ISO 17636:2003中文版 焊缝的无损检验.熔焊接头的放射检验
ISO17637-2003 中-焊缝无损检测-目视检验
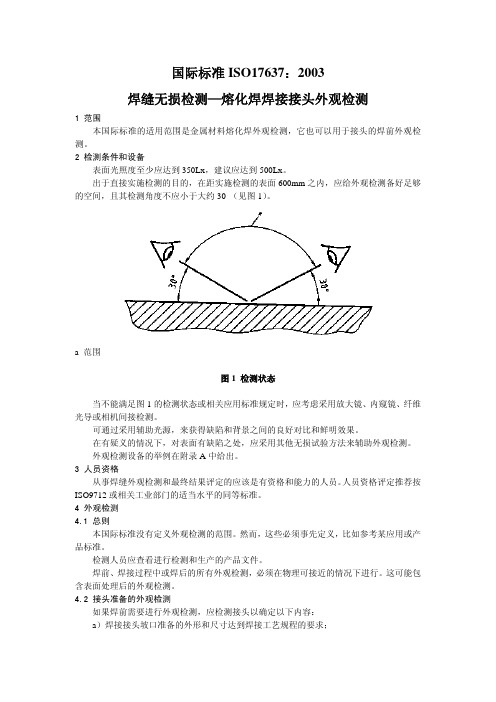
1 范围 本国际标准的适用范围是金属材料熔化焊外观检测,它也可以用于接头的焊前外观检
测。 2 检测条件和设备
表面光照度至少应达到 350Lx,建议应达到 500Lx。 出于直接实施检测的目的,在距实施检测的表面 600mm 之内,应给外观检测备好足够 的空间,且其检测角度不应小于大约 30°(见图 1)。
平焊缝
凹形
凸面
对接 焊缝
测量 范围
mm
读数 精度
mm
夹角或角 焊缝角度
夹角或角 焊缝允许
偏差
错边量钩状检查器具
测量板材和管材对接焊缝坡
—
—
—
X
0~100
0.05
—
—
口错边量。
万用对接焊缝测量器具
测量接头准备和完成的对接
焊缝:
1)坡口角度
2)根部间隙宽度
X
3)焊缝余高
4)焊缝表面宽度
5)咬边的深度
6)填充材料的直径
A.3 表 1 中详细列出了典型测量设备和量规。 注:这些设备和量规是检测设备的一个例子,其中的一些设计可能是注册的设计或专利。
焊缝量具
附录 A(资料性)检测设备举例
表 A.1 测量仪器和焊缝量具——测量范围和读数精度
焊缝类型
说明
平焊缝
角焊缝 凹形
凸面
对接 焊缝
测量 范围
mm
读数 精度
mm
夹角或角 焊缝角度
4.4.5 焊后热处理 焊后热处理之后可能需要进一步的检测。
4.5 修补焊缝外观检测 4.5.1 总则
如果焊缝不符合或部分符合合格标准且需要修补时,焊接接头须在重新焊接前根据 4.5.2 和 4.5.3 进行检测。
ISO17635:2003_焊缝的无损检测-金属材料熔化焊焊缝的一般原则

焊缝的无损检测—— 金属材料熔化焊焊缝的一般原则
1 范围
本标准给出了金属材料熔化焊无损检测方法选择指导,主要根据材料、焊缝 厚度、焊接工艺、质量控制细则和检测范围来选择。本标准规定了金属材料不同 检测方法应用的标准,以及方法选择活验收等级总则。测量方法可以单独(或组 合)使用。
本标准适用于下列材料及其合金(或其相互组合)的熔化焊焊缝的无损检测: ——钢铁; ——铝; ——铜; ——镍; ——钛。 注:本标准可用于其他金属材料的检测,但可能需要做进一步的规定。
6 人员资格
从事焊缝无损检验和最终结果评定的人员应具有资格和能力。人员资格的评 定建议按 ISO9712 或有关工业部门相应等级的类似标准。
Page 6 of 13
应用同一种方法。
8.2 检测后的文件
8.2.1 单独的检测记录 所有的检测结果应根据书面工艺规程或用于该方法的标准进行记录。 8.2.2 最终报告 对于每个被检构件或每组被检构件,其最终报告应包含检测计划所要求的信 息,至少包括如下: —构件标识; —被检焊缝标识和/或标识这些焊缝的文件编号; —实施检测的人员和机构标识; —根据按照相关检测标准编制的所有报告; —包含状态(没有检测、合格和不合格)在内的单独的检测记录; —应用的标准在检测技术和验收等级方面的偏差记录。
表面缺欠检查应在内部缺欠检测之前进行,一旦发现不合格表面缺陷,可以 将成本降到最低。
10.4 不合格缺陷
应规定处理不合格缺陷的规程,比如参考某个应用标准。 所有修复焊缝至少要按照原始焊缝的质量等级进行检测。 附录 D 给出了在不合格缺陷检查之后附加检测指南。
