浅谈镁合金材料的热处理方法
【电镀技术】详解镁合金的四种防腐蚀处置方法
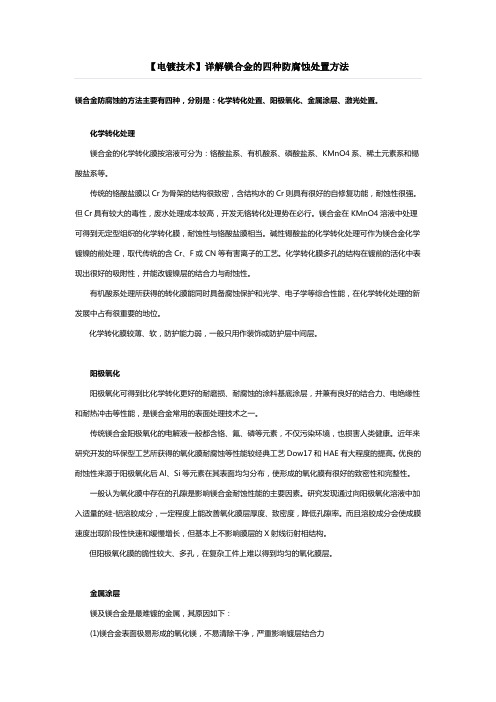
【电镀技术】详解镁合金的四种防腐蚀处置方法镁合金防腐蚀的方法主要有四种,分别是:化学转化处置、阳极氧化、金属涂层、激光处置。
化学转化处理镁合金的化学转化膜按溶液可分为:铬酸盐系、有机酸系、磷酸盐系、KMnO4系、稀土元素系和锡酸盐系等。
传统的铬酸盐膜以Cr为骨架的结构很致密,含结构水的Cr则具有很好的自修复功能,耐蚀性很强。
但Cr具有较大的毒性,废水处理成本较高,开发无铬转化处理势在必行。
镁合金在KMnO4溶液中处理可得到无定型组织的化学转化膜,耐蚀性与铬酸盐膜相当。
碱性锡酸盐的化学转化处理可作为镁合金化学镀镍的前处理,取代传统的含Cr、F或CN等有害离子的工艺。
化学转化膜多孔的结构在镀前的活化中表现出很好的吸附性,并能改镀镍层的结合力与耐蚀性。
有机酸系处理所获得的转化膜能同时具备腐蚀保护和光学、电子学等综合性能,在化学转化处理的新发展中占有很重要的地位。
化学转化膜较薄、软,防护能力弱,一般只用作装饰或防护层中间层。
阳极氧化阳极氧化可得到比化学转化更好的耐磨损、耐腐蚀的涂料基底涂层,并兼有良好的结合力、电绝缘性和耐热冲击等性能,是镁合金常用的表面处理技术之一。
传统镁合金阳极氧化的电解液一般都含铬、氟、磷等元素,不仅污染环境,也损害人类健康。
近年来研究开发的环保型工艺所获得的氧化膜耐腐蚀等性能较经典工艺Dow17和HAE有大程度的提高。
优良的耐蚀性来源于阳极氧化后Al、Si等元素在其表面均匀分布,使形成的氧化膜有很好的致密性和完整性。
一般认为氧化膜中存在的孔隙是影响镁合金耐蚀性能的主要因素。
研究发现通过向阳极氧化溶液中加入适量的硅-铝溶胶成分,一定程度上能改善氧化膜层厚度、致密度,降低孔隙率。
而且溶胶成分会使成膜速度出现阶段性快速和缓慢增长,但基本上不影响膜层的X射线衍射相结构。
但阳极氧化膜的脆性较大、多孔,在复杂工件上难以得到均匀的氧化膜层。
金属涂层镁及镁合金是最难镀的金属,其原因如下:(1)镁合金表面极易形成的氧化镁,不易清除干净,严重影响镀层结合力(2)镁的电化学活性太高,所有酸性镀液都会造成镁基体的迅速腐蚀,或与其它金属离子的置换反应十分强烈,置换后的镀层结合十分松散(3)第二相(如稀土相、γ相等)具有不同的电化学特性,可能导致沉积不均匀(4)镀层标准电位远高于镁合金基体,任何一处通孔都会增大腐蚀电流,引起严重的电化学腐蚀,而镁的电极电位很负,施镀时造成针孔的析氢很难避免(5)镁合金铸件的致密性都不是很高,表面存在杂质,可能成为镀层孔隙的来源。
镁合金表面处理的研究现状
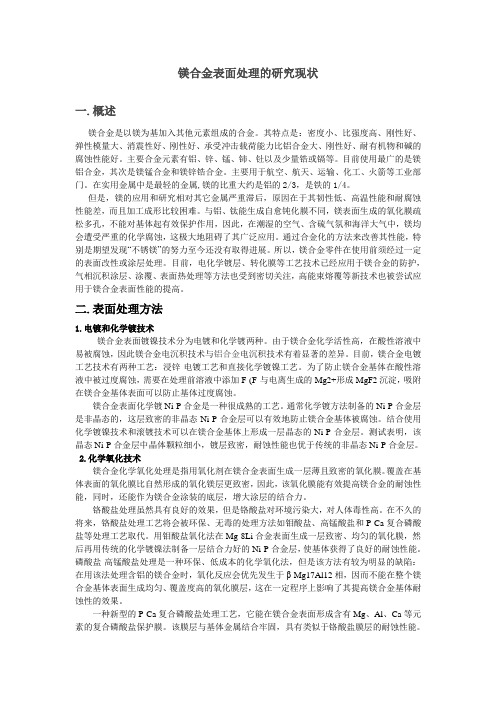
镁合金表面处理的研究现状一.概述镁合金是以镁为基加入其他元素组成的合金。
其特点是:密度小、比强度高、刚性好、弹性模量大、消震性好、刚性好、承受冲击载荷能力比铝合金大、刚性好、耐有机物和碱的腐蚀性能好。
主要合金元素有铝、锌、锰、铈、钍以及少量锆或镉等。
