加氢裂化工艺 精品
加氢裂化工艺及过程

◎ 采用一次通过或未转化油循环裂化的方式操作均可。 ◎ 其特点是: ⊙ 工艺流程简单,体积空速相对较高; ⊙ 催化剂应具有较强的耐 S、N、O等化合物的性能; ⊙ 原料油的氮含量不宜过高,馏分不宜过重; ⊙ 反应温度相对较高,运转周期相对较短。
相同.
◎ 原料油中类烃分子的加氢裂化反应, 与FCC过程类同,其反应历程
都遵循羰离子(正碳离子)反应机理和正碳离子β位断链的原则; 所不同的是, 加氢裂化过程自始至终伴有加氢反应, 并具有以下 特点。
催化加氢技术
⊙ 多环芳烃加氢裂化以逐环加氢饱和/开环的方式进行, 生成小分子 的烷烃及环烷-芳烃;
1.2 国内加氢裂化技术的发展
◎ 50年代, 恢复了页岩粗柴油高压加氢, 发展了页岩油全馏分固定 床加氢裂化, 以及低温干馏煤焦油的高压三段加氢裂化技术。
◎ 60年代中期, 开发了107、219无定型加氢裂化催化剂和H-06沸石 催化剂;
◎ 1966年在大庆炼厂建成了40万吨/年加氢裂化装置, 加工大庆常三 线/减一线混合油, 生产喷气燃料和-50#低凝柴油;
R-2循环氢 加热炉
循环氢 R-2
循环氢压缩机
急冷氢
空冷
高分
酸性水
闪蒸气
补充氢 补充氢
进料泵
增压机
循环油
注水泵
洗涤水
ቤተ መጻሕፍቲ ባይዱ
低分 取分馏系统
循环油泵
来自分馏塔底的未转化油
催化加氢技术
◎ 一段串联加氢裂化的特点
⊙ 精制段催化剂应具有较高的加氢活性(尤其是HDN活性); ⊙ 裂化段催化剂应具有耐 H2S 和 NH3 的能力; ⊙ 严格控制精制油氮含量 ⊙ 产品质量好, 生产灵活性大, 一次运转周期长; ⊙ 与一段法加氢裂化相比, 其原料油适应性较强, 体积
加氢裂化工艺及过程ppt课件

ppt课件.
2
催化加氢技术
2.0 加氢裂化工艺流程
2.1 两段法加氢裂化
2.2 单段加氢裂化
2.3 一段串联(单程通过,未转化油全循环、部分循环)
3.0 中压加氢裂化及相关的加氢转化技术
3.1 提高十六烷值技术〔MCI〕
3.2 低凝柴油生产技术〔HDW〕
3.4 柴油深度加氢脱硫脱芳烃技术
3.5 提高车用汽油质量的相关技术
FCC比加氢裂化要经济, 加氢裂化的发展再度受到冲击而有所减
缓。
ppt课件.
11
催化加氢技术
◎ 70年代加氢裂化已成为一项成熟的工艺技术, 催化剂的发展, 允 许现有装置的设备转向重质原料的加工, 其柴油的收率可高达 95v%(对原料油)。
◎ 加氢裂化是增产石脑油、喷气燃料最有效的途径, 这是其它炼油 技术所无法替代的。
催化加氢技术
◎ 在60年代, 加氢裂化能满足石脑油、喷气燃料、柴油、润滑油基 础油、低硫燃料油、液化石油气及石油化工原料生产的要求,
充分证明加氢裂化技术具有极重要的作用和广泛的应用前景。
◎ 60年代末和70年代初, 是美国加氢裂化迅速增长的时期; 70年代 中
期, FCC广泛使用了分子筛催化剂, 氢气费用高, 对于生产汽油,
4.6 加氢催化剂的卸出
4.7 加氢裂化装置现场事故剖析
ppt课件.
