湿法回转窑尾气余热利用的探讨
汽车尾气余热再利用技术探讨及应用

散发。 燃料燃烧的总热量大体由转变为有效功的热量
,
1 新 的汽车尾气余热再利用技术介绍
1 . 1 尾 气余 热再 利用原 理
它热 量损 失
废气带走的热量 Q T , 冷却介质带走 的热量 , 其 四部 分 组成 。在全 负荷 工 况下 , 发 动
表 1 汽 柴 油机 发 动 机 热 平 衡 表
价值 。
关键词 : 尾气余热 热 交 换器 节油 除霜 制 暖
Di s c us s i o n an d a p pl i c at i o n o f a ut o mo t i v e e xha us t g a s r e s i dua l he a t r e c y c l i n g t e c h no l og y
排放指 标偏 低 ,同时发 动机 各部 件出 , 汽 车燃 料转 化 为有效 功 只 占全 部热 量 的 3 0 %~ 4 0 %左右 ,而随着 尾气 排人
大气 中的也 占了 1 / 3 左右 , 汽车发动机尾气的温度最 高可达 6 0 0。 C ~ 7 0 0。 C ,巨大的汽车保有量意味着巨
度很高 , 而冷却介质又可能具有轻微腐蚀性 , 同时又 要 求具 有较 强热 传 导性 能 。 故 要求 排气 管及 热交 换器
媾
熊
汽车尾气余热再利用技术探讨及应用
余 云
( 保 定长 安客 车制造 有 限公 司 )
摘要 : 发动机排气管路加装热交换器是利用发动机尾气 释放 的热量对冷却介质进行再加热 、 升温 , 实现节油 、 环保 的 目的。 同 时可延长发动机使用寿命 , 提升风 窗除霜及车厢取暖效果 , 间接取得 降噪功效 。 此项改进技术在我 国寒冷区域具有 良好推广
汽车尾气余热回收利用装置探索

汽车尾气余热回收利用装置探索汽车尾气余热回收利用装置是一种用于汽车尾气热能回收和利用的装置。
在汽车运行过程中,大量的热能会以废气的形式散失掉,而这些热能的浪费不仅导致了资源的浪费,也增加了环境负荷。
开发一种高效的汽车尾气余热回收利用装置具有重要意义。
汽车尾气余热回收利用装置的主要作用是通过吸收汽车尾气中的热能,将其转化为其他形式的能源或用于车内的供暖和空调等。
目前,有多种技术和装置可以实现汽车尾气余热回收利用,如热交换器、热电联供、蓄热材料等。
热交换器是一种常用的技术,通过将汽车尾气和进气进行换热,实现能量的传递和回收。
热交换器的原理是利用热传导和对流来实现热能的转移。
具体来说,热交换器将进气通过热交换器与废气进行接触,使进气得到预热,从而提高了燃料的燃烧效率。
废气通过热交换器与进气进行换热,将部分热能转移给进气,从而达到回收废气余热能的目的。
热电联供是一种将汽车尾气中的热能转化为电能和热能供应给车辆的技术。
该技术利用热电元件将汽车尾气中的热能转化为电能,并通过电能来供应车辆的电子设备和驱动系统。
与传统的发电方式不同,热电联供技术可以实现废气热能的高效利用,从而提高了汽车的能源利用率和性能表现。
蓄热材料是一种将汽车尾气中的热能储存起来,并在需要的时候释放出来供应给车辆的技术。
蓄热材料通过吸收汽车尾气中的热能,将其转化为化学能或物理能,储存起来。
当需要利用热能时,蓄热材料可以释放出储存的热能,用于供应车辆的热能需求。
