Definition and diagnostics for the model-observations - Knmi定义与诊断模型的观察——KNMI共16页
什么是 NDT
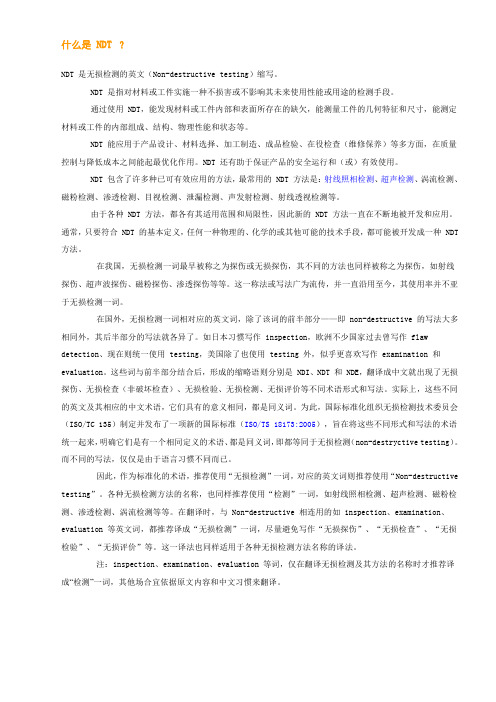
什么是 NDT ?NDT 是无损检测的英文(Non-destructive testing)缩写。
NDT 是指对材料或工件实施一种不损害或不影响其未来使用性能或用途的检测手段。
通过使用 NDT,能发现材料或工件内部和表面所存在的缺欠,能测量工件的几何特征和尺寸,能测定材料或工件的内部组成、结构、物理性能和状态等。
NDT 能应用于产品设计、材料选择、加工制造、成品检验、在役检查(维修保养)等多方面,在质量控制与降低成本之间能起最优化作用。
NDT 还有助于保证产品的安全运行和(或)有效使用。
NDT 包含了许多种已可有效应用的方法,最常用的 NDT 方法是:射线照相检测、超声检测、涡流检测、磁粉检测、渗透检测、目视检测、泄漏检测、声发射检测、射线透视检测等。
由于各种 NDT 方法,都各有其适用范围和局限性,因此新的 NDT 方法一直在不断地被开发和应用。
通常,只要符合 NDT 的基本定义,任何一种物理的、化学的或其他可能的技术手段,都可能被开发成一种 NDT 方法。
在我国,无损检测一词最早被称之为探伤或无损探伤,其不同的方法也同样被称之为探伤,如射线探伤、超声波探伤、磁粉探伤、渗透探伤等等。
这一称法或写法广为流传,并一直沿用至今,其使用率并不亚于无损检测一词。
在国外,无损检测一词相对应的英文词,除了该词的前半部分——即 non-destructive 的写法大多相同外,其后半部分的写法就各异了。
如日本习惯写作 inspection,欧洲不少国家过去曾写作 flaw detection、现在则统一使用 testing,美国除了也使用 testing 外,似乎更喜欢写作 examination 和 evaluation。
这些词与前半部分结合后,形成的缩略语则分别是 NDI、NDT 和 NDE,翻译成中文就出现了无损探伤、无损检查(非破坏检查)、无损检验、无损检测、无损评价等不同术语形式和写法。
实际上,这些不同的英文及其相应的中文术语,它们具有的意义相同,都是同义词。
ford 福特 全合成手动变速箱油 msds说明书

SAFETY DATA SHEET1. IdentificationFull Synthetic Manual Transmission FluidProduct identifierOther means of identification175246FIR No.Transmission fluidRecommended useNone known.Recommended restrictionsManufacturer/Importer/Supplier/Distributor informationCompany Name Ford Motor CompanyAddress Attention: MSDS Information, P.O. Box 1899Dearborn, Michigan 48121USATelephone1-800-392-3673SDS Information1-800-448-2063 (USA and Canada)Emergency telephonenumbersPoison Control Center: USA and Canada: 1-800-959-3673INFOTRAC (Transportation): USA and Canada 1-800-535-50532. Hazard(s) identificationNot classified.Physical hazardsNot classified.Health hazardsNot classified.Environmental hazardsNot classified.OSHA defined hazardsLabel elementsNone.Hazard symbolSignal word None.Hazard statement The mixture does not meet the criteria for classification.Precautionary statementPrevention Observe good industrial hygiene practices.Response Wash hands after handling.Storage Store away from incompatible materials.Disposal Dispose of waste and residues in accordance with local authority requirements.Hazard(s) not otherwise classified (HNOC)Direct contact with eyes may cause temporary irritation. Frequent or prolonged contact may defat and dry the skin, leading to discomfort and dermatitis. Inhalation of vapors/fumes generated by heating this product may cause respiratory irritation with throat discomfort, coughing or difficulty breathing.Supplemental information None.3. Composition/information on ingredientsMixturesCAS numberCommon name and synonymsChemical name%68649-42-3 Phosphorodithioic acid,O,O-di-C1-14-alkyl esters, zincsalts2 - 5Specific chemical identity and/or exact percentage (concentration) of composition has been withheld as a trade secret. 4. First-aid measuresMove to fresh air. Call a physician if symptoms develop or persist.InhalationWash off with soap and water. Get medical attention if irritation develops and persists.Skin contact Rinse with water. Get medical attention if irritation develops and persists.Eye contact Rinse mouth. Get medical attention if symptoms occur.IngestionDirect contact with eyes may cause temporary irritation.Most importantsymptoms/effects, acute and delayedTreat symptomatically.Indication of immediatemedical attention and special treatment needed Ensure that medical personnel are aware of the material(s) involved, and take precautions to protect themselves.General information5. Fire-fighting measuresFoam. Powder. Carbon dioxide (CO2).Suitable extinguishing media Do not use water jet as an extinguisher, as this will spread the fire.Unsuitable extinguishing mediaDuring fire, gases hazardous to health may be formed. Upon decomposition, this product emits carbon monoxide, carbon dioxide and/or low molecular weight hydrocarbons.Specific hazards arising from the chemicalSelf-contained breathing apparatus and full protective clothing must be worn in case of fire.Special protective equipment and precautions for firefighters Move containers from fire area if you can do so without risk.Fire fightingequipment/instructions Use standard firefighting procedures and consider the hazards of other involved materials.Specific methods No unusual fire or explosion hazards noted.General fire hazards6. Accidental release measuresAvoid inhalation of vapors or mists. Avoid contact with eyes, skin, and clothing. Keep unnecessary personnel away. For personal protection, see section 8 of the SDS.Personal precautions,protective equipment and emergency procedures The product is immiscible with water and will spread on the water surface.Large Spills: Stop the flow of material, if this is without risk. Dike the spilled material, where this is possible. Absorb in vermiculite, dry sand or earth and place into containers. Following product recovery, flush area with water.Small Spills: Wipe up with absorbent material (e.g. cloth, fleece). Clean surface thoroughly to remove residual contamination.Never return spills to original containers for re-use. For waste disposal, see section 13 of the SDS.Methods and materials for containment and cleaning upAvoid discharge into drains, water courses or onto the ground.Environmental precautions7. Handling and storageAvoid breathing mist or vapor. Avoid contact with eyes, skin, and clothing. Observe good industrial hygiene practices. For personal protection, see section 8 of the SDS.Precautions for safe handling Store in original tightly closed container. Store away from incompatible materials (see Section 10of the SDS).Conditions for safe storage,including any incompatibilities8. Exposure controls/personal protectionOccupational exposure limitsNot established.No biological exposure limits noted for the ingredient(s).Biological limit values Use adequate ventilation to control airborne concentrations below the exposure limits/guidelines. If user operations generate a vapor, dust and/or mist, use process enclosure, appropriate local exhaust ventilation, or other engineering controls to control airborne levels below the recommended exposure limits/guidelines.Appropriate engineering controlsIndividual protection measures, such as personal protective equipmentWear safety glasses with side shields (or goggles).Eye/face protectionSkin protectionSuitable chemical protective gloves should be worn when the potential exists for skin exposure.The choice of an appropriate glove does not only depend on its material but also on other quality features and is different from one producer to the other. Nitrile gloves are recommended.Hand protectionWear appropriate chemical resistant clothing if applicable.OtherIf engineering controls do not maintain airborne concentrations to a level which is adequate to protect worker health, an approved respirator must be worn. Respirator selection, use and maintenance should be in accordance with the requirements of OSHA Respiratory Protection Standard 29 CFR 1910.134 and/or Canadian Standard CSA Z94.4.Respiratory protectionWear appropriate thermal protective clothing, when necessary.Thermal hazards Always observe good personal hygiene measures, such as washing after handling the material and before eating, drinking, and/or smoking. Routinely wash work clothing and protective equipment to remove contaminants.General hygiene considerations9. Physical and chemical propertiesAppearanceLiquid.Physical state Liquid.Form Amber.Color Oily.OdorOdor threshold Not available.pHNot available.Melting point/freezing point Not available.Initial boiling point and boiling range Not available.Flash point 366.8 °F (186.0 °C) Cleveland Closed Cup Evaporation rate Not available.Not applicable.Flammability (solid, gas)Upper/lower flammability or explosive limits Flammability limit - lower(%)Not available.Flammability limit - upper (%)Not available.Explosive limit - lower (%)Not available.Explosive limit - upper (%)Not available.Vapor pressure Not available.Vapor density Not available.Relative density0.872Relative density temperature 59 °F (15 °C)Solubility(ies)Solubility (water)Insoluble Partition coefficient (n-octanol/water)> 3Auto-ignition temperature Not available.Decomposition temperature Not available.Viscosity76 cSt Viscosity temperature 104 °F (40 °C)Other informationDensity0.87 g/cm³ @ 15°C10. Stability and reactivityThe product is stable and non-reactive under normal conditions of use, storage and transport.Reactivity Material is stable under normal conditions.Chemical stabilityNo dangerous reaction known under conditions of normal use.Possibility of hazardous reactionsContact with incompatible materials.Conditions to avoid Strong oxidizing agents.Incompatible materials Upon decomposition, this product emits carbon monoxide, carbon dioxide and/or low molecular weight hydrocarbons.Hazardous decomposition products11. Toxicological informationInformation on likely routes of exposureInhalationInhalation of vapors/fumes generated by heating this product may cause respiratory irritation with throat discomfort, coughing or difficulty breathing. Prolonged inhalation may be harmful.Skin