机械毕业设计英文外文翻译460数字控制 (2)
机械类毕业设计外文翻译
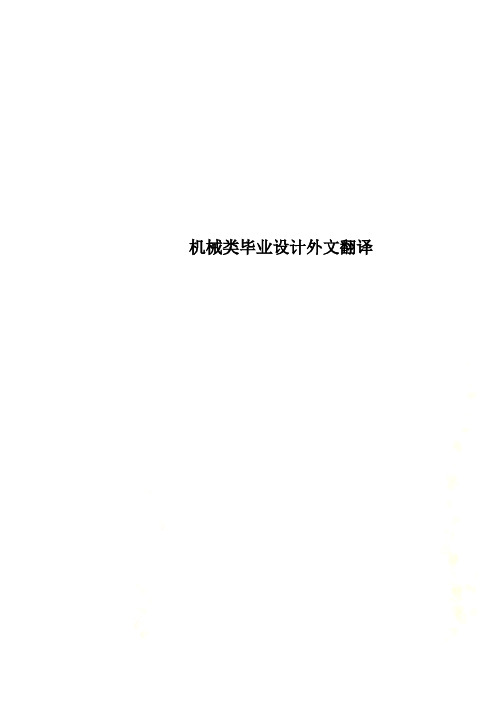
机械类毕业设计外文翻译外文原文Options for micro-holemakingAs in the macroscale-machining world, holemaking is one of the most— if not the most—frequently performed operations for micromachining. Many options exist for how those holes are created. Each has its advantages and limitations, depending on the required hole diameter and depth, workpiece material and equipment requirements. This article covers holemaking with through-coolant drills and those without coolant holes, plunge milling, microdrilling using sinker EDMs and laser drilling.Helpful HolesGetting coolant to the drill tip while the tool is cutting helps reduce the amount of heat at the tool/workpiece interface and evacuate chips regardless of hole diameter. But through-coolant capability is especially helpful when deep-hole microdrilling because the tools are delicate and prone to failure when experiencing recutting of chips, chip packing and too much exposure to carbide’s worst enemy—heat.When applying flood coolant, the drill itself blocks access to the cutting action. “Somewhere about 3 to 5 diam eters deep, the coolant has trouble getting down to the tip,” said Jeff Davis, vice president of engineering for Harvey Tool Co., Rowley, Mass. “It becomes wise to use a coolant-fed drill at that point.”In addition, flood coolant can cause more harm than good when microholemaking. “The pressure from the flood coolant can sometimes snap fragile drills as they enter the part,” Davis said.The toolmaker offers a line of through-coolant drills with diameters from 0.039" to 0.125" that are able to produce holes up to 12 diameters deep, as well as microdrills without coolant holes from 0.002" to 0.020".Having through-coolant capacity isn’t enough, though. Coolant needs to flow at a rate that enables it to clear the chips out of the hole. Davis recommends, at a minimum, 600 to 800 psi of coolant pressure. “It works much better if you have higher pressure than that,” he added.To prevent those tiny coolant holes from becoming clogged with debris, Davis also recommends a 5μm or finer coolant filter.Another recommendation is to machine a pilot, or guide, hole to prevent the tool from wandering on top of the workpiece and aid in producing a straight hole. When applying a pilot drill, it’s important to select one with an included angle on its point that’s equal t o or larger than the included angle on the through-coolant drill that follows.The pilot drill’s diameter should also be slightly larger. For example, if the pilot drill has a 120° included angle and a smaller diameter than a through-coolant drill with a 140°included angle, “then you’re catching the coolant-fed drill’s corners and knocking those corners off,” Davis said, which damages the drill.Although not mandatory, pecking is a good practice when microdrilling deep holes. Davis suggests a pecking cycle that is 30 to 50 percent of the diameter per peck depth, depending on the workpiece material. This clears the chips, preventing them from packing in the flute valleys.Lubricious ChillTo further aid chip evacuation, Davis recommends applying an oil-based metalworking fluid instead of a waterbased coolant because oil provides greater lubricity. But if a shop prefers using coolant, the fluid should include EP (extreme pressure) additives to increase lubricity and minimize foaming. “If you’ve got a lot of foam,” Davis noted, “the chips aren’t being pulled out the way they are supposed to be.”He added that another way to enhance a tool’s slipperiness while extending its life is with a coating, such as titanium aluminum nitride. TiAlN has a high hardness and is an effective coating for reducing heat’s impact when drilling difficult-to-machine materials, like stainless steel.David Burton, general manager of Performance Micro Tool, Janesville, Wis., disagrees with the idea of coating microtools on the smaller end of the spectrum. “Coatings on tools below 0.020" typically have a negative effect on every machining aspect, from the quality of the initial cut to tool life,” he said. That’s because coatings are not thin enough and negatively alter the rake and relief angles when applied to tiny tools.However, work continues on the development of thinner coatings, and Burton indicated that Performance Micro Tool, which produces microendmills and microrouters and resells microdrills, is working on a project with others to create a submicron-thickness coating. “We’re probably 6 months to 1 year from testing it in the market,” Burton said.The microdrills Performance offers are basically circuit-board drills, which are also effective for cutting metal. All the tools are without through-coolant capability. “I had a customer drill a 0.004"-dia. hole in stainless steel, and he was amazed he could do it with a circuit-board drill,” Burton noted, adding that pecking and running at a high spindle speed increase the d rill’s effectiveness.The requirements for how fast microtools should rotate depend on the type of CNCmachines a shop uses and the tool diameter, with higher speeds needed as the diameter decreases. (Note: The equation for cutting speed is sfm = tool diameter × 0.26 × spindle speed.)Although relatively low, 5,000 rpm has been used successfully by Burton’s customers. “We recommend that our customers find the highest rpm at the lowest possible vibration—the sweet spot,” he said.In addition to minimizing vibration, a constant and adequate chip load is required to penetrate the workpiece while exerting low cutting forces and to allow the rake to remove the appropriate amount of material. If the drill takes too light of a chip load, the rake face wears quickly, becoming negative, and tool life suffers. This approach is often tempting when drilling with delicate tools.“If the customer decides he wants to baby the tool, he takes a lighter chip load,” Burton said, “and, typically, the cutting edge wears much quicker and creates a radius where the land of that radius is wider than the chip being cut. He ends up using it as a grinding tool, trying to bump material away.” For tools larger than 0.001", Burton considers a chip load under 0.0001" to be “babying.” If the drill doesn’t snap, premature wear can result in abysmal tool life.Too much runout can also be destructive, but how much is debatable. Burton pointed out that Performance purposely designed a machine to have 0.0003" TIR to conduct in-house, worst-case milling scenarios, adding that the company is still able to mill a 0.004"-wide slot “day in and day out.”He added: “You would think with 0.0003" runout and a chip load a third that, say, 0.0001" to 0.00015", the tool would break immediately because one flute would be taking the entire load and then the back end of the flute would be rubbing.When drilling, he indicated that up to 0.0003" TIR should be acceptable because once the drill is inside the hole, the cutting edges on the end of the drill continue cutting while the noncutting lands on the OD guide the tool in the same direction. Minimizing run out becomes more critical as the depth-to-diameter ratio increases. This is because the flutes are not able to absorb as much deflection as they become more engaged in the workpiece. Ultimately, too much runout causes the tool shank to orbit around the tool’s center while the tool tip is held steady, creating a stress point where the tool will eventually break.Taking a PlungeAlthough standard micro drills aren’t generally available below 0.002", microendmills that can be used to “plunge” a hole are. “When people want to drillsmaller than that, they use our endmills and are pretty successful,” Burton said. However, the holes can’t be very deep because the tools don’t have long aspect, or depth-to-diameter, ratios. Therefore, a 0.001"-dia. endmill might be able to only make a hole up to 0.020" deep whereas a drill of the same size can go deeper because it’s designed to place the load on its tip when drilling. This transfers the pressure into the shank, which absorbs it.Performance offers endmills as small as 5 microns (0.0002") but isn’t keen on increasing that line’s sales. “When people try to buy them, I very seriously try to talk them out of it bec ause we don’t like making them,” Burton said. Part of the problem with tools that small is the carbide grains not only need to be submicron in size but the size also needs to be consistent, in part because such a tool is comprised of fewer grains. “The 5-m icron endmill probably has 10 grains holding the core together,” Burton noted.He added that he has seen carbide powder containing 0.2-micron grains, which is about half the size of what’s commercially available, but it also contained grains measuring 0.5 and 0.6 microns. “It just doesn’t help to have small grains if they’re not uniform.”MicrovaporizationElectrical discharge machining using a sinker EDM is another micro-holemaking option. Unlike , which create small holes for threading wire through the workpiece when wire EDMing, EDMs for producing microholes are considerably more sophisticated, accurate and, of course, expensive.For producing deep microholes, a tube is applied as the electrode. For EDMing smaller but shallower holes, a solid electrode wire, or rod, is needed. “We try to use tubes as much as possible,” said Jeff Kiszonas, EDM product manager for Makino Inc., Auburn Hills, Mich. “But at some point, nobody can make a tube below a certain diameter.” He added that some suppliers offer tubes down to 0.003" in diameter for making holes as small as 0.0038". The tube’s flushing hole enables creating a hole with a high depth-to-diameter ratio and helps to evacuate debris from the bottom of the hole during machining.One such sinker EDM for produc ing holes as small as 0.00044" (11μm) is Makino’s Edge2 sinker EDM with fine-hole option. In Japan, the machine tool builder recently produced eight such holes in 2 minutes and 40 seconds through 0.0010"-thick tungsten carbide at the hole locations. The electrode was a silver-tungsten rod 0.00020" smaller than the hole being produced, to account for spark activity in the gap.When producing holes of that size, the rod, while rotating, is dressed with acharged EDM wire. The fine-hole option includes a W-axis attachment, which holds a die that guides the electrode, as well as a middle guide that prevents the electrode from bending or wobbling as it spins. With the option, the machine is appropriate for drilling hole diameters less than 0.005".Another sinker EDM for micro-holemaking is the Mitsubishi VA10 with afine-hole jig attachment to chuck and guide the fine wire applied to erode the material. “It’s a standard EDM, but with that attachment fixed to the machine, we can do microhole drilling,” said Dennis Powderly, sinker EDM product manager for MC Machinery Systems Inc., Wood Dale, Ill. He added that the EDM is also able to create holes down to 0.0004" using a wire that rotates at up to 2,000 rpm.Turn to TungstenEDMing is typically a slow process, and that holds true when it is used for microdrilling. “It’s very slow, and the finer the details, the slower it is,” said , president and owner of Optimation Inc. The Midvale, Utah, company builds Profile 24 Piezo EDMs for micromachining and also performs microEDMing on a contract-machining basis.Optimation produces tungsten electrodes using a reverse-polarity process and machines and ring-laps them to as small as 10μm in diameter with 0.000020" roundness. Applying a 10μm-dia. electrode produces a hole about 10.5μm to 11μm in diameter, and blind-holes are possible with the company’s EDM. The workpiece thickness for the smallest holes is up to 0.002", and the thickness can be up to 0.04" for 50μm holes.After working with lasers and then with a former EDM builder to find a better way to produce precise microholes, Jorgensen decided the best approach was DIY. “We literally started with a clean sheet of paper and did all the electronics, all the software and the whole machine from scratch,” he said. Including the software, the machine costs in the neighborhood of $180,000 to $200,000.Much of the company’s contract work, which is provided at a shop rate of $100 per hour, involves microEDMing exotic metals, such as gold and platinum for X-ray apertures, stainless steel for optical applications and tantalum and tungsten for the electron-beam industry. Jorgensen said the process is also appropriate for EDMing partially electrically conductive materials, such as PCD.