焦化厂生产工艺对比及选择探究
新建焦化厂工艺、设备选型经验总结

焦化厂工艺、设备选型经验总结张长胜如何建设一个工艺先进、设备优良、投资不多的焦化厂是所有企业领导考虑的第一要务。
长胜从事焦炉建设、焦炉管理五十多年,亲率各阶层干部及领导参观考察全国90%以上的焦化厂,现将焦化厂平面布置、工艺选型、设备选型经验小结如下供有心人参考。
焦化厂在选址后的第一项工作就是总图布置,依据焦化行业最新准入规定及焦化工艺发展趋势建议:一、备煤车间工艺选择先配后碎工艺为好,即原料接收煤场→受煤皮带→运煤皮带→储煤场→堆取料机械→配煤塔→配煤秤→除铁器→破碎机→上煤皮带→焦炉煤塔。
(煤场建有封闭大棚、外购洗精煤的焦化厂不设置预破碎设备)备煤车间工艺设备选型须要掌握的原则:因为各焦化厂原料精煤一般都以汽车+火车的方式从各地运输进厂,精煤到达后,如何快速将来煤卸到地上是工艺首选任务。
大型焦化厂多采用螺旋卸煤机卸煤,独立中小型焦化厂一般采用人工加装载机卸煤工艺。
大型焦化厂把相同或者接近的煤质分为气煤、肥煤、焦煤和瘦煤四类,然后根据煤质的类别用堆取料机把运来的煤存取到规定位置。
备煤车间煤场接收工段设备选型的原则是卸煤设备要快,目的是最大限度缩短来煤卸煤时间。
百万吨规模的企业选择机械化卸煤设备最为科学。
运煤皮带、破碎机设备选型时,皮带速度、破碎能力需要设备选留有一定余地。
配煤塔仓内由于挂煤原因,为减少下煤阻力各焦化厂都采用不同材质的衬板+空气炮以达到下煤顺溜目的,所以配煤塔建设时一定要选择坚实光滑材料。
配煤仓下计量设备是焦化厂的重要设备,所选计量皮带要准确,控制软件要可靠。
备煤车间上煤、配煤仪表、监控设施全部选择智能化控制同时与中央控制室联网。
注:煤种划分目的由于各焦化厂来煤品种繁多,名称、煤质不一样,为减少和方便配煤管理大型焦化厂常把配煤分类为。
①气煤类气煤的煤化程度比长焰煤高,煤的分子结构中侧链多且长,含氧量高。
在热解过程中,不仅侧链从缩合芳环上断裂,而且侧链本身又在氧键处断裂,所以生成了较多的胶质体,但粘度小,流动性大,其热稳定性差,容易分解。
毕业论文---焦化厂化产工艺流程的研究与思考
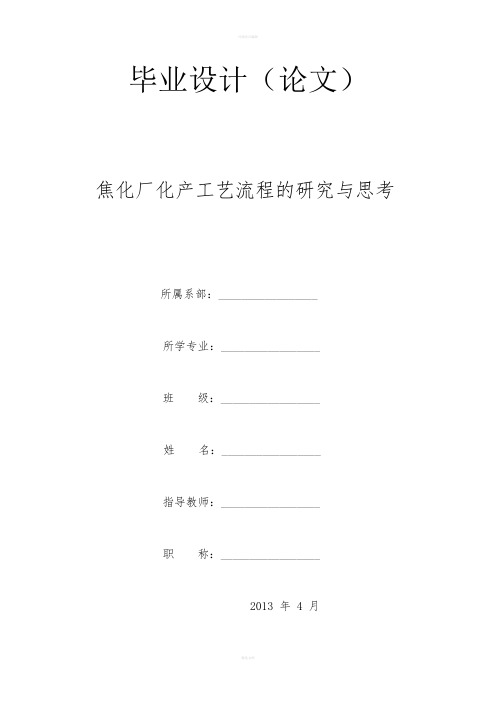
毕业设计(论文)焦化厂化产工艺流程的研究与思考所属系部:_________________所学专业:_________________班级:_________________姓名:_________________指导教师:_________________职称:_________________2013 年 4 月目录概述第一章化产工艺流程第一节冷鼓工段工艺流程 (3)第二节循环水工艺流程 (3)第三节脱硫及硫回收系统 (4)第四节硫胺系统 (4)第五节粗苯系统 (4)第六节化产工艺流程图 (5)第二章化产车间脱硫工艺第一节焦化厂化产车间的脱硫工艺第二节脱硫系统存在的主要问题第三节脱硫系统的改造及改造后的运行情况第四节结论致谢煤炭由高温炼焦得到的焦炭可供高炉冶炼、铸造、汽化和化工等工业部门作为燃料和原料;炼焦过程中得到的干馏煤气经回收、精制可得到各种芳香烃和杂环混合物,供合成纤维、医药、染料、涂料和国防等工业作原料;经净化后的焦炉煤气既是高热值燃料,也是合成氨、合成燃料和一系列有机合成工业的原料。
