warehouse management
仓库管理系统英文简称

Warehouse Management System (WMS) Warehouse Management System (WMS) plays a crucial role in the efficient operation of modern supply chains. It serves as the backbone of warehouse operations by automating various processes such as receiving, storing, picking, and shipping goods. The primary goal of a WMS is to optimize inventory management, minimize stockouts, and enhance overall operational efficiency.Key Features of WMSInventory TrackingOne of the core functions of a WMS is to provide real-time visibility into inventory levels and locations. By tracking the movement of goods throughout the warehouse, WMS enables accurate inventory management and reduces the risk of stock discrepancies.Order FulfillmentWMS streamlines the order fulfillment process by optimizing picking routes, suggesting the most efficient order picking strategies, and providing tools for order consolidation and packing. This helps warehouses fulfill customer orders accurately and quickly.Warehouse Layout OptimizationWith advanced algorithms and data analysis capabilities, WMS can help optimize warehouse layout and storage strategies. By grouping fast-moving items together and locating them near the packing area, WMS reduces travel time and improves overall warehouse productivity.Integration with Other SystemsWMS is designed to seamlessly integrate with other systems such as Enterprise Resource Planning (ERP) software, Transportation Management Systems (TMS), and Order Management Systems (OMS). This ensures smooth flow of information across different departments and enhances overall supply chain visibility.Reporting and AnalysisWMS provides powerful reporting and analytics tools that offer insights into key performance indicators (KPIs) such as order fulfillment rates, inventory accuracy, and warehouse utilization. By analyzing these metrics, warehouse managers can make data-driven decisions to improve operational efficiency.Benefits of WMSImproved Inventory AccuracyBy automating inventory management processes and providing real-time visibility into inventory levels, WMS helps reduce stockouts, overstocks, and shrinkage. This leads to improved inventory accuracy and better customer service.Increased EfficiencyWMS optimizes warehouse operations by improving order picking processes, reducing travel time, and enhancing overall productivity. This results in faster order fulfillment, lower operating costs, and increased throughput.Enhanced Customer SatisfactionWith accurate inventory management and efficient order fulfillment, WMS enables warehouses to deliver orders on time and in full. This leads to improved customer satisfaction and loyalty, ultimately driving business growth.Scalability and FlexibilityWMS is highly customizable and scalable, allowing warehouses to adapt to changing business needs and scale their operations as they grow. Whether it’s adding new functionalities or integrating with new systems, WMS provides the flexibility to meet evolving warehouse requirements.ConclusionWarehouse Management System (WMS) is a critical component of modern supply chain management, providing the tools and capabilities to optimize warehouse operations, enhance inventory management, and improve overall efficiency. By leveraging the key features and benefits of WMS, warehouses can streamline their operations, improve customer service, and gain a competitive edge in today’s fast-paced business environment.In conclusion, the adoption of a Warehouse Management System (WMS) is essential for warehouses looking to improve their operational efficiency and stay ahead in the competitive market landscape. With its advanced features and benefits, WMS offers a strategic advantage to businesses seeking to optimize their warehouse operations and deliver exceptional customer service.。
20《物流专业英语》-PPT-Unit-20-Warehouse-management
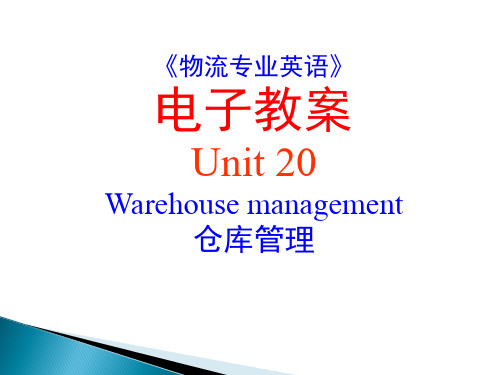
在线分拣屏
经理们应当把仓库看作是一个向客 户转运货物的临时地点,它 (指仓库)也许会涉及到临时 性的贮存,但是从本质上来说, 这是一个承担着完成客户订单 的场所,可能会分割大宗产品、 并从各处把单个物件拼装起来。
CORPORATE DATA DESIGN, INC
A BUSINESS DATABASE DEVELOPMENT COMPANY
第一部分 Section 1
本单元核心术语 Core terms
warehousing 仓储 trans-shipment 转运 bulk purchase 批量采购 split bulk items 分割散装
品种
MHE 机械搬运设备
(Mechanical Handling Equipment )
时间来温习单词。
课堂教学之——
Step 2 重点内容
➢ 掌握核心术语 ➢3 难点学习
➢ 理解并背诵核心概念 ➢ 学习时间5分钟
课堂教学之——
Step 4 课文学习
➢ 理解课文的意思 ➢ 对难句进行语法和结构讲解 ➢ 学习时间30分钟
课文学习提示:
➢ 教师在讲解课文时,除对课文进 行翻译之外,还要顺带讲解一下 难句的语法结构。
仓库的目的 仓库和配送中心有一个基本目的,就是促使物资从供应商向客
户流转。这样,仓库应当成为一个为物资或人进行高效接 收、发放或运输的转运区,客运车站的情况也一样。
