汽车变速器齿轮的加工工艺
同步器齿套倒锥齿加工工艺

同步器齿套倒锥齿加工工艺刘庆相孙国(大同齿轮集团有限责任公司)随着汽车工业的发展和对汽车使用性能要求的不断提高,带同步器的变速器在汽车工业中得到越来越广泛的应用。
在设计中,将同步器啮合齿都设计成收缩齿,通过收缩齿所产生的轴向分力防止齿套和锥盘在传动过程中相互脱开,以达到防止脱档的目的。
这样在加工过程中,为加工出收缩齿,就需要从工艺上提出解决方法,锥盘倒锥齿加工,由于引进电子束焊接和激光焊接技术,将双联齿轮分解成单片齿轮,锥盘在加工时可以通过带倾斜工作台的插齿机直接加工成功,而齿套由于是整体结构,采用拉内花键后,再加工倒锥齿,这就给加工制造带来了难度。
同步器齿套的啮合齿一般设计为2︒一4︒的收缩角,因开始设计是用插齿方法,在径向插出倒锥来获得收缩角,所以通常称作倒锥齿。
图1`目前,同步器齿套倒锥齿的加工方法主要有三种。
1 滚轧法滚轧法是最早用来加工倒锥齿的方法。
我厂早在70年代就采用滚轧法加工“铁牛”拖拉机齿轮的倒锥齿。
当时尚没有适合这种工艺方法的设备。
我们是采用自制专机进行,该方法一直沿用至今。
这种方法采用的齿部加工的工艺路线为拉(或插齿)——滚轧加工,倒锥齿加工是用带收缩角的轧轮与工件做正向和反向的滚轧来实现的,效率比较高,所需工装、刀具也比较简单。
缺点是适用性比较差,对齿数较少或有缺齿、不等厚齿的齿套见图2就难于加工;由于滚轧法是用轧轮对结合齿进行正向和反向滚轧,这就带来了齿向精度差的缺点,左右齿面不对称,先滚轧的齿面吃刀深,反向滚轧的齿面吃刀浅。
滚轧加工是刀具和工件相互对滚啮合加工的方法,刀具磨损快,刀具齿面容易产生点蚀现象,轧轮用钝后常在齿高根部产生毛刺,不易清理。
滚轧法加工所产生的多余金属流向结合齿花键小径影响热处理的淬火加工,如热处理采用压淬工艺淬火后容易出现喇叭口现象,特别是单面加工倒锥齿的齿套影响更为明显。
近年来,国内已有机床厂定型生产了采用这种工艺方法的倒锥齿滚轧机。
2 插齿法这是我厂“七五”期间引进日产柴油汽车变速箱制造技术中的一种工艺方法。
齿轮工艺流程

齿轮工艺流程
齿轮是机械传动中常见的零部件,其工艺流程对于齿轮的质量和性能起着至关
重要的作用。
下面将介绍齿轮的工艺流程,包括材料选择、加工工艺、热处理和精加工等内容。
首先,齿轮的材料选择至关重要。
常见的齿轮材料包括碳素钢、合金钢和不锈
钢等。
在选择材料时,需要考虑到齿轮的使用环境、传动功率和工作温度等因素,以确保齿轮具有足够的强度和耐磨性。
接下来是齿轮的加工工艺。
齿轮的加工工艺通常包括车削、铣削、磨削和齿轮
切削等工艺。
在进行加工时,需要根据齿轮的尺寸、精度要求和齿轮的类型选择合适的加工工艺,以确保齿轮的加工质量。
然后是齿轮的热处理工艺。
热处理是提高齿轮硬度和耐磨性的重要工艺环节。
常见的热处理工艺包括淬火、渗碳和表面强化等。
在进行热处理时,需要控制好加热温度、保温时间和冷却速度,以确保齿轮具有良好的组织结构和性能。
最后是齿轮的精加工工艺。
精加工是保证齿轮精度和表面质量的关键环节。
常
见的精加工工艺包括滚齿、磨齿和齿面修形等。
在进行精加工时,需要控制好加工参数,确保齿轮的精度和表面质量达到要求。
总的来说,齿轮的工艺流程包括材料选择、加工工艺、热处理和精加工等环节,每个环节都对齿轮的质量和性能起着至关重要的作用。
只有严格控制每个环节,才能保证齿轮具有良好的工艺性能,满足不同工况下的使用要求。
同步器齿套倒锥齿加工工艺

同步器齿套倒锥齿加工工艺同步器齿套是汽车变速器中的重要零件,其作用是实现不同齿轮之间的同步换挡。
而倒锥齿则是同步器齿套中常用的一种齿形,其具有良好的同步性能和耐磨性能。
因此,倒锥齿加工工艺的优化对于提高同步器齿套的性能具有重要意义。
