原材料检验规范
原材料检验规范

原材料检验规范原材料检验规范是指在生产过程中对原材料进行检验的一系列规范。
原材料是产品制造中不可缺少的物质基础,其质量直接影响着产品的质量和性能。
因此,对原材料进行检验是确保产品质量和安全的重要环节。
一、检验前的准备工作1. 确定原材料的检验标准和要求:根据产品的生产需求和国家相关标准,制定检验标准和要求,包括物理性质、化学成分、微生物指标等。
2. 确定检验项目和方法:根据原材料的特点和检验要求,确定检验项目和方法,包括外观检查、尺寸检测、成分分析、微生物检测等。
3. 准备检验设备和仪器:根据检验项目和方法的要求,准备合适的检验设备和仪器,确保检验工作的准确性和可靠性。
二、检验的操作步骤1. 取样:按照规定的取样数量和方法,从原材料中取出代表性样品,避免取样过程中的污染和失真。
2. 外观检查:对原材料的外观进行检查,包括颜色、形状、气味等方面,确保其符合产品的要求。
3. 尺寸检测:对原材料的尺寸进行测量,包括长度、宽度、厚度等参数,确保其符合产品的要求。
4. 成分分析:利用化学分析方法对原材料的化学成分进行分析,包括含量、纯度、稳定性等方面,确保其符合产品的要求。
5. 微生物检测:对原材料进行微生物指标检测,包括总菌落数、大肠菌群、霉菌等指标,确保其符合产品的卫生要求。
6. 数据记录和分析:对检验结果进行记录和分析,及时发现问题和异常情况,并采取相应的措施进行处理。
三、检验结果的处理与分析1. 合格品的处理:对经检验合格的原材料,按照规定的存储和使用要求进行标识和放置,确保在生产过程中不受污染。
2. 不合格品的处理:对经检验不合格的原材料,应按照标准和要求进行分类和处理,包括退货、重新检验、改良等措施,确保不合格品不进入产品生产流程。
3. 数据分析:对检验结果进行统计分析,找出问题的原因和改进的措施,为后续的生产和质量控制提供参考和依据。
通过制定和实施原材料检验规范,可以确保原材料的质量和安全性,保证产品的质量和性能,提高企业的竞争力和市场信誉度。
原材料检验规范
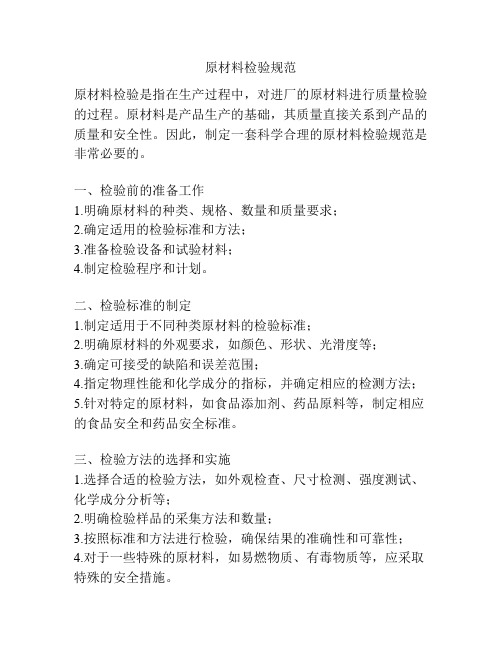
原材料检验规范原材料检验是指在生产过程中,对进厂的原材料进行质量检验的过程。
原材料是产品生产的基础,其质量直接关系到产品的质量和安全性。
因此,制定一套科学合理的原材料检验规范是非常必要的。
一、检验前的准备工作1.明确原材料的种类、规格、数量和质量要求;2.确定适用的检验标准和方法;3.准备检验设备和试验材料;4.制定检验程序和计划。
二、检验标准的制定1.制定适用于不同种类原材料的检验标准;2.明确原材料的外观要求,如颜色、形状、光滑度等;3.确定可接受的缺陷和误差范围;4.指定物理性能和化学成分的指标,并确定相应的检测方法;5.针对特定的原材料,如食品添加剂、药品原料等,制定相应的食品安全和药品安全标准。
三、检验方法的选择和实施1.选择合适的检验方法,如外观检查、尺寸检测、强度测试、化学成分分析等;2.明确检验样品的采集方法和数量;3.按照标准和方法进行检验,确保结果的准确性和可靠性;4.对于一些特殊的原材料,如易燃物质、有毒物质等,应采取特殊的安全措施。
四、检验结果的记录和处理1.将检验结果记录在检验报告中,包括样品编号、检验日期、检验结果等信息;2.对不合格的原材料,应及时通知供应商,并进行处理,如退货、更换等;3.对合格的原材料,按照规定进行存储和使用。
五、监控和改进1.建立原材料检验质量控制体系,定期对检验结果进行分析和评估;2.根据检验结果,及时对检验方法和标准进行调整和改进;3.对于出现重大质量问题的原材料,应进行追溯调查和整改,并与供应商进行沟通和协商。
六、人员培训和管理1.培训检验人员的专业知识和技能,提高其检验水平;2.制定人员考核和奖惩制度,激励员工积极参与和推动原材料检验工作的质量提升。
