锂电池内部微短路控制方法
锂电池微短路、腐蚀和漏液问题前沿解决方案-190716
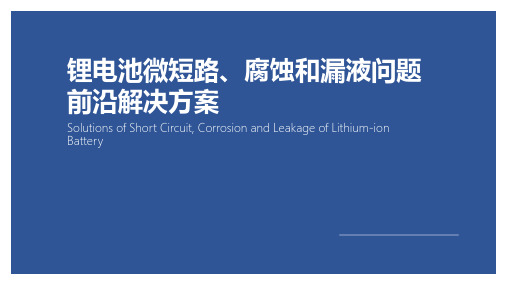
锂电池微短路、腐蚀和漏液问题前沿解决方案Solutions of Short Circuit, Corrosion and Leakage of Lithium-ion Battery电池安全/Safety of Lithium Battery开发设计•能量密度•成本•CPK体系选择•材料/三元、铁锂•系统安全•电池类型制程控制•设计阶段•工艺开发•过程控制产业链•材料设备上游•电池模组制造•整车设计安全安全检测/Safe T esting of Lithium Battery前海久禾安全检测方案微短路检测方案密封性检测方案腐蚀检测方案Hi-pot测试电解液泄漏测试软包电池腐蚀测试导致电池内部微短路原因⚫搅拌不均匀⚫来料金属屑⚫金属焊渣⚫环境粉尘⚫毛刺⚫隔离膜不良⚫极片错位⚫极片损伤⚫设备金属磨损⚫电解质分布不均等制程中应用中⚫析锂长成为锂枝晶刺穿隔离膜电解液SEI 膜锂金属负极微短路检测的现状目前基本还停留在绝缘阻抗测试仪、耐压测试仪的阶段。
传统检测仪的基理通过用一个高电压激励到被测装置相互隔离的两端,持续一段时间,然后采集激励所产生的电流,利用欧姆定律U=IR测量出阻抗或漏电流。
是电子设备/电子元件进行电气安全标准测试的仪表。
⚫单电池⚫电池组⚫车载充电器⚫家用充电插头AC/DC耐压和绝缘一体机新型微短路检测解决途径⚫需满足C=(ε*S)/d=Q/U 原理⚫脉冲电压技术绝缘脉冲检测的解决方案⚫高精度脉冲电压⚫超短时间⚫微损伤漏液检测的必要性电解液泄漏与电池爆炸,是软包电池生产企业同级别零容忍对待的质量问题。
目前,电解液泄漏问题仍是一个较难杜绝的品质缺陷。
电解液泄漏的原因⚫铝塑膜成型⚫装配⚫热封不良⚫电解液在封口残留⚫折边过分⚫制程中造成铝塑膜破损等PP尼龙AL 内部外部传统漏液检测手段石蕊试纸检测⚫成本高⚫过杀率高⚫不适合批量性全检⚫更不适合自动化检测人工外观检测⚫完全依赖人工目测⚫检出率低⚫信赖度差⚫防呆效果不能保证充正压法检测⚫检出率低⚫对电池的破坏性大⚫机理不易实现⚫依然依赖人工目测辨别⚫设备安全要求高漏液检测前沿解决方案电解液中含有EMC、DEC、EC、PC、VC 等脂类有机化合物作为示踪物质,利用其挥发特性,通过广域的VOC气体检测传感器技术探测有机物浓度来确定电解液的泄量。
锂电池内部微短路控制方法
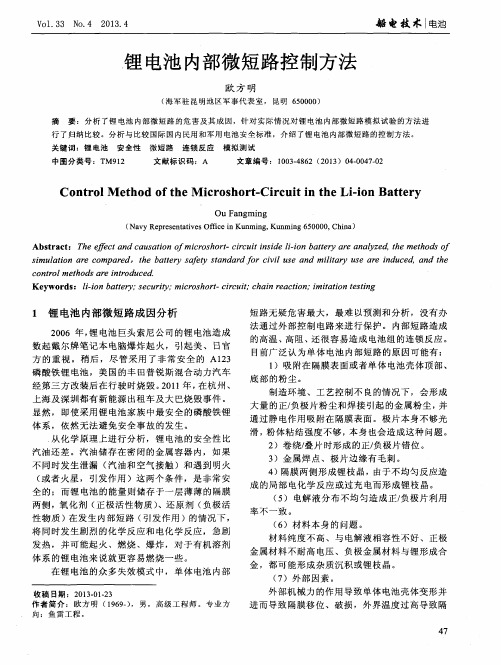
船 电技 术 f 电池
锂 电池 内部 微 短路控 制 方法
欧 方 明
( 海 军驻 昆明地 区军事 代表 室 , 昆明 6 5 0 0 0 0 )
摘
要 :分 析 了锂 电池 内部 微 短路 的危 害及 其成 因 ,针对 实 际情 况对 锂 电池 内部 微短 路模拟 试 验 的方法 进
s i mu l a t i o n a r e c o m p a r e d ,t h e b a t t e r y s a f e y t s t a n d a r df o ,c i v i l u s e a n d mi l i t a y r u s e a r e i n d u c e d a n d t h e