倒锥齿加工工艺的主要步骤包括:齿形设计、数控加工、热处理和精加工。
其中,齿形设计是倒锥齿加工的关键,其目的是确定齿形参数,包括齿高、齿距、齿顶圆直径和齿根圆直径等。
齿形设计需要考虑同步器齿套的使用条件和工艺要求,以确保齿形的精度和耐磨性能。
数控加工是倒锥齿加工的主要方法,其优点是加工精度高、生产效率高、重复性好。
数控加工需要使用专用的数控机床和刀具,根据齿形设计参数进行加工。
在加工过程中,需要注意刀具的选择、切削参数的调整和加工过程中的冷却液的使用,以确保加工质量和刀具寿命。
热处理是倒锥齿加工的重要环节,其目的是改善齿轮的力学性能和耐磨性能。
常用的热处理方法包括淬火、回火和表面渗碳等。
在热处理过程中,需要控制加热温度、保温时间和冷却速度等参数,以确保齿轮的硬度和韧性。
精加工是倒锥齿加工的最后一道工序,其目的是提高齿轮的精度和表面质量。
常用的精加工方法包括磨削、抛光和擦拭等。
在精加工过程中,需要使用高精度的加工设备和工具,以确保齿轮的精度和表面质量。
总之,倒锥齿加工工艺的优化对于提高同步器齿套的性能具有重要意义。
在倒锥齿加工过程中,需要注意齿形设计、数控加工、热处理和精加工等环节,以确保齿轮的精度和耐磨性能。
同时,需要不断探索新的加工技术和工艺,以满足汽车工业对同步器齿套的不断提高的需求。
变速器齿轮动力学性能的优化设计
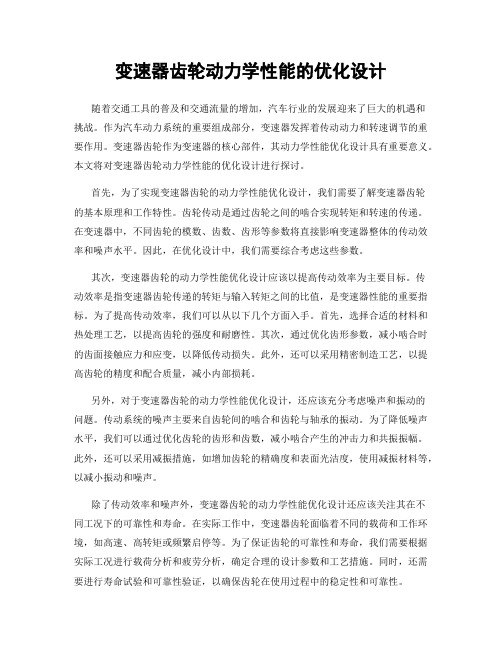
变速器齿轮动力学性能的优化设计随着交通工具的普及和交通流量的增加,汽车行业的发展迎来了巨大的机遇和挑战。
作为汽车动力系统的重要组成部分,变速器发挥着传动动力和转速调节的重要作用。
变速器齿轮作为变速器的核心部件,其动力学性能优化设计具有重要意义。
本文将对变速器齿轮动力学性能的优化设计进行探讨。
首先,为了实现变速器齿轮的动力学性能优化设计,我们需要了解变速器齿轮的基本原理和工作特性。
齿轮传动是通过齿轮之间的啮合实现转矩和转速的传递。
在变速器中,不同齿轮的模数、齿数、齿形等参数将直接影响变速器整体的传动效率和噪声水平。
因此,在优化设计中,我们需要综合考虑这些参数。
其次,变速器齿轮的动力学性能优化设计应该以提高传动效率为主要目标。
传动效率是指变速器齿轮传递的转矩与输入转矩之间的比值,是变速器性能的重要指标。
为了提高传动效率,我们可以从以下几个方面入手。
首先,选择合适的材料和热处理工艺,以提高齿轮的强度和耐磨性。
其次,通过优化齿形参数,减小啮合时的齿面接触应力和应变,以降低传动损失。
此外,还可以采用精密制造工艺,以提高齿轮的精度和配合质量,减小内部损耗。
另外,对于变速器齿轮的动力学性能优化设计,还应该充分考虑噪声和振动的问题。
传动系统的噪声主要来自齿轮间的啮合和齿轮与轴承的振动。
为了降低噪声水平,我们可以通过优化齿轮的齿形和齿数,减小啮合产生的冲击力和共振振幅。
此外,还可以采用减振措施,如增加齿轮的精确度和表面光洁度,使用减振材料等,以减小振动和噪声。
除了传动效率和噪声外,变速器齿轮的动力学性能优化设计还应该关注其在不同工况下的可靠性和寿命。
在实际工作中,变速器齿轮面临着不同的载荷和工作环境,如高速、高转矩或频繁启停等。
为了保证齿轮的可靠性和寿命,我们需要根据实际工况进行载荷分析和疲劳分析,确定合理的设计参数和工艺措施。
同时,还需要进行寿命试验和可靠性验证,以确保齿轮在使用过程中的稳定性和可靠性。
综上所述,变速器齿轮动力学性能的优化设计在汽车工程中具有重要意义。
齿轮设计过程
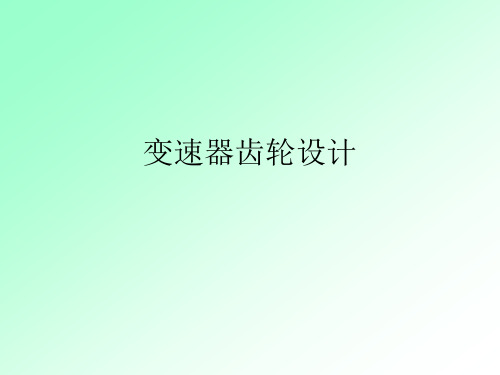
(二)根据接触强度计算确定中心距a或者小齿轮的直径d1, 根据弯曲强度计算确定模数。
