与氧反应从线EF 移至线GH.阴极过程(线GH )与阳极过程(线CD )交点对应腐蚀电位E 5处的腐蚀速度很高(i 5),腐蚀电位E 5位于DS 海水腐蚀电位之间.由于硫化物阻碍保护性腐蚀产物膜形成,腐蚀速度始终维持较高.硫化物在海水中的浓度不稳定,特别是当O 2存在时,在充气海水,硫化物的半寿命仅20min [22].海水中铜离子增大溶解氧对硫化物氧化的速度,硫化物的氧化产物有S (S 0)、S 2O 3(S +2)、S 4O 6(S +2.5)、SO 3(S +4)、SO 4(S +6)以及多硫化物.Latimer 氧化-还原电位描述了一些硫化物与其平衡氧化-还原电位(E i=0)关系:S -2=-+0.51V -S 0-+0.74V -S +32O =3-+0.58V -S +4O +0.66V+0.59V =3 -+0.98V -S +6O =4531期朱小龙等:Cu -Ni 合金海水腐蚀行为研究进展54腐蚀科学与防护技术9卷Haffmann指出在硫化物较低的溶液中,硫化物氧化速度可用下式表示[23]:=K[Cu2+][HS-]式中[Cu2+]和[HS-]表示Cu(Ⅱ)和硫化物离子的浓度,K为常数.在硫化物离子浓度较高时,反应动力学则不同.Hoffm ann证实铜离子与硫化物反应动力学具有不重现性[23].因此,硫化物浓度低或高所遵循的反应动力学不同以及反应动力学的不重现性增大了研究硫化物对Cu-Ni合金腐蚀影响复杂程度,可能是得到不同实验结果的原因.硫化物加速Cu-Ni合金海水腐蚀特别是局部腐蚀愈来愈受到重视.2.3生物因素海生物是海水环境的特征之一.生物因素主要海生物可分为宏观生物如藤壶、牡蛎和石灰虫等以及微生物如细菌.Cu-Ni合金具有良好抗海生物附着的性能.Efir d在Nor th Caroli-na Wr ig ht海滩试验发现[24],90Cu-10Ni和70Cu-30Ni合金经过3a暴露才有轻微宏观海生物附着,经过5a暴露,90Cu-10N i合金所附着的海生物占表面70%,70Cu-30Ni合金附着量达整个表面60%.宏观海生物对腐蚀过程的影响主要通过如下几个方面:(1)阻碍金属表面海水流动,同时增加局部紊流;(2)对金属表面供氧起屏蔽作用,从而形成充气电池;(3)海生物分泌的产物参与腐蚀过程;(4)腐烂的海生物产生硫化物,从而改变金属表面环境.海水微生物影响腐蚀可分为两种情况,一是与腐蚀表面不直接接触的微生物产生化学中间体引起的腐蚀;二是在金属/生物膜界面上的生物膜中产生的化学物质引起微生物诱发腐蚀.微生物最初在Cu-Ni合金上附着的是抗铜能力强的细菌、硅藻和原生动物类[25,26].附着的细菌和硅藻可以改变合金表面的毒性,这样使耐铜能力低的微生物能够附着上去.在Cu-Ni合金海水管道系统中,还发现在缝隙、闭塞处、接缝不规则或焊接处有硫酸盐还原菌存在. Gam ez等[27]研究了厌氧菌、硫酸盐还原菌和需氧菌单独及共存是70Cu-30Ni合金和90Cu-10Ni合金腐蚀行为.海水中的微生物可以改变金属与溶液界面性质,从而影响腐蚀过程,主要途径如下:(1)形成界面扩散障碍层;(2)改变细菌群下腐蚀产物结构特性;(3)形成生物膜与腐蚀产物混合层-层结构,改变腐蚀产物粘附力;(4)产生腐蚀性代谢物,这些代谢物降低氧化物层的保护性.海生物的附着过程及与Cu-Ni合金之间的作用机理方面的研究很不够,主要原因是涉及的因素较多,过程复杂及多因素的协同效应,从而使整个腐蚀过程变得错综复杂.这方面尚有待进一步研究.参考文献1E fird K D.Corrosion,1975,31(3),772M acdonald D D,Syrett B C,W ing S S.Corrosion,1979,35:3673C rousier J,Beccaria A.W erks toffe und Korrosion,1990,41:1854E fird K D.Corrosion,1977,33:3475Beccaria A M,Crous ier J.Br.C or rosion J.,1991,26(3):2156North R F,Pryor M J.Corros.S ci.,1970,10:297M acdonald D D,Syrett B C,W ing S S.Corrosion,1978,34:2898苗善慧.