第二章 材料的脆性断裂与强度
第二章 钢结构的材料
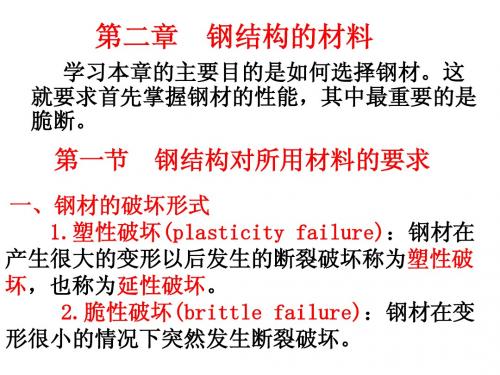
五、复杂应力状态的影响
在复杂应力如平面或立体 应力作用下,钢材的屈服并 不只取决于某一方向的应力, 而是由反映各方向应力综合 影响的 屈服条件来确定。
eq ( x y y z z x ) 3( )
第二节
钢材的主要机械性能
• 钢材的机械性能(力学性能)通常是指钢厂生 产供应的钢材在标准条件下拉伸、冷弯和冲击 等单独作用下显示出的各种机械性能。它们由 相应实验得到,试验采用的试件的制作和试验 方法都必须按照各相关国家标准规定进行。 一、单向拉伸时的性能 标准试件在室温(100C~350C) 、以满足静 力加载的加载速度一次加载所得钢材的应力 ζ ~ ε 应变曲线显示的钢材机械性能如下::
二、疲劳计算
• 反复荷载作用产生的应力重复一周叫做一个循环。 Δ ζ =ζ max-ζ min称为应力幅,表示应力变化的幅 度。 • 试验表明,焊接结构发生疲劳破坏并不是名义最 大应力ζ max作用的结果,而是焊缝部位足够大小 的应力幅反复作用的结果。非焊接结构的的疲劳 寿命不仅与应力幅有关,还与 其他因素有关。 规范把疲劳计算公式中的应力幅调整为折算应力 幅,以反映其实际工作情况。 • 疲劳计算的公式是以试验为依据的,分为常幅和 变幅疲劳两种情况进行计算。
(2)槽钢
有热轧普通槽钢和轻型槽钢两种。槽 钢规格用槽钢符号 [ 或Q[表示。 例如,普通槽钢[10、[20a,轻型槽钢Q[20a。 (3)工字钢 有普通工字钢和轻型工字钢两种。 例如,普通工字钢I18、I50a,轻型工字钢QI50。 (4)H型钢 H型钢比工字钢的翼缘宽度大并为等 厚度,截面抵抗矩较大且质量较小,便于与其它 构件连接。热轧H型钢分为宽、中、窄翼缘H型钢, 它们的代号分别为HW、HM和HN。例如HW260a、 HM360、HN300b。
材料的脆性断裂范文

材料的脆性断裂范文材料的脆性断裂是指在受到应力作用时,材料很快且突然地发生断裂现象。
相比之下,塑性断裂是指材料在受到应力作用时发生塑性变形,即产生塑性流动,直到最终断裂。
脆性断裂通常发生在脆性材料中,例如陶瓷、玻璃和一些金属。
脆性断裂的原因有很多,可以从微观和宏观两个层面进行解释。
首先,从微观层面来看,脆性断裂主要是由于材料中的微观缺陷引起的。
材料中存在各种形式的缺陷,如晶格缺陷、孔洞或裂纹。
当外部应力施加到材料上时,应力集中于缺陷周围,导致局部应力非常高,从而发生断裂。
此外,微观缺陷还可以作为裂纹的起始点,在外部应力的作用下裂纹扩展,最终导致材料的完全破坏。
其次,从宏观层面来看,脆性断裂还与材料的结构和形状有关。
晶体结构的不规则性和结晶缺陷可以导致应力集中,从而增加材料的脆性。
此外,材料的形状和尺寸也会影响脆性断裂的发生。
