自动配料系统的比较
自动配料系统的两种配料模式
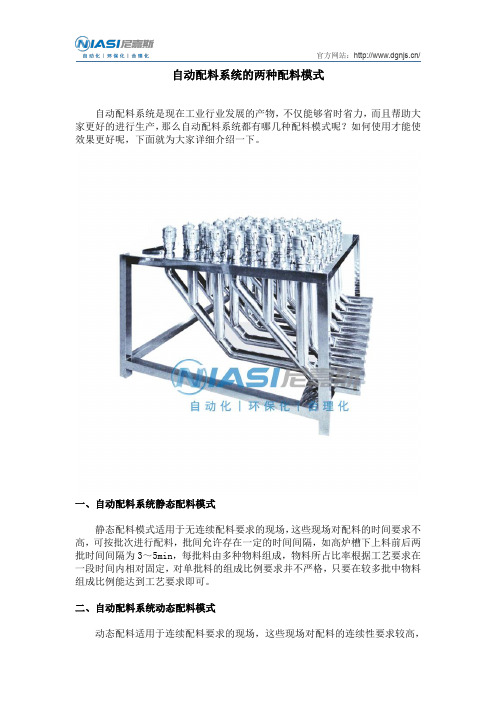
自动配料系统的两种配料模式
自动配料系统是现在工业行业发展的产物,不仅能够省时省力,而且帮助大家更好的进行生产,那么自动配料系统都有哪几种配料模式呢?如何使用才能使效果更好呢,下面就为大家详细介绍一下。
一、自动配料系统静态配料模式
静态配料模式适用于无连续配料要求的现场,这些现场对配料的时间要求不高,可按批次进行配料,批间允许存在一定的时间间隔,如高炉槽下上料前后两批时间间隔为3~5min,每批料由多种物料组成,物料所占比率根据工艺要求在一段时间内相对固定,对单批料的组成比例要求并不严格,只要在较多批中物料组成比例能达到工艺要求即可。
二、自动配料系统动态配料模式
动态配料适用于连续配料要求的现场,这些现场对配料的连续性要求较高,
动配料系统计量一般采用电子皮带秤或核子秤作为计量设备,主机都带有PID 调节及报警功能,可以实现一个仓的自动控制。
对于整个自动配料系统而言,配料秤一般作为计量仪表使用,有些自动控制功能比较强的配料秤可以利用其自控功能,配料秤通过现场总线与控制主机进行联系,构成一个分散式的体系,配料秤在体系中作为一个子站或从站。
以上就是为大家详细介绍的自动配料系统的配料模式,根据不同的生产线选择合适的系统配料模式才能使生产效果更好。
配料系统自动化控制系统
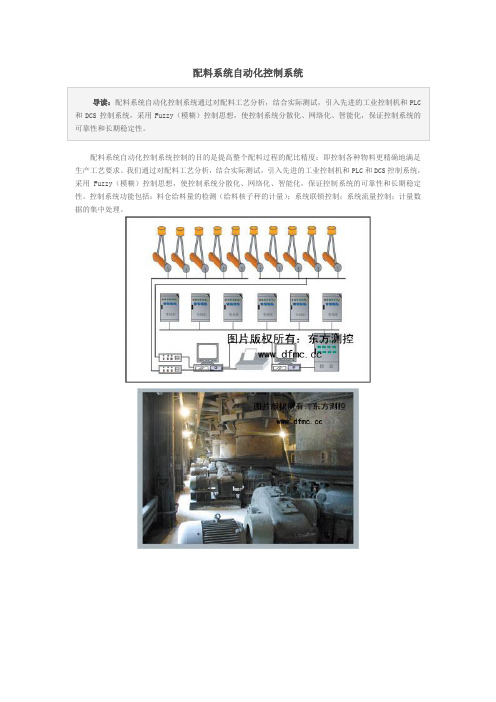
配料系统自动化控制系统
导读:配料系统自动化控制系统通过对配料工艺分析,结合实际测试,引入先进的工业控制机和PLC 和DCS控制系统,采用Fuzzy(模糊)控制思想,使控制系统分散化、网络化、智能化,保证控制系统的可靠性和长期稳定性。
配料系统自动化控制系统控制的目的是提高整个配料过程的配比精度:即控制各种物料更精确地满足生产工艺要求。
我们通过对配料工艺分析,结合实际测试,引入先进的工业控制机和PLC和DCS控制系统,采用Fuzzy(模糊)控制思想,使控制系统分散化、网络化、智能化,保证控制系统的可靠性和长期稳定性。
控制系统功能包括:料仓给料量的检测(给料核子秤的计量);系统联锁控制;系统流量控制;计量数据的集中处理。
系统特点:
1、设备选型
为了确保系统运行可靠,故障少,操作维护方便,在设备选择时,选择经过长期检验证明性能稳定可靠的设备来适应工业现场恶劣环境,保证系统的可靠运行。
2、系统组态
系统组态采用软件二次开发功能,除动态显示工作流程外,包括趋势图、棒图、历史数据等数据显示、报表、打印等功能。
3、易于扩充
系统保留必要的接口,为厂级管理、全部过程实现自动控制设计必要的接口与界面。
4、实用性强
系统具有自动、仪表室内手动、现场手动三类控制方法。
自动配料系统实验报告

一、实验目的1. 了解自动配料系统的工作原理和组成。
2. 掌握自动配料系统的操作方法。
3. 通过实验验证自动配料系统的配料精度和效率。
二、实验原理自动配料系统是一种利用计算机技术、传感器技术、执行器技术等实现自动化配料过程的设备。
其工作原理如下:1. 通过传感器采集原料的重量信息。
