离心泵转子的强度和刚度计算.
离心泵转子的强度和刚度计算.

轴的强度与刚度计算1。
0输入数据1 设计流量Q1500(m3/h2 设计扬程H40(m3 设计转数n1450(r/min4 设计效率η0.855 介质温度T(℃6 介质粘度ν(m2/s7 介质密度ρ1000(kg/m3 8 介质饱和蒸汽压Pv(kgf/cm2 9 轴材料允许切应力τ55000000(N/m2Pa 10 轴材料的屈服极限σs 6.37E+08(N/m2Pa 11 轴材料的弯曲极限σb 8.34E+0812 轴材料的弯曲疲劳极限σ-13.55E+08(N/m2Pa13 轴材料的剪切疲劳极限τ-12.04E+08(N/m2Pa 14 轴材料的弹性模量E2100000kg/cm215 弯矩单独作用时的有效应力集中系数kσ1.6916 扭矩单独作用时的有效应力集中系数kτ1.6117 弯矩单独作用时的绝对尺寸影响系数εσ0.7318 扭矩单独作用时的绝对尺寸影响系数ετ0.7819 弯矩单独作用时材料对应力循环不对称性的敏感性系数ψσ0.120 扭矩单独作用时材料对应力循环不对称性的敏感性系数ψτ0.0521 轴表面质量系数β122 叶轮外径D20.4(m23 24 25 26 27 27叶轮出口宽度B20.1(m叶轮动不平衡余量Gc1.5(g叶轮重量Gy245(N轴重量Gz258(N联轴器重GL20(N插入轴的三维及二维图已确定轴段各尺寸) 3。
0计算作用在轴上的载荷3.1径向力 1)水力径向力设计流量时与隔舌夹角195°50%设计流量时与隔舌夹角135°因隔舌角为60°,故:Fsjx =Fsj*COS75°-1680.41设计流量时第三象限Fsj*COS15°26511.8650%设计流量时第三象限Fsjy=Fsj*SIN75°-6254.78设计流量时第三象限Fsj*SIN15°7100.06150%设计流量时第三象限2 叶轮不平衡量引起的径向力Fyp =1.12*9.8*10-9Gc*n2*D2/2=6.930176N3 转子重量叶轮G1=245N 悬臂轴G2=2583.2轴向力N这里我们认为轴向力为零3.3扭矩M=Mn=1520.252N.myp 全部加在Y方向上)-134.433N.m 2120.949N.m -480.228N.m 588.1593N.m 498.6892N.m 2200.99N.m -352.887N.m 5567.491N.m -1260.6N.m 1543.918N.m 1309.059N.m 5777.598N.m -470.515N.m 7423.322N.m -1680.8N.m 2058.558N.m 1745.412N.m7703.465N.m 444.3436N.m -7010.41N.m 1590.949N.m -1940.41N.m 1651.835N.m 7273.998N.m 107.3922N.m 469.4983N.m3Cr135.1σa=M x ===M y ===W=σa=a2120.949y50%设计流量时-480.782587.60493.01E-0516593879731546705.2弯曲应力幅常量:σσm=M c =(F sjy +G ⨯L 1设计流量时50%设计流量时设计流量时50%设计流量时m=σm=18428.395.3切应力幅变量:τaτa=0.25τ=59625525.4切应力幅常量:τmτm=τ=238502075.5求疲劳安全系数:n1 弯曲疲劳安全系数:nσn σ===2n τ==n===所以所设计的轴是满足疲劳强度要求的。
