超精密切削加工技术探析
机械工程中的超精密加工与表面工程研究

机械工程中的超精密加工与表面工程研究近年来, 机械工程领域的超精密加工与表面工程研究取得了重要的进展。
随着科技的不断发展,人们对机械加工的要求越来越高,需要更加精细、精确的加工技术来满足不同领域的需求。
超精密加工与表面工程研究就是针对这一需求而发展起来的。
超精密加工技术是机械工程中的一项关键技术,它通过运用高精密的工具和设备,采用微细切削或其他物理、化学手段,对工件进行加工。
超精密加工过程中,要求加工诸元素的误差控制在亚微米、纳米乃至更小的尺度上。
这种高精度的加工方法可以用于制造电子元件、光学仪器、精密仪器等各种高精度设备。
同时,超精密加工技术在飞机、汽车等交通工具制造以及军事、医疗等领域也有广泛的应用。
超精密加工技术的研究与应用离不开表面工程的支持。
表面工程是指改变物体表面形貌、组织结构或化学性质的技术。
在机械工程领域,表面工程常用于提高零件的抗腐蚀性、磨损性和减摩性等性能,以及实现零件的精密加工。
表面工程研究的主要内容包括表面涂层技术、微细加工技术、表面改性技术等。
在超精密加工与表面工程研究中,一种常用的方法是利用光学干涉技术来测量和控制工件的形状和尺寸。
光学干涉是指两束或多束光波相互干涉形成干涉条纹的现象。
通过分析干涉条纹的形态和位置,可以准确测量出工件的尺寸和形状误差,并及时调整加工工艺,从而实现高精度的加工控制。
光学干涉技术在超精密加工与表面工程中的应用不仅提高了加工质量和效率,还降低了成本和浪费。
另外,超精密加工与表面工程研究还重视对切削力、热变形、金属材料的变形行为等物理现象的探究。
了解这些现象有助于优化机械加工过程,减少误差和损耗。
超精密加工和表面工程的研究还涉及到材料的选择与设计,包括材料的力学性能、热性能、化学性能等方面的考虑。
选择合适的材料可以提高加工的精度和效率,降低成本和资源消耗。
在超精密加工与表面工程研究中,还有一个重要的方向是发展全自动化或智能化的加工设备和系统。
应用先进的控制技术和传感器技术,实现机械加工过程的自动化和高效化,提高产品的一致性和稳定性。
超精密切削加工主要指金刚石刀具的超精密切削

超精密切削加工主要指金刚石刀具的超精密切削。
超精密切削的工作机理:普通的切削的切削深度一般远大于材料晶粒的尺寸,切削加工以数十计的晶粒团为加工单位,在切削力的作用下从基体上去除金属。
而超精密加工的切削层很薄或尺寸很小,切削深度和进给量必然很小,特别是亚微米和纳米级的超精密切削,切削深度通常小于材料晶粒直径,使的切削只能在晶粒内部进行。
超精密切削时的切削力的特征为:切削力微小,单位切削力很大,切削力随着切削深度的减小而增大,而在切深很小时切削力却急剧上升。
超精密切削加工的特点与应用(1)单位切削力大实现纳米级的超精密加工的物理实质是切断材料的分子、原子间的结合,实现原子或者分子的去除,因此切削力必须超过晶体内部的分子、原子结合力。
(2)切削温度由于超精密切削的切削用量极小以及金刚石刀具和工件材料具有的高导热性,因此超精密切削温度相当低。
(3)刀刃圆弧半径对最小切削厚度的限制刀具刃口半径限制了其最小的切削厚度,刀具刃口越小,允许的最小切削厚度也越小。
超精密切削的应用超精密加工主要用于加工软金属材料以及光学玻璃、大理石和碳素纤维板等非金属材料,主要加工对象是精度要求很高的镜面零件。
