船体分段大组立制作工艺流程
现代造船用分段法

,现代造船用分段法,即把船体按场地条件,分成若干个模块,先造好模块然后移到船台上合拢,以下都假定是按分段造船处理大流程:钢材下料是第一个环节(一般造船合约付定金后的第一个付款阶段)进行小组装:把加工好的单独的钢材部件装配成大部件,主要是强化平板分段组装:把大部件和切割好的及加工成型的钢材并装成分段模块,这是船体模组开始成形,一般从底部开始造,船的艏艉比较复杂,也会先开工分段焊接的同时也进行预舾装,一些跟结构有紧密关系的部件会先安装在分段里,主要是各种管子,通海阀组,部分楼梯,大型基座等,因为分段合并后不好施工分段装焊完成通过报验后进行涂装,主要是密闭舱室的内部油漆,如双层底,边舱等,需要打沙除锈,在分段时做效率高效果好造好若干个分段后开始上船台,这个英文叫 keel laying 是传统放龙骨的意思,现代造船没有真正放龙骨的概念,所以最初一批分段放到船台上定位就等于是放龙骨。
这是很重要的环节,一般船舱收取第二期的付款在船台上进行分段合拢,即把独立的分段模组结合起来,其中包括准确定位,割除结构余量,合龙缝施焊。
如此车间继续生产分段,陆续移到船台上合拢,船体开始成形主机是最大的机器,和其他比较大型的设备一样,在机舱部份的分段完全合拢前会先会先放到机舱底分段上,因为需要大型吊机吊装,所以同时定位摆放在基座上船艉部分装配完成后,进行艉轴镗孔,加工出与主机轴准确对中的轴套。
这工序要求很高的精准度,不能出现结构变形,所以一般在晚上进行,因为不平均的日照会令船体缘中轴线弯曲。
而且镗孔后不能够再有大型焊接施工,因为烧焊会引致钢结构变形,所以一般会等到船体差不多完成时才做。
当船体完全合拢后,基本上形成完整水密结构,船体就会下水。
有几个理由船要在没有造完前就下水:1.船台的承重力有限,不能承担整条造好的船的重量,特别是对从斜轨道滑下水的船台.2.如果船是滑下水的,船体进水时产生的应力限制了最大下水重量3.即便船台有足够能力,又比如在干船坞里造船,基本上下水重量没有限制,但船台是重要的生产资产,其利用率直接影响船厂的营利,所以当在建船只一旦能自浮便得马上腾空船台造另外一条船,尽量利用生产资源下水前会做第一度船底外板涂装船体下水时第三个付款点,船体结构大致完成船体下水后移舶到舾装码头,进行内部装配包括所有的机械设备,管路连接,电工装配,舱室内装等工程,就好像毛房装修一样,同时甲板机械也进行安装。
船体制造工艺程序

船体制造工艺程序船体制造工艺程序是制造船体的一系列操作步骤和程序。
以下是一般船体制造工艺程序的示例:1. 设计规划:在开始制造船体之前,首先需要进行船体设计规划。
这包括船体结构的设计、船体尺寸和形状的确定,以及选取合适的船体材料。
2. 材料准备:根据设计规划,选择适当的材料来制造船体。
材料可以包括钢铁、铝合金或复合材料等。
材料准备包括材料切割、折弯和打磨等操作。
3. 钢结构制造:如果船体是由钢结构构成,需要进行钢结构的制造。
这包括将钢板切割成所需的尺寸和形状,然后进行焊接和点焊等工艺,以组装成船体的结构。
4. 级别装配:船体结构制造完后,需要进行级别装配。
这包括将船体的各个部分进行装配和焊接,以形成一个完整的船身结构。
5. 船体内部装配:完成船体结构的装配后,需要进行船体内部的装配工作。
这包括安装甲板、舱室、设备和管道等。
