船舶分段设计
《船体分段划分》课件

船体结构检验
• 检查船体分段的结构强 度和完整性,确保符合 相关规范要求。
防范灾害检验
• 检查船体分段的安全性, 包括防火、防泄漏等。
使用功能检验
• 检查船体分段的使用功 能,确保满足船舶的工 作需求。
适应不同载货和运输需求。
并在发生事故时减少船体
的泄漏和沉没风险。
分段划分的基本原则
单元一致性
每个船体分段应具备一致和相对独立的结构和 功能。
结构强度
分段划分应满足船舶的结构强度要求,确保船 体的安全性。
材料经济性
分段划分应考虑材料的使用效率和成本,实现 材料经济性。
施工和维护便利性
分段划分应考虑施工和维护的便利性,减少工 期和维护成本。
船体分段划分的目的和意义
1 提高结构强度和安全 2 提高施工和维护效率 3 增加设计灵活性
性
分段划分可以使船舶的建
船体分段划分可以提高设
通过分段划分,可以将船
造和维护过程更加简化和
计的灵活性,使得船舶可
体结构分解为若干独立部
高效,提高施工安全性和
根据具体需求进行改造,
分,提高整体结构的强度,
减少维护成本。
船体分段划分
船体分段划分是指将船体划分为不同的部分,对船体进行分段设计和制造。 本课件将详细介绍船体分段的目的、原则、标准、种类以及相关的设计、制 造、管理和维护等方面内容。
什么是船体分段划分
船体分段划分是将船体划分为若干段或区域,以方便船舶的设计、制造、管理和维护。通过分段划分,可以有 效提高船体的结构强度、安全性以及施工和维护的效率。
对分段完工的船体部分进行测试和验收,确 保质量和安全性。
船舶分类社的分段要求
规范要求
分段造船工艺

分段造船工艺船舶建造是一个复杂的过程,其中分段造船工艺是关键步骤之一。
分段造船工艺是指将船体分成若干个独立的模块,然后分别进行制造和装配的工艺流程。
这种工艺使船舶建造更加高效、灵活和可控。
下面将详细介绍分段造船工艺的步骤和特点。
一、分段制造步骤1. 设计方案确定:在分段造船工艺开始之前,首先需要确定船体的设计方案。
设计方案包括船舶的结构设计、管道系统设计、电气系统设计等。
这些设计方案将作为分段制造的依据。
2. 分段制造计划编制:根据设计方案,制定分段制造计划。
计划包括分段的数量、尺寸、制造工艺和装配顺序等。
分段制造计划的编制需要考虑到船体的结构强度、制造工艺的可行性以及工期的安排等因素。
3. 材料准备:在分段制造之前,需要准备好所需的材料。
这些材料包括钢板、型钢、焊材、涂料等。
材料的选择需要根据设计要求和船舶的使用环境来确定。
4. 分段制造:根据分段制造计划,将船体分成若干个独立的模块进行制造。
制造过程包括钢板切割、型钢加工、焊接、校直和涂装等。
每个模块的制造过程需要严格按照设计要求和工艺规范进行。
5. 分段装配:分段制造完成后,将各个模块进行装配。
装配过程包括模块之间的焊接、螺栓连接、管道安装、设备安装等。
装配的顺序需要根据设计要求和工艺规范来确定,以确保各个模块能够准确无误地连接在一起。
6. 分段试验:在分段装配完成后,需要进行分段试验。
试验内容包括结构强度试验、水密性试验、设备功能试验等。
试验的目的是验证分段制造和装配的质量,以确保船体的安全性和可靠性。
