PPAP 检验报告
PPAP中英文报告模板-4.尺寸检验报告

MIL-105D, SINGL源自 NORMAL, LEVEL II, CRITICAL: 0.01 MAJ: 1.0 MIN:2.5 按正常抽样一般水平II进行抽样,严重缺陷:0.01 主要缺陷:1.0 次要缺陷:2.5 Dimensions 尺寸 Inspection Results 检验结果 Maximum 最大尺寸 Method 检验方法 No.1 No.2 No.3 No.4 No.5 No.6 No.7 No.8 No.9 No.10 Comments 评论
Item 序号 1 2 3 4 5 6 7 8 9 10 11 12 13 14 15 16 17 18 19 20 21 22 23 24 25 26 27 28 29 30 31
SPEC 尺寸规格
Minimum 最小尺寸
Hardness硬度 Surface表面 Packing包装 职责 Title 邮箱 Email 日期 Date 1900/1/0
检测 Inspected by
客户验证 Verified by Customer 评估 Evaluated by Approved 批准 备注 Remarks 职责 Title Failed 拒收 邮箱 Email Approved with deviation 有条件接受 日期 Date Resubmit 重新送样
Dimension Inspection Report 尺寸 检 验 报 告
Part name. 产品名称 Part No. 产品图号 Drawing Rev. 图纸版本号 AQL Description. 产品描述 Material. 材 质 Drawing Date. 图纸日期 Po No. 订单号 Sample Qty. 样品数量 Inspection date. 检验日期 Supplier Name. 供应商名称
ppap报告
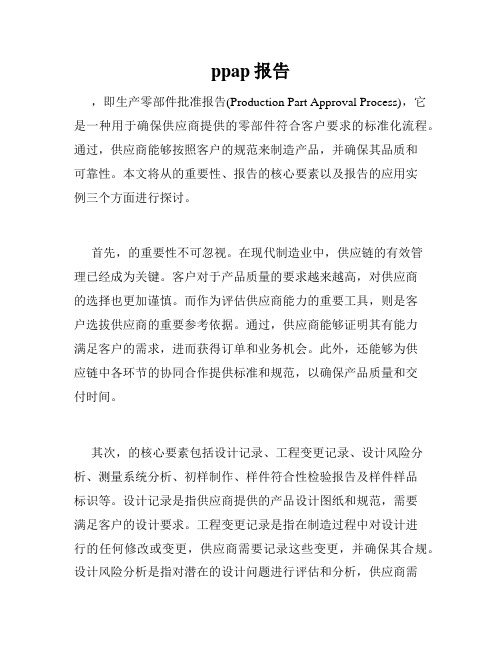
ppap报告,即生产零部件批准报告(Production Part Approval Process),它是一种用于确保供应商提供的零部件符合客户要求的标准化流程。
通过,供应商能够按照客户的规范来制造产品,并确保其品质和可靠性。
本文将从的重要性、报告的核心要素以及报告的应用实例三个方面进行探讨。
首先,的重要性不可忽视。
在现代制造业中,供应链的有效管理已经成为关键。
客户对于产品质量的要求越来越高,对供应商的选择也更加谨慎。
而作为评估供应商能力的重要工具,则是客户选拔供应商的重要参考依据。
通过,供应商能够证明其有能力满足客户的需求,进而获得订单和业务机会。
此外,还能够为供应链中各环节的协同合作提供标准和规范,以确保产品质量和交付时间。
其次,的核心要素包括设计记录、工程变更记录、设计风险分析、测量系统分析、初样制作、样件符合性检验报告及样件样品标识等。
设计记录是指供应商提供的产品设计图纸和规范,需要满足客户的设计要求。
工程变更记录是指在制造过程中对设计进行的任何修改或变更,供应商需要记录这些变更,并确保其合规。
设计风险分析是指对潜在的设计问题进行评估和分析,供应商需要识别并降低这些风险。
测量系统分析是指对用于测量的设备和工具进行评估,以确保测量结果准确可靠。
初样制作是指供应商按照客户的要求制作出第一批样品,并交付给客户进行评估和确认。
样件符合性检验报告是指供应商对样品进行全面的检验和测量,确保其符合设计要求。
最后,样件样品标识是为了标识样品的唯一性和追踪性。
最后,我们来看一下的应用实例。
以汽车行业为例,汽车制造商通常会与多家供应商合作,以满足复杂的供应链。
这些供应商可能分别负责汽车的发动机、座椅、悬挂系统等部件的制造。