6. 推进系统安装:船体内部装配完成后,需要进行推进系统的安装。
这包括安装发动机、螺旋桨和推进器等设备,以及相应的管道和电气系统。
7. 涂装和防腐处理:船体完成后,需要进行涂装和防腐处理。
这包括对船体进行刷漆和喷漆等工艺,以保护船体免受腐蚀和氧化。
8. 测试和调试:最后,在船体制造完成后,需要进行测试和调试。
这包括对船体结构的强度测试、漏水测试和船舶性能测试等,以确保船体符合设计要求。
以上是一般船体制造工艺程序的示例,具体的工艺程序可能会因船体类型、规模和材料等因素而有所不同。
继续写相关内容9. 定型试验:在完成测试和调试后,还需要进行定型试验。
定型试验是对船体的整体性能进行全面测试和评估。
这包括航行性能测试、稳性试验、滞留试验、抗风试验、抗波试验等。
这些试验旨在验证船体的结构稳定性、承载能力和适航性能,确保船体能够在各种环境条件下安全航行。
10. 完善船体:根据定型试验的结果,对船体进行必要的改进和调整。
可能需要加强船体的结构强度、调整船体的重心和稳定性参数,或对船体的设计和制造进行优化。
船舶分段制作及焊接工艺

船舶分段制作及焊接工艺1目的本工艺阐述了分段建造程序、分段精度的控制方法以及分段焊接工艺,旨在保证船舶分段质量满足船东及船级社的要求。
2适用范围适用于本公司船舶分段建造及焊接全过程。
3职责3.1技术部负责提供分段施工图、施工要领、建造规范、负责分段建造细则工艺的编制,并及时对图纸上存在的错误、遗漏等问题进行修正。
焊接规格表和焊接原则工艺等有关资料。
3.2公司结构部负责分段建造详细计划的编制,负责总体生产计划的下达。
3.3生产管理部负责分段作业计划的安排、产品质量的控制以及生产过程中的调度和协调。
3.4结构部管理人员同时负责对施工人员提出技术要求,并现场进行指导。
3.5安环部负责对生产过程中的安全进行监控。
3.6质量部负责对分段制造过程中的精度、制造质量进行检查控制;负责对新材料(包括进口钢材)牵头进行工艺评定,对船体结构焊接质量进行控制和检验。
3.7船厂各相关部门负责做好本工序的自检、互检工作,确保焊接质量。
4分段制作工艺4.1结构部在产品开工之前应先组织施工人员进行分段建造规范及有关节点图册的学习。
4.2施工人员在接收到分段图纸后应先熟悉图纸,掌握施工要领以及施工工艺,以确保在施工过程中对图纸不存在模糊感觉。
4.3结构部根据分段作业计划要求于分段开工前填写送料申请单交内业,结构部材料接收人在内业送料结束核对齐全后,在送料通知单存根联上签字,交内业留存备查。
4.4部件预制4.4.1施工过程中应按照图纸核对零件号安装,并且检查此代号是否符合图纸上规定的尺寸要求。
4.4.2施工过程中应检查零部件的材质是否符合图纸要求。
4.4.3施工过程中要按照装配节点图册及焊接规格表进行施工。
4.4.4板列预装及“T”型材预装a、板列预装前应先检查零件上的数控粉线是否准确或重新划出结构安装线,标出理论线位置及折边方向,然后再安装其上面的结构。
b、“T”型直梁采用倒装法,要先在面板上划出腹板安装线再安装腹板,“T”型弯梁采用侧装法安装,装配完工后在腹板上划出辅助检验线,以检验“T”型材经焊接后的型线是否准确,并作为火工矫正线型的依据。
船体分段大组立制作工艺流程.doc

产范围大组立是船舶制造的一种生产管理模式,是船体分段装配的一个生产阶段。
