船体合拢装配作业指导书
船体分段合拢施工要领
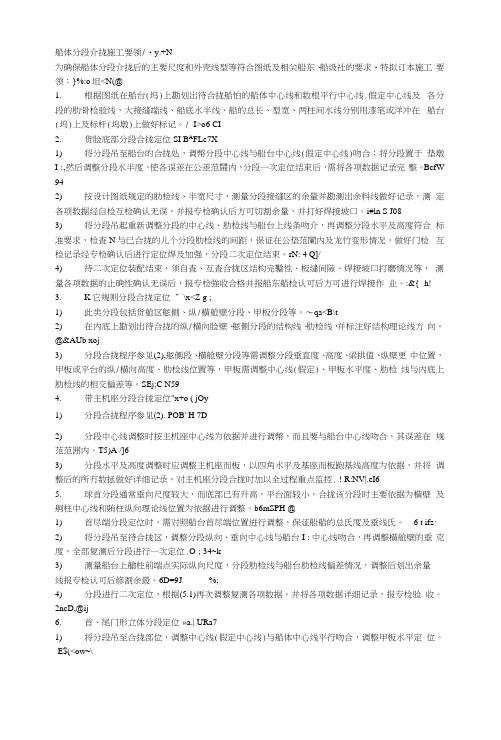
船体分段介拢施工要领/・y.+N_为确保船体分段介拢后的主要尺度和外壳线型等符合图纸及相关船东、船级社的要求・特拟订本施工要领:}%:o坦<N(@1.根据图纸在船台(坞)上勘划出待合拢船怕的船体中心线和数根平行中心线.假定中心线及各分段的肋骨检验线,大接缝端线、船底水半线、船的总长、型宽、两柱间水线分别用漆笔或洋冲在船台(坞)上及标杆(坞墩)上做好标记。
/ I>o6 CI2.货脸底部分段合拢定位SI B A FLe7X1)将分段吊至船台的合拢处,调幣分段中心线与船台中心线(假定中心线)吻合:将分段置于垫墩I:,然后调整分段水半度,使各误差在公差范鬧内,分段一次定位结束后,需将各项数据记录完整。
BcfW 942)按设计图纸规定的肋检线、半宽尺寸,测量分段接缝区的余量并勘测出余料线做好记录,测定各项数据经自检互检确认无误,并报专检确认后方可切割余量,并打好焊接坡口。
i#ln S J083)将分段吊起重新调整分段的中心线、肋检线与船台上线条吻介,再调整分段水平及高度符合标准要求,检査N与已合拢的儿个分段肋检线的间距,保证在公垫范闌内及龙竹变形情况,做好门检互检记录经专检确认后进行定位焊及加强,分段二次定位结束。
rN: 4 Q]/4)待二次定位装配结束,须自査、互査合拢区结构完鑿性、板缝间隙、焊接坡口打磨情况等,测量各项数据的止确性确认无误后,报专检強收合格并报船东船检认可后方可进行焊接作业。
:&{ -h! 3.K它规则分段合拢定位“ \x<Z g ;1)此类分段包括货舱区舷侧、纵/横舱壁分段、甲板分段等。
〜qa<B\t2)在内底上勘划出待合拢的纵/横向脸壁、舷侧分段的结构线、肋检线,并标注好结构理论线方向。
@&AUb xoj3)分段合拢程序参见(2),舷侧段、横舱壁分段等需调整分段垂直度、高度、梁拱值、纵壁更中位置,甲板或平台的纵/横向高度、肋检线位置等,甲板需调整中心线(假定)、甲板水平度、肋检线与内底上肋检线的相交偏差等。
船体大合拢作业指导书

船体大合拢作业指导书
1. 确定合拢作业的目标和要求:明确合拢作业的目的,包括船体大合拢的时间、质量和安全要求等。
2. 编制合拢作业计划:根据船体大合拢的要求,制定详细的作业计划,包括合
拢的顺序、方法和时间安排等。
3. 准备合拢作业所需的材料和设备:根据作业计划,准备好合拢所需的材料和
设备,确保其数量、质量和完好性。
4. 安排合拢作业人员:根据作业计划,合理安排合拢作业的人员,包括技术人员、操作人员和监督人员等,确保作业的顺利进行。
5. 进行合拢作业前的准备工作:在进行合拢作业前,必须进行一系列的准备工作,包括清理作业区域、检查设备和材料的完好性、组织人员进行安全培训等。
6. 开始合拢作业:按照作业计划和要求,开始进行船体大合拢作业,确保作业
过程中的安全和质量。
7. 监督和检查合拢作业:在合拢作业过程中,进行定期的监督和检查,确保作
业的质量和安全。
8. 完成合拢作业后的清理和整理:在合拢作业完成后,进行作业区域的清理和
