压力容器焊后消除应力热处理
压力容器焊后消除应力热处理(2009年8月13日)

�
�
2.哪些压力容器及主要受压元件需焊 后消除应力热处理? 哪些压力容器及主要受压元件需焊 后消除应力热处理?笔者认为:应按 照GB150 10.4.1款和GB151 6.4、6.8 款(指拼接管板、管箱和浮头盖)判 定。凡符合GB150 10.4.1款和GB151 6.4、6.8款规定的压力容器及主要受 压元件均应进行焊后消除应力热处理。
果好,因此在条件具备的情况下,应 优先选用炉内整体热处理方法。
� 对于球形储罐和大型压力容器可 採
取使用现场整体消除应力热处理方法。 � 由于焊后局部消除应力热处理的效 果较炉内整体消除应力热处理差,因 而《容规》和标准对局部消除应力热 处理方法的应用作出了较为明确的限 制。目前局部消除应力热处理只限应 用于B、C、D类焊接接头以及球形封头 与园筒连接的A类焊接接头。
�
� GB/T9452-2003“热处理炉有效加热区
测定方法”等安全技术规范和标准之中。 因而在使用过程中出现了理解上的不 一致和偏差。为了满足钢制压力容器 焊后消除应力热处理的要求,保证钢 制压力容器的安全质量,本文将重点 讨论钢制压力容器焊后消除应力热处 理中常见的一些问题,并就此提出笔 者的认识和看法。
Ⅰ Ⅱ Ⅲ Ⅳ Ⅴ Ⅵபைடு நூலகம்
≤2 ≤4 ≤5 ≤6 ≤8 ≤10
(1)允许用修改量程的方法提高分辨力。
�
�
JB/T10175规定:热处理炉的每个加热区至 少有两支热电偶,一支接记录仪表,另一 支接控温仪表,安放在有效加热区内,其 中一个仪表应具有报警功能。 每台热处理炉必须定期检测有效加热 区,检测周期见表3,检测方法按GB/T9452 的规定,其保温精度应符合表2要求。应在 明显位置悬挂带有有效加热区示意图的检 验合格证。热处理炉只能在有效加热区检 验合格证规定的有效期内使用。
热处理技术中石化压力容器中的问题及解决

在石油化工行业压力容器具有多种用途。
压力容器具备出色的压力承受能力,因此其通常被人们用于盛装液态或者气体。
在压力容器中应用热处理技术,能够在不破坏容器金属材料外部形状的条件下,改变其内部成分的化学性质以及纤维结构,如此能够实现人工调控金属材料性能的目的,有利于相关金属材料发挥其最大潜力。
因此,如何做好石化压力容器热处理的问题应当引起有关方面的高度重视。
1热处理技术概述热处理技术是通过有效衔接与配合加热、冷却以及保温等环节而形成的一类技术。
通常情况下,人们在热处理过程中使用较为频繁的加热方式有燃烧火焰加热以及电加热等。
值得注意的是,在热处理过程中,需要严格把控火焰以及基体的温度。
由于石化压力容器的设计通常采用不同的金属材料或者合金材料,各种金属材料在化学性质上有所差异,为此,工作人员在采用热处理技术设计制造石化压力容器时,往往会采取在适当的时间设置合理温度的做法,如此方能最大限度地保障相关压力容器能发挥最大的性能。
对于热处理技术而言,能否在设备处理工作中发挥最大的效用,很大程度上取决于冷却工作的质量。
由于不同压力容器的技术标准以及材质存在着一定的差异,因此人们一般会采用不同的冷却速度。
经过艰苦的探索与思考,技术人员设计出了一种冷却方式以及三种冷却速度,它们分别是冷却速度最快的淬火,冷却最慢的退火、冷却速度适中的正火以及与淬火关系密切的回火。
