硬质合金刀具角度
硬质合金刀具选用明细表

加工高温合金的硬质合金刀具1.加工高温合金的硬质合金刀具材料,宜选择超细微粒硬质合金YS2,YG8W,YG813,YG643,YM052,YM051和钨钴类YG8及钨钛钽(铌)钴类YG8N,YW3,YW4等.其中,YS2,YG8W用于粗加工,其他用于精加工.不宜选择YT类.(进口刀具材料各品牌的编号不一样,要查清楚需要他们材料供应商提供一些资料,难度大些,我手上资料不够,以后有了再介绍).2.刀具合理几何参数选择:前角应选正值,后角稍大些,前面宜磨成圆弧断屑槽形,刃区一般不磨负倒棱.主偏角根据工艺系统刚性来定,刚性好取小些,反之取大些.3.合理选择切削用量.背吃刀量粗加工取1-6mm,精加工0.2-0.5.进给取0.1-0.5mm/r.根据被切削材料查一下切削速度.根据切削温度原理,以700-1000度为宜.4.选择切削液,可选择压力切削油,尽量不选择含硫的切削液.实际加工时,要多做测试和调整,自己的经验比较保险.硬质合金常用牌号及用途介绍牌号/相当标准ISO/ 物理机械性能(min):抗弯强度N/mm2 ;硬度HRA/用途1、YG3x/ K01/ 1420; 92.5 /适于铸铁.有色金属及合金.淬火钢合金钢小切削断面高速精加工.2、YG6/ K20 /1900; 90.5 /适于铸铁.有色金属及合金.非金属材料中等到切削速度下半精加工和精加工.3、YG6x /K15/ 1800; 92.0/ 适于冷硬铸铁.球墨铸铁.灰铸铁.耐热合金钢的中小切削断面高速精加工.半精加工.4、YG6A/ K10/ 1800 ;92.0 /适于冷硬铸铁.球墨铸铁.灰铸铁.耐热合金的中小切削断面高速精加工5、YG8/ K30/ 2200 ;90.0/ 适于铸铁.有色金属及合金.非金属材料低速粗加工.6、YG8N/ K30/ 2100; 90.5 /适于铸铁.白口铸铁.球墨铸铁以及铬镍不锈钢等合金材料的高速切削.7、YG15/ K40/ 2500 ;87.0 /适于镶制油井.煤炭开采钻头.地质勘探钻头.8、YG4C/ 1600; 89.5/ 适于镶制油井.煤炭开采钻头.地质勘探钻头.9、YG8C/ 1800; 88.5 /适于镶制油井.矿山开采钻头一字.十字钻头.牙轮钻齿.潜孔钻齿.10、YG11C/ 2200 ;87.0 /适于镶制油井.矿山开采钻头一字.十字钻头.牙轮钻齿.潜孔钻齿.11、YW1/ M10/ 1400; 92.0 /适于钢.耐热钢.高锰钢和铸铁的中速半精加工.12、YW2/ M20/ 1600; 91.0 /适于耐热钢.高锰钢.不锈钢等难加工钢材中.低速粗加工和半精加工.13、GE1/ M30/ 2000; 91.0 /适于非金属材料的低速粗加工和钟表齿轮耐磨损零件.14、GE2 /2500; 90.0 /硬质合金顶锤专用牌号.15、GE3/ M40/ 2600; 90.0 /适于制造细径微钻.立铣刀.旋转挫刀等.16、GE4/ 2600; 88.0/ 适于打印针.压缸及特殊用途的管. 棒.带等.17、GE5 /2800 ;85.0 /适于轧辊.冷冲模等耐冲击材料.。
车刀种类和角度选择原则详解
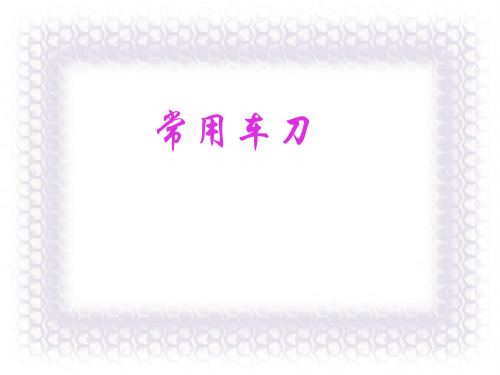
车刀不对准工件中心对角度的影响
