船体分段装配图设绘要领
船体分段结构图的识读与绘制

【本项目知识点】
• 2.分段结构图的组成和表达内容 • 分段结构图主要由视图和明细栏组成,有些分段结构图中,还用文字
对分段的技术要求、工艺措施和注意事项作简要说明。 • 分段结构图的视图通常有主视图、剖面图和节点详图。视图中标注构
件尺寸、件号和构件连接的焊缝代号。 • (1)主视图 • 主视图是表示分段结构基本组成的视图,主视图中反映了构件的布置
上一页 下一页 返回
【本项目知识点】
• 所以,在主视图中不用剖切符号表示肋骨剖面的位置及视向,而只在
剖面图的上方画出视向符号(粗实线大箭头),并在其上标注剖切位
置的肋位号,如
。其中“#8”表示剖面位置在#8肋骨平面,
而“←”则表示剖面视向为向尾看,因为船体在图纸中的布置通常总
是尾左首右,箭头向左表示向尾看,箭头向右,则表示向首看。
情况、板的排列、厚度、焊接要求及板上开口的位置和大小。
上一页 下一页 返回
【本项目知识点】
• 一般来说,甲板、平台、上层建筑、底部分段和基座结构常以基本结 构图中相应位置的甲板图、平台图或舱底图为依据,用较大比例绘制 而成;舷侧分段常以外板展开图中相应位置的图形为依据,用较大比 例绘制而成,也可以从舷侧有构架的一面进行投影所得的视图作为主 视图;横舱壁结构则以它的肋位剖面图作为主视图;首、尾段结构常 以基本结构图中相应位置的纵剖面图为依据;首、尾柱结构是以它的 侧面投影图为主视图。
等还不能将结构表示清楚,须在剖面图或向视图、剖视图上再作剖面
图,此剖面图即为分剖面图。分剖面图标注方式为在原剖面图(或向
视图、剖视图)上标注剖切符号及位
置
、
,在分剖面图上方对应标
写“8-1”、“A-1”。
项目八船体生产设计工作图绘制教材(精)

外板展开图 SHELL EXPANSION
SHOW IS PORT.SID SYM
图为左舷,右舷对称
:待焊区(L=300)
BL.10
14.5 AH32
此外板纵骨为222分段延伸
-S1000
BL.9
14.5 AH32
COVS
-S1001
N3.5
COVS
BL.8
COVS
16.4
BL.7
16.47
18.0 AH32
A3 4.8896 2
D3 912 936 D2 S102 C D
E3 921 E2 962 1027 E1
300 S2223
Fore
20.0000
911
1 1 A 300
0.3233 7.9020
B 1000
E 652
Sightline (X) 2
1087
(胎架支柱间距为1000mm)
图 8-1 胎架图表实例 3)余量、补偿量的布置 根据结构放样、号料、构件加工、装配、焊接收缩和火工矫 正等因素,确定余量、补偿量的加放和预修正时机。余量、补偿量和预修正时一般应采用相 应的工艺符号,并标在零、部件带余量或补偿一端边缘上。 4)工艺孔 工艺孔包括:手孔、人孔、通风孔、通道孔等临时开孔。应注明工艺孔的 位置、尺寸。 5)预开孔 预开孔包括:管子、通风管、电缆等穿过结构的开孔,以及门、窗等开孔。 预开孔应与相关专业协调后,设绘在船体分段工作图上。 6)预装件 预装件包括:放水塞、梯子、人孔盖、电缆托架、海底阀箱、设备底座等。 预装件应与相关专业协调后,设绘在船体分段工作图上。亦可用预装件清册或托盘表示。 7)零、部件编码和零、部件明细表 按照分段建造装配、焊接工艺要领和本厂工艺流 程及编码标准等进行编码。代码可用英文字母和阿拉伯数字表示,分段中任何一个零、部组 件都应有相应的代码。 船台散装件应有相应的船台散装件代码, 全船通用件应有相应的通用 件代码,标准件应有相应的标准件代码。