4
催化加氢技术
1.0 概 述
◎ 加氢裂化具有加工原料范围宽、原料适应性强、产品方案灵 活、产品质量好、液体产品收率Байду номын сангаас等独具的特点。
◎ 能生产从液化石油气、石脑油、喷气燃料、柴油到蒸汽裂解、 润滑油基础油等多种优质产品和石油化工原料。
加氢裂化工艺及过程PPT课件

◎ 1925年建成了第一套褐煤焦油加氢裂化装置,1943年已有12套
装置投入生产。
◎ 二次大战后期,为德国提供了95%的航空汽油和47%的烃类产
品。
◎ 英、法、日(在中国东北-当时的“满洲”)、韩国都进行过类
似的尝试;
◎ 类似技术的研究, 在美国则是直接面向重石油馏分加氢转化技术
的开发。
.
7
催化加氢技术
石化公司建成投产。 ◎ 80年代中期以来, 相继在抚顺、镇海、辽阳、吉林、天津和山东
等地建设了40 140 万吨/年规模的多套加氢裂化装置。 ◎ 90年代末, 大连 WEPEC 和茂名石化公司分别建成了200万吨/年
渣油固定床加氢处理装置。表明我国已具备开发成套催化加氢 技术的能力, 步入了世界加氢技术先进水 平的行列。 ◎ 在清洁燃料的生产中, 加氢技术必将会得到稳步持续地发展。
.
9
催化加氢技术
◎ 1959年Chevron研究公司宣布“加氢异构裂化工艺”在里奇蒙炼 厂
投入工业运转, 证实该发明的催化剂可允许在200400 ℃ 、3.5 14MPa 的条件下操作后, 加氢裂化从此走出低谷。 ◎ 1960年UOP公司开发了 “Lomax”加氢裂化工艺;Union oil 公司开发了“Unicacking”工艺; 60年代加氢裂化作为炼油 技术很快为人们所接受。 ◎ 1966年有7种加氢裂化技术获得了销售许可证; 60年代末 已投产和在建的有9种不同的工艺; 其催化剂的活性、稳 定性都好于早期催化剂, 特别是.分子筛催化剂得到工业 10
催化加氢技术
◎ 在60年代, 加氢裂化能满足石脑油、喷气燃料、柴油、润滑油基 础油、低硫燃料油、液化石油气及石油化工原料生产的要求, 充分证明加氢裂化技术具有极重要的作用和广泛的应用前景。
《加氢裂化工艺》课件
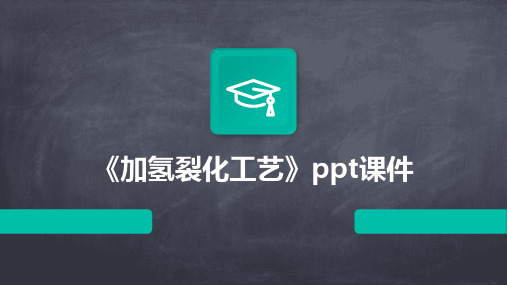
反应器的设计应考虑压力降、温度分布、催化剂装填量等因素,以确 保原料油在最佳条件下进行反应。
04
反应器的操作应控制适当的反应温度和压力,以获得所需的加氢裂化 产物。
加热炉
加热炉是加氢裂化工艺中用于 加热原料油的关键设备。
加热炉通常采用管式加热炉, 炉管内通过原料油,炉管外燃 烧燃料油或天然气,通过热传 导和热辐射将热量传递给原料
技术发展趋势与展望
高效催化剂
研发高效、稳定的催化剂是加氢裂化工艺的重要 发展方向。新型催化剂可提高反应活性和选择性 ,降低能耗和原料消耗,提高产品收率和质量。
智能化控制
智能化控制技术可以提高加氢裂化工艺的安全性 和稳定性。通过实时监测、自动控制和优化操作 ,可降低人工操作成本和事故风险,提高生产效 率。
压缩机的设计应考虑压缩比、 输送能力、机械效率等因素, 以确保气体和液体能够被顺利 压缩和输送。
压缩机的操作应控制适当的入 口和出口压力,以防止气体和 液体在压缩过程中发生泄漏和 堵塞。
分离器
分离器是加氢裂化工艺中用 于分离液体和气体的关键设
备。
1
分离器通常采用立式或卧式 分离器,通过重力或离心力 的作用将液体和气体进行分
绿色低碳发展
随着环保意识的提高,低碳、环保的加氢裂化工 艺成为未来的发展趋势。通过优化反应条件、降 低能耗和减少废物排放,实现加氢裂化工艺的绿 色低碳发展。
拓展应用领域
随着市场需求的变化,加氢裂化工艺的应用领域 也在不断拓展。例如,在生产高品质润滑油、石 蜡、高纯度溶剂等化学品方面,加氢裂化工艺具 有广阔的应用前景。
