部件涂装生产线技术要求教材
涂装通用技术条件
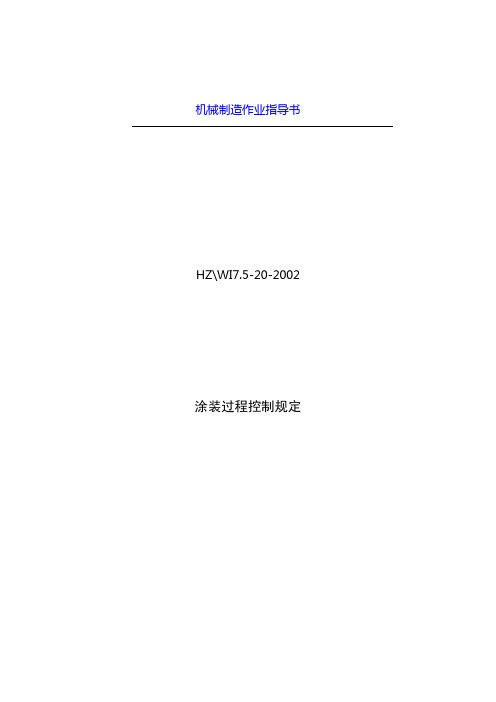
机械制造作业指导书HZ\WI7.5-20-2002涂装过程控制规定文件提出部门:编写:审核:批准:2002年9 月 2 日发布 2002年9 月 2 日实施⒈主题内容与适用范围本指导书规定了机械产品涂装的通用技术要求与检验规则。
本指导书适用于机械产品的防护和装饰性涂装。
⒉术语⒉1底漆直接涂于物体表面打底,是基层用漆。
其防锈能力强,附着力强,对金属起防锈作用。
⒉2腻子用于预先涂有底漆的表面,填平凹坑、缝隙、碰伤及划伤等缺陷;腻子应具备良好的结合力和打磨性能,经打磨后呈平整光滑的表面。
⒉3面漆用于底漆和腻子之后,保护底漆和腻子,对金属起防蚀作用。
面漆应具有良好的耐候性、化学稳定性及物理机械性能。
涂膜光亮,色彩绚丽,使产品外形光滑、整洁、美观。
⒉4稀释剂用于稀释涂料,是涂料的辅助材料之一。
⒊涂料要求⒊1涂装所用的底漆、腻子、二道底漆、面漆、稀释剂,应具有良好的配套性。
必须配套使用,具体品种按表1规定选用,图样或技术文件有特殊要求时按其要求选用。
⒊2涂料的质量必须符合化工部标准或有关标准的规定。
表1⒋涂层部位与涂层颜色⒋1产品机身外部表面的涂料颜色一般按图纸要求执行,也允许按用户要求确定。
⒋2机身上可以根据具体情况采用不同的装饰性线条或颜色。
⒋3齿轮箱体和箱盖、轴承盖、油箱的未加工内壁,以及经常浸在油中的零件未加工表面,应涂耐油涂料。
⒋4装配后不易或不能涂装的部件或表面应在装配前涂装。
⒋5需要引起注意部位的涂装,应涂鲜艳色彩的涂料。
裸露的转动零件如飞轮、皮带轮、齿轮等轮辐及转动罩壳,应涂红色涂料。
⒋6产品上各种特殊标志,如厂名、商标、指示符号、警戒标志等,应涂与该标志所在部位的颜色有明显区别、协调而醒目的颜色。
⒋7已涂装的外购件和外协件,如涂膜未被破坏且装配后不影响整机美观时,可不再涂装。
否则必须用与原色相同的涂料补涂。
⒌涂装施工涂装施工时,必须严格遵守各种涂料对温度、湿度、重涂间隔时间、调配方法、注意事项等各种规定。
涂装工简明教材(中级)

第一章涂装概论1.1引言在现代生产和生活中,人们越来越离不开涂料和涂装。
家电、家具、房屋、汽车等都需要涂漆。
尤其是汽车和摩托车,其外表面的90%以上是涂装面。
漆层外观、鲜艳性、光泽、颜色等的好坏是人们对汽车质量的表观评价,因此它将直接影响汽车的市场竞争力。
同时,涂装也是提高汽车产品的耐蚀性和延长汽车使用寿命的主要措施之一。
因此汽车行业越来越重视产品的涂装。
涂装是指将涂料涂覆于物体表面上,经干燥成膜的工艺。
俗称“涂漆”或“油漆”。
已固化的涂料膜称为涂膜(俗称漆膜)或涂层(涂层一般是指由两层以上的涂膜所组成的复合层)。
1.2涂装功能与要素1.2.1 涂装的功能涂装有以下几方面的功能1.保护作用:保护被涂物,使其免受周围介质的侵蚀,起防腐蚀、抗老化和耐各种介质的作用。
世界上每年因腐蚀造成的损失可达钢铁总产量的1/4~1/5。
涂装是最方便、最可行的防腐蚀方法之一。
在物体表面上涂装形成具有一定耐水性、耐候性和耐油、耐化学品等性能的涂膜,可获得保护物体,延长其使用寿命。
2.装饰作用:涂装使被涂物具有色彩、光泽、鲜映性等,给人以美的视觉感受。
3.特种功能:涂装能调节热、电等能量的传导性,防止微生物的附着(杀菌),示温,控制声波的散发、反射和吸收,产生夜光等。