离心泵计算公式范文

离心泵计算公式范文离心泵是一种常见的工业泵,广泛应用于供水、排水、空调、石油化工、冶金和化工等领域。
它通过离心力将液体从一处吸入,然后通过叶轮转动产生离心力,将液体压入叶轮的出口。
要计算离心泵的性能参数,需要了解以下几个主要的公式:1.流量(Q)计算公式:流量是离心泵的关键性能参数,表示单位时间内流经泵体的液体体积。
流量的计算公式如下:Q=n*V其中,n为泵的转速,单位为rpm;V为泵的容积,单位为m³。
2.扬程(H)计算公式:扬程是液体从进口到出口的压力能量转换的高度,也是离心泵的另一个重要性能参数。
扬程的计算公式如下:H=(P2-P1)/(ρ*g)其中,P2为泵出口压强,单位为Pa;P1为泵进口压强,单位为Pa;ρ为液体密度,单位为kg/m³;g为重力加速度,单位为m/s²。
3.功率(N)计算公式:离心泵的功率是泵所需的功率,表示泵的能量消耗程度。
功率的计算公式如下:N=(P2*Q)/η其中,P2为泵出口压强,单位为Pa;Q为流量,单位为m³/s;η为泵的效率,无单位。
4.效率(η)计算公式:泵的效率是指泵输送液体的能量转化效率,是衡量泵性能的重要指标。
效率的计算公式如下:η=(转速*扬程)/(367*功率)5.叶轮直径计算公式:叶轮直径是泵型号和尺寸设计的重要参数,它直接影响到泵的性能和效率。
叶轮直径的计算公式如下:D=(c*Q)/(π*v)其中,D为叶轮直径,单位为m;c为单位流量,单位为m³/(s·m);Q为流量,单位为m³/s;v为泵转速,单位为m/s。
以上是离心泵的一些常用计算公式,根据具体的实际情况和需求,可以选择合适的公式进行计算和应用。
需要注意的是,实际的泵性能还受到一些其他的因素影响,如摩擦阻力、泵的结构和材料等,因此,在应用这些公式时需要进行适当的修正和调整。
电机转子计算书
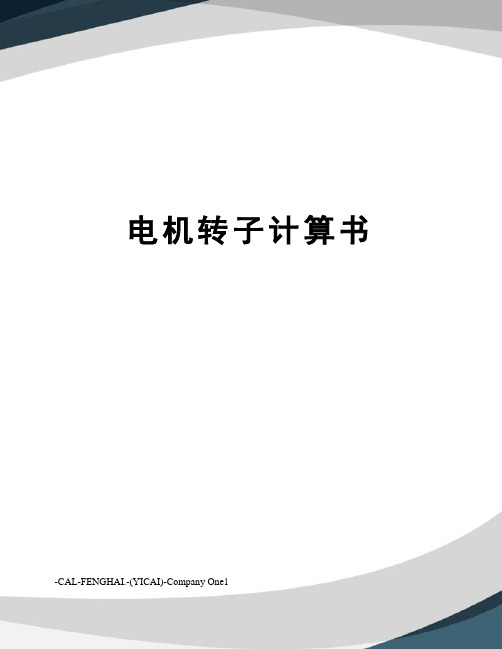
电机转子计算书-CAL-FENGHAI.-(YICAI)-Company One1一.轴的挠度及临界转速、强度、刚度计算书(一)、轴的挠度及临界转速计算1. 转子重量:G =38000Kg2. 有效铁心长度:L =109cm3. 转子外径:D =4. 转轴的简化图形如图1所示 图1 转轴简化图形5. 单边平均气隙:δ=6. 轴在b 点的挠度系数:αbb =62622221221017.11.43110238.241.1791.82523-⨯=⨯⨯⨯⨯+⨯=⨯+⨯EL K L K L cb ab 7. 磁拉力刚度 k 0=cm Kg B DLs /73257)70005160(7.01096.2883)7000(322=⨯⨯⨯=δ8. 初始单边磁拉力P 0==73257××=5153Kg9. 由重量G 引起在b 点的挠度: f 1=G αbb =2200××10-6=10. 单边磁拉力引起轴在b 点的挠度:f 2=f 0(1-m)== 式中:f 0=[P 0/G ]f 1=[1412/2200]×= m= f 0/e 0== e 0=δ=×= 11. 轴在b 点的总挠度f=f 1+f 2=+= 12. 挠度占气隙的百分数f ′=×100%=%13. 许用挠度[f ]=8%>%,因此轴的挠度满足要求。