环保要求与处理措施
01
02
03
04
加氢裂化工艺应符合国家和地 方环保法规要求,确保排放的 废气、废水等污染物达到标准
演示文稿加氢裂化工艺及过程
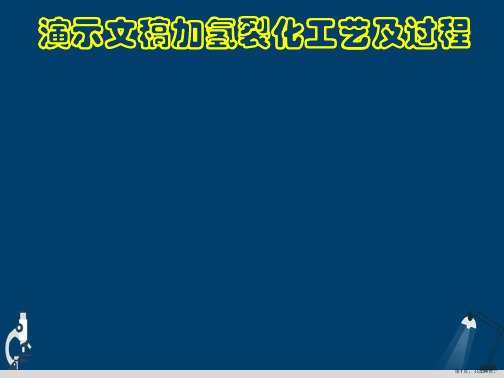
应用。
第11页,共334页。
催化加氢技术
◎ 在60年代, 加氢裂化能满足石脑油、喷气燃料、柴油、润滑油基
础油、低硫燃料油、液化石油气及石油化工原料生产的要求, 充分证明加氢裂化技术具有极重要的作用和广泛的应用前景。
◎ 加氢裂化是增产石脑油、喷气燃料最有效的途径, 这是其它炼油
技术所无法替代的。
◎ 在清洁燃料生产中,加氢裂化正扮演着一个重要的角色。
第13页,共334页。
催化加氢技术
1.2 国内加氢裂化技术的发展
◎ 50年代, 恢复了页岩粗柴油高压加氢, 发展了页岩油全馏分固定 床加氢裂化, 以及低温干馏煤焦油的高压三段加氢裂化技术。
3.6 渣油加氢处理技术
第4页,共334页。
催化加氢技术
4.0 加氢裂化应用技术 4.1 加氢裂化催化剂的开工(催化剂装填、催化剂硫化及钝化、
换进原料油) 4.2 加氢裂化装置正常运转及相关工艺参数的影响 4.3 加氢裂化装置正常停工及紧急停工
4.4 加氢裂化催化剂器内及器外再生技术
4.5 加氢裂化催化剂器外硫化技术
催化加氢技术
◎ 70年代末, 引进了4套加氢裂化装置, 19821990年相继开工投产。 ◎ 80年代中期, 引进了140万吨/年重油加氢联合装置, 1992年在齐鲁
石化公司建成投产。 ◎ 80年代中期以来, 相继在抚顺、镇海、辽阳、吉林、天津和山东
等地建设了40 140 万吨/年规模的多套加氢裂化装置。 ◎ 90年代末, 大连 WEPEC 和茂名石化公司分别建成了200万吨/年
加氢裂化工艺流程介绍
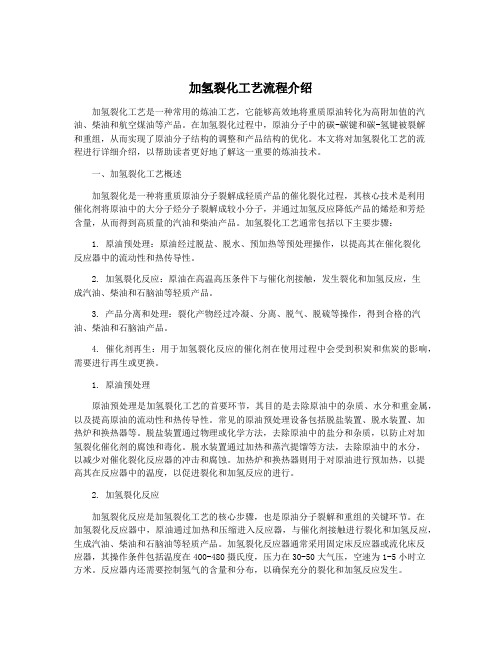
加氢裂化工艺流程介绍加氢裂化工艺是一种常用的炼油工艺,它能够高效地将重质原油转化为高附加值的汽油、柴油和航空煤油等产品。
在加氢裂化过程中,原油分子中的碳-碳键和碳-氢键被裂解和重组,从而实现了原油分子结构的调整和产品结构的优化。
本文将对加氢裂化工艺的流程进行详细介绍,以帮助读者更好地了解这一重要的炼油技术。
一、加氢裂化工艺概述加氢裂化是一种将重质原油分子裂解成轻质产品的催化裂化过程,其核心技术是利用催化剂将原油中的大分子烃分子裂解成较小分子,并通过加氢反应降低产品的烯烃和芳烃含量,从而得到高质量的汽油和柴油产品。
加氢裂化工艺通常包括以下主要步骤:1. 原油预处理:原油经过脱盐、脱水、预加热等预处理操作,以提高其在催化裂化反应器中的流动性和热传导性。
2. 加氢裂化反应:原油在高温高压条件下与催化剂接触,发生裂化和加氢反应,生成汽油、柴油和石脑油等轻质产品。
3. 产品分离和处理:裂化产物经过冷凝、分离、脱气、脱硫等操作,得到合格的汽油、柴油和石脑油产品。
4. 催化剂再生:用于加氢裂化反应的催化剂在使用过程中会受到积炭和焦炭的影响,需要进行再生或更换。
1. 原油预处理原油预处理是加氢裂化工艺的首要环节,其目的是去除原油中的杂质、水分和重金属,以及提高原油的流动性和热传导性。
常见的原油预处理设备包括脱盐装置、脱水装置、加热炉和换热器等。
脱盐装置通过物理或化学方法,去除原油中的盐分和杂质,以防止对加氢裂化催化剂的腐蚀和毒化。
脱水装置通过加热和蒸汽提馏等方法,去除原油中的水分,以减少对催化裂化反应器的冲击和腐蚀。
加热炉和换热器则用于对原油进行预加热,以提高其在反应器中的温度,以促进裂化和加氢反应的进行。
2. 加氢裂化反应加氢裂化反应是加氢裂化工艺的核心步骤,也是原油分子裂解和重组的关键环节。