零、部件代码顺序号,应按统一的规律编排。标注 代码要清晰、正确,避免与结构尺寸、剖面的字母、符号相混淆。零、部件明细表应包括: 代码、数量、材料规格、尺寸、工艺流程等内容。 8)分段重量重心 分段重量应提供结构净重、焊后重量和吊重。分段重心位置应标注 三维坐标。将结构重量、重心标注在分段工作图的规定栏目内。 9)吊环 根据分段结构重量、重心和分段运输、平吊、翻身、上船台等工况进行分段 吊环的布置。将吊环绘制在分段工作图的相应图面上,在分段工作图上无法表达清楚的,应 另外绘分段吊环布置图。在图面上注明选用吊环的吨位、数量、焊接坡口、焊接规格及焊接 材料。 在图面上注明吊环部位结构加强焊的范围及焊接规格。 在图面上注明吊运临时加强要 求。吊环可用规定的符号表示。 10)工时定额和材料定额 工时定额和材料定额可表示在分段工作图上,亦可用其他 方式提供。工时定额的项目包括:装配、切割、电焊、冷热加工、批扣、完工矫正和吊运等 工时。工时定额的编定按有关规定进行。工时定额一般应以表格形式编制。材料定额的项目 包括:钢材、辅助材料、焊接材料等的材料定额。钢材应在套料结束后,再以分段为单位编 制成分段钢材定额表。分段钢材定额表应将本分段中所有的板材、型材按板厚、牌号、规格 的耗量和余料分别统计汇总,并按工艺流程注明材料的流向。辅助材料包括:胎架、吊环、 眼板、马板等材料,定额一般可以分段重量的百分比计算统计。焊接材料定额一般以焊接长 度乘以板材的厚度、焊缝种类、焊缝形式、边缘处理形式等的影响系数得出,有标准规定的 按标准编定。 4.校审项目 1)分段装配焊接施工要领应与建造方针、船体施工要领一致; 2)分段制造工艺应符合有关标准的要求;
船体规范化制图

4.理论线(MOULD LINE)表达
6)需要注意以下情况处理
图 面 标 记 桁材及横向腹板 施 工 方 法
800 800
4.理论线(MOULD LINE)表达
6)需要注意以下情况处理
图 面 标 记 施 工 方 法
1000
1000
4.理论线(MOULD LINE)表达
6)需要注意以下情况处理
图 面 标 记 施 工 方 法
GIR.
SS
W W
7.零件端部的表达
1) 图 面 表 示 及 施 工 基 准:
ON DWG
S S Sn Sn 角钢,球钢
30~40 25
15
30
15
削斜(SNIP)施工角度
平铁
30~40 30~40
削斜(SNIP)
15
15
Sn
Sn
25
30
图纸标记 S Sn
施工角度 30 N
30°
30°
15
Sn
Sn
5.零件尺寸标注
图 面 标 记 施 工 方 法
XXX-XX 2 250X12.0
250
12
250
5.零件尺寸标注
图 面 标 记 施 工 方 法
当斜度大的时候,可以 在原点作R来确定肘板大小。
XXX-XX 2 300X300X12
300
12
300
5.零件尺寸标注
其他大构件尺寸的标注,以平面板架为例说明:
2.船体分段图纸的绘制顺序(封面示意)
2.船体分段图纸的绘制顺序(封面示意)
3.船体分段图纸视图基准
1) 视图基准
MAINDECK(主甲板) (外) (内) (内) (外)
全船精度布置图设绘要领
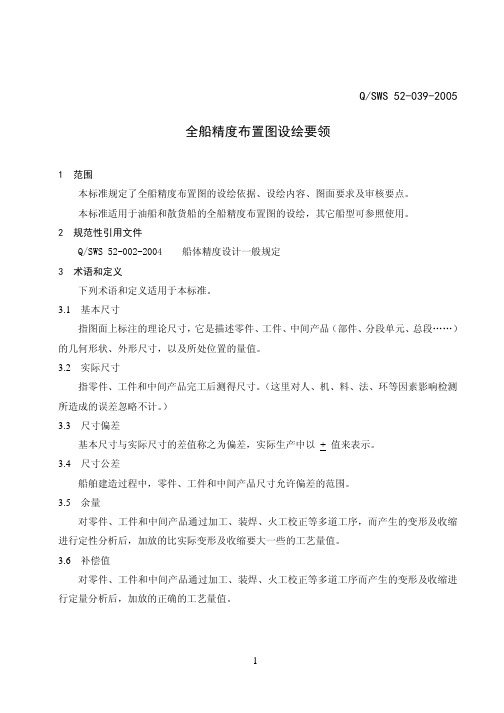
Q/SWS 52-039-2005全船精度布置图设绘要领1 范围本标准规定了全船精度布置图的设绘依据、设绘内容、图面要求及审核要点。
本标准适用于油船和散货船的全船精度布置图的设绘,其它船型可参照使用。
2 规范性引用文件Q/SWS 52-002-2004 船体精度设计一般规定3 术语和定义下列术语和定义适用于本标准。