contact Frequent or prolonged contact may defat and dry the skin, leading to discomfort and dermatitis.Eye contact Direct contact with eyes may cause temporary irritation.IngestionIngestion may cause gastrointestinal irritation, nausea, vomiting and diarrhea.Symptoms related to the physical, chemical andtoxicological characteristics Direct contact with eyes may cause temporary irritation.Information on toxicological effectsAcute toxicityNot expected to be hazardous by OSHA criteria.Prolonged skin contact may cause temporary irritation.Skin corrosion/irritation Direct contact with eyes may cause temporary irritation.Serious eye damage/eye irritationRespiratory or skin sensitizationRespiratory sensitizationNot a respiratory sensitizer.This product is not expected to cause skin sensitization.Skin sensitization No data available to indicate product or any components present at greater than 0.1% are mutagenic or genotoxic.Germ cell mutagenicity CarcinogenicityThis product is not considered to be a carcinogen by IARC, ACGIH, NTP, or OSHA. Base oil severely refined: Not carcinogenic in animal studies. Representative material passes IP-346,Modified Ames test, and/or other screening tests.This product is not expected to cause reproductive or developmental effects.Reproductive toxicitySpecific target organ toxicity -single exposureNot classified.Specific target organ toxicity -repeated exposure Not classified.Aspiration hazard Not an aspiration hazard.Chronic effectsProlonged inhalation may be harmful.12. Ecological informationThe product is not classified as environmentally hazardous. However, this does not exclude the possibility that large or frequent spills can have a harmful or damaging effect on the environment.EcotoxicityNo data is available on the degradability of this product. Persistence and degradabilityBioaccumulative potentialPartition coefficient n-octanol / water (log Kow)Full Synthetic Manual Transmission Fluid > 33No data available.Mobility in soil Other adverse effectsNo other adverse environmental effects (e.g. ozone depletion, photochemical ozone creation potential, endocrine disruption, global warming potential) are expected from this component.13. Disposal considerationsCollect and reclaim or dispose in sealed containers at licensed waste disposal site. Don't pollute.Conserve resources. Return used oil to collection centers.Disposal instructions Dispose in accordance with all applicable regulations.Local disposal regulationsThe waste code should be assigned in discussion between the user, the producer and the waste disposal company.Hazardous waste code Dispose of in accordance with local regulations. Empty containers or liners may retain some product residues. This material and its container must be disposed of in a safe manner (see:Disposal instructions).Waste from residues / unused productsSince emptied containers may retain product residue, follow label warnings even after container is emptied. Empty containers should be taken to an approved waste handling site for recycling or disposal.Contaminated packaging14. Transport informationDOTNot regulated as dangerous goods.IATANot regulated as dangerous goods.IMDGNot regulated as dangerous goods.Not established.Transport in bulk according toAnnex II of MARPOL 73/78 and the IBC Code15. Regulatory informationThis product is not known to be a "Hazardous Chemical" as defined by the OSHA Hazard Communication Standard, 29 CFR 1910.1200.US federal regulationsTSCA Section 12(b) Export Notification (40 CFR 707, Subpt. D)Not regulated.CERCLA Hazardous Substance List (40 CFR 302.4)Phosphorodithioic acid, O,O-di-C1-14-alkyl esters, zinc salts (CAS 68649-42-3)Listed.SARA 304 Emergency release notificationNot regulated.Superfund Amendments and Reauthorization Act of 1986 (SARA)Immediate Hazard - No Delayed Hazard - No Fire Hazard - NoPressure Hazard - No Reactivity Hazard - NoHazard categoriesSARA 302 Extremely hazardous substanceNot listed.NoSARA 311/312 Hazardous chemicalSARA 313 (TRI reporting)Chemical name% by wt.CAS number Phosphorodithioic acid, O,O-di-C1-14-alkyl esters, zinc salts5.00000000000068649-42-3Other federal regulationsClean Air Act (CAA) Section 112 Hazardous Air Pollutants (HAPs) ListNot regulated.Clean Air Act (CAA) Section 112(r) Accidental Release Prevention (40 CFR 68.130)Not regulated.Not regulated.Safe Drinking Water Act(SDWA)California Safe Drinking Water and Toxic Enforcement Act of 1986 (Proposition 65): This material is not known to contain any chemicals currently listed as carcinogens or reproductive toxins.US state regulations International InventoriesAll components are listed or are exempt from listing on the Toxic Substances Control Act Inventory.16. Other information, including date of preparation or last revision02-08-2017Issue dateVersion 01Health: 1Flammability: 1Physical hazard: 0HMIS® ratingsHealth: 1Flammability: 1Instability: 0NFPA ratingsThis document was prepared by FCSD-Toxicology, Ford Motor Company, Fairlane Business Park IV, 17225 Federal Drive, Allen Park, MI 48101, USA, based in part on information provided by the manufacturer. The information on this data sheet represents our current data and is accurate to the best of our knowledge as to the proper handling of this product under normal conditions and in accordance with the application specified on the packaging and/or technical guidance literature.Any other use of the product which involves using the product in combination with any other product or any other process is the responsibility of the user. To the extent that there are anydifferences between this product’s Safety Data Sheet (SDS) and the consumer packaged product labels, the SDS should be followed.Preparation Information and DisclaimerXT-M5-QSPart number(s)。
中西医疗差异英文
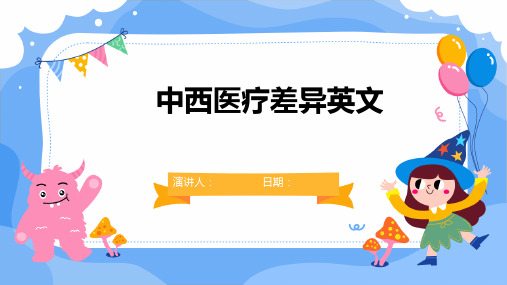
Chinese Medicine
Employees a variety of therapies including global medicine, insurance, mass, dietary therapy, and exercise to restore balance and harmony within the body
02
Fundamental Differences between Eastern and Western
Medicine
Philosophical Basis
Chinese Medicine
Based on the concept of balance and harmony with nature Emphasis on the interconnectivity of bodily functions and the importance of qi (life force)
Western medicine, also known as allopathic medicine or biomedicine, is a system of medical practice that originated in Europe and later spread to other parts of the world
Western Medicine
Relies primary on physical examination, laboratory tests, imaging techniques, and other technical tools for diagnostics Focuses on identifying specific issues or conditions
Artisan Technology Group 产品说明书

PNOZ mc3pConfigurable Control System PNOZmultiContentsContents PageChapter 1Introduction1.1Validity of the documentation1-11.1.1Retaining the documentation1-11.2Overview of documentation1-21.3Definition of symbols1-3Chapter 2Overview2.1Unit structure2-12.1.1Scope of supply2-12.1.2Unit features2-12.2Front view2-2Chapter 3Safety3.1Intended use3-13.1.1System requirements3-13.2Safety regulations3-23.2.1Use of qualified personnel3-23.2.2Warranty and liability3-23.2.3Disposal3-23.2.4For your safety3-3Chapter 4Function description4.1Unit description4-14.1.1Operation4-14.1.2Input and output data4-14-24.1.3Assigning the inputs/outputs in thePNOZmulti Configurator to the EtherCATinputs/outputs4.1.4Block diagram4-2Chapter 5Installation5.1General installation guidelines5-15.1.1Dimensions5-15.2Connecting the base unit and expansion5-2modulesContentsChapter 6Commissioning6.1Wiring6-16.1.1General wiring guidelines6-16.1.2Connecting the supply voltage6-16.1.3PROFIBUS DP interface6-16.2Preparing for operation6-26.2.1Setting the station address6-26-26.2.2Download modified project to the controlsystem PNOZmulti6.2.3Connection example6-3Chapter 7Operation7.1Messages7-17.2Display elements7-27.2.1Display elements for device diagnostics7-2Chapter 8Technical Details8.1Technical Details8-18.2Order reference8-21Introduction1.1Validity of the documentationThis documentation is valid for the product PNOZ mc3p. It is valid untilnew documentation is published.This operating manual explains the function and operation, describesthe installation and provides guidelines on how to connect the product.1.1.1Retaining the documentationThis documentation is intended for instruction and should be retainedfor future reference.1Introduction1.2Overview of documentation1 IntroductionThe introduction is designed to familiarise you with the contents, struc-ture and specific order of this manual.2 OverviewThis chapter provides information on the product's most important fea-tures.3 SafetyThis chapter must be read as it contains important information on in-tended use.4 Function DescriptionThis chapter describes the product's mode of operation.5 InstallationThis chapter explains how to install the product.6 CommissioningThis chapter describes the product's commissioning and wiring.7 OperationThis chapter describes how to operate the product and gives tips in thecase of a fault.8 Technical DetailsThis chapter contains the product's technical details and order refer-ence.1Introduction2Overview2.1Unit structure2.1.1Scope of supply❝Expansion module PNOZ mc3p❝Jumper 774 6392.1.2Unit featuresUsing the product PNOZ mc3p:Expansion module for connection to a base unit from the configurablecontrol system PNOZmultiThe product has the following features:❝Can be configured in the PNOZmulti Configurator❝Connection for PROFIBUS-DP❝Station addresses from 0 ... 