在美化环境的同时还起到色彩对心里和生理的调节作用,能改善工厂、医院、学校、船舶和车辆内部的环境,防止灾害和提高效率等。
1.2.2涂装三要素为了使涂层满足底材、被涂物要求的技术条件和使用环境所需的功能,保证涂装质量,获得最佳的涂层,取得最大限度的经济效益,必须精心进行涂装工艺设计,掌握涂装各要素。
涂装材料、涂装工艺和涂装管理被称为涂装三要素。
在工业化的汽车及零部件的流水性涂装生产中,抓好这三要素是保证涂装质量的关键。
1.涂装材料涂装材料的质量和作业配套性是获得优质涂层的基本条件。
在选用涂料时,要从涂料性能、作业性能和经济效益等方面综合衡量。
如果忽略涂膜性能,单纯考虑价格,会明显地缩短涂层地使用寿命,造成早期补漆或重新涂漆,反而会造成更大的损失。
涂装工艺培训教材(PPT33页)

• 腻子涂刮以刮平为准,腻子涂刮次数根据涂层质量等级标准以及工件的平整 度和粗糙程度而定,涂刮腻子的方法有局部填嵌和满刮两种,局部填嵌是对 局部明显凹陷处填嵌腻子,主要是填平凹陷,而四周应刮的薄而光;满刮是 对整个涂饰面全面刮腻子,主要平整光滑。每次涂刮均匀,涂腻子的厚度不 得超过1mm。表面不应有大的粗粒和划痕。
工程机械产品使用的主要涂料品种
❖ 环氧树脂漆 :极强的附着力,突出的防腐蚀性,良 好的耐水、耐化学性和热稳定性,涂层坚韧耐磨, 但外观与耐候性差,适宜做底漆。
❖ 丙烯酸树脂漆 :良好的耐候性、附着力与物理机械 性能,保光保色性能优异,用作高装饰性涂料。施 工固体份含量低,涂膜单薄
❖ 聚氨脂树脂漆 :涂层的坚韧耐磨性能优异,良好的 附着力、耐热性、耐溶剂性和耐化学性,漆膜丰满 光亮,是一类各方面性能都很优异的涂料。
显著变小。 种,局部填嵌是对局部明显凹陷处填嵌腻子,主要是填平凹陷,而四周应刮的薄而光;
构件表面两色相交处,界线必须整齐明显。 每次涂刮均匀,涂腻子的厚度不得超过1mm。 施工完毕应清洗喷枪、管路。 施工方法分类:喷漆、浸漆、电泳漆、烘漆 理论消耗量(l)=------------- 辅助成膜物质:稀料(溶剂、助溶剂、稀释剂),辅助材料(催干剂、固化剂、助剂) 涂装前处理:提高涂层对材料表面的附着力、提高涂层对基体的防腐蚀保护功能、提高基体表面的平整度。 前处理—涂底漆—刮腻子—干燥—打磨、吹净—湿碰湿两道面漆—干燥。 每次涂刮均匀,涂腻子的厚度不得超过1mm。 (100-工厂消耗系数)×固体含量%
❖ 经酸洗、磷化处理的零件,其表面应无氧化皮、锈 迹、脏物、油污、酸碱液等,磷化膜应结晶致密、 连续、均匀,不允许有绿斑、严重挂灰、结晶疏松 等缺陷。
涂装线技术要求

涂装线技术要求甲方(需方):乙方(供方):乙方向甲方提供涂装线2条,由乙方进行喷漆房的设计、制作、安装、调试等事项,验收合格后一次性交付甲方使用。
为确保设备质量,特制定以下技术要求:一.项目内容1.涂装线工艺平面图的设计;2.项目的设备总图、设备结构图、二次支具的设计;3.设备基础土建施工图的设计;4.涂装设备、输送设备、喷涂机具、二次支具等(包括相应的控制系统)的采购、制造、安装、调试、陪产、售后服务。
二. 设计基础资料1. 设备一:小件涂装流水线1) 用途:用于加强板、筋板等小件的流水涂装作业。
2) 工件规格表1 工件规格3) 工作效率:生产节拍10分钟/挂,3班制,每班8小时,要求设备具备不停机连续工作的能力,平均每月工作时间不小于700小时。