3.1 基本尺寸指图面上标注的理论尺寸,它是描述零件、工件、中间产品(部件、分段单元、总段……)的几何形状、外形尺寸,以及所处位置的量值。
3.2 实际尺寸指零件、工件和中间产品完工后测得尺寸。
(这里对人、机、料、法、环等因素影响检测所造成的误差忽略不计。
)3.3 尺寸偏差基本尺寸与实际尺寸的差值称之为偏差,实际生产中以+ 值来表示。
3.4 尺寸公差船舶建造过程中,零件、工件和中间产品尺寸允许偏差的范围。
3.5 余量对零件、工件和中间产品通过加工、装焊、火工校正等多道工序,而产生的变形及收缩进行定性分析后,加放的比实际变形及收缩要大一些的工艺量值。
3.6 补偿值对零件、工件和中间产品通过加工、装焊、火工校正等多道工序而产生的变形及收缩进行定量分析后,加放的正确的工艺量值。
Q/SWS 52-039-20054 设计依据4.1 Q/SWS 52-002-2004《船体精度设计一般规定》。
4.2 分段总段划分图4.3 典型分段总段建造要领4.4 搭载要领4.5 全船主结构排板图4.6 船体基本结构图4.7 全船焊接工艺图5 内容要点5.1 设计内容5.1.1 大接缝与分段接缝的余量及补偿量的加放值和修割时机。
5.1.2 拼板的焊接收缩补偿量的加放值。
5.1.3 T型材的装焊收缩补偿量加放值。
5.1.4 其它纵横骨材的焊接收缩补偿量加放值5.1.5 骨材焊接时板的收缩补偿量加放值。
5.1.6 构件的安装补偿量加放值5.1.7 以上未包括的其它构件余量及补偿量的加放值和修割时机。
5.2 端部补偿量设计原则5.2.1 加工余量加放原则5.2.1.1 卷板机预弯板,边缘最小剩余直边75mm,否则加放2×t(t为板厚)压头余量。
船体分段划分图的识读与绘制
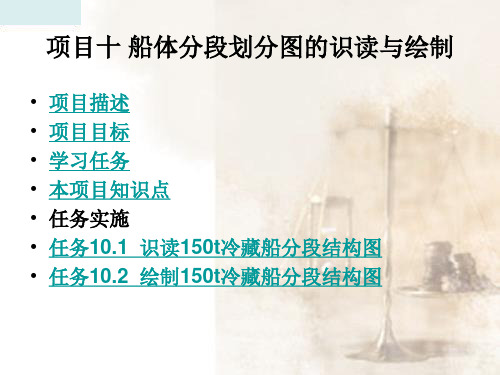
• 5.主尺度
• 分段划分图的主尺度主要有总长、垂线间长、型宽、型深、吃水和肋 距等。
上一页
返回
任务10.1 识读150t冷藏船分段划分图
• 10.1.1 了解船体的分段划分概况
• 根据明细栏,结合侧面图、甲板图、舱底图和分段号可知主船体的首 、尾段划分情况,中段划分的底部分段数、舷侧分段数、甲板分段和 舱壁分段数,还可了解上层建筑中首楼、尾楼等的划分情况,这样可 对整个船体的分段划分情况有个概括的了解。
返回
【学习任务】
• 学习任务1:识读150t冷藏船分段划分图。 • 学习任务2:绘制150t冷藏船分段划分图。
返回
【本项目知识点】
• 1.分段划分图的特点 • 分段划分图表示了全船分段的数量、各分段的分段接缝位置和分段的
理论重量以及船台装配余量的数量和加放部位。 • 由于分段划分图主要用来表明分段接缝的位置,所以视图中除与分段
• 除上述视图外,若船体分段的板和内部骨架的分段接缝不在同一平面 内时(图10-1),则分段划分图通常还绘有纵剖面图和横剖面图。
上一页 下一页 返回
【本项目知识点】
• ④纵剖面图:是用纵向平面剖切船体而得的剖面图,它表示了剖切平 面处的分段的板和内部纵向骨架沿船长方向的分段接缝位置。
• ⑤横剖面图:是用横向平面剖切船体而得的剖面图,它表示了剖切平 面处的分段的板和横向骨架沿船宽方向的分段接缝位置。
定位有关的结构(如甲板、平台、舱壁、内底、水密肋板等)外,其他 结构均省略不画。图中也不画一般的板缝线,只画分段接缝线。图样 简洁、清晰,画图方便,读图也一目了然,便于使用。
下一页 返回
船舶建造----施工要领(适合快速理解和适应船厂各个工序)
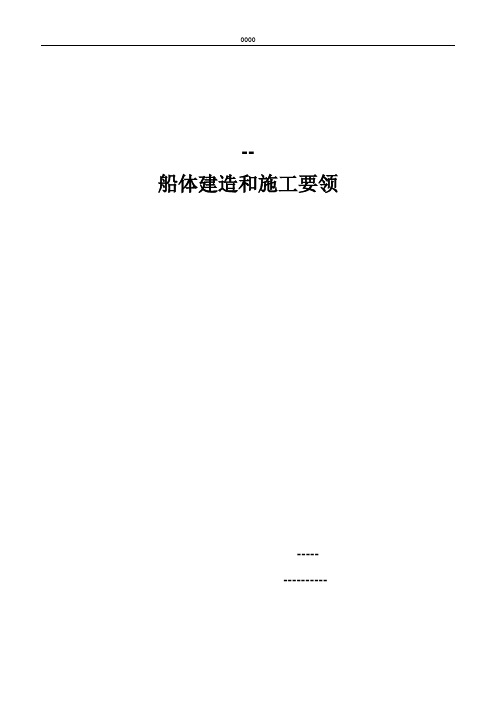