( 5 ) 电解 液 分 布 不 均 匀 造 成 正 / 负极 片 利 用
率不一致 。
( 6 )材料 本 身 的 问题 。
材 料 纯 度 不 高 、与 电解 液 相 容 性 不好 、正 极
2 )卷 绕/ 叠 片 时 形 成 的 正/ 负 极 片错 位 。 3 ) 金 属 焊 点 、 极 片边 缘 有 毛 刺 。 4 ) 隔 膜 两 侧 形 成锂 枝 晶 ,由于 不 均匀 反 应 造
成 的局 部 电化 学 反 应 或 过 充 电而 形 成 锂 枝 晶 。
汽 油还 差 。汽 油储 存 在 密 闭 的金 属 容器 内,如 果 不 同 时 发 生 泄漏 ( 汽 油 和 空气 接 触 )和 遇 到 明 火 ( 或 者火 星 , 引发 作用 )这 两 个 条件 ,是 非 常 安 全 的 ; 而 锂 电池 的 能 量 则 储 存 于 一 层 薄 薄 的 隔 膜
锂电池保护电路
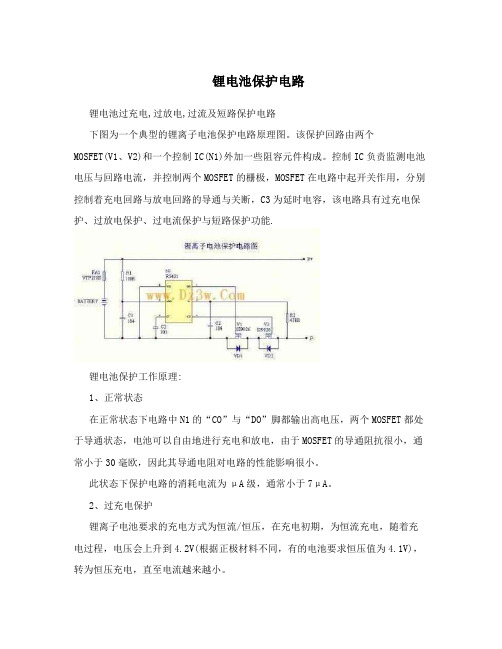
锂电池保护电路锂电池过充电,过放电,过流及短路保护电路下图为一个典型的锂离子电池保护电路原理图。
该保护回路由两个MOSFET(V1、V2)和一个控制IC(N1)外加一些阻容元件构成。
控制IC负责监测电池电压与回路电流,并控制两个MOSFET的栅极,MOSFET在电路中起开关作用,分别控制着充电回路与放电回路的导通与关断,C3为延时电容,该电路具有过充电保护、过放电保护、过电流保护与短路保护功能.锂电池保护工作原理:1、正常状态在正常状态下电路中N1的“CO”与“DO”脚都输出高电压,两个MOSFET都处于导通状态,电池可以自由地进行充电和放电,由于MOSFET的导通阻抗很小,通常小于30毫欧,因此其导通电阻对电路的性能影响很小。
此状态下保护电路的消耗电流为μA级,通常小于7μA。
2、过充电保护锂离子电池要求的充电方式为恒流/恒压,在充电初期,为恒流充电,随着充电过程,电压会上升到4.2V(根据正极材料不同,有的电池要求恒压值为4.1V),转为恒压充电,直至电流越来越小。
电池在被充电过程中,如果充电器电路失去控制,会使电池电压超过4.2V后继续恒流充电,此时电池电压仍会继续上升,当电池电压被充电至超过4.3V时,电池的化学副反应将加剧,会导致电池损坏或出现安全问题。
在带有保护电路的电池中,当控制IC检测到电池电压达到4.28V(该值由控制IC决定,不同的IC有不同的值)时,其“CO”脚将由高电压转变为零电压,使V2由导通转为关断,从而切断了充电回路,使充电器无法再对电池进行充电,起到过充电保护作用。
而此时由于V2自带的体二极管VD2的存在,电池可以通过该二极管对外部负载进行放电。
在控制IC检测到电池电压超过4.28V至发出关断V2信号之间,还有一段延时时间,该延时时间的长短由C3决定,通常设为1秒左右,以避免因干扰而造成误判断。
3、过放电保护电池在对外部负载放电过程中,其电压会随着放电过程逐渐降低,当电池电压降至2.5V时,其容量已被完全放光,此时如果让电池继续对负载放电,将造成电池的永久性损坏。
