三氯氢硅氢气还原工序操作指导书
试说明三氯氢硅的合成原理

试说明三氯氢硅的合成原理
三氯氢硅的合成原理如下:
1. 制备原料:将硅粉和氯化氢进行反应,制备出三氯化硅。
Si + 3HCl →SiCl3 + H2
2. 氯化氢和硅源反应:将三氯化硅和氢气进行反应,在高温下制备出三氯氢硅。
SiCl3 + H2 →H3SiCl
3. 精制和稳定化处理:三氯氢硅经过精制和稳定化处理后,即可成为工业上所使用的三氯氢硅。
三氯氢硅的合成原理,主要就是通过氯化氢和硅源的反应,制备出三氯化硅,再经过氢气还原后得到三氯氢硅。
整个反应过程需要在高温下进行,并需要精制和稳定化处理,以保证制备出的三氯氢硅的纯度和质量。
三氯氢硅合成操作规程
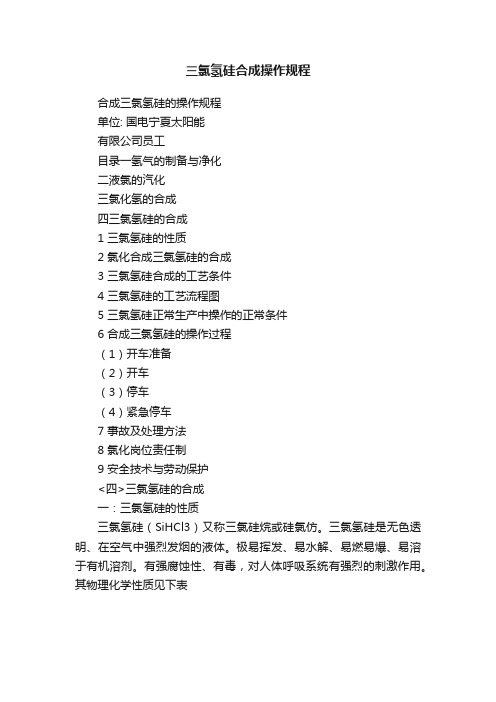
三氯氢硅合成操作规程合成三氯氢硅的操作规程单位: 国电宁夏太阳能有限公司员工目录一氢气的制备与净化二液氯的汽化三氯化氢的合成四三氯氢硅的合成1 三氯氢硅的性质2 氯化合成三氯氢硅的合成3 三氯氢硅合成的工艺条件4 三氯氢硅的工艺流程图5 三氯氢硅正常生产中操作的正常条件6 合成三氯氢硅的操作过程(1)开车准备(2)开车(3)停车(4)紧急停车7 事故及处理方法8 氯化岗位责任制9 安全技术与劳动保护<四>三氯氢硅的合成一:三氯氢硅的性质三氯氢硅(SiHCl3)又称三氯硅烷或硅氯仿。
三氯氢硅是无色透明、在空气中强烈发烟的液体。
极易挥发、易水解、易燃易爆、易溶于有机溶剂。
有强腐蚀性、有毒,对人体呼吸系统有强烈的刺激作用。
其物理化学性质见下表三氯氢硅的物理化学性质附:四氯化硅的性质四氯化硅(SiCl4)是无色透明、无极性、易挥发、有强烈刺激性的液体。
水解后生成二氧化硅和氯化氢。
可与苯、乙醚、氯仿及挥发油混合;与醇反应生成硅酸酯。
因其易水解,并生成氯化氢,故它具有强腐蚀性。
四氯化硅的性质二:氯化合成三氯氢硅的原理。
氯化合成三氯氢硅是在氯化沸腾反应炉中进行的,它是将干燥好的HCL通入硅粉沸腾层反应,生成三氯氢硅。
其主要的反应式为:Si + 3HCL = SiHCL3 + H2反应温度以280—320℃为宜,温度过高,过低都会发生副反应,反应产物中其他杂质含量也会相应增高Si +4HCL = SiCL4 + 2H2(温度高于350℃)Si +4HCL = SiH2CL2 + 2H2(温度低于280℃)合成三氯氢硅过程中,反应是一个复杂的平衡体系,可能有很多种物质同时生成,因此要严格的控制操作条件,才能得到更多的三氯氢硅。
三:三氯氢硅的合成工艺条件:(1)反应温度:280—320℃(2)反应压力:一般不超过0.05MPa(3)硅粉粒度:一级品,80—120目(4)催化剂用量:Si:CuCL2=100:(0.4~1)(5)氯化氢的纯度:96%以上,含水量0.05%~0.1%(6)氧和水:当Si和HCL中含水量为0.05%,SiHCL3含量小于80%;当Si和HCL中含水量为0.1%,SiHCL3含量可达90%(7)氢气对氯化氢的稀释:H2:HCL摩尔比为1:(3~5)为宜(8)料层高度:H=Q(硅)/(D(硅)×F)(9)产品质量要求:SiHCL3≥80%四:三氯氢硅合成工艺流程图如下图所示,干燥后的氯化氢气体先经缓冲罐(1),再经转子流量计以适当流量进入合成炉(4)中,与干燥器(2)干燥后的硅粉在280~320℃的温度范围内发生反应。
冷氢化操作规程

冷氢化操作规程一、工艺流程1岗位流程将经过干燥的硅粉、催化剂(氯化铜)和受热汽化混合的气体(四氯化硅、氯气、氯化氢)按照规定的摩尔比进入氢化反应炉(R3101)内,在汽化固流化床的条件下,反应生成三氯氢硅气体;工艺气体经过多级的除尘除杂、冷凝、分离、冷却过程后,废渣料进入四氯化硅蒸化罐分离四氯化硅,废料进入淋洗处理,冷却气体进入压缩机升压再次进入汽化混合工序,液化(四氯化硅、三氯氢硅和二氯二氢硅)输送进入精馏、精馏工序提纯至满足要求后,三氯氢硅送还原工序使用,四氯化硅再次送入汽化混合工序循环使用,少量的二氯二氢硅进入反歧化装置;从装置过滤、沉降、解析等装置收集的废气进入尾气淋洗塔处理,渣浆进入液体淋洗塔处理。
