分散式控制系统共54页文档
分散控制系统

分散控制系统分散由多台计算机分别控制生产过程中多个控制回路,同时又可集中获取数据和集中管理的自动控制系统。
分散控制系统是控制(Control)、计算机(Computer)、数据通信(Communication)和屏幕(CRT──阴极射线管屏幕)显示技术的综合应用。
这些技术术语的英文第一个字母均为C,所以通常也将分散控制称为4C技术。
分散控制系统(见图)采用微处理机分别控制各个回路,而用中小型工业控制计算机或高性能的微处理机实施上一级的控制。
各回路之间和上下级之间通过高速数据通道交换信息。
分散控制系统具有数据获取、直接数字控制、人机交互以及监控和管理等功能。
生产过程的控制系统,经历了从模拟控制(即未经量化的变量控制)系统、计算机监督控制系统、直接数字控制系统、多级控制系统到分散控制系统的发展过程。
直接数字控制系统的缺点是可靠性低,计算机本身的故障会使整个系统失去控制。
因此一般把计算机监督控制系统与直接数字控制系统组合起来,只把模拟控制器不能胜任的任务和发生故障后不致危及整个系统的任务交给直接数字控制系统去完成。
随着对生产过程控制的要求越来越高,出现了计算机多级控制系统,使得数据获取和控制装置大为增加,电缆大为延长,监督控制系统的中央数字控制任务趋于繁重,它的设计成本增加,并且安装费时,因而应用受到限制。
分散控制系统是在计算机监督控制系统、直接数字控制系统和计算机多级控制系统的基础上发展起来的,是生产过程的一种比较完善的控制与管理系统。
在分散控制系统中,按地区把微处理机安装在测量装置与控制执行机构附近,将控制功能尽可能分散,管理功能相对集中。
这种分散化的控制方式能改善控制的可靠性,不象在直接数字控制系统中那样,会由于计算机的故障而使整个系统失去控制。
当管理级发生故障时,过程控制级(控制回路)仍具有独立控制能力,个别控制回路发生故障时也不致影响全局。
相对集中的管理方式有利于实现功能标准化的模块化设计。
分散控制系统概论
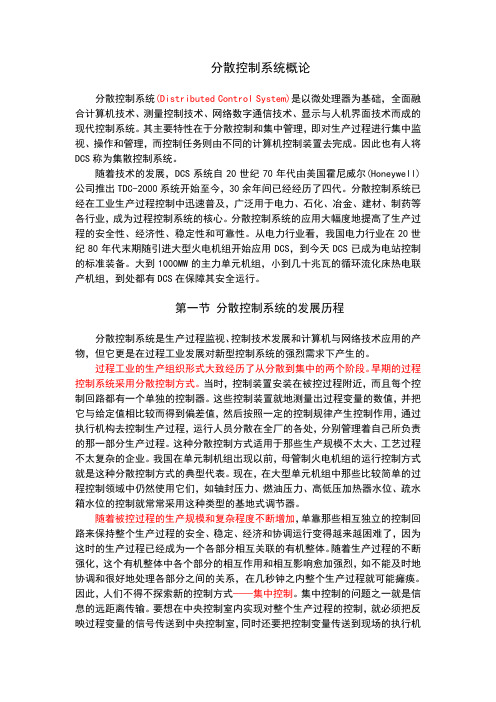
分散控制系统概论分散控制系统(Distributed Control System)是以微处理器为基础,全面融合计算机技术、测量控制技术、网络数字通信技术、显示与人机界面技术而成的现代控制系统。
其主要特性在于分散控制和集中管理,即对生产过程进行集中监视、操作和管理,而控制任务则由不同的计算机控制装置去完成。
因此也有人将DCS称为集散控制系统。
随着技术的发展,DCS系统自20世纪70年代由美国霍尼威尔(Honeywell)公司推出TDC-2000系统开始至今,30余年间已经经历了四代。
分散控制系统已经在工业生产过程控制中迅速普及,广泛用于电力、石化、冶金、建材、制药等各行业,成为过程控制系统的核心。
分散控制系统的应用大幅度地提高了生产过程的安全性、经济性、稳定性和可靠性。
从电力行业看,我国电力行业在20世纪80年代末期随引进大型火电机组开始应用DCS,到今天DCS已成为电站控制的标准装备。