“The customer normally doesn’t care too much about the cost,” he said. “We’ve done parts where there’s $20,000 [in time and material] involved, and you can put the whole job underneath a fingernail. We do everything under a microscope.”Light CuttingBesides carbide and tungsten, light is an a ppropriate “tool material” formicro-holemaking. Although most laser drilling is performed in the infrared spectrum, the SuperPulse technology from The Ex One Co., Irwin, Pa., uses a green laser beam, said Randy Gilmore, the company’s director of laser tec hnologies. Unlike the femtosecond variety, Super- Pulse is a nanosecond laser, and its green light operates at the 532-nanometer wavelength. The technology provides laser pulses of 4 to 5 nanoseconds in duration, and those pulses are sent in pairs with a delay of 50 to 100 nanoseconds between individual pulses. The benefits of this approach are twofold. “It greatly enhances material removal compared to other nanosecond lasers,” Gilmore said, “and greatly reduces the amount of thermal damage done to the workpiece material” because of the pulses’ short duration.The minimum diameter produced with the SuperPulse laser is 45 microns, but one of the most common applications is for producing 90μm to 110μm holes in diesel injector nozzles made of 1mm-thick H series steel. Gilmore noted that those holes will need to be in the 50μm to 70μm range as emission standards tighten because smaller holes in injector nozzles atomize diesel fuel better for more efficient burning.In addition, the technology can produce negatively tapered holes, with a smaller entrance than exit diameter, to promote better fuel flow.Another common application is drilling holes in aircraft turbine blades for cooling. Although the turbine material might only be 1.5mm to 2mm thick, Gilmore explained that the holes are drilled at a 25° entry angle so the air, as it comes out of the holes, hugs the airfoil surface and drags the heat away. That means the hole traverses up to 5mm of material. “Temperature is everything in a turbine” he said, “because in an aircraft engine, the hotter you can run the turbine, the better the fuel economy and the more thrust you get.”To further enhance the technology’s competitiveness, Ex One developed apatent-pending material that is injected into a hollow-body component to block the laser beam and prevent back-wall strikes after it creates the needed hole. After laser machining, the end user removes the material without leaving remnants.“One of the bugaboos in getting lasers accepted in the diesel injector community is that light has a nasty habit of continuing to travel until it meets another object,” Gilmore said. “In a diesel injector nozzle, that damages the interior surface of the opposite wall.”Although the $650,000 to $800,000 price for a Super- Pulse laser is higher than a micro-holemaking EDM, Gilmore noted that laser drilling doesn’t require electrodes. “A laser system is using light to make holes,” he said, “so it doesn’t have a consumable.”Depending on the application, mechanical drilling and plunge milling, EDMing and laser machining all have their place in the expanding micromachining universe. “People want more packed into smaller spaces,” said Makino’s Kiszonas.中文翻译微孔的加工方法正如宏观加工一样,在微观加工中孔的加工也许也是最常用的加工之一。
机械专业毕业设计外文翻译1

本科毕业设计(本科毕业论文)外文文献及译文文献、资料题目:High-rise Tower Crane designed文献、资料来源:期刊(著作、网络等)文献、资料发表(出版)日期:2000.3.25院(部):机电工程学院专业:机电工程及自动化High-rise Tower Crane designed under Turbulent Winds At present, construction of tower cranes is an important transport operations lifting equipment, tower crane accident the people's livelihood, major hazards, and is currently a large number of tower crane drivers although there are job permits, due to the lack of means to monitor and review the actual work of a serious violation . Strengthen the inspection and assessment is very important. Tower crane tipping the cause of the accident can be divided into two aspects: on the one hand, as a result of the management of tower cranes in place, illegal operation, illegal overloading inclined cable-stayed suspended widespread phenomenon; Second, because of the tower crane safety can not be found in time For example,Took place in the tower crane foundation tilt, micro-cracks appear critical weld, bolts loosening the case of failure to make timely inspection, maintenance, resulting in the continued use of tower cranes in the process of further deterioration of the potential defect, eventually leading to the tower crane tipping. The current limit of tower crane and the black box and can not be found to connect slewing tower and high-strength bolts loosening tightened after the phenomenon is not timely, not tower verticality of the axis line of the lateral-line real-time measurement, do not have to fight the anti-rotation vehicles, lifting bodies plummeted Meng Fang, hook hoists inclined cable is a timely reminder and record of the function, the wind can not be contained in the state of suspended operation to prevent tipping on the necessary tips on site there is a general phenomenon of the overloaded overturning of the whole security risks can not be accurately given a reminder and so on, all of which the lease on the tower crane, use, management problems,Through the use of tower crane anti-tipping monitor to be resolved. Tower crane anti-tipping Monitor is a new high-tech security monitoring equipment, and its principle for the use of machine vision technology and image processing technology to achieve the measurement of the tilt tower, tower crane on the work of state or non-working state of a variety of reasons angle of the tower caused by the critical state to achieve the alarm, prompt drivers to stop illegal operation, a computer chip at the same time on the work of the state of tower crane be recorded. Tower crane at least 1 day overload condition occurs, a maximum number of days to reach 23 overloading, the driver to operate the process of playing the anti-car, stop hanging urgency, such as cable-stayed suspended oblique phenomenon often, after verification and education, to avoid the possible occurrence of fatal accidents. Wind conditions in the anti-tipping is particularly important, tower cranes sometimes connected with the pin hole and pin do not meet design requirements, to connect high-strength bolts are not loose in time after the tightening of the phenomenon, through timely maintenance in time after the tightening of the phenomenon, through timely maintenance and remedial measures to ensure that the safe and reliable construction progress. Reduced lateral line tower vertical axis measuring the number of degrees,Observation tower angle driver to go to work and organize the data once a month to ensure that the lateral body axis vertical line to meet the requirements, do not have to every time and professionals must be completed by Theodolite tower vertical axismeasuring the lateral line, simplified the management link. Data logging function to ensure that responsibility for the accident that the scientific nature to improve the management of data records for the tower crane tower crane life prediction and diagnosis of steel structures intact state data provides a basis for scientific management and proactive prevention of possible accidents, the most important thing is, if the joint use of the black box can be easily and realistically meet the current provisions of the country's related industries. Tower crane safety management at the scene of great importance occurred in the construction process should be to repair damaged steel, usually have to do a good job in the steel tower crane maintenance work and found that damage to steel structures, we must rule out potential causes of accidents, to ensure safety in production carried out smoothly. Tower crane in the building construction has become essential to the construction of mechanical equipment, tower crane at the construction site in the management of safety in production is extremely important. A long time, people in the maintenance of tower crane, only to drive attention to the conservation and electrical equipment at the expense of inspection and repair of steel structures, to bring all kinds of construction accidents.Conclusion: The tower crane anti-tipping trial monitor to eliminate potential causes of accidents to provide accurate and timely information, the tower crane to ensure the smooth development of the leasing business, the decision is correct, and should further strengthen and standardize the use of the environment (including new staff training and development of data processing system, etc.).The first construction cranes were probably invented by the Ancient Greeks and were powered by men or beasts of burden, such as donkeys. These cranes were used for the construction of tall buildings. Larger cranes were later developed, employing the use of human treadwheels, permitting the lifting of heavier weights. In the High Middle Ages, harbour cranes were introduced to load and unload ships and assist with their construction – some were built into stone towers for extra strength and stability. The earliest cranes were constructed from wood, but cast iron and steel took over with the coming of the Industrial Revolution.For many centuries, power was supplied by the physical exertion of men or animals, although hoists in watermills and windmills could be driven by the harnessed natural power. The first 'mechanical' power was provided by steam engines, the earliest steam crane being introduced in the 18th or 19th century, with many remaining in use well into the late 20th century. Modern cranes usually use internal combustion engines or electric motors and hydraulic systems to provide a much greater lifting capability than was previously possible, although manual cranes are still utilised where the provision of power would be uneconomic.Cranes exist in an enormous variety of forms – each tailored to a specific use. Sizes range from the smallest jib cranes, used inside workshops, to the tallest tower cranes,used for constructing high buildings, and the largest floating cranes, used to build oil rigs and salvage sunken ships.This article also covers lifting machines that do not strictly fit the above definition of a crane, but are generally known as cranes, such as stacker cranes and loader cranes.The crane for lifting heavy loads was invented by the Ancient Greeks in the late 6th century BC. The archaeological record shows that no later than c.515 BC distinctive cuttings for both lifting tongs and lewis irons begin to appear on stone blocks of Greek temples. Since these holes point at the use of a lifting device, and since they are to be found either above the center of gravity of the block, or in pairs equidistant from a point over the center of gravity, they are regarded by archaeologists as the positive evidence required for the existence of the crane.The introduction of the winch and pulley hoist soon lead to a widespread replacement of ramps as the main means of vertical motion. For the next two hundred years, Greek building sites witnessed a sharp drop in the weights handled, as the new lifting technique made the use of several smaller stones more practical than of fewer larger ones. In contrast to the archaic period with its tendency to ever-increasing block sizes, Greek temples of the classical age like the Parthenon invariably featured stone blocks weighing less than 15-20 tons. Also, the practice of erecting large monolithic columns was practically abandoned in favour of using several column drums.Although the exact circumstances of the shift from the ramp to the crane technology remain unclear, it has been argued that the volatile social and political conditions of Greece were more suitable to the employment of small, professional construction teams than of large bodies of unskilled labour, making the crane more preferable to the Greek polis than the more labour-intensive ramp which had been the norm in the autocratic societies of Egypt or Assyria.The first unequivocal literary evidence for the existence of the compound pulley system appears in the Mechanical Problems (Mech. 18, 853a32-853b13) attributed to Aristotle (384-322 BC), but perhaps composed at a slightly later date. Around the same time, block sizes at Greek temples began to match their archaic predecessors again, indicating that the more sophisticated compound pulley must have found its way to Greek construction sites by then.During the High Middle Ages, the treadwheel crane was reintroduced on a large scale after the technology had fallen into disuse in