当材料的粗细比较大时,断裂形式可能更加脆性,因为裂纹的扩展路径更直接。
此外,材料的温度和湿度也会影响脆性断裂的发生。
高温和高湿环境会导致材料内部的微观缺陷扩展和形成新的裂纹,从而加剧脆性断裂的发生。
针对脆性断裂的问题,可以采取一些措施来改善材料的断裂韧性。
首先,加入适量的合金元素可以改变材料的晶界形态,减少晶界裂纹的形成,并增加材料的韧性。
其次,合理控制材料的热处理过程可以调整晶粒大小和组织结构,从而改善材料的韧性。
此外,合理设计材料的形状和尺寸,减少应力集中区域的存在,也可以降低材料的脆性断裂风险。
总之,材料的脆性断裂是由微观缺陷和宏观结构等多种因素共同作用引起的。
了解脆性断裂的原因和机制,可以指导我们采取适当的措施来改善材料的韧性,提高材料的断裂强度和可靠性。
材料力学性能-第2章

1.6 塑性材料的拉伸力学行为
当塑性材料所受的应力低于弹性极限, 其力学行为可近似地用虎克定律加以表述。 当材料所受的应力高于弹性极限,虎克定律 不再适用。此时,材料的变形既有弹性变形 又有塑性变形,进入弹塑性变形阶段,其力 学行为需要用弹-塑性变形阶段的数学表达 式,或称本构方程加以表述。
真应力—真应变的定义:
L dL
0
L
ln
L 1 ln(1 e) ln( ) Lo 1
在弹-塑性变形阶段,只有真应力-真 应变曲线才能描述材料的力学形为。 绝大多数金属材料在室温下屈服后, 要使塑性变形继续进行,必须不断增 大应力,所以在真应力-真应变曲线上 表现为流变应力不断上升。这种现象 称为形变强化。
第二章 材料在拉伸载荷下 的力学行为
例题
1、图示为四种材料的工程 应力-应变曲线,请根据该图 回答以下问题并简述原因 (1)弹性模量最高的材料 (2)伸长量最大的材料 (3)韧性最好的材料 (4)脆性断裂的材料 (5)出现“颈缩”的材料
2、某圆柱形金属拉伸试样的直径为10mm,标距为
2、典型的拉伸曲线
s= 0.2
s
e
e
e
b
e
e
e
E /e
1.4 拉伸性能 弹性模量E: 单纯弹性变形过程中应力与应变 的比值。
E e
屈服强度s:
对于拉伸曲线上有明显的屈服平台的材料,塑性 变形硬化不连续,屈服平台所对应的应力即为屈服强度, 记为s
s = Ps / A0
σb = Pmax/A0 延伸率:
材料的塑性常用延伸率表示。测定方法如下:拉伸 试验前测定试件的标距L0,拉伸断裂后测得标距为Lk, 然而按下式算出延伸率
第二章 材料的脆性断裂与强度
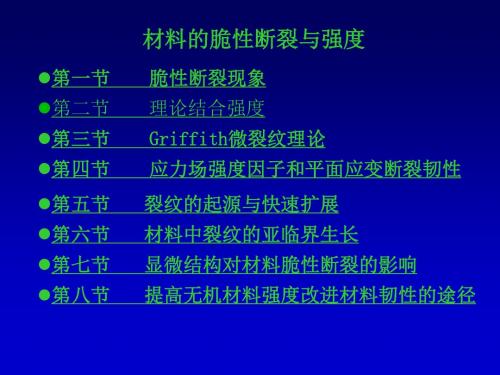
裂纹的三种扩展方式或类型 Ⅰ型(掰开型)张开或拉伸型,裂纹表面直 接分开。
Ⅱ型(错开型)滑开或面内剪切型,两个裂 纹表面在垂直于裂纹前缘的方向上相对滑动。 Ⅲ型(撕开型)外剪切型,两个裂纹表面在
平行于裂纹前缘的方向上相对滑动。
裂纹长度与断裂应力的关系:
等有关的系数.
