膜分离法回收合成氨放空气中氢气技术
合成氨的工艺流程
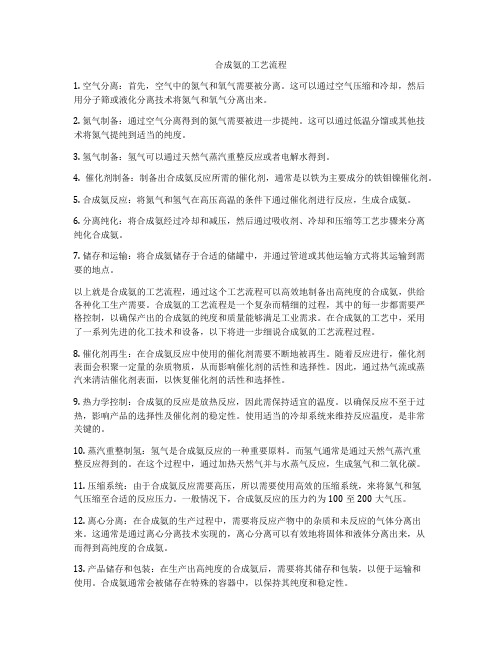
合成氨的工艺流程1. 空气分离:首先,空气中的氮气和氧气需要被分离。
这可以通过空气压缩和冷却,然后用分子筛或液化分离技术将氮气和氧气分离出来。
2. 氮气制备:通过空气分离得到的氮气需要被进一步提纯。
这可以通过低温分馏或其他技术将氮气提纯到适当的纯度。
3. 氢气制备:氢气可以通过天然气蒸汽重整反应或者电解水得到。
4. 催化剂制备:制备出合成氨反应所需的催化剂,通常是以铁为主要成分的铁钼镍催化剂。
5. 合成氨反应:将氮气和氢气在高压高温的条件下通过催化剂进行反应,生成合成氨。
6. 分离纯化:将合成氨经过冷却和减压,然后通过吸收剂、冷却和压缩等工艺步骤来分离纯化合成氨。
7. 储存和运输:将合成氨储存于合适的储罐中,并通过管道或其他运输方式将其运输到需要的地点。
以上就是合成氨的工艺流程,通过这个工艺流程可以高效地制备出高纯度的合成氨,供给各种化工生产需要。
合成氨的工艺流程是一个复杂而精细的过程,其中的每一步都需要严格控制,以确保产出的合成氨的纯度和质量能够满足工业需求。
在合成氨的工艺中,采用了一系列先进的化工技术和设备,以下将进一步细说合成氨的工艺流程过程。
8. 催化剂再生:在合成氨反应中使用的催化剂需要不断地被再生。
随着反应进行,催化剂表面会积聚一定量的杂质物质,从而影响催化剂的活性和选择性。
因此,通过热气流或蒸汽来清洁催化剂表面,以恢复催化剂的活性和选择性。
9. 热力学控制:合成氨的反应是放热反应,因此需保持适宜的温度。
以确保反应不至于过热,影响产品的选择性及催化剂的稳定性。
使用适当的冷却系统来维持反应温度,是非常关键的。
10. 蒸汽重整制氢:氢气是合成氨反应的一种重要原料。
而氢气通常是通过天然气蒸汽重整反应得到的。
在这个过程中,通过加热天然气并与水蒸气反应,生成氢气和二氧化碳。
11. 压缩系统:由于合成氨反应需要高压,所以需要使用高效的压缩系统,来将氮气和氢气压缩至合适的反应压力。
一般情况下,合成氨反应的压力约为100至200大气压。
膜分离法回收合成氨弛放气探讨

膜分离法回收合成氨弛放气探讨摘要:现代市场经济,经济效益是首要关注的问题,本文就以分析膜分离法回收合成氨的气体的主要设备、设备特点、装置特点及工艺流程,为社会带来更大的经济效益。
关键词:驰放气合成氨膜分离回收氢分析设置本装置的目的,是将氨合成岗位的弛放气经过脱盐水洗涤氨、预热和预放空等处理后,通过普里森膜分离装置分离出含H290%的渗透气送往氢氮气/循环气联合压缩机回收利用,产生的尾气(非渗透气)送加热炉作燃料气。
以下对该装置进行分析。
一、相关工艺流程和设备1.主要工艺流程氢回收的工艺流程可以分为两个基本过程,一是放空气的预处理过程,二是原料气的膜分离过程。
