汽车变速器齿轮的加工技术
同步器齿套倒锥齿加工工艺

同步器齿套倒锥齿加工工艺刘庆相孙国(大同齿轮集团有限责任公司)随着汽车工业的发展和对汽车使用性能要求的不断提高,带同步器的变速器在汽车工业中得到越来越广泛的应用。
在设计中,将同步器啮合齿都设计成收缩齿,通过收缩齿所产生的轴向分力防止齿套和锥盘在传动过程中相互脱开,以达到防止脱档的目的。
这样在加工过程中,为加工出收缩齿,就需要从工艺上提出解决方法,锥盘倒锥齿加工,由于引进电子束焊接和激光焊接技术,将双联齿轮分解成单片齿轮,锥盘在加工时可以通过带倾斜工作台的插齿机直接加工成功,而齿套由于是整体结构,采用拉内花键后,再加工倒锥齿,这就给加工制造带来了难度。
同步器齿套的啮合齿一般设计为2︒一4︒的收缩角,因开始设计是用插齿方法,在径向插出倒锥来获得收缩角,所以通常称作倒锥齿。
图1`目前,同步器齿套倒锥齿的加工方法主要有三种。
1 滚轧法滚轧法是最早用来加工倒锥齿的方法。
我厂早在70年代就采用滚轧法加工“铁牛”拖拉机齿轮的倒锥齿。
当时尚没有适合这种工艺方法的设备。
我们是采用自制专机进行,该方法一直沿用至今。
这种方法采用的齿部加工的工艺路线为拉(或插齿)——滚轧加工,倒锥齿加工是用带收缩角的轧轮与工件做正向和反向的滚轧来实现的,效率比较高,所需工装、刀具也比较简单。
缺点是适用性比较差,对齿数较少或有缺齿、不等厚齿的齿套见图2就难于加工;由于滚轧法是用轧轮对结合齿进行正向和反向滚轧,这就带来了齿向精度差的缺点,左右齿面不对称,先滚轧的齿面吃刀深,反向滚轧的齿面吃刀浅。
滚轧加工是刀具和工件相互对滚啮合加工的方法,刀具磨损快,刀具齿面容易产生点蚀现象,轧轮用钝后常在齿高根部产生毛刺,不易清理。
滚轧法加工所产生的多余金属流向结合齿花键小径影响热处理的淬火加工,如热处理采用压淬工艺淬火后容易出现喇叭口现象,特别是单面加工倒锥齿的齿套影响更为明显。
近年来,国内已有机床厂定型生产了采用这种工艺方法的倒锥齿滚轧机。
2 插齿法这是我厂“七五”期间引进日产柴油汽车变速箱制造技术中的一种工艺方法。
双联行星齿轮设计要点

双联行星齿轮设计要点一、齿轮参数的确定齿轮的参数是双联行星齿轮设计的基础,包括齿轮的模数、齿数、压力角等。
需要确定伞齿轮和太阳齿轮的齿数,常见的设计方法是将伞齿轮的齿数设为奇数,太阳齿轮的齿数设为偶数,这样可以避免重合频率的产生。
选择合适的压力角可以使齿轮传动效率更高。
确定模数时需要考虑扭矩和载荷等因素。
二、齿轮的加工和制造1. 齿轮的加工精度要求较高,需要使用高精度的加工设备。
2. 齿轮的硬度要求较高,需要采用合适的热处理工艺,以确保齿轮的强度和耐磨性。
3. 在齿轮的组装过程中,需要保证齿轮轴线的精度和同步,以确保传动稳定性和寿命。
三、传动的平稳性双联行星齿轮传动过程中,需要注意传动的平稳性和稳定性,以减少噪音、振动和冲击等问题。