Some valid reasons for holding stock include the following: As a buffer between two production processes To cover demand during suppliers’ lead time To enable savings to be made through bulk purchases or
仓库管理制度英文版
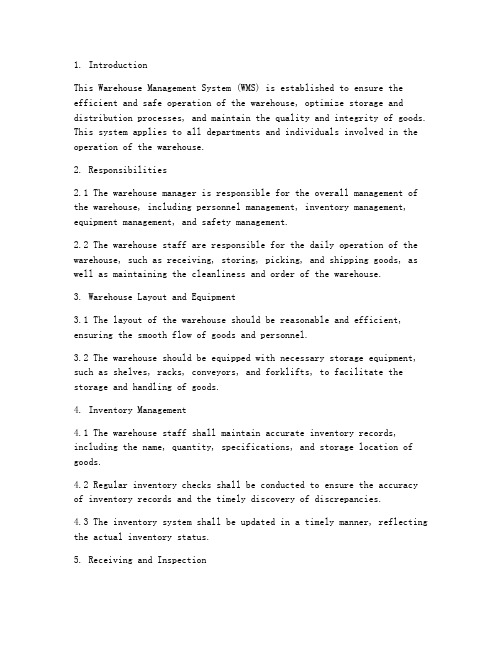
1. IntroductionThis Warehouse Management System (WMS) is established to ensure the efficient and safe operation of the warehouse, optimize storage and distribution processes, and maintain the quality and integrity of goods. This system applies to all departments and individuals involved in the operation of the warehouse.2. Responsibilities2.1 The warehouse manager is responsible for the overall management of the warehouse, including personnel management, inventory management, equipment management, and safety management.2.2 The warehouse staff are responsible for the daily operation of the warehouse, such as receiving, storing, picking, and shipping goods, as well as maintaining the cleanliness and order of the warehouse.3. Warehouse Layout and Equipment3.1 The layout of the warehouse should be reasonable and efficient, ensuring the smooth flow of goods and personnel.3.2 The warehouse should be equipped with necessary storage equipment, such as shelves, racks, conveyors, and forklifts, to facilitate the storage and handling of goods.4. Inventory Management4.1 The warehouse staff shall maintain accurate inventory records, including the name, quantity, specifications, and storage location of goods.4.2 Regular inventory checks shall be conducted to ensure the accuracy of inventory records and the timely discovery of discrepancies.4.3 The inventory system shall be updated in a timely manner, reflecting the actual inventory status.5. Receiving and Inspection5.1 When receiving goods, the warehouse staff shall check the quality, quantity, and specifications of the goods against the purchase order and inspection report.5.2 Any discrepancies shall be reported to the relevant department for handling.6. Storage and Handling6.1 Goods shall be stored in designated areas according to their characteristics, such as shelf life, flammability, and toxicity.6.2 Goods shall be handled with care to prevent damage or contamination.6.3 The warehouse staff shall regularly inspect the stored goods to ensure their quality and integrity.7. Picking and Shipping7.1 Picking operations shall be conducted according to the order requirements, ensuring the accuracy and efficiency of the picking process.7.2 Goods shall be packed and labeled properly before shipping.8. Safety and Environment8.1 The warehouse shall comply with safety regulations and standards, including fire prevention, electrical safety, and personal protective equipment.8.2 The warehouse staff shall be trained on safety procedures and emergency response measures.8.3 The warehouse shall maintain a clean and tidy environment, with proper waste disposal and ventilation.9. Training and Evaluation9.1 The company shall provide regular training for the warehouse staff on warehouse management, safety, and other relevant issues.9.2 The performance of the warehouse staff shall be evaluated periodically to ensure the continuous improvement of the warehouse management system.10. Confidentiality10.1 The warehouse staff shall keep the company's business information confidential and not disclose it to unauthorized personnel.11. Violation and Punishment11.1 Any violation of this Warehouse Management System shall be subject to disciplinary measures, including warnings, fines, and termination of employment.12. Revision12.1 This Warehouse Management System may be revised and updated from time to time as needed.By implementing this Warehouse Management System, the company aims to achieve efficient, safe, and reliable warehouse operations, ensuring the satisfaction of customers and the continuous improvement of the company's competitive advantage.。
Unit 3 Warehousing Management and Inventory Control 《物流英语》教学课件

Control
➢Warehousing Management ➢Inventory Control
Listening & Speaking
Ⅰ. Listen to the sentences and fill in the blanks with what you exactly heard.
5. Inventories are vital to a company to help it function smoothly.
Ⅱ. Listen to the dialogues and fill in the blanks with what you exactly heard.
1. A: Why are public warehouses so popular with manufacturers and retailers?
拥有私人仓库的零售商在某些情况下,比如当他们的 仓库存储能力不够,或他们在进行特别的大批量的采购时 也会租用公共仓库。
Ⅲ. Listen to the passage and fill in the blanks with what you exactly heard, the first letters have been given.