放空气的预处理包括高压水洗、预热及预放空,由合成系统送来的高压弛放气经调节阀减压至11.0MPa进入水洗塔。
由高压水泵送来的软水由塔顶喷淋净化气体。
水洗后的气体(原料气)经预热至40~50℃(高出露点5~10℃),然后送膜分离组进行氢分离回收。
高压水洗的目的是将弛放气中的氨进行回收,同时还要保证水洗后原料气中的氨含量必须低于5ppm才允许进入膜分离器(正常操作条件下,水洗后原料气的氨含量为5ppm)。
为防止原料气中的饱和状态的水凝结,水洗后的原料气必须进行预热处理。
原料气的预放空是膜装置在开车过程中的必要步骤,通过放空阀将原料气放空一段时间,经采样分析确认氨含量低于5ppm及温度达到40—50℃时方可允许原料气进入膜分离器中。
每个膜分离器可被看成外型类似管壳式热交换器,膜分离器壳体由纤维来填充,类似于管束。
原料气从下端侧面进入膜分离器,在壳程与纤维芯侧恒定压差作用下,氢气扩散进入纤维。
在原料气沿膜分离器长度方向流动时,更多的氢气扩散进入纤维,从而在纤维芯侧得到富氢产品称为渗透气;在壳程得到富含惰性气体的物流称为非渗透气。
来自液氨分离器的弛放气,温度11℃、压力14.3MPa,经压力调节阀控制弛放气压力为11MPa后从弛放气洗涤塔下部进入从下向上流动;来自脱盐水总管的脱盐水用阀门控制脱盐水液位再用高压洗氨泵柱塞泵增压后,从洗涤塔上部进入,从上向下流动,与从下向上流动的弛放气体在填料层中逆向接触,弛放气中的气氨被脱盐水洗涤吸收至氨含量≤5ppm从塔顶离开;吸氨后的脱盐水变为浓度15—17%的稀氨水,下降至塔底部,然后经液位调节阀调节液位后去氨蒸馏系统。
合成氨弛放气、排放气的氢气回收技术

主 要 利 用 吸 附 剂 对 不 同气 体 的 吸 附 容 量 随 压 力 的不 同 而 差 异 的特 性 , 吸 附 剂 选 择 吸 附 的条 件 下 , 在
氢 气 和燃 料气 , 者 返 回合 成 氨原 料 气 系统 , 者 作 前 后
燃 料用 。
1 2 变 压 吸 附 技 术 .
目 前 变 压 吸 附 技 术 发 展 较 快 , 附 工 艺 主 要 有 吸
三 塔 一 均 , 塔 二 均 , 塔 二 均 , 塔 二 均 , 塔 二 四 五 六 八
在 合 成 氨 生 产 过 程 中 , 提 高 氨 的 合 成 率 , 成 为 合 塔 中有 一 部 分 惰 性 气 需 放 空 , 为 排 放 气 ; 氨 中 间 称 从
罐 释放 出来 的 气 体 称 为 弛 放 气 。这 两 部 分 气 体 的组
成 见 表 l 。
表 1 弛放 气 、 放气 组 成 ( ) 排 %
均 , 塔 三 均 等 技 术 。针 对 合 成 氨 排 放 气 和 弛 放 气 八
I 排 放 气 和 弛 放 气 的氢 气 回 收 技 术
1 1 膜 分 离技 术 .
的氢 气 回 收 , 文 简 要 介 绍 四 塔 二 均 工 艺 。 本 1 2 1 工 作 原 理 . .
