DCS控制系统与PLC控制区别
DCS控制系统与PLC控制系统区别

u 操作站安装有操作系统、监控软件和控制器的驱动软件。显示系统的标签、动态流程图和报警信息。
u 工程师工作站给控制器组态(CAD),也可以给操作站组态(作动态流程图)。如果监控软件作图能力很强,作图工作可以由监控软件独立完成。工程师站的另外一个功能是读控制器的组态,用于控制器升级,查找故障。我们称之为逆向工程师站。
首先提出DCS这样一种思想的是原制造仪表的厂商,当时主要应用于化工行业。后又有计算机行业从事DCS的开发。70年代微机技术还不成熟,计算机技术还不够发达。操作站、控制器、I/O板和网络接口板等都是DCS生产厂家自行开发的,也就是所有部件都是专用的。70年代初,有人用如PDP/1124这样的小型机代替原来的集中安装的模拟仪表控制。连接到中央控制室的电缆很多。如用小型机既作为控制器、同时把连接小型机的CRT又作为显示设备(即人机界面)。一台小型机需接收几千台变送器或别的传感器来的信号,完成几百个回路的运算。很显然其危险有点集中。和模拟仪表连接的电缆一样多,并且一旦小型机坏了,控制和显示都没有了。数字控制没有达到预期的目的。后有人提出把控制和显示分开。一台计算机完成控制计算任务,另一台计算机完成显示任务。另外,一个工艺过程作为被控对象可能需要显示和控制的点很多,其中有一些还需要闭环控制或逻辑运算,工艺过程作为被控对象的各个部分会有相对独立性,可以分成若干个独立的工序,再把在计算机控制系统中独立的工序上需要显示和控制的输入、输出的点分配到数台计算机中去,把原来由一台小型机完成的运算任务由几台或几十台计算机(控制器)去完成。其中一台机器坏了不影响全局。所谓“狼群代替老虎”的战术,这就是危险分散的意思。把显示、操作、打印等管理功能集中在一起,用网络把上述完成控制和显示的两部分连成一个系统。当时有人把这种系统称为集散系统。
DCS系统与PLC系统区别
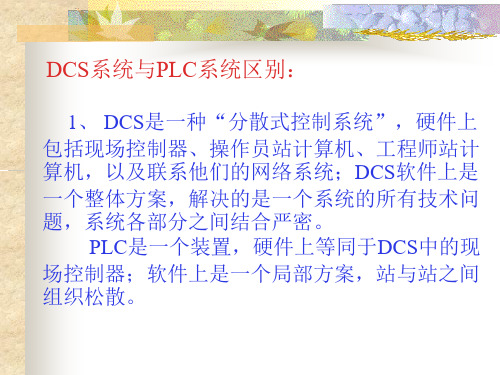
3、 DCS开发控制算法采用仪表技术人员熟悉 的风格,仪表人员很容易将P&I图转化成 DCS提供的控制算法,而PLC采用梯形图 逻辑来实现过程控制,对于仪表人员来说 相对困难。尤其是复杂回路的算法,不如 DCS实现起来方便。
பைடு நூலகம்
4、DCS系统通常提供完整的系统给用户,包 括机柜,电源,工程站,操作员站,用户 只需在现场简单的安装。而PLC则需要系 统集成。
5、DCS实现顺序连锁功能相对于PLC来讲是 弱势,且逻辑执行速度不如PLC, 也不如 PLC编程方便。 6、DCS的现场控制站层‘通常采用集中式控 制,尽管支持远程分布式I/O, 但由于成本 原因, 很少采用。而PLC基于现场总线的 远程分布式I/O更灵活易用,能有效的节省 接线成本。 7、目前来说两者越来越接近了,基本都相互 替用。
2、 DCS系统采用一个统一的开发环境,工程师 站(过程管理层)用于现场控制站的组态,控制 算法的开发以及流程图画面的开发。采用一个统 一数据库!而PLC用于过程控制需要不同的开发 环境,首先要对PLC(相当于DCS的现场控制站 层)进行逻辑开发,建立相应的数据库,然后再 通过相应的上位机软件,例如GE Fanuc 的roficy HMI/SCADA - iFIX 或CIMPLICITY Plant Edition 软件,建立与PLC相对应的数据库,然后进行流 程图画面的开发。
DCS系统与PLC系统区别:
1、 DCS是一种“分散式控制系统”,硬件上 包括现场控制器、操作员站计算机、工程师站计 算机,以及联系他们的网络系统;DCS软件上是 一个整体方案,解决的是一个系统的所有技术问 题,系统各部分之间结合严密。 PLC是一个装置,硬件上等同于DCS中的现 场控制器;软件上是一个局部方案,站与站之间 组织松散。