目前使用最广的是镁铝合金,其次是镁锰合金和镁锌锆合金。
主要用于航空、航天、运输、化工、火箭等工业部门。
在实用金属中是最轻的金属,镁的比重大约是铝的2/3,是铁的1/4。
但是,镁的应用和研究相对其它金属严重滞后,原因在于其韧性低、高温性能和耐腐蚀性能差,而且加工成形比较困难。
与铝、钛能生成自愈钝化膜不同,镁表面生成的氧化膜疏松多孔,不能对基体起有效保护作用,因此,在潮湿的空气、含硫气氛和海洋大气中,镁均会遭受严重的化学腐蚀,这极大地阻碍了其广泛应用。
通过合金化的方法来改善其性能,特别是期望发现“不锈镁”的努力至今还没有取得进展。
所以,镁合金零件在使用前须经过一定的表面改性或涂层处理。
目前,电化学镀层、转化膜等工艺技术已经应用于镁合金的防护,气相沉积涂层、涂覆、表面热处理等方法也受到密切关注,高能束熔覆等新技术也被尝试应用于镁合金表面性能的提高。
二.表面处理方法1.电镀和化学镀技术镁合金表面镀镍技术分为电镀和化学镀两种。
由于镁合金化学活性高,在酸性溶液中易被腐蚀,因此镁合金电沉积技术与铝合金电沉积技术有着显著的差异。
目前,镁合金电镀工艺技术有两种工艺:浸锌-电镀工艺和直接化学镀镍工艺。
为了防止镁合金基体在酸性溶液中被过度腐蚀,需要在处理前溶液中添加F-(F-与电离生成的Mg2+形成MgF2沉淀,吸附在镁合金基体表面可以防止基体过度腐蚀。
镁合金表面化学镀Ni-P合金是一种很成熟的工艺。
通常化学镀方法制备的Ni-P合金层是非晶态的,这层致密的非晶态Ni-P合金层可以有效地防止镁合金基体被腐蚀。
结合使用化学镀镍技术和滚镀技术可以在镁合金基体上形成一层晶态的Ni-P合金层。
镁合金铸件

镁合金铸件
镁合金铸件是由镁合金材料制成的铸件,是一种常见的金属铸造
工艺。
镁合金具有密度低、强度高、刚性好、导热性能好等优点,因
此被广泛应用于航空航天、汽车、电子、电器等领域。
镁合金铸件的制造过程一般包括材料准备、模具设计、熔炼和浇注、冷却和回复以及后处理等步骤。
首先,将合适比例的镁合金原料
混合,并通过加热熔炼的方式得到熔融的镁合金液态材料。
然后,将
熔融的镁合金通过浇注的方式倒入预先设计好的模具中,待凝固后即
可获得所需的铸件形状。
冷却和回复过程有助于提高铸件的力学性能
和表面质量。
最后,还需要进行去毛刺、修整、热处理等后处理步骤,以使铸件达到设计要求。
镁合金铸件具有重量轻、强度高、刚性好、耐腐蚀等优势,因此
在航空航天和汽车领域得到广泛应用。
随着镁合金材料和铸造工艺的
不断进步,镁合金铸件在其他领域也逐渐应用,如电子产业中的手机壳、电器领域的散热器等。
镁合金的塑性变形及再结晶热处理对其组织性能的影响

4
轧制前的平均晶粒尺寸约40um, 15%压下量轧制并退火后平均晶粒
3.3 EX-AZ31B: tensile properties on different directions
TD 45
TD
orientation
σb/ MPa
σ0.2/ MPa
δ/ %
ED
280.0
200.4
13.2
ED
45°
258.0
125.2
19.0
