MPS计划表
第6讲MPS(2015)
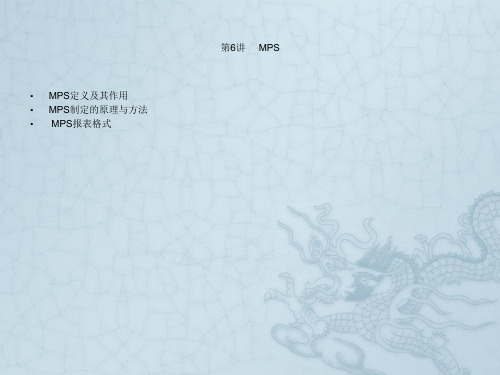
毛需求 计划接收量 库存量 (前) 库存量 (后) 净需求 计划产出量 计划投入量
当 12 3 4 5 6 7 8 期 2/03 2/10 2/17 2/24 3/03 3/10 3/17 3/2
10
10
20
10
10
10
20
10
20
20
20
20
20
20
10
10
20
当期预计可用库存量=现有库存量-已分配量 第3步 推算PAB初值。考虑毛需求推算特定时段的预计库存量。
PAB初值=上期末预计可用库存量+计划接收量-毛需求量 第4步 推算净需求。考虑安全库存推算特定时段的净需求。
当PAB初值≥安全库存,净需求=0 当PAB初值<安全库存,净需求=安全库存-PAB初值 第5步 推算计划产出量。考虑批量推算特定时段的计划产出量。 当净需求>0,计划产出量=N ×批量 满足:计划产出量≥净需求>(N-1)×批量 第6步 推算预计可用库存量。推算特定时段的预计库存量。 预计可用库存量=计划产出量+PAB初值 第7步 递增一个时段,分别重复进行第3到第6步,循环计算至计划期终止。 第8步 推算计划投入量。考虑提前期推算计划期全部的计划投入量。 第9步 推算可供销售量。在有计划产出量时往后倒推到上一个计划产出量位置进行计算。
100
合同订货量
300
200
250
200
250
200
150
100
100
方式1:毛需求
100
200
300
150
150
200
100
200
MPS详细介绍
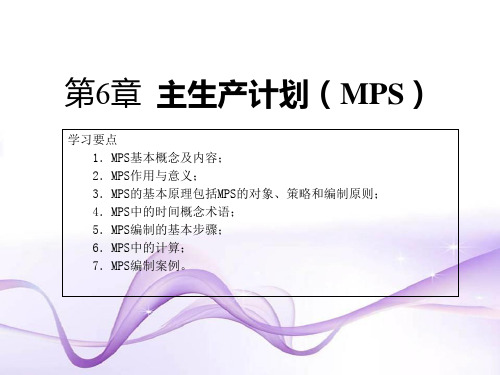
计划时区
预测时区
当前
需求
计划
时期
时界
时界
计划
1 2 3 4 5 6 7 8 9 10 11 12 13 14 15 16 17 18 19 20 21
周期
6.3.2 编制MPS计划的基本步骤
1.编制MPS的基本思路
(1)根据生产规划和计划清单确定对每个最终项目的生产预测。 (2)根据生产预测、已收到的客户订单、配件预测以及该最终项目作为
❖ ❖ ❖ ❖ ❖ ❖
6.2 MPS基本原理
6.2.1 MPS编制原则
适适全关独最 当当面键立少 稳裕代项具项 定量表目体目 原原原原原原 则则则则则则
6.2.2 主生产计划的对象
MPS
➢ ➢ ➢ ➢
6
.
交展预主 流望测生
2 .