2 工艺流程简介首先将40-120目的工艺硅粉人工加入烘粉炉(E3108)蒸汽进行干燥,烘粉炉加入量5吨/批次,并通过氮气电加热器(E3107)置换、干燥硅粉,干燥器温度200℃,时间8小时除尽空气、水分后,向硅粉接受罐(V3106)、计量罐(V3107)进料。
将40-120目的催化剂(氯化铜)人工加入催化剂接受罐(V3108)进行氮气置换除尽空气、水分后,以氢气置换氮气氛围合格,根据硅粉进料而向计量罐(V3107)进料(硅粉与催化剂混合加入的质量比为100:2或100:1);外界氢气进入压缩机(C3101→C3102)气体压缩机增压至3.2MPa左右,由外界四氯化硅进入四氯化硅缓冲罐(V3101)增压输送至四氯化硅预热器(E3101),氢气和四氯化硅的加入摩尔比为2:1左右,预热后的氢气与四氯化硅进入按照规定的比例经过静态混合器(M3101)混合后进入四氯化硅汽化器混合,混合后的气体(四氯化硅、氢气、氯化氢)四氯化硅过热器继续汽化混合后,混合气进入电加热器升温至550℃左右。
预先将压缩氢气通入氢化炉内并注入一定的硅粉、催化剂底料,建立流化床之后,将四氯化硅与氢气混合气通入氢化炉流化床(R3101)内,在530-590℃、2.2-2.9MPa左右的气固流化床条件下,反应生成三氯氢硅气体。
氢化锂还原三氯氢硅制备硅烷.

氢化锂还原三氯氢硅制备硅烷沃银花 张金波 余京松氢化锂还原三氯氢硅制备硅烷是世界上工业化生产硅烷的方法之一。
使三氯氢硅或者四氯化硅进入熔融的KCL-LiCl 和氢化锂的混合盐中进行化学反应,即可制得硅烷。
反应中LiH,转化为LiCl,KCl 的作用仅仅是起到降低熔盐的熔点。
硅烷反应器中LiH 因为不断地转化为LiCl,所以必须补充KCl 以保持LiCl 与KCl 之间的1∶1比例,始终使熔盐熔点保持在315-425℃之间。
化学反应式: ,3431542533o KCl LiCl C SiHCl LiH SiH LiCl −+⎯⎯⎯⎯→+生产过程:熔盐(KCl 、LiCl )→加入LiH 、KCl,加热至熔。
通入SiHCl 3→产生硅烷,经过滤器→进入冷却器→低温吸附装置→硅烷液化器→硅烷气化后压缩充装钢瓶。
整个过程请见氢化锂还原三氯氢硅制备硅烷工艺流程图,其中包括硅烷制备系统,硅烷提纯系统和硅烷气化压缩系统。
A.硅烷制备系统主要设备及技术数据:1. 硅烷反应器。
外壳以钢板为材质,Ф127cm,H102cm,内衬耐火材料,反应室Ф61cm,H91cm.2.坑式加热炉。
上温区有三个3千瓦的加热原件,下温区有三个4千瓦的加热炉。
3.风机冷却装置。
4.三氯氢硅供给器。
不锈钢为材质,Ф51cm,H69cm 。
操作步骤:1.开始反应时,反应器中要有近100千克LiCl·KCl的熔盐。
LiCl:KCl为50:50(重量比)。
LiCl和KCl的熔点分别是614℃和776℃,50∶50的混合盐熔点为300℃左右。
事先将两种混合盐称取1千克放在长柄勺里,在煤气炉上加热熔融后倒入反应器,此时反应器的温度加热到500℃左右,随后逐渐加入混合盐,初始熔融的液相盐慢慢熔解加入的固相混合盐,经3-4小时整个反应器中的物料全部熔为液体。
2.加入氢化锂称取10千克氢化锂和57千克氯化钾混和均匀后,将混合物加放在反应器中已熔融的熔盐上面,反应器仍需维持在500℃左右。
三氯氢硅氢还原培训1