A warehouse is a commercial building for storage of goods. Warehouses are used by manufacturers, importers, exporters, wholesalers, transport businesses, customs, etc. They are usually large plain buildings in industrial areas of cities and towns. They come equipped with loading docks to load and unload trucks, or sometimes are loaded
Warehouse Management System _07 - Stock Receipt

Goods receiptPurposeA goods receipt in the Warehouse Management system (WMS) is the physical inbound movement of goods or materials into the warehouse. It is a goods movement that is used to post goods received from external vendors or from in-plant production. All goods receipts result in an increase of stock in the warehouse.IntegrationA goods receipt in the WMS can be triggered by several business transactions in various components of the SAP system. The corresponding reference document in the WMS triggers the goods receipt:Reference documents for goods receipt in the WMSPrerequisitesThe data in the reference documents for the goods issue in the WMS is complete.FeaturesYou have the following possibilities for goods receipt posting:∙Goods Receipt Handling With Reference to Inbound DeliveryIf you use the decentralized Warehouse Management system or Handling UnitManagement, the data necessary for creating the transfer orders is transferred from the inbound delivery. You can decide whether you want to post the goods receipt before orafter the putaway.∙Goods Receipt Handling Without Reference to Inbound DeliveryIf you want to post the goods receipt for unpackaged materials, the goods receipt is first posted in Inventory Management, from which the Warehouse Management systemgenerates a transfer requirement. Typical processes for this are, for example:o Goods receipts with reference to a purchase ordero Goods receipts with reference to a production order∙Goods Receipt Without Previous Goods Receipt Posting in IMIn this case, you put away the goods first by creating a transfer order in the WMS and not posting the goods receipt until later.Goods Receipt Handling with Reference to Inbound DeliveryPurposeIf you work with a decentralized Warehouse Management system (WMS) or Handling Unit Management, the basis of goods receipt handling in Warehouse Management is the inbound delivery . The system then creates transfer orders for putaway with reference to inbound deliveries or to handling units.Process FlowYou have the following possibilities to create transfer orders with reference to inbound deliveries:∙Entry of the inbound delivery numberHere you can create transfer orders as follows:o Via the inbound delivery monitoro Bycreating a transfer order for an inbound deliveryo Automatically in the background if you have set up the message WMTA and assigned it to the inbound delivery (see alsoAssigning Output Type WMTA to Inbound Deliveries)The SAP system creates the transfer orders from the materials or handling units in theoutbound delivery and determines the destination storage bins.∙If you have set up Handling Unit Management, you have the following possibilities for creating a transfer order with reference to a handling unit:o By creating a transfer order for a storage unito By creating a transfer order from the stock listo Automatically in the background if you have set up the message WMTA and assigned it to the inbound delivery (see also Assigning Output Type WMTA toInbound Deliveries)The SAP system determines in the background which inbound delivery is assigned towhich handling unit. The inbound delivery is updated via the transfer order for putaway.This function is also supported if the handling unit is nested and refers to several delivery items.This kind of transfer order creation is particularly suitable if you scan handling units, since you can process every handling unit individually.If you work with a decentralized WMS, you can find more detailed information under Goods Issue in a Decentralized Warehouse.Putaway Before Goods Receipt Posting1.Create an Inbound Delivery2. If you work with handling units, pack the materials (see also:Packing for Inbound and Outbound Deliveries)3. Carry out theputaway (of handling units).Confirm the putaway transfer order before posting the goods receipt. The storage unit is in the destination storage bin of the transfer order. The system creates a negative quant with the storage unit number in the source storage bin.You can enter differences when you confirm the transfer order. However, you can onlyconfirm difference in the source storage bin. If you have set the indicator TransferPutaway Quantity, the putaway quantity is reduced (see also Define ShippingControl).After confirmation the quantities are available in the destination storage bin. In this case, you can move the storage unit within the warehouse. However, you can only removepartial quantities or pick for a delivery after posting the goods receipt.4.Post the goods receipt.When you post the goods receipt for inbound delivery, the system deletes the negativequants in the goods receipt area and makes a note in the storage unit that partialwithdrawal is now possible. You can now post the goods receipt for the entire inbounddelivery.Goods Receipt Posting Before Putaway1.Create an Inbound Delivery2. If you work with handling units, pack the materials (see also:Packing for Inbound and Outbound Deliveries)3.Post the goods receipt.4.Carry out the putaway (of handling units).Manual Creation of Transfer Orders for Putaway UseYou