western Europe with the demise of the Western Roman Empire. The earliest reference to a treadwheel (magna rota) reappears in archival literature in France about 1225, followed by an illuminated depiction in a manuscript of probably also French origin dating to 1240. In navigation, the earliest uses of harbor cranes are documented for Utrecht in 1244, Antwerp in 1263, Brugge in 1288 and Hamburg in 1291, while in England the treadwheel is not recorded before 1331.Generally, vertical transport could be done more safely and inexpensively by cranes than by customary methods. Typical areas of application were harbors, mines, and, in particular, building sites where the treadwheel crane played a pivotal role in the construction of the lofty Gothic cathedrals. Nevertheless, both archival and pictorial sources of the time suggest that newly introduced machines like treadwheels or wheelbarrows did not completely replace more labor-intensive methods like ladders, hods and handbarrows. Rather, old and new machinery continued to coexist on medieval construction sites and harbors.Apart from treadwheels, medieval depictions also show cranes to be powered manually by windlasses with radiating spokes, cranks and by the 15th century also by windlasses shaped like a ship's wheel. To smooth out irregularities of impulse and get over 'dead-spots' in the lifting process flywheels are known to be in use as early as 1123.The exact process by which the treadwheel crane was reintroduced is not recorded, although its return to construction sites has undoubtedly to be viewed in close connection with the simultaneous rise of Gothic architecture. The reappearance of the treadwheel crane may have resulted from a technological development of the windlass from which the treadwheel structurally and mechanically evolved. Alternatively, the medieval treadwheel may represent a deliberate reinvention of its Roman counterpart drawn from Vitruvius' De architectura which was available in many monastic libraries. Its reintroduction may have been inspired, as well, by the observation of the labor-saving qualities of the waterwheel with which early treadwheels shared many structural similarities.In contrast to modern cranes, medieval cranes and hoists - much like their counterparts in Greece and Rome - were primarily capable of a vertical lift, and not used to move loads for a considerable distance horizontally as well. Accordingly, lifting work was organized at the workplace in a different way than today. In building construction, for example, it is assumed that the crane lifted the stone blocks either from the bottom directly into place, or from a place opposite the centre of the wall from where it could deliver the blocks for two teams working at each end of the wall. Additionally, the crane master who usually gave orders at the treadwheel workers from outside the crane was able to manipulate the movement laterally by a small rope attached to the load. Slewing cranes which allowed a rotation of the load and were thus particularly suited for dockside work appeared as early as 1340. While ashlar blocks were directly lifted by sling, lewis or devil's clamp (German Teufelskralle), other objects were placed before in containers like pallets, baskets, wooden boxes or barrels.It is noteworthy that medieval cranes rarely featured ratchets or brakes to forestall the load from running backward.[25] This curious absence is explained by the high friction force exercised by medieval treadwheels which normally prevented the wheel from accelerating beyond control.目前,塔式起重机是建筑工程进行起重运输作业的重要设备,塔机事故关系国计民生、危害重大,而目前众多的塔机司机虽然有上岗证,由于缺少监督和复核手段,实际工作中违规严重。
机械毕业设计中英翻译

英语原文:CAD/CAM is the technical expression, indicates the computer-aided design and the computer aided manufacturing.This is one item in the design and the production, carries out certain function technology about the use computer data.This technology is completing the design and the production direction to the place develops.In these two traditions was considered is in the production process out of the ordinary, independent function.In brief, CAD/CAM will be able to provide the technology base for the future complete computer production.Looked from the computer science angle that, the design and the manufacture process is one has, processing, the exchange and the management process about the product information.The people use the computer to take the main technical method, from forms in one's mind to the product to put in the market in the entire process information to carry on the analysis and processing, produces and utilizes each kind of numerical information and the graph information, carries on the product the design and the manufacture.The CAD/CAM technology is not the traditional design, the manufacture flow method simple reflection, also is not limits in the partial use computer takes the tool in the individual step or the link, but is unifies the computer science and the project domain specialized technology as well as human's wisdom and the experience take the modern scientific method as the instruction, in the design, in the manufacture entire process each completely manager, as far as possible use computer system completes the work which these duplication high, the labor big, the computation complex as well as depends on purely artificially completes with difficulty, but assists must replaces the engineers and technicians to complete the entire process, obtains the desired effec The CAD/CAM system as well as plans the hardware, the software for supports the environment, (subsystem) realizes through each function module to the product description, the computation, the analysis, optimized, the cartography, the technological process design, the simulation as well as the NC processing.But the generalized CAD/CAM integrative system also should include aspects and so on production plan, management, quality control.Since 1946 first electronic accounting machine has been born in US, people on unceasing computer technology Introduces the machine design? Manufacture domain.As early as in the 50's, for the first time develops successfully the numerical control engine bed, may realize through the different numerical control procedure to the different components processing Afterwards, Massachusetts Institute of Technology's servo laboratory succeeds with the computer manufacture numerical control paper tape, has realized the NC programming automation.In this foundation, the people proposed the following tentative plan: The APT software is feeds the path method realization computer assistance programming through the description, that, can not describe feeds the path, but is direct description components itself? From this has had the CAD initial concept.The entire 50's, the electronic accounting machine also is in the electron tube time, uses the machine language programming, the computer mainly uses in thescience computation, also only has the output function for it disposition graph equipment.CADCAM system basic compositionCAD/CAM system hardware dispositionCAD/CAM system software compositionCAD/CAM system software dispositionComputer aided manufacturing (CAM) may define for uses the computer system to design, to manage and controls a productive plan the movement, through direct or indirect planned production resources computer contact surface.If defines states, the computer aided manufacturing application has 2 big aspects:1) computer supervisory control.This is the direct application, the computer with the production process connection, uses in supervising directly and the control production process2) produces the support application.This is the indirect application, middle the productive plan, the computer uses in supporting the production operation, but is not the computer and the production process links directly.Charting productive forces increaseThe CAD/CAM system may undertake the one whole set new charting theory to be able to strengthen the productivity.Again completes next step, keeps firmly in mind the entire design to be possible to store up the system.When the planner receives one with has saved the blueprint specification similar work piece, he only must recollect, and adjusts it the work storage place, revises in the original blueprint not to conform to a new work piece request part, productivity enhances.The original work piece efficiency enhances, but this can enhance the next step working efficiency.This is a complete at times renewal database support, can facilitate the user to use Improve mapping analysisThe charting analysis is another important work, it can by certain synthesize the CAD/CAM system automatic operation.This in pipeline design, in particular an important application.The pipeline design paper very is usually complex moreover must conform to the precise industry specification.The other giftedCAD/CAM also can affect a company in other aspects the project system.It can enhance the entire physical process the efficiency, the permission present project plan and the report procedure appraisal.CAD/CAM can improve improves the quality of the product the guarantee technology.It can automatic accurate and the integrity document material, the maintenance partial data accurate and bill of materials accurate.DeficiencyCAD/CAM insufficient spot not that obvious, but they can destroy even the most perfect design, the biggest shortcoming is only can directly skips from the manual charting and the recordpreservation to CAD/CAM, the elephant installs a set of jet engine in the populace automobile.The automobile possibly can run quick somewhat, but if the foundation enhancement has not coordinated the heavy pressure, the entire automobile can disperse the frame.CAD/CAM applicationSKETCHPAD, the CAD/CAM technology has passed through very long chi.It is already applied in the middle of each widespread industry.It uses in each aspect, controls from the airplane to the weapon research, manufactures from the map to the movement medical service, from circuit analysis to building steel analysis.CAD/CAM is being applied in each kind of charting and the production, installs the schematic diagram from the movie to the large-scale long-distance monitoring direct set battleship, its application to is developing variously.Now CAD/CAM market.Now in the market has four kind of different CAD/CAM sellers.First is some subordinate companies sells comes from a big enterprise part or the branch CAD/CAM technology.The IBM CAD/CAM branch is an example.If belongs to Mc-Donnell-Douglas McAuto; Belongs to General Electric Lalma, with belongs to Schlumberger Applican, if the multi-large number CAD/CAM subordinate company the main corporation has the massive service intercourse, not only sale supervisory system moreover when one's position is lowly one's words carry no weight service office.When they control the massive accounts also with provides the service, these companies on in optimum condition, because they may extract the massive profits.But they must undertake the complex administrative chain of command, this obstructs in them makes the fast response to the market tendency, or their itself studies and outside the development department, the merge improves on again their new production line the new technical developmentCAD/CAM technology and the product development road of futureAfter many year promotions, the CAD technology already widely applied in professions and so on machinery, electron, astronautics, chemical industry, building.Played using the CAD technology enhanced the enterprise the rated capacity, the optimization design proposal, reduces technical personnel's labor intensity, reduction design cycle, beefed-up design roles and so on standardization.In recent years, our country CAD technology development and the application have obtained the considerable development, besides has carried on sinicizing and the re-development to many overseas softwares, but also was born many had the independent copyright CAD system, If high Chinese CAD, opens item CAD and so on, because these software price is cheap, conforms to our country national condition and the standard, therefore has received widespread welcome, has won the more and more big market share. But, our country CAD/CAM software no matter is from the product development level from the commercialization, the marketability degree all has not the small disparity with the developed country.Because the overseas CAD/CAM software appears early, the development and the application time is also long,therefore they develop quite maturely, now basically already has seized the international market.These overseas software company uses its technical and the fund superiority, starts vigorously to our country market march At present, the overseas some outstanding softwares, like UG, SolidWorks, Pro/Engineer, CATIA and so on, already have seized part of domestic markets.Therefore, our country CAD/CAM software prospect is unoptimistic.But, we also should see clearly own superiority, for instance understood our country market, provides the technical support to be convenient, price small advantage and so on.Not only under these premises, we importantly with the trend of the times, the track international newest tendency, observe each international standard, in international domestic forms the oneself unique superiority, must base the home, the union national condition, face the domestic economic development need,develops has oneself characteristic, conforms to CAD/CAM software which the Chinese is familiar with.。