1.渐开线圆柱齿轮受力分析及计算 (1)直齿受力分析
Fr Fn α
Ft
P
法向载荷Fn垂直于齿面,为计算方便Fn在节点P 处分解为两个互相垂直的分力,即圆周力Ft与Fr。
公式:
T1
9549
P n1
Ft
2T1 d1
T1——传递的转矩 d1——分度圆直径
α——啮合角
(2)斜齿受力分析
Fr Ft tan
Fn
Ft cos
Fr
αt
Ft
P
αn Fn Fr
F’ P
F’ Fa β
Ft P
如图所示:
圆周力 径向力
Ft
2T1 d1
,
F ' Ft ห้องสมุดไป่ตู้os
F'
F'
tan n
Ft tann cos
轴向力 Fa Ft tan
举例 名称:输出齿轮 材料:20CrMnTi 热处理技术条件:齿面渗碳淬火,渗碳层深度0.8~1.2mm,齿面硬度 HRC58~62,心部硬度HRC32~45。 加工工艺路线:下料→锻造→正火→加工齿形→局部镀铜(防渗)→渗 碳、淬火、低温回火→喷丸→磨齿。
热处理工艺:正火、渗碳、淬火及低温回火。
r1 r2
Fn1 FR1
β1
Fa1
1
2
Fa2
T
β2
FR2
Fn2
中间轴轴向力的平衡
由上图可知,欲使中间轴上两斜齿轮的轴向力平衡, 需满足下述条件: Fa1=Fn1tanβ1 Fa2=Fn2tanβ2
由于传递的转矩T=Fn1r1=Fn2r2,为使两轴向力平衡,必须满足
汽车变速器齿轮设计及问题研讨

汽车变速器齿轮设计及问题研讨1. 引言1.1 研究背景汽车变速器齿轮设计是汽车传动系统中的核心部件,直接影响着汽车的性能和稳定性。
随着汽车工业的快速发展,对于汽车变速器齿轮设计的要求也越来越高。
目前市场上存在着很多变速器齿轮设计方面的问题,例如噪音过大、传动效率低、寿命短等。
这些问题不仅影响了汽车的运行效果,还可能对驾驶员的驾驶体验造成不良影响。
进一步研究汽车变速器齿轮设计原理及问题成为了当下的重要课题。
通过对现有变速器齿轮设计进行深入分析,找出问题所在,并提出优化设计方法,可以有效提高变速器齿轮的性能和可靠性。
对材料选择与加工工艺进行研究,也能够为汽车变速器齿轮的设计和制造提供更好的支持。
通过性能测试与评估,更加客观地了解汽车变速器齿轮的性能表现,为进一步的优化设计提供依据。
【这是研究背景的内容,总字数2000字。
】1.2 研究目的汽车变速器齿轮设计及问题研讨研究目的:研究目的是通过深入探讨汽车变速器齿轮设计及存在的问题,找出优化设计方法,提高变速器的效率和性能,减少故障率,增强汽车的可靠性和耐久性。
研究目的还包括对现有的材料选择和加工工艺进行分析和评估,以寻找更加适合变速器齿轮的材料和工艺,从而提高变速器的质量和寿命。
通过对变速器齿轮的性能测试和评估,进一步验证优化设计方法的可行性和效果,为汽车行驶安全和稳定提供更好的保障。
研究目的在于为汽车行业提供更加先进和可靠的变速器技术,促进汽车工程的发展和进步,为广大汽车用户提供更好的驾驶体验和安全保障。
通过本研究,希望能够为汽车变速器齿轮设计领域的研究和实践提供一定的参考和借鉴,推动汽车工业的持续发展和提升。
1.3 意义和价值汽车变速器齿轮设计及问题研讨的意义和价值在于提高汽车传动系统的效率和性能,从而提升整车的性能和驾驶体验。
通过深入研究变速器齿轮的设计原理,分析现有设计中存在的问题,探讨优化设计方法和材料选择与加工工艺,可以有效提高汽车变速器的可靠性和耐久性,减少故障率和维修成本。
20CrMnTiH、20CrMoH等温正火工艺
20CrMnTiH、20CrMoH等温正火工艺正火是汽车变速器齿轮、轴类零件锻坯预先热处理的常用工艺。
目的是为了获得均匀、接近理想平衡状态的组织(铁素体和珠光体)和合适的硬度范围(160-190HB),以提高切削加工性和控制最终热处理变形。
