设计一卧式单面多轴钻孔组合机床动力滑台的液压系统
液压传动课程设计-卧式单面多轴钻孔组合机床动力滑台的液压系统
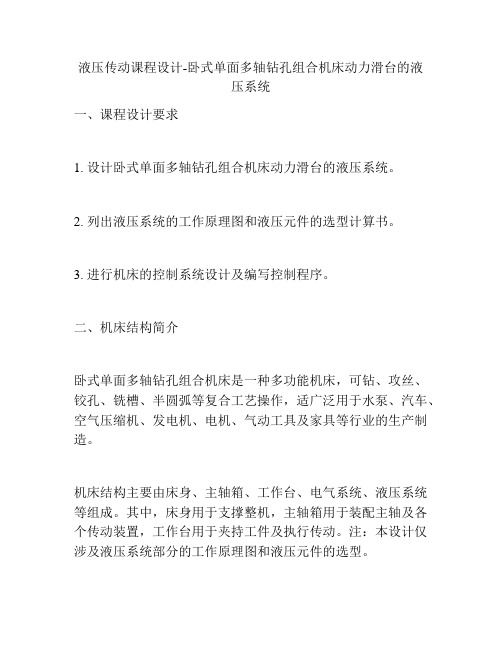
液压传动课程设计-卧式单面多轴钻孔组合机床动力滑台的液压系统一、课程设计要求1. 设计卧式单面多轴钻孔组合机床动力滑台的液压系统。
2. 列出液压系统的工作原理图和液压元件的选型计算书。
3. 进行机床的控制系统设计及编写控制程序。
二、机床结构简介卧式单面多轴钻孔组合机床是一种多功能机床,可钻、攻丝、铰孔、铣槽、半圆弧等复合工艺操作,适广泛用于水泵、汽车、空气压缩机、发电机、电机、气动工具及家具等行业的生产制造。
机床结构主要由床身、主轴箱、工作台、电气系统、液压系统等组成。
其中,床身用于支撑整机,主轴箱用于装配主轴及各个传动装置,工作台用于夹持工件及执行传动。
注:本设计仅涉及液压系统部分的工作原理图和液压元件的选型。
三、液压系统工作原理图液压系统主要用于机床的升降、夹紧、进给等控制操作。
下面的工作原理图展示了该机床的主要液压系统结构。
液压油泵为双联泵,分别提供高压和低压液压油,高压系统主要用于机床的动力传输和工作台的升降,低压系统则用于工作台和主轴箱的夹持、进给和径向递进。
四、液压元件的选型计算本文中设计的液压系统主要包括液压油泵、液压缸、液压阀、液压滤清器、液压压力表等液压元件。
针对所需控制的液压作用,根据相应的公式和数据手册,进行液压元件的选型计算。
液压元件选型计算书如下:五、控制系统设计本设计中,机床的控制系统主要由PLC控制器、触摸屏、传感器、执行器和电磁阀等组成,通过编写相应的控制程序,实现机床的高效稳定运行。
液压系统的控制程序中主要包括如下控制命令:1. 单向液压缸的伸出和缩回控制命令。
2. 双向液压缸的伸出和缩回控制命令。
3. 液压油泵的控制启停命令。
4. 电磁阀的开关控制命令。
5. 液压滤清器的定期清洗命令。
通过不同的控制命令组合,可以实现机床的不同运动状态和操作需求,从而提高机床的生产效率和工作质量。
六、总结本文对卧式单面多轴钻孔组合机床动力滑台的液压系统进行了详细介绍,并给出了液压系统的工作原理图和液压元件的选型计算书,同时简要讲述了机床的控制系统设计流程和控制命令。
设计一台卧式单面多轴钻孔组合机床动力滑台的液压系统

2
第一张 明确液压系统的设计要求
设计一台卧式单面多轴钻孔组合机床动力滑台的液压系统。要实现的动作顺 序为�启动→加速→快进→减速→工进→快退→停止。液压系统的主要参数与性 能要求如下�轴向切削力总和 Fg=30000N�移动部件总重量 G�10000N�快进 行程长度 150mm 工进行程 30mm�快进、快退的速度为 4.2m/min�工进速度 �20~1000�mm/min�其中 20mm/min 为粗加工� 1000mm/min 为精加工�该动 力滑台采用水平放置的平导轨�静摩擦系数 fs�0.2�动摩擦系数 fd�0.1。液压 系统的执行元件使用液压缸。
� � A2 � � D 2 � d 2 4 � 32.43 �10 �4 m 2
工作台在快进过程中�液压缸采用差动连接�此时系统所需要的流量为
q快进 � � A1 � A2 �� v1 � 23 .07 L min
工作台在快退过程中所需要的流量为
q 快退 � A2 � v3 � 22 .7 L min
1
引言
液压传动是用液体作为来传递能量的�液压传动有以下优点�易于获得较大 的力或力矩�功率重量比大�易于实现往复运动�易于实现较大范围的无级变速� 传递运动平稳�可实现快速而且无冲击�与机械传动相比易于布局和操纵�易于 防止过载事故�自动润滑、元件寿命较长�易于实现标准化、系列化。
液压传动的基本目的就是用液压介质来传递能量�而液压介质的能量是由其 所具有的压力及力流量来表现的。而所有的基本回路的作用就是控制液压介质的 压力和流量�因此液压基本回路的作用就是三个方面�控制压力、控制流量的大 小、控制流动的方向。所以基本回路可以按照这三方面的作用而分成三大类�压 力控制回路、流量控制回路、方向控制回路。
课程设计_卧式单面多轴钻孔组合机床动力滑台的液压系统之欧阳德创编

目录引言1第一章明确液压系统的设计要求2第二章负载与运动分析3第三章负载图和速度图的绘制5第四章确定液压系统主要参数54.1确定液压缸工作压力54.2计算液压缸主要结构参数64.3绘制液压缸工况图8第五章液压系统方案设计85.1选用执行元件85.2速度控制回路的选择95.3选择快速运动和换向回路105.4速度换接回路的选择105.5组成液压系统原理图115.5系统图的原理12第六章液压元件的选择136.1确定液压泵的规格和电动机功率146.2确定其它元件及辅件156.3主要零件强度校核17第七章液压系统性能验算187.1验算系统压力损失并确定压力阀的调整值187.2油液温升验算20设计小结21参考文献22引言液压系统已经在各个部门得到越来越广泛的应用,而且越先进的设备,其应用液压系统的部门就越多。
液压传动是用液体作为来传递能量的,液压传动有以下优点:易于获得较大的力或力矩,功率重量比大,易于实现往复运动,易于实现较大范围的无级变速,传递运动平稳,可实现快速而且无冲击,与机械传动相比易于布局和操纵,易于防止过载事故,自动润滑、元件寿命较长,易于实现标准化、系列化。
液压传动的基本目的就是用液压介质来传递能量,而液压介质的能量是由其所具有的压力及力流量来表现的。
而所有的基本回路的作用就是控制液压介质的压力和流量,因此液压基本回路的作用就是三个方面:控制压力、控制流量的大小、控制流动的方向。
所以基本回路可以按照这三方面的作用而分成三大类:压力控制回路、流量控制回路、方向控制回路。
第一章明确液压系统的设计要求要求设计一台卧式单面多轴钻孔组合机床动力滑台的液压系统。
要求实现的动作顺序为:启动→加速→快进→减速→工进→快退→停止。
液压系统的主要参数与性能要求如下:轴向切削力总和F g=12700N,移动部件总重量G=20000N;行程长度400mm(其中工进行程100mm)快进、快退的速度为7m/min,工进速度(20~1000)mm/min,其中20mm/min为粗加工,1000mm/min为精加工;启动换向时间△t≤0.15s;该动力滑台采用水平放置的平导轨;静摩擦系数f s=0.2;动摩擦系数f d=0.1。
卧式单面多轴钻孔组合机床动力滑台液压系统方案

卧式单面多轴钻孔组合机床动力滑台液压系统设计要求设计的动力滑台实现的工作循环是:快进工进快退停止。
