等离子体喷涂ZrC涂层耐磨性能研究
ZrO_2热障涂层耐高温冲刷性能研究

响报道较少。电解液的组成和浓度是影响微弧氧化 膜结构和性能最主要的因素之一[ 2] , 不同试验条件 下微弧氧化陶瓷层的性能差别较大。根据各种专利 和文献的相关报道[ 3] , 碱性硅酸盐溶液是目前试验 中应用最广泛的电解液, 研究这种常用电解液体系 中镁合金的微弧氧化行为具有更普遍的意义。因此 本文在试验基础上探讨了镁合金在硅酸盐体系下最 优配方的选取, 并对在该配方条件下得到的微弧氧 化陶瓷膜的相结构、微观形貌特征进行了评定。希 望此结论能为镁合金微弧氧化技术在试验阶段和工 业化生产中提供试验经验和参考依据, 使镁合金微 弧氧化技 术为 我 国镁 合 金表 面 处理 工 业 发展 做 贡献。
图 3 不同冲刷时间内涂层冲刷的宏观形貌
图 4 为 ZrO 2 涂层未冲刷、冲刷 10 s、冲刷 15 s 及冲刷 20 s 时的微观形貌 SEM 照片。由图 4 可 见, 涂层经高温高速粒 子冲刷后, 涂层基体结 合良 好, 未出现大面积的剥落、崩裂现象, 涂层微观尺度 上仍保持较好的完整性。由图 4a 可见, ZrO 2 颗粒 熔化充分, 颗粒撞击基体后铺展顺利, 形成的扁平状 颗粒间搭接较为紧密, 但仍存在少 量微孔及裂纹。 这主要是由于等离子喷涂温度较高, ZrO 2 粉末在火 焰中充分受热熔化并已获得较高的动能, 从而改善 颗粒撞击基体后的变形形貌以及颗粒相互之间的结 合质量。涂层经受 10 s 高温高速粒子冲刷后, 形貌 如图 4b 所示, 由图可以看出, 涂层表面较未冲刷时 光滑, 呈现出较为明显的冲刷方向性, 涂层内裂纹有 所扩展, 涂层表面微凸颗粒被磨平, 同时出现少量粒 子剥落形成的凹坑( 箭头指示处) 。这主要是因为高 速粒子以 30 角冲刷涂层表面时, 其速度可 分解为 垂直于涂层表面的垂直分速度与平行于涂层表面的
等离子喷涂氧化锆涂层的性能研究进展
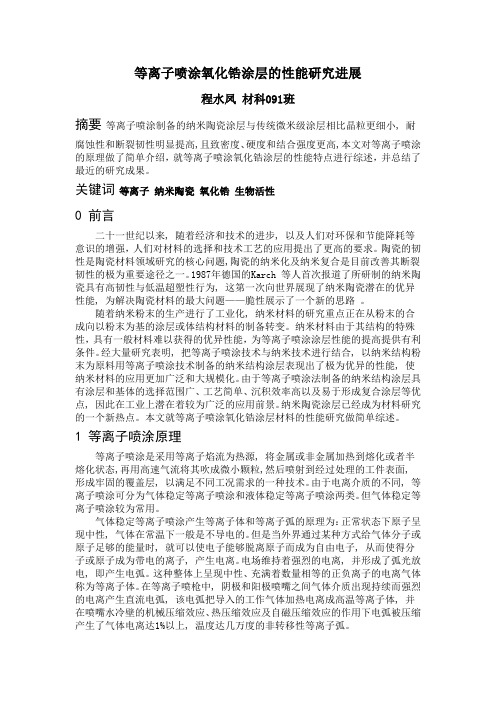
等离子喷涂氧化锆涂层的性能研究进展程水凤材科091班摘要等离子喷涂制备的纳米陶瓷涂层与传统微米级涂层相比晶粒更细小, 耐腐蚀性和断裂韧性明显提高,且致密度、硬度和结合强度更高,本文对等离子喷涂的原理做了简单介绍,就等离子喷涂氧化锆涂层的性能特点进行综述,并总结了最近的研究成果。
关键词等离子纳米陶瓷氧化锆生物活性0 前言二十一世纪以来, 随着经济和技术的进步, 以及人们对环保和节能降耗等意识的增强,人们对材料的选择和技术工艺的应用提出了更高的要求。
陶瓷的韧性是陶瓷材料领域研究的核心问题,陶瓷的纳米化及纳米复合是目前改善其断裂韧性的极为重要途径之一。
1987年德国的Karch 等人首次报道了所研制的纳米陶瓷具有高韧性与低温超塑性行为, 这第一次向世界展现了纳米陶瓷潜在的优异性能, 为解决陶瓷材料的最大问题——脆性展示了一个新的思路。
随着纳米粉末的生产进行了工业化, 纳米材料的研究重点正在从粉末的合成向以粉末为基的涂层或体结构材料的制备转变。
纳米材料由于其结构的特殊性,具有一般材料难以获得的优异性能,为等离子喷涂涂层性能的提高提供有利条件。
经大量研究表明, 把等离子喷涂技术与纳米技术进行结合, 以纳米结构粉末为原料用等离子喷涂技术制备的纳米结构涂层表现出了极为优异的性能, 使纳米材料的应用更加广泛和大规模化。
由于等离子喷涂法制备的纳米结构涂层具有涂层和基体的选择范围广、工艺简单、沉积效率高以及易于形成复合涂层等优点, 因此在工业上潜在着较为广泛的应用前景。
纳米陶瓷涂层已经成为材料研究的一个新热点。
本文就等离子喷涂氧化锆涂层材料的性能研究做简单综述。
1 等离子喷涂原理等离子喷涂是采用等离子焰流为热源, 将金属或非金属加热到熔化或者半熔化状态,再用高速气流将其吹成微小颗粒,然后喷射到经过处理的工件表面, 形成牢固的覆盖层, 以满足不同工况需求的一种技术。
由于电离介质的不同, 等离子喷涂可分为气体稳定等离子喷涂和液体稳定等离子喷涂两类。
结晶器铜板等离子喷涂镍-石墨涂层的耐磨性

结晶器铜板等离子喷涂镍-石墨涂层的耐磨性张亚楠;杨军;常卓;王帅;白宇;唐长斌;邹德宁【摘要】为提高连铸结晶器铜板的使用寿命和铸坯质量,采用超音速等离子喷涂技术在结晶器铜板材料Cr-Zr-Cu基体上制备镍-石墨自润滑涂层,利用扫描电镜(SEM)对喷涂粉末和涂层的组织形貌进行表征,通过球-盘式摩擦磨损实验研究载荷和温度对镍-石墨自润滑涂层、摩擦系数、磨损量的影响,并对涂层的磨损机制进行分析.结果表明:利用超音速等离子喷涂制备的镍-石墨涂层与基体结合良好,结构致密;涂层的摩擦系数和磨损量均随着载荷的增加而增加,不同载荷下涂层的磨损机制均是磨粒磨损,且随着载荷增加,磨粒磨损加剧;涂层的摩擦系数随着温度的增加而增加,且磨损机制均为氧化磨损,但是温度为225℃时,以石墨的润滑作用为主,温度为425℃时,石墨相被氧化镍覆盖,石墨的润滑作用降低,以氧化镍的润滑作用为主.镍-石墨涂层能显著降低Cr-Zr-Cu基体的摩擦系数和磨损量,提高结晶器的耐磨性能.【期刊名称】《材料科学与工艺》【年(卷),期】2019(027)003【总页数】8页(P71-78)【关键词】超音速等离子喷涂;镍-石墨涂层;摩擦系数;磨损量;结晶器铜板【作者】张亚楠;杨军;常卓;王帅;白宇;唐长斌;邹德宁【作者单位】西安建筑科技大学冶金工程学院,西安710055;陕西省冶金工程技术研究中心,西安710055;西安建筑科技大学冶金工程学院,西安710055;陕西省冶金工程技术研究中心,西安710055;西安建筑科技大学冶金工程学院,西安710055;陕西省冶金工程技术研究中心,西安710055;西安建筑科技大学冶金工程学院,西安710055;陕西省冶金工程技术研究中心,西安710055;金属材料强度国家重点实验室(西安交通大学),西安710049;西安建筑科技大学冶金工程学院,西安710055;陕西省冶金工程技术研究中心,西安710055;西安建筑科技大学冶金工程学院,西安710055;陕西省冶金工程技术研究中心,西安710055【正文语种】中文【中图分类】TH117.1铜合金的高导热性使其成为连续铸造结晶器的首选材料[1].但是,铜及其合金在连续铸钢恶劣的工作环境中耐磨性较低,导致其在使用过程中过早失效,对铸坯质量产生不利影响[2].分析表明,结晶器工作状态内壁底角附近磨损最大,宽面比窄面磨损更严重,其顶部磨损可忽略不计[3].因此,使用不同的表面处理技术包括电镀、热喷涂及渗透技术对结晶器铜板表面进行改性,可提高结晶器的性能,延长结晶器使用寿命.热喷涂技术是有效提高基体表面性能的涂层制备工艺[4-5].在众多的喷涂技术中,大气等离子喷涂由于成本低廉而被广泛应用于各种涂层的制备[6],尤其在环保方面,等离子技术制备的耐磨涂层正在逐渐取代电镀技术制备的镀层[7-9].超音速等离子喷涂技术(SAPS)制备的涂层与APS技术相比具有更精细的微观结构和更高的结合强度[10-13].镍基合金和钴基合金由于高强度、高硬度以及优良的耐腐蚀性和耐磨损性能已被作为涂层材料应用于现代工业中[14].石墨具有优良的耐磨性和低摩擦系数,作为喷涂粉末的补强材料用来增强涂层的摩擦学性能[15].镍-石墨复合材料由于具有良好的润滑性能,被广泛应用于制备耐磨密封材料[16].涂层的摩擦磨损行为受到测试载荷、磨粒尺寸、试验环境、硬质相的形状和分布以及体积分数、基体本身的硬度等很多因素的影响[17].Guilemany 等[18]研究了镍-石墨、铝硅-聚苯酯和铝硅-石墨3种涂层在低温下的摩擦磨损性能,结果表明,镍-石墨表现出更好的摩擦学性能;Gao等[19]从比能量和法向硬度两方面评价了镍-石墨的耐磨性,得出实际最大沟槽深度与预设侵入深度之比随着划痕尺寸的增加而增加,沟槽形成机制也不同;Ma等[20]使用低速标准划痕仪测试了镍-石墨、铝硅-聚苯酯和铝硅-石墨3种涂层的性能,证实了涂层在磨损过程中存在塑性变形以及致密化;Xue等[21]利用高速摩擦测试实验研究了镍-石墨涂层线速度与磨损之间的关系,得出涂层磨损随着线速度的增加而增加.但是,对于施加载荷以及温度对镍-石墨涂层摩擦磨损性能的影响研究较少,因为结晶器服役时不仅受到钢水的静压力的作用,还存在很大的温度梯度和热应力,其弯月面处温度可达300~350℃[22],且增大拉坯速度或者铜板厚度,温度会上升到400 ℃左右[23].本文利用HEPJet-高效能超音速大气等离子喷涂技术在结晶器Cr-Zr-Cu基体表面制备镍-石墨涂层,研究载荷及温度对镍-石墨涂层摩擦系数和磨损量的影响,揭示镍-石墨涂层在不同载荷及不同温度下的磨损机制.1 试验1.1 试验材料选用Cr-Zr-Cu作为基体材料,化学成分(质量分数/%)为:Cr,0.5 ~1.0;Zr,0.05 ~0.25;Si,0.02;Mg,0.02;Cu,余量.试样加工为两种尺寸:10 mm×10mm×10 mm的试样用于涂层组织形貌表征;Φ25 mm×10 mm的试样用于涂层的摩擦磨损性能及结合强度测试.粉末材料选用Sulzer Metco公司的Ni 25Graphite 喷涂粉末(牌号Metco 307NS),石墨质量分数25%,余量是镍;粘结层粉末选用北京颐鑫安科技发展有限公司的铝包镍热喷涂粉末(牌号YF-05),其中铝质量分数为30%,余量为镍.1.2 涂层制备首先,用砂纸对基体进行打磨,除去基体表面的氧化膜;然后,将基体置于酒精中超声清洗15 min,除去基体表面的油污;最后,采用20目金刚砂对基体进行喷砂处理.采用西安交通大学金属材料强度国家重点实验室HEPJet-高效能超音速大气等离子喷涂设备(SAPS)制备涂层,喷涂工艺参数列于表1.