不锈钢管焊缝无损检测方法介绍
管道焊接与无损检测
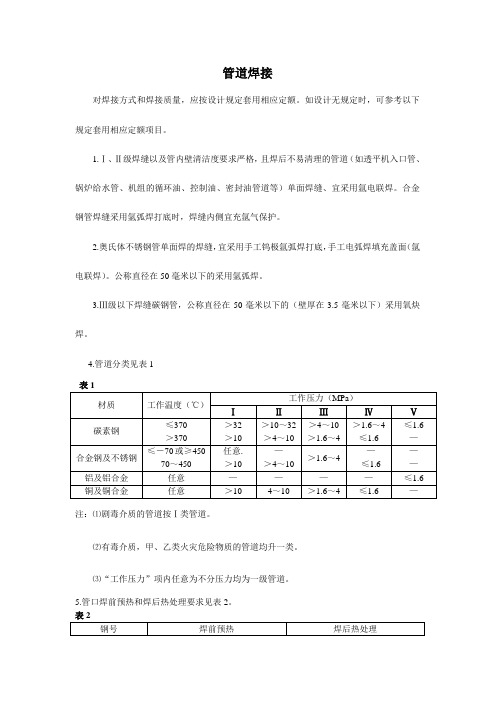
管道焊接对焊接方式和焊接质量,应按设计规定套用相应定额。
如设计无规定时,可参考以下规定套用相应定额项目。
1.Ⅰ、Ⅱ级焊缝以及管内壁清洁度要求严格,且焊后不易清理的管道(如透平机入口管、锅炉给水管、机组的循环油、控制油、密封油管道等)单面焊缝、宜采用氩电联焊。
合金钢管焊缝采用氩弧焊打底时,焊缝内侧宜充氩气保护。
2.奥氏体不锈钢管单面焊的焊缝,宜采用手工钨极氩弧焊打底,手工电弧焊填充盖面(氩电联焊)。
公称直径在50毫米以下的采用氩弧焊。
3.Ⅲ级以下焊缝碳钢管,公称直径在50毫米以下的(壁厚在3.5毫米以下)采用氧炔焊。
4.管道分类见表1注:⑴剧毒介质的管道按Ⅰ类管道。
⑵有毒介质,甲、乙类火灾危险物质的管道均升一类。
⑶“工作压力”项内任意为不分压力均为一级管道。
5.管口焊前预热和焊后热处理要求见表2。
表2注:⑴当焊接环境温度低于零度时,除规定壁厚必须作预热要求的金属外,其余金属壁厚也均应作适当的预热,使被焊接母材有手温感。
规定必须作预热要求的金属,定额项目内的预热消耗已考虑了温度变化因素,故不再增加预热。
⑵有应力腐蚀的碳素钢、合金钢,不论其壁厚条件,均应进行焊后热处理。
6.管口焊缝无损探伤计算规定数据:(1)管口焊接含量取定见表3。
(2)每个管口焊缝X光拍片张数,如无规定者可按表4计算。
表4注:⑴公称直径80毫米以下的管道焊缝X光透视检查拍片,一个焊口要求至少拍两张片。
定额中采用的胶片为85×300毫米的,实际上可用85×150毫米的胶片,执行定额时,人工和机械使用费壁变,材料费乘0.5系数。
⑵片子有效长度按片长减去搭接每边25毫米计算。
⑶管道焊口透视拍片的张数=管道等级规定的探伤百分比×焊口数量×张数(见表4)(3)管道各级焊缝射线探伤数量,应按设计规定计算。
如设计无规定时,按表5规定计算。
注:每条管线上最低探伤不得少于一个焊口。
不锈钢焊缝超声波探伤标准

不锈钢焊缝超声波探伤标准不锈钢焊缝超声波探伤是一种常用的无损检测方法,其标准化是确保焊缝质量的重要手段。
本文将介绍不锈钢焊缝超声波探伤的标准要求,以及相关的操作规程和注意事项。
首先,不锈钢焊缝超声波探伤的标准主要包括国际标准、行业标准和企业标准。
国际标准通常是作为参考依据,行业标准则是根据特定行业的需求和实际情况而制定,而企业标准则是根据企业内部管理和生产情况而制定。
在进行不锈钢焊缝超声波探伤时,应当严格按照相关标准进行操作,以确保检测结果的准确性和可靠性。
其次,不锈钢焊缝超声波探伤的操作规程包括设备准备、检测参数设置、探头校准、扫描检测、数据分析等步骤。
在进行设备准备时,应当检查超声波探伤仪器和探头的状态,确保其正常工作;在进行检测参数设置时,应根据焊缝的类型和厚度等因素进行合理的参数选择;在进行探头校准和扫描检测时,应当按照标准要求进行操作,以获取准确的检测数据;最后,在进行数据分析时,应当结合实际情况进行判断,对焊缝的缺陷进行合理评定。
此外,不锈钢焊缝超声波探伤时需要注意的事项包括环境条件、人员素质、设备维护等方面。
在进行超声波探伤时,应当选择相对安静、无干扰的环境,以确保检测的准确性;在进行操作时,应当由经过专门培训的人员进行,以确保操作的规范性和准确性;在进行设备维护时,应当定期对超声波探伤仪器和探头进行检查和维护,以确保其正常工作。
总的来说,不锈钢焊缝超声波探伤是一项重要的无损检测方法,其标准化是确保焊缝质量的关键。
