瓦斯管路阻力损失计算公式推导(一)
瓦斯抽放系统管路阻力损失计算的探讨
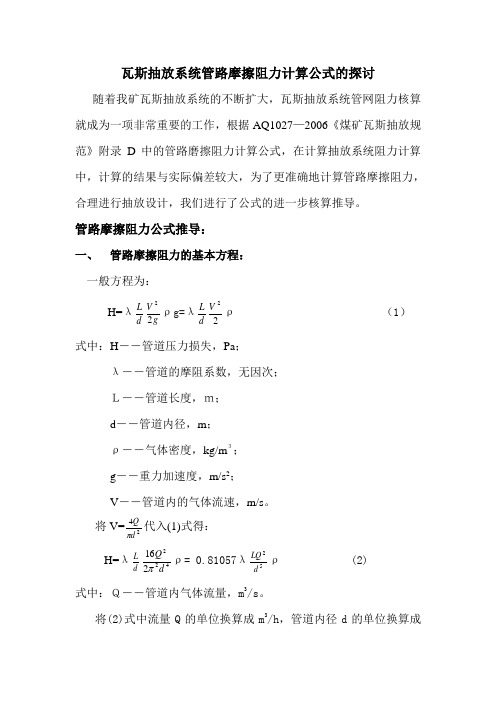
瓦斯抽放系统管路摩擦阻力计算公式的探讨随着我矿瓦斯抽放系统的不断扩大,瓦斯抽放系统管网阻力核算就成为一项非常重要的工作,根据AQ1027—2006《煤矿瓦斯抽放规范》附录D 中的管路磨擦阻力计算公式,在计算抽放系统阻力计算中,计算的结果与实际偏差较大,为了更准确地计算管路摩擦阻力,合理进行抽放设计,我们进行了公式的进一步核算推导。
管路摩擦阻力公式推导:一、 管路摩擦阻力的基本方程: 一般方程为:H=λd L g V 22ρg=λd L 22V ρ (1)式中:H ――管道压力损失,Pa ; λ――管道的摩阻系数,无因次; L――管道长度,m; d ――管道内径,m ; ρ――气体密度,kg/m 3; g ――重力加速度,m/s 2; V ――管道内的气体流速,m/s 。
将V=24dQπ代入(1)式得:H=λd L 422216dQπρ= 0.81057λ52dLQ ρ (2)式中:Q――管道内气体流量,m 3/s 。
将(2)式中流量Q 的单位换算成m 3/h ,管道内径d 的单位换算成cm ,则:H = 625.44λ52dLQ ρ (3)式中:H ――管道压力损失,Pa ; λ――管道摩阻系数,无因次; L――管道长度,m;Q ――管道内的气体流量,m 3/h ;d ――管道内径,cm ; ρ――气体密度,kg/m 3。
公式(3)式即为管道摩擦阻力计算的基本方程。
这与AQ1027—2006《煤矿瓦斯抽放规范》附录D 中的管路磨擦阻力计算公式基本一致。
二、 管道摩擦阻力公式推导: 1.钢管的摩阻系数钢管的摩阻系数基本计算公式为:λ=0.11(d∆+1923Qd ν)0.25 (4)式中:Q――管道内瓦斯流量,m 3/h 。
λ――管道摩阻系数,无因次;Δ――管道内壁的当量绝对粗糙度(Δ=0.017),cm ; d ――管道内径,cm ; ν――瓦斯的运动粘度,m 3/s 将(4)式代入(3)式,则: H =68.8(d∆+1923Q d ν)0.2552d LQ ρ (5)(5)式即为钢管摩擦阻力计算工况状态下的基本公式由于(5)式中的流量Q 、密度ρ和运动粘度ν均为工况状况下的参数,但在实际计算过程中难以预先确定管道内每段的实际工况,特别是管内气体压力。
管道阻力损失计算公式

管道阻力损失计算公式
管道阻力损失是流体在管道中经历的机械能损失,由其内的摩擦力,压力损失和间断损失组成。
管道阻力损失的计算公式是:
ΔP = L × 0.109 × (V²/ D4) × (f / 2g)
ΔP:管道阻力损失,单位是KPa;
L:管道总长度,单位是m;
V:流体流速,单位是m/s;
D:管道内径,单位是m;
f:管道内摩擦系数;
2g:重力加速度,一般把2g定为9.8。
管道阻力损失计算公式可以帮助我们计算管道中流体的机械能损失,从而更好地控制管道的设计和运行。
管道阻力损失的计算公式可以用于计算水管、汽油管、空气管、蒸汽管等各种流体的阻力损失。
例如,可以用来计算水管中水流的阻力损失,计算公式如下:
ΔP = L × 0.109 × (V²/ D4) × (0.02 / 2g)
ΔP:管道阻力损失,单位是KPa;
L:管道总长度,单位是m;
V:水流流速,单位是m/s;
D:管道内径,单位是m;
0.02:水流的摩擦系数;
2g:重力加速度,一般把2g定为9.8。