k c c
1 2
k 是与材料、试件尺寸、形状、受力状态
在接近平衡位置 O 的区域,曲线可以用直线代替,服 从虎克定律:
x E E a
a 为原子间距 x 很小时 sin
因此,得:
2x
2x
th
E a
可见,理论结合强度只与弹性模量,表面能和晶 格距离等材料常数有关。 通常, 约为 aE ,这样,
E th 10
100
五.裂纹扩展的动力和阻力
1.裂纹扩展的动力 Irwin将裂纹扩展单位面积所降低的弹性 应变定义为应变能释放率或裂纹扩展力。 对于有内裂纹 2c 的薄板:
G
d we 2dc
c
E
2
其中 G为裂纹扩展的动力。
对于有内裂的薄板:
K
a c
临界状态:G c K c
E
2
(平面应力状态)
Inglis研究了具有孔洞的板的应力集中问题,得 到结论:孔洞两个端部的应力几乎取决于孔洞的长度 和端部的曲率半径,而与孔洞的形状无关。 Griffith根据弹性理论求得孔洞端部的应力 A
A c a2 1 2 , a c
c A 1 2
式中, 为外加应力。
K
3 xy 2r cos 2 sin 2 cos 2
第二章 焊接结构的脆性断裂

造成脆性断裂的原因
材料选用不当 起源于焊接结构的不利因素 结构的构造越来越复杂 使用条件越来越恶劣(如低温、海洋环境等) 荷载、钢材强度、板厚等都越来越大 设计计算方法越来越先进精细,安全储备降低
二、金属材料脆性断裂的能量理论
(格里菲斯)Griffith裂纹理论
基点:材料中已存在裂纹 在裂纹尖端引起应力集中,在外加应力小于理 论断裂强度时裂纹扩展,实际断裂强度大大降低。 大量研究和试验表明,固体材料的实际断裂强度只 有它理论断裂强度的1/10~1/1000.
防止结构发生脆性破坏的两个设计准则
①
开裂控制(防止裂纹产生准则)
设计要求在焊接结构最薄弱的部位,即焊接接头 处具有抵抗脆性裂纹产生的能力,即抗裂能力。
②
扩展控制(止裂性能准则)
设计要求如果在这些部位产生了脆性小裂纹,其 周围材料应具有将其迅速止住的能力。
(二)断裂评定方法
金属材料的断裂除与材料本质特征有关外,还与 结构所处于的温度、加载速度、应力状态等外加因 素有关,其中温度是个主要因素。 对于一种材料有两个临界温度即开裂温度和 止裂温度。开裂、止裂温度的高低可以用来衡量材 料的抗裂性能和止裂性能。且开裂、止裂的温度越 低,材料的抗开裂性能和止裂性能就越好。
1、冷应变时效:材料经历切割、冷热成形(剪切、弯
曲、矫正)等工序使材料发生应变时效导致材料变脆。
2、热应变时效:在焊接时,近缝区某些加工时留下的刻
槽,即缺口尖端附近或多层焊道中已焊完焊道中的缺陷附 近,金属受到热循环和热塑变循环的作用,产生焊接应力-应 变集中,导致较大的塑性变形,引起应变时效。 解决措施:焊后经过550~650℃热处理可以消除两类应变时 效对低碳钢和一些合金结构钢的影响,恢复其韧性。
《无机材料物理性能》课后习题答案解析

课后习题《材料物理性能》第一章材料的力学性能1-1一圆杆的直径为2.5 mm 、长度为25cm 并受到4500N 的轴向拉力,若直径拉细至 2.4mm ,且拉伸变形后圆杆的体积不变,求在此拉力下的真应力、真应变、名义应力和名义应变,并比较讨论这些计算结果。
解:由计算结果可知:真应力大于名义应力,真应变小于名义应变。
1-5一陶瓷含体积百分比为95%的Al 2O 3 (E = 380 GPa)和5%的玻璃相(E = 84 GPa),试计算其上限和下限弹性模量。
若该陶瓷含有5 %的气孔,再估算其上限和下限弹性模量。
解:令E 1=380GPa,E 2=84GPa,V 1=0.95,V 2=0.05。