99, selected via rotary switch❝Status indicators for communication with PROFIBUS-DP and for er-rors❝24 virtual outputs on the control system PNOZmulti can be defined inthe PNOZmulti Configurator for communication with the fieldbusPROFIBUS DP. The number of inputs and outputs can be extendedto 128. Please note that when the extended inputs and outputs 24 -127 are used they have different properties (see document entitled"Communication Interfaces").❝Max. 1 PNOZ mc3p can be connected to the base unit❝Please refer to the document "PNOZmulti System Expansion" for thePNOZmulti base units that can be connected3.1Intended useThe expansion module PNOZ mc3p is used for communication be-tween the configurable control system PNOZmulti and PROFIBUS-DP.PROFIBUS-DP is designed for fast data exchange at field level. The ex-pansion module PNOZ mc3p is a passive subscriber (Slave) ofPROFIBUS-DP (DPV0). The basic functions of communication withPROFIBUS-DP conform to EN 50170. The central controller (Master)reads input information from the slaves and writes output information tothe slaves as part of each cycle. As well as the cyclical transfer of usabledata, PROFIBUS-DP can also be used for diagnostics and commission-ing functions. Data traffic is monitored on the Master/Slave side.The expansion module may only be connected to a base unit from theconfigurable control system PNOZmulti (please refer to the document"PNOZmulti System Expansion" for details of the base units that can beconnected)The configurable control system PNOZmulti is used for the safety-relat-ed interruption of safety circuits and is designed for use in:❝E-STOP equipment❝Safety circuits in accordance with VDE0113 Part 1 and EN60204-1The expansion module may not be used for safety-related functions.Intended use includes making the electrical installation EMC-compliant.The product is designed for use in an industrial environment. It is notsuitable for use in a domestic environment, as this can lead to interfer-ence.The following is deemed improper use in particular:❝Any component, technical or electrical modification to the product❝Use of the product outside the areas described in this manual❝Use of the product outside the technical details (see chapter entitled“Technical Details”)3.1.1System requirementsPlease refer to the "Product Modifications" document in the "Versionoverview" section for details of which versions of the base unit andPNOZmulti Configurator can be used for this product.3.2.1Use of qualified personnelThe products may only be assembled, installed, programmed, commis-sioned, operated, maintained and decommissioned by competent per-sons.A competent person is someone who, because of their training, experi-ence and current professional activity, has the specialist knowledge re-quired to test, assess and operate the work equipment, devices,systems, plant and machinery in accordance with the general standardsand guidelines for safety technology.It is the company's responsibility only to employ personnel who:❝Are familiar with the basic regulations concerning health and safety /accident prevention❝Have read and understood the safety guidelines given in this descrip-tion❝Have a good knowledge of the generic and specialist standards ap-plicable to the specific application.3.2.2Warranty and liabilityAll claims to warranty and liability will be rendered invalid if:❝The product was used contrary to the purpose for which it is intended❝Damage can be attributed to not having followed the guidelines in themanual❝Operating personnel are not suitably qualified❝Any type of modification has been made (e.g. exchanging compo-nents on the PCB boards, soldering work etc.).3.2.3Disposal❝In safety-related applications, please comply with the mission time t Min the safety-related characteristic data.❝When decommissioning, please comply with local regulations regard-ing the disposal of electronic devices (e.g. Electrical and ElectronicEquipment Act).3.2.4For your safetyThe unit meets all necessary conditions for safe operation. However,you should always ensure that the following safety requirements aremet:❝This operating manual only describes the basic functions of the unit.Information on the advanced functions can be found in the online helpfor the PNOZmulti Configurator and in the PNOZmulti technical cata-logue. Only use these functions after you have read and understoodthe documentation. All necessary documentation can be found on thePNOZmulti Configurator CD.❝Do not open the housing or make any unauthorised modifications.❝Please make sure you shut down the supply voltage when performingmaintenance work (e.g. exchanging contactors).4.1.1OperationThe virtual inputs and outputs that are to be transferred via PROFIBUSare selected and configured in the PNOZmulti Configurator. The baseunit and the expansion module PNOZ mc3p are connected via a jumper.The expansion module PNOZ mc3p is also supplied with voltage via thisjumper.The station address is set via rotary switches. After the supply voltage isswitched on or the PNOZmulti control system is reset, the expansionmodule PNOZ mc3p is configured and started automatically.LEDs indicate the status of the expansion module on PROFIBUS.The configuration is described in detail in the PNOZmulti Configurator'sonline help.4.1.2Input and output dataThe data is structured as follows:❝Input rangeThe inputs are defined in the master and transferred to the PNOZmul-ti. Each input has a number, e.g. input bit 4 of byte 1 has the numberi12.❝Output rangeThe outputs are defined in the PNOZmulti Configurator. Each outputthat is used is given a number there, e.g. o0, o5... The status of out-put o0 is stored in bit 0 of byte 0; the status of output o5 is stored inbit 5 of byte 0 etc.❝Output range only: Byte 3Bits 0 … 4: Status of LEDs on the PNOZmulti–Bit 0: OFAULT–Bit1:IFAULT–Bit 2: FAULT–Bit3:DIAG–Bit4:RUNBit 5: Data is being exchanged.Detailed information on data exchange (tables, segments) is available inthe document "Communication Interfaces" in the section entitled "Field-bus modules".5.2Connecting the base unit and expansion modulesYou can install a maximum of 1 PNOZ mc3p to the left of the base unit.❝Do not connect a terminator to the last expansion module on the left-hand side.❝Install the expansion module in the position in which it is configuredin the PNOZmulti Configurator.7.1MessagesWhen the supply voltage is switched on, the PNOZmulti safety systemcopies the configuration from the chip card.The LEDs "POWER","DIAG", "FAULT", "IFAULT" and "OFAULT" light upon the base unit.The expansion module PNOZ mc3p is configured and started automat-ically. The "ONLINE" and "OFFLINE" LEDs indicate the status of thePNOZ mc3p on PROFIBUS-DP.If the expansion module PNOZ mc3p does not receive a configurationfrom the base unit for a period of 30 s, the expansion modulePNOZ mc3p connects to PROFIBUS-DP and "ONLINE" status is dis-played on PROFIBUS-DP. The error message "External Error" is sent tothe Master.8.1Technical DetailsThe standards current on 2011-09 apply.Technical detailsElectrical dataModule's supply voltage via base unit 5 V DC Voltage tolerance -2 %/+2 %Power consumption 2.5 W Status display LED TimesSupply interruption before de-energisation 20 msFieldbus interface Fieldbus interface PROFIBUS DP Device type Slave Station address 0 - 99dTransmission rate 9.6 kBit/s - 12 MBit/sConnectionFemale 9-pin D-SUB connector Galvanic isolation yesTest voltage500 V ACEnvironmental data Ambient temperature 0 - 60 °C Storage temperature-25 - 70 °CClimatic suitability in accordance with EN 60068-2-30, EN 60068-2-7893 % r. h. at 40 °C Condensation not permitted EMCEN 61131-2Vibration to EN 60068-2-6Frequency10 - 150 Hz Max. acceleration1g Airgap creepage in accordance with EN 61131-2Overvoltage category III Pollution degree2Rated insulation voltage 30 V Shock stress EN 60068-2-2715g 11 msMechanical data Protection typeMounting (e.g. cabinet)IP54Housing IP20Terminals IP20DIN rail Top hat rail 35 x 7.5 EN 50022Recess width 27 mm Housing material Housing PPO UL 94 V0FrontABS UL 94 V0Dimensions Height 94.0 mm Width 22.5 mm Depth 119.0 mm Weight119 g8.2Order referenceOrder referenceProduct type Features Order no. PNOZ mc3p Fieldbus module, PROFIBUS-DP773 732Order reference: Terminator, jumperProduct type Features Order no. PNOZmulti bus terminator Terminator779 110 KOP-XE Jumper774 639...21010-E N -05, 2012-04 P r i n t e d i n G e r m a n y© P i l z G m b H & C o . K G , 2011+49 711 3409-444****************Pilz GmbH & Co. KG Felix-Wankel-Straße 273760 Ostfildern, Germany Telephone: +49 711 3409-0Telefax: +49 711 3409-133E-Mail:***************** Technical supportIn many countries we arerepresented by our subsidiaries and sales partners.Please refer to our homepage for further details or contact our headquarters.d u r a N E T p ®, P i l z ®, P I T ®, P M C p r o te g o ®, P M I ®, P N O Z ®, P r i m o ®, P S E N ®, P S S ®, P V I S ®, S af e t y B U S p ®, S a f e t y E Y E ®, S a f e t y N E T p ®, t h e s p i r i t o f s a f e t y ® a r e r eg i s t e r e d a n d p r o t e c t e d t r a d e m a r k s P i l z G m b H & C o . K G i n s o m e c o u n t r i e s . W e w o u l d p o i n t o u t th a t p r o d u c t f e a t u r e s m a y v a r y f r o m t h e d e t ai l s s t a t e d i n t h i s d o c u m e n t , d e p e n d i n g o n t h e s t a t u s a t t h e t i m e o f p u b l i c a t i o n a n d t h e s c o p e t h e e q u i p m e n t . W e a c c e p t n o r e s p o n s i b i l i t y f o r t h e v a l i d i t y , a c c u r a c y a n d e n t i r e t y o f t h e t e x t a n d g r a p h i c s p r e s e n t e d i n t h i s i n f o r m a t i o n . P l e a s e c o n t a c t o u r T e c h n i c a l S u p p o r t i f y o u h a v e a n y q u e s t i o n s .。