大到1000MW的主力单元机组,小到几十兆瓦的循环流化床热电联产机组,到处都有DCS在保障其安全运行。
第一节分散控制系统的发展历程分散控制系统是生产过程监视、控制技术发展和计算机与网络技术应用的产物,但它更是在过程工业发展对新型控制系统的强烈需求下产生的。
过程工业的生产组织形式大致经历了从分散到集中的两个阶段。
早期的过程控制系统采用分散控制方式。
当时,控制装置安装在被控过程附近,而且每个控制回路都有一个单独的控制器。
这些控制装置就地测量出过程变量的数值,并把它与给定值相比较而得到偏差值,然后按照一定的控制规律产生控制作用,通过执行机构去控制生产过程,运行人员分散在全厂的各处,分别管理着自己所负责的那一部分生产过程。
这种分散控制方式适用于那些生产规模不太大、工艺过程不太复杂的企业。
我国在单元制机组出现以前,母管制火电机组的运行控制方式就是这种分散控制方式的典型代表。
现在,在大型单元机组中那些比较简单的过程控制领域中仍然使用它们,如轴封压力、燃油压力、高低压加热器水位、疏水箱水位的控制就常常采用这种类型的基地式调节器。
分散式控制系统

• 2.操作站 • 操作站由Compaq 386/16主机,19in大屏幕显示器,专用、通用键盘,
声光报警装置及打印机组成。
• 3.监测站
• 监测站具有对生产过程的各种参数的采集、处理、并传送到操作站显 示、储存的功能。监测站由主机、S1板、PI板、双机切换电路、监测 站机柜电源等部件构成。
• 2)采用带CRT显示器的操作站与过程单元分离,实现集中 监视,集中操作
• 3)采用较先进的冗余通信系统 第二阶段
1980—1985.,在这个时期集散控制系统的技术特点表现为: 1)微处理器的位数提高,CRT显示器的分辨率提高 2)强化的模块化系统 3)强化了系统信息管理,加强通信功能
第三阶段
1985年以后,集散系统进入第三代,其技术特点表现为: 1)采用开放系统管理 2)操作站采用32位微处理器 3)采用实时多用户多任务的操作系统
4、典型应用
石油化工工业DCS应用
1、概述
• 石化工业的特点是连续大生产,特别强调安全、稳定、长期、满负荷 、优化的运行。随着生产装置的大型化、复杂化,过程控制在生产上 占有的地位日趋重要。多年来,我国石化工业也努力采用先进的电子 技术改造传统生产方法,积极开发投资少、见效快、经济效益好的微 机控制项目。例如催化裂化监控系统、常减压控制系统、加热炉低氧 燃烧控制、油品调和的离线调优等。同时在一些工艺复杂、效益较高 、管理有一定基础的重要关键生产装置上采用DCS。
物理媒体(通信路径)
物理媒体(通信路径)
系统 A
中继节点 OSI 参考模