还原、氢化培训教材一、V1500单元(多晶硅沉积单元)的工序划分TCS蒸发T1200/1201还原T100/101钟罩清洗T800/801硅芯、硅棒化学腐蚀及洗涤T400废气处理T1000STC蒸发T1100/1101氢化T200/201冷却水单元T901供电单元二、主要设备三氯氢硅(TCS)蒸发器4个气体混合器18个(还原炉)、9个(氢化炉)还原炉18台四氯化硅(STC)蒸发器4个氢化炉9台三、工艺流程描述TCS蒸发、还原1、用屏蔽泵AP200A/B送来的高纯三氯氢硅进入三氯氢硅蒸发器T1200AB001、AB002和T1201AB001、AB002中。
2、在蒸发器的夹套中通入10bar蒸汽加热,使三氯氢硅汽化到压力为9bar(温度约120℃)送入混合器AM100与高纯氢气(压力9.5bar,温度约20℃)混合(摩尔比H2/TCS=5:1)后进入与还原炉尾气换热后从还原炉底部进入还原炉中。
尾气用130℃的热水进行冷却后送往V9200进行分离回收。
3、炉内的反应压力为6bar,反应温度控制在1080℃。
化学反应方程式为:SiHCl3+H2=Si+3HCl还原过程中还发生一系列副反应,产生大量四氯化硅。
反应产率大约为10~12kg/kg多晶硅;反应式如下:HCl+3SiHCl3SiCl4+2H2以及杂质还原反应:2BCl3+3H2 2B+6HCl2PCl3+3H2 2P+6HCl4、在还原炉的夹套和底座及窥视孔中均通入130℃的热水来冷却。
在电极夹套中通入30℃的去离子水来冷却电极。
5、窥视孔内部通入高纯氢气来吹扫窥视孔,以便于清楚观察炉内情况。
6、停炉后所有通130℃的热水来冷却的改为通入冷却水来降低炉温。
钟罩清洗1、将钟罩放在AB101中。
2、用5%的氢氧化钠溶液清洗钟罩。
3、去离子水在换热器AW101中与130℃热水(换热后从130℃降到90℃)换热后被加热(从20℃被加热到80℃)后用加压泵AP101/102加压后进入钟罩内通过喷头冲洗钟罩内壁,冲洗30分钟。
还原工序操作规程1

版次初版文件号编制审核文件名称还原车间工艺操作规程批准内蒙古锋威硅业有限公司技术文件还原车间工艺操作规程2009年 12 月版次初版文件号编制审核文件名称还原车间工艺操作规程批准目录第一章:原料及成品性质及质量指标第二章:车间操作规程1.主题内容及适用范围2.生产目的3.生产所需原材料4.原材料消耗情况5.生产原理6.工艺流程图及简述7.工艺控制点及控制指标8.设备一览表9.岗位操作9.1开车前的准备9.2开车操作9.3常规操作9.4停车操作9.4.1正常停车9.4.2紧急停车9.5其他辅助装置操作规范10.生产异常现象的产生原因及处理方法11.生产安全和环保注意事项12.规章制度12.1巡回检查制度(包括检查路线、时间频次、检查内容)12.2设备维护保养制度12.3交接班制度12.4操作人员岗位职责版次初版文件号编制审核文件名称还原车间工艺操作规程批准第一章:原料及成品性质及质量指标一、原料性质及质量指标1.氢气:分子式:H2分子量:2.0161.1物理性质密度:0.08987kg/m3(标况下);熔点:-259.2℃沸点:-252.78℃;水中溶解性:几乎不溶解于水;难以液化,液态氢是无色透明液体,有超导性;外观嗅味:无色、无味的气体。
1.2化学性质在常温下氢气的化学性质很稳定,但在加热或燃烧的情况下,氢气能与许多物质发生化学反应;氢气能与氧、碳、氮、氯分别反应生成水、碳氢化合物、氨和氯化氢;氢气能与活泼的碱金属反应,生成该金属的氢化物;氢气能与多种具有氧化性的化合物发生还原反应;氢气能与不饱和的烃类发生加成反应;1.3氢气的爆炸性:在空气中自燃温度为510℃,最小点火能量(空气中)为0.019H焦耳,爆炸极限:a、空气中4~74.5% b、氧气中4.5~95% c、氯气中5~87.5% d、氯化氢、氯气、氢气混合物中5~13%。