锂电池短路三大情况
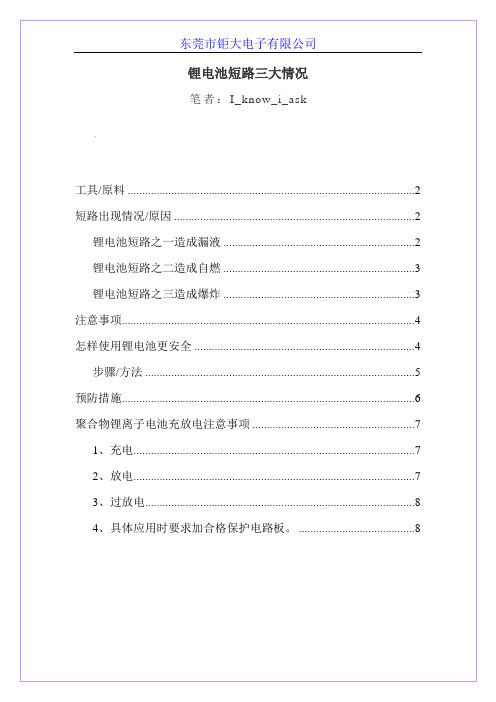
随着数码产品普及,锂电池也随着普遍存在我们生活中,然而对于锂电池带来的危险依旧是一个老生常谈的话题,据调查锂电池出现安全问题而导致的较严重后果归于短路造成的;下面是笔者心德与广大友人共享。
工具/原料锂电池短路出现情况/原因锂电池短路之一造成漏液锂电池体内温度上升较慢的情况下,外壳逐渐溶化,保护层起不到保护作用,导致有腐蚀性的电解液的泄漏。
锂电池短路之二造成自燃当锂电池短路时产生的火花会在瞬间点燃电解液,这是由于电解液由易燃液体构成,燃烧的电解液会跟着引燃塑料机身,导致电池燃烧,电池周围如果有易燃物的话将会造成火灾。
锂电池短路之三造成爆炸锂电池体内温度上升较快,由于外壳不象在温度上升较慢时会逐渐溶化,因而导致电池内部空间不足以容纳加热情况下的膨胀气体,电池容器因压力过大而爆炸。
注意事项1、数码产品使用锂电池时一定要原装锂电池、原装充电器、适宜的环境温度工作、切忌不自行改装电池等;2、对于废旧的锂电池要科学回收;怎样使用锂电池更安全锂离子电池(Li-ion)是可充电电池的一种,通常被用在笔记本电脑、手机和iPod上。
一些简单的使用注意事项将让您的锂离子电池相对更安全,也更长寿。
预防措施为了防止电池可能发生泄漏、发热、爆炸,请注意以下预防措施:禁止在任何情况下拆卸电芯。
禁止将电池浸入水中或海水中,不能受潮。
禁止在热源旁,如火、加热器等,使用或放置电池。
禁止将电池加热或丢入火中。
禁止直接焊接电池。
禁止在火边或很热的环境中充电。
禁止将电池放入微波炉或高压容器内。
禁止在高温下(如强阳光或很热的汽车中)使用或放置电池,否则会引起过热、起火或者功能衰退、寿命减小。
如有电解液泄漏或散发电解液气味的电池应远离火源以避免着火或爆炸。
锂电池保护板短路保护原理
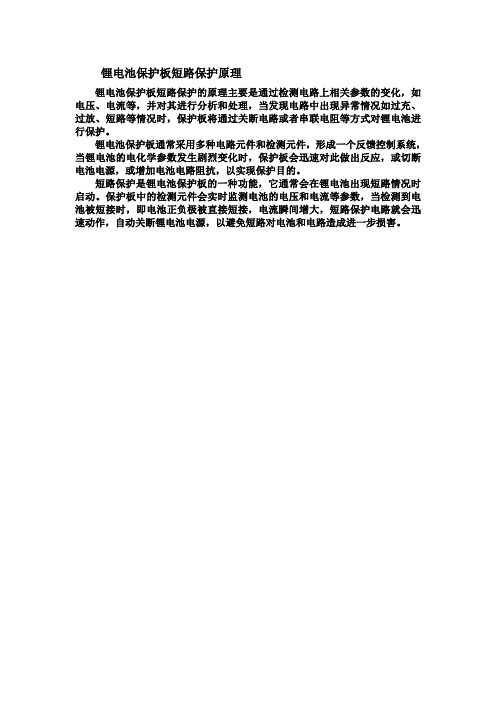
锂电池保护板短路保护原理
锂电池保护板短路保护的原理主要是通过检测电路上相关参数的变化,如电压、电流等,并对其进行分析和处理,当发现电路中出现异常情况如过充、过放、短路等情况时,保护板将通过关断电路或者串联电阻等方式对锂电池进行保护。
锂电池保护板通常采用多种电路元件和检测元件,形成一个反馈控制系统,当锂电池的电化学参数发生剧烈变化时,保护板会迅速对此做出反应,或切断电池电源,或增加电池电路阻抗,以实现保护目的。
短路保护是锂电池保护板的一种功能,它通常会在锂电池出现短路情况时启动。
保护板中的检测元件会实时监测电池的电压和电流等参数,当检测到电池被短接时,即电池正负极被直接短接,电流瞬间增大,短路保护电路就会迅速动作,自动关断锂电池电源,以避免短路对电池和电路造成进一步损害。
锂电池安全问题汇总及常见预防措施
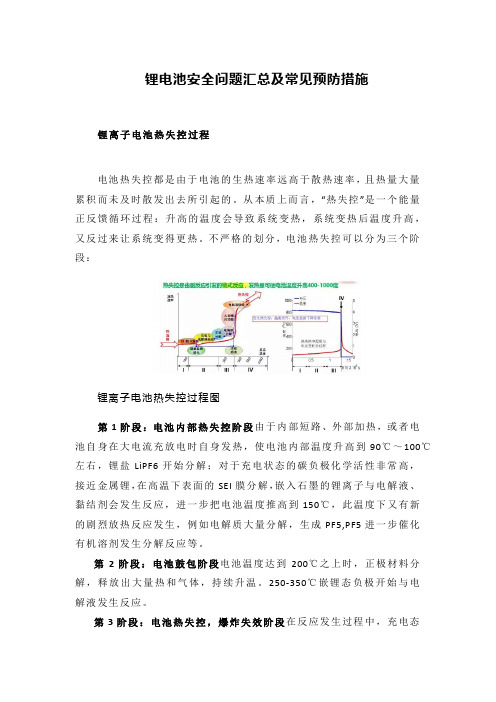
锂电池安全问题汇总及常见预防措施锂离子电池热失控过程电池热失控都是由于电池的生热速率远高于散热速率,且热量大量累积而未及时散发出去所引起的。
从本质上而言,“热失控”是一个能量正反馈循环过程:升高的温度会导致系统变热,系统变热后温度升高,又反过来让系统变得更热。