通过在容器冷却速度以及方式上开展严格的控制把关工作,能够有效地提升压力容器的密实度,并有助于金属材料或者合金材料发挥其最大应用性能[1]。
2在压力容器设计工作中应用热处理技术的注意事项热处理技术的应用必须在石化压力容器焊接元件工序完成后才能进行。
如果压力容器在制造过程中需要进行多次焊接处理,则需要在检验人员充分确认焊接质量合格、结果满意后方能应用热处理技术,否则可能引发安全事故。
在对碳质钢材开展焊接工作时,应当确保管箱侧面的开口不小于圆筒内径的三分之一。
热处理技术在碳质钢材上的应用,主要目的是消除应力。
压力容器消除应力热处理工艺守则

1目的本守则规定压力容器的消除应力热处理基本程序和要求。
2适用范围2.1本守则适用于压力容器消除应力热处理工序。
2.2消除应力热处理的外包外协厂家亦应按照此守则要求执行。
3职责3.1本程序文件由工艺部制定,其解释权、修改权归工艺部所有。
4.3焊件进炉时炉内温度不得高于400℃。
焊件出炉时,炉温不得高于400℃,出炉后应在静止的空气中冷却。
4.4升温速度最大不应超过5500/δPWHT℃/h,且不应超过220℃/h,最小不低于55℃/h;降温速度最大不应超过7000/δPWHT℃/h,且不应超过280℃/h,最小不低于55℃/h。
4.5焊件升温期间,加热区内任意长度为4600毫米内的温差不得大于120℃。
4.6焊件保温期间,加热区内最高与最低温度之差不宜大于80℃。
4.7升温和保温期间应控制加热区气氛,防止焊件表面过度氧化。
5工艺操作5.1升温和保温期间应控制加热区气氛,防止焊件表面过度氧化。
5.2消除应力热处理应尽可能采取整体热处理。
当无法整体热处理时,允许分段加热进行。
分段热处理时,其重复加热长度至少为1500mm,加热区以外部分应采取保温措施,防止产生有害的温度梯度。
5.3对于B、C、D、E类焊接接头,球形封头与圆筒连接接头以及缺陷焊补部位允许采取局部热处理。
局部热处理的有效加热范围为:1)最大宽度焊缝两侧各加δPWHT或50mm,取两者较小值;2)返修焊缝端部方向上加δPWHT或50mm,取两者较小值;3)接管与壳体相焊时,应环绕包括接管在内的筒体全圆周加热,且在垂直于焊缝方向上自焊缝边缘加δPWHT或50mm,取两者最小值。
4)加热区以外部分靠近加热部位的地方应采取措施防止较大的温度梯度。
5.4装炉时,工件距炉门不得小于500毫米,距炉墙不得小于300毫米,加热炉对炉温应能控制,对工件不得产生过度氧化和有害影响。
5.5装炉时需要将工件垫平、垫稳。
工件之间保持一定距离,不要靠紧。
若需垛装时,上下工件之间要用垫板垫起。
钢制压力容器焊接工艺及焊后热处理方法分析

钢制压力容器焊接工艺及焊后热处理方法分析【摘要】本文主要探讨了钢制压力容器焊接工艺及焊后热处理方法的分析。
首先分析了钢制压力容器的焊接工艺,包括焊接材料选择、焊接方法、焊接参数控制等内容,对焊接工艺进行了详细的解析。
接着对焊后热处理方法进行了分析,包括焊接残余应力的消除、组织结构的调整等方面的内容。
最后对钢制压力容器的焊接工艺及焊后热处理方法进行了综合分析,总结出了钢制压力容器在焊接过程中需要注意的问题和提出了相应的解决方法,为提高钢制压力容器的焊接质量提供了参考。