在加氢裂化反应器中,原油通过加热和压缩进入反应器,与催化剂接触进行裂化和加氢反应,生成汽油、柴油和石脑油等轻质产品。
加氢裂化反应器通常采用固定床反应器或流化床反应器,其操作条件包括温度在400-480摄氏度,压力在30-50大气压,空速为1-5小时立方米。
一段加氢裂化工艺流程

一段加氢裂化工艺流程英文回答:Hydrocracking is a refining process used to convert heavy hydrocarbon feedstocks into lighter products. It involves the use of hydrogen and a catalyst to break down the long-chain hydrocarbons into smaller molecules. The process is commonly used in the petroleum industry to produce gasoline, diesel, and other high-value products.The hydrocracking process typically begins with thepre-treatment of the feedstock, which involves removing impurities such as sulfur and nitrogen compounds. This is done to protect the catalyst from being deactivated. Once the feedstock is pre-treated, it is mixed with hydrogen gas and introduced into the hydrocracking reactor.Inside the reactor, the feedstock and hydrogen are heated to high temperatures and pressures. The hydrogen acts as a carrier gas and helps to facilitate the crackingreactions. The catalyst, which is typically composed of metals such as platinum or palladium supported on a solid material, promotes the breaking of the hydrocarbon molecules.During the hydrocracking reactions, the long-chain hydrocarbons are broken into smaller molecules, which are then further processed to produce desired products. The reactions involve the breaking of carbon-carbon bonds and the addition of hydrogen atoms to the resulting fragments. This results in the production of lighter hydrocarbons with improved properties, such as higher octane numbers for gasoline.After the reactions take place, the mixture