汽车法规--ISO9141-2的国际标准文档4(pdf 58)

SSF 14230Road Vehicles - Diagnostic SystemsKeyword Protocol 2000 - Part 2 - Data Link LayerSwedish Implementation StandardBased on ISO 14230-2 Data Link LayerStatus:Issue 1Date: April 22, 1997This document is based on the InternationalStandard ISO 14230 Keyword Protocol 2000 andhas been further developed to meet Swedishautomotive manufacturer's requirements by theSwedish Vehicle Diagnostics Task Force.It is based on mutual agreement between thefollowing companies:•Saab Automobile AB•SCANIA AB•Volvo Car Corp.•Volvo Bus Corp.•Mecel ABFile: 14230-2s.DOC / Definition by “Samarbetsgruppen för Svensk Fordonsdiagnos” / Author: L. Magnusson Mecel ABDocument updates and issue historyThis document can be revised and appear in several versions. The document will be classified in order to allow identification of updates and versions.A. Document status classificationThe document is assigned the status Outline, Draft or Issue.It will have the Outline status during the initial phase when parts of the document are not yet written.The Draft status is entered when a complete document is ready, which can be submitted for reviews. The draft is not approved. The draft status can appear between issues, and will in that case be indicated together with the new issue number E.g. Draft Issue 2.An Issue is established when the document is reviewed, corrected and approved.B. Version number and history procedureEach issue is given a number and a date. A history record shall be kept over all issues.Document in Outline and Draft status may also have a history record.C. HistoryIssue #Date Comment197 04 22Frst issueTable of Content1. SCOPE (1)2. NORMATIVE REFERENCE (2)3. PHYSICAL TOPOLOGY (3)4. MESSAGE STRUCTURE (4)4.1 Header (4)4.1.1 Format byte (4)4.1.2 Target address byte (5)4.1.2.1 Physical addressing (5)4.1.2.2 Functional addressing (5)4.1.3 Source address byte (5)4.1.4 Length byte (5)4.1.5 Use of header bytes (6)4.2 Data Bytes (6)4.3 Checksum Byte (6)4.4 Timing (7)4.4.1 Timing Exceptions (9)4.4.2 Periodic transmission (9)4.4.3 Server (ECU) Response Data Segmentation (12)4.5 End Of Message (12)5. COMMUNICATION SERVICES (13)5.1 StartCommunication Service (14)5.1.1 Service Definition (14)5.1.1.1 Service Purpose (14)5.1.1.2 Service Table (14)5.1.1.3 Service Procedure (14)5.1.2 Implementation (14)5.1.2.1 Key bytes (15)5.1.2.2 Fast Initialisation (17)5.2 StopCommunication Service (19)5.2.1 Service Definition (19)5.2.1.1 Service Purpose (19)5.2.1.2 Service Table (19)5.2.1.3 Service Procedure (19)5.2.2 Implementation (20)5.3 AccessTimingParameter Service (21)5.3.1 Service Definition (21)5.3.1.1 Service Purpose (21)5.3.1.2 Service Table (21)5.3.1.3 Service Procedure (22)5.3.2 Implementation (23)5.4 SendData Service (25)5.4.1 Service Definition (25)5.4.1.1 Service Purpose (25)5.4.1.2 Service Table (25)5.4.1.3 Service Procedure (25)5.4.2 Implementation (26)6. ERROR HANDLING (27)6.1 Error handling during physical/functional Fast Initialisation (27)6.1.1 Client (tester) Error Handling during physical/functional Fast Initialisation (27)6.1.2 Server (ECU) Error Handling during physical Fast Initialisation (27)6.1.3 Server (ECU) Error Handling during functional Fast Initialisation (28)6.2 Error handling after Initialisation (28)6.2.1 Client (tester) communication Error Handling (28)6.2.2 Server (ECU) communication Error Handling. physical addressing (29)6.2.3 Server (ECU) Error Handling, functional addressing (29)APPENDIX A - ARBITRATION1. DEFINITIONS (1)1.1 Random response time (1)1.2 Start bit detection (1)1.3 Transmission latency (1)1.4 Collision detection (1)2. MAINSTREAM COMMUNICATION (1)APPENDIX B - TIMING DIAGRAMS1. PHYSICAL ADDRESSING (1)1.1 Physical addressing - single positive response message (1)1.2 Physical addressing - more than one positive response message (3)1.3 Physical addressing - periodic transmission (5)2. FUNCTIONAL ADDRESSING (7)2.1 Functional addressing - single positive response message -single server (ECU) addressed (7)2.2 Functional addressing - more than one response message -single server (ECU) addressed (9)2.3 Functional addressing - single positive response message -more than one server (ECU) (11)2.4 Functional addressing - more than one response message -more than one server (ECU) (13)APPENDIX C - MESSAGE FLOW EXAMPLES1. PHYSICAL INITIALISATION - MORE THAN ONE SERVER (ECU) INITIALISED (1)2. PERIODIC TRANSMISSION MODE (4)2.1 Message Flow Example A (4)2.2 Message Flow Example B (5)IntroductionThis document (The Swedish Keyword Protocol 2000 Implementation Standard) is based on the ISO 14230-2 International Standard. Changes are indicated by changing the font from "Arial" to "Times New Roman"!It has been established in order to define common requirements for the implementation of diagnostic services for diagnostic systems.To achieve this, the standard is based on the Open System Interconnection (O:S:I.) Basic Reference Model in accordance with ISO 7498 which structures communication systems into seven layers. When mapped on this model, the services used by a diagnostic tester and an Electronic Control Unit (ECU) are broken into:- Diagnostic services (layer 7)- Communication services (layers 1 to 6)See figure 1 below.1. ScopeThis national Standard specifies common requirements of diagnostic services which allow a tester to control diagnostic functions in an on-vehicle Electronic Control Unit (e.g. electronic fuel injection, automatic gear box, anti-lock braking system,...) connected on a serial data link embedded in a road vehicle.It specifies only layer 2 (data link layer). Included are all definitions which are necessary to implement the services (described in "Keyword Protocol 2000 - Part 3:Implementation) on a serial link (described in "Keyword Protocol 2000 - Part 1: Physical Layer") Also included are some communication services which are needed for communication/session management and a description of error handling.This Standard does not specify the requirements for the implementation of diagnostic services.The physical layer may be used as a multi-user-bus, so a kind of arbitration or bus management is necessary. If arbitration is used it shall comply to the technique described in Attachment A. The car manufacturers are responsible for the correct working of bus management.Communication between ECUs are not part of this document.The vehicle diagnostic architecture of this standard applies to:• a single tester that may be temporarily or permanently connected to the on-vehicle diagnostic data link and• several on-vehicle electronic control units connected directly or indirectlySee figure 2 below.2. Normative ReferenceThe following standards contain provisions which, through reference in this text, constitute provisions of this document. All standards are subject to revision, and parties to agreement based on this document are encouraged to investigate the possibility of applying the most recent editions of the standards listed below. Members of ISO maintain registers of currently valid International Standards.ISO 7498-1:1984Information processing systems - Open systemsinterconnection - Basic reference model.SAE J-1979:Dec,1991E/E Diagnostic Test ModesSAEJ-2178 :June, 1993Class B Data Communication Network MessagesISO 14229:1996Road Vehicles - Diagnostic systems -Diagnostic Services SpecificationSSF 14230-1:1997Road Vehicles - Diagnostic systems - Keyword Protocol 2000 -Issue 2Part 1: Physical LayerSSF 14230-3:1996Road Vehicles - Diagnostic systems - Keyword Protocol 2000 -Draft Part 3: ImplementationISO 14230-4:1996Road Vehicles - Diagnostic systems - Keyword Protocol 2000 -Part 4: Requirements For Emission related Systems3. Physical topologyKeyword Protocol 2000 is a bus concept (s. diagram below). Figure 3 shows the general form of this serial link.Figure 3 - TopologyThe K-Line is used for communication and initialisation. Special cases are node-to-node-connections, that means there is only one ECU on the line, which also can be a bus converter.4. Message structureThis section describes the structure of a message.The message structure consists of three parts:• header• data bytes• checksumHeader Data bytes ChecksumFmt Tgt1 Src1 Len1SId2 . .Data2 . . CSmax . 