不严格的划分,电池热失控可以分为三个阶段:锂离子电池热失控过程图第1阶段:电池内部热失控阶段由于内部短路、外部加热,或者电池自身在大电流充放电时自身发热,使电池内部温度升高到90℃~100℃左右,锂盐LiPF6开始分解;对于充电状态的碳负极化学活性非常高,接近金属锂,在高温下表面的SEI膜分解,嵌入石墨的锂离子与电解液、黏结剂会发生反应,进一步把电池温度推高到150℃,此温度下又有新的剧烈放热反应发生,例如电解质大量分解,生成PF5,PF5进一步催化有机溶剂发生分解反应等。
第2阶段:电池鼓包阶段电池温度达到200℃之上时,正极材料分解,释放出大量热和气体,持续升温。
250-350℃嵌锂态负极开始与电解液发生反应。
第3阶段:电池热失控,爆炸失效阶段在反应发生过程中,充电态正极材料开始发生剧烈分解反应,电解液发生剧烈的氧化反应,释放出大量的热,产生高温和大量气体,电池发生燃烧爆炸。
锂离子电池材料的安全性负极材料负极材料虽然比较稳定,但嵌锂状态下的碳负极在高温下会与电解液发生反应。
负极与电解液之间的反应包括以下三个部分:SEI的分解;嵌入负极的锂与电解液的反应;嵌入负极的锂与黏结剂的反应。
常温下电子绝缘的SEI膜能够防止电解液的进一步分解反应。
但在100℃左右会发生SEI膜的分解反应。
锂离子电池各种放热反应的温度区间与反应焓在更高温度下,负极表面失去了SEI膜的保护,嵌入负极的锂将与电解液溶剂直接反应有C2H4O产生,可能为乙醛或氧化乙烯。
嵌入锂的石墨在300℃以上与熔融的PVDF–HPF共聚物发生如下反应:反应热随着嵌锂程度的增加而增加,反应热随黏结剂种类不同而不同。
锂电池热失控的原因及预防措施
锂电池热失控的原因分析及预防措施对于锂电池热失控的研究,众多研究者一直都在不断深入研究,以此来预防和降低锂电池在使用过程中的风险。
以下锂电池的失控原理也是一些研究者的看法。
一.热失控的原理分析对于热失控的原理,分为了三个阶段:第1阶段:热失控开始阶段:125℃左右,这个阶段是一般认为是负极SEI膜反应分解,使得负极与电解液直接接触,从而导致了电解液与负极中的锂反应并生成气体。
第2阶段:电池内部气体释放和升温加速,温度在125~180℃左右,这个阶段正极材料分解释氧,锂盐也会分解,如LiPF6分解生成LiF和路易斯酸PF5。
而路易斯酸会在高温下与电解液反应产生大量的气体。
第3阶段:热失控阶段,大约为180℃以上。
在这个阶段正/负电极材料与电解液发生盛剧烈的放热反应和电解液分解放热,电池内部温度急剧升高,电池泄压阀打开或引发自燃。
也有研究者将热失控细分为如下范围:一般动力电池的热失控有三个特征温度,起始发热温度T1,热失控引发温度T2,热失控最高温度T3。
T1:指的是SEI膜分解的温度,T3:它取决于整个反应焓,T2:这个温度跟电池本身的状态,电池体系,使用状态相关,这个温度会由一个缓慢的升热会突然引发急剧的升热,这个生热速率可以达到几百到1000度/秒,这是引发热失控的关键。
通过一些研究发现,它主要有3个方面的原因,内部短路,正极释氧,负极析锂。