(完整版)机械毕业设计外文翻译7243268

Introduciton of MachiningHave a shape as a processing method, all machining process for the production of the most commonly used and most important method. Machining process is a process generated shape, in this process, Drivers device on the workpiece material to be in the form of chip removal. Although in some occasions, the workpiece under no circumstances, the use of mobile equipment to the processing, However, the majority of the machining is not only supporting the workpiece also supporting tools and equipment to complete.Machining know the process . For casting, forging and machining pressure, every production of a specific shape of the workpiece, even a spare parts, almost the shape of the structure, to a large extent, depend on effective in the form of raw materials. In general, through the use of expensive equipment and without special processing conditions, can be almost any type of raw materials, mechanical processing to convert the raw materials processed into the arbitrary shape of the structure, as long as the external dimensions large enough, it is possible. Because of a production of spare parts, even when the parts and structure of the production batch sizes are suitable for the original casting, Forging or pressure processing to produce, but usually prefer machining.Strict precision and good surface finish, Machining the second purpose is the establishment of the and surface finish possible on the basis of. Many parts, if any other means of production belonging to the large-scale production, Well Machining is a low-tolerance and can meet the requirements of small batch production. Besides, many parts on the production and processing of coarse process to improve its generalshape of the surface. It is only necessary precision and choose only the surface machining. For instance, thread, in addition to mechanical processing, almost no other processing method for processing. Another example is the blacksmith pieces keyhole processing, as well as training to be conducted immediately after the mechanical completion of the processing.Primary Cutting ParametersCutting the work piece and tool based on the basic relationship between the following four elements to fully describe : the tool geometry, cutting speed, feed rate, depth and penetration of a cutting tool.Cutting Tools must be of a suitable material to manufacture, it must be strong, tough, order to effectively processing, and cutting speed must adapt to the level of specific parts -- with knives. Generally, the more the work piece or tool for reciprocating movement and feed rate on each trip through the measurement of inches. Generally, in other conditions, feed rate and cutting speed is inversely proportional to。
机械工程毕业设计外文翻译

毕业设计论文外文资料原文及译文学院:机电工程学院专业:机械设计制造及其自动化班级:学号:姓名:Mechanical engineering1.The porfile of mechanical engineeringEngingeering is a branch of mechanical engineerig,it studies mechanical and power generation especially power and movement.2.The history of mechanical engineering18th century later periods,the steam engine invention has provided a main power fountainhead for the industrial revolution,enormously impelled each kind of mechznical biting.Thus,an important branch of a new Engineering – separated from the civil engineering tools and machines on the branch-developed together with Birmingham and the establishment of the Associantion of Mechanical Engineers in 1847 had been officially recognized.The mechanical engineering already mainly used in by trial and error method mechanic application technological development into professional engineer the scientific method of which in the research,the design and the realm of production used .From the most broad perspective,the demend continuously to enhance the efficiencey of mechanical engineers improve the quality ofwork,and asked him to accept the history of the high degree of education and training.Machine operation to stress not only economic but also infrastructure costs to an absolute minimun.3.The field of mechanical engineeringThe commodity machinery development in the develop country,in the high level material life very great degree is decided each kind of which can realize in the mechanical engineering.Mechanical engineers unceasingly will invent the machine next life to produce the commodity,unceasingly will develop the accuracy and the complexity more and more high machine tools produces the machine.The main clues of the mechanical development is:In order to enhance the excellent in quality and reasonable in price produce to increase the precision as well as to reduce the production cost.This three requirements promoted the complex control system development.The most successful machine manufacture is its machine and the control system close fusion,whether such control system is essentially mechanical or electronic.The modernized car engin production transmission line(conveyer belt)is a series of complex productions craft mechanizationvery good example.The people are in the process of development in order to enable further automation of the production machinery ,the use of a computer to store and handle large volumes of data,the data is a multifunctional machine tools necessary for the production of spare parts.One of the objectives is to fully automated production workshop,three rotation,but only one officer per day to operate.The development of production for mechanical machinery must have adequate power supply.Steam engine first provided the heat to generate power using practical methods in the old human,wind and hydropower,an increase of engin .New mechanical engineering industry is one of the challenges faced by the initial increase thermal effciency and power,which is as big steam turbine and the development of joint steam boilers basically achieved.20th century,turbine generators to provide impetus has been sustained and rapid growth,while thermal efficiency is steady growth,and large power plants per kW capital consumption is also declining.Finally,mechanical engineers have nuclear energy.This requires the application of nuclear energy particularly high reliability and security,which requires solving many new rge power plants and the nuclear power plant control systems have become highly complex electroonics,fluid,electricity,water and mechanical parts networks All in all areas related to the mechanical engineers.Small internal combustion engine,both to the type (petrol and diesel machines)or rotary-type(gas turbines and Mong Kerr machine),as well as their broad application in the field of transport should also due to mechanical enginerrs.Throughout the transport,both in the air and space,or in the terrestrial and marine,mechanial engineers created a variety of equipment and power devices to their increasing cooperation with electrical engineers,especially in the development of appropration control systems.Mechanical engineers in the development of military weapons technology and civil war ,needs a similar,though its purpose is to enhance rather than destroy their productivity.However.War needs a lot of resources to make the area of techonlogy,many have a far-reaching development in peacetime efficiency.Jet aircraft and nuclear reactors are well known examples.The Biological engineering,mechanical engineering biotechnology is a relatively new and different areas,it provides for the replacement of the machine or increase thebody functions as well as for medical equipment.Artficial limbs have been developed and have such a strong movement and touch response function of the human body.In the development of artificial organ transplant is rapid,complex cardiac machines and similar equipment to enable increasingly complex surgery,and injuries and ill patients life functions can be sustained.Some enviromental control mechanical engineers through the initial efforts to drainage or irrigation pumping to the land and to mine and ventilation to control the human environment.Modern refrigeration and air-conditioning plant commonaly used reverse heat engine,where the heat from the engine from cold places to more external heat.Many mechanical engineering products,as well as other leading technology development city have side effects on the environment,producing noise,water and air pollution caused,destroyed land and landscape.Improve productivity and diver too fast in the commodity,that the renewable naturalforces keep pace.For mechanical engineers and others,environmental control is rapidly developing area,which includes a possible development and production of small quantities of pollutants machine sequnce,and the development of new equipment and teachnology has been to reduce and eliminate pollution.4.The role of mechanical engineeringThere are four generic mechanical engineers in common to the above all domains function.The 1st function is the understanding and the research mechanical science foundation.It includes the power and movement of the relationship dynamics For example,in the vibration and movement of the relationship;Automatic control;Study of the various forms of heart,energy,power relations between the thermodynamic;Fluidflows; Heat transfer; Lubricant;And material properties.The 2nd function will be conducts the research,the desing and the development,this function in turn attempts to carry on the essential change to satisfy current and the future needs.This not only calls for a clear understanding of mechanical science,and have to breakdown into basic elements of a complex system capacity.But also the need for synthetic and innovative inventions.The 3rd function is produces the product and the power,include plan,operation and maintenance.Its goal lies in the maintenance eitherenhances the enterprise or the organization longer-tern and survivabilaty prestige at the same time,produces the greatest value by the least investments and the consumption.The 4th function is mechanical engineer’s coordinated function,including the management,the consultation,as well as carries on the market marking in certain situation.In all these function,one kind unceasingly to use the science for a long time the method,but is not traditional or the intuition method tendency,this is a mechanical engineering skill aspect which unceasingly grows.These new rationalization means typical names include:The operations research,the engineering economics,the logical law problem analysis(is called PABLA) However,creativity is not rationalization.As in other areas,in mechanical engineering,to take unexpected and important way to bring about a new capacity,still has a personal,marked characteristice.5.The design of mechanical engineeringThe design of mechanical is the design has the mechanical property the thing or the system,such as:the instrument and the measuring appliance in very many situations,the machine design must use the knowledge of discipline the and so on mathematics,materials science and mechanics.Mechanical engineering desgin includeing all mechanical desgin,but it was a study,because it also includes all the branches of mechsnical engineering,such as thermodynamics all hydrodynamics in the basic disciplines needed,in the mechanical engineering design of the initial stude or mechanical design.Design stages.The entire desgin process from start to finish,in the process,a demand that is designed for it and decided to do the start.After a lot of repetition,the final meet this demand by the end of the design procees and the plan.Design considerations.Sometimes in a system is to decide which parts needs intensity parts