期产 和计
3
计划
划的
时基 区本
原 则
的 策 略
6.2.4 确定MPS需求数据
6.1 MPS概述
1. 概念及内容
主生产计划(Master Production Schedule,简称MPS)是对 企业生产计划大纲的细化,用以协调生产需求与可用资源之间 的差距。
主要解决的问题是:
1. 生产什么(通常是具体的产品)。 2. 生产多少。 3. 什么时间交货。
2. MPS作用
主生产计划是计划系统中的关键环节。一个 有效的主生产计划是生产对客户需求的一 种承诺 ,它充分利用企业资源,协调生产与市场,实现 生产计划大纲中所表达的企业经营计划目标。
非独立需求项的需求数量,计算毛需求。 (3) 根据毛需求量和事先确定好的订货策略和批量,以及安全库存量
和期初库存量,计算各时区的主生产计划产出量和预计可用库存量。 (4)计算可供销售量供销售部门决策选用。
第6章 - 第6章 主生产计划(MPS)
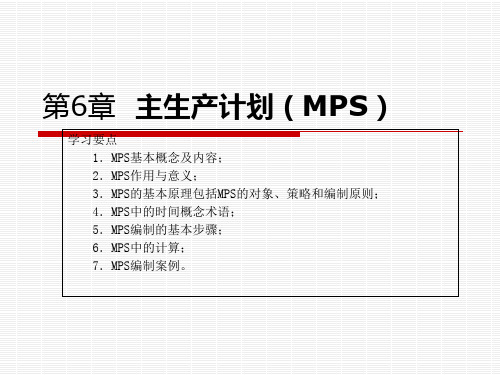
2
开始
.
编
收集整理需求数据
制
MPS
确定展望期和计划周期 并划分时区
的
计算毛需求
基
本
计算净需求
步
净需求>0?
骤
否
是
产生MPS计划
进入下一个计划周期
否
展望期结束?
是
结束
6.4 主生产计划的计算
1.毛需求量 (Gross Requirement)
在计算主生产计划项目的毛需求量时,要充分考虑该项目 所在的时区(需求时区、计划时区和预测时区)。 ➢ 在需求时区内,订单已经确定,客户需求便取代了预测值, 此时毛需求量为客户订单数量。 ➢ 在计划时区内,需要将预测需求和实际需求加以合并,此 时毛需求量通常为实际需求或预测数值中较大者。 ➢ 在预测时区内,毛需求量为预测值。
第6章 主生产计划(MPS)
学习要点 1.MPS基本概念及内容; 2.MPS作用与意义; 3.MPS的基本原理包括MPS的对象、策略和编制原则; 4.MPS中的时间概念术语; 5.MPS编制的基本步骤; 6.MPS中的计算; 7.MPS编制案例。
6.1 MPS概述 6.2 MPS基本原理
6.2.1 MPS编制原则 6.2.2 主生产计划的对象 6.2.3 MPS的策略 6.2.4 确定MPS需求数据 6.3 编制MPS初步计划 6.3.1 编制MPS计划的相关术语 6.3.2 编制MPS计划的基本步骤 6.4 主生产计划的计算 6.5 编制粗能力计划 6.6 MPS报表 6.7 评估MPS 6.9 MPS实施与控制 6.10 MPS编制案例 6.11 习题六
(3) 推算净需求。 当PAB初值≥安全库存时,净需求=0 当PAB初值<安全库存时,净需求=安全库存-PAB初值
实验四--MPS与MRP计划

实验四 MPS与MRP计划(4学时)一、M PS计划1、相关理论原理2、MPS计划前的检查累计提前期天数推算.库存异常状况查询。
仓库是否参与计算的查询。
设置MPS的预测版本为01,时栅代号,重复计划时格代号,计划的起始日期为2013。
5。
1,冻结日期为一周后,结束日期为半年后。
3、MPS计划执行执行MPS计划。
查询MPS计划后所有的销售订单的情况。
查询MPS计划后MPS件的物料供需情况。
查询MPS计划后的错误信息。
4、系统自动处理对于自制件,自动生成正式生产订单或重复计划订单。
对于委外件,自动生成委外订单。
对于采购件,自动生成采购订单。
5、报表查询(MPS)建议计划量明细表预测消抵明细表供需追溯明细表待处理订单明细表二、MRP计划1、相关理论原理2、MPS计划前的检查累计提前期天数推算。