又 称 普 里 森 分 离 器 氢 回 收 技 术 , 技 术 主 要 依 该 靠 普 里 森 分 离 器 来 分 离 氢 气 。普 里 森 分 离 器 外 形 与 管 壳 式 换 热 器 相 似 , 里 面 是 中 空 纤 维 管 。 气 体 进 但
合成氨厂膜分离氢回收装置运行问题及改造

第 4期
李
坤 等 :合 成氨 厂膜 分 离氢回收 装置运 行 问题 及 改造
・ 7・ 2
少 ,由最 后一 台分离 器 的尾部 调 节 阀 HV 32减 70
压 至 07M a 出 。 . P 排
期 处于 带氨 的边缘 ,对膜 分离器 有较 大的损 伤 。
( ) 蒸汽加 热器 起不 到加热 的作用 3 由于放空 气流量 长时 间在较 大状 态 ,氨含量 又较 高 ,导致洗 氨塔 的温度 较高 ,洗氨 塔 出 口气 体 温度较 高 ,未 经蒸 汽加 热器加 热其温 度就 已经
厂 20 0 8年采用 中 国科 学 院 大 连化 学 研究 所 研 究
来器
为套 管式 加热器 ,热 源为 13MP . a饱和蒸 汽 。原
开发 的 中空纤 维膜 气体 分离技术 建设 了氢 回收装 置 。现将该装 置运 行过 程 中出现 的问题 及采 取 的 相应措 施作一 介绍 。
达 到人膜 指标 ,工艺 气没 有 了再 加热 的空 间 ,工
2 运行 中 出现 的 问题 及原 因分析
合成 2 和合成 3 ,其操作压力分别是 3 P 、 0 0M a 3
MP 和 1 a a 5MP 。氨 合 成 放 空气 由 H 、N 、N 3 2 H 和C H 组成 ,其 中 H 含 量高 达 5 % 以上 。为 了 0 对合成 氨放 空气 中的 H 回收 再利 用 ,提 高原 料 气 的转 化率 ,进一 步降低 合成 氨 的生 产成本 ,我
甲醇 洗 工 序 。此 问 题 准 备通 过 增 加 1套 汽提 装 置 ,将冷凝 水汽 提后再 使用来 解决 。
汽 ,降低能耗。但 由于低水气 比耐硫 C O变换工 艺是初次用于壳牌粉煤气化制气,不可避免地会
膜分离提氢运用

膜分离提氢在楚星公司的运用公司老合成氨系统生产能力为12万吨/年,合成氨成放空气经过简单的洗氨后,送吹风气锅炉炉作燃料,在以煤为原料生产合成氨的工艺中,原料气中所含有的少量甲烷和氩、不参与合成反应。
随着合成的进行、这些气体逐渐积累,不断减少了入塔循环气中有效气体的比例,以致合成率下降,反应压力升高。
为了保证生产能连续进行,通常要排放一部分循环气,以利于降低循环气中的甲烷含量。
但在排放甲烷的同时,会有大量有用的氢气随同排出。
放空气中的氢气含量高达57-62 ﹪。
而氢气的热值仅有相同体积的甲烷热值的三分之一,将氢气烧掉是一个很不经济的做法。
在合成氨生产中,氢气是宝贵的原料气体,要耗费相当多的能量和复杂的工艺才能制得。
合理地、经济地回收利合成氨放空气中的氢气是合成氨生产中的一项重大的节能课题。
合成氨厂放空气回收氢气的方法、主要有深冷法、变压吸附法和中空纤维膜分离法三种、由于分离工艺不同,它们各具特点,我们对三种方法的投资、收率、收益分析对比,选择了氢回收率高、投资省、运行费用低、操作管理简单的膜分离法。
1、膜分离的过程原理膜分离器是装置的核心,它的芯部由数以万计的中空纤维管组成。
气体接触到中空纤维膜时便进行渗透、溶解、扩散、解析过程,所有气体对高分子膜都是可以渗透的,但由于各种气体分子的半径不同,它们的渗透能力各不相同。
在压力的作用下,让合成放空气通向高分子膜, H2能较快的通过,而N2、CH4等气体则要比H2慢得多,结果膜的低压侧H2浓度不断提高,而大部分N2和 CH4则被滞留在离子膜的高压侧,从而达到分离氢气的目的。