(下图是超精密切削球面镜的加工原理图)球面镜的加工原理1-主轴;2-凹面镜;3-刀具轴超精密磨削超精密磨削是当代能达到最低磨削表面粗糙度值和最高加工精度的磨削方法。
超精密磨削去除量最薄,采用较小修整导程和吃刀量来修整砂轮,是靠超微细磨粒等高微刃磨削作用,并采用较小的磨削用量磨削。
超精密磨削要求严格消除振动,并保证恒温及超净的工作环境。
超精密磨削的光磨微细摩擦作用带有一定的研抛作用性质。
1.超精密砂轮磨削的磨削超精密砂轮磨削机理:( 1 ) 超微量切除超精密磨削是一种极薄切削,切屑厚度极小,磨削深度可能小于晶粒的大小,磨削就在晶粒内进行,因此磨削力一定要超过晶体内部非常大的原子、分子结合力,从而磨粒上所承受的切应力就急速地增加并变得非常大,可能接近被磨削材料的剪切强度的极限。
机械加工中的超精密加工技术研究

机械加工中的超精密加工技术研究引言:机械工程和制造是现代工业领域中至关重要的一部分。
随着科技的不断进步,人们对机械加工的要求也越来越高,尤其是在超精密加工领域。
本文将探讨机械加工中的超精密加工技术研究,旨在进一步提升机械加工的精度和效率。
一、超精密加工技术的定义和意义超精密加工技术是指在机械加工过程中,通过采用先进的工艺和设备,实现高精度、高效率的加工过程。
这种技术的出现,不仅可以满足现代工业对高精度零件的需求,还可以提高产品的质量和性能,从而推动整个工业的发展。
二、超精密加工技术的应用领域超精密加工技术广泛应用于航空航天、光学仪器、电子设备等领域。
例如,在航空航天领域,超精密加工技术可以用于制造发动机零件、航天器结构件等。
在光学仪器领域,超精密加工技术可以用于制造高精度的光学镜片、光学棱镜等。
在电子设备领域,超精密加工技术可以用于制造微电子器件、集成电路等。
三、超精密加工技术的关键技术1. 先进的加工设备:超精密加工需要使用高精度的加工设备,如数控机床、激光加工设备等。
这些设备具有高速度、高精度和高稳定性的特点,能够满足超精密加工的需求。
2. 先进的加工工艺:超精密加工需要采用先进的加工工艺,如喷射加工、电火花加工等。
这些工艺能够实现高精度、高效率的加工过程,提高产品的质量和性能。
3. 先进的加工材料:超精密加工需要使用高性能的加工材料,如高硬度的陶瓷材料、高强度的合金材料等。
这些材料具有优异的物理和化学性能,能够满足超精密加工的要求。
四、超精密加工技术的发展趋势随着科技的不断进步,超精密加工技术也在不断发展。
未来,超精密加工技术可能会朝着以下几个方向发展:1. 更高的精度:随着工业对高精度零件的需求不断增加,超精密加工技术需要进一步提高加工的精度,以满足市场的需求。
2. 更高的效率:超精密加工技术需要进一步提高加工的效率,以降低生产成本,并提高生产效率。
3. 更广泛的应用:超精密加工技术将进一步扩大应用领域,涉及到更多的行业和领域,如医疗器械、新能源等。
机械实习总结之精密和超精密加工技术学习总结心得

《精密和超精密加工技术》学习总结0.引言随着现代高科技的先进制造技术的发展,超精密加工技术应运而生,在现代高科技尖端产品的生产和开发中超精密加工技术是必不可少的关键技术,一个国家超精密加工技术的先进程度,直接影响着一个国家的制造业水平,是先进制造技术基础和关键,不管是在军事领域还是日常生活中,超精密加工技术都有着极其广阔的发展空间,对于任何一个国家的发展而言,发展超精密加工技术都是势在必行的[1]。