表1 喷涂工艺参数Table 1 Parameters of the spraying process喷涂材料电流/A 电压/V 氩气流量/(L·min-1) 氢气流量/(L·min-1) 氮气流量/(L·min-1) 喷涂距离/mm镍-石墨293 91 91.4 1.9 0.9 110铝-镍368 110 149.8 3.3 1.9 1101.3 粉末及涂层表征采用型号LS800的激光粒度分布仪测试两种喷涂粉末的粒度分布;采用型号8801的电液伺服疲劳试验机(50 kW)在室温条件下测试涂层的结合强度,拉伸速率是0.03 mm/min;利用环境扫描电镜(FEI Q45,美国)对喷涂粉末和涂层的组织形貌进行表征;采用 Image J软件测量涂层孔隙率.1.4 摩擦磨损试验球-盘式摩擦磨损实验在型号为HT-1000的高温摩擦磨损实验机上进行,测试前用砂纸对涂层进行打磨并抛光,再用酒精超声清洗15 min,测试前后分别用分析天平对试样进行称重.摩擦副选用直径6 mm的Al2O3球,摩擦半径3 mm,转速为224 r/min,测试载荷分别为5、10、15 N,测试温度为室温;高温实验载荷固定为10 N,温度为225和425℃,试验时间为30 min.2 结果与讨论2.1 喷涂粉末的形貌与粒度表征图1为工作层镍-石墨粉末与粘结层铝-镍粉末的扫描照片.比较图1(a)与(b)可以看出:两种粉末均为不规则形貌,这是由于两种粉末都是通过化学包覆工艺制备的;镍-石墨粉末表面附着有非常小的镍颗粒,数量多且很密集;铝-镍粉末表面较为光滑.镍-石墨粉末中有少量条棒状粉末,条棒状粉末的存在会导致粉末的流动性变差,但只要粒度合适,并不会对涂层组织的均匀性造成影响.图1 喷涂粉末的SEM照片Fig.1 SEM images of sprayed powder:(a)Nickel-Graphite;(b)aluminium-nickel图2 喷涂粉末的粒度分布Fig.2 Particle size distribution of spray powders:(a)nickel-graphite;(b)aluminium-nickel图3 镍-石墨涂层的截面SEM照片Fig.3 Cross-sectional SEM images of nickel-graphite coating:(a)smaller magnification;(b)larger amgnification采用激光粒度分布仪测试两种喷涂粉末的粒度分布,结果如图2所示.由图2可以看出:镍-石墨粉末的粒度为30~300μm,主要集中在130μm左右;铝-镍粉末的粒度为30~160μm,主要集中在80μm左右,两种粉末的粒度均符合喷涂设备的要求.2.2 涂层的组织结构图3是镍-石墨涂层的截面SEM照片.从图3(a)可以看出:镍-石墨涂层、粘结层及基体之间结合良好,没有出现明显的裂纹,涂层结合强度是(15.86±0.32)MPa;涂层最顶层有部分未完全熔融的粉末颗粒,这是因为在喷涂过程中,并不是所有的粉末在喷涂过程中都能通过高温等离子体区域,因此部分粉末未能达到熔化温度而处于未熔融或者半熔融状态[24];涂层总体厚度约600μm,其中粘结层厚度约100μm,镍-石墨涂层厚度约500μm.从图3(b)可以看出,涂层由浅色的金属镍基体相与深色的石墨相组成,涂层中的石墨相之间距离越近,越容易在摩擦期间形成石墨润滑膜,可以在摩擦表面和摩擦副之间起到有效的润滑作用[25].涂层呈典型的层状分布,符合超音速等离子喷涂制备的涂层特点.另外,用Image J软件测量后得出该涂层孔隙率大约为2%.2.3 基体的摩擦磨损性能图4是Cr-Zr-Cu基体在10 N载荷下的磨痕形貌.由图 4(a)可以看出,磨痕宽度约1 600μm,基体的磨损表面出现大片剥落坑,见图4(b),且磨损表面布满了深深的犁沟,见图4(c),可见,Cr-Zr-Cu基体的磨损机制是严重的磨粒磨损,并伴有疲劳磨损.由图5可以看出,Cr-Zr-Cu基体在载荷为10 N时摩擦系数波动较大,因为在摩擦过程中,磨粒磨损较严重,且磨损表面出现大片剥落,摩擦系数在试验结束时稳定在0.5左右,经过称量,Cr-Zr-Cu基体在磨损后质量损失27.2 mg.图4 Cr-Zr-Cu基体的磨损形貌Fig.4 Wear morphology of Cr- Zr- Cu substrate:(a)smaller magnification;(b)larger magnification;(c)BSE imageof(b)图5 Cr-Zr-Cu基体的摩擦系数曲线Fig.5 Friction coefficient curve of Cr-Zr- Cu substrate2.4 涂层的摩擦磨损性能图6 是镍-石墨涂层在不同载荷下的磨痕形貌.对比图6(a)、(b)和(c)可知,涂层磨痕宽度随着载荷的增加而增加,且暴露出来的石墨相也随着载荷的增加相应地增加.载荷5 N时,从图6(d)可看出磨槽表面有轻微的犁沟,这主要是由于涂层与对磨副相互摩擦产生的磨屑颗粒在磨槽里面反复摩擦所致,表明此条件下涂层的磨损机制以轻微的磨粒磨损为主;载荷增加到10 N时,磨槽表面出现较为明显的犁沟,并且出现鳞片状的氧化镍,如图6(e)所示,这是因为在滑动摩擦过程中磨损表面氧含量更高,所以很容易被氧化生成氧化镍[16],同时在高载荷作用下产生明显微裂纹[26],且随着摩擦试验的不断进行,裂纹会不断扩大,氧化镍终会出现剥落,暴露出下边的石墨相,此时涂层的磨损机制仍然以磨粒磨损为主,并伴有轻微氧化磨损;当载荷增加到15 N时(结晶器实际工作时单位面积承载能力达不到该试验条件),磨槽形貌如图(f)所示,此条件下磨槽表面鳞片状氧镍增多(图6(c)与6(b)相比),且犁沟加深数量增多,氧化镍掉落后暴露出下层的石墨,并形成一个石墨坑,石墨坑中可观察到有少量磨屑,同时由于磨损表面受到法向载荷和反复切向摩擦力的作用,磨槽表面出现局部分层剥落现象[15],此条件下涂层的磨损机制是较为严重的磨粒磨损和氧化磨损,并逐渐向疲劳磨损过渡.镍-石墨涂层在不同载荷下的摩擦系数和磨损量如图7和8所示,可以看出,涂层的摩擦系数和磨损量均随着载荷的增加而增加.3种载荷下,涂层与摩擦副很快便结束跑和阶段,之后又非常快地进入稳定摩擦阶段,这表明镍-石墨涂层有显著的减摩作用.当载荷分别为5和10 N时,涂层的摩擦系数是0.15和0.18,并且摩擦系数相对稳定,基本保持不变.图6 不同载荷下镍-石墨涂层的磨损形貌Fig.6 Wear morpholgy of Nickel-Graphite-Graphite coating under different load:(a)smaller magnification(5 N);(b)smaller magnification(10 N);(c)smaller magnification(15 N);(d)smaller magnification(5 N);(e)smaller magnification(10 N);(f)smaller magnification(15 N);(g)and(h)EDSresultes of the points 1and 2图7 不同载荷下涂层的摩擦系数曲线Fig.7 Friction coefficient curve of coating under different load图8 不同载荷下涂层的磨损质量Fig.8 Wear mass of coating under different load磨损量分别为0.04和0.1 mg;当载荷增加到15 N时,涂层的摩擦系数从实验开始时的0.21一直增加到0.37,且有继续增加的趋势.这是因为载荷增加到15 N时,磨擦表面暴露出更多的石墨坑,使摩擦表面粗糙度增大;并且由于压应力和切应力的增加,磨损表面出现局部分层剥落现象,磨损机制逐渐开始向疲劳磨损过渡,相应条件下的磨损量为0.2 mg,是载荷10 N时磨损量的2倍.镍-石墨涂层在不同温度下的磨损形貌如图9所示,可以看出:随着温度从225℃增加到425℃,磨痕宽度也相应增大;与225℃时的磨痕形貌相比,425℃时的磨痕形貌发生了较大的变化.从图9(a)和(d)可以看出,225℃时磨痕表面暴露出比较多的石墨相,而425℃时磨痕表面石墨相却非常少.从高倍图9(b)和(e)及背散图9(c)和(f)可以看出,225℃时的磨痕表面有大量不连续的氧化镍,说明此条件涂层的磨损机制是以氧化磨损为主,但氧化不是很严重,与常温下相比,暴露出来的石墨相不多,但仍可起到主要润滑作用.而425℃时磨痕表面出现大量连续的氧化镍,表明此时涂层的磨损机制是严重的氧化磨损,磨损表面石墨润滑相非常少,这是因为大量氧化镍被对磨球碾平,填满了石墨坑,覆盖住了石墨润滑相,这会导致石墨的润滑作用降低,变成以氧化镍的润滑作用为主.图9 不同温度下镍-石墨涂层的磨损形貌Fig.9 Wear morphology of nickel-grqphite coating under different temperature:(a)smallermagnification(225 ℃);(b)smaller magnification the point 1(225℃);(c)BSE image of(b);(d)smaller magnification(425℃);(e)smallermagnification(425℃);(f)BSE image of(e);(g)E DSresult of the points 1镍-石墨涂层在225和425℃的摩擦系数如图10所示.225℃时,涂层的摩擦系数随着时间的增加从0.27缓慢增加到0.33,这是因为磨损表面逐渐氧化,氧化镍覆盖了部分石墨,使石墨的润滑性能降低,但涂层仍然具有较低的摩擦系数,说明石墨在225℃时还能起到很好的减摩所用.当试验温度升到425℃时,涂层摩擦系数升高明显,摩擦系数在前10 min与225℃时相比增加了0.05左右,且在10~20 min增长较快,之后基本趋于平稳.