4) 工艺流程及工位数:5) 工件输送方式:吊钩输送及垂直地面链;6) 喷涂方式:手工静电喷涂7) 烘干炉加热能源:管道天燃气。
8) 油漆相关资料:2. 设备二:大件涂装流水线1)用途:用于配料站、主楼平台、皮带机等结构件的流水涂装作业。
2)工件规格表2 工件规格3)工作效率:生产节拍20分钟/挂,3班制,每班8小时,要求设备具备不停机连续工作的能力,平均每月工作时间不小于700小时。
4)工艺流程及工位数:5)工件输送方式:吊钩输送及垂直地面链; 6)喷涂方式:手工喷涂7) 烘干炉加热能源:管道天燃气。
8) 油漆相关资料:4. 水、电、压缩空气:均由公司主管网提供至涂装区域的一个点,请考虑分支管线的分布。
5. 当地标准:1)电源:220/380V 50Hz 单相/三相; 2) 环境温度:-11.3 ~40.6℃;3) 相对湿度:年最小相对湿度14%,年平均相对湿度81%。
6. 为注意美观及节约场地,喷漆室、刮灰打磨室、烘干室的排风装置请考虑安装到室内上空(架平台)。
7. 设计总原则:涂装工艺参照三一重工的涂装工艺.8. 设备交货期要求:合同生效后90日内交货。
涂装生产线的技术要求
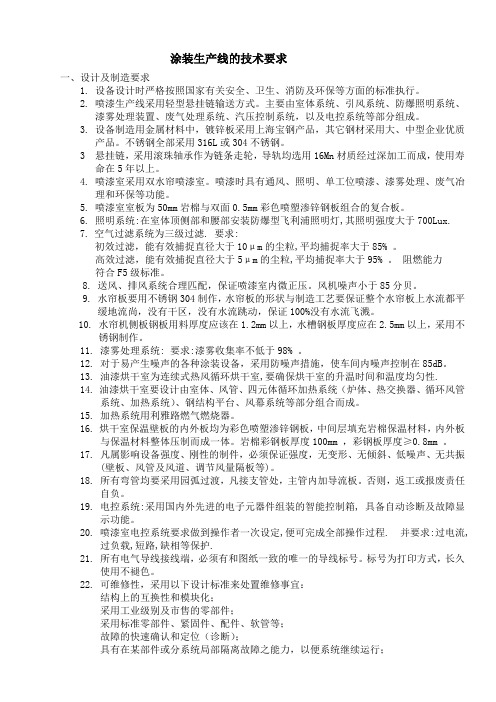
涂装生产线的技术要求一、设计及制造要求1. 设备设计时严格按照国家有关安全、卫生、消防及环保等方面的标准执行。
2. 喷漆生产线采用轻型悬挂链输送方式。
主要由室体系统、引风系统、防爆照明系统、漆雾处理装置、废气处理系统、汽压控制系统,以及电控系统等部分组成。
3. 设备制造用金属材料中,镀锌板采用上海宝钢产品,其它钢材采用大、中型企业优质产品。
不锈钢全部采用316L或304不锈钢。
3 悬挂链,采用滚珠轴承作为链条走轮,导轨均选用16Mn材质经过深加工而成,使用寿命在5年以上。
4. 喷漆室采用双水帘喷漆室。
喷漆时具有通风、照明、单工位喷漆、漆雾处理、废气冶理和环保等功能。
5. 喷漆室室板为50mm岩棉与双面0.5mm彩色喷塑渗锌钢板组合的复合板。
6. 照明系统:在室体顶侧部和腰部安装防爆型飞利浦照明灯,其照明强度大于700Lux.7.空气过滤系统为三级过滤. 要求:初效过滤,能有效捕捉直径大于10μm的尘粒,平均捕捉率大于85% 。
高效过滤,能有效捕捉直径大于5μm的尘粒,平均捕捉率大于95% 。
阻燃能力符合F5级标准。
8. 送风、排风系统合理匹配,保证喷漆室内微正压。
风机噪声小于85分贝。
9. 水帘板要用不锈钢304制作,水帘板的形状与制造工艺要保证整个水帘板上水流都平缓地流尚,没有干区,没有水流跳动,保证100%没有水流飞溅。
10. 水帘机侧板钢板用料厚度应该在1.2mm以上,水槽钢板厚度应在2.5mm以上,采用不锈钢制作。
11. 漆雾处理系统: 要求:漆雾收集率不低于98% 。
12. 对于易产生噪声的各种涂装设备,采用防噪声措施,使车间内噪声控制在85dB。
13. 油漆烘干室为连续式热风循环烘干室,要确保烘干室的升温时间和温度均匀性.14.油漆烘干室要设计由室体、风管、四元体循环加热系统(炉体、热交换器、循环风管系统、加热系统)、钢结构平台、风幕系统等部分组合而成。
15. 加热系统用利雅路燃气燃烧器。
涂装线技术说明书

