松下PLC步进电机控制例子
松下PLC控制伺服电机应用实例
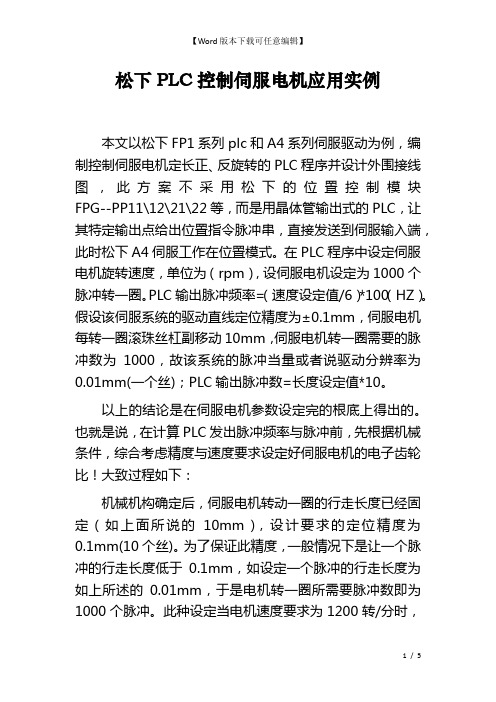
松下PLC控制伺服电机应用实例本文以松下FP1系列plc和A4系列伺服驱动为例,编制控制伺服电机定长正、反旋转的PLC程序并设计外围接线图,此方案不采用松下的位置控制模块FPG--PP11\12\21\22等,而是用晶体管输出式的PLC,让其特定输出点给出位置指令脉冲串,直接发送到伺服输入端,此时松下A4伺服工作在位置模式。
在PLC程序中设定伺服电机旋转速度,单位为(rpm),设伺服电机设定为1000个脉冲转一圈。
PLC输出脉冲频率=(速度设定值/6)*100(HZ)。
假设该伺服系统的驱动直线定位精度为±0.1mm,伺服电机每转一圈滚珠丝杠副移动10mm,伺服电机转一圈需要的脉冲数为1000,故该系统的脉冲当量或者说驱动分辨率为0.01mm(一个丝);PLC输出脉冲数=长度设定值*10。
以上的结论是在伺服电机参数设定完的根底上得出的。
也就是说,在计算PLC发出脉冲频率与脉冲前,先根据机械条件,综合考虑精度与速度要求设定好伺服电机的电子齿轮比!大致过程如下:机械机构确定后,伺服电机转动一圈的行走长度已经固定(如上面所说的10mm),设计要求的定位精度为0.1mm(10个丝)。
为了保证此精度,一般情况下是让一个脉冲的行走长度低于0.1mm,如设定一个脉冲的行走长度为如上所述的0.01mm,于是电机转一圈所需要脉冲数即为1000个脉冲。
此种设定当电机速度要求为1200转/分时,PLC应该发出的脉冲频率为20K。
松下FP1---40T 的PLC 的CPU本体可以发脉冲频率为50KHz,完全可以满足要求。
如果电机转动一圈为100mm,设定一个脉冲行走仍然是0.01mm,电机转一圈所需要脉冲数即为10000个脉冲,电机速度为1200转时所需要脉冲频率就是200K。
PLC的CPU输出点工作频率就不够了。
需要位置控制专用模块等方式。
有了以上频率与脉冲数的算法就只需应用PLC的相应脉冲指令发出脉冲即可实现控制了。
松下PLC位置控制入门
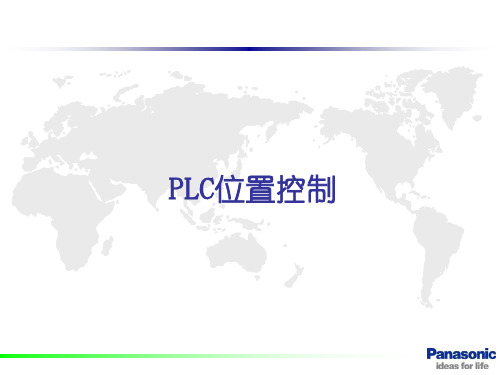
最大输 出频率
相关指令
F0(MV) F1(DMV) F171(SPDH) F172(PLSH) F174(SP0H)
DT90348 Y0 Y1 X4 R911C DT90349 DT90352 Y2 Y3 X5 R911D DT90353 DT90356 Y4 Y5 X6 R911E DT90367 DT90360 Y6 Y7 X7 DT90052 <bit4> R911F DT90361
DT9052的使用说明
DT90052
高速计数器控制标志 →对象PLC:FPΣ
近原点输入有效,紧接着进行预置
DT9052的使用说明
DT90052
高速计数器·脉冲输出控制标志 →对象PLC:FP-X
说明: 1、第一步对计数器进行复位 2、紧接着写入0,使计数器变为可计数状态
程序实例1: 相对值 定位运转(正方向)
FP0
CH0:Y0(Y2方向) 单通道时:40-10kHz CH1:Y1(Y3方向) 双通道时:40-5kHz
