锌合金压铸缺陷分析及解决办法
压铸产品质量缺陷分析及解决对策

龚春2011-09-30 龚春
压铸产品质量缺陷分析及解 决对策
分类: 分类: 冷隔、拉伤、裂纹、变形、花纹、 冷隔、拉伤、裂纹、变形、花纹、 斑点、网状毛刺、凹陷、欠铸、 斑点、网状毛刺、凹陷、欠铸、夹 外观类) 皮(外观类) 气孔、缩孔、气泡、夹杂( 气孔、缩孔、气泡、夹杂(内在组 织缺陷) 织缺陷)等
TU5JP4进排气浇口直冲型芯有被冲凹陷的立即进行更换以减少变形
上模时压铸机上的4根推杆一定要长度一样, 公差在0.5mm内,以保证顶出平稳
开模后静模弹簧推杆没有出来,说明已经卡死不 起作用了,需修模
DUG:977机框下抽芯
变形:
1. 铸件几何形状与图纸不符 2. 整体变形或局部变形 产生的原因: 产生的原因: 1. 铸件结构设计不良,引起不均匀收缩 铸件结构设计不良, 2. 开模过早,铸件刚性不够 开模过早, 3. 顶杆设置不当,顶出时受力不均匀 顶杆设置不当, 4. 切除浇口方法不当 5. 由于模具表面粗糙造成举报阻力大而引起顶出时变形 改进措施 (检查分析判断是开模变形还是顶出变形\收缩变形) 检查分析判断是开模变形还是顶出变形\收缩变形) 1. 改进铸件结构,比如机体人为增加倒拔,倒钩平衡包紧力, 改进铸件结构,比如机体人为增加倒拔,倒钩平衡包紧力,人为增 加渣包等。 加渣包等。 2. 调整开模时间 3. 合理设置顶杆位置及数量,有必要加6 合理设置顶杆位置及数量,有必要加6根推杆 4. 选择合适的切除浇口方法比如热切边 选择合适的切除浇口方法比如热切边 5. 加强模具型腔表面抛光0.4 减少脱 加强模具型腔表面抛光0.4,减少脱模阻力 0.4, 6、上模时推杆配平 7、更换断推杆 8、检查有无倒拔,及时消除 检查有无倒拔,
锌合金生产的注意事项及缺陷原因分析
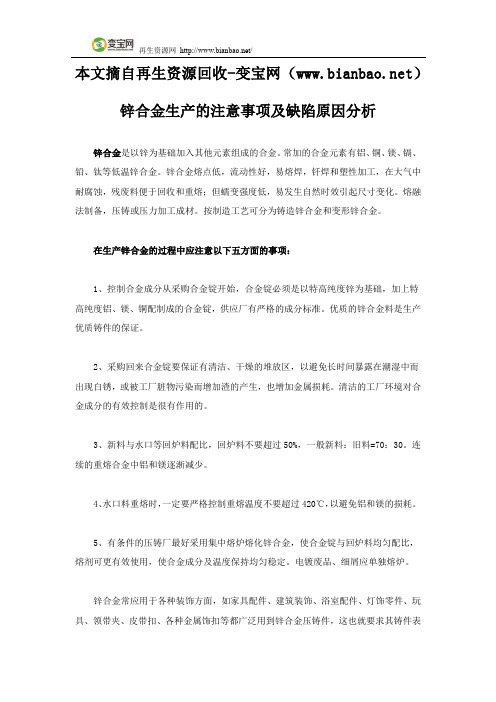
本文摘自再生资源回收-变宝网()锌合金生产的注意事项及缺陷原因分析锌合金是以锌为基础加入其他元素组成的合金。
常加的合金元素有铝、铜、镁、镉、铅、钛等低温锌合金。
锌合金熔点低,流动性好,易熔焊,钎焊和塑性加工,在大气中耐腐蚀,残废料便于回收和重熔;但蠕变强度低,易发生自然时效引起尺寸变化。