铜加工,1990,(4):839Rich ter F,Pep perhoff W.Z.M etallkde,1983,74:50010Drolenga L J P,J sseling F P I,et al.W erks toffe und Korrosion ,1983,34:16711M orsden D D.M aterials Performance,1978,17:912Nagata K,Atsu mi T ,Yon emits u M .S umitomo L ight M etal T echnical Rep orts ,1992,33(4):2013Gus man o G ,T ravers a E ,Simoncelli C ,et al .M aterials Chemis try and Ph ysics ,1990,24:45714Gus man o G ,S imoncelli C ,Valota N M ,et al .Desalina 1989,74:25915E fird K D.Corrosion,1977,33(1):316Sato S,Nagata K.Sum itomo Light M etal T echnical Reports,1978,19(3~4):8317Ferrara R J ,Gudas J P.Proc.3rd Int.Cong.M arine Corr os.and Fouling ,1972,October.18Francis R.Br.Corros ion J.,1983,18:3519W ang Y Z ,Beccaria A M ,Pogg i G .C orros .Sci .,1994,36(8):127720Kato C,Castle J E,Ateya B C ,et al.J.Electroch emical S oc.,1980,127:189721Eisels tein L E ,S yr ett B C,Wing S S,et al.C or ros.Sci.,1983,23:223.22S yrett B C.Corros.Sci.,1981,21:18723Glas stone S.T extbook of Phys ical Chemistry.New Yor k,NY:D.Van Nostrand Co.Inc.,1940.110424Hoffmann M R ,Environ .Sci .T ech .,1980,14:106125Efird K D.Int.C onf.Corros ion '75,Toronto,Ont.,NACE ,1975,12426Videla H A,de M ele M F L,Br ank vich G B.Corrosion/89,291,(Hous ton ,TX:NACE,1981)27Gom ez de Saravia S G,de M ele M F L,Videla H A .Corros ion ,1990,46(4):302REVIEW ON CORROSION BEHAVIORS OFCu -Ni ALLOYS IN SEAWATERZHU Xiao long ,LIN Ley un ,LEI Tingquan 1(General Resear ch I nstitute f or N on -f err ous M etals ,Beij ing 100088)(1H ar bin I ns titute of T echnology ,H ar bin 150001)ABSTRACT T he cor rosion behav ior o f Cu-Ni alloy s in seaw ater is r ev iew ed in ter ms of pa-rameters related w ith the allo ys and envirom ent .T he relatio n is revealed of the co rrosio n r e-sistance and materials characteristics ,w hich include the cor rosio n ther modynam ics ,chemical co