主要性能参数与性能要求如下:切削阻力FL=30468N;运动部件所受重力G=9800N:快进、快退速度5= p3=O.lm/s,工进速度p2=0.88X 10-3m/s;快进行程Ll = 100mm,工进行程L2=50mm:往复运动的加速时间△ t=0.2s;动力滑台釆用平导轨,静摩擦系数2=0.2,动摩擦系数P d=0.1o液压系统执行元件选为液压缸。
液压传动课程设计一般包括以下容:(1)明确设计要求进行工况分析;(2)确定液压系统主要参数;(3)拟定液圧系统原理图;(4)计算和选择液压件;(5)验算液圧系统性能;(6)编制技术文件。
1•负载分析1)切削阻力F L=30468N2)计算摩擦阻力静摩擦阻力:F s=UsG=0.2X9800=1960N动摩擦阻力:F d=u d G=0」X9800=980N3)计算惯性阻力F"』也9800x0.匕拠g t 9.8 x 0.24)计算各工况负载反向启动 Fs=u s G 1960 2180 加速 F (i=U (jG+ Fm 1480 1640 快退 Fd=UdG 980 1090 制动F d =u d G- F m480530这里取液压缸效率为0・92.绘制液压缸的F-t 图与v-t 图1) 工进速度 V2=0.88mm/s 2) 快进,快退时间 快进:ti=Ll/vl=ls 工进:t 2=L2/v2=56.8s 快退:t3=(Ll+L2)/v3=1.5s3) 绘制液压缸的F-t 图与v-t 图 如图3 •确定液压系统参数1)初选液压工工作压力由工况分析可知,工进阶段的负载力最大,所以,液压缸的工作压力按此负载力计算,根据 液压缸与负载关系以及列表,选pi=40x 105Pa.本机床为钻孔组合机床,为防止钻通时发生 前冲现象,液压缸回油腔应有背压,设背压P 2=6X 10?Pa,为使快进快退速度相等,选用 A 1=2A 2,差动油缸,假宦快进,快退的回油压力损失为Ap=7xlO 5Pa u 2)计算液压缸尺寸由工进工况出发,计算汕缸大腔面积,由(PI A I ・P ?A2)n m =F 得液丿k.缸直径D= * -—- = '4x94 5 圆整后取标准直径=0.707 x 110=77.8mm,圆整后取标准直径d=80mm则液压缸有效面积为A 町D2=95昭A 2=£( DTM4.7c 時3)计算液压缸在工作循环中各阶段的压力,流量和功率使用值 液压缸工作循环各阶段压力,流量和功率计算结果如下表工况计算公式F/N^p! MpaP 】/mpaq/(m 3/s) p/kW启动nF + S21800.43快 进 加速q=( Ai-Az)vi16400.70.95F _ 31448〃(刃-牛)0.9(40-》=94.5cm 2因为A i=2Az >所以d=4)绘制液压缸工况图如图4.拟定液压系统图1)选择液压回路(1)调速方式。
课程设计-卧式单面多轴钻孔组合机床动力滑台的液压系统

资料范本本资料为word版本,可以直接编辑和打印,感谢您的下载课程设计-卧式单面多轴钻孔组合机床动力滑台的液压系统地点:__________________时间:__________________说明:本资料适用于约定双方经过谈判,协商而共同承认,共同遵守的责任与义务,仅供参考,文档可直接下载或修改,不需要的部分可直接删除,使用时请详细阅读内容目录TOC \o "1-3" \h \u HYPERLINK \l "_Toc295240605" 引言 1 HYPERLINK \l "_Toc295240606" 第一章明确液压系统的设计要求2HYPERLINK \l "_Toc295240607" 第二章负载与运动分析 3HYPERLINK \l "_Toc295240608" 第三章负载图和速度图的绘制 5 HYPERLINK \l "_Toc295240609" 第四章确定液压系统主要参数 6 HYPERLINK \l "_Toc295240610" 4.1确定液压缸工作压力 6HYPERLINK \l "_Toc295240611" 4.2计算液压缸主要结构参数 6 HYPERLINK \l "_Toc295240612" 4.3绘制液压缸工况图8HYPERLINK \l "_Toc295240613" 第五章液压系统方案设计9 HYPERLINK \l "_Toc295240614" 5.1选用执行元件9HYPERLINK \l "_Toc295240615" 5.2速度控制回路的选择9HYPERLINK \l "_Toc295240616" 5.3选择快速运动和换向回路 1 0 HYPERLINK \l "_Toc295240617" 5.4速度换接回路的选择 1 0HYPERLINK \l "_Toc295240618" 5.5组成液压系统原理图 1 1HYPERLINK \l "_Toc295240619" 5.5系统图的原理 1 2HYPERLINK \l "_Toc295240620" 第六章液压元件的选择 1 5HYPERLINK \l "_Toc295240621" 6.1确定液压泵的规格和电动机功率1 5HYPERLINK \l "_Toc295240622" 6.2确定其它元件及辅件 1 6HYPERLINK \l "_Toc295240623" 6.3主要零件强度校核 1 8HYPERLINK \l "_Toc295240624" 第七章液压系统性能验算 2 0 HYPERLINK \l "_Toc295240625" 7.1验算系统压力损失并确定压力阀的调整值 2 0HYPERLINK \l "_Toc295240626" 7.2油液温升验算 2 1HYPERLINK \l "_Toc295240627" 设计小结 2 3HYPERLINK \l "_Toc295240628" 参考文献 2 4引言液压系统已经在各个部门得到越来越广泛的应用,而且越先进的设备,其应用液压系统的部门就越多。
卧式单面多轴钻孔机床液压系统设计解读
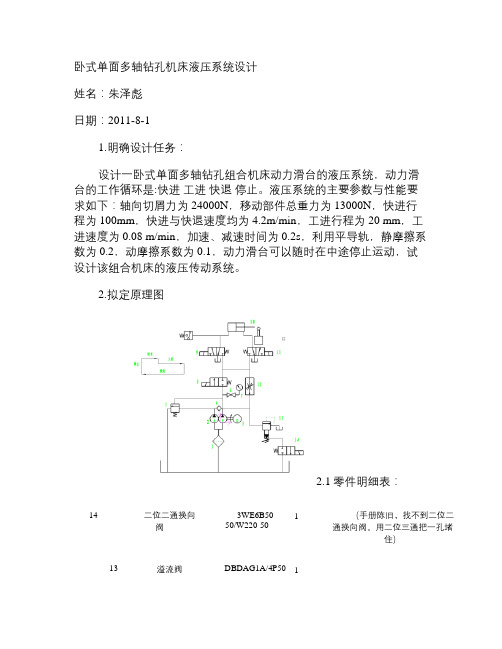
卧式单面多轴钻孔机床液压系统设计姓名:朱泽彪日期:2011-8-11.明确设计任务:设计一卧式单面多轴钻孔组合机床动力滑台的液压系统,动力滑台的工作循环是:快进工进快退停止。
液压系统的主要参数与性能要求如下:轴向切屑力为24000N,移动部件总重力为13000N,快进行程为100mm,快进与快退速度均为4.2m/min,工进行程为20 mm,工进速度为0.08 m/min,加速、减速时间为0.2s,利用平导轨,静摩擦系数为0.2,动摩擦系数为0.1,动力滑台可以随时在中途停止运动,试设计该组合机床的液压传动系统。