总之,制定一套科学合理的原材料检验规范是确保产品质量的重要保障措施。
只有通过严格的检验,确保原材料的质量合格,才能生产出安全可靠的产品,满足客户的需求。
原材料检验规范

原材料检验规范原材料检验规范是指对用于生产的原材料进行检验的一套规范和流程。
通过原材料检验规范的实施,可以确保原材料的质量符合生产需求,以提高生产效率、保障产品质量。
1. 检验程序:(1)接收原材料:接收原材料时应进行验收,确认原材料是否符合规定的来料标准和数量要求。
(2)取样:根据取样方案,从接收的原材料中取样,并确保取样方法准确、代表性。
(3)检验项目和方法:根据产品要求和原材料特性,确定相应的检验项目和检验方法。
(4)检验记录:对每个原材料进行检验,记录检验项目、结果和检验人员信息。
2. 检验项目:(1)外观检验:检查原材料的外观是否有异常,如杂质、变色等。
(2)尺寸检验:测量原材料的尺寸,确认其是否符合规定的尺寸范围。
(3)化学成分检验:通过化学分析方法,检测原材料中的化学成分,确保其符合产品要求。
(4)物理性能检验:如强度、韧性、硬度等,根据产品要求确定相应检验方法。
(5)微生物检验:对一些易受微生物污染的原材料,进行微生物检验,确保原材料不含有害微生物。
(6)包装检验:检查原材料的包装是否完好,是否符合规定的包装要求。
3. 检验设备和工具:检验原材料时,需要使用各种检验设备和工具,如显微镜、测量仪器、化学分析仪器等。
这些设备和工具应符合标准并定期维护和校准,以确保其准确性和可靠性。
4. 检验依据和标准:原材料的检验依据主要包括生产标准、国家法规、行业标准和企业内部质量管理文件等。
检验应根据相关标准和规范进行,确保检验结果的科学性和可比性。
5. 不合格品处理:若原材料检验不合格,应按照不合格品管理程序进行处理。
可以选择退货、返工或者废弃等不同方式,依据不合格品管理程序进行处理,以避免不合格原材料对产品质量产生影响。
6. 数据分析和持续改进:定期对原材料检验数据进行分析,查找数据中的规律和异常情况,以寻找潜在问题,并采取相应的改进措施,以提高原材料检验的质量和效率。
综上所述,原材料检验规范是保证原材料质量符合生产需求的标准和流程。
原材料检验规范

原材料检验规范
1.材料标识:
每批次的原材料必须有明确的标识,包括材料牌号、生产日期、供应商信息等,以便追溯和管理。
2.外观检查:
检验人员对原材料进行外观检查,包括表面是否有明显划痕、裂纹、凹痕等缺陷,同时检查原材料的形状、尺寸是否符合要求。
3.化学成分分析:
采用光谱分析仪对原材料进行化学成分分析,检测元素含量是否符合标准要求。
关注的主要元素包括碳(C)、硅(Si)、锰(Mn)、磷(P)、硫(S)等。
4.金相组织检查:
取样后进行宏观和显微观金相分析,观察和评估原材料的晶粒结构、晶界清晰度、相分布等情况,判断其是否符合要求。
5.机械性能测试:
进行拉伸试验和弯曲试验,测试原材料的屈服强度、延伸率、韧性等机械性能指标,并与标准要求进行比较和评估。
6.表面处理检查:
若原材料经过表面处理,如镀锌、氧化等,需检查处理层的厚度、附着力、耐腐蚀性等性能是否符合要求。
7.包装和存储:
原材料在运输和储存过程中需要符合相应的包装要求,并采取合适的储存方式,以确保原材料的质量不受损。
8.记录和报告:
对每批次的原材料检验结果进行详细记录,并及时报告给相关部门,以便进行下一步的制造工序和质量控制。
以上仅为一份冷轧板原材料检验规范的示例,具体的检验要求可以根据实际情况进行调整和补充。
重要的是要确保原材料的质量符合要求,以保证最终产品的质量稳定和可靠性。
原料检验标准

原料检验标准1. 引言原料检验是确保生产过程中使用的原材料符合质量要求的重要环节。