在进行超声波探伤时,应当严格按照相关标准进行操作,以确保检测结果的准确性和可靠性。
同时,也需要注意环境条件、人员素质、设备维护等方面的问题,以确保整个检测过程的顺利进行。
希望本文的介绍能够对不锈钢焊缝超声波探伤的标准化有所帮助,谢谢阅读!。
奥氏体不锈钢焊管焊缝铁素体含量及其测定_何德孚

试验与研究奥氏体不锈钢焊管焊缝铁素体含量及其测定何德孚1,曹志樑2,周志江3,蔡新强2,徐阿敏2(1.久立焊管研究所,上海200233;2.久立不锈钢管有限公司,浙江湖州313012;3.久立集团股份有限公司,浙江湖州313012)摘 要:奥氏体不锈钢焊缝通常含有少量铁素体,它对奥氏体不锈钢焊管的强韧性、耐腐蚀性、焊接性都可能有优化或劣化影响,简要评述了这些影响及铁素体含量的测定方法。
关键词:奥氏体不锈钢焊管;焊缝;铁素体含量;磁测法;金相法;化学分析-图谱法中图分类号:TG115.2 文献标志码:B 文章编号:1001-3938(2007)05-0030-060 前 言浙江久立不锈钢管有限公司销售给江苏常熟某日资企业一批奥氏体不锈钢焊管,客户对其中一根钢管材质提出了质疑,依据是他们可以用磁铁吸住这根钢管,因此认为其材质不是奥氏体不锈 钢 而是 铁 。
虽经销售员多方解释说明,该客户仍坚持要委托第三方做仲裁检验。
后经上海材料研究所检测中心证明,这根钢管不仅材质,而且晶间腐蚀试验均符合订货合同所依据的GB /T 12771 2000标准的规定。
这种现象反映出来的问题实质是奥氏体不锈钢及其焊缝金属中铁素体的含量和铁素体含量测定方法以及对不锈钢可能产生的有害影响,这个问题国外在1960~1980年曾经讨论过。
我国目前正处于不锈钢及不锈钢焊管生产及工业应用的快速发展时期,2005年不锈钢年产量已达316 104,t 仅次于日本,2006年有可能会超过日本而成为全球不锈钢第一生产大国。
正确认识这些问题对广大用户及不锈钢管制造商都十分有意义。
笔者对上述问题进行分析,以供广大业内人士讨论和参考。
1 奥氏体不锈钢焊管焊缝铁素体含量稍高是常见现象常温下奥氏体(面心立方晶格)不锈钢是无磁性的,而铁素体(体心立方晶格)不锈钢是有磁性的,因此人们常用磁铁能否吸引来区分它们。
但是这种简单的方法有时可能会造成误判,原因是:(1)奥氏体是奥氏体不锈钢冶炼、轧制后期的相变产物,其前期即不锈钢熔炼到铸锭冷却结晶的过程中会出现铁素体及铁素体相变为奥氏体的过程,由于种种原因,奥氏体不锈钢会包含少量铁素体且分布不均匀。
无损检测介绍

无损检测无损检测(Nondestructive Testing,缩写就是NDT),工作中也被叫做无损探伤。
是在不损坏工件或原材料工作状态的前提下,对被检验部件的表面和内部质量进行检查的一种检测手段。
无损检测通常被称为无损评估(NDE,non-destructive evaluation),但从技术上讲,它们涵盖的领域略有不同。
NDE 方法通常用于更定量的测量,例如定位缺陷以及提供有关缺陷的测量信息,例如尺寸、形状和方向。
NDE 方法还用于确定材料的物理性能,例如成形性和断裂韧性。
传统的无损检测的方法比较常见的是以下的几种:1、目视检测(VT,Visual and Optical Testing)这是最基本的无损检测方法,范围从简单的肉眼目视检查到计算机控制的远程摄像系统。
这些设备能够自动识别和测量组件的特征。
2、射线照相法(RT,Radiographic Testing)工业射线照相涉及使用辐射穿透测试对象来识别缺陷或检查内部特征。
X 射线通常用于较薄或密度较小的材料,而伽马射线则用于较厚或较密的材料。