二、热失控的原因分析1、机械滥用破坏性变形和位移是机械滥用的两个共同特征,在外力的作用下导致的锂电池(电芯)发生形变,隔膜被破坏,正负极之间短路而诱发热失控,比如挤压、碰撞、针刺等。
2、热滥用比如长期使得锂电池在高温环境下工作,比如:外界高温环境,大电流过程中使用产生的了很多的极化热、反应热、分解热等。
3、电滥用锂电池过充电导致活性物质结构遭到破坏,电解液分解产气,导致电池内部压强增大。
除此之外,还包括过放电、大倍率(超过规格)充电等。
1)外短路锂电池的正负极不通过负载直接导通连接。
谈锂离子电池热失控火灾事故调查及防范对策
谈锂离子电池热失控火灾事故调查及防范对策发布时间:2021-08-10T11:17:16.930Z 来源:《城市建设》2021年8月上15期作者:唐彪[导读] 锂离子电池具有火灾爆炸燃烧危险特性,燃烧时会产生高温毒气,发生火灾后一旦处置不当,后果极为严重,还可能会造成人员伤亡。
因此,如何防范锂离子电池火灾是一项值得研究的课题,也是急需解决的消防安全问题。
本文从锂离子电池的构造原理、制作工艺、工作机理出发,分析其火灾风险性和热失控火灾调查要点,提出其热失控防范措施,从而来提升火灾防范能力。
钦州市消防救援支队浦北大队唐彪广西钦州 535000摘要:锂离子电池具有火灾爆炸燃烧危险特性,燃烧时会产生高温毒气,发生火灾后一旦处置不当,后果极为严重,还可能会造成人员伤亡。
因此,如何防范锂离子电池火灾是一项值得研究的课题,也是急需解决的消防安全问题。
本文从锂离子电池的构造原理、制作工艺、工作机理出发,分析其火灾风险性和热失控火灾调查要点,提出其热失控防范措施,从而来提升火灾防范能力。
关键字:锂离子电池热失控火灾调查防范对策引言:随着科学技术的迅猛发展和能量运用方式的逐渐改变,传统插电式设备逐步进步到储能系统式设备,加之锂电池制造及充放电技术、检测技术逐渐成熟,锂电池应用进入高速发展期。
使用锂电池及其产品越来越常见于大众日常生活中的每个角落,小到可携式的电子产品如手机、笔记本电脑、移动式电源、手表、耳机、相机等数码产品,大到交通运输工具如电动自行车、电动汽车、太阳能及风力发电的储能柜等,成为新能源和储能领域的生力军。
随着国家大力推广绿色能源发展,储能式系统必将会是未来建设与相关产业发展的趋势。
近年来,全球各国都强力推行节能减碳政策,锂离子电池凭借能量密度高、自放电率低和循环寿命长等优点而广泛应用于轻便类电子设备和储能系统等领域,未来全球锂电池市场还将持续保持迅猛增长的势头。
但由于锂离子电池主要由易燃电解液和活性电极材料组成,在滥用条件下很容易引发电池自放热反应导致电池热失控,从而酿成火灾事故。
影响锂离子电池储存时电压降较大的因素
影响锂离子电池储存时电压降较大的因素
发布日期:2012-06-27
电池内部存在的微短路、电极材料的副反应以及电极材料间的反应可能导致电池在储存中(特别是60℃的高温下)电压降较大,即电池的自放电较大。
一、电池内部的微短路
下列原因可能造成电池的微短路:
1、集流体的毛刺刺穿隔膜;
2、粘合剂用量不够或粉体材料润湿不好,造成涂层与集流体粘接牢度不够,涂层剥落而刺穿隔膜;
3、浆料中存在大颗粒粉体,在电池抽真空后对隔膜的局部过压造成隔膜破裂;