2. 将采集到的重量信息传输至计算机控制系统。
3. 计算机控制系统根据预设的配料配方,计算出所需原料的重量。
4. 控制系统将计算结果发送至执行器,执行器驱动配料设备进行配料。
5. 通过传感器实时监测配料过程,确保配料精度。
三、实验设备与材料1. 自动配料系统一台2. 配料原料若干3. 计算机一台4. 传感器一套5. 执行器一套6. 配料设备一套四、实验步骤1. 熟悉自动配料系统的组成及各部分功能。
2. 将自动配料系统连接至计算机,并打开控制系统软件。
3. 设置配料配方,包括原料名称、配比、重量等信息。
4. 启动配料系统,观察传感器采集原料重量信息的过程。
5. 计算机控制系统根据配料配方计算所需原料的重量,并驱动执行器进行配料。
6. 观察配料过程,记录配料结果。
7. 对配料结果进行检验,分析配料精度。
五、实验结果与分析1. 实验结果:通过实验,自动配料系统能够根据预设的配料配方,实现自动化配料过程。
配料精度较高,满足实际生产需求。
2. 分析:(1)自动配料系统具有以下优点:a. 提高配料效率,降低人工成本。
b. 提高配料精度,保证产品质量。
c. 实现自动化生产,降低劳动强度。
(2)实验过程中,传感器能够实时采集原料重量信息,并传输至计算机控制系统。
控制系统根据配料配方计算出所需原料的重量,并驱动执行器进行配料。
实验结果表明,自动配料系统能够实现自动化配料过程,配料精度较高。
(3)实验过程中,配料设备运行稳定,未出现故障。
控制系统软件操作简单,易于上手。
六、实验结论1. 自动配料系统能够实现自动化配料过程,提高配料效率,降低人工成本。
自动化配料系统策划书
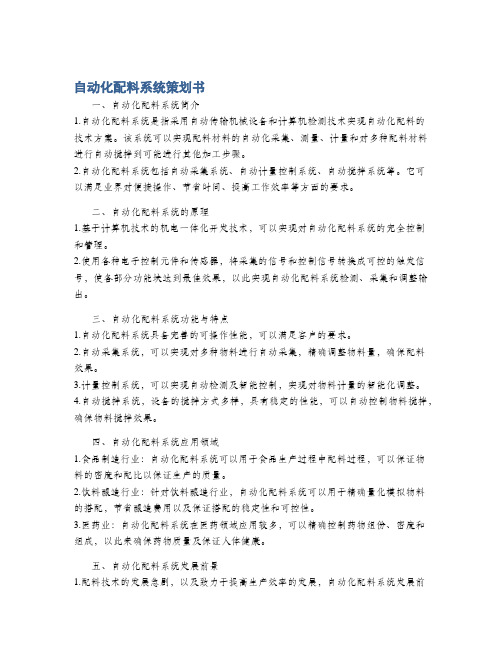
自动化配料系统策划书一、自动化配料系统简介1.自动化配料系统是指采用自动传输机械设备和计算机检测技术实现自动化配料的技术方案。
该系统可以实现配料材料的自动化采集、测量、计量和对多种配料材料进行自动搅拌到可能进行其他加工步骤。
2.自动化配料系统包括自动采集系统、自动计量控制系统、自动搅拌系统等。
它可以满足业界对便捷操作、节省时间、提高工作效率等方面的要求。
二、自动化配料系统的原理1.基于计算机技术的机电一体化开发技术,可以实现对自动化配料系统的完全控制和管理。
2.使用各种电子控制元件和传感器,将采集的信号和控制信号转换成可控的触发信号,使各部分功能块达到最佳效果,以此实现自动化配料系统检测、采集和调整输出。
三、自动化配料系统功能与特点1.自动化配料系统具备完善的可操作性能,可以满足客户的要求。
2.自动采集系统,可以实现对多种物料进行自动采集,精确调整物料量,确保配料效果。
3.计量控制系统,可以实现自动检测及智能控制,实现对物料计量的智能化调整。
4.自动搅拌系统,设备的搅拌方式多样,具有稳定的性能,可以自动控制物料搅拌,确保物料搅拌效果。
四、自动化配料系统应用领域1.食品制造行业:自动化配料系统可以用于食品生产过程中配料过程,可以保证物料的密度和配比以保证生产的质量。