这是因为在425℃试验条件下,磨损表面出现大量氧化镍,氧化镍被对磨球碾碎,填补到石墨坑中,覆盖了石墨相,此时,氧化镍在摩擦过程中逐渐起到主要的润滑作用,而石墨的润滑作用逐渐降低.在10~20 min内,氧化镍不断填充磨损表面的石墨坑,磨损表面暴露的石墨相不断减少,摩擦系数增长加快.20 min后,摩擦系数趋于平稳,表明此时,石墨坑已基本被填满,磨损表面覆盖了一层氧化镍如图9(e)和(f)所示,所以摩擦系数趋于稳定,不再增加,此条件下氧化镍已起到主要润滑作用.图11是涂层在225和425℃的磨损质量,可以看出:温度225℃时涂层的磨损质量是0.18 mg;与常温下载荷为10N时的磨损质量相比,仅增加了0.08 mg,而温度为425℃时,涂层的磨损质量是0.19 mg,比225℃时仅增加了0.01 mg.这一方面是因为部分磨屑在摩擦过程中掉落在石墨坑中,没有掉落;另一方面是因为涂层在高温摩擦过程中氧化增重,导致高温下涂层的磨损质量增加不明显.图10 不同温度下涂层的摩擦系数曲线Fig.10 Friction coefficient curve of coating under different temperature图11 不同温度下涂层的磨损质量Fig.11 Wear mass of coating under different temperature3 结论1)利用超音速等离子喷涂技术在结晶器铜板材料Cr-Zr-Cu基体上制备的镍-石墨涂层与基体结合良好,组织均匀,结构致密,孔隙率低,无氧化物夹杂生成.2)涂层在不同载荷下磨损机制均为磨粒磨损为主.载荷为5 N时,磨损机制为轻微的磨粒磨损;当载荷增加到10 N时,磨损机制以磨粒磨损为主,伴有轻微的氧化磨损;当载荷增加到15 N时,磨损机制是严重的磨粒磨损,伴有氧化磨损,并且涂层开始向疲劳磨损过渡.3)涂层的摩擦系数和磨损量均随着载荷的增加而增加,载荷为5和10 N时,摩擦系数分别为0.15和0.18,载荷为15 N时,摩擦系数从试验开始一直增加到0.37,与Cr-Zr-Cu基体相比,镍-石墨涂层具有更低的摩擦系数和磨损质量,可以显著提高结晶器铜板的耐磨性能.4)涂层在高温条件下的磨损机制均以氧化磨损为主.温度为225℃时,摩擦系数从0.27增加到0.33,石墨起主要润滑作用;当温度为425℃时,氧化镍起主要的润滑作用;高温磨擦磨损实验结束后,涂层磨损质量增加不多,这是由于在磨损过程中涂层出现严重氧化,导致涂层氧化增重且在磨擦过程中,磨屑填充到石墨坑中并未掉落引起的.参考文献:【相关文献】[1] YAN Hua,ZHANG Jie,ZHANG Peilei,et ser cladding of Co-basedalloy/TiC/CaF2 self-lubricating composite coatings on copper for continuous casting mold [J].Surface and Coatings Technology,2013,232:362-369.[2] BARELLA S,GRUTTADAURIA A,MAPELLI C,et al.Investigation of failure and damages on a continuous casting copper mould[J].Engineering Failure Analysis,2014,36:432 -438.[3] PANDEY J C,RAJ M,MISHRA R,et al.Failure of nickel coating on a copper moldof a slab caster[J].Journal of Failure Analysis and Prevention,2008,8:3-11.[4] MIGUEL J M,VIZCAINO S,LORENZANA C,et al.Tribological behavior of bronze composite coatings obtained by plasma thermal spraying[J].Tribology Letters,2011,42:263-273.[5] DAVID C, ANTHONY B, SANDRA C, et al.Improving tribological properties of cast Al-Si alloys through application of wear-resistant thermal spray coatings[J].Journal of Thermal Spray Technology,2013,22:491-501.[6] MIGUEL J M,GUILEMANY J M,DOSTA S.Effect of the spraying process on the microstructure and tribological properties of bronze-alumina composite coatings[J].Surface and Coatings Technology,2010,205:2184-2190.[7] BALAMURUGAN G M, DURAISELVAM M,ANANDAKRISHNAN parison of high temperature wear behaviour of plasma sprayed WC-Co coated and hard chromium plated AISI 304 austenitic stainless steel[J].Materials & Design,2012,35:640-646. [8] SERRESN, HLAWKA F, COSTIL S, et al.Microstructures of metallic NiCrBSi coatings manufactured via hybrid plasma spray and in situ laser remelting process[J].Journal of Thermal Spray Technology,2011,20:336 -343.[9] SOHI M H,GHADAMI parative tribological study of air plasma sprayed WC-12%Co coating versus conventional hard chromium electrodeposit[J].TribologyInternational,2010,43:882 -886.[10] BAI Y,HAN Z H,LI H Q,et al.Structure-property differences between supersonic and conventional atmospheric plasma sprayed zirconia thermal barrier coatings[J].Surface and Coatings Technology,2011,205:3833-3839.[11] BAI Y,HAN Z H,LI H Q,et al.High performance nanostructured ZrO2 based thermal barrier coatings deposited by high efficiency supersonic plasma spraying [J].Applied Surface Science,2011,257:7210-7216.[12] BAI Y,TANG J J,QU Y M,et al.Influence of original powders on the microstructure and properties of thermal barrier coatings deposited by supersonic atmospheric plasma spraying,Part I:microstructure[J].Ceramics International,2013,39:5113 -5124.[13] BAI Y,ZHAO J J,TANG J J,et al.Influence of original powders on the microstructure and properties of thermal barrier coatings deposited by supersonic atmospheric plasma spraying,part II:properties[J].Ceramics International,2013,39:4437 -4448.[14] NATARAJAN S,ANAND E E,AKHILESH K S,et al.Effect of graphite addition on the microstructure,hardness and abrasive wear behavior of plasma sprayed NiCrBSi coatings[J]. Materials Chemistry and Physics,2016,175:100-106.[15] YANG Jie,ZHANG Yunjing,ZHAO Xiaoqin,et al.Tribological behaviors of plasma sprayed CuAl/Nigraphite composite coating [J]. Tribology International,2015,90:96 -103.[16] HUANG Chunjie,LI Wenya,XIE Yingchun,et al.Effect of substrate type on deposition behavior and wear performance of Ni-coated graphite/Al composite coatings deposited by cold spraying[J].Journal of Materials Science& Technology,2017,33:338-346.