mpo sitions,micr o-structure and initial surface o f the allo ys,T he influences o f physical factors (e.g.flo w velocity ,temper ature),chemical factors (e.g.disso lved oxy gen,sulfide),bio logical factors o f seaw ater and their synerg istic action on cor rosion of Cu -Ni alloy s are dis-cussed.KEY WORDS Cu-Ni allo y ,seaw ater co rrosion,material charateristics,seaw ater enviro n-ment 551期朱小龙等:Cu -Ni 合金海水腐蚀行为研究进展。
铜元素对不锈钢耐腐蚀性的影响

铜元素对不锈钢耐腐蚀性的影响
在⽇本,随着Cu-Nb的18Cr铁素体不锈钢的开发,铜元素对铁素体不锈钢的耐⼤⽓腐蚀性的影响特加别的⼤。
含铜不锈钢经森源牌不锈钢钝化液钝化处理后可达1500⼩时以上盐雾测试不⽣锈蚀。
有⼈研究了铜元素对19Cr-0.5Cu-Nb钢耐锈性的影响。
即使添加Cu,⽣锈点也不会变⼤,只是⼀部分有所停⽌,加上Cu有利于钝态的稳定化,所以不仅在受CI离⼦影响很强的沿海地区,⽽且在⼯业地带的SO2环境当中,也具有⼀定的耐锈性。
对于有特殊要求做防腐处理的不锈钢,建议⽤森源环保不锈钢钝化液钝化防锈。
若Cr含量增加,其耐⼤⽓腐蚀性也会增强,⽽且当BA材料的表⾯的Cu元素浓度较⼤时候,锈难以向两边扩展,证明了耐锈性很好。
特别是对于铁素体不锈钢,铜元素当初是为了提⾼耐⼤⽓腐蚀性替代钼元素⽽添加的,但证实了铜的耐蚀性效果是⾮常⼤的。
森源牌铁素体不锈钢钝化液,环保,操作简单,可循环利⽤,有效节约成本。
不锈钢海水的腐蚀研究
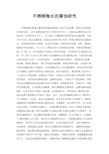
不锈钢海水的腐蚀研究不锈钢保护膜海水腐蚀原理腐蚀原理浸入海水中的金属,表面会出现稳定的电极电势)。
由于金属有晶界存在,物理性质不均一;实际的金属材料总含有些杂质,化学性质也不均一;加上海水中溶解氧的浓度和海水的温度等,可能分布不均匀,因此金属表面上各部位的电势不同,形成了局部的腐蚀电池或微电池。
电势较高的部位为阴极,较低的为阳极。
电势较高的金属,如铁,腐蚀时阳极进行铁的氧化:?Fe→Fe 2e释放的电子从阳极流向阴极,使氧在阴极被还原:?O 2HO 4e→4OH氢氧离子经海水介质移向阳极,与亚铁离子生成氢氧化亚铁:?Fe 2OH→Fe(OH)它易与海水中的溶解氧反应生成氢氧化铁。
后者经部分脱水成为铁锈FeO?HO,它的结构疏松,对金属的保护性能低。
电势较低的金属,例如镁,被海水腐蚀时,镁作为阳极而被溶解,阴极处释放出氢。
当电势不同的两种金属在海水中接触时,也形成腐蚀电池,发生接触腐蚀。
例如锌和铁在海水中接触时,因锌的电势较低,腐蚀加快;铁的电势较高,腐蚀变慢,甚至停止。
工业用的大多数金属,金属状态不稳定,在海水中有转变成化合物或离子态物质的倾向。
但是金和铂等贵金属,金属状态稳定,在海水中不发生腐蚀。
海洋环境对金属腐蚀的影响金属在海水中的腐蚀,影响因素很多,包括化学、物理和生物等因素。
化学因素①溶解氧。
海水溶解氧的含量越多,金属的腐蚀速度越快。
但对于铝和不锈钢一类金属,当其被氧化时,表面形成一薄层氧化膜,保护金属不再被腐蚀,即保持了钝态。
此外,在没有溶解氧的海水中,铜和铁几乎不受腐蚀。
②盐度。
海水含盐量较高,其中所含的钙离子和镁离子,能够在金属表面析出碳酸钙和氢氧化镁的沉淀,对金属有一定的保护作用。
河口区海水的盐度低,钙和镁的含量较小,金属的腐蚀性增加。
海水中的氯离子能破坏金属表面的氧化膜,并能与金属离子形成络合物,后者在水解时产生氢离子,使海水的酸度增大,使金属的局部腐蚀加强。
③酸碱度。
用pH值表示。
海洋环境下不锈钢管道腐蚀机理分析及防腐研究

海洋环境下不锈钢管道腐蚀机理分析及防腐研究本文就复杂海洋环境下不锈钢管道腐蚀原因进行综合分析,重点分析高湿度海风及盐雾中氯离子对不锈钢管道表面腐蚀破坏的机理,并提出几种防腐措施,为以后同类工程的实施提供有效的解决办法。