2.饮料酿造行业:针对饮料酿造行业,自动化配料系统可以用于精确量化模拟物料的搭配,节省酿造费用以及保证搭配的稳定性和可控性。
3.医药业:自动化配料系统在医药领域应用较多,可以精确控制药物组份、密度和组成,以此来确保药物质量及保证人体健康。
五、自动化配料系统发展前景1.配料技术的发展急剧,以及致力于提高生产效率的发展,自动化配料系统发展前景广阔。
2.随着生产企业不断完善自动化配料系统,自动化配料系统未来将会得到更多应用,自动化配料系统将会把生产效率提高到前所未有的水平。
3.由于自动化配料系统可以降低人工开销,大大提高了运行效率,未来自动化配料系统将会是市场上重要的产品。
自动配料系统的计量

自动配料系统的计量自动配料系统是指通过计算机控制自动化配药、混料、计量等操作的系统。
在工业生产、医药等领域得到广泛应用,能够大大提高产品质量和生产效率。
本文将着重介绍自动配料系统的计量部分。
计量原理自动配料系统的计量部分主要包括称量、计量仪表和控制系统。
整个计量过程在计算机程序的控制下自动进行,相对人工计量而言,更加准确、方便、高效。
1.称量称量是自动配料系统中最基本的计量方式之一。
传统的称量方式是使用电子称进行称量,但随着科技的发展,压力式称量和重心称量等新技术不断涌现,提高了称量的准确性和效率。
在自动化生产线中,称量主要应用于对原料和成品重量的测量。
2.计量仪表计量仪表是自动配料系统中进行计量的关键设备,一般包括变送器和控制器两部分。
通过采集传感器得到的实时数据信号,变送器对其进行放大、滤波等处理后,传输给控制器进行计量。
3.控制系统自动化控制系统是配料系统中的信息处理中心,负责采集、处理各传感器传输来的数据信号,并根据设定程序发出控制信号,实现自动化配料的目的。
不同的控制系统可适用于不同的生产场所和要求。
计量应用自动配料系统的计量应用十分广泛,例如:1.食品工业在食品生产过程中,自动化计量可保证原料的质量和含量,提高产品的口感、色泽和营养价值。
同时,自动化计量还可以防止工人操作不当和环境等因素对生产产生影响。
2.医药工业在药品生产过程中,自动化计量可保证药品的质量和药性,控制药品的含量和剂量,防止因人为因素而产生误差。
同时,自动化计量还能够提高药品生产的效率,降低成本,促进产业的发展。
3.化工、冶金工业自动化计量可帮助化工、冶金等行业进行合理的配料和计量,提高产品的纯度和质量,降低能耗,提高生产效率。
同时,自动化计量还能够保证工人的安全和生产环境的安全。
总结自动配料系统的计量是自动化生产环节中最为关键的部分之一,不论是食品工业还是医药工业、化工、冶金等领域,计量都具有重要意义。
通过采用先进的计量技术和控制系统,可提高产品质量、生产效率和安全性,从而推动整个行业的发展。
水泥生产线施工技术实现生产工艺的自动化与智能化

水泥生产线施工技术实现生产工艺的自动化与智能化近年来,随着科技的不断发展以及工业制造领域的进步,水泥生产线施工技术也在不断演进。
自动化与智能化技术的引入,使得水泥生产工艺更加高效、精确和环保。
本文将讨论水泥生产线施工技术实现生产工艺的自动化与智能化的现状、优势和应用。
一、自动化技术在水泥生产线施工中的应用自动化技术在水泥生产线施工中起到了至关重要的作用。
