转速切削速度
切削速度值计算公式

切削速度值计算公式切削速度是指刀具在切削加工过程中的线速度,是切削加工中的重要参数之一。
切削速度值的计算对于加工质量和效率有着重要的影响。
在切削加工中,切削速度值的选择直接影响到切削加工的效率和刀具的使用寿命。
因此,了解切削速度值的计算公式是非常重要的。
切削速度值的计算公式可以根据切削加工的具体情况来确定,一般来说,切削速度值的计算公式可以表示为:Vc = π× D × n。
其中,Vc表示切削速度值,单位为m/min;π表示圆周率,取3.14;D表示刀具直径,单位为mm;n表示主轴转速,单位为r/min。
通过这个计算公式,我们可以很容易地计算出切削速度值。
在实际的切削加工中,我们可以根据这个公式来选择合适的切削速度值,以确保切削加工的效率和质量。
在实际的切削加工中,切削速度值的选择需要考虑多个因素。
首先,我们需要考虑刀具的材料和硬度。
不同材料和硬度的刀具,其适用的切削速度值也是不同的。
通常来说,硬度较高的刀具适用的切削速度值较低,而硬度较低的刀具适用的切削速度值较高。
其次,我们还需要考虑工件材料和硬度。
不同材料和硬度的工件,其适用的切削速度值也是不同的。
通常来说,硬度较高的工件适用的切削速度值较低,而硬度较低的工件适用的切削速度值较高。
此外,我们还需要考虑切削加工的类型和要求。
对于粗加工,一般可以选择较高的切削速度值,以提高加工效率;而对于精加工,一般需要选择较低的切削速度值,以保证加工质量。
在实际的切削加工中,我们可以根据这些因素来选择合适的切削速度值。
通常来说,我们可以根据刀具和工件的材料和硬度,以及切削加工的类型和要求,来确定合适的切削速度值范围。
然后,根据实际情况和经验,来选择具体的切削速度值。
在选择切削速度值时,我们还需要考虑切削加工的稳定性和安全性。
通常来说,切削速度值过高会导致切削加工的不稳定性和安全隐患,而切削速度值过低会导致加工效率低下。
因此,在选择切削速度值时,我们需要综合考虑各种因素,以确保切削加工的稳定性和安全性。
拉刀加工槽时切削速度计算
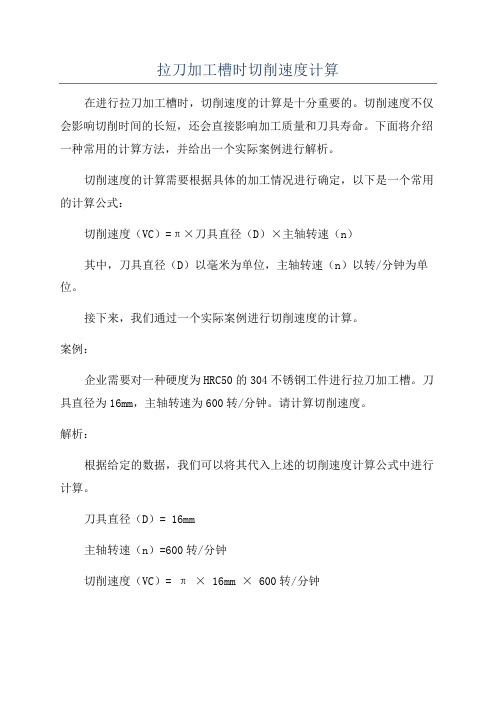
拉刀加工槽时切削速度计算在进行拉刀加工槽时,切削速度的计算是十分重要的。
切削速度不仅会影响切削时间的长短,还会直接影响加工质量和刀具寿命。
下面将介绍一种常用的计算方法,并给出一个实际案例进行解析。
切削速度的计算需要根据具体的加工情况进行确定,以下是一个常用的计算公式:切削速度(VC)=π×刀具直径(D)×主轴转速(n)其中,刀具直径(D)以毫米为单位,主轴转速(n)以转/分钟为单位。
接下来,我们通过一个实际案例进行切削速度的计算。
案例:企业需要对一种硬度为HRC50的304不锈钢工件进行拉刀加工槽。
刀具直径为16mm,主轴转速为600转/分钟。
请计算切削速度。
解析:根据给定的数据,我们可以将其代入上述的切削速度计算公式中进行计算。
刀具直径(D)= 16mm主轴转速(n)=600转/分钟切削速度(VC)= π × 16mm × 600转/分钟首先,我们需要将主轴转速(n)转换为秒单位。
1分钟=60秒,所以主轴转速(n)=600转/分钟=600/60=10转/秒切削速度(VC)= π × 16mm × 10转/秒接下来,我们计算切削速度的具体数值。
切削速度(VC)= 3.14 × 16mm × 10转/秒= 502.4 mm/秒所以,切削速度为502.4 mm/秒。