在这种情况下,汽车制造商需要对每个供应商的能力进行评估和验证。
于是,就成为了汽车制造商与供应商之间的重要沟通工具。
供应商通过提交,证明其产品可以满足汽车制造商的质量和性能需求。
同时,汽车制造商根据的内容,对供应商的能力和合作意愿进行综合评估,以决定是否选择该供应商。
PPAP检查清单

PPAP 检查清单
供应商名称 : 产品名称 提交PPAP的样品数量 : 供应商承诺PPAP日期:
序号 PPAP 文件种类 零件提交保证书 产品工程批准的技术规范 产品工程批准的工程更改清单(如果有) 产品批准样品(如适用) 初始、生产过程流程图(工位编号与FMEA和控制计划一致) 过程失效模式和后果分析/FMEA 样件、试生产、生产控制计划. 材料/外协/D特性分供方清单(如适用) 材料/外协/D特性检验报告、第三方验证报告(如适用)
项目名称 :
通用K216
产品图号及PDM代码 : P00057552/P00057850 PPAP的提交等级 :3级 PPAP 实际提交日期:
递交 无要求 递交 备注
1 2 3 4 5 6 7 8 9
√ √ √ √ √ √ √ √ √ √ √ √ √ √ √ √ √ √ √ √ √ √
审核:ห้องสมุดไป่ตู้
10 首件、首批检验报告(外观、全尺寸、性能) 11 外观批准报告(如适用) 12 性能测试第三方验证报告 13 操作/检验人员配置/顶岗清单 14 生产设备/辅助设备清单 15 工装/模具、夹具清单 16 检测设备/检具清单(如果有) 17 初始过程能力/SPC 18 测量系统分析/MSA 19 场地平面布置图 20 包装规范 21 产品试生产过程改进项目(计划、责任部门/人、期限) 22 顾客的特殊要求 编制:
五大工具手册APQP、PPAP、SPC、MSA、FMEA
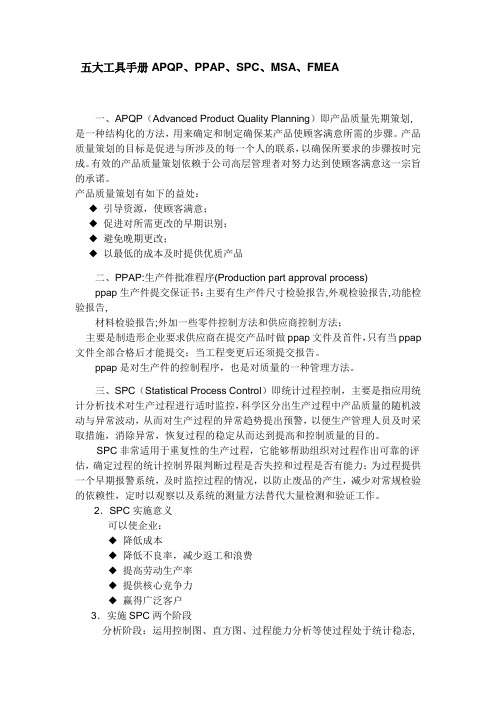
五大工具手册APQP、PPAP、SPC、MSA、FMEA一、APQP(Advanced Product Quality Planning)即产品质量先期策划,是一种结构化的方法,用来确定和制定确保某产品使顾客满意所需的步骤。
产品质量策划的目标是促进与所涉及的每一个人的联系,以确保所要求的步骤按时完成。
有效的产品质量策划依赖于公司高层管理者对努力达到使顾客满意这一宗旨的承诺。
产品质量策划有如下的益处:◆引导资源,使顾客满意;◆促进对所需更改的早期识别;◆避免晚期更改;◆以最低的成本及时提供优质产品二、PPAP:生产件批准程序(Production part approval process)ppap生产件提交保证书:主要有生产件尺寸检验报告,外观检验报告,功能检验报告,材料检验报告;外加一些零件控制方法和供应商控制方法;主要是制造形企业要求供应商在提交产品时做ppap文件及首件,只有当ppap 文件全部合格后才能提交;当工程变更后还须提交报告。
ppap是对生产件的控制程序,也是对质量的一种管理方法。
三、SPC(Statistical Process Control)即统计过程控制,主要是指应用统计分析技术对生产过程进行适时监控,科学区分出生产过程中产品质量的随机波动与异常波动,从而对生产过程的异常趋势提出预警,以便生产管理人员及时采取措施,消除异常,恢复过程的稳定从而达到提高和控制质量的目的。
SPC非常适用于重复性的生产过程,它能够帮助组织对过程作出可靠的评估,确定过程的统计控制界限判断过程是否失控和过程是否有能力;为过程提供一个早期报警系统,及时监控过程的情况,以防止废品的产生,减少对常规检验的依赖性,定时以观察以及系统的测量方法替代大量检测和验证工作。