14. 转轴临界转速:n kp =200min /912044.0/)086.01(200/)1(1r f m =-=- (n kp -n N )/n N =(912-200)/200=356%>30%,因此轴的临界转速满足要求。
(二)、轴的疲劳强度的安全系数计算:轴的疲劳强度按轴上长期作用的最大变载荷进行计算,对同步电动机来说可按3倍的额定转矩来计算,轴的疲劳强度校核主要是长期受载荷作时危险截面的安全系数校核,具体计算如下: 1、轴系受力分布图轴系受力可按集中载荷考虑,受力如下图所示,其中G =38000Kg (按转子整个重量计算), 单边磁拉力P0=5153Kg,P0+G=43153Kg 。
离心泵转子的强度和刚度计算

离心泵转子的强度和刚度计算1.根据离心力计算转子的强度:离心泵在工作状态下会受到离心力的作用,转子的承载能力需要满足系统给定的要求。
离心力的大小与泵的转速、流量及离心泵的几何形状等有关。
根据泵的额定参数,可以计算出离心力的大小,并与转子的强度进行比较。
2.根据压力载荷计算转子的强度:离心泵在工作状态下还会受到液体的压力载荷的作用,转子的承载能力同样需要满足系统给定的要求。
压力载荷的大小与液体的密度、流量、压力以及泵的设计参数有关。
根据泵的额定参数,可以计算出压力载荷的大小,并与转子的强度进行比较。
3.强度计算的材料性能:在强度计算中,需要考虑所使用材料的机械性能。
不同的材料有不同的抗拉强度、屈服强度、弹性模量等参数,这些参数会直接影响到转子的强度计算结果。
1.根据转距力矩计算转子的刚度:转子在工作状态下会受到转距力矩的作用,转子的刚度需要满足给定的要求。
转距力矩的大小与转子的几何形状、材料性能以及液体的流量、压力等参数有关。
根据给定的转距力矩和相应的刚度要求,可以计算出转子的刚度。
2.刚度计算的几何结构:在刚度计算中,需要考虑转子的几何结构,如转子的长度、直径、材料的截面形状等因素。
这些因素会直接影响到转子的刚度计算结果。
3.刚度计算的材料性能:在刚度计算中,同样需要考虑所使用材料的弹性模量等机械性能。
不同的材料有不同的弹性模量值,这会影响到转子的刚度计算结果。
离心泵转子的强度和刚度计算是离心泵设计的重要一环,通过对转子的强度和刚度进行计算,可以保证离心泵在运行过程中能够承受外力的作用而不发生破坏,并且保证泵的运行稳定性和寿命。
在实际设计中,需要根据具体的工作条件和要求,选用适当的材料和优化转子的几何参数,以提高转子的强度和刚度。
通过科学合理的计算和设计,可以有效地提高离心泵的性能和使用寿命。
离心泵的性能影响因素及其换算

离心泵的性能影响因素及其换算离心泵生产部门所供给的特性曲线通常是在肯定转速和常温(20℃)条件下,以清水作为输送介质进行测定出来的。
若使用时的使用条件差别较大,所输送的液体性质和水相差较大时,则要考虑物性、转速和叶轮直径不同所带来的影响。
选用时应进行换算。
下面就离心泵的性能影响因素和换算进行说明。
1、密度ρ的影响由离心泵的基本方程式可知,离心泵的压头、流量、与密度无关,故其效率变不随密度更改而变化,故由离心泵的轴功率计算式表明,离心泵的轴功率随液体的密度更改而变化,故原特性曲线N~Q或性能表的轴功率应作相应的换算:式中,N——操作条件下,离心泵的轴功率,KW;ρ——操作条件下,被输送液体的;N0——试验条件下,离心泵的轴功率,KW;ρ0——20℃时清水的密度,kg/m3。