通过使用自动化控制系统,可以实现生产线各个环节的自动操作和监控。
例如,利用自动化技术可以对水泥原料进行自动配料、自动研磨和自动搅拌,提高生产效率和生产质量。
此外,还可以通过自动化技术对整个生产过程进行监控,及时发现和解决问题,提高生产线的稳定性和可靠性。
二、智能化技术在水泥生产线施工中的应用智能化技术的引入使得水泥生产线施工更加智能化和智能。
通过使用智能化技术,可以实现生产线的智能监控、智能调度和远程操作。
例如,可以通过智能化技术对生产设备进行智能监控,实时收集和分析设备运行数据,预测设备故障,及时进行维修和保养,减少停机时间和生产成本。
此外,还可以通过智能化技术对生产流程进行智能调度,实现最佳的生产计划和资源分配,提高生产效率和资源利用率。
三、自动化与智能化技术的优势和价值自动化与智能化技术的应用给水泥生产线施工带来了诸多优势和价值。
首先,自动化与智能化技术可以提高水泥生产线的生产效率和生产质量。
通过自动化的操作和监控,可以减少人为因素的干扰,提高生产线的稳定性和可靠性。
其次,自动化与智能化技术可以降低劳动强度和人员成本。
自动化设备能够代替人们进行一些重复性和危险性高的操作,减少了工人的劳动强度和工伤风险。
此外,自动化与智能化技术还可以提高生产线的能源效率和资源利用率,降低生产成本和环境污染。
四、自动化与智能化技术在水泥生产线施工中的应用案例分析1. 自动配料系统:通过使用自动化控制系统,实现水泥配料过程的自动化,提高了配料的准确性和稳定性。
根据生产需求和材料参数,系统可以自动调整配料比例,确保产品质量的稳定性。
配料系统介绍
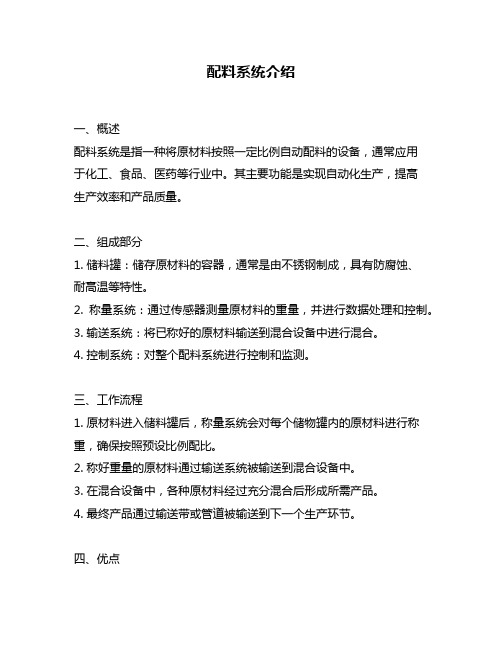
配料系统介绍一、概述配料系统是指一种将原材料按照一定比例自动配料的设备,通常应用于化工、食品、医药等行业中。
其主要功能是实现自动化生产,提高生产效率和产品质量。
二、组成部分1. 储料罐:储存原材料的容器,通常是由不锈钢制成,具有防腐蚀、耐高温等特性。
2. 称量系统:通过传感器测量原材料的重量,并进行数据处理和控制。
3. 输送系统:将已称好的原材料输送到混合设备中进行混合。
4. 控制系统:对整个配料系统进行控制和监测。
三、工作流程1. 原材料进入储料罐后,称量系统会对每个储物罐内的原材料进行称重,确保按照预设比例配比。
2. 称好重量的原材料通过输送系统被输送到混合设备中。
3. 在混合设备中,各种原材料经过充分混合后形成所需产品。
4. 最终产品通过输送带或管道被输送到下一个生产环节。
四、优点1. 提高生产效率:自动化操作减少了人工干预,提高了生产效率。
2. 提高产品质量:配料精度高,减少了人为误差,保证了产品质量。
3. 节约成本:自动化生产减少了人力成本和原材料浪费,节约了成本。
4. 安全可靠:使用不锈钢材料制造的储料罐具有防腐蚀、耐高温等特性,保证了设备的安全可靠性。
五、适用范围配料系统广泛应用于化工、食品、医药等行业中。
例如,在食品行业中,配料系统可以用于制作各种饼干、糖果等甜点;在医药行业中,可以用于制作各种口服液体药剂。