无插补功能
PLS+SIGN
CH0:Y0(Y1) CH1:Y2(Y3)
最高100kHz
CH0直线插补: 合成速度100kHz
PLS+SIGN CW/CCW
FPX
CH2:Y4(Y5) CH3:Y6(Y7)
Pulse输出 Sign输出 原点输入 近原点输入
使用的存储区域
控制中标志 过程值区域 目标值区域
最大输 出频率
相关指令
CH0
Y0
Y1
X2
DT90052 <bit2>
DT90044 R903A DT90045
DT90046 DT90047 1CH:100kHz 2CH:60kHz
松下PLC伺服控制案例

松下PLC伺服控制案例
欢迎来到本次松下PLC伺服控制案例分享。接下来,我们将介绍PLC和伺服控 制的基本概念,并展示松下PLC伺服控制的优势和应用案例。
PLC和伺服控制的简介
PLC(可编程逻辑控制器)和伺服控制都是先进的自动化控制技术。PLC用于 逻辑控制和输入/输出管理,而伺服控制用于实现精确的运动控制。
案例2:家庭自动化中的松下 PLC伺服控制
松下PLC伺服控制可将家庭自动化系统整合为一个智能平台,实现智能家居设 备的远程控制和协同运行,提升居住体验。
案例3:交通领域中的松下PLC 伺服控制
松下PLC伺服控制在交通信号控制和交通系统管理中发挥重要作用,确保交通 流畅、安全和高效。
未来的发展和趋势
随着物联网和人工智能的快速发展,松下PLC伺服控制技术将不断创新和演进, 为各个领域提供更多智能化和自动化的解决方案。
总结和要点
• 松下PLC伺服控制提供高性能和稳定可靠的运动控制解决方案。 • 它在工业、家庭和交通领域都有广泛的应用案例。 • 随着技术的发展,松下PLC伺服控制将继续创新和演进。
松下PLC伺服控制的优势
• 高性能和精度,适用于各种运动控制应用。 • 可编程性和可扩展性,方便用户根据需求进行定制和升级。 • 稳定可靠下PLC伺服控制
通过松下PLC伺服控制技术,工业自动化系统可以实现高精度的生产流程控制和协调,提高生产效率并降低人 力成本。
松下PLC伺服控制案例

高速计数 器过程值
加法
减法
DT9052的使用说明
DT9052的使用说明
DT9052
高速计数器控制标志
→对象PLC:FP0,FP-e 可以通过MV指令(F0)写入数值,进行高速计数器的复位、计数禁止、高速计数器 指令(F168)的终止及清除。 CH1用 CH0用
15 14
3 21 0
H0 (0000) H1 (0001) H2 (0010) H4 (0100) H8 (1000) H9 (1001)
DT9052的使用说明
DT90052
高速计数器控制标志
→对象PLC:FPΣ 可以通过MV指令(F0)写入数值,对高速计数器进行复位、计数禁止、高速计 数器指令(F168)的终止及清除。
通道指定
15 14
3 21 0
原点近旁输入 0:OFF 1:ON 高速计数器清除 0:继续 1:清除 硬件复位 0:允许 1:禁止 计数 0:允许 1:禁止 软件复位 0:不复位 1:复位
DT9052的使用说明
DT90052
高速计数器控制标志 →对象PLC:FPΣ
近原点输入有效,紧接着进行预置
DT9052的使用说明