of products is cooled and separated. The lighter products, such as gasoline and diesel, are typically separated from the heavier components, such as waxes and lubricants. The separated products are then further processed and treated to meet the required specifications.Overall, hydrocracking is a complex and importantprocess in the petroleum refining industry. It allows for the conversion of heavy hydrocarbon feedstocks into more valuable products, such as gasoline and diesel. The use of hydrogen and catalysts enables the breaking of long-chain hydrocarbons and the production of lighter molecules. This process plays a crucial role in meeting the demand for cleaner and higher-quality fuels.中文回答:加氢裂化是一种精炼工艺,用于将重质烃原料转化为较轻的产品。
最新-加氢裂化工艺概况-PPT文档资料

1.2 炼油各工艺过程简介
1 常减压
常压蒸馏和减压蒸馏习惯上称为常减压蒸馏,常减压 蒸馏基本属物理过程。常减压装置往往被称为炼油厂的 “龙头”装置,是因为原油进厂加工的第一道工序就是 常减压。原料油在蒸馏塔里按蒸发能力分成沸点范围不同 的油品(称为馏分),这些油有的经调合、加添加剂后以 产品形式出厂,相当大的部分是后续加工装置的原料。因 此,常减压蒸馏又被称为原油的一次加工,我们日常所说 的一次加工能力就是指常减压装置的加工能力。常减压装 置包括三个工序:原油的脱盐、脱水 ;常压蒸馏;减压 蒸馏。
2 催化裂化
催化裂化是在热裂化工艺上发展起来的,是提高原油 加工深度,生产优质汽油、柴油最重要的工艺操作。原料 主要是原油蒸馏或其他炼油装置的350~540℃馏分
的重质油。催化裂化工艺由三部分组成:原料油催化
裂化、催化剂再生、产物分离。催化裂化所得的产物经分 馏后可得到气体、汽油、柴油和重质馏分油。部分重质油 返回反应器继续加工称为回炼油。催化裂化操作条件的改 变或原料波动,可使产品组成出现变化。
3 催化重整
常压蒸馏所得的轻汽油转化成含芳烃较高的重整汽油的 过程。如果以80~180℃馏分为原料,产品为高辛烷值汽 油;如果以60~165℃馏分为原料油,产品主要是苯、甲 苯、二甲苯等芳烃, 重整过程副产氢气,可作为炼油厂 加氢操作的氢源。重整的反应条件是:反应温度为490~ 525℃,反应压力为1~2兆帕。重整的工艺过程可分为原 料预处理和重整两部分。 催化重整(简称重整)是在催化剂和氢气存在下,将
2.2 加氢裂化装置的化学反应
烯烃的加氢裂化反应。加氢裂化条件下,烯烃很容易加氢 变成饱和烃,此外还会进行聚合和环化等反应。(饱和) 芳香烃的加氢裂化反应。对于侧链有三个以上碳原子的芳 香烃,首先会发生断侧链生成相应的芳香烃和烷烃,少部 分芳香烃也可能加氢饱和生成环烷烃。双环、多环芳香烃 加氢裂化是分步进行的,首先是一个芳香环加氢成为环烷 芳香烃,接着环烷环断裂生成烷基芳香烃,然后再继续反 应。 (加氢断环) 非烃化合物的加氢裂化反应。在加氢裂化条件下,含硫、 氮、氧杂原子的非烃化合物进行加氢反应生成相应的烃类 以及硫化氢、氨和水。