4、隔膜的宽度设计不当。
二、电池材料的副反应
电池材料(包括电解液)在高温下可能存在正常的电化学反应之外的副反应。
三、电池材料间的化学反应
在高温和一定的电压下,电池材料间可能会发上额外的化学反应。
四、电池材料
无论采用何种活性材料、导电剂、电解液和粘合剂,如果存在上述隐患,都有可能出现电池储存时电压降过大的问题。
在正常情况下使用LA型水性粘合剂,不会出现电池储存时电压降过大的问题,即LA型水性粘合剂材料本身不会形成较大的自放电。
五、事例
1、某电池厂所生产的容量型消费电子产品电池(以LA132为粘合剂),在0.2C情况下充满电并在60℃下储存,发现电压降较大,并且相同批次电池的电压降情况较为一致。
通过仔细分析和查找原因,更换电解液解决了电池在60℃下储存电压降较大的问题。
2、某电池厂所生产的倍率型消费电子产品电池(以LA133为粘合剂)在储存时发现电压降较大,但同一批次电池的电压降情况存在较大差异。
通过仔细分析和查找原因,发现由于粘合剂使用量较少,涂层与集流体粘接牢度不够,导致涂层剥离而刺穿隔膜,形成微短路,致使电池储存时电压降较大。
锂电池自放电的原因及控制手段
【技术π】锂电池自放电的原因及控制手段编者按物理微短路是造成锂电池低压的直接原因,其直接表现是电池在常温、高温存储一段时间后,电池电压低于正常截止电压。
与化学反应引起自放电相比,物理微短路引起的自放电是不会造成锂电池容量不可逆的损失的。
【文/锂电派】锂电池由于受到电解液适配性、石墨负极特性、装配不一致等原因,常常会在使用或存放过程中出现电压下降的现象。
电压下降,很大一部分原因是电芯自身的自放电引起的。
电池自放电大小可以用两种形式来表示:一是用每天电压下降了多少mV来衡量,单位便是mV/天,好的电池一天压降不会超过2mV;另外一种也是常用的K值表示法,即单位时间内压降多少,也就是mV/h,一个小时电压下降了多少mV,好的电池K值一般都在0.08mV/h以内。
K=OCV2-OCV1/△T一、引起自放电的原因引起锂电池自放电过大的原因有二:物理微短路和化学反应。
下面将对两个原因进行分析:1、物理微短路物理微短路是造成锂电池低压的直接原因,其直接表现是电池在常温、高温存储一段时间后,电池电压低于正常截止电压。
与化学反应引起自放电相比,物理微短路引起的自放电是不会造成锂电池容量不可逆的损失的。
引起物理微短路的情况很多,分为如下几种:a、粉尘和毛刺我们将微短路的电池拆开,经常发现电池的隔膜上会出现黑点。
如果黑点的位置处于隔膜中间,那么便大概率是粉尘击穿。
如果黑点处于边缘位置占多数,便是极片分切过程中产生的毛刺引起的,这两点比较好辨别。
b.正负极的金属杂质在电池中,金属杂质发生化学和电化学腐蚀反应,溶解到电解液中:M →Mn+ + ne-;此后,Mn+迁移到负极,并发生金属沉积:Mn+ + ne-→M;随着时间的增加,金属枝晶在不断生长,最后穿透隔膜,导致正负极的微短路,不断消耗电量,导致电压降低。
①正极金属杂质正极的金属杂质经过充电反应后,也是击穿隔膜,在隔膜上形成黑点,造成了物理微短路。
一般来说,只要是金属杂质,都会对电池自放电产生较大影响,一般是金属单质影响最大。