二、分段造船工艺的特点1. 提高生产效率:分段造船工艺将船体分成若干个模块,不同模块可以同时制造和装配,大大提高了生产效率。
同时,分段制造可以将船体制造的风险和难度分散到各个模块中,降低了制造过程中的错误和损失。
2. 灵活性和可控性强:分段造船工艺使船舶建造过程更加灵活和可控。
每个模块都是独立制造和装配的,可以根据需要进行调整和优化。
同时,分段制造可以根据工期和资源的限制来安排制造计划,确保项目的顺利进行。
船舶分段生产工艺
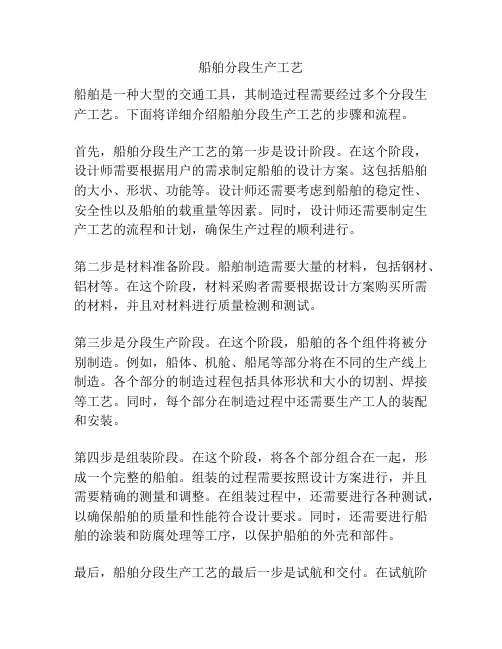
船舶分段生产工艺船舶是一种大型的交通工具,其制造过程需要经过多个分段生产工艺。
下面将详细介绍船舶分段生产工艺的步骤和流程。
首先,船舶分段生产工艺的第一步是设计阶段。
在这个阶段,设计师需要根据用户的需求制定船舶的设计方案。
这包括船舶的大小、形状、功能等。
设计师还需要考虑到船舶的稳定性、安全性以及船舶的载重量等因素。
同时,设计师还需要制定生产工艺的流程和计划,确保生产过程的顺利进行。
第二步是材料准备阶段。
船舶制造需要大量的材料,包括钢材、铝材等。
在这个阶段,材料采购者需要根据设计方案购买所需的材料,并且对材料进行质量检测和测试。
第三步是分段生产阶段。
在这个阶段,船舶的各个组件将被分别制造。
例如,船体、机舱、船尾等部分将在不同的生产线上制造。
各个部分的制造过程包括具体形状和大小的切割、焊接等工艺。
同时,每个部分在制造过程中还需要生产工人的装配和安装。
第四步是组装阶段。
在这个阶段,将各个部分组合在一起,形成一个完整的船舶。
组装的过程需要按照设计方案进行,并且需要精确的测量和调整。
在组装过程中,还需要进行各种测试,以确保船舶的质量和性能符合设计要求。
同时,还需要进行船舶的涂装和防腐处理等工序,以保护船舶的外壳和部件。
最后,船舶分段生产工艺的最后一步是试航和交付。
在试航阶段,船舶将进行各种测试和调整,以确保船舶的稳定性和性能。
一旦测试通过,船舶将交付给用户,准备投入使用。
总而言之,船舶分段生产工艺是一个复杂而精细的过程,需要多个环节的配合和协调。
从设计、材料准备、分段生产、组装到试航和交付,每个阶段都需要严格按照工艺流程进行。
只有这样,才能保证船舶的质量和性能符合设计要求。
船舶分段吊装翻身设计方法

船舶分段吊装翻身设计方法随着船舶工程的不断发展,船舶分段吊装翻身设计方法已经成为了船舶建造过程中不可或缺的一部分。
在船舶建造过程中,船舶分段吊装翻身设计方法可以帮助工程师们更好地完成船舶的建造工作,提高船舶的建造效率,降低船舶建造成本。
本文将介绍船舶分段吊装翻身设计方法的相关内容,帮助读者了解这一技术的基本原理和实际应用。
一、船舶分段吊装翻身设计方法的基本原理船舶分段吊装翻身设计方法是指在船舶建造过程中,将船体分成若干个部分进行吊装和翻身的一种技术。
这种技术的基本原理是将船体分成若干个部分,然后将每个部分吊装起来,进行翻身操作,最终完成整个船体的建造。
这种技术的优点在于可以提高船舶的建造效率,降低建造成本,同时也可以减少建造中的安全隐患。
二、船舶分段吊装翻身设计方法的实际应用船舶分段吊装翻身设计方法在实际应用中有着广泛的应用。
下面我们将通过实例来介绍这种技术的应用过程。
以某船舶为例,该船舶总长300米,总宽60米,总吨位为20万吨。