can also create transfer orders manually if you have a goods movement that only involves internal transfer of goods.Procedure1. If you wish to manually create a transfer order for a transfer requirement, choose fromthe SAP menu Logistics → Logistics Execution→ Inbound Process → Goods Receipt for Purchase Order, Order, Other Transactions → Putaway → Create Transfer Order → For Transfer Requirement.If you wish to manually create a transfer order for a material document, choose from the SAP menu Logistics → Logistics Execution→ Inbound Process → Goods Receipt forPurchase Order, Order, Other Transactions → Putaway → Create Transfer Order → For Material Document.If you wish to manually create a transfer order for an inbound delivery, choose from the SAP menu Logistics → Logistics Execution→ Inbound Process → Goods Receipt forPurchase Order, Order, Other Transactions → Putaway → Create Transfer Order → For Inbound Delivery.If you want to manually create a transfer order without a source object, choose from the SAP menu Logistics → Logistics Execution → Internal Whse Processes → StockTransfer → Create Transfer Order → No Source Object.2.Enter the required data and choose Continue.You cano Enter palletization data to have the goods ready for being set to storage status.o Enter the destination bin manually.o Add the material to stock in storage bins where there are already quants of the same material. Choose Add to Existing Stock.If you choose Putaway background, the system will create the destination storage bin.If you process the transfer requirement in the foreground, you can change the destination storage bin proposed by the system.You receive a list of all bins where this material is already stored and where you can add to the existing stock. Here you can select bins for calculation of the respective additional stock quantity, or you can enter the open quantity to be added to the existing stock.If the capacity check is not active for the storage bin, the column Available capacity remains empty.If you select bins and choose Max.quantity to be added to stock, the system adds the open quantity to the Column Qty to be added from top to bottom based on the available capacity for the bins.If the quantity shown in the Available capacity column is displayed as a decimalnumber, you may need to manually adjust the quantity calculated by the system in the Qty to be added field. If the open quantity to be added is 200 pieces, forexample, and the available capacity is shown as 123,648 pieces, you need tocorrect the quantity in the Qty to be added column to 123 pieces.3. To post the transfer order to the database, choose Transfer order → Post.Processing ReturnsPurposeUsing this process, you can put rejected goods from a return back into your warehouse.Prerequisites∙You have created and released a return for a complaint.For more information, see Creating Returns.∙You have flagged the item category for returns deliveries as relevant for picking in the Customizing for Shipping under Picking →Define Relevant Item Categories.Process Flow1. You create a returns delivery for the return.If you use Handling Unit Management (HUM) and you want to put away the goods in a HU-managed storage location, pack the goods.2.You create a transfer order based on the (returns) delivery.When the transfer order is created, the system determines the destination bin for thematerial to be putaway on the basis of predifined putaway strategies.3.You put away the goods and confirm the transfer order.4.You post the goods receipt for the (returns) delivery.Goods Receipt Handling Without Reference to Inbound DeliveryPurposeIf you only want to post the goods receipt for materials that are not packed (that is, not in handling units) and you do not want to use the decentralized Warehouse Management system, you post the goods receipt in Inventory Management. The Warehouse Management system then generates a transfer requirement.Process FlowWhen goods are received in the warehouse, the processes that take place in Warehouse Management (WM) are generally automatic and transparent to the user. From the time a dock worker scans a bar code on the container slip until the goods are putaway in a storage bin within the warehouse, WM records of all the transactions for a material. The system can automatically execute all of the necessary steps – from posting the goods receipt in Inventory Management (MM-IM) to confirming the movement. The individual steps in this process are:1.To trigger the transactions necessary for goods receipt in WM, post the good issue inInventory Management (see also: Goods Receipt in Inventory Management).2.As a result of stock posting, the system creates a quant in a storage bin in a goodsreceipt interim storage area and creates a transfer request in WM.