第二章-材料的断裂强度
材料失效分析(第二至四章解理断裂和沿晶断裂)

青鱼骨花样、瓦纳线
§3、影响解理断裂的因素
1、晶体结构 bcc、hcp—易发生解理断裂 fcc——不易发生解理断裂
2、显微组织 F—断口较光滑,微观呈河流条纹或舌状花样 P—断口呈不连续片层状 M—断口呈锯齿状,出现小刻面
3、温度 T↓,易导致解理断裂
T<Tc,晶体在塑性变形前产生解理裂纹,断口呈现脆性 T>Tc,晶体先发生塑变,后产生解理,即断裂时伴随一定的塑性变形
存在确定的位向关系
准解理裂纹形成机理示意图
准解理断口形貌
准解理断口形貌
第四章 沿晶断裂
1、定义:材料沿晶界(原奥氏体晶界、相界、焊合界面) 发生的断裂。
2、类型:韧性沿晶断裂(沿晶韧断) 脆性沿晶断裂(沿晶脆断)
3、产生原因
※脆性沉淀相沿晶界析出:钢中的碳化物
Al-Li合金中的δ(AlLi)相
扭转晶界——在亚晶界出产生新的裂纹,河流激增
大角度晶界:河流不能通过,在晶界出产生新的裂纹,向外扩展 ,
形成扇形花样
大角度晶界,扇形花样
3、舌状花样
特点:形状象“舌头”,一般在钢铁材料中成组出 现。
形成机理:
解理裂纹沿着孪晶面{112}产生二次解理及局部塑性变 形撕裂的结果。在低温、高速变形时容易发生孪生变形, 也就容易出现舌状花样。
例2 晶粒过分粗大—细化晶粒处理 晶界弱化——净化晶界 环境介质——改善工作环境 热应力——退火消除
精品文档 欢迎下载
读书破万卷,下笔如有神--杜甫
瓦纳线
(二)形成机理(模型)
1、解理台阶 解理裂纹与螺位错交截形成台阶
台阶形成过程的简化图
通过二次解理或撕裂相互连接形成台阶(撕裂棱)
台阶的性质
台阶在扩展过程中会发生合并或消失(台阶高度减小) 相同方向的台阶合并后高度增加 相反方向的台阶合并后高度减小或消失 台阶高度与柏氏矢量大小、位错密度之间存在一定关系
第二章 材料的脆性断裂与强度
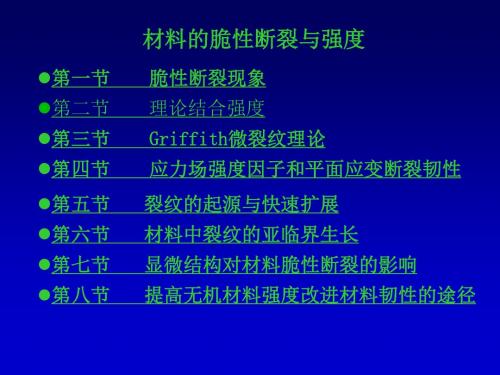
裂纹的三种扩展方式或类型 Ⅰ型(掰开型)张开或拉伸型,裂纹表面直 接分开。
Ⅱ型(错开型)滑开或面内剪切型,两个裂 纹表面在垂直于裂纹前缘的方向上相对滑动。 Ⅲ型(撕开型)外剪切型,两个裂纹表面在
平行于裂纹前缘的方向上相对滑动。
裂纹长度与断裂应力的关系:
等有关的系数.