[17] HEJWOWSKI T,SZEWCZYK S,WERON'SKI A.An investigation of the abrasive and erosive wear of flamesprayed coatings[J].Journal of Materials Processing Technology,2000,106:54-57.[18] GUILEMANY J M,NAVARRO J,LORENZANA C,et al.Tribological behaviour of abradable coatings obtained by atmospheric plasma spraying(APS)[C]//International Thermal Spray Conference.Geauga:ASM International,2001:1115 -1118.[19] GAO Siyang,LIU Suwei,LI Shu,et al.Evaluation of wear resistance of abradable coatings by a single-pass pendulum scratch method[J].Tribology,2010,30:385-391. [20] MA Xiao,MATTHEWS A.Evaluation of abradable seal coating mechanical properties[J].Wear,2009,267:1501-1510.[21] XUE Weihai,GAO Siyang,DUAN Deli,et al.Study on the high-speed rubbing wearbehavior between Ti6Al4V blade and nickel-graphite abradable seal coating[J].Tribology,2013,139:21604 -21610.[22]樊自拴,潘继岗,孙冬柏,等.结晶器失效分析和表面处理技术的研究进展[J].铸造技术,2004,25(12):952-954.FAN Zishuan,PAN Jigang,SUN Dongbai,et al.Research progress on disabled analyzing and dispose of surface technology on crystallizer[J]. Foundry Technology,2004,25(12):952-954.[23]朱立光,李琨,李曜光,等.板坯连铸结晶器铜板传热行为[J].铸造技术,2016,37(4):706 -709.ZHU Liguang,LI Kun,LI Yaoguang,et al.Heat transfer behavior of crystallizer copper plate for slab continuous casting[J].Foundry Technology,2016,37(4):706-709.[24] REZA S,MAHMOUD H S,MOHAMMAD A,et al.Effect of APS process parameters on high-temperature wear behavior of nickel-graphite abradable seal coatings[J].Surface and Coatings Technology,2017,321:403-408.[25] TANGJ J,LIU K,YANG Q Z,et al.The influence of size and distribution of graphite on the friction and wear behavior of Ni-graphite coatings[J].Surface and Coatings Technology,2014,252:48-55.[26] ZHAO Xiaoqin,LI Shuangjian,HOU Guoliang,et al.Influence of doping graphite on microstructure and tribological properties of plasma sprayed 3Al2O3-2SiO2 coating [J].Tribology International,2016,101:168-177.。
等离子喷涂耐磨陶瓷涂层的组织研究

层 本 身 组 织 不 均匀 以及 不 同相 结 构 的存 在 ,在 测 试 中 出 现 高 硬 度 和 低 硬度 值 ,调 整 视 场 打 至 少 1 压 痕 点 , 0个 然
后 取 显 微 硬 度 的 平 均 值 。如 下 表 所 示 的涂 层 的 显 微 硬 度 。
为主 , 时产 生 部分 微 冶 金结 合 。微 冶 金结 合 的产 生 是 因 同
为 喷涂 过 渡 层 时 , 末 中 的 N 和 A 发 生 放 热 反 应 , 种 粉 i l 这
放 热 反 应 可 在 粉末 微 粒 到 达基 体 表 面之 后 仍 然 持 续很 短
时间 , 而使 涂 层 与基 体 之 间产 生很 强 的 微 冶金 结合 。 从
磨性 。
关键 词 : 离子喷 涂 等
A - i 1 T O 性 能 O
前 言
涂 层 与 基 材 的 界 面 呈 锯齿 状 ,结 合 形 式 属 于 以 机 械结 合
高 性 能 的 陶瓷 涂 层 是 一 种 具 有 较 大 发 展 前 景 的 新 型 材 料 , 既具 有 陶瓷 材 料 耐 高 温 、 腐 蚀 、 磨 损 和 重 量 它 耐 耐 轻 等优 良性 能 , 能保 持原 有底 材 的结 构 强度 。 目前 已被 又
单次 测 量 的显 微 硬 度值 ( V 0 H 10)
8 0. 5 9 2 9 . 6 1 7 5 l 5. 01 1 1 5. O oo 5 18 5 3 0.
平均 值 折 合 值
( 。 ( C) HV ) HR
9 4. 4 9 15 6 9
1 1 O 7 4. 1 1 2 0 1 1 O 6 9. 7 o6 . 6 4 7 0 2. 4 O6 . 6 9 6
等离子喷涂铁―镍―钴―碳化钨涂层制动摩擦特性的研究

等离子喷涂铁―镍―钴―碳化钨涂层制动摩擦特性的研究摘要:本文研究了等离子喷涂铁―镍―钴―碳化钨涂层在制动系统中的摩擦特性。
通过制备不同厚度的涂层,并利用摩擦试验机对其摩擦性能进行了研究,包括摩擦系数、磨损率等指标。
结果表明,涂层厚度对摩擦性能具有明显影响,随着涂层厚度的增加,摩擦系数和磨损率均呈现出先增加后减小的趋势。
同时,本研究还分析了涂层的微观结构和化学成分,探讨了涂层的摩擦机理。
关键词:等离子喷涂;铁―镍―钴―碳化钨涂层;制动摩擦特性;摩擦系数;磨损率Study on the Friction Characteristics of Plasma-sprayed Iron-nickel-cobalt-tungsten Carbide Coating in Brake SystemAbstract:This paper studies the friction characteristics of plasma-sprayed iron-nickel-cobalt-tungsten carbide coating in the brake system. Different thicknesses of coatings were prepared, and their friction properties were studied by using a friction tester, including the coefficient of friction, wear rate and other indicators. The results show that the thickness of the coating has a significant impact on the friction performance. With the increase of the coating thickness, the coefficient of friction and wear rate show a trend of increasefirst and then decrease. At the same time, this study also analyzes the microscopic structure and chemical composition of the coating, and discusses the friction mechanism of the coating.Keywords: plasma spraying, iron-nickel-cobalt-tungsten carbide coating, brake friction characteristics, coefficient of friction, wear rate.进一步分析表明,涂层厚度对涂层摩擦性能影响的原因主要与涂层的内部应力有关。
激光重熔等离子喷涂NiCr-Cr_3C_2涂层微观结构和性能研究

占总面积的百分 比, 从而确定在给定范围内黑色区域 元素。 打底层氧化物分为两层 , 与基体结合部位以
使用显微硬度计( x 一 00 C)) 0 H P 10T (1 0g荷载 ,  ̄1 1