(For more information about types of interim storage areas, see WM Interface toInventory Management (IM).)3.The system then (automatically) creates a transfer order on the basis of the information inthe transfer request.ing a predetermined search strategy, the system determines the storage bin in whichthe goods are to be stored and divides them into pallets.5.The transfer order is used to transfer the goods from the interim storage bin in the goodsreceipt area zone to one or more storage bins in the warehouse.6.The warehouse worker confirms the transfer of the goods. He can enter this manuallyinto the system or automatically by using RF equipment to scan the bar code on thecontainer.Differences between the quantity requested and the quantity transferred into thewarehouse are recorded in WM. You must post these in IM later.ResultThe goods receipt process is complete.ExampleThe following figure shows a possible scenario for an inbound movement in conjunction with a transfer order (TO). This example shows the processes in the warehouse and in WM for a goods receipt.Creating Transfer Orders Immediately at the IM PostingUseYou can set up your system so that transfer orders are created immediately in the background when you post material documents in the Inventory Management component. PrerequisitesYou have set up automatic transfer order creation in the system. You have assigned mail message recipients separately for each movement type.You can define these settings in Customizing for Warehouse Management under Interfaces →Inventory Management→ Define Movement Types →LE-WM Interface inventory management in the TR Create transf. requirement field.FeaturesYou create material documents in Inventory Management (IM) as usual. The Warehouse Management system (WMS) then creates the relevant transfer requirements and posting change notices automatically if this function is included in the relevant WM movement type.If the following conditions are met, the system immediately creates a transfer order for a material posting in Inventory Management (MM-IM)When you post a material document in IM, and movement types both "with" and "without" automatic transfer order creation exist in that document, the system does not start the automatic transfer order creation program. Instead, it goes directly to the screen for creating a transfer order for a material document.If the system does not create a transfer order automatically, even though youhave set the indicator for Automatic TO creation in the transport requirementsheader you should set up your system so that it sends a mail message to a userin cases like these. The user can then process the error from within the message. ActivitiesIf direct transfer order creation is not possible, you have to create the transfer order for the material document manually.Goods Receipt Without Previous Goods Receipt Posting in IMPurposeYou put goods away by creating a transfer order in the Warehouse Management system (LE-WM) first, without posting a goods receipt in Inventory Management (MM-IM) first.PrerequisitesYou use SAP Inventory Management (MM-IM).You have made the following settings in the Customizing for Warehouse Management:∙You have not set the indicator TR (for automatic creation of transfer requirement) for the relevant WM reference movement type under Interfaces → Inventory Management →Define Movement Types →LE-WM Interface inventory management.∙You use a special movement indicator for when you want to make an exception and activate automatic transfer requirement creation for this movement type. To do this,define a new movement type, assign a special movement indicator to the new movement type and set the indicator TB (for automatic creation of transfer requirement)∙Negative stock is allowed in the interface storage type.To do this, choose the menu path Master Data→ Define Storage Type in theCustomizing for Warehouse Management and set the indicator Allow negative stock. Process Flow1. The goods to be put away are in the goods receipt interim storage area of yourwarehouse.2. You create atransfer order for goods putaway.When you create the transfer order, the system determines the storage bin for thematerial on the basis of a predefined search strategy.The system creates a negative quant in the goods receipt interim storage area.3.You put away the goods from the goods receipt interim storage area in one or morestorage bins, based on the transfer order.4.You confirm the transfer order and enter any differences.Once you confirm the transfer order, the goods are available in the system.You can find additional information on entering differences under handling differences.5.You post the goods receipt in Inventory Management (MM-IM).When you post the goods receipt, you increase the stock and clear the negative quant inthe goods receipt interim storage area, and a positive quant is created in the destinationstorage bin for the material.ResultThe goods receipt process is complete.Creating a TO in WM Without Previous Posting in IMThis process is explained using the transfer of a pallet from production into the warehouse as an example. The goods are brought to the identification point of a high rack storage area on a conveyor belt and are to be put away there.1.To create the transfer order, choose Logistics→Logistics Execution→InternalWarehouse Processes→Stock transfer→Create Transfer Order→No Source Objectin the SAP menu.2.In the initial screen, enter the warehouse number, WM movement type (103), quantity,material number, and plant. If you enter a storage unit type (in the Stor.unit type field), the system uses the unit type you enter instead of the storage unit type in the material master record (if available).If you have a single storage unit type, choose Goto → Single item to go to the itemgeneration screen. If you are creating a transfer order for more than one storage unit type, choose Enter or Goto → Preparation to go to the preparation screen where the systemproposes storage unit types and quantities.3.If you selected the item generation screen (for a single storage unit type), the systemproposes the destination storage bin and type, as