2、工艺流程2、1工艺流程简介H2的回收工艺分两个过程,即放空气的预处理和膜分离合成排出的放空气经减压到 10MPa左右、进人到水洗塔的下部与高压水泵送来的软水逆流接触,去除气体中的残留氨。
除氨后的气体经气水分离器、预热器,并通过自调阀门进入膜分离器析氢。
回收的浓缩的H2送入氢氮压缩机五段进口,重新返生产系统。
膜分离氢回收装置在CCR法合成氨双系统中的应用

6 00 ) 130
中解决 了存在的问题。经半年多的生产运行表 明, 该装置操作筒捷 、 稳. 平 各参数都达到设计指标 , 对 大系统的平衡没有造成影响, 在提高氨产量和降低
消 耗 上都 收 到 很好 的 效 果 。 1 工艺流程
铵) 采用 天然气间 歇转化 ( C , C R法 )高 压合 成工 、
为此 , 我们将 A点压力远传至操作室 , 先将I 系
空, 并且较高压力 系统的放空 气窜人较 低压 力系 统, 直至两者压力平衡 , 2个系统 根据 自身压 力高
低和 阻力大小 自动按 比例 放空, 人为无法调节 , 影
响 了 2个 合 成 系 统各 自的 正 常操 作
三出总管 , 使渗透 气与绝大部 分系统气 在脱碳 系 统充分混合 , 2 合成 系统补充 气成分趋于一 使 个
致; 转化 系统 再根据需要 充分调节 但 这样无疑 加重 了脱碳的 负荷, 增加 了无谓 的消耗。 因此我 们决定在渗透气总管 上并联一条 管线 , 四进总 去 管的另一端 , 用阀 门控制 , 并根据循环 气氢氮比调 节分送 2 合成系 统 实际生产 中 , 方法操 作 个 该
灵活 、 效, 果不错: 有 效 2 4 氨 水 的 消 化 . 由 于 我 公 司主 产 尿 素 , 铵 产 量 低 ( 6 碳 约 ol /
艺 , 系 统 并 联 , 用 氢 氮 气 压 缩 机 ( M8型 和 双 共 4 6 D2 )流 程 较 长 , M 0型 , 系统 分散 长 期 以来 合 成 系 统 放 空 气 与 氨 罐弛 放 气 汇合 , 过 水 洗 塔 洗 氨 后 送 通 转 化 系 统 作燃 料 , 水洗 塔 氨 水送 至 碳 化 系 统 生 产 碳 铵 , 空 气 中 H 的 利 用率 低 , 耗 高 。 由 于 尿 素 的 放 2 消 改 造 和 完善 , 素 产 量 不 断 提 高 , 统 氨 碳 平衡 困 尿 系 难 , 年 拉 库 存 液 氨 约 1 , 制 了 尿 素 的 生 产 。 每 2 t限 为了 提 高 氨 产 量 、 衡 尿 素 生 产 用 氨 ,0 1年 初 我 平 20 公 司 建 设 r由 大连 化物 所 研 究 开 发 的 膜 分 离 氢 回 收装置 投 入 运 行 , 收 合 成 放 空 气 的 。该 装 置 回 由大 连 化物 所提 供膜 管 和 工 艺 流 程 以及 设 备 施 工 图纸 , 司 固 地 制 宜 地 进 行 配 管 及 其 配 套 设 计 , 公 由
二级膜法从合成氨弛放气提取高浓度氢在双氧水生产上的应用开发

为生 产 出 符合双氧水生产需要的原料氢气 ,我们对生产高纯氢气的变压吸附法和二级 中空纤维膜法进行比较,两种方法的特点如下:
变压 吸 附 法是利用吸附剂对各种气体有不同的吸附容量,而吸附容量又随压力的不同 而有差异的特性,在加压下经选择性吸附除去杂质组分,在减压下脱除这些杂质而使吸附 剂得到再生。该法具有设备简单,动力设备少,产品纯度高等优点,但存在着氢收率低,国 产分子筛吸附剂易粉碎的缺点。
6.7 .8 .一 级 1# ,2 #, 3 # 膜 分离 器 ;9 .加 热 器 ;1 0 二级 4 #膜分离器。
四、试车