五、车刀刃磨
无论硬质合金车刀(焊接)或高速钢 车刀,在使用之前都要根据切削条 件所选择的合理切削角度进行刃磨 ,一把用钝了的车刀,为恢复原有 的几何形状和角度,也必须重新刃 磨。
重 要 性
三分手艺、七分刀 徒弟的手、师傅的刀
1.磨刀步骤(图a~d)
⑴磨前刀面 把前角和刃倾角磨正确。 ⑵磨主后刀面 把主偏角和主后角磨正确。 ⑶磨副后刀面 把副偏角和副后角磨正确。 ⑷磨刀尖圆弧 圆弧半径约0.5~2mm左右。 ⑸研磨刀刃 车刀在砂轮上磨好以后,再用油石加些机油研磨车 刀的前面及后面,使刀刃锐利和光洁。这样可延长车刀的使用寿命。 车刀用钝程度不大时,也可用油石在刀架上修磨。硬质合金车刀可 用碳化硅油石修磨。
前角γo
——在主切削刃选定点的正交平面po内, 前刀面与基面之间的夹角
。
后角αo
——在正交平面po内,主后刀面与切削 平面之间的夹角。
主偏角κr
——主切削刃在基面上的投影与进给方 向的夹角。
刃倾角λs ——在切削平面ps内,主切削刃与 基面pr的夹角。
其他角度:
副前角γoˊ、 副后角αoˊ、 副偏角κrˊ、 刃倾角λsˊ
3.主偏角、副偏角的选择 (1)主偏角的选择 A、主偏角κr的增大或减小对切削加工有利的一 面 在背吃刀量ap与进给量f 不变时,主偏角κr减小 将使切削厚度hD减小,切削宽度bD增加,参加 切削的切削刃长度也相应增加,切削刃单位长度 上的受力减小,散热条件也得到改善。 主偏角κr减小时,刀尖角增大,刀尖强度提高, 刀尖散热体积增大。 所以,主偏角κr减小,能提高刀具耐用度。
(4)良好的工艺性和经济性
车刀的主要角度及其作用

车刀的主要角度及其作用车刀的主要角度有前角(γ0)、后角(α0)、主偏角(Kr)、副偏角(Kr’)和刃倾角(λs)。
为了确定车刀的角度,要建立三个坐标平面:切削平面、基面和主剖面。
对车削而言,如果不考虑车刀安装和切削运动的影响,切削平面可以认为是铅垂面;基面是水平面;当主切削刃水平时,垂直于主切削刃所作的剖面为主剖面。
(1)前角γ0在主剖面中测量,是前刀面与基面之间的夹角。
其作用是使刀刃锋利,便于切削。
但前角不能太大,否则会削弱刀刃的强度,容易磨损甚至崩坏。
加工塑性材料时,前角可选大些,如用硬质合金车刀切削钢件可取γ0=10~20,加工脆性材料,车刀的前角γ0应比粗加工大,以利于刀刃锋利,工件的粗糙度小。
(2)后角α0在主剖面中测量,是主后面与切削平面之间的夹角。
其作用是减小车削时主后面与工件的摩擦,一般取α0=6~12°,粗车时取小值,精车时取大值。
(3)主偏角Kr在基面中测量,它是主切削刃在基面的投影与进给方向的夹角。
其作用是:1)可改变主切削刃参加切削的长度,影响刀具寿命。
2)影响径向切削力的大小。
小的主偏角可增加主切削刃参加切削的长度,因而散热较好,对延长刀具使用寿命有利。
但在加工细长轴时,工件刚度不足,小的主偏角会使刀具作用在工件上的径向力增大,易产生弯曲和振动,因此,主偏角应选大些。
车刀常用的主偏角有45°、60°、75°、90°等几种,其中45°多。
(4)副偏角Kr’在基面中测量,是副切削刃在基面上的投影与进给反方向的夹角。
其主要作用是减小副切削刃与已加工表面之间的摩擦,以改善已加工表面的精糙度。