1.4主要质量指标氢气纯度(H2)≥99.999%氮气含量:(N2)<5 ppmw 甲烷含量:(CH4)<1ppmw氧气含量:(O2)<1ppmw 水含量:(H2O)<1 ppmw2. 氮气2.氮气分子式:N2 分子量:282.1物理性质:单质氮在常况下是一种无色无臭的气体,在标准情况下的气体密度是 1.25Kg/m3,熔点-210℃,沸点-198℃,临界温度为-147℃,它是个难于液化的气体。
三氯氢硅氢还原法和烷硅分解法
三氯氢硅氢还原法最早由西门子公司研究成功,有的文献上称此法为西门子法。
三氯氢硅氢还原法可分为三个重要过程:一是中间化合物三氯氢硅的合成,二是三氯氢硅的提纯,三是用氢还原三氯氢硅获得高纯硅多晶。
1.三氯氢硅的合成三氯氢硅(SiHCl3)由硅粉与氯化氢(HCl)合成而得。
化学反应式为上述反应要加热到所需温度才能进行。
又因是放热反应,反应开始后能自动持续进行。
但能量如不能及时导出,温度升高后反而将影响产品收率。
反应除了生成SiHCl3外,还有SiCl4或SiH2Cl2等氯硅烷以及其他杂质氯化物,如BCl3、PCl3、FeCl3、CuCl、TiCl3等。
合成设备可以是固定床,也可以是沸腾床,以沸腾床为优,可连续生产且效率高。
影响产率的重要因素是反应温度与氯化氢的含水量。
产出率与含水量的关系可粗略地由图2.1中的曲线表示。
此外,硅粉粗细对反应也有影响。
因此,对硅粉的粒度要有适当选择。
2.三氯氢硅的提纯三氯氢硅的提纯是硅提纯技术的重要环节。
在精馏技术成功地应用于三氯氢硅的提纯后,化学提纯所获得的高纯硅已经可以免除物理提纯(区域提纯)的步骤直接用于拉制硅单品,符合器件制造的要求。
精馏是近代化学工程有效的提纯方法,可获得很好的提纯效果。
三氯氢硅精馏一般分为两级,常把前一级称为粗馏,后一级称为精馏。
完善的精馏技术可将杂质总量降低到10-7~10-10量级。
精馏对于各种中间化合物有共同的提纯原理,将在2.2.1节中介绍讨论。
3.氢还原三氯氢硅用氢作为还原剂还原已被提纯到高纯度的三氯氢硅,使高纯硅淀积在1100~1200℃的热载体上。
载体常用细的高纯硅棒,通以大电流使其达到所需温度。
化学反应式为用于还原的氢必须提纯到高纯度以免污染产品。
如氢与三氯氢硅的克分子比值按理论配比则反应速度慢,硅的收率太低。
氢与三氯氢硅的配比在生产上通常选在20~30之间。
还原时氢通人SiHCl3液体中鼓泡,使其挥发并作为SiHCl3的携带气体。
三氯氢硅的工艺
三氯氢硅的工艺三氯氢硅的生产大多采用沸腾氯化法,主要包括氯化氢合成、三氯氢硅合成、三氯氢硅精制等工序。
氯气和氢气在氯化氢合成炉内通过燃烧反应生成氯化氢,氯化氢气体经空冷、水冷、深冷和酸雾捕集脱水后进人氯化氢缓冲罐,然后送三氯氢硅合成炉。
硅粉经过干燥后加入到三氯氢硅合成炉,与氯化氢在300℃左右的高温下反应,生成三氯氢硅和四氯化硅。
生成的粗三氯氢硅气体经过旋风分离和除尘过滤后,进入列管冷凝器进行水冷和深冷,不凝气通过液封送入尾气洗涤塔,处理后达标排放,冷凝液蒸馏塔分离提纯,通常采用二塔连续提纯,一塔塔顶排低沸物,二塔塔底排高沸物四氯化硅,同时塔顶出三氯氢硅产品。
第一节氯化氢合成工艺1.1氯化氢的性质氯化氢是无色有刺激性气体,熔点为-114.2℃,沸点为85℃,比热容为812.24J\kg℃,临界温度为51.28℃,临界压力为8266kPa。
干燥的氯化氢气体不具有酸的性质,化学性质不活泼,只有在高温下才发生反应。
氯化氢极易溶于水。
在标准情况下1体积水可溶解500体积氯化氢,溶于水后即得盐酸。
由于三氯氢硅生产主要需要氯化氢气体,所以本文对盐酸性质不做深入研究。
1.2 氯化氢合成条件氯化氢的合成是在特制的合成炉中进行的。
未了确保产品中不含有游离氯,氢气要较氯气过量15%~20%。
实际生产的炉中火焰温度在200℃左右。