标签:海洋环境;氯离子;表面腐蚀;防腐措施1 前言某海岛输电工程项目中,采用0Cr18Ni9Ti不锈钢无缝管道进行水系统输送。
室外管路表面处理方式为喷砂处理。
该系统管道在投用10个月后,发现室外管道表面锈蚀比较严重,出现较多的锈迹。
现场通过对管道表面锈迹处理发现,此锈迹为浮锈,只需用拉丝布擦拭即可清除掉锈迹。
为彻底弄清室外不锈钢管道短时间产生锈蚀的原因,解决不锈钢管道运行寿命的问题。
本文就高温、高湿度、高盐分海风、盐雾、海水飞溅等复杂海洋环境下不锈钢管道腐蚀原因进行综合分析,重点分析高湿度海风及盐雾中氯离子对不锈钢管道表面腐蚀破坏的机理,并提出一些列防腐措施,为以后同类工程的实施提供有效的解决办法。
2 腐蚀原因综合分析2.1 管道化学成分分析用材质分析仪对不锈钢管道化学成分进行分析,结果表明:管道化学成分符合0Cr18Ni9Ti牌号的要求。
2.2 海洋环境下不锈钢管道腐蚀分析海洋大气环境与内陆大气环境有很多区别,对不锈钢管道腐蚀分析时,需要考虑高温、高湿度、高盐分海风、盐雾、海水飞溅等多种因素[1]。
2.2.1 高盐分海风、盐雾、海水飞溅在海洋环境下的海风、海浪比较频繁,海风引起的海浪使得海水中的大量盐液与大气混合,使得大气中还有大量盐分,而这些盐分中还有大量的氯离子,这些盐分中的氯离子具有较高的电导率,容易形成电解质溶液,在金属表面形成微电池,增强了腐蚀的活性,破坏金属表面的钝化膜。
海洋环境下在温度较高的情况下,大量的海水产生雾化现象,形成大量盐雾,而盐雾的主要成分与海水及其相似,对不锈钢管道的表面也会产生腐蚀。
产生腐蚀的主要原因还是盐雾中的大量氯离子。
盐雾对不锈钢管道表面的腐蚀的主要形式还是电化学腐蚀。
不锈钢的组织和性能
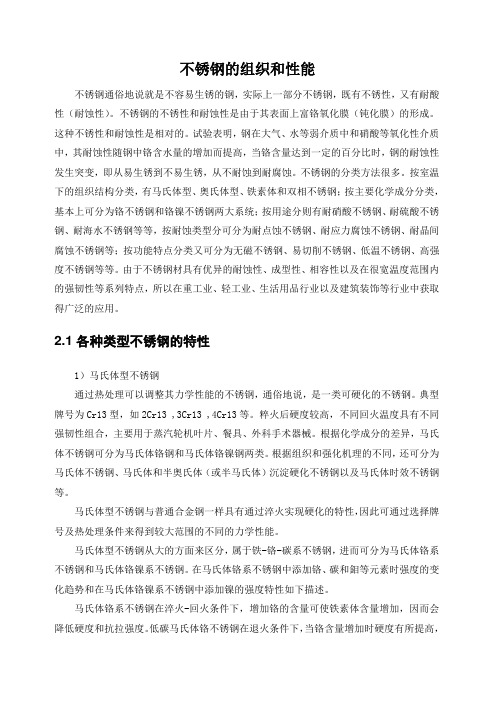
不锈钢的组织和性能不锈钢通俗地说就是不容易生锈的钢,实际上一部分不锈钢,既有不锈性,又有耐酸性(耐蚀性)。
不锈钢的不锈性和耐蚀性是由于其表面上富铬氧化膜(钝化膜)的形成。
这种不锈性和耐蚀性是相对的。
试验表明,钢在大气、水等弱介质中和硝酸等氧化性介质中,其耐蚀性随钢中铬含水量的增加而提高,当铬含量达到一定的百分比时,钢的耐蚀性发生突变,即从易生锈到不易生锈,从不耐蚀到耐腐蚀。
不锈钢的分类方法很多。
按室温下的组织结构分类,有马氏体型、奥氏体型、铁素体和双相不锈钢;按主要化学成分分类,基本上可分为铬不锈钢和铬镍不锈钢两大系统;按用途分则有耐硝酸不锈钢、耐硫酸不锈钢、耐海水不锈钢等等,按耐蚀类型分可分为耐点蚀不锈钢、耐应力腐蚀不锈钢、耐晶间腐蚀不锈钢等;按功能特点分类又可分为无磁不锈钢、易切削不锈钢、低温不锈钢、高强度不锈钢等等。
由于不锈钢材具有优异的耐蚀性、成型性、相容性以及在很宽温度范围内的强韧性等系列特点,所以在重工业、轻工业、生活用品行业以及建筑装饰等行业中获取得广泛的应用。
2.1各种类型不锈钢的特性1)马氏体型不锈钢通过热处理可以调整其力学性能的不锈钢,通俗地说,是一类可硬化的不锈钢。
典型牌号为Cr13型,如2Cr13 ,3Cr13 ,4Cr13等。
粹火后硬度较高,不同回火温度具有不同强韧性组合,主要用于蒸汽轮机叶片、餐具、外科手术器械。
根据化学成分的差异,马氏体不锈钢可分为马氏体铬钢和马氏体铬镍钢两类。
根据组织和强化机理的不同,还可分为马氏体不锈钢、马氏体和半奥氏体(或半马氏体)沉淀硬化不锈钢以及马氏体时效不锈钢等。
马氏体型不锈钢与普通合金钢一样具有通过淬火实现硬化的特性,因此可通过选择牌号及热处理条件来得到较大范围的不同的力学性能。
马氏体型不锈钢从大的方面来区分,属于铁-铬-碳系不锈钢,进而可分为马氏体铬系不锈钢和马氏体铬镍系不锈钢。
在马氏体铬系不锈钢中添加铬、碳和鉬等元素时强度的变化趋势和在马氏体铬镍系不锈钢中添加镍的强度特性如下描述。
各种元素对不锈钢的性能和组织的影响和作用

各种元素对不锈钢性能和组织的影响和作用1铬在不锈钢中的决定作用决定不锈钢性属的元素只有一种,这就是铬,每种不锈钢都含有一定数量的铬。
迄今为止,还没有不含铬的不锈钢。
铬之所以成为决定不锈钢性能的主要元素,根本的原因是向钢中添加铬作为合金元素以后,促使其内部的矛盾运动向有利于抵抗腐蚀破坏的方面发展。