图 1 )( 、 ) 同扫描速度下激光重熔涂层 ( 、 )( 为不 b c d
保持时间为 1s进行显微硬度测量。本实验采用激 横截面的 S M 形貌图 。和等离子喷涂涂层比较可 5) E
这是 由于激光束辐照在试样表面上的时间短, 表层吸 收的激光热量较少 , 冷却速度快 , 试样表面薄层大量 的晶核来不及进一步长大就凝固成为固态, 其显微组
光 重熔 涂 层 的孔 隙 率 可 以看 出 ,当扫 描 速 度 为
1 mrn , . / i 时 激光重熔涂层的孔隙率最低 , 5 a 重熔效果
8 0 移动步距 2 m 光斑直径 =4 m保持不变, 0W, . m, 1 m
表 1等离子喷涂工艺参数
Ta . Prc s aa t r fpa ma s ryn b 1 o e s p rme es o ls pa ig
收稿 日期 :010—5 21—22
通 汛联系人 : 陆益军 ,- a : u U n 6 y h o o . E m i L yu2 @ ao. rc l cn l l
将试 样制成金相 试样 ,使 用 扫描 电子显微镜 瓷与金属基体间存在明显的分 其
(E Ht h S 3 0N) S M, i ci -0 0 和光 学显 微镜 ( G 0 ) a Ⅺ 一 5 进
行显微组织观察 ,采用 T I C 通用图像分析 系统进行 的分析结果得 出浅灰色 区域 富含 N 、eO元素 , j 、 F 而 孔隙率的测定 。 定量分析原理见文献[ , 4 将灰度等级 深灰色区域主要 以 C 的碳化物为主 ,与打底层结合 ] r 根据经验定为覆盖涂层黑色区域 , 并计算黑色区域所
等离子喷涂MCr—Cr3C2涂层高温摩擦磨损性能研究

7 6‘
旁
研究与设计
瑚 瑚 瑚 姗
刘
艳 等 : 离子 喷 涂 NC - r z 层 高 温摩 擦 磨 损 性 能 研究 等 irC 3 涂 C
卯。
第 4期
2 O
3 O
4 O
5 O
6 O
7 O
8 O
9 O
lO O
衍射角 2 /。 0()
图 2 等 离 子 喷涂 涂 层 衍 射 图
表 2 磨 损试 验条 件
Ta . Pa a ee fwe r t s b2 r m t ro a e t
射 图谱 如 图 2所 示 , 图 2可 知 , 由 喷涂 态 的涂 层 主 要 含 有 C 2 6C73C 32 硬 质 相 和 N C rC 、 r 、 r 等 3 C C ir粘 结 相 , 层中 C 涂 r的碳 化 物 主要 以 C2 6C , rC 、 r 的形式 3 C
试 验基材 选择 Q 3 2 5板材 。 采用 G 一 0 P 8 A等离 子 喷涂系 统进 行涂 层制 备 ,
喷涂主要 T艺参 数如 表 1 示 。 所
表 1 等 离子 喷 涂 工 艺参 数
Ta . Pa a e e f l s a s r yn b1 r m t ro a m p a i g p
磨 损机理 还缺乏 深入 的研究 。 而铁路 内燃机 车气缸
缸 套 内壁 的 高温 磨损 、 腐蚀 情况 非 常 严重 , 长期 困 扰其服役性 能和寿命 的进一 步提高 。 为此 , 本研究针
对 内燃机 的气 缸套 内壁 的高 温摩擦 磨损 工况 , 采用 等离子 喷涂 方法制 备 N C— r z 层 , 对其 高温 irC , 涂 C 并 摩擦磨损 性能进 行 了研 究 。
等离子喷涂碳化铬―镍铬涂层的摩擦学特性

等离子喷涂碳化铬―镍铬涂层的摩擦学特性Title:Frictional characteristics of plasma sprayed chromium-carbon-nickel-chromium coatingsAbstract:Plasma sprayed chromium-carbon-nickel-chromium (Cr-C-Ni-Cr) coatings are widely used in various applications due to their excellent wear resistance and high temperature strength. In this study, the frictional characteristics of Cr-C-Ni-Cr coatings were investigated. The Cr-C-Ni-Cr coatings were prepared by plasma spraying on a steel substrate. The microstructure and surface morphology of the coatings were examined by scanning electron microscopy (SEM) and atomic force microscopy (AFM), respectively. The frictional characteristics of the coatings were evaluated using a pin-on-disk tribometer under dry sliding conditions.The results indicated that the Cr-C-Ni-Cr coatings exhibited low friction coefficients in both low and high sliding speeds. The coefficient of friction decreased with the increase of sliding velocity, which is attributed to the decrease of adhesive and ploughing wear at high sliding velocity. The microstructure of the coatings showed a dense and uniform microstructure, and the surface roughness was within the range of 0.2-0.3 μm. AFM results showed that the coatings had a low surface roughness with a mean roughness (Ra) o f 0.23 μm. SEM observations revealed that the coatings were compact and had a fine, equiaxed microstructure.The results suggest that plasma sprayed Cr-C-Ni-Cr coatings possess excellent frictional characteristics, which make them suitable for use in applications requiring high wear resistance under dry sliding conditions.Keywords: plasma sprayed coatings, Cr-C-Ni-Cr, frictional characteristics, wear resistance, high temperature strength, pin-on-disk tribometer, microstructure, surface morphology, surface roughnessIntroduction:Plasma spraying is a widely used coating technique for improving the wear resistance of metallic substrate materials. Chromium-carbon-nickel-chromium (Cr-C-Ni-Cr) coatings have attracted significant attention due to their excellent wear resistance, high temperature strength and corrosion resistance. Cr-C-Ni-Cr coatings exhibit high hardness, low coefficient of thermal expansion and good thermal shock resistance. As a result, they have been used in a wide range of applications, such as aerospace, automotive, and energy industries.The frictional characteristics of coatings are one of the most important factors in determining their wear resistance under different sliding conditions. Thus, it is essential to investigate the influence of sliding speed and load on the tribological properties of materials. In this study, the frictional characteristics of Cr-C-Ni-Cr coatings were investigated under different sliding conditions. Experimental:The