- 1、下载文档前请自行甄别文档内容的完整性,平台不提供额外的编辑、内容补充、找答案等附加服务。
- 2、"仅部分预览"的文档,不可在线预览部分如存在完整性等问题,可反馈申请退款(可完整预览的文档不适用该条件!)。
- 3、如文档侵犯您的权益,请联系客服反馈,我们会尽快为您处理(人工客服工作时间:9:00-18:30)。
锂电池内部微短路控制方法
1锂电池内部微短路成因分析
2006年,锂电池巨头索尼公司的锂电池造成数起戴尔牌笔记本电脑爆炸起火,引起美、日官方的重視。
稍后,尽管采用了非常安全的A123磷酸铁锂电池,美国的丰田普锐斯混合动力汽车经第三方改装后在行驶时烧毁。
2011年,在杭州、上海及深圳都有新能源出租车及大巴烧毁事件。
显然,即使采用锂电池家族中最安全的磷酸铁锂体系,依然无法避免安全事故的发生。
从化学原理上进行分析,锂电池的安全性比汽油还差。
汽油储存在密闭的金属容器内,如果不同时发生泄漏(汽油和空气接触)和遇到明火(或者火星,引发作用)这两个条件,是非常安全的;而锂电池的能量则储存于一层薄薄的隔膜两侧,氧化剂(正极活性物质)、还原剂(负极活性物质)在发生内部短路(引发作用)的情况下,将同时发生剧烈的化学反应和电化学反应,急剧发热,并可能起火、燃烧、爆炸,对于有机溶剂体系的锂电池来说就更容易燃烧一些。
在锂电池的众多失效模式中,单体电池内部短路无疑危害最大,最难以预测和分析,没有办法通过外部控制电路来进行保护。
内部短路造成的高温、高阻、还很容易造成电池组的连锁反应。
目前广泛认为单体电池内部短路的原因可能有:
1)吸附在隔膜表面或者单体电池壳体顶部、底部的粉尘。
制造环境、工艺控制不良的情况下,会形成大量的正/负极片粉尘和焊接引起的金属粉尘,并通过静电作用吸附在隔膜表面。
极片本身不够光滑,粉体粘结强度不够,本身也会造成这种问题。
2)卷绕/叠片时形成的正/负极片错位。
3)金属焊点、极片边缘有毛刺。
4)隔膜两侧形成锂枝晶,由于不均匀反应造成的局部电化学反应或过充电而形成锂枝晶。
5)电解液分布不均匀造成正/负极片利用率不一致。
6)材料本身的问题。
材料纯度不高、与电解液相容性不好、正极金属材料不耐高电压、负极金属材料与锂形成合金,都可能形成杂质沉积或锂枝晶。
7)外部因素。
外部机械力的作用导致单体电池壳体变形并进而导致隔膜移位、破损,外界温度过高导致隔膜过度收缩、破损,过充电、强制放电造成单体电池内部形成锂枝晶,都可能造成内部短路。
2锂电池内部微短路的模拟试验方法
鉴于内部微短路对锂电池安全的严重威胁,国际和国内各种锂电池安全标准设计了很多相应的内短路模拟测试项目。
这些模拟的测试方法主要有平板挤压法、圆柱挤压法、针刺、重物撞击、金属填埋法等等,其中金属填埋法是在日本锂离子电池在笔记本电脑中出现自燃后所诞生的新方法,目前主要用于二次电池。
日本的JIS标准和美国的NASA标准采用了金属填埋法,将微小的金属片预先放置于单体电池内部扎穿隔膜,考察锂电池在发生内部短路的情况下的安全性,非常直接。
但是此法本身具备很大的危险性,最好采用机器人操作的方式。
重物撞击是一种模拟内部短路的测试方法,一般是在电池上方放置一根金属圆棒,然后利用重物撞击此金属圆棒,造成电池壳体变形产生内部短路。