这种变化可以从以下方面得到说明:①铬使铁基固溶体的电极电位提高②铬吸收铁的电子使铁钝化钝化是由于阳极反应被阻止而引起金属与合金耐腐蚀性能被提高的现象。
构成金属与合金钝化的理论很多,主要有薄膜论、吸附论及电子排列论。
2. 碳在不锈钢中的两重性碳是工业用钢的主要元素之一,钢的性能与组织在很大程度上决定于碳在钢中的含量及其分布的形式,在不锈钢中碳的影响尤为显著。
碳在不锈钢中对组织的影响主要表现在两方面,一方面碳是稳定奥氏体的元素,并且作用的程度很大(约为镍的30倍),另一方面由于碳和铬的亲和力很大,与铬形成—系列复杂的碳化物。
所以,从强度与耐腐烛性能两方面来看,碳在不锈钢中的作用是互相矛盾的。
认识了这一影响的规律,我们就可以从不同的使用要求出发,选择不同含碳量的不锈钢。
例如工业中应用最广泛的,也是最起码的不锈钢——0Crl3~4Cr13这五个钢号的标准含铬量规定为12~14%,就是把碳要与铬形成碳化铬的因素考虑进去以后才决定的,目的即在于使碳与铬结合成碳化铬以后,固溶体中的含铬量不致低于11.7%这一最低限度的含铬量。
就这五个钢号来说由于含碳量不同,强度与耐腐蚀性能也是有区别的,0Cr13~2Crl3钢的耐腐蚀性较好但强度低于3Crl3和4Cr13钢,多用于制造结构零件,后两个钢号由于含碳较高而可获得高的强度多用于制造弹簧、刀具等要求高强度及耐磨的零件。
又如为了克服18-8铬镍不锈钢的晶间腐蚀,可以将钢的含碳量降至0.03%以下,或者加入比铬和碳亲和力更大的元素(钛或铌),使之不形成碳化铬,再如当高硬度与耐磨性成为主要要求时,我们可以在增加钢的含碳量的同时适当地提高含铬量,做到既满足硬度与耐磨性的要求,又兼顾—定的耐腐蚀功能,工业上用作轴承、量具与刃具有不锈钢9Cr18和9Cr17MoVCo钢,含碳量虽高达0.85~0.95%,由于它们的含铬量也相应地提高了,所以仍保证了耐腐蚀的要求。
合金元素对钢性能的影响

合金元素
硅 (Si)
锰 (Mn)
镍 (Ni)
铬(Cr)
钼(Mo)
铝 (Al)
铜 (Cu)
对钢性能的影响 是钢中常见元素之一,在炼钢过程中用作还原剂和脱氧剂。所以钢中常含有0.20%~0.30%的硅。如果钢中硅含量超过0.50%~0.60% 时,硅就算作特殊的合金元素,这种钢就称为“硅钢” 硅能显著提高钢的弹性极限、屈服强度和抗拉强度,故可广泛用于制造重负的弹 簧钢。在凋质结构钢中,硅不仅能增加钢的淬透性,还增加钢淬火后的抗回火性。因此,常被用作调质结构钢的合金元素,并可用于制造 承受重负荷的较大截面零件的无镍铬、高强度、高韧性的高级调质钢。硅和其他合金元素如钼、钨、铬等结合,有提高钢抗腐蚀和抗高温 氧化的作用,可用于制造无镍低铬的不锈耐热钢。含硅1.0%~4.5%低碳和超低碳钢,具有极高的导磁率,可做电气制造业中的硅钢片。 在热处理时硅易于促使石墨化、产生脱碳现象,故在弹簧中,常加入钨、钒、铬等元素来加以防止。也用于制造耐磨的石墨钢或模具钢。 但钢中含硅量较高时,在焊接时喷溅较严重,有损焊缝质量,并易导至冷脆,会增加镀锌时锌对铁的破坏作用 是良好的脱氧剂和脱硫剂。因此,钢中含0.30%~0.50%的锰是经常的。在碳素钢中加入0.7%~1.8%或以上的锰时,就算是特殊钢“锰 钢”了。这种含锰量较高的碳素钢的力学性能,要比一般含锰量的好得多,不但有足够的韧性(在适当的热处理条件之下),且有较高的强 度和硬度,能提高钢的淬透性,改善钢的热加工性能。故在低合金结构钢中,含锰钢种发展十分迅速。利用锰和硫化合所生成的硫化锰 (MnS)夹杂,有使切屑易于碎断的作用。所以在钢中可加适量的锰和硫来生产易切削钢。此外,锰在合金结构钢、弹簧钢、轴承钢,工具 钢、耐磨钢、无磁钢、不锈钢、耐热钢中,也获得广泛的应用。但锰能使钢的抗腐蚀能减弱,对钢的焊接性能也有不利的影响 能使钢强化,改善钢的低温性能,特别是韧性,还可以提高钢的淬透性。镍钢的抗锈性也很强,具有较高的对酸、碱和海水的耐腐蚀能 力,但在高温高压下对氧介质的抗腐蚀能力无明显效果,反会造成脱碳促使钢腐蚀破裂 。 一般国产低合金结构钢中不加入镍。镍在高 含量时,可显著改变钢和合金的一些物理性能。但镍是一种重要的战略物资,在全世界范围内比较稀缺,所以作为钢的一种合金元素,应 该只在不能用其他元素来获得所需的性能时,才考虑使用镍。