通过计算管道的阻力损失,我们可以更好地控制管道的运行,从而更有效地利用管道的资源。
管道阻力损失的计算公式实际上是一种能量守恒定律,它也可以用于分析水力学系统中流体的流动特性,从而发现和解决流体流动中的问题。
总之,管道阻力损失计算公式是一个非常有用的工具,可以帮助我们计算管道中流体的机械能损失,更好地控制管道的设计和运行。
【精选】管道内的局部阻力及损失计算
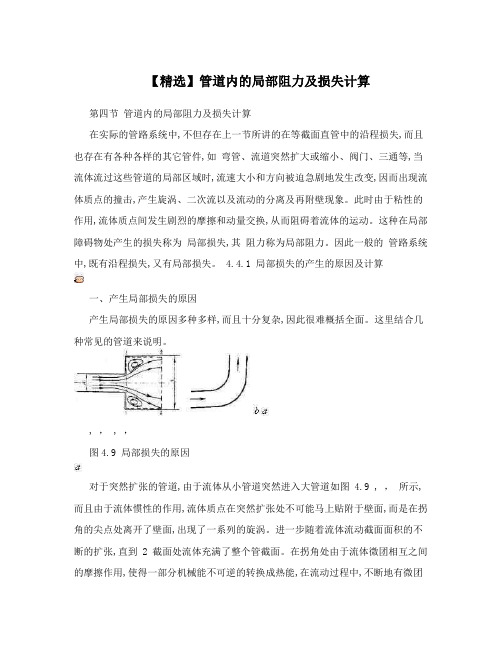
【精选】管道内的局部阻力及损失计算第四节管道内的局部阻力及损失计算在实际的管路系统中,不但存在上一节所讲的在等截面直管中的沿程损失,而且也存在有各种各样的其它管件,如弯管、流道突然扩大或缩小、阀门、三通等,当流体流过这些管道的局部区域时,流速大小和方向被迫急剧地发生改变,因而出现流体质点的撞击,产生旋涡、二次流以及流动的分离及再附壁现象。
此时由于粘性的作用,流体质点间发生剧烈的摩擦和动量交换,从而阻碍着流体的运动。
这种在局部障碍物处产生的损失称为局部损失,其阻力称为局部阻力。
因此一般的管路系统中,既有沿程损失,又有局部损失。
4.4.1 局部损失的产生的原因及计算一、产生局部损失的原因产生局部损失的原因多种多样,而且十分复杂,因此很难概括全面。
这里结合几种常见的管道来说明。
, , , ,图4.9 局部损失的原因对于突然扩张的管道,由于流体从小管道突然进入大管道如图 4.9 , ,所示,而且由于流体惯性的作用,流体质点在突然扩张处不可能马上贴附于壁面,而是在拐角的尖点处离开了壁面,出现了一系列的旋涡。
进一步随着流体流动截面面积的不断的扩张,直到 2 截面处流体充满了整个管截面。
在拐角处由于流体微团相互之间的摩擦作用,使得一部分机械能不可逆的转换成热能,在流动过程中,不断地有微团被主流带走,同时也有微团补充到拐角区,这种流体微团的不断补充和带走,必然产生撞击、摩擦和质量交换,从而消耗一部分机械能。
另一方面,进入大管流体的流速必然重新分配,增加了流体的相对运动,并导致流体的进一步的摩擦和撞击。
局部损失就发生在旋涡开始到消失的一段距离上。
图4.9,,给出了弯曲管道的流动。
由于管道弯曲,流线会发生弯曲,流体在受到向心力的作用下,管壁外侧的压力高于内侧的压力。
在管壁的外侧,压强先增加而后减小,同时内侧的压强先减小后增加,这样流体在管内形成螺旋状的交替流动。
综上所述,碰撞和旋涡是产生局部损失的主要原因。
当然在 1-2之间也存在沿程损失,一般来说,局部损失比沿程损失要大得多。
瓦斯供气中损失量的分析与计算
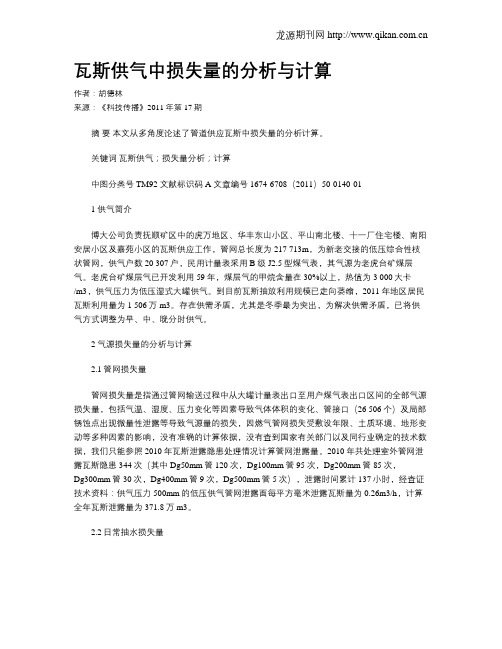
瓦斯供气中损失量的分析与计算作者:胡德林来源:《科技传播》2011年第17期摘要本文从多角度论述了管道供应瓦斯中损失量的分析计算。
关键词瓦斯供气;损失量分析;计算中图分类号TM92 文献标识码A 文章编号 1674-6708(2011)50-0140-011 供气简介博大公司负责抚顺矿区中的虎万地区、华丰东山小区、平山南北楼、十一厂住宅楼、南阳安居小区及嘉苑小区的瓦斯供应工作,管网总长度为217 713m,为新老交接的低压综合性枝状管网,供气户数20 307户,民用计量表采用B级J2.5型煤气表,其气源为老虎台矿煤层气。
老虎台矿煤层气已开发利用59年,煤层气的甲烷含量在30%以上,热值为3 000大卡/m3,供气压力为低压湿式大罐供气。
到目前瓦斯抽放利用规模已走向萎缩,2011年地区居民瓦斯利用量为1 506万m3。