由于反应是一个放热反应,为了不使反应温度过高,工业生产通过控制氯气和氢气的流量和在壁炉外夹套间通冷却水的办法控制氯化氢出炉温度小于350℃。
在生产中为确保安全生产,要求氢气纯度不小于98%和含氧不大于0.4%;氯气纯度不小于65%和含氢不大于3%。
1.3 氯化氢合成工艺氯化氢合成方程式:Cl2+H2→2HCl氯气经涡轮流量计计量氯气(氯气含量97%,压力为0.5MPa)含量进入氯气缓冲罐。
氢气经涡轮流量计计量氢气(含量98%,压力为0.09MPa)含量经分水罐脱水与循环氢经涡轮流量计进入氢气缓冲。
三氯氢硅氢还原制备多晶硅
二、三氯氢硅氢还原反应基本工艺流程
冷凝器 来自精馏工 序 蒸 发 器
F
L
氢 气 放 空 补 充 电 解 氢
蒸 发 器
F
还原炉
P T
P
P
蒸 发 器
冷却水 系统
多 晶 硅
热水制 备
回收H2
回收至合成工序 回收氯硅烷至精 馏
CDI 尾气回收 系统
SiHCI3氢还原工艺流程示意图
SiHCI3氢还原制备多晶硅主要工序包括混合气 氢还原制备多晶硅主要工序包括混合气 氢还原制备多晶硅主要工序包括 制备系统、氢还原炉、 系统、 制备系统、氢还原炉、DCS系统、电器控制系统和 系统 与之配套的冷却水系统、吹扫系统。 与之配套的冷却水系统、吹扫系统。 从精馏塔提纯出来的精制SiHCI3原料,按照还 原料, 从精馏塔提纯出来的精制 原料 原工艺条件的要求,经管道连续加入到SiHCI3蒸 原工艺条件的要求,经管道连续加入到 蒸 发器中。 发器中。经尾气回收系统收下来的氢气与来自电解 制氢系统的补充氢气在氢气总管中汇合后也进入蒸 发器中, 发器中,氢气总管的压力通过调节补充电解氢的流 和氢气放空的流量)控制, 量(和氢气放空的流量)控制,以实现进入蒸发气 的氢气压力恒定。 的氢气压力恒定。 蒸发器中的SiHCI3液体在一定的温度和压力下 蒸发器中的 液体在一定的温度和压力下 蒸发,氢气对SiHCI3液体进行集中鼓泡。形成一 液体进行集中鼓泡。 蒸发,氢气对 液体进行集中鼓泡 定体积比的H2和 的混合气体。 定体积比的 和SiHCI3的混合气体。SiHCI3蒸发 的混合气体 蒸发 所需的热量由专门的热水制备系统供给。 所需的热量由专门的热水制备系统供给。
3.在光和热的作用下,能使电子激发,从而使导电 在光和热的作用下,能使电子激发,
GMP-三氯氢硅工艺概述
GMP-三氯氢硅工艺概述wiki]多晶硅[/wiki]工艺流程[wiki]氢[/wiki]气制备与净[wiki]化工[/wiki]序在电解槽内经电解脱盐水制得氢气。
电解制得的氢气经过冷却、分离液体后,进入除氧器,在[wiki]催化剂[/wiki]的作用下,氢气中的微量氧气与氢气反应生成水而被除去。
除氧后的氢气通过一组吸附干燥器而被干燥。
净化干燥后的氢气送入氢气贮罐,然后送往氯化氢合成、三氯氢硅氢还原、四氯化硅氢化工序。
电解制得的氧气经冷却、分离液体后,送入氧气贮罐。
出氧气贮罐的氧气送去装瓶。
气液分离器排放废吸附剂、氢气脱氧器有废脱氧催化剂排放、干燥器有废吸附剂排放,均供货商回收再利用。
氯化氢合成工序从氢气制备与净化工序来的氢气和从合成气干法分离工序返回的循环氢气分别进入本工序氢气缓冲罐并在罐内混合。
出氢气缓冲罐的氢气引入氯化氢合成炉底部的燃烧枪。
从液氯汽化工序来的氯气经氯气缓冲罐,也引入氯化氢合成炉的底部的燃烧枪。
氢气与氯气的混合气体在燃烧枪出口被点燃,经燃烧反应生成氯化氢气体。
出合成炉的氯化氢气体流经空气冷却器、水冷却器、深冷却器、雾沫分离器后,被送往三氯氢硅合成工序。
为保证安全,本装置设置有一套主要由两台氯化氢降膜吸收器和两套盐酸循环槽、盐酸循环泵组成的氯化氢气体吸收系统,可用水吸收因装置负荷调整或紧急泄放而排出的氯化氢气体。
该系统保持连续运转,可随时接收并吸收装置排出的氯化氢气体。