--船体建造和施工要领---------------一、概述:本船舶建造方案主要统筹和指导协调本船从设计开始至交船期间船舶建造各环节的相关工作,是我厂建造船舶的纲要文件。
本船为入ABS船级社的散货船,尾部单机单浆推进,甲板间4个30吨克令吊,折叠双扇液压舱盖;钢质船体,高强度钢占主结构70%,货舱区船体为纵骨架式,双底双壳结构,机舱和艏尖舱为横骨架式,设有球鼻艏。
(一)主要技术参数和特征:1.船型参数:总长: --垂向间长: -----型宽: ----------型深: ---------设计吃水: -----------结构吃水: ---------服务航速: ----------货舱:由6道水密舱壁分隔为5个货舱,其中3号货舱兼为压载舱。
2.结构参数:肋骨间距: ----- (600mm首/尾)主甲板距基线: ---------主甲板到A甲板: ----------其他生活区甲板: ---------驾驶甲板: ----------艏楼甲板: ---------主甲板梁拱: ---------双层底高度: ---------(二)船体分段划分及基本建造方针1.分段划分原则及方针:根据我厂的情况,采用‘平面分段与立体分段结合’的建造方针,实行:桁材和梁的小组--平(曲)面分段中组---立体分段大组---下水平台立体总段总组---坞内总段大合拢(搭载)的工艺流程;2.分段划分原则上为8米、10米或12 米;3.立体小分段的划分根据预制场地起重能力,原则上不得大于65吨,一般分段应控制在45吨左右;4.分段划分方式详见《分段划分图》;5.艉部分段和艏部分段的搭载分别先后在3#坞东预制场地进行,采用下水驳下水,最后在2#坞内对接合拢;6.尾段包括尾尖舱、机舱、NO.5货舱、NO.4货舱和NO.3货舱后部;7.首段包括首尖舱、NO.1货舱及内部锚链舱等结构、NO.2货舱、NO.3货舱前部;8.尾部上层建筑整体预制并进行预舾装,待船舶主体合拢后整体上船吊装(主甲板上第一层结构散装);9.钢板定货基本尺寸:a.12mx2.4m和10mx2.4m为主b.10mx2.4m和9mx2.4m 和8mx2.4m10.船舶主体分段数量为225个,其中包括平面分段和立体分段;总段数量8个;(三)船舶建造重点考虑内容:1.首尖舱及球鼻首部位的制造工艺、精度控制、线形光顺等;2. 尾轴位置的建造工艺、精度控制、尾轴安装、尾轴镗孔等;3.舵系部分结构及安装调试等;4.甲板舱口围及舱盖液压动力系统的安装调试,舱口围板和舱盖的建造工艺、精度控制等。
造船生产设计船体图纸
江苏科技大学先进制造技术中心
© 2004 MCAMT JUST 8
5.3 船体生产设计工作图
江苏科技大学先进制造技术中心
© 2004 MCAMT JUST 9
5.3 船体生产设计工作图
三、按工序工位出图 1、一般图示 1.1、理论线标记 理论线是指零件装配基线和在基准线上装配时的方向基准。
江苏科技大学先进制造技术中心
江苏科技大学先进制造技术中心
© 2004 MCAMT JUST 31
结构图问题(2)
这表示什 么视向?
江苏科技大学先进制造技术中心
© 2004 MCAMT JUST 32
结构图问题(3)
护圈的表达完 整了吗?
江苏科技大学先进制造技术中心
© 2004 MCAMT JUST 33
结构图问题(4)
图中箭头表示 什么含义?
江苏科技大学先进制造技术中心
© 2004 MCAMT JUST 34
结构图问题(5)
图中所示 7790+30表示什 么含义?
江苏科技大学先进制造技术中心
© 2004 MCAMT JUST 35
结构图问题(6)
这张补板视图上 是否有错误?