通过本文的研究可以更好地了解钢制压力容器的焊接工艺和焊后热处理方法,为实际工程应用提供重要的指导。
【关键词】钢制压力容器、焊接工艺、焊后热处理、分析、综合、方法、压力容器、焊接、钢制、热处理、工艺、结论、引言。
1. 引言1.1 钢制压力容器焊接工艺及焊后热处理方法分析钢制压力容器在工业领域中起着至关重要的作用,它承载着各种液体或气体的压力,因此其质量和安全性至关重要。
而钢制压力容器的焊接工艺及焊后热处理方法对其性能和寿命有着直接的影响。
钢制压力容器的焊接工艺分析是确保容器质量的重要一环。
在焊接过程中,应根据不同材料和厚度选择合适的焊接方法,控制好焊接参数,确保焊缝质量。
常见的焊接方法包括气体保护焊、焊丝焊接等,每种方法都有其适用的情况和注意事项。
焊后热处理方法也是影响钢制压力容器性能的重要因素。
热处理可以消除焊接过程中产生的残余应力,改善焊缝组织,提高容器的强度和韧性。
常见的热处理方法包括回火、正火等,需要根据具体情况选择合适的方法。
2. 正文2.1 钢制压力容器焊接工艺分析钢制压力容器是工业生产中常见的设备之一,其质量和安全性直接关系到生产工艺和人员生命财产安全。
钢制压力容器的焊接工艺至关重要。
钢制压力容器的焊接工艺主要包括选择合适的焊接方法、焊接电流、焊接电压、焊接速度等。
一般来说,常用的焊接方法包括氩弧焊、埋弧焊、气保护焊等,其中氩弧焊在焊接过程中能够提供良好的焊缝形态和焊接质量,广泛应用于钢制压力容器的焊接中。
压力容器中焊接残余应力的消除问题分析
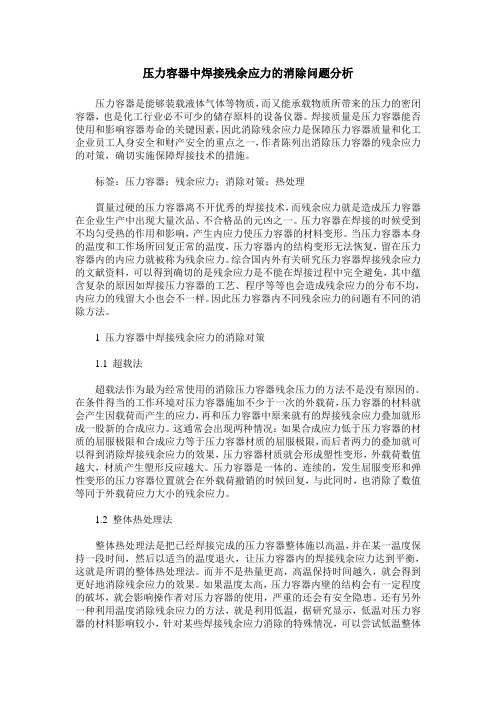
压力容器中焊接残余应力的消除问题分析压力容器是能够装载液体气体等物质,而又能承载物质所带来的压力的密闭容器,也是化工行业必不可少的储存原料的设备仪器。
焊接质量是压力容器能否使用和影响容器寿命的关键因素,因此消除残余应力是保障压力容器质量和化工企业员工人身安全和财产安全的重点之一,作者陈列出消除压力容器的残余应力的对策,确切实施保障焊接技术的措施。
标签:压力容器;残余应力;消除对策;热处理質量过硬的压力容器离不开优秀的焊接技术,而残余应力就是造成压力容器在企业生产中出现大量次品、不合格品的元凶之一。
压力容器在焊接的时候受到不均匀受热的作用和影响,产生内应力使压力容器的材料变形。
当压力容器本身的温度和工作场所回复正常的温度,压力容器内的结构变形无法恢复,留在压力容器内的内应力就被称为残余应力。
综合国内外有关研究压力容器焊接残余应力的文献资料,可以得到确切的是残余应力是不能在焊接过程中完全避免,其中蕴含复杂的原因如焊接压力容器的工艺、程序等等也会造成残余应力的分布不均,内应力的残留大小也会不一样。
因此压力容器内不同残余应力的问题有不同的消除方法。
1 压力容器中焊接残余应力的消除对策1.1 超载法超载法作为最为经常使用的消除压力容器残余压力的方法不是没有原因的。
在条件得当的工作环境对压力容器施加不少于一次的外载荷,压力容器的材料就会产生因载荷而产生的应力,再和压力容器中原来就有的焊接残余应力叠加就形成一股新的合成应力。
这通常会出现两种情况:如果合成应力低于压力容器的材质的屈服极限和合成应力等于压力容器材质的屈服极限,而后者两力的叠加就可以得到消除焊接残余应力的效果,压力容器材质就会形成塑性变形,外载荷数值越大,材质产生塑形反应越大。