2.拟定原理图2.1零件明细表:14 二位二通换向阀3WE6B50-50/W220-501(手册陈旧,找不到二位二通换向阀。
用二位三通把一孔堵住)13 溢流阀DBDAG1A/4P50-50112 单向节流阀MK6G1.2 111 二位三通换向阀3WE6B50-50/W220-50110 液压缸19 二位三通换向阀3WE6B50-50/W220-5018 二位二通换向阀3WE6B50-50/W220-501(手册陈旧,找不到二位二通换向阀。
用二位三通把一孔堵住)7 压力表Y-60 0-10Mpa 16 压力表开关15 顺序阀DZ6DP350/75 14 单向阀S6A30 13 电机Y132M-6 12 双联泵YB-40/6.3 11 滤油器WU-63X180 1序号名称型号数量备注2.2工步叙述:A泵低压大流量,B泵高压小流量快进:A泵出油经单向阀与B泵出油汇合,往阀8左位、阀9左位进入液压缸左腔,回流由液压缸右腔经阀11右位与液压缸左腔连接形成差动连接。
工进:快进结束时,压下行程开关,阀11带电。
A泵出油升压,阀5打开,泵A卸荷,泵B单独向系统供油,压力油经阀8左位、阀9左位进入液压缸左腔,回油由液压缸右腔经阀11右位经节流阀经阀12流回油箱。
快退:工进结束时,压力继电器得到信号,开始快退。
课程设计卧式单面多轴钻孔组合机床动力滑台的液压系统
目录引言 (1)第一章明确液压系统的设计要求 (2)第二章负载与运动分析 (3)第三章负载图和速度图的绘制 (5)第四章确定液压系统主要参数 (6)确定液压缸工作压力 (6)计算液压缸主要结构参数 (6)绘制液压缸工况图 (8)第五章液压系统方案设计 (9)选用执行元件 (9)速度控制回路的选择 (9)选择快速运动和换向回路 (10)速度换接回路的选择 (10)组成液压系统原理图 (11)系统图的原理 (12)第六章液压元件的选择 (15)确定液压泵的规格和电动机功率 (15)确定其它元件及辅件 (16)主要零件强度校核 (18)第七章液压系统性能验算 (20)验算系统压力损失并确定压力阀的调整值 (20)油液温升验算 (21)设计小结 (23)参考文献 (24)引言液压系统已经在各个部门得到越来越广泛的应用,而且越先进的设备,其应用液压系统的部门就越多;液压传动是用液体作为来传递能量的,液压传动有以下优点:易于获得较大的力或力矩,功率重量比大,易于实现往复运动,易于实现较大范围的无级变速,传递运动平稳,可实现快速而且无冲击,与机械传动相比易于布局和操纵,易于防止过载事故,自动润滑、元件寿命较长,易于实现标准化、系列化;液压传动的基本目的就是用液压介质来传递能量,而液压介质的能量是由其所具有的压力及力流量来表现的;而所有的基本回路的作用就是控制液压介质的压力和流量,因此液压基本回路的作用就是三个方面:控制压力、控制流量的大小、控制流动的方向;所以基本回路可以按照这三方面的作用而分成三大类:压力控制回路、流量控制回路、方向控制回路;第一章明确液压系统的设计要求设计一卧式单面多轴钻孔组合机床动力滑台的液压系统含图;动力滑台的工作循环是:快进→工进→快退→停止;液压系统的主要参数与性能要求如下:切削力Ft=20000N,移动部件总重力G=10000N,快进行程l1=100mm,工进行程l2=50mm,快进快退的速度为4m/min,工进速度为min;加速、减速时间Δt=,静摩擦系数fs=,动摩擦系数fd=;该动力滑台采用水平放置的平导轨,动力滑台可在任意位置停止;第二章 负载与运动分析负载分析中,暂不考虑回油腔的背压力,液压缸的密封装置产生的摩擦阻力在机械效率中加以考虑;因工作部件是卧式放置,重力的水平分力为零,这样需要考虑的力有:夹紧力,导轨摩擦力,惯性力;在对液压系统进行工况分析时,本设计实例只考虑组合机床动力滑台所受到的工作负载、惯性负载和机械摩擦阻力负载,其他负载可忽略; 1工作负载F W工作负载是在工作过程中由于机器特定的工作情况而产生的负载,对于金属切削机床液压系统来说,沿液压缸轴线方向的切削力即为工作负载,即N F t 12700=2阻力负载f F阻力负载主要是工作台的机械摩擦阻力,分为静摩擦阻力和动摩擦阻力两部分;导轨的正压力等于动力部件的重力,设导轨的静摩擦力为f F ,则静摩擦阻力 N F fs 4000200002.0=⨯= 动摩擦阻力 N F fd 2000200001.0=⨯=3惯性负载最大惯性负载取决于移动部件的质量和最大加速度,其中最大加速度可通过工作台最大移动速度和加速时间进行计算;已知启动换向时间为,工作台最大移动速度,即快进、快退速度为min,因此惯性负载可表示为N N t v F 68.158515.060781.920000m m =⨯⨯=∆∆⨯=如果忽略切削力引起的颠覆力矩对导轨摩擦力的影响,并设液压缸的机械效率w η=,根据上述负载力计算结果,可得出液压缸在各个工况下所受到的负载力和液压缸所需推力情况,如表1所示;表1 液压缸总运动阶段负载表单位:Nm/m in 731==v v m m /m in 502=v sv L t 57.2607103003111=⨯==-s v L t 1206005.0101003222=⨯==-s s v l v l t 61000740060100073006033111=⎥⎦⎤⎢⎣⎡⨯⨯+⨯⨯=+=1A 2A p ∆p ∆≈2p 11221112/(/2)m F A p A p A p A p η=-=-26211m 006282.028.031033.163332=-⨯=-=p p F A mηmmA D 46.8941==π242110585.634m D A -⨯==π()242221043.324m d D A -⨯=-=π()m in 07.23v 121L A A q =⨯-=快进m in 7.22v q 32L A =⨯=快退()()212'1A A pA F p -∆+=()121v A A q -=q p P 1=p p p ∆+=12()1221'A A p F p +=21v A q =q p P 1=()2121'A A p F P +=32v A q =q p P +=1fs F F =m fd F F F += fdF F =m fd F F F -=m/'ηF F =1t 2t ()()()()()()[]ss v l v l t 61000740060100073006033111=⨯⨯+⨯⨯=+=()()s s v l t 120100005.010060222=⨯⨯==12t t向回路b.