库存异常状况查询.仓库是否参与计算的查询。
无物料清单查询.订单异常状况查询。
设置MRP的预测版本为11,时栅代号为01,重复计划时格代号为01,计划的起始日期为当前,冻结日期为一周后,结束日期为半年后。
3、MPS计划执行执行MPS计划。
查询MPS计划后MPS件的物料供需情况。
查询MPS计划后的错误信息。
4、系统自动处理对于自制件,自动生成正式生产订单或重复计划订单.对于委外件,自动生成委外订单。
对于采购件,自动生成采购订单.5、报表查询(MPS)建议计划量明细表预测消抵明细表供需追溯明细表待处理订单明细表替换料处理供需资料表。
主生产计划(MPS)的编制
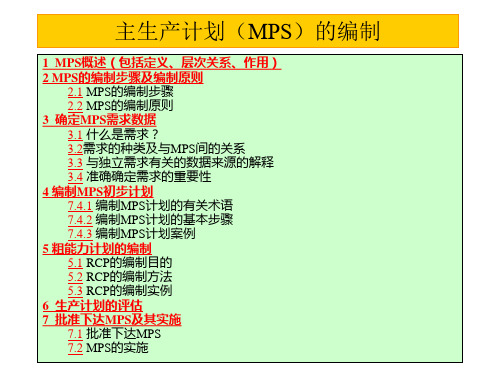
4.1 编制MPS计划的有关术语(4/13)
• 2.毛需求量
毛需求量是指在任意给定的计划周期内,项目的总需求量。 在计算主生产计划项目的毛需求量时,要充分考虑该项目所在的 时区(需求时区、计划时区和预测时区)。 (1)在需求时区内,订单已经确定,客户需求便取代了预测值, 此时毛需求量为客户订单数量。 (2)在计划时区内,需要将预测需求和实际需求加以合并,此 时毛需求量通常为实际需求或预测数值中较大者。 (3)在预测时区内,毛需求量为预测值。
4.1 编制MPS计划的有关术语(7/13)
• 5.安全库存量
安全库存量是指库存量的最低限。 设置安全库存量旨在预防需求或供方面不可预料的波动,避免造 成生产或供应中断,减缓用户需求与工厂之间、供应商和工厂之间、 制造和分配之间的矛盾。充分地利用企业现有的人力物力资源,更好 地满足客户的需求。
• 6.净需求量
1 MPS概述(1/2)
• 1、什么是主生产计划
– 主生产计划(Master Production Schedule, MPS)是对企业生产计划大纲 的细化,说明在可用资源的条件下,企业3一18月中: – (1)生产什么(通常是具体的产品); – (2)生产多少; – (3)什么时间交货。 – 主生产计划的计划展望期一般为3—18个月,一般按周或月分解。 – 主生产计划用以协调生产需求与可用资源之间的差距。
主生产计划(MPS)的编制
1 MPS概述(包括定义、层次关系、作用) 2 MPS的编制步骤及编制原则 2.1 MPS的编制步骤 2.2 MPS的编制原则 3 确定MPS需求数据 3.1 什么是需求? 3.2需求的种类及与MPS间的关系 3.3 与独立需求有关的数据来源的解释 3.4 准确确定需求的重要性 4 编制MPS初步计划 7.4.1 编制MPS计划的有关术语 7.4.2 编制MPS计划的基本步骤 7.4.3 编制MPS计划案例 5 粗能力计划的编制 5.1 RCP的编制目的 5.2 RCP的编制方法 5.3 RCP的编制实例 6 生产计划的评估 7 批准下达MPS及其实施 7.1 批准下达MPS 7.2 MPS的实施
第五章 主生产计划
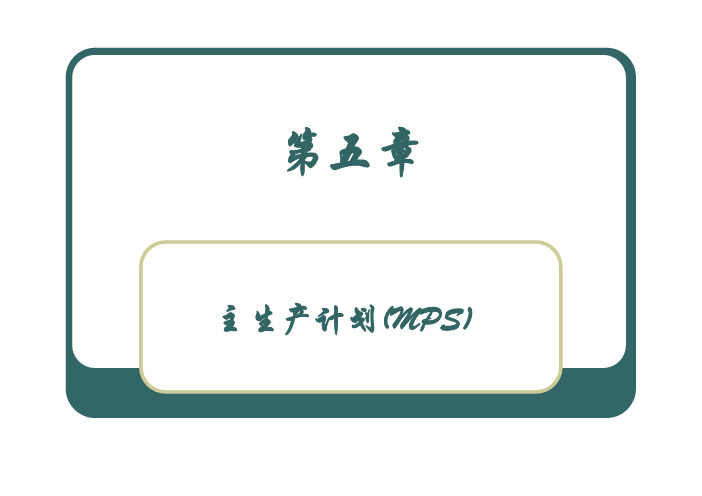
毛需求量的确定
毛需求量是生产信息,是分时段给出的。 将订单与预测结合起来,不同时段的毛需求确定有 如下方法:
⎧ Di (t ) ⎪ ⎪ GRi (t ) = ⎨max[ Di (t ), Fi (t )] ⎪ ⎪ Fi (t ) ⎩
t ≤ td td < t ≤ t p tp < t
毛需求量的确定
如何制定1-10周的主生产计划!
主生产计划的制定
