氢氮压缩机开停车操作
操作规程循环氢压缩机的开、停机操作

5.1循环氢压缩机的开、停机操作5.1.1 开机5.1.1.1开机纲要(A级)5.1.1.1.1开机准备工作(1)动力蒸汽引汽暖管(2)K102机体N2置换(3)投用机组循环水(4)投用后置隔离密封气和二级密封气(5)投用润滑油系统(6)凝汽器建立软化水循环(7)机组静态调试(8)投用真空抽汽器建立真空(9)启动盘车器(10)投用轴封蒸汽(11)机体充压(12)投用一级密封气5.1.1.1.2机组冲转暖机(1)启动机组1000rpm转速暖机(2)机组2500rpm转速暖机5.1.1.1.3机组升速加负荷运行(1)机组升速至正常工作转速(2)正常运行状态调整和确认5.1.1.2开机操作(B级)初始状态卡机组本体状态确认()一机组检修安装完毕,验收合格()一汽轮机单机试车完毕()一调速器与调速系统正常可靠()一汽轮机与压缩机联轴器安装完毕()一联轴器防护罩安装好()一两个速关阀关闭工艺系统状态确认()一压缩机入口、出口电动阀、手阀关闭()一压缩机防喘振电动阀关闭,防喘振调节阀FV1502全开()一各氮气系统管线进机组隔离()一机体放火炬线隔离()一机体管线设备保温完整现场环境状态确认()一机组周围环境整洁()一梯子平台安全可靠()一消防设施完备润滑油系统状态确认()一润滑油系统所有过滤器干净安装完毕()一润滑油蓄能器已充压至0.25MPa()一控制油蓄能器已充压0.65MPa()一确认两个蓄能器进口阀关闭()一润滑油系统主、备用油泵盘车正常()一润滑油过滤器手柄扳到要投用过滤器侧()一润滑油冷却器手柄扳到要投用冷却器侧()一油系统冷却器放空阀及排液阀关闭()一油系统过滤器放空阀及排液阀关闭()一油系统管线上各排液阀关闭()一高位油箱快装油阀关闭()一油过滤器的出口阀关闭()一确认各冷却水进出口阀关闭循环水系统状态确认()一循环水已引入装置()一循环水系统各压力表、温度计安装完毕,量程正确校验合格,铅封完好干气密封系统状态确认()一一级密封气线隔离,给气阀关()一后置隔离气线和二级密封气隔离,盲板盲()一后置隔离气线和二级密封气0.7MPa氮气引至给气阀前()一各密封气管路安装完毕()一各密封气管路上各测量仪表安装完毕,量程正确,校验合格蒸汽系统状态确认()-1.0MPa蒸汽已引到自装置主线至机组引汽阀前()一1.0MPa蒸汽进汽轮机管路上各排凝阀打开()一汽轮机机体至凝汽器疏水膨胀箱各排凝阀稍开2-3扣()—汽轮机入口放空阀打开()—真空抽汽器安装完毕,各给汽阀关闭()—蒸汽管线各支撑、吊架、膨胀节完好()—蒸汽系统各测量仪表安装完毕,量程正确,校验合格仪表、电气系统状态确认()一各就地仪表已按规格型号联校好()一仪表盘仪表校验合格()一各控制阀完好备用()一与DCS、ESD系统相联接仪表联校完好()一各电动阀已送电,且完好备用()一机组自保联锁系统试验合格5.1.1.2.1开机准备工作(1)动力蒸汽引汽暖管P [ ] -打开蒸汽管线至速关阀前的各支排凝P [ ] -打开蒸汽进汽轮机前放空P [ ] -缓慢打开1.0MPa蒸汽自系统引汽阀,将阀后压力控制在0.2MPaP [ ] -保持20-30分钟进行暖线排水,其间排水量减少时关小各排凝阀开度保持见汽P [ ] -同时关小蒸汽进汽轮机前放空阀,保持见汽P [ ] -缓慢开大系统引汽阀,控制升压速率不大于0.1MPa/min,温度梯度不大于50℃/h,直至管线末端至机头温度达到230℃P [ ] -对管线进行检查,各回弯、支吊架及膨胀节变形情况正常P [ ] -检查蒸汽管路无泄漏,配合对蒸汽管线各法兰进行热紧P [ ] -全开1.0MPa蒸汽自系统引汽阀(2)K102机体N2置换P ( ) -确认7.5MPa氮气已引至进机组阀前P ( ) -确认K102入口阀7.5MPa氮气线盲板调通,放空关闭P [ ] -缓慢打开7.5MPa氮气进机组给气阀,控制升压速度<0.2MPa/minP [ ] -机体充压至1.0 MPa后,关闭7.5MPa氮气进机组给气阀P [ ] -打开压缩机出口放火炬阀泄压至0.1MPa后关闭P [ ] -按以上步骤反复充压置换三次P [ ] -取机体爆炸气样,确认N2置换合格(含氧量小于0.5%)放火炬线盲板,放空阀盲板P [ ] -拆除压缩机机体排凝线盲盖,确认机体无凝液后恢复盲盖P [ ] -再次用7.5MPa氮气对机体充压,保持机体有0.1MPa的氮气P ( ) -确认7.5MPa氮气进机组阀关闭,机体压力保持0.1MPa不上升P ( ) -确认压缩机出口放火炬阀关闭放火炬线盲板(3)投用机组循环水P ( ) -确认循环水已引入装置P [ ] -打开油冷器循环水出入口连通线建立循环P [ ] -打开凝汽器循环水出入口连通线建立循环P [ ] -打开抽汽器循环水出入口连通线建立循环P [ ] -开油冷器循环水进口手阀,在出口阀前放空见水后关闭放空阀P [ ] -开凝汽器循环水进口手阀,在出口阀前放空见水后关闭放空阀P [ ] -开抽汽器循环水进口手阀,在出口阀前放空见水后关闭放空阀P [ ] -全开油冷器循环水出口手阀投用油冷器循环水P [ ] -全开凝汽器循环水出口手阀投用凝汽器循环水P [ ] -全开抽汽器循环水出口手阀投用抽汽器循环水P [ ] -关闭各循环水出入口连通线P [ ] -打开各压力表手阀,确认压力指示正确,入口压力在0.4MPa左右P [ ] -确认循环水线上各温度计指示正确,入口温度在25℃左右P [ ] -检查循环水线及水冷器各连接部位无泄漏(4)投用后置隔离密封气和二级密封气P ( ) -配合仪表确认密封系统管线上各测量仪表安装完毕无缺失P ( ) -确认0.7MPa氮气已引至后置隔离气线和二级密封气给气阀前P [ ] -打开PI1582引压线手阀,关闭放空阀P [ ] -打开二级密封气过滤器底排凝,确认无水后关闭P [ ] -打开压差表PDI1580前后引压线手阀P [ ] -关闭压差表PDI1580旁通线手阀和放空阀P [ ] -打开自力压控阀PCV1581前后手阀P [ ] -打开PIT1585引压线手阀,关闭放空阀P [ ] -打开自力压控阀PCV1582前后手阀P [ ] -打开PI1583引压线手阀P [ ] -将二级密封气双联精过滤器切换至单组P [ ] -打开二级密封气两路给气线手阀P [ ] -打开两路泄漏密封气低压瓦斯放空线上PIT1580和PIT1581引压线手阀,关闭放空阀P [ ] -打开两路泄漏密封气低压瓦斯放空线上安全爆破片的前后手阀P [ ] -打开泄漏密封气放低压瓦斯放空线手阀P [ ] -将0.7MPa氮气进二级密封和后置隔离气的给气阀前盲板调通P [ ] -关闭0.7MPa氮气进二级密封和后置隔离气的给气阀后放空P [ ] -打开0.7MPa氮气进二级密封和后置隔离气给气阀P [ ] -检查密封气管线各连接部位有无泄漏P [ ] -将PCV1581控制压力设定为0.6MPaP [ ] -将PCV1582控制压力设定为0.4MPaP [ ] -调整操作,使二级密封和后置隔离气线各参数在以下范围内PI1582 0.8 MPa PDI1580 ≤0.2 MPaPI1585 0.03MPa PI1583 0.16MPaFIT1582 3.42Nm3/h FIT1583 3.42Nm3/hPIT1580 0.062 MPa PIT1581 0.062 MPaFIT1582 16.42Nm3/h FIT1583 16.42Nm3/h(5)投用润滑油系统P ( ) -确认润滑油管线安装完毕P ( ) -确认润滑油箱D412内壁已用面团清洁干净P ( ) -配合仪表确认油箱及油系统管路上各仪表测量表安装完毕无缺失,量程正确P ( ) -确认滤油过滤机完好备用,已送电P [ ] -关闭油箱放空,向油箱中加入合格的L-TSA46#汽轮机润滑油至液位计的2/3 P [ ] -打开油箱氮封给气阀向油箱充入N2,使油箱保持微正压P [ ] -投用润滑油箱D412电加热器,油箱油温控制在25-55℃P [ ] -倒通润滑油线流程,投用控制阀PV-1528和PCV-1532,将PV-1528副线开3扣P [ ] -检查主辅油泵P405、P406各零件齐全完好,各连接部位无松动P ( ) -确认后置隔离气已正常投用至少10分钟(见C级说明5.1.1.2.1 a)P [ ] -对润滑油主、辅助油泵P405、P406盘车,检查转动灵活无卡涩P [ ] -联系电工给润滑油主辅油泵P405、P406送电,将联锁开关打在“手动”位置P [ ] -打开润滑油主辅油泵P405、P406的出入口阀及压力表阀P [ ] -投用润滑油主辅油泵P405、P406的出口安全阀P [ ] -分别点动主辅油泵P405、406电机,检查电机转向正确后停泵P [ ] -启动一台润滑油泵,建立油路循环P [ ] -检查运行润滑油泵振动、温度在正常范围,无机械杂音P [ ] -检查润滑油管路各连接部位无泄漏P [ ] -打开投用油冷器回油箱阀,在视镜中见油后关闭P [ ] -打开投用过滤器回油箱阀,在视镜中见油后关闭I [ ] -调节PV1528开度,使泵出口压力在1.1 MPaP [ ] -设定润滑油压自控阀PCV1532控制油压在0.3 MPaP [ ] -打开润滑油和控制油蓄压器入口阀P [ ] -打开高位油罐快装油阀,见溢流回油后关闭I [ ] -将PV1528改为手动,调节使润滑油总管油压在0.3 MPa,控制油压在0.85 MPaP [ ] -调节润滑油进机组各支路油压在0.15 MPa,确认各路回油正常P [ ] -调节油冷却器冷却水量,控制油冷却器后油温在43-48℃P [ ] -检查过滤器前后差压<0.15 MPaI ( ) -确认高位油箱的液位报警消除I ( ) -确认油压低低报警PALL消除I ( ) -确认油压低报警PAL消除P [ ] -将主辅助润滑油泵投自动(6)凝汽器建立软化水循环P ( ) -确认凝汽器及配管安装完毕,压力表、温度计、液面计完好,校验合格铅封完好P [ ] -打开除盐水进凝汽器给水阀向凝汽器热井补水至液面计指示的75%P [ ] -将液位控制阀LV1552B前后手阀关闭,副线阀关闭P [ ] -将液位控制阀LV1552A前后手阀关闭,副线阀打开P [ ] -联系电工给凝结水泵电机送电P [ ] -将凝结水泵选择开关都打在“手动”位置P [ ] -盘车、检查电机转动是否灵活,无卡住及异常声音P [ ] -全开P407/AB入口阀门,投用出口线压力表P [ ] -点动电机,检查电机转向正确后停泵P [ ] -启动一台凝结水泵,出口压力正常后打开出口阀建立凝结水循环P [ ] -稍开凝结水泵出口至凝汽器膜板式安全阀上水阀建立水封,并打开安全阀底部放空见水P [ ] -待凝汽器热井液位稳定后,投用液位控制阀LV1552A及LV1552BP [ ] -检查各连接部位无泄漏P [ ] -将主备用凝结水泵的选择开关打在“自动”位置I [ ] -将LIC1552液位控制打在手动,将液位设定为50%I ( ) -确认液位控制阀LV1552A及LV1552B工作正常,凝汽器热井液位控制在±150mm内(7)机组静态调试a、辅助油泵自启动试验P [ ] -确定一台油泵为主油泵P [ ] -启动主油泵,将油压调节至正常范围P [ ] -将辅助油泵开关打至“自动”位置P [ ] -配合主操逐渐开大油泵出口回油箱副线手阀,缓慢降低总管油压直至辅泵自启动I [ ] -将辅泵自启动时的压力进行记录,并确认辅泵自启动声光报警P [ ] -将总管油压调回至正常值,按以上步骤再重复操作2次P [ ] -将油泵切换到另一台泵,根据以上操作步骤进行调试三次b、润滑油压低低停机自保试验P ( ) -确认润滑油系统运行正常P ( ) -确认汽轮机1.0Mpa主蒸汽线进汽手阀关闭P ( ) -确认汽轮机2个速关阀关闭P [ ] -配合仪表给出入口电动阀MHV1503全开信号P [ ] -配合仪表给出出口电动阀MHV1505全开信号P [ ] -配合仪表给出防喘振线电动阀MHV1504全开信号P [ ] -配合仪表将一级密封气流量FI1580、FI1581设定为250m3/hI [ ] -将K102联锁复位P [ ] -现场启动脱扣阀P ( ) -现场确认2个脱扣阀全开P [ ] -现场按“启动”启动气压机I [ ] -配合仪表给出模拟的正常运行转速P [ ] -将辅助润滑油泵的选择开关打在“手动”P [ ] -缓慢开大油泵出口回油箱控制阀PI1528副线,使总管油压缓慢下降直至油压低停机I ( ) -确认K102停机声光报警正常I ( ) -确认汽轮机2个速关阀关闭I ( ) -确认K102出入口及防喘振电动阀关闭,防喘振控制阀全开I [ ] -记录联锁停机时的润滑油总管压力值c、状态监测联锁停机试验P ( ) -确认汽轮机1.0Mpa主蒸汽线进汽手阀关闭P ( ) -确认汽轮机2个速关阀关闭I [ ] -配合仪表给出入口电动阀MHV1503全开信号I [ ] -配合仪表给出出口电动阀MHV1505全开信号I [ ] -配合仪表给出防喘振线电动阀MHV1504全开信号I [ ] -配合仪表将一级密封气流量FI1580、FI1581设定为250m3/hI [ ] -将K102联锁复位P [ ] -现场启动脱扣阀P ( ) -现场确认2个脱扣阀全开P [ ] -现场按“启动”启动气压机I [ ] -配合仪表给出模拟的正常运行转速I [ ] -配合仪表模拟给出轴位移、振动高高等联锁信号I ( ) -确认K102停机声光报警正常I ( ) -确认汽轮机2个速关阀关闭I ( ) -确认K102出入口及防喘振电动阀关闭,防喘振控制阀全开I [ ] -将静态调试结果记录在静态调试表中d、超速联锁停机试验P ( ) -确认汽轮机1.0Mpa主蒸汽线进汽手阀关闭P ( ) -确认汽轮机2个速关阀关闭I [ ] -配合仪表给出入口电动阀MHV1503全开信号I [ ] -配合仪表给出出口电动阀MHV1505全开信号I [ ] -配合仪表给出防喘振线电动阀MHV1504全开信号I [ ] -配合仪表将一级密封气流量FI1580、FI1581设定为250m3/hI [ ] -将K102联锁复位P [ ] -现场启动脱扣阀P ( ) -现场确认2个脱扣阀全开P [ ] -现场按“启动”启动气压机I [ ] -配合仪表给出模拟的正常运行转速I [ ] -配合仪表将“转速高高停机”联锁项的信号值给为“1”I ( ) -确认K102停机声光报警正常I ( ) -确认汽轮机2个速关阀关闭I ( ) -确认K102出入口及防喘振电动阀关闭,防喘振控制阀全开I [ ] -将静态调试结果记录在静态调试表中e、手动停机静态试验P ( ) -确认汽轮机1.0Mpa主蒸汽线进汽手阀关闭P ( ) -确认汽轮机2个速关阀关闭I [ ] -配合仪表给出入口电动阀MHV1503全开信号I [ ] -配合仪表给出出口电动阀MHV1505全开信号I [ ] -配合仪表给出防喘振线电动阀MHV1504全开信号I [ ] -配合仪表将一级密封气流量FI1580、FI1581设定为250m3/hI [ ] -将K102联锁复位P [ ] -现场启动脱扣阀P ( ) -现场确认2个脱扣阀全开P [ ] -现场按“启动”启动气压机I [ ] -配合仪表给出模拟的正常运行转速I [ ] -按“紧急停机”按钮I ( ) -确认K102停机声光报警正常I ( ) -确认汽轮机2个速关阀关闭I ( ) -确认K102出入口及防喘振电动阀关闭,防喘振控制阀全开I [ ] -将静态调试结果记录在静态调试表中f、排汽压力高高联锁停机试验P ( ) -确认汽轮机1.0Mpa主蒸汽线进汽手阀关闭P ( ) -确认汽轮机2个速关阀关闭I [ ] -配合仪表给出入口电动阀MHV1503全开信号I [ ] -配合仪表给出出口电动阀MHV1505全开信号I [ ] -配合仪表给出防喘振线电动阀MHV1504全开信号I [ ] -配合仪表将一级密封气流量FI1580、FI1581设定为250m3/hI [ ] -将K102联锁复位P [ ] -现场启动脱扣阀P ( ) -现场确认2个脱扣阀全开P [ ] -现场按“启动”启动气压机I [ ] -配合仪表给出模拟的正常运行转速I [ ] -配合仪表将三个排汽压力PSA1550、PSA1551、PSA1552中的任意两个设定为0.07MPaI ( ) -确认K102停机声光报警正常I ( ) -确认汽轮机2个速关阀关闭I ( ) -确认K102出入口及防喘振电动阀关闭,防喘振控制阀全开I [ ] -将静态调试结果记录在静态调试表中g、辅助凝结水泵自启动试验P [ ] -按本章1.5节步骤建立凝结水系统的正常循环P [ ] -将辅助凝结水泵的选择开关打在“自动”位置P [ ] -打开凝汽器补水线向凝汽器加水,使热井液位达到+150mmP [ ] -检查辅助凝结水泵是否自启动I [ ] -将静态调试结果记录在静态调试表中(8)投用真空抽汽器建立真空P ( ) -确认真空抽汽器管路连接完好,各测量仪表安装完毕,量程正确校验合格P ( ) -确认凝汽器及真空抽汽器冷却水已正常投用P [ ] -打开凝汽器至启动抽汽器及一、二级抽汽器的空气连通阀P ( ) -确认一、二级抽汽器冷凝水回凝汽器阀全开,放空关闭P [ ] -全开启动抽汽器的给汽阀,维持凝汽器真空度在-0.04MPa(表压)P [ ] -打开二级抽汽器的给汽阀,投用二级抽汽器P [ ] -然后打开一级抽汽器的给汽阀,投用一级抽汽器P [ ] -主抽汽器检查运行正常后,停启动抽汽器P ( ) -确认此时凝汽器真空度在-0.06MPa(表压)P [ ] -检查各连接部位无泄漏(检查泄漏方法)(9)启动盘车器P ( ) -确认润滑油系统已正常投用P [ ] -打开压力油进盘车器入口阀P [ ] -将盘车器与机组啮合P [ ] -启动盘车器,注意连续盘车时间不超过30min(见C级说明5.1.1.2.1 b)P [ ] -检查机组及盘车器运行无异常声音(10)投用轴封蒸汽(见C级说明5.1.1.1 c)P ( ) -确认循环机盘车运行正常P [ ] -打开轴封蒸汽给汽阀,将轴封蒸汽压控阀设定在0.008MPa(表压),向轴封供汽(11)机体充压I ( ) -确认反应系统已充压至3.0MPaP [ ] -开K102机体入口阀7.5MPa氮气充压线向机体充压至3.0MPa,升压速度≯0.2MPa/min 关闭充压阀I [ ] -在SIS上打开K102进出口电动阀MHV1503和MHV1505I [ ] -在SIS上打开K102防喘振电动阀MHV1504P [ ] -打开K102进出口线手阀(12)投用一级密封气P [ ] -打开PI1580引压线手阀,关闭放空阀P [ ] -打开KO除湿器底排凝,确认无水后关闭P [ ] -打开KO除湿器进、出口线手阀P [ ] -关闭KO除湿器进出口副线手阀P [ ] -打开压差表PDIT1580前后引压线手阀P [ ] -关闭压差表PDIT1580旁通线手阀和放空阀P [ ] -打开压差表LT1580前后引压线手阀,关闭引压线放空阀P [ ] -关闭KO除湿器顶放空线手阀P [ ] -打开PCV1580前后手阀P [ ] -关闭PCV1580副线手阀P [ ] -打开一级密封气双联精过滤器底排凝,确认无水后关闭P [ ] -打开压差表PDIT1581前后引压线手阀P [ ] -关闭压差表PDIT1581旁通线手阀和放空阀P [ ] -打开压差表PDIT1582前后引压线手阀P [ ] -关闭压差表PDIT1582旁通线手阀和放空阀P [ ] -打开PI1581引压线手阀,关闭放空阀P [ ] -将一级密封气双联精过滤器切换至单组P [ ] -打开FIT1580、FIT1581前后给气手阀P [ ] -打开一级密封气进密封气增压器前后手阀P [ ] -打开PI1584引压线手阀,关闭放空阀P [ ] -打开PIT1582引压线手阀,关闭放空阀P [ ] -打开密封气增压器出口缓冲罐底排凝,确认无水后关闭P [ ] -打开出口缓冲罐顶安全阀PSV1580前手阀,关闭安全阀副线P [ ] -打开PI1585引压线手阀,关闭放空阀P [ ] -打开PIT1583引压线手阀,关闭放空阀P [ ] -打开K102出口至一级密封给气阀P [ ] -打开PI1586引压线手阀,关闭放空阀P [ ] -打开PI1587引压线手阀,关闭放空阀P [ ] -打开PI1588引压线手阀,关闭放空阀P [ ] -打开PIT1584引压线手阀,关闭放空阀P [ ] -将PCV1583、PCV1584压力设定为0.612 MPaP [ ] -打开密封气增压器动力风给气阀,使一级密封气增压器正常备用P [ ] -检查密封气管线各连接部位无泄漏P [ ] -调整操作,使一级密封各参数在以下范围内PI1580 0.8 MPa PDIT1580 ≤0.02 MPaLT1580 ≤50 mm PDIT1581 ≤0.02 MPaPDIT1582 ≥0.25 MPa PI1586 0.8 MPaFIT1580 250Nm3/h FIT1581 250Nm3/hPI1588 0.4 MPa PIT1584 <0.1 MPa稳定状态卡()一动力蒸汽引汽暖管结束,各排凝脱水见汽,管路末端温度230℃以上()一机体氮气置换合格,氧含量小于0.5%()一机组循环水系统投用正常()一后置隔离气和二级密封气正常投用()一一级密封气正常投用,FI1580、FI1581≮187Nm3/h,PDIT1582≥0.25 MPa()一润滑油及控制油正常投用,油温43-48℃,总管油压0.3 MPa,控制油压0.85MPa,进机组各支路油压0.15 MPa,过滤器压差<0.15MPa()一凝汽器软化水循环正常,热井液位50%()一凝汽器真空度建立正常-0.06MPa(表压)()一机组盘车正常()一轴封蒸汽已投用,压力0.008MPa(表压)()一机组静态调试完毕合格5.1.1.2.2机组冲转暖机(1)启动机组1000rpm暖机I [ ] -通知生产调度准备启动K102机组I [ ] -通知机、电、仪相关人员到现场P [ ] -停用盘车装置,并确认盘车脱开I [ ] -接到开机指令后,按联锁“复位”按钮I ( ) -确认启动画面上所有启动条件满足,无报警项P [ ] -现场按“准备启动”按钮打开速关阀2301、2302P ( ) -确认速关阀2301、2302全开I ( ) -在SIS上确认“气压机允许启动”灯变绿I [ ] -在SIS上将启动方式打在“冷启动”I [ ] -在SIS上将升速方式打在“自动”I [ ] -在SIS上将操作方式打在“控制室”I [ ] -将1000rpm暖机时间设定在1800sI [ ] -将2500rpm暖机时间设定在600sI [ ] -将防喘振画面上防喘振控制打在“半自动”I [ ] -在SIS上点击“启动”按钮I ( ) -确认机组转速正常,稳定在1000rpm左右P ( ) -确认现场实际转速与反馈转速一致P [ ] -暖机时,检查机组各部运转情况机体各部热膨胀正常转动部件无机械杂音机组振动在正常范围内机体各密封部位无泄漏P [ ] -调整油冷器冷却水,控制润滑油冷后温度在43~48℃I [ ] -检查机组SIS上各参数在正常范围汽轮机轴振动<50μm压缩机轴振动<63.5μm汽轮机轴位移<0. 65 mm压缩机轴位移<0. 