系统 BΒιβλιοθήκη 3. 令牌环网通信协议令牌环网是IBM公司于80年代中期推出的一种环形网 ,以屏蔽/非屏蔽双绞线为介质,传输速率为4 Mbps 和16 Mbps。平时,有一个称为“令牌”的特殊数据 帧在网上顺序传送。某站点截获“令牌”后,方可在 一定的时间发送数据;若不发送数据,则将“令牌” 顺序向下传送;若收到的不是发送给自己的数据帧时 ,立即转发。令牌环网采用的是IEEE 802.5或Token Ring协议标准。由于网上只有一个“令牌”,并且只 有截获“令牌”的站点才能发送数据,因此不会发生 数据碰撞。
分散控制系统
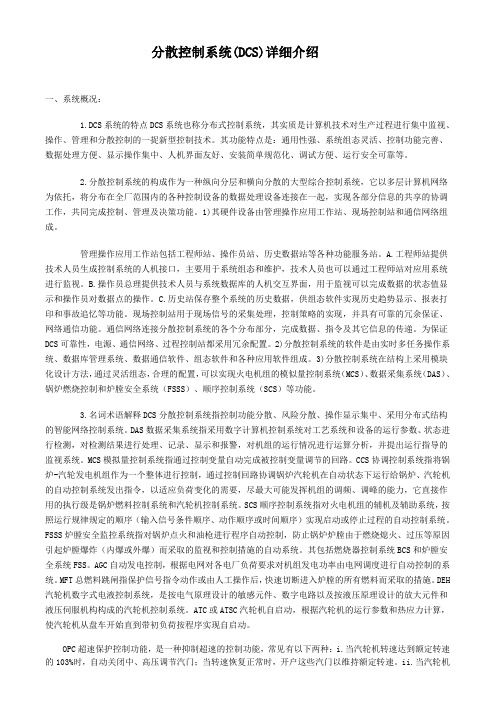
分散控制系统(DCS)详细介绍一、系统概况:1.DCS系统的特点DCS系统也称分布式控制系统,其实质是计算机技术对生产过程进行集中监视、操作、管理和分散控制的一捉新型控制技术。
其功能特点是:通用性强、系统组态灵活、控制功能完善、数据处理方便、显示操作集中、人机界面友好、安装简单规范化、调试方便、运行安全可靠等。
2.分散控制系统的构成作为一种纵向分层和横向分散的大型综合控制系统,它以多层计算机网络为依托,将分布在全厂范围内的各种控制设备的数据处理设备连接在一起,实现各部分信息的共享的协调工作,共同完成控制、管理及决策功能。
1)其硬件设备由管理操作应用工作站、现场控制站和通信网络组成。
管理操作应用工作站包括工程师站、操作员站、历史数据站等各种功能服务站。
A.工程师站提供技术人员生成控制系统的人机接口,主要用于系统组态和维护,技术人员也可以通过工程师站对应用系统进行监视。
B.操作员总理提供技术人员与系统数据库的人机交互界面,用于监视可以完成数据的状态值显示和操作员对数据点的操作。
C.历史站保存整个系统的历史数据,供组态软件实现历史趋势显示、报表打印和事故追忆等功能。
现场控制站用于现场信号的采集处理,控制策略的实现,并具有可靠的冗余保证、网络通信功能。
通信网络连接分散控制系统的各个分布部分,完成数据、指令及其它信息的传递。
为保证DCS 可靠性,电源、通信网络、过程控制站都采用冗余配置。
2)分散控制系统的软件是由实时多任务操作系统、数据库管理系统、数据通信软件、组态软件和各种应用软件组成。
3)分散控制系统在结构上采用模块化设计方法,通过灵活组态,合理的配置,可以实现火电机组的模似量控制系统(MCS)、数据采集系统(DAS)、锅炉燃烧控制和炉膛安全系统(FSSS)、顺序控制系统(SCS)等功能。
3.名词术语解释DCS分散控制系统指控制功能分散、风险分散、操作显示集中、采用分布式结构的智能网络控制系统。
DAS数据采集系统指采用数字计算机控制系统对工艺系统和设备的运行参数、状态进行检测,对检测结果进行处理、记录、显示和报警,对机组的运行情况进行运算分析,并提出运行指导的监视系统。
分散式控制系统
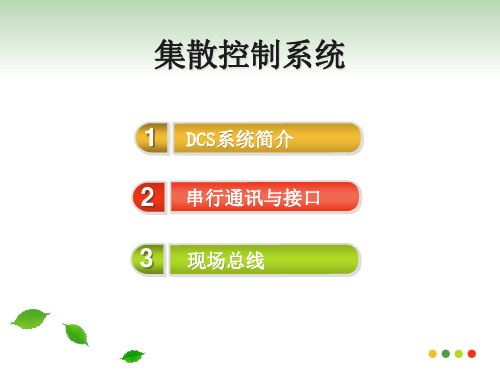
采用9600Kb/s。
二、串行通讯及接口
(2)EIA485 (Electronic Industries Association 485)
属半双工通讯形式,仅需2个双绞线即可通讯,也可采用DB9接口、
水晶头等形式。
485总线式现场总线的鼻祖!