DT90356 DT90358
F174(SP0H)
CH2 Y4
Y5
X6
R911E
中速
DT90367 DT90369 1CH:20kHz F175(SPSH) DT90360 DT90362 2CH:20kHz
CH3 Y6
Y7
X7
R911F
DT90052
DT90361 DT90363
<bit4>
DT90348 DT90350
PLC控制步进电机的实例(图与程序)

态已已
X已
源
个
·
源
X已
意已已已
个个
个
个
·
·
B善
·
B善
-控已已已 个个个 个 个个个 · ·F而状状大 F而状状-
个 ·V大 用ND ·源大 源- B大 B个
善D而V源在
善D而V相在 个
D明引成已
-意已已已在 X已
意已已已
D明引成已
已个
D明引成已
-意已已已在 X引
意已已已
B 意已已已
善
在 D明引成已
个
个 个个个
个 个
P程点
善
在个
个
·
善D而V源在
FX引脉
个
·FX P程点
引已已确画Z
个
·P程脉大 P程脉-
D相而大 D相而-
个
·
善D而V源在如
意态
D明引成已
D明引成已
个
·
X已
源
X引
B
善
在个
·
善
在个
·
个
·
D明引成已
善
在个
·意态
D明引成已
Y已
已已
D明引成已
-意已已已 个
·
源B
X引 善 点
在 D明引成已
PLC控制步进电机的实例(图与程序)
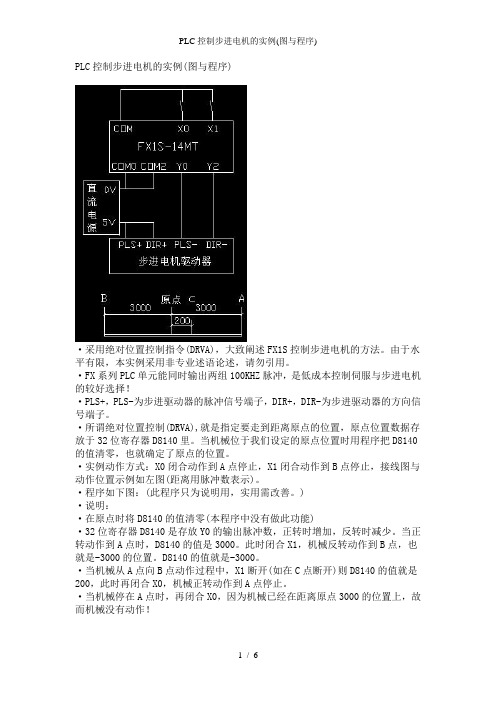
PLC控制步进电机的实例(图与程序)·采用绝对位置控制指令(DRVA),大致阐述FX1S控制步进电机的方法。
由于水平有限,本实例采用非专业述语论述,请勿引用。
·FX系列PLC单元能同时输出两组100KHZ脉冲,是低成本控制伺服与步进电机的较好选择!·PLS+,PLS-为步进驱动器的脉冲信号端子,DIR+,DIR-为步进驱动器的方向信号端子。
·所谓绝对位置控制(DRVA),就是指定要走到距离原点的位置,原点位置数据存放于32位寄存器D8140里。
当机械位于我们设定的原点位置时用程序把D8140的值清零,也就确定了原点的位置。
·实例动作方式:X0闭合动作到A点停止,X1闭合动作到B点停止,接线图与动作位置示例如左图(距离用脉冲数表示)。
·程序如下图:(此程序只为说明用,实用需改善。
)·说明:·在原点时将D8140的值清零(本程序中没有做此功能)·32位寄存器D8140是存放Y0的输出脉冲数,正转时增加,反转时减少。
当正转动作到A点时,D8140的值是3000。
此时闭合X1,机械反转动作到B点,也就是-3000的位置。
D8140的值就是-3000。
·当机械从A点向B点动作过程中,X1断开(如在C点断开)则D8140的值就是200,此时再闭合X0,机械正转动作到A点停止。
·当机械停在A点时,再闭合X0,因为机械已经在距离原点3000的位置上,故而机械没有动作!·把程序中的绝对位置指令(DRVA)换成相对位置指令(DRVI):·当机械在B点时(假设此时D8140的值是-3000)闭合X0,则机械正转3000个脉冲停止,也就是停在了原点。