k c c
1 2
k 是与材料、试件尺寸、形状、受力状态
在接近平衡位置 O 的区域,曲线可以用直线代替,服 从虎克定律:
x E E a
a 为原子间距 x 很小时 sin
因此,得:
2x
2x
th
E a
可见,理论结合强度只与弹性模量,表面能和晶 格距离等材料常数有关。 通常, 约为 aE ,这样,
E th 10
100
五.裂纹扩展的动力和阻力
1.裂纹扩展的动力 Irwin将裂纹扩展单位面积所降低的弹性 应变定义为应变能释放率或裂纹扩展力。 对于有内裂纹 2c 的薄板:
G
d we 2dc
c
E
2
其中 G为裂纹扩展的动力。
对于有内裂的薄板:
K
a c
临界状态:G c K c
E
2
(平面应力状态)
Inglis研究了具有孔洞的板的应力集中问题,得 到结论:孔洞两个端部的应力几乎取决于孔洞的长度 和端部的曲率半径,而与孔洞的形状无关。 Griffith根据弹性理论求得孔洞端部的应力 A
A c a2 1 2 , a c
c A 1 2
式中, 为外加应力。
K
3 xy 2r cos 2 sin 2 cos 2
2.2材料的强度理论与断裂理论
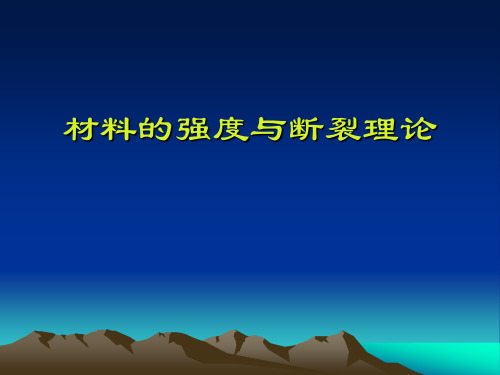
y
H B A D K
ys
o rp a
x
The region ABH represents forces that would be 上述简单分析是以裂纹尖端弹性解为基础的,故 present in an elastic material but cannot be carried 并非严格正确的。屈服发生后,应力必需重分布, in the elastic-plastic material because the stress 以满足平衡条件。 cannot exceed yield. The plastic zone must increase in size in order to carry these forces.
K Ic 如图所示。
1 b 。 2
无损检测发现裂纹长度在4mm以上,设计工作应力为 d
讨论:a 工作应力d=750MNm-2 时,检测手段能否保证防止发生脆断? b 企图通过提高强度以减轻零件重量,若b提高到1900MNm-2 是否合适? c 如果b提高到1900MNm-2 ,则零件的允许工作应力是多少?
计 算 主 应 力
屈 服 准 则
y xy 裂纹尖 y x dy 端屈服 r dx 区域的 (5-1) 2a x 形状与 尺寸
这里仅简单讨论沿裂纹线上屈服区域的大小。 在裂纹线上(=0),注意到 K p a ,有; x y
K1 a ; xy 0 2r 2p r
x= a cos[1 - sin sin3 ] 2 2 2r 2 a cos [1 sin sin3 ] (5-1) y 2 2 2 2r a sin cos cos3 xy r 2 2 2 2
材料的脆性断裂

2)产生新表面所需的表面能 使单位面积的原子平面分开所作的功应等于产生 两个单位面积的新表面所需的表面能,材料才能断裂。 设分开单位面积原子平面所作的功为 v ,则 λ λ 2 λσth 2πx 2πx 2 λσth (2.2)
v =∫ σth sin
0
设材料形成新表面的表面能为γ ,则 3)理论强度 λσ th 从上式可得: = 2γ
23
断裂力学
均匀性假设 仍成立,但 且仅在缺陷 选 处不连续 材
K IC
σ
C
工 维 缺陷 艺 修 评定
a
应用
i ,C
Ji, JC JR TR
SU
K
阻力C
断裂力学
裂纹扩展准则
响应
奇异场 控制参量
i
C T
T TC N f f i , a,...
f i C
24
25
26
27
28
29
§2 .4
应力场强度因子和平面应变 断裂韧性
一.断裂力学的提出
断裂力学是研究含裂纹物体的强度和裂纹扩展规律的科学。
30
1.断裂力学的产生
1.1 从二战以来的若干断裂事故说起
1943-1947年, 美国近500艘全焊船1000多起脆性破坏,238 艘报废。总是在焊接缺陷等应力集中区域,-3~4 °C水 1947年,苏联4500m3石油储罐,-43 ° C,底部和下部壳连 接处,大量裂纹。(低温、脆性、焊点应力集中、内外温差) 五十年代,美国北极星导弹固体燃料发动机壳体试验,发生 爆炸。高强度合金,传统强度和韧性指标合格,爆炸时工作压 力远低于许用应力。(裂纹) 1963年,美国F-111飞机训练中,左翼脱落,飞机坠毁,而 当时飞行速度、负荷远低于设计指标。(热处理不当、机翼枢 轴出现缺陷,疲劳载荷,裂纹)
断裂力学 第二章 能量守恒和断裂判据

对于小应变情况,由
c
2 x
2.1 固体的理论断裂强度
c
2 x
引入弹性系数E,则
E Ex
.