2、粘度的影响由于离心泵内部的流动阻力损失与被输送液体粘度有关,粘度增大,液体通过叶轮与泵壳的流动阻力变增大,因此压头、流量减小,效率降低、轴功率增大。
一般来说,当液体的运动粘度过ν>0.2m2/s时,应以下列式子进行换算:式中,Q,H,η——为输水时的流量、压头与效率;Q",H",η"——为被输送液体的流量、压头与效率;CQ,CH,Cη——换算系数,其值皆小于1。
可从有关手册中查取。
3.转速n的影响当离心泵的转速更改时,其流量、压头、轴功率与转速可依下述比例定律换算:式中,Q1,H1,N1——分别为转速为n1时离心泵的性能;Q2,H 2,N2——分别为转速为n2时离心泵的性能。
值得注意的是,引出上述关系式的基本假设是转速更改后其效率不变,因此只有在转速变化小于20%时,比例定律才接近正确。
4.叶轮直径D2的影响当离心泵的转速n肯定时,由基本方程式可知其压头、流量与时轮的直径D2有关。
其变化可依下述切割定律进行换算:式中,Q,H,N——分别为叶轮直径为D2时泵的性能;Q,H,N——分别为叶轮直径为D2时泵的性能。
离心泵转子的强度和刚度计算

轴的强度与刚度计算1。
0输入数据1)设计流量Q1500(m3/h)2)设计扬程H40(m)3)设计转数n1450(r/min)4)设计效率η0.855)介质温度T(℃)6)介质粘度ν(m2/s)7)介质密度ρ1000(kg/m3)8)介质饱和蒸汽压Pv(kgf/cm2)9)轴材料允许切应力τ55000000(N/m2)Pa10)轴材料的屈服极限σs 6.37E+08(N/m2)Pa11)轴材料的弯曲极限σb8.34E+0812)轴材料的弯曲疲劳极限σ-1 3.55E+08(N/m2)Pa13)轴材料的剪切疲劳极限τ-1 2.04E+08(N/m2)Pa14)轴材料的弹性模量E2100000kg/cm215)弯矩单独作用时的有效应力集中系数kσ 1.6916)扭矩单独作用时的有效应力集中系数kτ 1.6117)弯矩单独作用时的绝对尺寸影响系数εσ0.7318)扭矩单独作用时的绝对尺寸影响系数ετ0.7819)弯矩单独作用时材料对应力循环不对称性的敏感性系数ψσ0.120)扭矩单独作用时材料对应力循环不对称性的敏感性系数ψτ0.0521)轴表面质量系数β122)叶轮外径D20.4(m)23)叶轮出口宽度B20.1(m)24)叶轮动不平衡余量Gc 1.5(g)25)叶轮重量Gy245(N)26)轴重量Gz258(N)E:\LK30轴.SLDPRT27)联轴器重GL20(N)27)插入轴的三维及二维图已确定轴段各尺寸) 3。
0计算作用在轴上的载荷3.1径向力1)水力径向力设计流量时与隔舌夹角195°50%设计流量时与隔舌夹角135°因隔舌角为60°,故:F sjx=Fsj*COS75°-1680.41设计流量时第三象限Fsj*COS15°26511.8650%设计流量时第三象限Fsjy=Fsj*SIN75°-6254.78设计流量时第三象限Fsj*SIN15°7100.06150%设计流量时第三象限2)叶轮不平衡量引起的径向力F yp=1.12*9.8*10-9Gc*n2*D/22= 