车磨复合加工技术在航空业的应用
举例说明复合材料在生活中的应用

举例说明复合材料在生活中的应用复合材料是由两种或两种以上的不同材料组成的,具有优良性能的新材料。
它有着广泛的应用领域,可以在生活中的许多方面得到应用。
1. 航空航天领域:复合材料在航空航天领域中得到广泛应用。
例如,飞机的机身、机翼和尾翼等部件通常采用碳纤维复合材料制造,以减轻重量,提高飞行效率和燃油经济性。
2. 汽车工业:复合材料在汽车工业中也有广泛的应用。
例如,一些高档汽车的车身和零部件采用碳纤维复合材料,以提高车辆的刚度和安全性能。
3. 建筑领域:复合材料在建筑领域中的应用也越来越多。
例如,一些现代化的建筑结构中使用的玻璃钢复合材料具有轻质、高强度、耐腐蚀等特点,被广泛用于建筑外墙、屋顶和立面等部位。
4. 体育用品:复合材料在体育用品制造中也得到广泛应用。
例如,高尔夫球杆、网球拍、自行车车架等产品通常采用碳纤维复合材料制造,以提高产品的强度和耐用性。
5. 电子产品:复合材料在电子产品中也有重要的应用。
例如,手机、电脑等电子设备的外壳通常采用塑料复合材料制造,以提高产品的外观质感和耐用性。
6. 医疗器械:复合材料在医疗器械制造中也有广泛应用。
例如,一些人工关节、牙科修复材料等产品通常采用陶瓷复合材料制造,以提高产品的生物相容性和耐磨性。
7. 管道和容器:复合材料在管道和容器制造中也得到广泛应用。
例如,一些化工管道和储罐通常采用玻璃钢复合材料制造,以提高耐腐蚀性能和使用寿命。
8. 包装材料:复合材料在包装材料制造中也有重要的应用。
例如,一些食品包装袋、塑料瓶等产品通常采用塑料复合材料制造,以提高产品的耐用性和防潮性能。
9. 玩具制造:复合材料在玩具制造中也有一定的应用。
例如,一些高档玩具的外壳和结构部件通常采用塑料复合材料制造,以提高产品的强度和耐用性。
10. 家具制造:复合材料在家具制造中也得到一定的应用。
例如,一些现代化的家具表面采用塑料复合材料制造,以提供更加丰富多样的外观效果和耐用性。
复合材料在生活中的应用十分广泛,涉及航空航天、汽车工业、建筑、体育用品、电子产品、医疗器械、管道和容器、包装材料、玩具制造和家具制造等多个领域。
华鲁恒升dmc工艺技术

华鲁恒升dmc工艺技术华鲁恒升(DMC)工艺技术是一种先进的复合材料加工工艺,具有很高的强度、耐腐蚀性和耐磨性。
它由华鲁恒升公司自主研发,已经广泛应用于航空航天、汽车、轨道交通等领域。
华鲁恒升(DMC)工艺技术的核心是采用高性能树脂粘结剂和玻璃纤维增强材料进行复合加工。
通过预先制作好的玻璃纤维布料与树脂粘结剂的复合,再加入适量的填料和助剂,在一定的温度和压力条件下进行热固化。
这样可以得到具有较高强度和刚度的复合材料。
华鲁恒升(DMC)工艺技术具有以下优点:首先,华鲁恒升(DMC)制品具有较高的强度和刚度,能够满足高强度、低变形的要求。
在航空航天领域,DMC制品可以替代传统的金属材料,减轻飞机的重量,提高飞行性能。
其次,华鲁恒升(DMC)制品具有耐腐蚀性和耐磨性。
这些制品可以在恶劣的环境中长时间工作,不易受到腐蚀和磨损的影响。
在汽车领域,DMC制品可以作为车身结构部件和零部件,提高汽车的安全性和耐久性。