这种技术可以提高汽车尾气余热的利用效率,并减少对传统能源的依赖。
汽车尾气余热回收利用装置的研发和应用对于提高汽车能源利用效率、减少环境负荷具有重要意义。
目前,不同的技术和装置已经得到了一定的应用和研究,但仍有许多挑战需要克服,如装置的效率和稳定性等。
在未来的研究中,需要进一步探索汽车尾气余热回收利用装置的新技术和新方法,以实现更高效、更经济的汽车能源利用。
锅炉尾部烟气余热回收利用的可行性及方案研究

锅炉尾部烟气余热回收利用的可行性及方案研究摘要:锅炉尾部烟气(引风机至烟囱入口)中含有大量的热能(原烟气温度通常高达130°C ~160°C)未被充分利用而被损失掉,且该项热损失进入脱硫塔后会增大水的蒸发量。
锅炉热损失中最大的一项正是这项排烟热损失,设法减少排烟热损失可以有效地提高机组的经济性、减少电力生产过程中的水耗。
本文分析了目前常见三种锅炉尾部烟气余热回热方式,并通过对其余热回收原理和运行效果的比较得出最佳的烟气余热回收方式为加装低压省煤器,同时为某电厂600 MW机组设计加装低压省煤器,得到了良好的效果。
关键词:烟气余热回收气气换热器(GGH)省煤器低压省煤器1、绪论随着世界能源危机的日益加深,化石燃料已近乎枯竭[1]。
我国的能源又是以煤炭为主,很多电力生产的主要能量来源均是来自煤炭燃烧放出的热能。
据不完全统计,2010年我国的煤电比重占总发电量的77%[2]。
众所周知,在火力发电厂中,锅炉的排烟余热问题(暨锅炉的排烟温度高)一直是困扰着人们的一个难题。
因为仅仅锅炉的排烟温度高这一项损失所造成的能源消耗就相当可观[3][4]。
据统计,在火力发电厂中,锅炉的排烟热损失占锅炉热损失的70%~80%。
同时由于受热面污染程度随着锅炉运行时间的增加而加剧,排烟温度要比设计温度高20°C~30°C[5]。
锅炉的排烟温度过高,造成了火力发电厂煤的消耗量的增加。
而目前中国现役燃煤电厂的排烟温度普遍达到了120°C~130°C[6],对于循环流化床电厂来说,排烟温度甚至高达150°C,这也使得排烟热损失成为了锅炉各项热损失中最大的一项。
对于配备独立脱硫系统的燃煤发电机组,过高的烟气温度在脱硫时还会携带大量水汽,增加脱硫水耗。
因此锅炉排烟热能不仅是一项潜力很大的余热资源[7],而且降低后的烟气还会降低脱硫水耗,节省水资源。
现有的烟气余热回收方式有很多,如气气换热器(GGH)、改造省煤器以及加装低压省煤器。
湿法回转窑存在问题及传动系统的探讨

3 6
云 南 建 材
20 年 5 02 期
( )窑 的加 热 功 能 和 反 应 容 器 功 能 被 连 为 一 4
期短 的问题 进 行 了不懈 的努 力 ,提 出了湿 磨 干 烧 ,
窑 ,是 因为其 整 个庞 大 的窑 体 只通 过窑 中唯一 的一 个 传 动 齿 轮带 动 如 3 5 . m×1 5 的华 新 窑 只有 窑 4m
中 的一 个 传 动轮 ) ,这 种单 级 传 动 决定 了整 个 窑 体
维普资讯
20 0 2年 5期
祝李红: 湿法回 转窑存在问题及传动系统的 探讨
3 5
湿 法 回 转 窑 存 在 问 题 及 传 动 系 统 的 探 讨
祝 李红 昆明水 泥股份有 限公 司 (5 19 600 )