在建造过程中,该船舶被分成了若干个部分,每个部分的长度为50米,宽度为30米,高度为20米。
在吊装和翻身的过程中,需要使用多台吊车,每台吊车的起重能力为600吨。
在进行吊装和翻身操作之前,需要对各个部分进行详细的计算和设计,确定吊装和翻身的具体方案。
在进行吊装和翻身操作时,需要先将各个部分分别吊装到指定的高度,然后进行翻身操作。
在翻身操作中,需要将各个部分按照一定的顺序进行翻转,最终完成整个船体的建造。
三、船舶分段吊装翻身设计方法的注意事项在进行船舶分段吊装翻身设计方法时,需要注意以下事项:1.在进行吊装和翻身操作时,需要对各个部分进行详细的计算和设计,确定吊装和翻身的具体方案。
2.在进行吊装和翻身操作时,需要使用多台吊车,每台吊车的起重能力需要符合实际需要。
3.在进行吊装和翻身操作时,需要按照一定的顺序进行翻转,避免出现不必要的安全隐患。
4.在进行吊装和翻身操作时,需要进行详细的安全检查,确保各项工作的安全可靠。
船舶分段制造方法

船舶分段制造方法
船舶分段制造方法是指将一艘船舶按照设计图纸分成若干个部
分进行制造的方法。
这种方法可以提高船舶制造工艺的效率和质量,降低制造成本,同时也方便了船舶的维护和维修。
船舶分段制造一般分为以下几个步骤:
1. 设计分段方案:根据船舶设计图纸,确定船舶分段的位置、数量和大小,制定分段方案。
2. 制作模板:按照设计图纸制作模板,用于制作船舶分段的模型。
3. 切割分段:根据模板进行切割,将船舶分段进行切割和加工,制作成符合要求的零件。
4. 焊接分段:根据设计要求,将分段进行钢结构焊接,形成船舶分段的零件。
5. 组装分段:将焊接好的分段进行组装,形成完整的船舶结构。
6. 检验和验收:对船舶分段进行质量检验和验收,确保船舶分段的质量符合要求。
船舶分段制造方法可以有效提高船舶制造工艺的效率和质量,降低制造成本,也方便了船舶的维护和维修。
因此,船舶制造企业普遍采用船舶分段制造技术,以提高船舶制造的效率和质量。
- 1 -。
船体分段制作工艺流程

船体分段制作工艺流程船体分段现场制造工艺流程生产范围大组立是船舶制造的一种生产管理模式,是船体分段装配的一个生产阶段。
就是将零件和部件组成分段的生产过程。
人员搭配大组立生产以班为单位,一个班一般分为三到四个班组,一个班组的成员有一个组长、三个师傅、六个徒弟、两个电焊工、一个打磨工。
图纸资料大组立相关图纸有零件明细表、产品完工图、制作工艺、焊接工艺等。
工具割枪、米尺、线垂、千斤顶、水平尺、水平管、花兰螺丝、铁锤、铁楔、角尺、电焊机、自动二氧化碳焊接、打磨机机舱双层底大组立机舱双层底工艺流程胎架或平台准备——铺内底板——构件安装位置划线——构件安装——焊接——管铁舾装安装焊接——外板安装——焊前检查——构件与外板焊接——打磨——密性实验——交验装配作业标准分段长:L <±4mm分段宽: B <±4mm分段高:H <±4mm分段方正度:(内底板四角水平)<±8mm(加测机座内底板水平)货舱双层底大组立工艺流程胎架或平台准备——内底板拼装——自动二氧化碳焊接——构件安装位置划线——内底纵骨安装焊接——构件小组(肋板)安装焊接——舾装——补漆¬外底板拼装——焊接——构件安装位置划线——外底纵骨装焊——组装完成——焊接——打磨——舾装——完工检查——报验装配作业标准分段长:L <±4mm分段宽:B <±4mm分段高:H <±3mm分段方正度:<4mm (内、外底板对角线差值)分段扭曲度:<±8mm (内底板四角水平)纵骨端平面度:<±4mm内、外底板中心线偏差<±3mm内、外底板肋位线偏差<±3mm货舱顶边水舱大组立货舱顶边水舱分段工艺流程胎架或平台准备——斜板拼装——焊接——构件安装位置划线——斜板纵骨安装焊接——构件(肋板)安装焊接——舾装——补漆¬甲板拼装——焊接——纵骨装焊——组装完成——焊接——打磨——舾装——完工检查——报验装配作业标准分段长: L <±4mm分段宽: B <±4mm分段高: H <±4mm分段方正度:(测上甲板)<4mm分段扭曲度:(上甲班)<±8mm纵骨端平面:<±4mm货舱舭部大组立工艺流程胎架或平台准备——斜底板拼装——焊接——构件安装位置划线——斜底纵骨安装焊接——构件小组(肋板)安装焊接——舾装——补漆¬外底板拼装——焊接——构件安装位置划线——外底纵骨装焊——组装完成——焊接——打磨——舾装——完工检查——报验装配作业标准分段长: L <±4mm分段宽: B <±4mm内底高:H1±3mm舭部尖顶高:H2±4mm分段方正度:(测斜板)<4mm分段扭曲度:(测斜板)<±8mm。
6-1 分段建造的方法

侧造法
卧造法
船 体 装 配
第一节 分段建造的方法
回分类
船 体 装 配
第一节 分段建造的方法
回分类
船体 装配
第一节 分段建造的方法
回分类
装焊示例
船 体 装 配
第一节 分段建造的方法
选择分段建造方法的原则: 选择分段建造方法的原则:
正确选择分段建造方法,对于改善分段装配、焊接和安 全操作的条件,方便分段对接,减少胎架材料消耗,提高生 产场地利用率,都有极大的作用。 1、同一类型的分段,应尽可能选择相同的建造方法; 、同一类型的分段,应尽可能选择相同的建造方法; 如一条船的所有双层底分段,要么都采用正装法,要么 都采用倒装法。这样可使分段的变形一致。 2、根据各种类型分段的特点,选用尽可能少的几种类 、根据各种类型分段的特点, 型的胎架来建造分段。 型的胎架来建造分段。 如: 平面分段、带平台的半立体分段和双层底分段,用平面 胎架反造; 甲板分段和上层建筑分段,可根据它们具有相同抛势的 特点,采用通用胎架或在同一胎架上,稍加修改后合造; 曲度变化较大的舷侧分段和底部纵向升高值较大的底部 分段,可在正斜切或斜斜切胎架上建造。
构件装配方法
分段的装配程序一般是铺板、画线、安装构架。 按构件安装的情况,分为:
构件装配 方法
散装法 分离法 放射法
框架法 插入法
(1)分离法(separate method of assembling) )分离法( )
先装配布置较密的主向构件并进行焊接,再安装交叉构件并进 行焊接。 特点: ① 特点 主向骨架先装;装配与焊接交替进行。 【顺口溜】 主向先装后施焊, 焊完再装另一向; 骨架型式定主次, 目前应用较广泛。 ② 优点 扩大自动焊、半自动焊的使用范围, 减小分段的总体焊接变形和提高工效。 ③ 缺点 装配、焊接工作分离,使装配作业不连续; 主向骨架的焊接变形可能影响后继阶段的装配工作。 ④ 适用范围 结构刚性大钢板厚的平直分段;多用于纵骨架式 。