切削速度的计算对于拉刀加工槽的工艺参数确定至关重要。
正确设置切削速度不仅可以提高产品加工的效率和质量,还可以延长刀具的使用寿命,减少切削过程中的磨损和刀具断裂的风险。
因此,在实际工作中,必须根据实际情况和经验值来选择合适的切削速度。
同时,在切削速度计算中,还应考虑到切削液的使用和冷却系统的稳定性,以保证加工过程的顺利进行。
刀具转速计算公式

刀具转速计算公式刀具转速是在机械加工中非常重要的参数之一,它直接影响着切削加工的效率和质量。
在进行切削加工时,刀具的转速需要根据材料的硬度、切削深度、切削速度等因素进行合理的计算和选择。
本文将介绍刀具转速的计算公式及其应用。
刀具转速计算公式的基本原理是根据切削速度和刀具直径之间的关系来确定刀具的转速。
切削速度是指在切削过程中刀具切削材料的线速度,它是刀具转速和刀具直径的函数。
刀具转速计算公式可以表示为:N = (1000 V) / (π D)。
其中,N表示刀具的转速,单位为转/分钟;V表示切削速度,单位为米/分钟;D表示刀具的直径,单位为毫米;π表示圆周率,取3.14。
在实际应用中,切削速度是根据材料的硬度和切削工艺来确定的。
一般来说,硬度较高的材料需要较低的切削速度,而硬度较低的材料则需要较高的切削速度。
刀具的直径也是根据加工件的尺寸和形状来选择的。
因此,刀具转速计算公式可以帮助工程师根据具体的加工要求来确定刀具的转速,从而实现高效、高质量的切削加工。
除了上述的基本刀具转速计算公式外,还有一些特殊情况下的计算方法。
例如,在车削加工中,如果需要根据车刀刀尖半径和工件直径来确定刀具转速,可以使用以下公式:N = (1000 V) / (π D + π R)。
其中,R表示车刀刀尖半径,单位为毫米。
这个公式可以更精确地计算车刀的转速,从而提高车削加工的精度和效率。
另外,在铣削加工中,刀具的转速也是非常重要的参数。
铣削刀具的转速计算公式可以表示为:N = (1000 V) / (π D n)。
其中,n表示铣削刀具的刀齿数。
这个公式可以根据铣削刀具的刀齿数来确定合理的转速,从而实现高效的铣削加工。
在实际应用中,刀具转速的计算不仅仅是根据公式来确定的,还需要考虑到具体的加工情况和经验。
工程师在进行切削加工时,需要根据材料的特性、加工件的要求以及刀具的性能来综合考虑,从而确定合理的刀具转速。
此外,还需要根据实际情况对刀具转速进行调整和优化,以实现最佳的加工效果。
切削速度值计算公式

切削速度值计算公式在机械加工领域,切削速度是一个非常重要的参数,它直接影响着加工效率和加工质量。
切削速度值的计算对于机械加工过程中的刀具选择、切削参数确定等方面都具有重要的意义。
本文将从切削速度值的定义、计算公式以及影响因素等方面进行介绍。
一、切削速度值的定义。
切削速度是指刀具在加工过程中相对于工件表面的线速度,通常用Vc来表示,单位是m/min。
切削速度的大小直接影响着切削热量的产生和刀具的磨损情况,因此在实际加工中需要根据工件材料和刀具材料等因素来确定合适的切削速度值。
二、切削速度值的计算公式。
切削速度值的计算公式通常采用下面的公式来表示:Vc = π× D × n。
其中,Vc表示切削速度,π表示圆周率,D表示刀具直径,n表示主轴转速。
由此可见,切削速度值与刀具直径和主轴转速有直接的关系,通过调整这两个参数可以控制切削速度的大小。
三、影响切削速度值的因素。
1. 刀具材料。
不同的刀具材料对切削速度的要求也不同。