表 5.2 预测和合同量
1 预测量 合同量 20 25 2 20 18 3 20 23 4 20 16 5 20 28 6 20 15 7 20 24 8 20 18 9 20 20 10 20 18
需求时界
计划时界
毛需求量的确定
表 3 毛需求计算结果 1 20 25 25 2 20 18 18 3 20 23 23 4 20 16 20 期间(周) 5 6 20 20 28 15 28 20 7 20 24 24 8 20 18 20 9 20 20 20 10 20 18 20
不同生产模式下的毛需求量确定 将订单与预测结合起来,有如下方法: (1)毛需求量=预测量------ 适合于备货生产 (2)毛需求量=订单量 ----- 适合于定货生产 (3)毛需求量=Max(预测量,订单量) ------适合于既有订单又有市场需求
在途量及预计在库量的确定
在途量(Scheduled Receipt, SR) 已经订购或者生产,预计在期间t到货的物料量SR(t)。 预计在库量(Projected On-Hand, POH) 假定某期间没有计划订单产出,则期末预计库存量 称为预计在库量。 POHi(1)= OH+SRi(1)-GRi(1) POHi(t)=PABi(t-1)+SRi(t)-GRi(t) 其中PABi(t-1)为预计可用库存量。
MPS的计算过程【范本模板】

3.4 MPS的计算过程在编写MPS过程中,关键是如何得到MPS方案。
在MPS方案中,需要依据客户订单、预测等数据计算毛需求量、净需求量、计划产出量、计划投入量和可供销售量等数据。
本节介绍MPS的详细计算过程。
首先,介绍MPS计算过程中用到的基本数据的概念;然后介绍MPS的计算流程。
最后通过一个具体的例子演示整个MPS的计算过程.3.4。
1 基本数量概念在MPS计算过程中,经常用到9大基本数量的概念.这些数量概念分别是:预测量、订单量、毛需求量、计划接收量、预计可用库存量、净需求量、计划产出量、计划投入量和可供销售量。
预测量是企业生产计划部门根据企业的经营计划或销售计划,采用合适的预测方法预测的最终产品项目将要生产的数量。
订单量是企业已经明确得到的、将要为客户提供的最终产品的数量,是企业明确的生产目标。
预测量和订单量是企业组织生产管理活动的核心目标.在不同类型的企业中,预测量和订单量所起的作用也不尽相同。
毛需求量是根据预测量和订单量计算得到的初步需求量.可以根据表3—8的数据计算毛需求量。
毛需求量的计算与时区的确定、企业的生产政策有关。
在MPS中,毛需求量是除了预测量和订单量之外的其他量的计算基础.计划接收量是指正在执行的订单量。
在制定MPS计划时,往往把制定计划日期之前的已经发出的、将要在本计划期内到达的订单数量作为计划接收量来处理。
如果希望手工修改MPS,也可以把手工添加的接收量作为计划接收量处理.预计可用库存量(PAB)是指现有库存中扣除了预留给其他用途的已分配量之后,可以用于需求计算的那部分库存量。
PAB的计算公式如下:PAB=前一时段末的PAB+本时段计划接收量-本时段毛需求量+本时段计划产出量在PAB的计算公式中,如果前3项的计算结果是负值,表示如果不为库存补充,将会出现缺料。
因此需要借助第4项,即本时段计划产出量,用于库存的补充。
净需求量(NR)是根据毛需求量、安全库存量、本期计划产出量和期初结余计算得到的数量。
mps主生产计划

mps主生产计划MPS主生产计划。