但常规正火由于受设备限制采用堆装、堆冷方式,会造成不同零件之间或同一零件不同部位的冷却速度及其组织、应力和硬度的较大差别,导致切削加工性能恶化和热处理变形加大,从而降低齿轮精度等级和影响齿轮的使用性能。
另外,随着汽车行业中齿轮、轴类零件精度等级的提高以及Ni-Cr钢的普及应用,采用常规正火工艺已经不能适应生产的要求,为此我们公司于2007年底进行技术改造,购进了一条等温正火线,并于2008年六月份调试完成。
在等温正火线的调试以及试生产过程中,我们对20CrMnTiH、20CrMoH、SAE8620 H等材料进行了等温正火试验,通过工艺试验得出以下结论:要获得均匀分布的组织、硬度以及良好的机械切削加工性能,主要取决于正火工艺过程中快冷、缓冷的设计和等温温度、时间的确定。
下面做一简单的总结回顾:一、等温正火及其关键工艺参数:根据常用低碳合金渗碳钢的奥氏体连续冷却转变曲线,其共同特点是:奥氏体均匀化后,在随后的冷却过程中,由于冷却速度的不同,正火后不同零件之间或同一零件的表面与心部组织也不相同(铁素体与珠光体的含量比例或含有贝氏体)。
要完全获得理想均匀的铁素体和珠光体,则对冷却速度的限制较为严格,这是常规正火很难实现的。
等温正火的原理是将工件加热到AC3或ACcm以上30~50℃,保温适当时间后,以合适的方式冷却到珠光体转变区域某一合适温度,并在此温度下保温,使不同零件和同一零件的不同部位温度均匀化,并在该温度下均匀地完成铁素体+珠光体转变,然后在空气中冷却的正火工艺。
由于不同零件和零件的不同部位基本上是在同一温度下完成组织转变的,所以转变产物及应力、硬度分布是均匀的,从而克服了常规正火过程中零件冷却速度难以控制、零件冷却不均匀的问题。
汽车制造工艺流程详解作业指导书
汽车制造工艺流程详解作业指导书第1章汽车制造工艺概述 (4)1.1 汽车制造工艺发展历程 (4)1.2 汽车制造工艺分类及特点 (4)第2章汽车车身制造工艺 (5)2.1 车身冲压工艺 (5)2.1.1 冲压工艺概述 (5)2.1.2 冲压模具及设备 (5)2.1.3 冲压工艺流程 (5)2.2 车身焊接工艺 (6)2.2.1 焊接工艺概述 (6)2.2.2 焊接方法 (6)2.2.3 焊接工艺流程 (6)2.3 车身涂装工艺 (6)2.3.1 涂装工艺概述 (6)2.3.2 前处理 (6)2.3.3 底漆、面漆和清漆 (7)2.3.4 涂装工艺流程 (7)第3章发动机制造工艺 (7)3.1 发动机铸造工艺 (7)3.1.1 概述 (7)3.1.2 铸造材料 (7)3.1.3 铸造方法 (7)3.1.4 铸造工艺参数 (7)3.2 发动机机加工工艺 (7)3.2.1 概述 (8)3.2.2 主要加工方法 (8)3.2.3 加工顺序 (8)3.2.4 机床及工具选择 (8)3.3 发动机装配工艺 (8)3.3.1 概述 (8)3.3.2 装配顺序 (8)3.3.3 装配方法 (8)3.3.4 装配精度及质量控制 (8)第4章变速器制造工艺 (8)4.1 变速器齿轮加工工艺 (8)4.1.1 齿轮材料选择与准备 (8)4.1.2 齿轮热处理 (9)4.1.3 齿轮加工 (9)4.1.4 齿轮检测 (9)4.2 变速器壳体加工工艺 (9)4.2.1 壳体材料选择与准备 (9)4.2.3 壳体检测 (9)4.3 变速器装配工艺 (9)4.3.1 齿轮装配 (10)4.3.2 同步器装配 (10)4.3.3 轴承、密封件装配 (10)4.3.4 总装与调试 (10)4.3.5 检验与包装 (10)第5章汽车底盘制造工艺 (10)5.1 悬挂系统制造工艺 (10)5.1.1 制造前准备 (10)5.1.2 零部件加工 (10)5.1.3 