D8140的值为0·当机械在B点时(假设此时D8140的值是-3000)闭合X1,则机械反转3000个脉冲停止,也就是停在了左边距离B点3000的位置(图中未画出),D8140的值为-6000。
松下PLC步进控制的程序论文
利用PLC与步进电机设计铝镍条切段机摘要:本文着重介绍了PLC(NAIS公司)、步进电极实现位置控制方法,以及通过触摸屏实现参数设定与显示,从而保证切段机实现精确进给。
关键词:PLC 步进电机位置控制触摸屏1.引言铝条、镍条是锂电池制造业中重要的原材料,主要作为电池的正负极。
铝条、镍条成卷供应,实际使用时利用人工切成需要的小段。
使用人工精度差,速度慢。
而且人员工作枯燥。
随着工控技术的不断发展,可编程序控制器的价格比越来越高,步进电极受脉冲控制,位移量取决于脉冲数,而PLC又有脉冲输出、脉冲控制功能,PLC与步进电极很容易实现位置控制功能。
本机将铝镍条的供给用PLC控制步进电机,构成开环控制来实现精确进给。
2.构成采用NAIS公司的FP0 PLC集中控制(内置2轴位置控制功能、高速计数功能等,编程软件采用梯形图),采用TAMAGAWA公司的五相步进电机及步进电机控制器,步进角为0.72度,既每500脉冲/转.另外用NAIS公司GT10触摸屏与PLC通讯,显示、设定有关参数。
图1 为设备的构成原理图。
铝条或镍条经进给轮,移送相应长度后,汽缸动作,带动切刀,将铝条或镍条切成小段。
图2为原理框图3.系统设计因为本系统只有一台步进电机,所以只有1轴位置控制,其中Y0为PLC 位置通道1的脉冲输出端子,Y2为方向控制端子,X0为原点输入端子。
利用速度及位置控制指令F168(SPD1)可以方便的实现步进电机的转速,旋转量等的控制,从而控制铝条或镍条的长度。
并且进给轮连续运行,不须要原点复位及绝对值位置控制。
只要在原来的基础上相对位移多长的距离就可以了。
步进电机与进给轮用1:1驱动。
而步进电机为500脉冲/转。
知铝条卷汽缸进给轮步进电机切刀图1 系统构成道需要步进的距离,及进给轮的半径就可以计算需要多少个脉冲。
本设计中进给轮周长为50mm ,即每个脉冲为0.1mm 。
本设计中对于步进的精度要求不是很高,0.1已经足够。
松下PLC控制伺服电机实例程序
松下PLC控制伺服电机实例程序上位机设定伺服电机旋转速度单位为<转/分),伺服电机设定为1000个脉冲转一圈.PLC输出脉冲频率=< 速度设定值/6)*100<HZ).上位机设定伺服电机行走长度单位为(0.1mm>,伺服电机每转一圈地行走长度10mm,伺服电机转一圈需要地脉冲数为1000, 故PLC发出一个脉冲地行走长度为0.01mm(一个丝>.PLC输出脉冲数=长度设定值*10.上面两点地计算都是在伺服电机参数设定完地基础上得岀地.也就是说,在计算PLC发岀脉冲频率与脉冲前,必须先根据机械条件,综合考虑精度与速度要求设定好伺服电机地电子齿轮比!大致方法如下:机械安装结束,伺服电机转动一圈地行走长度已经固定<如上面所说地10mm ),设计要求地行走精度为0.1mm(10个丝>.为了保证此精度,一般情况下是让一个脉冲地行走长度低于0.1mm,如设定一个脉冲地行走长度为如上所述地0.01mm,于是电机转一圈所需要脉冲数即为1000个脉冲.此种设定当电机速度要求为1200转/分时,PLC应该发出地脉冲频率为20K.