江苏科技大学先进制造技术中心
© 2004 MCAMT JUST 36
(4) 宽度方向:中心线或中心线方向第一根纵骨为起点,往舷 侧方向累计尺寸。
(5) 高度方向:双层底向上第一根纵骨为起点,向上累计尺寸。
江苏科技大学先进制造技术中心
© 2004 MCAMT JUST 11
5.3 分段生产设计工作图
(6) 所有尺寸都是理论线间的尺寸。 (7) 表示零件本身大小的尺寸与理论线无关,自该零件端部 标注。 (8) 曲形面板的半径标注,是标注至腹板边缘的尺寸。
第八章-分段装配-货舱区环型各分段制造
货舱区环型各分段制造货油舱区的环型分段包括底部分段、下边舱分段、舷侧分段、上边舱分段、甲板分段、横舱壁分段和纵舱壁分段,各类分段的结构形式不一样,所以制造方式和安装方法有所差别(见示图8—20),而共同点是分段首尾端的构架与壳板“一刀齐”。
示图8—20一、底部分段制造大型船舶底部一般分为平底线区的“方箱”底部,及其二侧舭部的底边水舱组成。
1、制造方式:大型船舶“方箱”底部均分为不对称的左右(P.S)二个片段分别制造,搭载前才总组合拢成整体。
制造方式是在“平面分段装焊流水线”上的内底板为基面反造,然后贴盖外板拼板。
而特殊船舶LNG则以内底板为基面反造,而外板纵骨则安装在另一外板胎架的铺板上。
将反造的内底片段翻身反扣至正态外板片段中成形分段。
1、安装方法我厂曾用过三种。
(1)七、八十年代曾用框架式装配法(见示图8—21)示图8—21(1)九十年代之后用放射式装配法(见示图8—22)示图8—22(3)LNG船用顺序式装配法(见示图8—23)示图8—232、操作控制要领(1)纵骨、纵桁及横向肋板间距尺寸按“LNG分段建造精度控制表”标准。
(2)纵骨、纵桁及横向肋板的垂直度按“LNG分段建造精度控制表”标准。
(3)纵骨、纵桁、内底板及外板首、尾端应在同一横断面内,检测办法用线锤或激光经纬仪。
4、构架装配顺序内底板拼板划线及切割→纵骨安装→16极焊接→安装肋板→插入纵桁板→架设外板纵骨材→构架焊接→预舾装→贴盖外板拼板→定位加强焊。
(1)内底纵骨安装。
将纵骨按零件号吊到分段内底板相对应的位置。
根据图纸尺寸确定纵骨轮廓与外板端缝的相对位置,然后用点焊固定。
点焊时应从纵骨中间向二端固定,定位焊结束后,要用角尺或水平尺检测盘直度,在关键部位肋骨与内底板的垂直度须用钢板条临时加强以防止纵材焊接变形。
(2)肋板安装。
吊装肋板按相应的肋位线插入纵材之间。
在吊装肋板时会遇到肋板上的纵骨切口不易插入纵骨,这时须修正肋板上的切口。
船体分段划分概要
(7)扩大预舾装原则;
现代造船分段划分一般分为二个阶段: 粗划分阶段; 细划分阶段。
本船主船体各划分成: 首立体分段(含首尖舱舱壁); 尾立体分段(尾尖舱舱壁); 中段则划分成 8个底部分段; 10个舷侧分段(左、右舷各5个); 5个甲板分段和2个舱壁分段。 上层建筑中( 7个分段) 尾部划分成 5个立体分段(包括烟囱分段); 中部起货机平台为1个立体分段; 首楼为1个立体分段。
配、运输、起吊、翻身等过程中不会有倾覆的危险。
4.生产工艺相关
5.钢材供货规格:为了提高钢材的利用率,分段的长度、
宽度要尽可能地与可供钢材,特别是钢板的尺寸匹配。
三、分段划分
分段划分 原则如下: (1)吊车最大起重量原则;
(2) 原材料最佳利用率原则;
(3)组织均衡生产原则; (4)船体结构强度合理性原则; (5)施工工艺合理性原则; (6)安全施工原则;
亚项目1.2
船体分段划分
目前,船厂建造船体时一般采用分段制造、船台合拢的
方法,即根据船体结构特点和船厂生产条件(包括起重能力)、
船舶建造工艺等,将船体划分为若干分段,先在车间或其他
场地的胎架或平台上分别建造,并将小型分段组装成大型分
段或总段,最后在船台上依次合拢成完整的船体。
一、分段划分的职责分担
分段划分图绘制
74500吨散货船分段划分图
主尺度 总 长: 225m 两间柱长: 217m 型 宽:32.26m 型 深: 19.60m 设计吃水: 12.50m 结构吃水: 14.25m 分段总数: 230只
A甲板平面
B甲板平面
C甲板平面
D甲板平面
驾驶甲板平面
罗径甲板平面
主甲板平面
内底平面
船舶平面分段设计方案