6.930176N3)转子重量叶轮G1=245N悬臂轴G2=258N3.2轴向力这里我们认为轴向力为零3.3扭矩M=Mn=1520.252N.m全部加在Y方向上)yp-134.433N.m2120.949N.m-480.228N.m588.1593N.m498.6892N.m2200.99N.m-352.887N.m5567.491N.m-1260.6N.m1543.918N.m1309.059N.m5777.598N.m-470.515N.m7423.322N.m-1680.8N.m2058.558N.m1745.412N.m7703.465N.m 444.3436N.m -7010.41N.m1590.949N.m -1940.41N.m 1651.835N.m 7273.998N.m 107.3922N.m 469.4983N.m3Cr135.1aσa=M x ===2120.94950%设计流量时M y ==-480.782设计流量时=587.604950%设计流量时W= 3.01E-05σa=16593879设计流量时7315467050%设计流量时5.2弯曲应力幅常量:σmσm=M c==σm=18428.395.3切应力幅变量:τaτa=0.25τ=59625525.4切应力幅常量:τmτm=τ=238502075.5求疲劳安全系数:n 1)弯曲疲劳安全系数:n σn σ===2)n τ==3)n===4)所以所设计的轴是满足疲劳强度要求的。
离心泵主要零部件的强度计算
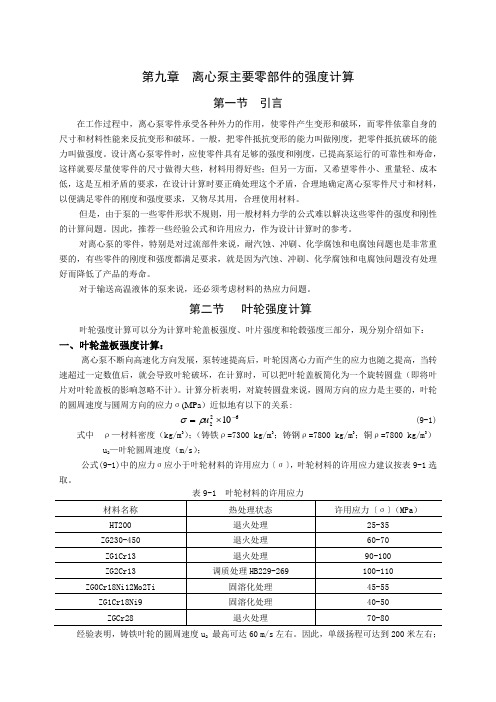
第九章 离心泵主要零部件的强度计算第一节 引言在工作过程中,离心泵零件承受各种外力的作用,使零件产生变形和破坏,而零件依靠自身的尺寸和材料性能来反抗变形和破坏。
一般,把零件抵抗变形的能力叫做刚度,把零件抵抗破坏的能力叫做强度。
设计离心泵零件时,应使零件具有足够的强度和刚度,已提高泵运行的可靠性和寿命,这样就要尽量使零件的尺寸做得大些,材料用得好些;但另一方面,又希望零件小、重量轻、成本低,这是互相矛盾的要求,在设计计算时要正确处理这个矛盾,合理地确定离心泵零件尺寸和材料,以便满足零件的刚度和强度要求,又物尽其用,合理使用材料。
但是,由于泵的一些零件形状不规则,用一般材料力学的公式难以解决这些零件的强度和刚性的计算问题。
因此,推荐一些经验公式和许用应力,作为设计计算时的参考。
对离心泵的零件,特别是对过流部件来说,耐汽蚀、冲刷、化学腐蚀和电腐蚀问题也是非常重要的,有些零件的刚度和强度都满足要求,就是因为汽蚀、冲刷、化学腐蚀和电腐蚀问题没有处理好而降低了产品的寿命。
对于输送高温液体的泵来说,还必须考虑材料的热应力问题。
第二节 叶轮强度计算叶轮强度计算可以分为计算叶轮盖板强度、叶片强度和轮毂强度三部分,现分别介绍如下:一、叶轮盖板强度计算:离心泵不断向高速化方向发展,泵转速提高后,叶轮因离心力而产生的应力也随之提高,当转速超过一定数值后,就会导致叶轮破坏,在计算时,可以把叶轮盖板简化为一个旋转圆盘(即将叶片对叶轮盖板的影响忽略不计)。
计算分析表明,对旋转圆盘来说,圆周方向的应力是主要的,叶轮的圆周速度与圆周方向的应力σ(MPa )近似地有以下的关系:62210-⨯=u ρσ (9-1)式中 ρ—材料密度(kg/m 3);(铸铁ρ=7300 kg/m 3;铸钢ρ=7800 kg/m 3;铜ρ=7800 kg/m 3) u 2—叶轮圆周速度(m/s );公式(9-1)中的应力σ应小于叶轮材料的许用应力〔σ〕,叶轮材料的许用应力建议按表9-1选取。
第三章:转子、叶轮结构和强度计算_最终