b0
综
合 考 虑
c
2 x
2
2 0
dx
c
2
2 0
dx
c
c
E
b0
1/ 2
此式即为完整晶体的理 想断裂强度的计算公式
2.1 固体的理论断裂强度 公式的几点说明
c
E
b0
1/ 2
裂纹对材料强度的影响
2.2 裂纹对材料强度的影响
一:实际的断裂强度
1:金属的实际断裂强度要比理论计算的断裂强度低的 多,至少低一个数量级,而陶瓷、玻璃的实际断裂强 度则更低。
2:原因 (1) 实际断裂强度低的原因是因为材料内部存在有裂纹
2.2 裂纹对材料强度的影响
裂纹萌生:
(a)玻璃结晶后,由于热应力产生固有的裂纹;
2.2 裂纹对材料强度的影响
例如如图所示无限大薄平板,
承受单向均匀拉应力作用,板
中存在贯穿的椭圆形切口,其
长轴为2a,短轴为2b,则最大
y
拉应力发生在椭圆长轴端点A(
或A′)处,其值为
A 2b
Ax
y
(1 2 a)
max
b
2a
2.2 裂纹对材料强度的影响
端点A点处的 曲率半径
b2
a
y
2.2 裂纹对材料强度的影响
(2)裂纹尖端的应力集中必然导致材料的实际断裂强度 远低于该材料的理论断裂强度
具有裂纹的弹性体受力以后,在裂纹尖端区域将 产生应力集中现象。但是应力集中是局部性的,离开 裂纹尖端稍远处,应力分布又趋于正常。
材料的断裂失效形式与机理

第二章 材料的断裂失效形式与机理
2.5 硬度(hardness) ● 材料抵抗表面局部变形的能力叫硬度
材料的硬度与抗拉强度、弹性模量等有一定的关 联性,对材料的加工、磨损都有重要影响。
测试方法常有三种:压痕法、回跳法和刻痕法。
1. 布氏硬度HB(Brinell hardness)
布氏硬度是用一定载荷P,将淬火钢球压头压入被 测材料表面,保持一定时间后卸载,根据压入的直径d 的压痕面积A(图2-12)来获得。计算式为:
洛氏硬度可以直读,操作方便,适用广泛,可测 量低硬度和高硬度的金属材料。但洛氏硬度载荷大, 标尺不统一,不适用于测定硬而脆的薄层。薄层材料 一般采用维氏硬度测定。
表 2-1 三种类型的洛氏硬度值及应用
K 0.2 0.26 0.2
第二章 材料的断裂失效形式与机理
3. 维氏硬度HV(Vickers hardness)
3. 断口分析内容 断口分析一般涉及宏观分析和微观分析。
(1)宏观分析 用肉眼、放大镜或体视显微镜对断口进行直接观察,
依据断口的宏观形貌,初步确定失效模式和断裂起裂点, 为深入分析和判明失效原因提供依据。
(2)微观分析 采用多种分析仪器对断口进行观察和分析。一般采
用扫描电镜 (SEM) 和能谱仪(EDS),初步观察断口的 微观形态、确定材料成分,为后续所需的深度分析比如表 面分析如XPS、AES、SIMS等指明方向,厘清失效机理。
显微硬度的压头形状与维氏硬度一样,只是体积 小、载荷小,小到仅有几十克至几百克,。例如,10g、 50g、100g、200g。其压痕长度以微米表示,计算 公式为:
HVP=1854.4P/d2 其中,P是g,d是μm。
(2-9)
第二章 材料的断裂失效形式与机理
高分子材料的断裂与强度
取向
高聚物加工过程中分子链沿一定方向取向,使材料力学性 能产生各向异性,在取向方向得到增强。 对于脆性材料,取向使材料在平行于取向方向的强度、模 量和伸长率提高,甚至出现脆-韧转变,而在垂直于取向