Page 9 of 13
附录 A (资料性附录)
本国际标准也给出了基于质量控制目的的无损检测结果评定导则,主要根据 材料、焊缝厚度、焊接工艺、质量控制细则和检测范围来选择。
ISO接头标准

塑料管和配件.电熔焊接头的自动识别系统
Plastics pipes and fittings - Automatic recognition systems forelectrofusionjoints
ISO 13953-2001
聚乙烯管材和管件拉申强度的测定和熔接对接接头试件的失效模型
IEC 62275-2006
电缆管理系统.电器设备用电缆接头
Cable management systems - Cable ties for electrical installations
ISO 10042 Technical Corrigendum 1-2006
焊接.铝和铝合金的弧焊接头.缺陷质量分级.技术勘误1
电熔焊接头的自动识别系统plasticspipesandfittingsautomaticrecognitionsystemsforelectrofusionjointsiso139532001聚乙烯管材和管件拉申强度的测定和熔接对接接头试件的失效模型polyethylenepepipesandfittingsdeterminationofthetensilestrengtandfailuremodeoftestpiecesfromabuttfusedjointiso146151997粘合剂结构型粘合剂粘结接头的耐久性荷载下暴露在湿度和温度之中adhesivesdurabilityofstructuraladhesivejointsexposuretohumidityandtemperatureunderloadiso14651989航空器液态氧充填接头相配尺寸aircraft
ISO 10955-1999
航空航天航空器操纵钢丝绳用末端接头和松紧套筒技术规范
ISO17637:2003_焊缝的无损检测-熔化焊接头的外观检验
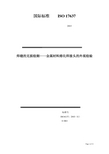
国际标准ISO 176372003焊缝的无损检测——金属材料熔化焊接头的外观检验标准号ISO4137:2003(E)© ISO目录1 范围 (3)2 检测条件和设备 (3)3 人员资格 (4)4 外观检验 (4)5 检测报告 (6)焊缝的无损检测——金属材料熔化焊接头的外观检验1 范围本标准规定了金属材料熔化焊焊缝的外观检验方法。
本标准也可用于焊接之前的接头外观检验。
2 检测条件和设备表面光照度至少应达到350LX,推荐采用500LX的光照度。
为了便于直接检查,在检查表面600mm,视角至少30°范围内,应为外观检测备好足够的空间(见图1)。
a 范围图1 检测范围当不具备图1规定的检测范围条件,或应用标准另有规定时,应考虑采用放大镜、内窥镜、纤维光导或相机做间接检查。
为了获得缺欠和背景之间良好对比和鲜明的效果,可采用辅助光源。
外观检验无法提供决定性结果时,应附加其他表面无损试验方法。
附录A给出了外观检验设备示例。
3 人员资格焊缝外观检验和最终结果评定应由具备资格和能力的人员进行。
人员资格的评定建议按ISO9712或有关工业部门相应等级的类似标准。