为此,需要采用合适的传动布局,使传动的力矩分布均匀,同时减小传动的漂移和滞后现象。
还可以通过合理的齿轮几何形状和加工精度等措施来减小传动噪声。
四、传动效率的提高双联行星齿轮传动效率高,但在实际应用过程中,由于齿轮的制造质量、润滑状态和工作环境等因素的影响,传动效率可能会有所下降。
为此,需要通过采用优质材料和精密加工工艺,选用适当的润滑剂并保持良好的润滑状态,以及对传动环境进行控制等措施来提高传动效率。
双联行星齿轮设计中需要考虑齿轮参数的确定、齿轮的加工和制造、传动的平稳性和稳定性以及传动效率的提高等因素。
只有综合考虑这些要点,才能设计出高效、稳定的双联行星齿轮传动系统。
五、结构材料的选择双联行星齿轮传动系统在设计和制造时,需要考虑选择合适的结构材料。
通常采用的材料包括合金钢、碳素钢、不锈钢等,还可以根据实际工况和需求选择各种高强度材料。
结构材料的选择应该综合考虑传动的承载能力、耐磨性、强度和硬度等因素,以确保齿轮传动的耐用性和寿命。
还需要考虑齿轮结构的复杂性和制造难度等问题,以便在材料选择上能够达到经济、实用和可行的目标。
一般来说,高性能合金钢是一种理想的结构材料,它的强度和硬度较高,耐磨性好,承载能力强,尤其在高扭矩和高载荷情况下性能表现更加突出。
齿轮变速器的工作原理
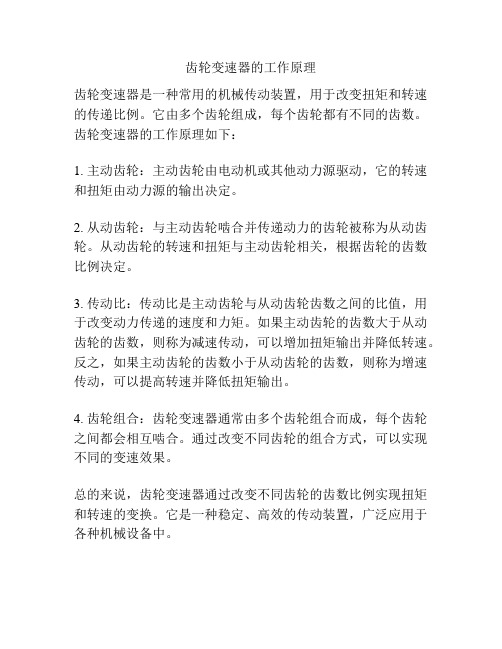
齿轮变速器的工作原理
齿轮变速器是一种常用的机械传动装置,用于改变扭矩和转速的传递比例。
它由多个齿轮组成,每个齿轮都有不同的齿数。
齿轮变速器的工作原理如下:
1. 主动齿轮:主动齿轮由电动机或其他动力源驱动,它的转速和扭矩由动力源的输出决定。
2. 从动齿轮:与主动齿轮啮合并传递动力的齿轮被称为从动齿轮。
从动齿轮的转速和扭矩与主动齿轮相关,根据齿轮的齿数比例决定。
3. 传动比:传动比是主动齿轮与从动齿轮齿数之间的比值,用于改变动力传递的速度和力矩。
如果主动齿轮的齿数大于从动齿轮的齿数,则称为减速传动,可以增加扭矩输出并降低转速。
反之,如果主动齿轮的齿数小于从动齿轮的齿数,则称为增速传动,可以提高转速并降低扭矩输出。
4. 齿轮组合:齿轮变速器通常由多个齿轮组合而成,每个齿轮之间都会相互啮合。
通过改变不同齿轮的组合方式,可以实现不同的变速效果。
总的来说,齿轮变速器通过改变不同齿轮的齿数比例实现扭矩和转速的变换。
它是一种稳定、高效的传动装置,广泛应用于各种机械设备中。
齿轮工艺流程

齿轮工艺流程
齿轮是机械传动中常见的零部件,其工艺流程对于齿轮的质量和性能起着至关
重要的作用。
下面将介绍齿轮的工艺流程,包括材料选择、加工工艺、热处理和精加工等内容。
首先,齿轮的材料选择至关重要。
常见的齿轮材料包括碳素钢、合金钢和不锈
钢等。