well as the quantity of material that will be placed in the storage bin. The proposed values depend on the storage unit type andputaway strategy for the storage type, among other things. To create a transfer order that consists of only one item choose Enter. The system returns to the initial screen andissues a message that the transfer order has been created.If you create a transfer order for more than one storage unit type, you arrive at thepreparation screen. The system proposes the palletization from the material masterrecord. You can accept the proposed values or overwrite them. Choose either Goto→Generate TO item→Foreground process, or Goto → Generate TO item→Backgroundprocess, to create the transfer order items, which are displayed on the preparation screen.To save the transfer order, choose Transfer order→Post. The system returns to theinitial screen and issues a message that the transfer order has been created.The quantity is posted in WM via this transfer order. A negative quantity is posted to the goods receipt interim storage area, while a positive quantity is posted to the destination storage area. These individual quantities cancel each other out, balancing the WM total stock out to zero.Displaying the Stock BalanceIf you want to see the summarized stock overview for a particular material according to storage type, choose Logistics→Logistics Execution→Internal Warehouse Processes→Bins and Stocks→Display→Total Stock per Material (Warehouse Management) in the SAP menu. Posting Goods Receipt in IMYou complete this type of goods receipt by posting it in IM.1. Choose Logistics → Logistics Execution → Inbound Process → Goods Receipt forPurchase Order, Order, Other Transactions → Putaway → Create Transfer Order → For Material Document from the SAP menu.2. On the initial screen, enter (at least) movement type 101 with reference to the productionorder, and the plant.The stock in IM is increased via this function. Additionally a positive quantity is posted to the goods receipt interim storage area in WM. This means that the negative quantity inthe interim storage area is deleted, resulting in a positive quantity in the storage bin.Allowing Negative StockUseWarehouse Management (WM) manages negative stock in interim storage areas. If movements occur that require the use of interim storage areas, the stock balance between Inventory Management (IM) and WM must remain constant. This is made possible by posting negative stock.The system posts negative stock when a goods receipt is posted in IM before the goods receipt posting, for example.ProcedureYou can define whether you want to allow negative stock by making the relevant settings for each storage type in Customizing.1.To do this, choose Logistics Execution → Warehouse Management → Interfaces →Inventory Management →Allow Negative Stocks in Interim Storage Types →Allownegative stock for each storage type in the Implementation Guide (IMG).2.When the allow negative stock indicator is set, the system lets you post negativequants to the corresponding storage type.Additionally, you can define whether you want the system to issue an error message (E) or a warning message (W) or no message (blank) when posting negative stock. You can make therelevant setting in the activity Control of System Messages in Warehouse Management. You can determine the notification type using the parameter MSV in the user master record.1.To do this, choose System → User profile → Own data.2.Then select the tab page Parameters.3.Enter MSV in the Parameters field and enter the value with which you want to groupcertain users in the value field (for example 01).4.Choose Logistics Execution → Warehouse Management → Interfaces → InventoryManagement →Allow Negative Stocks in Interim Storage Types →Control of SystemMessages in Warehouse Management in the Implementation Guide (IMG).5.Create a new entry with the version number (Value) you have chosen and enter thedesired system reaction in the Message Category field (E, W, or blank).∙Version= Parameter MSV from the user master∙Application area= L9∙Message No.= 040∙Message Category= E, W, or blankIf the parameter MSV is not maintained in the user master, the system uses version 00.Adding Goods to Existing StockUseWhen addition to existing stock has been defined for a storage type, the system places goods in storage bins that already contain the same material. When you create the transfer order for the putaway, the system uses the storage type record to determine whether the particular putaway strategy or the indicator in the material master allows additional stock.PrerequisitesDefine that addition to existing stock is allowed for the desired storage type.1.Define the storage types in the IMG under Logistics Execution→WarehouseManagement→Master Data→ Define Storage Type.2.Select the storage type you want and choose Goto → Details.a.If you want to allow addition to existing stock generally, enter X in the Addn tostock field.b.If you want to allow addition to existing stock according to the settings in thematerial master, enter M in the Addn to stock field.If you want to allow addition to existing stock in a storage type according to theindicator in the material master, set the Allow addn to stock indicatorfor the relevant material in the material master.a.To do this, choose Logistics→Logistics Execution →Master Data → Material → Change → Immediately inthe SAP menu, if you want to change a material whichalready exists.b.Enter the