本文旨在建立一套适用于原料检验的标准,以保证产品的质量和安全性。
2. 检验要求2.1 外观检验外观是原料质量的直观反映,应采用目测或仪器测量的方式进行检验。
合格的原料应具备以下特征:(1)无异味、无明显色差;(2)无可见杂质、异物。
2.2 化学成分检验化学成分检验是判断原料是否符合规定标准的重要指标。
根据不同原料的特性,可以采用以下检验方法:(1)质量分析:通过质谱仪、红外光谱仪等仪器进行定性和定量分析;(2)元素含量:采用原子吸收光谱、电感耦合等离子体发射光谱等方法测定元素的含量;(3)溶解度:通过溶解度实验判断原料的纯度。
2.3 微生物检验微生物检验是针对易受微生物污染的原料进行的一项重要检测。
常用的检验项目包括:(1)菌落总数:采用菌落数平板计数法进行测定;(2)霉菌和酵母菌数量:通过涂布法或培养法进行监测;(3)致病菌:采用PCR、酶联免疫吸附试验等方法进行检测。
3. 检验方法3.1 取样方法取样应符合国家标准和相关技术要求,避免样品受到外界因素的影响。
取样过程应注意卫生和防止污染。
3.2 检验设备与仪器检验设备与仪器应经过校准和验证,确保其准确度和可靠性。
相关仪器的使用和维护应按照操作规程进行。
3.3 检验流程检验应严格按照标准流程进行,包括样品准备、实验操作、数据记录和结果分析等环节。
检验人员应熟悉操作规范,遵守实验室操作规程。
4. 检验结果与判定标准检验结果应准确无误地记录在检验报告中,并根据相关标准进行判定。
如果原料不满足标准要求,则应采取相应措施,如退货、调整生产工艺等。
5. 报告与记录对每批原料的检验结果应及时编制检验报告,并保留相关记录。
检验报告应包含样品信息、检验规范、检验结果和判定结论等内容,并签字确认。
6. 质量控制与改进为了提高原料的质量稳定性和生产过程的可控性,应建立全面的质量控制体系,包括供应商评估、原料登记及跟踪、异常原料处理等。
原材料质量检验规范

原材料质量检验规范一、前言原材料质量对于产品的最终品质具有重要影响。
为了确保产品的质量稳定和满足客户需求,制定本原材料质量检验规范。
二、适用范围本规范适用于所有涉及原材料采购和使用的相关部门,包括但不限于采购部门、生产部门等。
三、定义1. 原材料:指用于产品生产的原始物料,包括但不限于主要配方原料和辅助原料。
2. 质量检验:对原材料进行的系统性、规范化的检查和测试,以确保其符合相关质量标准和要求。
四、原材料质量检验要求1. 供应商选择a) 与供应商建立长期稳定的合作关系,确保供应链的可靠性和稳定性。
b) 严格审核供应商的资质和质量管理体系,确保供应商具备提供优质原材料的能力。
c) 对新供应商进行试验采购,并评估其产品的质量水平,必要时进行现场考察。
2. 样品提取和保管a) 从供应商处按照一定比例提取原材料样品,确保样品具有代表性。
b) 对样品进行封存和标识,包括样品来源、采样时间等信息,以便日后查询和追溯。
3. 检验项目和方法a) 根据原材料的特性和使用要求,确定相应的检验项目和方法。
b) 检验项目包括外观、化学成分、物理性能、微生物指标等。
c) 使用合适的检验设备和仪器,确保检验结果准确可靠。
4. 检验结果评定a) 对检验结果进行合理评定,判断原材料是否符合质量标准和要求。
b) 对不合格的原材料及时采取措施,如拒收、退货等,确保不符合要求的原材料不进入生产环节。
5. 检验记录和报告a) 检验人员应严格按照要求记录检验过程和结果,确保数据的真实性和完整性。
b) 生成检验报告,并将报告归档,以备后续查阅和审计。
六、质量改进和持续监控1. 定期评估供应商的绩效和配合度,与供应商进行沟通和协商,推动其持续改进质量管理体系和产品质量水平。
2. 对不合格原材料的处理进行追踪和分析,找出问题的根本原因,并采取纠正措施,以避免类似问题的再次发生。