仪表控制系统DCS和PLC最大的区别在哪

仪表控制系统DCS和PLC最大的区别在哪一、PLe系统1.从开关量控制发展到顺序控制、运送处理,是从下往上的连续 PlD 控制等多功能,PlD在中断站中。
2.可用一台PC机为主站,多台同型PLC为从站。
3.也可一台PLC为主站,多台同型PLC为从站,构成PLC网络。
这比用PC机作主站方便之处是:有用户编程时,不必知道通信协议,只要按说明书格式写就行。
4. PLC网格既作为独立DCS,也可作为DCS的子系统。
5. PLC主要用于工业过程中的顺序控制,新型PLC也兼有闭环控制功能。
二、DCS系统1.分散式控制系统 DCS 集 4C (Communication, Computer, Control, CRT)技术于一身的监控技术。
2.从上到下的树状拓扑大系统,其中通信是关键。
3. PID在中断站中,中断站联接计算机与现场仪器仪表与控制装置是树状拓扑和并行连续的链路结构,也有大量电缆从中断站并行到现场仪器仪表。
4.模拟信号,A/D-—D/A、带微处理器的混合。
5. 一台仪表一对线接到I/O,由控制站挂到局域网LAN6. DCS是控制(工程师站)、操作(操作员站)、现场仪表(现场测控站)的3级结构。
用于大规模的连续过程控制,如石化等。
三、如何抉择PLC和DCS系统在可编程逻辑控制器(PLC)和分散式控制系统(DCS)之间如何抉择,要具体情况具体分析,因为应用场合不同,对控制系统的要求也各不相同。
控制系统平台,对自动化系统满足优化生产、维持可用性和获取数据等需求的方式,会有一定的影响。
在选择控制系统方面缺乏远见,也可能会影响未来的扩展、流程优化、用户满意度和公司利润。
除了一些基本准则之外(比如如何控制过程),设计团队还必须考虑安装、可扩展性、维护、保养等方面的各种因素。
目前,虽然对小设备来讲,PLe系统可能是最划算的,但DCS系统则提供了更具经济性的可扩展能力,更可能获得较高的初始投资回报。
PLC是一种工业计算机,用于控制生产制造过程,如机器人、高速包装、装瓶和运动控制等。
DCS系统和PLC有哪几点不同

DCS是PLC的另一种表现形式。
它与PLC有许多相似之处,但本质上还是不尽相同的。
大体来说,DCS与PLC有以下4点不同:
1)PLC的大部分模块是不具备智能的,由CPU模块上的程序控制各模块的运行;DCS的大部分模块都是智能的,可以独自完成需要执行的任务,仅需将与其他功能模块有关联的数据与外界交换。
2)PLC的模块因硬件的不同而区分,每种类型的硬件是一种模块;DCS的模块除了按硬件划分,还需要根据预装的软件来细分,每个功能是一种模块。
驱动器被定义为DCS模块的一种。
3)绝大部分的DCS模块是不需要编程的,只需要简单的设置几个参数即可使用。
4)PLC分砖头式和框架式两种结构,需要将一定数量的模块组装在一起使用;DCS分单板式与模块式两种结构,每个模块都能单独放置在任何需要的地方。
使用DCS系统后,硬件成本与使用PLC系统大致持平,但系统成本大幅下降。
南昌联控自动化设备有限公司就是一家从事工厂自动化控制产品销售、维修、系统成套的专业技术型公司。
公司的经营项目主要是交流变频器、伺服驱动器、直流调速器、可编程控制器(PLC)、控制元器件以及电气自动化成套设备的设计开发、系统集成、现场调试等。
DCS和PLC区别及优缺点

plc和dcs在工业自动化控制中占有举足轻重的地位,而工业自动化控制是国家工业发展战略的核心。
PLC以及DCS在工业控制的各个环节中不断的升级、完善,已经成为现代工业生产制造中不可或缺的工具。
1、DCS和PLC的定义DCS控制系统,在国内自控行业又称之为集散控制系统。