此外,华鲁恒升(DMC)工艺技术还具有工艺性好、生产效率高的特点。
相比于传统的金属加工工艺,DMC工艺可以实现批量生产,大幅提高生产效率。
同时,由于DMC制品的成型过程是通过模具进行的,可以实现复杂形状的制品生产。
华鲁恒升(DMC)工艺技术的应用领域广泛。
在航空航天领域,DMC制品被广泛应用于飞机机身、机翼和发动机罩等部件。
在汽车领域,DMC制品被用于汽车车身、底盘和内饰等部件。
在轨道交通领域,DMC制品被应用于高速列车的车身和内装件。
综上所述,华鲁恒升(DMC)工艺技术是一种先进的复合材料加工工艺,具有很高的强度、耐腐蚀性和耐磨性。
它在航空航天、汽车、轨道交通等领域的应用广泛,并为提高产品的性能和降低成本做出了重要贡献。
随着科技的不断发展,DMC工艺技术有望在更多领域得到应用,推动产业的发展。
顶级的复合加工技术使生产能力和加工精度都发生飞跃
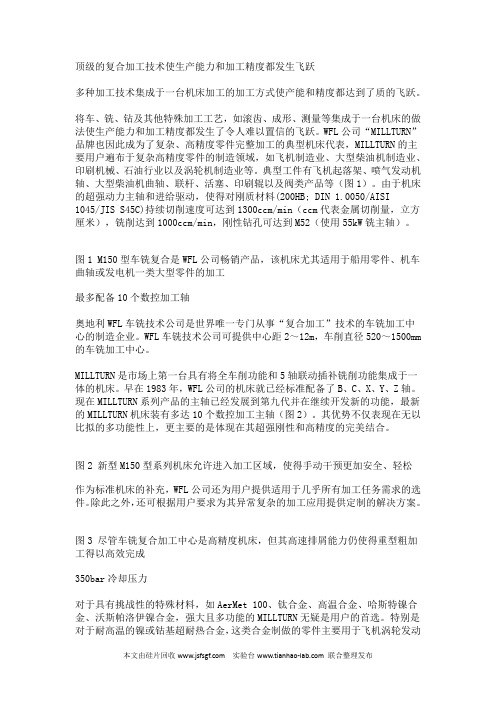
顶级的复合加工技术使生产能力和加工精度都发生飞跃多种加工技术集成于一台机床加工的加工方式使产能和精度都达到了质的飞跃。
将车、铣、钻及其他特殊加工工艺,如滚齿、成形、测量等集成于一台机床的做法使生产能力和加工精度都发生了令人难以置信的飞跃。
WFL公司“MILLTURN”品牌也因此成为了复杂、高精度零件完整加工的典型机床代表,MILLTURN的主要用户遍布于复杂高精度零件的制造领域,如飞机制造业、大型柴油机制造业、印刷机械、石油行业以及涡轮机制造业等。
典型工件有飞机起落架、喷气发动机轴、大型柴油机曲轴、联杆、活塞、印刷辊以及阀类产品等(图1)。
由于机床的超强动力主轴和进给驱动,使得对刚质材料(200HB; DIN 1.0050/AISI1045/JIS S45C)持续切削速度可达到1300ccm/min(ccm代表金属切削量,立方厘米),铣削达到1000ccm/min,刚性钻孔可达到M52(使用55kW铣主轴)。
图1 M150型车铣复合是WFL公司畅销产品,该机床尤其适用于船用零件、机车曲轴或发电机一类大型零件的加工最多配备10个数控加工轴奥地利WFL车铣技术公司是世界唯一专门从事“复合加工”技术的车铣加工中心的制造企业。
WFL车铣技术公司可提供中心距2~12m,车削直径520~1500mm 的车铣加工中心。
MILLTURN是市场上第一台具有将全车削功能和5轴联动插补铣削功能集成于一体的机床。
早在1983年,WFL公司的机床就已经标准配备了B、C、X、Y、Z轴。
现在MILLTURN系列产品的主轴已经发展到第九代并在继续开发新的功能,最新的MILLTURN机床装有多达10个数控加工主轴(图2)。
其优势不仅表现在无以比拟的多功能性上,更主要的是体现在其超强刚性和高精度的完美结合。
图2 新型M150型系列机床允许进入加工区域,使得手动干预更加安全、轻松作为标准机床的补充,WFL公司还为用户提供适用于几乎所有加工任务需求的选件。
mfp复合材料加工工艺

mfp复合材料加工工艺MFP复合材料加工工艺随着现代科技的发展,复合材料在各个领域中得到了广泛应用。
MFP 复合材料是一种常见的复合材料,其加工工艺对于最终产品的质量和性能至关重要。