3. 建立原材料质量监控指标体系,定期进行质量分析和评估,及时发现和解决质量问题,提高产品质量。
原材料检验规程
原材料检验规程1.介绍本文档旨在规范原材料的检验过程,以确保所采购的原材料符合质量标准和要求。
这些规程适用于所有采购的原材料,包括但不限于......2.检验要求2.1 原材料质量标准:描述原材料必须满足的质量和物理性质要求,如外观、尺寸、硬度等。
2.2 抽样检验:规定抽取样本的方法和标准,以确保样品能够代表整批原材料,并进行必要的实验室测试。
2.3 检验指标及方法:列出各项检验指标,以及相应的测试方法和设备。
包括理化性质、成分分析、微生物指标等。
2.4 检验记录和文件管理:要求记录所有检验结果和相关数据,并妥善管理,以备查阅和追溯。
3.检验流程3.1 接受原材料:原材料送货到货检验部门后,进行外观检查和标示确认,并填写接收记录。
3.2 抽样检验:按抽样计划进行样品的选取和编号,并记录相应的抽样方法和依据。
3.3 实验室测试:将样品送至实验室进行必要的测试,如化学分析、物理性能测试等。
测试结果应及时记录。
3.4 检验结果评定:根据检验指标和质量标准,评定样品是否合格。
如有不合格情况,应及时通知供应商。
3.5 检验报告和文件管理:生成检验报告,并妥善管理,以便追踪和核查。
4.供应商管理4.1 供应商评估:对原材料供应商进行评估,包括质量管理体系、生产设备、技术能力等方面的考察。
4.2 监督抽检:定期进行对供应商的原材料进行监督抽检,以确保其质量的稳定性。
4.3 不合格原材料处理:对于不合格的原材料,采取相应的措施,如退货、整改要求等。
5.培训与改进5.1 培训计划:制定定期培训计划,提高检验人员的专业知识和技术水平。
5.2 检验流程改进:根据经验和反馈,不断改进检验流程和方法,提高效能和精确度。
5.3 不良事件管理:建立不良事件管理机制,及时处理和纠正不良发生的问题。
6.附则6.1 本规程的制订和修改应经质保部门评审批准。
6.2 本规程应向供应商进行宣贯,并确保其理解和执行。
6.3 如原材料的质量标准和要求发生变更,应及时更新本规程。
原材料送检规范
原材料送检规范原材料送检是指将供应商或生产单位提供的原材料送往质量检测机构进行检验,以确保原材料的质量合格。
原材料的质量直接关系到产品的质量,因此原材料的送检工作十分重要。
下面是一份原材料送检的规范,以供参考。
一、送检前的准备工作1.委托书:供应商或生产单位需提供委托书,明确指示送检的原材料及要求。
2.样品选择:供应商或生产单位需按照规定的比例,按照随机抽样的方法选择样品。
3.样品数量:根据原材料的特性和送检的要求,确定合理的样品数量。
二、送检过程1.样品接收:接收样品时应认真核对样品数量和样品信息,确保与委托书一致。
2.样品分装:根据实验项目的要求,对样品进行分装,确保样品的完整性和代表性。
3.实验项目:根据原材料的性质和送检要求,选择相应的实验项目进行检测。
4.实验方法:检验人员应按照规定的实验方法进行检测,确保测试结果的准确性。
5.测试仪器:使用规定的测试仪器进行检测,保证测试结果的可靠性。
6.测试条件:根据实验项目的要求,设置合适的测试条件,确保测试结果的准确性和可比性。
7.检验记录:检验人员应认真记录检测过程中的相关数据和结果,确保数据的真实可靠。
8.数据分析:对检测数据进行分析,得出相应的结论和评估。
三、送检结果处理1.合格判定:根据原材料的质量标准和检测结果,进行合格与否的判定。
2.不合格处理:若原材料不合格,应按照质量管理体系的要求进行不合格品处理,包括退货、返工等。
3.结果反馈:将检测结果及时反馈给供应商或生产单位,以供其参考和改进。
四、送检报告1.报告编制:检验人员应按照规定的格式编制送检报告,包括样品信息、测试项目和结果等。