即所谓的分布式控制系统,是相对于集中控制系统而言的一种新型计算机控制系统,它是在集中控制系统的基础上发展、演变而来的。
DCS作为一个集过程控制和过程监控为一体的计算机综合系统,在通信网络的不断带动下,DCS系统已经成为了一个综合计算机,通信、显示和控制等4C技术的完整体系。
其主要特点是分散控制、集中操作、分级管理、配置灵活以及组态方便。
现如今的DCS系统可以广泛地用于工业装置的生产控制和经营管理,在化工、电力、冶金等流程自动化领域的应用已经十分普及。
PLC,即逻辑可编程控制器,是一种数字运算操作的电子系统,专为在工业环境应用而设计的。
它采用一类可编程的存储器,用于其内部存储程序,执行逻辑运算、顺序控制、定时、计数与算术操作等面向用户的指令,并通过数字或模拟式输入/输出控制各种类型的机械或生产过程,是工业控制的核心部分。
2、DCS和PLC控制器的差别DCS和PLC控制器的主要差别是在开关量和模拟量的运算上,即使后来两者相互有些渗透,但是仍然有区别。
80年代以后,PLC除逻辑运算外,也增加了一些控制回路算法,但要完成一些复杂运算还是比较困难,PLC用梯形图编程,模拟量的运算在编程时不太直观,编程比较麻烦。
但在解算逻辑方面,表现出快速的优点。
而DCS使用功能块封装模拟运算和逻辑运算,无论是逻辑运算还是复杂模拟运算的表达形式都非常清晰,但相对PLC来说逻辑运算的表达效率较低。
3、DCS和PLC在火电厂的应用在火电厂热工自动化领域,DCS和PLC是两个完全不同而又有着千丝万缕联系的概念。
DCS和PLC都是计算机技术与工业控制技术相结合的产物,火电厂主机控制系统用的是DCS,而PLC主要应用在电厂辅助车间。
dcs与plc的什么区别_DCS与PLC你怎么选择?

dcs与plc的什么区别_DCS与PLC你怎么选择?工业界对于分布式控制系统(dcs)与可编程逻辑控制器(plc)两者孰优孰劣的争论已经持续了至少40年。
然而,随着技术的发展,争论并未停止。
由于两者功能特性越来越接近,价格差异也在缩小,曾经一度很清晰的选择,现在似乎变得越来越模糊。
要想理解这两者之间的争论,就一定要明确这两种平台之间的根本性差异。
要想理解这两者之间的争论,就一定要明确这两种平台之间的根本性差异。
例如,DCS体系结构源自一种完整的系统方法,其焦点在于基于网络实现分布式控制,协助作业人员监视并操控工厂中的任何一个区域。
通过高性能的确定性网络实现一致、同步并且完整的过程数据正是DCS体系结构的核心。
另一方面,PLC体系结构聚焦于灵活快速的本地控制,PLC技术最近的发展为其增加了过程控制能力。
当PLC和hmi软件集成在一起时,其最终形态看起来与DCS十分类似,但是这仍旧是一种自建(DIY)的实现方法,意味着工程师必须亲力亲为实现系统的每一个环节。
对于控制来说这种方法更加灵活,但是DIY通常意味着在组网和性能上更大的技术风险,其导致的成本增加会在后期慢慢体现。
以前,相对于PLC系统来说,DCS通常更加昂贵,而且与今天面临的状况不同,当年很多工厂对生产速度、产量、废物排放、安全性和遵循法规上的需求并不高。
正是因为这样,基于PLC的系统才获得了发展,因为它们能够提供更低的固定资产投资,同时提供的功能也足够用。
但是随着时代的变迁,在全球市场范围DCS系统的价格不断降低,制造企业对其需求也随之上升。
因此,在投建新自动化项目时,很多控制系统工程师、维护经理和工厂经理开始重新审视DCS 和PLC控制系统两者的优劣。
在评价DCS和基于PLC架构的自建分布式控制系统时,需要注意的是:网络性能优良的网络性能始于合理的网络设计,而合理的网络设计依赖于对每一个网络节点的通讯行为和用来承载网络信息的协议的详尽了解。
plc与dcs的区别

plc与dcs的区别
plc与dcs在自动化的角度来说,它的控制模式的区别在哪里?