在选择材料时,需要考虑到齿轮的使用环境、传动功率和工作温度等因素,以确保齿轮具有足够的强度和耐磨性。
接下来是齿轮的加工工艺。
齿轮的加工工艺通常包括车削、铣削、磨削和齿轮
切削等工艺。
在进行加工时,需要根据齿轮的尺寸、精度要求和齿轮的类型选择合适的加工工艺,以确保齿轮的加工质量。
然后是齿轮的热处理工艺。
热处理是提高齿轮硬度和耐磨性的重要工艺环节。
常见的热处理工艺包括淬火、渗碳和表面强化等。
在进行热处理时,需要控制好加热温度、保温时间和冷却速度,以确保齿轮具有良好的组织结构和性能。
最后是齿轮的精加工工艺。
精加工是保证齿轮精度和表面质量的关键环节。
常
见的精加工工艺包括滚齿、磨齿和齿面修形等。
在进行精加工时,需要控制好加工参数,确保齿轮的精度和表面质量达到要求。
总的来说,齿轮的工艺流程包括材料选择、加工工艺、热处理和精加工等环节,每个环节都对齿轮的质量和性能起着至关重要的作用。
只有严格控制每个环节,才能保证齿轮具有良好的工艺性能,满足不同工况下的使用要求。
同步器齿套倒锥齿加工工艺

同步器齿套倒锥齿加工工艺同步器齿套是汽车变速器中的重要零件,其作用是实现不同齿轮之间的同步换挡。
而倒锥齿则是同步器齿套中常用的一种齿形,其具有良好的同步性能和耐磨性能。
因此,倒锥齿加工工艺的优化对于提高同步器齿套的性能具有重要意义。
倒锥齿加工工艺的主要步骤包括:齿形设计、数控加工、热处理和精加工。
其中,齿形设计是倒锥齿加工的关键,其目的是确定齿形参数,包括齿高、齿距、齿顶圆直径和齿根圆直径等。
齿形设计需要考虑同步器齿套的使用条件和工艺要求,以确保齿形的精度和耐磨性能。
数控加工是倒锥齿加工的主要方法,其优点是加工精度高、生产效率高、重复性好。
数控加工需要使用专用的数控机床和刀具,根据齿形设计参数进行加工。
在加工过程中,需要注意刀具的选择、切削参数的调整和加工过程中的冷却液的使用,以确保加工质量和刀具寿命。
热处理是倒锥齿加工的重要环节,其目的是改善齿轮的力学性能和耐磨性能。
常用的热处理方法包括淬火、回火和表面渗碳等。
在热处理过程中,需要控制加热温度、保温时间和冷却速度等参数,以确保齿轮的硬度和韧性。
精加工是倒锥齿加工的最后一道工序,其目的是提高齿轮的精度和表面质量。
常用的精加工方法包括磨削、抛光和擦拭等。
在精加工过程中,需要使用高精度的加工设备和工具,以确保齿轮的精度和表面质量。
总之,倒锥齿加工工艺的优化对于提高同步器齿套的性能具有重要意义。
在倒锥齿加工过程中,需要注意齿形设计、数控加工、热处理和精加工等环节,以确保齿轮的精度和耐磨性能。
同时,需要不断探索新的加工技术和工艺,以满足汽车工业对同步器齿套的不断提高的需求。
汽车变速器毕业设计

汽车变速器毕业设计汽车变速器毕业设计引言汽车变速器是汽车传动系统中至关重要的组成部分,它能够根据车辆的速度和负载情况,实现发动机输出转矩和车轮转速之间的匹配。
