正确的电镀的前处理非常关键
不锈钢电镀工艺流程

不锈钢电镀工艺流程不锈钢电镀是一种常用的金属表面处理工艺,其目的是在不锈钢表面形成一层金属镀层,以增加其表面的硬度、耐磨性和防腐蚀性。
下面是一种常见的不锈钢电镀工艺流程。
首先,准备工作是非常关键的。
首先需要将不锈钢件进行清洗,以去除表面的污垢和氧化物。
常用的清洗方法有酸洗、碱洗和机械清洗等。
酸洗可以去除氧化层,碱洗可以去除油脂和有机物,机械清洗可以去除表面的污垢和磨损层。
接下来是进行不锈钢电镀前的预处理工艺。
首先要进行酸洗处理,使用浓硫酸或盐酸溶液进行浸泡,以去除表面的氧化层和污垢。
然后进行钝化处理,即使用酸性溶液浸泡,使不锈钢表面形成一层钝化膜,以减少后续电镀工艺中的氧化和腐蚀。
接下来是电镀工艺。
首先是进行镀前处理,即将经过预处理的不锈钢件放入除油槽中进行除油处理,以去除表面的油脂和有机物。
然后进行镀层处理,即将不锈钢件放入电解槽中,与阳极材料连接,通过电流的作用,使金属离子在阳极材料上析出,并在不锈钢件表面形成一层金属镀层。
最后进行镀后处理,即将电镀后的不锈钢件进行清洗、干燥和检验,以确保镀层的质量和外观。
最后是进行保护处理。
不锈钢电镀后的镀层容易受到氧化和腐蚀的影响,因此需要进行保护处理,以延长镀层的使用寿命。
常用的保护方法有热处理、涂层和封闭处理等。
热处理可以使镀层结构变得更加致密和稳定;涂层可以形成一层保护膜,防止氧化和腐蚀;封闭处理可以将镀层与环境隔绝,减少与外界的接触。
综上所述,不锈钢电镀工艺流程包括准备工作、预处理工艺、电镀工艺和保护处理。
通过合理的工艺流程和严格的操作,可以制备出质量好、外观漂亮且具有优良性能的不锈钢电镀件。
电镀前处理工艺流程

电镀前处理工艺流程电镀前处理工艺流程是指在进行电镀之前对工件进行处理,以保证电镀的质量和效果。
下面是一份常见的电镀前处理工艺流程:1. 清洗(Cleaning):将工件放入清洗槽中,使用碱性或酸性清洗剂清洗表面的油脂、污渍和其他杂质。
清洗槽中可以加热或超声波来增加清洁效果。
2. 酸洗(Acid Pickling):将工件放入酸洗槽中,使用酸性溶液(如硫酸或盐酸)进行酸洗,目的是去除表面的氧化物、锈蚀物和其他有害物质,以提高镀层的附着力。
3. 防酸处理(Acid Resistant Treatment):将工件浸入防酸液中,例如磷酸或硼酸液体,目的是形成一个防止酸洗液对工件表面的继续侵蚀和氧化的保护层。
4. 水冲洗(Water Rinsing):将工件从酸洗槽中取出,通过水冲洗去除残留的酸洗液和防酸液,以防止其对后续工艺造成不良影响。
5. 除油(Degreasing):将工件放入除油槽中,使用有机溶剂或碱性溶液去除表面的油脂和其他有机物,以提高电镀的附着力和均匀性。
6. 再水冲洗(Water Rinsing):将工件从除油槽中取出,通过水冲洗去除残留的溶剂或碱性溶液,以防止其对后续工艺造成不良影响。
7. 预光(Pre-polishing):将工件放入预光槽中,使用研磨材料或预光剂进行预光处理,以去除表面的凹陷、细微划痕和氧化物,以改善镀层的外观和质量。
8. 再次水冲洗(Water Rinsing):将工件从预光槽中取出,通过水冲洗去除残留的研磨材料或预光剂,以防止其对后续工艺造成不良影响。