熔融法制备,压铸或压力加工成材。
按制造工艺可分为铸造锌合金和变形锌合金。
在生产锌合金的过程中应注意以下五方面的事项:1、控制合金成分从采购合金锭开始,合金锭必须是以特高纯度锌为基础,加上特高纯度铝、镁、铜配制成的合金锭,供应厂有严格的成分标准。
优质的锌合金料是生产优质铸件的保证。
2、采购回来合金锭要保证有清洁、干燥的堆放区,以避免长时间暴露在潮湿中而出现白锈,或被工厂脏物污染而增加渣的产生,也增加金属损耗。
清洁的工厂环境对合金成分的有效控制是很有作用的。
3、新料与水口等回炉料配比,回炉料不要超过50%,一般新料:旧料=70:30。
连续的重熔合金中铝和镁逐渐减少。
4、水口料重熔时,一定要严格控制重熔温度不要超过420℃,以避免铝和镁的损耗。
5、有条件的压铸厂最好采用集中熔炉熔化锌合金,使合金锭与回炉料均匀配比,熔剂可更有效使用,使合金成分及温度保持均匀稳定。
电镀废品、细屑应单独熔炉。
锌合金常应用于各种装饰方面,如家具配件、建筑装饰、浴室配件、灯饰零件、玩具、领带夹、皮带扣、各种金属饰扣等都广泛用到锌合金压铸件,这也就要求其铸件表面的质量要高,并需具有良好的表面处理性能。
而锌合金压铸件最常见的缺陷是表面起泡。
缺陷表征:压铸件表面有突起小泡。
主要表现为:压铸出来就发现,抛光或加工后显露出来,还有喷油或电镀后会出现。
产生原因:1、孔洞引起:主要是气孔和收缩机制,气孔往往是圆形,而收缩多数是不规则形。
(1)气孔产生原因:①金属液在充型、凝固过程中,由于气体侵入,导致铸件表面或内部产生孔洞。
②涂料挥发出来的气体侵入。
③合金液含气量过高,凝固时析出。
压铸缺陷产生原因及解决方案
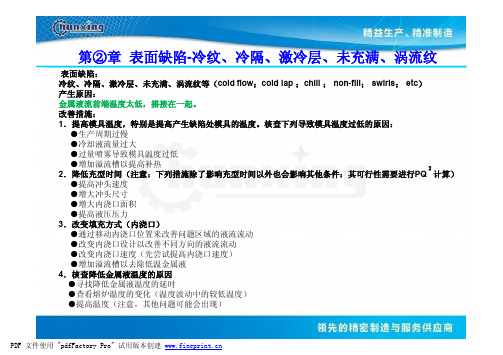
---润滑不够
---套管冷却不当
---热压室-核查冲头浇口套
---热压室-如果冲头底部和浇口套正常,更换鹅颈管
PDF 文件使用 "pdfFactory Pro" 试用版本创建
第⑦章 缺陷-缩孔、缩松
3.在缩松处提供额外的金属液 ●能够使用挤压杆么? ●能够在缩松处附近引入额外的内浇口么? ●能够增加内浇口和缩松处之间铸件的壁厚么?