整理,确保作业区域的安全和整洁。
9. 进行合拢作业的验收:对合拢作业进行验收,检查作业的质量和合格性,确
保作业的达到要求。
10. 编制合拢作业的总结报告:在合拢作业完成后,编制作业的总结报告,包
括作业的过程、结果和存在的问题等,为以后的类似作业提供参考。
以上是船体大合拢作业的指导书,希翼对您有所匡助。
船舶作业指导书

1 概述本工艺根据《钢质海船入级规范》(CCS-2009版)、《材料与焊接规范》(CCS-2009版)、中国船舶工业集团公司第七O八研究所38000吨级自航半潜船以及详细设计“船体焊接规格表”(见附件1)和生产设计的工艺要领(见附件2)结合本企业具体情况而编制。
2 目的本工艺对焊接过程进行有效的控制,确保该船的焊接质量能满足上述规范和技术文件规定的质量要求。
3 工艺要求:3.1 焊工资格审查:焊工必须经培训、考核合格后持证上岗。
3.2 焊接设备:现场采用的焊接设备应能保证焊接参数的稳定性、调节灵活、安全可靠。
焊工对所使用的焊接设备应进行认真检查、确保焊接设备的完好。
3.3 焊接方法:3.3.1 本船采用手工电弧焊、CO2气体保护焊、埋弧自动焊等三种焊接方法。
其中,内底板、甲板板、平台板、纵横舱壁、外板平直部分等板材的拼板对接采用埋弧自动焊,主甲板内底板、小分段合拢组装焊采用CO2衬垫焊打底埋弧自动焊盖面;外板及构架对接,构架与板平角,立角,构件平角,构件合拢垂直角,中、大组立板材对接,总组立中合拢对接,总组立中合拢旁板,纵、横舱壁的垂直对接采用CO2气体保护焊(CO2气体纯度不低于99.5%);全位臵角焊,部分补焊采用手工电弧焊。
3.3.1.1 主体结构焊接①甲板部分为一般结构钢,甲板板平直拼接缝采用焊接方法为埋弧自动焊:焊丝JW-2、焊剂JF-A。
与纵骨、纵桁、纵壁、舷顶列板等角接焊缝采用CO2气体保护焊:TWE-711、衬垫采用JN或HS01系列。
CO2气体纯度不低于99.5%。
可以少部分点焊或补焊采用手工电弧焊:焊条NJ507或NJ502。
②除主甲板以外全部结构为高强度钢,所以采用的埋弧自动焊为适用高强度的:焊丝JW-1、焊剂JF-B。
CO2气体保护焊:TWE-711、衬垫采用JN或HS01系列。
CO2气体纯度不低于99.5%。
可以少部分点焊或补焊采用手工电弧焊:焊条NJ507。
3.3.1.2 上建结构拼板采用埋弧自动焊。
船体装配工艺指导书
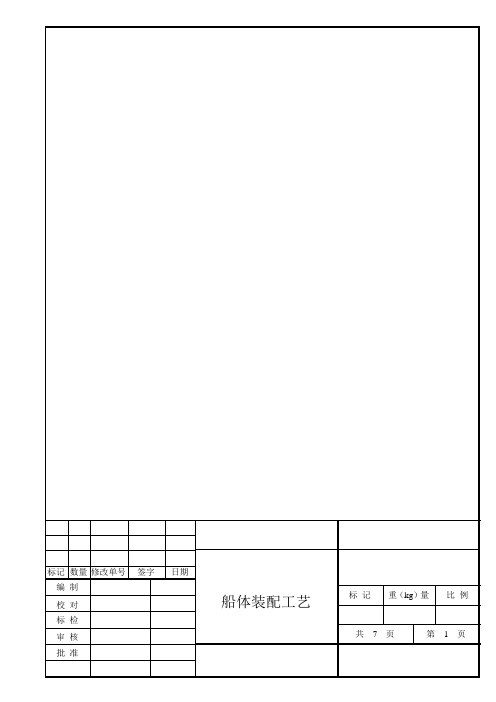
1.6.报检合格后转下道工序。
2.肋骨框架装焊
2.1.肋骨框架由横梁、肋骨、肋板和肘板等组合而成的环形框架,通常分普通肋骨框架和强肋骨框架。
2.2.肋骨框架装配前应在平台上画出左右对称的全宽肋骨型线图,其型值由放样提供。平台上的型线作为装焊接时对线定位和检验的依据。
4.校正锤击时,榔头要平击,不能在产品上留下明显的榔头印迹。
注:本通用工艺若与特定产品的施工工艺矛盾,以特定产品的施工工艺为准。
10.分段建造完工后,必须用洋冲打上检验线(中心线,水平检验线,定位肋骨线)。
六、临时性加强
1.结构临时性加强应能有效地防止焊接变形,防止分段、部件在吊运、翻身、搁置等情况下的变形和损坏,且能作为船台(或总段)装配时保证型线的有效措施。