最佳答案
1、这是两个不同的概念:dcs系统——分散控制系统和plc系统——可编程逻辑控制系统。
2、应用的侧重点不同:dcs追求的是回路控制,而plc 追求的是速度和逻辑。
3、应用的规模:dcs应用于大规模的控制,而plc适合控制比较少量的控制。
4、应用的行业不同:过程工业追求的生产过程的统一控制而采用dcs;产品制造行业适用plc较多。
5、二者对整个系统的功能要求不同:dcs要求完成更多的消息管理、设备诊断、数据传递的方式、关注工厂的结构等等都与plc要求不同,plc紧要求完成少量的逻辑控制和少量的报警管理。
plc是从继电器控制发展起来的,最早多用于逻辑控制,象工厂加工设备的控制等,多开关量的控制。
而dcs是从仪表系统发展起来的,主要用于过程控制,象类似化工行业的控制,多模拟量的检测和控制。
但是随着技术的发展,两者的差别越来越小,硬件上现在基本已趋于同质化了。
但在化工行业和电厂用dcs比较多,钢铁行业用plc较多,plc一样能在庞大的系统。
DCS与PLC的区别与联系

DCS与PLC的区别与联系DCS(分散控制系统)和PLC(可编程逻辑控制器)是在工业自动化领域中常用的控制系统。
它们在设计、功能和应用方面存在一些区别和联系。
本文将探讨DCS与PLC之间的区别与联系,旨在帮助读者更好地理解这两种控制系统。
一、DCS与PLC的定义和概述DCS是一种分层结构的控制系统,它通常由多个分布在不同位置的控制单元组成,这些控制单元可以通过网络进行通信。
每个控制单元都可以独立地执行控制任务,并与其他控制单元共享信息。
DCS广泛用于大型工业过程控制系统,例如发电厂、化工厂和石油炼厂等。
PLC是一种用于自动控制的专用计算机,它可以根据预先编写的程序来控制各种设备和过程。
PLC通常用于小型或中型控制系统,例如自动化生产线、机械设备和建筑物自动化系统等。
虽然DCS和PLC具有不同的定义和概述,但它们都能够实现工业自动化控制的目标,并在不同的应用场景中发挥重要作用。
接下来将详细讨论DCS与PLC的具体区别与联系。
二、DCS与PLC的区别1. 结构与组成DCS的结构更加复杂,由多个控制单元组成,这些单元可以相互通信和共享信息。
每个单元都具有独立的性能和功能,可以实现高度分布式和协作控制。
相比之下,PLC通常是一个单独的设备,它独立执行控制任务。
2. 网络通信DCS的控制单元通过网络进行通信,可以实现异地操作和远程监控。
这使得DCS适用于大型的、分布式的控制系统。
PLC通常通过本地连接进行通信,适用于较小规模的控制系统。
3. 灵活性和可扩展性DCS具有较高的灵活性和可扩展性,可以根据需要灵活地增加或减少控制单元,并实现系统的动态调整。
相比之下,PLC相对独立,扩展性较低。
4. 编程语言和功能DCS通常使用高级编程语言进行控制和编程,具备更为复杂的功能和逻辑。
PLC则使用简化的Ladder Diagram(梯形图)等编程语言,功能相对较简单。
这使得DCS适用于需要更复杂控制逻辑的应用,而PLC则适合于一些简单的控制任务。
- 1、下载文档前请自行甄别文档内容的完整性,平台不提供额外的编辑、内容补充、找答案等附加服务。
- 2、"仅部分预览"的文档,不可在线预览部分如存在完整性等问题,可反馈申请退款(可完整预览的文档不适用该条件!)。
- 3、如文档侵犯您的权益,请联系客服反馈,我们会尽快为您处理(人工客服工作时间:9:00-18:30)。
DCS控制系统与PLC控制区别