通常来说,硬度较高的刀具材料可以承受更高的切削速度,而且还能够提高刀具的使用寿命。
因此在选择刀具材料时需要考虑到切削速度的要求。
2. 工件材料。
不同的工件材料对切削速度的要求也不同。
一般来说,硬度较高的工件材料需要较低的切削速度,而硬度较低的工件材料则可以采用较高的切削速度。
因此在加工不同材料的工件时需要根据具体情况来确定切削速度的数值。
3. 主轴转速。
主轴转速是影响切削速度的重要因素之一。
通过调整主轴转速可以改变切削速度的大小,从而适应不同的加工要求。
在实际加工中需要根据刀具直径和工件材料等因素来确定合适的主轴转速。
四、切削速度值的应用。
切削速度值的计算对于机械加工过程中的刀具选择、切削参数确定等方面都具有重要的意义。
合理的切削速度值可以提高加工效率,减少刀具磨损,提高加工质量。
因此在实际加工中需要根据具体情况来确定合适的切削速度值,以达到最佳的加工效果。
总之,切削速度值的计算是机械加工中的重要内容,它直接影响着加工效率和加工质量。
vc切削速度公式

vc切削速度公式VC切削速度公式是机械加工中常用的一个重要公式,它表达了切削速度与刀具直径、旋转速度之间的关系。
这个公式在金属切削、雕刻、雕铣、切割等领域都非常有用。
那么,让我们来详细了解一下VC切削速度公式吧。
首先,VC公式中的V代表切削速度,一般用m/min来表示。
C代表理论周长,单位为mm,通常是指刀具周长。
我们可以将公式表示为:Vc=π×C×n/1000其中,n表示刀具转速,单位为r/min。
这个公式的意义在于,在机械加工中,可以通过合理地计算刀具的切削速率来提高生产效率,减少加工时间和成本,并且可以降低刀具磨损和制造废品的风险。
这对生产效率和经济效益都非常重要。
对于不同的材料和加工方式,VC公式中的参数也会有所不同。
例如,对于铸铁,由于其具有较低的切削性和硬性,VC值通常较低;而对于钢材,VC值较高。
同样的,刀具的直径和转速也会因材质和加工要求而异。
除此之外,在使用VC公式时,还需要注意以下几点:1. 刀具要做好切削前的准备。
要保证刀具的清洁和正确安装,避免出现偏差或其他不必要的问题。
2. 要进行准确的切削速度计算。
不要盲目地提高切削速度,否则会导致刀具的损坏或不稳定的加工质量。
3. 要定期检查刀具的切削性能。
这些包括切削力、切削温度、切削深度和刀具磨损等指标。
总之,VC切削速度公式是机械加工中不可或缺的公式之一。
通过合理使用这个公式,我们可以提高生产效率和经济效益,实现机械加工的高品质和高效率。
对于从事机械加工的工人和工程师来说,这个公式是必须要掌握并善加利用的。
外圆加工转速计算公式

外圆加工转速计算公式在机械加工中,外圆加工是常见的工艺之一。
外圆加工包括车削、磨削、镗削等多种加工方法,其中车削是最常用的一种。
在进行外圆加工时,转速的选择对加工质量和效率有着重要的影响。
因此,正确地计算外圆加工的转速是非常重要的。
外圆加工转速的计算涉及到一些基本的物理学原理和机械加工的知识。
在进行外圆加工时,为了保证加工质量和工件的表面粗糙度,需要选择合适的切削速度。
切削速度是指刀具在加工过程中切削工件的线速度,它是影响加工表面粗糙度和切削温度的重要参数。
在外圆加工中,切削速度的选择需要根据工件材料、刀具材料、刀具类型等因素来确定。
外圆加工转速的计算公式如下:n = 1000 V / (π D)。
其中,n为转速(单位,r/min),V为切削速度(单位,m/min),D为工件直径(单位,mm)。