4 外观检验4.1 总则本国际标准不规定外观检验的范围。
外观检验范围应根据应用文件或产品标准事先规定。
检查人员应有条件获得必要的检验文件和产品文件。
所有焊前、焊接过程中或焊后的外观检验应在操作可达性条件下进行。
这可能包括含表面处理的外观检验。
4.2 坡口的外观检验要求做焊前外观检验时,应对接头做如下检查:a)焊接坡口的形状和尺寸满足焊接工艺规程的要求;b)熔化面和相邻表面是清洁的,根据应用标准或产品标准进行了所要求的表面处理;c)按照图样和工艺指令,对被焊工件进行了正确的固定。
4.3 焊接过程中的外观检验有要求时,在焊接过程应对焊缝进行如下检查:a)每条焊道或焊层被后续焊道覆盖前进行了清理,特别要注意焊缝金属和熔化面的结合处;b)无外观缺陷,比如裂纹或气孔;如果发现缺陷,应做记录以便在进一步焊接之前进行补救;c)焊道之间、焊缝与母材之间的过渡良好,便于下道焊缝熔合良好;d)为了保证能按照规定完整地去除焊缝金属,气刨的深度和形状应符合WPS要求,或与原始坡口大体一致;e)进行了所有必要的修复或补救措施之后,焊缝符合WPS的原始要求。
X射线探伤检测规程

X射线探伤检测规程一、依据及适用范围依据ISO17636:2003、ISO10675-1:2008标准和本公司设备的特殊性制定本操作规程,本规程适用于对焊缝进行无损检测射线探伤前应做的准备工作和射线探伤中全过程的管理。
二、探伤前工艺准备1.人员要求从事射线照相检验的人员必须持有国家有关部门颁发的,并与其工作相适应的资格证书。
无损检测人员应每年检查一次身体,校正视力不得低于1.0。
2.工件表面状态要求工件焊缝及热影响区表面质量应经焊接检验员外观检查合格,表面的不规则状态在底片上的图象应不掩盖焊缝中缺陷或与之相混淆(如溅物、油污、锈蚀、凹坑、焊瘤、咬边等),否则应做适当的修整。
3.工件划线按照射线检测工艺卡在规定的检测部位划线。
采用单壁透照时需在工件两侧(射源侧和胶片侧)同时划线,并要求所划的线段尽可能对准。
采用双壁单影透照时,只需在工件胶片侧划线。
划线顺序由小号指向大号,纵焊缝按从左至右顺序,环向焊缝采用顺时针方向划线编号。
(工件表面应作出永久性标记以作为对每张底片重新定位的依据,工件不适合打印标记时,应采用详细的透照部位草图和其它的有效方法标注)。
4.像质计和标记摆放4.1像质计的摆放丝型像质计应放在射源一侧的工件表面上,位于被检焊缝的一端(被检长度的1/4处),钢丝横跨焊缝并与焊缝方向垂直,细丝置于外侧。
当射源一侧无法放置像质计时,可将其放在胶片侧,像质计应附加“F”标记以示区别,做一次对比试验,使实际像质指数达到规定要求。
外径大于等于200 mm的管子或容器环缝,采用射线中心法做周向曝光时,整圈环焊缝应等间隔放置至少三个像质计。
4.2.标记的摆放各种铅字标记应齐全,包括有:(↑)中心标记、(↑)搭接标记(↑)、工件编号、焊缝编号,部位编号,钢板厚度、焊工代号和透照日期。
返修透照时,应加返修标记R1、R2。
各种标记的摆放位置应距离焊缝边缘至少5mm,其中搭接标记的位置:在双壁单影或射源在内F>R的透照方式时,应放在胶片侧,其余透照方式应放在射源侧。
ISO17639:2003_金属材料焊缝的破坏性试验-焊缝宏观和微观检验
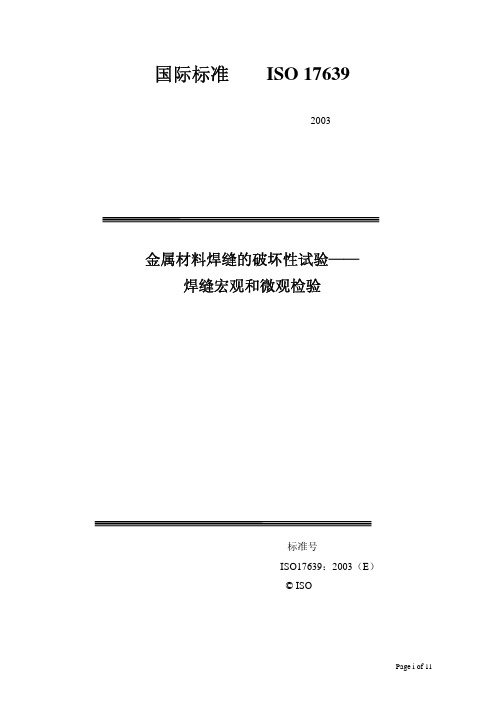
附录 A (资料性附录)