9. 碱洗(Alkaline Cleaning):将工件放入碱洗槽中,使用碱性溶液进行碱洗,目的是去除预光过程中生成的氧化物和其他杂质,以提高电镀的质量和光亮度。
10. 最后水冲洗(Final Water Rinsing):将工件从碱洗槽中取出,通过水冲洗去除残留的碱洗液和其他杂质,以确保工件表面干净无污染。
以上是一份常见的电镀前处理工艺流程,其中细节还可以根据具体的工件和要求进行调整。
电镀前预处理

电镀前预处理前处理的意义一般前处理工程过程为,研磨,预备,洗净水,洗电解脱酯水,洗酸浸及活性化水,中和,水洗,电镀。
1.1 前处理的目的前处理的目的是为了得到良好的镀层,由于镀件在制造、加工搬运、保存期间会有油酯、氧化物锈皮、氢氧化物、灰尘等污物附着于镀件表面上,若不去除这些污物而进行电镀将得不到良好的镀层。
镀· 件品质,前处理占很重要的地位。
1.2 前处理不良所造成之镀层缺陷前处理不良所造成之镀层缺陷,有下列几项:(1)剥离, (2)气胀,(3)污点,(4)光泽不均,(5)凹凸不平,(7)小孔 (8)降低耐蚀性,(9)脆化。
电镀之不良,前处理占很大的原因。
1.3 污物的种类污物的种类,可分为有机物及无机物。
有机物污物主要是动物性油酯,植物性油酯及矿物性油酯,无机物污物是金属氧化物、盐类、尘埃、及砂土。
另外由有机物和无机物污物之物如研磨屑、研磨材料。
动物性及植物性油酯可被化缄剂皂去除。
矿物性油污无法被缄剂皂去除需用三菉乙烯、汽油、石油溶剂乳化剂等去除。
无机物污物可被酸或缄溶解,利用酸、缄浸渍、化学或电解方法去除及机械研磨方法去除。
无机、有机混合污物,去除较困难,除了利用化学方法,亦须用电解,机械研磨等方法联合应用去除。
1.4 电镀前处理去除的典型污物(1) 润滑油 (6) 淬火残留物(2) 切削油 (7) 热处理盐(3) 研磨油 (8) 热处理盐(4) 热斑 (9) 污迹(5) 锈及腐蚀物 (10) 油漆及油墨1.5 表面清洁测定表面清洁度测定,在工场最实用的方法是用水冲(water-beaktest),检查表面水是否均匀润湿,如果是均匀润湿则为清洁表面,反之则不清洁。
(工件表面有一层连续的水膜存在,无间断状态,即表示脱脂彻底,反之,如果有水珠存在,则表示脱脂不彻底,还得继续进行脱脂)材质的判别水钻(不能电解)水钻是一种俗称(又名水晶钻石,莱茵石英文名:crystal,rhinestone)其主要成分是水晶玻璃,是将人造水晶玻璃切割成钻石刻面得到的一种饰品辅件,这种材质因为较经济,同时视觉效果上又有钻石般的夺目感觉。
电镀工序质量控制
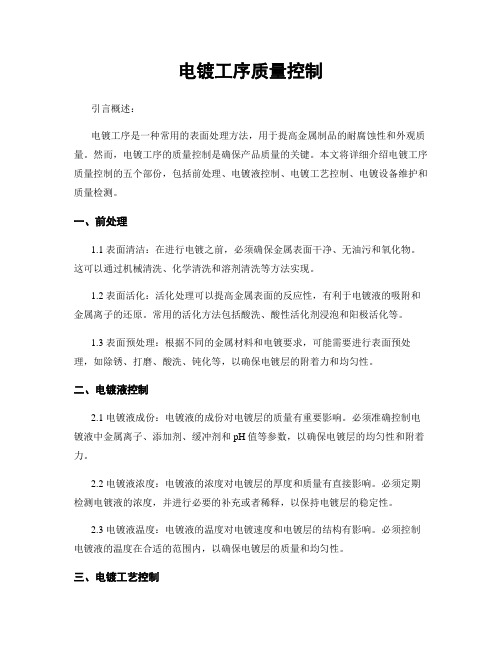
电镀工序质量控制引言概述:电镀工序是一种常用的表面处理方法,用于提高金属制品的耐腐蚀性和外观质量。
然而,电镀工序的质量控制是确保产品质量的关键。
本文将详细介绍电镀工序质量控制的五个部份,包括前处理、电镀液控制、电镀工艺控制、电镀设备维护和质量检测。
一、前处理1.1 表面清洁:在进行电镀之前,必须确保金属表面干净、无油污和氧化物。
这可以通过机械清洗、化学清洗和溶剂清洗等方法实现。
1.2 表面活化:活化处理可以提高金属表面的反应性,有利于电镀液的吸附和金属离子的还原。
常用的活化方法包括酸洗、酸性活化剂浸泡和阳极活化等。