速度换接回路图4 换向和速度切换回路的选择参考同类组合机床,选用双作用叶片泵双泵供油,调速阀进油节流阀调速的开式回路,溢流阀做定压阀;为了换速以及液压缸快退时运动的平稳性,回油路上设置背压阀,初定背压值P b =;组成液压系统原理图选定调速方案和液压基本回路后,再增添一些必要的元件和配置一些辅助性油路,如控制油路、润滑油路、测压油路等,并对回路进行归并和整理,就可将液压回路合成为液压系统,即组成如图5所示的液压系统图;为便于观察调整压力,在液压泵的进口处,背压阀和液压腔进口处设置测压点,并设置多点压力表开关,这样只需一个压力表即能观察各压力;要实现系统的动作,即要求实现的动作顺序为:启动→加速→快进→减速→工进→快退→停止;则可得出液压系统中各电磁铁的动作顺序如表5所示;表中“+”号表示电磁铁通电或行程阀压下;“—”号表示电磁铁断电或行程阀复位;表5 电磁铁的动作顺序表图 5 液压系统图系统图的原理1.快进快进如图所示,按下启动按钮,电磁铁1YA通电,由泵输出地压力油经2三位五通换向阀的左侧,这时的主油路为:进油路:泵→向阀10→三位五通换向阀21YA得电→行程阀3→液压缸左腔;回油路:液压缸右腔→三位五通换向阀21YA得电→单向阀6→行程阀3→液压缸左腔;由此形成液压缸两腔连通,实现差动快进,由于快进负载压力小,系统压力低,变量泵输出最大流量;2.减速当滑台快到预定位置时,此时要减速;挡块压下行程阀3,切断了该通路,电磁阀继续通电,这时,压力油只能经过调速阀4,电磁换向阀16进入液压缸的左腔;由于减速时系统压力升高,变量泵的输出油量便自动减小,且与调速阀4开口向适应,此时液控顺序7打开,单向阀6关闭,切断了液压缸的差动连接油路,液压缸右腔的回油经背压阀8流回油箱,这样经过调速阀就实现了液压油的速度下降,从而实现减速,其主油路为:进油路:泵→向阀10→三位五通换向阀21YA得电→调速阀4→电磁换向阀16→液压缸左腔;回油路:液压缸右腔→三位五通换向阀2→背压阀8→液控顺序阀7→油箱;3.工进减速终了时,挡块还是压下,行程开关使3YA通电,二位二通换向阀将通路切断,这时油必须经调速阀4和15才能进入液压缸左腔,回油路和减速回油完全相同,此时变量泵输出地流量自动与工进调速阀15的开口相适应,故进给量大小由调速阀15调节,其主油路为:进油路:泵→向阀10→三位五通换向阀21YA得电→调速阀4→调速阀15→液压缸左腔;回油路:液压缸右腔→三位五通换向阀2→背压阀8→液控顺序阀7→油箱;4.死挡铁停留当滑台完成工进进给碰到死铁时,滑台即停留在死挡铁处,此时液压缸左腔的压力升高,使压力继电器14发出信号给时间继电器,滑台停留时间由时间继电器调定;5.快退滑台停留时间结束后,时间继电器发出信号,使电磁铁1YA、3YA断电,2YA通电,这时三位五通换向阀2接通右位,,因滑台返回时的负载小,系统压力下降,变量泵输出流量又自动恢复到最大,滑快速退回,其主油路为:进油路:泵→向阀10→三位五通换向阀22YA得电→液压缸右腔;回油路:液压缸左腔→单向阀5→三位五通换向阀2右位→油箱;6.原位停止当滑台退回到原位时,挡块压下原位行程开关,发出信号,使2YA断电,换向阀处于中位,液压两腔油路封闭,滑台停止运动;这时液压泵输出的油液经换向2直接回油箱,泵在低压下卸荷;系统图的动作顺序表如表5所示;第六章 液压元件的选择确定液压泵的规格和电动机功率本设计所使用液压元件均为标准液压元件,因此只需确定各液压元件的主要参数和规格,然后根据现有的液压元件产品进行选择即可; 1计算液压泵的最大工作压力由于本设计采用双泵供油方式,根据液压系统的工况图,大流量液压泵只需在快进和快退阶段向液压缸供油,因此大流量泵工作压力较低;小流量液压泵在快速运动和工进时都向液压缸供油,而液压缸在工进时工作压力最大,因此对大流量液压泵和小流量液压泵的工作压力分别进行计算;根据液压泵的最大工作压力计算方法,液压泵的最大工作压力可表示为液压缸最大工作压力与液压泵到液压缸之间压力损失之和;对于调速阀进口节流调速回路,选取进油路上的总压力损失p 0.8MPa ∑∆=,同时考虑到压力继电器的可靠动作要求压力继电器动作压力与最大工作压力的压差为,则小流量泵的最高工作压力可估算为()MPaMPa P p 27.45.08.097.21=++=大流量泵只在快进和快退时向液压缸供油,图4表明,快退时液压缸中的工作压力比快进时大,如取进油路上的压力损失为,则大流量泵的最高工作压力为:()MPa MPa P p 36.25.086.12=+= 2计算总流量表3表明,在整个工作循环过程中,液压油源应向液压缸提供的最大流量出现在快进工作阶段,为 L/min,若整个回路中总的泄漏量按液压缸输入流量的10%计算,则液压油源所需提供的总流量为:min 97.30min 07.231.1L L q p =⨯= 工作进给时,液压缸所需流量约为 L/min,但由于要考虑溢流阀的最小稳定溢流量3 L/min,故小流量泵的供油量最少应为min;据据以上液压油源最大工作压力和总流量的计算数值,因此选取PV2R12-6/26型双联叶片泵,其中小泵的排量为6mL/r,大泵的排量为26mL/r,若取液压泵的容积效率v η=,则当泵的转速n p =940r/min 时,液压泵的实际输出流量为()[]min 072.27221.5min 10009.0960266L L q p =+=⨯⨯+=)(由于液压缸在快退时输入功率最大,这时液压泵工作压力为、流量为min;取泵的总效率0.75pη=,则液压泵驱动电动机所需的功率为:kW kW q p P ppp 42.175.0601.2736.2=⨯⨯==η根据上述功率计算数据,此系统选取Y100L-6型电动机,其额定功率kW P n 5.1=,额定转速min 960r n n =;确定其它元件及辅件1 确定阀类元件及辅件根据系统的最高工作压力和通过各阀类元件及辅件的实际流量,查阅产品样本,选出的阀类元件和辅件规格如表6所列;表6 液压元件规格及型号注:此为电动机额定转速为940r/min 时的流量;2 确定油管在选定了液压泵后,液压缸在实际快进、工进和快退运动阶段的运动速度、时间以及进入和流出液压缸的流量,与原定数值不同,重新计算的结果如表7所列;表7各工况实际运动速度、时间和流量由表可以看出,液压缸在各阶段的实际运动速度符合设计要求;根据表中数值,当油液在压力管中流速取3m/s 时,可算得与液压缸无杆腔和有杆腔相连的油管内径分别为:()()()mm mm v