2.临时性加强材料尽量利用废旧料和边余料。
3.组件和部件的临时性加强
2.4.1.胎架要有足够的强度和刚度,以支撑分段的重量,保证装配线型。
2.4.2.根据分段生产批量、场地面积、劳动力分配、分段建造周期、起重设备范围等因素选择适当的胎架形式和数量,并应考虑分段的船体线型与形式决定合理的胎架基面切取方法,以满足生产计划的要求,改善施工条件,扩大自动、半自动焊接的应用范围。
有线型的胎架制作前,应准备好所要建造分段的内(外)卡样板,样板在搬运和使用中必须注意避免撞击,样板应平放在平坦的地方,更不要将样板任意丢抛,要尽量保证精度不使变形,用后应妥善保存好。准备好划线前所需的一切工具,包括:墨盒,卷尺,水平管,水平尺等。
2.2.胎架基准面的切取与选择
2.2.1.胎架基准面的选择主要根据船体或型线的变化及施工条件的改善决定。整个胎架的最低高度一般取1.30米,最小不得低于1.20米。
船体分段合拢施工要领

船体分段合拢施工要领/ - y.+N`_为确保船体分段合拢后的主要尺度和外壳线型等符合图纸及相关船东、船级社的要求,特拟订本施工要领:}%;o#!<N(@1. 根据图纸在船台(坞)上勘划出待合拢船舶的船体中心线和数根平行中心线,假定中心线及各分段的肋骨检验线,大接缝端线、船底水平线、船的总长、型宽、两柱间水线分别用漆笔或洋冲在船台(坞)上及标杆(坞墩)上做好标记。
/ I>o6 CI2. 货舱底部分段合拢定位S1 B^FLe7X1) 将分段吊至船台的合拢处,调整分段中心线与船台中心线(假定中心线)吻合;将分段置于垫墩上,然后调整分段水平度,使各误差在公差范围内,分段一次定位结束后,需将各项数据记录完整。
BcfW 942) 按设计图纸规定的肋检线、半宽尺寸,测量分段接缝区的余量并勘测出余料线做好记录,测定各项数据经自检互检确认无误,并报专检确认后方可切割余量,并打好焊接坡口。
i#ln S J08 3) 将分段吊起重新调整分段的中心线、肋检线与船台上线条吻合,再调整分段水平及高度符合标准要求,检查其与已合拢的几个分段肋检线的间距,保证在公差范围内及龙骨变形情况,做好自检互检记录经专检确认后进行定位焊及加强,分段二次定位结束。
~rN: 4 Q]/4) 待二次定位装配结束,须自查、互查合拢区结构完整性、板缝间隙、焊接坡口打磨情况等,测量各项数据的正确性确认无误后,报专检验收合格并报船东船检认可后方可进行焊接作业。
:&{ -h!3. 其它规则分段合拢定位" \x<Z g ;1) 此类分段包括货舱区舷侧、纵/横舱壁分段、甲板分段等。
~ q.a<B`,t2) 在内底上勘划出待合拢的纵/横向舱壁、舷侧分段的结构线、肋检线,并标注好结构理论线方向。
@&AUb xoj3) 分段合拢程序参见(2),舷侧段、横舱壁分段等需调整分段垂直度、高度、梁拱值、纵壁距中位置,甲板或平台的纵/横向高度、肋检线位置等,甲板需调整中心线(假定)、甲板水平度、肋检线与内底上肋检线的相交偏差等。
【推荐下载】船体装配指导书word版本 (9页)
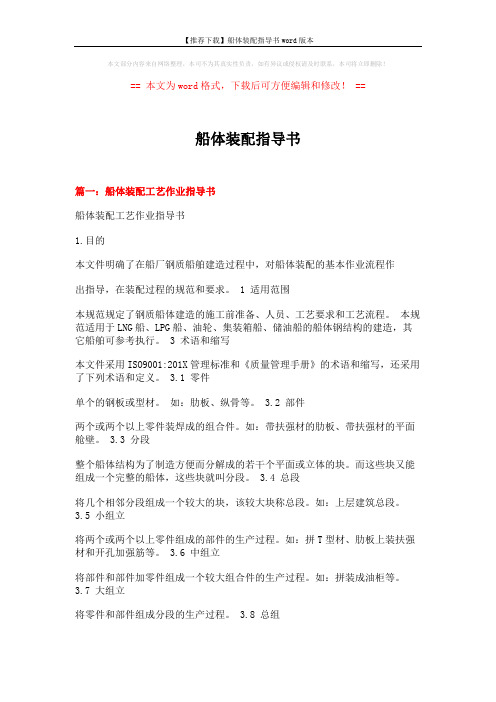