则有当该陶瓷含有5%的气孔时,将P=0.05代入经验计算公式E=E 0(1-1.9P+0.9P 2)可得,其上、下限弹性模量分别变为331.3 GPa 和293.1 GPa 。
0816.04.25.2ln ln ln 22001====A A l l T ε真应变)(91710909.4450060MPa A F =⨯==-σ名义应力0851.0100=-=∆=A A l l ε名义应变)(99510524.445006MPa A F T =⨯==-σ真应力)(2.36505.08495.03802211GPa V E V E E H =⨯+⨯=+=上限弹性模量)(1.323)8405.038095.0()(112211GPa E V E V E L =+=+=--下限弹性模量1-11一圆柱形Al 2O 3晶体受轴向拉力F ,若其临界抗剪强度τf 为135 MPa,求沿图中所示之方向的滑移系统产生滑移时需要的最小拉力值,并求滑移面的法向应力。
解:1-6试分别画出应力松弛和应变蠕变与时间的关系示意图,并算出t = 0,t = ∞ 和t = τ时的纵坐标表达式。
解:Maxwell 模型可以较好地模拟应力松弛过程:Voigt 模型可以较好地模拟应变蠕变过程:).1()()(0)0()1)(()1()(10//0----==∞=-∞=-=e EEe e Et t t στεσεεεσεττ;;则有:其蠕变曲线方程为:./)0()(;0)();0()0((0)e (t)-t/e στσσσσσστ==∞==则有::其应力松弛曲线方程为0123450.00.20.40.60.81.0σ(t )/σ(0)t/τ应力松弛曲线0123450.00.20.40.60.81.0ε(t )/ε(∞)t/τ应变蠕变曲线)(112)(1012.160cos /0015.060cos 1017.3)(1017.360cos 53cos 0015.060cos 0015.053cos 82332min 2MPa Pa N F F f =⨯=︒︒⨯⨯=⨯=︒⨯︒⨯=⇒︒⨯︒=πσπτπτ:此拉力下的法向应力为为:系统的剪切强度可表示由题意得图示方向滑移以上两种模型所描述的是最简单的情况,事实上由于材料力学性能的复杂性,我们会用到用多个弹簧和多个黏壶通过串并联组合而成的复杂模型。
2.2材料的强度理论与断裂理论
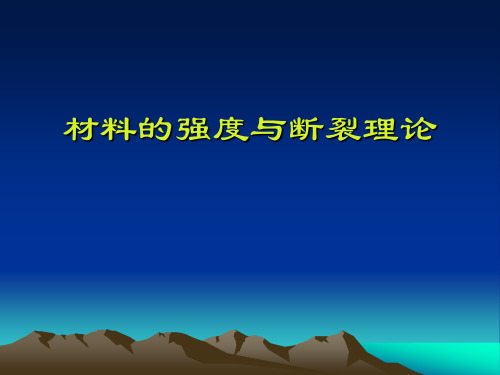
y
H B A D K
ys
o rp a
x
The region ABH represents forces that would be 上述简单分析是以裂纹尖端弹性解为基础的,故 present in an elastic material but cannot be carried 并非严格正确的。屈服发生后,应力必需重分布, in the elastic-plastic material because the stress 以满足平衡条件。 cannot exceed yield. The plastic zone must increase in size in order to carry these forces.
K Ic 如图所示。
1 b 。 2
无损检测发现裂纹长度在4mm以上,设计工作应力为 d
讨论:a 工作应力d=750MNm-2 时,检测手段能否保证防止发生脆断? b 企图通过提高强度以减轻零件重量,若b提高到1900MNm-2 是否合适? c 如果b提高到1900MNm-2 ,则零件的允许工作应力是多少?
