汽车塑料外饰件的设计
汽车内外饰结构设计讲解

门护板下本体,通常作为门护板骨架,连接和安装门护板总成的其他零件,并且设计有与 门内板钣金的主要安装定位结构。通常采用注塑工艺成型,需要有足够的刚度和强度,以 保持门护板总成的形状。安装点要分布均匀。
地毯的典型结构、工艺和材料
地毯主要有簇绒地毯、针刺地毯和PVC地毯等。 簇绒地毯一般由尼龙簇绒软面、EVA重涂层和无纺布3层构成,(如下图所示)。其 制作工艺一般是将尼龙和涤纶丝织成簇绒毯面,再将尼龙簇绒软面、EVA重涂层和无纺 布放入模具热压成型。高档簇绒地毯背面还有PU发泡层,其主要作用是为了提供舒适的 感觉和良好的隔声\吸音性能,这要求地毯在热压成型后增加模具内发泡的工艺。 尼龙针刺地毯没有EVA重涂层和无纺布,采用热压工艺成型。 PVC地毯没有EVA重涂层和无纺布,同样采用热压工艺成型。 目前簇绒地毯和针刺地毯在成型后多采用水切割工艺来加工边界和开口。
目前主流汽车厂,大量采用钣金焊接型仪表台横梁。根据其断面形状,又可分为盒形 横梁和管柱型横梁。管柱型横梁,由于有比较明显的价格及性能优势,因而被广泛应 用。 管柱形横梁又分为直管型和弯管型。 直管型横梁对结构和安全性能非常有利,成本较低,但受仪表台总成系统中个零件布 置有较大限制。 弯管型横梁对仪表台总成零件布置相对有利,但会削弱结构和安全性能,制造相对复 杂一些,尺寸稳定性较差。
比较简单的门护板,如左图,由门护板 本体加必要功能件:内扣手、扶手面板、 地图袋、玻璃升降开关等组成。这类门 护板一般在经济型轿车和货车中较常见, 甚至比左图中的更简单。 这类门护板本体,通常采用注塑成型。
Q-JLY_J711168-2008汽车内外饰塑料件通用技术条件

湿箱中保温 24 h,温度为 40℃±2℃,相对温度为 95%。接着在本标准 4.1.2 规定的环境下冷却 24 h。
5.10.2.2 在本标准 4.3 规定的环境温度下,通过测力计测定其所能承受的最大拉伸力,其拉伸速度为
100mm/min,拉伸方向垂直于焊缝方向。
5.10.2.3 试验后,将评估结论及可能观察到的现象进行记录。
5.10.2.1 在待测试的产品上截取两块焊缝长度为 50 mm 的试样。把两块试样分别进行下述两种不同的老
化处理:在本标准 4.1.1 规定的环境箱中保温 100 h,温度为 90℃±2℃;在本标准 4.1.3 规定的恒温恒
共 10 页 第 5 页
GEELY
汽车内外饰塑料件通用技术条件
Q/JLY J711168-2008
要求
外饰件
1
低温抗冲击性能
经低温抗冲击性能试验后,不允许出现开裂、折断、剥离和永久变形等现象。
2
抗划伤性能
经抗划伤性能试验后,不允许出现肉眼可见的划伤。
3
燃烧性能
应符合 GB8410 中的规定。
4
耐候性能
经耐候性能试验后,应不出现龟裂、斑点或其它缺陷,灰色标度值不小于 4 级。
5
气味性能
气味性应高于 6 级。
Q/JLY J711168-2008
4.1.4 振动试验台:应能实现上下、左右、前后三个坐标轴的振动。 4.1.5 氙光曝晒试验箱: 应符合 GB/T 16422.2-1999 的规定。 4.1.6 测力计:应该能适应拉延速率(0~100)mm/min。 4.2 试验仪器 4.2.1 燃烧特性测定仪:符合 GB 8410 的规定。 4.2.2 耐磨试验仪 4.2.3 钢球:直径 60mm、质量 0.9kg 的钢球,用来做冲击试验。 4.2.4 抗划伤性试验仪:应具有下述特点的刀具组成:
汽车外饰件的镶嵌结构设计

汽 车外饰件 的镶嵌 结构设 计
刘廷 福 ,陈 晓玲
( 上汽通用五 菱汽车股份有 限公 司 ,广西 柳 州 40 7 I 50) 5
【 要】 摘 文章主要阐述汽车外饰件的几种镶嵌结构的设计及其镶嵌结构对塑料件的影响,分析了各种镶嵌结构的
件 内部 ,对 产 品 的 外 观 和 装 配并 无 影 响 ;如 果 镶 嵌 螺 栓 不 能 在
模 具中被放置到位 ,容易使 整个产 品报废或者造成模具损坏。
11 镶 嵌 螺栓卡 入 式结 构 的设计 .. 2
镶嵌螺栓卡入式 的结 构与镶嵌螺栓 直接注塑在塑料件 中结 构的设计主要 的不 同是镶嵌螺栓 与尾 门拉手 主体 的连接方式 ,
别 以 X 微 型 车 的 尾 门拉 手 、前 盖 装 饰 板 来 说 明几 种 镶 嵌 结 构
的设 计 。
11 尾 门拉 手镶 嵌 结构 的设 计 .