譬如需要在高强度时具有高韧性的重要用途的结构钢,在低温工作条件下具 有高韧性的钢,高合金铬镍奥氏体不锈耐热钢,以及要求具有特殊物理性能的钢等 加入钢中能显著提高钢的抗氧化作用,增加钢的抗腐蚀能力。并能提高钢的强度和耐磨性。由于铬加入钢中能改善钢的力学性能及物理和 化学性能,因此在各种用途的合金钢中,普遍含有不同数量的铬。由于目前我国铬资源较少,故因尽量节约使用,特别是在大量生产的结 构钢中,应当少用或不用铬 是一种贵重的合金元素,在我国是富产,但在整个世界范围内的储量却并不丰富。钼在钢中的作用,可归纳为提高淬透性和热强性,防止 回火脆性,提高剩磁和矫顽力,提高在某些介质中(如硫化氢、氨、一氧化碳、水等介质)的抗蚀性与防止点蚀倾向等。故在结构钢、弹簧 钢、轴承钢、工具钢、不锈耐酸钢、耐热钢(也称热强钢)、磁钢等一系列的钢种中,得到广泛的应用。铬钼钢在很多情况下,可以代替较 贵重的铬镍钢来制造各种重要的机件,由于钼增加钢的热强性,所以钼含量较高时,也会增加热加工的困难 是炼钢时的脱氧定氮剂,并且能细化钢的晶粒,提高钢在低温下的韧性,铝对氮有极大的亲和力,含铝的钢渗氮后,在钢种表面牢固地形 成一层薄而硬的弥散分布的氮化铝层,从而提高其硬度和疲劳强度,并改善其耐磨性。铝还具有耐腐蚀性和抗氧化性,可作为不锈耐酸钢 的主要合金元素。在钢的表面镀铝或渗铝,可提高其抗氧化性。 铝和铬、硅复合应用,可以显著提高钢的高温不起皮性和耐高温腐蚀能 力。铝还适用于作电热合金材料和磁性材料。但是,铝会影响钢的热加工性能、焊接性能和切削加工性能 在钢中加入0.20%~0.50%的铜,特别是和磷配合使用时,可以使低合金结构钢和钢轨钢获得优良的抗大气腐蚀性能,并且也有利于提高 钢的强度、耐磨性和屈强比,而对钢的焊接性并没有不良的影响,是目前建造桥梁、船舶、汽车、机车车辆、化工石油设备及高压容器等 的主要钢类。在奥氏体不锈钢中加入2%~3%的钢,可以提高其在酸性介质中的抗蚀性。但铜是稀缺金属之一,也是战略物资,因此一般 不应在炼制中有意地加入。不过由于钢中含铜无法从冶炼过程中去除,而我国又有丰富的含铜铁矿,所以可以利用含铜铁矿来发展含铜钢
- 1、下载文档前请自行甄别文档内容的完整性,平台不提供额外的编辑、内容补充、找答案等附加服务。
- 2、"仅部分预览"的文档,不可在线预览部分如存在完整性等问题,可反馈申请退款(可完整预览的文档不适用该条件!)。
- 3、如文档侵犯您的权益,请联系客服反馈,我们会尽快为您处理(人工客服工作时间:9:00-18:30)。
在析 出相上选择白 色区域 ( 图 3 所 示 a 点 ) 打 点, 其元素含量是 F e 、 Cr 、 N i的碳化物, 其中 C r 含量 比试样名义 C r含量稍高, 因差别较小 , 周围的贫铬区 较小, 故可获得较好的耐蚀性。在析出相颜色较深区 域打点 (图 1 所示 ) , 可以看出是 F e 与 C r 、 N i等元素 [ 8] 的化合物, 其可能由多种相组成 。此部分的 C r 含 量稍低 , 且在这两区域内没有发现 M o 元素 , 可见 M o 大部分都溶在基体中 , 这对稳定试验钢的耐蚀性有很 大帮助。 2 . 4 力学性能分析
应用与试验
∀ 机械研究与应用 ∀
*
Cu含量对耐海水腐蚀不锈钢组织与性能的影响
刘广桥 , 王克政 , 魏代刚
1 2 3
( 1. 兰州城市学院培黎职业技术学院 , 甘肃 兰州 2 . 兰州理工大学可再生能源研究院 , 甘肃 兰州
730070; 730050; 730050 )
3 . 兰州理工大学甘肃省有色金属新材料省部共建国家重点实验室 , 甘肃 兰州
表 2 不同 Cu含量的力学性能
Cu /% 抗拉强度 ( M Pa) 延伸率 ( % ) 硬度 ( HR B) 0 583 23 . 3 98 . 0 0 . 3 642 27 .1 93 .3 0. 8 605 29. 6 89. 3
2 . 2 XRD 分析 在 D /M AX - 2400 型 x 射线衍射仪上 进行衍射 分析。实验条件为: Cu 靶 K a 线 , 电压为 40kV, 衍射 范围为 20#~ 100# , 测量角度误差小于 0. 02# , 试样尺 寸为 ! 5 ! 5mm, 表面磨平。 通过 x 衍射图谱与 PDF 卡片对照分析发现试验 钢由 ∀- Fe 、 相和碳化物组成。 ∀- Fe 中有 C r 、 Ni 合金元素固溶其中。同时 F e 与部分 Cr 、 N i等合金元 素形成金属间化合物, 是强化材料的金属相 , 从而提 高材料的机械性能。在 Cu 为 0 . 3 % 时第二峰显著上 升, 由于 相 是一种强度高、 硬度大的 化合物, 使得 试验钢的抗拉强度和硬度都有不同程度的上升。但 随着 Cu 含量的增加, 相主峰先变强后变弱 , 2 号试