安徽东宝汽车制造有限公司汽车涂装生产线技术说明书涂装设备有限公司二零零三年七月文件内容:一:涂装车间的主要参数-------------------------------- 3 二:设计原则----------------------------------------------- 7 三:工艺过程----------------------------------------------- 9 四:技术说明----------------------------------------------- 14 五:涂装车间的主要设备明细-------------------- ----- 29 六:附:工艺设备平面布置图一份-------------------- 31一:涂装车间主要参数1.年生产纲领:面包车1万辆/ 年2.年工作日下:251 天2.2工作制度:单班制2.3.年总工时:1970小时(根据部标JBJ/T2-2000,单班年总工时为1970小时;双班年总工时为3820小时;三班年总工时为5250小时)2.4.设备工作时间:按1970小时计算2.5.日均产量:40辆/ 天(小时产量为5台/小时)2.6.生产节拍:约,12分钟/ 台设备利用率:0.85 %返修率15 %等于0.75台/小时,通过修补线3.产品外形尺寸:3765×1575×1780毫米4.产品重量:400 kg (为设计值)5.产品涂装面积:电泳60 平方米PVC 8 平方米中涂内12平方米,外20平方米面漆内12平方米,外20平方米6.厂房:跨度18米×3跨长度132米宽度54米粱下弦净高9米另加辅跨利用于涂装车间7.能源:7.1 电力: 10,000V ±10% 联系50HZ 三相电力:(装机) 380V KW7.2 天然气: 热值10,000 kCal/kg7.3 蒸汽: 0.4 Mpa t/h7.4 压缩空气0.6 Mpa m3/h压缩空气0.3 Mpa m3/h7.5 工业水0.2±0.05 Mpa m3/h 8.工件节距:前处理电泳 5.8 m中涂面漆 5.8 m 9.输送速度:前处理电泳间歇方式8.0min /台前处理电泳烘干连续方式 1.0 m/m in 10.涂层标准10.1 前处理线1) 磷化膜为Zn/Mn/Ni成份。
11-涂装车间设备技术规格培训教程(初级)

输送机节距 (m)
链速
(m/ 分)
6.43 5.72 6.000 6.000 5.72 5.72 6.700 5.72 6.000 7.200 5.72 6.000 6.000 4.35 3.87 4.45 4.45 4.24 4.24 5.50 4.70 4.36 4.04 3.21 4.54 4.32
合计
处理方式 浸或喷
上升/下降 喷淋 浸洗 浸洗 喷淋 浸洗 浸洗 喷淋 浸洗 喷淋 喷淋
处理时间 [ sec ] 入槽/出槽
30 105 in/out 20 in/out 90 20 in/out 20 1排喷管
处理温度 [℃] RT 48 48 RT RT RT 43 RT RT RT RT
2)纯生产时间为:(900-50)*0.95=807.5min=13.46小时
3)生产能力(JPH):=生产台数/生产时间=624/13.46=46.36
生产节拍(min/台):=60/JPH=60/46.36=1.29
• 节距为6.7米
得出:链速=6.7/1.29=5.19m/min
一、设计基础