方向的强度和伸长率降低。
对于延性、易结晶材料,在平行于取向方向的强度、模量
提高,在垂直于取向方向的强度下降,伸长率增大。
当应力状态由压缩改变为简单剪切、拉伸或冲击时,热塑 性高聚物材料的韧性依次减小、脆性增大。动态负荷下, 高聚物可在106~107周期后破裂。另外,长期维持静态负 荷下,由于蠕变,高聚物也可以在低应力值时断裂。
(一)高聚物的基本结构参数对强度的影响
高聚物弹性模量依赖于结构因素,凡属分子量较大、柔顺性较小、极 性较强、取向度较高、结晶度较高和交联密度较大的高聚物,弹性模 量的数值均较大。高聚物的其他力学性能与弹性模量之间有相互对应 的关系。弹性模量较大的聚合物,抗冲击强度就较小,但硬度、挠曲 强度、抗压强度均较大。
(1)高分子的化学结构
一般来说,分子链间的作用力小、取代基体积小、极性弱的大分子
链其柔顺性较好,此类高聚物在较小外力下便产生高弹形变,因此较 软,屈服强度低、弹性模量小、拉伸强度低、伸长率达;而增大高分
子的极性或产生氢键可使强度提高,另外主链具有芳杂环结构的高聚
物,其强度和模量都比脂肪族主链高。为了提高弹性模量和强度,可 以在分子链中引入极性基团或环状结构。 注意:极性基团过密或取代基过大,僵硬性太大,会造成加工成型的 困难,还会带来脆性,反而限制了聚合物的使用范围。
高分子材料断裂过程:
裂纹引发(成核)
裂纹扩展
脆性断裂过程基本可分为三个阶段:
断裂源首先在材料最薄弱处形成,一般是主裂纹通过单 个银纹扩展; 随着裂纹扩展和应力水平提高,主裂纹不再是通过单个 银纹扩展,而是通过多个银纹扩展,因而转入雾状区; 当裂纹扩展到临界长度时,断裂突然发生。
材料物理性能 第二部分 材料的断裂
脆性断裂 是材料断裂前没有明显的宏观塑性变形,没有明显的迹象,往往
表现为突然发生的快速断裂过程。 根据断裂时应力和时间的关系,断裂大致可以分为两大类: 一类称为瞬时断裂,指的是在以较快的速率持续增大的应
力作用下发生的断裂; 另一类称为延迟断裂,包括材料在以缓慢的速率持续增大
的外力作用下发生的断裂、材料在承受恒定 外力作用一段 时间之后发生的断裂以及以及材料在交变荷载作用一段时 间之后发生的断裂等。延迟断裂有时也称为疲劳断裂
2、Griffith的理论推导 裂纹的存在使得实际材料的断裂强度σC低于理论结合强σth
Griffith从能量平衡的观点出发,认为 裂纹扩展的条件是:物体内储存的弹性 应变能的减小大于或等于开裂形成两个 新表面所需增加的表面能。反之,裂纹 不会扩展。即物体内储存的弹性应变能 的是裂纹扩展的动力
外力力做功 弹性应变能
实际断裂强度c
2 c E
临界情况 c
c
E
4c
裂纹的存在使得实际材料的断裂强度σC低于理论结合强σth。 裂纹扩展条件为:
2
c a
E a
实际材料中存在的微裂纹或缺陷端部处的应力状态比Inglis所 考虑的椭圆孔的情况要复杂 得多。因此,Griffith的微裂纹理 论是从能量的角度出发研究裂纹扩展条件的。
当
<
时为稳态状态,裂纹不会扩展;
反之,为失稳定状态,裂纹发生迅速扩展;
当:
=
则为裂纹扩展的临界状态。
因为:
则,平面应力状态的临界应力为:
c
2E C
平面应变状态的临界应力为:
c
2E (1 u2 )c
Griffith推导的结果与(2.12)基本一致,只系数稍有差别,与 (2.6)理论强度公式类似。(2.6)中a为原子间距,而上式中c 为裂纹半长,可见使a、 c在同一数量级,就可以使材料达到理论 强度
材料物理性能考试重点
第一章无机材料的受力形变1.形变:材料在外力的作用下发生形状与尺寸的变化2.影响弹性模量大小的因素?①化学键(本质):共价键、离子键结合力强,弹性模量大。
分子键结合力弱,弹性模量小。
②原子间距:正应力使原子间距减小,弹性模量增大;张应力使原子间距增大,弹性模量减小。
温度升高,原子间距增大,弹性模量降低。
3.弹性模量的测定⏹静态法:采用常规三点弯曲试验加载方式;在正式读数前,在低载荷进行几次反复加载、卸载;试样尺寸有要求。
误差较大⏹动态法:三点弯曲受力,外加载荷周期性性变化,产生谐振;弯曲振动测E,扭曲振动测G;试样尺寸有要求。
误差较小4.塑性:材料在外力去除后仍保持部分应变而不能恢复的特性5.延展性:材料发生塑性形变而不断裂(破坏)的能力6.晶体塑性形变两种基本形式:•滑移是指在剪切应力作用下晶体一部分相对于另部分发生平移滑动。
在显微镜下可观察到晶体表面出现宏观裂纹,并构成滑移带。
•孪晶是晶体材料中原子格点排列一部分与另部分呈镜像对称的现象。
镜界两侧的晶格常数可能相同、也可能不同。
7.晶体滑移的条件几何条件:滑移一般发生在晶面指数小、原子密度大的晶面(主要晶面)和晶面指数小的晶向(主要晶向)上:由于晶面指数小的面,面间距越大,原子间的作用力越小,易产生相对滑动;晶面指数小的面,原子的面密度大,滑过滑动平面使结构复原所需的位移量最小,即柏氏矢量小,也易于产生相对滑动。
静电作用因素:同号离子存在巨大的斥力,如果在滑动过程中相遇,滑动将无法实现。
8.粘度定义:使相距一定距离的两个平行平面以一定速度相对移动所需的力。
单位:Pa· s,9.影响粘度的因素?温度:一般温度升高,粘度下降。
时间:从高温状态冷却到退火点,再加热其粘度随时间增加而增加;而预先在退火点以下保持一定时间后,其粘度随时间增加而降低,但时间大大缩短。
组成:改性阳离子不同,粘度变化不同;但改性阳离子的加入,在任何温度下总会使粘度降低。
材料的断裂和韧性
脆性断裂是材料断裂前基本上不产生明显的宏观塑 性变形,没有明显预兆,往往表现为突然发生的快 速断裂过程,因而具有很大的危险性。
脆性断裂的断口,一般与正应力垂直,宏观上 比较齐平光亮,常呈放射状或结晶状.
淬火钢、灰铸铁、陶瓷、玻璃等脆性材料的断 裂过程及断口常具有上述特征。
2.高分子材料的脆性断裂和韧性断裂
脆韧判据:
断裂面形貌 σ-ε曲线 断裂伸长率 或断裂能
注意
试样发生脆性断裂或者韧性断裂与材料组成有关,除 此之外,同一材料是发生脆性断裂还是韧性断裂还与 温度、拉伸速率、试样的几何形状以及所承受的应力 状态有关。
二、断裂强度
强度是材料抵抗外力破坏的能力。对于各种不同的破坏力, 有不同的强度指标:拉伸强度、弯曲强度、冲击强度、压缩 强度。
2
102 109 2.5 1010
2
2
40 109 40GPa
若用E的百分数表示,则 σth≈40GPa=E/5 .