计 算 主 应 力
屈 服 准 则
y xy 裂纹尖 y x dy 端屈服 r dx 区域的 (5-1) 2a x 形状与 尺寸
这里仅简单讨论沿裂纹线上屈服区域的大小。 在裂纹线上(=0),注意到 K p a ,有; x y
K1 a ; xy 0 2r 2p r
x= a cos[1 - sin sin3 ] 2 2 2r 2 a cos [1 sin sin3 ] (5-1) y 2 2 2 2r a sin cos cos3 xy r 2 2 2 2
第二章材料的断裂强度

第⼆章材料的断裂强度第⼆章2.1固体的理论结合强度 2.2 材料的断裂强度2.3 裂纹的起源与快速扩展 2.4 材料的断裂韧性2.5显微结构对脆性断裂的影响 2.6⽆机材料强度的统计性质 2.7材料的硬度第⼆章材料的脆性断裂与强度2.1固体的理论结合强度⽆机材料的抗压强度约为抗拉强度的10倍。
所以⼀般集中在抗拉强度上进⾏研究,也就是研究其最薄弱环节。
要推导材料的理论强度,应从原⼦间的结合⼒⼊⼿,只有克服了原⼦间的结合⼒,材料才能断裂。
如果知道原⼦间结合⼒的细节,即知道应⼒-应变曲线的精确形式,就可算出理论结合强度。
这在原则上是可⾏的,就是说固体的强度都能够根据化学组成、晶体结构与强度之间的关系来计算。
但不同的材料有不同的组成、不同的结构及不同的键合⽅式,因此这种理论计算是⼗分复杂的,⽽且对各种材料都不⼀样。
为了能简单、粗略的估计各种情况都适应的理论强度,Orowan 提出了以正弦曲线来近似原⼦间约束⼒随原⼦间距离X 的变化曲线(见图2.1),得出λπσσXth 2sin= 2-1式中,σth 为理论结合强度;λ为正弦曲线的波长。
图2.1 原⼦间约束⼒与距离的关系将材料拉断时,产⽣两个新表⾯,因此单位⾯积的原⼦平⾯分开所做的功应等于产⽣两个单位⾯积的新表⾯所需的表⾯能,材料才能断裂。
设分开单位⾯积原⼦平⾯所做的功为w,则πλπλλπσλπσσλλth th th x dxxw ===-?]2cos [22022sin2-2 设材料形成新表⾯的表⾯能为γ(这⾥是断裂表⾯能,不是⾃由表⾯能),则w=2γ,即γπλο2=th ,λπγσ2=th 2-3接近平衡位置o 的区域,曲线可以⽤直线代替,服从虎克定律: E a xE ==εσ 2-4 a 为原⼦间距。
X 很⼩时 sinλπλπxx22≈2-5将(2.3),(2.4)和(2.5)式代⼊(2.1)式,得aE th γσ=2-6 式中a 为晶格常数,随材料⽽异。
- 1、下载文档前请自行甄别文档内容的完整性,平台不提供额外的编辑、内容补充、找答案等附加服务。
- 2、"仅部分预览"的文档,不可在线预览部分如存在完整性等问题,可反馈申请退款(可完整预览的文档不适用该条件!)。
- 3、如文档侵犯您的权益,请联系客服反馈,我们会尽快为您处理(人工客服工作时间:9:00-18:30)。
第二章材料的脆性断裂与强度§2.1 脆性断裂现象一、弹、粘、塑性形变在第一章中已阐述的一些基本概念。
1.弹性形变正应力作用下产生弹性形变,剪彩应力作用下产生弹性畸变。
随着外力的移去,这两种形变都会完全恢复。
2.塑性形变是由于晶粒内部的位错滑移产生。
晶体部分将选择最易滑移的系统(当然,对陶瓷材料来说,这些系统为数不多),出现晶粒内部的位错滑移,宏观上表现为材料的塑性形变。