一种船舶分段建造的指导方法与流程

一种船舶分段建造的指导方法与流程摘要船舶的分段建造是船舶制造的重要工艺环节,对船体的质量和良好的结构起着关键作用。
本文提出了一种船舶分段建造的指导方法与流程,旨在帮助船舶制造企业提高生产效率、降低成本、提高产品质量。
本方法以实践为基础,结合了船舶制造工程的经验和技术,通过详细的流程和步骤,将船舶分段建造过程分解为若干个可控的任务,以提高建造过程的组织性和系统性,实现分段建造的高效率和高质量。
1. 引言船舶制造是一个复杂而庞大的工程项目,涉及材料、工艺、设备等多个方面的技术要求。
分段建造是船舶制造中的重要环节,指的是将整个船体分解为若干部分进行独立建造,然后再进行组装。
良好的分段建造方法和流程能够提高船体质量,减少生产周期,降低制造成本,并且有利于质量管理和后续工序的衔接。
本文提出了一种船舶分段建造的指导方法与流程,通过详细的步骤和流程,对船舶分段建造过程进行了合理的规划和组织。
2. 船舶分段建造的指导方法2.1 分段设计分段设计是船舶分段建造的首要步骤。
制定细致的分段方案,合理划分出各个分段单元,对后续的建造工作具有重要意义。
在分段设计中,需要考虑以下几个要点:•分段尺寸和形状:根据船舶的设计要求和需要,确定每个分段的尺寸和形状。
•分段的结构类型:根据船舶的用途和设计要求,确定每个分段的结构类型,如船首段、中段、船尾段等。
•分段的拆解和组装性:考虑到后续的拆解和组装工作,对分段进行合理设计,使得分段的拆解和组装过程更加顺利。
2.2 材料准备在船舶分段建造过程中,需要准备各种材料,包括船体板材、焊接材料、涂料等。
在材料准备阶段,需要根据船舶分段的设计要求,选择合适的材料,并进行采购和准备工作。
材料准备的主要步骤包括:•材料选择:根据船舶的设计要求,选择适合的材料,包括船体板材、焊接材料、涂料等。
•材料采购:按照船舶分段的设计需求,进行材料采购,保证材料的质量和供应的及时性。
•材料验收:对采购的材料进行验收,确保材料符合设计和质量要求。
- 1、下载文档前请自行甄别文档内容的完整性,平台不提供额外的编辑、内容补充、找答案等附加服务。
- 2、"仅部分预览"的文档,不可在线预览部分如存在完整性等问题,可反馈申请退款(可完整预览的文档不适用该条件!)。
- 3、如文档侵犯您的权益,请联系客服反馈,我们会尽快为您处理(人工客服工作时间:9:00-18:30)。
大连海事大学毕业论文二○年月船舶分段设计学院:大连海事大学专业:船舶海洋工程姓名: 张学驹指导教师:引言船舶工业是为水上交通、海洋开发和国防建设等行业提供技术装备的现代综合性产业,也是劳动、资金、技术密集型产业,对机电、钢铁、化工、航运、海洋资源勘采等上、下游产业发展具有较强带动作用,对促进劳动力就业、发展出口贸易和保障海防安全意义重大。
我国是一个水路资源比较丰富的国家,可用来作为水路运输的江、河总长达十万公里。
我国对外贸易货物的百分之九十是依靠海运来完成。
船舶工程是研究、设计和制造水上交通运输工具的一项大型综合性系统工程,其主要研究对象是研究船舶的经济性、快速性、可靠性、安全性和舒适性。
我国的海洋资源比较丰富,其专属海洋经济开发区的面积接近500万平方公里,几乎是我国陆地面积的百分之五十。