在切削深度ap、进给量f、主偏角Kr相等的条件下,减小副偏角Kr’,可减小车削后的残留面积,从而减小表面粗糙度,一般选取Kr′=5~15°。
(5)刃倾角入λs 在切削平面中测量,是主切削刃与基面的夹角。
其作用主要是控制切屑的流动方向。
5个硬质合金钻头标准
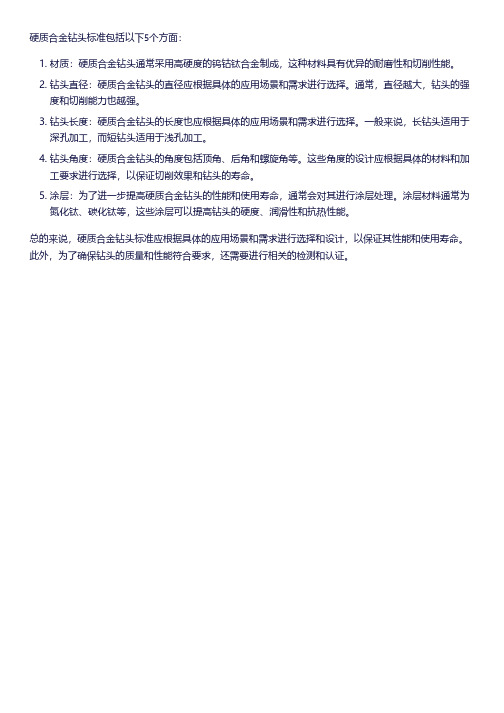
硬质合金钻头标准包括以下5个方面:
1. 材质:硬质合金钻头通常采用高硬度的钨钴钛合金制成,这种材料具有优异的耐磨性和切削性能。
2. 钻头直径:硬质合金钻头的直径应根据具体的应用场景和需求进行选择。
通常,直径越大,钻头的强
度和切削能力也越强。
3. 钻头长度:硬质合金钻头的长度也应根据具体的应用场景和需求进行选择。
一般来说,长钻头适用于
深孔加工,而短钻头适用于浅孔加工。
4. 钻头角度:硬质合金钻头的角度包括顶角、后角和螺旋角等。
这些角度的设计应根据具体的材料和加
工要求进行选择,以保证切削效果和钻头的寿命。
5. 涂层:为了进一步提高硬质合金钻头的性能和使用寿命,通常会对其进行涂层处理。
涂层材料通常为
氮化钛、碳化钛等,这些涂层可以提高钻头的硬度、润滑性和抗热性能。
总的来说,硬质合金钻头标准应根据具体的应用场景和需求进行选择和设计,以保证其性能和使用寿命。
此外,为了确保钻头的质量和性能符合要求,还需要进行相关的检测和认证。
刀具角度的实验报告
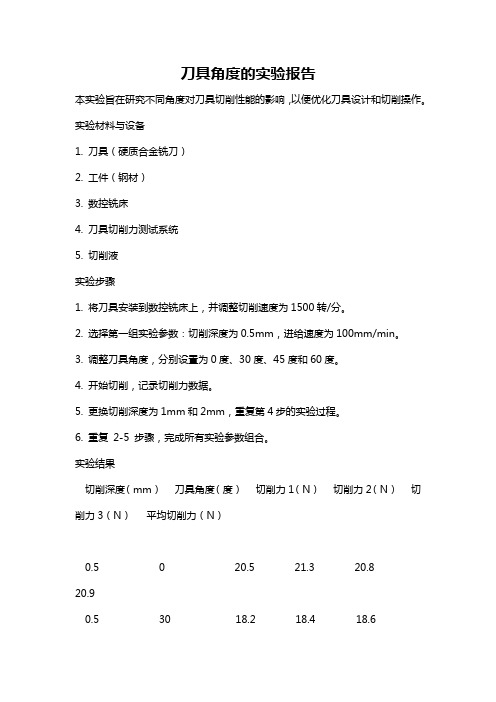
刀具角度的实验报告本实验旨在研究不同角度对刀具切削性能的影响,以便优化刀具设计和切削操作。
实验材料与设备1. 刀具(硬质合金铣刀)2. 工件(钢材)3. 数控铣床4. 刀具切削力测试系统5. 切削液实验步骤1. 将刀具安装到数控铣床上,并调整切削速度为1500转/分。
2. 选择第一组实验参数:切削深度为0.5mm,进给速度为100mm/min。
3. 调整刀具角度,分别设置为0度、30度、45度和60度。
4. 开始切削,记录切削力数据。
5. 更换切削深度为1mm和2mm,重复第4步的实验过程。
6. 重复2-5 步骤,完成所有实验参数组合。
实验结果切削深度(mm)刀具角度(度)切削力1(N)切削力2(N)切削力3(N)平均切削力(N)0.5 0 20.5 21.3 20.820.90.5 30 18.2 18.4 18.618.40.5 45 16.7 16.8 16.6 16.70.5 60 15.2 15.3 15.4 15.31 0 25.1 24.8 25.3 25.11 30 21.6 22.1 21.8 21.81 45 19.8 19.6 19.7 19.71 60 17.9 17.7 18.1 17.92 0 30.3 30.6 30.5 30.52 30 26.7 26.9 26.6 26.72 45 24.5 24.6 24.4 24.52 60 22.1 21.8 22.3 22.1数据分析通过对实验结果的分析,我们可以得出以下结论:1. 随着切削深度的增加,切削力也随之增加。
这是由于加工过程中材料的剪切面积增大,切削力的需要也增加。
2. 在相同切削深度下,刀具角度增加会导致切削力的减小。
这是由于增大的刀具角度可以降低刀具与工件之间的接触面积,减小切削力的需要。