3.粘性形变无机材料中的晶界非晶相,以及玻璃、有机高分子材料则会产生另一种变形,称为粘性流动。
塑性形变和粘性形变是不可恢复的永久形变。
4.蠕变:当材料长期受载,尤其在高温环境中受载,塑性形变及粘性形变将随时间而具有不同的速率,这就是材料的蠕变。
蠕变的后当剪应力降低(或温度降低)时,此塑性形变及粘性流动减缓甚至终止。
蠕变的最终结果:①蠕变终止;②蠕变断裂。
二.脆性断裂行为断裂是材料的主要破坏形式。
韧性是材料抵抗断裂的能力。
材料的断裂可以根据其断裂前与断裂过程中材料的宏观塑性变形的程度,把断裂分为脆性断裂与韧性断裂。
1.脆性断裂脆性断裂是材料断裂前基本上不产生明显的宏观塑性变形,没有明显预兆,往往表现为突然发生的快速断裂过程,因而具有很大的危险性。
因此,防止脆断一直是人们研究的重点。
2.韧性断裂韧性断裂是材料断裂前及断裂过程中产生明显宏观塑性变形的断裂过程。
韧性断裂时一般裂纹扩展过程较慢,而且要消耗大量塑性变形能。
一些塑性较好的金属材料及高分子材料在室温下的静拉伸断裂具有典型的韧性断裂特征。
3.脆性断裂的原因在外力作用下,任意一个结构单元上主应力面的拉应力足够大时,尤其在那些高度应力集中的特征点(例如内部和表面的缺陷和裂纹)附近的单元上,所受到的局部拉应力为平均应力的数倍时,此过分集中的拉应力如果超过材料的临界拉应力值时,将会产生裂纹或缺陷的扩展,导致脆性断裂。
虽然与此同时,由于外力引起的平均剪应力尚小于临界值,不足以产生明显的塑性变形或粘性流动。
因此,断裂源往往出现在材料中应力集中度很高的地方,并选择这种地方的某一个缺陷(或裂纹、伤痕)而开裂。
各种材料的断裂都是其内部裂纹扩展的结果。
因而,每种材料抵抗裂纹扩展能力的高低,表示了它们韧性的好坏。
韧性好的材料,裂纹扩展困难,不易断裂。
脆性材料中裂纹扩展所需能量很小,容易断裂;韧性又分断裂韧性和冲击韧性两大类。
断裂韧性是表征材料抵抗其内部裂纹扩展能力的性能指标;冲击韧性则是对材料在高速冲击负荷下韧性的度量。
二者间存在着某种内在联系。
三.突发性断裂与裂纹的缓慢生长裂纹的存在及其扩展行为,决定了材料抵抗断裂的能力。
1.突发性断裂断裂时,材料的实际平均应力尚低于材料的结合强度(或称理论结合强度)。
在临界状态下,断裂源处的裂纹尖端所受的横向拉应力正好等于结合强度时,裂纹产生突发性扩展。
一旦扩展,引起周围应力的再分配,导致裂纹的加速扩展,出现突发性断裂,这种断裂往往并无先兆。
2.裂纹的生长当裂纹尖端处的横向拉应力尚不足以引起扩展,但在长期受应力的情况下,特别是同时处于高温环境中时,还会出现裂纹的缓慢生长,尤其在有环境侵蚀,如存在O 2,H 2,SO :,H 2O(汽)等的情况下,对金属及玻璃更易出现缓慢开裂。
§2.2 理论结合强度一.理论强度的概念无机材料的抗压强度约为抗拉强度的10倍。
所以一般集中在抗拉强度上进行研究,也就是研究其最薄弱的环节。
材料的理论强度,就是从理论角度上材料所能随的最大应力。
我们可以这样考虑: ①当一对原子相距无限远时,不发生相互作用,当它们接近到一定程度时,吸引力开始显著起来,随着距离的缩短而吸引力增大。
当距离r 达到某一值时,原子间的合力(引力和斥力之和)最大,此时表示物质具有最大的强度。
即理论强度。
②从原子结合的情况来看,理论强度就是分离原子(或离子)所需的最小应力。
所以,要推导材料的理论强度,应从原子间的结合力入手,只有克服了原子间的结合力,材料才能断裂。