为保证安全,本工序设置一套主要由废气处理塔、碱液循环槽、碱液循环泵和碱液循环冷却器组成的含氯废气处理系统。
必要时,氯气缓冲罐及管道内的氯气可以送入废气处理塔内,用氢氧化钠水溶液洗涤除去。
该废气处理系统保持连续运转,以保证可以随时接收并处理含氯气体。
三氯氢硅合成工序原料硅粉经吊运,通过硅粉下料斗而被卸入硅粉接收料斗。
硅粉从接收料斗放入下方的中间料斗,经用热氯化氢气置换料斗内的气体并升压至与下方料斗压力平衡后,硅粉被放入下方的硅粉供应料斗。
- 1、下载文档前请自行甄别文档内容的完整性,平台不提供额外的编辑、内容补充、找答案等附加服务。
- 2、"仅部分预览"的文档,不可在线预览部分如存在完整性等问题,可反馈申请退款(可完整预览的文档不适用该条件!)。
- 3、如文档侵犯您的权益,请联系客服反馈,我们会尽快为您处理(人工客服工作时间:9:00-18:30)。
三氯氢硅氢气还原工序操作指导书一、范围1、目的按本作业指导书对生产过程进行标准化作业,确保三氯氢硅氢气还原制取合格的多晶硅。
2、适用范围本作业指导书适用于在还原炉中用氢气还原三氯氢硅制取多晶硅工艺的操作。
二、工艺标准1、原理三氯氢硅和氢气在挥发器中以一定的摩尔配比混合后进入还原炉中,炉内安装的高纯硅芯载体通过石墨加热组件与电源连接,混合气在1080℃左右温度下反应,还原出的高纯硅沉积在硅芯载体上形成棒状多晶硅,反应后的尾气进入干法回收工序。
炉内主要反应是:SiHCl3+H2 Si+3HCl 氢还原反应4SiHCl3 Si+3SiCl4+2H2热分解反应2、原辅材料规格及要求2.1硅芯:直径¢7~8mm 长度2100mm 经过磨尖、切割开槽后再表面腐蚀、清洗、干燥。
要求如下:硅芯电阻率:N型电阻率≥50欧姆·厘米,P型硅芯不用。
每根硅芯电阻率检验不得少于七点(即硅芯七等分处各测一点)。
2.2高纯SiHCl3原料:来自提纯工序干法塔和合成塔产品,其质量要求为:产品SiHCl3含量>98%且Fe≤10PPb P≤0.02PPb Al≤10PPb B≤0.03PPb。
2.3高纯H2原料:来自干法回收工序回收H2和电解纯氢。
露点<-50℃,其中O2含量小于5ppm,HCl含量小于0.1%。
3、检验频次及方法每炉次需随机抽检一根硅棒,从石墨卡瓣位置以上50mm处截取150mm长硅棒进行钻芯,获得¢16mm左右硅棒料进行磷、硼杂质检验。
三、作业程序3.1 操作步骤(1)开炉准备A.通知提纯车间准备向还原送合格原料,根据原料来源分别打开相应产品储罐进料阀,使原料装入干法塔产品储罐或合成塔产品储罐中,待料位达到储罐容量的80%时停止接料,关闭进料阀并计录加料量。
(注意:加原料时不能开启尾气放空阀,利用塔压差可接料。
否则会影响提纯塔的工艺操作)B.向产品罐中缓慢充入H2使压力达到0.2Mpa,再分别打开挥发器SiHCl3进料阀(可用流量计旁路阀即可)、产品罐底部阀向挥发器供料,待料位稍超过挥发器加热管时停止加料,关挥发器SiHCl3进料旁路阀,转入调节阀自控。
C.检查电解纯氢补氢阀路、干法氢阀路、还原氢缓冲罐阀路是否处于待开状态,各储罐压力设定是否正常(干法氢缓冲罐压力设定为0.65Mpa、还原氢缓冲罐压力设定为0.35Mpa)。
D.将冷油分别用齿轮油泵打入保安油槽、液封油槽、热油槽中,打开相应油系统管路阀、开启还原炉冷却油泵,使油槽至油泵至汽化器至还原炉再回到油槽形成循环。
E.腐蚀装炉操作详见还原炉腐蚀装炉操作规程。
(2)开炉A.按照腐蚀装炉工序提供的启炉时间准备启炉。
B.还原炉启炉准备工作以及启炉操作见电器操作。
C.待三相硅芯均启动完毕后逐步调节电流保持硅芯发热体在1100℃温度下,炉内空烧30分钟,尾气走放空淋洗塔。
打开该炉炉前混合气调节阀,待按供料表1条件操作时(因条件1气量较小可用手动控制,条件2以后转入自动控制),尾气开始改为干法回收系统回收。