在使用这个公式进行转速的计算时,需要首先确定切削速度。
切削速度的选择需要根据工件材料和刀具材料来确定。
一般来说,对于不同的工件材料,其切削速度的选择也会有所不同。
例如,对于碳钢、合金钢等普通钢材,其切削速度一般在30-60m/min之间;而对于不锈钢、铸铁等材料,其切削速度则需要在20-40m/min之间。
确定了切削速度后,就可以根据工件直径和上述公式来计算出转速。
例如,对于直径为100mm的工件,切削速度为40m/min的情况下,其转速计算如下:n = 1000 40 / (π 100) ≈ 1273r/min。
通过这个计算,我们可以得到在这种情况下,外圆加工的转速应该在1273r/min左右。
在进行外圆加工转速的计算时,还需要考虑到刀具的最大转速。
刀具的最大转速是指刀具在不发生破裂、变形的情况下所能承受的最大转速。
在进行转速的选择时,需要确保所选择的转速不超过刀具的最大转速,否则会对刀具造成损坏,甚至发生危险。
除了刀具的最大转速外,还需要考虑工件的加工精度和表面粗糙度。
在进行外圆加工转速的选择时,需要根据工件的要求来确定转速。
切削速度和进给速度公式
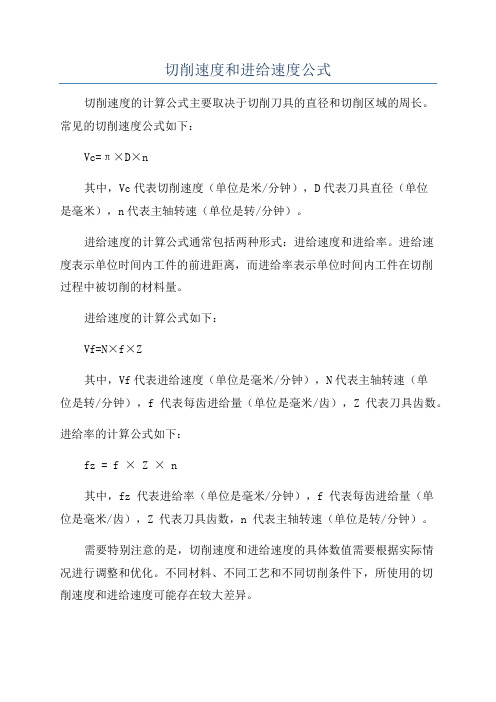
切削速度和进给速度公式切削速度的计算公式主要取决于切削刀具的直径和切削区域的周长。
常见的切削速度公式如下:Vc=π×D×n其中,Vc代表切削速度(单位是米/分钟),D代表刀具直径(单位是毫米),n代表主轴转速(单位是转/分钟)。
进给速度的计算公式通常包括两种形式:进给速度和进给率。
进给速度表示单位时间内工件的前进距离,而进给率表示单位时间内工件在切削过程中被切削的材料量。
进给速度的计算公式如下:Vf=N×f×Z其中,Vf代表进给速度(单位是毫米/分钟),N代表主轴转速(单位是转/分钟),f代表每齿进给量(单位是毫米/齿),Z代表刀具齿数。
进给率的计算公式如下:fz = f × Z × n其中,fz 代表进给率(单位是毫米/分钟),f 代表每齿进给量(单位是毫米/齿),Z 代表刀具齿数,n 代表主轴转速(单位是转/分钟)。
需要特别注意的是,切削速度和进给速度的具体数值需要根据实际情况进行调整和优化。
不同材料、不同工艺和不同切削条件下,所使用的切削速度和进给速度可能存在较大差异。
在实际应用中,切削速度和进给速度的选择通常需要考虑以下几个因素:1.材料硬度:通常情况下,硬度较高的材料需要使用较低的切削速度和进给速度,以避免刀具过快磨损。
2.切削刀具:不同切削刀具的切削速度和进给速度存在一定差异,需根据刀具特性进行选择。
3.机床性能:机床的主轴转速和进给速度对切削速度和进给速度的选择也有一定的限制。
4.切削过程:对于不同的切削过程(如粗加工、精加工等),切削速度和进给速度的选择也存在差异。
总之,切削速度和进给速度是工业加工过程中重要的参数,其选择需要综合考虑材料、刀具、机床和加工要求等方面的因素,并根据实际情况进行调整和优化。
钻孔加工之切削速度、转速、进给量的计算

钻孔加工之切削速度、转速、进给量的计算公式切削速度(vc)(m/min)主轴转速(n)(rpm)每转进给量(fn)(mm/r)穿透率(vf)(mm/min)加工时间(Tc)(min)净功率要求(Pc)(kW)扭矩(Mc)(Nm)特定切削力force (kc)(Nm/mm2)进给力(Ff)(N)用于整体式钻头:(CoroDrill Delta-C,型号840) fz = fn/2kr = 70°γ0 = 30°用于可转位刀片钻头:(CoroDrill 880)fz = fnkr = 88°γ0 = 15°钻削定义钻削生产率与穿透率vf密切相关。