4 byte max. 255 byte 1 byte1 bytes are optional, depending on format byte2 Service Identification, part of data bytesHeader and Checksum byte are described in this document. The area of data bytes always begins with a Service Identification. Use of the data bytes for communication services is described in this document. Use of the data bytes for diagnostic services is described in "Keyword Protocol 2000 - Part 3: Implementation".4.1 HeaderThe header consists of 3 or 4 bytes. A format byte includes information about the form of the message. A separate length byte allows message lengths up to 255 bytes.4.1.1 Format byteThe format byte contains 6 bit length information and 2 bit address mode information. The tester is informed about use of header bytes by the key bytes (s.5.1.2.1).msb lsbA1A0L5L4L3L2L1L0• A1,A0: Define the form of the header which will be used by the message:A1A0Mode Mnemonic HeaderMode210Header with address information, physical target address HM2 311Header with address information, functional target address HM3HM0 and HM1 are not defined in this document.HM3 (functional target address) shall only be used in request messages see §5.1.2.2.2• L5..L0: Define the length of the data field of a message, i.e. from the beginning of the data field (Service Identification byte included) to Checksum byte (not included). A message length of 1 to 63 bytes is possible. If L0 to L5 = 0 then the additional length byte is included.In the Swedish Implementation Standard L0 to L5 shall always be set to 0 (except in theStartCommunicationRequest message, see §5.1.2.2).This is the target address for the message. It may be a physical or a functional address. For emission related (CARB) messages this byte is defined in ISO 14230 KWP 2000 Part 4: Requirements For Emission related Systems.4.1.2.1 Physical addressingPhysical addressing (HM2) can be used in both request and response messages. The target address of a physically addressed request shall be interpreted as a physical server (ECU) address, the source address is the physical address of the client (tester).In the response message the target and source addresses are also physical addresses (HM2). Physical addresses shall be according to SAE J2178-Part 1, or as specified by the vehicle manufacturer.4.1.2.2 Functional addressingFunctional addressing (HM3) can only be used in request messages. The target address of a functionally addressed request shall be interpreted as a functional (group) address, the source address is the physical address of the client (tester).In the response messages the target and source addresses are physical addresses, i.e. response messages are always physically addressed (HM2).Functional addressing requires that the servers (ECUs) must support arbitration (see appendix A).4.1.3 Source address byteThis is the address of the transmitting device. It must be a physical address (also in the case where the target address is a functional address). There are the same possibilities for the values as described for physical target address bytes. Addresses for testers are listed in SAE J2178 Part 1, but the ECU must accept all tester addresses.4.1.4 Length byteThis byte is provided if the length in the header byte (L0 to L5) is set to 0. It allows the user to transmit messages with data fields longer then 63 bytes. With shorter messages it may be omitted. This byte defines the length of the data field of a message, i.e. from the beginning of the data field (Service Identification byte included) to Checksum byte (not included). A data length of 1 to 255 bytes is possible. The longest message consists of a maximum of 260 byte (255 data bytes + 4 bytes header + Checksum). For messages with data fields of less than 64 bytes there are two possibilities: Length may be included in the format byte or in the additional length byte. An ECU may support both possibilities, the tester is informed about this capability through the keybytes ( see section 5.1.2.1).Length Length provided inFmt byte Length byte< 64XX00 0000present< 64XXLL LLLL not present≥ 64XX00 0000presentXX: 2 bit address mode information (see §4.1.1)LL LLLL: 6 bit length informationIn the Swedish Implementation Standard the Length byte shall always be provided (L0 to L5 = 0) (except in the StartCommunicationRequest message, see §5.1.2.2).With the above definitions there are two different forms of message. These are shown diagramatically below.LengthFmt Tgt Src SId Data CSChecksumHeader with address information, no additional length byteLengthFmt Tgt Src Len SId Data CSChecksumHeader with address information, with additional length byteFmt Format byteTgt Target addressSrc Source addressLen additional length byteSId Service Identification byteData depending on serviceCS Checksum byte4.2 Data BytesThe data field may contain up to 255 bytes of information. The first byte of the data field is the Service Identification Byte. It may be followed by parameters and data depending on the selected service. These bytes are defined in "Keyword Protocol 2000 - Part 3: -Implementation" (for diagnostic services) and in section 5 of this document (for communication services).4.3 Checksum ByteThe Checksum byte (CS) inserted at the end of the message block is defined as the simple 8-bit sum series of all bytes in the message, excluding the Checksum.If the message is<1> <2> <3> ... <N> , <CS>where <i> (1 ≤ i ≤ N) is the numeric value of the i th byte of the message, then:<CS> = <CS>Nwhere <CS>i (i = 2 to N) is defined as<CS>i = { <CS> i-1 + <i> } Modulo 256 and <CS>1 = <1>Additional security may be included in the data field as defined by the manufacturer.4.4 TimingDuring normal operation the following timing parameters are relevant:Value DescriptionP1Inter byte time in ECU response.P2Time between end of tester request and start of ECU response, or time between end of ECU response and start of next ECU response.The next ECU response may be from the same ECU or it may be from another ECUin case of functional addressing.P3Time between end of ECU response and start of new tester request, or time between end of tester request and start of new tester request if ECU fails torespond.P3 shall be measured from the last byte in the latest response message from anyECU responding.P4Inter byte time in tester request.There are two sets of default timing parameters, normal and extended. Only normal timing parameters are supported by this document (Swedish Implementation Standard).Table 1a shows the timing parameters which are used as default (all values in ms).Table 1a - Normal Timing Parameter Set, default valuesTiming min. values max. valuesParameter default defaultP1020P2 P2*2525505000P3555000P4520Note: The timing parameter P2* becomes active if the server (ECU) responds with Negative response and the response code $78 "reqCorrectlyRcvd-RspPending", see §4.4.1.The values of the timing parameters may be changed with the communication service "AccessTimingParameters" (see §5.3).Table 1b shows the resolution and the possible limits within which the timing parameters can be changed with AccessTimingParameters (ATP).Table 1b -Normal Timing Parameter Set, lower and upper limitsAll values in msTiming Min. values Max. valuesParameter Lower limit Resolution 1Upper limit Resolution 1P10---20---P200.589600 ; ∞see Table 1cP300.563500∞250 see note 2P400.520---1) Min./Max. value calculation method [ms] = ATP parameter value * Resolution2) ATP parameter value = $FF => Max. value = ∞Table 1c - P2max Timing Parameter calculationTiming Parameter Hex valueof ATPparamete rResolutionin [ms]valuein [ms]Maximum value calculation methodin [ms]P2max01 to F02525 to 6000(hex value) - (Resolution) F1F2F3F4F5F6 F7 F8 F9 FA FB FC FD FE see maximumvaluecalculationmethod640012800192002560032000384004480051200576006400070400768008320089600(low nibble of hex value) - 256 - 25Example of $FA:($0A - $0100) - 25 = 64000FF---∞= ∞The P2max timing parameter calculation uses 25 [ms] resolution in the range of $01 to $F0.Beginning with $F1 a different calculation method shall be used by the server and the client in order to reach P2max timing values greater than 6000 [ms].Calculation Formula for P2max values > $F0Calculation_Of_P2max [ms] = (low nibble of ATP parameter P2max) * 256 * 25Note:The P2max timing parameter value shall always be a single byte value in the AccessTimingParameter service. The timing modifications shall be activated by implementation of the AccessTimingParameter service.Users must take care for limits listed above and the following restrictions:P3min > P2max(to avoid collisions in case of func. addressing or data segm.)P3min > P4min(to guarantee that the ECU can receive the first byte)Pimin < Pimax for i=1,...,4When the tester and listening ECUs detect the end of a