改造 后 的 氢气回收装置于 1990年 10月15日进行试车,首先开高压水泵向水洗塔加水 到 1/2液位,并将液位自调投入运行,然后打开充压阀向水洗系统充压至 1OMMa,开启人水 洗塔压力自调 ,用自动放空控制水洗系统压力在 11---12MMa,打开原料气加热器 ,待原料气
二、改造的目的
199 0年 , 我厂新上的葱酿法双氧水生产线建成,由黎明化工研究院设计的这套生产装
置对原料氢气提出了如下要求 :
1.纯 度 : >98% (体积%)
6,一氧化碳含量:毛loppm
2. 氨 含 量 :镇1.6% 7 .二 氧 化 碳 含 量 : 簇 5PPm
0
1 D6 4.68 1.% 4.5 2.26 3.45 2.4 6.9
0 1.05 4.5 1.8 5.7 24
J总回收 率(%)
91 91.5
鬓
表 2 二级膜分离装置运行结果
溉 气体名称 }流a}H;{ NZ {一(NM=/h):--( })_{ (%)
原料 气
96 0 ; 63_76 23.29
3. 甲 烷 含量 :<2.0% 8 .总 硫 量 : < O. 1P Pm
合成氨生产工艺流程
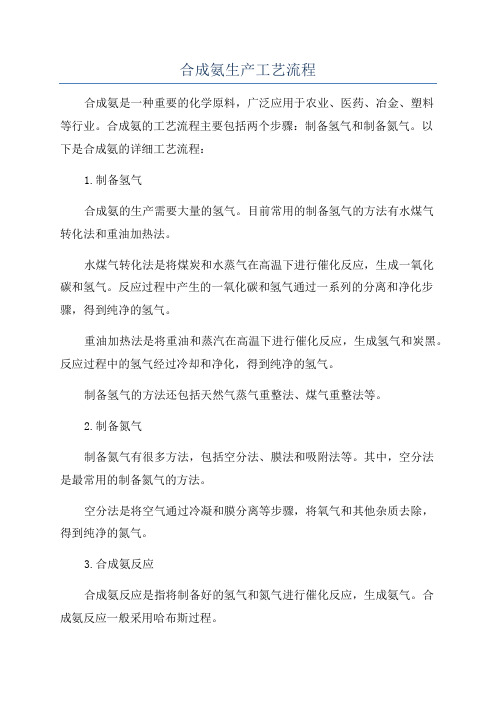
合成氨生产工艺流程合成氨是一种重要的化学原料,广泛应用于农业、医药、冶金、塑料等行业。
合成氨的工艺流程主要包括两个步骤:制备氢气和制备氮气。
以下是合成氨的详细工艺流程:1.制备氢气合成氨的生产需要大量的氢气。
目前常用的制备氢气的方法有水煤气转化法和重油加热法。
水煤气转化法是将煤炭和水蒸气在高温下进行催化反应,生成一氧化碳和氢气。
反应过程中产生的一氧化碳和氢气通过一系列的分离和净化步骤,得到纯净的氢气。
重油加热法是将重油和蒸汽在高温下进行催化反应,生成氢气和炭黑。
反应过程中的氢气经过冷却和净化,得到纯净的氢气。
制备氢气的方法还包括天然气蒸气重整法、煤气重整法等。
2.制备氮气制备氮气有很多方法,包括空分法、膜法和吸附法等。
其中,空分法是最常用的制备氮气的方法。
空分法是将空气通过冷凝和膜分离等步骤,将氧气和其他杂质去除,得到纯净的氮气。
3.合成氨反应合成氨反应是指将制备好的氢气和氮气进行催化反应,生成氨气。
合成氨反应一般采用哈布斯过程。
哈布斯过程是将氢气和氮气通过铁催化剂进行反应,在高温和高压下,生成氨气。
反应过程中,氮气和氢气经过多级催化剂反应器,进行一系列的反应和净化步骤,得到高浓度的氨气。
为了提高合成氨的产量和效率,可以采用以下措施:1.优化催化剂:改进催化剂的配方和制备工艺,提高催化剂的活性和稳定性。
2.调整反应条件:通过调整反应温度、压力和气体流量等参数,优化反应条件,提高反应效率。
3.循环气体:将反应后的气体进行回收和再利用,减少气体的浪费,提高氨气的产量。
4.节能减排:采用节能的加热和冷却设备,减少能量的消耗和二氧化碳的排放。
5.安全措施:建立完善的安全管理系统,确保生产过程中的安全。
总之,合成氨的生产工艺流程包括制备氢气和制备氮气两个步骤,通过优化反应条件和提高催化剂的活性,可以提高合成氨的产量和效率,从而满足农业、医药、冶金等行业对氨气的需求。
- 1、下载文档前请自行甄别文档内容的完整性,平台不提供额外的编辑、内容补充、找答案等附加服务。
- 2、"仅部分预览"的文档,不可在线预览部分如存在完整性等问题,可反馈申请退款(可完整预览的文档不适用该条件!)。
- 3、如文档侵犯您的权益,请联系客服反馈,我们会尽快为您处理(人工客服工作时间:9:00-18:30)。
科技简讯
循环氢气分析误差原因浅析
山西永济中浓化工有限公司合成岗位的氢气
含量使用QF1904型奥氏气体分析仪所分析出的数值比RD -004A 型氢气表上所显示的数值高,并且氢气含量越高误差越大。
经过两年的分析观察,笔者认为是由以下两方面原因引起的。
(1)量气管上端0刻度线至梳形管三通活塞间的容积的影响。