就是将零件和部件组成分段的生产过程。
人员搭配大组立生产以班为单位,一个班一般分为三到四个班组,一个班组的成员有一个组长、三个师傅、六个徒弟、两个电焊工、一个打磨工。
图纸资料大组立相关图纸有零件明细表、产品完工图、制作工艺、焊接工艺等。
工具割枪、米尺、线垂、千斤顶、水平尺、水平管、花兰螺丝、铁锤、铁楔、角尺、电焊机、自动二氧化碳焊接、打磨机机舱双层底大组立机舱双层底工艺流程胎架或平台准备——铺内底板——构件安装位置划线——构件安装——焊接——管铁舾装安装焊接——外板安装——焊前检查——构件与外板焊接——打磨——密性实验——交验装配作业标准分段长:L <±4mm分段宽: B <±4mm分段高:H <±4mm分段方正度:(内底板四角水平)<±8mm(加测机座内底板水平)货舱双层底大组立工艺流程胎架或平台准备——内底板拼装——自动二氧化碳焊接——构件安装位置划线——内底纵骨安装焊接——构件小组(肋板)安装焊接——舾装——补漆¬外底板拼装——焊接——构件安装位置划线——外底纵骨装焊——组装完成——焊接——打磨——舾装——完工检查——报验装配作业标准分段宽:B <±4mm分段高:H <±3mm分段方正度:<4mm (内、外底板对角线差值)分段扭曲度:<±8mm (内底板四角水平)纵骨端平面度:<±4mm内、外底板中心线偏差<±3mm内、外底板肋位线偏差<±3mm货舱顶边水舱大组立货舱顶边水舱分段工艺流程胎架或平台准备——斜板拼装——焊接——构件安装位置划线——斜板纵骨安装焊接——构件(肋板)安装焊接——舾装——补漆¬甲板拼装——焊接——纵骨装焊——组装完成——焊接——打磨——舾装——完工检查——报验装配作业标准分段长: L <±4mm分段宽: B <±4mm分段高: H <±4mm分段方正度:(测上甲板)<4mm分段扭曲度:(上甲班)<±8mm纵骨端平面:<±4mm货舱舭部大组立工艺流程胎架或平台准备——斜底板拼装——焊接——构件安装位置划线——斜底纵骨安装焊接——构件小组(肋板)安装焊接——舾装——补漆¬外底板拼装——焊接——构件安装位置划线——外底纵骨装焊——组装完成——焊接——打磨——舾装——完工检查——报验装配作业标准分段长: L <±4mm分段宽: B <±4mm内底高: H1±3mm舭部尖顶高:H2±4mm分段方正度:(测斜板)<4mm分段扭曲度:(测斜板)<±8mm舷侧分段大组立舷侧分段工艺流程胎架或平台准备——铺舷侧板——安装肋板框和斜边舱顶板——安装肋骨——焊接——焊后整形——打磨——自检——报验装配作业标准分段长:L <±4mm分段宽: B <±4mm分段高:H <±4mm分段方正度:(舷侧板)<4mm纵骨端平面:<±4mm尾部分段大组立工艺流程胎架制作——尾轴管前铸钢件定位——肋板安装——尾轴管定位——尾尖舱壁板定位——焊前检查——构件焊接——尾轴管与铸钢件预热焊接——尾轴管密性——舾装——外板安装——焊接——打磨——报验装配作业标准前后尾轴管偏心<3mm (施工中焊接变形进行监控)后尾轴毂后端至前尾轴毂前端总长L其余量为:+30~+40,余量前后端各占一半。
船体分段制作工艺流程

船体分段制作工艺流程船体分段现场制造工艺流程生产范围大组立是船舶制造的一种生产管理模式,是船体分段装配的一个生产阶段。
就是将零件和部件组成分段的生产过程。