辐射穿过被检查的物体到达胶片等记录介质上,生成的阴影图可识别厚度和密度变化等特征。
3、超声波检测(UT,Ultrasonic Testing)该方法涉及将超高频声波传输到材料上,然后将其返回到接收器(可以在视觉显示器上呈现)。
如果材料特性存在缺陷或变化,这些反射将记录不同的声密度和速度。
最常见的UT 技术是脉冲回波。
4、磁粉检测(MT,Magnetic Particle Testing)该方法用于定位铁磁材料中的表面和近表面缺陷或缺陷。
感应磁场后,表面会撒上铁颗粒(干燥或悬浮在液体溶液中),这些铁颗粒也可能是有色或荧光的。
如果存在不连续性,它将扰乱磁场的流动并迫使部分磁场在表面泄漏,从而使检查人员能够明显地识别缺陷。
5、渗透检测(PT,Penetrant Testing)渗透检测法涉及用含有可见或荧光染料的溶液涂覆干净的测试物体。
不锈钢管道产品的检验项目
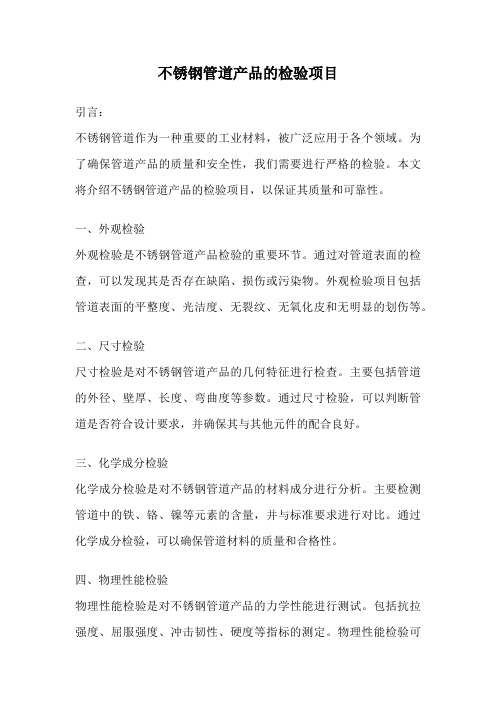
不锈钢管道产品的检验项目引言:不锈钢管道作为一种重要的工业材料,被广泛应用于各个领域。
为了确保管道产品的质量和安全性,我们需要进行严格的检验。
本文将介绍不锈钢管道产品的检验项目,以保证其质量和可靠性。
一、外观检验外观检验是不锈钢管道产品检验的重要环节。
通过对管道表面的检查,可以发现其是否存在缺陷、损伤或污染物。
外观检验项目包括管道表面的平整度、光洁度、无裂纹、无氧化皮和无明显的划伤等。
二、尺寸检验尺寸检验是对不锈钢管道产品的几何特征进行检查。
主要包括管道的外径、壁厚、长度、弯曲度等参数。
通过尺寸检验,可以判断管道是否符合设计要求,并确保其与其他元件的配合良好。
三、化学成分检验化学成分检验是对不锈钢管道产品的材料成分进行分析。
主要检测管道中的铁、铬、镍等元素的含量,并与标准要求进行对比。
通过化学成分检验,可以确保管道材料的质量和合格性。
四、物理性能检验物理性能检验是对不锈钢管道产品的力学性能进行测试。
包括抗拉强度、屈服强度、冲击韧性、硬度等指标的测定。
物理性能检验可以评估管道在不同工况下的承载能力和耐久性。
五、耐腐蚀性检验耐腐蚀性检验是对不锈钢管道产品的抗腐蚀性能进行评估。
通过模拟真实工况下的腐蚀环境,测试管道的耐蚀性能。
主要检测管道在酸、碱、盐等介质中的耐蚀性,并评估其使用寿命和安全性。
六、焊接接头检验焊接接头是不锈钢管道中的重要部分,其质量直接影响整个管道的性能。
焊接接头检验主要包括焊缝外观、焊缝强度、焊接变形等方面的评估。
通过焊接接头检验,可以确保管道在使用过程中的可靠性和安全性。
七、压力试验压力试验是对不锈钢管道产品的耐压性能进行测试。
通过对管道施加一定的压力,观察管道是否发生泄漏或变形。
压力试验可以评估管道在正常工作压力范围内的安全性和可靠性。
八、非破坏性检验非破坏性检验是一种通过检测不锈钢管道产品的隐蔽缺陷来评估其质量和安全性的方法。
主要包括超声波检测、射线检测、磁粉检测等技术手段。
非破坏性检验可以发现管道中的裂纹、气孔、夹杂等缺陷,并进行评估和修复。
双相不锈钢特殊焊接工艺及无损检测要求

双相不锈钢特殊焊接工艺及无损检测要求摘要:随着社会经济的稳步增长和现代科技的快速进步,我国工业行业得以快速发展,整体生产工艺水平得到大幅度提升。
双相不锈钢是属于当前电厂以及工业制造业当中应用的一种材料,其本身有着良好的焊接性和力学性能,可适用于多项服役环境。
双相不锈钢特殊焊接要求较高,尤其特殊焊接工艺与无损检测方面较为明显。