压力容器是一体的、连续的,发生屈服变形和弹性变形的压力容器位置就会在外载荷撤销的时候回复,与此同时,也消除了数值等同于外载荷应力大小的残余应力。
1.2 整体热处理法整体热处理法是把已经焊接完成的压力容器整体施以高温,并在某一温度保持一段时间,然后以适当的温度退火,让压力容器内的焊接残余应力达到平衡,这就是所谓的整体热处理法。
钢制压力容器焊接与热处理
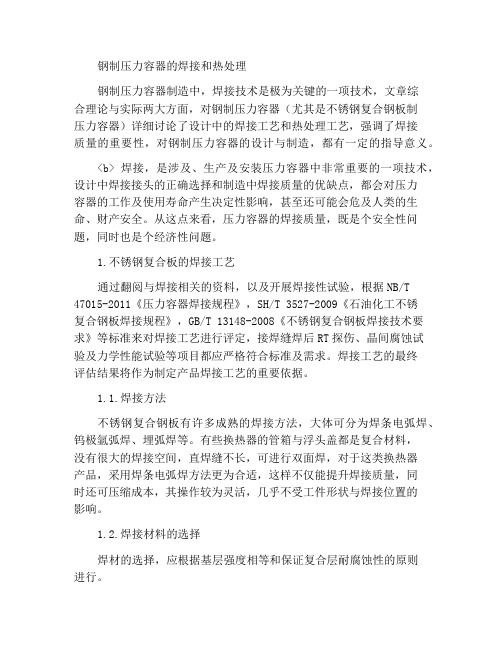
钢制压力容器的焊接和热处理钢制压力容器制造中,焊接技术是极为关键的一项技术,文章综合理论与实际两大方面,对钢制压力容器(尤其是不锈钢复合钢板制压力容器)详细讨论了设计中的焊接工艺和热处理工艺,强调了焊接质量的重要性,对钢制压力容器的设计与制造,都有一定的指导意义。
<b> 焊接,是涉及、生产及安装压力容器中非常重要的一项技术,设计中焊接接头的正确选择和制造中焊接质量的优缺点,都会对压力容器的工作及使用寿命产生决定性影响,甚至还可能会危及人类的生命、财产安全。
从这点来看,压力容器的焊接质量,既是个安全性问题,同时也是个经济性问题。
1.不锈钢复合板的焊接工艺通过翻阅与焊接相关的资料,以及开展焊接性试验,根据NB/T 47015-2011《压力容器焊接规程》,SH/T 3527-2009《石油化工不锈复合钢板焊接规程》,GB/T 13148-2008《不锈钢复合钢板焊接技术要求》等标准来对焊接工艺进行评定,接焊缝焊后RT探伤、晶间腐蚀试验及力学性能试验等项目都应严格符合标准及需求。
焊接工艺的最终评估结果将作为制定产品焊接工艺的重要依据。
1.1.焊接方法不锈钢复合钢板有许多成熟的焊接方法,大体可分为焊条电弧焊、钨极氩弧焊、埋弧焊等。
有些换热器的管箱与浮头盖都是复合材料,没有很大的焊接空间,直焊缝不长,可进行双面焊,对于这类换热器产品,采用焊条电弧焊方法更为合适,这样不仅能提升焊接质量,同时还可压缩成本,其操作较为灵活,几乎不受工件形状与焊接位置的影响。
1.2.焊接材料的选择焊材的选择,应根据基层强度相等和保证复合层耐腐蚀性的原则进行。
1.3.焊接设备和环境通常可选择直流焊机,基层、复层及过渡层这3种焊缝均可选择焊条电弧焊。
所采用的钢丝刷、扁铲等工具都,都应是不锈钢材料。
焊接应在0 ℃以上的环境下进行,同时,现场应采取必要的防风措施。
1.4.焊接沟槽和接头装配1.4.1.沟槽选用沟槽形式时,应充分考虑焊接渡层的特点,焊接顺序应依次为焊基层、渡层到复层,,要尽可能不对复层进行焊接或进行少量焊接,同时还应避免复层焊缝被多次受热,从而逐步增强复层焊缝的耐腐蚀性能,该沟槽形式还能有效降低设备内部的铲磨工作量。
压力容器焊缝返修及焊后热处理

41中国设备工程Engineer ing hina C P l ant中国设备工程 2019.02 (下)某装置在进行全面检验过程中,一级反应器经TOFD 检测发现其最下方两个筒体对接焊缝存在超标埋藏缺陷,缺陷长度160mm,缺陷深度为20~30mm,TOFD 图谱如图1所示,根据相关标准需要对此缺陷进行消除,设备焊缝局部返修,坡口尺寸受缺陷大小及现场操作条件影响较大,以下对现场开槽的坡口的结构尺寸进行应力分析,得到开槽后坡口周边的应力分布,为焊缝焊接及焊后热处理提供参考。