摘 要 : 针 对 湿 法 回 转 窑 在 熟料 生产 过 程 中 存 在 的 一 系 列 问 题 ,指 出 湿 法 回 转 窑 单 级 传 动 的 结 构 方 式 存 在 的 弊 端 ,提 出改 单 级 传 动 湿 法 回 转 窑 为 两级 传 动 的 煅 烧 方 式 的 设 想 , 以便 在 分 离 窑的 功 能 性 的 基 础 上 ,充 分 发 挥 湿 法 回 转 窑 的 加 热 和 反 应 容 器 功 能 并 实现 最 佳 配 合 , 以 达 到 大 幅 提 高湿 法 回 转 窑 的 传 热 效 率 、 产 质 量 以及 安 全 运 转 周
期 的 目的 。
关键 词 :湿 法 回 转 窑 ; 问题 ;传 动 系统
1 前 言
湿 法 水 泥 生 产 工 艺 的 存 在 已经 有 较 长 的 时 间
以 ,以上 针对 料 浆水 分 问题 采取 的一 系列 工艺 改 进 在湿 法水 泥生 产 企业 中并 没有得 到 广泛 的推 广 。 综合 来 看 ,这几 年 虽 然我们 研 究 了料 的 问题 、 窑 内辅助 设 置 的问题 、煤 的燃烧 问题 ,但 湿法 水 泥 生 产 中 ,回转 窑 低传 热 效率 ,低 台时产 量 和安 全 运 转 周 期短 的 问题 并没 有 得到 很好 的解 决 。我认 为 这 可能 是 长期 以来 我们 忽 略 了窑 本身 结构 问题 的研 究 所 至 为此 ,根据 多 年 的实践 经验 ,总结 了湿法 回转 窑 的弊端 所在 ,提 出 了改传 统单 级 传动 湿法 回转 窑 为两 级传 动 的湿 法 回转 窑 的设 想 。
湿法回转窑尾气余热利用的探讨

湿法回转窑尾气余热利用的探讨【摘要】由于湿法回转窑窑尾处排出的废气温度不高,目前针对这些废弃余热进行合理利用的研究还在探索当中。
本文介绍某氧化铝生产企业,在采用烧结法处理低品位铝土矿的生产中,利用湿法回转窑废气余热进行发电作业,初步研究效果较好。
企业将有机介质朗肯循环发电机工作原理应用于湿法窑尾气的余热利用中,在电收尘器设备的前后两端增设热交换器,对有机介质进行加热处理使其发生气化。
在一定的工作压力条件下驱动汽轮发电机组发电。
同时,将汽轮发电机排除出来的低压工作介质进行冷却处理,最后转变为液态,继续循环使用。
【关键词】余热发电湿法回转窑窑尾废气回收近年来,我国经济发展势头良好,但是各个行业在节能减排工作方面压力也在不断增大。
对回转窑窑尾余热利用技术在不断研究当中,尤其是在干法窑窑尾余热发电技术方面,有了较大突破[1]。
但是对湿法窑而言,利用窑尾余热进行发电这一技术还在深入研究。
因此,为了提高湿法窑废气余热利用效率,本文针对以烧结法工艺生产氧化铝的企业,在湿法窑余热利用方面的技术研究进行分析,结果表明,如果回转窑废气温度超过了200℃,在这样的情况下,可以利用余热锅炉(热交换器)驱动汽轮发电机组进行发电,达到了节能减排的目的,提高了企业经济效益,不断推动企业发展。
1 介绍湿法回转窑窑尾废气余热温度和流量情况某氧化铝厂熟料烧成所用设备为回转窑,回转窑废气排放量约27万m3/h,废气带走的热量大约3万kJ/h,在电收尘器设备的进口处废气余热温度为235~250℃,出口处废气温度为185~200℃。
比较理想化的收尘设备是电收尘器,电收尘器收尘效果较好,在一定时间之内能处理大量含尘废气。
对于能采用电收尘器设备进行处理的废气,其温度应该是高于露点温度值[2]。