- 1、下载文档前请自行甄别文档内容的完整性,平台不提供额外的编辑、内容补充、找答案等附加服务。
- 2、"仅部分预览"的文档,不可在线预览部分如存在完整性等问题,可反馈申请退款(可完整预览的文档不适用该条件!)。
- 3、如文档侵犯您的权益,请联系客服反馈,我们会尽快为您处理(人工客服工作时间:9:00-18:30)。
加氢裂化工艺馏份油加氢裂化是将重瓦斯油和重柴油或者近似馏程的重馏分油转化成轻质馏分(石脑油、煤油、柴油等等)或者润滑油基础料的加工过程。
这个工艺在催化剂的存在下和在特定的条件(温度,压力和空速)下,使原料和氢气发生反应。
加氢裂化反应脱硫原料脱硫是通过使含硫化合物加氢反应生成烃类和硫化氢来进行的。
从反应器出口产品中除去硫化氢,只留下烃类产品。
脱硫反应热量大约是60Btu/scf消耗氢+4 H2RCH2CH2CH2CH3+ H2S噻吩烷烃硫化氢脱氮通过含氮化合物的加氢反应生成氨和烃类将原料中的氮脱除。
随后将反应器出口产品中的氨除掉,只保留烃类。
脱氮反应热大约是67-75Btu/scf消耗氢,但是原料中的氮含量一般很少,只有百万分之几的水平。
因此可以忽略它对总反应热的贡献。
R-CH 2CH 2NH 2+ H 2 RCHCH 2CH 3 + NH 3胺 链烷烃 氨烯烃加氢烯烃加氢反应是最迅速的反应之一,因此几乎所有的烯烃均被饱和。
反应热大约是140Btu/scf 消耗氢。
直馏产品中的烯烃含量普遍很低,但是对于来自二次加工过程或者热加工过程例如焦化,减粘裂化,或渣油加氢裂化(H-OIL*等.)的原料,加氢裂化反应器中烯烃的加氢反应将释放大量的热。
RCH 2CH = CH 2 + H 2 RCH 2CH 2CH 3烯烃 烷烃芳烃饱和原料中的芳烃饱和生成环烷烃。
芳烃饱和会导致大量的氢耗增加和反应热。
反应热会随着芳烃饱和程度从40变到80Btu/scf 消耗氢。
一般来说,反应压力越高,反应温度越低芳烃饱和程度越大。
+3H 2 =H-OIL指由美国烃研究公司授权的渣油加氢裂化/渣油脱硫工艺生产的油。
大分子的加氢裂化几乎所有有过量氢气存在的工艺中都会发生大分子烃加氢裂解成小分子烃的反应。
这个反应释放出大约50Btu/scf氢消耗的热量。
加氢裂化反应放出的热量远远少于反应器中放出的全部热量。
在加氢裂解反应的产物中,大分子的裂化反应会降低比重并生成轻产品,如裂化产品中的气体和轻石脑油。
加氢裂化反应举例如下:RCH2CH2CH2CH 3 + H2RCH 3+ CH3CH2CH3轻烃产品的产率取决于反应温度。
所以,当在反应末期,提高反应温度以补偿催化剂活性的下降时,轻尾烃产品的产率显著增加。
原料规格典型的加氢裂化原料是沸点高于成品柴油的重柴油或者来自于原油蒸馏装臵、减压蒸馏装臵、常压渣油脱硫装臵、焦化装臵和溶剂脱沥青等装臵的减压瓦斯油。
加氢裂化催化剂对于某些杂质(例如氮和金属)非常敏感,所以原料必须符合催化剂厂商为得到合理的催化剂寿命而制定的原料规格。
原料的氮原料里的氮能中和催化剂的酸性。
原料中的氮含量越高,要求的操作条件越苛刻,尤其是反应温度,反应温度提高会导致催化剂失活更快。
原料沸程原料的干点高于设计值会加速催化剂的失活,因而需要更高的反应温度,这样就会降低催化剂寿命。
原料性质对轻产品产率没有直接的影响,但是它们能影响获得希望的转化率所需的反应温度。
轻气体(C4-)和石脑油沸程物料的产率随着催化剂温度的提高而增加。
沥青质在高切割点减压蒸馏中,经常能在减压瓦斯油中发现过高分子量的多环芳烃(沥青质)。