message by time-out, the following restrictions are also valid:P2min > P4maxP2min > P1maxIt is in the system designers responsibility to ensure proper communication in the case of changing the timing parameters from the default values.He also has to make sure that the chosen communication parameters are possible for all ECUs which participate in the session.The possible values depend on the capabilities of the ECU. In some cases the ECU possibly needs to leave its normal operation mode for switching over to a session with different communication parameters.For complete timing diagrams see appendix B.4.4.1 Timing ExceptionsThe extended P2 timing window is a possibility for (a) server(s) to extend the time to respond on a request message. A timing exception is only allowed with the use of one or multiple negative response message(s) with response code $78 (requestCorrectlyReceived-ResponsePending) by the server(s). This response code shall only be used by a server in case it cannot send a positive or negative response message based on the client's request message within the active P2 timing window.After the transmission of the first negative response message, with response code $78, from the server (ECU) the timing parameter P2* becomes active, instead of the original timing parameter P2, in both the server and the client.The timing parameter P2* shall be generated as described in the following formula: P2*min = P2minP2*max = P3maxThe server(s) shall send multiple negative response messages with the negative response code $78 if required.As soon as the server has completed the task (routine) initiated by the request message it shall send either a positive or negative response message (with a response code other than $78) based on the last request message received. When the client has received the response message, which has been preceded by the negative response message(s) with response code $78, the timing parameter P2 becomes active again in both the server and the client. The client shall not repeat the request message after the reception of a negative response message with response code $78.4.4.2Periodic transmissionThe Keyword Protocol 2000 Periodic Transmission Mode shall be enabled by starting a diagnostic session with the startDiagnosticSession service and the diagnosticMode (DCM_) parameter set to $82 for PeriodicTransmission.PeriodicTransmission shall be supported in connection with physical addressing, normal and modified timing. The description below explains in steps how the PeriodicTransmission mode shall be activated, handled and de-activated.Step #1:To enable the PeriodicTransmission mode in the client (tester) and the server (ECU) the client (tester) shall transmit a startDiagnosticSession request message containing thediagnosticMode parameter for the PeriodicTransmission. After the reception of the firstpositive response message from the server (ECU) the PeriodicTransmission mode isenabled and periodic transmission mode communication structure and timing becomesactive. From now on, the server (ECU) shall periodically transmit the last responsemessage with current (updated, if available) data content, until the client (tester) sends arequest message within the timing window P3*. The timing parameters can be changedwithin the possible limits of the periodic transmission timing parameter set (see Table1d) with the communication service AccessTimingParameters.Step #2:After reception of any request message within the timing window P3*, the server (ECU) shall periodically transmit the corresponding response message which can be either apositive or a negative response message.Step #3:After reception of a stopDiagnosticSession or stopCommunication request message within the timing window P3*, the server (ECU) shall transmit the correspondingpositive response message only once.After reception of a stopDiagnosticSession or stopComunication positive responsemessage the periodicTransmissionMode is disabled and the default diagnostic sessionwith the default timing values, defined by the key bytes becomes active.After reception of a stopDiagnosticSession or stopComunication negative responsemessage the periodicTransmissionMode shall continue. In such case the server (ECU)shall transmit negative response messages unless the client (tester) sends a new requestmessage within the timing window P3*.During the standardDiagnosticModeWithPeriodicTransmission the following rules have to be considered:1.The client (tester) has to ignore the original timing window P3 and shall generate a new timingparameter for the jump-in timing window, which is called from now on P3*.The timing parameter P3* shall be generated as described in the following formula:P3*max = P2min - 2 msP3*min = P3minNote: The original P3max timing parameter is only used for time out detection during negative response message handling with the response code $78 "reqCorrectlyRcvd-RspPending".2.The timing window P3*, which starts at P3*min and ends at P3*max, shall be at least 5ms. It isimportant for the client (tester) to guarantee a minimum size of the jump-in window for the start of a request message.3.The timing window P3* starts and ends before the timing window P2 starts.4.P1max shall not exceed P2min. This is required in order to support resynchronisation betweenthe server (ECU) and client (tester) to meet the error handling requirements.5.Default and optimised timing parameter valuesThe timing table below specifies the timing parameter values with the diagnostic mode standardDiagnosticModeWithPeriodicTransmission.Table 1d -Timing parameter - periodic transmission.All values in msTiming minimum values maximum valuesParameter lower limit default resolution 1default upper limit resolution 1 P100---20200.5P27250.55089600; ∞see Table 1cP2* 37250.5500063500∞250 see note 2P3050.5500063500∞250 see note 2P3* 4050.523125.50.5P4050.520200.51) Min./Max. value calculation method [ms] = ATP parameter value * Resolution2) ATP parameter value = $FF => Max. value = ∞3) The timing parameter P2* becomes active if the server (ECU) responds with Negative response and the response code $78 "reqCorrectlyRcvd-RspPending", see §4.4.14) The timing parameter P3* can be changed, indirectly, by changing the timing parameters P2 and P3 with the service “AccessTimingParameters”.6.When implementing the standardDiagnosticModeWithPeriodicTransmission the followinglimits and restrictions must be considered as listed below:•Pimin < Pimax for i=1, ,4•P1max < P2min•P3min ≤ P2min - 10msIt is the system designers responsibility to ensure proper communication in the case of changing the timing parameters from their default values.It is also the system designers responsibility to ensure proper communication when periodic transmission is used in combination with multiple diagnose, see §5.1.2.2.For complete timing diagrams and message flow examples see appendix B and C.4.4.3Server (ECU) Response Data SegmentationServer (ECU) Response Data Segmentation is used if a client (tester) has sent a request message which causes the server (ECU) to split the response message content (data bytes) into several data segments. The data segments shall be transmitted consecutively in repeated response messages. Each message shall be transmitted within the timing window P2. The data field of each response message shall consist of the Service ID and the corresponding data segment (see figure 5).Data segmentation shall be detected by the client (tester) by comparing source addresses and Service IDs which must be identical for all response messages during segmentation.Server (ECU) response data segmentation shall only be used when the data length exceeds the maximum length that the server (ECU) can transmit in a single message. Data segmentation shall not be supported in periodic transmission mode.This procedure shall also be used to meet the requirements of ISO 14230-4 Keyword Protocol 2000 - Part 4: Requirements For Emission Related Systems.If data segmentation is used the following restriction shall apply:P3min > P2max4.5End Of MessageThe end of a received message shall be detected as:Number of bytes received equals message length (as defined in the format byte or length byte) orTime-out of inter byte time in the received message (P1max exceeded in ECU transmission, P4max exceeded in tester transmission)whichever occurs first.5. Communication servicesSome services are necessary to establish and maintain communication. They are not diagnostic services because they do not appear on the application layer. They are described in the formal way and with the conventions defined in ISO/WD 14229, i.e. a definition of the service purpose, a service table and a verbal description of the service procedure. A description of implementation on the physical layer of Keyword Protocol 2000 is added.The StartCommunication Service and the AccessTimingParameters Service are used for starting a diagnostic communication. In order to perform any diagnostic service, communication must be initialised and the communication parameters need to be appropriate to the desired diagnostic mode. A chart describing this is shown in figure 6.Figure 6 - Use of communication services。