图1 TOFD 图谱 图2 开槽成型焊缝内部埋藏缺陷的消除过程大致分为挖除缺陷、局部焊接及热处理、检测确认三个步骤,分三个部分对返修过程进行分析研究。
1 应力分析(1)建立数值模型:根据TOFD 图谱确定缺陷位置,将缺陷完全刨除,并将刨槽打磨成型如图2所示。
设备主要结构参数如表1所示,由于设备结构尺寸较大,坡口尺寸与筒体尺寸相差较大,为方便计算含坡口的圆柱面简化为平面,且数值模型具有对称性,数值模型如图3所示,其中模型高750mm,长为450mm,坡口形状为等腰梯形,长度分比为60mm、20.9mm,角度为60°。
(2)网格划分及应力分析:将建立好的数值模型导入应力分析软件,首先进行划分网格,由于坡口尺寸与筒体尺寸相差较大,因此需要对坡口周边进行网格加密,节点数为360184,网格数量为156584,对网格进行无关性验证,结果表明网格划分数量不影响应力计算结果,网格划分如图4所示,设定对称边界条件,压力边界条件,顶部筒体重力影响,底面设置为固定边界条件,设置好边界条件并进行计算。
计算结果可得应力分布及变形量大小如图5所示,由图可知,坡口周围存在应力集中,坡口棱角分明,应力集中越大,因此在现场返修过程中应圆滑过渡,从而减小应力集中的情况,减小棱角处应力的大小,为减少焊接的难度,从图5(b)中可以看出,坡口上方筒体形变量大于同水平位置形变量,随着高度的下降形变量变小,坡口下方形变量小于同水平位置形变量,这是由于坡口的存在造成筒体的不连续,从而坡口上斜面形变量较大,而坡口下斜面由于上方重力的不连续性,形变量较小,此种规律与坡口深度有关,因此在焊缝局部返修过程中应避免坡口深度小于1/2筒体厚度,从而较小焊接的难度。
压力容器的焊后热处理

压力容器的焊后热处理摘要:介绍化工压力容器焊后需要热处理的原因以及热处理的方法、使用条件及过程特征。
前言压力容器是石油、化工等行业生产应用十分广泛的重要设备之一。
随着各个领域的技术进步,压力容器设备朝着大型化方向发展,所使用的材料也更加高强化和壁厚化,焊接后的热处理技术对于制造出高质量、可靠的设备起着重要作用。
压力容器进行焊后热处理的原因所谓焊后热处理,广义地讲就是在工件焊完之后对焊接区域或焊接构件进行热处理,其内容包括消除应力退火、完全退火、固熔、正火、正火加回火、回火、低温消除应力、调质等。
狭义地讲焊后热处理仅指消除应力退火,即为了改善焊接区的性能和消除焊接残余应力,减少脆性破坏和疲劳破坏等有害影响,从而对焊接区及有关部位在金属相变温度点以下均匀而又充分地加热,并保持一定的时间,然后又均匀冷却的过程。
压力容器焊接时,当母材相邻区域产生温差大于100℃的急剧温度梯度时,在铁素体钢或相当的其他材料中引起不均匀的塑性应变,而在随后的冷却过程中,将产生一个峰值应力达到屈服点的残余应力。
当残余应力与焊缝中的氢相结合时,将促使热影响区硬化,由此而导致应力腐蚀裂纹的产生和发展。
焊制的压力容器,焊接区存在着较大的残余应力,而残余应力的不利影响,在一定的条件下表现出来,主要在以下场合中出现:a 容器高、低温使用;b 耐压试验时;c 由焊接引起的母材淬硬。
残余在焊缝中的应力与介质的腐蚀作用相结合时,将引起裂纹状腐蚀,焊接残余应力即是产生应力腐蚀裂纹的重要因素。