所以,在进行余热锅炉设计过程中应将这点内容也考虑在内,确保电收尘器设备的入口处温度值不小于露点温度值。
但如果电收尘器入口处温度很高的话,也会对设备结构产生不良影响,从而阻碍电收尘器正常运行,影响收尘效果。
工业炉窑排气热回收利用技术研究
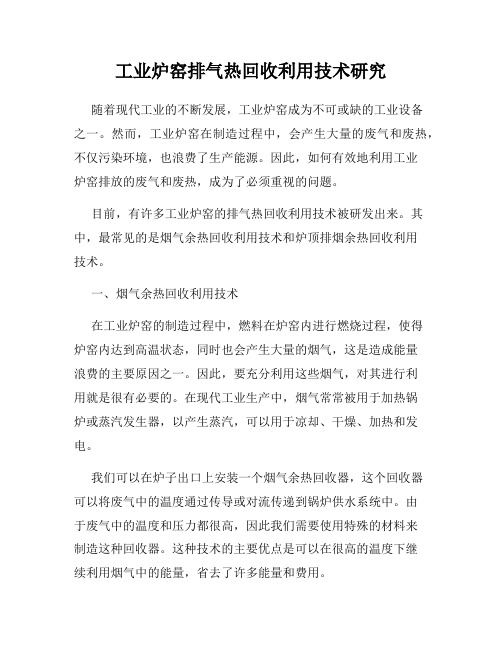
工业炉窑排气热回收利用技术研究随着现代工业的不断发展,工业炉窑成为不可或缺的工业设备之一。
然而,工业炉窑在制造过程中,会产生大量的废气和废热,不仅污染环境,也浪费了生产能源。
因此,如何有效地利用工业炉窑排放的废气和废热,成为了必须重视的问题。
目前,有许多工业炉窑的排气热回收利用技术被研发出来。
其中,最常见的是烟气余热回收利用技术和炉顶排烟余热回收利用技术。
一、烟气余热回收利用技术在工业炉窑的制造过程中,燃料在炉窑内进行燃烧过程,使得炉窑内达到高温状态,同时也会产生大量的烟气,这是造成能量浪费的主要原因之一。
因此,要充分利用这些烟气,对其进行利用就是很有必要的。
在现代工业生产中,烟气常常被用于加热锅炉或蒸汽发生器,以产生蒸汽,可以用于凉却、干燥、加热和发电。
我们可以在炉子出口上安装一个烟气余热回收器,这个回收器可以将废气中的温度通过传导或对流传递到锅炉供水系统中。
由于废气中的温度和压力都很高,因此我们需要使用特殊的材料来制造这种回收器。
这种技术的主要优点是可以在很高的温度下继续利用烟气中的能量,省去了许多能量和费用。
二、炉顶排烟余热回收利用技术炉顶排烟余热回收利用技术可以在生产过程中捕获废气中的热量,以产生热能和电能。
这样,我们就可以把产生的热量回收利用,节省燃料成本,达到节能减排的目的。
该技术的主要优点在于,不需要安装额外的设施,而且操作简单可靠,安全性高。
通过炉子顶部垂直管道捕获排放的废气,然后利用换热器将废气中的热能转化为电能,再通过电池存储起来。
在这个回收过程中,换热器是一个适当的设计,以便可以在几个小时的时间里捕获尽可能多的废气中的热能。
实际上,利用这种技术,我们可以在炉顶的温度达到几千度的情况下实现高效的能量回收。
三、其他应用除了以上介绍的常见技术之外,还有一些其他技术也被广泛应用。
例如,在冶金厂,我们可以利用冷却排水余热,把排放的废气用于冷却或加热水,这样可以降低燃料消耗,减少废气排放。
分析火力发电厂锅炉尾部烟气余热利用技术

分析火力发电厂锅炉尾部烟气余热利用技术摘要:随着电力供应的增加,目前消耗的大部分能源来自碳氢燃料的燃烧,其中一个主要的燃烧产物是水蒸气。
对于燃煤电厂来说,水蒸气以体积百分比12%~16%的烟气排出。
其他工业试验过程,如干燥、湿洗涤器、干洗涤器、脱水和水冷却产生的烟气含水量为20%~90%。通常,水蒸气及其基本潜热被排放到大气中,限制了工艺工程热效率的充分发挥。
如果能够回收40%~60%的水蒸气及其潜热,大多数过程的热效率将提高5%以上。
本文基于现有技术上开发了一种基于纳米多孔陶瓷分离膜的新技术,从烟气中提取部分水蒸气及其潜热,将回收的水和热量返回到蒸汽循环中。
这是通过使用其专门的运输膜冷凝器(TMC)来实现的。
水蒸气通过膜,然后与低温水流直接接触而凝结。
二氧化碳、氧气、氮氧化物和二氧化硫等污染物因其高选择性而无法通过膜。
回收的水质量高、不含矿物质,可以用作几乎所有工业过程的补充水。