1.超精密切削超精密切削技术是在上世纪60年代发展起来的技术,在国防和尖端技术的发展中扮演着极其重要的角色,超精密切削技术主要是指金刚石超精密切削技术,其中包括金刚石超精密车削技术和金刚石超精密铣削, 使用的刀具是天然单晶金刚石刀具,其切削刃可磨得非常锋利[2]。
超精密切削技术是超精密加工技术的重要分支,是最早发展的超精密加工技术,在多个领域中均有运用到该项技术。
金刚石超精密加工的切削深度一般在微米量级,可加工出微米及亚微米级的形状精度及纳米级表面粗糙度的精密工件,在符合条件的机床和环境条件下,表面粗糙度Ra0.02-0.005Mm,精度<0.01Mm。
不同的背吃刀量、不同的进给量和不同的切削速度对加工表面粗糙度都有着不同程度的影响。
通过用两把几何角度相同的金刚石车刀,当在不同的背吃刀量下加工工件,可发现切削刃锋锐度对加工表面粗糙度影响最为明显;在不同的进给量下,锋锐的金刚石车刀加工表面粗糙度较小,二者差别明显;而在不同的切削速度下,两把车刀切出的加工表面粗糙度差别不大,可知切削速度对加工表面粗糙度影响不大。
金刚石刀具根据其切削刃的形状可以分为圆弧刃和直线刃,其中圆弧刃可用于加工各种形状的工件,尤其适用于加工复杂曲面的工件;而直线刃主要用于加工平面、柱面以及锥面等简单规则形状的工件, 就切削阻力而言,直线切削刃比圆弧切削刃的切削阻力要小,在尺寸精度和表面粗糙度方面更易于控制,并且制造容易、研磨方便, 直线切削刃在高品质、高精度加工方面有着不可替代的优势,当然,直线切削刃也有其不足之处,直线切削刃比较难安装调整。
超精密加工技术的发展及对策
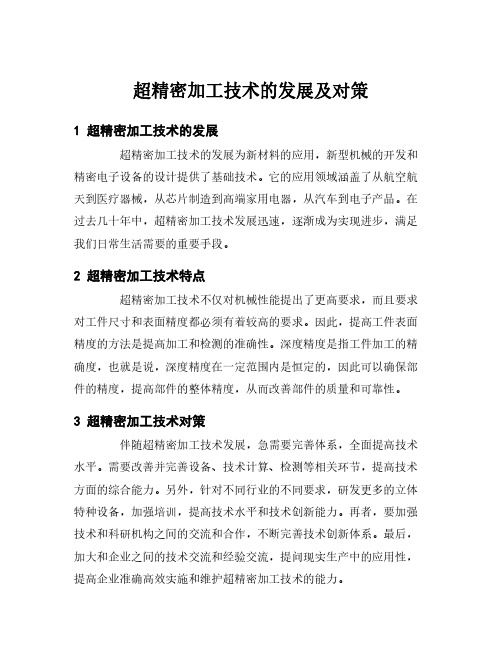
超精密加工技术的发展及对策
1超精密加工技术的发展
超精密加工技术的发展为新材料的应用,新型机械的开发和精密电子设备的设计提供了基础技术。
它的应用领域涵盖了从航空航天到医疗器械,从芯片制造到高端家用电器,从汽车到电子产品。
在过去几十年中,超精密加工技术发展迅速,逐渐成为实现进步,满足我们日常生活需要的重要手段。
2超精密加工技术特点
超精密加工技术不仅对机械性能提出了更高要求,而且要求对工件尺寸和表面精度都必须有着较高的要求。
因此,提高工件表面精度的方法是提高加工和检测的准确性。
深度精度是指工件加工的精确度,也就是说,深度精度在一定范围内是恒定的,因此可以确保部件的精度,提高部件的整体精度,从而改善部件的质量和可靠性。
3超精密加工技术对策
伴随超精密加工技术发展,急需要完善体系,全面提高技术水平。
需要改善并完善设备、技术计算、检测等相关环节,提高技术方面的综合能力。
另外,针对不同行业的不同要求,研发更多的立体特种设备,加强培训,提高技术水平和技术创新能力。
再者,要加强技术和科研机构之间的交流和合作,不断完善技术创新体系。
最后,加大和企业之间的技术交流和经验交流,提问现实生产中的应用性,提高企业准确高效实施和维护超精密加工技术的能力。
随着科技的进步,超精密加工技术在日常生活中起到了重要的作用,它的发展能够直接带来更佳的生活质量。
同时为了更好的发展,要加强技术支持,提升技术水平,增加技术的应用性,从而让超精密加工技术发挥更大的作用。
超精密切削加工技术

刀具锋锐性
• 刀具锋锐性主要取决于刃口钝圆半径,刃口钝圆 半径越小刀具越锋锐,有效切削厚度就越小,对 加工表面变质层和毛刺的影响也会减少。精密刀 具刃口钝圆半径可达到20nm以下。而金刚石刀具 刃口圆角半径可达2~4nm,切削厚度可达1nm。 • 如果复映正常,刃口粗糙度将决定表面粗糙度的 极限。研磨金刚石刀具表面达到nm级并不困难, 使切削可达到nm级的表面质量。