MPS主生产计划(Master Production Schedule)是指企业根据销售订单、库存情况、生产能力等因素,制定的生产计划,是生产计划中最核心的部分之一。
MPS主要确定了在特定时间范围内需要生产的产品数量,以及生产的时间安排,是生产计划的总体框架。
首先,MPS主生产计划是基于销售订单和市场需求进行制定的。
企业需要根据市场需求和销售订单情况,确定未来一段时间内需要生产的产品数量。
通过对市场需求的分析和预测,可以有效地制定MPS,以满足市场需求,同时避免库存积压或缺货的情况发生。
其次,MPS主生产计划需要考虑企业的生产能力和资源情况。
企业在制定MPS时,需要充分考虑自身的生产能力、设备情况、人力资源等因素,确保生产计划的可行性。
同时,还需要考虑原材料的供应情况,以确保生产过程中不会出现原材料短缺的情况。
再次,MPS主生产计划需要与物料需求计划(MRP)和产能规划相协调。
MPS确定了产品的生产计划,而MRP则根据MPS确定的生产计划,进一步细化原材料和零部件的需求计划,以确保生产过程中所需的物料能够及时供应。
同时,产能规划则需要根据MPS确定的生产计划,进行生产资源的合理规划和安排,以确保生产计划的顺利实施。
最后,MPS主生产计划需要不断进行调整和优化。
市场需求和销售订单可能会发生变化,生产能力和资源情况也可能会发生变化,因此MPS需要不断进行调整和优化,以适应外部环境和内部情况的变化。
通过不断地对MPS进行调整和优化,可以提高生产计划的准确性和灵活性,确保企业能够及时、高效地满足市场需求。
总之,MPS主生产计划在企业的生产计划中起着至关重要的作用。
通过合理制定MPS,可以有效地调配生产资源,提高生产效率,满足市场需求,从而实现企业的可持续发展。
因此,企业在制定MPS时,需要充分考虑市场需求、生产能力、资源情况等因素,不断进行调整和优化,以确保生产计划的顺利实施。
- 1、下载文档前请自行甄别文档内容的完整性,平台不提供额外的编辑、内容补充、找答案等附加服务。
- 2、"仅部分预览"的文档,不可在线预览部分如存在完整性等问题,可反馈申请退款(可完整预览的文档不适用该条件!)。
- 3、如文档侵犯您的权益,请联系客服反馈,我们会尽快为您处理(人工客服工作时间:9:00-18:30)。
在编写mps过程中,关键是如何得到mps方案。在mps方案中,需要依据客户订单、预测等数据计算毛需求量、净需求量、计划产出量、计划投入量和可供销售量等数据。本节介绍mps的详细计算过程。首先,介绍mps计算过程中用到的基本数据的概念;然后介绍mps的计算流程。最后通过一个具体的例子演示整个mps的计算过程。 3.4.1 基本数量概念 在mps计算过程中,经常用到9大基本数量的概念。这些数量概念分别是:预测量、订单量、毛需求量、计划接收量、预计可用库存量、净需求量、计划产出量、计划投入量和可供销售量。 预测量是企业生产计划部门根据企业的经营计划或销售计划,采用合适的预测方法预测的最终产品项目将要生产的数量。 订单量是企业已经明确得到的、将要为客户提供的最终产品的数量,是企业明确的生产目标。预测量和订单量是企业组织生产管理活动的核心目标。在不同类型的企业中,预测量和订单量所起的作用也不尽相同。 毛需求量是根据预测量和订单量计算得到的初步需求量。可以根据表3-8的数据计算毛需求量。毛需求量的计算与时区的确定、企业的生产政策有关。在mps中,毛需求量是除了预测量和订单量之外的其他量的计算基础。 计划接收量是指正在执行的订单量。在制定mps计划时,往往把制定计划日期之前的已经发出的、将要在本计划期内到达的订单数量作为计划接收量来处理。