转子是透平十分重要的部件,保证转子安全工作是设 计制造部门的重要任务之一。 转子的工作条件相当复杂,转子处在高温工质中,并以 高速旋转。 转子承受由于叶片和转子本身离心力引起的很大的应力 以及由于温度分布不均匀引起的温度应力。 透平转子和其他高速旋转机械一样,由于不平衡质量的 离心力,将引起转子振动。此外,转子还要传递作用在叶片上 的气流力产生的扭矩等。 因此,必须对转子、叶轮进行强度计算,任何设计、 制造、运行等方面工作的疏忽,均会造成重大事故。
3-1 转子和叶轮结构
广泛采用的是轮式整锻转子。由于采用叶轮弥补了上述空心 鼓式转子强度不足的缺点,其圆周速度容许达到170-200米/秒以上。
3-1 转子和叶轮结构
整锻转子加工过程
3-1 转子和叶轮结构
为了保证锻件的良好质量,整锻转子的尺寸是受到一定限制的。如 果转子有几级叶轮直径过大而锻造困难而且由于后面低压级蒸汽温度低, 叶轮可用低一级的材料。此时亦可以采用组合转子,即在整锻转子轴上套 上几级叶轮。如图3-5所示为整锻和套装组合的转子,高压部份的前11级叶 轮是整锻,后面低压部分7级叶轮为套装。
着手设计叶轮时,先必须考虑叶轮与透平轴的联结方法。 对套装叶轮,通常是用键来联结,同时为了使叶轮与轴可靠的联结, 也就是说要保证在叶轮工作时,叶轮与轴保持对中 (同心),且相对于轴的 位置不变,还必须把叶轮红套在轴上。
3-1 转子和叶轮结构
图3-11用键和过盈联结叶轮与轴。扭矩 借接触摩擦力和键来传递。
3-1 转子和叶轮结构
焊接转子具有整锻转子所有的许多优点,但它比整锻转子重量轻;特别 是锻件小容易获得高质量锻件。它比套装转子结构紧凑,而且刚度大。此外,焊 接转子的显著优点是强度大。焊接转子适于作为高温和高速条件下工作的转子型 式,而转子的重量和尺寸几乎不受限制。
- 1、下载文档前请自行甄别文档内容的完整性,平台不提供额外的编辑、内容补充、找答案等附加服务。
- 2、"仅部分预览"的文档,不可在线预览部分如存在完整性等问题,可反馈申请退款(可完整预览的文档不适用该条件!)。
- 3、如文档侵犯您的权益,请联系客服反馈,我们会尽快为您处理(人工客服工作时间:9:00-18:30)。
轴的强度与刚度计算1。
0输入数据1 设计流量Q1500(m3/h2 设计扬程
H40(m3 设计转数n1450(r/min4 设计效率η0.855 介质温度T(℃6 介质粘度ν(m2/s7 介质密度ρ1000(kg/m3 8 介质饱和蒸汽压Pv(kgf/cm2 9 轴材料允许切应力
τ55000000(N/m2Pa 10 轴材料的屈服极限σs 6.37E+08(N/m2Pa 11 轴材料的弯曲极限σb 8.34E+08
12 轴材料的弯曲疲劳极限σ
-1
3.55E+08(N/m2Pa
13 轴材料的剪切疲劳极限τ-12.04E+08(N/m2Pa 14 轴材料的弹性模量
E2100000kg/cm215 弯矩单独作用时的有效应力集中系数kσ1.6916 扭矩单独作用时的有效应力集中系数kτ1.6117 弯矩单独作用时的绝对尺寸影响系数εσ0.7318 扭矩单独作用时的绝对尺寸影响系数ετ0.7819 弯矩单独作用时材料对应力循环
不对称性的敏感性系数ψσ0.120 扭矩单独作用时材料对应力循环
不对称性的敏感性系数ψτ0.0521 轴表面质量系数β122 叶轮外径D20.4(m23 24 25 26 27 27