试验报告实例
根据 ISO17639(1)试(WPAR):No.(d):
生产厂:
检验目的:
试件:
试样:
母材:
焊接材料:
焊厚热处理或时效处理:
说明(b)
宏观检验(e)
微观检验(e)
(g)和(f)
(g)和(f)
图:No
图:No
位置(c)
位置(c)
放大倍数(g)
7 试样的截取
试样的截取方向一般垂直于焊缝轴线(横截面),试样包括焊缝熔敷金属和
焊缝两侧的热影响区。然而,也可以从其它方向截取试样。
在试验前应确定试件的位置、方向和数量,例如参照应用标准。
表 1 宏观和微观检验评定特性指南
特征
根据 ISO6521-1 不腐蚀宏 腐蚀宏观 不腐蚀微
缺欠
观检验
检验
观检验
-
-
×
-
15 纤维组织(晶粒)方向
-
-
×
-
16 偏析
-
-
×
-
17 沉淀
-
-
-
-
18 使用情况和不均匀性
-
(×)
×
(×)
19 力/热影响
-
-
×
-
×表示显示的特征;(×)表示显示或不显示的特征
注:表中列的特征数可能超出光学显微镜的分辨率,例如沉淀和夹渣。
腐蚀微 观检验
× × × × × × × (×) × × × × × × ×
Page 7 of 11
—腐蚀剂:xy。
43 92
54
例 1 a)试验对象:仅焊缝金属 检验—ISO17639—I—E—43—5.4/9.2/43/xy 式中 ISO17639=参照的国际标准; I=微观检验; E=经腐蚀; 43=试验对象; 5.4=钢,Cr 含量≤9%,Mo 含量≤40%; 9.2=奥氏体不锈钢 43=焊缝金属:Ni/Fe/Cr/Mo,Ni 含量≤1.2%; xy=腐蚀剂。 注:xy 代表 ISO/TR16060 相关附录中表数字代号。
外观检验ISO17637

外观检验ISO17637:2003-焊缝外观检验-熔化焊接头外观检验1 范围本国际标准的覆盖范围是金属材料熔化焊外观检验。
它也可以用于接头的焊前外观检验。
2 检测条件和设备表面光照度至少应达到350LX,建议应达到500LX。
出于直接实施检查的目的,在将实施检查的表面600mm之内,应给外观检测备好足够的空间,而且其检测角度不应小于大约30°(见图1)。
a 范围图1 检测范围当不能根据图1的检测范围或有应用标准规定时,应考虑采用放大镜、内窥镜、纤维光导或相机间接检查。
可采用辅助光源获得缺陷和背景之间的良好对比和鲜明效果。
在有疑义的情况下,对表面有缺陷之处,应采用其他无损试验方法来辅助外观检测。
外观检验检测设备的举例在附录A中给出。
3 人员资格从事焊缝外观检验和最终结果评定应该是有资格和能力的人。
人员资格评定推荐按ISO9712或相关工业部门的适当水平的同等标准。
4 外观检验4.1 总则本国际标准没有定义外观检验的范围。
然而,这些必须事先定义,比如参考某应用或产品标准。
检查者应可接近进行检测和查找产品文件。
焊前、焊接过程中或焊后的所有外观检验必须在物理可接近的情况下进行。
这可能包含表面处理的外观检验。
4.2 接头外观检验准备如果焊前需要外观检验,应检验接头以确定:a)焊接接头坡口准备的外形和尺寸达到焊接工艺规程的要求;b)熔化面和相邻表面是清洁的,且已进行了所有根据应用或产品标准的表面处理;c)将被焊的部分根据划线或说明互相对正正确。