人员搭配大组立生产以班为单位,一个班一般分为三到四个班组,一个班组的成员有一个组长、三个师傅、六个徒弟、两个电焊工、一个打磨工。
图纸资料大组立相关图纸有零件明细表、产品完工图、制作工艺、焊接工艺等。
工具割枪、米尺、线垂、千斤顶、水平尺、水平管、花兰螺丝、铁锤、铁楔、角尺、电焊机、自动二氧化碳焊接、打磨机机舱双层底大组立机舱双层底工艺流程胎架或平台准备——铺内底板——构件安装位置划线——构件安装——焊接——管铁舾装安装焊接——外板安装——焊前检查——构件与外板焊接——打磨——密性实验——交验装配作业标准分段长:L <±4mm分段宽: B <±4mm分段高:H <±4mm分段方正度:(内底板四角水平)<±8mm(加测机座内底板水平)货舱双层底大组立工艺流程胎架或平台准备——内底板拼装——自动二氧化碳焊接——构件安装位置划线——内底纵骨安装焊接——构件小组(肋板)安装焊接——舾装——补漆¬外底板拼装——焊接——构件安装位置划线——外底纵骨装焊——组装完成——焊接——打磨——舾装——完工检查——报验装配作业标准分段长:L <±4mm分段宽:B <±4mm分段高:H <±3mm分段方正度:<4mm (内、外底板对角线差值)分段扭曲度:<±8mm (内底板四角水平)纵骨端平面度:<±4mm内、外底板中心线偏差<±3mm内、外底板肋位线偏差<±3mm货舱顶边水舱大组立货舱顶边水舱分段工艺流程胎架或平台准备——斜板拼装——焊接——构件安装位置划线——斜板纵骨安装焊接——构件(肋板)安装焊接——舾装——补漆¬甲板拼装——焊接——纵骨装焊——组装完成——焊接——打磨——舾装——完工检查——报验装配作业标准分段长: L <±4mm分段宽: B <±4mm分段高: H <±4mm分段方正度:(测上甲板)<4mm分段扭曲度:(上甲班)<±8mm纵骨端平面:<±4mm货舱舭部大组立工艺流程胎架或平台准备——斜底板拼装——焊接——构件安装位置划线——斜底纵骨安装焊接——构件小组(肋板)安装焊接——舾装——补漆¬外底板拼装——焊接——构件安装位置划线——外底纵骨装焊——组装完成——焊接——打磨——舾装——完工检查——报验装配作业标准分段长: L <±4mm分段宽: B <±4mm内底高:H1±3mm舭部尖顶高:H2±4mm分段方正度:(测斜板)<4mm分段扭曲度:(测斜板)<±8mm。
浅谈船舶在上层建造分段中的重要流程

浅谈船舶在上层建造分段中的重要流程摘要:本文详细描述了船舶上层建筑分段建造工艺流程、总组合拢工艺及合拢后整体校正工艺,提出建造船必须规范建造工艺流程,制定各流程质量标准,提高建造精度,才能确保上层建筑分段分道建造,船台整体吊装的质量和周期。
关键词:船舶建造上层建造分段1.上层建筑分段建造储备工艺1.1材料起水、吊运工艺要求(1)材料起水吊运按我司场地起重设备条件,采用磁吸吊进行板材起水吊运;(2)磁吸吊吊运板材要求每次起吊一张钢板。
1.2材料堆放工艺要求(1)板材吊运至钢板堆场后,要求根据板材船级社认证等资料进行分类摆放,摆放时要求每张板材端部的船级社认证、炉批号、规格等信息必须可视,以确保后续板材检验及记录。
(2)板材堆放过程中,板材放落前,要求对下面一张板材表面进行杂质清洁,并沿板材宽度方向垫放3条以上垫木。
1.3材料吊运上线方式及工艺板材上预处理线的吊运方式为磁吸吊,磁吸吊吊运板材要求每次起吊一张钢板。