本文部分内容来自网络整理,本司不为其真实性负责,如有异议或侵权请及时联系,本司将立即删除!== 本文为word格式,下载后可方便编辑和修改! ==船体装配指导书篇一:船体装配工艺作业指导书船体装配工艺作业指导书1.目的本文件明确了在船厂钢质船舶建造过程中,对船体装配的基本作业流程作出指导,在装配过程的规范和要求。
1 适用范围本规范规定了钢质船体建造的施工前准备、人员、工艺要求和工艺流程。
本规范适用于LNG船、LPG船、油轮、集装箱船、储油船的船体钢结构的建造,其它船舶可参考执行。
3 术语和缩写本文件采用ISO9001:201X管理标准和《质量管理手册》的术语和缩写,还采用了下列术语和定义。
3.1 零件单个的钢板或型材。
如:肋板、纵骨等。
3.2 部件两个或两个以上零件装焊成的组合件。
如:带扶强材的肋板、带扶强材的平面舱壁。
3.3 分段整个船体结构为了制造方便而分解成的若干个平面或立体的块。
而这些块又能组成一个完整的船体,这些块就叫分段。
3.4 总段将几个相邻分段组成一个较大的块,该较大块称总段。
如:上层建筑总段。
3.5 小组立将两个或两个以上零件组成的部件的生产过程。
如:拼T型材、肋板上装扶强材和开孔加强筋等。
3.6 中组立将部件和部件加零件组成一个较大组合件的生产过程。
如:拼装成油柜等。
3.7 大组立将零件和部件组成分段的生产过程。
3.8 总组将几个相邻分段组成一个总段的生产过程。
3.9 搭载在船坞内将分段和总段组成完整一艘船体的生产过程。
4.职责与权限5 工作程序 5.1 施工前准备 5.1.1图纸资料:施工前有关图纸,零件明细表,焊接工艺和完工测量表等。
5.1.2材料:施工前查对零件的材质牌号,钢板厚度,型材尺寸等应与图纸相符合。
5.1.3工具:钢卷尺、线锤、水平橡皮管、油泵、花兰螺丝、铁楔、各种“马”、激光经纬仪、锤、氧乙炔割炬、电焊龙头、电焊面罩、角尺、角度尺。
5.2 人员装配工上岗前应进行专业知识和安全知识的培训。
主船体大合拢建造作业指导书

主船体大合拢建造作业指导书1.本指导书适用于各类钢质焊接船舶2.船台准备:2.1主船体定位分段上船台合拢后填写工程进度证明书。
2.2了解《墩木图》、《熳缝分类与拍片张数》等图纸资料供图情况。
2.3检查施工所需行车、焊接设备及风、水、电、气保障情况2.4了解船台中心线划线草图及大合拢测量标杆的提供情况2.5清理船台,铺设中心线板,划船台中心线、半宽线、肋骨检验线和肋位站号并打上洋冲作标记用油漆标明,在船台一侧竖立大合拢测量标杆2.6督促保障部按《墩木图》摆设墩木,及各分(总)段合拢大、小车就位2.7督促保障部准备搭设主船体大合拢施工临时舱室上下梯、主甲板周边临时安全护栏、人孔盖安全护盖板,安装船台接地线,拉施工安全照明用电3.