TD
276.0
107.4
16.2
ED
350
➢ 有色金属材料制品中70%以上是板、带材,轧制变形 镁合金板材的研究和加工技术的突破对开发变形镁合 金产品有重要促进作用。
2、变形镁合金塑性变形原理
➢ 镁合金的塑性变形特征:HCP晶体结构及c/a轴比值造成镁的 塑性变形困难。
➢ 塑性变形机制:滑移、孪生、超塑性; ➢ 板材塑性加工方法:热加工、温加工、冷(常温)加工;
压下量
14
退火工艺
15%
30%
45%
55%
12
200度退火1h
8.9um
6.9um
5.8um
4.9um
10
400度退火5min
12.1um
8.2um
7.5umum
9.2um
7.8um
7.0um
6
annealing1h at 2000c annealing1h at 3500c
0.01 s-1
0.1 s-1
1 s-1
5s-1
10s-1
1
σ
1 0.0227
l 82
n
Z 5.5 5 1 01 2
热处理-有机覆膜预处理镁合金表面的快速仿生矿化研究

热处理-有机覆膜预处理镁合金表面的快速仿生矿化研究[摘要]本文研究了热处理-有机覆膜处理对镁合金在不同模拟体液中仿生矿化过程的影响。
实验首先比较了未处理、热处理-有机覆膜预处理后的镁合金az91d试样在模拟体液(simulated body fluid,sbf)中的腐蚀速率和对溶液ph的影响。
然后提高sbf中的某些离子浓度,研究未处理和预处理试样在改性模拟体液(modified sbf, m-sbf)中的仿生矿化行为。
研究结果表明,经过热处理-有机覆膜预处理的az91d试样在sbf溶液中的耐蚀性有较大的提高,有机覆膜的离子诱导作用以及m-sbf溶液中充足的离子供给使羟基磷灰石涂层在试样表面快速、均匀生长。
[关键词]镁合金预处理腐蚀仿生矿化羟基磷灰石中图分类号:tg178文献标识码:a文章编号:1009-914x(2013)17-0097-03镁合金作为一种潜在的人体植入材料,具有优越的生物相容性和力学相容性[1-2]。
它有较好的抗凝血和血液相容性,能促进骨细胞的生成和加速骨折的愈合,不必担心微量金属离子对细胞的毒性[3]。
镁合金的密度(~1.80 g/cm3)与人体密质骨的密度(~1.75 g/cm3)相近;强度和弹性模量等综合力学性能也与人体骨相近,能够有效避免应力阻挡效应[4,5]。
从上世纪就有科学家曾尝试将纯镁用于整形与外伤的手术中[6,7]。
然而,镁合金在人体环境中腐蚀速率过快,所产生的大量气体容易引起皮下鼓泡,导致手术失败[8]。
因此,镁合金在人体中的耐腐蚀研究显得异常关键。
要解决医用镁合金的耐腐蚀性问题,就需要研究镁合金表面改性的方法。
但是,目前关于生物医用镁合金表面改性的报道较少,大部分研究集中于医用纯镁的研究[9]。
目前,医用纯镁表面改性方法主要包括仿生矿化法、激光熔覆、等离子喷涂、电泳沉积等。
与其他表面改性技术相比,仿生矿化法具有所需设备简单、操作方便、沉积工艺易控制等特点[9,10]。
镁合金的热处理工艺与力学性能改善