结论:
1
th
E
a
2
• 理论强度与弹性模量、表面能、晶格间距等材料常数 有关,要想得到高强度的固体,就要求E、大,而a小
一、断裂的类型
材料的断裂过程大都包括裂纹的形成与扩展两个阶 段。随着材料温度、应力状态、加载速度的不同,材 料的断裂表现出多种类型。 按照不同的分类方法,将 断裂分为以下几种:
根据断裂前与断裂过程中材料的宏观塑性变形的程度 脆性断裂;韧性断裂;
按照晶体材料断裂时裂纹扩展的途径
穿晶断裂;沿晶断裂;
根据断裂机理分类 解理断裂;剪切断裂;
根据断裂面的取向分类 正断;切断。
- 1、下载文档前请自行甄别文档内容的完整性,平台不提供额外的编辑、内容补充、找答案等附加服务。
- 2、"仅部分预览"的文档,不可在线预览部分如存在完整性等问题,可反馈申请退款(可完整预览的文档不适用该条件!)。
- 3、如文档侵犯您的权益,请联系客服反馈,我们会尽快为您处理(人工客服工作时间:9:00-18:30)。
第二章2.1固体的理论结合强度 2.2 材料的断裂强度2.3 裂纹的起源与快速扩展 2.4 材料的断裂韧性2.5显微结构对脆性断裂的影响 2.6无机材料强度的统计性质 2.7材料的硬度第二章 材料的脆性断裂与强度2.1固体的理论结合强度无机材料的抗压强度约为抗拉强度的10倍。
所以一般集中在抗拉强度上进行研究,也就是研究其最薄弱环节。
要推导材料的理论强度,应从原子间的结合力入手,只有克服了原子间的结合力,材料才能断裂。
如果知道原子间结合力的细节,即知道应力-应变曲线的精确形式,就可算出理论结合强度。
这在原则上是可行的,就是说固体的强度都能够根据化学组成、晶体结构与强度之间的关系来计算。
但不同的材料有不同的组成、不同的结构及不同的键合方式,因此这种理论计算是十分复杂的,而且对各种材料都不一样。
为了能简单、粗略的估计各种情况都适应的理论强度,Orowan 提出了以正弦曲线来近似原子间约束力随原子间距离X 的变化曲线(见图2.1),得出λπσσXth 2sin ⨯= 2-1式中,σth为理论结合强度;λ为正弦曲线的波长。
图2.1 原子间约束力与距离的关系 将材料拉断时,产生两个新表面,因此单位面积的原子平面分开所做的功应等于产生两个单位面积的新表面所需的表面能,材料才能断裂。
设分开单位面积原子平面所做的功为w,则πλπλλπσλπσσλλth th th x dxxw ===-⎰]2cos [22022sin2-2 设材料形成新表面的表面能为γ(这里是断裂表面能,不是自由表面能),则w=2γ,即γπλο2=th ,λπγσ2=th 2-3 接近平衡位置o 的区域,曲线可以用直线代替,服从虎克定律: E a xE ==εσ 2-4 a 为原子间距。
X 很小时 sinλπλπxx22≈2-5将(2.3),(2.4)和(2.5)式代入(2.1)式,得aE thγσ=2-6 式中a 为晶格常数,随材料而异。
可见理论结合强度只与弹性模量、表面能和晶格距离等材料常数有关,属于材料的本证性能。
(2.6)式虽然是粗略的估计,但对所有固体均能应用而不涉及原子间的具体结合力。
通常γ约为aE/100,这样,(2.6)式可写成10Eth =σ 2-7 更精确的计算说明(2.6)式的估计稍偏高。
一般材料性能的典型数值为:E=300GPa,/1J =γm 2,a=3⨯10-10m,代入(2.6)式算出σth=30GPa ≈10E2-8 要得到高强度的固体,就要求E 和γ大,a 小。
实际材料中只有一些极细的纤维和晶须其强度接近理论强度值.例如熔融石英纤维的强度可达24.1GPa,约为E/3(E,72Gpa),碳化硅晶须强度6.47GPa,约为E/70(E,470Gpa),氧化铝晶须强度为15.2GPa,约为E/25(E,380Gpa)。