本文将介绍MFP复合材料的加工工艺,并探讨其应用和发展前景。
一、MFP复合材料的特点MFP复合材料是由纤维增强材料和基体材料组成的复合材料。
纤维增强材料可以是碳纤维、玻璃纤维、芳纶纤维等,基体材料可以是树脂、金属、陶瓷等。
MFP复合材料具有重量轻、强度高、刚度大、耐腐蚀、耐磨损等特点,广泛应用于航空航天、汽车、船舶、建筑等领域。
二、MFP复合材料的加工工艺1. 预处理:对纤维增强材料进行处理,包括去除杂质、表面处理等。
2. 基体制备:选择合适的基体材料,进行制备和调配。
3. 纤维增强:将纤维增强材料与基体材料进行混合,使其均匀分布。
4. 成型:采用注塑、压缩成型、拉伸成型等方法将混合物制成所需形状。
5. 固化:通过加热或添加固化剂等方式,使混合物固化成为具有一定强度和刚度的复合材料。
6. 表面处理:对固化的复合材料进行表面处理,包括打磨、涂层等。
7. 检验和测试:对成品进行检验和测试,确保其质量和性能符合要求。
三、MFP复合材料的应用MFP复合材料在航空航天领域中得到了广泛应用,用于制造飞机、火箭等载具。
由于MFP复合材料具有重量轻、强度高的特点,可以减轻载具的重量,提高其性能和燃油效率。
在汽车领域,MFP复合材料可以用于制造车身、悬挂系统等部件,提高汽车的安全性和燃油效率。
MFP复合材料还可以应用于船舶、建筑、体育器材等领域,用于制造船体、建筑结构、高尔夫球杆等产品。
四、MFP复合材料加工工艺的发展前景随着科技的不断进步,MFP复合材料的加工工艺也在不断改进和创新。
目前,一些新的加工技术和设备正在被引入到MFP复合材料的生产中,如3D打印、自动化生产线等。
这些新技术和设备将进一步提高MFP复合材料的加工效率和质量。
传说中的欧洲十大车铣复合机床制造商,都是谁?

传说中的欧洲十大车铣复合机床制造商,都是谁?传说中的欧洲十大车铣复合机床制造商,都是谁?机床复合化是机床发展的重要方向之一。
复合机床又包括车铣复合、车铣磨复合、铣磨复合、切削与3D打印复合、切削与超声振动复合、激光与冲压复合等多种多样的形式,复合的目的就是让一台机床具有多功能性,可一次装夹完成多任务,提高加工效率和加工精度。
复合机床中,车铣复合机床最多见,也是使用最多的复合机床种类。
欧洲是世界机床最先进的地区,复合机床同样走在世界前列,下面向大家介绍10家最有影响力的欧洲车铣复合机床的制造商。
1、奥地利EMCO集团奥地利EMCO公司是一家有着近60年历史的专业车床制造厂家同时也是全世界最大的工业培训系统设计开发和制造厂,迄今为止全世界有超过100万台EMCO机床在为各行各业进行服务。
EMCO公司总部坐落在奥地利的萨尔斯堡附近,现在的EMCO公司600多名员工的规模已成为奥地利第一大机床厂,欧洲最大车床厂之一。
EMCO公司生产的数控车床品种丰富,从简单的两轴数控车床直到拥有八根轴的数控车铣复合机床;从用于产品研究开发的双主轴车铣中心到用于大批量生产的四主轴双刀塔车铣中心;从最大加工直径仅为的小型车削中心到加工直径为的大型车削中心;从最大工件长度仅为的小型车床直到可加工长零件的大型卧车,EMCO几乎拥有车床领域的所有先进技术。
EMCO九轴车铣复合加工中心也令人亮眼。