( 1. Lanzhou city college, sehool of p eili professional techno logy, Lanzhou Gansu 730070, China; 730050 , China; 730050, China; ) ) is 2. Lanzhou university of teehnology, renewable energy research ins titute, Lanzhou Gansu 3. S ta te key laboratory of gansu advanced non - ferrous m etalm ater ia ls , Lanzhou Gansu
[ 6] -
表 1 选用的合金元素种类 、 纯度
Fe 99. 95 Cr 99. 9 Ni 99. 8 Mo 99 . 94 Cu 99 . 95 Mn 99 . 6
( 2) 熔炼 原材料在熔炼前用超声波清洗仪进行 振荡清洗 , 每个合金锭按 60g 进行配料 , 将清洗过的 原材料在 W S- 4 非自耗电弧熔炼炉内熔炼 3 次后将 合金吸铸成直径 8mm, 长度 100mm 的圆棒合金试样。 ( 3) 固溶时效处理 将铸锭、 棒状试样在 SX6- B 箱式 电 阻 炉 中 进 行 固 溶 时 效 处 理。 固 溶 温 度 1100 、 固溶时间 2h , 时效温度 520 、 时效时间 4h 。 ( 4) 拉伸试验 将拉伸试样在 WDW - 300J型电 子万能试验机进行力学性 能测试 (拉 伸试样设计依 据: GB /T 228- 2002 金属材 料室温拉伸实 验方法 )。 试样通过 试 验机 采 集试 样的 拉 伸 曲线、 抗拉 强 度 (
如表 2 所示为 1 、 2 、 3 号试样刚固溶时效处理后 ∀ 61∀
应用与试验
∀ 机械研究与应用 ∀
的力学性能结果。如图 4 所示为抗拉强度 (
b
)、 延
量增加 , 析出相虽变的粗大, 但其并未形成连续的网 状结构 , 在拉伸过程中不会形成对基体的割裂作用, 试验钢的韧性一直增加。
伸率 ( ) 和硬度 ( H ardness) 随 Cu 含 量变化的曲线。 由图 4 可以看出, 随着 Cu 含量的增加, 试验钢的抗拉 强度先增加后下降 , 在 Cu 为 0 . 3 % 时最大。延伸率 随 Cu 含量的增加始终保持上升趋势, 在 Cu 为 0. 8 % 时最大。而硬度随 Cu 含量的增加逐渐降低 , 其在 Cu 含量为 0 % 时有最大值。
3 结
论
( 1) 在试验钢中 Cu 元素对其力 学性能有显著 影响, 其作用主要体现在二次相的析出和对晶粒形态 及大小的影响上。析出相和晶粒大小变化, 对试验钢 的抗拉强度、 延伸率和硬度有不同程度的影响。 ( 2) 试验钢中加入 Cu 时, 随着 Cu 含量的增高, 抗拉强度和硬度先增大后变小 , 当 Cu 为 0 . 3 % 时, 抗 拉强度 ( b ) 最大为 642MP a ; 硬度 (HRB ) 为 93 . 28 。 延伸率 ( ) 随 Cu 含 量的增加一直提高, 当 Cu 为 0 . 8 % 时最大值为 29 . 6 %。 ( 3) 通过 Cu 含量变化对试验钢 力学性能影响 的研究可知 , 当 Cu 含量为 0 . 3 % 时试验钢具有最优 的力学性能。因此 , 经优化后的试验钢成分为 20C r - 18N i- 6M o- 0 . 2 M n- 0 . 3Cu- 0 . 8V - 0 . 1S i 。 参考文献:
b
。笔者是在
耐点蚀性能优良的 20C r- 18N i- 6 M o- 0 . 2 Mn- 0 . [ 7] 8V - 0 . 1S i试验钢的基础上 , 以对腐蚀性能影响较 大的 Cu 元素为变量, 通过优化设计, 在上述合金的 基础上得到一种耐腐蚀性能良好、 强度高的新型奥氏 体钢 C r20N i18 M o6 M n0. 2Cu0 . 3V0 . 8S i0 . 1, 并对其力 学性能及微观组织进行了系统分析。