如果知道原子间结合力的细节,即知道应力一应变曲线的精确形式,就可算出理论结合强度。
这在原则上是可行的,就是说固体的强度都能够根据化学组成、晶体结构与强度之间的关系来计算。
但不同的材料有不同的组成、不同的结构及不同的键合方式,因此这种理论计算是十分复杂的,而且对各种材料都不一样。
二.理论强度的计算1.计算依据为了能简单、粗略地估计各种情况都适用的理论强度,orowan 提出了以正弦曲线来近似原子间约束力随原子间的距离X 的变化曲线(见图2.1)。
2.计算公式推导1)以上曲线的一部分可近似地由下式表示:λπ⨯σ=σX2sin th (2.1)式中,σth 为理论结合强度,λ为正弦曲线的波长。
2)产生新表面所需的表面能众所周知,将材料拉断时,产生两个新表面,因此使单位面积的原子平面分开所作的功应等于产生两个单位面积的新表面所需的表面能,材料才能断裂。
设分开单位面积原子平面所作的功为v ,根据功=力×距离,则πλσ=⎥⎦⎤⎢⎣⎡λπ-πλσ=λπσ=λλ⎰th 20th 20th x 2cos 2dx x 2sinv (2.2) 设材料形成新表面的表面能为γ(这里是断裂表面能,不是自由表面能),使功与两个新表面的表面能2γ相等,即v=2γ,则γ=πλσ2th3)理论强度λπγ=σ2th (2.3)对于接近平衡距离(原子间距)a 的曲线起始部分,即图2.1中的平衡位置O 的区域,曲线可以用直线代替,服从虎克定律E a x E ⋅=ε=σ (2.4)(因为0L L ∆=ε) 式中,a 为原子间距。
x 很小时λπ≈λπx 2x 2sin (2.5)将(2.3),(2.4)和(2.5)式代入(2.1)式,得γ⋅σ=σπγπ⋅σ=λπ⋅σ≈λπ⋅σ=σx 2x 2x 2x 2sin2th th th th tha E x E a x x th γ⋅=γ⋅⋅=γ⋅σ=σ (2.6) 式中,a 为晶格常数,随材料而异。
由此可见,理论结合强度只与弹性模量、表面能和晶格距离等材料常数有关。
(2.6)式虽是粗略的估计,但对所有固体均能应用而不涉及原子间的具体结合力。
通常γ约为 aE /100,这样(2.6)式可写成10E 100E a a E th =⋅⋅=σ (2.7)上式是粗略估算,更精确的计算说明(2.6)式的估计稍偏高。
—般材料性能的典型数值为:E=300GPa ,γ=1J /m 2,a=3×10-10m ,代入(2.6)式算出10EGPa 30th ≈=σ3.讨论从式(2.6)可知,要得到高强度的固体,就要求E 和γ大,a 小。
实际材料中只有一些极细的纤维和晶须其强度接近理论强度值。
例如熔融石英纤维的强度可达24.1GPa ,约为E /4,碳化硅晶须强度6.47GPa ,约为E /23,氧化铝晶须强度为15.2GPa ,约为E /33。
尺寸较大的材料的实际强度比理论值低得多,约为E /100一E /1000,而且实际材料的强度总在一定范围内波动,即使是用同样材料在相同的条件下制成的试件,强度值也有波动。
一般试件尺寸大,强度偏低。
为了解释玻璃、陶瓷等脆性材料的实际断裂强度和理论强度之间的差异,1920年Griffith 提出了微裂纹理论,后来经过不断的发展和补充,逐渐成为脆性断裂的主要理论基础。