关键词:火力发电厂;锅炉;尾部烟气;余热利用技术引言将原系统热力除氧改为化学或真空除氧方式,布置低温加热器用于加热经除氧后的冷凝水;同时将低压系统整体布置在高压省煤器后,低压系统给水由低温加热器提供。
该方案可充分利用160~230℃温度区间的中低温烟气逐步生产低压蒸汽,并最终进入汽轮机低压缸做功发电,排烟余热回收的能力取决于设定的低压蒸汽参数。
低压汽水系统方案有效解决了原有单压汽水系统节点温差对中温烟气余热利用的限制,可实现较高品位烟气的梯级利用,排烟温度降至90℃时,不增加天然气耗量的情况下单台机组可增加发电功率约 2.8MW,即可回收项目投资。
1.基本概述(1)从锅炉设备的角度来说,余热利用系统主要是根据锅炉实际运转情况所展开的,并且锅炉系统常用的仪器在余热利用系统中起到了关键的作用。
基于此,余热利用系统的主要部件位于锅炉系统,这直接决定着该项技术应用的效果。
(2)余热利用系统在锅炉系统中,根据情况设置余热设备,并且通过深度再循环应用系统实现节能降耗的目的。
探讨回转窑烟气余热利用方法

探讨回转窑烟气余热利用方法炭素是冶金行业不可缺的生产材料,炭素生产主要是以煤或石油焦为原料进行煅烧而成。
炭素回转窑出口烟温很高,达1200℃以上。
一般大型炭素回转窑烟气出口都设置有余热蒸汽锅炉回收高温烟气余热,而炭素生产工艺用热一般另外配置燃(重)油或燃(煤)气锅炉。
随着能源价格的不断上涨,这种能源配置系统的缺点逐渐呈现,导致炭素工艺用热设备使用维护成本增加,生产系统的综合能源成本增加,企业产品成本增加。
1 现有导热油系统和回转窑烟气简介1.1 导热油系统炭素一厂配有2台导热油锅炉,I系统2.5MW的燃重油导热油锅炉,常年运行,满足成型工艺的热需求,年耗重油约1400t/a;II系统2.0MW的燃煤气导热油锅炉年运行时间约为重油炉的三分之二,满足沥青熔化和保温用热,消耗煤气折算成重油约700t/a。
根据年重油消耗量计算导热油炉热功率(1400+700÷0.66)×1000×0.8÷300÷24×42000÷3600=3190kW考虑系统管损8%,系统余量30%,则烟气余热导热油炉热功率为:3190×1.38=4402kW1.2 回转窑云铝炭素一厂拥有4台炭素阳极回转窑,一般情况下3台运转(1台检修备用),其规格为Φ2.2×45,设计生产能力6t/h,尾部设有一台10t/h、压力为2.45MPa、温度390℃余热锅炉,生产为连续性。
石油焦煅烧的实收率为75%左右,挥发份及粉尘燃烧释放出的热量较大。
目前使用余热产生的蒸汽35%用于厂内外供热,65%用于发电,年发电量在3350万度。
单台回转窑烟气量约为40000Nm3/h左右,沉灰室出口烟气温度为1200℃左右,经余热锅炉后,最终排入烟囱的温度为200℃左右。
(1)根据锅炉蒸发段参数计算回转窑烟气量:锅炉蒸发段平均烟温:(734+318)÷2=526℃12.1×1000×(2802.3-830.5)÷[(734-318)×1.43×0.98]=40925Nm3/h(2)根据锅炉给水加热段参数计算回转窑烟气量:锅炉给水加热段平均烟温:(198+318)÷2=258℃12.1×1000×(967-438)÷[(318-198)×1.38×0.98]=39441Nm3/h取煅烧窑烟气量为两计算的平均值:(40925+39441)÷2=40183Nm3/h (3)过热器进口烟温计算:t=734+12.1×1000×(3220.5-2802.3)÷(40183×1.44×0.95)=826℃2 回转窑烟气余热利用设计设计烟气预热加热导热油站拟建两台4402kW的余热导热油炉,一用一备,用一台余热炉替代原有两台燃油燃气导热油炉。