三、现场总线
现场总线(Fieldbus)起源于 20世纪80年代末、90年代初 用于现场总线技术、过程自动
二、串行通讯及接口
(3)模拟数据编码:ASK、FSK、PSK
ASK(amplitude-sheft keying ):幅值键控编码
FSK(frequency-sheft keying): 频率键控编码
PSK(phase-sheft keying):相位键控
二、串行通讯及接口
(4)单字节数据的报文帧
一、概述
(4)管理级由:若干个管理计算机组成
功能: 监测企业各部门的运行情况,利用历史数据和实
时数据预测可能发生的各种情况,从企业全局利
益出发,帮助企业管理人员进行决策,帮助企业 实现其计划目标。 配置要求: 能够对控制系统做出高速反应的实时操作系统。 能够连续运行可冗余的高可靠性系统。 优良的、高性能的、方便的人机接口,丰富的
相应的外部设备: 显示器、大屏幕显示装置、打印机、键盘、鼠标等 开放型DCS采用个人计算机作为人机接口站。
一、概述
操作站
一、概述
(3)监控级 工程师站 工程师站功能及其配置
功能:
控制工程师对DCS进行配置、组态、调试、维护所设置。
对各种设计文件进行归类和管理,形成各种设计、组态文件, 如各种图样、表格等。
三、现场总线
(2)数据链路层 是建立在物理传输能力的基础上,以帧为单位 传输数据。 它的主要任务就是进行数据封装和数据链接的 建立。封装的数据信息中,地址段含有发送节点和 接收节点的地址,控制段用来表示数据连接帧的类 型,数据段包含实际要传输的数据,差错控制段用 来检测传输中帧出现的错误。常见的集线器和低档 的交换机网络设备都是工作在这个层次上。
分散式控制系统的组态

分散式控制系统的组态1. 分散式控制系统的硬件组态1.1 机柜结构,硬件和供电1.1.1 机柜结构:主要部分:左右侧垂直安装板;上下层适配板;SAE 端子区;PC 接口盖板;过程电缆定位槽;各层机架。
右侧垂直安装板上带有供电,保险和分配器标准结构所需的机械部分。
左侧垂直安装板上装有过程接线排列所需部分。
一些机柜的SAE 端子区配置有过程连接所需部分,并且还提供接入的过程电缆和连接部分的电磁兼容性防护。
过程电缆定位槽用做机械上固定过程电缆,并把电缆屏蔽层接到机柜地上。
机柜上下层适配板从上下固定住左右侧垂直安装板和SAE 端子部分,所有机柜内部的机械部分用螺钉和机柜机架固定。
1.1.2 供电:为机柜和机架供电:冗余供电通过二极管解耦;内部的24V 分配:每一层机架提供三种电压:操作电压,总线电压和辅助电压。
对于每一种电压信号回路上都有通过数字集成逻辑开关的熔断丝。
集中控制层AP 层机架供电:内部控制电源提供每层机架供电,事先相应的跳线要跳好,并且通过跳线还可监视外部24V 输入有无故障。
机柜中装有备用电池,备用电池的更换不会影响系统的正常运行,在失电情况下,电池代替工作而不使数I&C 模件防护栏SAE:机柜连接部分 过程电缆槽 接地连接条 总线电缆槽机柜灯 自动断路器及解耦二极管FUM 机架 电源条AP 层机架冗余24V 供电AP层机架有三个风扇,故障通过红色发光二极管显示。
机柜的连接和绕线:过程电缆用压线枪固定在机柜里,屏蔽线接在机柜地上。
接地概念:老系统里一般是多点接地,TXP多采用单点接地。
1.2 FUM-B 模件FUM-B 模件包括:FUM-210 既能作为开关量采集又可用于驱动器控制模件用于开关量采集的FUM 210BT:采集28个单节点或14个双节点信号;多种参数化监视功能;可冗余配置。
用做驱动器控制的FUM210DCM:每一块模件最多控制3个双向驱动器,5个执行器或5个马达/电磁阀;驱动器的类型可以混合使用;采集并监视反馈信号;可冗余配置。
分散控制系统(DCS)

第一章分散控制系统(DCS)一、DCS系统SM 系列硬件系统是和利时公司基于现场总线技术而设计、开发的分布、开放式过程控制硬件系统,具有先进、可靠、高效、节能等特点。