机床整体内部空间宽敞,有主轴及副主轴、大小相同主轴端部均采用A2-6型号、左右两个夹盘可以同时工作。
床身最大回转直径φ500,但在车削棒料时直径只能达到φ65,稍微有些受限。
刀塔安装在主轴下部,也是12工位的动力刀盘,上部安装的是B轴;但在行程方向上分别有X/X2、Z/Z2/Z3、Y向再加上俩主轴一共九轴,可以车、铣、钻、攻任意一个角度都可以完成。
视频1:EMCO ht665车铣复合加工2、德国埃马克集团倒立式车床在埃马克诞生,和一般的卧式车床不一样的是倒立车通过主轴抓取工件,以一种革命性的方式颠覆了传统的自动化概念。
航空航天工程中的新型材料研究

航空航天工程中的新型材料研究航空航天工程是现代科技的重要组成部分,新型材料的研究是航空航天工程最重要的基础研究之一。
随着科技的不断发展,人类对航空航天行业的要求也在不断提高。
这就要求我们在新型材料的研究和应用方面不断进行探索和创新。
本文将从新型材料的发展历程、新型材料在航空航天工程中的应用以及当前新型材料研究的发展趋势三个方面进行探讨。
一、新型材料的发展历程随着人类科技的不断进步,新型材料的研究也取得了长足的进步。
航空航天行业的快速发展,也促进着新型材料领域的发展。
在新型材料发展的历程中,人们创造了许多非常具有代表性的材料,例如:1. 碳纤维:碳纤维是一种优质材料,以其高强度、高弹性、低密度和抗腐蚀等特性广泛应用于航空航天工程、国防、汽车制造和体育器材等领域。
2. 硅酸盐陶瓷材料:硅酸盐陶瓷材料是一种优质耐高温材料,由于其高强度、高耐热和抗磨损等特性,被广泛应用于发动机制造等领域。
3. 超合金:超合金是一种具有高强度、高抗氧化和高温强度等特性的金属材料,因其被广泛应用于航空航天制造等领域。
二、新型材料在航空航天工程中的应用航空航天工程是新型材料的应用领域之一。
在航空航天工程中,新型材料有着广泛的应用,常见的应用场景如下:1. 机身结构件:新型材料在机身结构件制造方面具有一定的优势,主要体现在重量轻、强度高、抗腐蚀等方面。
例如,碳纤维等材料被广泛应用于飞机机身的制造中。
2. 发动机燃烧室:在航空发动机制造方面,新型材料的应用在防止高温腐蚀等方面有着重要的优势。
例如,高温合金、耐热陶瓷等材料被广泛应用于发动机燃烧室的制造中。
3. 航空部件:新型材料在航空部件制造方面具有很大的应用前景。
例如,炭纤维复合材料被广泛应用于制造航空部件中,如导航航天器的蒙皮、加油机的油箱等部件。
3. 航空材料:新型材料在航空材料领域也有广泛的应用。
例如,航空用塑料、航空泡沫材料等应用领域也在不断扩大。
三、新型材料研究的发展趋势随着人类对科技的不断追求和探索,新型材料的研究也面临着新的挑战和机遇。
复合材料行业
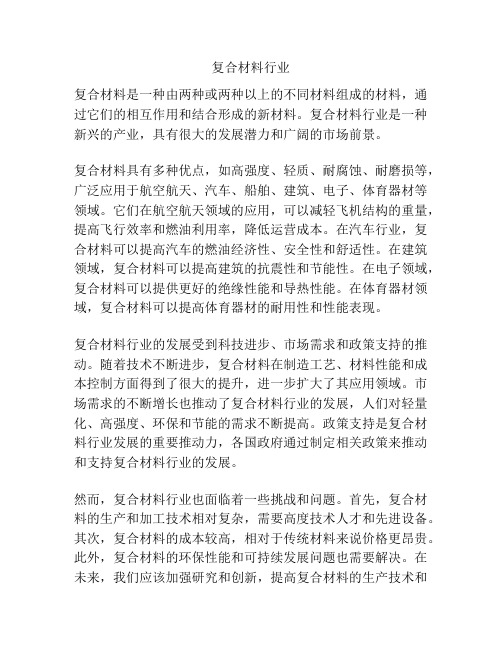
复合材料行业复合材料是一种由两种或两种以上的不同材料组成的材料,通过它们的相互作用和结合形成的新材料。
复合材料行业是一种新兴的产业,具有很大的发展潜力和广阔的市场前景。
复合材料具有多种优点,如高强度、轻质、耐腐蚀、耐磨损等,广泛应用于航空航天、汽车、船舶、建筑、电子、体育器材等领域。
它们在航空航天领域的应用,可以减轻飞机结构的重量,提高飞行效率和燃油利用率,降低运营成本。