量气管上端0刻度线至梳形管三通活塞间的容积对吸收法干扰较小,但对爆炸法的影响比较大。
例如,某试样由含H 299%(体积分数)的H 2和N 2组成,若取20mL 样气:80mL 空气通电爆炸,假设此容积为1mL,则在分析过程中就多1mL 样气爆炸,由反应式知道1mL 样气的缩减体积为1.5mL,根据缩减体积算出1mL 的H 2在试样中的体积分数为5%。
通过计算知道,在测定含H 299%(体积分数)的样气时,量气管上端0刻度线至梳形管三通活塞间的容积每毫升可使分析结果偏高5%。
经校正,从量气管上端0刻度线至梳形管三通活塞间的体积校正系数为0.6,如果测定含H 265%(体积分数)的样气,0.6mL 的H 2在试样中的体积分数为2%,通过计算可知,分析出的结果偏高2%;
(2)合成循环气中NH 3含量的影响。
因为样气必须首先除NH 3后方可作H 2的测定,这样测出的是除NH 3后的余气中H 2的含量,应该将无氨基换算成有氨基,由于合成循环气进口NH 3≤3%(体积分数),如果测定的样气中H 2体积分数65%,则实际的H 2体积分数为63%。
所以,当H 2体积分数在55%~65%之间时,分析的结果比实际数据高2%。
综上所述,用奥氏仪分析出的结果总比氢气表上所显示数据高3%~4%,这就是氢气表显示的数值与分析工分析数据不相符的原因。
(山西永济中农化工有限公司
044500 曹海云)
膜分离法回收合成氨放空气中氢气技术
青岛昌华集团股份有限公司现年产200kt 总
氨、160kt 尿素、60kt 甲醇以及碳铵、液氨等产品,合成氨系统配有两套合成装置。
对合成放空气的处理是净氨后部分送吹风气燃烧炉直接烧掉,部分用作城市生活煤气。
为了经济合理地回收和利用合成放空气中的氢气,通过市场调研,选择了膜分离法回收放空气中的氢气技术。
1 膜分离回收氢气工艺及主要设备
(1)工艺流程。
来自合成系统的放空气,其压力(表压)为30.0MPa,放空气先经薄膜调节阀减压至8.0~11.2MPa 左右,然后进入洗氨塔,气体在洗氨塔中与高压水泵打进的脱盐水在填料层中逆流接触,气相中的氨被水吸收后变成氨水,由塔底排出,经水洗后的气体中氨体积分数小于200×10
-6
,由塔顶排出后进入气液分离器,分离
水洗过程中夹带的雾沫,经套管式换热器加热到35~45℃,使原料气中的水含量远离饱和点,防止原料气进入膜分离器后产生水雾,影响分离效果,加热后的原料气送入膜分离器,靠中空纤维膜内、外两侧分压差为推动力,通过渗透、溶解、扩散、解吸等步骤而实现分离,使中空纤维膜内侧形成富氢气流,而外侧形成了惰性气流,90%以上氢气被分离出来经压缩重返合成系统,剩余尾气经尾部薄膜调节阀减压到0.8MPa 送余热回收系统中的燃烧炉燃烧,副产蒸汽。
(2)主要设备。
高压水泵的型号为3DP I 21.38/16,水泵的额定压力为16MPa,额定流量为1.38m 3
/h;脱盐水贮槽为 1000mm ×1400mm
圆柱形脱盐水贮存槽;洗氨塔为一填料塔,塔内填充16mm ×16mm ×0.6mm 不锈钢鲍尔环填料,填料层高度约2600mm ,脱盐水由塔上方输入,从塔顶排出进入气液分离器。
氨水液位经高压液位计自动控制,设有液位上限报警。
操作压力为8.0~11.2MPa,放空气进塔温度为30~35℃;气液分离器用来分离原料气从洗氨塔内夹带出的雾
沫,液体从气液分离器的底部定时手动排放。
分离后的气体从顶部排出后进入加热器;加热器为套管式换热器,加热介质为1.0MPa饱和蒸汽,原料气走管程,蒸汽走壳程,原料气被加热到35~45℃,温度通过薄膜调节蒸汽量控制;中空纤维膜分离器组采用了1根 200mm×3000mm和3根 100mm×3000mm膜分离器组成,4根膜分离器为串接,每根膜分离器的渗透气为并联连接。