焊后热处理的方法为了提高断裂韧性、降低残余应力水平,以增加抗脆断的能力,软化材料组织消除应力腐蚀开裂的可能性,对压力容器等焊接结构要进行焊后热处理,其主要目的:a 释放焊接过程中参与的应力;b 修整焊接处的形状、减少应力集中系数;c 改善母材的金属塑性,降低热影响区硬度;d 提高断裂韧性;e 改善疲劳强度;f 恢复或提高机械成型中降低的屈服强度;g 提高抗应力腐蚀的能力。
- 1、下载文档前请自行甄别文档内容的完整性,平台不提供额外的编辑、内容补充、找答案等附加服务。
- 2、"仅部分预览"的文档,不可在线预览部分如存在完整性等问题,可反馈申请退款(可完整预览的文档不适用该条件!)。
- 3、如文档侵犯您的权益,请联系客服反馈,我们会尽快为您处理(人工客服工作时间:9:00-18:30)。
压力容器焊后消除应力热处理的目 的是为了消除焊件的残余焊接应力, 以保证焊件的使用性能及稳定尺寸, 保证焊件的安全使用。因此,决定焊 后消除应力热处理厚度的规范参数是 焊缝厚度而不完全是A、B类焊接接头 处钢材厚度。显而易见JB/T4709的规 定较之GB150的规定更为具体,更为合 理且符合实际。
4.怎样确定压力容器焊后消除应力热 处理最短保温时间? 笔者认为:压力容器焊后消除应力热 处理最短保温时间应按照JB/T4709第 8章确定。 值得注意的是GB150 10.4款将A、B类 焊接接头处钢材厚度δs作为50是按照钢材厚度δs确定焊后热 处理最短保温时间的。而JB/T4709则 将压力容器焊后消除应力热处理厚度 δPWHT作为确定压力容器焊后消除应 力热处理规范参数的依据,也就是将 δPWHT作为确定焊后消除应力热处理 最短保温时间的厚度。
2.哪些压力容器及主要受压元件需焊 后消除应力热处理? 哪些压力容器及主要受压元件需焊 后消除应力热处理?笔者认为:应按 照GB150 10.4.1款和GB151 6.4、6.8 款(指拼接管板、管箱和浮头盖)判 定。凡符合GB150 10.4.1款和GB151 6.4、6.8款规定的压力容器及主要受 压元件均应进行焊后消除应力热处理。
关于钢制压力容器焊后消除
应力热处理有关问题的讨论
摘要:本文对钢制压力容器焊后是否 需要消除应力热处理,焊后消除应力 热处理方法的选择,热处理最短保温 时间的确定进行了分析,并针对安全 技术规范和标准的相关内容进行了讨 论
关键詞: 压力容器 焊后消除应力热 处理 相关安全技术 1.前言 有关钢制压力容器焊后消除应力热处理, 至今国内尚无专业标准。目前对钢制压力 容器焊后消除应力热处理要求的有关内容 仅分散在《压力容器安全技术监察规程》、 GB150“钢制压力容器”、 GB151“管壳式换 热器”、 JB/T4709“钢制压力容器焊接规程” 以及JB/T10175-2000“热处理质量控制要 求”、
3.采用何种消除应力热处理方法? 需进行焊后消除应力热处理的压力容 器,应按照《容规》第73条、第74条 规定选择热处理方法,进行焊后消除 应力热处理。 按照压力容器有关安全技术规范和标 准,压力容器焊后消除应力热处理方 法可分为以下四种:
⑴炉内整体焊后消除应力热处理; ⑵炉内分段焊后消除应力热处理; ⑶焊后局部消除应力热处理; ⑷使用现场整体消除应力热处理。