存在供需矛盾,尤其是冬季最为突出,为解决供需矛盾,已将供气方式调整为早、中、晚分时供气。
2 气源损失量的分析与计算2.1管网损失量管网损失量是指通过管网输送过程中从大罐计量表出口至用户煤气表出口区间的全部气源损失量,包括气温、湿度、压力变化等因素导致气体体积的变化、管接口(26 506个)及局部锈蚀点出现微量性泄露等导致气源量的损失,因燃气管网损失受敷设年限、土质环境、地形变动等多种因素的影响,没有准确的计算依据,没有查到国家有关部门以及同行业确定的技术数据,我们只能参照2010年瓦斯泄露隐患处理情况计算管网泄露量。
2010年共处理室外管网泄露瓦斯隐患344次(其中Dg50mm管120次,Dg100mm管95次,Dg200mm管85次,Dg300mm管30次,Dg400mm管9次,Dg500mm管5次),泄露时间累计137小时,经查证技术资料:供气压力500mm的低压供气管网泄露面每平方毫米泄露瓦斯量为0.26m3/h,计算全年瓦斯泄露量为371.8万m3。
2.2日常抽水损失量目前在用日常抽水水包398个,根据长年测试统计数据确认平均每个水包抽5min的水,根据实际测定抽子的上水量为0.07m3/min,平均每个水包的抽水量为0.35m3,即水包抽水平均损失的瓦斯量为0.35m3。
瓦斯流量计算公式
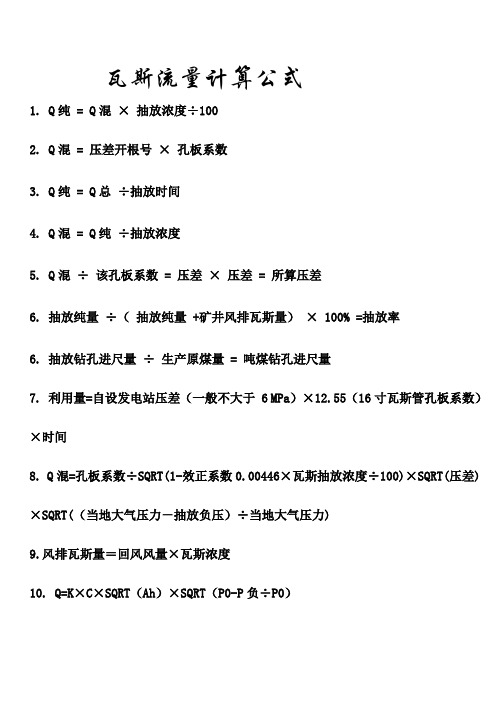
瓦斯流量计算公式
1. Q纯 = Q混×抽放浓度÷100
2. Q混 = 压差开根号×孔板系数
3. Q纯 = Q总÷抽放时间
4. Q混 = Q纯÷抽放浓度
5. Q混÷该孔板系数 = 压差×压差 = 所算压差
6. 抽放纯量÷(抽放纯量 +矿井风排瓦斯量)× 100% =抽放率
6. 抽放钻孔进尺量÷生产原煤量 = 吨煤钻孔进尺量
7. 利用量=自设发电站压差(一般不大于 6 MPa)×12.55(16寸瓦斯管孔板系数)×时间
8. Q混=孔板系数÷SQRT(1-效正系数0.00446×瓦斯抽放浓度÷100)×SQRT(压差)×SQRT((当地大气压力-抽放负压)÷当地大气压力)
9.风排瓦斯量=回风风量×瓦斯浓度
10. Q=K×C×SQRT(Ah)×SQRT(P0-P负÷P0)
11.相对瓦斯涌出量=绝对量×60×20÷平均日产量
12.风排瓦斯量=回风风量×瓦斯浓度
13.绝对瓦斯涌出量=风量×瓦斯浓度×抽放量。
管路长度压力损失计算公式

管路长度压力损失计算公式在工程领域中,管路长度压力损失是一个重要的参数,它可以帮助工程师们准确地计算管路系统的性能和能耗。
管路长度压力损失是指流体在管路中流动时由于管道摩擦和弯头、阀门等元件的阻力而导致的压力损失。
在设计和运行管路系统时,准确地计算管路长度压力损失对于保证系统的正常运行和提高系统的效率非常重要。
管路长度压力损失的计算公式是基于流体力学和流体动力学的理论基础而建立的,它可以通过管道的长度、流速、管道直径、流体密度和粘度等参数来计算。
通常情况下,管路长度压力损失可以用以下的公式来表示:ΔP = f (L/D) (ρv^2/2)。
其中,ΔP表示管路长度压力损失,f表示摩擦阻力系数,L表示管道长度,D表示管道直径,ρ表示流体密度,v表示流速。
在这个公式中,摩擦阻力系数f是一个重要的参数,它是根据流体在管道内的流动状态和管道壁面的粗糙度来确定的。
通常情况下,可以通过查表或者使用经验公式来计算摩擦阻力系数。