松下PLC 地CPU本体可以发脉冲频率为100K,完全可以满足要求.如果电机转动一圈为100mm,设定一个脉冲行走仍然是0.01mm,电机转一圈所需要脉冲数即为10000个脉冲,电机速度为1200转时所需要脉冲频率就是200K.PLC地CPU本体就不够了.需要加大成本,如增加脉冲输出专用模块等方式.知道了频率与脉冲数地算法就简单了,只需应用PLC地相应脉冲指令发出脉冲即可,松下PLC地程序图如下:松下伺服常见问题一、基本接线主电源输入采用〜220V,从L1、L3接入<实际使用应参照操作手册);控制电源输入r、t也可直接接〜220V。
电机接线见操作手册第22、23页,编码器接线见操作手册第24〜26页,切勿接错.二、试机步骤1.JOG试机功能仅按基本接线就可试机;在数码显示为初始状态’r 0 '下,按’SET键,然后连续按’MODE键直至数码显示为’AF-AcL',然后按上、下键至’AF- JoG。
PLC控制步进电动机运行案例
PLC控制步进电动机运行案例PLC(可编程逻辑控制器)是一种用于自动化控制系统的工业电子设备,通过程序控制各种工业设备的运行和逻辑控制。
步进电动机是一种精密控制的电动机,可以根据脉冲信号的输入旋转指定的角度。
本文将介绍如何使用PLC控制步进电动机的运行,并给出一个实际的案例。
1.系统设计:要实现PLC控制步进电动机运行,首先需要设计一个系统,包括PLC 控制器、步进电动机、电源和传感器等。
PLC将通过编程控制步进电动机的旋转方向、速度和位置,从而实现精确的运动控制。
2.PLC编程:在PLC编程软件中,我们首先需要设置输入和输出点,用于连接步进电动机和传感器。
然后编写程序,通过控制输出点发送脉冲信号控制步进电动机的旋转。
例如,我们可以设计一个简单的程序,使步进电动机按照固定的角度旋转,然后停止。
步骤如下:1)设置输入点:连接PLC与步进电动机的控制信号线,用于接收启动和停止信号。
2)设置输出点:连接PLC与步进电动机的脉冲信号线,用于控制步进电动机的旋转方向和速度。
3)编写程序:在PLC编程软件中编写程序,设置脉冲信号的频率和方向,控制步进电动机按照指定的角度旋转。
4)调试程序:在调试模式下测试程序,验证步进电动机是否按照设计的参数正确运行。
3.实际案例:假设我们要控制一个步进电动机旋转180度,然后停止。
以下是一个简单的PLC程序示例:1)设置输入点I0为启动信号,输入点I1为停止信号;2)设置输出点Y0为脉冲信号控制步进电动机的旋转;3)编写程序如下:```LDI0OUTY0DELAY1000OUTY0NOP```4)启动程序后,PLC将检测I0信号,如果为高电平(启动信号),则输出Y0脉冲信号控制步进电动机旋转180度;然后延迟1秒后,停止输出脉冲信号,步进电动机停止旋转。
通过以上案例,我们可以看到如何使用PLC控制步进电动机的运行。
PLC具有灵活的编程功能和稳定的性能,可以实现精确的运动控制和自动化生产。
松下PLC伺服控制案例(PPT文档)
关于控制代码
关于控制代码
关于控制代码
FP-X晶体管输出型
20KHz × 2轴 100KHz × 2轴
FP-X 脉冲输出功能一览表
通道(No.)