3. 当刀具角度达到一定程度后,再增加刀具角度对切削力的减小作用有限。
这是由于角度过大会导致刀具的切削效率降低,进而增加切削力。
硬质合金刀具角度
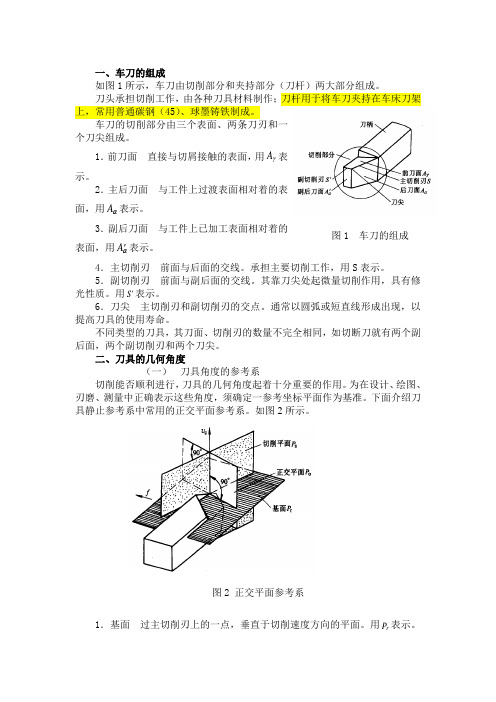
一、车刀的组成如图1所示,车刀由切削部分和夹持部分(刀杆)两大部分组成。
刀头承担切削工作,由各种刀具材料制作;刀杆用于将车刀夹持在车床刀架上,常用普通碳钢(45)、球墨铸铁制成。
车刀的切削部分由三个表面、两条刀刃和一个刀尖组成。
1.前刀面直接与切屑接触的表面,用γA表示。
2.主后刀面与工件上过渡表面相对着的表面,用αA表示。
3.副后刀面与工件上已加工表面相对着的表面,用αA'表示。
4.主切削刃前面与后面的交线。
承担主要切削工作,用S表示。
5.副切削刃前面与副后面的交线。
其靠刀尖处起微量切削作用,具有修光性质。
用S'表示。
6.刀尖主切削刃和副切削刃的交点。
通常以圆弧或短直线形成出现,以提高刀具的使用寿命。
不同类型的刀具,其刀面、切削刃的数量不完全相同,如切断刀就有两个副后面,两个副切削刃和两个刀尖。
二、刀具的几何角度(一)刀具角度的参考系切削能否顺利进行,刀具的几何角度起着十分重要的作用。
为在设计、绘图、刃磨、测量中正确表示这些角度,须确定一参考坐标平面作为基准。
下面介绍刀具静止参考系中常用的正交平面参考系。
如图2所示。
图2 正交平面参考系1.基面过主切削刃上的一点,垂直于切削速度方向的平面。
用r P表示。
图1 车刀的组成2.切削平面过主切削刃上的一点,与主切削刃相切并垂直于基面的平面。
用s P表示。
3.正交平面垂直于主切削刃在基面上投影的平面,又称主剖面,用o P表示。
切削平面、基面、正交平面(主剖面)在空间相互垂直,构成一个空间直角坐标系,是车刀几何角度的测量平面。
(二)车刀的基本角度(图3)图3 车刀的几何角度1.在正交平面(主剖面)中测量、标注的角度⑴前角前刀面(γA)与基面(r P)的夹角,用oγ表示。
当前刀面与基面的夹角小于90°时,oγ为正值;大于90°时,oγ为负值。
⑵后角后刀面αA与切削平面s P间的夹角,用oα表示。
当后刀面与切削平面的夹角小于90°时,oα为正值;大于90°时,oα为负值。
硬质合金钻头钻削不同材料时钻尖角度的选择
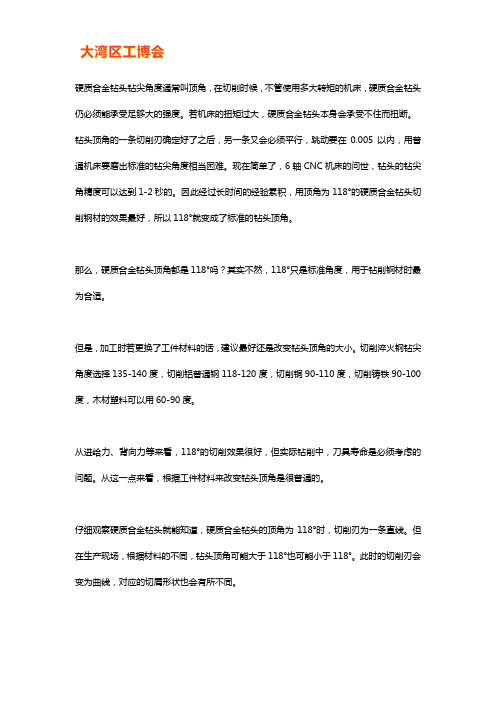
硬质合金钻头钻尖角度通常叫顶角,在切削时候,不管使用多大转矩的机床,硬质合金钻头仍必须能承受足够大的强度。
若机床的扭矩过大,硬质合金钻头本身会承受不住而扭断。
钻头顶角的一条切削刃确定好了之后,另一条又会必须平行,跳动要在0.005以内,用普通机床要磨出标准的钻尖角度相当困难。
现在简单了,6轴CNC机床的问世,钻头的钻尖角精度可以达到1-2秒的。
因此经过长时间的经验累积,用顶角为118°的硬质合金钻头切削钢材的效果最好,所以118°就变成了标准的钻头顶角。
那么,硬质合金钻头顶角都是118°吗?其实不然,118°只是标准角度,用于钻削钢材时最为合适。
但是,加工时若更换了工件材料的话,建议最好还是改变钻头顶角的大小。
切削淬火钢钻尖角度选择135-140度,切削铝普通钢118-120度,切削铜90-110度,切削铸铁90-100度,木材塑料可以用60-90度。