4.3 焊接过程中的外观检验如果需要的话,须检测焊接过程以确定:a)每条焊道或层应在被覆盖前进行清理,特别要注意焊缝金属和熔化面的结合处;b)没有外观缺陷,比如裂纹或孔;如果发现缺陷,应提出来以便在进一步焊接之前进行补救;c)焊道之间、焊缝与母材之间的过渡成型良好,以便下一道完成良好;d)刨削的深度和外形是根据WPS的或与原始凹槽外形比较以确定焊缝金属按规定的完全去除;e)在所有必要的修补或补救措施之后,焊缝符合WPS的原始要求。
射线检测工艺标准

射线检测工艺标准1.适用范围本工艺标准适用于锅炉、压力容器、压力管道特种设备熔化焊对接接头的射线检测和质量级。
本工艺标准为锅炉、压力容器、压力管道特种设备通用的射线检测工艺标准,它与施工图纸和相关标准、规范配合使用。
2.编制依据2.1 本工艺标准主要依据JB4730编制,锅炉、压力容器、压力管道检测中若需执行行业标准时,应以现行行业标准为准。
2.2 本工艺标准执行时若与国家,行业标准相抵触时,应以现行行业标准为准。
3.射线检测范围及要求3.1 射线检测范围3.1.1 锅炉、压力容器、压力管道对接接头检测的数量抽查比例,应与施工图纸和相应标准、规范的要求相一致。
3.1.2 焊接接头进行抽查检测时,若发现有不合格的缺陷,应做抽查数量双倍数目的补充检测抽查,双倍补充检测仍有不合格,则应对焊工焊接的全部焊接接头进行无损检测。
3.2 射线检测要求3.2.1 焊接接头的射线检测,应执行G B3323《钢熔化焊对接接头射线照相和质量分级》的规定,射线照相的质量要求不应低于AB级。
3.2.2 焊接接头质量的评定,应根据锅炉、压力容器、压力管道检测行业标准要求执行的相关标准满足施工图纸的要求。
4.检测人员4.1 从事射线检测人员,必须持有锅炉、压力容器无损检测人员资格证书。
评片人员必须具备II级或II级以上的资格,操作人员必须具备I级或I级以上的检测资格。
4.2 评片人员的视力应符合JB4730标准4.3.3条的规定。
5.检测时机5.1 射线检测前,焊缝及热影响区的表面质量应经外观检查合格。
表面的不规则状态在底片上的影象应不掩盖焊缝中的缺陷或与之混淆,否则表面应经修整合格后方可进行检测。
5.2 具有延迟裂纹倾向材质的焊缝,射线检测应在焊后24小时后方可进行。
6.设备、胶片、增感屏6.1 射线机、观片机、黑度计等射线检测设备,应经调试合格并符合有关标准规定。
6.2 射线检测应使用中粒、中速工业用胶片和铅箔增感屏。
7.象质计7.1 射线检测用象质计必须符合JB4730的要求。
- 1、下载文档前请自行甄别文档内容的完整性,平台不提供额外的编辑、内容补充、找答案等附加服务。
- 2、"仅部分预览"的文档,不可在线预览部分如存在完整性等问题,可反馈申请退款(可完整预览的文档不适用该条件!)。
- 3、如文档侵犯您的权益,请联系客服反馈,我们会尽快为您处理(人工客服工作时间:9:00-18:30)。
ISO国际标准化组织ISO 17636:2003焊缝的无损检测 —— 熔化焊接头的射线检测Non-destructive testing of welds —— Radiographic testing of fusion-welded joints(翻译稿)国际标准化组织 发布ww .b z f xw .c o m国际标准化组织标准焊缝的无损检测 —— 熔化焊接头的射线检测翻译单位:哈尔滨焊接研究所 翻 译:陈宇校 对:朴东光 编 辑:朴东光2006年8月ww .b zf xw .c o1 范围本国际标准规定了金属材料熔化焊接头射线检验的基本方法。