2.报告审核:送检报告应经过质检部门的审核,确保报告的准确性和完整性。
3.报告发送:送检报告应及时发送给供应商或生产单位,并保存备查。
以上是原材料送检的规范,通过规范的操作流程,能够确保原材料的质量符合要求,并为产品质量提供可靠的保障。
同时,也能及时发现问题原材料,促进供应商或生产单位的改进,提高整体供应链的质量水平。
原材料进货检验规范
原材料进货检验规范原材料进货检验是产品质量控制的第一道关口,对于确保产品质量和安全具有重要意义。
因此,建立一套科学合理的进货检验规范对企业来说至关重要。
本文将从规范的制定、检验项目的确定、检验方法的选择以及检验结果的处理等方面进行详细阐述。
一、规范的制定1.明确检验目的和要求:企业应明确原材料进货检验的目的是为了确保原材料的质量和安全符合生产要求。
2.参考相关法规和标准:制定规范时企业应参考国家法规和相关行业标准,确保检验规范符合法律要求并满足行业标准。
3.根据实际情况制定细则:考虑到企业的具体情况和原材料的种类,制定具体的进货检验规范,包括检验的范围、项目、要求等。
二、检验项目的确定1.根据风险评估确定重点项目:通过风险评估,确定对于产品质量和安全具有重要影响的检验项目,将其列为重点检测项目。
2.参考相关法规和标准确定项目:参考国家法规和行业标准,确定必须检测的项目,如重金属含量、残留农药、致敏物质等。
3.根据原材料的特性确定项目:根据原材料的特性,确定需要检测的项目,如粒度、含水率、颜色、外观等。
三、检验方法的选择1.选择合适的分析方法:根据检验项目的要求,选择合适的分析方法,确保检验结果的准确性和可靠性。
2.参考国家法规和标准的方法:参考国家法规和标准中所推荐的检验方法,确保检验的科学性和规范性。
3.根据企业实际情况选择方法:考虑到企业的实际情况,如仪器设备、人员技术水平等,选择适合企业的检验方法。
四、检验结果的处理1.合格原材料的处理:对于合格的原材料,进行相应的登记和记录,并及时安排入库。
2.不合格原材料的处理:对于不合格的原材料,应及时通知供应商,协商解决办法。
同时,记录不合格情况,并按照规定进行退货处理。
3.异常情况的处理:对于出现异常情况的原材料,应及时调查原因,并根据实际情况决定是否需要进行特殊处理。
综上所述,原材料进货检验规范的制定对于企业确保产品质量和安全至关重要。
通过明确检验目的和要求,参考相关法规和标准,并根据实际情况进行制定规范。
2-原材料进料检验规范及标准
1.目的为了规范采购的原材料检验方式和标准,保证所购入的原材料符合本公司的要求。
2.范围适用于本公司所购原材料的进厂检验。
3.职责3.1货仓部:来料的验收、保存等作业。
3.2 IQC:来料品质判定、标识及处理。
3.3生产部/品质部:来料的终审决定。
4.定义无5.程序5.1检验内容及要求5.1.1铜线采购标准5.1.1.1外观要求:光亮光洁、无氧化斑迹、毛刺及碰伤,包装应有防潮防护措施。
5.1.1.2尺寸要求:外径符合要求,采用千分尺进行检验。
圆铜线的直径及公差应满足下表要求。
5.1.1.3性能要求:质地均匀,纯度高,无空心现象。
5.1.1.4伸长率应满足下表要求5.1.1.5电阻率要求:电阻率ρ20℃≤0.017241Ω·mm2/m;计算时,20℃时的铜线物理参数应取以下数值:密度8.89g/cm3,线膨胀系数为0.000017/℃,温度系数为0.00393/℃。
5.1.1.6包装:有产品合格证、并标明生产厂家、型号规格、重量、名称、生产日期。
5.1.1.7贮存期:半年。
5.1.2绝缘漆5.1.2.1绝缘漆采购标准5.1.2.1外观要求:颜色均匀透明的液体,无机械杂质和不溶解粒子。
采取目测方式进行检验,按《抽样计划》检验。