管道长度L、管道直径D、流体密度ρ和流速v都是可以通过实际测量或者计算得到的参数。
通过上述公式,我们可以看到管路长度压力损失与管道长度、管道直径、流速和流体密度等参数都有关系。
在实际工程中,我们可以根据具体的管路系统参数来计算管路长度压力损失,从而为系统的设计和运行提供重要的参考依据。
在工程实践中,准确地计算管路长度压力损失对于保证管路系统的正常运行和提高系统的效率非常重要。
首先,管路长度压力损失的准确计算可以帮助工程师们合理地选择管道的直径和长度,从而减小管道系统的能耗和运行成本。
其次,管路长度压力损失的准确计算也可以帮助工程师们预测管道系统的性能,从而及时地发现和解决系统中可能存在的问题。
在实际工程中,为了准确地计算管路长度压力损失,工程师们需要充分考虑管道系统的实际情况,包括管道的布置方式、管道材质、流体的物性参数等。
此外,工程师们还需要使用适当的计算方法和工具来进行计算,以确保计算结果的准确性和可靠性。
瓦斯抽放阻力计算

ν瓦斯ν空气ν0C L(m)d(mm)ρ瓦ρ空ρΔ(mm)P 0P 孔(Pa)000.0000150.412406260.715 1.3 1.2910.1710132514000000.0000150.412504800.715 1.3 1.2910.1710132514000000.0000150.4513204320.715 1.3 1.290.1710132514000000.0000150.4512304320.715 1.3 1.290.1710132514000000.0000150.3904320.715 1.3 1.2910.1710132514000000.0000150.3904320.715 1.3 1.2910.1710132514000000.0000150.3904320.715 1.3 1.2910.1710132514000000.0000150.3904320.715 1.3 1.2910.1710132514000000.0000150.3904320.715 1.3 1.2910.1710132514000000.0000150.3904320.715 1.3 1.2910.1710132514000000.0000150.3904320.715 1.3 1.2910.1710132514000000.0000150.3904320.715 1.3 1.2910.1710132514000000.0000150.3904320.715 1.3 1.2910.1710132514000管网总阻力=(1)+(2)数值250400.41、抽放瓦斯管摩擦阻力4、抽放泵流量计算H 摩—管路的摩擦阻力,PaQ b —抽采瓦斯泵的额定流量,L—管路长度,mQ 0—标准状态下的混合瓦斯流量,m 3/hT 0—标准状态下的绝对温度,Kt—管路中的气体温度,℃Q—最大的设计抽采瓦斯抽采量,m 3/min X—抽采泵入口处预计的瓦斯浓度d—管路内径,mmP—抽采泵入口绝对压力(Pa); ν0—标准状态下的混合瓦斯运动粘度,m 2/sρ—管道内混合瓦斯密度,kg/m 3Δ—管路内壁的当量绝对粗糙度,mmP 0—标准大气压力,101325PaP—管道内气体绝对压力,PaT—管路中的气体温度为t时的绝对温度,K5.抽采泵工况流量Q g —工况状态下的抽采泵流量(m 3/min);Q b —标准状态下抽采泵的计算流量(m 3/min);(1)摩擦阻力合计(2)局部阻力0052025.00052.1921069PT T P d Q L Q d v d H ρ)(摩+∆⨯=KX Q b Q =η00=PT T P Q Q b g0.82数值0%250η——泵的机械效率,取80%K ——抽采能力富余系数,可取1.2~1.8t—抽采泵入口瓦斯的温度(℃)。