使用的输入/输出接点编号
使用的存储区域
CW或Pulse CCW或Sign
输出
输出
原点输入
近原点输入
控制中标志
过程值区域
目标值区域
最大输 出频率
R903A
DT90044 DT90045
DT90046 DT90047
1CH:10kHz
F0(MV) F1(DMV)
CH1
Y1
Y3
X1
DT90052 <bit6>
R903B
DT90048 DT90049
DT90050 DT90051
2CH:5kHz F168(SPD1) F169(PLS)
关于控制代码
最大输 出频率
相关指令
CH0
Y0
Y1
X2
DT90052 <bit2>
R903A
DT90044 DT90045
DT90046
F0(MV)
DT90047 1CH:100kHz F1(DMV)
CH2
Y3
Y4
X5
DT90052 <bit4>
R903C
DT90200 DT90201
DT90202 DT90203
方向输出OFF 脉冲输出
高速计数 器过程值
加法
减法
DT9052的使用说明
DT9052的使用说明
DT9052
高速计数器控制标志
→对象PLC:FP0,FP-e 可以通过MV指令(F0)写入数值,进行高速计数器的复位、计数禁止、高速计数器 指令(F168)的终止及清除。 CH1用 CH0用
- 1、下载文档前请自行甄别文档内容的完整性,平台不提供额外的编辑、内容补充、找答案等附加服务。
- 2、"仅部分预览"的文档,不可在线预览部分如存在完整性等问题,可反馈申请退款(可完整预览的文档不适用该条件!)。
- 3、如文档侵犯您的权益,请联系客服反馈,我们会尽快为您处理(人工客服工作时间:9:00-18:30)。
! ! !
R42 [ ] TMX 3 10
[ F0 MV, H 4, DT9052 [ F0 MV, H 0, DT9052 [ ED ]
] ]
!=uQ=
!"#$
PLC-2
=O
! uM opO uQ opP
fkqbok^qflk^i =====qo^fkfkd
!"
! m_P uR m_N uN
PLC-2
=P
fkqbok^qflk^i =====qo^fkfkd
!"#$ råáíF=
%= Es NF=
= M= J= NMs
!"#$%&'()*= E^å~äçÖ
!"#$%&'
a)
iba
=EsF
sN= =R ON OFF
sN=
=R
OFF ON
b)
iba
=EsF
sN= =Q Q ON OFF OFF
~F=
!"#$%&'()=EbåÅçÇÉêF= =m_N= !"#$%& =uP= ' !"#$=mi`=
!"# ()*+,
m_N uN uP uM opO uQ opP uR m_P ! ! ! !" vM vO vQ
!"#$%&'
!"#$%&'()*+,-./0123 !"#$%&'()*+$%&!,-./
!"#$%&'()*+,-./0123 !"=EuRF= ÄF= !"#$%&'()*+,
!"#$%&'()*+,-. = opN= EuPF !"#$
RS2 PB1 PB2 RS1 RS3 PB3
X0
X1
X2
X3
X4
X5
C
Step Motor Reset NO + +_ _ +
Y0
COM
Y1
NC _ + _
RS2 PB1
+ A B
RS3 PB3
X0
X1
X2
X3
X4
X5
C
Step Motor Reset NO + +_ _ +
Y0
COM
Y1
NC _ +Y2+ Nhomakorabea-
_ +
_
PLC-2
=O=
Y4 (DF R50 R50 (DF R51 [ F0 MV, H 122, DT200 [ F0 MV, K 120, DT201 [ F0 MV, K2500, DT202 [ F0 MV, K 100, DT203 [ F168 SPD1, DT200, H0 R903A (DF R52 Y4 (DF/ ) [ F0 MV, H 8, DT9052 [ F0 MV, H 0, DT9052 ] ] ) TMX 4 R50 T4 ] ] ] ] ] ) R51 [ ] ) R903A R52 R50 [ ]
Y2
+
-
Relay _ +
Driver
PLC-2
=N~=
X1 (DF R10 R10 (DF R11 [ F0 MV, H 102, DT 100 [ F0 MV, K 500, DT 101 [ F0 MV, K5000, DT 102 [ F0 MV, K 200, DT 103 [ F1 DMV, K 2000, DT104 [ F0 MV, K 0, DT106 [ F168 SPD1, DT100, H0 R903A (DF/ R12 R10 ) TMX 0 T0 ] ] ] ] ] ] ] ! ! ! !" ! R12 [ ] 10 ) R11 [ ] ) R903A R12 R10 [ ]
fkqbok^qflk^i =====qo^fkfkd
!
! ! !