在 尾 门 卜的尾 门拉 手 是 汽 车 外 装 饰 件 ,更 是 在 尾 门 开 启 中
图 1 镶嵌 结构截 面 ( 单位 :mm)
部件功能的要求 。本文 以安装截面 图的形式 ,分析 了各种安装
方式 的优 缺点 ,最 终 确 定 _适 合 汽 车 外 饰 件 的镶 嵌 结 构 。 r
1 汽车外饰件镶嵌结构 的设 计
所 谓 镶 嵌 结 构 是 指 在 塑 料 产 品 中镶 嵌 或 装 配 有 金 属 紧 固件
或者非金属 紧固件 ( 如螺栓 、螺母 、 扣等) 的结构 。我们分
镶 嵌 螺 栓 与 装 配 支撑 座 配 合 尺 寸不 同 。 卡பைடு நூலகம் 式 的结 构 主 要 是 零
汽车轻量化下塑料铰链结构的设计与应用

13910.16638/ki.1671-7988.2021.09.041汽车轻量化下塑料铰链结构的设计与应用刘志明(上汽大众汽车有限公司,上海 210805)摘 要:为实现汽车轻量化设计,汽车塑料零件的集成是一个有效的手段。
以两个典型实例介绍了塑料铰链结构在汽车外饰中的应用场景和设计方法。
利用该技术实现了减少零件和模具数量、节省装配工时等目标。
关键词:铰链结构;塑料;外饰零件;轻量化中图分类号:U464.13 文献标识码:A 文章编号:1671-7988(2021)09-139-04Design and Application of Plastic Hinge Structure in Lightweight AutomobileLiu Zhiming( SAIC V olkswagen Automobile Co., Ltd., Shanghai 210805 )Abstract: In order to realize the lightweight design of automobile, the integration of plastic parts is an effective means. The application scene and the development method of plastic hinge structure in automobile exterior parts are introduced with two examples. The purpose of reducing the number of parts and molds, and saving the assembly time was achieved. Keywords: Hinge structure; Plastic; Exterior parts; LightweightCLC NO.: U464.13 Document Code: A Article ID: 1671-7988(2021)09-139-04引言随着汽车造型的日益复杂化,塑料件占据整车重量和成本的比例越来越高。
JT 汽车外饰塑料零件通用技术条件
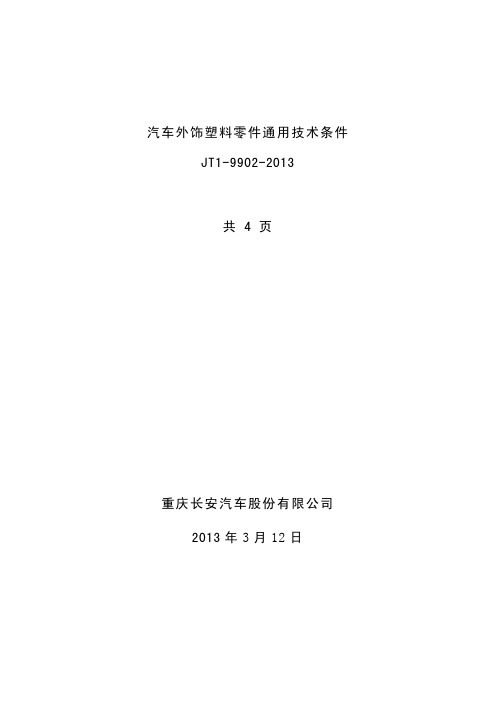
汽车外饰塑料零件通用技术条件JT1-9902-2013共 4 页重庆长安汽车股份有限公司2013年3月12日汽车外饰塑料零件通用技术条件JT1-9902-2013编制 赖 礼 汇校核 陈 雷审定 王 晓批准 曹 渡更改记录规范编号制定/修订者制定/修订日期批准日期JT1-9902-2013 赖礼汇2013-3-11 曹渡2013-3-12JT1-9902-2013汽车外饰塑料零件通用技术条件1 范围本技术条件规定了前格栅、前罩装饰件、扰流板、防擦条、侧围护板、轮罩衬板、保险杠、三角窗外盖板、后牌照灯盖、发动机装饰罩盖等等外饰塑料零件的基本性能要求及试验方法。