Cr-C-Ni-Cr coatings were prepared using plasma sprayingtechnique on a steel substrate with a thickness of 6mm. The coating thickness was approximately 200 μm. The microstructure and surface morphology of the coatings were characterized using scanning electron microscopy (SEM) and atomic force microscopy (AFM), respectively. The mechanical properties of the coatings were also investigated using a Vickers microhardness tester. The tribological properties of the coatings were evaluated using a pin-on-disk tribometer under dry sliding conditions. The sliding distance was 3000 m and the sliding speed ranged from 0.1 to 1.0 m/s. The load was varied from 10 to 50 N.Results and Discussion:SEM images of the Cr-C-Ni-Cr coatings showed a dense and uniform microstructure with a fine, equiaxed morphology (Fig.1(a)). The coatings were crack-free and exhibited a smooth surface with a low roughness (Fig. 1(b)). The mean roughness (Ra) of the coatings was 0.23 μm, which indicated that the coatings had a low surface roughness.AFM images of the coatings also showed a low surface roughness with a mean roughness of 0.25 μm (Fig. 2(a)). The coatings exhibited a smooth and uniform surface morphology. The Vickers microhardness of the coatings was 1300 Hv, which indicated that the coatings had high hardness.The frictional characteristics of the coatings were evaluated using a pin-on-disk tribometer. The friction coefficient decreased with increasing sliding speed (Fig. 3(a)). This phenomenon can be attributed to the increased contribution of ploughing wear at low sliding velocity and the decreased contribution of adhesive wear athigh sliding velocity. Under a fixed load, the friction coefficient of the coatings decreased with increasing sliding velocity from 0.1 to 1.0 m/s (Fig. 3(b)). This was because the contribution of adhesion and ploughing wear decreased with increasing sliding speed. The coatings also exhibited a low friction coefficient under different loads (Fig. 3(c)). The friction coefficient showed a decreasing trend with increasing load, which can be attributed to the increased contact area and the reduced asperity contact stress. Conclusions:In this study, the tribological properties of plasma sprayed Cr-C-Ni-Cr coatings were investigated. The coatings exhibited excellent frictional characteristics with a low coefficient of friction and the coefficient of friction decreased with the increase of sliding velocity. The microstructure of the coatings showed a dense and uniform microstructure with a fine, equiaxed morphology, and the surface roughness was low. The results suggest that plasma sprayed Cr-C-Ni-Cr coatings have great potential for use in applications requiring high wear resistance under dry sliding conditions.The excellent wear resistance and high temperature strength of Cr-C-Ni-Cr coatings make them ideal for use in various applications, such as aerospace, automotive, and energy industries. In the aerospace industry, where components are subjected to extreme conditions, the use of plasma sprayed Cr-C-Ni-Cr coatings can significantly prolong the service life of these components by reducing wear and enhancing their resistance to high temperatures and corrosion.In the automotive industry, Cr-C-Ni-Cr coatings are widely used for engine components such as pistons, cylinder liners, and valvesdue to their excellent wear resistance under high stress and high temperature conditions. The use of these coatings in these components can significantly reduce engine maintenance and repair costs.In the energy industry, the use of Cr-C-Ni-Cr coatings in gas turbines can improve their efficiency and reduce maintenance costs by reducing wear and enhancing their resistance to high temperatures and corrosion. Furthermore, the use of these coatings in steam turbine blades can reduce corrosion and wear and increase their service life.In conclusion, the excellent frictional characteristics of Cr-C-Ni-Cr coatings make them an ideal choice for use in applications requiring high wear resistance under dry sliding conditions. Their wear resistance, high temperature strength, and corrosion resistance make them an ideal choice for use in various