of geometric shapesand size an important factor in this context that we must consider that the intensity is an important factor in the design.When we use expression design considerations,we design parts that may affect the entire system design features.In the circumstances specified in the design,usually for a series of such functions must be taken into account.Howeever,to correct purposes,we should recognize that,in many cases thedesign of important design considerations are not calculated or test can determine the components or systems.Especially students,wheen in need to make important decisions in the design and conduct of any operation that can not be the case,they are often confused.These are not special,they occur every day,imagine,for example,a medical laboratory in the mechanical design,from marketing perspective,people have high expectations from the strength and relevance of impression.Thick,and heavy parts installed together:to produce a solid impression machines.And sometimes machinery and spare parts from the design style is the point and not the other point of view.Our purpose is to make those you do not be misled to believe that every design decision will needreasonable mathematical methods.Manufacturing refers to the raw meterials into finished products in the enterprise.Create three distinct phases.They are:input,processing exprot.The first phase includes the production of all products in line with market needs essential.First there must be the demand for the product,the necessary materials,while also needs such as energy,time,human knowledge and technology resourcess .Finall,the need for funds to obtain all the other resources. Lose one stage after the second phase of the resources of the processes to be distributed.Processing of raw materials into finished products of these processes.To complete the design,based on the design,and then develop plans.Plan implemented through various production processes.Management of resources and processes to ensure efficiency and productivity.For example,we must carefully manage resources to ensure proper use of funds.Finally,people are talking about the product market was cast.Stage is the final stage of exporting finished or stage.Once finished just purchased,it must be delivered to the users.According to product performance,installation and may have to conduct further debugging in addition,some products,especially those very complex products User training is necessary.6.The processes of materials and maunfacturingHere said engineering materials into two main categories:metals and non-ferrous,high-performance alloys and power metals.Non-metallic futher divided into plastice,synthetic rubber,composite materials and ceramics.It said the productionproccess is divided into several major process,includingshape,forging,casting/ founding,heat treatment,fixed/connections ,measurement/ quality control and materal cutting.These processes can be further divide into each other’s craft.Various stages of the development of the manufacturing industry Over the years,the manufacturing process has four distinct stages of development, despite the overlap.These stages are:The first phase is artisanal,the second Phase is mechanization.The third phase is automation the forth Phase is integrated.When mankind initial processing of raw materials into finished products will be,they use manual processes.Each with their hands and what are the tools manuslly produced.This is totally integrated production take shape.A person needs indentification,collection materials,the design of a product to meet that demand,the production of such products and use it.From beginning to end,everything is focused on doing the work of the human ter in the industrial revolution introduced mechanized production process,people began to use machines to complete the work accomplished previously manual. This led to the specialization.Specialization in turn reduce the manufacture of integrated factors.In this stage of development,manufacturing workers can see their production as a whole represent a specific piece of the part of the production process.One can not say that their work is how to cope with the entire production process,or how they were loaded onto a production of parts finished.Development of manufacting processes is the next phase of the selection process automation.This is a computer-controlled machinery and processes.At this stage,automation island began to emerge in the workshop lane.Each island represents a clear production process or a group of processes.Although these automated isolated island within the island did raise the productivity of indivdual processes,but the overall productivity are often not change.This is because the island is not caught in other automated production process middle,but not synchronous with them .The ultimate result is the efficient working fast parked through automated processes,but is part of the stagnation in wages down,causing bottlenecks.To better understand this problem,you can imagine the traffic in the peak driving a red light from the red Service Department to the next scene. Occasionally you will find a lot less cars,more than being slow-moving vehicles,but the results can be found by thenext red light Brance.In short you real effect was to accelerate the speed of a red Department obstruction offset.If you and other drivers can change your speed and red light simultaneously.Will advance faster.Then,all cars will be consistent,sommth operation,the final everyone forward faster.In the workshop where the demand for stable synchronization of streamlined production,and promoted integration of manufacturing development.This is a still evolving technology.Fully integrated in the circumstances,is a computer-controllrd machinery and processing.integrated is completed through computer.For example in the preceding paragraph simulation problems,the computer will allow all road vehicles compatible with the change in red.So that everyone can steady traffic.Scientific analysis of movement,timing and mechanics of the disciplines is that it is composed of two pater:statics and dynamics.Statics analyzed static system that is in the system,the time is not taken into account,research and analysis over time and dynamics of the system change.Dynameics from the two componets.Euler in 1775 will be the first time two different branches: Rigid body movement studies can conveniently divided into two parts:geometric and mechanics.The first part is without taking into account the reasons for the downward movement study rigid body from a designated location to another point of the movement,and must use the formula to reflect the actual,the formula would determine the rigid body every point position. Therefore,this study only on the geometry and,more specifically,on the entities from excision.Obviously,the first part of the school and was part of a mechanical separation from the principles of dynamics to study movement,which is more than the two parts together into a lot easier.Dynamics of the two parts are subsequently divided into two separate disciplines,kinematic and dynamics,a study of movement and the movement strength.Therefore,the primary issue is the design of mechanical systems understand its kinematic.Kinematic studies movement,rather than a study of its impact.In a more precise kinematic studies position,displacement,rotation, speed,velocity and acceleration of disciplines,for esample,or planets orbiting research campaing is a paradigm.In the above quotation content should be pay attention that the content of the Euler dynamics into kinematic and rigid body dynamics is based on the assumptionthat they are based on research.In this very important basis to allow for the treatment of two separate disciplines.For soft body,soft body shape and even their own soft objects in the campaign depends on the role of power in their possession.In such cases,should also study the power and movement,and therefore to a large extent the analysis of the increased complexity.Fortunately, despite the real machine parts may be involved are more or less the design of machines,usually with heavy material designed to bend down to the lowest parts.Therefore,when the kinematic analysis of the performance of machines,it is often assumed that bend is negligible,spare parts are hard,but when the load is known,in the end analysis engine,re-engineering parts to confirm this assnmption.机械工程1.机械工程简介机械工程是工程学的一个分支,它研究机械和动力的产,尤其是力和动力。
机械专业毕业设计外语翻译

本科毕业设计(论文)外文译文院(系):机电工程学院专业:机械设计制造及其自动化姓名:学号:外语文献翻译原文:3.4.1CAD HARDWAREComputersThere are two major types of hardware used in a CAD system. Computer and input/output (I/O) devices. In the early days of CAD. Some commercial CAD systems used proprietary computers. Today, nearly all CAD software runs on a general-purpose computer.Depending on the complexity of the CAD package, it may require a mainframe computer, a minicomputer, or simply a microcomputer. In general, the more functionalities a CAD system provides, the more powerful the computer needed. Three dimensional solid modelers require much more computing than do two-dimensional drafting systems; thus, they need more powerful computers. Systems that integrate engineering analysis or simulation packages generally are more computation-intensive. A powerful computer not only speeds up the response of a CAD system, but also can support multiple users without significant performance degradation.Several other parameters and components concerning the computer also have to be considered.CAD HARDWARErandom-access memory (RAM)capacitypermanent disk-storage capacityspecial graphics acceleratortape backupsRAM is the actual physical memory (vs. virtual memory)of a computer. A small memory capacity means slow processing due to frequent swapping between the physical memory and the virtual memory on disk. Because CAD is extremely storage demanding, disk capacity is important. Small disk capacity limits the system to the storage of only a few drawings. CAD is graphics-based and requires tremendous data processing. A graphics accelerator can drastically increase the performance of the system. Another component, the hard disk, is typically the major cost of a computer system. Therefore, it is not cost-justifiable to store all drawings on line on disk. Magnetic tape is still the most economical medium to use for off-line data storage. It is necessary for a CAD system to have a tape backup subsystem.Currently, all levels of computers are used in CAD systems. Personal computers are used in low-cost,2-D drafting applications, and with the new power of these computers, hey are also being used for some 3-D solid modeling applications. Engineering workstations have been the mainstay in CAD, and are usually a single-user CAD workstation in a network. Minicomputers are used in multiuser CAD systems. Mainframes are used for large multiuser CAD systems to support real time simulation and engineering analysis. Sometimes, in a large corporation, all levelsof CAD systems are implemented. All these systems are linked together through a hierarchical computer network.3.4.2 Input. Output (I/O)DevicesFigure 3.7 shows the typical I/O devices used in a CAD system. Input devices are generally used to transfer information from a human or storage medium to a computer where ”CAD functions” are carried out. A keyboard is the standard input device used to transmit alphanumeric data to the system. Function keypads are also used to make input easier. Joysticks, track balls, and mousse are also used to manipulate a cursor. They can be used to position the graphic cursor(e.g. cross hair)on a monitor and feed back the location of an object on the monitor to the computer. Using these devices allows an operator to address terminal locations to interactively in reaching an accurate position. Mouses have been used extensively with windows and pull-down menus. They are easy to use for pointing; However, using a mouse to trace a curve is not an easy task.There are three basic approaches to input an existing drawing;(1)model the object on a drawing,(2)digitize the drawing, or (3)scan the object. Digitizing is usually much easier than modeling. A digitizer is a device that translates the X-Y locations on a drawing than modeling. A digitizer is a device that translates the X-Y locations on a drawing into a digital and feeds that signal to a computer. Graphics scanners scan a drawing and convert it to a CAD-system-readable format. Some scanners have built-in character-recognition software that can convert characters