材料热特性对动态变形一致性的影 响
• 刀具切削部位的动态弹性变形要一致,否 则会产生基于材料杂质和晶界的表面阶梯。 • 材料较好的热稳定性和进行适当的热处理, 将使之均匀化,阶梯平均化,获得光滑的 加工表面。
加工环境与边缘技术是不可忽视的 间接因素
①环境温度 • 环境温度影响加工精度有两个方面,一是 温度的高低,二是温度场的均匀性。 • 机床自身局部发热的原因是轴承及运动部 分的摩擦与润滑,有一个热平衡过程。 • 人体及其运动,室内空气的对流都会引起 环境发生0.001K的温差变化。照明灯辐射 到花岗石底座,黑白点材料之间亦有0.1K 的差别。
③机床的热变形
• 理论上提高温度的控制精度就能减少热变形量。 控制精度达到1mk,热变形就可控制在1~10nm /m之间。 • 超精密切削机床结构采用铟钢、某种玻璃、陶瓷 等热膨胀系数较低(10-6~10-7/K)材料,能 有效减少自身的热变形量。床身可采用花岗岩材 料。 • 机床(包括刀具)与工件的热变形之间存在着某 种关系,也会对加工精度的界限产生重要的影响。 • 尽管在整体上要求控制温度到一定的精度,但在 不同部分和不同阶段总会有差别的,因此需要进 行热补偿,通过机床调整和软件控制其影响。
金刚石刀具材料
• 优质的单晶金刚石刀具SPDT技术是实现超 精密切削的关键技术。 • 通常的人造单晶金刚石无法磨出极锋锐的 刃口,ρ很难达到≤1μm,只能用于有色金 属和非金属的精密切削,很难达到超精密 镜面切削的要求。 • 大颗粒人造单晶金刚石已能用于工业生产, 并已开始用于超精密切削,但价格仍很昂 贵。
超精密加工技术详解

超精密加工技术——试论述AFM,接触式粗糙度测量仪及白光干涉仪对表面粗糙度的测试原理及应用范围1.1 AFM对表面粗糙度的测试原理AFM 是一种类似于STM 的微观技术,它的许多元件和STM是共同的,如用于三维扫描的电压陶瓷系统以及反馈控制器等。
它和STM 最大的不同是用一個对微弱作用力极其敏感的微观臂针尖代替了STM隧道针尖,并以探测原子间的微小作用力(Vander Walls’ Force)代替了STM 的微小穿透电流。
因为这样所以AFM 不在像STM 局限于样品必须为导体才行,AFM 适用于导体和非导体,它的应用范围比STM 广泛的多,因此AFM为目前最被广泛应用在工业界的扫描探针式显微术。
但值得注意的是AFM 的解析度并沒有STM 来的的好!AFM的探针,一般是利用半导体工业的平面制程方法一体成行的。
为了使探针有原子级的解析度,探针乃呈角锥形,使顶端只具有一颗或数颗稳定原子;为使探针具高灵敏的原子力感应度,角锥形探针底部乃连接与一杠杆的前缘,此杠杆弯曲程度将反映出原子力的大小。
为测量弯曲度的大小,常用的方法是打一雷射光与悬臂上,而反射回來的雷射光則利用一能区分光点位置的感光二极体来接收,如此便能得到悬臂受原子力弯曲的程度,进而得到原子力图像。
(AFM工艺由美国与萨诸塞州Dynetics公司开发的Dynaflow磨料流加工工艺(AFM)是一种强迫含磨料的介质在工件表面或孔中往复运动的金属精加工工艺, 它具有广泛的应用前景。
AFM当最先出现时, 它主要用于清除金属件中难于到达的内通道及相交部位的毛刺。