从进给力、背向力等来看,118°的切削效果很好,但实际钻削中,刀具寿命是必须考虑的问题。
从这一点来看,根据工件材料来改变钻头顶角是很普通的。
仔细观察硬质合金钻头就能知道,硬质合金钻头的顶角为118°时,切削刃为一条直线。
但在生产现场,根据材料的不同,钻头顶角可能大于118°也可能小于118°。
此时的切削刃会变为曲线,对应的切屑形状也会有所不同。
硬质合金刀具材料性能和特点
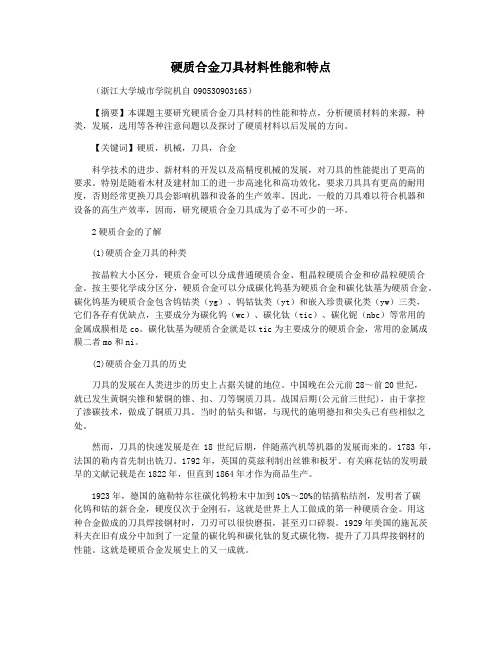
硬质合金刀具材料性能和特点(浙江大学城市学院机自************)【摘要】本课题主要研究硬质合金刀具材料的性能和特点,分析硬质材料的来源,种类,发展,选用等各种注意问题以及探讨了硬质材料以后发展的方向。
【关键词】硬质,机械,刀具,合金科学技术的进步、新材料的开发以及高精度机械的发展,对刀具的性能提出了更高的要求。
特别是随着木材及建材加工的进一步高速化和高功效化,要求刀具具有更高的耐用度,否则经常更换刀具会影响机器和设备的生产效率。
因此,一般的刀具难以符合机器和设备的高生产效率,因而,研究硬质合金刀具成为了必不可少的一环。
2硬质合金的了解(1)硬质合金刀具的种类按晶粒大小区分,硬质合金可以分成普通硬质合金、粗晶粒硬质合金和矽晶粒硬质合金。
按主要化学成分区分,硬质合金可以分成碳化钨基为硬质合金和碳化钛基为硬质合金。
碳化钨基为硬质合金包含钨钴类(yg)、钨钴钛类(yt)和嵌入珍贵碳化类(yw)三类,它们各存有优缺点,主要成分为碳化钨(wc)、碳化钛(tic)、碳化铌(nbc)等常用的金属成膜相是co。
碳化钛基为硬质合金就是以tic为主要成分的硬质合金,常用的金属成膜二者mo和ni。
(2)硬质合金刀具的历史刀具的发展在人类进步的历史上占据关键的地位。
中国晚在公元前28~前20世纪,就已发生黄铜尖锥和紫铜的锥、扣、刀等铜质刀具。
战国后期(公元前三世纪),由于掌控了渗碳技术,做成了铜质刀具。
当时的钻头和锯,与现代的施明德扣和尖头已有些相似之处。
然而,刀具的快速发展是在18世纪后期,伴随蒸汽机等机器的发展而来的。
1783年,法国的勒内首先制出铣刀。
1792年,英国的莫兹利制出丝锥和板牙。
有关麻花钻的发明最早的文献记载是在1822年,但直到1864年才作为商品生产。
1923年,德国的施勒特尔往碳化钨粉末中加到10%~20%的钴搞粘结剂,发明者了碳化钨和钴的新合金,硬度仅次于金刚石,这就是世界上人工做成的第一种硬质合金。
- 1、下载文档前请自行甄别文档内容的完整性,平台不提供额外的编辑、内容补充、找答案等附加服务。
- 2、"仅部分预览"的文档,不可在线预览部分如存在完整性等问题,可反馈申请退款(可完整预览的文档不适用该条件!)。
- 3、如文档侵犯您的权益,请联系客服反馈,我们会尽快为您处理(人工客服工作时间:9:00-18:30)。
一、车刀的组成如图1所示,车刀由切削部分和夹持部分(刀杆)两大部分组成。
刀头承担切削工作,由各种刀具材料制作;刀杆用于将车刀夹持在车床刀架上,常用普通碳钢(45)、球墨铸铁制成。
车刀的切削部分由三个表面、两条刀刃和一个刀尖组成。
1.前刀面直接与切屑接触的表面,用γA表示。