零部件装配 (10)5.1.4 调试与检验 (10)5.2 制动系统制造工艺 (10)5.2.1 制造前准备 (11)5.2.2 零部件加工 (11)5.2.3 零部件装配 (11)5.2.4 调试与检验 (11)5.3 轮胎制造工艺 (11)5.3.1 制造前准备 (11)5.3.2 橡胶部件制备 (11)5.3.3 骨架部件制备 (11)5.3.4 轮胎成型 (11)5.3.5 硫化 (11)5.3.6 检验与包装 (11)第6章电气系统制造工艺 (11)6.1 电池制造工艺 (11)6.1.1 电池包装配 (11)6.1.2 电池测试 (12)6.2 线束制造工艺 (12)6.2.1 线束设计 (12)6.2.2 线束制作 (12)6.2.3 线束测试 (12)6.3 传感器制造工艺 (12)6.3.1 传感器设计 (12)6.3.2 传感器制造 (13)6.3.3 传感器测试 (13)第7章汽车内饰制造工艺 (13)7.1 内饰材料加工工艺 (13)7.1.1 内饰材料选择 (13)7.1.2 内饰材料切割 (13)7.1.3 内饰材料压痕 (13)7.1.4 内饰材料热压成型 (13)7.2.1 内饰组件预装配 (13)7.2.2 内饰组件定位 (14)7.2.3 内饰组件装配 (14)7.2.4 内饰组件调整 (14)7.3 内饰表面处理工艺 (14)7.3.1 表面清洁 (14)7.3.2 表面涂装 (14)7.3.3 表面烫印 (14)7.3.4 表面保护 (14)7.3.5 表面检验 (14)第8章汽车总装工艺 (14)8.1 总装工艺流程规划 (14)8.1.1 工艺流程概述 (14)8.1.2 车身内饰装配 (15)8.1.3 底盘装配 (15)8.1.4 电器系统装配 (15)8.1.5 动力总成装配 (15)8.1.6 调试及检验 (15)8.2 总装线设备及技术 (15)8.2.1 装配设备 (15)8.2.2 检测设备 (16)8.2.3 信息技术应用 (16)8.3 总装质量检测与控制 (16)8.3.1 质量检测 (16)8.3.2 质量控制 (16)第9章汽车制造过程中的自动化与信息化 (16)9.1 汽车制造自动化技术 (16)9.1.1 自动化概述 (16)9.1.2 技术在汽车制造中的应用 (16)9.1.3 自动输送线在汽车制造中的应用 (17)9.1.4 自动检测与控制在汽车制造中的应用 (17)9.2 汽车制造信息化技术 (17)9.2.1 信息化概述 (17)9.2.2 企业资源规划(ERP)在汽车制造中的应用 (17)9.2.3 制造执行系统(MES)在汽车制造中的应用 (17)9.2.4 产品生命周期管理(PLM)在汽车制造中的应用 (17)9.3 智能制造在汽车制造中的应用 (17)9.3.1 智能制造概述 (17)9.3.2 智能制造关键技术 (17)9.3.3 智能制造在汽车制造企业的实践案例 (18)9.3.4 智能制造发展趋势 (18)第10章汽车制造质量与生产管理 (18)10.1 汽车制造质量控制策略 (18)10.1.2 质量控制流程 (18)10.1.3 质量控制方法 (18)10.2 汽车制造生产管理方法 (18)10.2.1 生产计划管理 (18)10.2.2 生产线平衡 (18)10.2.3 精益生产与智能制造 (18)10.3 汽车制造环境保护与安全生产措施 (18)10.3.1 环境保护策略 (19)10.3.2 安全生产管理 (19)10.3.3 职业健康与劳动保护 (19)第1章汽车制造工艺概述1.1 汽车制造工艺发展历程汽车制造工艺的发展历程可追溯到19世纪末。
齿轮加工工艺说明书