镁合金的热处理工艺与力学性能改善镁合金作为一种轻量化材料,在航空航天、汽车制造等领域有着广泛的应用。
然而,镁合金在实际应用中存在一些问题,如低强度、低韧性和不良的耐腐蚀性能。
因此,研究镁合金的热处理工艺,以提高其力学性能,具有重要意义。
本文将介绍镁合金的热处理工艺以及力学性能改善的方法。
热处理是一种通过控制材料的加热和冷却过程,改变其晶体结构和性能的方法。
对于镁合金的热处理,主要包括固溶处理、时效处理和变形加工。
首先,固溶处理是指将镁合金加热到高温区,使合金中的固态溶质元素溶解在镁基体中,然后快速冷却。
这一步骤能够消除合金中的析出相和晶界相,提高合金的强度和塑性。
同时,通过调节固溶温度和时间,还可以控制合金的晶粒尺寸,从而进一步提高其力学性能。
其次,时效处理是在固溶处理后将镁合金再次加热到较低的温度,保持一定的时间,使合金中的溶质元素重新析出形成弥散的析出相。
时效处理可以提高镁合金的强度和硬度,同时还能增加合金的韧性和耐腐蚀性能。
不同类型的镁合金需要在不同的时效温度和时间下进行处理,以获得最佳的力学性能。
最后,变形加工是通过机械或热加工使镁合金发生塑性变形,从而改变其晶体结构和力学性能。
常用的变形加工方式包括挤压、拉伸、压缩等。
通过变形加工,可以使晶粒细化,提高材料的塑性,并改善其力学性能。
除了热处理工艺,还有其他一些方法可以改善镁合金的力学性能。
例如,合金化是通过添加适量的合金元素,如锆、铝、锡等,来改善镁合金的强度和韧性。
同时,采用纳米颗粒强化技术和表面改性技术,也可有效增强镁合金的力学性能和耐腐蚀性能。
总结起来,镁合金的热处理工艺和力学性能改善涉及到固溶处理、时效处理、变形加工以及其他一些方法的综合应用。
通过合理选择和控制这些工艺参数,可以显著提高镁合金的强度、塑性和耐腐蚀性能,满足实际工程应用的需求。
进一步的研究和探索,将有助于推动镁合金材料的发展与应用。
镁合金的热处理工艺与力学性能优化

镁合金的热处理工艺与力学性能优化在当今工业领域中,镁合金由于其优异的力学性能和较低的密度而备受关注。
然而,镁合金的综合性能受到热处理工艺的影响,在工业应用中具有重要意义。
本文将探讨镁合金的热处理工艺及力学性能优化的方法。
一、热处理工艺的基本原理热处理是指通过加热和冷却等工艺操作,改变材料的显微组织和力学性能。
对于镁合金而言,主要包括固溶处理和时效处理两个阶段。
1. 固溶处理固溶处理是指通过加热镁合金到一定温度,使其固解体中的非稳定相或析出相溶解于基体中,形成固溶体。
镁合金的固溶温度通常在450℃-500℃范围内,时间取决于合金的成分和厚度。
2. 时效处理时效处理是在固溶处理完成后,将材料进行特定温度下的保温处理,以实现析出相的形成和析出相粒子尺寸的增长。
时效温度通常在100℃-250℃之间,时间也根据合金的具体需求进行调控。
二、热处理对力学性能的影响热处理对镁合金的力学性能有着显著影响,主要体现在以下几个方面:1. 强度与硬度通过适当的固溶处理和时效处理,能够提高镁合金的抗拉强度和硬度。
适当的固溶处理有助于消除合金中的组织缺陷,提升结晶度和强度,而时效处理则能进一步提高合金的硬度。