5.1.2.2粘度:;聚氨酯漆(40±1℃;4号粘度杯);20 ~ 60s;5.1.2.3包装:装绝缘漆的容器应洁净、无锈迹不得有泄漏现象。
采取目测方式进行检验,按《抽样计划》检验。
5.1.2.4合格证:有产品合格证,标明批号、生产厂家、名称、型号、重量、生产日期。
5.1.2.5贮存期:一年。
5.1.3自粘漆采购标准:5.1.3.1外观要求:颜色均匀透明的液体,无机械杂质和不溶解粒子。
采取目测方式进行检验,按《抽样计划》检验。
5.1.3.2粘度:醇溶自粘漆(40±1℃;4号粘度杯);20 ~ 120s热熔自粘漆(40±1℃;4号粘度杯);20 ~ 120s5.1.3.3包装:装绝缘漆的容器应洁净、无锈迹不得有泄漏现象。
- 1、下载文档前请自行甄别文档内容的完整性,平台不提供额外的编辑、内容补充、找答案等附加服务。
- 2、"仅部分预览"的文档,不可在线预览部分如存在完整性等问题,可反馈申请退款(可完整预览的文档不适用该条件!)。
- 3、如文档侵犯您的权益,请联系客服反馈,我们会尽快为您处理(人工客服工作时间:9:00-18:30)。
原材料检验规范
1.1原材料材质报告应符合GB/T699优质碳素结构钢GB/T700普通碳素结构钢和GB/T3077合金结构钢要求。
板材外形尺寸应符合GB/T709热轧钢板品种,抽查率100%。
圆钢外形尺寸应符合GB/T702热轧圆钢抽查率100%见CHFT-ZY-01-8.
2.4-200
3.
4.1.4 型材尺寸应符合GB/T9787-1988热轧等角钢,GB/T706-1988热轧工字钢,GB/T707-1988热轧槽钢,GB/T3277-1991花纹钢板,GB/T8162-1999结构用无缝钢管,GB/T8163-1999输送液体用无缝钢管,GB/T3091-2001低压流体输送用无缝钢体管,抽查率100%.4.1.5不合格品按<不合格品控制程序>执行.
1.2用于焊接结构的各种钢材在划线下料前,其钢板局部的平面度,型钢各种变形超过下列规定,均须矫正,达到要求的允许偏差才可划线。
a)厚度小于14mm的钢板,钢带的直线度,每1m长度内,小于1.5mm。
厚度大于14mm的,每1m长度内,不大于1mm。
b)角钢,槽钢,工字钢,管子的直线,每1m长度内,不大于1mm,且最大不大于5mm。
c)角钢两腿的垂直度,不大于腿宽度的1%。
d)工字钢,槽钢翼缘的倾斜度,不大于翼缘宽度的1.25%。
1.2.1用于焊接结构的钢材的钢号,规格,尺寸应符合图样要求.若不符合要求时,应按工厂材料代用制度代用.材料代用应有责任工程师签字.
1.2.2用焊接结构件的焊条应符合图样规定。
图样未做出规定的,应符合GB5117《低碳钢焊条》,GB5118《低合金钢焊条》,GB948《对焊焊条》的规定。
1.2.3用于焊接结构件的钢材和焊接材料,须经技术检查部门依据其质量证明书检验后方可使用。
对方无牌号,无质量证书的钢材和焊接材料,须进行检验和鉴定,确定其牌号后方可使用。
1.2.4钢材上必须有清晰,牢固的标志。
严禁使用牌号不明,为经技术检查部门验收的各种材料。
1.2.5成批验收的钢板,每批钢板应有统一炉号,同一厚度,统一热处理制度的钢板组成。
1.2.6图样规定有力学性能和工艺性能要求,应做力学和工艺性能试验。
试验项目和试验方法应符合GB150,GB223,GB228,GB232,GB/2106,GB4159,GB4338,GB/T2970的相关规定。
2.2钢材表面质量。
2.2.1钢材表面应平整,端头和边缘整齐,不允许存在有凹凸,裂纹,气泡,结疤,折叠和夹杂等缺陷,不允许有分层,无严重锈蚀。
2.2.2有上述表面缺陷的钢板,允许清理。
清理深度从钢板实际尺寸算起,不得超过钢板厚度公差之半,并应保证钢板的最小厚
度。
缺陷清理处应平滑无棱角。
其他缺陷允许存在,但其深度从钢板实际尺寸算起,不得超过钢板厚度允许公差之半。