因此,高温炼焦不仅是煤综合利用的重要途径,也是冶金工业的重要组成部分。
第一章化产工艺流程第一节冷鼓工段工艺流程来自82~83℃的荒煤气,带着焦油和氨水沿吸煤气管道至气液分离器,气液分离后进入横管初冷器,在此分两段冷却:上段采用32℃循环水、下段采用16℃制冷水将煤气冷却至22℃。
冷却后的煤气进入煤气鼓风机加压后进入电捕焦油器,除掉其中夹带的焦油雾后煤气被送至脱硫工段。
初冷器中段和下段排出的冷凝液进入冷凝液循环槽,由冷凝液循环泵送入初冷器下端循环喷洒,如此循环使用,多余部分送机械化氨水澄清槽。
从气液分离器出来的焦油、氨气进入机械化焦油氨水澄清槽,经澄清分离后,上部氨水送至循环氨水槽,由循环氨水泵及高压氨水泵送往炼焦工段供冷却荒煤气和集气管吹扫及无烟装煤使用。
剩余氨水则由剩余氨水泵送至硫胺工段蒸氨。
分离出的焦油至焦油中间槽贮存,当达到一定液位时,用焦油泵将其送至焦油槽。
焦化厂几种烟气脱硫工艺的对比和分析
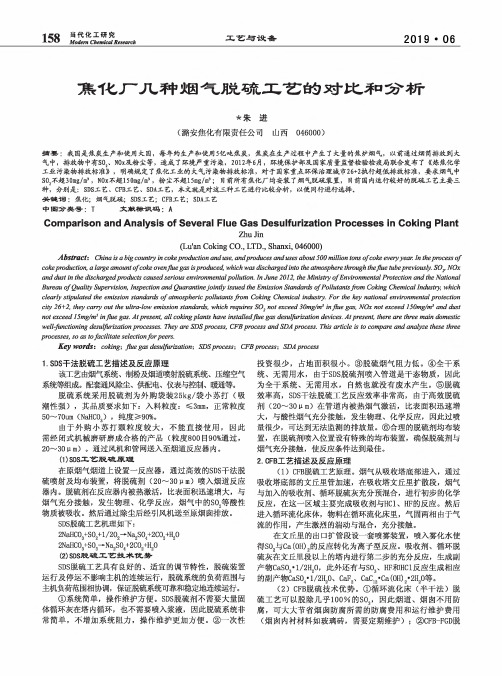
当代化工研究Modem Chemical Research158工艺与设备2019 ・ 06焦化厂几种烟气脱硫工艺的对比和分析*朱进(潞安焦化有限责任公司山西046000)摘耍:我国是焦炭生产和使用大国,每年约生产和使用5亿吨焦炭,焦炭在生产过程中产生了大量的焦炉烟气,以前通过烟筒排放到大 气中,排放物中有SO?、NOx 及粉尘等,造成了环境严重污染,2012年6月,环境保护部及国家质量监督检验检疫局联合发布了《炼焦化学 工业污染物排放标准》,明确规定了焦化工业餉大气污染物排放标准,对于国家重点环保治理城市26+2执行超低排放标准,要求烟气中 SO?不超30mg/m 1*3 , NOx 不超150mg/m 3,粉尘不超15mg/m 3;目前所有焦化厂均安装了烟气脱硫装置,目前国内运行较好的脱硫工艺主要三 种,分别是:SDS 工艺、CFB 工艺、SDA 工艺,本文就是对这三种工艺进行比较分析,以便同行进行选择.1. S DS 干法脱硫工艺描述及反应原理该工艺由烟气系统、制粉及烟道喷射脱硫系统、压缩空气 系统等组成。
配套通风除尘、供配电、仪表与控制、暖通等。
脱硫系统采用脱硫剂为外购袋装25kg/袋小苏打(吸 潮性强),其品质要求如下:入料粒度:W3mm,正常粒度 50〜70um (NaHC03),纯度M90%。
由于外购小苏打颗粒度较大,不能直接使用,因此 需经闭式机械磨研磨成合格的产品(粒度800目90%通过,20-30um )。
通过风机和管网送入至烟道反应器内。