主船体分(总)段准备:3.1检查各分(总)段的船台定位线和对合线3.1.1船体分段:分段中心线、分段基准肋骨线、分段水平检验线、内底板上舱壁位置线3.1.2舷侧分段:甲板边线、分段基准肋骨线(与船体同号)、分段水平检验线、舱壁位置线3.1.3甲板分段:分段中心线、分段基准肋骨线(与舷侧同号)、舱壁位置线3.1.4舱壁分段:分段中心线、分段水平检验线3.1.5分段对合线:对接的两个分段对合线要统一3.2 船台各分(总)段的临时支撑的设置(假舱壁) 、安装吊码应符合工艺要求3.3 各分(总)段局部变形或缺陷要矫正、修补完工3.4各分(总)段装焊基本完工,分段内焊接经船东代表和船级社验船师认可,分段合拢口预留500mm缓焊区,待分段合拢后再施焊,以便合拢时微调3.5各分(总)段应进行完工测量且经船东代表和船级社验船师认可,并以表格形式记录备查,同时反馈给技术部、检验部,供船台大合拢时作参考3.6各分(总)段按照本船《油漆明细表》要求进行涂装完工3.7 各分(总)段建造要符合《中国造船质量标准》要求4.人员和组织准备5.主船体装焊、报验程序:(以684型产品为例)5.1一般选择机舱双层底分段或靠近机舱平行舯体处双层底分段作为基准分段,向前、后、左、右按规划好的合拢顺序进行合拢5.2基准分段上船台定位→自检、互检→验船方代表检验→与基准分段相邻的底部分段吊装→自检、互检→验船方代表检验→舱壁分段吊装→舷侧分段吊装→自检、互检→验船方代表检验→甲板分段吊装→自检、互检→验船方代表检验→艏、艉总段吊装→全船装配总体测量→自检、互检→验船方代表检验→全船大接头内部板缝扣槽、打磨→自检、互检→验船方代表检验→大接头内部板缝焊接→大接头外板板缝扣槽、打磨→自检、互检→验船方代表检验→外板缝焊接、批磨→全船焊接自检、互检→验船方代表检验→全船焊后总体测量→自检、互检→验船方代表检验→全船焊后火工矫正→自检、互检→验船方代表检验→全船板缝拍片。
NCS船体大合拢作业指导书

大合拢作业指导书1、目的本指导书阐明了公司船舶建造大合拢作业从坞内水平船台合拢从基线勘划、船台设置、分段定位,分段合拢直至船舶下水全过程各有关工序的控制要求,以确保船舶建造符合规范及精度要求,满足用户的期望。
2、适用范围本指导书适用于公司船舶建造大合拢作业全过程。
3、职责3.1 设计所提供船舶建造过程中必需的图纸及原则工艺,解决船舶合拢过程中技术图纸问题,必要时提供处理措施;3.2 工程管理科负责提供分段精度测量数据;3.3 大合拢工区参与对分段的验收,对大合拢各个施工过程进行控制,,并配合完成船东及船检必检项目的报验;3.4 船舶工程部负责编制关键分段的总组或定位工艺,解决现场工艺问题,协调各工序的施工,参予合拢精度管理;3.5 检验科负责对分段总组及合拢的质量进行跟踪检验;3.6 安全管理科负责对船体分段合拢全过程施行安全管理及监控;4、实施根据船舶在大合拢过程中的关键工序识别,主要从以下六个方面进行控制:a. 龙骨变形量控制;b. 分段总组及无余量切割精度控制;c. 分段二次定位的控制;d. 舱口主要尺度控制;e. 舱口围定位精度控制;f. ABXX分段定位精度控制。
4.1 龙骨变形量控制4.1.1 设计所根据船体结构形式和分段划分及大于船舶总重量一定系数(船体所有结构、设备、设施和施工中所需的所有辅助性设备、设施在内的重量)的估算吨位为依据,绘制船台布墩图。
船台布墩应考虑结构型式,布墩应避开舱室放泄塞、外板标记等位置,对于机舱区域、龙骨和舷侧区域、货舱近艏下水前需压载区域、艏部瘦狭区域均要加密布墩。