1.3 表面预处理:根据不同的金属材料和电镀要求,可能需要进行表面预处理,如除锈、打磨、酸洗、钝化等,以确保电镀层的附着力和均匀性。
二、电镀液控制2.1 电镀液成份:电镀液的成份对电镀层的质量有重要影响。
必须准确控制电镀液中金属离子、添加剂、缓冲剂和pH值等参数,以确保电镀层的均匀性和附着力。
2.2 电镀液浓度:电镀液的浓度对电镀层的厚度和质量有直接影响。
必须定期检测电镀液的浓度,并进行必要的补充或者稀释,以保持电镀层的稳定性。
2.3 电镀液温度:电镀液的温度对电镀速度和电镀层的结构有影响。
必须控制电镀液的温度在合适的范围内,以确保电镀层的质量和均匀性。
三、电镀工艺控制3.1 电流密度:电流密度对电镀层的均匀性和结构有重要影响。
必须根据产品要求和电镀液特性,合理选择和控制电流密度,以确保电镀层的质量。
3.2 电镀时间:电镀时间决定了电镀层的厚度和质量。
必须根据产品要求和电镀液特性,精确控制电镀时间,以保证电镀层的一致性和稳定性。
3.3 搅拌和过滤:搅拌和过滤可以提高电镀液的均匀性和纯净度。
必须定期检查和维护搅拌和过滤设备,以确保电镀液的质量和稳定性。
四、电镀设备维护4.1 设备清洁:电镀设备的清洁是确保电镀质量的前提。
必须定期清洗电镀槽、电极和管道等设备,以去除污垢和残留物。
4.2 设备维护:电镀设备的正常运行对电镀质量的稳定性至关重要。
电镀紧急事项处理
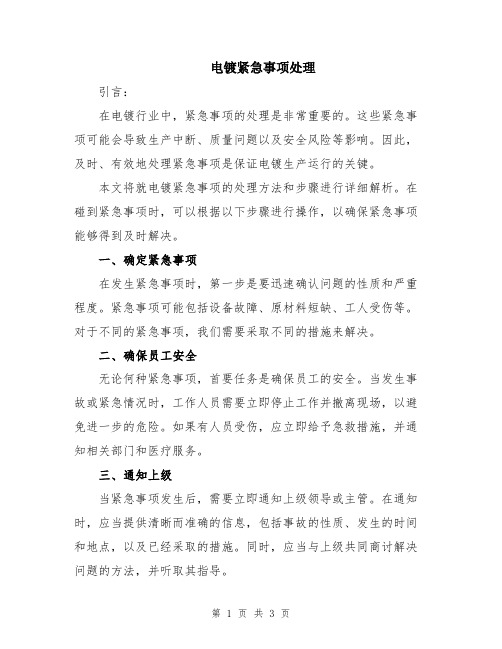
电镀紧急事项处理引言:在电镀行业中,紧急事项的处理是非常重要的。
这些紧急事项可能会导致生产中断、质量问题以及安全风险等影响。
因此,及时、有效地处理紧急事项是保证电镀生产运行的关键。
本文将就电镀紧急事项的处理方法和步骤进行详细解析。
在碰到紧急事项时,可以根据以下步骤进行操作,以确保紧急事项能够得到及时解决。
一、确定紧急事项在发生紧急事项时,第一步是要迅速确认问题的性质和严重程度。
紧急事项可能包括设备故障、原材料短缺、工人受伤等。
对于不同的紧急事项,我们需要采取不同的措施来解决。
二、确保员工安全无论何种紧急事项,首要任务是确保员工的安全。
当发生事故或紧急情况时,工作人员需要立即停止工作并撤离现场,以避免进一步的危险。
如果有人员受伤,应立即给予急救措施,并通知相关部门和医疗服务。
三、通知上级当紧急事项发生后,需要立即通知上级领导或主管。
在通知时,应当提供清晰而准确的信息,包括事故的性质、发生的时间和地点,以及已经采取的措施。
同时,应当与上级共同商讨解决问题的方法,并听取其指导。
四、组织应急小组针对不同的紧急事项,我们可以组织应急小组来处理。
应急小组成员应包括相关管理人员、技术专家、工程师和维修人员等。
应急小组的主要任务是通过讨论和分析来找出解决紧急事项的最佳方式,并及时采取行动。
五、制定应急计划针对紧急事项,制定详细的应急计划非常重要。
应急计划应包括应对措施、责任分工、资源需求等。
在制定应急计划时,应充分考虑安全因素和风险评估。
确保每个应急措施都符合相关的标准和规定。
六、实施应急措施在制定好应急计划后,要立即实施应急措施。
这可能包括修理设备、调整生产计划、购买紧急原材料等。
在实施应急措施时,一定要确保工作人员的安全,并密切监控进展情况。
七、监控并评估在处理紧急事项过程中,需要不断监控并评估效果。
这样可以及时发现问题并进行调整。