2.SPC实施意义可以使企业:◆降低成本◆降低不良率,减少返工和浪费◆提高劳动生产率◆提供核心竞争力◆赢得广泛客户3.实施SPC两个阶段分析阶段:运用控制图、直方图、过程能力分析等使过程处于统计稳态,使过程能力足够。
PPAP填写说明(提交给伟创力的PPAP如何填写)

2. Shifted mold:
Supplier provides the samples and FAI/PPAP report to Flex ASQE;
中文解释 图纸编号 零件名称。 版本编号参见flex 图纸 提交文件编号 模号或穴号 材质或材料规格 检验者 检验日期,月/日/年 格式 审核者 填写测量实际数据 关键尺寸
12
PPAP Instruction
Sheet C : CPK(制程能力指数)
注意:
1.至少32pcs样品实际测量值!! 2.CPK值须≥1.5,CP值须≥2.0!!
Reviewed By: PPAP提交之前的审核人。 Supplier Comments: 供应商注释或建议 Submission Reason 提交原因(只能填选一种)
Initial Submission 首次提交 Engineering Change(s) 工程变更
Tooling: Transfer, Replacement, 模具搬迁更换,翻新等
Sheet B: FAI (首件样本尺寸检查)
注意: 1. FAI中的Location要求必须对应图纸中所有尺寸所处位置填写, 例如: D5, A2, C3……; 2. FAI中CTF尺寸是指图纸中的重点管控尺寸(即Cpk尺寸), 若图纸要求是Cpk尺寸 的就必须选择Yes, 否则不需要填写. 因此有CTF尺寸的就必须做CPK与GR&R分析. 3. 在FAI sheet 输入正负公差时不需要加上正负号, 否则后面的公式无效. 4.
ppap报告

ppap报告PPAP 报告简介PPAP 报告全名为 Production Part Approval Process(生产零件批准流程),是由美国汽车工业 Action Group(AIAG)所制订和推广的一种产品质量保证流程。
该流程的目的是确保供应商生产的零件能够满足客户的需求和要求,并确保零件的质量稳定。
PPAP 报告通常由供应商提交给顾客,以证明其产品符合顾客的要求和要求。
该报告通常包括以下部分:1. 质量文件质量文件包括供应商的质量控制体系文件、控制计划、流程流程图、FMEA(失效模式和影响分析)、MSA(测量系统分析)以及各种检验报告等。
2. 样品报告样品报告包括生产的样品部件的数据、外观检查、功能测试、物理和材料测试等。
3. 测量系统分析测量系统分析是针对测量系统进行的分析,以确保其准确性和稳定性。
4. 样品批准在提交样品报告之后,应该获得客户的批准才能进行量产。
PPAP 报告要旨PPAP 报告包括以下几个要点:1. 确定顾客的要求和要求在整个生产零件的过程中,应该与客户保持良好的沟通,并确保了解其要求和要求。
2. 实施和监控过程控制制定并实施有关生产流程的规定以及对生产过程的监控,包括进行统计过程控制,以确保零件质量的稳定性。
3. 有关测量和检验的要求详细列出指标和程序,并规定测量和检验的方法。
4. 确定问题解决的程序应该建立问题解决过程,以确保及时、全面地识别、跟踪和消除问题。
5. 根据质量标准进行认证进行认证以确保供应商的质量控制体系和生产零件的合规性。
PPAP 报告的意义根据 PPAP 报告规范进行质量管理,可以帮助企业更好地了解顾客需求、加强过程控制、提高产品质量并规避风险。
作为制造企业,能够正确理解和掌握PPAP 报告的规定和实施,才能适应如今市场现实和产品质量要求的不断提高,才能不断提高产品和服务质量,在激烈的市场竞争中获得成功。
结论PPAP 报告是美国汽车工业标准,对于提高产品和服务质量具有重要意义。
PPAP资料审核常见问题一览