2. 韧性在热处理过程中,通过调控固溶温度和时效时间,可以使镁合金中析出相的尺寸和分布均匀化,从而提高合金的韧性。
均匀分布的析出相能够限制晶界滑移和裂纹扩展,从而提高镁合金的抗拉伸性能。
3. 耐蚀性适当的热处理工艺能够改善镁合金的耐蚀性能。
通过固溶处理和时效处理可以调控合金中的析出相含量和类型,进而改善合金的耐蚀性能。
例如,合金中的镁铝相能够提高合金的耐蚀性。
三、力学性能优化的方法为了优化镁合金的力学性能,可以采取以下几种方法:1. 优化热处理工艺参数通过调节固溶和时效处理的温度、时间和冷却速率等工艺参数,可以获得适合特定应用需求的镁合金。
不同合金成分对应不同的热处理参数,因此需要对不同合金进行个性化的热处理优化。
2. 添加合金元素通过添加适量的合金元素,如铝、锌、锰等,可以调节镁合金的相结构、晶粒尺寸和析出相的类型,从而优化合金的力学性能。
镁合金的热处理与力学性能研究

镁合金的热处理与力学性能研究镁合金作为一种轻质高强度材料,具有广泛的应用前景。
但是,由于镁合金的低熔点和高固溶度,使得其在加工和使用过程中容易发生晶粒长大、力学性能下降等问题。
因此,研究镁合金的热处理方法以及其对力学性能的影响,对于进一步提高镁合金的应用性能具有重要意义。
一、热处理方法1. 固溶处理固溶处理是对镁合金进行热处理的一种常用方法。
通过在高温下加热镁合金,使其中的合金元素溶解于基体中,然后在适当的速度下冷却,从而达到改善镁合金组织和性能的目的。
2. 时效处理时效处理是指在固溶处理后,将镁合金在适当的温度下保持一段时间,以促进析出相的形成和组织的稳定。
3. 淬火处理淬火处理是通过将加热至高温的镁合金迅速冷却至常温,以改变其组织和性能的方法。
淬火能够使镁合金中的相转变、晶粒细化,并提高材料的强度和硬度。
二、热处理对力学性能的影响1. 强度和硬度的提高热处理能够减少镁合金中的晶界、亚晶界和位错,促使其晶粒细化,从而提高了材料的强度和硬度。
此外,通过合理的热处理方法,还能促使析出相的形成,进一步提高镁合金的力学性能。
2. 可塑性的改善热处理能够改善镁合金的可塑性,降低其断裂韧性,从而增加了材料的加工性能。
通过热处理使镁合金中的晶粒细化和析出相的形成,能够提高材料的成形能力,减少加工过程中的损伤和断裂。
3. 耐腐蚀性能的提升热处理可以减少镁合金中的含氧化物和含气孔,改善材料的表面质量和耐腐蚀性能。
热处理还能够促使形成致密的氧化膜,提高材料的耐蚀性和耐氧化性。
三、热处理工艺优化的研究针对不同类型的镁合金,研究者通过调整热处理工艺参数,优化镁合金的组织和性能。
例如,通过改变固溶处理温度、时效处理时间和淬火速度等工艺参数,可以实现镁合金力学性能的最佳化。
此外,还可以通过引入微合金元素、添加合适的强化相等方法来改善镁合金的力学性能。
研究者们也通过采用不同的热处理方法结合其他表面处理技术,如电沉积、喷涂等,进一步提高镁合金的耐腐蚀性、磨损性和疲劳寿命等。
- 1、下载文档前请自行甄别文档内容的完整性,平台不提供额外的编辑、内容补充、找答案等附加服务。