监控方式可以包括现场检查、数据分析、反馈收集等。
通过不断监控和评估,可以确保紧急事项得到有效解决。
电镀的工艺流程
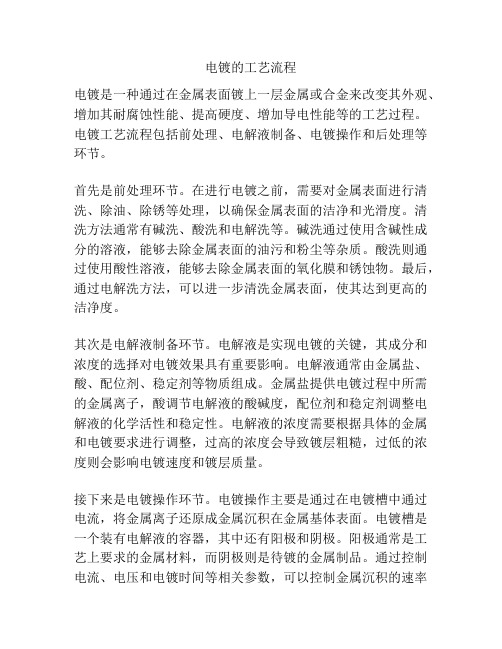
电镀的工艺流程电镀是一种通过在金属表面镀上一层金属或合金来改变其外观、增加其耐腐蚀性能、提高硬度、增加导电性能等的工艺过程。
电镀工艺流程包括前处理、电解液制备、电镀操作和后处理等环节。
首先是前处理环节。
在进行电镀之前,需要对金属表面进行清洗、除油、除锈等处理,以确保金属表面的洁净和光滑度。
清洗方法通常有碱洗、酸洗和电解洗等。
碱洗通过使用含碱性成分的溶液,能够去除金属表面的油污和粉尘等杂质。
酸洗则通过使用酸性溶液,能够去除金属表面的氧化膜和锈蚀物。
最后,通过电解洗方法,可以进一步清洗金属表面,使其达到更高的洁净度。
其次是电解液制备环节。
电解液是实现电镀的关键,其成分和浓度的选择对电镀效果具有重要影响。
电解液通常由金属盐、酸、配位剂、稳定剂等物质组成。
金属盐提供电镀过程中所需的金属离子,酸调节电解液的酸碱度,配位剂和稳定剂调整电解液的化学活性和稳定性。
电解液的浓度需要根据具体的金属和电镀要求进行调整,过高的浓度会导致镀层粗糙,过低的浓度则会影响电镀速度和镀层质量。
接下来是电镀操作环节。
电镀操作主要是通过在电镀槽中通过电流,将金属离子还原成金属沉积在金属基体表面。
电镀槽是一个装有电解液的容器,其中还有阳极和阴极。
阳极通常是工艺上要求的金属材料,而阴极则是待镀的金属制品。
通过控制电流、电压和电镀时间等相关参数,可以控制金属沉积的速率和质量。
在电镀过程中,还需要定时检查镀液的浓度和PH值,并根据需要进行调整。
最后是后处理环节。
在电镀结束后,为了提高镀层的表面质量,可以进行一些后处理操作。
常见的后处理包括清洗、抛光、封孔等。
清洗可以去除镀液残留在镀层上的杂质,抛光可以提高镀层的光亮度,封孔则能够增加镀层的密封性和耐腐蚀性能。
完成这些后处理操作后,电镀的工艺流程就算完整。
总之,电镀是一项复杂的工艺,其工艺流程包括前处理、电解液制备、电镀操作和后处理等环节。
每一个环节的操作都需要专业的知识和经验,以确保电镀的质量和效果。
“铜包钢”镀铜的前处理和后处理工艺
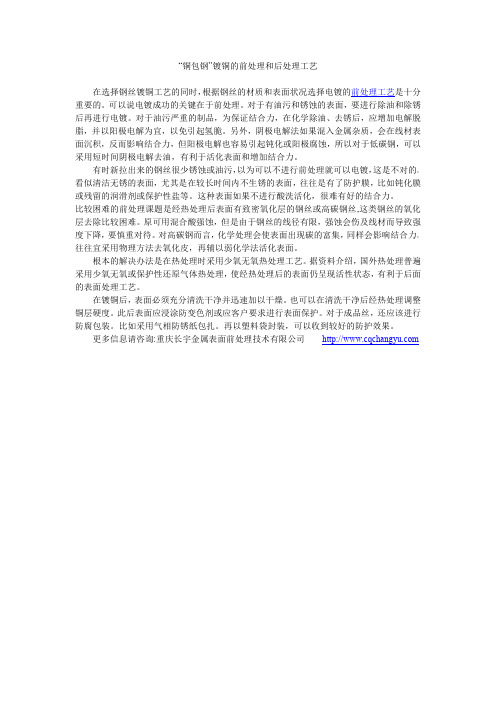
“铜包钢”镀铜的前处理和后处理工艺在选择钢丝镀铜工艺的同时,根据钢丝的材质和表面状况选择电镀的前处理工艺是十分重要的。
可以说电镀成功的关键在于前处理。
对于有油污和锈蚀的表面,要进行除油和除锈后再进行电镀。
对于油污严重的制品,为保证结合力,在化学除油、去锈后,应增加电解脱脂,并以阳极电解为宜,以免引起氢脆。
另外,阴极电解法如果混入金属杂质,会在线材表面沉积,反而影响结合力,但阳极电解也容易引起钝化或阳极腐蚀,所以对于低碳钢,可以采用短时间阴极电解去油,有利于活化表面和增加结合力。
有时新拉出来的钢丝很少锈蚀或油污,以为可以不进行前处理就可以电镀,这是不对的。
看似清洁无锈的表面,尤其是在较长时间内不生锈的表面,往往是有了防护膜,比如钝化膜或残留的润滑剂或保护性盐等。
这种表面如果不进行酸洗活化,很难有好的结合力。
比较困难的前处理课题是经热处理后表面有致密氧化层的钢丝或高碳钢丝,这类钢丝的氧化层去除比较困难。