目标是通过经济的方法得到满意的和可重复的结果。
该方法总体基于该学科中认可的实践和基本原理。
本国际标准适用于板或管的熔化焊接头检验。
它遵循ISO5579中给出的规则。
本国际标准没有规定缺陷的验收等级。
注:由于本国际标准的目的,术语“管”适用于“导管”、“管”、“水管”、“锅炉”和“压力导管”。
2 规范性引用文件下列文件对于本标准的应用是不可或缺的。
对于注日期的引用文件,只能引用指定的版本。
对于未注日期的引用文件,应采用其最新版本(包含所有修改版)。
ISO2504 焊缝射线检验和胶片观察条件——推荐模式的图象质量指示器的使用 ISO5580 无损检测——工业射线照明——最低要求ISO11699-1 无损检测——工业射线胶片——第一部分:工业射线照相系统分级ISO11699-2 无损检测——工业射线胶片——第二部分:照相过程控制,通过参考值的方法3 术语和定义由于本文件的目的,使用以下术语和定义。
3.1 公称壁厚 t指母材的公称厚度。
注:制造偏差不予考虑。
3.2 透照厚度 w射线入射方向上的材料厚度,基于公称壁厚来计算。
注:多壁透照时的透照厚度由公称壁厚计算取得。
3.3工件—胶片的距离 b在射线中心束方向上被检工件的非射线照射一侧至胶片间的距离。
3.4射线源的尺寸 d放射性源的尺寸。
3.5射线源—胶片的距离 SFD在射线透照方向上射线源与胶片之间的距离。
3.6ww .b zf xw .c of在射线中心束方向上被检工件的射线源一侧至射线源之间的距离。
3.7 直径 D e管的公称外径。
4 符号和缩略语基于本文件的目的,运用的符号和缩略语见表1。
表1 符号和缩略语符 号定 义t 公称壁厚 w 透照厚度b 工件—胶片的距离 d 射线源的尺寸SFD 射线源—胶片的距离f 射线源—工件的距离D e直径5 射线照相技术分级射线照相技术分为两个等级:—等级A :普通级 —等级B :较高级技术的选择应在检测前规定。
当等级A 的灵敏度无法达到要求时,才应用等级B 的检验技术。
注:可能有比等级B 更好的技术,但是不在本国际标准的含盖范围之内。
如果由于技术原因,不能达到等级B 规定的某一个条件,比如射线源类型或射线源-工件之间的距离f ,可以使用等级A 中规定的条件。
但是,灵敏度的降低应通过将最小密度增至3.0或高对比度的照相系统来补偿。
由于相对于等级A 的较高的灵敏度,检测样本可被看作检验成等级B 。
但如果应用象7.6中针对检测安排7.1.4和7.1.5描述的特殊SFD 缩减,以上将不应用。
6 一般性说明6.1 电离射线的防护当使用电离射线时,必须严格遵守地方、国家和国际上相关的安全法规。
警告:人体的任何部位被x-射线或γ-射线照射都会对健康造成很大损害。
任何使用x-射线机或放射源的地方,应有适当的法定设备。
6.2 表面准备和制造状态如果表面缺陷或涂层给缺陷扫查造成困难,表面须被磨平或涂层须被消除。
否则,没有必要进行表面准备。
除非另有规定,射线探伤应该在最终制造状态之后(如打磨或热处理之后)进行。
6.3 焊缝在射线照片中的位置如果照片不能清晰的显示焊缝,应该在焊缝的任何一边做高密度标记。
ww .b zf xw .c o m应该在被检工件的每一部分作标记。