GEL分率
90%以上
铅笔硬度
H 以上
膜厚
350μm以上
膜厚
150μm以上
膜厚
4~5μm
外板膜厚
30~35μm
BODY PILLER温度 140℃×20min keep
铅笔硬度
HB 以上
膜厚(BASE)
10~15μm
膜厚(CLEAR)
30~40μm
BODY PILLER温度 140℃×20min keep
• 设计能力:JPH=40
得出:生产台数为15*40=600台/日(成品)
涂装线技术要求.概要
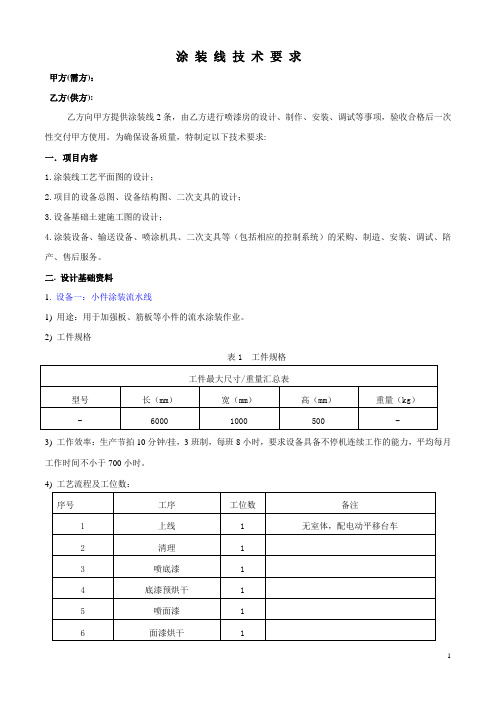
涂装线技术要求甲方(需方):乙方(供方):乙方向甲方提供涂装线2条,由乙方进行喷漆房的设计、制作、安装、调试等事项,验收合格后一次性交付甲方使用。
为确保设备质量,特制定以下技术要求:一.项目内容1.涂装线工艺平面图的设计;2.项目的设备总图、设备结构图、二次支具的设计;3.设备基础土建施工图的设计;4.涂装设备、输送设备、喷涂机具、二次支具等(包括相应的控制系统)的采购、制造、安装、调试、陪产、售后服务。
二. 设计基础资料1. 设备一:小件涂装流水线1) 用途:用于加强板、筋板等小件的流水涂装作业。
2) 工件规格表1 工件规格3) 工作效率:生产节拍10分钟/挂,3班制,每班8小时,要求设备具备不停机连续工作的能力,平均每月工作时间不小于700小时。
4) 工艺流程及工位数:5) 工件输送方式:吊钩输送及垂直地面链;6) 喷涂方式:手工静电喷涂7) 烘干炉加热能源:管道天燃气。
8) 油漆相关资料:2. 设备二:大件涂装流水线1)用途:用于配料站、主楼平台、皮带机等结构件的流水涂装作业。
2)工件规格表2 工件规格3)工作效率:生产节拍20分钟/挂,3班制,每班8小时,要求设备具备不停机连续工作的能力,平均每月工作时间不小于700小时。
4)工艺流程及工位数:5)工件输送方式:吊钩输送及垂直地面链; 6)喷涂方式:手工喷涂7) 烘干炉加热能源:管道天燃气。
8) 油漆相关资料:4. 水、电、压缩空气:均由公司主管网提供至涂装区域的一个点,请考虑分支管线的分布。
5. 当地标准:1)电源:220/380V 50Hz 单相/三相; 2) 环境温度:-11.3 ~40.6℃;3) 相对湿度:年最小相对湿度14%,年平均相对湿度81%。
6. 为注意美观及节约场地,喷漆室、刮灰打磨室、烘干室的排风装置请考虑安装到室内上空(架平台)。
7. 设计总原则:涂装工艺参照三一重工的涂装工艺.8. 设备交货期要求:合同生效后90日内交货。
- 1、下载文档前请自行甄别文档内容的完整性,平台不提供额外的编辑、内容补充、找答案等附加服务。
- 2、"仅部分预览"的文档,不可在线预览部分如存在完整性等问题,可反馈申请退款(可完整预览的文档不适用该条件!)。
- 3、如文档侵犯您的权益,请联系客服反馈,我们会尽快为您处理(人工客服工作时间:9:00-18:30)。
部件涂装生产线技术要求(涂装部分)工程内容工程内容:新建部件喷漆线1套、移动水帘喷漆房1套、脱脂室4套一、心体要求1、本工程为交钥匙工程,承建方负责生产线的设计、制造、安装、调试、人员培训和售后服务等内容。
2、承建方必须严格按照建设方提出的技术要求制定合理的工艺流程和设计切实可行的技术方案,满足建设方涂装生产要求。