如果希望手工修改mps,也可以把手工添加的接收量作为计划接收量处理。 预计可用库存量(pab)是指现有库存中扣除了预留给其他用途的已分配量之后,可以用于需求计算的那部分库存量。 pab的计算公式如下: pab=前一时段末的pab+本时段计划接收量-本时段毛需求量+本时段计划产出量 在pab的计算公式中,如果前3项的计算结果是负值,表示如果不为库存补充,将会出现缺料。因此需要借助第4项,即本时段计划产出量,用于库存的补充。 净需求量(nr)是根据毛需求量、安全库存量、本期计划产出量和期初结余计算得到的数量。 净需求量的计算公式如下: 净需求量=本时段毛需求量-前一时段末的pab-本时段的计划接收量+安全库存量 计划产出量是指在计算pab时,如果出现负值,表示需求不能被满足,需要根据批量政策计算得到的供应数量。 计划产出量只是一个计算过程中的数据,并不是真正的计划投入数据。 计划投入量是根据计划产出量、提前期等数据计算得到的计划投入数量。 可供销售量(atp)是指销售部门可以销售的产品数量。 atp的计算公式如下: atp=本时段计划产出量+本时段计划接收量-下一次出现计划产出量之前各时段订单量之和 mps的详细计算过程如图3-4所示。在该计算过程中,首先需要确定系统设置的内容。系统设置包括整个mps计算需要的数据环境。例如,需要明确编制mps的日期,划分时段、时区,确定需求时界、计划时界、生产批量、批量增量、安全库存量和提前期等。 系统设置之后,可以计算毛需求量。计算毛需求量的基础数据是预测量和订单量。如何根据预测量和订单量得到毛需求量,取决于企业的类型、时区和生产政策。例如,可以制定这样的政策:在时区1,毛需求量等于订单量;在时区2,毛需求量等于订单量和预测量中的较大者;在时区3,毛需求量等于预测量。 计算计划接收量需要确认在编制计划日期之前已经下达的订单数量。在erp系统中可以由系统自动确认。 计算当期pab往往也是当前数据的一种确认。当期pab是指编制计划日期时可用的库存量。 接着逐个时段进行计算。计算本时段pab初值表示,在一个时段中,pab有两个值,一个是pab初值,一个是pab值。这是因为在计算pab值时,如果计算结果是负值,需要借助计划产出量进行调整。 计算本时段的净需求量。如果pab初值大于或等于安全库存量,表示不需要补充,因此净需求量为0;如果pab初值小于安全库存量,则需要补充库存,这时净需求量为安全库存量减去pab初值。 如果净需求量为0,表示不需要补充物料,因此,pab等于pab初值。如果净需求量不为0,则需要计算计划产出量。 计算计划产出量需要依据企业的批量政策。计划产出量的计算公式如下: 计划产出量=n 生产批量 n 生产批量≥净需求量 (n-1) 生产批量 n为大于或等于1的整数 计算计划产出量之后,需要计算pab值。这时,计算pab值要考虑计划产出量的影响。计算pab值之后,需要判断计划期中的各个时段是否已全部计算完毕。如果没有全部计算完毕,需要计算下一个时段的数据。 计划期循环完毕之后,可以计算计划投入量和可供销售量。 3.4.3 一个mps示例 本节通过一个具体的示例来介绍mps的计算过程。假设将要编写自行车zxca-f的mps,编写mps的日期是2006年6月1日,现有库存量为120,安全库存量为20,生产批量为160,批量增量为160,提前期是1个时段。 第一步,计算毛需求量。在需求时区,毛需求量等于订单量。 在计划时区,毛需求量等于预测量和订单量中的较大值。 在预测时区,毛需求量等于预测量。 