56 mm汽轮机推力轴瓦温度<95℃压缩机推力轴瓦温度<105℃汽轮机径向轴承温度<95℃压缩机径向轴瓦温度<105℃润滑油总管压力0.3 MPa控制油压力>0.85 MPa润滑油经过轴承后的温升≤30℃离开轴承的润滑油温度应<80℃汽轮机排汽压力0.009 MPa热井液位在50%P [ ] -关闭1.0 MPa蒸汽进汽轮机线上各排凝P [ ] -关闭1.0 MPa蒸汽进汽轮机前放空阀I [ ] -根据实际开机情况,可将启动选择开关转换到手动状态,延长1000rpm暖机时间(2)机组2500rpm转速暖机I ( ) -确认升速方式在自动状态下,1000rpm暖机30分钟结束,机组自动升速至2500rpm暖机I [ ] -当升速方式在手动状态时,1000rpm暖机结束后,通过手操器将转速升至2500rpm暖机(速度的限制)I ( ) -SIS上确认2500rpm运行状态下机组各参数在正常范围内P ( ) -现场确认2500rpm运行状态下机组各参数在正常范围内稳定状态卡()一机组2500rpm暖机合格()一机组各轴振动在正常范围()一机组各轴位移在正常范围()一机组各轴承温度在正常范围()一润滑油总管压力0.3 MPa()一控制油压力>0.85 MPa()一润滑油温度43~48℃()一汽轮机排汽压力0.009 MPa()一热井液位在50%5.1.1.2.3机组升速加负荷运行I ( ) -当启动方式在自动状态时,确认2500rpm暖机结束后汽轮机按照升速曲线快速通过临界转速区4500rpm-6200rpm升至调速器最小控制转速8078rpmI [ ] -当启动方式在手动状态时,2500rpm暖机结束后通过手操器将转速逐渐升到最小临界转速4500rpmIP( ) -当转速达到4500rpm时机组将自动快速通过4500rpm-6200rpm临界转速区,最终在6200rpm后停止升速,确认该过程中机组各运行参数在正常范围I [ ] -通过手操器将K102逐渐升速到8000rpmIP( ) -再次确认8000rpm运行状态下机组各参数在正常范围内I [ ] -通过手操器将转速升到调速器最小控制转速8078rpm,此时防喘振调节阀FV1502带电(2)正常运行状态调整和确认I [ ] -根据反应循环氢量要求和防喘振画面逐步关小防喘振调节阀FV1502加负荷,注意保持喘振裕度≥2%I [ ] -若循环氢量未达到反应要求,通过手操器在8078 rpm-11310 rpm范围内提转速加负荷IP( ) -确认正常转速下各参数在正常范围内a. 辅助系统各点润滑油温度、压力正常润滑油过滤器差压正常各润滑点回油顺畅(油流占管径1/3左右)润滑油高位油箱液位、油温正常调节油油压、温度正常冷却水系统正常级间密封气压力及流量正常隔离气压力及流量正常干气密封密封气与平衡气压差正常所有报警联锁系统正常b. 循环机循环机轴振动、位移正常循环机轴承温度正常压缩机防喘振量正常循环机无异常声响循环机无异常泄漏循环机转速波动小于±20转c. 动力设备蒸汽压力为0.9~1.3MPa蒸汽温度为200~260℃汽轮机进气流量2.97 kg/s真空系统正常,排汽压力0.009MPa汽轮机轴振动<50μm汽轮机轴位移<0. 65 mm轴封蒸汽压力正常0.008 MPa汽轮机无异常声响汽轮机无泄漏汽轮机轴瓦温度正常热膨胀正常汽轮机转速正常联锁自保系统投用正常d. 工艺系统机组入口压力为14.6MPa机组出口压力17MPa机组入口温度为50℃机组出口温度为65~69℃充氮气线盲板隔离机体排凝阀、放空阀加盲板稳定状态卡()一循环机入口阀开()一循环机出口阀开()一防喘振电动阀开,防喘振调节阀投用()一仪表电气投用正常(压力表、压力开关、温度表、报警和自保联锁)()一充氮气线加盲板隔离()一机体放火炬阀关闭()一无异常泄漏()一机组运行正常5.1.3辅助说明(C级)5.1.1.2.1 a后置隔离气投用稳定至少10min后,再投用润滑油系统,以防止润滑油进入干气密封系统损坏密封5.1.1.1 b 机组盘车不可连续超过30分钟,以防止低转速下损坏干气密封的旋转密封面;当30分钟机组仍未进入开机,可考虑停用盘车装置5.1.1.1 c 轴封蒸汽的投用应在机组盘车中进行,以保证机组各部位均匀热膨胀,防止机组在静态下造成转子和汽缸上下热变形不一致而损坏5.1.2停机5.1.2.1停机纲要(A级)5.1.2.1.1循环氢压缩机停机(1)正常停机(2)紧急停机5.1.2.1.2循环氢压缩机备用(1)循环氢压缩机热备用(2)循环氢压缩机冷备用5.1.2.1.3循环氢压缩机交付检修5.1.2.2停机操作(B级)初始状态卡()一循环机入口电动阀及手阀全开()一循环机出口电动阀及手阀全开()一防喘振电动阀全开()一速关阀2301、2302全开()一防喘振调节阀FV1502正常可操()一仪表电气投用正常(压力表、压力开关、温度表、报警和自保联锁)()一机体排凝阀、放火炬阀关闭加盲板()一循环机在正常转速8078~11310rpm内运行()一循环机各轴振动、位移、温度在正常范围()一循环机润滑油系统、干气密封系统运行正常5.1.2.2.1循环氢压缩机停机(1)正常停机I [ ] -随着反应系统泄压,逐步开大防喘振调节阀并提转速,防止工作点进入喘振区I [ ] -当通过防喘振调节阀和转速调节,工作点仍靠近喘振区,通知调度准备停机I [ ] -在启动画面内将保持1000 rpm倒计时时间设定为“180s”(待定)I [ ] -按下启动画面中“正常停机”按钮I ( ) -当转速降到3000rpm时,确定干气密封增压泵启动,否则通知外操启动增压泵I ( ) -确认转速降到1000rpm运行180s后转速归零I ( ) -在SIS上确认K102进出口电动阀MHV1503、1505关闭I ( ) -确认K102防喘振电动阀MHV1504关闭,FV1502全开P ( ) -现场确认循环机转速归零P ( ) -现场确认MHV1503、MHV1504和MHV 1505关闭P ( ) -现场确认速关阀2301、2302关闭P [ ] -关闭K102进、出口线手阀P [ ] -打开1.0Mpa蒸汽进汽轮机线上各排凝脱水P [ ] -稍开1.0Mpa蒸汽进汽轮机前放空见汽P [ ] -启动液压盘车装置P [ ] -停用一级、二级真空抽汽器P [ ] -停用轴封抽汽器P [ ] -将备用凝结水泵控制打在手动,按停运行凝结水泵(2)紧急停机I [ ] -通知反应岗位K102紧急停机I [ ] -在辅操台上按“紧急停机”按钮I ( ) -当转速降到3000rpm时,确定干气密封增压泵启动,否则通知外操启动增压泵I ( ) -确认循环机转速归零I ( ) -在SIS上确认K102进出口电动阀MHV1503、1505关闭I ( ) -确认K102防喘振电动阀MHV1504关闭,FV1502全开P ( ) -现场确认循环机转速归零P ( ) -现场确认MHV1503、MHV1504和MHV 1505关闭P ( ) -现场确认速关阀2301、2302关闭。
压缩机的开、停机步骤方法

压缩机的开、停机步骤方法1、开机准备(1)投用曲轴箱的氮气系统,在曲轴箱内充满氮气。
(2)投用各气缸填料函处的氮气封闭系统。
(3)投用电动机循环水冷却系统。
(4)投用压缩机气缸冷却水系统。
(5)投用1级进气阀卸荷器的仪表控制系统。
(6)将压缩机高压、低压填料泄漏气流程打通。
(7)压缩机填料排油阀关闭。
(8)起动给曲轴箱润滑的齿轮泵。
(9)起动给填料冷却、冲洗的齿轮泵。
(10)利用盘车器盘车。
(11)确认现场没有冷却水泄漏。
(12)确认润滑油没有泄漏。
(13)确认仪表系统完好,连锁保护系统完好。
2、起动压缩机(1)在现场操作按钮上起动压缩机。
(2)压缩机进行氮气置换。
(3)确认压缩机氮气置换合格。
(4)压缩机进行乙烯置换。
(5)确认压缩机乙烯置换合格。
(6)确认润滑油箱温度在40~50℃之间。
(7)确认压缩机系统温度正常。
(8)确认齿轮泵运转声音正常。
(9)确认机组没有泄漏。
(10)确认填料注油器运行正常。
(11)按表1和表2测量数据,填入表内。
表1.压缩机气阀出入口压力和温度表2.气缸振动值(12)确认机组运行正常。
3、停止压缩机(1)手动按压缩机的主电动机停止按钮。
(2)当主电动机停止运行5min以后,现场手动停止曲轴箱润滑油泵的按钮。
(3)确认填料部位的冷却冲洗润滑泵已经停止运行。
(4)关闭压缩机的入口阀门。
(5)关闭压缩机的出口阀门。
(6)打开压缩机的出口放空阀,进行泄压。
(7)打开压缩机的入口放空阀,进行泄压。
(8)确认压缩机系统压力为0。
(9)打开压缩机与火炬线连接的阀门。
(10)关闭压缩机出口放空阀门。
(11)打开压缩机入口充氮气阀门,充氮气的压力为0.5MPa。
(12)打开压缩机的出口放空阀,进行泄压。
(13)氮气置换三次,取样化验合格为止。
(14)确认压缩机系统内部无压力。
(15)关闭与压缩机与外界联系的阀门。
(16)办理断电手续,切断电源。
新氢压缩机操作规程.