本技术条件适用于长安汽车股份有限公司所开发的所有轿车车型。
2 规范性引用文件SAE J2527 汽车外饰材料加速老化实验标准:可控辐照度氙弧灯SJ-NW-15 塑料件涂装要求规范SJ-NW-16 塑料镀铬件性能要求规范SJ-NW-57 汽车塑料内饰件耐刮擦实验方法及结果判定SJ-NW-101 汽车塑料内饰件耐刮擦实验方法(划格法)3 要求3.1 除非另外规定,否则应符合本技术条件的要求,并按经规定程序批准的图样与技术文件制造。
喷漆零件除了满足本技术条件外,还应满足SJ-NW-15的要求。
电镀零件除了满足本技术条件外,还应满足SJ-NW-16的要求。
3.2 外观要求:所有零件外观应与经确认后的样品一致。
1)产品外观面不允许有裂纹、变形、银纹、波纹、烧焦、飞边、毛刺、气泡、浇口痕迹、顶杆印痕、熔接痕和收缩痕等不可接受表面缺陷。
2)喷涂或镀铬的产品,表面涂层或镀层均匀一致、色泽均匀,外观表面不允许有目视可见的麻点、起泡、漏镀、变色、脱落及其他不可接受缺陷。
3)产品A面上的分模线应小于0.1mm;非主视外观面分模线的痕迹小于0.2mm。
且必须经过长安公司技术部门的认可。
4)零件表面的颜色和花纹应与经规定程序批准的色板或样品一致。
皮纹要清晰、色泽均匀,皮纹类型、纹理方向、纹理深度以及皮纹范围应与长安公司所要求的一致,由于因脱模方向引起的非主要表面皮纹深度变化要均匀,不允许出现皮纹拉伤。
汽车外饰件品质标准

汽车外饰件品质标准
汽车外饰件的品质标准通常包括以下几个方面:
1. 材料质量:汽车外饰件通常使用的材料包括塑料、玻璃纤维、铝合金等。
这些材料需要具备一定的强度、韧性和耐磨性,以确保外饰件在使用过程中不易损坏。
同时,材料还需要符合环保要求,如不含有有害物质。
2. 表面处理:汽车外饰件的表面通常需要经过特殊处理,如镀铬、喷涂等,以提高其表面光泽度和防腐蚀性。
这些处理需要符合相关标准,如耐腐蚀性、耐候性等要求。
3. 外观尺寸和精度:汽车外饰件的外观尺寸和精度需要符合设计要求,以保证其与其他零部件的配合。
这包括外饰件的平直度、曲率、角度等方面的测量。
4. 安装性能:汽车外饰件需要具备一定的安装性能,以便安装在车身上。
这包括外饰件的连接方式、安装孔的位置和尺寸等方面的要求。
5. 耐用性和抗疲劳性:汽车外饰件需要具备一定的耐久性和抗疲劳性,以承受长期使用和各种路况带来的振动和冲击。
这包括外饰件材料的强度、刚度等方面的要求。
以上是一些常见的汽车外饰件品质标准,不同的汽车制造商和车型可能会有不同的要求和标准。
汽车保险杠的配方设计
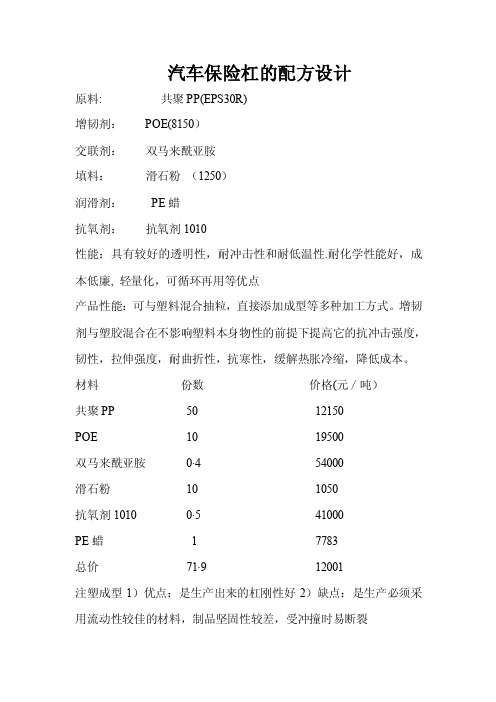
汽车保险杠的配方设计原料: 共聚PP(EPS30R)增韧剂:POE(8150)交联剂:双马来酰亚胺填料:滑石粉(1250)润滑剂:PE蜡抗氧剂:抗氧剂1010性能:具有较好的透明性,耐冲击性和耐低温性.耐化学性能好,成本低廉, 轻量化,可循环再用等优点产品性能:可与塑料混合抽粒,直接添加成型等多种加工方式。
增韧剂与塑胶混合在不影响塑料本身物性的前提下提高它的抗冲击强度,韧性,拉伸强度,耐曲折性,抗寒性,缓解热胀冷缩,降低成本。