本篇文章主要针对双相不锈钢特殊焊接工艺及无损检测相关要求作出简要的讨论,首先介绍双相不锈钢的产生和具体焊接性,再阐述双相不锈钢特殊焊接工艺相关要求以及无损检测相关要点,以期能够为现场焊接施工质量的提升提供一点参考。
关键词:双相不锈钢;特殊焊接工艺;无损检测目前来讲,我国科技的快速发展下,对于各项资源与能源的利用率也不断提升,尤其在各项资源材料的加工和应用方面的整体工艺水平进步速度较快。
双相不锈钢在化学工业、电力行业以及石油天然气等行业当中的应用相对较为广泛,在实际应用当中,针对双相不锈钢的焊接需要重点考虑多方面因素,无论在材料的选择还是工艺技术应用等多项环节当中都需要注重工艺操作的规范性和各项要点的质量控制,如此方能够保证双相不锈钢的焊接质量,提高材料与能源的利用率,这就需要相关技术人员能够全面掌握双相不锈钢特殊焊接工艺的各项要点和操作步骤,完成加工后还要仔细进行无损检测,针对其各项特殊要求进行全面分析,如此才能够确保双相不锈钢的加工质量,发挥双相不锈钢的优势特点。
1.关于双相不锈钢双相不锈钢主要是组织当中铁素体、奥氏体含量约各占50%,其中量少相的含量也需要满足30%以上的不锈钢。
如果含C量相对较低,则Cr含量应维持在18%-28%的含量,Ni需维持在3%-10%。
此外,双相不锈钢具有奥氏体铁素体不锈钢的性能优势,其韧性相比铁素体相要高,且无室温脆性,所以,可以用于厚板。
另外,还具备良好的耐晶间腐蚀性能和焊接性能,同时还具备铁素体不锈钢较高的导热系数与475摄氏度脆性、超塑性等等。
管道无损检测方案
1. 概述本工程各种管道约 15000 米,分不锈钢 SS304、SS316、碳钢、合金钢、PP/GRP、CS+PTFE 等多种材质。
根据工艺、技术的不同要求,现场需拍片约40000 张,硬度试验 900 点。
本方案编制参考了招标文件中技术说明 S-00-1540-002 以及美国 ASME 标准(1986)。
2.检验项目2. 1 射线探伤⑴ 射线探伤的检查比例,按照 JGC 在“技术说明”中的要求执行。
⑵ 射线探伤的检查比例应符合设计要求及有关技术条件的规定。
⑶ 要求 100%检查的管道应逐个焊口整圈 100%检查,确保不漏检。
⑷ 要求 10%抽检的管道应按相应焊工的相应焊缝按 10%比例整圈检查。
⑸ 管径≤3″厚度δ ≤7.62mm 采用双壁双影椭圆透照,每一个焊口间隔 90°各拍一张,共两张。
⑹ 管径=2″厚度≥8.74mm;管径=2-1/2″厚度≥9.53mm;管径=3″厚度≥11—13mm 时应采用双壁单影分段透照,拍摄四张。
⑺ 管径≥4″采用双壁单影或者单壁单影透照,每一个管口至少拍摄四张,T 各种规格管道焊缝的拍摄数量应与现场测试检查程序中的要求一致。
⑻胶片选用FUJI“100”型。
采用的铅箔增感屏,当采用 X 射线探伤时,前屏厚 0.03mm,后屏厚 0.1mm;当采用γ 射线探伤时,先后屏厚均为 0.1mm。
⑼ 10″以下包括10″的管道探伤时,胶片规格为10″×4″;12″-72″的管道探伤时,胶片规格为12″×3-1/3″。
有特殊要求的按要求执行。
⑽ 所摄底片应无划伤,水迹,伪缺陷,当采用 X 射线时 AB 级的底片黑度 D=1.8-3.5,当采用γ 射线时底片黑度 D=2.0-3.5,底片象质指数均应满足不同厚度的要求。
底片上标识应齐全(包括管段号,焊口号,焊工号,拍摄日期,返修次数)。
⑾ 用 Ir192γ射线探伤时,应加装准直器,以减少散射线对底片像质的影响。
不锈钢管道焊接规范(精)
不锈钢管道焊接规范一、焊前准备;焊接坡口制备质量检查、依据施工图样和焊接工艺指导书中规定的坡口尺寸、精度和表面质量的要求,坡口质量包括平整度、垂直度和清洁度等。