2.材料预处理工艺要求2.1预处理涂装工艺要求材料预处理工艺要求严格按照《车间底漆质量控制》,对材料外观检验、温度、相对湿度、钢板温度、盐分、清洁度、粗糙度及漆膜厚度等指标进行控制;2.2材料预处理后检验要求(1)双面检查板材是否存在麻点。
(2)材料流出预处理线后,材料吊运方式为磁吸吊吊运,磁吸吊吊运板材要求每次起吊一张钢板。
(3)材料流出预处理线后,要求对材料按批次、船级社认证、炉批号、规格等进行分类堆放,并显示材料端头板材信息,便于后续检验和记录。
3.分段板材和型材下料工艺3.1数控下料(HGG型材流水线)。
技术中心提供数控下料指令,加工作业区使用等离子数控切割机按指令进行下料。
等离子数控下料切割过程精度控制要求:(1)数控切割机参数确定。
上建分段下料阶段加工作业区根据本厂数控切割机自身的切割精度统计数据,按照FPSO上建板材厚度,确定满足下料精度要求的“割缝补偿”参数,确保零件下料尺寸偏差范围为0-2mm。
一种船舶分段建造的指导方法与流程

一种船舶分段建造的指导方法与流程摘要船舶的分段建造是船舶制造的重要工艺环节,对船体的质量和良好的结构起着关键作用。
本文提出了一种船舶分段建造的指导方法与流程,旨在帮助船舶制造企业提高生产效率、降低成本、提高产品质量。
本方法以实践为基础,结合了船舶制造工程的经验和技术,通过详细的流程和步骤,将船舶分段建造过程分解为若干个可控的任务,以提高建造过程的组织性和系统性,实现分段建造的高效率和高质量。
1. 引言船舶制造是一个复杂而庞大的工程项目,涉及材料、工艺、设备等多个方面的技术要求。
分段建造是船舶制造中的重要环节,指的是将整个船体分解为若干部分进行独立建造,然后再进行组装。
良好的分段建造方法和流程能够提高船体质量,减少生产周期,降低制造成本,并且有利于质量管理和后续工序的衔接。
本文提出了一种船舶分段建造的指导方法与流程,通过详细的步骤和流程,对船舶分段建造过程进行了合理的规划和组织。
2. 船舶分段建造的指导方法2.1 分段设计分段设计是船舶分段建造的首要步骤。
制定细致的分段方案,合理划分出各个分段单元,对后续的建造工作具有重要意义。
在分段设计中,需要考虑以下几个要点:•分段尺寸和形状:根据船舶的设计要求和需要,确定每个分段的尺寸和形状。
•分段的结构类型:根据船舶的用途和设计要求,确定每个分段的结构类型,如船首段、中段、船尾段等。
•分段的拆解和组装性:考虑到后续的拆解和组装工作,对分段进行合理设计,使得分段的拆解和组装过程更加顺利。
2.2 材料准备在船舶分段建造过程中,需要准备各种材料,包括船体板材、焊接材料、涂料等。
在材料准备阶段,需要根据船舶分段的设计要求,选择合适的材料,并进行采购和准备工作。
材料准备的主要步骤包括:•材料选择:根据船舶的设计要求,选择适合的材料,包括船体板材、焊接材料、涂料等。
•材料采购:按照船舶分段的设计需求,进行材料采购,保证材料的质量和供应的及时性。
•材料验收:对采购的材料进行验收,确保材料符合设计和质量要求。
船舶上层建筑分段建造及予合拢通用工艺
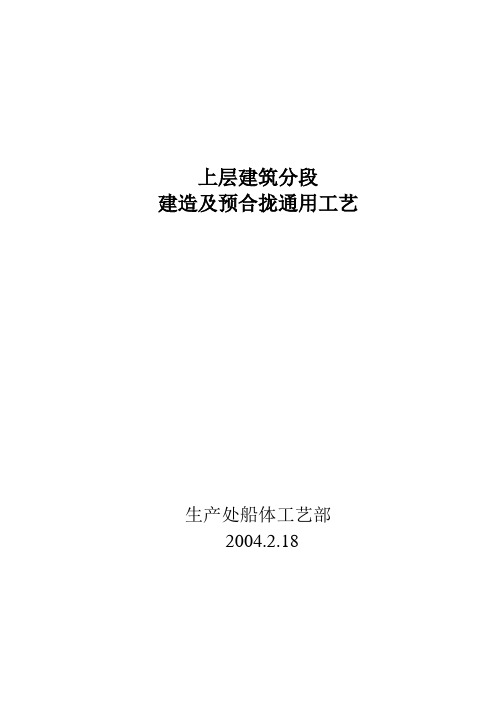
上层建筑分段建造及预合拢通用工艺生产处船体工艺部2004.2.18上层建筑分段建造及大合拢通用工艺(根据船体五车间上层建筑施工流程质量控制手册整理)一. 目的:为了进一步提高我厂建造入级钢质船舶上层建筑建造质量。