2.主后刀面与工件上过渡表面相对着的表面,用αA表示。
3.副后刀面与工件上已加工表面相对着的表面,用αA'表示。
4.主切削刃前面与后面的交线。
承担主要切削工作,用S表示。
5.副切削刃前面与副后面的交线。
其靠刀尖处起微量切削作用,具有修光性质。
用S'表示。
6.刀尖主切削刃和副切削刃的交点。
通常以圆弧或短直线形成出现,以提高刀具的使用寿命。
不同类型的刀具,其刀面、切削刃的数量不完全相同,如切断刀就有两个副后面,两个副切削刃和两个刀尖。
二、刀具的几何角度(一)刀具角度的参考系切削能否顺利进行,刀具的几何角度起着十分重要的作用。
为在设计、绘图、刃磨、测量中正确表示这些角度,须确定一参考坐标平面作为基准。
下面介绍刀具静止参考系中常用的正交平面参考系。
如图2所示。
图2 正交平面参考系1.基面过主切削刃上的一点,垂直于切削速度方向的平面。
用r P表示。
图1 车刀的组成2.切削平面过主切削刃上的一点,与主切削刃相切并垂直于基面的平面。
用s P表示。
3.正交平面垂直于主切削刃在基面上投影的平面,又称主剖面,用o P表示。
切削平面、基面、正交平面(主剖面)在空间相互垂直,构成一个空间直角坐标系,是车刀几何角度的测量平面。
(二)车刀的基本角度(图3)图3 车刀的几何角度1.在正交平面(主剖面)中测量、标注的角度⑴前角前刀面(γA)与基面(r P)的夹角,用oγ表示。
当前刀面与基面的夹角小于90°时,oγ为正值;大于90°时,oγ为负值。
⑵后角后刀面αA与切削平面s P间的夹角,用oα表示。
当后刀面与切削平面的夹角小于90°时,oα为正值;大于90°时,oα为负值。
前刀面、后刀面间的夹角β称为楔角。
β=90°-(oγ+oα)2.在基面内测量、标注的角度:⑴主偏角主切削刃在基面上的投影与进给运动方向的夹角,用r k表示。
它总为正值。
⑵副偏角副切削刃在基面上的投影与进给运动相反方向的夹角,用r k'表示。
主切削刃和副切削刃在基面上的投影的夹角称为刀尖角。
ε=180°-(r k+r k')r3.在切削平面内测量、标注的角度:刃倾角主切削刃与基面(r P)之间的夹角,用sλ表示。
刃倾角也有正负之分,如图4所示,当刀尖在切削刃最高点时,刃倾角为正;刀尖在最低点时,刃倾角为负。
当主切削刃与基面平行时,刃倾角为0°。
图4 车刀的刃倾角4.在副正交平面中测量、标注的角度:参照主切削刃的研究方法,在负切削刃上同样可定义一副正交平面(副剖面)P'。
在副正交平面中测量、标注的角度有副后角oα',它是副后面αA'与副切削o平面s P'间的夹角。
当副后面与副切削平面的夹角小于90°时,后角为正值。
由于车刀有主、副两个切削刃,每个切削刃都可建立一个坐标系,在每一坐标系的坐标平面上,又都可测量出三个基本角度:前角(副前角)、后角(副后角)和刃倾角(副刃倾角),加上主、副偏角,这样,车刀就共有八个基本角度。
但因主、副切削刃处于一个前刀面上,当前角oγ和刃倾角sλ确定后,副前角oγ'和副刃倾角sλ'可以通过换算求得,故为派生角度。
刀尖角rε、楔角β也属派生角度。
所以车刀的基本角度为六个,即前角oγ、后角oα、刃倾角sλ、主偏角r k、副偏角r k'和副后角oα'。
这是在刀具图纸上必须标出的,其它角度则不必标注。