在汽车行业,复合材料可以提高汽车的燃油经济性、安全性和舒适性。
在建筑领域,复合材料可以提高建筑的抗震性和节能性。
在电子领域,复合材料可以提供更好的绝缘性能和导热性能。
在体育器材领域,复合材料可以提高体育器材的耐用性和性能表现。
复合材料行业的发展受到科技进步、市场需求和政策支持的推动。
随着技术不断进步,复合材料在制造工艺、材料性能和成本控制方面得到了很大的提升,进一步扩大了其应用领域。
市场需求的不断增长也推动了复合材料行业的发展,人们对轻量化、高强度、环保和节能的需求不断提高。
政策支持是复合材料行业发展的重要推动力,各国政府通过制定相关政策来推动和支持复合材料行业的发展。
然而,复合材料行业也面临着一些挑战和问题。
首先,复合材料的生产和加工技术相对复杂,需要高度技术人才和先进设备。
其次,复合材料的成本较高,相对于传统材料来说价格更昂贵。
此外,复合材料的环保性能和可持续发展问题也需要解决。
在未来,我们应该加强研究和创新,提高复合材料的生产技术和性能,降低成本,改善环保性能,推动复合材料行业向更加可持续和绿色的方向发展。
总之,复合材料行业是一个具有很大潜力和广阔市场前景的产业。
随着科技进步和市场需求的推动,复合材料的应用领域将进一步扩大,其在航空航天、汽车、建筑、电子和体育器材等领域的应用将逐步普及和推广。
同时,我们也需要解决复合材料生产技术、成本和环保性能等方面的问题,推动复合材料行业向更加可持续和绿色的方向发展。
复合材料在国防建设领域的应用
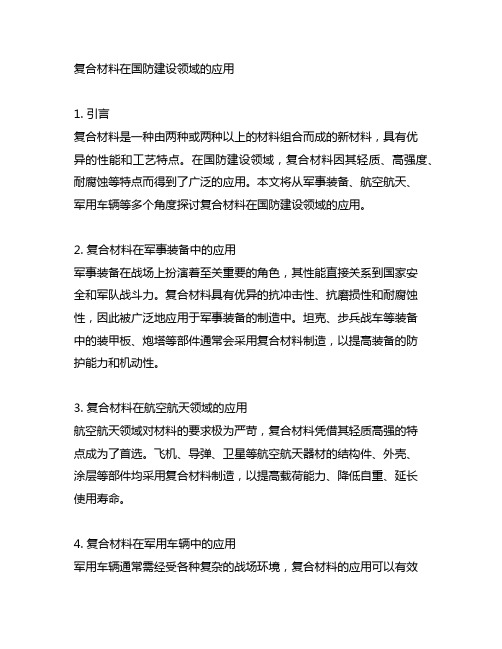
复合材料在国防建设领域的应用1. 引言复合材料是一种由两种或两种以上的材料组合而成的新材料,具有优异的性能和工艺特点。
在国防建设领域,复合材料因其轻质、高强度、耐腐蚀等特点而得到了广泛的应用。
本文将从军事装备、航空航天、军用车辆等多个角度探讨复合材料在国防建设领域的应用。
2. 复合材料在军事装备中的应用军事装备在战场上扮演着至关重要的角色,其性能直接关系到国家安全和军队战斗力。
复合材料具有优异的抗冲击性、抗磨损性和耐腐蚀性,因此被广泛地应用于军事装备的制造中。
坦克、步兵战车等装备中的装甲板、炮塔等部件通常会采用复合材料制造,以提高装备的防护能力和机动性。
3. 复合材料在航空航天领域的应用航空航天领域对材料的要求极为严苛,复合材料凭借其轻质高强的特点成为了首选。
飞机、导弹、卫星等航空航天器材的结构件、外壳、涂层等部件均采用复合材料制造,以提高载荷能力、降低自重、延长使用寿命。
4. 复合材料在军用车辆中的应用军用车辆通常需经受各种复杂的战场环境,复合材料的应用可以有效提升车辆的防护性能和使用寿命。
军用车辆的车身、底盘等部件通常会采用复合材料制造,以提高防弹、防爆和抗冲击的能力。
5. 个人观点和理解从上面的例子可以看出,复合材料在国防建设领域的应用已经成为了不可或缺的一部分。
随着科技的不断进步,相信复合材料在国防领域的应用还会迎来更多的发展和突破。
未来,我期待复合材料能够在国防建设中发挥更加重要的作用,为国家安全和军事实力提供有力支撑。
6. 总结复合材料在国防建设领域的应用具有非常广泛的前景。
从军事装备到航空航天,从军用车辆到军事工程,复合材料都扮演着重要的角色。