⑴SDS 工艺脱硫原理在原烟气烟道上设置一反应器,通过高效的SDS 干法脱 硫喷射及均布装置,将脱硫剂(20〜30U m )喷入烟道反应器内。
脱硫剂在反应器内被热激活,比表面积迅速增大,与 烟气充分接触,发生物理、化学反应,烟气中的SO?等酸性 物质被吸收。
然后通过除尘后经引风机送至原烟囱排放。
SDS 脱硫工艺机理如下:2NaHC03+S02+l/202^Na 2S04+2C02+H 202NaHC03+S03^Na 2S04+2C02+H 20(2) SDS 脱硫工艺技术优势SDS 脱硫工艺具有良好的、适宜的调节特性,脱硫装置运行及停运不影响主机的连续运行,脱硫系统的负荷范围与 主机负荷范围相协调,保证脱硫系统可靠和稳定地连续运行。
焦化厂生产工艺流程
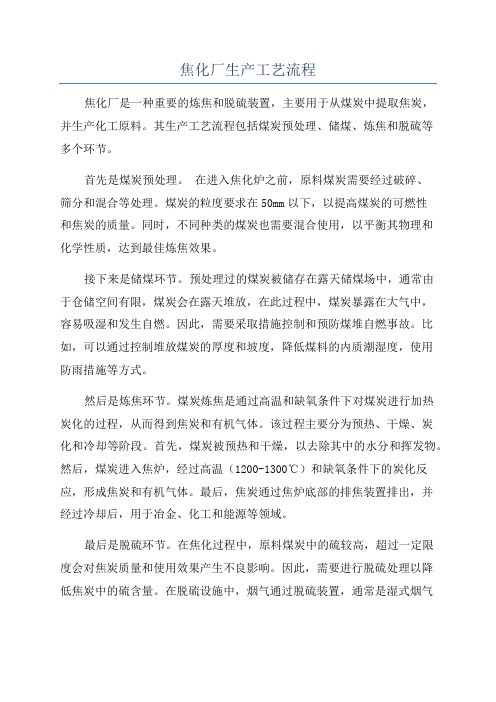
焦化厂生产工艺流程焦化厂是一种重要的炼焦和脱硫装置,主要用于从煤炭中提取焦炭,并生产化工原料。
其生产工艺流程包括煤炭预处理、储煤、炼焦和脱硫等多个环节。
首先是煤炭预处理。
在进入焦化炉之前,原料煤炭需要经过破碎、筛分和混合等处理。
煤炭的粒度要求在50mm以下,以提高煤炭的可燃性和焦炭的质量。
同时,不同种类的煤炭也需要混合使用,以平衡其物理和化学性质,达到最佳炼焦效果。
接下来是储煤环节。
预处理过的煤炭被储存在露天储煤场中,通常由于仓储空间有限,煤炭会在露天堆放,在此过程中,煤炭暴露在大气中,容易吸湿和发生自燃。
因此,需要采取措施控制和预防煤堆自燃事故。
比如,可以通过控制堆放煤炭的厚度和坡度,降低煤料的内质潮湿度,使用防雨措施等方式。
然后是炼焦环节。
煤炭炼焦是通过高温和缺氧条件下对煤炭进行加热炭化的过程,从而得到焦炭和有机气体。
该过程主要分为预热、干燥、炭化和冷却等阶段。
首先,煤炭被预热和干燥,以去除其中的水分和挥发物。
然后,煤炭进入焦炉,经过高温(1200-1300℃)和缺氧条件下的炭化反应,形成焦炭和有机气体。
最后,焦炭通过焦炉底部的排焦装置排出,并经过冷却后,用于冶金、化工和能源等领域。
最后是脱硫环节。
在焦化过程中,原料煤炭中的硫较高,超过一定限度会对焦炭质量和使用效果产生不良影响。
因此,需要进行脱硫处理以降低焦炭中的硫含量。
在脱硫设施中,烟气通过脱硫装置,通常是湿式烟气脱硫法,将烟气中的硫化氢等硫化物转化为硫酸盐,从而降低焦炭中的硫含量,保证焦炭的质量。
此外,焦化厂还有烟气除尘、废气处理和废水处理等环节,以减少对环境的影响。
其中,烟气除尘主要通过静电除尘器和袋式除尘器等设备,去除煤炭燃烧产生的灰尘和颗粒物。
废气处理主要是对焦炉废气进行处理,通过溶液喷射吸收法或者吸附剂吸附法,去除有机气体和二氧化硫等有害物质。
废水处理则是通过物理、化学和生物方法处理焦化厂废水,以使之符合排放标准。
总之,焦化厂的生产工艺流程包括煤炭预处理、储煤、炼焦和脱硫等多个环节。
焦化厂生产工艺对比及选择探究