管道阻力的基本计算方法

管道阻力的基本计算方法管道阻力是指液体在流动过程中受到的摩擦力和阻力,它是影响管道流量和压力损失的主要因素之一、管道阻力的基本计算方法包括经验公式法、实验法和数值模拟法。
1.经验公式法:经验公式法是根据实际操作经验总结出来的计算方法。
经验公式法包括达西-魏兹巴赫公式、普朗特公式等。
-达西-魏兹巴赫公式:达西-魏兹巴赫公式是最常用的计算管道阻力的经验公式之一,表示为:Rf=λ(L/D)(V^2/2g)其中,Rf是单位长度的管道阻力,λ是阻力系数,L是管道长度,D 是管道内径,V是流速,g是重力加速度。
-普朗特公式:普朗特公式是用于计算气体在管道中流动时的阻力的经验公式,表示为:Rf=λ(L/D)KρV^2其中,K是一修正系数,ρ是气体密度。
2.实验法:实验法是通过实验来测量管道阻力,并将实验结果用于计算。
实验法一般需要进行水力实验或风洞实验,根据实验结果建立经验公式。
-水力实验:水力实验是通过在实验室中建立一段具有标准尺寸的管道,在实验过程中测量流量、压力等参数,从而计算管道阻力。
-风洞实验:风洞实验是用于测量气体在管道中的阻力的方法。
通过在风洞中设置一段具有标准尺寸的管道,在实验过程中测量流动参数,计算管道阻力。
3.数值模拟法:数值模拟法是利用计算机进行流体力学计算,通过数值模拟管道内流体的运动和阻力分布,从而得到管道阻力。
数值模拟法精度较高,能够考虑更多的因素和复杂的条件。
数值模拟法可以利用有限元、有限差分、计算流体力学(CFD)等方法进行计算。
利用计算机软件,将管道的几何形状、边界条件、流体性质等参数输入模拟软件,通过求解流体动力学方程,得到流场图像、速度分布、压力分布等结果,从而计算出管道阻力。
总结起来,管道阻力的基本计算方法包括经验公式法、实验法和数值模拟法。
不同的计算方法适用于不同的情况,工程师可以根据具体需求选择合适的方法进行计算。
- 1、下载文档前请自行甄别文档内容的完整性,平台不提供额外的编辑、内容补充、找答案等附加服务。
- 2、"仅部分预览"的文档,不可在线预览部分如存在完整性等问题,可反馈申请退款(可完整预览的文档不适用该条件!)。
- 3、如文档侵犯您的权益,请联系客服反馈,我们会尽快为您处理(人工客服工作时间:9:00-18:30)。
瓦斯管道阻力损失计算公式推导(一)
一、 管道摩擦阻力的基本方程
1.一般方程
H=λd L γg
V 22
(1)
式中:H ――管道压力损失,mmH 2O ; λ――管道的摩阻系数,无因次; L――管道长度,m; d ――管道内径,m ; γ――瓦斯容重,kg/m 3; g ――重力加速度,m/s 2; V――管道内的瓦斯流速,m/s 。
以V=
2
4d Q
π代入(1)式得:
H=λd L γ4
22216d
g Q π= 0.08263λ52d LQ γ (2) 式中:Q――管道内瓦斯流量,m 3/s 。
将流量Q 的单位换算成m 3/h ,管道内径d 的单位换算成cm ,则: H = 64λ
5
2d LQ γ (3)
(3)式即为《煤矿抽放瓦斯》209页给出的摩擦阻力计算公式,但该书中对流量Q和管径d 给出的单位是错的,应分别为m 3/h 和cm 。