并应保证缺陷出钢板的最小厚度。
2.3 钢材检验后应做好检验记录。
(表1)
钢材检查记录
产品(零部件)编号表1
2.4 下料前,钢材的变形超过允许偏差时,必须矫正后方可使用。
矫正的方法分冷矫正和热矫正两种:
a. 钢材冷矫正应使用辊式矫正机或压力机进行。
也可采用手工矫正,但锤痕深度不得超过下列规定。
钢板、钢带厚度小于10㎜的,锤痕深度不大于0.5㎜。
厚度大于10㎜的,锤痕深度不大于1㎜。
型钢腿或翼上,锤痕深度不大于1㎜。
腹板上,锤痕深度不大于0.5㎜。
b.当钢材变形程度大或设备能力不足时,可采用热矫正。
热矫正时,应将钢材加热到900~1100℃进行矫正(普通低合金钢采用较低温度)。
矫正后的钢材表面不得有凹凸伤痕和锤迹。
当钢材的温度在300~500℃或低于-25℃时,不允许对钢材进行任何打击。
c.对允许局部加热的钢材,其局部变形可用火焰矫正。
火焰矫正时,常采用600~800℃的加热温度,一般不超过850℃。
2.5 成批生产的零部件,必须依下料样板下料。
下料样板必须按下料、划线、和装配工序分别制作。
各类样板均用薄铁皮制作。
2.5.1 下料样板的制作须考虑到结构件在焊接时所产生的收缩量。
收缩量大小按工艺要求的规定。
2.5.2 焊接结构件的装配间隙在设计图样中不作考虑。
但制作下料样板时应予以考虑。
装配间隙允许为1~1.5㎜。
(图1)
图1
2.5.3 样板的制作还须考虑切割余量、火焰矫正收缩余量及加工余量。
2.5.4 样板的外围尺寸偏差应在-0.5~ -1㎜范围内。
2.5.5 钻孔用划线样板的孔距应符合图样要求。
若图样无公差要求的,两孔中心距偏差为±0.5㎜。
孔中心线与板边缘的距离偏差为±1㎜。
2.5.6 每个样板都必须注明工号、图号、材料断面尺寸、钢号和用该样板所制造零件的每台数量。
样板须经检验合格后方可使用。
2.6 号料前应仔细检查下料样板是否有变形。
号料时,应划出实际用料线、余量线、中心线及弯曲线,并注明接头处的字母和焊缝代号,如零件在现场装配(或现场加工),应根据图样要求注明。
号好料的钢材,应注明工号、图号、名称、件号、规格、钢号、每件台数。
并应进行钢号移植。
钢材下料可用机械剪切或气割,厚度大于16㎜的钢材应优先采用气割。
2.7 钢材切断后,边棱应与表面垂直。
切断面的倾斜度应不大于1:10。
边棱上的堆积物、毛刺和凹凸不平须铲除。
2.8 机械剪切后,切断边的表面允许有深度不超过1㎜的压痕和高度不大于0.5的毛刺。
2.9机械剪切线与号料线,偏差不大于表2规定
表2 ㎜
2.10 气割线允许偏差如下:
a.用手工切割时,不得超过±1.5㎜。
b.自动或半自动切割时,不得超过±1.0㎜。
2.11 气割的质量按JB3092《火焰切割面质量技术要求》中的规定。
对非焊接面的切割表面上的缺陷,必须焊补修平。
2.12 图样未注明的焊接结构零件的尺寸偏差按表3规定。
表3 ㎜
注:尺寸偏差对孔、槽取“+”值,轴、厚度、长度取“-”值,不通孔深度取“+”值。
2.13 厚度大于16㎜的钢板剪切后,含碳量大于0.27﹪的钢材气割后,以及必须除去的扁钢两边的弯曲度又无法用辊子矫正时,必须刨边。
其它钢材切割后要求刨边的,应注明。
2.14 钢材刨边后,边棱直线度不大于构件长度的1/2000,最大不得超过1.5㎜。
刨过边的零件尺寸与设计尺寸相差不得超过1.5㎜。
2.15 焊接坡口的尺寸偏差应符合GB/T985-1988《手工电弧焊、焊接接头的基本型式与尺寸》的规定。
2.16 钢材成型弯曲时,应符合相关规定。
弯曲成型的筒体尺寸偏差(表4)
管子弯曲半径偏差,圆度偏差及允许的波纹深度(表5)
弯曲成型的筒体尺寸偏差
表4 ㎜
管子弯曲半径偏差,圆度偏差及允许的波纹深度
表5 ㎜。