在现代汽车工业中,变速器的设计和优化一直是一个重要的研究领域。
本文将探讨汽车变速器的毕业设计,包括设计目标、设计流程和关键技术。
设计目标汽车变速器的设计目标是提高汽车的性能和燃油经济性。
性能包括加速性能、爬坡能力和最高速度等方面。
燃油经济性则是指在保证性能的前提下,尽可能降低油耗。
因此,在进行变速器设计时,需要考虑以下几个方面:1. 齿轮比的选择:齿轮比是决定车辆行驶性能的关键因素之一。
通过合理选择齿轮比,可以实现加速度和爬坡能力的提升,同时降低发动机负荷,提高燃油经济性。
2. 齿轮材料和制造工艺:齿轮的材料和制造工艺直接影响变速器的可靠性和寿命。
选择高强度、耐磨损的材料,并采用先进的制造工艺,可以提高变速器的使用寿命。
3. 润滑系统设计:润滑系统对变速器的正常运行至关重要。
合理设计润滑系统,确保齿轮和轴承的充分润滑,可以减少摩擦和磨损,提高变速器的效率和寿命。
设计流程汽车变速器的设计流程通常包括以下几个步骤:1. 确定设计要求:根据汽车的使用条件和性能要求,确定变速器的传动比范围、最大扭矩和最高转速等参数。
2. 齿轮设计:根据设计要求,选择合适的齿轮模数和齿轮比,进行齿轮的几何设计。
通过计算和仿真,优化齿轮的齿形和齿向,提高传动效率和静音性能。
3. 轴承设计:根据变速器的负载情况,设计合适的轴承布局和尺寸。
通过计算和有限元分析,确定轴承的载荷和寿命,确保变速器的可靠性。
4. 润滑系统设计:根据变速器的结构和工作条件,设计合适的润滑系统。
选择合适的润滑油和润滑方式,确保变速器的正常运行。
5. 性能评估和优化:通过试验和仿真,评估变速器的性能和燃油经济性。
根据评估结果,对设计进行优化,提高变速器的性能和燃油经济性。
关键技术在汽车变速器的设计过程中,有几个关键技术需要重点考虑:1. 齿轮传动技术:齿轮传动是汽车变速器的核心技术。
变速器齿轮动力学性能的优化设计
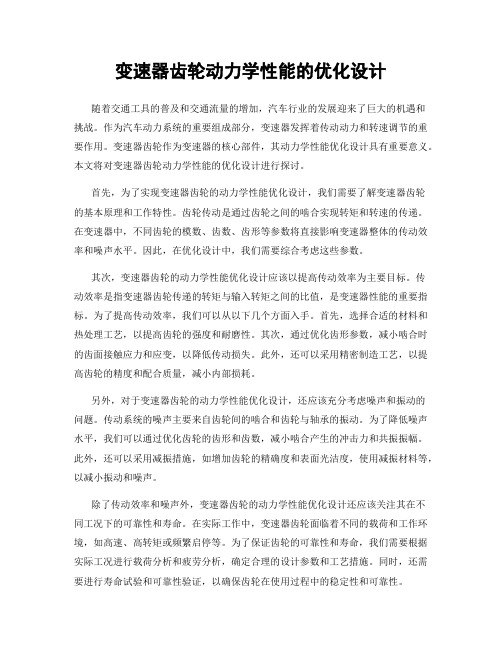
变速器齿轮动力学性能的优化设计随着交通工具的普及和交通流量的增加,汽车行业的发展迎来了巨大的机遇和挑战。
作为汽车动力系统的重要组成部分,变速器发挥着传动动力和转速调节的重要作用。
变速器齿轮作为变速器的核心部件,其动力学性能优化设计具有重要意义。
本文将对变速器齿轮动力学性能的优化设计进行探讨。
首先,为了实现变速器齿轮的动力学性能优化设计,我们需要了解变速器齿轮的基本原理和工作特性。
齿轮传动是通过齿轮之间的啮合实现转矩和转速的传递。
在变速器中,不同齿轮的模数、齿数、齿形等参数将直接影响变速器整体的传动效率和噪声水平。
因此,在优化设计中,我们需要综合考虑这些参数。
其次,变速器齿轮的动力学性能优化设计应该以提高传动效率为主要目标。