q d 78.19601031059.632236=⨯⨯⨯⨯⨯==ππ取标准值20mm ;()()()mm mm v q d 85.1360103101.272236=⨯⨯⨯⨯⨯==ππ取标准值15mm;因此与液压缸相连的两根油管可以按照标准选用公称通径为20φ和15φ的无缝钢管或高压软管;如果液压缸采用缸筒固定式,则两根连接管采用无缝钢管连接在液压缸缸筒上即可;如果液压缸采用活塞杆固定式,则与液压缸相连的两根油管可以采用无缝钢管连接在液压缸活塞杆上或采用高压软管连接在缸筒上;3油箱的设计油箱的主要用途是贮存油液,同时也起到散热的作用,参考相关文献及设计资料,油箱的设计可先根据液压泵的额定流量按照经验计算方法计算油箱的体积,然后再根据散热要求对油箱的容积进行校核;油箱中能够容纳的油液容积按JB/T7938—1999标准估算,取7=ζ时,求得其容积为L L q V p 7.1891.277=⨯==ζ按JB/T7938—1999规定,取标准值V =250L;主要零件强度校核① 缸筒壁厚δ=4㎜因为方案是低压系统,校核公式[]δδ2e DP ≥, D 1.0<δ 式中:δ-缸筒壁厚me P -实验压力 1e )5.1~25.1(P P =,其中1p 是液压缸的额定工作压力 D-缸筒内径 D=[]δ-缸筒材料的许用应力;n b /][σσ=,b σ为材料抗拉强度MPa,n 为安全系数,取n=5;对于P 1<16MPa.材料选45号调质钢,对于低压系统mm D P e 3.310100211.01045.1][266=⨯⨯⨯⨯⨯=≥σδ 因此满足要求;② 缸底厚度δ=11㎜对于平缸底,厚度 1δ 有两种情况: a. 缸底有孔时:mm P D d e 069.23100226.045.14.103433.0][433.021=⨯⨯⨯⨯=≥σϕδ 其中mm D d D d 226.04.103804.103202=-=-=ϕ b. 缸底无孔时,用于液压缸快进和快退;mm P D e 97.10101001045.14.103433.0][433.06621=⨯⨯⨯⨯⨯=≥σδ 其中mm D D 4.1033.3211022=⨯-=-=δ③ 杆径d 由公式:[]σπF4d ≥式中:F 是杆承受的负载N,F=12700N[]δ 是杆材料的许用应力,[]δ=100a MPmm F d 01272.01010014.3127004][46=⨯⨯⨯=≥σπ ④ 缸盖和缸筒联接螺栓的底径d1mm z KF d 00725.010100614.3127005.12.5][2.561=⨯⨯⨯⨯⨯=≥σπ式中 K------拧紧系数,一般取K=~; F-------缸筒承受的最大负载N ; z-------螺栓个数;[]σ----螺栓材料的许用应力,[]n s /σσ= ,s σ为螺栓材料的屈服点MPa,安全系数n=~第七章 液压系统性能验算验算系统压力损失并确定压力阀的调整值由于系统的管路布置尚未具体确定,整个系统的压力损失无法全面估算,故只能先按课本式3-46估算阀类元件的压力损失,待设计好管路布局图后,加上管路的沿程损失和局部损失即可;但对于中小型液压系统,管路的压力损失甚微,可以不予考虑;压力损失的验算应按一个工作循环中不同阶段分别进行;① 快进滑台快进时,液压缸差动连接,由表3和表4可知,进油路上油液通过单向阀10的流量是22L/min,通过电液换向阀2的流量是min,然后与液压缸有杆腔的回油汇合,以流量min 通过行程阀3并进入无杆腔;因此进油路上的总压降为()MPaMPap v 2796.0231.0057.0024.0633.553.0801.275.063222.0222=++=⎥⎥⎦⎤⎢⎢⎣⎡⎪⎭⎫ ⎝⎛⨯+⎪⎭⎫ ⎝⎛⨯+⎪⎭⎫ ⎝⎛⨯=∆∑ 此值不大,不会使压力阀开启,故能确保两个泵的流量全部进入液压缸;回油路上,液压缸有杆腔中的油液通过电液换向阀2和单向阀6的流量都是min,然后与液压泵的供油合并,经行程阀3流入无杆腔;由此可算出快进时有杆腔压力p 2与无杆腔压力p 1之差;()MPa MPap p p 3331.0231.004.00621.0633.553.0632.282.0802.285.022212=++=⎥⎥⎦⎤⎢⎢⎣⎡⎪⎭⎫ ⎝⎛⨯+⎪⎭⎫ ⎝⎛⨯+⎪⎭⎫ ⎝⎛⨯=-=∆ 此值小于原估计值见表2,所以是偏安全的;② 工进工进时,油液在进油路上通过电液换向阀2的流量为min,在调速阀4处的压力损失为;油液在回油路上通过换向阀2的流量是min,在背压阀8处的压力损失为,通过顺序阀7的流量为0162+22L/min=min,因此这时液压缸回油腔的压力为p 2为MPa MPa p 53712.063162.223.05.080162.05.0222=⎥⎥⎦⎤⎢⎢⎣⎡⎪⎭⎫ ⎝⎛⨯++⎪⎭⎫ ⎝⎛⨯=可见此值小于原估计值;故可按表2中公式重新计算工进时液压缸进油腔压力p 1,即MPa MPa A A p F p 84.2101059.631043.3210537.033.16333'64461221=⨯⨯⨯⨯⨯+=+=--此值与表3中数值相近;考虑到压力继电器可靠动作需要压差Δp e =,故溢流阀9的调压p p1A 应为MPa MPa p p p P e p 84.35.05.0805.05.084.22111=⎥⎥⎦⎤⎢⎢⎣⎡++⎪⎭⎫⎝⎛⨯+=∆+∆∑+>③ 快退快退时,油液在进油路上通过单向阀10的流量为22L/min,通过换向阀2的流量为min ;油液在回油路上通过单向阀5、换向阀2和单向阀13的流量都是min;因此进油路上总压降为MPa MPa p v 082.0801.275.063222.0222=⎥⎥⎦⎤⎢⎢⎣⎡⎪⎭⎫ ⎝⎛⨯+⎪⎭⎫ ⎝⎛⨯=∆∑此值较小,所以液压泵驱动电动机的功率是足够的;回油路上总压降为MPa MPa p 616.06313.532.08013.535.06313.532.02222=⎥⎥⎦⎤⎢⎢⎣⎡⎪⎭⎫ ⎝⎛⨯+⎪⎭⎫ ⎝⎛⨯+⎪⎭⎫ ⎝⎛⨯=∆∑此值与表3的估计值相近,故不必重算;所以,快退时液压泵的最大工作压力p p 应为()MPa MPa p p p v p 492.2082.041.211=+=∆∑+= 因此大流量液压泵卸荷的顺序阀7的调压应大于;油液温升验算液压传动系统在工作时,有压力损失、容积损失和机械损失,这些损失所消耗的能量多数转化为热能,使油温升高,导致油的粘度下降、油液变质、机器零件变形等,影响正常工作;为此,必须控制温升ΔT 在允许的范围内,如一般机床∆= 25 ~ 30 ℃;数控机床∆≤ 25 ℃;粗加工机械、工程机械和机车车辆∆= 35 ~ 40 ℃;液压系统的功率损失使系统发热,单位时间的发热量φkW 可表示为φ=-P P 12式中 P 1—— 系统的输入功率即泵的输入功率kW ; P 2—— 系统的输出功率即液压缸的输出功率kW;若在一个工作循环中有几个工作阶段,则可根据各阶段的发热量求出系统的平均发热量对于本次设计的组合机床液压系统,其工进过程在整个工作循环中所占时间比例达95%%23.956120120212=+=+=t t t α因此系统发热和油液温升可用工进时的发热情况来计算; 工进时液压缸的有效功率即系统输出功率为kW kW Fv P 01225.0601005.01470030=⨯⨯== 这时大流量泵通过顺序阀10卸荷,小流量泵在高压下供油,所以两泵的总输出功率即系统输入功率为:kWkW q p q p P pp p p p i 432.01075.010631.51084.31060226322103.03363262112=⨯⨯⨯⨯+⨯⨯⎪⎭⎫ ⎝⎛⨯⨯=+=--η 由此得液压系统的发热量为()kW kW P P H i i 42.001225.0432.00=-=-=即可得油液温升近似值:()()c C T 0032345.112501042.0=⨯=∆温升小于普通机床允许的温升范围,因此液压系统中不需设置冷却器;设计小结经过大家近周的共同努力,终于有了成果,完成了此次课程设计,再一次系统性的学习了有关液压方面的知识,此次课程设计,感触良多,收获颇丰;通过这次课程设计,让我们每个人都再一次切身体验了课程设计的基本模式和相关流程;在这次课程设计中,我学会了怎样根据老师所给的题目去构思,收集和整理设计中所需要的资料;在这些日子里,我们都夜以继日的演算相关数据,在参考书上寻找参考资料,使我们真正地尝试到了作为一名设计者的辛酸与喜悦;通过本次课程设计,我们将理论知识与实际设计相结合,真正做到了理论联系实际,并且学会了如何综合去运用所学的知识,使我们对所学的知识有了更加深刻的认识和了解,让我们受益匪浅;还有,通过本次设计也让我们体验到了团队合作的重要性和必要性;设计是一个庞大而复杂的系统工程,单枪匹马是很难顺利完成任务的,这就要求我们要有合理的分工和密切的配合,将一个个复杂的问题分解成一个个小问题,然后再各个击破,只有这样才能设计出很实用的产品,同时也可以大大提高工作效率;而且大家都参与进来,都能学到知识;从设计过程中,我复习了以前学过的知识,AUTOCAD的画图水平有所提高,Word输入、排版的技巧也有所掌握,这些应该是我最大的收获;设计是一个系统性的工程,越做到后面,越发现自己知识的局限性,在今后的学习中,还得加紧学习;参考文献1 王积伟,章宏甲,黄谊.液压传动.第二版.北京:机械工业出版社,20108重印2 马振福.液压与气动传动.第二版.北京:机械工业出版社,3成大先.机械设计手册单行本液压传动. 北京:化学工业出版社,2004 4陈启松.液压传动与控制手册M. 上海:上海科学技术出版社,2006。
设计一台卧式单面多轴钻孔组合机床动力滑台的液压系统
负载分析中�暂不考虑回油腔的背压力�液压缸的密封装置产生的摩擦阻力 在机械效率中加以考虑。因工作部件是卧式放置�重力的水平分力为零�这样需 要考虑的力有�夹紧力�导轨摩擦力�惯性力。
在对液压系统进行工况分析时�本设计实例只考虑组合机床动力滑台所受到 的工作负载、惯性负载和机械摩擦阻力负载�其他负载可忽略。
防止油液温升过高。
从工况图中可以清楚地看到�在这个液压系统的工作循环内�液压要求油源
交替地提供低压大流量和高压小流量的油液。而快进快退所需的时间 t1 和工进所 需的时间 t 2 分别为
工进时液压缸的推力计算公式为
F / �m � A1 p1 � A2 p2 � A1 p1 � ( A1 / 2) p2 �
根据已知参数�液压缸无杆腔的有效作用面积可计算为
F
A1 �
�m
p1 �
p2 2
16333 .33 �10 6
�
0.8
3�
2
� 0.006282 m 2
液压缸缸筒直径为
D � 4 A1 � � 89 .46 mm mm
5
工进过程中�当孔被钻通时�由于负载突然消失�液压缸有可能会发生前 冲的现象�因此液压缸的回油腔应设置一定的背压(通过设置背压阀的方式)�选 取此背压值为 p2=0.8MPa。
快进时液压缸虽然作差动连接,但连接管路中不可避免地存在着压降 �p �且 有杆腔的压力必须大于无杆腔�估算取 �p � 0.5MPa。快退时回油腔中也是有背 压的�这时选取被压值 p2 =0.6MPa。
3
Fm
� m�
�v �t
�
20000 9.81
7 �
60 � 0.15
N
设计一卧式单面多轴钻孔组合机床动力滑台的液压系统
设计一卧式单面多轴钻孔组合机床动力滑台的液压系统。
1)工作循环:快进一工进一快退一停止。
2)工作参数轴向切削力21000N,移动部件总重10000N,快进行程100mm, 快进与快退速度4.2m / min,工进行程20mm,工进速度0・05m/min,力口、减速时间为0.2s,静摩擦系数0.2,动摩擦系数0.1,动力滑台可在中途停止。
一、负载分析负载分析中,暂不考虑回油腔的背压力,液压缸的密封装置产生的摩擦阻力在机械效率中加以考虑。
因工作部件是卧式放置,重力的水平分力为零,这样需要考虑的力有:切削力,导轨摩擦力和惯性力。
导轨的正压力等于动力部件的重力,设导轨的静摩擦力为行,动摩擦力为F®,则F t. = f x F N = 0.2 x 10000 N = 2000 NF(d =f d F N =0」x 10000 N = 1000 N而惯性力厂Av G Av 10000 X4.2/60 “=m —=———= -------------- N = 357 N,n 0 g Ar 9.8x0.2如果忽略切削力引起的颠覆力矩对导轨摩擦力的影响,并设液压缸的机械效率%=0.95,则液压缸在各工作阶段的总机械负载可以算出,见表1。
表液压缸各运动阶段负载表根据负载计算结果和已知的各阶段的速度,可绘制出负载图(F-/)和速度图(卩-/ ),见图1a. bo横坐标以上为液压缸活塞前进时的曲线,以下为液压活塞退回时的曲线。
a)b)图1 负载速度图a)负载图b)速度图二、液压系统方案设计1.确定液压泵类型及调速方式参考同类组合机床,同时根据本题要求。
选用双作用叶片泵双泵供油,同时这是调速阀进油调速的开式回路来满足快进、快退和丄进的功能。
快进或快退时双泵进行供油,工进时,小泵单独供油,同时利用节流阀调速保证工进速度。