1、检查坡口的加工尺寸(高度、角边及钝边等)和精度是否符合有关技术标准的规定。
2、检查坡口表面粗糙度及表面缺陷(气割缺口、裂纹、分层和夹渣)如果超出标准允许范围的缺陷,应进行修复处理,如表面粗糙度未达标准,可采用砂布修磨。
3、检查坡口的表面清理质量。
坡口面及其两侧至少200mm 范围内应清理干净,不保留有毛刺、挂渣、铁锈、油污、氧化膜及油漆等有害异物。
4、坡口表面的无损探伤检查。
对于焊接工艺文件规定对坡口表面要进行无损探伤(如着色等)的材料(如CY-M 钢、Fe-CY-N 高温含合金钢等,应进行无损检查,如发现裂纹等缺陷应予清除。
二、组装和定位焊检查;1、检查组装后的几何尺寸和形状,是否符合图样规定。
:2、组装装配间隙为1.5—2mm ,采用TIG 焊三点定位焊,焊﹤缝位置为时钟3点,9点和12点位置,使用的焊接材料应与焊件材料相同,焊点长度为10—15mm ,要求焊透和保证无缺陷,错边量≤1.5—2mm 。
3、组对是不得采用强力组装,接头内壁必须齐平。
4、点固焊时不得有空气、夹渣、夹钨、裂纹存在。
5、检查定位焊所用的焊接工艺和焊工资质是否符合规定,定位焊的焊接工艺应与正式施焊的工艺相同。
6、检查定位焊的焊接质量和尺寸是否符合标准规定。
定位焊缝中不允许有裂纹、气孔、夹渣缺陷,发现缺陷及时清除。
7、用焊口检测器或样板测量组装坡口的形状、尺寸、间隙和错边量是否符合要求规范,如不符合应进行返修或重新组对焊接处理。
8、定位焊的焊点长度及间距应根据结构形状及厚度而定,工件越薄焊点间距越小,板状比管状间距要小。
9、不锈钢采用TIG 焊接管道时,必须通入氩气进行保护。
10、焊接作业场地必须通风良好,无易燃,易爆物品存放,通道保持整洁畅通。
三、焊工技能资格查验;1、现场进行焊接的焊工,必须具备政府相关部门颁发的资质和证书,并由业主及监理部门查验后认可。
不锈钢管件检测方法
不锈钢管件检测方法
不锈钢管件是广泛应用于工业、建筑和家居领域的重要材料之一。
为了确保不
锈钢管件的质量和性能满足要求,进行有效的检测是必不可少的。
下面介绍三种常见的不锈钢管件检测方法:
1. 目视检测:目视检测是最简单和常用的检测方法之一。
通过肉眼观察不锈钢
管件的外观,检查其是否存在表面凹凸不平、裂纹、氧化等缺陷。
目视检测可快速进行,但只适用于表面缺陷的检测。
2. 射线检测:射线检测是一种常用的无损检测方法,适用于检测不锈钢管件内
部的缺陷。
常用的射线检测方法包括X射线检测和γ射线检测。
射线通过管件后,会在胶片或探测器上形成影像,用于评估管件内部是否存在裂纹、夹杂物等隐蔽缺陷。
3. 超声波检测:超声波检测是利用超声波在材料中传播和反射的特性来检测不
锈钢管件的方法。
通过探头向管件表面发送超声波脉冲,根据接收到的超声波信号的强弱和时间延迟来判断管件的质量。
超声波检测可以检测不锈钢管件内部的裂纹、气孔等缺陷,并且可以定量评估其尺寸和位置。
总之,不锈钢管件的质量检测是确保其安全可靠运行的关键步骤。
目视检测、
射线检测和超声波检测是常用的不锈钢管件检测方法,各具特点,可以结合使用,以获得更全面和准确的检测结果。
N08810奥氏体不锈钢无损检测要点
N08810奥氏体不锈钢无损检测要点N08810属于镍基合金,又因为该材料在常温下,主要以奥氏体形态存在,同时该材料含有大量的F e元素(约40%),故该材料与奥氏体不锈钢具有同样的声学特征。
但是该材料在声速上与真正的奥氏体不锈钢又有区别。