第一章 零件的分析1.1零件的工作状态及工作条件汽车行驶时,齿轮始终在重载荷、高转速中工作。
在换挡时,还承受冲击载荷,所以要求齿轮具有较高的耐磨性和抗冲击性。
在齿轮加工中,为保证齿轮能满足以上要求,应对齿轮在滚齿之后采取磨齿,对齿轮的热处理应采用渗碳淬火,在最终加工中还应采取磷化处理以提高齿轮的防腐性能。
第五速齿轮从结构上来分析属于多联齿轮,由结合齿和传动齿组成。
为使润滑用能充分的起到润滑作用,在齿轮钻出3个油孔。
换挡时为减少齿轮的冲击,在齿轮大端加工出四个止口。
1.2零件的技术条件分析齿轮加工分为齿坯和齿轮轮齿加工。
齿轮的加工部位有轮缘、轮辐、轮毂和内孔。
齿坯的加工精度对齿轮的加工、检验和装配精度影响很大,所以其加工精度应满足GB10095-88的要求。
齿轮轮齿的加工部位有齿形和倒角,同时还要进行热处理,以提高承载能力和使用寿命。
热处理后还要进行内孔、内孔端面的磨削加工和齿形的精整加工。
综上所述,零件的技术条件主要分以下两种: 1.零件的表面粗糙度和加工精度如零件图所示:齿面的粗糙度Ra 0.8,加工精度IT5~IT6; 齿轮内孔尺寸ø025.0030+,由于齿轮与第二轴上的轴承有配合要求,故其不仅加工经济公差等级比较高而且其表面粗糙度为Ra 0.4。
一般载货汽车变速器和拖拉机变速箱齿轮的精度一般是6到7级精度,表面粗糙度不大于Ra 3.2. 2.各表面间的位置精度如零件图所示,零件的D 、E 、F 面三处具有形位公差要求;D 面对于定位基面φ029.001.070++的定位基准垂直度为0.015,平面度为0.01;E 面对于内孔的定位基准的垂直度为0.05,端面的平面度为0.01;F 面对于内孔的定位基准的垂直度为0.03;1.3零件的其它技术要求1.未注明倒角1X45○2.应除去加工时产生的毛刺,夹角平滑。
3.强力喷丸处理(磨齿后)。
4.热处理:渗碳淬火表面硬度650~800HV;以大端齿根部为准,渗碳层厚度为0.4~1.0mm;心部硬度513HV。
20CrMnTiH、20CrMoH等温正火工艺
20CrMnTiH、20CrMoH等温正火工艺正火是汽车变速器齿轮、轴类零件锻坯预先热处理的常用工艺。
目的是为了获得均匀、接近理想平衡状态的组织(铁素体和珠光体)和合适的硬度范围(160-190HB),以提高切削加工性和控制最终热处理变形。
但常规正火由于受设备限制采用堆装、堆冷方式,会造成不同零件之间或同一零件不同部位的冷却速度及其组织、应力和硬度的较大差别,导致切削加工性能恶化和热处理变形加大,从而降低齿轮精度等级和影响齿轮的使用性能。
另外,随着汽车行业中齿轮、轴类零件精度等级的提高以及Ni-Cr钢的普及应用,采用常规正火工艺已经不能适应生产的要求,为此我们公司于2007年底进行技术改造,购进了一条等温正火线,并于2008年六月份调试完成。
在等温正火线的调试以及试生产过程中,我们对20CrMnTiH、20CrMoH、SAE8620 H等材料进行了等温正火试验,通过工艺试验得出以下结论:要获得均匀分布的组织、硬度以及良好的机械切削加工性能,主要取决于正火工艺过程中快冷、缓冷的设计和等温温度、时间的确定。
下面做一简单的总结回顾:一、等温正火及其关键工艺参数:根据常用低碳合金渗碳钢的奥氏体连续冷却转变曲线,其共同特点是:奥氏体均匀化后,在随后的冷却过程中,由于冷却速度的不同,正火后不同零件之间或同一零件的表面与心部组织也不相同(铁素体与珠光体的含量比例或含有贝氏体)。
要完全获得理想均匀的铁素体和珠光体,则对冷却速度的限制较为严格,这是常规正火很难实现的。
等温正火的原理是将工件加热到AC3或ACcm以上30~50℃,保温适当时间后,以合适的方式冷却到珠光体转变区域某一合适温度,并在此温度下保温,使不同零件和同一零件的不同部位温度均匀化,并在该温度下均匀地完成铁素体+珠光体转变,然后在空气中冷却的正火工艺。