焦化厂生产工艺对比及选择探究焦化厂一般是由备煤车间、炼焦车间、回收车间、焦油加工车间、苯加工车间、脱硫车间以及废水处理车间等车间组成,其生产工艺主要体现在上述几个流程中,在本文中笔者将结合多年工作经验,对焦化厂生产工艺对比及选择进行研究。
标签:焦化厂;生产工艺;对比及选择我国是焦化产品生产和消费以及出口大国,焦化产品广泛应用在化学工业、医药工业合国防工程中,随着国民经济不断增长,焦化产业在近年来得到快速发展,更是将山西省发展为我国第一产焦大省,焦化产业成为国民经济发展的催化剂。
在焦化产品生产过程中要遵循环保和清洁的原则,因此在生产工艺选择上尤为慎重,采用先进的生产技术,促进焦化产业健康可持续发展。
1.焦化生产工艺流程首先由备煤车间将配合煤装入煤塔,经过计量之后将煤装入碳化室,煤炭在碳化室内经过一周时间的高温干馏制成焦炭并产生荒煤气。
再将焦炭运至凉焦台上,冷却一定时间之后送往筛焦工段,经过筛选和分类之后储存起来。
在碳化过程中产生的荒煤气汇集到碳化室顶部空间,经过上升管和桥管进入集气管,经过氨水喷洒冷却至90℃左右,与焦油等物质一起经过吸煤气管送到煤气净化车间。
焦化生产工艺每一个步骤都是连贯而成的,每个步骤都会影响焦化产品质量。
2.焦化生产工艺对比与选择2.1焦炉炉型本文将对JN60型焦炉、JN55型焦炉、JN43型焦炉、JND系列捣固焦炉四种炉型进行对比和选择。
JN型焦炉有很多种类,例如两分式、下喷式、侧入式以及捣固式等。
JN60型焦炉炉体结构为双联火道、焦炉煤气下喷、废气循环、复热式顶装焦炉,特点是蓄热室主墙宽度达到290mm,采用三沟舌结构,斜道宽度为120mm,边斜道出口宽度为120mm,中部斜道出口宽度为96mm,这样的结构设计能够减少砖型,提高边火道温度。
碳化室的厚度采用上下一致的做法,采用100mm墙体,墙面采用宝塔砖结构。
其结构能够保证良好的操作和生产环境,为工作人员创造更为舒适的作业条件。
焦化生产工艺流程

焦化生产工艺流程焦化生产炼焦生产是以一定特性的洗精煤为原料,在焦炉中密闭高温干馏,使之分解炭化生产出焦炭和焦炉煤气,再通过各种化工单元,对焦炉煤气进行净化,并回收其中的焦油、硫铵、粗苯、硫磺等化工产品。
一、备煤车间1、概述备煤主要由煤场、受煤坑及转运站、粉碎机室及高架栈桥等设施组成。
用以完成煤场内煤的配合、堆放、上料、粉碎等任务,最终得到按一定比例配合好的炼焦煤,运送到焦炉煤塔中备用。
本工程备煤系统采用两级粉碎的工艺方案。
备煤系统能力是按年产90万吨的捣固焦炉生产能力而配套设计的。
备料、粉碎及配煤能力为360t/h。
2、工艺流程进厂的洗精煤按不同煤种卸在各自的堆场、分类堆存。
贮煤塔需要供煤时,精煤堆场的各种煤分别由装载机将煤送入各自受煤坑内的受煤漏斗,受煤坑下部设有可调容积式给料机将煤送入破碎机,可调容积式给料机控制各种煤量大小,通过控制给煤速度达到精确配煤目的。
此工艺既提高了配煤效果,又降低了投资。