三、前角的选择1.前角的功用前角主要影响切屑变形和切削力的大小及刀具耐用度和加工表面质量的高低。
增大oγ,可减小切屑变形和摩擦,故切削力小、切削热少,加工表面质量高。
但oγ过大,会降低刀刃强度,散热体积减小,刀具耐用度下降。
减小oγ,刀具强度提高,切屑变形增大,易断屑。
但oγ过小,会使切削力和切削热增加,刀具耐用度降低。
2.前角的选择原则⑴根据工件材料选加工塑性材料时,特别是加工硬化严重的材料(如不锈钢等),为了减小切屑变形和刀具磨损,应选用较大的γ;加工脆性材料时,由o于产生的切屑为崩碎切屑,切屑变形也小,增大的意义不大,而这时刀—屑间的作用力集中在切削刃附近,为保证切削刃具具有足够的强度,应采用较小的γ。
o 工件的强度和硬度低时,由于切削力不大,为使切削刃锋利,可选用较大的甚至很大的γ;工件材料的强度高时,应选用较小的oγ;加工特别硬的工件材o料(如淬火钢)时,应选用很小的γ;甚至选用负前角;这是因为工件的强度、o硬度愈高,产生的切削力愈大,切削热愈多,为了使切削刃具有足够的强度和散热容量,防止崩刃和迅速磨损,因此应选用较小的oγ。
⑵根据刀具材料选刀具材料的抗弯强度和冲击韧性较低时应选较小的oγ;高速钢刀具比硬质合金刀具的合理前角约大5°~10°。
陶瓷刀具的合理前角应选得比硬质合金刀具更小一些。
⑶根据加工性质选粗加工时,特别是断续切削或加工有硬皮的铸、锻件,不仅切削力大,切削热多,而且承受冲击载荷,为保证切削刃有足够的强度和散热面积,应适当减小oγ;精加工时,对切削刃强度要求较低,为使切削刃锋利,减小切屑变形和获得较高的表面质量,应取得较大一些。
数控机床和自动机、自动线用的刀具,为保证刀具工作的稳定性(不发生崩刃和破损),通常选用较小的oγ。
在一般情况下,前角oγ主要根据被加工材料来选择。
硬质合金车刀前角oγ的选择参考值见表1。
四、后角的选择1.后角的功用后角的主要功用是减小主后刀面与过渡表面的弹性恢复层之间的摩擦,减轻刀具磨损。
oα小,使主后刀面与工件表面的摩擦加剧,刀具磨损加大,工件冷硬程度增加,加工表面质量差;尤其是切削厚度较小时,上述情况更严重。
oα增大,摩擦减小,也减小了刃口钝圆半径,这对切削厚度较小的情况有利,但使刀刃强度和散热情况变差。
2.后角的选择原则⑴根据切削厚度选切削厚度D h愈大,则oα应愈小;反之亦然。
如进给量较大的外圆车刀oα=6°~8°;每齿进刀量很小的立铣刀oα=6°;而每齿进刀量不超过0.01㎜的圆盘铣刀oα=30°。
这是因为切削厚度较大时,切削力较大,切削温度也较高,为了保证刃口强度和改善散热条件,所以应取较小的oα。
切削厚度愈小,切削层上被切削刃的钝圆半径挤压而留在已加工表面上的、并与主后刀面挤压摩擦的这一薄层金属占切削厚度的比例就越大。
若增大oα,就可减小刃口钝圆半径,使刃口锋利,便于切下薄切屑,可提高刀具耐用度和加工表面质量。
综上,粗加工、强力切削(大进给量)切削以及承受冲击载荷的刀具,增大刃口强度是主要的。
这时应选取较小的oα;精加工时则应选取较大的oα。
⑵适当考虑被加工材料的力学性能工件材料硬度、强度较高时,为保证切削刃强度,宜选取较小的oα;工件材料的硬度较低、塑性较大,以及易产生加工硬化时,主后刀面的摩擦对已加工表面质量和刀具磨损影响较大,此时应取较大的oα;加工脆性材料时,切削力集中在刀刃附近,为强化切削刃,宜选取较小的oα。