毛需求量的计算结果如表3-14所示。 表 pab初值=120-100=20=安全库存量 净需求量=0 计划产出量=0 pab=120-100=20 第三步,计算第2时段数据。 pab初值=20-90= -70<20 净需求量=20-(-70)=90 计划产出量=1 160=160 pab=20+160-90=90 第四步,计算第3时段数据。 pab初值=90-80=10<20 净需求量=20-10=10 计划产出量=1 160=160 pab=90+160-80=170 其他时段的pab初值、净需求量、计划产出量和pab值依次类推,这里不再一一介绍了。 下面介绍如何计算计划投入量和atp。 第五步,计算各时段的计划投入量。由于提前期是1个时段,因此将计划产出量的所有数据提前1个时段,即可以得到相应时段的计划投入量。 第六步,计算各时段的atp。可以通过各个时段的计划产出量、相应的订单量和提前期等数据计算atp。 例如,在第6时段,atp=160-90-50=20。篇二:主生产计划(mps)和物料需求计划(mrp)逻辑计算(练习题)20151230 主生产计划(mps)和物料需求计划(mrp)逻辑计算(练习题) 已知某独立需求物料的有关数据如下表1,现有库存量为120,安全库存量为20,生产批量为160,批量增量为160,提前期为1个时段。库存初值为120。预测量和订单量如下表1所示。试根据相关的法则完成该独立需求物料mps计算过程,并将相应数据填入下表中。 已知某独立需求物料(最终产品)zxc的bom结构如图1所示。每个zxc由2个物料a和1个物料b组成,每个物料b由1个物料c和2个物料d组成。 图1 最终产品zxc的bom结构图 最终产品zxc的mps如表2前三行所示(即最终产品zxc的装配提前期为1 时段,表2中第2行和第3行分别给出其最终产品zxc计划产出量和计划产出量的有关数据)。 表2还同时给出其他物料a、b、c、d有关数据。其中物料a的有关属性是:计划接收量为140,pab初值为50,订货批量为140,安全库存量为30,提前期为1个时段。物料b的有关属性是:计划接收量为90,pab初值为40,订货批量为90,安全库存量为25,提前期为1个时段。物料c的有关属性是:计划接收量为180,pab初值为70,订货批量为180,安全库存量为80,提前期为1个时段。物料d的有关属性是:计划接收量为280,pab初值为120,订货批量为280,安全库存量为120,提前期为1个时段。 试根据相关的法则完成物料a、b、c、d的mrp计算过程,并将相应数据填入下表中。 篇三:主生产计划(mps) 主生产计划(mps) 一、为什么要编制主生产计划mps 二、主生产计划的对象 end items的定位:对最少品目数进行排产原则 1、备货生产方式:对最终产品排产 2、订单装配方式:对标准分装件和通用模块排产 三、主生产计划的时间范围 1、计划期 ( planning horizon ) 2、时间单位 (time buckets ) 3、时间栏 ( time fence ) 1)确认区间 ( firm portion, frozen ) 2)暂定区间 ( tentative portion ) 四、mps的作用 五、不同生产方式下mps对象的选择 六、主生产计划时间范围示意图 篇四:mrp与mps的区别 mrp与mps的区别 mps:主生产计划 mps是产成品的计划表,描述一个特定的产成品的生产时间和生产数量,mps是一个决定产成品生产排程及可承诺量(atp)的程序。 