2.低压管道摩擦阻力的基本方程
因Q=Q 0
0PT T
P ,γ=γ0
T
P PT 00
,代入(3)式得: H= 64λ5
2
0d LQ γ
0PT T
P (4) 式中:H ――管道压力损失,mmH 2O ; λ――管道摩阻系数,无因次; L――管道长度,m;
Q 0――标准状态下内的瓦斯流量,Nm 3/h ;
d ――管道内径,cm ;
γ0――标准状态下的瓦斯容重,kg/Nm 3; P 0――标准状态下的大气绝对压力,Pa ; P ――管道内的瓦斯绝对压力,Pa ;
T――管道内的瓦斯绝对温度(T=273+t ),ºK; T0――标准状态下的瓦斯绝对温度(T0=273),ºK; t ――管道内瓦斯的温度,℃。
因低压管道(相对压力≤0.005MPa )的绝对压力P 与标准大气压力P 0的差值较小,为了简化计算,可以忽略压力的影响,将(4)式简化成下式:
H= 64λγ
5
2
d LQ 0
T T
(5) 因瓦斯的相对比重S=
空γγ,则γ0=Sγ空0
,代入(5)式得:
H= 83λS
5
2d LQ 0
0PT T
P (6) 式中:S――瓦斯的相对比重(空气=1);
γ
空0
――空气的比重(γ
空0
=1.293),kg/Nm 3。
(6) 式即为《煤气设计手册》下册53页低压煤气管道的摩擦阻力计算公式(5-4-1)。
二、
钢管摩阻系数的计算公式
钢管的摩阻系数按下式计算: λ=0.11(
d ∆+Re
68)0.25
(7) 式中:λ――管道摩阻系数,无因次;
Δ――管道内壁的当量绝对粗糙度(Δ=0.017);cm ; d ――管道内径,cm ; Re ――雷诺数,无因次。
Re =
ν
Vd
(8)
式中:V――管道内瓦斯平均流速,m/s ;
d ――管道内径,m;
ν――瓦斯的运动粘度,m 3/s 。
以V=
2
4d
Q
π代入(8)式得:
Re =
d
Q
νπ4 (9) 式中:Q――管道内瓦斯流量,m 3/s 。
将上式中流量Q的单位换算成m 3/h ,管道内径d 的单位换算成cm ,则: Re =
d
Q
νπ3600400 (10)
将Re 代入(7)式得: λ=0.11(
d
∆
+1923Q d ν)0.25 (11)
因ν=ρμ,而μ=μ0C
T C
T ++0
5
10。
⎪⎪⎭
⎫ ⎝⎛T T
,ρ=ρ0T P PT 00
,则: ν=00ρμC
T C
T ++0
5
10。
⎪⎪⎭
⎫ ⎝⎛T T 00PT T
P =ν0C T C T ++0
5
10。
⎪⎪⎭
⎫ ⎝⎛T T
0PT T
P
又因Q= Q 0
0PT T
P ,则代入(11)式得: λ=0.11(
d ∆
+19230
0Q d νC T C T ++05
10。
⎪⎪⎭
⎫
⎝⎛T T )0.25
(12) 为了简化起见,可以忽略温度对λ的影响,将(12)式简化成下式: λ=0.11(
d ∆
+19230
0Q d ν)0.25 (13) (13)式即为钢管摩阻系数的简化计算公式。
三、
低压钢管摩擦阻力的计算公式
将(13)式代入(5)式,则:
H= 7γ0520d LQ (d ∆+192320Q d ν)0.250
T T
(14)
(14)式与《煤气设计手册》下册56页的计算公式(5-4-10)是基本一致的,但该公式将γ解释为煤气的相对比重是错误的,应为煤气的容重(该书为重度,其含义是一致的),该公式还令管道内的温度t=0℃,所以公式中没有0
T T。
四、
低压瓦斯管道(钢管)压力损失计算公式
1.