它特别适用于加工难加工合金材料制成的结构复杂的航空元件。
近年来, 它已被用于精加工流体动力元件中表面粗糙度要求达0.127µm的不能接近的内表面。
AFM的基本原理:介质速度最大时, 磨光的能力也最大。
这里, 夹具的结构起着重要作用, 它决定着介质速度在何处最大。
夹具用于使工件定位和建立介质流动轨迹, 是精加工所选择部位而不触及相邻部位的关键所在。
超精密切削加工技术介绍

超精密切削加工技术介绍
超精密加工技术是适应现代高科技的需要而发展起来的先进制造技术, 是高科技尖端产品开发中不可或缺的关键技术, 是一个国家制造业水平重要标志, 是先进制造技术基础和关键, 也是装备现代化不可缺少的关键技术之一, 在军用和民用工业中有着十分广阔的应用前景。
金刚石超精密切削技术, 是超精密加工技术发展最早的、应用最为广泛的技术之一。
超精密切削加工技术
1、超精密切削的历史
60年代初,由于宇航用的陀螺,计算机用的磁鼓、磁盘,光学扫描用的多面棱镜,大功率激光核聚变装置用的大直径非圆曲面镜,以及各种复杂形状的红外光用的立体镜等等,各种反射镜和多面棱镜精度要求极高,使用磨削、研磨、抛光等方法进行加工,不但加工成本很高,而且很难满足精度和表面粗糙度的要求。
为此,研究、开发了使用高精度、高刚度的机床和金刚石刀具进行切削加工的方法加工。
2、超精密切削加工的应用
(1)平面镜的切削
平面度
金刚石刀具
1、金刚石刀具特点
金刚石刀具拥有很高的高温强度和硬度,而且材质细密,经过精细研磨,切削刃可磨得极为锋利,表面粗糙度值很小,因此可进行镜面切削。
金刚石刀具超精密切削主要用于加工铜、铝等有色金属,如高密度硬磁盘的铝合金基片、激光器的反射镜、复印机的硒鼓、光学平面镜,凹凸镜、抛物面镜等。
超精切削刀具材料有天然金刚石,人造单晶金刚石。
金刚石刀具磨损的常见形式为机械磨损和破损。
机械磨损——机械摩擦、非常微小;破损。
- 1、下载文档前请自行甄别文档内容的完整性,平台不提供额外的编辑、内容补充、找答案等附加服务。
- 2、"仅部分预览"的文档,不可在线预览部分如存在完整性等问题,可反馈申请退款(可完整预览的文档不适用该条件!)。
- 3、如文档侵犯您的权益,请联系客服反馈,我们会尽快为您处理(人工客服工作时间:9:00-18:30)。
用 的 区 域 ) 是 加 工 单 位 , 工 单 位 的 大 小 和 材 料 缺 陷 分 布 切 削 刃钝 圆 圆 弧 上 某 一 质 点 A 的受 力 情 况 见 图 。该 点 有 切 就 加 的尺 寸 大 小 不 同 时 , 加 工 材 料 的 破 坏 方 式 就 不 同 。 被 向分 力 F 和 法 向 分 力 F , 力 为 F , 。切 向 分 力 使 质 点 z y合 yZ 向前 移 动 , 成 切 屑 ; 向 分 力 使 质 点 压 向 被 加 工 表 面 , 形 法 形 2 超精 : 精 密 切 削加 工 主 要 是 由 高精 度 的 机 床 和 单 晶 金 刚 石 刀 具 进 行 的 , 一 般 称 为金 刚 石 刀 具 具 切 削 或 S D 超 故 P T。
对 超 精 密 切 削加 工 技 术 及 其 机 理 进 行 介 绍 和 总 结 , 望 对 超 精 密加 工 行 业 同事 有 所 指 导 。 希
21 年第 6 01 期
1 2 材 料 缺 陷 及 其 对 超 精 密 切 削 的 影 响 .