随着陆地石油及其它稀有资源的逐步减少直至最终枯竭,人们已经并将把未来石油及其它稀有资源的开发转向海洋。
海洋工程是研究、设计和建造海洋资源开发工作平台和工具,比如离岸石油钻井平台、海上施工船舶等。
船舶工业是现代大工业的缩影,是关系到国防安全及国民经济发展的战略性产业。
就现在来看,船舶工业也将要成为我国的一个支柱产业。
经过改革开放后二十多年的快速发展,船舶工业已成为我国为数不多的几个具备了较强国际竞争能力的外向型产业之一,成为世界船舶工业的一支重要力量。
目录一船舶的种类及其用途 (5)二船体结构 (7)三船舶分段的分类 (9)四船模制作的必要性 (10)五具体船模分段的设计与制作 (11)六我国船舶工业发展现状及未来展望 (18)七总结及参考文献 (20)一船舶的种类及其用途(一)按船舶用途分航空母舰巡洋舰驱逐舰水面战斗舰艇护卫舰军用快艇猎潜舰战斗舰艇登陆作战舰水雷战舰1.军用舰船水下作战舰艇供应补给运输舰侦察巡逻艇辅助舰艇训练舰靶船海洋测量船修理船救生船医院船客船客船客货船旅游船干货船液货船运输船冷藏船货船全集装箱船滚装船载驳货船2.民用船舶其他货船渡船驳船海洋资源开发船生物资源开发船海洋开发船海洋资源开发船海上海底空间利用船海洋调查船浮船坞潜水工作船航标船挖泥船起重船3.工程工作船舶海洋打捞救生船布缆船浮船坞消防船引导船其它工程工作船渔政船网渔船4.渔业船舶渔船钓鱼船特种渔船渔业辅助船5.其他船舶拖带船舶.农用船.教学实习船(二)按航行区域海船内河船(三)按航行状态排水型船水翼艇和滑行蜓气垫船冲翼艇(四)按动力装置1. 蒸汽动力船2. 内燃机动力船:⑴柴油机船⑵燃气轮机船3 .核动力装置船4 .电力推进船(五)按推进器分类目前绝大数船都以各种形式的螺旋桨作为船舶推进器,也有喷水推进和空气螺旋桨推进。
个别的采用明轮、平旋轮、帆助航等其他推进方式。
(六)按船体材料分类钢质船在各类船舶中占绝大多数,采用高强度低合金钢时,可减少船体重量,以增加有效负荷和航速。
小型船艇和某些特殊用船有以木材,铝合金、玻璃钢、丝网水泥作为建造船体的材料。
二船体结构(一)船体结构组成船体结构主要由壳板和纵横交叉的骨架组成。
其中壳板由钢板焊接而成,骨架则是由具有一定剖面形状的型材构成的。
船用轧制的型材主要有:扁钢、球扁钢、等边角钢、不等边角钢、槽钢及圆钢和管子等。
除了采用轧制型材外,受力较大的部位,还采用由钢板焊接而成的组合型材。
如图所示船体构件的命名方法:船体板架中主要构件(强构件)由组合型材构成,一般纵向称为“桁”或“龙骨”,如:甲板纵桁、舷侧纵桁,双层底船的船底有中桁材、旁桁材,单底船称为中内龙骨、旁内龙骨;横向构件有强横梁、舷侧强肋骨、底肋板等。
板架中的次要构件(普通构件)由型材构成,纵向的叫“纵骨”,如船底纵骨、舷侧纵骨、甲板纵骨等;横向的叫甲板横梁、舷侧肋骨等。
主船体结构:分为船底结构(分为单底和双底两种形式)、舷侧结构、甲板结构、现编结构、水密舱壁结构、首部结构、尾部结构。
(二)船体结构形式船体结构分为:纵骨架式、横骨架式、混合骨架式三种类型。
纵骨架式:板格长边沿船长方向,短边沿船宽方向,纵向骨材间距小,横向桁材间距大。