粘结性差的本地煤和晋城无烟煤通过受煤坑、可调容积式给料机进入PFCK 可逆反击锤式破碎机粉碎至小于1mm粒度达到75%以上。
粉碎后的弱粘结煤再与未经破碎的焦煤共同进入PFJ反击式破碎机再次破碎并混合,将其中的焦煤粉碎至3mm以下。
完成粉碎、混合、粉碎三个过程的配合煤最后由带式输送机将煤运至贮煤塔,供焦炉炼焦使用。
备煤工艺的关键在于将粘结差的本地煤和无烟煤由PFCK可逆反击锤式破碎机进行高细度破碎后再与未经粉碎的焦煤共同进入粗粒度的PFJ反击式破碎机进行粉碎。
如此设计的目的是使弱粘结煤的粒度小于主焦煤的粒度,粉碎并混合后,不同粒度的煤料能够形成更合理的颗粒级配,提高煤料的堆密度,并使主焦煤与弱粘结煤或不粘结煤能够项目包裹,从而达到更好的捣固和结焦效果。
该技术是实现大量采用当地廉价的非炼焦煤生产优质冶金焦炭的关键之一。
二、焦化车间1、概述炼焦车间主要由2×45孔550-D型,炭化室高5.5m蓄热室式捣固焦炉,双联火道、废气循环、下喷、单热式焦炉及配套设施组成。
[讲解]焦化生产工艺简介和设备工艺特点
![[讲解]焦化生产工艺简介和设备工艺特点](https://img.taocdn.com/s3/m/5bff0c78dcccda38376baf1ffc4ffe473368fda5.png)
生产工艺简介和设备工艺特点炼焦生产工艺简介原料煤进入煤场后,通过堆取料机取煤或受煤坑受煤送入配煤仓,经电子自动配料秤配煤,再通过粉碎机粉碎混合最后送入煤塔为炼焦车间提供入炉煤。
装煤车将捣固成型的煤饼从机侧装入炭化室。
煤饼在950℃~1050℃的温度下高温干馏。
经干馏后,成熟的焦炭被推焦车经拦焦车导焦栅推出落入熄焦车内,由熄焦车送至熄焦塔用水喷洒熄焦,熄焦后的焦炭由熄焦车送至凉焦台,经补充熄焦,凉焦后,由刮板放焦机放至皮带机送至筛焦楼进行筛分送焦场。
干馏过程中产生的荒煤气经炭化室顶部空间、上升管、桥管入集气管。
在桥管集气处用压力为0.3MPa,温度为78℃的循环氨水喷洒冷却,使700~800℃的荒煤气冷却到85℃左右,再经过吸气弯管和吸气管抽吸至鼓风冷凝工段,依次经过硫铵工段、粗苯工段,对氨和粗笨进行回收,最后经脱硫工段脱硫,送甲醇和焦炉使用。
在集气管冷凝下来的焦油、氨水经气液分离器到机械化澄清槽分离。
氨水进氨水储槽,经过氨水循环泵送焦炉桥管处喷洒,剩余下的氨水经过蒸氨后送生化站处理,生化处理后的复用水供给焦炉熄焦和煤场喷洒使用;焦油入焦油储槽,脱水后外卖。
焦炉加热用焦炉煤气由外部架空管道引入煤气预热器至焦炉地下室,从焦炉下部加热煤气管道喷入立火道,与经蓄热室预热后进入立火道的空气在立火道汇合后燃烧。
部分废气经废气循环孔进入上升燃烧火道,火焰加长,使高向加热均匀合理。
燃烧后的废气通过立火道顶部跨越孔进入下降气流的立火道,再经过蓄热室,由格子砖把废气的部分显热吸收后,经过小烟道、废气开闭器、分烟道、总烟道、烟囱排入大气。