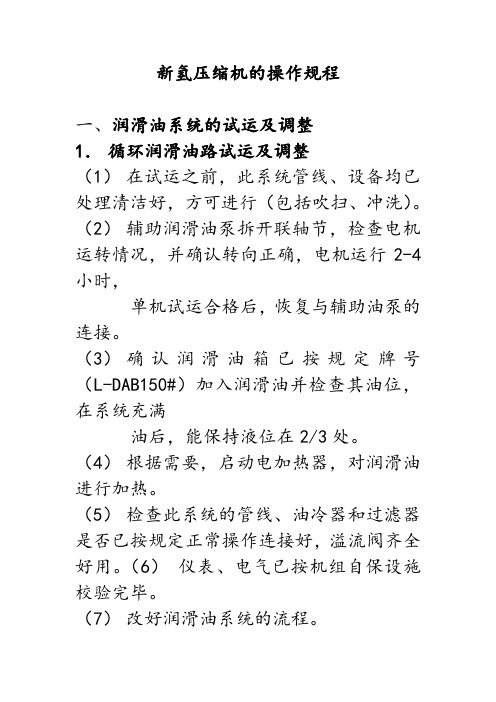
新氢压缩机的操作规程一、润滑油系统的试运及调整1.循环润滑油路试运及调整(1)在试运之前,此系统管线、设备均已处理清洁好,方可进行(包括吹扫、冲洗)。
(2)辅助润滑油泵拆开联轴节,检查电机运转情况,并确认转向正确,电机运行2-4小时,单机试运合格后,恢复与辅助油泵的连接。
(3)确认润滑油箱已按规定牌号(L-DAB150#)加入润滑油并检查其油位,在系统充满油后,能保持液位在2/3处。
(4)根据需要,启动电加热器,对润滑油进行加热。
(5)检查此系统的管线、油冷器和过滤器是否已按规定正常操作连接好,溢流阀齐全好用。
(6)仪表、电气已按机组自保设施校验完毕。
(7)改好润滑油系统的流程。
(8)过滤器的操作手柄处于正确位置(任一侧)。
(9)盘车检查辅助油泵,应无偏重、卡涩的现象。
(10)启动辅助油泵,建立润滑油系统的循环,并检查确认下列内容:①润滑油泵出口压力0.35"0.45MPa②冷后温度40"50℃③润滑油总管压力≮0.25MPa④过滤器差压≯0.01,一般在0.06"0.08MPa(11)一般循环油路经4"6小时的单独试运转,停车后除检查清洗系统中可能有的积垢外,还应检查润滑油的品质,必要时再次更换润滑油。
2.气缸(填料)润滑油系统试运转及调整(1)将注油器及注油箱清扫干净后,装入规定牌号的润滑油(L-DAB150#)。
(2)拆下各气缸注油点的单向阀,启动注油器油泵的电机,让润滑油将管内气体赶走,直至清洁的油出现。
然后将单向阀回装,恢复原流程。
观察各单点单柱动作是否良好。
(3)确认各润滑点均有润滑油后,再调节注油器的注油量,观察其变化是否正常,否则应予以排除。
二.气缸及填料冷却水系统试运及调整1、在试运之前,此系统管线、设备均已处理清洁好,方可进行(包括吹扫、冲洗)。
2、冷却水主、备泵拆开联轴节,检查电机运转情况,并确认转向正确,电机运行2-4小时,单机试运合格后,恢复与水泵的连接。
无润滑氢气氮气压缩机生产安全操作规程

无润滑氢气氮气压缩机生产安全操作规程无润滑氢气氮气压缩机是一种特殊的压缩机,广泛应用于医药、化工、冶金、航空航天等领域。
由于其工作介质是氢气和氮气,具有易爆性、毒性和高温高压等特点,因此在操作过程中必须严格遵守相应的安全操作规程,以保障员工和设备的安全。
一、操作前准备工作1.检查设备及安全阀是否正常。
2.检查氢气和氮气系统是否正常,阀门是否关闭或处于正常状态。
3.检查冷却水、润滑油是否充足,并保证正常供应。
4.检查工作区域是否清洁、整齐、安全。
5.安全防护措施:操作人员必须穿戴防静电工作服、防爆手套、防毒面具等防护装备,确保操作过程中的安全。
二、操作规程1.开启压缩机进气阀门,打开电源开关,启动压缩机。
2.观察压缩机的运行情况,尤其要注意压缩机的电流、压强、温度等情况是否正常。
3.在氢气或氮气压力超过设定值时,自动安全阀会打开,将氢气或氮气放出。
4.当需要停机时,先关闭进气阀门,让压缩机自动停机。
5.关闭电源开关,关闭出气阀门。
6.记录每次操作的参数和数据。
三、事故处理1.如果观察到电流、压强等数值异常,或压缩机发生异响、振动等异常情况,应立即停机检查,找出故障原因,并及时进行处理。
2.在氢气或氮气泄漏时,应立即关闭压缩机进气阀门及系统阀门,并立即开启通风系统,远离泄漏区域,切勿操作电器和手机以避免火花产生,并通知专业技术人员及时处理泄漏情况。
3.在紧急情况下,应立即按下紧急停止开关,切断电源,停止压缩机运转。
四、安全注意事项1.在操作前,必须进行充分的培训,掌握无润滑氢气氮气压缩机的基础知识和操作规程,严格遵守操作规程。
2.在操作过程中,必须注意安全,坚持以人为本的原则,避免因疏忽大意而造成人身伤害或设备损坏。
3.对于无润滑氢气氮气压缩机的维护保养,应根据规定进行定期检查和维护,确保设备的正常运转。
4.在任何情况下,都不要将压缩机用于不正常的工作场合,以免发生意外事故。
总之,无润滑氢气氮气压缩机是一种具有较高风险的设备,必须严格遵守安全操作规程,采取切实可行的措施,确保人员和设备的安全,防止不安全事故的发生。
氢压机开停车

氢压机开停车操作1开车前准备1.1、氢压机安装完成,已通过试压、试漏、试运转,所有连锁经调试合格,设备交接手续齐全,或氢压机经检修合格后完成交接手续,氢压机处于正常待机状况。
1.2、联系调度给车间送仪表空气、压缩空气、循环冷却水、氢气、氮气。
1.3、现场清理干净,确保无任何不必要的和与岗位操作无关的杂物垃圾,做好现场的5S工作。
1.4、检查各温度计、压力表、液位计、连锁报警装置等正常,检查各设备、管道气密性是否良好,无渗漏;设备运转是否完好,盲板是否拆除,各手动阀是否都灵活,并关闭各阀门。
1.5、联系仪表工检查所有仪表正常,联系电工电器检查合格,检查电机绝缘良好并送电。
1.6、检查氢压机油位要求在油位计的"H"位置。
1.7、准备好记录本,报表及各项用品。
1.8、检查并确定所有的安全保护装置完好。
2开车操作2.1、氮气、氢气置换氢压机系统及管道。
2.2、氢压机开车。
2.2.1 检查所有安全阀的根部阀处于全开,各仪表阀打开,其他阀门开车前应该处关闭的位置;开启盘车器给氢压机盘车3-4转,运转灵活,无卡碰现象,与调度及前后岗位联系好准备开车。
2.2.2 开水冷器,油冷器的上水阀和回水阀,调节水量正常。
2.2.3 全开1#、2#,3#,4#气缸夹套水进出口阀,并排气。
2.2.4开氮气保护气进出口阀,并调节好保护气量。
2.2.5联系电工给氢压机系统送电,开辅助润滑油泵,给氢压机各润滑点供油,调节好油压及油量,并检查油位在视镜的中上部为合适。
2.2.6 开氢压机吸入罐进口阀,全开氢压机进口缓冲罐前截止阀,全开氢压机卸载阀。
2.2.7 开氢压机主电机,待氢压机空载运转3分钟后,辅助油泵自动停止并调节好油压和油量。
2.2.8 缓慢关闭氢压机卸载阀,待出口压力达到1.5MPa时缓慢打开氢压机出口阀向后工序送气。
2.2.9 联系HCL吸收岗位HCL吸收岗位送气。
2.2.10 全面检查所有压力温度在正常指标范围内,氢压机运转正常无异响,做好氢压机开车纪录。
新氢压缩机开停机步骤