●对于铝合金: Si元素含量在要求范围内尽可能高 金属液尽可能干净
●对于锌合金: 铝含量尽可能高 其他组分含量适中
●通风口畅通,大小正确 ●真空系统工作正常 ●如果有薄壁部件出现:
核对目前采用的充型时间和温度下能够生产的最小壁厚 设计缺陷,设计者对铸造问题缺少理解 模具制造问题(尺寸不是所期望的) 不均匀壁厚(零件设计不理想)
PDF 文件使用 "pdfFactory Pro" 试用版本创建
缺陷:
第⑦章 缺陷-缩孔、缩松
缩松(shrinkage porosity)
产生原因:
铸件材料凝固时会产生体积收缩,这种固体和液体之间的体积差异会再热节处形成空腔(缩松和缩孔)
改善措施:
1.在凝固时对半固态金属(在缩松产生的位置)增加压力
【压铸机】压铸过程中常见的问题和解决方法
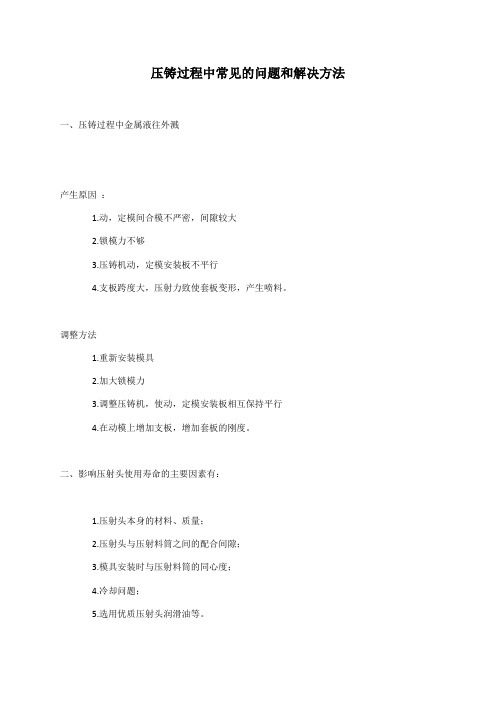
压铸过程中常见的问题和解决方法一、压铸过程中金属液往外溅产生原因:1.动,定模间合模不严密,间隙较大2.锁模力不够3.压铸机动,定模安装板不平行4.支板跨度大,压射力致使套板变形,产生喷料。
调整方法1.重新安装模具2.加大锁模力3.调整压铸机,使动,定模安装板相互保持平行4.在动模上增加支板,增加套板的刚度。
二、影响压射头使用寿命的主要因素有:1.压射头本身的材料、质量;2.压射头与压射料筒之间的配合间隙;3.模具安装时与压射料筒的同心度;4.冷却问题;5.选用优质压射头润滑油等。
三、缺陷名:(一)产品表面起皱症状:产品表面形成的不规则褶皱,主要出现在壁较薄的前段部分。
原因:由于吸入了脱模剂和压缩空气,被封闭在前段的气压较高,把产品表面顶起而导致这一现象的发生解决方案:排气彻底,清除多余的脱模剂。
调整高速高压区的位置以防止溶液降温(二)缺陷名:起皱症状:镶件附近的圆柱状部分,表面的皮膜出现起皱现象起皱的表面部分,根据发生状态有差异。
在靠近镶件的拐角处,出现与镶件平行的褶皱。
在离拐角稍远处,表面皮膜起皱部分有细小的铝颗粒聚集,呈粉末状附着在表面起皱的断面可以观察到起皱导致的凹凸,细小的铝颗粒被压碎后嵌入褶皱里。
原因:在模具温度低时进行铸造容易发生此现象。
铝液在流道流淌时前锋冷却,形成氧化皮膜,在距离浇口较远的突起部分凝固,由于压力增大在表面形成褶皱。
解决方案:对模具进行预热,在设定的温度条件下进行生产是很重要的,将模具温度设定在适当的范围。
换导柱以及导套时一定要注意尺寸变化,尤其是长时间使用但是没有回火或者测量的模具,一定要检查模具的尺寸,包括模板平行度、孔直线度、孔内外径是否变化。
一般情况下基准尺寸会变化。
锌压铸件毛坯看不到麻点,电镀前抛光就出现麻点,这是怎么回事?这是锌压铸件最易出现的问题之一。
要注意:1.原材料的质量(纯净度);2.熔化时的精炼除气除渣;3.压铸时速度、压力的调整(特别是皮下气孔等缺陷);4.抛光时摩擦的压力和温度不要太高。