横骨架式:板格长边沿船宽方向,短边沿船长方向,横向骨材间距小,纵向桁材间距大。
混合骨架式:船体结构中的混合骨架式是指甲板、船底采用纵骨架式,而舷侧采用横骨架式。
三船舶分段分类方法(一)分段是构成船体结构的实体根据船舶建造工艺、场地条件、起重能力、周期要求等,一艘3—6 万吨级船舶分段划分大致在100—200 个(大型船体结构如MPF1000 钻井储油船分段划分351 个)。
(二)分段名称分段按几何特征可分为1.平面分段平面板列带有骨架的单层平面板架2.曲面分段平面板列带有骨架的单层曲面板架3.半立体分段两层或两层以上板架所组成的不封闭分段4.立体分段两层或两层以上板架所组成的封闭分段5.总段主船体沿船长划分,其深度和宽度等于该处船深和船宽的环形分段。
特别需要指出的是:立体分段和总段是由若干平面分段和曲面分段所组成,由于平面分段和曲面分段是分段建造中的基本单位,作为船舶建造主流程,必须组织流水线生产。
分段按其结构所属部位可分为(1)底部分段(2)舷侧分段(3)甲板分段(4)首尾分段(5)上层建筑等面四船模制作的重要性船模在船舶设计制作中起着重要的作用。
概括如下:通过船模静水中比较船型确定船的浮性、稳性、抗沉性。
通过船模的静水阻力试验确定船的阻力性能,计算阻力(粘性阻力、兴波阻力),确定各阻力成分的特性。
通过船模的螺旋桨模型敞水试验,确定船的速度性能。
通过船模的自航试验,确定船的航行状态、回转特性。
通过船模可确定附件的形状和安装位置为船体放样和生产设计提供指导。
对我们来说,通过设计和制作模型过程中所遇到实际问题,通过认真思考,运用所学的理论知识,一步一步的去探索,去解决问题。
这一过程是我们开始运用所学知识解决实际问题的过程,能增加我们对理论知识的理解,提高我们解决问题的能力,将理论知识和实践紧密联系起来,增加我们的创新能力。
对即将进入工厂进行顶岗实习的我们意义重大,可以使我们能更快的融入到实际的生产当中。
现在我们就以6650T散货船底部分段和首部分段的制作来具体分析。
五 6650T散货船底部分段和舷侧分段制作(一)准备阶段1.制作所需材料(1)木材制作模型骨架等,是常用的材料。
1)轻木:材质很硬、比重很轻、纹理均匀、不易变形易于加工,用来制作受力不大的零件。
2)胶合板材:较薄的胶合板材(3层)可用来制作船的龙骨,具有强度大、不易变形的特点。
(2)金属材料有强度大柔韧性好、可塑性强等特点。
1)薄铁片:用作支架、固定电机等。
2) 钢丝:用做栏杆。
(3)塑料不同成分和工艺的塑料,其性质的差异可能很大,用途也非常不同。
1)有机玻璃:聚甲基丙酸甲酯塑料,高度透明,比重轻,不易碎.110摄氏度变软,可成型加工、可加工成才各类特殊形状的沟槽和零部件。
2)玻璃钢(FRP)亦称作GRP,即纤维强化塑料,一般指用玻璃纤维增强不饱和聚脂、环氧树脂与酚醛树脂基体,一般指用玻璃纤维增强不饱和聚脂、环氧树脂与酚醛树脂基体。
3)ABS树脂(丙烯腈-苯乙烯-丁二烯共聚物,ABS是Acrylonitrile Butadiene Styrene的首字母缩写)是一种强度高、韧性好、易于加工成型的热塑型高分子材料。
因为其强度高、耐腐蚀、耐高温,所以常被用于制造仪器的塑料外壳。
(4)粘合剂在连接模型的骨架外壳及各种零件时最常用到,胶合结构具有重量轻,强度大,应力分布均匀,外型光滑整齐,工艺简单等优点.(502和氯仿)。