1、DCS是一种“分散式控制系统”,而PLC只是一种(可编程控制器)控制“装置”,两者是“系统”与“装
置”的区别。
系统可以实现任何装置的功能与协调,PLC装置只实现本单元所具备的功能。
2、在网络方面,DCS网络是整个系统的中枢神经,和利时公司的MACS系统中的系统网采用的是双冗余的100Mbps的工业以太网,采用的国际标准协议TCP/IP。
它是安全可靠双冗余的高速通讯网络,系统的拓展性与开放性更好。
而PLC因为基本上都为个体工作,其在与别的PLC或上位机进行通讯时,所采用的网络形式基本都是单网结构,网络协议也经常与国际标准不符。
在网络安全上,PLC没有很好的保
护措施。
我们采用电源,CPU,网络双冗余。
3、DCS整体考虑方案,操作员站都具备工程师站功能,站与站之间在运行方案程序下装后是一种紧密联合的关系,任何站、任何功能、任何被控装置间都是相互连锁控制, 协调控制;而单用PLC互相连接构成的系统,其站与站(PLC与PLC)之间的联系则是一种松散连接方式,是做不出协调控制的功能。
4、DCS在整个设计上就留有大量的可扩展性接口,外接系统或扩展系统都十分方便,PLC所搭接的
整个系统完成后,想随意的增加或减少操作员站都是很难实现的。
5、DCS安全性:为保证DCS控制的设备的安全可靠,DCS采用了双冗余的控制单元,当重要控制单元出现故障时,都会有相关的冗余单元实时无扰的切换为工作单元,保证整个系统的安全可靠。
PLC所搭接的系统基本没有冗余的概念,就更谈不上冗余控制策略。
特别是当其某个PLC单元发生故障时,不得不将整个系统停下来,才能进行更换维护并需重新编程。
所以DCS系统要比其安全可靠性上高一个等级。
6、系统软件,对各种工艺控制方案更新是DCS的一项最基本的功能,当某个方案发生变化后,工程师只需要在工程师站上将更改过的方案编译后,执行下装命令就可以了,下装过程是由系统自动完成的,不影响原控制方案运行。
系统各种控制软件与算法可以将工艺要求控制对象控制精度提高。
而对于PLC构成的系统来说,工作量极其庞大,首先需要确定所要编辑更新的是哪个PLC,然后要用与之对应的编译器进行程序编译,最后再用专用的机器(读写器)专门一对一的将程序传送给这个PLC,在系统调试期间,大量增加调试时间和调试成本,而且极其不利于日后的维护。
在控制精度上相差甚远。
这就决定了为什么在大中型控制项目中(500点以上),基本不采用全部由PLC所连接而成的系统的原因。
7、模块:DCS系统所有I/O模块都带有CPU,可以实现对采集及输出信号品质判断与标量变换,故障带电插拔,随机更换。
而PLC模块只是简单电气转换单元,没有智能芯片,故障后相应单元全部瘫痪。
“PLC和DCS控制系统究竟有什么不同”这个问题,我们不得不从PLC和DCS的起源谈起:PLC的发展基于制造业的现场控制需求,DCS大发展基于化工行业的连续过程控制和监控。
从控制需求分类看,控制系统可分成:顺序控制(PLC的基本功能)、过程控制(DCS)、位置控制(CNC)、传动控制(调速或同步),但从发展的角度来看,这几部分控制方式在渐渐融合。
如果非要说出不同来,我认为有如下几
点:
1、面向对象不同:PLC面向一般工控制领域,通用性强。
DCS偏重过程控制,用于化工行业。
2、DCS强调连续过程控制的精度,可实现PID、前馈、串级、多级、模糊、自适应等复杂控制,一
般PLC仅具有PID功能,控制精度不如DCS高。