可转位刀片钻头–一个中心刀片和一个周边刀片中心刀片从切削速度零工作至50%的vc最大值,周边刀片从50%的vc最大值直至vc最大值。
中心刀片形成锥形切屑,而周边刀片形成类似于使用大切削深度在内圆车削中形成的切屑。
整体式和焊接硬质合金钻头从中心到周边的两个切削刃。
背锥整体式或焊接硬质合金钻头在其外径稍加研磨成一定锥度,以提供间隙防止钻头卡滞在孔中。
孔深最大推荐孔深度计算刀具寿命刀具寿命(TL)可以用米表示的距离、孔数或分钟数来测量。
理论示例:Dc 20 mm vc = 200m/min n = 3184 rpmfn = 0.20 mm/r,孔深50 mmTL(m):15 mTL(孔数):15 x 1000/50 = 300个孔TL(min):15 x 1000/vf = 15 x 1000/(fn xn)= 15 x 1000 /(0.20 x 3184)= 23 min钻削中最常用的刀具寿命准则为后刀面磨损量。
刀具寿命取决于:•切削参数•硬质合金材质和刀片槽型•工件材料•直径(小钻头在较短时间内通过较长的距离)•孔深(许多短孔意味着多次进刀/退刀,这降低刀具寿命)•稳定性。
- 1、下载文档前请自行甄别文档内容的完整性,平台不提供额外的编辑、内容补充、找答案等附加服务。
- 2、"仅部分预览"的文档,不可在线预览部分如存在完整性等问题,可反馈申请退款(可完整预览的文档不适用该条件!)。
- 3、如文档侵犯您的权益,请联系客服反馈,我们会尽快为您处理(人工客服工作时间:9:00-18:30)。
π・D
OSG Co F2 2000
3
转速・切削速度的计算(例)
• 刃径=Φ10
切削速度 V=20 m/min 转速 N (min-1) 是? N = 1000・V π・D = 1000×20 3.1415×10 = 636 (min-1)
• 刃径=Φ10
转速 500 min-1 切削速度 V (m/min) 是? V =
☆ 顺铣
1、切削厚度由最大逐渐减小到零。 2、易产生振动。
☆ 逆铣
1、开始切削的厚度为零。 2、可以延长刀具的寿命。
OSG Co F2 2000
14
技巧篇
OSG Co F2 2000
15
立铣刀的特点
•是一端固定的工具。
• 与其他的切削工具相比,L/D偏大。
(让刀量)
• 槽加工与孔加工相似,切削处理
碳素钢・铸铁 S50C・FC250 加工工件 折损率490~735Nm 数据 (mm) 1 2 3 4
合金钢 SCM・SNCM・SNC 折损率735~980Nm
进给速度 转速 进给速度 转速 (min-1) (mm/min) (min-1) (mm/min) 12,500 63 11,200 56 8,300 75 5,600 56 4,500 3,550 95 106
种类 短刃 长刃 加长型
切削速度 100 70 40
进给 100 80 50
D
L
OSG Co F2 2000
18
影响切削的要素
• 功率
主轴动力(~kw) +主轴大小(BT ~)
• 刚性
刀把的把持力 +工件的刚性 +夹具刚性 +机械刚性
OSG Co F2 2000
19
影响刀具寿命的要素
• • • • • • 铣刀的种类和材质 工件的材质、硬度和加工性 使用机械和刀把的刚性 工件的形状 加工精度 切深量