2.压铸产品铸造缺陷产生原因及处理办法
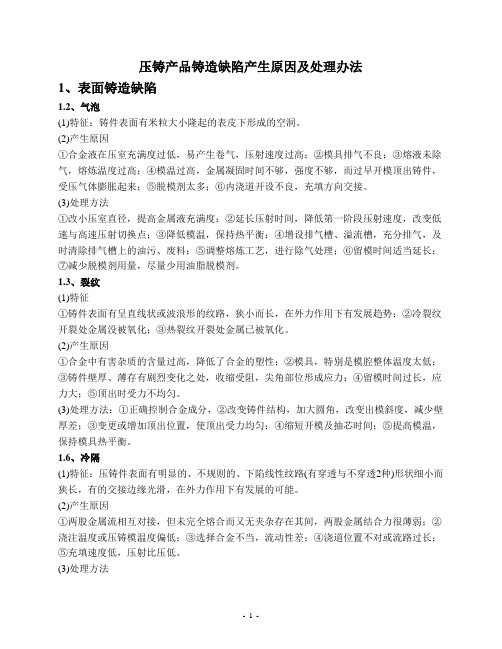
压铸产品铸造缺陷产生原因及处理办法1、表面铸造缺陷1.2、气泡(1)特征:铸件表面有米粒大小隆起的表皮下形成的空洞。
(2)产生原因①合金液在压室充满度过低,易产生卷气,压射速度过高;②模具排气不良;③熔液未除气,熔炼温度过高;④模温过高,金属凝固时间不够,强度不够,而过早开模顶出铸件,受压气体膨胀起来;⑤脱模剂太多;⑥内浇道开设不良,充填方向交接。
(3)处理方法①改小压室直径,提高金属液充满度;②延长压射时间,降低第一阶段压射速度,改变低速与高速压射切换点;③降低模温,保持热平衡;④增设排气槽、溢流槽,充分排气,及时清除排气槽上的油污、废料;⑤调整熔炼工艺,进行除气处理;⑥留模时间适当延长;⑦减少脱模剂用量,尽量少用油脂脱模剂。
1.3、裂纹(1)特征①铸件表面有呈直线状或波浪形的纹路,狭小而长,在外力作用下有发展趋势;②冷裂纹开裂处金属没被氧化;③热裂纹开裂处金属已被氧化。
(2)产生原因①合金中有害杂质的含量过高,降低了合金的塑性;②模具,特别是模腔整体温度太低;③铸件壁厚、薄存有剧烈变化之处,收缩受阻,尖角部位形成应力;④留模时间过长,应力大;⑤顶出时受力不均匀。
(3)处理方法:①正确控制合金成分,②改变铸件结构,加大圆角,改变出模斜度,减少壁厚差;③变更或增加顶出位置,使顶出受力均匀;④缩短开模及抽芯时间;⑤提高模温,保持模具热平衡。
1.6、冷隔(1)特征:压铸件表面有明显的、不规则的、下陷线性纹路(有穿透与不穿透2种)形状细小而狭长,有的交接边缘光滑,在外力作用下有发展的可能。
(2)产生原因①两股金属流相互对接,但未完全熔合而又无夹杂存在其间,两股金属结合力很薄弱;②浇注温度或压铸模温度偏低;③选择合金不当,流动性差;④浇道位置不对或流路过长;⑤充填速度低,压射比压低。
(3)处理方法①适当提高浇注温度和模具温度;②提高压射比压,缩短充填时间;③提高压射速度,同时加大内浇道截面积;④改善排气、填充条件;⑤正确选用合金,提高合金流动性。
压铸产品缺陷的诊断

压铸产品缺陷的诊断过程是一个复杂过程。
压铸产品合格率一般在70%~90%之间,影响产品的因素有如下几点:机器本身的性能;机器的各项工作参数;压铸型(模)的结构和性能;压铸的质量及操作者的技能。
为了提高生产效率和产品的合格率,操作人员必须具备有一定的预防和排除产品缺陷的工作能力。
一、压铸产品缺陷诊断实例分析(一)铸件出现缺陷时,应分析缺陷产生的原因,一般从如下几个方面考虑:调机(调整压铸工艺参数);换料(换另一种料或改变新料与回炉料比例);修改型(模)具结构(内浇口、溢流槽、排气槽)。
1、分析思路(1)先作成分分析,判断料的质量,对缺陷影响程度。
(2)可以剖开缺陷部位,进行金相分析,判断压铸工艺因素影响。
(3)对型(模)具方案重新分析。