desired material.c.Choose the Warehouse Management 1 view.d.Enter the plant, warehouse number, and storagetype for the material.e.Set the allow addn stock indicator in the Storagestrategies area.Procedure1. If additional stock is allowed, choose Goto→Add to existing stock in the preparation screen to display the information about thestorage bins in which the material is already being stored. This screen shows the storage type and storage bin, total stock in the storage bin and the remaining available capacity.2.On the add to additional stock screen, you can select one or more storage bins, in whichyou want to store the material.To create the transfer order item, choose either Edit→ For stock placement→ Foreground or Edit→ For stock removal→ Background.If the strategy for the storage type is set for addition to existing stock, the systemautomatically selects the appropriate storage bin.3.Once you have created the transfer order item, choose Transfer order→Post from thepreparation screen to save the transfer order to the database.Goods Receipt for InspectionPurposeFor goods that are delivered from an external supplier or from internal production, you can first of all post them to inspection stock. Goods that you have posted to inspection stock do not belong to unrestricted stock and are not available for stock removal.PrerequisitesWhen posting the goods receipt in Inventory Management (MM-IM), the quality check indicator is set on the item screen for the stock type. This means that the quant, which is created in the interim storage area, and the transfer requirements (TR) for putaway in WMS receive the stock category Q (inspection stock).To make sure that the inspection stock indicator is always set, you have defined it in the material master or set it when creating the order.Process FlowReceiving Material into Inspection Stock1. You post a goods receipt for the purchase order.2. A quant with dynamic coordinates and stock category Q is created in the goods receiptinterim storage area of WMS for the material received.3. The system creates a transfer requirement (TR) with stock category Q.4. You create a transfer order in WMS for putting away the material on the basis of the TR.5. You put the material away in the warehouse and confirm the transfer requirement. ResultYou have put away the material. However, although the material is in the warehouse, you cannot remove it from stock because it is part of the quality inspection stock with stock category Q.See also:Release from Quality Inspection StockProcessing Preallocated StockPurposePreallocated stocks are materials that you urgently need for goods issue but which are not available in the warehouse, for example materials required urgently by production, materials required by the customer, or quantities in backlog. In the Warehouse Management system (WMS), you can flag materials as preallocated stock in the system and forward them directly from the goods receipt interim storage area to the goods issue interim storage area.You provide the goods issue interim storage area with the preallocated stock via what is know as a bypass, directly from the goods receipt interim storage area. This way, you miss out putting away the preallocated stock and then removing it from storage again.Prerequisites∙You have set up the relevant movement types for the bypass in the Customizing for Warehouse Management under Activities→Transfers→Define Movement Types.There you set the Consider Pre-Alloc. Stock indicator for the respective movement type.∙You have flagged the material as preallocated stock in the preallocated stock table and entered the necessary data under SAP Menu→Logistics→Logistics Execution→Outbound Process→Goods Issue for Other Transactions→Picking→Maintain Missing Stock.In doing so, the system uses the current number to differentiate entries for the samematerial. You can enter any number as the current number.Process Flow1. During creation of the putaway transfer order, the system determines, on the basis of thesystem settings for the source movement type, whether the material to be put away is to be checked for preallocated stock.If you have set the Consider Pre-Alloc. Stock indicator for the source movement type, the system checks the entries in the preallocated stock table.2. If you have entered the material in the preallocated stock table, the system emits amessage to show that the material is preallocated stock.3. During transfer order creation, you can display information from the preallocated stocktable.4. If you choose Calculate Selected Quantity, the system transfers the open quantity fromthe preallocated stock table into the column Selected Quantity.5. You save the transfer order.ResultThe material flagged as preallocated stock is transferred directly from goods receipt to the goods issue interim storage area.If the quantity of material to be away in the transfer order is less than the quantityentered in the preallocated stock table, the system transfers the smaller quantityas the Selected Quantity and reduces the quantity in the preallocated stock tableaccordingly.If the quantity of material to be put away in the transfer order corresponds to orexceeds the quantity entered in the preallocated stock table, the system removesthe entry from the preallocated stock table when the transfer order is confirmed. Putaway Using Storage Unit TypesThe Warehouse Management system (WMS) component allows you to use a number of different storage unit types when you transfer and put away materials. You can transfer and put away materials on pallets of various sizes, such as Europallets or industrial pallets.。