2.制作船模的工具(1)尺子:用来测量和划线、常用刻度尺、直角尺。
(2)剪刀:用来剪割较薄的材料,如铁皮、纸张、木片等。
(3)刀具:最普遍的是刻刀(美工刀或裁纸刀),亦可用钢锯条改制刀。
(4)钢丝钳:作用是坚固及切断,并可用于夹持折弯、切断各种金属件。
(5)锯:手锯用以切割木材、塑料、金属等材料的工具。
钢丝锯是切割曲线的主要工具。
(6)锉刀:使零件表面光洁并具备一定的尺寸和形状。
(7)台钻:用于孔的加工。
(8)镊子:夹持细小零件、接线头。
(9)电烙铁:模型上各种金属部件的结合加工.搭配焊油及锡焊使用。
(10)其它:螺丝刀、板子、砂纸、毛刷、锤子、冲子、空压机喷枪等等。
(二) 制作阶段1.读懂并绘制设计图纸(详细数据看内附图纸)(1)底部分段1内底板2内底横骨3透气孔4内底边板5舭部外板6加强筋7框架肋板8流水孔9中底桁10、15 肘板11船底肋骨12 扶强材13 边接缝14 框架肋板肘板16 加强筋 17 框架肋板18 旁底桁19 人孔20 切口21 减轻孔(2)实肋板结构(横骨架式结构)○1内底板○2 旁桁材○3 加强筋○4 中桁材○5 船底板○6 实肋板○5○2 ○3 ○4 ○6○1○7○8○15 ○14 ○13 ○12 ○11 ○10 ○9 图3.5.2 纵骨架式双层底结构○1 ○2 ○3○6 ○5 ○4图3.5.4 实肋板结构○1 ○2 ○3 ○4 ○5 ○8 ○6 ○7 图3.4.3 加强肋骨式横骨架舷侧结构(3)横骨架式船侧结构图○1 横梁○2 梁肘板○3 强横梁○4 强肋骨○5舷侧纵桁 ○6主肋骨 ○7 舭肘板○8 舭部列板(三) 过程步骤1.选取1、5mm 厚的ABS 板注意事项:表面光滑平整,无凹坑,厚度均匀。
2.放样根据图纸计算尺寸,划线,示意图如下,具体尺寸看附带图纸。
注意事项:在划线时要考虑到ABS 板厚度的影响。
3.下料用雕刻机雕刻出料块,下料完毕后。
去毛刺,用纱布打磨切边,用壁纸刀修平,切割面不得有圆角。
注意事项:保证尺寸,注意去除壁厚。
切面要平且直。
不得划伤表面。
4.组装主要用氯仿粘制。
船底分段组装顺序如图所示(船舷侧分段组装顺序与其相同),最后装上底板。
注意事项:粘贴组装时,氯仿要适量不要过多,尽量在内侧粘贴,不得将氯仿滴落在ABS板上,氯仿对其有腐蚀性形成凹坑。
胶渍要均匀适量。
5.喷涂带组装完毕后修整喷漆。
喷涂后表面色度均匀,平整无凹坑。
操作注意事项1)喷涂时,切勿将手指、手掌或身体的任何部位接触喷嘴。
2)严禁将喷枪口对着自己或他人。
3)严禁将喷嘴护套卸下后喷涂。
4)除了喷涂或清洗外,任何时候都必须将喷枪保险关上。
5)在进行任何有关设备的维修或保养前,先泄压。
6)清洗时,禁止使用漂白水或汉强酸碱之溶剂。
7)必须配备相应的电源稳压器。
施工注意事项1)在通风良好及照明充足的场所施工。
2)禁止在有火花或有可燃物的区域施工。
3)设备在无涂料的情况下空转不得超过10秒。
4)此喷涂设备不能使用含胶水成分、含颗粒溶剂或含强腐蚀性的涂料进行喷涂。
5)此喷涂设备只能使用220伏单相电,严禁接驳380伏电源,否则将烧毁电机。
6)在拔下电源插座时,切勿拉扯设备电源线。