(4)对熔炼过程的检查。
2、采取措施(1)调整工艺参数:填充速度、填充时间、模温等。
(2)换料:换另一个品牌的料;新料与回炉料的比例。
(3)修改型(模)具:内浇口,入水的射流角度,溢流槽,排气槽。
(二)实例分析1、初步了解铸件名称:汽车化油器本体;压铸:ADC12;产生缺陷:加工后漏气,废品率达40%以上。
2、分析过程及解决方法(1)进行成分化学分析,列出分析表,见表7-1。
表7-1ADC12压铸成分化学分析表CuSiMgZnFeMnNiSn铸件.铸件.铸件.规定值~3.59.6~<<<<<<分析结果:Zn含量在2%、Fe含量在3%左右,大大超过了规定值。
杂质Zn:高温脆性大,使铸件有产生裂纹的倾向。
杂质Fe:当Fe含量低于%,会产生与压铸型(模)焊合现象;含量在~%范围比较好压铸,但含量超过%,又会产生金属化合物,降低物理性能,是产生缩孔、收缩裂纹的原因之一。
解决方法:控制中杂质含量。
(2)金相分析分析结果:发现基本组织晶体粗大,有铁-锌-硅的化合物,有气孔、缩孔。
解决方法:成分中杂质含量控制,压铸工艺调整。
(3)对熔炼过程采取措施估计金属液中含气量较高,在保温炉内,采用氩气脱气处理15分钟。
压铸件常见的缺陷分析及其改善措施
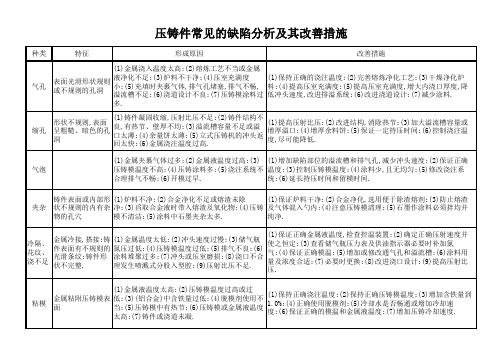
粘模
金属粘附压铸模表 面
(1)金属液温度太高;(2)压铸模温度过高或过 低;(3)(铝合金)中含铁量过低;(4)脱模剂使用不 当;(5)压铸模中有热节;(6)压铸模或金属液温度 太高;(7)铸件或浇道未凝.
(1)保持正确浇注温度;(2)保持正确压铸模温度;(3)增加含铁量到 1.0%;(4)正确使用脱模剂;(5)冷却水是否畅通或增加冷却速 度;(6)保证正确的模温和金属液温度;(7)增加压铸冷却速度.
纯净.
ቤተ መጻሕፍቲ ባይዱ
冷隔、 花纹、 浇不足
金属冷接,搭接;铸 (1)金属温度太低;(2)冲头速度过慢;(3)储气瓶
件表面有不规则的 氮压过低;(4)压铸模温度过低;(5)排气不良;(6)
光滑条纹;铸件形 涂料堆聚过多;(7)冲头或压室磨损;(8)浇口不合
状不完整.
理发生喷溅式分股入型腔;(9)压射比压不足.
(1)保证正确金属液温度,检查控温装置;(2)确定正确压射速度并 使之恒定;(3)查看储气瓶压力表及供油指示器必要时补加氮 气;(4)保证正确模温;(5)增加或修改通气孔和溢流槽;(6)涂料用 量及浓度合适;(7)必要时更换;(8)改进浇口设计;(9)提高压射比 压.
气泡
(1)金属夹裹气体过多;(2)金属液温度过高;(3) (1)增加缺陷部位的溢流槽和排气孔,减少冲头速度;(2)保证正确
压铸模温度不高;(4)压铸涂料多;(5)浇注系统不 温度;(3)控制压铸模温度;(4)涂料少,且无均匀;(5)修改浇注系
合理排气不畅;(6)开模过早.
统;(6)延长持压时间和留模时间.