D.按供料表操作到停炉条件,在生产期间应严格控制反应炉温及反应料气用量,每半小时记录一次数据。
(3)停炉A.准备停炉前先关该炉炉前混合气阀(包括调节阀及其前后球阀),开炉前侧路氢向炉内赶气,尾气仍走干法系统。
B.逐步降低硅棒电流,大概1小时左右全部降到零。
(棒小时停炉稍快些,但过快会引起棒裂、脆)。
C.特殊情况下若挥发器所供炉子全停炉时,应关闭挥发器鼓泡氢、停止向挥发器供SiHCl3、关加热温水进出阀,挥发器内保持正压待用。
D.通知腐蚀装炉人员拆炉和重新装炉。
工员3.2异常情况现象的处理(1)多晶硅中产生夹层的主要原因及其消除方法A. 由于氧化而生成氧化夹层原因①氢气净化效果不好,露点或含氧量超标;②炉壁吸附着水分;③炉筒内漏油、底盘或电极有微量渗水;④操作不当引入氧气和水分。
消除方法①严格控制净化后的纯氢质量及干法系统回收氢质量,要求氢中氧含量≤5PPm,露点低于-50℃;②还原大厅内要求保持干燥;③开炉前按规定通入氮气、纯氢分别置换炉内的空气和氮气。
装拆炉时间要求短些,避免炉内在空气中暴露时间太长;停炉前控制炉筒出水温度~60℃;④炉壁、底盘、电极等处出现沙眼,有微量渗水时,可见泄漏处有白色水解物。
发现这种现象立即停炉,然后拆下清洗,清晰完毕进行焊补。
若电极泄漏,则调换一根,视炉内情况,可重新投入生产,也可拆下进行清洗再投入生产。
B. 由于无定形硅的生成而产生的夹层原因①硅芯高压启动后,表面温度若低于900℃进行还原反应,就容易生产无定形硅。
在硅芯发热体和新沉积的硅之间有一圈,许多情况是属于这一类。
②突然停电,硅棒温度迅速降低,而通入炉内的三氯氢硅和氢气尚未停止,此时反应仍在进行,于是产生一层无定形硅。
如果把这种硅棒重新击穿继续生产也要形成夹层。
消除方法③开炉时硅芯发热体表面温度达到1050℃后,才能通入混合气体。
④若停电时间较长,停电后还要继续开炉,则在停电前,首先关闭挥发器混合气体出口阀,停止三氯氢硅的通入,氢气从侧路进入炉内,把残余气体尽可能赶走,然后再氢气气氛中慢慢降温。
降温完毕继续通氢,直至重新开炉。
C 温度夹层:是由于生长过程中温度不稳定而形成的。
(2) 生产中由于某种原因需临时停炉,视炉内生长情况,若不再重新开炉,则按停炉操作步骤进行。
如准备再次开炉,则按下列步骤操作。
①关闭挥发器混合气体出口阀,氢经侧路直接进入炉内。
根据具体情况决定通氢时间的长短。
②将电流逐渐下降到零。
继续通氢,待排出故障后重新开炉,恢复生产。
(3) 突然停电①短期停电(指跳闸引起瞬时停电),发现停电后,操作者立即再次送电。
若送上了就继续生产;若送不上就关闭挥发器混合气体出口阀,继续通氢,保持正压。
随后同电工联系,查明原因,排除故障再重新生产。
②较长时间的停电,视炉内生长情况,若不再重新开炉,则按停炉操作步骤操作;如准备再次开炉,则按临时停炉操作步骤操作。
(4) 突然停冷却水冷却水突然中断时,则立即停炉。
(5) 生产过程中发现硅棒倒壁,则拆炉重装。
(6) 突然停氢气发现氢气中断后,立即与氢氧站、干法工序联系,了解原因及停氢时间的长短。
A.短时停氢(指管道压力能维持在0.02Mpa以上)不需降温,但要随之减小三氯氢硅通入量,降低配比。
待氢恢复供应时,进入正常生产。
B.长期停氢①关闭挥发器混合气体出口阀和主氢阀,微开侧氢阀,切断电源,立即降温停炉。
②关闭还原尾气进入尾气回收系统入口阀,打开放空阀进入尾气淋洗塔处理。
③过2~3分钟后即关闭侧氢阀,开启氮气阀,氮气经进气管进入还原炉。
④待氢气恢复供应后,视其炉内情况,若硅棒直径已基本达到要求,就不必再次开炉,拆炉重装;若硅棒直径相差较大,能启动则可再次进行高压启动(但要用氢气置换炉内氮气后重新开炉;若不能启动则拆炉重装。
(7) 由于电极烧坏,未能及时发现,造成大量水进入炉内,并且进入尾气回收管道,按下列步骤进行:①切除电源,关闭电极冷却水。