查国外文献得知,常规奥氏体不锈钢声速一般在5660左右,而N08810声速一般在5710附近。
网上有文献研究奥氏体不锈钢(304)超声声速与晶粒度之间的关系,声速越小,晶粒越粗大。
可是实际检测的时候,粗晶的N08810声速实测为5750,没有粗晶回波现象的N08810声速实测却在5710附近,这种情况值得进一步研究。
N08810的声速与晶粒度之间的依赖关系,还没有试验数据出来。
本文通过一些实际检测实例,向大家介绍一些笔者近期接触n08810检测方面的一些心得体会。
希望抛砖引玉,让做过此方面检测的专家学者不吝赐教;与同道之人共勉。
1原材料检测原材料检测,主要是纯N08810板材检测和N08810复合板(覆材为N08810)的检测。
N08810板材检测,一般不做超声检测,只做外观、尺寸、超声测厚,化学元素、力学性能方面的检测。
但4730标准对n08810板材检测是适用的,参照钢板检测执行。
这里要注意:超声测厚容易出现测厚不准,主要是常规超声检测仪都是针对铁素体钢(细晶)进行配置的,一般都是5M及以上频率的双晶直探头,N08810与铁素体钢最大的不同,就是晶粒较为粗大,声衰减极为严重。
故配备一般探头的测厚仪,遇到N08810粗晶材料,要么显示值偏小,要么无显示。
对于显示值偏小的解决方案,换低频探头、或低频单晶探头进行重新检测(检测之前一定要校准声速和零点);对于无显示的解决办法,同样采取低频单晶探头进行重新检测。
- 1、下载文档前请自行甄别文档内容的完整性,平台不提供额外的编辑、内容补充、找答案等附加服务。
- 2、"仅部分预览"的文档,不可在线预览部分如存在完整性等问题,可反馈申请退款(可完整预览的文档不适用该条件!)。
- 3、如文档侵犯您的权益,请联系客服反馈,我们会尽快为您处理(人工客服工作时间:9:00-18:30)。
不锈钢管焊缝无损检测方法介绍作者:不锈钢管来源:未知日期:2010/10/4 13:27:50 人气:2 标签:不锈钢管不锈钢管焊缝无损检测导读:(1)渗透探伤(PT)采用带有荧光染料(荧光法)或红色染料(着色法)的渗透剂的渗透作用,来显示焊接接头表面微小缺陷的无损检验法。
检测时一要求被测表面平整光洁。
此方…(1)渗透探伤(PT)采用带有荧光染料(荧光法)或红色染料(着色法)的渗透剂的渗透作用,来显示焊接接头表面微小缺陷的无损检验法。
检测时一要求被测表面平整光洁。
此方法分为荧光探伤和着色探伤,其中荧光探伤的测量精度较高,可达10μm。
焊接构件表面检查常用着色法渗透探伤。
(2)磁粉探伤(MT)利用在强磁场中,铁磁材料表层缺陷产生的漏磁场吸附磁粉的现象而进行的无损检验方法。
在有缺陷处,由于漏磁的作用会集中吸附撒上的铁粉。
可根据吸附铁粉的形状、厚度和多少,来判断焊接缺陷的位置和大小。
该方法不适用无磁性的奥氏体型不锈钢。
(3)射线探伤(RT)采用X射线或γ射线照射焊接接头检查其内部缺陷的一种无损检验方法。
它能准确地显示出焊缝中焊接缺陷的种类、形状、尺寸、位置和分布情况。
评定标准按《钢熔化焊对接接头射线照相法和质量分级》(GB3329-87)进行。
该探伤方法长期操作,对操作者身体有一定的影响。
(4)超声波探伤(UT)借助于超声波探伤仪来检测焊缝内部缺陷的一种无损探伤方法。
此法适用于探伤厚板,可确定5mm以内缺陷。
探伤周期短、成木低、设备简单,对操作者身体无害,但不能准确判断缺陷的性质。
(5)涡流探伤(ET)涡流探伤是以电磁感应原理为基础,当钢管(指碳钢、合金钢和不锈钢)通过交流电的绕组时,钢管表面或近表面出现集肤效应,使其有缺陷部位的涡流发生变化,导致绕组的阻抗或感应电压产生变化,从而得到关于缺陷的信号。