PPAP资料审核常见问题一览相信各位SQE在审核PPAP资料时,都遇见过各种各样奇葩的错误,本文总结了以下常见的问题以供参考。
零件提交保证书(PSW):▪必须使用正确的版本(其他主机厂的PSW表格是不能接受的)▪必须完整填写所能填写的内容(供应商常忽略重量、 xxx产品图纸)▪版本号正确▪提交等级正确▪详细填写试生产日期,生产率,生产数量零件检验计划、检验报告、材料代用申请单及材料检验报告:▪零件检验计划应包含灯笼图(可另附带灯笼标记的图纸)▪零件检验计划与检验报告对比图纸有漏项,还有项目、顺序不对应。
▪材料代用申请单没有PE签字▪尺寸和材料检验报告为打印版,无人签字且没有附原始报告。
▪部分尺寸没有公差。
一定要有,以未注公差/通过形位公差换算/过程控制公差等方式确定。
▪检测方法不可操作特殊特性清单KPC:▪未能识别图纸要求的特殊特性或内容/要求不符合图纸;▪供应商自己识别的特殊特性未填入KPC清单中(如地方法律法规要求、企业标准和产品验收标准)过程流程图:▪如有自制件,仅放入总成装配过程流程图,是不够的;同时需要放入自制件的过程流程图。
▪过程流程图,应仅体现“过程流程”即可,不需要体现具体控制特性/控制方法/频率等主要由控制计划体现的内容。
▪流程图不包括返工和报废, PCPA审核中此项有要求。
PFMEA:▪文件只有一人编写,没有PFMEA团队,没有签署发布,表头填写不全或不正确▪自制件没有提供PFMEA。
▪PFMEA的评分定义不正确,如定义为特殊特性项目,但其严重度低于5-8且频度低于4-10▪改进项已实施却没有将措施更新到现行控制方法中。
▪有些失效模式原因/措施,并非真正的失效模式/原因/措施,还有一些PFMEA明显能看出敷衍。
▪与过程流程图不符,序号未与过程流程图对应,有意无意漏掉项目而未进行识别。
▪确保所有高RPN的项目均有改进/预防措施,确保高RPN的项目的改善行动在控制计划中体现控制计划PCP:▪文件只有一人编写,没有控制计划编制团队,没有签署发布表头填写不全或不正确。
PPAP检查表

结果
PPAP Checklist / PPAP 检查内容清单
No. 序号
PPAP Element PPAP 文件内容
第三方材料告 10
检查内容 尺寸报告是否有检测人员的签字、检测日期? 试验机构是否是客户认可的、或者是权威机构认可的实验室?
10 供应商原材料质保书
执行的标准号及版本号是否与图纸/试验大纲相一致? 是否提交了所有分零件的原材料质保书?
PPAP Checklist / PPAP 检查内容清单
No.
PPAP Element
序号
PPAP 文件内容
1 客户正式发放的图纸
检查内容 顾客的图纸及客户发放的图纸复印件是否包括在提交的文件中?
特殊特性是否在图纸中标明?
2 工程更改文件(如果有)
图纸的版本是否为最新状态? 是否有授权的工程更改,该工程更改已发生在零件上,但还未在设计记录反映出来?
检查内容
外观认可报告是否按照要求格式进行填写(如有客户格式,按客户格式填写)? 是否有颜色、皮纹、光泽的标准样块? 表面纹理加工的供应商是否经过认可(若有此要求)? 是否有客户工程师确认的认可样件? 是否提交全尺寸测量的样件?(提交的PPAP样品与全尺寸测量的样品一一对应,并编号) 每个/箱样件上是否悬挂/粘贴了客户规定的样品标识? 样品代号与尺寸检验报告相对应。 是否提交了每一付模具的每一个模腔的产品,并保留了每一模具、模腔的样件? 是否有客户认可签字 是否包括检具清单? 是否包含客户特殊要求且满足? 客户批准的偏差申请 分供方清单是否获得采购的批准? 分供方清单中是否包含贸易商?(必须体现原材料的生产方) PSW是否已经获得签字批准 签字盖章 针对每道工序都提交了产能分析么? 潜在产能百分比是否>120% ? 表格是否填写完整?