原可用混合酸强蚀,但是由于钢丝的线径有限,强蚀会伤及线材而导致强度下降,要慎重对待。
对高碳钢而言,化学处理会使表面出现碳的富集,同样会影响结合力。
往往宜采用物理方法去氧化皮,再辅以弱化学法活化表面。
根本的解决办法是在热处理时采用少氧无氧热处理工艺。
据资料介绍,国外热处理普遍采用少氧无氧或保护性还原气体热处理,使经热处理后的表面仍呈现活性状态,有利于后面的表面处理工艺。
在镀铜后,表面必须充分清洗干净并迅速加以干燥。
也可以在清洗干净后经热处理调整铜层硬度。
此后表面应浸涂防变色剂或应客户要求进行表面保护。
对于成品丝,还应该进行防腐包装。
比如采用气相防锈纸包扎。
再以塑料袋封装,可以收到较好的防护效果。
更多信息请咨询:重庆长宇金属表面前处理技术有限公司。
铁件电镀前处理工艺(一)

铁件电镀前处理工艺(一)
铁件电镀前处理工艺
引言
•铁件的电镀前处理工艺是确保电镀质量的关键环节之一。
•正确的电镀前处理工艺能够提高铁件的表面光洁度和粘着力,有效延长电镀层的使用寿命。
清洗
1.使用溶液清洗铁件表面,去除铁锈、灰尘和油污等杂质。
2.可选用碱性清洗溶液和酸性清洗溶液。
碱性清洗溶液适用于去除
油污,酸性清洗溶液适用于去除铁锈和氧化层。
脱脂
•脱脂的目的是去除铁件表面的油脂,提高电镀层的附着力。
1.使用有机溶剂脱脂,如石油醚、酒精等。
2.也可以采用碱性脱脂剂,如钠碱、氢氧化钠等。
酸洗
•酸洗可以去除铁件表面的氧化层和其他污染物。
1.使用稀硫酸、盐酸等酸性溶液进行酸洗。
2.酸洗时间和温度要控制好,过长或过高的温度可能会导致铁件表
面的腐蚀。
磷化
•铁件表面磷化可以提高电镀层的附着力和耐蚀性。
1.使用磷酸进行磷化处理,可以形成均匀的磷化层。
2.磷化处理的温度和时间要根据具体情况进行调整。
上述步骤的注意事项
•操作过程要严格按照工艺要求进行,避免操作失误。
•避免不必要的浪费和污染,根据实际情况控制使用的溶液和溶液的浓度。
•操作环境要干燥,避免水气对处理效果产生影响。
结论
•铁件电镀前处理工艺对电镀质量和使用寿命具有重要影响。
•清洗、脱脂、酸洗和磷化是常用的铁件电镀前处理步骤。
•合理控制工艺参数,严格按照操作要求进行,能够提高电镀层的质量和稳定性。
- 1、下载文档前请自行甄别文档内容的完整性,平台不提供额外的编辑、内容补充、找答案等附加服务。
- 2、"仅部分预览"的文档,不可在线预览部分如存在完整性等问题,可反馈申请退款(可完整预览的文档不适用该条件!)。
- 3、如文档侵犯您的权益,请联系客服反馈,我们会尽快为您处理(人工客服工作时间:9:00-18:30)。
正确的电镀的前处理非常关键,特别是化学镀镍。
前处理的重要性及其对最终镀层的影响是造成电镀生产故障的首要因素,但却经常被人们忽视。
并且很轻易地把注意力放在化学镀镍槽上。
本文的重要目的之一,就是希望大家能正确地看待这一问题。
要说明这一点,其实也非常简单,化学镀镍前处理的重要性与我们在日常生活中所遇到事情有许多相似之处。
比如,当我们想给家里的一件家俱上漆时所要面对的问题,与电镀操作人员所遇到的情况就非常相似。
颜色的选择在某种情况下我们可以先不予置否。
其它问题,比如漆的种类,就比较关键了。
漆有许多种,包括环氧漆、珐琅漆、聚酯漆等,我们还可以说出一大堆来。