由于不同零件和零件的不同部位基本上是在同一温度下完成组织转变的,所以转变产物及应力、硬度分布是均匀的,从而克服了常规正火过程中零件冷却速度难以控制、零件冷却不均匀的问题。
- 1、下载文档前请自行甄别文档内容的完整性,平台不提供额外的编辑、内容补充、找答案等附加服务。
- 2、"仅部分预览"的文档,不可在线预览部分如存在完整性等问题,可反馈申请退款(可完整预览的文档不适用该条件!)。
- 3、如文档侵犯您的权益,请联系客服反馈,我们会尽快为您处理(人工客服工作时间:9:00-18:30)。
汽车变速器齿轮的加工工艺
齿轮是机械传动中应用极为广泛的零件之一。
汽车同步器变速器齿轮起着改变输出转速传递扭矩的作用,所以加工齿轮的要求相对要严格一些。
标签:齿轮毛坯设计;加工工艺路线;工艺性分析;加工的余量及其公差;磨齿夹具
变速器齿轮转速较高,温度和压力也很大。
负责着发动机动力输出的重任,是变速器中非常重要的部分,还需要承受较大的外力,必须有一定的抗冲击能力,正由于变速器齿轮这种特殊的工作状态,变速器的齿轮必须有较高的强度刚度,而且在高速工作中,需要能承受循环载荷的能力足够。
1.1齿轮的技术要求
A齿面的粗糙度Ra0.8.精度IT5~IT6;内孔尺寸中φ70 有配合要求,故其表面粮糙度要求也比较高Ra0.4,精度等级IT7;
油槽顶面也有粗糙度Ra0.8的要求,故在设计时要加入光整加工工序(公差等级参考《几何量工公差的与测量技术》P17);
其他表面粗糙度要求Ra3.2。
为IT10-IT12级精度,精车加工表面即可保证。
1.零件表面要进行渗碳淬火,使表面硬度达到650-800HV;
2.以A齿根部为准,渗碳层深度为0.4-1.0mm;
3.心部硬度为513HV;
4.强力喷丸处理(磨齿后);
1.2齿轮材料的切削加工性于严重而于
在设计汽车变速器传动齿轮时,常用的加工材料有:20CrMnTi、20CrMo、20CrMnVB,40Cr、40MnB、45号钢等,在本论文中选用20CrMnTi。
20CrMnTi是渗碳钢,渗碳钢通常为含碳量为0.17%到0.24%的低碳钢。
汽车上多用其制造传动齿轮。
其淬透性较高,在保证淬透情况下,具有较高的强度和韧性,特别是具有较高的低温冲击韧性。
20CrMnTi表面渗碳硬化处理用钢。
1.3齿轮的加工工艺分析
1)零件的内腔与外形应尽量采用统一的几何类型和尺寸尤其是加工面转接
处的凹圆弧半径,一根轴上直径差不大的各轴肩处的退刀槽宽度等最好统一尺寸。
2)内槽及缘板之间的转接圆角半径不应过小这是因为此处圆角半径大小决定了刀的直径,而刀具直径的大小与被加工工件轮廓的高低影响着工件加工工艺性的好坏。
2.1毛坯种类的确定
毛坯种类的不同,决定零件的材料、形状、生产性质及生产中获得的可能性。
此零件毛坯外形比较简单,只有四个沿中φ84mm圆周均布的油槽,另外作为变速器齿轮在工作过程中要承受较大力的作用,要提高材料的强度,
3.1工艺路线的制定
所选加工方法应考虑每种加工方法加工经济精度、零件材料可加工性、工件结构形状和尺寸,生产类型及工厂现有身产条件。
加工表面技术要求,首先选择能保证该要求最终加工方法,然后依次向前选定各预备工序加工方法。
主要加工表面工艺路线安排如下:
大齿:粗车-精车-滚齿-磨齿
小齿:粗车-精车-插齿
齿轮内孔:粗车-半精-精车-磨削
对于那些加工质量要求较高或较复杂的零件,通常将整个工艺路线划分为以下几个阶段:
1)粗加工阶段:主要任务是切除各表面上的大部分余量,其关键问题是提高生产率,可进行几次粗加工。
2)半精加工阶段:完成次要表面的加工,并为主要表面的精加工做准备。