⑶考虑工艺系统的刚性工艺系统刚性差,易产生振动,为增强刀具对振动的阻尼,应选取较小的oα。
⑷考虑加工精度对于尺寸精度要求高的精加工刀具(如铰刀等)为减小重磨后刀具尺寸变化,保证有较高的耐用度,oα应取得较小。
硬质合金车刀后角参考值见表2。
α'与oα相副后角可减少副后面与已加工表面的摩擦。
一般车刀、刨刀等的o等;而切断刀、切槽刀及锯片铣刀等的因受刀头强度限制,只能取得较小,通α'=1°~2°。
常o五、主偏角及副偏角的选择1.主偏角的功用及选择原则主偏角r k的功用是影响刀尖部分的强度、散热条件、径向力和轴向力的比例等;在加工台阶或倒角时还决定着工件表面的形状。
减小r k会使刀尖强度增加,散热条件得到改善,切削厚度减小,切削宽度增加,单位长度刀刃上的负荷减轻,这些都有利于提高刀具耐用度;而加大r k,则有利于减小径向力r k,防止工件变形和减小加工中的振动。
主要根据工艺系统的刚度来选。
当工艺系统的刚性低(如车细长轴、薄壁套筒)时,须取较大的r k,甚至取r k≥90°,以减小p F;工艺系统的刚性足够时,应采用较小的r k,以提高刀具耐用度。
例如,车削细长轴时,常取r k=90°;车削高强度、高硬度的冷硬轧辊时,常取r k≤15°。
2.副偏角的功用及选择原则副偏角r k'的作用主要是减少刀具副切削刃、副刀面与已加工表面的摩擦。
减小r k'会使刀尖角加大,提高刀尖部分的强度,并且有利于降低残留面积的高度,降低已加工表面的表面粗糙度。
但是,小的r k'会使刀具与工件之间的摩擦和径向力增加。
增大r k'时,其结果正好相反。
k'主要根据工件已加工表面粗糙度的要求选。
粗加工时,r k'可取大些;精r加工时,r k'可取小些。
为降低工件的表面粗糙度值,必要时可磨出r k'=0°的修光刃,修光刃的长度应略大于进给量。
加工高强度、高硬度的材料或断续切削时,应取较小的r k'(4°~6°),以提高刀尖的强度。
工件刚性较差时,为减小径向力F,避免产生振动,r k'可稍大些。
p硬质合金车刀主偏角和副偏角的参考值见表3。
表3 硬质合金车刀主偏角和副偏角的参考值Array四、刃倾角的选择1.刃倾角的作用刃倾角主要影响切屑流向(图5)和刀尖强度(图6)。
sλ为正时,刀尖部分强度较差,切削时刀尖先与工件接触,容易打刀;正的刃倾角使切屑流向待加工表面,可避免缠绕和划伤已加工表面;sλ为负时,切削时刀刃先接触工件,不容易打刀,对刀尖起保护作用;负的刃倾角使切屑流向已加工表面,容易将已加工表面划伤。
sλ还将导致实际工作前角增大,切削力减小,切削轻快平稳。
图5 刃倾角对切屑流向的影响图6 刃倾角对刀尖强度的影响2.刃倾角的选择原则sλ主要根据刀尖强度、切屑流向和工艺系统的刚性来选。
一般遵循以下原则:⑴粗加工时取负值、精加工时取正值sλ<0°时,刀具具有较高的强度和散热条件,切入工件时刀尖免受冲击;sλ>0°时,使切屑流向待加工表面,以提高表面质量。
⑵断续切削、加工不规则表面取负值因断续切削、不规则表面加工时,冲击力大,负的刃倾角可提高刀尖强度。
⑶工件材料硬度高时取负值切削硬度很高的材料(如淬火钢),应取绝对值较大的负刃倾角,以使刀具有足够的强度。