通过本文的深度和广度的探讨,相信读者们已经对复合材料在国防建设领域的应用有了更加全面、深刻的理解。
至此,你已经阅读了关于复合材料在国防建设领域的应用的文章。
希望这篇文章能够对你有所帮助,如果有任何问题或需要进一步了解,请随时与我联系。
在国防建设领域,复合材料的应用已经成为不可或缺的一部分。
- 1、下载文档前请自行甄别文档内容的完整性,平台不提供额外的编辑、内容补充、找答案等附加服务。
- 2、"仅部分预览"的文档,不可在线预览部分如存在完整性等问题,可反馈申请退款(可完整预览的文档不适用该条件!)。
- 3、如文档侵犯您的权益,请联系客服反馈,我们会尽快为您处理(人工客服工作时间:9:00-18:30)。
车磨复合加工技术在航空业的应用
摘要:车磨复合加工技术的出现为大幅度提高高精度轴类零件的加工效率和加工精度提供了一种新的解决方案。
文章以瑞士STUDER公司的车磨复合加工机床为例,介绍了车磨复合机床的功能和绿色生态特点,分析了车磨复合加工相关的硬态车削技术和车磨复合工艺技术,并给出了车磨复合加工在航空产品中的应用实例。
实例表明,车磨复合加工技术在航空液压产品的加工中具有一定的应用前景。
关键词:车磨复合加工绿色生态机床硬态车削
1、复合加工技术
加工效率和加工精度是金属加工领域追求的永恒目标。
在传统的机械加工流程中,由于在制品在不同设备之间流转,不可避免的产生加工等待、运输和定位装夹,等行为,这些因素既影响加工精度,又增加了生产辅助时间。
随着计算机技术、数控技术,机床技术和工艺技术的不断发展,传统的加工理念已经不能满足人们对机械加工效率和精度的需要,在这样的背景下,复合加工技术孕育而生。
一般来讲,复合加工技术就是在一台加工设备上完成不同加工工序或者不同工艺方法的加工技术的总称。
目前,复合加工技术主要表现为两种不同的形式[1]:一种是以能量或运动方式为基础的不同加工方法的复合;另一种是以工序集中原则为基础的、以机械加工工艺为主的复合。
车磨复合加工技术是近年来产生的一种新的复合加工方式。
对于车削和磨削机床,适合加工的零件是回转类零件。
磨削的特点是:磨削前毛坯一般都进行了淬火处理,毛坯的硬度高,所留余量较少,砂轮每次吃刀量少,相对车削加工效率较低。
车削属于粗加工或半精加工工种,选择合适的和切削参数后加工效率高。
车磨复合加工设备集成了车削和磨削的特点,能够大幅度提高轴类零件,特别是高精度轴类零件的加工效率。
2、车磨复合机床及关键技术
目前,车磨复合加工技术作为一种先进的制造技术,由于它的高精度性和只能加工回转类零件的局限性,在国内外应用较少。
本文通过介绍一台车磨复合,对车磨复合技术的特点以及设备功能进行一定的研究和探索。
车磨复合,就是在同一台设备上既能进行车削加工,又能进行磨削加工的一种复合方式。
从复合加工的特点来说,就是一次装夹完成零件的车削和磨削工序,减少了的零件的装卸次数,避免重复定位误差,能够更好地保证零件精度。
但,车磨复合加工设备又具备许多特点。
为了大幅度提高轴类高精度零件的加工效率,瑞士STUDER公司推出车削和磨削复合的机床――S242车磨复合加工中心。
该设备可配置左、右、正斜砂轮架和
转塔刀架, 3种横向砂轮架和架可有15种配置方案。