2 2 金 刚 石 刀 具 超 精 密 车 削 的切 屑 形 成 . 金 刚 石 刀 具 超 精 密 车 削 是 一 种 原 子 、 子 级 加 工 单 位 分 金刚石 刀具超精密车削所 能切 除金 属层 的厚度 标志其 的去 除 ( 离 ) 工 方 法 , 从 工 件 上 去 除 材 料 , 要 相 当 大 加 工 水 平 。 当 前 , 小 切 削 深 度 可 达 0 1微 米 以 下 , 主 要 分 加 要 需 最 . 其 的能 量 , 种 能 量 可 用 临 界 加 工 能 量 密 度  ̄ J c ) 单 位 影 响 因素 是 刀 具 的锋 利 程 度 , 般 以 刀 具 的 切 削 刃 钝 圆 半 这 (/ m3 和 一
N o. 201 6, 1
现代 商贸工业 Mo enB s es rd d s y dr ui s T aeI ut n n r
21 0 1年 第 6期
超 精 密 切 削 加 工 技 术 探 析
邓 志博
( 安 航 空 职 业 技 术 学 院 , 西 西 安 70 8 ) 西 陕 1 0 9
体 积 切 削 能 量 o Jc ) 表 示 。临 界 加 工 能量 密 度 就 是 当 径 rt 表 示 。超 精 密 车 削 所 用 的 金 刚 石 车 刀 , 切 削 刃 钝 , /m3 来 ( u来 其 应 力 超 过 材 料 弹性 极 限 时 , 切 削 相 应 的 空 间 内 , 于 材 料 圆半 径 一 船 小 于 0 5微 米 , 切 削 时 的切 削 深 度 a 在 由 . 而 p和 进 给 缺 陷 而 产 生 破 坏 时 的 加 工 能 量 密 度 ; 位 体 积 切 削 能 量 则 量 f 单 都很 小 , 因此 , 在一 定的切削刃钝 圆半 径下 , 如果切 削深
可 能足够好 , 样在 高应 力和 高 温下 会快 速磨 损 和软 化 , 这 不 能 得 到 真 正 的 镜 面 切 削 表 面 。 而 金 刚 石 刀 具 却 有 很 好 的 高 金刚石 刀具超 精 密 切 削属 微 量 切 削 , 机理 和普 通切 其 能保 持 很 好 的 切 削 性 能 , 不 被 软 化 和 而 削有 较 大 差 别 精 密 切 削 时 要 达 到 0 1微 米 的 加 工 精 度 和 温 强 度 和 高 温 硬 度 , .
2 3 优 化 施 工 组 织 设 计 。 学 有 序 施 工 . 科
参 考 文 献
将 原 设 计 全 线 开 工 的 施 工 方 案 调 整 为 分 段 施 工 , 取 E 3刘 蜀 岷 . 于水 利 工程 项 目管 理 的探 讨 [ . 采 1 关 u] 东北 水 利 水 电 2 1 , 0 0 ( 1. 5 ) 改变 工程布局 、 桥 、 化 路 面等 措施 , 仅缓 解 了通 行压 架 硬 不
1 1 切 削 厚 度 与 材 料 切 应 力 的 关 系 .
Ra. 1 米 的 表 面 粗 糙 度 , 具 必 须 具 有 切 除 亚 微 米 级 以 OO 微 刀
磨损 。
参 建 各 方 之 间 的 沟 通 , 调 团 结 协 作 精 神 , 到 及 时 了 解 工 初 检 、 工 队 复 检 、 检 科 终 检 的 “ 检 制 ” 序 进 行 。 监 理 强 做 施 质 三 程 程 进 展 情 况 和 出 现 问 题 能 够 及 时 处 理 ; 强 内 部 规 章 制 度 单位 制定 了详 细 的监 理 规 划和 细 则 , 对 工 程 建设 中 易 出 加 针
是 指 在 产 生 该 加 工 单 位 切 削 时 , 耗 在 单 位 体 积 上 的 加 工 度 太 小 , 可 不 能 形 成 切 屑 。切 屑 能 否 形 成 主 要 取 决 于 切 消 则 能 量 。从 工 件 上 要 去 除 的 一 块 材 料 的 大 小 ( 削 应 力 所 作 削 刃 钝 圆 圆 弧 处 每 个 质 点 的 受 力 情 况 , 自 由 切 削 条 件 下 , 切 在
3 结 论
从工 程招标 并 签 订 相关 合 同 、 工 请 示 、 目划 分 、 开 项 各 应 急 调 水 工 程 是 一 项 事 关 全 局 , 系 错 综 复 杂 的 系 统 关 阶段验收 , 程 建设 的每一个 阶 段都 按规 定 的程 序进 行 , 工 每 工 程 , 织 保 障 是 顺 利 实 施 的 前 提 基 础 , 程 建 设 各 方 各 司 组 工 个 程序都 按有关规 定和规 范实 施 ; 时掌 握 工程 建设 进度 , 其 职 、 力配 合是 成 功 的关 键 因素 , 过 优 化组 织 设 计 , 及 通 通 科 监 理 处 每 5天 通 报 工 程 建 设 进 度 , 提 供 进 度 报 表 , 涉 及 学 有 序 施 工 , 取 工 程 相 关 体 的 理 解 和 支 持 , 而 实 现 工 程 并 对 获 进 进 度 的重 大 问 题 , 时 组 织 各 方 参 加 进 度 协 调 会 , 析 原 的 顺 利 完 成 和 实 施 。 及 分 因 , 出 赶 工 措 施 , 确 保 进 度 目标 的 实 现 。 提 以
建 立 了 由施 工 单 位 质 量 保 证 、 理 单 位 质 量 控 制 、 目 监 项
[]王卓甫 , 5 简迎辉. 工程项 目管理 : 模式及其创 新E . M3 北京 : 中国水
法 人 质 量 检 查 和 政 府 机 构 质 量 监 督 四 个 层 次 组 成 的 质 量 管 利 水 电 出 版社 , 0 . 20 6 理 体 系 。各 施 工 单 位 均 配 备 了 专 职 质 检 员 , 立 了 完 善 的 E3刘 小 平 . 筑 工 程 项 目管 理 [ . 京 : 等教 育 出版 社 ,0 2 建 6 建 M] 北 高 20. 质 量 保 证 体 系 , 行 全 面 质 量 管 理 , 工 质 量 检 查 按 照 班 组 [ ]陆 惠 民 等. 程 项 目管 理 E . 推 施 7 工 M3 南京 : 南 大 学 出版 社 ,0 2 东 20.