②关闭还原尾气进入干法回收系统入口阀,开启放空阀;其余生产炉子也同时进行这项操作。
③关闭挥发器混合气体出口阀,继续通氢(氢由侧路进入)。
④关闭氢气阀,开启氮气阀。
⑤清洗尾气管道和尾气冷凝器。
清洗、干燥、安装完毕,按有关规定进行操作,然后投入生产。
(8) 在操作无误的情况下,发现尾气压力慢慢升高。
处理如下:①首先电话询问干法回收车间是否有异常,若异常能短期恢复正常,此时应停挥发器鼓泡氢和SiHCl3、停炉前混合气,开侧路氢,尾气进入淋洗塔。
待干法工序正常后恢复开炉条件继续生产。
若不能短期恢复正常应按停炉处理。
②若干法工序正常而出现此情况应考虑是否炉前水冷器堵塞(包括尾气管道堵塞),则按经生产使用后尾气冷凝器的清洗步骤进行处理。
三氯氢硅还原岗位安全技术操作过程及事故处理规程1.安全技术操作规程1)氢气为无色无味气体,和一定比例的空气混合后,在火星以及700℃以上高温作用下极易发生爆炸。
(空气和氮气的混合气体爆炸极<体积>:上限为73.5%H2和26.5%空气,下限为5%和95%空气)为此要求:设备系统不许有漏气,备有充足的安全氮气。
生产过程中系统设备,管道用氮气充分置换后,才能通入氢气。
2)室内禁止有明火,在必须动火作业时,须经公司安全员同意,采取可靠安全措施,并有安全部门领导签发的动火证,公司安全监督员到现场才能动火,否则不得动火。
3)万一发生氢气着火或者爆炸事故,不得切断氢气,以免产生回火,引起更大的事故,而应在正压下充以氮气,逐渐关H2阀灭火,或用CO2封闭灭火。
4)SiHCl3易挥发,易水解,易燃易爆,对人体呼吸系统有强烈的刺激作用,因此要求设备系统不得泄露原料。
5)SiHCl3引燃点28℃,着火点220℃,所以要避免用火焰火花或高温物体接近。
万一发生着火爆炸,首先切断料源,迅速隔离着火点,用CCl4,CO2灭火器灭火。
6)SiHCl3溅入眼,手,脸上时,用干纱布或手巾擦,然后找医生治疗,不可用水冲洗。
7)清洗管道设备时,要戴上防酸手套和眼镜,以防酸碱烧伤。
8)操作台,设备,还原炉必须接地良好。
9)到楼下合,拉闸时必须戴绝缘手套。
10)高压启动时,必须先打报警铃,任何人不得进入还原大厅以及变压器室。
11)拆炉吊装时,还原炉壁有一层高硅履聚合物,该物附着物受到摩擦或机械冲击时,会引起火花,甚至着火,操作时应注意。
12)开炉通H2时,一定要先抽空再通H2,如不抽空则必须用氮气充分置换后再通入H2。
13)不许经常检查还原炉底盘冷却水,电极冷却水以及炉筒内导热油循环流通情况,发现异常(水管跳动或不畅通,导热油泄露)必须作停炉处理。
2.事故处理过程1)硅芯严重倾斜,掉横梁,需通知装炉人员重装。
2)启动时炉内拉弧,立即停止启动,拆炉后经处理在装炉启动。
3)启动后确认硅芯脏,有氧化等异常现象,当班人员可以及时停炉并通知装炉人员重装硅芯。
4)生产中突然停电,应马上关原料下料阀,挥发器混合气出料阀。
瞬间来电马上复位,复位不成功应作停炉处理。
若硅棒直径可以复位,空烧半小时(适当提高温度)后再进混合气继续生产。
5)还原炉防爆孔爆破或者窥视镜石英破裂时,应立即停电同时关料阀,氢气阀,尾气阀,并迅速通入氮气,慢慢改入直接放空,灭火后再处理。
6)挥发器转子流量计,液位计等泄露时,应关闭H2阀,加料阀,混合气阀,炉前改放空,关闭尾气阀,处理后再更换流量计和液位计。
7)电极,底盘冷却水在开炉过程中堵塞,应及时反冲处理,注意安全。
8)还原炉设备如有漏气严重时要及时处理,处理后仍然漏气的,应立即停炉处理。
9)系统压力超过正常范围,应立即查明原因进行处理,若压力继续升高,超过1.5Mpa,立即作停炉处理。
10)若发现炉内有漏油漏水现象,应立即停炉,并将尾气该入直接放空,避免尾气缓冲罐以及管道堵塞。