船舶平面分段设计方案船舶平面分段设计方案是针对船体结构的一种设计方案,通过将船体划分为若干个区域(即分段),以实现船体的平面分布和设计的目的。
下面是一份船舶平面分段设计方案的详细介绍。
1. 设计目的:(1) 提高船体的结构强度和刚度,增强船舶的耐久性和安全性;(2) 方便生产制造和船舶维修,减少制造成本和维护费用;(3) 符合船级社规章的要求,获得相关船级社的认证。
2. 设计步骤:(1) 分析船舶的功能需求和船型特点,确定平面分段的数量和位置;(2) 进行船体结构计算和强度分析,确定分段的尺寸和配置;(3) 根据分段的数量和尺寸,制定生产制造工艺和工序;(4) 进行船舶平面分段设计,绘制分段图纸,并标注必要的尺寸和要求。
3. 分段数量和位置:分段的数量和位置根据船体的结构和功能需求来确定。
一般来说,船头、船尾、船体中部和船舱等区域是常见的分段位置。
在确定分段位置时,还需考虑到船舶的造型和稳性等因素。
4. 分段尺寸和配置:分段的尺寸和配置需根据船体结构的要求和分段位置来设计。
一般来说,船头和船尾的分段尺寸较小,船舱的分段尺寸较大。
在设计分段尺寸时,还需考虑到分段之间的连接方式和强度要求。
5. 生产制造工艺和工序:生产制造工艺和工序的制定需根据分段的尺寸和配置来确定。
一般来说,先进行分段的制造和组装,然后进行船体结构的加固和连接。
在制定工序时,还需考虑到船舶的生产周期和制造成本等因素。
6. 分段图纸设计:分段图纸是船舶平面分段设计的重要成果,需绘制详细的设计图纸,并标注必要的尺寸和要求。
在图纸设计时,还需考虑到船级社的规定和标准。
通过以上步骤的设计和实施,可以实现船体结构的平面分布和设计的目的,提高船体的耐久性和安全性,减少制造成本和维护费用,并获得船级社的认证。
- 1、下载文档前请自行甄别文档内容的完整性,平台不提供额外的编辑、内容补充、找答案等附加服务。
- 2、"仅部分预览"的文档,不可在线预览部分如存在完整性等问题,可反馈申请退款(可完整预览的文档不适用该条件!)。
- 3、如文档侵犯您的权益,请联系客服反馈,我们会尽快为您处理(人工客服工作时间:9:00-18:30)。
Q/SWS 52-003-2005船体分段装配图设绘要领1 范围本标准规定了船体分段装配图的设计依据、内容要点、图面要求和校审要点。
本标准适用于各类船舶的船体生产设计。
2 规范性引用文件Q/SWS 12-001-2001 船体制图Q/SWS 41-003-2004 船舶结构焊接与坡口型式选用规定Q/SWS 52-012-2003 船体结构流水孔、透气孔和通焊孔形式3 设计依据3.1 船舶建造方针3.2 分段划分图3.3 肋骨型线图3.4 船舶结构焊接与坡口型式选用规定3.5 船体结构理论线图3.6 结构详细设计退审图(包括船东退审图、船检退审图)3.7 焊接规格表3.8 金属船体制图3.9 船体余量布置图3.10 船体临时通道及临时工艺孔图3.11 船体节点详图3.12 船体结构流水孔、透气孔和通焊孔形式3.13 船体强力构件开孔及补强4 内容要点4.1 设计要点4.1.1 分段装配图应准确反映分段所有的结构及精度、焊接等工艺信息,还应当包括标准舾1Q/SWS 52-003-2005装件、其它专业提出的结构加强和预开孔等内容。
其内容通过封面、组立树、分段重量重心、组立顺序图、安装材料及预舾装品目录、支柱胎架图、胎架二次划线图、外板展开图、甲板平面图、纵剖面图、横剖面图、局部剖面图和节点详图等方式进行表明。
4.1.2 船体分段装配图总体设计要领4.1.2.1 内容要求a) 船体分段装配图中除特记外,必须包括图号、页数、比例;b) 船体分段装配图中必须完整反映船体各类构件的组立名、零件号、板厚、材质等信息,必要时须标注几何尺寸;c) 组立内主要型材大小、板厚及材质等信息应标注在组立名下,剖面内可不需再次标注;d) 船体分段装配图中应标明在施工过程中的临时工艺孔;e) 对于可以做成永久性吊环的结构,应在装配图中反映出来;f) 装配图必须标明分段余量及余量切割阶段符号,焊接补偿量符号;g) 装配图需反映与其它专业的协调问题,其中包括:其它专业提供的通过结构的管子、风管、电缆、放水塞及人孔盖的预开孔和孔加强;参照舾装图纸确认与舾装有关联的基座垫板,确认甲板(平台)上面有没有安装柱子和垫板,并确认这些垫板与甲板(平台)下型材的通气孔、流水孔是否有干涉;垫板参照舾装图纸标明有舾装用途的管子支柱的安装精度要求;h) 结构图必须标明倾斜构件的安装角度。