六、维护保养1. 定期检查设备是否存在异常情况,并及时处理。
2. 定期清洗设备内部和外部的污垢和积尘,并消毒杀菌。
3. 定期检查传感器的精度,并及时校准。
七、总结配料系统是一种实现自动化生产的设备,其主要功能是按照一定比例自动配料。
其优点包括提高生产效率、提高产品质量、节约成本和安全可靠。
在使用过程中,需要定期进行维护保养,以确保设备的正常运行。
配料秤自动配料原理

配料秤自动配料原理
配料秤自动配料的原理是通过称重来实现准确配料的过程。
它通常由称重传感器、控制系统和配料执行机构组成。
首先,称重传感器是配料秤的核心部件,它负责将被称物体的重量转化为电信号。
一般情况下,配料秤采用负荷传感器或称量电子秤作为称重传感器。
当物体放到传感器上时,传感器会产生一个电信号,该信号与物体的重量成正比。
接下来,控制系统会接收传感器发送的电信号,并将其转化为数字信号进行处理。
控制系统一般由微处理器或单片机来完成,它可根据预设的目标重量和误差范围来判断配料过程是否完成。
若没有达到目标重量,控制系统会调整配料执行机构的动作,继续配料或进行微调。
最后,配料执行机构根据控制系统的指令进行相应动作。
常见的配料执行机构包括切断阀、传送带、气动阀等。
当控制系统判断需要配料时,配料执行机构会打开或关闭相应的通路,使配料物料流动或停止。
通过称重传感器、控制系统和配料执行机构的协调配合,配料秤可以实现自动准确地配料。
在工业生产中,配料秤广泛应用于化工、食品、医药等行业,提高了配料的精准度和生产效率。
- 1、下载文档前请自行甄别文档内容的完整性,平台不提供额外的编辑、内容补充、找答案等附加服务。
- 2、"仅部分预览"的文档,不可在线预览部分如存在完整性等问题,可反馈申请退款(可完整预览的文档不适用该条件!)。
- 3、如文档侵犯您的权益,请联系客服反馈,我们会尽快为您处理(人工客服工作时间:9:00-18:30)。
几种常用自动配料系统的比较与改进
济钢集团总公司计量管理处王庆河邵亚男
摘要:本文对现代自动配料系统进行了概述,并对不同的系统结构、计量仪表等进行了介绍与比较。
关键词:自动配料系统静态配料模式动态配料模式
1.钢铁自动化配料的应用现状
钢铁行业现在越来越重视配料,提出了“精料方针”,从原料进厂开始要求全过程控制。
“精料方针”的重要性是显而易见,但真要落实确存在一定的难度,首先,要提高配料系统的自动水平和配料精度;第二,要从生产管理上下功夫,制定配料计划;第三,要加强原料及成品化验,提高化验的准确性、抽样及化验的频度等。
自动化配料是其中的重要一环,它是配料计划正确执行的根本保证,如果没有高水平的自动化配料系统,精料方针根本无从谈起。
自80年代末期,钢铁企业陆续对配料系统进行改造,逐步实现了自动化配料,随着技术的发展形成了几种不同模式,包括静态计量、电子皮带秤计量、核子秤计量等,各种模式分别适用于不同的应用现场。
本文将针对这几种配料模式进行比较并提出一些必要改进措施。
2.几种自动配料模式的原理与优缺点
2.1.静态配料模式