叶轮出口宽度B20.1(m叶轮动不平衡余量Gc1.5(g叶轮重量Gy245(N轴重量Gz258(N联轴器重GL20(N插入轴的三维及二维图已确定轴段各尺寸
) 3。
0计算作用在轴上的载荷3.1径向力 1)水力径向力
设计流量时与隔舌夹角195°50%设计流量时与隔舌夹角135°
因隔舌角为60°,故:Fsjx =Fsj*COS75°-1680.41设计流量时第三象限
Fsj*COS15°26511.8650%设计流量时第三象限Fsjy=Fsj*SIN75°-6254.78设计流量时第三象限
Fsj*SIN15°7100.06150%设计流量时第三象限
2 叶轮不平衡量引起的径向力
Fyp =1.12*9.8*10-9Gc*n2*D2/2
=6.930176N
3 转子重量
叶轮G1=245N 悬臂轴G2=2583.2轴向力
N
这里我们认为轴向力为零3.3扭矩
M=Mn
=1520.252N.m
yp 全部加在Y方向上)
-134.433N.m 2120.949N.m -480.228N.m 588.1593N.m 498.6892N.m 2200.99N.m -352.887N.m 5567.491N.m -1260.6N.m 1543.918N.m 1309.059N.m 5777.598N.m -470.515N.m 7423.322N.m -1680.8N.m 2058.558N.m 1745.412N.m
7703.465N.m 444.3436N.m -7010.41N.m 1590.949N.m -1940.41N.m 1651.835N.m 7273.998N.m 107.3922N.m 469.4983N.m
3Cr13
5.1
σa=
M x ==
=M y ===W=σa=
a
2120.949
y
50%设计流量时
-480.782587.60493.01E-051659387973154670
5.2弯曲应力幅常量:σ
σm=M c =
(F sjy +G ⨯L 1
设计流量时50%设计流量时设计流量时50%设计流量时
m
=σm=18428.39
5.3切应力幅变量:τa
τa=0.25τ=5962552
5.4切应力幅常量:τm
τm=τ
=23850207
5.5求疲劳安全系数:n1 弯曲疲劳安全系数:nσ
n σ=
==2
n τ=
=n===所以所设计的轴是满足疲劳强度要求的。
临界转速计算
计算了轴的强度,还应计算轴的刚度,以确保转子的无摩擦及平稳运转。
计算轴的挠度叶轮部位的荷重G1
G1=G
y
=25kg
轴的自身荷重G2
G2=26.32653kg 联轴器重G3
3
4 6。
06.11
2 3
G3=2.040816kg
3 平均惯性矩J
J==
4 y 1==
y 2==y 3==6.2nc==3285.2833613.811 L9
0.043L100.07
0.080.075
取不同的值)
成得曲线方程如下:0-5n s +0. 0206
部加在Y方向上)
设计流量时50%设计流量时设计流量时50%设计流量时设计流量时50%设计流量时设计流量时50%设计流量时设计流量时50%设计流量时设计流量时50%设计流量时设计流量时50%设计流量时设计流量时50%设计流量时
设计流量时
50%设计流量时设计流量时50%设计流量时设计流量时50%设计流量时设计流量时50%设计流量时设计流量时50%设计流量时。