压铸件常见的缺陷分析及其改善措施
种类
特征
形成原因
改善措施
气孔
(1)金属浇入温度太高;(2)熔炼工艺不当或金属
锌合金压铸

02
锌合金压铸材料的种类及性能
锌合金压铸材料的种类及成分
锌合金压铸材料的种类
• Zamak:主要用于压铸件,如汽车零件、家具配件等 • Galvanneal:主要用于冲压件、汽车零件等 • Hot-dipped galvanized:主要用于防锈、装饰性零件等
锌合金压铸材料的成分
• 锌:锌合金的主要成分,具有良好的流动性和浸润性 • 铝:提高合金强度和硬度,降低熔点 • 铜:提高合金硬度和耐磨性,降低熔点 • 镁:提高合金强度和耐磨性,降低熔点 • 其他元素:如硅、锰、铅等,用于改善合金性能
03
锌合金压铸模具的设计及制造
锌合金压铸模具的设计原则及要点
锌合金压铸模具的设计原则
• 结构合理:模具结构要紧凑,便于生产和维修 • 材料合适:选用合适的模具材料,保证模具寿命 • 尺寸精确:模具尺寸要精确,保证压铸件尺寸符合要求 • 冷却充分:模具要设有足够的冷却通道,保证模具温度适中
锌合金压铸模具的设计要点
锌合金压铸工艺的创新
• 新型压铸技术:研究和应用新型压铸技术,如真空压铸、挤压压铸等 • 环保型压铸材料:研究和应用环保型压铸材料,如低铅锌合金等 • 智能化生产:引入智能化生产理念,提高压铸生产效率和质量
锌05合金压铸件的后处理及表面 处理
锌合金压铸件的清理及修整
锌合金压铸件的清理
• 去除毛刺:使用刮刀、砂布等工具去除压铸件上的毛刺 • 清理氧化皮:使用酸洗、抛光等方法清理压铸件表面的氧化皮 • 清洗:使用清洗剂清洗压铸件,去除表面污渍
锌合金压铸件的质量控制
• 原材料控制:选用优质的锌合金原料,保证压铸件质量 • 工艺控制:严格控制压铸工艺参数,保证压铸件质量 • 模具控制:保证模具质量和使用寿命,提高压铸件质量 • 过程控制:严格监控压铸生产过程,及时发现并解决质量问题
- 1、下载文档前请自行甄别文档内容的完整性,平台不提供额外的编辑、内容补充、找答案等附加服务。
- 2、"仅部分预览"的文档,不可在线预览部分如存在完整性等问题,可反馈申请退款(可完整预览的文档不适用该条件!)。
- 3、如文档侵犯您的权益,请联系客服反馈,我们会尽快为您处理(人工客服工作时间:9:00-18:30)。
锌合金压铸缺陷分析及解决办法
摘要:主要介绍锌合金压铸生产中常见缺陷;模具被腐蚀;产品表面硬杂点;铸件缩孔等。
分析了常见缺陷产生的原因,并提出解决办法及工艺措施。
一、前言
在锌合金生产中,压铸件的缺陷是复杂多见的,应对的办法和思维,压铸工作者需不断
地深入研究,吸收新的信息,不断地探索,提高专业技能和素质,掌握产生铸件缺陷的基础
理论知识,用科学的方法分析问题,解决问题。
要求高品质、高产量的产品,必需了解和掌握锌合金的性能、模具的设计、压铸工艺、
后工序加工处理的细节技术和过程控制。每个工作环节离不开技术的支撑。实践经验的积累
与科技的创新。
当缺陷出现时,需从实际的工艺检讨和追溯,核对每个工艺的细节步骤,设立有效的控
制程序,配置检测设备和工具,以下就锌合金压铸件三个典型案例作有效应对分析。
二、压铸模具易被腐蚀
锌合金压铸模具是在415-430℃合金熔液下注入型腔工作状态,型腔的工作恒温最佳为
160-180℃,局部高温易造成产品的缩孔、气孔、内藏气泡,模具受到热冲击而产生腐蚀。