on paper into ASCII codes. Another input device is a sketch pad called a graphics tablet. A graphics tablet is a special flat surface on which a user draws with a stylus. The location of the stylus is sent to the computer. The tablet is an absolute coordinate device. It is easy to implement overlay menus on the tablet and pull down menus on the screen to improve the operation. Currently. the tablet is the most popular input device used in CAD other than the keyboard.The standard output device for CAD is a monitor display. Modern monitor displays are raster-scan display monitors. Similar to a TV monitor, an electron gun(Sony Trinitron uses three guns for three basic colors)sends an electronic beam to the front of the monitor. Easy display dot is called a pixel(picture element).For color displays, each pixel is represented by three closely located dots with red, green , and blue colors. The electronic beam selects the color elements and the intensity of each color element. The resolution of the monitor is determined by the number of different colors or gray scales displayable at each pixel, usually measured in bits, A 1-bit display can turn each pixel either ON or OFF.A gray scale has at least v2 bits. A 1-bit display can turn each pixel either ON or OFF.A gray scale has at least 2 bits which allow three light intensities plus an OFF (2*2).Usually, displays are 4 bits(16 colors),8 bits(256 colors),16 bits(thousands of colors),and 24bits (millions of colors).The electronic beam sweeps the screen from the top to the bottom line by line. Because the dot is lit for only a very short period of time, the sweep must be done very quickly in order not to have a flickering image. The refresh rate is a measure of how many times the monitor is redrawn in one second.The computer does not draw directly on the monitor. Connecting the computer to the monitor is u-sually a RGB(red, green, blue)cable. Three separate signal lines are connected. On the graphics board in the computer are circuits to generate the analog signals required to drive the monitor. There is also a frame buffer that serves as memory to store the image. Each pixel on the screen has a corresponding address in the frame buffer. The data in the frame buffer are converted into the appropriate analog signal and sent to the monitor at the refresh rate. Separately, the computer writes directly to the frame buffer the image it intends to draw. The greater the display size and number of colors, the more frame buffer is needed. The frame buffer on the graphics board is made of random-access memory(RAM).The calculator lend support toes to paint the software AutoCAD to make us can be with the sketch that the astonishing speed draw the engineering sketch or machine sketch and other with accuracy to sophisticate. The calculator paints to paint the different place, one of them with handicraft the paintings with out the diagram divide a step proceed of, because of but would sometimes appear the traditional handicraft the painting hour the problem of the impossible emergence. General circumstance bottom, usage the AutoCAD proceeds painting, control the precision painting and not that difficult, but want accurate then need the certain technique out the diagram. Us- ually paint or outsing diagram to have no to need to change to measure to AutoCAD system worth make the modification with establish, take its the province worth can normal work, but have the special request, must modify the related system to change measure; Too sometimes the request of the diagram paper with make the diagram's way of doing the antinomy, and be to adopt the to make the diagram method to can't attain the request of the diagram paper, will adopt some techniqueiques to modify the related system to change to measure, and can make the calculator draw to attain the request of the diagram paper with output's sketch.AutoCAD line type establishing of comparison At teaching of process inside would usually run into what this kind of circumstance, while establishing diagram layer, clearly established the point lin eationed, and consequently output to however investigate its reason for the solid lined, and is usually because of the line typed the establishing of comparison is not appropriate and cau-sable. Should you so establish the comparison of what kind of line type? How to use the line type the comparison in the painting?Usage AutoCAD painting, besides continuous line type( Continuous), the other line type is all from the solid line segment, blank segment, point series for or text this constituting. On-line type definition document the inside have already defined these line types the segment's standard length, and show on held the act or at print the machine\ painting output, each length and ex-portation comparison with line type comparison direct proportion. When show or print, the painting boundary that customer that request, this hour establish is out of accordance with the painting boundary of the province difference big, on held the act show or paint output's line type would match the engineering graphics to will pass the changes line type comparison the system the method that change the deal, enlarge orcontract all line types each a small segment of length, make the sketch made meet the request. In the Auto CAD, imply the adjustment line type the comparison's order: Overall situation line type comparison factor tie department exportation ratio for line type ratio factor, used foring the control not continuous line type. The Ltscale is right to have the object validity, Celtscale the province for to new object validating, twoly changing the deal w-orth all for 1.For use the line type that Auto CAD2002 painting, big part contain three kinds of forms,( such as: Comparison that Center, Center2, Center*2, Dashed, Dashed2, Dashed*2) the first is a half, the third line type for the standard form, the second line type that comparison that the first line type is the first line type of two times, if line type the comparison establish to is not suitable for, and would then make some exportation diagrams the line( such as the point lineation, dotted line...etc.) change into a solid line.Two, line breadth the count of establishPass by what handicraft painting, its painting with outs the diagram is a synchronous proceeding of, now calculator painting, its painting with outs the diagram divide a step proceeds. Wether draw the construction engineering diagram or machine spare parts diagram, at print control that a work that exportation engineering drawing, the most is a line to print the drawing the breadth, line the type, color, seal a line breadth for, and eachly growing to line type all contain its cowgirl, in the AutoCAD painting process of the old edition, even defined the line type the width, its at see the diagram area can't also display the line type the width's differentiation.( not contain many righteousness lines the Pline)Width for color for can passing the diagram layer or set upping the line coming distinguish analysing the line.What research of current painting tries a, adopt of is this kind of method.But in the AutoCAD2002, add entity that" Lweight"( line type the width establish) order, provided the new function for customer, then make use of the entity characteristic to proceed the control, and establish the line breadth for the sketch, and make use of it can at hold the act to up show with print to output, control the entity's line breadth.2002 versions inside print to establish and can is divided into three part, and for printing machine belong to the sex to establish, print the style to establish respectively and the page establish.Because of the model of breadth line the space is different from diagram manifestation of space paper result, in the model space therefore the elephant vegetable show, but in the diagram paper the space is then then to print the width to proceed to show, because of but we while drawing ske tch should know at the diagram line that true width established by line breadth of model space, and is not equal with object. When the line breadth is worth to establish to"0", it show with the minimum width( plain breadth of an elephant) on held the act, and the line breadth settle to other worth, then come showing with the worth specific value of plain width and true unit of elephant.Three, the sketch output the establishing of comparison When we draw sketch that comparison that comparison output the sketch with us hour use different, canmake originally text in the sketch that draw word exportation comparison for marking noting waiting in the output's sketch take placing changing, therefore at drawing the sketch before returning the beard make suring the sketch.For guaranteeing the sketch to output our want the literalness size, should when the text word establish usage following formula: The text word draws the high degree the = the text word output high degree* the sketch to output the comparison; The sketch outputs the comparison= output the diagram the length for of length( width)/ diagram.( width) draw the width of the diagram line to also should consider this point, its to settle the width same as output the width to multiply by with its comparison worth.From above practice with analyze to can see out, calculator painting and incompletelyresemble handicraft painting so synchronously paint with out diagram, therefore sometimes make with the diagram method can't attain the request of the diagram paper. Some in common use system that this demand we are deep into control the calculator to paint the theories, and can expertly control the operation method to change the deal with establish the technique, and can make the work of our painting more convenient, smooth, consumedly increase to paint the level with paint the efficiency.译文:3.4.1CAD硬件计算机两大主要类型的硬件使用于CAD系统,计算机和输入/输出设备。
机械毕业设计英文外文翻译简易机械手及控制
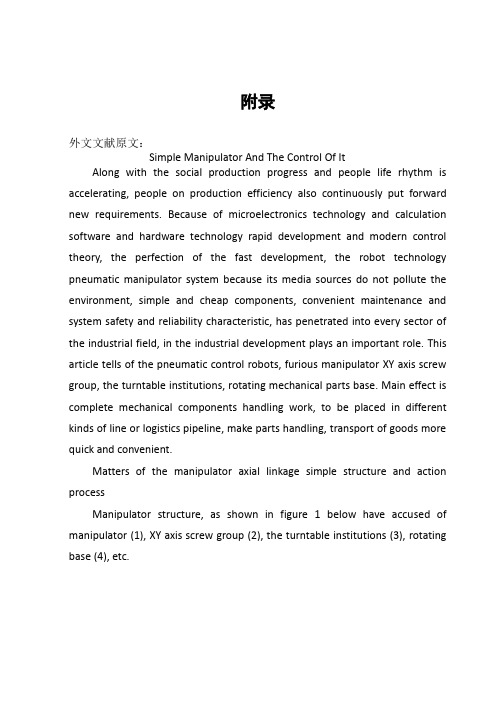
附录外文文献原文:Simple Manipulator And The Control Of ItAlong with the social production progress and people life rhythm is accelerating, people on production efficiency also continuously put forward new requirements. Because of microelectronics technology and calculation software and hardware technology rapid development and modern control theory, the perfection of the fast development, the robot technology pneumatic manipulator system because its media sources do not pollute the environment, simple and cheap components, convenient maintenance and system safety and reliability characteristic, has penetrated into every sector of the industrial field, in the industrial development plays an important role. This article tells of the pneumatic control robots, furious manipulator XY axis screw group, the turntable institutions, rotating mechanical parts base. Main effect is complete mechanical components handling work, to be placed in different kinds of line or logistics pipeline, make parts handling, transport of goods more quick and convenient.Matters of the manipulator axial linkage simple structure and action processManipulator structure, as shown in figure 1 below have accused of manipulator (1), XY axis screw group (2), the turntable institutions (3), rotating base (4), etc.Figure 1 Manipulator StructureIts motion control mode is: (1) can rotate by servomotor Angle for 360 °breath control manipulator (photoelectric sensor sure start 0 point); (2) by stepping motor drive screw component make along the X, Y manipulators move (have X, Y axis limit switches); (3) can rotates 360 °can drive the turntable institutions manipulators and bushings free rotation (its electric drag in part by the dc motivation, photoelectric encoder, close to switch etc); (4) rotating base main support above 3 parts; (5) gas control manipulator by pressure control (Zhang close when pressed on, put inflatable robot manipulators loosen) when gas.Its working process for: when the goods arrived, manipulator system begins to move; Stepping motor control, while the other start downward motion along the horizontal axis of the step-motor controller began to move exercise; Servo motor driver arrived just grab goods manipulators rotating the orientation of the place, then inflatable, manipulator clamped goods.Vertical axis stepper motor drive up, the other horizontal axis stepper motor driver started to move forward; rotary DC motor rotation so that the whole robot motion, go to the cargo receiving area; longitudinal axis stepper motor driven down again, arrived at the designated location, Bleed valve,mechanical hand release the goods; system