斑马技术公司DS8108数字扫描仪产品参考指南说明书
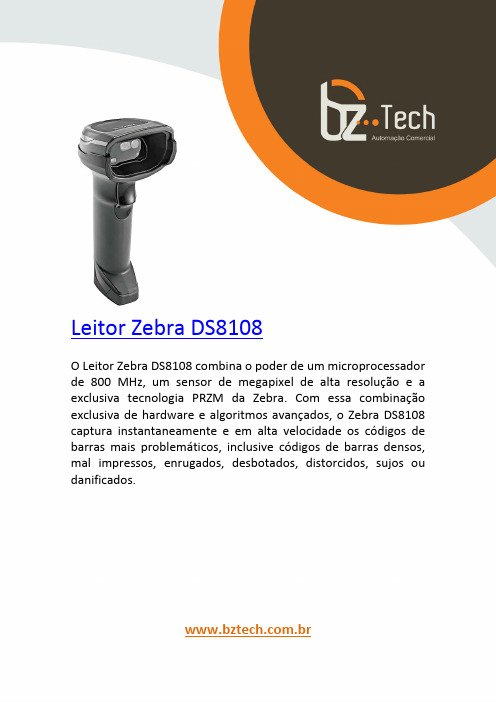
对医学伦理的看法和建议英语作文300词

医学伦理:挑战与建议In the realm of healthcare, ethics plays a pivotal role, guiding practitioners in their decisions and actions. As medicine advances, so do the ethical challenges it faces.In this essay, I delve into the complexities of medical ethics, offering insights and recommendations foraddressing these challenges.Firstly, the principle of non-maleficence, or doing no harm, is fundamental to medical ethics. However, with the advent of innovative technologies like genetic editing and advanced diagnostics, the definition of harm has expanded. For instance, the ethical implications of altering aperson's genetic code to prevent future diseases are profound and far-reaching. It raises questions about the limits of medical intervention and the potential misuse of technology.Secondly, the principle of beneficence, or doing good,is equally important. Medical professionals have a duty to promote the well-being of their patients. However, this can be complicated by resource allocation issues, especially in settings where healthcare resources are limited. Forinstance, in times of pandemics or disasters, decisions about who receives care and who does not can be fraught with ethical dilemmas.To address these challenges, I propose several recommendations. Firstly, continuous education and training for medical professionals on ethical principles and their application in real-world scenarios is crucial. This will help practitioners make informed decisions in complex ethical situations.Secondly, the involvement of patients and theirfamilies in ethical decision-making is essential. Patients have a right to understand the ethical implications oftheir treatment options and make informed choices. Medical professionals should strive to communicate clearly and comprehensively, respecting the autonomy of their patients. Lastly, the development of ethical frameworks and guidelines specific to emerging technologies and practices is necessary. These frameworks should address the unique ethical challenges posed by these technologies and provide practitioners with clear direction on how to proceed.In conclusion, medical ethics is a dynamic and evolving field, requiring continuous attention and reflection. By prioritizing education, patient autonomy, and the development of ethical frameworks, we can hope to address the challenges of medical ethics and ensure that healthcare remains a force for good in society.**医学伦理:挑战与建议**在医疗保健领域,伦理道德发挥着至关重要的作用,它引导着从业者做出决策和采取行动。
ENCOUNTERTRUE-TIMEATPG

Encounter True-Time ATPGPart of the Encounter Test family, Encounter True-Time ATPG offers robust automated test patterngeneration (ATPG) engines, proven to generate the highest quality tests for all standard design-for-test (DFT) methods, styles, and flows. It supports not only industry-standard stuck-at and transition fault models, but also raises the bar on fault detection by providing defect-based, user-definable modeling capability with its patented pattern fault technology.Pattern fault technology is what enables the Encounter “gate-exhaustive” coverage(GEC) methodology, proven to be two-to-four times more efficient at detecting gate intrinsic faults than any other static methodologies available on the market (e.g. SSF, N-Detect).For delay test, True-Time ATPGincludes a dynamic timing engine and uses either circuit timing information or constraints to automaticallygenerate transition-based fault tests and faster-than-at-speed tests for identifying very deep sub-micron design-process feature defects (e.g. certain small delay defects).Figure 1: Encounter True-Time ATPG provides a timing-based ATPG engine driven by SDF or SDC informationOn-product clock generation (OPCG) produces and applies patterns to effectively capture this class of faults while minimizing false failures. Use of SDF or SDC information ensures the creation of a highly accurate timing-based pattern set.True-Time ATPG optimizes test coverage through a combination of topological random resistant fault analysis (RRFA) and deterministic fault analysis (DFA)with automated test point insertion—far superior to traditional test coverage algorithms. RRFA is used for early optimi-zation of test coverage, pattern density, and runtime performance. DFA is applied downstream for more detailed circuit-level fault analysis when the highest quality goals must be met.To reduce scan test time while maintaining the highest test coverage, True-Time technology provides intelligent ATPG with on-chip compression (XOR- or MISR-based). It is also power-aware and uses patented technologies to significantly reduce and manage power consumption during manufacturing test.True-Time ATPG also offers a customizable environment to suityour project development needs.The GUI provides highly interactive capabilities for coverage analysis and debug; it includes a powerful sequence analyzer that boosts productivity. Encounter True-Time ATPG is available in two offerings: Basic and Advanced.Benefits• Ensures high quality of shipped silicon with production-proven 2-4x reduction in test escapes• Provides superior partial scan coverage with proprietary pattern fault modeling and sequential ATPG algorithms• Optimizes test coverage with RRFA and DFA test point insertion methodology • Boosts productivity by integrating with Encounter RTL Compiler• Delivers superior runtime throughput with high-performance model build and fault simulation engines as well as distributed ATPG • Lowers cost of test with patterncompaction and compressiontechniques that maintain fullscan coverage• Balances tester costs with diagnosticsmethodologies by offering flexiblecompression architectures with fullX masking capabilities (includingOPMISR+ and XOR-based solutions)• Supports low pin-count testingvia JTAG control of MBIST andhigh-compression ratio technology• Supports reduced pin-count testing forI/O test• Interfaces with Encounter Power Systemfor accurate power calculation andpattern IR drop analysis• Reduces circuit and switching activityduring manufacturing test to managepower consumption• Reduces false failures due tovoltage drop• Provides a GUI with powerfulinteractive analysis capabilitiesincluding a schematic viewer andsequence analyzerEncounter TestPart of the Encounter digital design andimplementation platform, the EncounterTest product family delivers an advancedsilicon verification and yield learningsystem. Encounter Test comprises threeproduct technologies:• Encounter DFT Architect: ensuresease of use, productivity, and predict-ability in generating ATPG-readynetlists containing DFT structures, fromthe most basic to the most complex;available as an add-on option toEncounter RTL Compiler• Encounter True-Time ATPG: ensuresthe fewest test escapes and the highestquality shipped silicon at the lowestdevelopment and production costs• Encounter Diagnostics: delivers themost accurate volume and precisiondiagnostics capabilities to accelerateyield ramp and optimize device andfault modelingEncounter Test also offers a flexible APIusing the PERL language to retrieve designdata from its pervasive database. Thisunique capability allows you to customizeSoC Test Infrastructure• Maximize productivity• Maximize predictabilityTest Pattern Generation• Maximize product quality• Minimize test costsDiagnostic• Maximize yeld and ramp• Maximize silicon bring-upEncounter DFT Architect• Full-chip test infrastructure• Scan compression(XOR and MISR), BIST,IEEE1500, 1149.1/6• ATPG-aware insertionverification• Power-aware DFT and ATPGEncounter True-Time ATPG• Stuck-at, at-speed, andfaster-than-at-speed testing• Design timing drivestest timing• High-quality ATPGEncounter Diagnostics• Volume mode finds criticalyield limiters• Precision mode locatesroot cause• Unsurpassed silicon bring-upprecisionSiliconFigure 2: Encounter Test offers a complete RTL-to-silicon verification flow and methodologies that enable the highest quality IC devices at the lowest costreporting, trace connections in the design, and obtain information that might be helpful for debugging design issues or diagnostics.FeaturesTrue-Time ATPG BasicTrue-Time ATPG Basic contains thestuck-at ATPG engine, which supports:• High correlation test coverage, easeof use, and productivity through integration with the Encounter RTL Compiler synthesis environment• Full scan, partial scan, and sequential ATPG for edge-triggered andLSSD designs• Stuck-at, IDDQ, and I/O parametric fault models• Core-based testing, test data migration, and test reuse• Special support for custom designs such as data pipelines, scan control pipelines, and safe-scan• Test pattern volume optimization using RRFA-based test point insertion• Test coverage optimization usingDFA-based test point insertion• Pre-defined (default) and user-defined defect-based fault modeling andgate-exhaustive coverage based on