3、设计工艺流程合理,技术切实可行,设备布置紧凑、整齐美观;设备选型既要满足技术要求,又要经济、合理、节省造价。
4、设计方案要达到国家环保和消防安全要求,并且作业环境符合国家安全、工业卫生的要求。
5、设计应充分考虑设备维修、维护的方便快捷。
6、电气系统采用集中控制,尽量靠近供电系统,自动化程度较高7、设计应考虑物料存储区域、转运方式。
8、设计及制造所选用的材料均不得含有硅酮成分。
三、涂装生产线基本生产纲领1、生产纲领:年产量:1200台/年,40挂/台2、产品基本参数:最大工件外形尺寸:L X W X H : 4500 X 1800 X 1700 mm 最大工件重量:6000 kg3、工作制度和年时基数:全年工作日:250 天工作班制:两班制班工作时制:10 小时设备开动率:90%以上4、厂房条件:L X W 60X 24m 下弦9.0m5、能源条件及要求:车间电源:380V/ 220V,50Hz加热采用电加热(能源为电能)气源、水源要求,乙方在设计图中明确提出。
四、工艺说明1 、工艺流程2、输送方式:自行葫芦输送生产节拍:6.5mi n/挂3、工艺参数:五、设备说明:品目一、上、下件用20吨电动车(数量:2套)设备说明:由我司废弃平车改造制作。
利用我司20吨平车由乙方改造成20吨电动平车,具体要求如下:品目二、喷漆、流平室(数量:各2套)1、工艺目的:为喷涂作业提供一个良好的涂覆场所和舒适的作业环境,提高涂层质量。
2、工艺设备:2.1喷漆室为水旋式喷漆室,由室体、三维小车、送风装置、地板格栅、排风装置、照明装置、漆雾处理装置、水槽、管路、远程可视系统等部分组成。
2.2喷、输漆系统选用美国固瑞克(GRACO)公司产品,采用人工静电喷涂方式,静电喷枪与外置式高压静电发生器连接,要求配套静电喷涂及辅助设备。
2.3在工作场所使用静电导体制作的操作工具应可靠接地。
2.4流平室由空调机组从设备的上部送风,保证室内温度为25C以上,排风机从设备的底部抽风。
3、设备组成说明:3.1 室体:喷漆室室体为通过式,室体主骨架采用型钢与 8 2.0 mm无花镀锌钢板制作,并在外部两侧安装钢化玻璃窗及外拆式照明灯箱装置,玻璃采用8 8.0m钢化玻璃,使操作区明亮舒适。
操作间两侧各安装一个门并带自动闭门器,供人员出入,所有室体必须设置逃生通道。
操作间壁板和型钢骨架单元及过滤框架之间涂密封胶(密封胶不能含有硅酮),确保密封,严防灰尘进入。
室体骨架为方钢管和工字钢,除考虑室体本身的承载外,还考虑送、排风风压不平衡时的风载和吊挂承载。
流平室室体为通过式,室体主骨架采用型钢与岩棉夹心保温板制作,并在两侧安装钢化玻璃窗及外拆式照明灯箱,玻璃采用8 8.0 m钢化玻璃,使操作区明亮舒适。
逃生门设置符合国家安全规定。
3.2三维小车:为便于喷漆操作,在底漆和面漆室两侧各设置一台三维小车,小车工作台可前伸800 m (电动伸缩)。
输漆泵、静电喷枪、油漆等要绑定在三维小车上。
另外,压缩空气管、静电喷枪与外置式高压静电发生器连接电缆一并置于桥式工程塑料拖链中,便于随车运动。
3.3 送风过滤装置:室体上部有动压室、静压室。
动压室内有空气分配器;静压室内有无纺布过滤层,从而保证风量均匀性和空气的洁净度。
顶部过滤材料设置在动静压室底部,过滤棉框架由碳钢板制作的框架支撑,中间用镀锌钢丝网支承,过滤棉放置在钢丝网上,上面用圆钢压框固定,更换过滤棉容易。
在动压室和静压室的侧面墙壁上,分区域设置带锁的空气密封门,门框装密封胶条。