静态配料模式适用于无连续配料要求的现场,这些现场对配料的时间要求不高,可按批次进行配料,批间允许存在一定的时间间隔,如高炉槽下上料前后两批间时间间隔为3~5分钟,每批料由多种物料组成,物料所占比率根据工艺要求在一段时间内相对固定,对单批料的组成比例要求并不严格,只要在较多批中物料组成比例能达到工艺要求即可。
静态配料模式下,各种物料分别贮放在不同料仓,料仓给料一般采用电振给料、螺旋给料或星形给料等形式,计量一般采用计量仓,并配装有压式或拉式重力传感器进行力电转换,信号经二次仪表放大处理后接入PLC或DCS等来完成计量。
在一些对时间要求宽的应用场合,可以采用一个计量小车进行统一计量,计量小车沿轨道运行,依次定位到各料仓下按比例进行物料配加,各种物料的配加量采用减差法计算出来。
亦有采用单一固定计量仓方式的,各料仓以环状分布在一个计量仓周围,各物料的计量亦采用减差法,物料自溜槽或皮带输送机依次按比例配加到计量仓。
分别计量和减差法计量之间各有优缺点,分别计量可以根据每次所加料的重量、体积来设计合适的计量仓和计量仪表,可以提高计量的准确性,尤其是对小比例物料,但计量仓与计量设备成倍增加,成本较高。
减差法计量采用一个计量仓或计量小车,计量设备投资少,同时由于采用同一计量设备,无论计量误差如何,但都可以保证物料按比例配加,但对于小比例物料配加往难以保证其准确性。
计量后的物料经过集中后一般形成层状或段状分布的一批料通过输送设备(如皮带或小车)输送到受料口,进入下一工序,即完成一批料的配加。
由于物料计量、输送、加入等环节在时间上可以重叠在,在控制流程可以采用并行方式,
以节省上料时间,提高上料速度。
2.2.动态配料模式
动态配料适用于连续配料要求的现场,如烧结配料、焦化配料。
这些现场对配料的连续性要求较高,一般不允许出现中间配料停止的情况,对各种物料的配比要求比较严格。
动态配料系统计量一般采用电子皮带秤或核子秤作为计量设备,配料秤主机都带有PID调节及报警功能,可以实现一个仓的自动控制。
对于整个自动配料系统而言,配料秤一般作为计量仪表使用,有些自动控制功能比较强的配料秤可以利用其自控功能,配料秤通过现场总线与控制主机进行联系,构成一个分散式的体系,配料秤在体系作为一个子站或从站。
2.2.1.电子皮带秤的计量原理及选型
电子皮带秤利用计量皮带来运输物料,当物流经过称量段时由称量段进行连续采样,由传感器进行力电转换为mV级信号,经放大器放大为电流信号后进行远传,电流信号可以与秤主机连接或直接与计算机系统连接,秤主机或计算机完成零点校验、标定、测试、控制等功能。
称量段是由一段皮带、一组称量托辊、支撑框架及力传感器组成,结构上有全悬浮式、半悬浮式、杠杆平衡式等多种形式,全悬浮式称架结构一般采用4只传感器,半悬浮式一般采用1或2只传感器、杠杆平衡式一般采用1只传感器,传感器有拉式传感器和压式传感器两种,根据称架结构的设计可以选用不同的传感器。
多传感器设计时各传感器可以采用并行和串行连接两种方式。
对电子皮带秤而言,其称架结构的设计与传感器的选择是整体计量精度重要影响因素。
秤架要具备足够强度、形变小、重量轻。
传感器要根据实际的负荷进行选择,有时会出现传感器选择过大,信号空间过窄,信燥比小,导致计量精度差、波动大等后果。