尺寸较大的材料实际强度比理论强度低的多,,约为E/100-E/1000,而且实际材料的强度总在一定范围内波动,即使是用同样的材料在相同的条件下制成的试件,强度值也有波动。
一般试件尺寸大,强度偏低。
为了解释这种现象,人们提出了各种假说,甚至怀疑理论强度的推导过程等,但都没有抓住断裂的本质。
直到1920年,Griffith 为了解释玻璃的理论强度与实际强度的差异,提出了微裂纹理论,才解决了上述问题。
后来经过不断的发展和补充,逐渐成为脆性断裂的主要理论基础。
§2.2 材料的断裂强度2.2.1 材料的断裂材料的断裂过程包括裂纹的形成与扩展两个阶段,按照材料宏观塑性变形的程度,可以分为韧性断裂与脆性断裂;按照断裂时裂纹扩展的路径,分为穿晶断裂与沿晶断裂;(1) 脆性断裂材料在实际应力远低于理论强度时发生断裂,不产生塑性形变仅产生很小的塑性形变,断裂前无先兆,这种断裂方式就称为脆性断裂。
它表现在断裂发生在弹性应变状态下,没有经过塑性变形阶段而直接形成的断裂。
不仅是脆性材料才会产生这种断裂,材料内部存在微裂纹,或者某些材料在低温下受到冲击等都有可能产生脆性断裂。
根据断口特征可以分为以下三种情况:解理断裂,裂纹沿解理面扩展;解理断裂断口的轮廓垂直于最大拉应力方向。
新鲜的断口都是晶粒状的,有许多强烈反光的小平面(称为解理刻面)。
图2-2为某材料典型的解理断口电子图像。
解理断口电子图像的主要特征是“河流花样”,河流花样中的每条支流都对应着一个不同高度的相互平行的解理面之间的台阶。
解理裂纹扩展过程中,众多的台阶相互汇合,便形成了河流花样。
在河流的“上游”,许多较小的台阶汇合成较大的台阶,到“下游”,较大的台阶又汇合成更大的台阶。
河流的流向恰好与裂纹扩展方向一致。
所以人们可以根据河流花样的流向,判断解理裂纹在微观区域内的扩展方向。
图2-2解理断口电子图像沿晶断裂如图2-3所示,裂纹走向沿着晶界,并不在某一平面内运动,晶粒特别粗大时形成石块或冰糖状断口,晶粒较细时形成结晶状断口(图2-3a)。
沿晶断裂的结晶状断口比解理断裂的结晶状断口反光能力稍差,颜色黯淡。
(a)沿晶断裂(b)穿晶断裂图2-3 某材料典型的断口扫描电镜图穿晶 ( 晶内 ) 断裂如图2-3b 所示,裂纹沿着多晶粒的解理穿过,而不管晶界的位置如何。
(2) 韧性断裂材料断裂时经过宏观塑性变形阶段、可观察到明显的缩颈现象,称为韧性断裂。
断口呈盆状或杯状,金属材料的断裂多属此种(图2-4)。
(a )材料的宏观图 (b )扫描电镜图图2-4 某材料典型的韧性断裂图2.2.2 裂纹尖端应力集中问题Griffith 认为实际材料中总是存在许多细小的裂纹或缺陷,在外力作用下,这些裂纹和缺陷附近产生应力集中现象。
当应力达到一定程度时,裂纹开始扩展而导致断裂。
所以断裂并不是两部分晶体同时沿整个界面拉开,而是裂纹扩展的结果,微裂纹理论抓住了脆性断裂问题的本质。
Inglis 研究了具有孔洞的板的应力集中问题,得到一个重要结论:空洞两个端部的应力几乎取决于孔洞的长度和端部的曲率半径而与孔洞的形状无关。
在一个大而薄的平板上,设有一穿透的孔洞,不管孔洞是椭圆还是菱形,只要孔洞的长度(2c )和端部曲率半径ρ不变,则孔洞端部的应力不会有很大的改变。
根据弹性理论求得孔洞端部的应力A σ为⎪⎪⎭⎫⎝⎛+=ρσσc A 21 2-9 式中,σ为外加应力。
如果c ﹥﹥ρ,即为扁平的锐裂纹,则c /ρ将很大,这时可略去式中括号内的1,得ρσσcA 2= 2-10Orowan 注意到ρ是很小的,可近似认为与原子间距a 的数量级相同,如图2.5所示,图2.5 微裂纹端部的曲率对应于原子间距这样可将(2.10)式写成 accA σρσσ22== 2-11 当A σ等于(2.6)式中的理论结合强度th σ时,裂纹就被拉开而迅速扩展,裂纹扩展,使c 增大,A σ又进一步增加。
如此恶性循环,材料很快断裂。