装煤过程中逸散的荒煤气由炉顶设的消烟除尘车抽吸至车上的燃烧室燃烧,燃烧后的废气经车上的文丘里洗涤器,将废气中的粉尘洗下来,排入大气。
洗涤水送至除尘车下水槽排到粉焦沉淀罐沉淀分离后循环使用。
设备工艺特点一、炼焦车间我公司采用的是TJL4350D型焦炉其特点和优势如下:1.宽炭化室、宽蓄热室、双联火道、废气循环、下喷单热、侧装煤捣固焦炉。
焦化粗苯工艺研究

焦化粗苯工艺研究摘要:粗苯是一种重要的有机化工原料,广泛的运用于各个行业中。
本文首先对粗苯工艺的三种主流加工方法进行分别阐述,在此基础上,对焦化厂粗苯加工工艺的流程进行了流程介绍,提出了改造的基本流程,并进行了新与旧工艺的特点比较,最后展望了未来焦化粗苯生产的方向并提出了合理的建议。
关键词:粗苯;焦化粗苯;工艺伴随着市场经济的飞速发展,对焦化粗苯的使用需求也日益增加。
焦化厂回收车间里粗苯工序是十分重要一项工序,对粗苯进行加工通常会有三种方法:第一种是加氢蒸馏法;第二种是加氢法;第三种是酸洗法。
一、粗苯工艺的主流加工方法1.加氢蒸馏法美国液/液萃取蒸馏(shelluop)与德国的morphylane萃取这两个是金典的低温低压加氢蒸馏方法。
下图是加氢蒸馏方法的主要流程。
该方法的基本条件是:p=3.0-4.0mpa;t=320-3900c,粗苯通过分流法分解出芳烃(c9+)、重芳烃(c9+)以及轻苯,通过这些物质来产生古马隆,轻苯去加氢。
轻苯获得加氢油,通过离合器产生出循环气体以供使用,加氢油所排出的尾气通过萃取后,可以获得非芳烃与芳烃馏分。
通过无数次的循环,陆续的补充氢气。
2.加氢法高温高压加氢方法的金典方法是litol法,具体的流程图二所示:加氢法流程的基本条件是:p=6.ompa,t=6100c,粗苯经过预分馏塔区分币苯与轻笨。
循环氢经mea脱硫以后,绝大部分的循环氢气返回加氢系统中进行利用,只有极少部分传到了制氢单位中,所制造的氢气通过加氢系统得到了补充。
制氢系统温度压力较高,流程也很复杂,建议用psa方法从煤气中制取氢气。
3.酸洗法酸洗法的主要原理是将粗苯通过第一步蒸馏,摆脱出低沸点的不饱和硫化物与化合物,例如戊烯、环戊二烯、二硫化碳等。
在此基础之上,分离出粗苯与轻苯两种物质,轻苯是通过浓硫酸洗涤的,而粗苯是用古马隆生产的,并且还要抛开这些物质中的苯类沸点相似的不饱和硫化物与化合物,举例来说有异丁烯、诊仃、咪吩等,一起产生了酸焦油与再生酸。
- 1、下载文档前请自行甄别文档内容的完整性,平台不提供额外的编辑、内容补充、找答案等附加服务。
- 2、"仅部分预览"的文档,不可在线预览部分如存在完整性等问题,可反馈申请退款(可完整预览的文档不适用该条件!)。
- 3、如文档侵犯您的权益,请联系客服反馈,我们会尽快为您处理(人工客服工作时间:9:00-18:30)。
焦化厂生产工艺对比及选择探究
作者:聂大伟
来源:《好日子(中旬)》2018年第02期