除了加剧催化剂的中毒之外,还能与催化剂发生化学结合,使催化剂永久失活。
金属沉积在催化剂孔道中的金属,尤其是砷、碱金属和碱土金属,能降低催化剂活性。
能够携带金属催化剂污染物的物质通常是润滑油或者润滑脂、焊剂和密封垫片等。
原料携带的铁可能是最难处理的金属催化剂的污染物,它可以与大分子烃化学结合,或者作为悬浮颗粒物质存在。
无论以哪种方式存在,铁不仅都能使催化剂失活,而且阻塞催化剂间隙使压力降增大。
通常,这种阻塞发生在第一个催化剂床层上部的外层。
氯化物原料可能含有痕量的有机氯化物和无机氯化物,它们和脱氮反应的产物氨化合,在反应器馏出物的换热器和管线里形成具有较高腐蚀性的沉积物。
氧原料中的含氧化物能加速催化剂的失活,氧还能增大原料换热器污垢的形成速率。
催化剂加氢裂化反应可以分为两种:(1)脱硫和脱氮与多环芳烃和单环芳烃的加氢——由催化剂(金属)的加氢功能完成(2)加氢脱烷基、加氢开环、加氢裂化和加氢异构化——由催化剂(载体)的酸功能促进。
载体的酸性功能受原料中氮含量的影响。
通常加氢裂化反应采用的催化剂基本上是硅铝载体上的(Ni-Co-Fe)、(Mo-W-U)型催化剂。
通过改变硅铝比来控制加氢裂化、加氢脱烷基、加氢异构化和加氢开环的程度。
裂化反应随着催化剂中硅含量的增加而加强。
金属硫化物能控制脱硫反应、脱氮反应和烯烃、芳烃的加氢等反应。
根据所要处理的原料和所需产品的性质来选择采用哪一种催化剂体系。
绝大多数情况下通过采用两个或多个具有不同酸功能和加氢功能的催化剂可以得到合适的催化剂体系。
在反应器最后一个床层中可以含有10%的脱硫和脱氮催化剂。
工艺构型加氢裂化装臵能够按下列可能的模式进行操作:单级(一次通过模式)操作、部分或全部循环的单级操作和两级操作。
见图3-1和图3-2。
工艺构型的选择取决于催化剂体系。
所要考虑的主要参数是原料质量、产品方案及所需质量、装臵的投资和操作费用。
单级操作这个操作模式对产品产量和质量有很大的影响。
单级操作能从每桶中间馏分油中生产出0.3桶石脑油。
单级设计适合于减压瓦斯油转化成柴油,并具有高选择性。
转化率大约在50-60%。
未转化的原料中的硫、氮和其它杂质少,既可以作为流化催化裂化装臵的原料,又可以作为燃料油调合组分。
单级工艺可以在未转化原料部分或者全部循环状况下操作。
在全部循环情况下,每桶中间馏分油可以得到0.45桶石脑油。
这种情况下,装臵新鲜原料的加工能力减少了。
因此,转化率的提高基本上是以牺牲装臵新鲜原料加工能力和略微增加消耗为代价获得的。
部分循环模式比全循环模式要优越。
因为全循环模式导致高熔点物在原料中累积,造成催化剂中毒速率提高。
两段操作在两段操作方案中,第一段中未转化的物料变成第二个加氢裂化装臵的原料。
这种情况下,原料已经通过脱硫、脱氮和脱其它杂质进行了净化;第二段能使大部分原料转化为高质量的产品。
重质瓦斯油原料含有一些高沸点的芳烃分子,它们很难裂化,在循环操作中将浓缩。
这些高沸点的芳烃分子的浓度高会增加催化剂的中毒率。
在两段操作中,第一段是一次通过操作,因此芳烃分子没有机会浓缩,因为没有物料循环。
第一段也减少了第二段原料中芳烃分子的浓度,所以第二段高沸点芳烃分子的浓度较低。
两段操作产生的轻气体较少,并且使每桶原料消耗的氢气减少。
一般说来,两段工艺中的第二段能生产出最好质量(最低的硫醇,最高的烟点,最低的倾点)的产品。
第一段的质量最差。
对于同样的原料,两段操作的产品与带有循环的单级操作的产品质量相近。
两段方案操作条件的调节更灵活,并且石脑油和中间馏分油的分布更加灵活。
与部分循环和全部循环的方案相比,两段方案需要更高的投资,但经济性更好。
工艺流程反应器部分的原料油由两个或者更多物流组成(见图3-3)。