通过带有梯子的维修检查平台,从动压室和静压室检修门可以分别进入动压室和静压室。
动压室和静压室保证空气平稳流动,在动压室内设有调节风量的机构,动、静压腔间设有压差计(压差计为数显,并可在集中控制面板上显示)。
3.4 地板格栅:地面有纵向双排工字钢支承,喷漆室操作间铺有碳钢地板格栅该格栅由40 x4扁钢和© 10圆钢焊接而成,其表面平整、防滑,成型后镀锌。
每块不超过30 kg/块,便于人员更换方便。
3.5 送、排风装置:喷漆室采用上送下吸的气流组织方式,送风装置采用分组送风,排风系统由排风机、防火风阀、风量调节阀及风管组成。
送风系统主要由送风机、风机座和型钢框架组成。
其中风机座壁板中均内填30伽厚岩棉保温材料,以便降声减振。
按涂装设计要求,喷漆房内有载风速为0.5 m/s 。
室体内径:见图送风管道上设有风量调节阀,风道采用厚度为2.0伽镀锌板制作。
排风系统风道用厚度为3.0伽钢板制作、防爆离心式排风机、防火风阀、手动风量调节风阀、排风管组成。
排风机布置在室外,风机为防爆风机,叶轮便于拆出检修,排风风道上设多叶调节阀,风阀能完全关闭。
排风机设有防雨隔音室。
排风机设有防火阀与自动消防系统及送风机组连锁。
排风风机壳体下应配备清除门和排水管及阀,积水可排入下水道。
排风风机底座上设有减震器。
排风系统中的水雾通过水盆底部的气水挡板碰撞后,大部份水滴顺挡水板流入底部集水池,同时在排风风管的风速设计上考虑较低的风速,避免风机运行过程中将水汽带出,不再在风道内设置气水分离室,降低设备投资费用。
3.6 漆雾处理装置:由水盆、水旋器、气水挡板组成。
水盆材料为4伽不锈钢板,水旋器选用2 mm不锈钢板制作,水旋器高出水盆60~75 mm,水旋口设有调节板,调节水旋器的高度,水盆下面的汽水挡板采用2 m不锈钢板,供水管采用孔状供水以保持一定液位,满足漆雾处理需要,水旋器之间的间距为1000m。
3.7 水循环系统:由循环管路、循环水泵、调节阀门、漆渣过滤装置等组成。
从喷漆室自流到循环水槽内的水经漆渣过滤装置过滤干净后再循环使用。
A、循环水泵:采用液下离心泵及不锈钢水管组成,将过滤后的净水送回喷漆室捕捉漆雾。
供水管采用Q235-A钢管制成。
阀门采用不锈钢阀门。
B 、循环水池:由循环水池、漆渣过滤装置等组成。
从喷漆室自流到循环水池内的水经漆渣过滤装置过滤干净后再循环使用。
过喷漆雾经过水旋器气水混合过滤后漆雾被截留在水中,流入到循环水池中,在水中加入漆雾凝聚剂,使水中的漆雾凝结成块,漂浮在水面上,定期进行人工捞渣。
循环水池:循环水池采用土建混凝土结构,制成迷宫式。
喷漆室含漆雾的水流入循环水池,经过滤沉降后净水由水泵送回喷漆室。
过滤装置:过滤装置安装在循环水池内,采用不锈钢网制造,用于挡住漆渣。
C、照明装置:在室体外侧壁安装照明装置,流平室内照度》800LUX,喷漆室内照度》800Lux,照明灯采用外拆式日光灯,采用钢化玻璃作为灯箱隔爆措施;在动、静压室内设有照明装置,便于过滤棉更换、检修用。
D、可燃气体浓度报警系统:室体内配置可燃性气体浓度报警器(一主机双探头)1套,当室体内的可燃性气体浓度过高时,发出警报,同时自动关闭设备的运行,以便随时检查设备,以防设备的使用出现意外情况。