选择哪一种漆取决于它的性能,以及家俱的用途、环境。
如果在上漆前,不做好必要的表面准备的话,恐怕你就要花更多的时间,更多的钱,以及忍受那些不必要的麻烦了。
希望大家能从这一事例中悟到点东西。
化学镀镍也是这样,当我们有了一定经验后,就会马上非常确定地意识到,合理的前处理工艺以及工序的选择与选择一种好的化学镀镍药水一样地重要。
作为一个电镀从业者,我见到过许多电镀生产线的不足甚至错误。
而每当我试图指出这些不足时,总是听到什么“我们要赶生产,没有多余的时间花在什么除油、水洗上,我们也没有多余的地方去放置另外的槽子,我们不能让生产停下。
只要没事,就够了”。
任何操作都会产生一定的后果,不论正确的、还是错误的,都会在最终工件的镀层质量上表现出来。
不幸的是,许多负面的后果,只有到造成质量问题,甚至是废品时,才能逐渐意识到:这都是自己没有调整那些工艺上的不足引起的。
以下谈到的正确的指导性原则,以及一些有效的操作工序,可以为生产提供保障。
有许多基本的概念、规则,会影响到镀层的最终质量。
以下的几点先给大家提供一些基础参考:1.所有的金属都是不同的。
2.不同的金属需要不同的前处理,除油剂工序以及具体地操作方法。
3.没有“万金油式”的除油剂。
4.更没有“放置四海皆准”的前处理工艺。
5.从没有哪个来源,可以提供经证实的适用于所有金属的前工艺。
但这样的信息却充滞各处。
6.许多发表的前处理工艺都有再思考的必要。
7.我们唯一的法宝就是不停地尝试,不断地调整和改进。
以上这些概念性东西,经常在有点急迫的化镀生产安排下被误用,误解,不被认同或忽视。
但是在镀后的工件上发现问题时,就把注意力首先放在化学镀液上。
当然,我们也无法清楚地感觉到以上的这几点会浪费我们多少不必要的精力。
但却不能停止一而再,再而三的强调:“已经可以证实的是电镀故障中有90-95%与除油或前处理有关。
”这一点你可以从许多有关电镀的专业杂志、书籍上的文章中看到。
其实这些概念,非常地浅显,但却一次次地被忘记、忽略掉了。
例如,在同一条生产线上用相同的工艺和工序处理铁件、铜件、黄铜件。
有许多正确的工艺实例,但这也一样需要做一些试验性的生产,以选择出最佳的操作工序。
如果我们假设任何工件都是始终如一的,比如有相同的热处理造成的氧化皮,相同数量的油污,以及镀液稳定,那除油和镀液操作就简单多了。
尽管我们所使用的药水都是非常好的产品,依然需要在针对一种具体工件基底,选择正确的前处理工艺时,做许多调整工作。
还有,生活中的许多思维方法,一样适用于化镀生产。
比如,人们总是“先看到树林,然后才能看清是槐树,还是杨树。
”这一句话移到化学镀镍生产中,简单地讲,意思就是:当你处理故障时,先要看那些基本的,显而易见的方面,然后再考虑那些比较特别的,不清楚的地方。
另外还有“带入,带出”,简单地说就是:成功的化学沉镍过程,需要一系列步骤,而这些步骤就是:前面的前处理工序,从工件表面上除去某些东西。
例如,在除油工序中除去零件上的油污,而我们也知道与此同时也不可避免地在工件表面会带有除油剂中的一些东西。
我们可以把化学镀镍生产简单地分解成几个单一步骤:每一个步骤,都是要除去表面上的一些东西,而在下一步骤中表面上又会带上另外一些东西。
要想生产顺利不出问题,这一概念一定要做到实处:从某一工艺步骤中表面带上的膜,必需与下一步骤相适应,而不能造成问题的产生。