照片的符号应该出现在照片中非重要的位置,且可以清楚的识别每一部分。
6.5 标记工件表面应作出永久性标记,以保证每张射线底片准确定位。
当工件不适合打印标记时,应采用详细的透照部位草图来标注。
6.6 底片的搭接采用两张或多张胶片照相时,底片上必须有一定的搭接区域,以确保整个被检区域都能反映在底片上。
在被检工件表面必须使用高密度材料的搭接标记,以保证每张底片上均能显现出来。
6.7 象质计(IQI )的类型和位置图象质量应根据ISO2504使用IQI 来评判。
象质计应优先放置在射线源侧工件表面并和表面紧贴。
IQI 应放置在照片中有标准光学密度特点的标准厚度区域。
针对使用的IQI 类型,它应被放置在: a ) 线型象质计的细丝应垂直于焊缝放置,同时应保证至少10mm 在具有标准光学密度区域,通常是在母材靠近焊缝的地方。
采用透照布置时,线型象质计的细丝应与穿过管子轴线方向的线放置在一起,但不能在焊缝图象上出现。
b ) 当使用步进/孔式IQI 时,它应该以这样的方法放置,即将必要的孔编号靠近焊缝。
采用7.1.6节和7.1.7节透照布置时,象质计既可放在射线源一侧又可放在胶片一侧。
如果不能按照上面 a ) 中列出的条件放置IQI ,IQI 应被放置在胶片一侧,同时图象质量决定于射线源侧和胶片侧的同等条件下的 IQI 的对比透照。
对于双墙透照,当IQI 放置在胶片侧,没有必要进行上面的检测。
这种情况下 ,参考表格A.1至A.12。
象质计采用胶片一侧放置时,应紧贴象质计放置“F ”标记,并在检验报告中给予说明。
如果能保证相似检测目标和区域的射线照片使用的是同样的透照方式,且过程技术和图象质量值的无差别很相似,图象质量不需要一一证明。
但是,图象质量的查证范围应该在检测前规定。
外径大于等于200mm 的管子,采用射线源置于圆心位置的周向曝光技术时,应至少放置3个在管子周长方向上均匀分布的象质计。
这些胶片指示的IQI 图象可被认为代表整个圆周。
6.8 图象质量评定照片观察应参照ISO5580。
应该检测射线照片中IQI 的图象,判定其中所能分辨出的最细的丝或最小的孔的数量。
如果在一个具有标准光学密度区域有一条至少10mm 的连续的线,则图象合格。
在使用步进和孔型IQI 情况下,如果有两个同样直径的孔,两个必须都是可分辨的,以使步进被认为是可见的。
所得到的图象质量应该记录在射线检验报告中。
使用的IQI 类型也应该有清晰的记录。
6.9图象质量最小值表格A.1至A.12给出了铁材料的最小质量值。
本国际标准的使用者应参考EN462-4,判断这些值是否适合其他材料。
6.10人员资格从事焊缝无损检验和最终结果评定应该是有资格和能力的人。
人员资格评定推荐按ISO9712或相关工业部门的适当水平的同等标准。
7 推荐的射线照片制作方法7.1 检测安排 7.1.1 总则推荐参照7.1.2节和7.1.9节中给出的射线检验技术。
外径大于100mm ,公称壁厚大于8 mm 和焊缝宽度大于De/4的管子对接焊缝,不适用双壁双影椭圆透ww .b zf xw .c o m缝宽度。
外径小于等于100mm ,不能采用双壁双影椭圆透照技术时,可参考7.1.7采用垂直透照技术(见图12)。
这种情况下,分三次透照,每次间隔120°或60°。
参照图11,13和14的测量安排,光速的倾斜应尽可能的小,以防止两个图象的重叠.射线源和工件之间的距离,f,应尽可能的小,参照7.6。