传动效率是指变速器齿轮传递的转矩与输入转矩之间的比值,是变速器性能的重要指标。
为了提高传动效率,我们可以从以下几个方面入手。
首先,选择合适的材料和热处理工艺,以提高齿轮的强度和耐磨性。
其次,通过优化齿形参数,减小啮合时的齿面接触应力和应变,以降低传动损失。
此外,还可以采用精密制造工艺,以提高齿轮的精度和配合质量,减小内部损耗。
另外,对于变速器齿轮的动力学性能优化设计,还应该充分考虑噪声和振动的问题。
传动系统的噪声主要来自齿轮间的啮合和齿轮与轴承的振动。
为了降低噪声水平,我们可以通过优化齿轮的齿形和齿数,减小啮合产生的冲击力和共振振幅。
此外,还可以采用减振措施,如增加齿轮的精确度和表面光洁度,使用减振材料等,以减小振动和噪声。
除了传动效率和噪声外,变速器齿轮的动力学性能优化设计还应该关注其在不同工况下的可靠性和寿命。
在实际工作中,变速器齿轮面临着不同的载荷和工作环境,如高速、高转矩或频繁启停等。
为了保证齿轮的可靠性和寿命,我们需要根据实际工况进行载荷分析和疲劳分析,确定合理的设计参数和工艺措施。
同时,还需要进行寿命试验和可靠性验证,以确保齿轮在使用过程中的稳定性和可靠性。
综上所述,变速器齿轮动力学性能的优化设计在汽车工程中具有重要意义。
齿轮设计过程
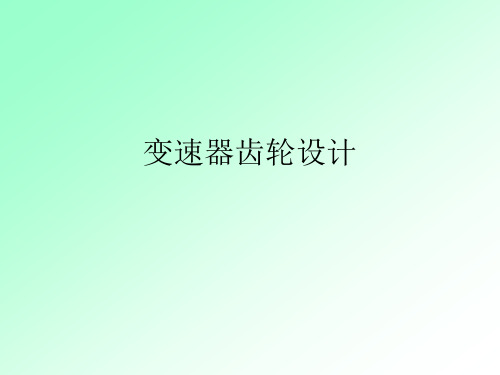
(二)根据接触强度计算确定中心距a或者小齿轮的直径d1, 根据弯曲强度计算确定模数。
1.渐开线圆柱齿轮受力分析及计算 (1)直齿受力分析
Fr Fn α
Ft
P
法向载荷Fn垂直于齿面,为计算方便Fn在节点P 处分解为两个互相垂直的分力,即圆周力Ft与Fr。
公式:
T1
9549
P n1
Ft
2T1 d1
T1——传递的转矩 d1——分度圆直径
α——啮合角
(2)斜齿受力分析
Fr Ft tan
Fn
Ft cos
Fr
αt
Ft
P
αn Fn Fr
F’ P
F’ Fa β
Ft P
如图所示:
圆周力 径向力
Ft
2T1 d1
,
F ' Ft ห้องสมุดไป่ตู้os
F'
F'
tan n
Ft tann cos
轴向力 Fa Ft tan
举例 名称:输出齿轮 材料:20CrMnTi 热处理技术条件:齿面渗碳淬火,渗碳层深度0.8~1.2mm,齿面硬度 HRC58~62,心部硬度HRC32~45。 加工工艺路线:下料→锻造→正火→加工齿形→局部镀铜(防渗)→渗 碳、淬火、低温回火→喷丸→磨齿。
热处理工艺:正火、渗碳、淬火及低温回火。
r1 r2
Fn1 FR1
β1
Fa1
1
2
Fa2
T
β2
FR2
Fn2
中间轴轴向力的平衡
由上图可知,欲使中间轴上两斜齿轮的轴向力平衡, 需满足下述条件: Fa1=Fn1tanβ1 Fa2=Fn2tanβ2
由于传递的转矩T=Fn1r1=Fn2r2,为使两轴向力平衡,必须满足