→单位 m/min
• 为什么要使用切削速度的概念? →即使刃径不同,也能以同一标准来衡量 →容易体现切削锋利性和加工效率
OSG Co F2 2000
5
切削条件(进给速度)
• 什么是进给速度? →工作台在单位时间(1分)内移动多少距离 (毫米) →单位 mm/min • 另一个进给 →每刃进给量 (mm/刃) →与切削速度无关,是体现刀具负荷的指标
刀具
机械的性质:硬度、强度、热传导率 合金成分、比率:SUS、Ti合金、耐热钢
OSG Co F2 2000
加工工件
9
转速和进给速度的总结
输入机械(M/C)的:
转速 + 工作台的进给速度 作为概念来使用的: 切削速度 + 每刃进给速度
OSG Co F2 2000
10
铣刀的条件表
V涂层XPM短刃型
槽加工 V-XPM-EDS・V-XPM-EMS
(前进距离)
S T = =
160 = 0.05 mm/刃
Z・N
4×800
(刃的切削次数)
OSG Co F2 2000
8
铣刀的切削条件
切 削 条 件 的 切削条件 3 要 素
机械 刀把
刚性・老朽化 转速 进给速度
软件
刚性・把持力 振动精度 平衡 使用灵活性 刚 性 切削阻力 抗崩性 耐磨损性 切屑处理性
• 切削油 的种类和有无
OSG Co F2 2000
20
END
OSG Co F2 2000
21
OSG Co F2 2000
1
所谓的切削条件是?
• • • • 转速(切削速度) 进给速度 切深量 切削方向
OSG Co F2 2000
2
切削条件(转速)
• 切削速度和转速
π・D・N V = N = 1000・V
1000
N:转速 ( min-1 ) V:切削速度 ( m/min ) D:刃径 ( mm )
OSG Co F2 2000
3,750 2,650
63 63
选自铣刀型录 11
切削条件(切深量)
侧面切削(4刃)
0.5D 1.5D 1D 0.1D
槽切削(2刃)
( D : 刃径 )
OSG Co F2 2000
12
切削条件的检查要点
切削速度 进给速度
切深量
OSG Co F2 2000
13
切削条件(切削方向)
会影响到刀具寿命。
16
OSG Co F2 2000
铣刀的让刀量
δ= 6.74xPxL3 ExD4 D L
首下长增加2倍的话,
让刀量=23=2× 2× 2=
8(倍)
P
刃径增加2倍的话,
让刀量= 1 2× 2× 2× 2
1 = 16
δ
17
OSG Co F2 2000
因刀具首下长不同而异的条件
L/D 2.0~2.5 2.6~5.5 5.6~8.0
OSG Co F2 2000
6
切削条件(进给速度)
• 工作台进给的速度和每刃进给速度 S S = T・N・ Z T =
Z・N
S:工作台进给的速度 (mm/min) T:每刃进给速度 (mm/刃) Z:刃数 N:转速 ( min-1给速度的计算(例)
• 计算方法(变换) 进给速度 ⇒ 每刃进给速度 例:进给速度 = 160 mm/min 转速 = 800 min-1 刃数= 4
π・D・N
1000
=
3.1415×10×500
1000
OSG Co F2 2000
=15.7 (m/min)
4
切削速度的含义
外周刃端的速度
V =
π・D・N
1000
=
圆周率×(转数/分)
换算成m
=1分钟内前进的距离 ( m/min )
• 什么是切削速度?
→工具的外周刃在回转时单位时间内(1分钟内) 能前进多少距离(米)