二. 适用范围:本工艺通用于我厂承接的各类船舶上层建筑分段建造及预合拢。
三. 质量控制点:船舶上层建筑简称上建,是船员的生活居住区域,上建分段的质量尤其是围壁、甲板的平整度以及整体美观显得尤为重要。
四. 工艺总则:十不准:1、不准用手工割刀切割板材(除圆角外);2、不准在板材上随意引弧及焊拉码、靠山之类的杂物;3、不准用铁锤锤击钢板;4、不准无证施焊、带水施焊;5、不准使用铁粉焊条;6、不准使用大电流、粗焊条搭焊;7、不准上道工序问题遗留到下道工序;8、不准上道工序未检验、报检合格进入下道工序;9、不准随意进行壁板校正;10、不准随意变更施工工艺。
十必须:1、板放线后,必须复核走方度,检查垂直线,理论线标注、收缩加放量等;2、构件安装,必须使用角尺,打好斜撑;3、围壁吊装,必须吊砣、打好斜撑;4、围壁交接,必须弹线装配;5、分段组装,必须按图检查安装是否正确完整,测量主尺度、垂直线数据,经区域/主管认可后交电焊;6、型材拼板,必须标识清楚,合理套用,避免材料浪费;7、吊码安装,必须焊前口头交验,焊后书面交验;8、各道工序,必须扫尾完、报检完方可进入下道工序;9、焊接工艺,与板材相连部位的电焊必须用CO2焊;10、分段校正,必须弹线用烘枪双道校正电焊应力区。
五、上层建筑分段建造:(一)、下料预制:1、内场应按要求下料和预制构件(详见《船体建造通用工艺》)质量标准摘抄如下:2、外场车间认真清点、验收上道工序的来料,剔除不合格件并及时与车间主管、区域长及项目经理部反馈联系。
3、拼板:(1)、楼子建造的板材必须由平板机滚平释放应力后,交拼板区域使用(对于有大于3mm的翘曲变形的板,需拖回内场重平,以消除起翘变形),拼缝边必须铣边;(2)、按工艺拼板图及套料图进行板材下料,切割一律使用自动割具,切割后的板材必须根据套料图进行标识,余料按套料图标注清楚,整齐堆放以便使用;(3)、拼板拼接板缝根据板厚留放0.5~1mm间隙以保证电焊熔透,板缝不允许有错位,注意板厚差,过渡坡口应在拼板前处理好(尽量采用机械刨边);(4)、δ6以下板拼缝全部采用Φ1.6焊丝自动焊施焊;δ7板拼缝搭焊面用φ1.6焊丝自动焊单面,翻身后用φ3.2焊丝埋弧自动焊第二面施焊;δ8以上板拼缝全部采用φ3.2焊丝自动焊施焊;(5)、施焊应参照板厚控制电流电压、速度,焊道宽度为1.4倍的板厚。
- 1、下载文档前请自行甄别文档内容的完整性,平台不提供额外的编辑、内容补充、找答案等附加服务。
- 2、"仅部分预览"的文档,不可在线预览部分如存在完整性等问题,可反馈申请退款(可完整预览的文档不适用该条件!)。
- 3、如文档侵犯您的权益,请联系客服反馈,我们会尽快为您处理(人工客服工作时间:9:00-18:30)。
船体分段大组立制作工艺流程
产范围
大组立是船舶制造的一种生产管理模式,是船体分段装配的一个生产阶段。
就是将零件和部件组成分段的生产过程。
人员搭配
大组立生产以班为单位,一个班一般分为三到四个班组,一个班组的成员有一个组长、三个师傅、六个徒弟、两个电焊工、一个打磨工。
图纸资料
大组立相关图纸有零件明细表、产品完工图、制作工艺、焊接工艺等。
工具
割枪、米尺、线垂、千斤顶、水平尺、水平管、花兰螺丝、铁锤、铁楔、角尺、电焊机、自动二氧化碳焊接、打磨机