back to the place ready for the next action.II.Device controlTo achieve precise control purposes, according to market conditions, selection of a variety of keycomponents as follows:1. Stepper motor and driveMechanical hand vertical axis (Y axis) and horizontal (X axis) is chosen Motor Technology Co., Ltd. Beijing Stone 42BYG250C type of two-phase hybrid stepping motor, step angle of 0.9 ° / 1.8 °, current is 1.5A. M1 is the horizontal axis motor driven manipulator stretch, shrink; M2 is the vertical axis motor driven manipulator rise and fall. The choice of stepper motor drive is SH-20403 type, the drive uses 10 ~ 40V DC power supply, H-phase bridge bipolar constant current drive, the maximum output current of 3A of the 8 optional, maximum fine of 64 segments of 7 sub-mode optional optical isolation, standard single-pulse interface, with offline capabilities to maintain semi-sealed enclosure can be adapted to environmental conditions even worse, provide semi-current energy-saving mode automatically. Drive the internal switching power supply design to ensure that the drive can be adapted to a wide voltage range, the user can according to their circumstances to choose between the 10 ~ 40VDC. Generally the higher rated power supply voltage can improve high-speed torque motor, but the drive will increase the loss and temperature rise. The maximum output drive current is 3A / phase (peak), six drive-panel DIP switch on the first three can be combined 5,6,7 8 out of state, corresponding to the 8 kinds of output current from 0.9A to 3A to meet the different motors. The drive can provide full step, half step improvement, subdivision 4, 8 segments, 16 segments, 32 segments and 64segments of 7 operating modes. The use of six of the drive panel DIP switches 1,2and3 can be combined from three different states.2. Servo motors and drivesManipulator with Panasonic servo motor rotational movement A series of small inertia MSMA5AZA1G, the rated 50W, 100/200V share, rotary incremental encoder specifications (number of pulses 2500p / r, resolution of 10000p / r, Lead 11 lines) ; a seal, no brakes, shaft with keyway connections. The motor uses Panasonic's unique algorithms, the rate increased by 2 times the frequency response, to 500Hz; positioning over the past adjust the scheduled time by Panasonic servo motor products for the V Series of 1 / 4. With the resonance suppression, control, closed loop control, can make up for lack of mechanical rigidity, in order to achieve high positioning accuracy can also be an external grating to form closed loop control to further improve accuracy. With a conventional automatic gain adjustment and real-time automatic gainInterest adjustment in the automatic gain adjustment methods, which also has RS-485, RS-232C communication port, the host controller can control up to 16 axes. Servo motor drives are a series MSDA5A3A1A, applicable to small inertia motor.3. DC machine360 ° swing of the turntable can be a brushless DC motor driven organization, the system is chosen when the profit company in Beijing and the 57BL1010H1 brushless DC motor, its speed range, low-speed torque, smooth running, low noise, high efficiency. Brushless DC motor drive using the Beijing and when Lee's BL-0408 produced by the drive, which uses 24 ~ 48V DC power supply, a start-stop and steering control, over current, overvoltage and locked rotor protection, and there is failure alarm output external analog speed control,braking down so fast.4. Rotary encoderCan swing 360 °in the body on the turntable, fitted with OMRON E6A2 produced incremental rotary encoder, the encoder signals to the PLC, to achieve precise positioning of rotary bodies.5. PLC SelectionAccording to the system design requirements, the choice of OMRON CPM2A produced minicomputer. CPM2A in a compact unit integrated with a variety of properties, including the synchronization pulse control, interrupt input, pulse output, analog set and clock functions. CPM2A the CPU unit is a stand-alone unit, capable of handling a wide range of application of mechanical control, it is built in the device control unit for the ideal product. Ensure the integrity of communications and personal computers, other OMRON PC and OMRON Programmable Terminal communication. The communication capability allows the robot to Axis simple easy integration into industrial control systems.III. Software programming1. Software flow chartPLC programming flow chart is based. Only the design flow, it may be smooth and easy to prepare and write a statement form the ladder, and ultimately complete the process design. So write a flow chart of program design is critical to the task first thing to do. Axis Manipulator based on simple control requirements, drawing flow chart shown in Figure 2.Figure 2 Software flow chart2. Program partBecause space is limited, here only paper listed the first two program segment for readers see.Figure 3 Program partIV. ConclusionAxis simple robot state by the various movements and PLC control, the robot can not only meet the manual, semi-automatic mode of operation required for such a large number of buttons, switches, position detection point requirements, but also through the interface components and Computer Organization PLC industrial LAN, network communication and network control. Axis simple robot can be easily embedded into industrial production pipeline.中文译文:简易机械手及控制随着社会生产不断进步和人们生活节奏不断加快,人们对生产效率也不断提出新要求。
机械类毕业设计外文翻译_New
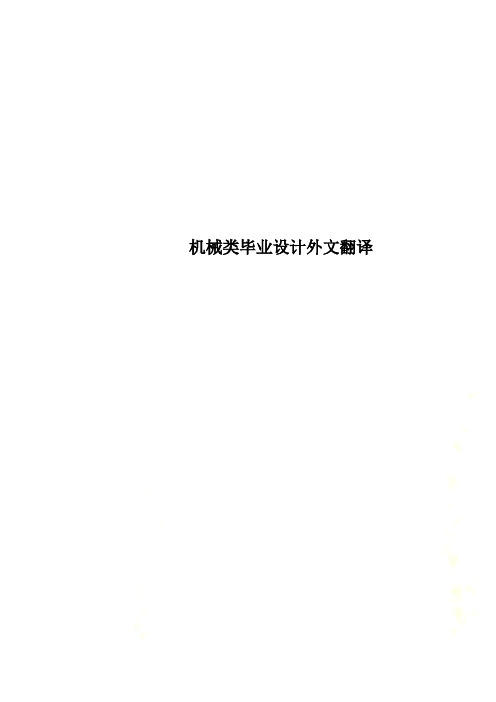
机械类毕业设计外文翻译外文原文Options for micro-holemakingAs in the macroscale-machining world, holemaking is one of the most— if not the most—frequently performed operations for micromachining. Many options exist for how those holes are created. Each has its advantages and limitations, depending on the required hole diameter and depth, workpiece material and equipment requirements. This article covers holemaking with through-coolant drills and those without coolant holes, plunge milling, microdrilling using sinker EDMs and laser drilling.Helpful HolesGetting coolant to the drill tip while the tool is cutting helps reduce the amount of heat at the tool/workpiece interface and evacuate chips regardless of hole diameter. But through-coolant capability is especially helpful when deep-hole microdrilling because the tools are delicate and prone to failure when experiencing recutting of chips, chip packing and too much exposure to carbide’s worst enemy—heat.When applying flood coolant, the drill itself blocks access to the cutting action. “Somewhere about 3 to 5 diam eters deep, the coolant has trouble getting down to the tip,” said Jeff Davis, vice president of engineering for Harvey Tool Co., Rowley, Mass. “It becomes wise to use a coolant-fed drill at that point.”In addition, flood coolant can cause more harm than good when microholemaking. “The pressure from the flood coolant can sometimes snap fragile drills as they enter the part,” Davis said.The toolmaker offers a line of through-coolant drills with diameters from 0.039" to 0.125" that are able to produce holes up to 12 diameters deep, as well as microdrills without coolant holes from 0.002" to 0.020".Having through-coolant capacity isn’t enough, though. Coolant needs to flow at a rate that enables it to clear the chips out of the hole. Davis recommends, at a minimum, 600 to 800 psi of coolant pressure. “It works much better if you have higher pressure than that,” he added.To prevent those tiny coolant holes from becoming clogged with debris, Davis also recommends a 5μm or finer coolant filter.Another recommendation is to machine a pilot, or guide, hole to prevent the tool from wandering on top of the workpiece and aid in producing a straight hole. When applying a pilot drill, it’s important to select one with an included angle on its point that’s equal t o or larger than the included angle on the through-coolant drill that follows.The pilot drill’s diameter should also be slightly larger. For example, if the pilot drill has a 120° included angle and a smaller diameter than a through-coolant drill with a 140°included angle, “then you’re catching the coolant-fed drill’s corners and knocking those corners off,” Davis said, which damages the drill.Although not mandatory, pecking is a good practice when microdrilling deep holes. Davis suggests a pecking cycle that is 30 to 50 percent of the diameter per peck depth, depending on the workpiece material. This clears the chips, preventing them from packing in the flute valleys.Lubricious ChillTo further aid chip evacuation, Davis recommends applying an oil-based metalworking fluid instead of a waterbased coolant because oil provides greater lubricity. But if a shop prefers using coolant, the fluid should include EP (extreme pressure) additives to increase lubricity and minimize foaming. “If you’ve got a lot of foam,” Davis noted, “the chips aren’t being pulled out the way they are supposed to be.”He added that another way to enhance a tool’s slipperiness while extending its life is with a coating, such as titanium aluminum nitride. TiAlN has a high hardness and is an effective coating for reducing heat’s impact when drilling difficult-to-machine materials, like stainless steel.David Burton, general manager of Performance Micro Tool, Janesville, Wis., disagrees with the idea of coating microtools on the smaller end of the spectrum. “Coatings on tools below 0.020" typically have a negative effect on every machining aspect, from the quality of the initial cut to tool life,” he said. That’s becaus e coatings are not thin enough and negatively alter the rake and relief angles when applied to tiny tools.However, work continues on the development of thinner coatings, and Burton indicated that Performance Micro Tool, which produces microendmills and microrouters and resells microdrills, is working on a project with others to create a submicron-thickness coating. “We’re probably 6 months to 1 year from testing it in the market,” Burton said.The microdrills Performance offers are basically circuit-board drills, which are also effective for cutting metal. All the tools are without through-coolant capability. “I had a customer drill a 0.004"-dia. hole in stainless steel, and he was amazed he could do it with a circuit-board drill,” Burton noted, adding th at pecking and running at a high spindle speed increase the drill’s effectiveness.The requirements for how fast microtools should rotate depend on the type ofCNCcharged EDM wire. The fine-hole option includes a W-axis attachment, which holds a die that guides the electrode, as well as a middle guide that prevents the electrode from bending or wobbling as it spins. With the option, the machine is appropriate for drilling hole diameters less than 0.005".Another sinker EDM for micro-holemaking is the Mitsubishi VA10 with afine-hole jig attachment to chuck and guide the fine wire applied to erode the material. “It’s a standard EDM, but with that attachment fixed to the machine, we can do microhole drilling,” said Dennis Powderly, sinker EDM product manager for MC Machinery Systems Inc., Wood Dale, Ill. He added that the EDM is also able to create holes down to 0.0004" using a wire that rotates at up to 2,000 rpm.Turn to TungstenEDMing is typically a slow process, and that holds true when it is used for microdrilling. “It’s very slow, and the finer the details, the slower it is,” said , president and owner of Optimation Inc. The Midvale, Utah, company builds Profile 24 Piezo EDMs for micromachining and also performs microEDMing on a contract-machining basis.Optimation produces tungsten electrodes using a reverse-polarity process and machines and ring-laps them to as small as 10μm in diameter with 0.000020" roundness. Applying a 10μm-dia. electrode produces a hole about 10.5μm to 11μm in diameter, and blind-holes are possible with th e company’s EDM. The workpiece thickness for the smallest holes is up to 0.002", and the thickness can be up to 0.04" for 50μm holes.After working with lasers and then with a former EDM builder to find a better way to produce precise microholes, Jorgense n decided the best approach was DIY. “We literally started with a clean sheet of paper and did all the electronics, all the software and the whole machine from scratch,” he said. Including the software, the machine costs in the neighborhood of $180,000 to $200,000.Much of the company’s contract work, which is provided at a shop rate of $100 per hour, involves microEDMing exotic metals, such as gold and platinum for X-ray apertures, stainless steel for optical applications and tantalum and tungsten for the electron-beam industry. Jorgensen said the process is also appropriate for EDMing partially electrically conductive materials, such as PCD.