一、新氢压缩机开机A级操作框架图初始状态S0新氢压缩机机处于空气状态、隔离,机、电、仪及辅助系统准备就绪1 压缩机氮气置换1.1 氮气置换状态S1压缩机氮气置换完毕2 压缩机启动前的准备2.1 投用润滑油系统2.2 投注油系统2.3 投机组冷却系统2.4 投用排放系统2.5 机组盘车状态S2压缩机启动准备工作完毕2.6 压缩机引入工艺介质状态S3压缩机引入工艺介质完毕3 启动新氢压缩机3.1 启动前检查3.2 投用自保联锁3.3 启动新氢机最终状态FS新氢压缩机启动完毕,处于稳定工作状态B级开机操作状态确认:(M)—确认压缩机试车完毕(P)—确认机体及周围卫生清洁(P)—确认机组及辅机所有连接螺栓已紧固<P>—确认消防设施完备<P>—确认机组所属所有安全阀经校验后已投用(P)—确认润滑油化验分析合格(P)—确认稀油站液位为2/3油位(P)—确认注油器油箱液位正常(P)—确认所有电器设备已送电(P)—确认电机空间加热器已经扳至自动位置(I)—确认自保系统试验合格(I)—确认与ESD、DCS系统相连接仪表联校完好(P)—确认机组机体接筒去D305的排油阀门已开1 压缩机氮气置换1.1 氮气置换[P]—翻通氮气管线上的盲板[P]—打开氮气阀,向机体充压,压力为管网低压氮气压力[P]—打开机体放空阀泄压[P]—重复氮气充压,泄压操作至合格(P)—确认放空阀关闭(P)—确认机体内压力大于零(表压)(P)—确认N2阀关闭[P]—氮气管线加盲板状态S1压缩机氮气置换完毕2 压缩机启动前的准备2.1 投用润滑油系统(P)—确认润滑油路流程正确[P]—将油站过滤器的手柄扳至指向一侧的过滤器,并锁紧[P]—投用油冷器(冬季或油温低时可暂时不开冷却水)(P)—确认油温正常[P]—转动主辅油泵泵轴数转(P)—确认主辅油泵泵轴无卡涩[P]—启动润滑油主泵(I)—确认润滑油压力(0.3~0.4)MPa[I]—做润滑油联锁试验[P]—将辅泵投入自动状态[P]—将油箱电加热器投入自动状态(P)—确认润滑油点回油正常(P)—确认过滤器压差正常2.2 投注油系统[P]—将电加热器投入自动状态(P)—确认油温正常[P]—启动注油器电机[P]—观察各润滑点来油情况(P)—确认各润滑点来油畅通2.3 投机组冷却系统(P)—确认冷却系统流程正确(P)—确认软化水箱液位正常,水位在70%左右(技改为除氧水时有水箱液位)[P]—将水站上的板式冷却器的阀门打开(改为除氧水时,循环水给除氧水降温的换热器)[P]—将投用的冷却器的冷却水阀门打开[P]—打开水站供机组软水阀门[P]—打开水站水泵的出入口阀门,打开排气阀门,灌泵排气[P]—打开运转水泵出口阀门,调整出口压力在范围之内[P]—打开电机上下水阀门,投用电机冷却水,观察视镜回水正常[P]—投用气缸冷却水,观察视镜回水正常,温度表指示正常(P)—确认各冷却点畅通2.4 投用排放系统(P)—确认排放系统的阀门是否打开[P]—投用填料密封N2保护(P)—确认仪表架上压力为管网来的低压氮气压力(P)—确认填料排放流程正确、畅通2.5 机组盘车[P]—投用盘车器(P)—确认减速机的油位在1/2~2/3位置(P)—确认盘车均匀灵活、无异常响动(P)—确认盘车15分钟以上[P]—脱离盘车器(P)—确认ESD有回讯2.6 压缩机引入工艺介质[P]—打开机体放空排火炬阀[P]—打开压缩机入口一、二道阀[P]—置换机组系统20分钟[P]—关闭放空阀(P)—确认机体内压力(0.9~1.0)MPa(表压)[P]—级间分液罐、级间冷却器、各级缓冲罐脱液、置换[P]—关闭入口阀门(P)—确认各处安全阀投用正常,机体无泄漏3 启动新氢压缩机3.1 启动前检查(I)—确认电机定子温度正常(I)—确认气路画面各点指示正常[I]—请示生产调度并获批准3.2 投用自保联锁(I)—确认无停机信号[I]—按ESD复位按钮(I)—确认开机条件满足状态S2压缩机启动准备工作完毕(I)—确认达到启动条件3.3 启动新氢机[M]—请示调度并得到开机命令(P)—确认仪表风压力正常,来气阀打开,确认回路全开[P]—按动主电机启动电钮(P)—确认空载电流正常(P)—检查机组各运转部位无异常[P]—缓慢打开入口阀门(P)—确认吸排气阀工作正常(I)—确认油压正常(0.3MPa为宜)[P]—开三级出口阀门、关三回一阀门(I)—确认各级入口压力正常,三级出口单向阀严密[P]—缓慢关三回一阀门(P)—确认带负荷后电流正常(P)—确认机组各运转部位无异常[P]—全关三回一阀门注意:启动新氢压缩机时,主控将FV4020、FV4021保持开度,PV4013开至50%。
氢氮气压缩机操作规程

氢氮气压缩机操作规程一.压缩岗位的任务压缩工段的任务就是将合格的甲烷化气经过压缩机逐级加压,逐级冷却分离油水,最终压缩到20—26Mpa,送到合成系统反应合成为氨。
压缩机在整个合成氨生产过程中,占有极其重要的地位。
压缩机生产能力的发挥及其工作的好坏,是决定产量,动力消耗的主要因素之一。
提高压缩机的生产能力,保证压缩机稳定、安全、长期运行,对安全生产,节能降耗,提高经济效益有着重要意义。
二、压缩岗位的职责1、严格执行操作规程。
2、全面负责压缩工序各设备运行状况以及工艺参数的监控和调节,按时做好各项记录。
3、负责压缩工序的平稳操作,现场加强设备运行状态监护,及时发现处理异常情况并汇报。
4、做好现场设备维护,定置定位和清洁卫生。
5、定时进行现场巡检。
6、服从班长的领导,协助班长做好本职工作,完成车间交给的各项任务。
7、对自己的工作失误负责。
8、各岗位加强安全学习,提高安全意识,保证本岗位安全平稳运行。
三、压缩机的工作原理及结构1、工作原理:活塞式压缩机由曲柄连杆机构将驱动机的回转运动变为活塞的往复运动,气缸和活塞共同组成压缩容积。
活塞在气缸内作往复运动,压缩容积发生周期性变化,使气体在气缸内完成进气、压缩、排出三过程从而达到提高气体压力之目的。
它是通过压缩机进、排气阀来控制气体进入和排出气缸。
活塞在气缸内分单作用和双作用。
所谓单作用是指活塞往复一次,只吸一次气和排一次气,作一次功。
双作用是指活塞往复一次,吸二次气和排二次气,作二次功2、结构:压缩机由主机和辅机组成。
压缩机主机由机身、曲轴、连杆、十字头、中体、气缸组件、活塞组件、填料组件、气阀组件等组成压缩机的辅机:压缩机的辅机主要包括电机、电器仪表、各级缓冲器、冷却器、分离器、稀油站、安全阀及管路、管件。
四、压缩机技术参数4M40-27.3/18.5~260型氮氢气压缩机五、压缩机工艺流程1、气路流程由造气工段送来的甲烷化气(主要成分为H2、N2)。