因此,模具的先材、热处理、浇口、流道、排气、溢流槽和运水的合理性设计极为重要。
分析问题首先从模具的设计开始,流道与浇口的设置流速太快,会引起模具高温冲蚀;充型
放射距离太远,会使充型终端区域产生水纹和气孔。流道与浇口的配合,需根据产品的厚薄、
形状和复杂程度选择,而模具的温度平衡控制,依据入水的位置、产品厚度的部位的冷却和
恒温来决定开设冷却水的位置。
总之,引起模具快速腐蚀的主要原因与浇口的速度、流向的设计与冷却水道的布置有密
切关系,克服模具腐蚀,延长模具的使用寿命,需做到以下几点:
(1) 模具的型芯材料的优良先择
(2) 型芯的热处理质量
(3) 浇道与浇口的正确设计和设置
(4) 避免高湿困气
(5) 冷却水道的合理开设,具有可控性
(6) 浇道充型、凝固设计合理
(7) 压铸工艺的参数设定和优化
(8) 合金熔液温度的控制
下面以手机外壳模具腐蚀分析作为案例一进行说明。
(1) 产品:手机电池壳
1)材料:Zamak 3
2)重量:35g
3)壁厚:1.2mm
(2) 质量要求
1)高精度装配尺寸
2)外观质量要求轮廓清晰,表面均匀,质感好
3)加工位无气孔与电镀后不起泡
(3) 压铸设备与工艺
1)设备:DC88
2)合金液控制温度:415-425℃
3)工艺参数:
① 压射时间:0.8s
② 压射速度:4m/s
③ 压射压力:11MPa
④ 冷却时间:2.4s
⑤ 储能时间:0.8s
⑥ 周期时间:0.8s
⑦ 冷却方式:水冷
(4) 结果
1)浇口前方区域在压铸约50000模次时发现冲蚀现象
2)产口前端的中间区域,出现困气起泡现象
3)毛坏产品的合格率不足60%
(5) 原因分析
1)浇口的中间部位充型流速过快,合金液冲涮型腔,温度高,造成浇口前方较近区域热
腐蚀,产品表面起小凸点。
2)由于产品中间部位充型速度过快,产品前方区域(接近溢流槽方向)气体回旋困气,造
成有局部高温气体无法全部排出,引起产品有气孔,起泡和热腐蚀。
3)由于困气使大量气孔于产品中,导致表面处理工序加热时,气孔中空气膨胀,表皮起
泡。
(6) 改良措施
1)针对产品较低的合格率,工程技术与工模相关人员对模具的充型结构做了调整和改
动,如图2所示。
1)改良部位:
① 入水方式,从长边开浇口,用分区充填做法。
② 主流道与分流道设分流三角区。
③ 溢充槽与产品的距离拉远1mm。
(7) 改良效果
1)生产1万模次未发现有冲蚀现象
2)毛坯产品合格率达95%以上
3)相同的设备,压射的压力和速度作降幅调整,提高了产品合格率,延长了模具使用寿
命。
(8) 小结
从产品的长边入水,把分流道和浇口拉长,加上分区多浇口形式进水,避免高速冲刷,
缩短充型距离,降低了压射速度,克服高温冲刷;把溢流槽距离拉离产品,克服气体和冷料
反弹引起溢流槽气孔现象,平衡模温效果。
三、产品抛光后有杂质硬点
杂质硬点(也称夹杂)的来源和生成,是锌合金在高湿的环境下合金中的Al成分和铁质
的热作件中的Fe成分化合而成;其次来源于水口料多次复用和废品使用杂质化合生成。从实
践中得出杂质的来源为。
(1) 电镀废品回炉料
(2) 压铸机热作件在高温通道下余料生成
(3) 水口料多次回炉氧化物生成
下面以手机面壳产品抛光后有杂质点分析作为案例二进行说明。
(1) 产品:手机面壳
1)材料:Zamak3 2)压铸设备:DC88压铸机
3)压铸合金温度:415-425℃ 4)模具型腔穴数为1件