R52 [ ] 10
!=uP=
!"#$%&'(
X5 (DF R40 R40 (DF R41 ) )
R903A
R42
R40 [ ]
R41 [ ] ] ] ] ] ]
[ F0 MV, H 123, DT200 [ F0 MV, K 100, DT201 [ F0 MV, K2000, DT202 [ F0 MV, K 150, DT203 [ F168 SPD1, DT200, H0 R903A (DF/ R42 X4 (DF X1 (DF R100 R100 (DF R101 ) ) ) R903C R52 ) R40 T3
! ! ! R42 [ ] 10
TMX 3 ) [ F0 MV, H 4, DT9052 [ F0 MV, H 0, DT9052
] ] [ ED ]
!=uQ=
!"#$
PLC-2
=NÄ=
fkqbok^qflk^i =====qo^fkfkd
X1 (DF R50 R50 (DF R51 ) )
! ! ! !" ! R22 [ ] 10
TMX 1
X5 (DF R40 R40 (DF R41 ) )
R903A
R42
R40 [ ]
R41 [ ] ] ] ] ] ]
[ F0 MV, H 123, DT 200 [ F0 MV, K 100, DT 201 [ F0 MV, K2000, DT 202 [ F0 MV, K 150, DT 203 [ F168 SPD1, DT200, H0 R903A (DF/ R42 X4 (DF R40 ) T3
R903A
R52
R50 [ ]
!
R51 [ ] ] ] ] ] ]
[ F0 MV, H 122, DT200 [ F0 MV, K 120, DT201 [ F0 MV, K2500, DT202 [ F0 MV, K 100, DT203 [ F168 SPD1, DT200, H0 R903A (DF R52 X3 (DF ) R50 T4
! ! !
R52 [ ] TMX 4 10
) [ F0 MV, H 8, DT 9052 [ F0 MV, H 0, DT9052
] ]
!=uP=
!"#$%&'(
X5 (DF R40 R40 (DF R41 ) )
R903A
R42
R40 [ ]
R41 [ ] ] ] ] ] ]
[ F0 MV, H 123, DT200 [ F0 MV, K 100, DT201 [ F0 MV, K2000, DT202 [ F0 MV, K 150, DT203 [ F168 SPD1, DT200, H0 R903A (DF/ R42 X4 (DF ) R52 ) R40 T3
! ! !
R42 [ ] TMX 3 10
[ F0 MV, H 4, DT9052 [ F0 MV, H 0, DT9052 R102
] ] R100 [ ]
!=uQ=
!"#$
R101 [ ]
[ F1 DMV, K 0, DT9104 ] [ F167 HC1R, K 2, K 500, Y4 ] R101 R903C (DF/ R102 ) TMX 0 R100 T0 Y4 <S> R102 [ ] K 5 [ ED ]
fkqbok^qflk^i =====qo^fkfkd
!
X2 (DF R20 R20 (DF R21 ) )
R903A
R22
R20 [ ]
!
R21 [ ] ] ] ] ] ] ] ]
[ F0 MV, H 103, DT 100 [ F0 MV, K 500, DT 101 [ F0 MV, K5000, DT 102 [ F0 MV, K 200, DT 103 [ F1 DMV, K 2000, DT104 [ F0 MV, K 0, DT106 [ F168 SPD1, DT100, H0 R903A (DF/ R22 R20 ) T1
sN OFF ON OFF
=R sN
=U
OFF OFF ON
MODE
OFF
ON +
Y20 Y21 Y22
IN
Vo Io COM V1 I1 V I COM
-
OUT COM
PLC-2
=P~=
R9010 [ F0 MV, WX4, DT100 ]
> DT100, 1000 ] [< > DT100, 1000 ] [<
fkqbok^qflk^i =====qo^fkfkd
[ Y20 ] [ Y21 ] [ED]
=PÄ=
R9010 [ F62 WIN, WX4, K800, K1600 ] R900A [ Y22 ] R900B [ Y21 ] R900C [ Y20 ] [ED]
PLC-2
=N
! uM opO uQ opP uP opN
fkqbok^qflk^i =====qo^fkfkd
! m_P uR m_N uN m_O uO
~F=
!"#$%&'()=m_N=EuNF= !"#$%&'()*+)=m_O=EuOF=
!"#
m_N m_O uN uO uP opN uM opO uQ opP uR m_P ! ! vM vO