依据mps,mrp得以计算在该产成品需求之下,所有组件,零件以至原材料的补充计算。mps不是销售预测,不代表需求。 mps须考虑生产规划、预测、待交订单、关键材料、关键产能及管理目标和政策。除了材料外,mps也是其它制造资源的规划基础。 mrp:物料需求计划 mrp利用bom将mps中的完成品需求转换为半成品及原材料需求。它利用库存状态如oh及sr等,以及材料主文件中的材料基本资料如lt及ss等,以及厂历,计算出何时需要多少何种材料。 mps主要是围绕成品展开生产计划表,mrp主要是依材料展开采购工作。 根据公司的情况,大型的公司可以一周运行一次,先进行mps,然后进行mrp,之间有一个时间差;对于小型企业,可以一天运行一次mps及mrp,正规的mrp会考虑当前的所有变化,如库存、在途等,关键是你们要及时把变化信息录入erp中:例如,前一次mrp分解后需要制造a产品100件,但因为某原因,实际只做了90件,就不做了,在erp中要进行完工入库90件,然后把这个加工命令关闭。在下一次跑mrp运算时,erp系统会自动产生下一个制造10件a的任务。 因此,关键是数据的维护工作要及时,系统数据准确,erp才会发挥作用。 主生产计划(mps,master production schedule) 主生产计划是一个计划的工具,主要针对独立需求的物料进行计划(该做什么,什么时候做),它是市场需求和工厂产能之间的桥梁。其输出结果可以作为mrp的来源。 物料需求计划(mrp,material requirements planning) 主生产计划(mps)及物料需求计划(mrp)系统是erp管理软件的核心,也是erp系统发展的基础。通过mps/mrp系统将企业外部销售市场对企业的销售需求转化为企业内部的生产需求和采购需求,将销售计划转化为生产计划和采购计划。mps/mrp管理方式可以解决“需要什么?什么时候需要?需要多少?”三大难题。相对与手工管理来说,mps/mrp计划可以大大提高计划下达的效率,并大大增加计划的准确性、及时性,从根源及计划层面杜绝不必要的库存,减少浪费。篇五:sap中的mrp与mps的区别 mps与mrp的区别 1、mps是mrp的直接目的,mps体现的是净需求,mrp运算出来的作业计划和采购计划的目的就是完成mps提出的任务,从而达到企业外部市场需求的目标。 2、mps主要针对有独立需求计划而言,它是整个计划系统的调节器,在充分考虑企业粗能力和资源平衡的基础上平衡外部需求和企业供给能力.有些行业可以没有mps,直接通过mrp来满足预测和订单的需要。 3、简单的说:mps针对的是总装,mrp针对的是总装下的采购及零件。 4、如果从客户订单或预测过来的需求都需要计划部评估一下这个成品的交期和粗能力,在成品的评审没有完成之前下阶的材料都不允许产生相关需求,这个时候就对成品run mps,当成品评审通过后再对它的一阶材料run mrp。有的公司直接rum mrp,对成品一run mrp,它下面所有组件的相关需求都带出来了。这要看每个公司实际的情况而定。 5、mps主要是控制那些对企业来说比较重要特别是那些高价值的半成品,这样在运行mps后调整后,再运行mrp产生下面相关件的需求。 6、两者的运行原理相同 运行mps的物料不能运行mrp,运行mrp的物料可以运行mps。(看物料主数据中设置的mrp类型) mps一般对公司有重大利润的产品或者关键物资进行计划。一般先运行mps,然后再对下一层的物料进行运行mrp 。 相同点: 功能相同、算法相同