一股是来自储罐的减压瓦斯油(VGO),另一股可以是直接来自于减压蒸馏装臵的减压瓦斯油。
可能还有一股来自分馏器底的含有未转化物料组成的循环物料。
混合原料通过过滤器F-01来除去大部分在反应器里能阻塞催化剂床层和导致压降升高的颗粒物质。
当油通过缓冲罐V-02以后,由泵P-01送至反应器系统。
来自于循环压缩机的富氢循环气与流出物/原料交换器E-01/02上部的进油混合。
当油气流经换热器02A和02B管壁时,与反应器热流出物进行热交换而被加热。
原料流交换器的下部流体混合物平行经过反应器原料加热器H-01时进一步被加热。
通过控制流向加热炉的燃料,温度控制记录器能控制反应器进口温度。
原料油的一部分分流通过原料流交换器,它降低了交换器的负荷,而使反应器原料加热器H-01很好控制反应器进口温度。
为了很好的控制,需要加热器整体温度高50-75O F。
反应器物流在交换器E-01管壁处将补充氢加热,然后补充氢流向反应器。
通常加氢裂解反应器是瓶型反应器。
补充氢在交换器E-01里预加热后,通过反应器外壁和内瓶的环隙流过反应器。
氢气将硫化氢清洗掉,阻止它在瓶和外壁之间的环隙里聚集。
它也能使反应器一次通过模式部分循环模式图3-1. 加氢裂化操作,一次通过和部分循环模式图3-2. 二段加氢裂化工艺壁保温。
在补充氢向上通过反应器以后,与循环气和来自反应器顶部原料加热器的热进油混合。
热的反应混合物蒸汽流向反应器底部。
循环压缩机将急冷气注入到反应器的催化剂床层之间,使放热反应导致的高温降低。
一些不等的催化剂床层将反应器分隔开。
它能在每个催化剂床层里提供大约相同的温升,并且将温升限制到50O F。
因此,第一个和第二个床层含有全部催化剂的10%和15%,而第三个和第四个床层含有全部催化剂的30%和45%。
反应器内部的催化剂床层能使反应物料充分混合,并且确保流向每个床层的蒸汽和液体有很好的分布。
反应物的良好分布对于阻止部分过热和最大的催化剂寿命是最重要的。
反应器进口喷油嘴的下部是遮蔽在入口篮里的锥形原料分布器。
这些内部部件进行原料分布并且拦住进入反应器的碎片。
在入口篮的下部,原料通过孔板和分布器,在进入第一个催化剂床层之前进一步分布。
内部床层的配备包括以下部分:一个在第一个床层里支撑催化剂的覆盖有金属丝网的催化剂载体栅格。
一些急冷环,将急冷气体分散进床层上部热反应物中。
一个分布总反应混合物的孔板。
一个在进入下一个床层之前最后分布反应混合物的分布座。
一个通过内部床层并且连接每一个下面的催化剂床层的催化剂排泄管。
为了卸载催化剂,通过反应器下面安装的催化剂排泄喷口排泄底部床层的催化剂。
每个床层通过床层排泄管连接到下一个床层,因此用最小的动力就能移走几乎所有的催化剂装料。
用压差指示计连续测量反应器床层顶部和整个反应器的压力降。
反应器里的热电偶可以观察轴向和径向的催化剂温度。
热电偶被安装在每个床层的上部和下部。
床层里同一高度但是不同位臵的测量温度能指示床层沟流的程度及位臵。
物料冷却反应器物流在反应器出口从运行的开始到结束的温度在800-850O F。
在补充氢/反应器物料交换器E01和反应物料/硫化氢气提塔原料交换器E03里将反应器物料冷却。
在反应器物料/空气冷却器E-04里将反应器物料进一步冷却到140O F。
水和多硫化物注入将冷凝液注入到空气冷凝器上部的反应物料中。
注入水的作用是将氨和一些硫化氢气体从反应物料中除去。
在注入点控制物料温度来阻止注入水的全部蒸发和清除固体二硫化铵沉淀。
反应器物料中的痕量氰化物离子能使物料空气冷却器腐蚀。
也可以注入象钠的多硫化物这样的缓蚀剂来阻止氰化物腐蚀。
高压分离器温度控制器通过调解空气冷却器风机将高压分离器V-02的温度控制在大约140O F。
通过控制分离器的温度来阻止下流物流硫化氢吸收器温度的波动。