1 金 刚 石 刀 具 切 削 的 机 理
大 。 当进 行 切 深 为 0 1微 米 的 普 通 车 削 时 , 切 应 力 只 有 . 其
0 MP ; . 切 超 精 密 切 削 加 工 主 要 是 由 高 精 度 的 机 床 和 单 晶 金 刚 石 5 0 a 当进 行 切 深 为 0 8微 米 的 精 密 切 削 时 , 应 力 约 为 O0M a 刀 刀具 进 行 的 , 一 般 称 为 金 刚 石 刀 具 切 削 或 S D Sn l 故 P T( ige 1 0 0 P 。 因 此 精 密 切 削 时 , 具 的 尖 端 将 会 产 生 根 大 的 尖 处 P it a n rig 。金 刚 石 刀 具 的 超 精 密 切 削 加 工 虽 应 力 和 很 大 的 热 量 , 端 温 度 极 高 , 于 高 应 力 高 温 的 工 作 on mo dTunn ) Di 状 态 , 对 于 一 般 刀 具 材 料 是 无 法 承 受 的 。 因 为 普 通 材 料 这 有 很 多 优 点 , 要 使 金 刚 石 刀 具 超 精 密 切 削 达 到 预 期 的 效 但 的 刀 具 , 刀 刃 的 刃 口不 可 能 刃 磨 得 非 常 锐 利 , 刃 性 也 不 其 平 果 , 不是 很简单 的事 , 多因素都对 它有影 响 。 并 许
2 0 ( ) 0 9, 3 .
法 提 水 灌 溉 , 此 , 过 开 挖 输 水 沟 渠 和 迁 建 临 时 泵 站 等 措 为 通
施 , 决 了这 2 0 余 亩 农 田的 灌 溉 问 题 。 解 00 2 4 建 立 完 善 的 质 量 保 证 体 系 。 行 全 面 质 量 管 理 . 推
作 者 简 介 : 志 博 ( 9 1 ) 男 , 西 乾 县 人 , 安 航 空职 业 技 术 学 院讲 师 , 究 方 向 : 械 制 造 。 邓 17一 , 陕 西 研 机
一
26 3 ~
No. 2Ol 6, l
现 代商 贸 工 业 M o enB s e rd n ut d r ui s T aeId s y ns r
建 设 , 订 完 善 的 内 部 管 理 制 度 , 到 事 事 有 章 可 循 , 制 制 做 按
现 质 量 问 题 的 重 点 环 节 , 持 旁 站 监 理 和 平 行 监 测 , 保 坚 确
“ 期 不 能 误 , 准 不 能 降 , 量 不 能 低 ” 工 标 质 。
度和程序 办事 。 2 2 严 格 遵 守 基 建 程 序 。 好 项 目实 施 阶 段 的 工 作 . 抓
[ 3高 家仓 , 波 云 . 利 工程 建设 项 目 管理 探 索 E .中 国新 技 术 新 3 马 水 U3
产 品 , 0 9, 1 1. 2 0 ( 5)
E 3中国人 民共和 国国务 院. 4 建设 工程 质量管理 条例 E 3 北京 : S. 中国