与挤压法一样,该法也存在一个不均衡的问题,即对壳体薄的电池不利,但事实上壳体薄的电池在发生内部短路时反而会安全一些。
枪击试验是将电池放置在大于25m距离的位置上,然后用枪射击造成电池内部短路。
此法为GJB 2374所创,除了我国的军用标准,其他的一般标准中没有此项目。
针刺试验是在电池中插入一金属针,直接造成电池内部的正负极接触短路,过于激烈,不能很好地模拟内部微小的短路情况,因为成品电池中往往不会出现这种激烈的内部短路,如果存在的话早已在制造过程中就被发现了。
针刺试验方法被1995版本的美国UL1642标准
所采用,但在后续UL 1642版本中都删除了这一试验方法。
而正在研制中的UL 2580,可能采用较为温和的钝针刺来模拟内部微短路,这种试验更接近微短路的真实情况。
挤压试验是常用的模拟内部微短路的方法,绝大部分电池安全标准中都有这种方法,但是挤压的方法差别非常大,主要有平板挤压法和圆柱挤压法等等,最新的IEC 62660-2:2010中关于挤压试验的方法,则可以看成是综合吸收了平板挤压法、圆柱挤压法、针刺、重物撞击、金属填埋法的优点而设计的一种方法。
我国在修订GJB 2374A的研讨过程中,考虑到现有技术中有些电池使用平板挤压法无法实施挤压、用圆柱挤压法又对微短路出现标准不清的情况,采用了平板挤压法和圆柱挤压法多种选项,根据实际电池情况选择确定,其中把电池电压的突变作为发生微短路现象的标志,这基本上是合理的。
3锂电池内部微短路危害控制方法
锂电池内部微短路危害控制必须从单体电池设计、材料选择、环境工艺控制等诸多方面来防止内部微短路。
此外,为了将单体电池的内部短路造成的影响控制在最小范围,不至于造成连锁反应,还必须在电池组的设计中注意以下问题。
1)单体电池过热隔离装置
单体电池过热隔离装置可以在单体电池发生内部短路或外力撞击时起到隔离作用,停止电池组对失效单体电池的充电/强制过放电作用,并防止失效单体电池的高温、火焰、爆炸物引起相邻单体电池的连锁放应,从而起到阻断作用。
2)单体电池连接措施
电池组中单体电池的电学连接措施(例如电线、镍带、固定螺丝)的脱落或虚焊会使局部电阻过高,造成脱落点区域的高温,并引起临近单体电池的内部短路。
3)尽量减小单体电池的能量
一般认为单体电池的能量越大,成组电池串并联的数量就越少,可靠性越高,这从串并联成组的可靠性分析来说是正确的。
但是如果单体电池的能量过大,一旦出现失控反应后对电池组的破坏力就越大,从原理上来说就越容易产生整个电池组的连锁反应,造成不可控的局面。
因此选择合适的单体电池能量设计是很重要的。
4)单体电池的串并联方式
单体电池的串并联方式、数目也对单体电池的内部短路、连锁反应有着很大的影响。
例如,串联容易造成某个单体电池强制放电,并联容易造成某个单体电池强制充电,都可能造成单体电池的内部压力、电流过大,从而形成内部短路。
这需要在单体电池的一致性方面和电池组的对称性设计方面多做研究和改进。
5)温度控制系统
需要利用温度控制系统将单体电池、电池组的温度控制在安全的范围内以保障安全性。
温度监控系统、强制风冷、水冷、油冷都已经有应用的实例,并以逐步出现在相应的标准中。