- 2、"仅部分预览"的文档,不可在线预览部分如存在完整性等问题,可反馈申请退款(可完整预览的文档不适用该条件!)。
- 3、如文档侵犯您的权益,请联系客服反馈,我们会尽快为您处理(人工客服工作时间:9:00-18:30)。
浅谈镁合金材料的热处理方法
摘要:镁在地壳中的含量很高,但由于纯镁的抗拉强度和硬度很低,所以在生产生活中一般通过加入合金元素,与镁形成固溶体进而提高其力学性能。
除此以外镁合金还可进行热处理,主要包括T2、T4、T5、T6 等热处理方法,改善合金使用性能和工艺性能、发挥材料潜力的一种有效的方法。
镁合金热处理的目的是在不同程度上改善它的力学性能,比如抗拉强度、屈服强度、硬度、塑性、冲击韧性和伸长率等。
镁是在自然界中分布最广的十个元素之一,在地壳中是第八丰富的元素,约占地球壳层质量的1.93%。
其在海洋质量含量为0.13% 。
镁的抗拉强度和硬度很低。
一般通过加入合金元素,与镁形成固溶体,或是在固溶体中加入一定数量的过剩强化相来强化合金,即固溶强化和第二相强化[1] 。
除此加入合金元素外还可以通过热处理来提高
镁合金的性能[2] 。
热处理是改善合金使用性能和工艺性能、发挥材料潜力的一种有效的方法。
镁合金热处理的目的是在不同程度上改善它的力学性能,比如抗拉强度、屈服强度、硬度、塑性、冲击韧性和伸长率等。
其热处理方法有以下几类:T1—部分固溶加自然时效;T2 —铸后退火;T3—固溶加冷加工;T4 —固溶处理;T5—人工时效;T6—固溶处理加人工时效;T7 —固溶处理加稳定化处理;T8 —固溶处理、冷加工加人工时效。
其中最常用的为T2 、T4、T5、T6 热处理方法。
关键词:镁合金热处理材料成型
一、T2 、T 4、T 5、T 6 热处理方法
1 T
2 处理
又称均质化退火,其目的是消除铸件在凝固过程中形成的晶内偏析。
减小或消除变形镁合金制品在冷热加工、成形、校正和焊接过程中产生的残余应力,也可以消除铸件或铸锭中的残余应力。
凝固过程中模具的约束、热处理后冷却不均匀或者淬火引起的收缩等都会导致镁合金铸件中出现残余应力。
此外,机加工过程中也会产生残余应力,所以在最终机加工前最好进行中间去应力退火处理。
2 T4 处理[3]
T4即固溶处理后进行自然时效。
镁合金中合金元素固溶到A—Mg 基体中形成固溶体时,镁合金的强度、硬度会得到提高,称为固溶强化,而这个过程就称为固溶处理。
加热温度越高,镁合金中强化相和合金元素溶解得也就越充分,固溶处理后的力学性能也就越高。
固溶过程中,保温时间与加热温度相互关联的,加热温度越高,保温时间就相对越短。
然而加热温度过高或者保温
时间过长,合金基体组织就会发生粗化甚至过烧现象,这样将导致合金的力学性能的下降。
为了获得最大的过饱和固溶度,同时又使基体不至于过烧,加热温度通常只比固相线低5~10℃。
3 T5处理
T4即时效处理,将固溶处理后的过饱和固溶体置于一定温度下,放置一定的时间后过饱和固溶体将会发生分解,引起合金的强度和硬度大幅度提高,这个过程称之为时效处理。
其本质是脱溶或沉淀,让固溶体中的溶质脱离出来,以沉淀相析出。