材料份数价格(元/吨)共聚PP 50 12150POE 10 19500双马来酰亚胺0·4 54000滑石粉10 1050抗氧剂1010 0·5 41000PE蜡 1 7783总价71·9 12001注塑成型1)优点:是生产出来的杠刚性好2)缺点:是生产必须采用流动性较佳的材料,制品坚固性较差,受冲撞时易断裂前言汽车保险杠是吸收缓和外界冲击力,防护车身前后部的安全装置。
20年前,轿车前后保险杠是以金属材料为主,用厚度为3mm 以上的钢板冲压成U型槽钢,表面处理镀铬,与车架纵梁铆接或焊接在一起,与车身有一段较大的间隙,好像是一件附加上去的部件。
随着汽车工业的发展,汽车保险杠作为一种重要的安全装置也走向了革新的道路。
今天的轿车前后保险杠除了保持原有的保护功能外,还要追求与车体造型和谐与统一,追求本身的轻量化。
为了达到这种目的,目前轿车的前后保险杠采用了塑料,人们称为塑料保险杠。
塑料保险杠是由外板、缓冲材料和横梁三部分组成。
其中外板和缓冲材料用塑料制成,横梁用厚度为1.5mm左右的冷轧薄板冲压而成U形槽;外板和缓冲材料附着在横梁上,横梁与车架纵梁螺丝连接,可以随时拆卸下来。
这种塑料保险杠使用的塑料,大体上使用聚丙烯系材料,采用注射成型法制成。
国外还有一种称为聚碳酯系的塑料,渗进合金成分,采用合金注射成型的方法,加工出来的保险杠不但具有高强度的刚性,还具有可以焊接的优点,而且涂装性能好,在轿车上的用量越来越多。
汽车外饰件生产工艺流程

汽车外饰件生产工艺流程
汽车外饰件生产工艺流程:
①设计与工程:根据汽车的设计需求,使用CAD软件进行外饰件的初步设计和工程分析。
②模具设计与制造:基于设计图纸,开发模具,这通常涉及数控加工中心(CNC)和电火花加工(EDM)等技术。
③注塑成型:将熔融的塑料注入模具中,冷却固化后得到外饰件的初型。
④后处理:对注塑成型的零件进行修边、打磨、抛光等处理,以去除毛刺和飞边。
⑤装配:将成型的外饰件与其他组件如灯组、徽标、传感器等进行装配。
⑥表面处理:对外饰件进行喷涂、镀铬、印刷标识等表面修饰,以提升外观和耐候性。
⑦钣金冲压(针对金属外饰件):使用冲压机将金属板材冲压成所需的形状。
⑧焊接与粘接:使用焊接或粘接技术将金属或复合材料的部件固定在一起。
⑨检验:通过视觉检查、尺寸测量和功能测试来确保零件符合质量标准。
⑩包装:对合格的外饰件进行防尘、防潮的包装,以保护其在运输过程中的完好性。
⑪存储:将包装好的外饰件存放于适当的环境中,等待装配线的调用。
⑫运输:将外饰件从制造工厂运送到汽车组装厂,进行最终装配。
- 1、下载文档前请自行甄别文档内容的完整性,平台不提供额外的编辑、内容补充、找答案等附加服务。
- 2、"仅部分预览"的文档,不可在线预览部分如存在完整性等问题,可反馈申请退款(可完整预览的文档不适用该条件!)。
- 3、如文档侵犯您的权益,请联系客服反馈,我们会尽快为您处理(人工客服工作时间:9:00-18:30)。
汽车塑料外饰件的设计
二.汽车外饰件简介
汽车外饰件主要指前后保险杠、轮口、进气格栅、散热器面罩、防擦条等通过螺栓和卡扣或双面胶连接在车身上的部件。
在车身外部主要起装饰保护作用,及开启等功能。
汽车外饰件在车身上主要位置及大致形状见图一。
1.前保险杠,后保险杠,散热器面罩,前后轮口,侧饰条,防擦条,后视镜,进气格栅,背门饰板,车门外开手柄,扰流板,行李箱手柄
三.汽车塑料外饰件设计标准
由于汽车的特殊功能,外饰件设计必须坚持标准化,系列化,通用化的“三化”设计原则,同时满足合理性,先进性,维修方便性,可靠性,经济性,制造工艺性“六性”要求。