pattern fault technology• Powerful GUI with interactive analysis capabilitiesPattern fault capability enables defect-based testing with a patented technology for accurately modeling the behavior of nanometer defects, such as bridges and opens for ATPG and diagnostics, and for specifying the complete test of a circuit. The ATPG engine, in turn, uses this definition wherever the circuit is instan-tiated within a design. By default, pattern faults are used to increase coverage of XOR, LATCH, FLOP, TSD, and MUX primi-tives. They can also be used to model unique library cells and transition and delay-type defects.True-Time ATPG AdvancedTrue-Time ATPG Advanced offers thesame capabilities as the Basic configu-ration, plus delay test ATPG functionality.It uses post-layout timing data from theSDF file to calculate the path delay of allpaths in the design, including distributiontrees of test clocks and controls. Usingthis information, you can decide on thebest cycle time(s) to test for in a givenclock domain.True-Time ATPG Advanced is capableof generating tests at multiple testfrequencies to detect potential early yieldfailures and certain small delay defects.You can specify your own cycle time orlet True-Time ATPG calculate one basedon path lengths. It avoids generating testsalong paths that exceed tester cycle timeand/or mask transitions along paths thatexceed tester cycle time. True-Time ATPGgenerates small delay defect patternsbased on longest path analysis to ensurepattern efficiency.A unique feature of the Advancedoffering is its ability to generate faster-than-at-speed tests to detect small delaydefects that would otherwise fail duringsystem test or result in early field failures.True-Time ATPG Advanced also usestester-specific constraint informationduring test pattern generation. Thecombination of actual post-layout timingand tester constraint information withTrue-Time ATPG Advanced algorithmsensures that the test patterns will work“first pass” on the tester.The test coverage optimizationmethodology is expanded beyond RRFAand DFA-based test point insertion(TPI) technology. The combinationof both topological and circuit-levelfault analysis with automated TPIprovides the most advanced capabilityfor ensuring the highest possible testcoverage while controlling the numberof inserted test points. DFA-based TPIBridge TestingFigure 3: Pattern faults model any type ofbridge behavior; net pair lists automaticallycreate bridging fault models; ATPG anddiagnostics use the models to detect andisolate bridgesFigure 4: Power-aware ATPG for scan and capture modes prevents voltage-drop–induced failures in test modeCadence is transforming the global electronics industry through a vision called EDA360.With an application-driven approach to design, our software, hardware, IP, and services helpcustomers realize silicon, SoCs, and complete systems efficiently and profitably. © 2012 Cadence Design Systems, Inc. All rights reserved. Cadence, the Cadence logo, Conformal, Encounter, and VoltageStorm are registered trademarks of Cadence Design Systems, Inc. All other s are properties of their respective holders.has links to Encounter Conformal ® Equivalence Checker to ensure the most efficient, logically equivalent netlist modifications with maximum controllability and observability.The ATPG engine works with multiple compression architectures to generate tests that cut costs by reducing scan test time and data volume. Actual compression ratios are driven by the compression architecture as well asdesign characteristics (e.g. available pins, block-level structures). Users can achieve compression ratios exceeding 100x.Flexible compression options allow you to select a multiple input signature register (MISR) architecture with the highest compression ratio, or an exclusive-or (XOR)–based architecture that enables a highly efficientcombinational compression ratio and a one-pass diagnostics methodology. Both architectures support a broadcast type or XOR-based decompressor.On-product MISR plus (OPMISR+) uses a MISR-based output compression, which eliminates the need to check the response at each cycle. XOR-based compression uses an XOR-tree–based output compression to enable a one-pass flow through diagnostics.Additionally, intelligent ATPG algorithms minimize full-scan correlation issues and reduce power consumption, deliv-ering demonstrated results of >99.5 stuck-at test coverage with >100x test time reduction. Optional X-state masking capability is available on a per-chain/ per-cycle basis. Masking is usuallyrequired when using delay test because delay ATPG may generate unknown states in the circuit.Using the Common Power Format (CPF), True-Time ATPG Advanced automatically generates test modes to enable individual power domains to be tested independently or in small groups. This, along with automaticrecognition and testing of power-specific structures (level shifters, isolation logic, state retention registers) ensures the highest quality for low-power devices.Power-aware ATPG uses industry-leading techniques to manage and significantly reduce power consumption due to scan and capture cycles during manufacturing test. The benefit is reduced risk of false failures due to voltage drop and fewer reliability issues due to excessive power consumption. True-Time ATPG Advanced uses algorithms that limit switching during scan testing to further reduce power consumption.Encounter Test offers a flexible API using the PERL language to retrievedesign data from its pervasive database. This unique capability allows users to customize reporting, trace connections in the design, and obtain information that might be helpful for debugging design issues or diagnostics.Platforms• Sun Solaris (64-bit)• HP-UX (64-bit)• Linux (32-bit, 64-bit)• IBM AIX (64-bit)Cadence Services and Support• Cadence application engineers can answer your technical questions by telephone, email, or Internet—they can also provide technical assistance and custom training • Cadence certified instructors teach more than 70 courses and bring their real-world experience into the classroom • More than 25 Internet Learning Series (iLS) online courses allow you the flexibility of training at your own computer via the Internet • Cadence Online Support gives you24x7 online access to a knowledgebase of the latest solutions, technicaldocumentation, software downloads, and more。
- 1、下载文档前请自行甄别文档内容的完整性,平台不提供额外的编辑、内容补充、找答案等附加服务。
- 2、"仅部分预览"的文档,不可在线预览部分如存在完整性等问题,可反馈申请退款(可完整预览的文档不适用该条件!)。
- 3、如文档侵犯您的权益,请联系客服反馈,我们会尽快为您处理(人工客服工作时间:9:00-18:30)。
• Diagnostics of key processes relevant for the effects of the different modes of transportations:
– stratosphere-troposphere exchange of O3 and NOx – boundary layer venting – convective transport of pollutants emitted at the surface
Fundamental evaluation ofrison with observations: • Comparison of observed and modelled tropospheric
ozone and CO (O3 at various altitudes, surface O3, CO) • Time series • Model biases • Correlations • Skill scores
Biogenic NO, isoprene, and monoterpene emissions soon available by MPI for chemistry
Lightning NOx: 5 Tg (N)/yr
Transport emissions: from Activity 1 if available (report by Peter) otherwise road traffic (Volker), air traffic (AERO2K or DLR1992), shipping emissions (via UiO, Endresen)
2019 quasi-monthly means (dates where ozonesonde data available only)
Brunner et al. (2019)
Testing the skill of the models: Taylor diagrams
• correlation coefficient, • pattern root-mean square (RMS) error, • ratio of modelled/observed standard
Definition and diagnostics for the model-observations comparison
Christina Schnadt Poberaj
Evaluation of multi-model performance (WP 3.1.1)
• Definition of model simulations: simulations of selected years, comparison of model results
Model-model intercomparisons: • Intercomparisons between models: zonal means and
horizontal distributions of relevant species (O3, CO, CH4, NO2, (NOx), CH2O, HNO3, OH, SO2, H2SO4)
Evaluation of multi-model performance
• Definition of model simulations: simulations of selected years, comparison of model results
with observations in the ETHmeg database
Identify model biases: Scatterplots O3, NOx, CO, …
Model biases at individual ozonesonde stations or airports (MOZAIC airport profiles)
TM4, RETRO project
Boundary conditions for 2019 runs:
Model will be run in the same set-up as in the current impact study (WP3.1.2)
Anthropogenic emissions year 2000: EDGAR 3.2 Fast Track 2000 - GHGs CO2, CH4, N2O, and F-gases (HFCs, PFCs, and SF6) - air pollutants CO, NMVOC, NOx, SO2 Large-scale biomass burning: annual burned area estimates for 2019-2000 average, or actual 2000 area, or EDGAR 3.2 emission factors, or factors compiled by Andreae and Merlet (2019)
Model evaluation of RETRO 2019 test simulations using ozonesonde station data (left) and CMDL stations data for surface ozone and CO (right)
Brunner et al. (2019)
Model evaluation: year 2019 Campaign data to be used: SPURT, UTOPOHIAN_Act, MOZAIC, CONTRACE, VINTERSOL, INTEX, SCIAMACHY NO2 columns
Evaluation of multi-model performance