industries, such as aerospace, automotive, and energy industries.In addition to the aforementioned industries, Cr-C-Ni-Cr coatings are also used in the manufacturing of industrial machinery, tools and equipment that experience high stress and wear. These coatings can be applied to hydraulic components, cutting tools, industrial valves, and bearings, among others. In the manufacturing industry, Cr-C-Ni-Cr coatings can help to improve production efficiency and reduce maintenance and repair costs.Another major application of Cr-C-Ni-Cr coatings is in the medical industry, particularly in the manufacturing of surgical instruments and implants. These coatings give medical instruments and implants a biocompatible, corrosion-resistant, and wear-resistantsurface, improving their service life and reducing the risk of infection.Furthermore, Cr-C-Ni-Cr coatings are used in the nuclear industry due to their resistance to high levels of radiation and corrosion. These coatings are applied to nuclear reactor components such as fuel rods, control rods, and primary coolant loop components.Overall, the versatility of Cr-C-Ni-Cr coatings makes them a preferred choice for various industries. Their unique combination of properties, such as wear resistance, high temperature strength, and corrosion resistance, make them indispensable in applications that require durable and long-lasting components. As technology continues to evolve, the use of Cr-C-Ni-Cr coatings is likely to become even more widespread in the coming years.Cr-C-Ni-Cr coatings also find application in the aerospace industry, where they are used to coat engine components, turbine blades, and structural parts in aircraft and spacecraft. These coatings provide improved thermal stability, oxidation resistance, and enhanced fatigue strength, making them critical for the safe and reliable operation of aerospace systems.Furthermore, in the oil and gas industry, Cr-C-Ni-Cr coatings are used to coat drilling tools, valves, pumps, and other components that are exposed to harsh corrosive environments. These coatings can withstand high pressures and temperatures, making them ideal for use in offshore drilling platforms and challenging oil and gas production environments.The electronics industry is another sector where Cr-C-Ni-Crcoatings are utilized. In the manufacture of microelectronics and electronic devices, these coatings are applied as thin films to improve the performance, durability, and reliability of the components. Cr-C-Ni-Cr coatings have excellent electrical conductivity and are resistant to both oxidation and corrosion, making them an ideal choice for use as interconnects and contact materials in electronic devices.In summary, Cr-C-Ni-Cr coatings have diverse and widespread industrial applications due to their unique properties. They are used in industries such as aerospace, automotive, medical, nuclear, oil and gas, and electronics, among others, to enhance the longevity and performance of critical components. With ongoing advancements in materials science and technology, there is potential for the development of new and exciting applications for these coatings in the future.Yes, that's correct. Ongoing research and development efforts are focused on improving the properties and performance of Cr-C-Ni-Cr coatings for existing applications, as well as exploring new applications for these coatings in emerging industries. Some of the areas of research include developing coatings with greater wear resistance, improving adhesion to various substrates, and enhancing thermal stability and conductivity. Additionally, new applications in areas such as renewable energy, advanced manufacturing, and biotechnology are being explored, which could further expand the scope of applications for Cr-C-Ni-Cr coatings in the future.。
- 1、下载文档前请自行甄别文档内容的完整性,平台不提供额外的编辑、内容补充、找答案等附加服务。
- 2、"仅部分预览"的文档,不可在线预览部分如存在完整性等问题,可反馈申请退款(可完整预览的文档不适用该条件!)。
- 3、如文档侵犯您的权益,请联系客服反馈,我们会尽快为您处理(人工客服工作时间:9:00-18:30)。
第7卷 第2期 热 喷 涂 技 术V ol.7, No.22015年6月 Thermal Spray Technology Jun., 2015等离子体喷涂ZrC 涂层耐磨性能研究苏运娟1,2,牛亚然1,黄利平1,郑学斌1(1.中国科学院上海硅酸盐研究所,上海 200050;2.中国科学院大学,北京 100049)摘要:采用大气等离子体喷涂技术制备了ZrC 涂层,表征了涂层的显微结构和基本性能。