化学镀镍生产中的这些简单的步骤就是,除油,酸活化,沉镍,后处理。
认知这一事实对于任何金属来讲,前处理也不过是一种简单的工艺。
而针对所加工的特定基材,选择正确的活化工艺,才是我们当前生产中要特别对待的困难。
言归正传,现在开始解释本文题目中的…五字经‟。
曾经几何时,沉镍的质量好坏好像只是沉镍操作人员的责任。
其实,现在的ISO、QS也好,还是其它质量体系,教给我们要在质检,设计,机加工,热处理,电镀及最终的使用者之间共同承担化学沉镍零件的质量责任。
而对于沉镍操作人员来讲,首要的就是理解好这…五字经‟。
这…五字经‟分别代表:基材、除油、水洗、活化和沉镍工序。
希望大家能活用这几点。
生产出问题时,人们容易手忙脚乱。
在这种烦燥的心情下,想短时间解决问题,往往是让人头痛的。
如果问题解决了,最好找出原因,找出需要改正、调整、注意的地方。
以便在今后的生产中避免再次发生类似的问题。
希望大家能以…五字经‟去梳理思路。
也许能减少些痛苦的发生。
…五字经‟中的基材化学镀镍有许多自己的特性,可以运用到许多材料表面,以提供或加强这些材料本身的性能。
大家都理解这样一个情况:化学镀镍层的质量好坏与金属基底的质量好坏息息相关,因为化学镀镍没有整平能力,也不能盖住基底的缺陷。
事实是,许多基底上的毛病,在工件沉镍处理后,会变得更加明显。
很少,如果有的话,化学镀镍能盖住基底上的问题,象什么:针孔,机加工或研磨后留下的纹路。
工件冲、压、钻或热处理的方式对化镀质量有非常大的影响。
嵌入工件表面的那些难以除去的油污,或是其它什么东西,会导致镀层白斑,结合力差,甚至不上镍。
在正常的生产线上加工一种工件时,它是否经过热处理或表面硬化处理,上线前必须搞清楚。
因为这也许需要对前处理工序的操作进行些调整。
这里要特别提出来的是,必须对来料的表面情况,在上线沉镍前进行检查,不能只让沉镍操作人员对一些机加工差所造成沉镍质量事故负责任。
这就需要机加工车间,五金厂,质检和沉镍操作人员加强沟通,大家一起合作,加工出质量高,稳定的化学镀层。
对于化学镀镍,并不是所有基材都是自发反应的。
镍,铁、铝经标准的前处理工序都能自发反应;铜、黄铜是不能自发反应的,需要另外的活化操作以保证引发。
这里需要理解的是,有些基材能否镀好还是有它的局限性的。
…五字经‟中的除油当我们谈到除油,提到的是前处理中的第一步骤:碱性化学除油。
除油剂的机理需要强调一下,这有助于解释那么多除油剂到底有什么不同的效用。
要除去的油污类型和基材类型决定着解决某种具体的除油问题及方法:基材除油方法铁、铁合金件热、强碱性除油剂及强酸铜、黄铜件热、低碱性除油剂及酸盐锌压铸件热、弱碱性或中性除油剂及专用活化酸铝合金件低温,弱碱性或中性除油剂及混有氟化物的硝酸要记住,前处理工序对某种基材上的某种油污很有效,但不一定对同一基材上的另一种油污就一样有效。
这一点经常被忽视,直到产生废品时才能让人意识到油污不但有它自己的特性,而且同一种油污,因为它使用的条件、方法不同也会变得难以去除。
工件上的油污是冲压、车削,还是热处理操作搞上去的?在电镀厂,可以看到各种各样的油污,包括什么:切削油、润滑油、研磨膏、硫化油、氯化油以及蜡,这些油污可以在工艺循环的除油部分除掉。
还有其它许多类型的东西也可以看作是油污,如:污迹、残渣、氧化物、锈和热处理造成的硬皮,这些油污由活化工序处理。