IQI 应有一个导向符号“F ”,且尽可能靠近胶片放置。
当工件的几何外型或材料厚度的不同不允许使用7.1.2至7.1.9中列出的方法时,可以使用其他射线照射方法。
工件截面形状均匀时,为缩短曝光时间,不允许采用多胶片透照技术。
注: 附录B 给出了足够覆盖管对接焊缝整个圆周的必要的射线照片最小数量。
7.1.2射线源位于工件前部,胶片位于另一侧(见图1)注:1 射线源2 胶片图1 平壁和单壁透照的透照布置7.1.3 射线源位于工件外部,胶片位于内侧(见图2至图4)ww .b zf x w .c o m注:1 射线源2 胶片图2 曲面单壁透照的透照布置注:1 射线源2 胶片图3 曲面单壁(插入式焊缝)透照的透照布置ww .b zf xw .c o注:1 射线源2 胶片图4 曲面单壁(骑座式焊缝)透照的透照布置7.1.4 射线源位于工件内部中心,胶片位于外侧(见图5至图7)注:1 射线源2 胶片图5 曲面单壁透照的透照布置ww .b zf xw .c o注:1 射线源2 胶片图6 曲面单壁(插入式焊缝)透照的透照布置注:1 射线源2 胶片图7 曲面单壁(骑座式焊缝)透照的透照布置7.1.5 射线源位于工件内部且不在中心,胶片位于外侧(见图8至图10)ww .b zf xw .c o注:1 射线源2 胶片图8 曲面单壁透照的透照布置注:1 射线源2 胶片图9 曲面单壁(插入式焊缝)透照的透照布置ww .b zf xw .c o注:1 射线源2 胶片图10 曲面单壁(骑座式焊缝)透照的透照布置7.1.6椭圆技术(见图11)注:1 射线源2 胶片图11 双壁评定时曲面双壁双影透照布置(射线源和胶片在工件外部)ww .b zf xw .c o m7.1.7 垂直透照技术(见图12)注:1 射线源2 胶片图12 双壁评定时曲面双壁双影透照布置(射线源和胶片在工件外部)7.1.8 射线源位于工件外部,胶片位于另外一侧(见图13至图18)注:1 射线源2 胶片图13 曲面双壁单影透照布置,评定其中靠近有IQI 附着的胶片的壁ww .b zf xw .c o m注:1 射线源2 胶片图14 双壁单影透照布置注:1 射线源2 胶片图15 纵缝双壁单影透照布置ww .b zf xw .c o注:1 射线源2 胶片图16 曲面双壁单影透照布置,评定靠近胶片的壁注:1 射线源2 胶片图17 角焊缝射线探伤的透照布置ww .b zf xw .c o注:1 射线源2 胶片图18 角焊缝射线探伤的透照布置7.1.9 母材厚度不同时的透照技术(见图19)注:1 射线源2 胶片图19 多胶片技术ww .b zf xw .c o7.2 线源和管电压的选择7.2.1 500kV 以下的x-射线设备为了更好地发现缺陷,应采用较低的管电压。
不同材质厚度对应的允许最高管电压见图20。
当工件被透照区域厚度变化时,可适当提高最高管电压,但值得注意的是,管电压的明显提高会降低缺陷分辨力。
钢的最高管电压最大允许提高50KV ;钛的最高管电压最大允许提高40KV ;铝的最高管电压最大允许提高30KV 。
3 钛及其合金4 铝及其合金x -射线电压透照厚度w1 铜/镍及其合金2 钢图20 不同透照厚度和不同材质允许使用的最高x-射线电压7.2.2 其他射线源γ射线和1MeV 以上的X 射线所允许的透照厚度范围见表2。