摘要:焦化厂一般是由备煤车间、炼焦车间、回收车间、焦油加工车间、苯加工车间、脱硫车间以及废水处理车间等车间组成,其生产工艺主要体现在上述几个流程中,在本文中笔者将结合多年工作经验,对焦化厂生产工艺对比及选择进行研究。
关键词:焦化厂;生产工艺;对比及选择
我国是焦化产品生产和消费以及出口大国,焦化产品广泛应用在化学工业、医药工业合国防工程中,随着国民经济不断增长,焦化产业在近年来得到快速发展,更是将山西省发展为我国第一产焦大省,焦化产业成为国民经济发展的催化剂。
在焦化产品生产过程中要遵循环保和清洁的原则,因此在生产工艺选择上尤为慎重,采用先进的生产技术,促进焦化产业健康可持续发展。
1.焦化生产工艺流程
首先由备煤车间将配合煤装入煤塔,经过计量之后将煤装入碳化室,煤炭在碳化室内经过一周时间的高温干馏制成焦炭并产生荒煤气。
再将焦炭运至凉焦台上,冷却一定时间之后送往筛焦工段,经过筛选和分类之后储存起来。
在碳化过程中产生的荒煤气汇集到碳化室顶部空间,经过上升管和桥管进入集气管,经过氨水喷洒冷却至90℃左右,与焦油等物质一起经过吸煤气管送到煤气净化车间。
焦化生产工艺每一个步骤都是连贯而成的,每个步骤都会影响焦化产品质量。
2.焦化生产工艺对比与选择
2.1焦炉炉型
本文将对JN60型焦炉、JN55型焦炉、JN43型焦炉、JND系列捣固焦炉四种炉型进行对比和选择。
JN型焦炉有很多种类,例如两分式、下喷式、侧入式以及捣固式等。
JN60型焦炉炉体结构为双联火道、焦炉煤气下喷、废气循环、复热式顶装焦炉,特点是蓄热室主墙宽度达到290mm,采用三沟舌结构,斜道宽度为120mm,边斜道出口宽度为120mm,中部斜道出口宽度为96mm,这样的结构设计能够减少砖型,提高边火道温度。
碳化室的厚度采用上下一致的做法,采用100mm墙体,墙面采用宝塔砖结构。
其结构能够保证良好的操作和生产环境,为工作人员创造更为舒适的作业条件。
JN55型焦炉具备的结构特点是在每个碳化室下面都有两个宽度相同的蓄热室,在蓄熱室异向气流之间的主墙内设置了垂直砖煤气道,单墙与主墙之间用带沟舌的异型砖砌筑,保证良好的气密性。
其斜道宽度为130mm,边斜道出口为
110mm,中部斜道出口宽度为80mm,但是与JN60型焦炉相比,由于其斜道出口宽度较小,
因此在节省砖型和提高温度的效果上有所欠缺。
JN43型焦炉事物我国其在早期设计与建设的,在后来经过多次改进和创新,其炉体特点是在每个碳化室栽面有两个宽度相同的蓄热室,在此基础上改造成JN43-58-1型和JN43-80型焦炉产品,主要是采用双沟舌“Z”型砖砌筑而成,蓄热室下部小烟道顶部采用圆孔扩散式箅子砖,使得使蓄热室气流分布均匀,小烟道两侧是采用粘土砖,并在小烟道和蓄热室处采用隔热砖,以减少热量的散失。
JND系列捣固焦炉中碳化室有3.2m、3.8m和4.3m三种高度,这三种焦炉均为双联火道、废气循环、下喷式焦炉,JND38型和JND32型焦炉前两者炭化室宽460mm,JNDK43型焦炉炭化室宽为500mm、炭化室锥度均为10mm。