- 1、下载文档前请自行甄别文档内容的完整性,平台不提供额外的编辑、内容补充、找答案等附加服务。
- 2、"仅部分预览"的文档,不可在线预览部分如存在完整性等问题,可反馈申请退款(可完整预览的文档不适用该条件!)。
- 3、如文档侵犯您的权益,请联系客服反馈,我们会尽快为您处理(人工客服工作时间:9:00-18:30)。
湿法回转窑尾气余热利用的探讨
作者:黄静
来源:《中国科技纵横》2013年第09期
【摘要】由于湿法回转窑窑尾处排出的废气温度不高,目前针对这些废弃余热进行合理利用的研究还在探索当中。
本文介绍某氧化铝生产企业,在采用烧结法处理低品位铝土矿的生产中,利用湿法回转窑废气余热进行发电作业,初步研究效果较好。
企业将有机介质朗肯循环发电机工作原理应用于湿法窑尾气的余热利用中,在电收尘器设备的前后两端增设热交换器,对有机介质进行加热处理使其发生气化。
在一定的工作压力条件下驱动汽轮发电机组发电。
同时,将汽轮发电机排除出来的低压工作介质进行冷却处理,最后转变为液态,继续循环使用。
【关键词】余热发电湿法回转窑窑尾废气回收
近年来,我国经济发展势头良好,但是各个行业在节能减排工作方面压力也在不断增大。
对回转窑窑尾余热利用技术在不断研究当中,尤其是在干法窑窑尾余热发电技术方面,有了较大突破[1]。
但是对湿法窑而言,利用窑尾余热进行发电这一技术还在深入研究。
因此,为了提高湿法窑废气余热利用效率,本文针对以烧结法工艺生产氧化铝的企业,在湿法窑余热利用方面的技术研究进行分析,结果表明,如果回转窑废气温度超过了200℃,在这样的情况下,可以利用余热锅炉(热交换器)驱动汽轮发电机组进行发电,达到了节能减排的目的,提高了企业经济效益,不断推动企业发展。
1 介绍湿法回转窑窑尾废气余热温度和流量情况
某氧化铝厂熟料烧成所用设备为回转窑,回转窑废气排放量约27万m3/h,废气带走的热量大约3万kJ/h,在电收尘器设备的进口处废气余热温度为235~250℃,出口处废气温度为185~200℃。
比较理想化的收尘设备是电收尘器,电收尘器收尘效果较好,在一定时间之内能处理大量含尘废气。
对于能采用电收尘器设备进行处理的废气,其温度应该是高于露点温度值[2]。
所以,在进行余热锅炉设计过程中应将这点内容也考虑在内,确保电收尘器设备的入口处温度值不小于露点温度值。
但如果电收尘器入口处温度很高的话,也会对设备结构产生不良影响,从而阻碍电收尘器正常运行,影响收尘效果。
废气进入电收尘器的温度以不高于200℃为好。
2 关于安装热交换器的工作分析
按照电收尘器的工作原理,并结合废气排放量和温度等特征确定热交换器的安装位置。
将热交换器设备划分成高温热交换器、低温热交换器两种不同类型交换器设备,其目的是为了能更好的利用废气余热[3]。
不同类型热交换器的安装位置也有所不同,低温热交换器安装在电收尘器出口处,高温热交换器安装在电收尘器入口处。
窑尾废气先经过旋风收尘器收