“The customer normally doesn’t care too much about the cost,” he said. “We’ve done parts where there’s $20,000 [in time and material] involved, and you can put the whole job underneath a fingernail. We do everything under a microscope.”Light CuttingBesides carbide and tungsten, light is an appropriate “tool material” formicro-holemaking. Although most laser drilling is performed in the infrared spectrum, the SuperPulse technology from The Ex One Co., Irwin, Pa., uses a green laser beam, said Randy Gilmore, the company’s director of laser technologies. Unlike the femtosecond variety, Super- Pulse is a nanosecond laser, and its green light operates at the 532-nanometer wavelength. The technology provides laser pulses of 4 to 5 nanoseconds in duration, and those pulses are sent in pairs with a delay of 50 to 100 nanoseconds between individual pulses. The benefits of this approach are twofold. “It greatly enhances material removal compared to other nanosecond lasers,” Gilmore said, “and greatly reduces the amount of thermal damage done to the workpiece material” because of the pulses’ short duration.The minimum diameter produced with the SuperPulse laser is 45 microns, but one of the most common applications is for producing 90μm to 110μm holes in diesel injector nozzles made of 1mm-thick H series steel. Gilmore noted that those holes will need to be in the 50μm to 70μm ra nge as emission standards tighten because smaller holes in injector nozzles atomize diesel fuel better for more efficient burning.In addition, the technology can produce negatively tapered holes, with a smaller entrance than exit diameter, to promote better fuel flow.Another common application is drilling holes in aircraft turbine blades for cooling. Although the turbine material might only be 1.5mm to 2mm thick, Gilmore explained that the holes are drilled at a 25° entry angle so the air, as it comes out of the holes, hugs the airfoil surface and drags the heat away. That means the hole traverses up to 5mm of material. “Temperature is everything in a turbine” he said, “because in an aircraft engine, the hotter you can run the turbine, the better the fuel economy and the more thrust you get.”To further enhance the technology’s competitiveness, Ex One developed apatent-pending material that is injected into a hollow-body component to block the laser beam and prevent back-wall strikes after it creates the needed hole. After laser machining, the end user removes the material without leaving remnants.“One of the bugaboos in getting lasers accepted in the diesel injector community is that light has a nasty habit of continuing to travel until it meets anothe r object,” Gilmore said. “In a diesel injector nozzle, that damages the interior surface of the opposite wall.”Although the $650,000 to $800,000 price for a Super- Pulse laser is higher than a micro-holemaking EDM, Gilmore noted that laser drilling doesn’t require electrodes. “A laser system is using light to make holes,” he said, “so it doesn’t have a consumable.”Depending on the application, mechanical drilling and plunge milling, EDMing and laser machining all have their place in the expanding microm achining universe. “People want more packed into smaller spaces,” said Makino’s Kiszonas.中文翻译微孔的加工方法正如宏观加工一样,在微观加工中孔的加工也许也是最常用的加工之一。
- 1、下载文档前请自行甄别文档内容的完整性,平台不提供额外的编辑、内容补充、找答案等附加服务。
- 2、"仅部分预览"的文档,不可在线预览部分如存在完整性等问题,可反馈申请退款(可完整预览的文档不适用该条件!)。
- 3、如文档侵犯您的权益,请联系客服反馈,我们会尽快为您处理(人工客服工作时间:9:00-18:30)。
附录科技译文:Numerical ControlNumerical Control(NC) is a method of controlling the movements of machineComponents by directly inserting coded instructions in the form of numerical data(numbers and data ) into the system.The system automatically interprets these data and converts to output signals. These signals ,in turn control various machine components ,such as turning spindles on and off ,changing tools,moving the work piece or the tools along specific paths,and turning cutting fluits on and off.In order to appreciate the importer of numerical control of machines ,let’s briefly review how a process such as machining has been carried out traditionally .After studying the working drawing of a part, the operator sets up the appropriate process parameters(such as cutting speed ,feed,depth of cut,cutting fluid ,and so on),determines the sequence of operations to be performed,clamps the work piece in a workholding device such as chuck or collet ,and proceeds to make the part .Depending on part shape and the dimensional accuracy specified ,this approach usually requires skilledoperators.Furthermore,the machining procedure followed may depend on the particular operators,and because of the possibilities of human error, the parts produced by the same operator may not all be identical .Part quality may thus depend on the particular operator or even the same operator on different days or different hours of the day. Because of our increased concern with product quality and reducing manufacturing costs,such variability and its effects on product quality are no longer acceptable this situation can be dliminated by numerical control of the mathining operation.We can illustrate the importance of numerical concrol by the following example. Asume that holes have to be drilled on a part in the positions shown in the picture.In the traditional manual method of machining thid part, the operator positions the drill with respect to the workpiece, using as erfererence points any of the three of the method shown. The operator then proceeds to drill these holes. Let,s assume that 100 parts, having exactly the same shape and dimensional accuracy, have to be dielled. Obviously, this operation is going to be tediious because the operator has to go throuth the same motions again and again. Moreover, the probabiluty is high that, faor warious reasons, some of the paths machined will be different fromorthers. Let`s further assume that during this production run, the order for these paths is changed, so that 10 of the paths now require holes in difficult positions. The machinisst now has to reset the mathine , wehich will be time consuming and subject to error. Such operations can be perfomedeasily by numerical conctrol machines that are capable of producing parts reeatedly and accurately and of handling differeent parts by simply londing differeent part programs.In numerical control ,data concerning all aspects of the machining operation,such as locations ,speeds,and cutting fluid,are stored on magnetic tape.,cassettes ,floppy or hard disks,or paper or plastic(Mylar,which is a thermoplastic polyester)tape,.Date are stored on punched 25 mm wide paper or plastic tape ,as originally developed and still used .The concept of NC control is that holes in the tape represent specific information in the form of alphanumeric codes ,The presence (on)or absence (off),of these holes is read by sensing devices in the contuol panel ,which then actuate relays and other devices (called hard-wired contuols),These devices control various mechanical and electrical system in the machine .This method eliminnated manual setting of machine positions and tool paths or the use of templates and othermechanical guides and devices. Conplex operations,such as turning a part having various contours and die sinking in milling machine ,can be carried out.Numerical control has had a major impact on all aspects of manufacturing operations.It is a widely applied technology ,particularly in the following areas:a)Machining centersb)Milling,turning,boring,drilling,and gringingc)Electrical-discharge,laser-beam,and electron-beam machiningd) Water-jet cuttinge) Punching and nibbling .f) Pipe bending and metal spinning.g) Sopt welding and metal spinning.h) Assembly operations.Numerical control machines are now used extensively in small-and-medium-quantity(typically 500 parts or less)of a wide variety of parts in small shops and large manufacture facilities. Older machines can be retrofitted with numerical control.Advantages and Limitations Numerical control has following advantages over conventional method of machine control:1.Flexibility of operation and ability to produce complex shape with good dimensional accuracy,repeatability,reduced scrap loss,and high production rates ,productivity,and product quality.2.Tooling costs are reduced,since templates and other fixtures are not required.3.Machine adjustments are easy to make with minicomputer and digital readout.4.More operations can be performed with each setup,and less lead time for setup and machining is required compared to conventional methods.Design changes are facilitated,and inventory is reduced.5.Programs can prepared rapidly and can be recalled at any time utilizing microprocessors,Less paperwork is involved.6.Faster prototype productiong is possible.7.Required operator skill is less,and the operator has more time to attend to other tasks in the work area.The major limitations of NC are the relatively high cost of the equipment and the need for programming and specialmaintenance,requiring trained personal.Because NC machines are complex systems,breakdowns can be very costly,so preventive maintenance is essential.However,these limitations are often easily outweighed by the overall economic advantages of NC.One of the most fundamental concepts in the area of advanced manufacturing technologies is numerical control(NC) Controlling a machine tool using a punched tape or stored program is known as numerical control (NC).NC has been defined by the ElectronicIndustries.Association(EIA)as "a system in which actions are controlled by the direct insertion of numerical data at some point.The numerical data at some point.The numerical data required to produce a part is known as a part program.A numerical control machine toll system contains a machine control unit(MCU) and the machine tool itself(Fig2.16)The MCU is further divided into two elements:The data processing unit(DPU)and the control loops unit (CLU). The DPU processes the code data from the tape or other media and passes information on the position of each axis,required direction of motion,feed rate, and auxiliary function control signals to the CLU. The CLU operates the drive mechanisms ofeach of the axes and signals the completion of operation.The DPU sequentially reads the data.When each line has completed execution of operation.The DPU sequentially read thedata.When each line has completed execution as noted by the CLU,another line of data is read.A data processing unit consists of some or all of the following parts:1)Data input device such as a paper tapereader,RS232-C port,etc2)Data-reading circuits and parity-checking logic3)Decoding circuits for distributing data among the controlled axes4)An interpolator,which supplies machine-motion commands between data points for tool motionA control loops unit,on the other hand consists of the following:1)Position control loops for all the axes ofmotion,where ach axis has a separate control loop2)Velocity control loops,where feed control is required3)Deceleration and backlash take up circuits4)Auxiliary functions control,such as coolanton/off,gear changes,spindle on/off controlGeometric and kinematics data are typically fed from the DPU to the CLU.The CLU then governs the physical system based on the data form the DPU.Numerical control was developed to overcome the limitation of human operators,and it has done so.Numerical control machines are more accurate than manually operated machines,they can produce parts more uniformly,they are faster,and the long-run tooling costs are lower.The development of NC led to the development of several Other innovations in manufacturing technology ;Electic discharge machiningLaser—cutingElectron beam weldingNumerical control has also made maching tools more versatile their manually operated predecessors . An NC machine tool can automatically produce a wide variety of parts ,each involving an assortment of widely varied and complex machining processes . Numerical control has allowed manufacturers to undertaken the production of part ,each involving an assortment of widely varied and complex machining processes .Numerical control has allowed manufactures to undertaken the production of products thatwould not have been feasible from an economic perspective using manually controlled machine tools and processes.翻译:数字控制数控是一种用数字控制机床各部件运动的方法,通过直接向系统输入指令代码(数字和字母)完成的。