整个回路釆用溢流阀作定压阀,起安全阀作用。
为防止钻孔钻通时滑台突然失去负载向前冲,回油路上设置背压阀,初定背压值为p h=^MPa o2.选用执行元件因系统循环要求正向快进和工作,反向快退,且快进、快退速度相等。
一种卧式单面多轴钻孔组合机床动力滑台液压系统设计
液压传动在运行中可以实现大范围的无级调速, 调速范围可达 2000:1;传递运动均匀平稳,易于实 现快速启动、制动和频繁的换向;操作控制方便、 省力,易于实现自动控制、中远程距离控制、过载 保护;元件标准化、系列化和通用化程度较高,且 元件布置不受严格的空间位置限制;单位质量输出 功率大,具有同等输出功率下体积小、质量小、运 动惯性小和动态性能好等优点。20 世纪中期以后, 液压传动在工业上被广泛采用。尤其二战后,液压 技术转入民用工业,在机床、工程机械、冶金机械、 塑料机械、农林机械、汽车、船舶等行业得到了大 幅度的应用和发展。如今,发达国家生产的 95%的 工程机械、90%的数控加工中心、95%以上的自动 线都采用了液压传动。随着液压传动的发展,国内 许 多 专 家 开 始 关 注 液 压 系 统 的 设 计 , 于 今 [1] 对 800MN 模锻液压机液压系统进行了设计,推导了主 驱动系统数学模型并对控制系统进行了仿真。司癸 卯等[2]利用电液比例技术对运输车吊装机构液压系 统进行设计计算和选型。王晔等[3]对 150t 液压机液 压系统设计,王丽梅[4]对自动翻转机液压系统设计, 王孝聪等[5]对汽车隔音垫成型机床液压系统设计, 苌晓兵等[6]对建筑模架顶升液压系统设计和吴正佳 等[7]对钢管打捆机液压系统设计,都采用了传统的 液压设计方法,利用经验公式进行了参数计算和选 型。综合以上文献对液压系统的设计都忽略了性能 的验算,即通过不同工况下压力损失计算,进而对 泵、液压缸和各种控制阀的参数或型号进行修正。 并且很多没有对液压系统进行发热和温升验算。基
������ = ������������������ /������������ ������ = ������������������ + ������������ /������������
- 1、下载文档前请自行甄别文档内容的完整性,平台不提供额外的编辑、内容补充、找答案等附加服务。
- 2、"仅部分预览"的文档,不可在线预览部分如存在完整性等问题,可反馈申请退款(可完整预览的文档不适用该条件!)。
- 3、如文档侵犯您的权益,请联系客服反馈,我们会尽快为您处理(人工客服工作时间:9:00-18:30)。
设计一卧式单面多轴钻孔组合机床动力滑台的液压系统。
1)工作循环:快进—工进—快退—停止。
2)工作参数轴向切削力21000N ,移动部件总重10000N ,快进行程 100mm ,快进与快退速度 4.2m /min ,工进行程 20mm ,工进速度 0.05m /min ,加、减速时间为0.2s ,静摩擦系数0.2,动摩擦系数0.1,动力滑台可在中途停止。
一、负载分析负载分析中,暂不考虑回油腔的背压力,液压缸的密封装置产生的摩擦阻力在机械效率中加以考虑。
因工作部件是卧式放置,重力的水平分力为零,这样需要考虑的力有:切削力,导轨摩擦力和惯性力。
导轨的正压力等于动力部件的重力,设导轨的静摩擦力为fs F ,动摩擦力为fd F ,则N N F f F N s fs 2000100002.0=⨯==N N F f F N d fd 1000100001.0=⨯== 而惯性力N N t v g G t v mF m 3572.08.960/2.410000 =⨯⨯=∆∆=∆∆= 如果忽略切削力引起的颠覆力矩对导轨摩擦力的影响,并设液压缸的机械效率95.0=m η,则液压缸在各工作阶段的总机械负载可以算出,见表1。
表1 液压缸各运动阶段负载表快进 m fd F F η/= 1053 工进 m fd t F F F η/)(+= 23158 快退 m fd F F η/=1053根据负载计算结果和已知的各阶段的速度,可绘制出负载图(l F -)和速度图(l v -),见图1a 、b 。
横坐标以上为液压缸活塞前进时的曲线,以下为液压活塞退回时的曲线。
a) b)图1 负载速度图 a )负载图 b )速度图二、液压系统方案设计1. 确定液压泵类型及调速方式参考同类组合机床,同时根据本题要求。
选用双作用叶片泵双泵供油,同时这是调速阀进油调速的开式回路来满足快进、快退和工进的功能。
快进或快退时双泵进行供油,工进时,小泵单独供油,同时利用节流阀调速保证工进速度。
整个回路采用溢流阀作定压阀,起安全阀作用。
为防止钻孔钻通时滑台突然失去负载向前冲,回油路上设置背压阀,初定背压值为MPa p b 8.0 。
2. 选用执行元件因系统循环要求正向快进和工作,反向快退,且快进、快退速度相等。
实现快进快退速度相等有以下几种方法:1)单活塞杆液压缸,快进时差动连接,无杆腔面积1A 等于有杆腔面积2A 的两倍。
2)采用双活塞杆液压缸,因两腔有效面积相等,即可满足快进、快退速度相等的要求。
差动连接可降低整个系统工作压力,同时可选用更小规格的油泵。
而且组合机床对工作压力要求的供油压力并不高,所以选择方案一3. 快速运动回路和速度换接回路根据题目运动方式和要求,采用方案一的快速回路系统,差动连接与双泵供油两种快速运动回路来实现快速运动。
即快进时,由大小泵同时供油,液压缸实现差动连接。
采用二位二通电磁阀的速度回路,控制由快进转为工进。
与采用行程阀相比,电磁阀可直接安装在液压站上,由工作台的行程开关控制,管路较简单,行程大小也容易调整,另外采用液控顺序阀与单向阀来切断差动油路。
因此速度换接回路为行程与压力联合控制形式。
4. 换向回路的选择本系统对换向的平稳性没有严格的要求,所以采用电磁换向阀的换向回路,采用三位五通阀。
5.组成液压系统绘原理图将上述所选定的液压回路进行组合,并根据要求作必要的修改补充,即组成如图2所示的液压系统图。
为便于观察调整压力,在液压泵的进口处、背压阀和液压缸无杆腔进口处设置测压点,并设置多点压力表开关。
这样只需一个压力表即能观测各点压力。
图2 组合机床动力滑台液压系统原理图液压系统中各电磁铁的动作顺序如表2所示。
表2 电磁铁动作顺序表三、液压系统的参数计算(一)液压缸参数计算1. 初选同类型组合机床,初定液压缸的工作压力为Pa p 511040⨯=。
2. 确定液压缸的主要结构尺寸要求动力滑台的快进、快退速度相等,现采用活塞杆固定的单杆式液压缸。
快进差动时,并取无杆腔有效面积1A 等于有杆腔有效面积2A 的两倍,即212A A = 。