3.1产品“三化”设计
根据设计车型将要投放国家地区的不同,设计过程中必须全面贯彻执行当地的法规标准。
在造型设计之初产品设计师须学习了解相关法规标准并以此为依据进行设计。
这主要包括前保险杠上牌照安装孔间距尺寸规定,是否需欲留雾灯安装孔,外部突出物表面圆角及开口尺寸等相关要求。
另外有关散热器面罩迎风面积是否满足发动机,空调制冷要求,需在设计发布前得到相关部门认可。
充分考虑系列化产品的发展,零件安装固定尽量采用统一的螺栓螺母及卡扣等连接件,或通用其他车型的固定件,提高零件通用化程度,保证维修安装的方便性。
3.2材料的确定
3.2.1材料种类确定
塑料的种类繁多,目前汽车上广泛采用的主要是一些TPO,PP,ABS,PA6/PA66。
根据汽车外饰件不同的功能,使用工况,大致如下:
汽车外饰件材料一览表
3.2.2材料标准确定
同一类材料执行不同材料标准,其试验项目,成品性能,模具设计均有差异。
根据产品将要投放国家地区的不同,汽车材料工程师可确定材料具体执行的标准,或请原材料供应商提供相关资料。
现代轿车外饰件一般多为注塑喷漆或皮纹件,喷漆件为保证与车身颜色及漆面质量的一致,在选材时必须考虑喷涂系统。
例如北美车身油漆多采用高温烘烤系统,外饰件选材时相应亦须选择可高温烘烤的原料。
皮纹件选材时须特别考虑原料的颜色及耐候性能是否满足设计要求。
四.汽车塑料外饰件安装
外饰件一般均通过螺栓卡扣等连接件与车身本体或相邻件诸如翼子板或车门等相连。
为保证汽车外型的美观和防盗,所有外饰件安装点设计尽量隐藏在四门两盖内,但同时为方便维修拆卸,设计时更需考虑在更换零件时尽可能少拆或不拆周边零件。
车身外饰件安装方式和安装点数量与外饰件形状、外形尺寸及其功能有直接关系。
4.1安装方式
最简单的安装即用螺栓、螺母。
大部分外饰件均用此方式,如图二所示P点。
在设计安装面时应考虑安装工具所占空间,并尽量采用相同和常见的标准件,方便调整及维修。
一些小型非开启件常采用销定位胶粘接的连接方式,如防擦条(图一零件6)。
采用双面胶粘接的件为使零件与车身装配后配合紧密,设计时预先在零件上留出一凹槽面定的粘胶位置,为保证粘接强度,双面胶粘双面胶厚度一般为1mm至1.2mm,宽8mm至10mm,零件上凹槽为双面胶厚度的一半,如右图为防擦条基本结构。
有些外饰件如散热器面罩(图一零件8),侧饰条(图一零件5)常无法用螺栓连接,又不宜采用胶粘接的形式,则常常利用零件自身结构与其他件相连,或通过卡扣直接装在车身上。
如图二所示保险杠和散热器面罩的配合。
两件可在分装线上先分装成一体或由供应商直接提供分总成。
4.2安装点数量
外饰件安装点数量与零件的大小有直接关系,其安装点位置直接影响装配质量,主要是间隙和面差。
其中前后保险杠又是外饰件中最主要也是最直接影响整车效果的零件。
以前保险杠为例,上下左右安装点是支撑整个零件的核心,至少保证上部中间两点,左右各一点,下部不可少于四点。
同时为防止零件下沉,中部及侧边需有支撑支架或托板,见图二。
五.汽车塑料外饰件结构设计
塑料件设计不仅要满足使用要求,而且要符合塑料的成型工艺特点,并且尽可能使模具结构简单。
这样,可使成型工艺稳定,保证制品的质量,又可使生产成本降低。
外饰件的结构设计主要包括形状、壁厚、脱模角度、加强筋、支撑面、圆角、孔等。
5.1零件的形状
在造型师进行零件造型的同时,产品设计师更多考虑的则是零件的可制造性,可靠性等细节。
5.1.1可制造性