Inglis 只考虑了裂纹端部一点的应力,实际上裂纹端部的应力状态是很复杂的。
2.2.3 材料的断裂强度Griffith 从能量的角度研究裂纹扩展的条件:物体内储存的弹性应变能的降低大于等于开裂形成两个新表面所需的表面能。
反之,前者小于后者,裂纹则不会扩展。
在求理论强度时曾将此概念用于理想的完整晶体。
Griffith 将此概念用于有裂纹的物体,认为物体内储存的弹性应变能的降低(或释放)就是裂纹扩展的动力。
我们用图 2.6来说明这一概念并导出这一临界条件。
图2.6 裂纹扩展临界条件的导出将一单位厚度的薄板拉长到,l l ∆+然后将两端固定。
此时板中储存的弹性应变能为)(211l F W e ∆•=。
然后人为地在板上割出一条长度为2c 的裂纹,产生两个新表面,原来储存的弹性应变能就要降低,有裂纹后板内储存的应变能为l F F W e ∆•∆-=)(212,应变能降低为l F W W W e e e ∆•∆=-=2121,欲使裂纹进一步扩展,应变能将进一步降低。
降低的数量应等于形成新表面所需的表面能。
由弹性理论可以算出,当人为割开长2c 的裂纹时,平面应力状态下应变能的降低为Ec W e 22σπ=2-12式中,c 为裂纹半长;σ为外加应力;E 是弹性模量。
如为厚板,则属平面应变状态,此时 Ec W e 222)1(σπμ-= 2-13式中,μ为泊松比。
产生长度为2c ,厚度为1的两个新断面所需的表面能为γc W s 4= 2-14 式中,γ为单位面积上的断裂表面能,单位为J/m 2。
裂纹进一步扩展2dc ,单位面积所释放的能量为dcdw e2,形成新的单位表面积所需的表面能为dc dw s 2,因此,当dc dw e 2<dc dw s 2时,为稳定状态,裂纹不会扩展;反之,dc dw e 2>dcdw s2时,裂纹失稳,迅速扩展;当dc dw e 2=dcdw s2时,为临界状态。
又因 dc dw e 2=E cE c dcd 222)(2πσσπ= 2.15dc dw s 2=γγ2)4(2=c dcd2.16 因此临界条件是γσπ22=Ec c 2-17由此推出的临界应力为CE c πγσ2=2-18 如果是平面应变状态,则cE c πμγσ)1(22-=2-19 这就是Griffith 从能量观点分析得出的结果,称之为断裂强度。
和(2.6)式理论强度的公式很类似,(2.6)式中a为原子间距,而式(2.18)中c为裂纹半长。
可见,如果我们能控制裂纹长度和原子间距在同一数量级,就可使材料达到理论强度。
当然,这在实际上很难做到,但已给我们指出了制备高强材料的方向。
即E和γ要大,而裂纹尺寸要小。
应注意(2.18)式是从平板模型推导出来的,物体几何条件的变化,对结果也会有影响。
Griffith用刚拉制的玻璃棒做实验。
玻璃棒的弯曲强度为6GPa,在空气中放置几小时后强度下降成0.4GPa。
强度下降的原因是由于大气腐蚀形成表面裂纹。
还有人用温水溶去氯化钠表面的缺陷,强度即由5Mpa提高到1.6GPa。
可见表面缺陷对断裂强度影响很大。
还有人把石英玻璃纤维分割成几段不同的长度,测其强度时发现,长度为12cm时,强度为275Mpa;长度为0.6cm时,强度可达760Mpa。
这是由于试件长,含有微裂纹的机会就多。
其他形状试件也有类似规律,大试件强度偏低,这就是所谓的尺寸效应。
弯曲试件的强度比拉伸试件的强度高,也是因为弯曲试件的横截面上只有一小部分受到最大拉应力的缘故。
从以上实验可知,Griffith微裂纹理论能说明脆性断裂的本质-------微裂纹扩展,且与实验相符,并能解释强度的尺寸效应。
在实际应用中,式2.18中的γ采用断裂表面能,断裂表面能γ比自由表面能大。
这是因为储存的弹性应变能除消耗于形成新表面外,还有一部分要消耗在塑性形变、声能、热能等方面。
表2.1列出了一些单晶材料的断裂表面能。