固溶处理后获得的都是过饱和固溶体,有分解的趋势,在一定的温度下,过饱和的溶质便会以B相脱溶出来,弥散分布在A相基体中。
能够起钉扎作用,对材料内部滑移、孪晶等起到阻碍作用。
4 T6处理
此种方法即是将镁合金进行固溶处理后进行人工时效。
通过以上的热处理方法可以提高镁合金的抗拉强度、屈服强度、硬度、塑性、冲击韧性和伸长率等性能。
二、固溶和时效
1、固溶处理
要获得时效强化的有利条件,前提是有一个过饱和固溶体。
先加热到单相固溶体相区内的适当温度,保温适当时间,使原组织中的合金元素完全溶入基体金属中,形成过饱和固溶体,这个过程就称为固溶热处理。
由于合金元素和基体元素的原子半径和弹性模量的差异,使基体产生点阵畸变。
由此产生的应力场将阻碍位错运动,从而使基体得到强化。
固溶后屈服强度的增加将与加入溶质元素的浓度成二分之一次方比。
根据Hmue-Rothery规则,如果溶剂与溶质原子的半径之差超过14%~15%,该种溶剂在此种溶质中的固溶度不会很大。
而Mg的原子直径为3.2nm,则Li,Al,Ti,Cr,Zn,Ge,Yt,Zr,Nb,Mo,Pd,Ti,Pb,Bi等元素可能在Mg 中会有显著的固溶度。
另外,若给定元素与Mg的负电性相差很大,例如当Gordy 定义的负电性值相差0.4以上(即∣xMg-x∣>0.4)时,也不可能有显著的固溶度。
因为此时Mg和该元素易形成稳定的化合物,而非固溶体。
2、人工时效
沉淀强化是镁合金强化(尤指室温强度)的一个重要机制。
在合金中,当合金元素的固溶度随着温度的下降而减少时,便可能产生时效强化。
将具有这种特征的合金在高温下进行固溶处理,得到不稳定的过饱和固溶体,然后在较低的温度下进行时效处理,即可产生弥散的沉淀相。
滑动位错与沉淀相相互作用,使屈服强度提高,镁合金得到强化:
Tyield=(2aGb)/L+τa (1)
式中Tyield为沉淀强化合金的屈服强度;τa为没有沉淀的基体的屈服强度;(2aGb/L)为在沉淀之间弯出位错所需的应力。
由于具有较低的扩散激活能,绝大多数镁合金对自然时效不敏感,淬火后能在室温下长期保持淬火状态。
部分镁合金经过铸造或加工成形后不进行固溶处理而是直接进行人工时效。
这种工艺很简单,可以消除工件的应力,略微提高其抗拉强度。
对Mg-Zn系合金就常在热变形后直接人工时效以获得时效强化效果,即可获得T5状态加工产品。
参考文献:
[1]H an B Q,Dlunand D C. Micro st ructure and mechanical pr dpert ies of magnesium co ntaining hig h volume fract io ns y tt ria dispersoids[ J] . Mater Sci Eng A,2000,P277:297.
[2]ASM. Inter nat ional Mag nesium and Magnesium Alloy[M].OH:MetalPark. 1999.
[3]张青辉. 耐热镁合金的组织与高温性能[D].成都:四川大学,2007,27~29.。