氢气压机操作规程

氢气压缩机操作规程一、开车前的准备工作1、检查现场是否清扫干净,检查消防.防护器材,报告记录本是否齐全好用。
2、检查所属设备,管道是否完整,各安全装置阀门,是否灵活好用。
3、联系仪表工检查各仪表根部阀是否打开,信号指示是否正确。
4、联系电工检查各电器,是否处于良好备用状态。
5、检查应开应关阀门(1)应开阀门:五回一阀,1—4段缸出口水冷却器进出口阀门,1—5缸套冷却水进出口阀,五段安全阀根部阀,油泵油冷却器冷却水进出口阀,五段出口管线放空阀。
(2)应关阀门:一段进口双阀,五段出口双阀,1—4段缸出口水冷却器排水阀,五段出口放空阀。
6、检查油泵油位,油液位处在油标的1/2—2/3属于正常。
7、检查马达接线是否可靠,盘车几圈无卡涩现象。
二、氮气置换1、关氢压机一段进口阀(第一道开第二道关)关五段出口阀,1—4段出口水冷器排水阀,关五回一阀。
2、开氮气进口阀冲压至0.3MPa置换三次放空后(从五段放空)至常压,气体经分析合格后关氮气进口阀,脱开氮气皮管。
关放空阀。
三、正常开车1、通知主控准备开车。
2、联系电工送电:1.氢压机送电,油泵.风机送电2.循环水泵送电。
3、开循环水泵,冷却水打循环(注意水泵出口水压~0.06MPa)。
4、按油泵按钮,开启油泵(注意油泵压力~0.4MPa)。
5、开一段进口双阀,变频旋转按钮箭头转向就地,按氢压机变频调节频率,频率开至现场数显20%(DCS显示10HZ)以上,关五回一阀,使用变频器开关逐渐慢慢加大频率。
氢压机逐段加压至(一段≤0.7MPa,二段压力≤2.8MPa,三段压力≤8.6MPa,四段压力≤16.4MPa,五段压力≤30MPa)当氢压机五段压力增至与系统压力接近或稍微≥系统压力时.全开五段出口双阀,氢压机并入系统。
6、全面检查一遍,看氢压机是否运转正常(震动、泄漏、进出口温度等)。
7、当氢压机开车成功后联系主控,变频旋转按钮箭头转向远程。
交给主控控制操作。
四、正常停车1、通知主控准备停车。
- 1、下载文档前请自行甄别文档内容的完整性,平台不提供额外的编辑、内容补充、找答案等附加服务。
- 2、"仅部分预览"的文档,不可在线预览部分如存在完整性等问题,可反馈申请退款(可完整预览的文档不适用该条件!)。
- 3、如文档侵犯您的权益,请联系客服反馈,我们会尽快为您处理(人工客服工作时间:9:00-18:30)。
氢氮压缩机开停车操作(本开停车方案适用于三出1.7MPa碳丙脱碳生产合成氨公司的HN压缩机,每段回一阀和放空阀为一个阀门,出口至收集总管,然后通过回一入总阀、回气柜总阀、总放阀按要求操作。
)1.开停车方案1.1正常开车步骤:1.1.1准备工作:1.1.1.1全面检查各设备管道、阀门、电器、仪表是否正常完好。
1.1.1.2检查稀油站及高压注油器油位是否正常。
1.1.1.3检查排净各分离器之积水。
1.1.1.4打开上水总阀,确保各水路畅通,水量正常。
1.1.1.5检查应开关的阀门正确:应开阀门:一入阀、一回一阀、二回一阀、三回一阀、四回一阀、五回一阀、六回一阀、总回一入阀(或回气柜阀)、各段排油阀、油回阀、压力表考克阀、上水阀;应关的阀门:二出阀、三入阀、三出阀、四入阀、五出阀、六入阀、六出阀、2-3阀、3-4阀、5-6阀、总放阀、油放阀。
1.1.2开车:1.1.2.1启动注油器,确保各部注油正常,启动滑环风机,启动循环油泵,使循环油压保持在0.18-0.35MPa之间,检查各段天窗部位是否正常注油。
1.1.2.2启动盘车电机(若电动盘车坏应人力盘车),将盘车手柄置于盘车位置(正、反均可),盘车二至三圈后,将盘车手柄置于开车位置,停盘车电机。
1.1.2.3联系脱硫、变换、脱碳、精炼、合成等有关岗位,并发出开车信号。
1.1.2.4联系电工到场,待允许合闸灯亮后,启动主机,检查电流、电机是否正常,同时逐步关闭各段油水阀。
1.1.2.5微开三入阀、四入阀、六入阀,以进口不抽负为准,平衡压缩机各段。
1.1.2.6关严一回一阀,关小二回一阀,待二出压力等于总管压力时,开二出阀,向变换送气,然后关严二回一阀。
1.1.2.7缓开三入阀,关小三回一阀,待三出压力等于总管压力时,开三出阀,向脱碳送气,然后关严三回一阀,开大三入阀。
1.1.2.8缓开四入阀,关严四回一阀,关小五回一阀,待五出压力等于总管压力时,开五出阀,向精炼送气,然后关严五回一阀,开大四入阀。
1.1.2.9缓开六入阀,关小六回一阀,待六出压力等于总管压力时,开六出阀,向合成送气,然后关严六回一阀,开大六入阀。
1.1.2.10系统送气后,再仔细检查确认应开关的阀门是否正确到位,全面巡检设备运行是否正常。
1.1.3注意事项:1.1.3.1准备工作要仔细,不准带压盘车、开车。
1.1.3.2各段加压,系统送气要缓慢开关阀门。
1.1.3.3时刻关注各压力变化,严禁超压。
1.2正常停车步骤:1.2.1联系有关岗位发出停车信号,并检查打开回气柜阀。
1.2.2关小六入阀以五出不超压为原则,然后缓开六回一阀,关六出阀,关注六段压力及回一总管压力,严禁超压;关严六出阀,切断合成送气。
1.2.3关小四入阀以三出不超压为原则,然后缓开五回一阀,关五出阀,关注五段压力及回一总管压力,严禁超压;关严五出阀,切断精炼送气,同时关六入阀以六入不抽负为标准,保证精炼压力稳定。
1.2.4关小三入阀以二出不超压为原则,然后缓开三回一阀,关三出阀,关注三段压力及回一总管压力,严禁超压;关严三出阀,切断脱碳送气,同时关四入阀以四入不抽负为标准,保证脱碳压力稳定。
1.2.5缓开二回一阀,关二出阀,关注二段压力及回一总管压力,严禁超压;关严二出阀,切断变换送气,同时关三入阀以三入不抽负为标准,保证变换压力稳定。
1.2.6打开各油水排污阀,开大各回一阀,卸压、停车,同时停循环油泵及注油器。
1.2.7根据要求,关上水总阀,交出检修,或按工艺要求使设备处于备用状况。
1.2.8注意事项:不准带压停车;卸压时,回路阀特别是高压端要缓慢,减少回气量,严禁猛开;全过程严防超压、抽负。
1.3紧急停车步骤:1.3.1下列情况下应作紧急停车处理:1.3.1.1断水、断电、油路故障,断气或自动跳闸;1.3.1.2主要机件损坏;1.3.1.3着火、爆炸事故;1.3.1.4严重电气故障;1.3.1.5外工段打来紧停信号铃;1.3.1.6严重抽负、带液;1.3.1.7毒害气体大量外漏;1.3.1.8油压异常高、低,无法调节。