装配角度是指两个零件装配面与面形成的角度,只在不等于90º时才在图纸上标记。
由于梁拱或舷弧完全相等而在零件之间发生装配角度时,在形成锐角的方向标记装配角度;2Q/SWS 52-003-2005组合零件(T或L2-TYPE)的腹板与面板之间发生装配角度时,则在截面处标注锐角;i) 船体所有构件上的开孔须与Q/SWS 52-012-2003《船体结构流水孔、透气孔和通焊孔形式》保持一致,并且不能与相邻构件相碰,距离至少15mm以上。
j) 同一组立下相同的构件零件名相同。
4.1.2.2 尺寸标注a) 除特记外,所有的标注尺寸是自理论线至理论线的尺寸;b) 零件本身大小的尺寸与理论线无关,自该零件端部标注;c) 倾斜或曲面部分的实长尺寸和投影尺寸(水平、垂直)均需标记;d) 长度方向尺寸标注尽量以分段内船尾方向第一个构件的肋位为起点,往船首方向累计尺寸;e) 宽度方向尺寸标注尽量以分段内中心线或中心线方向第一个纵骨为起点,往舷侧方向累计尺寸;3Q/SWS 52-003-2005f) 高度方向尺寸标注尽量以分段内双层底向上第一个纵骨为起点,向上累计尺寸;g) 同一区域内尺寸标注时避免形成封闭标注,留出误差标注区;h) 结构图应标注如:克令吊、火炬塔等重要构件的垂直度和水平度允许误差。
4.1.2.3 焊接要求a) 船体装配图必须表示焊接方法、规格、坡口形式、缓焊要求和板厚差过渡形式;b) 坡口焊接型式须与Q/SWS 41-003-2004《船舶结构焊接与坡口型式选用规定》保持一致;c)坡口符号标记在板缝线的中央,板厚差及板厚差削斜标注在削斜构件上。
在图纸上有几个板缝线的时候,尽可能在同一位置标记;d) 根据建造方法和可作业性确认坡口的方向,并确认与相邻分段对接板的焊接形式与坡口形式是否一致,通焊孔尺寸是否相同;e) 特殊焊接方式须单独表示。
4.2 设计方法4.2.1 封面(COVER)船体装配图封面表达了图纸的基本信息,样本见附录A——图A.1。
4.2.1.1 主要内容a) 公司名称(中英文);b) 工程名称(中英文);c) 工程号;d) 图名(中英文);e) 设计阶段(中英文);f) 图号;g) 比例;h) 图面型式;i) 设绘、标检、校对、审核人员签名及时间,需手工填写;j) 主办人员及联系电话;4Q/SWS 52-003-2005k) 总页数;l) 图纸发送单位及份数;m) 会签人员签名及时间,需手工填写;n) 注意事项;o) 修改纪录(包括日期、修订号、修改内容、船号、作业场所、页码、设绘、标检、校对、审核签名等)。
4.2.1.2 设计要领a) 设绘、标检、校对、审核和会签人员及时间均须手工如实填写;b) 工程号须手工圈出;c) 注意事项须与船舶建造方针、焊接规格表等设计依据保持一致;d) 图纸发送单位及份数须与公司有关规定保持一致;e) 每一次图纸修改须在修改纪录中手工如实完整填写,发施工图同样填写。
4.2.2 组立树(BLOCK ANALYSIS)该图标明了各组立从属情况,样本见附录A——图A.2。
4.2.2.1 主要内容a) 组立层次;b) 组立名;c) 组立数量;d) 组立阶段代码;e) 组立所在页数。
4.2.2.2 设计要领a) 组立树由设计人员用英文编制而成;b) 每一层次组立应上下对齐;c) 组立名、组立阶段名须与公司编码标准保持一致;d) 左右分段分别列出组立树。
4.2.3 分段重量重心(WEIGHT & C.O.G.)5Q/SWS 52-003-2005该图标明了分段及各组立的重量及重心位置,样本见附录A——图A.3。
4.2.3.1 主要内容a) 分段名、组立名;b) 分段、组立对应的重量;c) 分段、组立的重心位置;d) 分段、组立面积。
4.2.3.2 设计要领a) 此图是分段建模完成之后,由设计系统自动生成;b) 每一层次组立应上下对齐;c) 所有数据小数点后取三位有效数字;d) 各组立面积用括号内数据表示;e) 重量单位“吨”,重心单位“米”,面积单位“平方米”;f) 重心位置以在X轴、Y轴、Z轴的绝对坐标值来表示;g) 左右分段分别列出。