b
海洋开发因为可以缓解陆地资源的枯竭已成为 21 世纪研究开发的重点领域
[ 1, 2]
选用的合金元素种类、 纯度 ( w t) % 如表 1 所示。 所有合金的 C% 0 . 03 %。
/w t %
V 99 .5 Si 99. 6
。然而 , 金属材料在
海水中因 C l 及多种海生物的影响会产生严重腐蚀, 给海洋工程带来巨大的经济损失。虽然不锈钢在各 工业领域中的应用范围不断扩 大, 特别是 在海洋开 发、 石油及化工方面的应用更趋广泛。但普通不锈钢 在海水介质中 , 因 C l 与金属离子结合健较强, 因而 易侵入不锈钢表面的钝化膜, 使钝化膜受到破坏, 从 [ 3, 5] 而产生点 腐蚀、 缝隙 腐蚀 和应 力腐蚀 破裂 。因 此, 开发一种新型的具备优良的耐点蚀、 缝隙腐蚀性 能及较高强度的耐海水腐蚀不锈钢无疑有很大的经 济价值及重大的社会效 益。 Cu 是 稳定奥氏 体的元 素, Cu 加入铬镍不锈钢可以提高其在酸中及在含卤 素离子介质中 ( 如海水 ) 的耐腐蚀能力
2 试验结果及分析
2 . 1 金相分析 在 M eF3 金相显微镜下 观察固溶及时效处理后 不同 Cu 含量试验钢的显微组织。 如图 1 所示试验钢组织是奥氏体基体 + 不连续 的枝条状析出相, 是典型的树枝晶。析出相包括金属 间化合物、 碳化物 , 同时可能有 - 铁素体。但 1 号 合金枝条状析出相较细 , 在基体上不连续分布。 2 号 合金在加入 0. 3 % Cu 元素后析出相变粗, 同时枝晶 长度变短 , 枝晶粒度变小。当 Cu 含量达 0 . 8 % 时, 析 出相在晶界处变的更为粗大 , 晶粒有合并长大趋势。
b
) 为 642M pa ; 硬度 ( HRB) 为 93 . 28, 延伸率
关键词 : 耐海水腐蚀不锈钢 ; 组织 ; 力学性 能 中图分类号 : TG 142 文献标 识码 : A 文章编号 : 1006- 4414( 2009) 05- 0060- 03
Th e effect of Cu conten t on m icrostructure and p roperties of seaw ater corrosion resistence stain less steel 1 2 3 L iu Guang- qiao , W ang Ke- zhen , W e i Da i- gang
摘
要 : 借助 XRD、 SEM 等研究了 0 % ~ 0. 8% 的 Cu 对 20C r- 18N i- 6M o- 0. 2M n- 0 . 8V - 0. 1S i耐海 水腐蚀 不锈试 验钢力学性能的影响 。 结果表明 : 当 Cu 为 0. 3% 时 , 抗拉 强度 ( ( ) 为 27. 1 % , 其综合力学性能最优 。
图 2 1 号、 2 号、 3 号合金的 XRD
2 . 3 点扫描成分分析 用 EPMA - 1600 型电子探针对 2 号试验钢进行 点扫描成分分析 , 结果如图 3所示。图 3 电子探针点成分分析
图 1 不同 Cu 含量的试验钢光学金相照片
( a) 1号 ( Cu: 0% ) ; ( b) 2 号 ( Cu : 0 . 3 % ) ; ( c) 3 号 ( C u : 0 . 8% )
∀ 60∀
应用与试验
∀ 机械研究与应用 ∀
5 ! 5mm 的圆柱体, 测试前用砂纸将上下面打磨光 滑, 并保证上下面平行。使用 HRS- 150 数显洛氏硬 度计测定其洛氏硬度, 载荷为 980N。 ( 6) 实验过程 试验钢选择 C r 、 N、 iM o 、 Mn 、 V、 S i为定 值, 含 量 分别 为 20 % 、18 % 、6 % 、0 . 2 % 、0 . 8 %、 0 . 1 % , 以 Cu成分为变量 , 分别为 0 %、 0. 3 %、 0 . 8 % 。然后制备试样 , 测定其力学性能 , 确定最佳的 Cu 含量。试验钢编号如下 : 1 号 ( Cu : 0 % )、 2 号 ( Cu : 0 . 3 % )、 3 号 ( Cu : 0 . 8 % )。 样最后的铁基固溶体有两个衍射 峰消失, 只 剩一主 强峰。如图 2所示。