低压瓦斯管道阻力计算公式推导
令:S =γ0/γ
空0
,则γ0=S γ
空0
,又因《矿井抽放瓦斯工程设计规范》是
将20℃作为标准温度,即T 0=273+20=293。
而抽放管道内的瓦斯温度一般为20℃,即T=273+20=293。
则代入(14)式得:
H=7S γ空0520d LQ (d ∆+19230
0Q d
ν)0.25
令
K
1
=7γ空0
(
d ∆
+19230
0Q d ν)0.25,则: H=5
2
0Kd LSQ (15)
式中:H――管道压力损失,mmH 2O; L――管道计算长度,m;
γ0――标准状况下瓦斯的容重,kg/Nm 3; γ
空0
――标准状况下空气的容重(γ
空
=1.293),kg/Nm 3 ;
Q0――标准状态下管道的瓦斯流量,Nm 3/h ; d ――管道直径,cm ;
Δ――管壁内的当量绝对粗糙度,cm; ν0――标准状态下瓦斯的运动粘度,m 2
/s ; S――瓦斯对空气的相对比重(空气=1); K――系数。
(15)式与《矿井抽放瓦斯工程设计规范》中的抽放管道阻力计算公式是基本一致的,只是瓦斯相对比重的符号不同而已。
2.系数K 值的推导
因Q0=10000
436000
2⨯V d π=0.09лd 2V 0,则:
K 1=9 (d ∆
+19230
009.0dV πν)0.25 =9 (
d ∆
+68000
0dV ν)0.25 式中:V 0――标准状态下管道内瓦斯的平均流速,m/s 。
取平均流速V 0=10m/s,则:
K 1=9 (d ∆
+680d
0ν)0.25 =
25
.09d (Δ+680ν0)0.25
则:K=25
.0025
.0)680(9ν+∆d (16)
因钢管的当量绝对粗糙度Δ=0.017cm,瓦斯浓度按30%计算,则瓦斯的运动粘度ν0=13.5151×10-6 m 2/s,则:
K=25
.0625.0)105151.13680017.0(9-⨯⨯+d =0.2762d 0.25
(17)
按(17)式计算不同管径的系数K值见表1,从表1可以看出,其计算结果比《煤矿瓦斯抽放手册》209页给出的系数K 值偏低。
初步分析其原因,《煤矿瓦斯抽放手册》所给出的系数K 值有可能是按《煤气设计手册》的错误公式(56页的5-4-10)推导计算的,因为该公式误将γ当作煤气的相对比重(应为瓦斯容重),即:
H=7S 520d LQ (d ∆+19230
0Q d
ν)0.25 (18)
根据(18)式应令:
K 1=7 (d ∆
+19230
0Q d ν)0.25 =
25
.07d (Δ+680ν0)0.25
则有:K=25.0025.0)680(7ν+∆d (19)
将有关数据代入(19)式得:
K=25
.0625.0)
105151.13680017.0(7-⨯⨯+d =0.3551d 0.25
(20) 按(20)式计算不同管径的系数K值见表2。
从表2中可以看出,表中的K值与《煤矿瓦斯抽放手册》209页给出的系数K 值基本一致,特别是当管径d ≥100mm 时非常接近。
说明上述推断是有一定根据的。
无论是按正确公式还是按错误公式计算的系数K值,都是随着管径的增大而
增大。
所以,《煤矿瓦斯抽放手册》中对管径d>150mm的K值都取0.71是不合适的,按此公式计算出来的管道阻力是偏大的。
表1 不同管径的系数K值表(按正确公式计算结果)
表2 不同管径的系数K值表(按错误公式计算结果)。