SM 系列硬件系统的体系结构如下图所示,主要由工程师站、操作员站、主控机笼、I/O 机笼、端子模块和通讯网络等组成。
工程师站工程师站是配有系统组态软件的计算机,工程师站对应用系统进行功能组态,包括操作员站组态和控制器组态,并进行在线下装和在线调试,是工程师对工程实施各种控制策略和人机交互方式的工作平台。
操作员站操作员站由配有实时监控软件和各种可配置的人机接口设备的计算机,完成对生产过程和现场参数的实时监视与操作。
操作员站可全面完成对现场工艺状况的显示、报警、打印、历史数据记录和再现及报表等功能。
工程师站和操作员站均运行在基于Windows NT/2000 构架的PC 平台之上。
现场控制机柜SM 系列硬件系统的基础硬件设备如主控机笼(SM110)、扩展机笼(SM111)、端子模块等均置于现场控制机柜(FP051)中,它既可以在控制室中采用柜式集中安装,也可以分散安装。
每个控制机柜正面安装机笼,机笼之间的通讯联系通过预制电缆(SX00x/DB9)连接;每个机笼可以安装10 个模块,主控机笼中安装2 个电源模块(SM900)+2 个主控模块(SM201)+6 个I/O 模块,扩展机笼中安装2 个电源模块(SM900)+8 个I/O 模块;控制机柜背面有三列导轨,可以安装45个100 型端子模块(SM37x),或30 个150 型端子模块(SM32x),或15 个300 型端子模块(SM36x、SM38x)。
主控单元置于主控机笼内部的冗余主控模块是整个SM 系列硬件系统的控制单元,采用双机冗余配置,内部具有硬件构成的冗余切换电路和故障自检电路,是实施各种控制策略的平台,也是系统网络和控制网络之间的枢纽。
主控单元采用嵌入式无风扇设计,超低功耗运行(7.5W@24VDC),用于执行各种实时任务(算法、I/O 管理等)的调度、运算。
分散控制系统
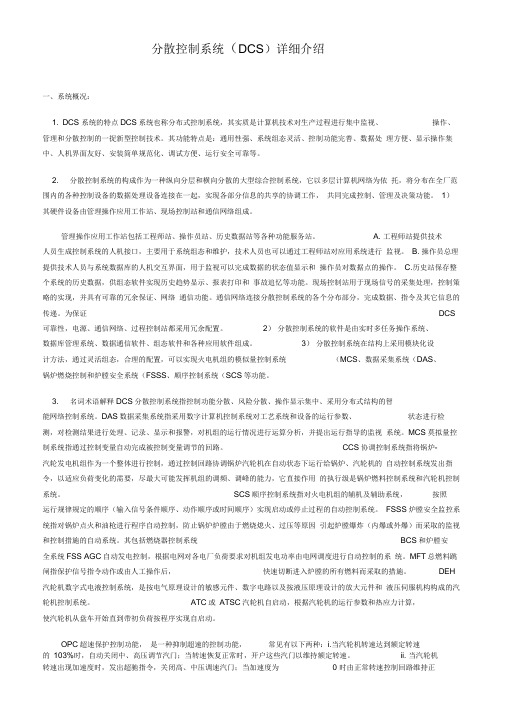
分散控制系统(DCS)详细介绍一、系统概况:1. DCS 系统的特点DCS系统也称分布式控制系统,其实质是计算机技术对生产过程进行集中监视、操作、管理和分散控制的一捉新型控制技术。
其功能特点是:通用性强、系统组态灵活、控制功能完善、数据处理方便、显示操作集中、人机界面友好、安装简单规范化、调试方便、运行安全可靠等。
2. 分散控制系统的构成作为一种纵向分层和横向分散的大型综合控制系统,它以多层计算机网络为依托,将分布在全厂范围内的各种控制设备的数据处理设备连接在一起,实现各部分信息的共享的协调工作,共同完成控制、管理及决策功能。
1)其硬件设备由管理操作应用工作站、现场控制站和通信网络组成。
管理操作应用工作站包括工程师站、操作员站、历史数据站等各种功能服务站。
A. 工程师站提供技术人员生成控制系统的人机接口,主要用于系统组态和维护,技术人员也可以通过工程师站对应用系统进行监视。
B. 操作员总理提供技术人员与系统数据库的人机交互界面,用于监视可以完成数据的状态值显示和操作员对数据点的操作。
C.历史站保存整个系统的历史数据,供组态软件实现历史趋势显示、报表打印和事故追忆等功能。
现场控制站用于现场信号的采集处理,控制策略的实现,并具有可靠的冗余保证、网络通信功能。
通信网络连接分散控制系统的各个分布部分,完成数据、指令及其它信息的传递。
为保证DCS 可靠性,电源、通信网络、过程控制站都采用冗余配置。
2)分散控制系统的软件是由实时多任务操作系统、数据库管理系统、数据通信软件、组态软件和各种应用软件组成。
3)分散控制系统在结构上采用模块化设计方法,通过灵活组态,合理的配置,可以实现火电机组的模似量控制系统(MCS、数据采集系统(DAS、锅炉燃烧控制和炉膛安全系统(FSSS、顺序控制系统(SCS等功能。
3. 名词术语解释DCS分散控制系统指控制功能分散、风险分散、操作显示集中、采用分布式结构的智能网络控制系统。