一旦选定除油工艺,操作温度、浓度及搅拌就是要考虑的重要因素。
通常,温度是除油剂的除油效果最重要的影响因素。
那怕只提高3、4度,也会很好地改善除油的效果。
在清除某些研磨膏和氯化蜡时,提高温度可以软化完全分解这些油污。
而这种化学除油剂,必须是那些可以高温操作的配方。
否则,超出它的温度操作范围反面会引出除油问题。
如果这种除油剂并不是可以用来高温操作的配方,那表面活性剂就会由于浊点问题而分离出来。
浊点代表的是:在特定浓度和温度下,一种表面活性剂的稳定性指标。
简单的讲,浊点是除油剂中表面活性剂成份的溶解度的一种测量方法。
这种情况一旦发生,不仅除油效果会变差,而且还会带到后序工序中去。
对任何除油剂来讲,它的表面活性剂体系才是最关键的。
表面活性剂可以溶解、分解、乳化、降解油污及其成份。
电解除油剂是通过电流来达到清洗作用的。
因为电解除油剂的主要作用并不在于清除油污,所以这一情况放到活化部分再讨论。
电解除油剂讲它是起活化作用的,似乎更适合些。
对于除油:需要记住的几点:1. 化学除油应该去除所有的油污及其成份2. 电解除油剂是用来去除某些特定的东西,而不是油污3. 通常只是一种油污在作怪,找到它然后除掉。
镀液还没有聪明到可以有选择地镀出点毛病的程度4. 除油剂的使用寿命,与工件上的油污种类、数量有关5. 化学除油槽之后水洗,能显著改善水洗效果及延长除油剂的使用寿命6. 水溶性的油污易于用低温、低碱性除油剂去除。
碱性越高就能更好地去除这类油污7. 抛光膏、研磨膏成份则在热碱性除油剂中可以去除8. 一些污渍可以在除油剂中泡掉9. 当出现故障时,不要急于提高除油剂的温度、浓度来解决,而应该先查清问题的来源10. 电解除油槽应该用正确的电极来提高效率,不要用槽壁做电极…五字经‟中的水洗水洗是化镀生产中,除了化学镀镍工序之外最重要的操作,但却经常被忽视。
在电镀这一行业里,废水处理及环保等问题与水洗在生产中的重要意义往往会产生冲突。
在一些地方,废水处理受到的关注甚至多于化镀本身。
但是,我们只要想一下:“电镀生产工序不过就是一些去除某些东西的一系列步骤组成的.”就可以理解到水洗在这其中所起到的作用啦。
化学除油后工件表面上有什么?正常情况下,上面有烧碱的残余、残余油污、润湿剂、表面活性剂。
增长水洗时间可以有效地去除这些表面的东西,尽管仍然会有一层含有少量的润湿剂或表面活性剂的水膜。
而在大多数情况下,这不会影响下一步工序(通常是电解除油工序)。
简单地在水里上下摇一下两下,并达不到什么效果。
就好像我们洗手,冲洗那么一下两下,洗不干净手上的肥皂。
化学除油之后的水洗时间增长(可以长至两分钟),对这一问题非常有好处。
还可以通过增加空气搅拌,逆流水洗等方法来提高水洗效率。
干净水应该从与水洗方向相反的水槽底部流入。
这一设计可以使干净水从高处的水槽底部流向低处水槽的液面出口。
在化学除油槽和电解除油槽之间加设水洗槽,对减少生产线上的油污污染非常有效。
许多生产线上,化学除油后就直接进入电解除油槽,中间没有水洗。
这确实简化了工艺步骤,但是从化学除油槽带出的乳化了的油污及其它副产物,会污染后续的工序,而且会缩短电解除油剂的使用寿命。
这一小小的改变,所带来的区别,你会不时地感觉到。
要减少废水的环保要求,越来越强烈,这其实也影响到提高水洗效率的能力。