机舱双层底大组立
机舱双层底工艺流程
胎架或平台准备——铺内底板——构件安装位置划线——构件安装——焊接——管铁舾装安装焊接——外板安装——焊前检查——构件与外板焊接——打磨——密性实验——交验装配作业标准
分段长:L <±4mm
分段宽: B <±4mm
分段高:H <±4mm
分段方正度:(内底板四角水平)<±8mm
(加测机座内底板水平)
货舱双层底大组立
工艺流程
胎架或平台准备——内底板拼装——自动二氧化碳焊接——构件安装位置划线——内底纵骨安装焊接——构件小组(肋板)安装焊接——舾装——补漆¬
外底板拼装——焊接——构件安装位置划线——外底纵骨装焊——组装完成——焊接——打磨——舾装——完工检查——报验
装配作业标准
分段长:L <±4mm
分段宽:B <±4mm
分段高:H <±3mm
分段方正度:<4mm (内、外底板对角线差值)
分段扭曲度:<±8mm (内底板四角水平)
纵骨端平面度:<±4mm
内、外底板中心线偏差<±3mm
内、外底板肋位线偏差<±3mm
货舱顶边水舱大组立
货舱顶边水舱分段工艺流程
胎架或平台准备——斜板拼装——焊接——构件安装位置划线——斜板纵骨安装焊接——构件(肋板)安装焊接——舾装——补漆¬甲板拼装——焊接——纵骨装焊——组装完成——焊接——打磨——舾装——完工检查——报验
装配作业标准
分段长: L <±4mm
分段宽: B <±4mm
分段高: H <±4mm
分段方正度:(测上甲板)<4mm
分段扭曲度:(上甲班)<±8mm
纵骨端平面:<±4mm
货舱舭部大组立
工艺流程
胎架或平台准备——斜底板拼装——焊接
——构件安装位置划线——斜底纵骨安装焊接——构件小组(肋板)安装焊接——舾装——补漆¬
外底板拼装——焊接——构件安装位置划线——外底纵骨装焊——组装完成——焊接——打磨——舾装——完工检查——报验
装配作业标准
分段长: L <±4mm
分段宽: B <±4mm
内底高: H1±3mm
舭部尖顶高:H2±4mm
分段方正度:(测斜板)<4mm
分段扭曲度:(测斜板)<±8mm
纵骨端面度:<±4mm
舷侧分段大组立
舷侧分段工艺流程
胎架或平台准备——铺舷侧板——安装肋板框和斜边舱顶板——安装肋骨——焊接——焊后整形——打磨——自检——报验
装配作业标准
分段长:L <±4mm
分段宽: B <±4mm
分段高:H <±4mm
分段方正度:(舷侧板)<4mm
纵骨端平面:<±4mm
尾部分段大组立
工艺流程
胎架制作——尾轴管前铸钢件定位——肋板安装——尾轴管定位——尾尖舱壁板定位——焊前检查——构件焊接——尾轴管与铸钢件预热焊接——尾轴管密性——舾装——外板安装——焊接——打磨——报验
装配作业标准
前后尾轴管偏心<3mm (施工中焊接变形进行监控)后尾轴毂后端至前尾轴毂前端总长L其余量为:+30~+40,余量前后端各占一半。
尾尖舱壁水平<±3mm
尾轴管水压试验≥0.02MPa
和铸钢件相焊焊缝铸钢件和钢板预热至≥120?C。
艏部分段大组立
工艺流程
胎架制作——主甲板板拼装——划线——横梁、肋骨安装——焊接——傍板安装——外板构件安装——焊接——检查——打磨——报验
装配作业标准
长度: L <±4mm
宽度: B <±4mm
高度: H <±4mm
开孔平台板四角水平<±8mm。