首先需分析确定零件的脱模方向,检查零件所有断面是否存在无法脱模的负角,尽量避免侧壁凹槽或与脱模方向垂直的孔,这样可简化模具结构,见图三。
零件边缘设计的好坏直接影响模具结构和制件的质量。
图四是一些设计中常常碰到的典型断面。
5.1.2可靠性
尽量避免零件局部突出过大的悬臂结构,如图二前保险杠上部两安装点M区域刚性较差,装配后零件易变形。
设计之初最好考虑两安装点连成一体或加宽凸缘,如图虚线所示,或背面加筋等方法解决。
在与车身要求有配合的边界加凸缘可以减少零件的变形量,提高配合精度,保证质量,见图二A-A、B-B断面所示。
5.2零件的壁厚
零件的壁厚一般力求均匀,否则会因固化或冷却速度不同而引起收缩不均匀,产生内因力,导致零件产生翘曲变形或缩孔。
图二散热器面罩基本断面,a为原结构,b为改进后结构,保持了料厚均匀一致,为提高模具寿命将局部不可见面削去。
汽车外饰件一般壁厚取2.5+0.25mm,大型件如保险杠取3+0.25mm至3.5+0.25mm。
为避免壁厚的变化影响零件表面质量,设计时特别强调料厚变化需保证足够的过渡区,如下图示。
T2-T1=T3
如果T3 1.0mm, D=25mm
如果T3 2.0mm, D=75mm
如果T3 2.5mm, D=100mm 推荐方案错误设计
5.3脱模角度
塑料件设计必须考虑脱模角度,避免脱模角度为零或负角。
脱模角度越大,零件越容易脱模,但容易造成零件厚度不均,影响制造精度。
图二散热器面罩断面,基本壁厚为3mm,如果脱模角度选择3,其最大壁厚处达7mm,最终零件表面会收缩,变形,并且浪费材料,减少迎风面积,甚至影响水箱冷却。
一般脱模角度与零件深度有关,最小和最大脱模角度可参考表二。
但皮纹件脱模角度相对非皮纹件需大些,具体与皮纹深度有关,一般每0.025皮纹深度需1脱模角度,皮纹深度增加时脱模角度随之加大。
表二:零件深度与脱模角度关系
4
15
130″6
26
2
5.4 加强筋
塑料件特别是大型零件如果仅仅有一定的壁厚是无法保证制件的形状和尺寸的,更谈不上一定的强度。
因此必须在一些如孔,大曲面或安装点处加筋,以提高强度和刚性。
外饰件主要表面(CLASSA)一般不宜加筋,次表面(CLASSB)加筋时根部壁厚也不可大于壁厚的3/4,对表面质量要求低或非可见表面(CLASS C&D),其相关尺寸见下图:
有时由于结构的限制,需在主要表面(CLASSA)背后布置安装点等,如图五为轮口安装点结构,此时为防止表面缩印,安装点壁厚尽量薄或局部开口,由于安装时此部位应力集中,为防止断裂,常加一些小筋。
5.5支撑面
若用整个面作为零件的支撑面,稍有变形就会影响与车身的配合。
因此实际常采用凸边或局部凸起的支角作为支撑面,而且对一些需紧密配合的零件设计时常采用如右图所示结构。
5.6圆角
外饰件表面不可有尖锐的楞线,凸出车身的外饰件圆角必须按相关标准设计,如我国GB11566《轿车外部突出物》对其有严格规定。
一般零件最小圆角取R0.5,但零件分型面避免有圆角,否则将增加制造成本和难度。
5.7孔
外饰件孔形状应尽量简单,孔与壁之间应保持一定距离,孔至边界最小至少是孔径的1.5倍。
6.结束语
现代汽车开发设计是汽车发展的核心,其本身又是一个技术高度密集的产业,强调各专业人员的团
队协作。
作为汽车设计的一部分,塑料外饰件的设计亦不例外,更是造型师,产品工程师,材料工程师,零件供应商以及方方面面各专业合作的结晶。
本人作为产品工程师,在多年的设计工作中更是深有体会,以上几个方面是本人在设计中积累的一点经验和体会,希望与各位交流探讨。