3、DCS系统具有功能强大的SCAND软件包,具有配方功能,并针对不同行开发了专家软件(化工工艺参数配置和控制算法),比PLC应用方便。
最后需要说的,现代PLC已经能够完成DCS的绝大部分功能,并能做冗余或热备,模块也可以带电插拔。
选用PLC还是DCS关键看你面向的对象是什么。
经
济、可靠、便捷才是最重要的。
DCS和PLC的设计原理区别较大,PLC是由摸仿原继电器控制原理发展起来的,70年代的PLC只
有开关量逻辑控制,首先应用的是汽车制造行业。
它以存储执行逻辑运算、顺序控制、定时、计数和运算等操作的指令;并通过数字输入和输出操作,来控制各类机械或生产过程。
用户编制的控制程序表达了生产过程的工艺要求,并事先存入PLC的用户程序存储器中。
运行时按存储程序的内容逐条执行,以完成工艺流程要求的操作。
PLC的CPU内有指示程序步存储地址的程序计数器,在程序运行过程中,每执行一步该计数器自动加1,程序从起始步(步序号为零)起依次执行到最终步(通常为END指令),然后再返回起始步循环运算。
PLC每完成一次循环操作所需的时间称为一个扫描周期。
不同型号的PLC,循环扫描周期在1微秒到几十微秒之间。
程序计数器这样的循环操作,这是DCS所没有的。
这也是使PLC的冗余不如DCS的原因。
DCS是在运算放大器的基础上得以发展的。
把所有的函数、各过程变量之间的关系都作成功能块(有的DCS系统称为膨化块)。
70年代中期的DCS只有模拟量控制。
如TDC2000系统,一个控制器一秒钟内能完成8个PID回路的运算。
首先应用的是化工行业。
DCS和PLC的表现的主要差别是在开关量的逻辑解算和模拟量的运算上,即使后来两者相互有些渗透,但是还是有区别。
80年代以后,PLC除逻辑运算外,也有一些控制回路用的算法,但要完成一些复杂运算还是比较困难,PLC用梯形图编程,模拟量的运算在编程时不太直观,编程比较麻烦。
但在解算逻辑方面,表现出快速的优点,在微秒量级,解算1K逻辑程序不到1毫秒。
它把所有的输入都当成开关量来处理,16位(也有32位的)为一个模拟量。
而DCS把所有输入都当成模拟量,1位就是开关量。
解算一个逻辑是在几百微秒至几毫秒量级。
对于PLC解算一个PID运算在几十毫秒,这与DCS的运算时间不相上下。
大型PLC使用另外一个CPU 来完成模拟量的运算。
把计算结果送给PLC的控制器。
不同型号的DCS,解算PID所需时间不同,但都在几十毫秒的量级。
如早期的TDC2000系统,1秒钟内完成8个回路的控制运算。
随着芯片技术的发展,解算一个算法的时简在缩短。
解算一个算法所需时间与功能块的安排方式和组态方式有关。
在接地电阻方面,对PLC也许要求不高,但对DCS一定要在几欧姆以下(通常在4欧姆以下)。
模拟量隔离也是非常重要的。
在有爆炸危险的地方,应配置本质安全栅。
相同I/O点数的系统,用PLC比用DCS,其成本要低一些(大约能省40%左右)。
PLC没有专用操作站,它用的软件和硬件都是通用的,所以维护成本比DCS要低很多。
一个PLC的控制器,可以接收几千个I/O点(最多可达8000多个I/O)。
DCS的控制器,只能几百个I/O点(不超过500个I/O)。
如果被控对象主要是设备连锁、回路很少,采用PLC较为合适。
如果主要是模拟量控制、并且函数运算很多,最好采用DCS。
DCS在控制器、I/O板、通讯网络等的冗余方面,一些高级运算、行业的特殊要求方面都要比PLC好的多。
PLC由于采用通用监控软件,在设计企业的管理信息系统方面,要容易一些。