4.1.2 大合拢工区须按下列要求进行控制:a. 熟悉船体底部结构图和船台布墩图及有关施工工艺要领,在船台基面勘划出船台中心线和假定中心线、水底段大接头位置线和区域基准分段肋检线、所有布墩位置线,在船体外形轮廓线的外侧艏、舯、尾两侧适当位置设置永久性标杆(可以借助于坞墙),将所确定的基线高度位置线用激光经纬仪勘划其上,并反复校核无误,并根据船底板厚情况,将主要几种板厚差以基线向下量取勘划,并用洋冲或漆线记号,且附文字说明;b. 按布墩图将所有水底相对平直部位的墩子一次性设置完毕。
- 1、下载文档前请自行甄别文档内容的完整性,平台不提供额外的编辑、内容补充、找答案等附加服务。
- 2、"仅部分预览"的文档,不可在线预览部分如存在完整性等问题,可反馈申请退款(可完整预览的文档不适用该条件!)。
- 3、如文档侵犯您的权益,请联系客服反馈,我们会尽快为您处理(人工客服工作时间:9:00-18:30)。
船体合拢装配施工作业指导书
一、本工艺适用范围
本工艺仅针对船台合拢阶段提出的具体要求和规定,以确保船体建造质量。
二、主要内容
船体分段从下料至分段建造完工进行船台合拢,由于分段精度、施工过程或转运过程中产生变形,错位等一些问题,而需要对分段结构进行校正,挖补,开调等修补工作,为加强合拢阶段质量过程控制,规范施工作业行为,现作如下工艺要求:
1、分段型材结构断缝及挖换工艺:
由于分段内部结构相互穿插,分段合拢口型材对接存在偏差等,为方便分段合拢定位,需要对构件增加断缝处理,还有些构件变形严重需进行局部挖换,原则上是按图纸上挑开原始板缝施工,考虑到构件的原始接缝较长,受舱室空间狭小不利条件影响,不利于施工现场作业,根据型材分类进行增加断缝及挖换处理的工艺要求:
a)平直型材:
根据IACS和CSQS的标准,对型材构件增加断缝或挖换,长度最短不得小于300mm,但为了型材整体美观性,江苏金陵设计公司要求长度不得小于3×H(H为型材高度),相邻型材接缝应互相错开200以上。
b)曲度型材:
对于有线型的型材,增加断缝及挖换长度同平直型材尺寸,下料后开好坡口,将型材放在铁平台上加工线型,并划出所需加工型材的线型,并在线型上标
出所加工型材的起止位置,板缝位置、纵桁及平台安装位置,肋号等标记,现场装配时参照这些标记进行定位。
c)T型材:
T型构件挖换长度不得小于腹板的高度且要大于300,装配前T型构件需预
制妥当后方可装配,T型构件相对接时面板与腹板接头应错开150mm。
2、分段结构焊接接头的装配:
对于下边舱卷龙板,外板线型较大区域,结构较密集区域,经过精控检测后发现构件错位需开调,开调长度不得少于错位偏差值的50倍,并按如下表格规范要求施工:
a)角接接头偏差及装配要求:
b)对接接头偏差及装配要求:
3、分段主板工艺挖换:
对于分段主板需要挖换,需及时向相关部门反馈,由技术部门出挖换方案,经船东船检认可后方可施工,严禁私自动割刀挖换。
4、分段内部结构增加断缝工艺要求:
分段内部结构经开调挖换后,与之对接的部分加强,如月牙肘板,T型肘板等结构出现间隙超差,需增加断缝,原则上按300*300的工艺要求施工。