从信号的幅值及相位等可以对缺陷进行判别,能有效地识别钢管内外表面的不连续性缺陷,如裂纹、未焊透、夹渣、气孔、点腐蚀等,对开放性线性缺陷最为敏感。
无缝钢管的工艺流程概述热轧(挤压无缝钢管):圆管坯→加热→穿孔→三辊斜轧、连轧或挤压→脱管→定径(或减径)→冷却→坯管→矫直→水压试验(或探伤)→标记→入库。
冷拔(轧)无缝钢管:圆圆管坯→加热→穿孔→打头→退火→酸洗→涂油(镀铜)→多道次冷拔(冷轧)→坯管→热处理→矫直→水压试验(探伤)→标记→入库。
无缝管和焊管的区别1、两种钢管的用途不同无缝钢管:GB/T8162-1999(结构用无缝钢管)。
主要用于一般结构和机械结构。
焊接钢管:主要用于中低压的流体材料的输送,严禁用于结构件。
2.材料不一样无缝钢管是优质碳素钢一般是用10、20、30、35、45等优质碳结钢16Mn、:5MnV等低合金结构钢或40Cr、30CrMnSi、45Mn2等合结钢热轧或冷轧制成的。
焊管是普通碳素钢是指用钢板卷成管,然后焊接成型。
材质多为Q195、Q215、Q235的普通碳钢,市面上常见的焊管有两种,直缝焊管、螺旋焊管,焊管易锈蚀.3、成型工艺不同。
无缝钢管一般是将熔融状态的钢水通过环形狭缝积压出来后再经拉伸等处理工艺成型,没有焊缝。
承压能力大,力学性能好和物理性能高,所以经常被用于结构件,机械构件和高压流体输送设备上使用。
焊管采用的坯料是钢板或带钢,通过将平板材经折弯后焊接起来的,可以在上面发现一条焊缝。
因其焊接工艺不同而分为炉焊管、电焊(电阻焊)管和自动电弧焊管。
焊管主要用于输送水、煤气、空气、油和取暖热水或蒸汽等一般较低压力流体和其他用途管,不能用于结构件。
4、物理性能不同抗拉强度差别很大,无缝钢管抗拉强度是410Mpa,焊管是195-235Mpa。
无缝钢管承压能力和力学性能较焊管区别很大。
焊管的焊缝部位是其薄弱环节。
焊丝和焊接母体是两种材料,焊缝质量也是影响其整体性能的主要因素。
在北方生活过的人一般都有过自来水管或暖气管在冬天被冻爆,爆的地方一般都是焊缝处。
5、价格不同无缝钢管的价格比焊管大约高了1200-3000元/吨.无缝管和焊管的区别1、两种钢管的用途不同无缝钢管:GB/T8162-1999(结构用无缝钢管)。
主要用于一般结构和机械结构。
焊接钢管:主要用于中低压的流体材料的输送,严禁用于结构件。
2.材料不一样无缝钢管是优质碳素钢一般是用10、20、30、35、45等优质碳结钢16Mn、:5MnV等低合金结构钢或40Cr、30CrMnSi、45Mn2等合结钢热轧或冷轧制成的。
焊管是普通碳素钢是指用钢板卷成管,然后焊接成型。
材质多为Q195、Q215、Q235的普通碳钢,市面上常见的焊管有两种,直缝焊管、螺旋焊管,焊管易锈蚀.3、成型工艺不同。
无缝钢管一般是将熔融状态的钢水通过环形狭缝积压出来后再经拉伸等处理工艺成型,没有焊缝。
承压能力大,力学性能好和物理性能高,所以经常被用于结构件,机械构件和高压流体输送设备上使用。
焊管采用的坯料是钢板或带钢,通过将平板材经折弯后焊接起来的,可以在上面发现一条焊缝。
因其焊接工艺不同而分为炉焊管、电焊(电阻焊)管和自动电弧焊管。
焊管主要用于输送水、煤气、空气、油和取暖热水或蒸汽等一般较低压力流体和其他用途管,不能用于结构件。
4、物理性能不同抗拉强度差别很大,无缝钢管抗拉强度是410Mpa,焊管是195-235Mpa。
无缝钢管承压能力和力学性能较焊管区别很大。
焊管的焊缝部位是其薄弱环节。