设备具有一次装夹完成磨外圆、内孔,车削外圆、内孔的强大功能。
其中之一配置参数如图1和表1所示。
图1 S242车磨复合加工中心
表 1 S242车磨复合加工机床特点
通过对S242的研究,对车磨复合加工的特点及关键技术进行探讨。
2.1、绿色生态机床
机床在使用过程中不仅消耗能源,还会产生各种废弃物,对工作环境和自然环境造成直接或间接的污染。
从整个机床生命周期内审视,如何减少对环境冲击的绿色生态机床就成为当前研究的热点。
绿色生态机床愿景应该具有以下特点[2]:(1)机床主要零部件由再生材料制造。
(2)机床的重量和体积减少50%以上。
(3)通过减轻移动部件质量、降低空
运转功率等措施使功率消耗减少30%~40%。
(4)使用过程的各种废弃物减少50%~60%,保证基本没有污染的工作环境。
(5)报废后机床的材料100%可
回收。
S242车磨复合加工中心具有绿色生态机床的主要特征如下:
1) 床身采用Granitan S103人造花岗石。
该种材料是树脂混凝土,与传统的铸铁结构相比,具有阻尼系数大、抗震性强、热稳定性好等一系列优点。
2) 可以进行硬车加工,硬车时采用干切削,不使用冷却液,消除了对环境的污染。
3) 采用斜床身,排屑路径通畅,切屑不与床身直接接触,保持机床的热稳定性。
机床绿色化是未来机床发展的一大特点。
车磨复合加工中心融入绿色元素后,机床的刚性更强,加工效率和机床精度也有了大幅提高。
2.2、硬车加工技术
车磨复合加工机床可以硬车加工。
过去高硬度零件的精加工一直是采用磨削完成, 由于超硬材料刀具的出现及等加工设备精度的提高, 以硬态切削代替磨削完成
零件的最终加工已成为一种新的精加工途径[3]。
硬态车削是指把淬硬钢的车削作为最终精加工工序的工艺方法。
硬态车削与常规切削相比的显著特点就是径向切削力要大于主切削力。
硬态车削还有切削温度高、刀具使用寿命短的特点,这就要求硬态车削的刀具耐热性和耐磨性应更好,机床系统要有高刚度、大功率以及较好的热稳定性。
表 2 硬态车削与磨削的比较[4]
S242车磨复合加工中心具有斜床身的导轨、足够的机床刚性和高精度,这些特征保证了该机床可以硬态车削。
试验表明,选择合适的刀具和切削参数,在S242上进行外圆,外槽的淬硬车削加工,不仅能够很好的保证零件的尺寸精度和表面粗糙度要求,而且可以大幅度提高切削效率。
对于高精度轴类零件的加工,完全可以采用“以车代磨”的加工思路。
由表2可看出,“以车代磨”不仅能够大幅提高产品加工效率,而且加工成本低。
车磨复合机床进行硬车加工具有很高的柔性,通过程序直接实现走圆弧、走斜线等运动轨迹,解决磨削对此类特征加工困难的问题。
2.3、车磨复合的工艺技术
车磨复合加工技术对零件加工工艺也产生了很大的影响。
传统的高精度轴类零件加工流程一般包括:毛坯-粗车-精车-热处理-粗磨-精磨工序。
这种工艺流程的思路是,用粗车去毛坯的大部分余量,热处理前精车完成零件的基本外形加工并给磨削留一定的余量,热处理后零件的硬度一般达到57HRC以上,分粗、精磨保证零件的精度要求。
对于细长轴或热处理易变形的轴类零件,这种典型的工艺流程具有一定的缺陷,主要会产生以下问题:
(1)热处理后零件易变形,尤其是在轴线方向也会发生伸长或缩短,磨削已无法消除零件的变形。
(2)精车后留多少余量合适难控制。
精车后余量的多少对磨削工序会产生很大影响,如果精车留余量较少,热处理后零件变形,无法磨出零件要求的精度尺寸;如果余量较大,磨削时间变长,成本高,磨削困难。
(4)工艺流程长,加工周期相应变长。
加工需要的设备较多,不可避免的产生等待浪费,搬运浪费等情况,增加产品的交付周期。
采用车磨复合加工工序后,零件的加工流程如下:毛坯-粗车-热处理-车磨复合。
粗车去大部分余量后热处理,然后进行车磨复合工序,对于易变形的加工特征,粗车留余量完全可满足要求。
车磨复合工序主要完成的内容和产生的效果有:
(1)一次装夹,完成车削和精磨的工序,消除重复装卸带来的定位误差;
(2)可以“以车代磨”,消除传统加工流程中精车留多少余量合适的问题,并且能够很好保证加工精度,提高加工效率;
(3)硬车时可采用干切,消除了对环境的污染,同时可降低处理切屑成本。
总之,采用以车代磨和车磨复合加工工艺方法,不仅能够大幅度提高产品的加工效率,而且能够更好的保证产品的加工质量。
车磨复合工艺技术是对传统工艺方
法的一次重大突破和变革。
3、车磨复合加工技术在航空业的应用
近年来,随着航空工业迅速发展,航空产品多品种、小批量等特点越来越明显,产品的加工工艺过程更加复杂,且难加工材料应用越来越广,在制造过程中普遍存在制造周期长、材料切除量大、加工效率低以及加工变形严重等瓶颈。
为了提高航空产品的加工效率和加工精度,工艺人员一直在寻求更为高效精密的加工工艺方法。
车磨复合加工技术的出现对航空轴类零件的高效精密加工无疑是一个新的思路和解决方法。
表3 零件基本信息及切削参数
在航空液压舵机等系统中,阀芯、阀套类零件主要包括的特征有:滤油的内外胶圈槽、内外储油槽、需要精密配合的外圆和内孔。
这些特征都有很高的尺寸、配合精度和表面质量,加工过程中易变形,加工难度大。
车磨复合加工技术的出现,为此类问题提供了一个解决方案。
如图2为航空某重点型号舵机液压阀芯,该零件的基本信息、切削参数、刀具参数及加工精度如表3所示。
图2 航空液压阀芯模型
实例表明,S242车磨复合加工中心通过“以车代磨”和车磨复合工艺技术的应用,不仅能够很好的保证加工精度,而且可大幅度提高加工效率。
车磨复合加工技术在航空液压产品加工领域具有较大的应用前景。
4、结束语
车磨复合加工机床的出现对提高高精度轴类零件的加工效率和加工精度有很大促进作用。
但是,国内外在此方面的应用还很少。
本文通过介绍S242车磨复合加工中心的功能和特点,分析了车磨复合加工的硬车技术和工艺技术,并给出了一个在航空产品方面的车磨复合加工应用实例。
以此对车磨复合技术在航空产品加工领域进行初步的探索和研究。
参考文献
[1]. 吴宝海,张亚南,等.车铣复合的关键技术及应用前景[J].航空制造技术,2010(19).
[2]. 张曙.绿色生态机床[J]. WMEM, 2009, 4(2).
[3]. 岳彩旭,刘献礼,等.硬态切削技术[J].航空制造技术,2008(18).
[4]. 郭丽君.硬态切削刀具的性能与选用[J].机械设计与制造,2007,7(7).(end) 文章内容仅供参考 () ()(2012-7-31)。