尘,废气含有的粉尘量大大减少,此时粉尘含量虽然降低了很多,但是其含尘量还是超过了1000mg/m3。
废气温度仍在235~250℃,此温度值会对电收尘器设备的正常运行造成不利影响。
窑尾排出的废气首先经过旋风收尘器收尘之后,进入到高温热交换器,热交换器的传热油和废气发生热交换作用,废气温度降低到160~180℃,同时,传热油温度也升高到210~220℃。
传热油在进入高温热交换器设备前,温度不能低于100℃。
因为废气含有大量水蒸气,当传热油温度低于100℃时,在热交换器设备表面会结成露珠,由于废气中含尘量超过了1000mg/m3,一旦热交换器设备表面产生露珠,其表面就会马上出现结疤现象,这种情况下会使热交换器发生堵塞,使废气不能正常排放,导致回转窑设备不能正常工作,从而影响工作进度[4]。
因此,应将传热油通过低温热交换器设备进行加热处理,使其温度超过100℃后,才可以进入高温热交换器设备。
另一方面,由于电收尘器表面具备散热作用,所以经过电收尘器收尘之后的废气温度会有所下降,温度一般介于135~150℃,并且废气中的粉尘含量也会明显减少,粉尘含量不超过50mg/m3,但是废气仍会携带很多水分。
而传热油首先要经过低温热交换器来预热,当废气与低温热交换器设备中的吸热片相互接触时,会使吸热片表面出现结露现象,但此时废气含尘量较小,不会在热交换器表面形成结疤情况。
3 分析发电设备和有机介质锅炉系统
发电设备和锅炉系统原理如下图(图1)所示。
传热油通过预热器设备进行两次加热之后,传热油的温度达到了200摄氏度左右。
传热油输入到有机介质锅炉,利用传热油的热量对锅炉中的有机介质进行加热处理,当有机介质达到某一个温度值后,会产生有机介质蒸汽,当蒸汽压力超过某个定值就能驱动汽轮发电机设备进行发电,从而实现了利用湿法回转窑窑尾废气余热进行发电[5]。
从汽轮发电机设备中排放出来的有机介质蒸汽,会通过冷凝器进行冷却处理,有机介质液体再从冷凝器排放出来,最后采用强制循环泵将有机介质输送到锅炉中,如此不断进行循环利用,可以减少企业生产成本,不断提高效益,推动企业不断向前发展。
因此,有机介质在冷凝器与锅炉之间可以实现无数次循环使用。
冷凝器中的冷却水经过冷却塔冷却后循环使用。
4 结语
综上所述,本文介绍了某氧化铝厂研究利用湿法回转窑窑尾废气余热进行发电的技术,实践工作中通过一定时间的运行观察,结果表明采用有机介质锅炉设备以及汽轮发电机设备,利用回转窑窑尾废气余热进行发电,这一技术具有非常重要的应用及研究价值。
该氧化铝厂运行研究后发现,其能回收废气显热达到了1/2左右,而且还可以将回收回来的全部热能的2/5变成电能,降低了生产成本,提高企业的经济效益,实现了节能、环保双重目标。
参考文献:
[1]唐金泉.新型干法水泥窑低温废气余热最大发电能力的探讨[J].中国水泥,2009(05):68-71.
[2]牛永贺.湿法回转窑窑尾废气余热发电的探讨[J].有色冶金节能,2010(04):54-58.
[3]杨永强,刘士喜,聂海军.瓦斯发电机组烟气余热利用实践[J].中州煤炭,2008(03):95-96.
[4]王亮,李清海,蒙爱红,张衍国.有机工质余热发电技术的研究进展及其应用前景[J].能源技术,2010(01):9-14.
[5]邹莹,张德刚.窑尾余热锅炉的开发[J].科技风,2009(06):19.。