焊丝和焊接母体是两种材料,焊缝质量也是影响其整体性能的主要因素。
在北方生活过的人一般都有过自来水管或暖气管在冬天被冻爆,爆的地方一般都是焊缝处。
不锈钢钢管的分类1.按生产方法分类(1)无缝钢管—冷拔管.挤压管.冷轧管(2)焊接钢管(a) 按工艺分类—气体保护焊接钢管.电弧焊管.电阻焊管(高频.低频)(b) 按焊缝分—直缝焊管.螺旋焊管2.按断面形状分类(1)圆形钢管(2)矩形管3.按壁厚分类—薄壁钢管.厚壁钢管4.按用途分类(1)民用管分圆管.矩管.花管,一般用于装饰.建筑.结构等方面;(2)工业管:工业配管用钢管.一般配管用钢管(饮用水管).机械构造/流体输送管.锅炉热交换管.食品卫生管等。
一般应用于工业的各个领域如:石油化工.造纸.核能.食品.饮料.医药等行业对流体介质要求较高管道。
不锈钢无缝钢管厚壁钢管不锈钢无缝钢管是一种具有中空截面.周边没有接缝的长条钢材。
1.无缝钢管的制造工艺及流程:冶炼>钢锭>轧钢>锯切>剥皮>穿孔>退火>酸洗>上灰>冷拔>切头>酸洗>入库2.无缝钢管的特点:从上面的工艺流程我们不难看出:其一.该产品的壁厚越厚,它就越具有经济性和实用性,壁厚越薄,它的加工成本就会大幅度的上升;其次.该产品的工艺决定它的局限性,一般无缝钢管精度低:壁厚不均匀.管内外表光亮度低.定尺成本高,且内外表还有麻点.黑点不易去除;其三.它的检测及整形必须离线处理。
因此,它在高压.高强度.机械结构用材方面体现了它的优越性。
不锈钢焊接钢管焊接钢管简称焊管,是用钢板或钢带经过机组和模具卷曲成型后焊接制成的钢管。
1. 钢板>分条>成型>溶接>感应光亮热处理>内外焊道处理>整形>定径>涡流检测>激光测径>酸洗>入库2.焊接钢管的特点:从上面的工艺流程我们不难看出:其一.该产品是连续在线生产,壁厚越厚,机组及溶接设备的投资就越大,它就越不具有经济性和实用性。
壁厚越薄,它的投入产出比就会相应下降;其次该产品的工艺决定它的优缺点,一般焊接钢管精度高.壁厚均匀.管内外表光亮度高(钢板的表面等级决定的钢管表面亮度).可任意定尺。
因此,它在高精度.中低压流体应用方面体现了它的经济性及美观性。
各种管件的标准名称对照表国家标准GB12459钢制对焊无缝管件GB/T13401钢板制对焊管件GB/T14383锻钢制承插焊管件GB/T14626锻钢制螺纹管件GB9112-9131钢制管法兰、法兰盖及法兰用垫片中石化标准SH3406石油化工钢制管法兰SH3408钢制对焊无缝管件SH3409锻钢制承插焊管件SH3410钢板制对焊管件化工标准HGJ514碳钢、低合金钢无缝对焊管件HGJ528钢制有缝对焊管件HGJ10锻钢制承插焊管件HGJ529锻钢制承插焊、螺纹和对焊接管台HGJ-44-76-91钢制管法兰、垫片、紧固件HG20592-20635钢制管法兰、垫片、紧固件中石油标准SY/T0510-1998钢制对焊管件SY5257-91钢制弯管电力标准GD87-1101火电发电厂汽水管道零件及部件典型设计手册DL/T515电站弯管美国标准ASME/ANSI B16.9工厂制造的锻钢对焊管件ASME/ANSI B16.11承插焊和螺纹锻造管件ASME/ANSI B16.28钢制对焊小半径弯头和回头弯ASME B16.5管法兰和法兰配件MSS SP-43锻制不锈钢对焊管件MSS SP-83承插焊和螺纹活接头MSS SP-97承插焊、螺纹和对焊端的整体加强式管座日本标准JIS B2311通用钢制对焊管件JIS B2312钢制对焊管件JIS B2313钢板制对焊管件JIS B2316钢制承插焊管件中国阀门国家标准大全。