与前三种焦炉型相比,JND系列捣固焦炉具有很明显的优势,其在设计上遵循工艺简单、适用等原则,在技术装备上水平比较适中,比较适合各个规模的焦化厂使用,不仅如此,JND 系列捣固焦炉在环保条件上也进行了一些列的改善,选择宽碳化室、粘土砖、宽蓄热室、双联火道以及单热式焦炉,在环境保护上具有一定促进作用。
在实际工作中,我们发现捣固焦炉高度与生产效率和质量之间也具有一定联系,例如5.5m和6.3m高度的捣固焦炉相比,6.3m捣固焦炉的碳化室孔数比较少,劳动生产率比较高,操作费用比较低,在一定程度上节约生产成本;在重量焦炭的焦炉中使用6.3m捣固焦炉能够有效降低焦炉的热损失量,增强焦炉的热工作率,使得生产效率和质量有了明显提高。
2.2煤气净化工艺
煤气净化工艺包括脱硫工艺和脱氨工艺,其中脱硫工艺有三种。
其一,HPF法,以HPF 为催化剂的焦炉煤气脱硫脱氰新工艺主要是以氨为碱源,具有很高的脱硫效率,并且对于催化剂的需求量也比较小,很大程度上节约了生产成本,脱硫废液的处理也比较简单,操作费用比较低,脱硫过程中接触的脱硫塔、再生塔、反应槽、泡沫槽、废液槽等易腐蚀的设备应该采用碳钢材质,并在内壁涂抹防腐涂料,输送脱硫液的泵类、管道等应该采用耐腐蚀的不锈钢,通过HPF法可以满足国家对排放尾气含氮量的标准要求,将对周边环境的污染程度降到最小。
其二,AS法即氨硫联合洗涤法,其具有脱硫效率高、节约资源、减轻生化废水处理负担等优势,但是同时具有操作难度大、脱硫效果具有局限性、低温用水量比较大的缺陷,并且会受到洗液质量、液气比、洗液温度、气液接触时间等因素影响,在生产过程中,需要解决的问题很多,因此此种方法并常用于生产中。
其三,真空碳酸钠法,其优势在于具有一定脱硫脱氰效率,碳酸钠价格比较便宜,并且具有一定保护性,工艺简单、投资少、节约成本,用碳酸钠进行脱硫不会产生废液。
脱氨工艺主要有两种,其一,采用水洗氨、蒸氨、氨分解工艺,其优势在于通过余热锅t 回收氨分解生成的高温低热值尾气余热,能够实现生产蒸汽的重复利用,等到尾气重新回到焦炉煤气系统中,对大气不会造成污染,具有很强的环保性能,但是其在使用过程中由于缺乏氨产品,导致实际产值并不高。
其二,采用喷淋式饱和器硫胺工艺,其优点是工艺流程短、能够取得高质量的脱氨效果,设备的使用周期比较长,但是其投资金额比较大。
在对上述各种脱硫和脱氨的方法进行比较之后,大部分焦化厂都都是选择通过喷淋式饱和器进行脱氨处理,通过真空碳酸钠法进行脱硫处理。
3.结语
对于焦化厂来说,只有选择正确的生产工艺,才能生产出高质高量的焦化产品,才能进一步促进国民收入水平提高。
参考文献
[1]武建英.化工厂废渣提取硫的工艺探讨[J].中小企业管理与科技(上旬刊),2015.
[2]黄源凯,韦朝海,吴超飞,吴海珍.焦化废水污染指标的相关性分析[J].环境化学,2015.
[3]邬富林.焦炉煤气脱硫工艺探究[J].化学工程与装备,2013.。