(2)缺陷情况
产品在生产2万模次,在抛光检中未检出有夹杂硬质点存在,在之后生产的产品中,抛
光后产品发现逐渐于产品溢流槽方向的分型线边延有硬质点。经过仔细观察,硬质点的质量
很高,抛光工艺无法除掉,试锉后,有打滑的钢声。
(3)原因分析和改良措施
1)停止生产,换用全新坩锅、鹅咀身和全新原料再生产,产品生产中未发现有硬质杂物
出现;试验证明,全新原料没有存在类似夹杂物,那么它的来源是来自压铸机热作件之中。
从坩锅、鹅颈和射咀身这三件热作件当中分析(前提是硬质点的生成是合金中Al成分与钢件
中Fe元素在高温的状态下化合而成),这三件工作件中工作温度最高是射咀身,它的身外表
面是设定在450-480℃之间,探温针探测位置距离发热套约有5-8mm。观察发现,设定在
450℃,在够温时,发热套的外观是暗红色的,超过500℃,射咀射在全新状态下,内孔是
光滑不藏料的。再经过一段时间生产,锌合金液在内孔不同程度不同位置有凹孔出现,特别
是中间高温部位;由于有凹孔藏料,合金中的铝成分与射咀身腐蚀的铁质成分化合成AlFe化
合物,硬质物由此产生。
2)除了以上办法外,需控制水口料或二次再生料的干净程度,电镀废品不能回炉使用,
因回炉的废品中有镍、铬及氧化物存在,这两样金属难以熔于合金熔液中,会以颗粒存在合
金中,因此就有可能混入生产压铸件中,造成抛光后现出硬质点的现象。
3)在手机壳加工中,除以下两种方式去避免外,从压铸机的角度看,改变压射比和模具
浇口、溢流槽的合理配合,也可以有效消除产品中夹杂的存在,利于充型和排气排渣,达到
将杂质和冷料快速充分排到溢流槽中的目的。
四、产品产生缩孔
缩孔的产生因素是多方面原因引起的,可能的原因有:
(1) 水口料重熔次数过多
(2) 废料使用比例过大
(3) 模具设计不合理,困气、卷气、走料尾端压力和温度不足等
(4) 生产用料被铅、镉、和镍元素污染
(5) 模具冷却水设置不合理或使用不当
(6) 离型剂喷涂量过大藏水,浓度太大造成
(7) 压铸工艺压力和速度不足
(8) 模具批锋太大,压力损失,充型不饱满
下面以手机电池盖产生缩孔分析作为案例三进行说明。
(1) 产品:手机壳大号电池盖
1)重量60g
2)材料:Zamak3
3)压铸设备:DC88热室压铸机
4)产品特征:产品的前方有一条3mm的凹槽
(2) 缺陷情况
在压铸过程中,毛坯产品有不足60%的合格率,主要现象是排冷料口和R斜面水纹和
缩孔现象严重。
(3) 应急改良办法
1)如图4所示,从产品的右上方接驳一条弯形流道,开设补充浇口,以解决水纹与缩孔
现象。
2)原因分析:因产品的面部有一条3mm的凹槽,在型腔中这凹槽给充型带来较大的阻
力,压力和速度受阻挡和损失,造成凹槽后面区域充型缓慢、压铸疏松,余留水纹,排气排
冷料过慢,引起缩孔。
3) 从产品右方增加了补充流道后,充型压力、速度和模具温度得到有效补充,从而解
决了缩孔难题,提高难度了质量和产量。
五、结束语
从以上锌合金压铸件的三个疑难问题的应对案例可见,有效地解决问题的关键为:模具
的流道、浇口和运水的设置设计的合理性,是有提高产品质量的关键;薄壁产品压铸,充型
条件有较高要求,体现在合金熔液的温度控制,热作件的一期检查和更换;水口料的使用比
例和重复回炉次数的控制有密切关系。
在锌合金压铸中,产品结构的差异,模具设计的技巧有所不同,技术的探讨和成熟设计
是实践和不断总结经验中得出的。