2 膜分离回收放空气中氢气的技术指标
中空纤维膜分离装置适用于合成氨装置放空气中回收氢气,并可提高合成氨产量2%以上。
工艺条件为:放空气气量为1300~2000m3/h (标态),放空气压力为26~30MPa,放空气温度为25℃,软水温度<30℃。
放空气组成(体积分数)如下:H
2
57.20%,N219.07%,CH411.34%, NH37.05%,A r5.34%。
经膜分离后,渗透气中氢气含量≥85%(体积分数),氢气回收率≥85%。
膜分离回收氢气技术各项技术指标(按处理放空气气量2000m3/h计)见表1。
由表1看出,系统本身消耗较低。
表1 各项技术消耗指标
名称消耗单价/元成本/元
电 7.2k W・h0.33 2.37
软水 1.0t0.800.80
蒸汽0.16t90.0014.40
3 经济效益分析
本装置总投资116万元,投运后取得了明显的节能增产经济效益。
(1)增产氨量。
按现平均放气量1400m3/h (标态),渗透气量800.8m3/h(标态),渗透气含H2体积分数85%,生产1t合成氨需要氢气量为1976.47m3(标态),以年生产天数310d计,1年回收的氢可增产氨量为2559.36t。
(2)净氨效率高。
放空气中氨能全部回收利用。
在未建提氢装置前,放空气中的氨回收率较低,每天回收的氨水折氨1.0t左右。
提氢装置投运后,由于采用高压泵,一次性吸收氨,净氨率几乎接近100%。
按每小时产100tt氨水1.38m3计算,则每年可多回收氨水10267.2m3。
由于回收的是无硫的、且浓度较高的氨水,全部可用于吸氨制浓氨水或送尿素水解系统制成液氨。
(3)节能效果。
提氢装置投运后,合成压力下降了4~5MPa,使循环机的功率明显降低。
装置投运前,循环机日平均功耗为27049k W・h;装置投运后,日平均功耗为20862k W・h,日节电6187k W・h,按日产氨390t计算,则吨氨循环机节电15.86k W・h。
加上压缩机功耗也有所下降,则吨氨总节电量高于20k W・h。
按年产140kt合成氨计算,年节电量2.8×106k W・h,而本装置自身年用电量约49600k W・h,则年净节电量可达2750400k W・h,按0.30元/(k W・h)计算,年实际节电费82.512万元。
(山东青岛昌华集团股份有限公司
莱西266600 葛方晋)
K DON214000/1500型全低压空分装置投运情况
山西丰喜肥业集团临猗分公司2005年12月新建1套K DON214000/1500型全低压大型空分装置。
该空分装置采用了全低压、透平膨胀、氮水预冷、分子筛吸附、内压缩(液氧泵)工艺流程。
空压机和增压机为“一拖二”形式,即由1台双出轴汽轮机分别驱动空压机和增压机。
空分装置设计规模为14000m3/h(最大14700m3/h,标态)产氧装置,氧气纯度为99.6%(体积分数),压力为6.5MPa。
该装置为100kt/a甲醇装置的配套装置,于2005年12月投产,一次开车成功运行, 1年来生产很稳定。
本空分设备采用分子筛吸附预净化,增压透平膨胀机,下塔筛板塔、上塔填料塔精馏及液氧内压缩工艺。
整套机组包括:空分过滤系统、空气压缩系统、空分预冷系统、分子筛纯化系统、分馏塔系统、液氮贮存冷化系统、液氧贮存、气化系统、仪控系统、电控系统等。
空压机的动力是由背压式蒸汽透平机驱动,进口气体4.90MPa(表压)、温度470℃,背压汽压1.27MPa(表压),送入低压蒸汽管网。
(1)空气过滤和压缩。
空气首先进入自洁式空气过滤器,正常流量为120000m3/h(标态),在空气过滤器中除去灰尘和其它颗粒杂质,然后进入空气压缩机,经过多级压缩压力达0.61MPa。