3.8远程可视系统:喷漆室内安装远程可视系统,可对工件输送及喷涂过程全程监控4、主要参数:品目三、烘干室(数量:2套)1、主要技术参数:2、设备结构说明: 2.1工艺目的:使工件表面得到干燥。
2.2工作原理:采用远红外线直接加热,室体两侧设有热风循环管路。
工作时,通过风机将室内热空气循环,经过内循环作用,除吸进少量新鲜空气外,绝大部分热空气又被继续加热利用,送入到烘房内部,使得烘房内温度均衡,当温度达到设定温度时,部分远红外加热管自动关闭,当温度下降到设定温度时,加热管开启,使烤房内温度相对保持恒定。
3、设备组成:设备主要由室体、热风循环风机、远红外加热系统、控制系统等部分组成。
3.1 室体:室体由矩形型钢、角钢及岩棉夹心保温板组成。
烘干室保温层厚度为150 伽。
室壁及室顶均采用整体式保温壁板和顶板,板与板间的缝隙满焊(氩弧焊)。
室体保温采用优质保温岩棉,使得烘干室的热量散失减少到了最小限度既减少热桥现象;室体外部采用1.5伽厚的镀锌钢板制成,内层采用2.0伽厚的锌板制成;室体底部用型钢做成骨架,并铺设100 mm (容重:大于100 kg / m3)岩棉保温层,有效地解决底部保温和支撑设备的问题。
设备运行时噪音W 85分贝。
烘干室内设温度探测点,其中一点显示、控制和记录,另一点为显示,温控精度士5C;并设极限温度保护,防止温度过高,同时有数据记录(可存储到U 盘)。
室体为通过式,在烘干室进出口门洞两侧设有热风幕装置,减少烘干室的热量损失,提高热效率。
室体顶部设有防油烟凝聚滴落装置,防止污染工件。
3.2 加热系统:烘干室采用室内远红外线+电加热管混合加热方式,远红外加热装置均匀布置在室体两侧工件相对应的高度。
远红外灯管之间连接采用铜排和耐温导线。
3.3 室内风管:吸风管布置在烘干室室内顶部,保证室内送风均匀;送风管布置在烘干室室内底部,配置有可调节风口,用来调节风量和风速,以保证烘干室温均匀一致,风管采用2.5 mm镀锌钢板制作。
3.4热风循环装置:放置在地面上,由热风箱、风机和风管组成。
为减少热量损失,外部循环风管敷设50 m厚岩棉保温层。
循环风机选用YDW系列离心风机。
3.5废气处理:废气处理采用催化燃烧法处理烘干室排出的有机废气。
油漆烘干室废气排放符合国家及当地环保及消防安全要求。
品目四、修整室(数量:1套)1、设备说明:室体为通过式,由2.0 m无花镀锌钢板制成壁板,用型钢做骨架加固而成,并在室外两侧安装钢化玻璃窗及照明灯箱装置,使操作区明亮舒适。
侧面设置操作门,门上设有玻璃窗,方便人员出入和观察。
载物车可手动升降。
室体内工作区的照明为外拆式日光灯箱,灯管选用飞利浦品牌产品,玻璃采用8.0 m 钢化玻璃,灯箱安装在框架上,光照度》800Lux。
修整室地面铺设格栅,格栅下设有水槽,用排污泵将槽内污水定期排放。
室内粉尘过滤后排放。
2、主要参数:品目五、强冷设备(数量:2套)1、工艺目的:冷却工件使工件由烘干后的温度快速下降为30 C以下。
2、设备组成:该设备由室体、送排风系统、风嘴、过滤系统、调节阀等组成。
室体为通过式,顶部板设置成向两侧倾斜形折板,以防止可能的凝结水滴到工件上;镀锌钢板8 2.0 mm做内壁,外蒙8 1.5 mm波纹板,用方管200X 200X 8 mm 做主骨架加固而成,并在两侧布置铝制可调万向风嘴。
送、排风系统,新鲜空气由风机从房顶吸入,风管为 2.0 m的镀锌钢板,经过滤后通过风嘴吹响高温工件,风嘴装在壁板上并且方向可以调节,使工件冷却。