采用球-盘接触方式,以WC-Co 硬质合金球为对磨球研究了ZrC 涂层在不同载荷下的磨损性能,同时,与常用的Al 2O 3耐磨涂层进行了比较。
结果表明:ZrC 涂层主要由立方相ZrC 组成,存在部分因氧化而生成的四方相ZrO 2。
5~30N 低载荷条件下,ZrC 涂层的稳定摩擦系数低于Al 2O 3涂层;40~60N 高载荷条件下,ZrC 涂层的稳定摩擦系数略高于Al 2O 3涂层。
不论低载荷条件还是高载荷条件下,ZrC 涂层的体积磨损率均低于Al 2O 3涂层。
载荷较低时,ZrC 涂层的磨损失效形式主要为疲劳剥落和颗粒拔出;在高载荷条件下,发生对磨球的物质转移,ZrC 涂层的磨损失效形式以转移膜磨损和犁削为主。
关键词:等离子体喷涂;ZrC 涂层;耐磨性能中图分类号:TG174.4 文献标识码:A 文章编号:1674-7127(2015)06-0006-05 DOI 10.3969/j.jssn.1674-7127.2015.02.006Tribological Property of ZrC Coating Preparedby Atmospheric Plasma SpraySUI Yun-juan 1,2,NIU Ya-ran 1,HUANG Li-ping 1,ZHENG Xue-bin 1(1.Shanghai Institute of Ceramics ,Chinese Academy of Sciences ,Shanghai 200050,China ;2.University of Chinese Academy of Sciences ,Beijing 100049,China )Abstract :ZrC coating was fabricated by atmospheric plasma spray(APS) and its microstructure and some basic properties were characterized. The tribological property of ZrC coating against WC-Co alloy was evaluated by sliding wear test using ball-on-disk contact configuration. Al 2O 3 coating was employed as comparison in the tribological evaluation. The results showed that ZrC coating was mainly composed of cubic ZrC and some content of tetragonal ZrO 2.The coefficient of friction of ZrC coating is lower than Al 2O 3 coating within a load range of 5N to 30N and is higher than Al 2O 3 coating with loads of 40N ,50N and 60N. The volume wear rate of ZrC coating is lower than Al 2O 3 coating under full range of loads. The observation of worn surface indicated that the dominant wear failure mechanism of ZrC coating was fatigue flaking off and particles pulling out under low load, while the wear failure mechanism of ZrC coating became ploughing effect under high load.Keywords :Plasma spray ;ZrC coating ;Tribological property作者简介:苏运娟(1988-),女,河北邢台人,硕士. Email :suyunjuan@ZrC 具有高熔点(3420℃)、高硬度(25.5GPa),良好的导热性(20.5W/m •K)以及电传导性、耐辐射等性能,被用作超高温陶瓷材料、硬质合金、核阻挡层材料等[1-2]。
文献报道的ZrC 涂层的制备方法有包埋法、化学气相沉积法(CVD)、液相脉冲放电沉积表面强化法(EDC)、氩弧熔覆法、第2期· 35 ·真空热蒸镀法和等离子体喷涂法等[3-4]。
等离子体火焰焰流温度高达10000℃,几乎可以熔化所有的材料,尤其适合高熔点涂层材料的制备。
吴恒等[4]在SiC-C/C复合材料表面采用超音速等离子体喷涂技术制备了ZrC涂层,发现其具有较好的抗烧蚀性能。
然而,ZrC涂层作为耐磨材料的研究报道很少。
本文采用大气等离子体喷涂方法制备了ZrC涂层,表征了其显微结构特征和基本性能,重点研究了其磨损性能,并与常用的Al2O3耐磨涂层进行比较,分析了其磨损失效形式。
1试验材料和方法1.1原材料论文所用的原材料包括ZrC粉(长沙琅峰金属有限公司)、Al2O3粉(沈阳双实磨料磨具有限公司)以及不锈钢基材(型号为AISI314)。
利用激光粒度仪(BT-9300S,丹东市百特仪器有限公司)测试粉体的粒径分布,其中,ZrC 粉体的粒径分布为10~80μm,Al2O3粉体的粒径分布为10~100μm,不锈钢基材的尺寸为Ф60mm×8mm。
1.2涂层制备与表征选用Sulzer Metro公司(瑞士)的A-2000自动大气等离子体喷涂系统,该系统主要由F4-MB 型喷枪以及ABB公司(美国)生产的S3型机械手组成,送粉器为Twin-10型双送粉系统。
等离子体产生气体为氩气(Ar)和氢气(H2),送粉气体是氩气。
为提高ZrC涂层和Al2O3涂层与不锈钢基体材料的结合性能,选择NiCr涂层作为过渡层。
采用场发射扫描电子显微镜(S-4800,Hitachi,日本)观察涂层的形貌,利用X射线衍射仪(XRD,CuKα,λ=1.5406nm,D/ Max-2550V,Rigaku,日本) 分析涂层的相组成。
涂层表面粗糙度采用表面轮廓仪(T8000,HOMMEL,德国)进行测试,测量步长和距离分别为0.5mm/s和4.8mm。
采用图像分析法测量ZrC涂层的气孔率,使用的图片为截面扫描电镜图片,每个样品采用放大倍数为1000倍的照片,分析软件为Qwin(Qwin Leica,德国);涂层抛光后在维氏硬度仪(TUKON-2100B,Instron,美国)测量显微维氏硬度数值,载荷为1.96N,停留时间为15s。
表面粗糙度、气孔率和显微硬度值均是取5个测试值得平均值。
1.3耐磨测试将实验用涂层样品(Ф60mm)进行表面研磨和抛光,抛光后涂层的平均粗糙度Ra为0.3-0.5μm。
采用UMT多功能摩擦磨损测试仪(UMT-3,CETR,美国),以球-盘接触方式对抛光后的涂层进行摩擦磨损性能测试。
对磨球选用YG6(WC-Co)硬质合金球,直径为9.525mm。
磨损实验选取低载荷5N、10N、20N、30N和高载荷40N、50N、60N,相对滑行速度0.5m/s,滑行距离450m。
由UMT多功能摩擦磨损测试仪的传感器测得涂层水平面和竖直方向的受力情况,采用仪器系统自带公式计算获得。
摩擦系数的计算公式为:(1)式中:Fx-涂层水平面x方向的受力;Fy-涂层水平面y方向的受力;Fz-涂层竖直方向(z轴)的受力。
采用表面轮廓仪测量磨痕截面积,再以截面积与磨痕周长相乘,得出磨损体积,每个试样取5个测量值求平均值,按下式计算磨损率。
(2)式中:W-体积磨损率;△V-磨损体积;F-正压力;L-摩擦行程。
2试验结果与讨论2.1显微结构与基本性能图1 ZrC涂层的XRD图谱Fig.1 XRD pattern of ZrC coating等离子体喷涂ZrC涂层耐磨性能研究· 36 · 热 喷 涂 技 术 7卷图3 ZrC 涂层的截面形貌Fig.3 Cross-sectional morphology of ZrC coating 图2 ZrC 涂层的表面形貌 Fig.2 Surface morphology of ZrC coating图1为大气等离子体喷涂ZrC 涂层的XRD 图谱。
从图中可以看出,涂层主要由立方相ZrC 组成。
大气环境喷涂过程中,ZrC 发生部分氧化,生成四方相的ZrO 2。
ZrO 2的硬度较高,常被用作耐磨材料[5-6]。
图2为ZrC 涂层的表面形貌。
涂层的表面存在熔融、半熔、微裂纹、孔隙等多种显微结构特征。
涂层存在复杂结构的原因可能有:首先,等离子体形成气体难以有效地把热量传递给被加热的粉末;其次,相对于金属材料,ZrC 的熔点较高,颗粒难以受热均匀;第三,喷涂过程中难以保证所有ZrC 粒子全部通过等离子体高温区。
以上几个因素都可能导致ZrC 颗粒未能完全熔化。
而这些未完全熔化的粒子沉积到基体上时,不能完全铺展形成了比较复杂的表面结构。
ZrC 涂层的平均粗糙度(Ra)为5.7±0.6μm ,最大粗糙度(Rmax)为37.8±4.8μm 。
图3为ZrC 涂层的截面形貌,可以发现,涂层厚度约为300~350μm ,涂层中气孔相对较多,但分布较均匀。
大气等离子体喷涂中粒子会与周围的空气发生反应,使喷涂粒子表面发生氧化,所以涂层中不可避免的含有ZrO 2,这已经被XRD 结果证实。
由于化学相容性的问题,在氧化物颗粒富集的区域易出现孔隙。
同时,涂层沉积过程中,夹杂着未熔或者半熔的粒子,在它们周围易出现孔隙,成为涂层脱落失效的裂纹源[7-8]。
图中靠近基体的涂层区域出现较大孔隙,这可能是金属基体与涂层硬度差别较大,抛光过程中造成的。
同时,采用图像分析法测量其气孔率为14.1%±1.3%,显微硬度测量结果为6.5±0.5GPa 。