4.2.4 分段组立顺序图(BLOCK DETAILED ASSEMBLY PROCEDURE)该图用立体图的形式标明了分段建造的主要顺序,样本见附录A——图A.4。
4.2.4.1 主要内容a) 主要小组立结构形式及外形尺寸;b) 主要中组立建造方式及外形尺寸;c) 大组立建造方式及外形尺寸;d) 组立流向;e) 主要板架拼板方式;f) 简要建造说明。
4.2.4.2 设计要领a) 该图仅表示主要组立及典型组立的建造顺序,非所有组立;b) 小、中、大组立从上至下按顺序进行排列;6Q/SWS 52-003-2005c) 主要板架须表示拼板信息及焊接坡口型式。
4.2.5 安装材料及预舾装品目录(PRE-OUTFITTING)该图标明了本分段内船体舾装件的基本情况,由相关专业提供。
样本见附录A——图A.5。
4.2.5.1 主要内容a) 设绘人员;b) 材料的图内代号;c) 材料编号;d) 材料描述;e) 材料单位;f) 材料数量;g) 单件重量;h) 所在位置。
4.2.5.2 设计要领a) 材料描述中除标明材料名称之外,还须标明材料规格;b) 重量单位为“千克”;c) 左右分段须分开描述。
4.2.6 预舾装件详图(PRE-OUTFITTING DETAIL)该图对需要标准安装的标准预舾装件(例如放水塞、锌块等)进行了详细的描述,由相关专业提供。
样本见附录A——图A.6和图A.7。
4.2.6.1 主要内容a) 详细定位尺寸;b) 三视详图;c) 节点详图;d) 施工简要说明。
4.2.6.2 设计要领a) 尽量以船体结构作为定位尺寸的依据;7Q/SWS 52-003-2005b) 标明板厚方向;c) 详图中标明方位;d) 材料代号须与“安装材料及预舾装品目录”保持一致。
4.2.7 支柱胎架图(PIN JIG DWG)该图标明了以曲型板架作为装配基面时,每一根支柱胎架的情况,样本见附录A——图A.8。
4.2.7.1 主要内容a) 图号;b) 修改编码;c) 胎架与正态相比的横倾角及纵倾角;d) 曲型板架的组立名;e) 胎架间距;f) 每一根胎架支柱的位置编号及高度尺寸;g) 曲型板架的定位尺寸及边缘尺寸;h) 曲型板架各拼板的零件名、板厚及材质;i) 曲型板架板缝线编号。
4.2.7.2 设计要领a) 胎架支柱高度单位为“毫米”;b) 该图是曲型板架建模完成之后,由设计软件系统自动生成。
4.2.8 胎架二次划线图(REMARKING)该图标明了以曲型板架作为装配基面时,曲型板架上胎架后各构件的划线尺寸,样本见附录A——图A.9和图A.10。
4.2.8.1 主要内容a) 图号;b) 页数;c) 修改编码;8Q/SWS 52-003-2005d) 曲型板架组立名;e) 曲型板架各拼板的零件名、板厚及材质;f) 曲型板架板缝线编号及定位尺寸;g) 曲型板架的定位尺寸;h) 曲型板架各构件的板厚方向及划线尺寸(尽量采用相对尺寸);i) 曲型板架各纵骨在每档肋位上的装配角度及参考详图。
4.2.8.2 设计要领a) 须标明曲型板架所有构件的划线尺寸;b) 各主要构件须标明板厚方向,应与船体结构理论线图保持一致;c) 同一方向多次尺寸标注,尽量采用同一基点,以减少误差;d) 纵骨装配参考图须采用立体图形式,角度大小取小数点后两位有效数字。
4.2.9 分段外板展开图(BLOCK SHELL EXPANSION)该图标明了分段外板近似展开之后外板及相连构件的型式及尺寸,样本见附录A——图A.11。
4.2.9.1 主要内容a) 分段外板展开视图;b) 分段外板板架定位尺寸;c) 分段外板各拼板尺寸、板厚、材质及零件名;d) 分段外板板架组立名;e) 分段外板板缝坡口焊接型式及板缝间距;f) 各种构件零件号、板厚方向及与板缝的相对尺寸;g) 分段范围内肋位号及纵骨顺序号;h) 肋位间距及纵骨间距;i) 补板位置及编号;j) 相邻分段的分段名、板厚及材质;k) 分段余量、补偿量;9Q/SWS 52-003-2005l) 待焊区标记。
4.2.9.2 设计要领a) 由于船体形状和外板的排列通常对称于中线面,故外板展开图一般表示展开图形的一半,习惯上是从右向左舷看,展开视图;b) 分段外板展开图采用近似的展开方法,即只展开船体表面的横向曲度,而纵向曲度不展开。