2.热处理准备
3.热处理过程
4.热处理报告 5、热处理分包质量控制
热处理温度-时间记录曲线
热处理报告 ⑴分包方评价⑵分包协议 ⑶分包项目质量控制
具体要求和内容见“中国化工装备协会” 编写的“压力容器制造单位质量保证人员 培训考核教材(2008版)”第十四章“热 处理质量控制系统”。 其中在“热处理准备”这个控制环节中, 设臵了热处理设备和记录、控温仪表、热 电偶数量和布臵两个控制点。在相应的程 序文件中设有“热处理炉有效加热区测定 方法”;在相应的工艺文件和质量记录表 卡中设有“热处理炉有效加热区测定报告 和检验合格证”
GB/T9452-2003“热处理炉有效加热区 测定方法”等安全技术规范和标准之 中。因而在使用过程中出现了理解上 的不一致和偏差。为了满足钢制压力 容器焊后消除应力热处理的要求,保 证钢制压力容器的安全质量,本文将 重点讨论钢制压力容器焊后消除应力 热处理中常见的一些问题,并就此提 出笔者的认识和看法。
上述质量控制要求保证了压力容器焊后消 除应力热处理是在热处理炉有效加热区进 行了测定并出具检验合格证之后才允许进 行。带有热处理炉有效加热区示意图的检 验合格证应悬挂在热处理炉明显位臵。 4.2热处理炉有效加热区的测定 目前国内关于热处理质量控制要求的 标准有两个:一个是JB/T10175-2000“热处 理质量控制要求”,另一个是GB/T9452 - 2003“热处理炉有效加热区测定方法”。
如图:有一台钢制压力容器,壳体 材料为16MnR,厚度36mm,接管材料为 16MnⅢ,厚度65mm,对于此结构,焊 后消除应力热处理需最短保温时间t计 算如下:
接管 壳体
⑴按照JB/T4709的8.2.2.3款修改前条 文计算 δPWHT=65mm t=(2+1/4×(65-50)/25)h= 2.15h=129min ⑵按照JB/T4709的8.2.2.3款更正后条 文计算 δPWHT=36mm t=36/25h=1.44h=86.4min 从以上两例可以看出,两者之间相差
由于炉内整体消除应力热处理的效 果好,因此在条件具备的情况下,应 优先选用炉内整体热处理方法。
对于球形储罐和大型压力容器可採 取使用现场整体消除应力热处理方法。 由于焊后局部消除应力热处理的效 果较炉内整体消除应力热处理差,因 而《容规》和标准对局部消除应力热 处理方法的应用作出了较为明确的限 制。目前局部消除应力热处理只限应 用于B、C、D类焊接接头以及球形封头 与园筒连接的A类焊接接头。
但是JB/T4709-2000标准的8.2.2.3 款有印刷错误。其间将“焊缝”两字 漏掉。应将原条文“接管、人孔与壳 体组焊时,在接管颈部厚度、壳体厚 度、封头厚度、补强板厚度和连接角 焊缝厚度中取较大者”的内容,更正 为:“接管、人孔与壳体组焊时,在 接管颈部焊缝厚度、壳体焊缝厚度、 封头焊缝厚度、补强板焊缝厚度和连 接角焊缝厚度中取较大者”。
4.压力容器焊后消除应力热处理质量 控制 4.1压力容器焊后消除应力热处理质量 控制系统的控制环节和控制点 压力容器焊后消除应力热处理质量控 制系统共设5个控制环节9个控制点, 见表1。
表1
控制环节
1.热处理工艺编制
控制点
⑴热处理工艺编制⑵热处 理工艺修改
⑴热处理设备和记录、控温仪 表;⑵热电偶数量和布臵