§2.3 Griffith 微裂纹理论一.Griffith 微裂纹理论要点Griffith 认为脆性材料发生断裂所需的能量在材料中的分布是不均匀的,实际材料中总是存在许多细小的裂纹或缺陷,在外力作用下,这些裂纹和缺陷附近产生应力集中现象。
当名义应力还很低时,局部应力集中已经达到很高的数值,当应力达到一定程度时,裂纹开始扩展,最后导致脆性断裂。
所以断裂过程中表面的分离是逐渐发生的,裂纹扩展的结果,而不是两部分晶体同时沿整个界面拉断。
从此概念出发,继而需要进行两种探讨:①直接考察裂纹端部附近的应力集中;②考察裂纹的裂纹的扩展过程:当和裂纹的伸长有关的储存于材料中的弹性能降低和新表面的形成有关的表面能增加时,裂纹就扩展。
二.裂纹端部的应力集中1.Inglis 的研究Inglis研究了具有孔洞的板的应力集中问题,得到的一个重要结论是:孔洞两个端部的应力几乎取决于孔洞的长度和端部的曲率半径而与孔洞的形状无关。
在一个大而薄的平板上,设有一穿透孔洞,不管孔洞是椭圆还是菱形,只要孔洞的长度(2c)和端部曲率半径ρ不变,则孔洞端部的应力不会有很大的改变。
2.Griffith 的研究由裂纹引起的应力集中设薄板的裂纹为一个扁平椭圆形,长度为2c ,宽度为a ,裂纹端部的曲率半径为ρ(如上图),则可根据弹性理论求得孔洞端部的应力σA 为: a c 21A +=σσ (σσA 称为应力集中系数)∵c a 2=ρ ∴⎥⎦⎤⎢⎣⎡ρ+σ=σc 21A (2.8)式中,σ为外加应力,即垂直作用于此裂纹的平均应力,相当于无应力集中区作用的名义应力。
从上式可见,c/ρ比值增大,σA 亦增大,如果c 》ρ,即为扁平的锐裂纹,则c /ρ将很大,这时可略去式中括号内的1,得ρσ=σc 2A (2.9)3.Orowan 的研究Orowan 注意到ρ是很小的,可近似认为与原子间距a 的数量级相同。
如图2.2所示,这样可将(2.9)式写成a c2A σ=σ (2.10)当σA 等于(2.6)式中的理论结合强度σth 时,裂纹就被拉开而迅速扩展。
裂纹扩展,使c 增大,σA 又进一步增加。
如此恶性循环,材料很快断裂。
4.裂纹扩展的临界条件从以上推导可知,裂纹扩展的临界条件是:裂纹端部的应力等于理论强度,即a E a c 2γ=σ(2.11)设临界应力为σc ,故 c 4E c γ=σ (1.12)Inglis 只考虑了裂纹端部一点的应力,实际上裂纹端部的应力状态是很复杂的。
三.裂纹扩展过程中的能量平衡Grfffith 从能量的角度来研究裂纹扩展的条件。
1.裂纹扩展的能量条件 物体内储存的弹性应变能的降低大于等于由于开裂形成两个新表面所需的表面能。
反之,前者小于后者,则裂纹不会扩展。
2.临界应力的推导1)材料内储存的弹性应变能(1)根据平板模型计算在求理论强度时曾将此概念用于理想的完整晶体。
Griffith 将此概念用于有裂纹的物体,认为物体内储存的弹性应变能的降低(或释放)就是裂纹扩展的动力。
我们用图2.3来说明这一概念并导出这一临界条件。
将一单位厚度的薄板拉长到l+Δl ,然后将两端固定。
此时板中储存的弹性应变能为W e1=1/2(F·Δl )然后人为地在板上割出一条长度为2c 的裂纹,产生两个新表面,原来储存的弹性应变能就要降低,有裂纹后板内储存的应变能为W e2=1/2(F -ΔF) ·Δl∴应变能降低为 W e =W e1-W e2=1/2ΔF ·Δl欲使裂纹进一步扩展,应变能将进一步降低。