全悬浮式和半悬浮式秤架由于其秤架的重量加在传感器上,传感器量程较大,相对灵敏度较差,此时要综合考虑秤架及物料负荷的情况选择传感器,既要满足最大物料负荷的要求,还要尽量提高相对灵敏度,满足计量精度的要求。
2.2.2.核子秤的计量原理及选型
核子秤是利用物料对核射线的吸收量与物料量相关的原理设计的。
其数学模型如下所示
I=I0e-μdδ(1)
F=AlnI/I0 (2)
L=FV (3)
I0 :无物料时的射线强度
I :被物料吸收后的射线强度
μ:物料的质量吸收系数
d :物料厚度
δ:物料比重
A :负荷常数
F :负荷
L :物料实际流量
核射线自核源发出成一定角度穿透物料到达电离室,电离室内装有惰性气体,惰性气体在核射线的作用下电离,由采集装置采集到电离的强度信号,经前置放大后进行远传(一般为脉冲信号,脉冲的频率与被射线照射的物料的量成线性相关),测速传感器采集物料的移动速度,放大后远传。
核子秤主机对现场传来的信
号进行放大处理后根据模型计算出实际的物料流量。
核子秤选型时要重要考虑核源强度、电离室、前置放大器等设备。
核源的强度要符合国家卫生防疫的有关规定,并满足计量的要求。
电离室和前置放大器要具备足够的灵敏度和较小的漂移量。
有时会以上各项选择不当造成因漂移量与灵敏度的影响而导致计量精度过小,不能满足计量的要求。
2.2.
3.电子皮带秤与核子秤的比较
电子皮带秤直接测量物料的重量信号并转换为质量流量,物料的比重、形状、粒度等对计量准确性影响不大,计量精度高,一般为0.3%,但秤架的维护量大,对环境要求较高。
核子秤通过间接方式测得质量流量,由于其测量的原理的限制,物料的比重、形状、粒度等对计量准确性影响较大,计量精度也不高,一般为1%,但秤架维护量不大,适合于各种恶劣环境。
核子秤由于具有核辐射,不能用在人员较多的场合,也不能应用于食品计量上。
2.2.4.动态配料系统的设计要点
计量仪表可以选用电子皮带秤或核子秤,可选用测速装置,如果秤具备自动控制及通讯功能,可以考虑分布式配料系统,否则只可将秤作为一台计量仪表,控制功能由计算机来完成。
计算机系统要具备完善的通讯功能、高精度的输入与输出模块、低故障率、易维护,软件设计要充分考虑工艺的要求,具有一定的灵活性,并提供故障诊断功能,以协助检修人员进行检修维护。
3.配料系统发展
随着研究的不断深入及相关技术的快速发展,配料系统也在不断更新发展,主要包括以下几个方面。
▲高精度:新型传感器、更科学的秤架结构、高精度AD转换模块的采用,系统的设计理念有效的提高了系统的整体计量精度;
▲高可靠性:电路的高集成度与简约化大大降低了系统的故障率,减少了维护量,故障时间大大缩短;
▲智能化:系统设计上采用了更多的新思想、新技术,系统的功能进一步完善,与管理信息系统、化验系统进行信息共享,可以为管理提供多种统计数据,自动对配料比例、数量等进行优化,达到智能化配料。
▲分布式:智能型的称重配料单元被广泛采用,现场单元的计量与控制功能逐步完善,形成分布式的结构体系,系统的可靠性有了较大提高,计算机也从繁重的计量与控制工作中解脱出来,将重点放在了数据处理与配料优化方面。