3)精加工阶段:保证各主要表面达到图样要求,其主要发问题是如何保证加工质量。
粗基准:用未加工过的毛坯表面做基准。
精基准:用已加工过的表面做基准。
粗车右端面以大端外圆轴线作为基准夹紧,以左端面作为轴向的定位基准;
为了保证零件工作正常,应该使外部较硬而心部较韧,因此采用渗碳淬火,为了粗车和半精车时方便加工,保证渗碳深度的均匀,将渗碳安排在粗加工之后,磨削加工之前。
1.检验丁序分别有:中间检查、热处理前检查、最终检查。
中问检验安排在滚齿在粗加工之后,热前加工安排在渗碳淬火之前,最终检验放在所有工序都完成之后。
2.加工后对A齿喷丸处理集磷化处理,以改变工件的表面物理化学性能,使齿轮外部较硬而心部较韧。
3.为了保证齿轮的加工要求,热前检验及对A齿进行喷丸处理之前要对工件进行清理。
3..1机床的选择
数控机床主要规格的尺寸应与工件的轮廓尺寸相适应。
即小的工件應当选择小规格的机床加工,而大的工件则选择大规格的机床加工,做到设备的合理使用。
3..2切削刀具的选择
20CrMnTi属于易加工合金钢,硬度较低,各种机床所带有的通用刀具就可以满足加工需求。
3.3量具的选择
正确合理的选用量具是保证产品零件质量的重要条件之一。
但选择量具要考虑多方面的因素。
例如,测量误差和加工误差之间的分配,被测对象的精度要求,结构尺寸的大小、形状、重量和所用的材料,加工的工艺条件、批量、使用测量器具的精确度和经济性等等。
因此选择量具是一个比较复杂的问题。
要正确合理
3..4夹具的选择
数控加工的特点对夹具提出了两个基本要求,一是保证夹具的坐标方向与机床的坐标方向相对固定;二是要能防调零件与机床坐标系的尺寸。
3.5各工序机床、夹具、刀具、量具汇总
00毛坯锻造:
央具:毛坯型模
5-15齿坯加工:
机床:S3-242数控车床
央具:通用三爪卡盘
刀具:车刀(具体型号见标准)
量具:长度测量用游标卡尺,角度测量用角度样板20齿坯加工:机床:LB-157数控车床
央具:通用三爪卡盘
刀具:车刀(具体型号见标准)
量具:长度测量用游标卡尺,角度测量用角度样板
25J中间检查:
量具:游标卡尺、角度样板、专用量具
30滚齿:
机床:YBA3132高效滚齒机
央具:专用夹具
35齿端倒角:
机床:YA9320齿轮倒角机
夹具:通用夹具
刀具:车刀
量具:角度仪器
40加工小端结合齿:
机床:YS5120高速插齿机
央具:通用夹具
刀具:插齿刀
量具:万能测齿仪
45钻油孔:
机床:ZF047液压半自动机床
夹具:通用夹具
刀具:麻花站
量具:内径千分尺
50清洗:
机床:QXLB-80喷淋式清洗机
55J热处理前检查:
量具:游标卡尺、角度尺、万能测齿仪60渗碳处理:
机床:CJ4462双排渗碳机
65磨内孔及大端端面:
机床:F115内孔端面磨床
央具:专用央具
刀具:砂轮
量具:游标卡尺、内径千分尺
70磨小端端面:
机床:MG7340高精度卧轴圆台平面磨床夹具:通用夹具
刀具:砂轮
量具:游标卡尺(用样板法测量表面粗糙度)
75磨齿:
机床:FKP3261蜗杆砂轮磨床
央具:通用夹具
刀具:砂轮
量具:万能测齿仪
80清洗:
机床:通过性清洗机
85喷丸:
机床:HC-34强力喷丸机
90磷化处理:
机床:磷化
95J最终检查:
量具:万能测齿仪、游标卡尺、角度样板、专用量具(检查形状位置公差等)
结束语
通过这次课设,我基本上掌握了汽车变速器齿轮加工的工艺规程。
感谢老师和学校提供的这次机会,我本来不怎么会汽车制造工艺学。
通过这个实习我学习到了如何查询公差,对互换性和汽车制造工艺学有了更深的了解。
参考文献:
[1] 徐知行.汽车拖拉机制造工艺设计手册北京理工大学出版社,1997
[2] 王宝玺.汽车制造工艺学机械工业出版社,2007。