WM简介
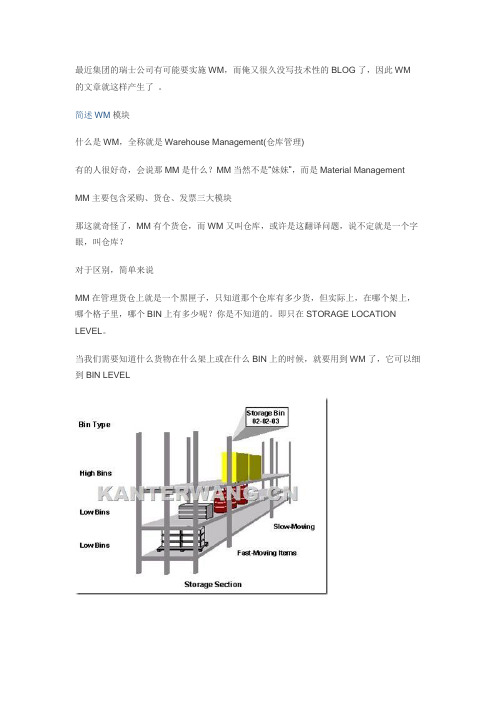
最近集团的瑞士公司有可能要实施WM,而俺又很久没写技术性的BLOG了,因此WM的文章就这样产生了。
简述WM模块什么是WM,全称就是Warehouse Management(仓库管理)有的人很好奇,会说那MM是什么?MM当然不是“妹妹”,而是Material ManagementMM主要包含采购、货仓、发票三大模块那这就奇怪了,MM有个货仓,而WM又叫仓库,或许是这翻译问题,说不定就是一个字眼,叫仓库?对于区别,简单来说MM在管理货仓上就是一个黑匣子,只知道那个仓库有多少货,但实际上,在哪个架上,哪个格子里,哪个BIN上有多少呢?你是不知道的。
即只在STORAGE LOCATION LEVEL。
当我们需要知道什么货物在什么架上或在什么BIN上的时候,就要用到WM了,它可以细到BIN LEVEL这个货架用来解释WM比较好,你可以准确地知道在那个格子中,如图片中的02-02-03,第一个02,表示02货架(SAP用SHELF),第二个02表示第二列(SAP用STACK),03则表示第三层SAP 用LEVEL)以下是MM结构图以下是WM的结构图根据MM与WM结构图一对比,就可发现其中的差异点。
但细分的TX会发现,MM中有个STORAGE LOCATION而在WM中没有,只有WAREHOUSE,这两玩意如何关联呢?由衷的赞美。
聪明,绝对是聪明,问题点一下就被发现了。
先来阐述我理解的程序开发吧。
像SAP这么大型的系统,不可能是一组人就把MM,PP,SD,FI,CO,WM,PS之类的完全开发出来,那要如何做呢,正常来说,就是每个模块都有不同的组负责,比如说MM部分,这是一组人在负责,这组人只管MM方面的一些操作,至于FI,WM等相关的,暂时不考虑而另一组人就去专门开发WM的程序,这些人也不管MM是如何整的各自按照各自行业或模块的专业去开发,只是等都开发完了,然后找个接口,把他们接起来就OK,这样在各个模块都比较专业。
当代物流学第十章WarehousingManagement
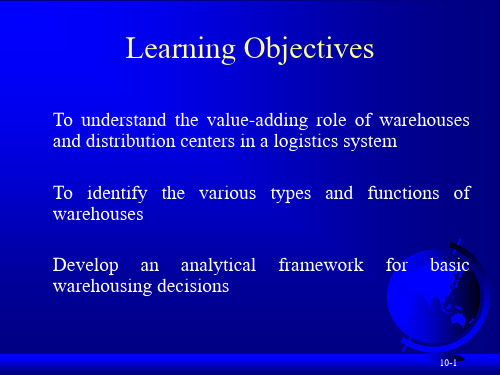
Manufacturer D
7,000 lb. D
11-6 10-15
Example: Storage Cost Savings
Direct shipments to customers
SHIPPING
WEIGHT LTL RATE TTOMER COST
公司的总裁具有良好物流管理意识,他在考虑如 何在全美国各地租用仓库可能会降低总成本。他认为 虽然那样仓储费用会增加,但可以先将资料以整车运 到各个仓库,然后由UPS从大约35个仓库做短距离运 输,送到当地分拨点。因为当地分拨点可以从仓库提 货,而不必直接向印刷厂订货,因而不会常常变化生 产计划,所以生产成本也可能会因此降低。
10-27
Firm Characteristics Affecting the Ownership Decision
10-28
The Number of Warehouses
Factors Affecting the Number of Warehouses
– Inventory costs – Warehousing costs – Transportation costs – Cost of lost sales – Maintenance of
10-26
The Ownership Decision
Factors to consider
– Throughput volume – Stability of demand – Density of market area to be served – Security and control needs – Customer service needs
10-23
Basic Warehouse Decisions: A Cost Trade-off Framework
仓库管理开题报告

开题报告1. 课题背景仓库管理WMS(Ware House Management System)是本世纪中期发展起来的一门新兴学科。
它最早产生于二战时期的美国,五十年代中期,仓库概念传人日本,并得到快速发展。
时至今日,仓库管理已成为西方企业管理中不可或缺的一部分,在许多国家得到了广泛的研究与应用。
总的说来,仓库管理就是通过采购、仓储、综合、出库、配送等活动,解决物资供需之间存在的时间、空间、数量、品种价格等方面的矛盾,以此衔接社会生产的各环节,从而确保生产的顺利进行。
计算机始于数值计算,却在非数值计算中得到了广泛的应用,显示了它强大的生命力。
在现代计算机应用领域中,数据处理约占70~80%。
数据库技术是数据处理的最新研究成果。
它的出现,使得计算机应用更加广泛地渗透到工业、农业、商业、文教、卫生及军事等各个领域。
数据库系统作为计算机软件的一个分之,与其他软件技术及其其他学科领域有着密切的关系。
它几乎涉及到计算机领域的所有知识,是各种知识和技术的综合应用。
随着社会经济的发展和工业生产的加速,仓库的进出更为频繁,仓库信息更为重要。
传统仓库管理完全由人来完成,以手工记录为主,当企业的物流业务成长到一定规模之后,随着订单数量的增加,客户需求不断个性化,执行效率就成为物流发展的瓶颈,单纯依靠人力资源的增加已不能提升出入库执行的速度,反而带来成本的大幅度上升与差错频频。
计算机信息管理技术的迅速发展恰恰解决了这个问题,它使计算机技术与现代的管理技术相互配合,来更加准确、高速地完成工业企业日常的仓库管理工作。
使企业能够以最少的人员来完成更多的工作。
2. 国内外形势分析随着我国市场经济的进一步开展,强大的信息保障,有力的电子化管理,使各大企业在国内经济市场的大潮中把现代高科技的信息技术发挥的淋漓尽致。
越来越多有远见的企业家,不惜重金从国外购买高新技术,高的投资、合理的管理往往换来巨大的利润。
经营的物质技术手段由简单落后转变成高科技与人工手段并存,进而更多地将高科技应用到零售商业。
- 1、下载文档前请自行甄别文档内容的完整性,平台不提供额外的编辑、内容补充、找答案等附加服务。
- 2、"仅部分预览"的文档,不可在线预览部分如存在完整性等问题,可反馈申请退款(可完整预览的文档不适用该条件!)。
- 3、如文档侵犯您的权益,请联系客服反馈,我们会尽快为您处理(人工客服工作时间:9:00-18:30)。
关于上海山隆实业有限公司新仓库管理的设想
经过半天的新老仓库参观考察,针对上海山隆公司仓库配送中心的定位以及仓储货品的特点,个人谈一些不成熟的意见,此文主要是提纲性质,限于篇幅不能展开,相对来说比较简单,希望起到抛砖引玉的作用,如有不当之处还望谅解。
所谓仓库就是指在产品生产或商品流通过程中因各种原因而使货物暂时存放的场所。
仓库管理就是对仓储的货物的收发、结存等活动进行有效控制,其目的是为企业保证仓储货物的完好无损,确保经营活动的正常进行,并在此基础上对各类货品的活动状况进行分类记录,以明确的图标方式表达仓储货物在数量、品质方面的状况,以及目前所在的位置、部门、订单归属和仓储程度等情况的综合管理形式。
针对仓库管理的这个定义特点,我准备分别从货物管理、账目
管理以及人员管理三方面来进行阐述。
一.货物管理
1.货仓的规划
货仓的设置是为了满足企业经营和产品的周转和储备的需要,所以货舱规划要满足以下原则:
a.符合产品特点原则
b.符合进出顺利原则
c.满足安全的原则
2. 货仓的内部分类
不同的食品对储存环境有其不同的要求,有些物品需要专品专库,例如糖果、巧克力需要放入恒温库,而有些物品需要做好防水、防尘、防潮、防腐等措施,以免损毁或变质。
所以要对物品进行归纳、分类,然后再进行分类储存。
另外对工具、原材料、液压车,叉车等仓库使用设备也需要在仓库里划定规定的摆放区域。
a.仓库工作人员区域
b.搬运组区域
c.食品库区域
d.恒温库区域
e.呆废料区域
f.包装材料区域
g.工具用品区域
h.卸货平台区域
i.办公区域
j.休息区域
3. 货架、托盘的选择
按货架构造分类:我认为公司可以在单元货格式立体仓库和贯通式立体仓库两者之间做个选择。
根据观察公司目前采用的托盘基本
都是木头材料,尺寸应该在80*120*10。
a.单元格式
b.贯通式
4.货物的堆放
货物堆放要多利用货仓空间,提高货舱实用率,由于采用了货架,所以要利用机器装卸,使用堆高机,通路要保证顺畅,保持装卸空间,考虑先进先出原则,考虑读取数量容易。
a.六号定位法:
按照:库号、仓位号、货架号、层号、订单号(入库号)、物料编号等六号对物料进行归类叠放,登记造册。
并填制货品储位图便于迅速查找。
b.托盘管理法:
货品码放在托盘上,成板叠放和运输,有利于叉车移动提高搬运效率。
C.分类管理法:
将品种繁多的物品,按其进出仓率,价值大小,资金占用情况,实效性等进行分类,并置放在不同区域,做到重点管理,兼顾一般。
5.仓库的5s管理:(不具体展开)
a.整理(seiri)
b.整顿(seiton)
c.清扫(selso)
d.清洁(seiketsu)
e.教养(shitsuke)
二.账目管理
账目是公司生产经营过程或结果的表达方式,清晰准确的货仓账目,是核查工作成效的基础,货舱的常用表单有«货物入仓单»、«发货单»、«退料单»、«补料单»、«出库单»、«废料处理单»、«报废单»等,我会根据实际情况采用相应的表单。
依据货仓性质还需准备«进货日报表»、«出货日报表»、«库存日报表»、«退货日报表»等。
1.依照货物验收规定,点收物料。
2.建立完整的物料账以及物料卡。
a.出库单
b.进库单
c.退货单
d.废料单
3.当日货物账目,当日完成。
4.依照发货规定发送货物。
5.做好定期盘点工作。
a.盘点票
b.盘点盈亏表
三. 人员管理
货仓的主要工作职责可以解释为三个字“收”、“管”、“发”,为了贯彻执行这个最终的目的,需要建立仓库管理的组织结构。
根据不同区域的相关人员的工作内容,需要制定相应的岗位操作说明书(工作职责),对员工进行培训,并随时在工作中改进说明书,完善工作职责规定,严格按照条例办事,形成系统化的岗位操作文件,这样可以形成山隆公司仓库的标准化操作流程。
任何新人到岗只要按照操作说明书就马上能够胜任岗位。
以下是我暂定的各个不同岗位人员的工作职责,在实际工作中一定会有改动变化。
1.仓库经理的工作职责:
a.负责仓库的整体工作事务。
b.与公司其他部门的沟通与协调。
c.参与公司宏观管理和策略制定。
d.仓库工作的筹划与控制。
e.审订和修改仓库的工作规划和管理制度。
f.检查审核仓库各级员工的工作进度和工作绩效。
g.签发仓库各种文件和单据。
h.仓库各级员工的培训工作。
2.经理助理的工作职责:
a.负责仓库内部各项具体工作的管理。
b.具体执行和督导仓库的各项工作计划的落实。
c.参与仓库整体工作的研究与完善。
d.参与评估现有工作的合理性与有效性并提出改善意见。
e.加强各区域之间工作的协调与控制,保障各区域协调运作。
f.落实分配仓库工作计划。
g.具体考核仓库员工的工作绩效。
3.仓库员工的工作职责:
a.负责公司日程事务。
b.按规定收发货物。
c.每日货物明细账目登记。
d.货物进仓库后仓位的筹划于排放(绘制仓库平面图)
e.仓库的安全工作和货物保管。
f.填写仓库相关报表。
g.盘点工作的具体执行。
h.接受岗位培训。
4.仓库文员的工作职责:
a.根据仓库的原始单据及时输入电脑。
b.根据电脑单定期或不定期对账目和实物进行抽查,并向经理反
映结果。
c.统计单据的进出库状况,打印电脑汇总表。
d.向会计部门提供成本核算资料。
e.对仓库进出仓货物活动情况的终端跟踪。
f.监督仓库货物进出发货收货情况。
5.搬运组的工作职责:
a.货物的搬运和仓库呆废品的回收和保管。
b.来货时的及时进仓和出货时的及时装车。
c.对待检货品的妥善保管,并做好标示。
d.对滞留货物进行维护,以防倒塌,遗失或变质。
e.对搬运货品要种类规格等区分明确,不混淆搬运。
f.搬运过程中对易碎物品要轻拿轻放。
g.维护和管理搬运工具。
h.接受搬运人员岗位的培训。
6.司机的工作职责:
a.遵守国家道路交通条例,尊守员工手册。
b.爱惜公司车辆,平时注重车辆保养,保证车辆正常行驶。
c.出车前货单货物对照确认,保证货物安全及时送达。
d.出车前检车车况,保证车体清洁。
e.对终端已下架货品或有问题货物要及时按调运单调回。
f.服从公司的安排,对安排工作有异议要在工作完成后提出。
g.接受岗位培训工作。