1.3.2紧停步骤:1.3.2.1关主机停机按钮,停止主机运行。
同时对外发出紧急停车信号,并迅速通知有关岗位。
1.3.2.2切断系统送气,依次关六出、六入、五出、四入、三出、三入、二出阀。
1.3.2.3根据气柜、汞柱合理使用回一入、回气柜及总放空阀。
1.3.2.4依次缓开六至一段回一阀卸压,严防回一总管压力超过0.3MPa以上,卸压前定时打开油水排放阀。
1.3.2.5卸压后停循环油泵及注油器,同时详细检查,使设备处于正常停机状况。
1.3.3紧急停车注意事项:1.3.3.1严禁慌乱,保持冷静,做到心中有数。
1.3. 3.2确认切断系统后再卸压,卸压时一定要缓慢进行。
1.3.3.3卸压时,密切关注气柜、汞柱指示变化,确保不抽负、不超压。
1.4合成切导操作步骤·接切导通知后,通知相关岗位,脱硫减汞柱(必要时停机)。
·关小六入阀以五出不超压为原则,然后缓开六回一阀放回气柜(多台放空),关六出阀,关注六段压力20MPa≤P≤30MPa及回一总管压力≤0.3MPa,严禁超压;关严六出阀,切断合成送气。
·合成正常,接通知,关六回一,开六出向合成送气;开大六入阀,再根据情况加量。
1.5精炼切导操作步骤·接切导通知后,通知相关岗位减量,脱硫减汞柱(必要时停机)。
·关小六入阀以五出不超压为原则,然后缓开六回一阀放回气柜(多台放空),关六出阀,关注六段压力20MPa≤P≤30MPa及回一总管压力≤0.3MPa,严禁超压;关严六出阀,切断合成送气。
·关小四入阀以三出不超压为原则,然后缓开五回一阀,关五出阀,关注五出压力8MPa≤P≤12MPa及回一总管压力≤0.3MPa,严禁超压;关严五出阀,切断精炼送气,同时关六入阀以六入不抽负为标准,保证精炼压力稳定。
·微量合格后,只切六段气的压缩机接通知关六回一,开六出向合成送气,开大六入阀;切五六段气的压缩机接通知关五回一,开五出向精炼送气,同时稍开六入阀,控制六回一阀,保持精炼压力稳定;再根据精炼情况关六回一,开六出向合成送气。
2.大修停开车方案2.1大修停车2.1.1根据大修停车总方案,听从调度指挥,逐渐减低生产负荷,并按正常停车步骤逐步停机。
2.1.2所有压缩机全部停止运转后,根据调度指令,利用氢氮气压缩机三入、四入、六入等阀门将三入总管,四入总管、六入总管卸压。
2.2大修停车置换方案2.2.1一入总管置换和机身置换:·脱硫送惰气(合格吹风气),静压置换压缩机一入总管;开一入阀、回一入总阀,通过总放放空,并取样分析CO+H2≤8%,O2≤1.0%。
·置换合格后,进行各压缩机系统内惰气静压置换,各压缩机盘车顺流程置换十分钟以上;应开阀:一入、回一入总阀、二-三、三-四、五-六、各段回一阀、各段排污阀、排污放空总阀,应关阀:二出、三入、三出、四入、五出、六入、六出、回气柜总阀、总放、排污回收阀。
·脱硫空气置换合格后送空气至本系统,进行各压缩机系统内空气静压置换,各压缩机盘车顺流程置换十分钟以上,应开阀:一入、回一入总阀、二-三、三-四、五-六、各段回一阀、各段排污阀、排污放空总阀,应关阀:二出、三入、三出、四入、五出、六入、六出、回气柜总阀、总放、排污回收阀。
(根据具体方案要求,启动各氢氮气压缩机打空气顺流程置换,用六放,总放进行放空)。
2.2.2二出三入总管置换:·在压缩机置换过程中,开二出阀,在变换工段放空对二出总管置换。
·在压缩机置换过程中,开启压缩机三入大阀,倒流程对变脱和三入总管进行置换,在变脱系统出口放空。
2.2.3三出四入总管置换:·在压缩机置换过程中,开三出大阀,对三出总管进行置换,在脱碳岗位进行放空。
·在压缩机置换过程中,开四入大阀,倒流程对四入总管进行置换,在脱碳系统出口放空。
2.2.4五出总管、六入总管、六出总管:根据大修需要或调令进行置换。
2.2.5所有氢氮气压缩机单机内及各总管用空气置换合格后,方可进行检修。
2.2.6置换期间严禁各类动火作业,同时防中毒。
2.3大修开车方案2.3.1根据大修后开车指令,联系循环水岗位送水,保证压缩机开车需要的冷却水用水量。
2.3.2一入总管置换和机身置换:·脱硫送惰气(合格吹风气),静压置换压缩机一入总管;开一入阀、回一入总阀,通过总放放空,并取样分析CO+H2≤8%,O2≤1.0%。
·置换合格后,进行各压缩机系统内惰气静压置换,各压缩机盘车顺流程置换十分钟以上;应开阀:一入、回一入总阀、二-三、三-四、五-六、各段回一阀、各段排污阀、排污放空总阀,应关阀:二出、三入、三出、四入、五出、六入、六出、回气柜总阀、总放、排污回收阀。
2.3.3各单机置换合格后,根据指令启压缩机运行向外工段送气置换开车。
2.3.4煤气开车2.3.4.1准备工作·全面检查各设备管道、阀门、电器、仪表是否正常完好。
·检查稀油站及高压注油器油位是否正常。
·检查排净各分离器之积水。
·打开上水总阀,确保各水路畅通,水量正常。
·检查应开关的阀门正确:应开阀门:一入阀、一回一阀、二回一阀、三回一阀、四回一阀、五回一阀、六回一阀、总回一入阀(或回气柜阀)、二-三阀、三-四阀、五-六阀、各段排油阀、油回阀、压力表考克阀、上水阀;应关的阀门:二出阀、三入阀、三出阀、四入阀、五出阀、六入阀、六出阀、总放阀、油放阀。
2.3.4.2开车·启动注油器,确保各部注油正常,启动滑环风机,启动循环油泵,使循环油压保持在0.18-0.35MPa之间,检查各段天窗部位是否正常注油。
·启动盘车电机(若电动盘车坏应人力盘车),将盘车手柄置于盘车位置(正、反均可),盘车二至三圈后,将盘车手柄置于开车位置,停盘车电机。
·联系脱硫、变换、脱碳、精炼、合成等有关岗位,并发出开车信号。
·联系电工到场,待允许合闸灯亮后,启动主机,检查电流、电机是否正常,同时逐步关闭各段油水阀。
·关严一回一阀、关小二回一阀,开二出阀,向变换送气充压,然后关严二回一阀、关小二-三阀,平衡压缩机后段。
(根据变换升温方案可采取循环升温,开三入阀、三回一阀、回气柜阀,关二-三阀)·变换制气合格后,缓开三入阀,关二-三阀,关小三回一阀,开三出阀,向脱碳送气充压,然后关严三回一阀,关小三-四阀,平衡压缩机后段。
(根据脱碳制气方案可采取循环制气,开四入阀、四回一阀、五回一阀、回气柜阀,关三-四阀)·脱碳净化气合格后,缓开四入阀,关三-四阀,关严四回一阀,关小五回一阀,开五出阀,向精炼送气充压,然后关严五回一阀,关小五-六阀,平衡压缩机后段。