为了防止钻孔钻通时滑台突然失去负载向前冲,在油路上设置背压阀,按[1]表8-2,初,选背压值Pa p b 5108⨯=。
由表1克制最大负载为工进阶段的负载N F 23158=,按此计算1A 则23255111043.61082110402315821m m P P F A b-⨯≈⨯⨯-⨯=-=液压缸直径cm cm A D 05.93.64441≈⨯==ππ由212A A =可知活塞杆直径cm cm D d 4.605.9707.0707.0≈⨯==按GB/T2348——1993将所计算得D 与d 值分别圆整打动相近的标准直径,以便采用标准的密封装置。
圆整后得cm D 10= cm d 7= 按标准直径算出22225.7810441cm cm D A ≈==ππ2222221.40)710(4)(42cm cm d D A ≈-=-=ππ按最低工进速度演算液压缸尺寸,查产品样本,调速阀最小稳定流量m in /05.0min L q =,因工进速度min /05.0m v =为最小速度,则由[1]式(8-11)2223min min 1101005.01005.0cm cm v q A =⨯⨯=≥ 上述计算中221105.78cm cm A >≈,满足最低速度的要求。
3. 计算液压缸各工作阶段的工作压力、流量和功率根据液压缸的负载图和速度图以及液压缸的有效面积,可以算出液压缸工作过程中各阶段的压力、流量和功率,在计算工进时按Pa p b 5108⨯=代入,快退时背压按Pa p b 5105⨯=代入计算公式和计算结果列于表3中。
表3液压缸所需的实际流量、压力和功率注:1.差动连接时,液压缸的回油口到进油口之间的压力损失Pa p5105⨯=∆,而p p p j b ∆+=。
2.快退时,液压缸有杆腔进油,压力为j p ,无杆腔回油,压力为b p 。
(二)液压泵的参数计算由表3可知工进阶段液压缸工作压力最大,若取进油路总压力损失Pa p 5105⨯=∆∑,则液压泵最高工作压力可按[1]式(8-5)算出Pa Pa p p p P55106.3810)56.33(1⨯=⨯+=∆∑+=因此泵的额定压力可取Pa Pa p r 551048106.3825.1⨯≈⨯⨯≥。
由表1-5可知,工进时所需流量最小是min /39.0L ,设溢流阀最小溢流量为min /5.2L ,则小流量泵的流量按[1]式(8-16)应为min /93.2min /)5.239.01.1(1L L q p ≈+⨯≥,快进快退时液压缸所需的最大流量是min /8.16L ,则泵的总流量为min /5.18min /8.161.1L L q p ≈⨯=。
即大流量泵的流量min /57.15min /)93.25.18(12L L q q q p p p =-=-≥。
根据上面计算的压力和流量,查相关产品样本得,选用YB-4/16型双联叶片泵。
该泵额定压力MPa 3.6,额定转速min /960r 。
(三)电动机的选择系统为双泵供油系统,其中小泵1的电动机的选择流量 s m s m q p /100667.0/)60/104(33331--⨯≈⨯= ,大泵2流量s m s m q p /10267.0/)60/1016(33332--⨯≈⨯=。
差动快进、快退时两个泵同时向系统供油;工进时,小泵1向系统供油,大泵2卸载。
下面分别计算三个阶段所需要的电动机功率P 。
1.差动快进差动快进时,大泵2的出口压力油经单向阀后与小泵1汇合,然后经单向阀2,三位五通3,二位二通阀4进入液压缸无杆腔,无杆腔压力Pa p p j 51096.71⨯==,查样本可知,小泵2的出口压力损失Pa p 51105.4⨯=∆,大泵2出口到小泵1出口的压力损失Pa p 52105.1⨯=∆。
于是计算可得小泵出压力Pa p P 51046.121⨯=(总效率5.01=η),大泵2出口压力Pa p P 51096.132⨯=(总效率5.02=η)。
电动机功率W W q P q P P P P 912)5.010267.01096.135.0100667.01046.12(35352221111=⨯⨯⨯+⨯⨯⨯=+=--μμ2.工进考虑到调速阀所需要的最小压力差Pa p 51105⨯=∆。
压力继电器可靠动作需要压力差Pa p 52105⨯=∆。
因此工进时小泵1的出口压力Pa p p p P P 52111106.43⨯=∆+∆+=。
而大泵2的卸载压力取Pa P P 51102⨯=。
(小泵1的总效率565.01=η,大泵2总效率3.02=η)。
W W q P q P P P P 650)3.0102.0102565.0100667.0106.43(35352221112≈⨯⨯⨯+⨯⨯⨯=+=--μμ3.快退类似差动快进分析知:小泵1的出口压力Pa P P 51109.16⨯=(总效率5.01=η):大泵2出口压力Pa p P 52104.18⨯=(总效率51.02=η)。
电动机功率W W q P q P P P P 947)51.0102.0104.185.0100667.0109.16(35352221113≈⨯⨯⨯+⨯⨯⨯=+=--μμ综合比较,快退时所需功率最大。
据此查样本选用Y90L-66封闭式三相异步电动机,电动机功率kW 1.1。
额定转速min /940r 。
四、液压元件的选择1.液压阀及过滤器的选择根据液压阀在系统中的最高工作压力与通过该阀的最大流量,可选出这些元件的型号及规格。
本系统中所有阀的额定压力都为Pa 51063⨯,额定流量根据各阀通过的流量,确定为min /10L ,min /25L 和min /63L 三种规格,所有元件的型号列于表4中。
过滤器按液压泵额定流量的两倍选取吸油用线隙式过滤器。
表中序号与系统原理图中的序号一致。
表4液压元件明细表2. 油管的选择根据选定的液压阀的连接油口齿轮确定管道尺寸。
液压缸的进、出油管按输入、排出的最大流量来计算。
由于本系统液压缸差动连接快进快退时,油管内通油量最大,其实际流量为泵的额定流量的两倍达min40L,则液压缸进、出油管/直径d按产品样本,选用内径为mm19的10号冷拔钢管。
15,外径为mm3. 油箱容积的确定中压系统的油箱容积一般取液压泵额定流量的5到7倍,本系统取7倍,故油箱容积为7(==16⨯)LLV112五、验算液压系统性能(一)压力损失的验算及泵压力的调整1.工进时的压力损失验算和小流量泵压力的调整工进时管路中的流量仅为min /39.0L ,因此流速很小,所以沿程压力损失和局部压力损失都非常小,可以忽略不计。